PVC木塑生产工艺与生产中常见问题
PVC生产中的常见问题及解决方法
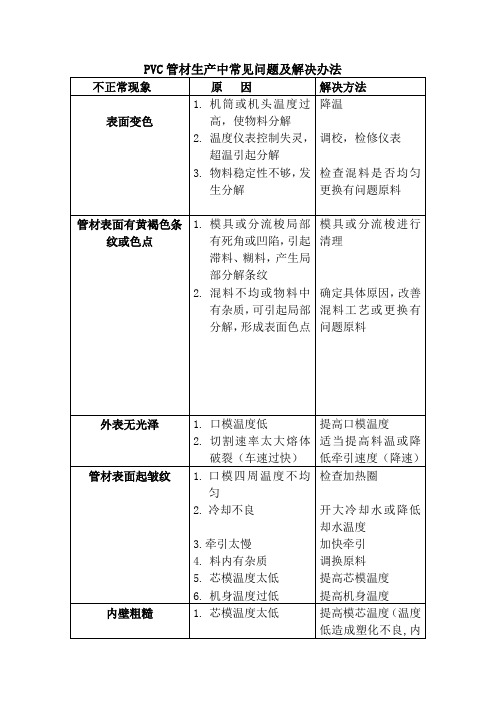
模具或分流梭进行清理
确定具体原因,改善混料工艺或更换有问题原料
外表无光泽
1.口模温度低
2.切割速率太大熔体破裂(车速过快)
提高口模温度
适当提高料温或降低牵引速度(降速)
管材表面起皱纹
1.口模四周温度不均匀
2.冷却不良
3.牵引太慢
4.料内有杂质
5.芯模温度太低
PVC管材生产中常见问题及解决办法
不正常现象
原 因
解决方法
表面变色
1.机筒或机头温度过高,使物料分解
2.温度仪表控制失灵,超温引起分解
3.物料稳定性不够,发生分解
降温
调校,检பைடு நூலகம்仪表
检查混料是否均匀更换有问题原料
管材表面有黄褐色条纹或色点
1.模具或分流梭局部有死角或凹陷,引起滞料、糊料,产生局部分解条纹
1.口模内壁不光滑,沾有析出物
2.定型模真空度不够,管材贴模不紧
3.温度太低,塑化不良
4.挤出速度过快,塑化不良
清理口模
提高真空度
提温或增加ACR加工助剂
降速
管材有明显的熔结线(合模线)
1.温度太低,塑化不良
2.挤出速度快,物料塑化不良
提高温度
降速
制作人;张忠诚
6.机身温度过低
检查加热圈
开大冷却水或降低却水温度
加快牵引
调换原料
提高芯模温度
提高机身温度
内壁粗糙
1.芯模温度太低
2.机筒温度过低,塑化不良
3.螺杆温度太高(给料转速与主机转速不合理;给料电机转速过快)
提高模芯温度(温度低造成塑化不良,内壁在模头处难以升温,故产生粗糙现象)
PVC管材生产中常见问题及解决办法
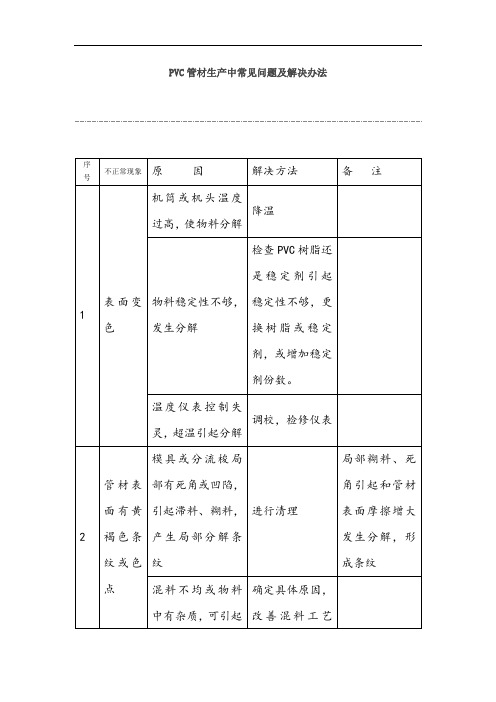
PVC管材生产中常见问题及解决办法PVC型材生产中常见问题及解决办法pvc管材变色问题2010-08-08 17:53型材在加工时就发现色泽不统一(如色泽有轻微偏差是允许的);(2)加热变形后型材明显黄变;(3)加热后状态良好,但型材制成门窗时间不长就变灰。
型材正常生产中不发黄,而在后来的成窗制品时发黄。
在型材生产过程中,当原料及模具等基本条件无变化时,如果将其塑化段及均化段的温度提高5℃左右,所产生的型材发生黄变倾向,也说明其热稳定效率不足,应增加热稳定剂的加入量,尤其是配方中加入荧光增白剂等增白助剂时,热稳定剂不足,增白效果不明显。
PVC分子结构与颜色的关系(1)因PVC树脂是一种热敏性塑料,其光稳定性较差,在热和光的作用下,支链发生脱HCI反应、多烯结构分子,当主链出现共扼双键数量不太多时产生微量色差,氯化氢首先会与周围潜在的对酸活性的物质发生反应,而共扼双键成为PVC分子链内新的活性位置,被光引发成大分子游离基后,PVC就容易遭受氧化,产生色变。
(2)PVC树脂中存在一定数量偏低低分子量组分,降低了聚合物的热稳定性,PVC分解的机理有游离基机理、离子机理、单分子机理等,PVC分解除稳定剂外还有可能受到PVC树脂本身质量的影响,如PVC树脂内是否存有残留过多的引发剂。
(3)聚合物中如存在某种杂质,例如在聚合过程中加人的引发剂、催化剂、酸、碱等去除不尽,或在储运过程中吸收水分,都会降低聚合物的稳定性。
