第五章精密加工中的测量技术
精密测量技术
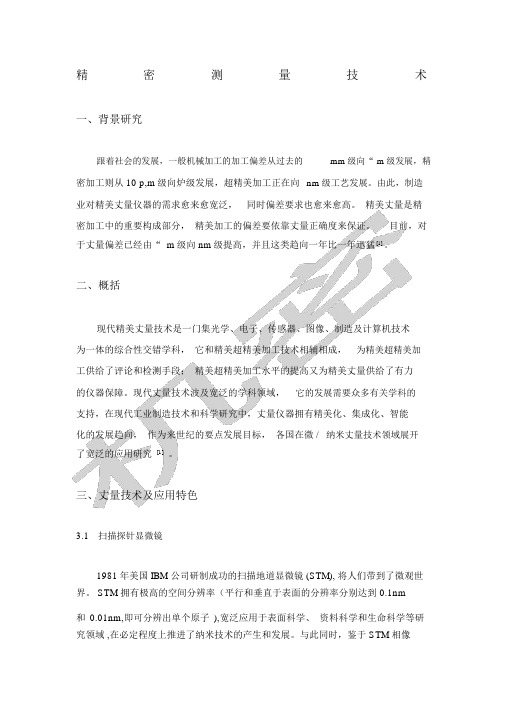
精密测量技术一、背景研究跟着社会的发展,一般机械加工的加工偏差从过去的mm级向“ m级发展,精密加工则从 10 p,m级向炉级发展,超精美加工正在向nm级工艺发展。
由此,制造业对精美丈量仪器的需求愈来愈宽泛,同时偏差要求也愈来愈高。
精美丈量是精密加工中的重要构成部分,精美加工的偏差要依靠丈量正确度来保证。
目前,对于丈量偏差已经由“ m级向 nm级提高,并且这类趋向一年比一年迅猛[1] 。
二、概括现代精美丈量技术是一门集光学、电子、传感器、图像、制造及计算机技术为一体的综合性交错学科,它和精美超精美加工技术相辅相成,为精美超精美加工供给了评论和检测手段;精美超精美加工水平的提高又为精美丈量供给了有力的仪器保障。
现代丈量技术波及宽泛的学科领域,它的发展需要众多有关学科的支持,在现代工业制造技术和科学研究中,丈量仪器拥有精美化、集成化、智能化的发展趋向,作为来世纪的要点发展目标,各国在微 /纳米丈量技术领域展开了宽泛的应用研究[1]。
三、丈量技术及应用特色3.1扫描探针显微镜1981年美国 IBM 公司研制成功的扫描地道显微镜 (STM), 将人们带到了微观世界。
STM 拥有极高的空间分辨率(平行和垂直于表面的分辨率分别达到 0.1nm和0.01nm,即可分辨出单个原子),宽泛应用于表面科学、资料科学和生命科学等研究领域 ,在必定程度上推进了纳米技术的产生和发展。
与此同时,鉴于 STM 相像原理与构造 ,接踵产生了一系列利用探针与样品的不一样互相作用来探测表面或界面纳米尺度上表现出来性质的扫描探针显微镜(SPM),用来获取经过 STM 没法获取的有关表面构造和性质的各样信息,成为人类认识微观世界的有力工具。
下边介绍几种拥有代表性的扫描探针显微镜。
(1)原子力显微镜( AFM ):AFM 利用微探针在样品表面划过时带动高敏感性的微悬臂梁随表面起伏而上下运动 ,经过光学方法或地道电流检测出微悬臂梁的位移 ,实现探针尖端原子与表面原子间排挤力检测 ,进而获取表面容貌信息。
精密超精密加工技术

精密超精密加工技术精密及超精密加工对尖端技术的发展起着十分重要的作用。
当今各主要工业化国家都投入了巨大的人力物力,来发展精密及超精密加工技术,它已经成为现代制造技术的重要发展方向之一。
本节将对精密、超精密加工和细微加工的概念、基本方法、特点和应用作一般性介绍。
一、精密加工和超精密加工的界定精密和超精密加工主要是根据加工精度和表面质量两项指标来划分的。
这种划分是相对的,随着生产技术的不断发展,其划分界限也将逐渐向前推移。
1.一般加工一般加工是指加工精度在10µm左右(IT5~IT7)、表面粗糙度为R a0.2µm~0.8µm的加工方法,如车、铣、刨、磨、电解加工等。
适用于汽车制造、拖拉机制造、模具制造和机床制造等。
2.精密加工精密加工是指精度在10µm~0.1µm(IT5或IT5以上)、表面粗糙度值小于R a0.1µm的加工方法,如金刚石车削、高精密磨削、研磨、珩磨、冷压加工等。
用于精密机床、精密测量仪器等制造业中的关键零件,如精密丝杠、精密齿轮、精密导轨、微型精密轴承、宝石等的加工。
3.超精密加工超精密加工一般指工件尺寸公差为0.1µm~0.01µm数量级、表面粗糙度R a 为0.001µm数量级的加工方法。
如金刚石精密切削、超精密磨料加工、电子束加工、离子束加工等,用于精密组件、大规模和超大规模集成电路及计量标准组件制造等方面。
二、实现精密和超精密加工的条件精密和超精密加工技术是一项内容极为广泛的制造技术系统工程,它涉及到超微量切除技术、高稳定性和高净化的工作环境、设备系统、工具条件、工件状况、计量技术、工况检测及质量控制等。
其中的任一因素对精密和超精密加工的加工精度和表面质量,都将产生直接或间接的不同程度的影响。
1.加工环境精密加工和超精密加工必须具有超稳定的加工环境。
因为加工环境的极微小变化都可能影响加工精度。
零件光学超精密加工检测技术
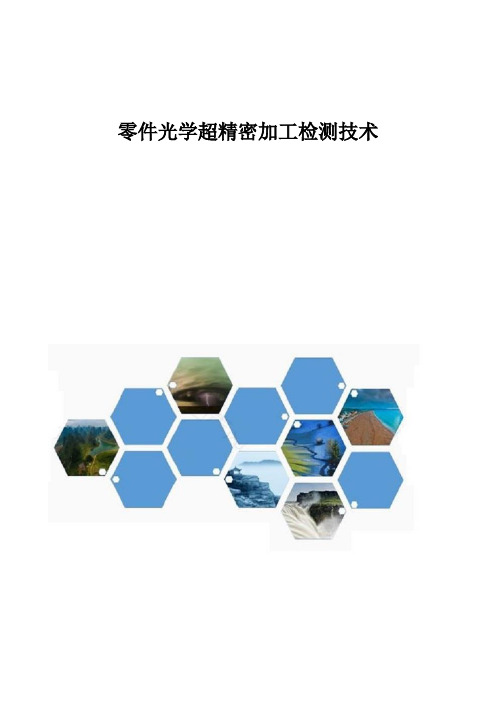
零件光学超精密加工检测技术摘要:随着数字数控机床和加工平台的产生与发展,机械零件的加工方式也向着大批量、专一化方向发展。
导致对机械零件的需求也逐渐加大,零件的尺寸和表面加工质量是否符合标准使用要求是影响机械零件正常工作的关键,因此,对机械零件的光学超精密检测成为主要研究任务。
机械零件表面的加工质量和尺寸大小虽然对零件的正常使用影响较低,但直接影响零件的可靠性、质量和使用寿命,而机械零件使用时间决定零件经济效益。
随着光学超精密加工技术的不断发展,零件光学超精密加工检测技术已成为超精密加工迫在眉睫的关键难题。
人工智能技术是一种新兴的用于模拟、延伸和扩展的智能理论、方法、技术及应用系统的一门新的技术科学。
人工智能技术中的机械学习法,使机械零件的光学超精密检测过程大大简化,并将操作结果保存在存储器中,便于后续光学超精密检测过程的快速执行。
关键词:光学检测;现状;发展引言单参数精密测量是精密测量中最简单的问题,近年来在复杂探测等问题中有了重要应用。
多参数精密测量复杂得多,参数之间存在精度制衡。
如何减少参数之间的精度制衡以实现多参数最优测量,是多参数精密测量的重要问题之一。
为了消除参数之间的精度制衡,研究人员将单参数测量实验中控制增强的次序测量技术应用到多参数测量中,通过调控测量系统动力学演化,完全解决了正演化算法中参数之间的精度制衡问题,实现了最优测量。
1测量系统将四组视觉传感器单元(包括CCD相机和激光器)分别竖直放置于精密零件两侧,垂直于精密零件中轴线,安装在精密零件两侧的立柱上;其中两组视觉传感器单元放置于精密零件一侧立柱上,另外两组视觉传感器单元放置于精密零件另一侧立柱上。
首先利用激光跟踪仪建立基坐标系统,然后对每个视觉传感器单元进行相机参数标定、光平面参数方程标定以及全局标定,最终得到相机的内参矩阵、相机到基坐标系下的全局标定矩阵以及激光平面在基坐标系下的平面方程,完成系统使用以及测量前的预处理。
CNC机床加工中的工件定位与测量技术