因为这些物质能引起分子-离子降解反应,CPE 中含有较多Cl2、HCl等低分子物,易加速树脂热分解。
因此对稳定不好的PVC+CPE体系,通过增加稳定剂用量也可消除一些型材泛黄问题。
(4)硬PVC结构型材,它是由PVC作连续相的多相聚合物与混合物捏合热稳定剂、光稳定剂润滑剂、填充剂与颜料构成的混合体系,当PVC异型材曝露在自然环境时,一旦PVC组分脱氯化氢后,碳酸钙原组分会转化成氯化钙新组分,它分散在氧化降解物层内,并形成潜在的吸水位置,这是户外型材发黄的原因之一。
PVC管材生产中常见问题及解决办法要点
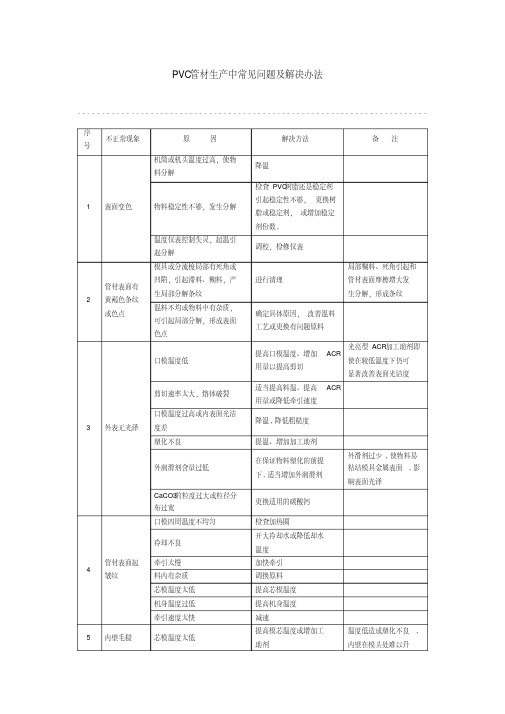
塑化不良 , 拉伸强度降低 PVC树脂质量不好 , 聚合度 低或分子量分布过宽 , 或分 子结构有缺陷
改性剂抗拉强度低 , 从而降 低了管材的抗拉强度
11 条中诸因素 , 同样会引起 管材抗拉强度低 , 使液压试 验不合格
塑化不良
配方中弹性橡胶体等高回缩 率物质组份过高,如 CPE 挤出速度与索引速度不匹 配,牵引速度过快 冷却不良 机头温度过高
得不到排除
型材表面粗
口模内壁不光滑,沾有析出
5
糙,光泽差, 物
解决办法 调整定型模具、牵引机的 位置 调节或修整模具 调整冷却水量或冷却水发 布 调整温度
降低挤出速度
降低牵引速度 检查是否有漏气或真空泵 系统有无堵塞 调节定型模与机头之间的 距离 调整定型模上下位置 加强冷却效果 清理机头 清理定型模
加工温度低
原铺料质量差
背压低
配方不良 加工温度高 ( 塑化 , 过度或 有分解 ) 使用 CPE抗冲改性时 , 螺杆 转速太快 , 剪切率过高使 CPE分散不均 , 呈堆集状态 , 搞抗冲作用下降
提高温度
加强螺杆冷却 干燥 检查泵工作状况 , 管路有 无堵塞 ( 抽粉子引起 ) 降低温度 调模 检查加热圈 , 检查螺杆有 无脉动现象 检查维修牵引机 检查真空泵及其管路 降螺杆温度
调校,检修仪表
进行清理
局部糊料、死角引起和 管材表面摩擦增大发 生分解,形成条纹
确定具体原因, 改善混料 工艺或更换有问题原料
提高口模温度、增加 用量以提高剪切
光亮型 ACR加工助剂即 ACR
使在较低温度下仍可
显著改善表面光洁度
适当提高料温、提高 ACR
PVC木塑板材生产中常见故障及解决办法

调节阻流块
外滑过量
降低外滑分数
内滑不足
提高内滑分数
模具温度设置不合理ຫໍສະໝຸດ 调整模具温度4板材发脆
挤出机温度设置太高
降低温度
挤出机温度设置太低
提高温度
配方不合理
调整配方
5
板材表面不光滑
外滑不足
增加外滑分数
加工助剂不足
增加分数
填料或者助剂分散不充分
调整填料或助剂分数
模具温度设置太低
提高模具温度
挤出机、模具温度设置太高
调节温度设置
厂房内局部温差大或者空气对流太快
改善厂房环境
9
发泡片泡孔大
挤出机温度设定高
降低温度
发泡调节剂少
提高用量
润滑调剂不当
调整配比
10
板材厚度不易控制且来回移动
外滑太多
降低外滑用量
模具温度不稳定
校正温度表,提高控制精度
11
片材芯部泡孔大,表面泡孔小
主机温度高
降低主机温度
润滑调节不当
调整配比
熔体强度不足