CNC机床加工中的工件定位与测量技术CNC机床加工在现代制造业中起着重要的作用。
它通过计算机控制,实现高精度、高效率的零件加工。
而在CNC机床加工过程中,工件定位与测量技术是确保加工质量的关键环节。
本文将就工件定位与测量技术在CNC机床加工中的应用进行探讨。
一、工件定位技术工件定位技术是指在CNC机床加工过程中确定工件的准确位置,使其与机床坐标系相一致,从而保证加工的精度和稳定性。
常见的工件定位技术有以下几种。
1. 机床装夹定位机床装夹定位是指通过夹具或定位基准来固定工件的位置。
夹具是一种专门设计的装置,可以固定工件并确保其准确定位。
在CNC机床加工中,夹具的设计和选择非常重要。
合理的夹具设计可以提高加工效率和准确性,减少加工过程中的误差。
2. 光学定位光学定位是利用光学测量仪器进行工件定位的技术。
通过测量工件表面上的特征点或边缘,根据光学原理计算出工件的几何中心或位置,从而确定工件的准确位置。
光学定位技术在CNC机床加工中应用广泛,可以实现高精度的定位和测量。
3. 触发式传感器定位触发式传感器定位是利用触发式传感器对工件进行检测,通过信号的反馈确定工件的位置。
触发式传感器可以是接触式的,也可以是非接触式的。
在CNC机床加工中,触发式传感器定位技术可以实现对工件位置的快速检测和自动校准,提高加工精度和效率。
二、工件测量技术工件测量技术是在CNC机床加工过程中对工件进行精确测量的技术。
工件测量可以用于加工前的工件检测,也可以用于加工中的自动测量和校正。
常见的工件测量技术有以下几种。
1. 坐标测量坐标测量是利用坐标测量机进行工件测量的技术。
坐标测量机是一种精密测量仪器,可以通过测量工件表面上的特征点或边缘,计算出工件的几何尺寸和形状。
坐标测量技术在CNC机床加工中广泛应用,可以实现对工件尺寸和形状的高精度测量。
2. 光学测量光学测量是利用光学测量仪器进行工件测量的技术。
通过测量工件表面上的特征点或边缘,根据光学原理计算出工件的几何尺寸和位置。
机械加工中常用的精密测量技术
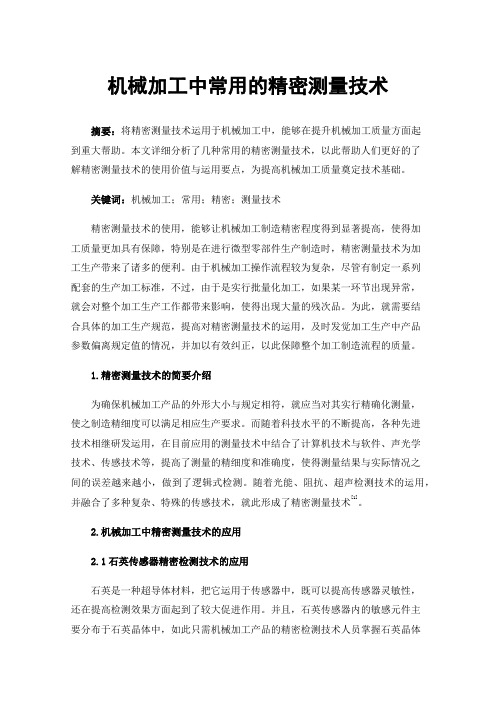
机械加工中常用的精密测量技术摘要:将精密测量技术运用于机械加工中,能够在提升机械加工质量方面起到重大帮助。
本文详细分析了几种常用的精密测量技术,以此帮助人们更好的了解精密测量技术的使用价值与运用要点,为提高机械加工质量奠定技术基础。
关键词:机械加工;常用;精密;测量技术精密测量技术的使用,能够让机械加工制造精密程度得到显著提高,使得加工质量更加具有保障,特别是在进行微型零部件生产制造时,精密测量技术为加工生产带来了诸多的便利。
由于机械加工操作流程较为复杂,尽管有制定一系列配套的生产加工标准,不过,由于是实行批量化加工,如果某一环节出现异常,就会对整个加工生产工作都带来影响,使得出现大量的残次品。
为此,就需要结合具体的加工生产规范,提高对精密测量技术的运用,及时发觉加工生产中产品参数偏离规定值的情况,并加以有效纠正,以此保障整个加工制造流程的质量。