添加发泡调节剂用量
降低温度
6
有垂直于挤出方向的条纹
发泡调节剂粘度太高
调整发泡调节剂牌号
挤出机温度设置太低
提高挤出机温度
模具温度设置太低
提高模具温度
牵引速度太快
降低牵引速度
7
板材内有大泡
熔体强度不足
增加发泡剂用量
挤出机5区温度太高
降低对应温度
对应处模具温度高
降低对应处温度
有杂质
注意原料杂质
回料块大
回料磨粉
8
板面弯曲
三辊温度设置不合理
PVC注塑问题的改善措施(大全五篇)

PVC注塑问题的改善措施(大全五篇)第一篇:PVC注塑问题的改善措施PVC注塑件问题的改善措施(一)解決PVC件的牛屎紋和夾水紋問題,首先是必須降低熔膠射進型腔的速度,防止產生折疊波浪形或螺旋形射膠和分流等不平穩的充型。
但是,有時會因模具型腔过于寬大的原故,當射膠速度已經降到螺杆几乎都不能前进時,牛屎紋和夾水紋問題仍然未能解決,這种情況在生產中時常出现。
如果在靠近入水口前的流道上,增加一個阻水針或者加一個緩沖包,可以起到帮助降低熔膠進入型腔之速度的作用,从而能夠达到減輕注塑件的牛屎紋和夾水紋程度的目的。
對于牛屎紋和夾水紋不是特別嚴重的情況,使用這种方法再配合調機技巧,牛屎紋和夾水紋問題是可以解決的。
但是如果問題比较嚴重,就需要再配合更多的解決措施了解決PVC注塑件的牛屎紋和夾水紋難題,需要用到非常慢的射膠速度進行一級射膠。
但是因為速度太慢,熔膠在流道中運行的時間過長,熱量散失將會很大,溫度下降得太多,熔膠的流動性會大大下降,充型將变得更加困難,這樣對解決問題极為不利。
升高熔膠溫度和模具溫度是解決問題的一个改善措施。
升高熔膠溫度,可以使慢速射膠有足夠的溫度來保証熔膠的流動性,但所調高的溫度以不使PVC燒膠為前提。
如果再增加一點背壓,效果就更好。
有時我們宁愿不調太高的熔胶溫度,而多增加一點背壓。
因為增加背壓不但可以使PVC熔膠溫度更加均勻,流動性更好,而且還有升溫的作用,所以比單獨升高溫度對改善流動性會更好。
既升高熔膠溫度又加大背壓PVC會很容易造成燒膠問題。
適當升高模具溫度,可以減慢熔膠散熱的速度,确保PVC長時間的慢速充型仍能保障足夠的流動性。
因此,在注塑件不產生縮水問題的情況下,應盡可能地多升高一點模具溫度,減小泠卻水的流量或是干脆不通冷却水注塑。
總之能夠提高流動性的措施都會對解決PVC夾水紋和牛屎紋問題有好處。
此外,減少水口料的含量,增加一點擴散油等等也都會對問題的解決有幫助。
新機和优质的注塑機的改善效果都會好过残机和普通机。
木塑生产工艺配方及注意事项
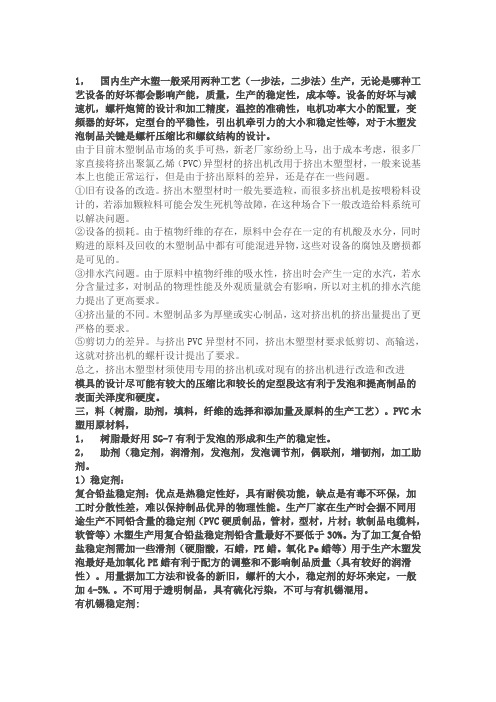
1,国内生产木塑一般采用两种工艺(一步法,二步法)生产,无论是哪种工艺设备的好坏都会影响产能,质量,生产的稳定性,成本等。
设备的好坏与减速机,螺杆炮筒的设计和加工精度,温控的准确性,电机功率大小的配置,变频器的好坏,定型台的平稳性,引出机牵引力的大小和稳定性等,对于木塑发泡制品关键是螺杆压缩比和螺纹结构的设计。
由于目前木塑制品市场的炙手可热,新老厂家纷纷上马,出于成本考虑,很多厂家直接将挤出聚氯乙烯(PVC)异型材的挤出机改用于挤出木塑型材,一般来说基本上也能正常运行,但是由于挤出原料的差异,还是存在一些问题。