1.精密测量技术的简要介绍为确保机械加工产品的外形大小与规定相符,就应当对其实行精确化测量,使之制造精细度可以满足相应生产要求。
而随着科技水平的不断提高,各种先进技术相继研发运用,在目前应用的测量技术中结合了计算机技术与软件、声光学技术、传感技术等,提高了测量的精细度和准确度,使得测量结果与实际情况之间的误差越来越小,做到了逻辑式检测。
随着光能、阻抗、超声检测技术的运用,并融合了多种复杂、特殊的传感技术,就此形成了精密测量技术[1]。
2.机械加工中精密测量技术的应用2.1石英传感器精密检测技术的应用石英是一种超导体材料,把它运用于传感器中,既可以提高传感器灵敏性,还在提高检测效果方面起到了较大促进作用。
并且,石英传感器内的敏感元件主要分布于石英晶体中,如此只需机械加工产品的精密检测技术人员掌握石英晶体特征,便能轻松熟悉传感器运作方式,以此防止石英传感器在实际运用时发生运作混乱、操作不当等情况。
并且,将石英传感器运用于机械加工产品的检测工作中,还可以促使传感器内使用的石英晶体在测量时发生正压电效应,以此提升检测效果的准确性与精确性,保证工作人员可以按照所掌握的检测结果来对加工生产流程加以优化改进,以免在开展机械加工时发生异常问题,从而威胁加工产品的质量[2]。
第5章 测量误差理论的基础知识
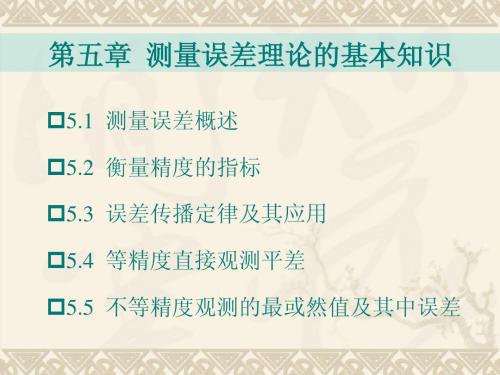
5.1 测量误差概述 5.2 衡量精度的指标 5.3 误差传播定律及其应用 5.4 等精度直接观测平差 5.5 不等精度观测的最或然值及其中误差
§5.1 测量误差概述
大量实践表明,当对某一未知量进行多次 观测时,无论观测仪器多么精密,观测进行得
多么仔细,观测值之间总是存在着差异。例如,
2 2 2 2 mZ A12 m12 A2 m2 An mn
§5.3.2 误差传播定律的应用
例1 量得某圆形建筑物得直径 D=34.50m, 其中误差mD 0.01m,
求建筑物得圆周长及其中误差。
解:圆周长:
P D 3.1416 34.50 108.38 中误差:
将以上各式两边平方、取平均,可得
Z 2 x12 x22 xn 2 n f2 f 2 ... f 2 xi x j 1 fi f j k 1 2 n k k k k i, j
i j
因 x 的观测值 l 彼此独立,则 xi x j 在 i j 时亦为偶 i i 然误差。根据偶然误差第4特性,上式末项当 k 时趋近于 零,故:
测量某一平面三角形的三个内角,其观测值之
和常常不等于理论值180°。这说明测量结果
不可避免地存在误差。
§5.1.1 测量误差的来源
测量工作是在一定条件下进行的,外界环境、观 测者的技术水平和仪器本身构造的不完善等原因,都 可能导致测量误差的产生。通常把测量仪器、观测者 的技术水平和外界环境三个方面综合起来,称为观测 条件。观测条件不理想和不断变化,是产生测量误差 的根本原因。通常把观测条件相同的各次观测,称为 等精度观测;观测条件不同的各次观测,称为不等精 度观测。
机械加工中常用的精密测量技术