①旧有设备的改造。
挤出木塑型材时一般先要造粒,而很多挤出机是按喂粉料设计的,若添加颗粒料可能会发生死机等故障,在这种场合下一般改造给料系统可以解决问题。
②设备的损耗。
由于植物纤维的存在,原料中会存在一定的有机酸及水分,同时购进的原料及回收的木塑制品中都有可能混进异物,这些对设备的腐蚀及磨损都是可见的。
③排水汽问题。
由于原料中植物纤维的吸水性,挤出时会产生一定的水汽,若水分含量过多,对制品的物理性能及外观质量就会有影响,所以对主机的排水汽能力提出了更高要求。
④挤出量的不同。
木塑制品多为厚壁或实心制品,这对挤出机的挤出量提出了更严格的要求。
⑤剪切力的差异。
与挤出PVC异型材不同,挤出木塑型材要求低剪切、高输送,这就对挤出机的螺杆设计提出了要求。
总之,挤出木塑型材须使用专用的挤出机或对现有的挤出机进行改造和改进模具的设计尽可能有较大的压缩比和较长的定型段这有利于发泡和提高制品的表面关泽度和硬度。
三,料(树脂,助剂,填料,纤维的选择和添加量及原料的生产工艺)。
PVC木塑用原材料,1,树脂最好用SG-7有利于发泡的形成和生产的稳定性。
2,助剂(稳定剂,润滑剂,发泡剂,发泡调节剂,偶联剂,增韧剂,加工助剂。
1)稳定剂:复合铅盐稳定剂:优点是热稳定性好,具有耐侯功能,缺点是有毒不环保,加工时分散性差,难以保持制品优异的物理性能。
聚氯乙烯(PVC)出现这些问题,该如何解决

聚氯乙烯(PVC)出现这些问题,该如何解决一、聚氯乙烯注射成型常见故障的排查·欠注故障分析及排除方法:(1)熔料温度太低。
应适当提高成型温度。
(2)成型周期太短。
应适当延长。
(3)注射压力不足。
应适当提高。
(4)注射速度太慢。
应适当加快。
(5)供料不足。
应增加供料量。
(6)模具温度太低,应适当提高。
特别是要合理设置模具的冷却回路,保持模具温度均匀。
(7)塑件形体结构设计不合理或壁太薄。
应在可能变动的情况下进行调整。
(8)浇注系统结构尺寸偏小。
应适当放大浇口和流道截面。
(9)模具排气不良。
应增加排气孔,改善模具的排气性能。
(10)模具强度不足。
应尽量提高其刚性。
·缩痕故障分析及排除方法:(1)料筒温度太高。
应适当降低料筒温度。
(2)注射压力不足。
应适当提高。
(3)保压时间太短。
应适当延长。
(4)冷却时间太短。
应适当提高冷却效率或延长冷却时间。
(5)供料不足。
应增加供料量。
(6)模具温度不均匀。
应调整模具的冷却系统,合理设置冷却回路。
(7)塑件的形体结构设计不合理,或塑件壁太厚。
应在可能变动的情况下适当调整。
(8)浇口截面积太小。
应适当加大。
·熔接痕故障分析及排除方法:(1)熔料温度太低。
应适当提高成型温度。
(2)注射压力不足。
应适当提高。
(3)注射速度太慢。
应适当加快。
(4)模具温度太低,应适当提高。
(5)浇口截面积太小。
应适当加大。
(6)模具排气不良。
应增加排气孔,改善模具的排气性能。
(7)冷料穴结构尺寸太小或位置不当。
应合理调整。
(8)原料内混入杂质。
应彻底清除异物杂质或换用新料。
(9)脱模剂用量偏多。
应尽量减少其用量。