机械加工中常用的精密测量技术摘要:精密检测技术在机械加工制造领域中的运用,可以极大地提高机械加工质量,尤其是微型零部件、异性零部件的生产加工中,精密检测技术给予了很多加工制造指导。
机械加工制造生产过程复杂,虽然制定了严格的生产加工工艺标准,在批量生产加工,若生产加工出现问题,未能及时测量发现,就会影响整个加工制造进度和质量,而且产生次品和废品。
结合当前对机械加工制造要求,加大对精密测量技术推广应用力度,及时检测机械加工制造中关于精度、质量等方面的问题,便能确保机械加工制造质量。
关键词:精密测量技术;机械加工;机器视觉检测引言工业离不开机械设备和零部件生产,在市场需求不断扩大的情况下,机械制造行业迎来新的发展机遇,同时也面对着较大的挑战。
由于我国对机械制造工艺和技术的研究较晚,整体的技术水平还有待进一步提升。
面对新的发展形势,分析当前机械制造工艺的变化以及精密加工技术与其他先进技术融合产生的价值,可使生产企业明确认识到必须对机械制造进行改革,加强对各类智能化和专业化技术的应用。
面对不同的产品类型和特质,选择不同组合的技术,使产品品质更高,整体的制造和生产流程规范高效,不断提升行业发展水平,使我国机械制造业能够紧跟世界发展的脚步,成为我国的支柱产业。
1机械制造工艺及其精密加工的特点1.1系统性系统性就是机械制造技术和精密加工技术的融合,使整体的制造成为系统化的过程,各技术的协调和配合可更高效地完成生产任务,整体的制造过程更加人性化和专业化。
具体而言,以成组的工艺为制造活动的基础,在可控制的范围内运用自动化系统对数据和参数进行识别,制订出制造的流程和方案。
在正式进行制造时选择符合制造工艺的单元,依据参数进行批量的生产。
这种系统性的生产制造模式,与传统机械制造相比较,更利于生产准确性提升,对于企业自身的发展有着促进的作用。
例如,智能手机的生产和制造,就集合了声控和光感等技术,并引入高精密的工业生产手法,使各类现代技术结合成完整的加工系统,加工制造和生产高效有序地进行。
第5章 精密、超精密加工技术
• 和表面粗糙度的检验,而且要测量加工设备 的精度和基础零部件的精度。 • 高精度的尺寸和几何形状可采用分辨率为 0.1~0.01µ m,的电子测微计、分辨率为 0.01~0.001µ m的电感测微仪或电容测微仪来 测量。圆度还可以用精度为0.01µ m的圆度仪 来测量。
加工设备必须具有高精度的主轴系统、进给 系统(包括微位移装臵),现在的超精密车 床,其主轴回转精度可达0.02µ m,导轨直线 度可达1000000:0.025,定位精度可达 0.013µ m,进给分辨率可达0.005µ m。其回转 零件应进行精密的动平衡。
• 2)高刚度
• 包括静刚度和动刚度,不仅要注意零件本身
• 精密和超精密磨料加工是利用细粒度的磨粒 和微粉主要对黑色金属、硬脆材料等进行加 工,按具体地加工方法分为精密和超精密磨 削,加工精度可达5~0.5µ m,表面粗糙度 Ra0.05~0.008µ m);精密和超精密研磨(加 工精度可达10~0.1µ m,表面粗糙度 Ra0.01~0.008µ m);