(10)镶件设置不合理。
应适当调整。
(11)原料着色不均匀。
应选用分散性较好的着色剂,以及延长混色的搅拌时间,使原料着色均匀。
·流料痕故障分析及排除方法:(1)熔料温度太低。
应适当提高成型温度。
(2)注射压力不足。
应适当提高。
(3)保压时间太短。
PVC管材生产中常见问题及解决办法分解

加强螺杆冷却
6
管壁起泡
料过潮
干燥
机筒二段后真空排气孔处真 空度过低或堵塞
检查泵工作状况,管路有 无堵塞(抽粉子引起)
有分解(机头温度过高)
降低温度
7
管壁厚度不
均匀
口模、芯棒不同心
调模
机头温度不均,岀料有快慢
检查加热圈,检查螺杆有
无脉动现象
牵引速度不稳
检查维修牵引机
真空槽真空度有波动
检查真空泵及其管路
降低温度
使用CPE抗冲改性时,螺杆 转速太快,剪切率过高使CPE分散不均,呈堆集状态,搞抗冲作用下降
降低螺杆转速
降低螺杆转速会使产 能下降,改用ACR作为 抗冲改性剂最佳解决 办法,ACR对温度高低、
进行清理
局部糊料、死角引起和
管材表面摩擦增大发
生分解,形成条纹
混料不均或物料中有杂质, 可引起局部分解,形成表面 色点
确定具体原因,改善混料
工艺或更换有问题原料
3
外表无光泽
口模温度低
提高口模温度、增加ACR用量以提高剪切
光亮型ACR加工助剂即
使在较低温度下仍可
显著改善表面光洁度
剪切速率太大,熔体破裂
PVC
序
号
不正常现象
原因
解决方法
备 注
1
表面变色
机筒或机头温度过高,使物
料分解
降温
物料稳定性不够,发生分解
检查PVC树脂还是稳定剂 引起稳定性不够,更换树 脂或稳定剂,或增加稳定 剂份数。
温度仪表控制失灵,超温引
起分解
调校,检修仪表
2
管材表面有 黄褐色条纹 或色点
模具或分流梭局部有死角或 凹陷,引起滞料、糊料,产 生局部分解条纹
- 1、下载文档前请自行甄别文档内容的完整性,平台不提供额外的编辑、内容补充、找答案等附加服务。
- 2、"仅部分预览"的文档,不可在线预览部分如存在完整性等问题,可反馈申请退款(可完整预览的文档不适用该条件!)。
- 3、如文档侵犯您的权益,请联系客服反馈,我们会尽快为您处理(人工客服工作时间:9:00-18:30)。
原料中影响木塑复合材料(WPC)性能的因素1、熔体流动速率:熔体流动速率一定程度反映相对分子量大下,熔体流动速率越小,相对分子量越大。
相对分子量越大型坯具有较好的熔体强度,可改变型坯自重下垂,制品拉伸强度、冲击强度、热变形温度等性能都有所提高,是有利的,但相对分子量越大粘度越高,流动性越差,加工困难,同时型坯有很高的“回缩”性,在合模前型坯会有较大的收缩。
同样的条件下,型坯不稳定流动现象加剧,甚至熔体破裂。
因此,考虑设备加工能力与工艺可行性,几乎所有200L塑料桶生产厂家都选用HMWHDPE树脂,熔体流动速率能够满足制品质量要求即可,一般为2.0左右(g/10min,21.6kg)。
2、分子量分布:从成型加工观点来看,宽的分子量分布比分布窄的,流动性要好,易于加工控制,并且宽的分子量分布可降低口模压力,减少型坯熔体破裂倾向,改善加工性能,同样的条件下可提高挤出速度。
但是宽的分子量分布也说明存在相对分子量偏低和较高部分,当相对分子量偏低部分所占比例过高时,制品力学性能、热稳定性等皆有所下降,并且流动过程中的分级效应,又使聚合物中低分子量级较多集中到挤出型坯表面,甚至从表面晰出,型坯表面看上去是在上面撒了一些细小白色粒子,吹塑制品内壁粗糙,脱落的白色粒子常易堵塞气阀,引起气路系统故障。
相对分子量偏高部分所占比例过高时,塑化困难,型坯表面出现未完全塑化颗粒,外观质量下降。
目前双峰分布的树脂有替代单峰分布趋势,同样的条件下,具有出色的加工性能与熔体强度,抗环境应力开裂也明显提高。
成型工艺及设备良好的加工工艺和设备应保证物料和发泡剂混合均匀,并保持足够高的、稳定的机头压力,使口模压力足够大和压力降足够快,以获得形态良好的泡孔。
1.混料和喂料原料的生产工艺:木纤维是吸水性较强的材料一般含水量在15%左右甚至更高,无机填料也达到5%左右,而水含量的高低是影响塑料特别是木塑生产稳定性和制品质量的天敌,如影响发泡倍率,制品的吸水率,制品的变形,制品的耐候性和其他物理性能。
所以水分最好控制在1%以内。
控制好合理水分的纤维和填料-----加入高混机里-----混到100度-----加入适量的偶联剂----混到110-115度----关掉马达不动时打开混合机大盖2-3分钟-----加入PVC,稳定剂-----混到80度-----加润滑剂及其他助剂-----100度加加工助剂,发泡剂------120-125卸粉-----粉卸完后马达停止了再打开大盖2-3分钟后再混下一手料(最好混五手料清理一次混合机)-----粉在泠拌桶令却到40度就可造粒或加入双螺杆生产(泠拌桶务必有循环泠却水)。
在混料是必须注意观察温度和时间如一般泠锅混一手料在20-25分钟左右,热锅在12-15分钟左右(温度设定125度左右),如果时间有相差3分钟或更长那可能是感温线有问题或温控不准,或混合机牛角刀磨损严重。
这样会影响发泡倍率的稳定,颜色。
造粒时常要注意各温控温度是否准确,风机是否正常运转,电流的大小,粒子的粒径,表面,长度是否粘料,下料是否稳定,千万不能断料的情况发生。
混料工艺通过影响不同组分之间的接触与反应影响各组分的分散,进而影响材料性能。
混料时,应该选择合适的加料顺序、加料温度、加料时间。
由于木粉粉料蓬松,加料过程中容易出现“架桥”和“抱杆”现象。
加料不稳定会使挤出波动,造成挤出质量降低,因此必须对加料方式和加料量作严格的控制,一般采用强制加料装置或饥饿喂料,以保证挤出的稳定。
PVC/木粉复合材料挤出发泡成型一般分两步法和一步法两种工艺路线:两步法即先造粒后成型;一步法即省去造粒工序,采用表面改性后的木粉与PVC 粉经高速混合后直接加料挤出。
研究表明:母粒法(两步法)有利于提高PVC/木塑的力学性能。
2.成型温度挤出工艺:主要注意以下几方面a,挤出机各段温度的设定,关键是压缩段,计量段,模具。
各温控的准确性如温控不准影响到发泡倍率和颜色。
发泡主要是压缩段和计量段温度的设定,成型主要是模具温度。
b,各段风机的正常运转。
c,主机电流的大小和稳定性。
如主机电流波动较大说明滑剂.加工助剂.纤维与PVC各组分之间分散不是很均匀。
d,主机速度务必保持一样,因速度的快慢会影响到发泡倍率及颜色。