合金等刀具进行精密和超精密切削,这些刀
具材料的切削效果不如金刚石,但能加工黑
色金属。对黑色金属等硬脆材料的精密加工
和超精密加工,一般多采用磨削、研磨、抛
光等方法。
• 精密和超精密磨削时,通常采用粒度240#~W7
或更细的白刚玉或铬刚玉磨料和树脂结合剂
制成的紧密组织砂轮,经金刚石精细修整后
• 进行加工。
• 出现了精密电火花加工、精密电解加工、精
密超声波加工、分子束加工、电子束加工、
离子束加工、原子束加工、激光加工、微波
加工、等离子体加工、光刻、电铸及变形加
工等。
• 4.复合加工
• 复合加工是将几种加工方法叠合在一起,发 挥各种加工方法的长处,达到高质量(加工
机械制造中的精密加工与测量技术
机械制造中的精密加工与测量技术机械制造在现代工业生产中扮演着至关重要的角色,而精密加工和测量技术则是机械制造领域中需要掌握和应用的重要技能,因为制造高精度零件和产品需要这些技术的支持。
一、精密加工技术精密加工技术包括切削、磨削、抛光、电化学加工等多种加工方式,其中最为常用的是机械切削。
高精度的零件制造需要采用高精度的切削工具和稳定的切削条件,以实现尺寸和表面质量的控制。
此外,高速切削、超声波切削、磁场切削、光学切削等技术也是精密加工领域不断发展的热点,它们可以进一步提高切削效率和工件质量。
二、测量技术测量技术是机械制造中不可或缺的环节,可分为尺寸测量和形位误差测量两大类。
常用的测量工具包括千分尺、衡器、显微镜、高度计、投影仪等。
为了提高测量精度和重复性,汽车、航空、列车等工业领域的精密测量中心使用高精度的测量仪器和系统,例如激光干涉仪、三坐标测量机、精密测量显微镜等,这些仪器的精度可以达到亚微米甚至纳米级。
三、加工与测量技术的应用高精度的机械加工和测量技术是制造高端精密设备的必要条件。
例如,航空航天、汽车制造、半导体制造、生物医药等领域需要制造和检测精度高、质量好的高精度零件和设备,这些行业对高精度制造和测量技术的要求更高。
而金属、玻璃、陶瓷等材料的加工技术也需要涉及精密加工和测量技术。
在中国,高端制造是未来的发展方向,提高企业自主创新能力和研发能力对于推动我国制造业的高质量发展具有至关重要的作用。
因此,加工和测量技术的进一步提高和创新对于推动整个制造业的不断升级与发展有着重要意义。
结语机械制造中的精密加工和测量技术是制造高质量产品的保障,这些技术的应用也促进了机械制造和制造业的进步与发展。
在未来的制造业发展中,需要不断提高和创新这些技术,以满足市场和客户对于精度、质量和效率的不断提高的要求。
精密测量技术基础
随着科技的不断进步,精密测量技术不断 发展,出现了许多高精度测量仪器和方法 ,如激光干涉仪、原子干涉仪等。
精密测量技术的应用领域
电子工程
用于测量电子元件、电路板等 参数,保证电子产品性能。
计量测试
用于测量各种物理量,保证计 量测试的准确性和可靠性。
机械制造
用于测量机械零件的尺寸、形 状、位置等参数,保证产品质 量。
有助于推动科技进步和社会发展。
05
精密测量技术的发展趋势与展望
新型测量原理与技术的研究
原子干涉测量技术
01
利用原子干涉效应进行高精度长度测量,具有极高的稳定性和
精度。
光学频率梳技术
02
利用光学频率梳产生高精度光谱,实现高精度光谱分析和时间
频率测量。
纳米光刻技术
03
利用光刻技术在纳米级别上制造微小结构,实现高精度微纳加
光学仪器
用于测量光学元件、透镜等参 数,保证光学仪器性能。
科学研究
用于测量各种物理量,推动科 学研究的深入发展。
02
精密测量技术的基本原理
测量误差理论
误差来源
误差传递
误差理论主要研究测量误差的来源, 包括仪器误差、环境误差、方法误差 和人员误差等。
误差传递是指测量误差对测量结果的 影响,通过误差传递公式可以评估不 同误差对最终结果的影响程度。
逻辑分析仪
用于测量数字电路的逻辑电平和时序 关系,广泛应用于数字系统和计算机 硬件的调试和测试。
万用表
用于测量电压、电流和电阻等电学参 数,具有便携式和易于使用的特点。
激光测量仪器
激光干涉仪
利用激光干涉现象测量长度、角度、表 面粗糙度等参数,具有高精度和高分辨
- 1、下载文档前请自行甄别文档内容的完整性,平台不提供额外的编辑、内容补充、找答案等附加服务。
- 2、"仅部分预览"的文档,不可在线预览部分如存在完整性等问题,可反馈申请退款(可完整预览的文档不适用该条件!)。
- 3、如文档侵犯您的权益,请联系客服反馈,我们会尽快为您处理(人工客服工作时间:9:00-18:30)。
6
三、工厂自己专用的长度基准
• 矩形量块作为长度基准存在问题:1)两端测量面不平行;2)两 端测量面和侧面不垂直;3)测量面平面度不好。
• 美国穆尔公司经过实践和反复研究,采用圆柱端面规作为长度基 准。外圆柱面可磨到很高圆柱度,水平放在V形支架内,可旋转以 校验端面和外圆柱面的垂直度,容易达到两端面的高度平行。
4)激光准直仪法
14
氦-氖激光器发出的激光的中心连线 构成激光准直测量的一条基准直线。 当光电接收靶5中心与激光束中心重合 时,指示表指示为零,若靶子中心偏 离激光束中心,指示表指示出数值即 偏差值。测量时首先将仪器与靶子调 整好,然后将靶子沿被测表面测量方 向移动,便能得到直线度误差的数值。
13
3)光轴法
测微准直望远镜或自准直仪发出的光线为理想直线,测出被测直线相 对于该理想直线的偏差值,经数据处理求出被测线的直线度误差。
测量步骤: 1)将被测线两端点连线调整到与光轴测量
基线大致平行; 2)若被测线为平面线,则xi代表被测线长
度方向的坐标值, yi为被测线相对于测量基 线的偏差值。
若被测线移动瞄准靶2,同时记录各点示值 (yi)。再经数据处理求出直线度误差值。
常用三块平台轮流对研,找出凸起进行刮研,直到接触斑点分布均匀。对高 精度测量平台用电子水平仪、自准直光管或双频激光干涉仪,测出平台的水平 倾角,经过数据处理,可得到平台各处不平面度误差的具体数值。
9
5.4 直线度、平面度和垂直度的测量
一、直线度的测量
线差法
线差法的实质是:用模拟法建立理想直线,然后把被测实际线上各被测 点与理想直线上相应的点相比较,以确定实际线各点的偏差值,最后通 过数据处理求出直线度误差值。