设定挤出成型温度应考虑到物料在挤出机机筒内的物理作用和化学反应。
加料段温度既要保证物料能够快速熔融,阻止分解气体的逃逸,又要防止发泡剂提前分解;压缩段和计量段温度设定则需要考虑到化学发泡剂分解温度和分解速率,木粉烧焦和PVC 分解等因素;机头温度应使熔体保持良好流动性的同时,具有足够的熔体黏度,以维持机头内的熔体处于高压下,使之在机头内不发泡。
姚祝平认为在充分塑化的条件下,应采用低温挤出。
螺杆和成型模具等设备也应具有低温挤出特性,以保证泡孔有良好的形态和较小的直径。
加料段温度应控制在165℃以下,压缩段和均化段在160~180℃之间,机头和口模设在160℃以下。
3.螺杆转速螺杆转速对挤出发泡的影响主要体现在以下几个方面:一是影响挤出压力,转速越高,挤出机内压力越大,从而越有利于成核,成核的泡孔数目也越多,发泡率也就越高。
但压力过高时成核的泡孔生长受到抑制,影响泡孔的充分生长;二是螺杆转速越高,剪切作用越强,剪切作用过强时容易使泡孔合并或破裂,影响发泡体质量和低密度泡沫塑料的形成;三是螺杆转速过高或过低,使停留时间过短或过长,容易发生提前发泡或发泡剂分解不充分等现象,不利于形成均匀细密的泡孔结构。
因此在其它影响因素不变的情况下,螺杆转速存在一个最佳值,一般在12~18r/min 之间。
4.挤出压力挤出压力不足会造成制品表面粗糙、强度低,而较高的挤出压力不仅能控制机头内的含气熔体不提前发泡,而且使机头口模内外压差大,从而使压降速率高,有利于气泡成核,成核的气泡数量增多,发泡率也随之增大,有利于得到均匀细密的泡孔结构。
但挤出压力过高对泡孔的生长不利。
要得到适宜的机头压力,可以通过调节螺杆转速、机头温度及口模形状来实现。
5.成型设备单螺杆挤出机主要靠摩擦输送物料,混炼效果差,木粉在机筒中停留时间长,易烧焦,因此,在PVC/木塑复合材料挤出中受到较大的限制。
为了提高PVC/木塑的混合效果,用于PVC/木塑加工的单螺杆应该设混炼区,或者先造粒,然后用粒料挤出成型,但这个过程消耗了助剂,降低了PVC 性能。
PVC发泡工艺控制关键点塑料发泡成型分为三个过程:气泡核的形成、气泡核的膨胀和泡体的固化。
对于添加化学发泡剂的PVC发泡片材来说,气泡核的膨胀对发泡片材的质量起决定性影响。
PVC属于直链分子,分子链较短,熔体强度低,在气泡核膨胀成气泡过程中,熔体不足以包覆住气泡,气体易溢出合并成大泡,降低发泡片材的产品质量。
提高PVC发泡片材质量的关键因素是提高PVC的熔体强度。
从高分子材料加工特性分析,提高PVC熔体强度的方法有多种,但最有效的方式是添加提高熔体强度的助剂和降低加工温度。
PVC属于非晶材料,随熔体温度的提高熔体强度降低,反之随熔体温度降低熔体强度提高,但降温的作用有限仅起到辅助作用。
ACR类加工剂都有提高熔体强度的作用,其中发泡调节剂最有效果。
熔体强度随发泡调节剂含量增加而提高。
一般而言,只要螺杆有足够的分散混合能力,添加高黏度的发泡调节剂对提高熔体强度效果更明显。
甲基丙烯酸甲酯树脂分子式C5H8O2;CH2C(CH3)COOCH挤出过程常见问题在PVC发泡片材挤出过程中,碰到的问题基本可以归为4类,一是稳定性问题;二是熔体强度问题;三是润滑问题;四是分散问题。
这四类问题特别是前三类问题会相互制约,交叉影响,从表面现象看有时很难立刻分清楚,要说方观察分析,找到问题根源才能根本解决。
稳定性不足,会影响整个板面,板面发黄,发泡片材脆性大。
熔体强度不足会导致发泡片泡孔大,纵切面泡很长。
判断熔体强度是否不足,最直接的办法是到三辊后面用手指按压包在中辊上的片材,熔体强度好按压时能感觉到弹性。
若按压后很难弹起,说明熔体强度较差。
因为螺杆结构和冷却方式差别较大,很难判断温度是否合理,一般来说,在挤出机允许的负荷内,3—5区温度以低为好。
在发泡管材中要想获得发泡均匀制品,也需要保证PVC物料有良好的融体强度。
公司开发的发泡助剂就是为解决发泡制品的这一问题而开发的,能有效地提高发泡管材的质量.润滑剂分为外润滑剂和内润滑剂,外滑有利于脱模,对板材表面的光洁性有好处,外滑太少,挤出机5区温度不易控制,易升温,这会导致合流芯温度高,板材中间出大泡、串泡、发黄等问题,板材表面也不光滑;外滑多,析出会变得严重,表现在模具内的结构和板材表面外滑的析出,也会表现为某些个别现象在板面上不定期的来回移动。
内滑有利于塑化和熔体的流动性,内滑不足板面难以控制厚度,表现为板材中间厚两边薄;内滑多,易出现合流芯温度高的现象。
分散不好会带来板材表面不光滑的现象。
工艺温度控制问题:上面提到的四个问题属于根本性问题,是基础,是深层次问题。
相对于上面四个问题,工艺温度控制则要直观得多,是表面问题,但温度控制不好,会诱发根本问题的出现。
提高加工工艺温度,材料稳定时间会降低,出现稳定性问题;原有的润滑平衡会被打破,一般表现为外润滑不足,特别是后期外润滑,需提高外润滑添加量;温度提高也会导致熔体强度降低,发泡片材泡孔增大,泡孔数量减少,片材发脆易断裂;温度提高降低了熔体强度也会降低熔体粘度,粘度降低剪切分散能力降低,对分散能力不强的螺杆而言,有时会出现分散不均匀。
木塑复合材料质量隐患及其解决方案1. 木塑复合材料的含水量过高,由于木塑材料具有16%~21%的的孔隙度,因而易折易污染。
解决方案是在生产加工过程中严格控制温度和加工速度,减少含水量。
2. 因为抗氧化剂用量不够,导致木塑板材容易被氧化,表面过脆、容易脱落。
解决方案为添加适量的抗氧化剂3. 生产加工过后的塑木材料出现褶皱,多出现于材料在快速冷却过程中。
解决方案是给木塑材料成品以充分的冷却、收缩、放置的时间,并且尽量不要为了提高产能而进行高速生产。
4. 产品褪色,此现象是由于颜料不足或者打磨过渡造成的。
解决方案是减少打磨度或添加无机颜料。
5. 木塑产品表面过于光滑。
解决方案是通过在材料表面印刷纹理、改变塑料含量来增加牵引力,并且使用质量较好的专门涂料来解决此类问题。
机头压力对木塑复合材料加工成型性能的影响邹良凤挤出机温度高,机头压力小,使挤出的型材不密实,因此导致制品性能的缺陷,破坏稻壳粉作为填充剂的优良性质,并且严重影响外观形象。
当机头压力较低时,制品表面出现条纹,并产生分段现象,挤出不成型,经常出现物料不成型而造成的物料堆积现象,得不到连续得外观质量好的制品,影响生产的连续性。
只要在压力许可的范围内,压力越高挤出制品越密实,挤出质量就越好。