• 继圆柱端面规后又制成步距规,英制的步距规每一步距的增量为 1in(全长18和16in),公制的步距规每一步距的增量为30mm (全长480mm)。全长步距的误差不超过0.05µm。
7
5.3 测量平台
一、测量平台的选择
• 1.平台精度等级 • 测量平台采用00或0级,生产中使用的平台的测量表面多数为矩形,长 宽比约为4:3,高精度的平台采用正方形台面,平面度达到0.6µm。
4
5.2 长度基准
一、长度基准和米定义
• 米制是18世纪法国最早提出的,“以经过巴黎的地球子午线自北极至赤道这 一段弧长的一千万分之一为一米”。1880年国际计量局又制作了30多根铂 铱合金的高精度米尺——国际米原器。
• 1960年10月14日在巴黎通过用氦Kr86在真空中的波长作为长度基准:1m= 1650763.73×Kr86的波长。
• 1983年11月第17届国际计量大会上,批准了米的最新定义。 • 新定义的内容:米是光在真空中在1/299792458 s的时间间隔内所进行的路
程长度。
5
二、量块的检定
• 量块是由两个平行的测量面之间的距离来确定其工作长度的高精 度量具,其长度为计量器具的长度标准。按J系统》的规定,量块分为00、0、K、 1、2、3六级。我国对各类量块的检定按JJG146-1994进行。
目前在基础工业的某些领域,精密测量已成为不可分割的重要组成部分。 在电子工业部门,精密测量技术也被提到从未有过的高度。例如制造超大 规模集成电路,目前半导体工艺的典型线宽为0.25µm,正向0.18µm过渡, 2009年的预测线宽是0.07µm。此外,在高纯度单晶硅的晶格参数测量中, 以及对生物细胞、空气污染微粒、石油纤维、纳米材料等基础研究中,无 不需要精密测量技术。
1)干涉法
等厚干涉条纹
对于小尺寸精密表面的直线度误差。 把平晶置于被测表面上,在单色光 的照射下,两者之间形成等厚干涉 条纹,然后读出条纹弯曲度a及相 邻两条纹的间距b值,被测表面的 直线度误差为 a 。条纹向外弯,
b2
表面是凸的,反之,则表面是凹的。
10
用平晶测平尺的直线度
对于较长的研磨表面,如研磨平尺,可采用圆形平晶进行分段测量, 即所谓3点连环干涉法测量。若被测平尺长度为200mm,则可选用 Φ100mm的平晶,将平尺分成4段进行测量,每次测量以两端点连线 为准,测出中间的偏差。测完一次,平晶向前移动50mm(等于平晶 的半径)。然后通过数据处理,得出平尺的直线度误差。
• 2.平台结构 • 多数采用箱式结构,扁平的箱中有加强筋支承。
• 3.测量平台的材料 • 铸铁:一定耐磨性、较好短期稳定性,受潮长锈不变形,碰撞有毛刺。 • 花岗岩:耐磨性好、长期稳定性好、受潮变形不生锈,碰撞有小坑无 毛刺。
8
二、测量平台的支承
三点支承法 多点支承法
三、测量平台的本身的精度检验
11
干涉法举例:
测量数据
数据处理
2)跨步仪法
12
原理:以两支承点的连线作为理想 直线测量第三点相对于此连线的偏 差。测量前,把此装置放在高精度 平尺或平板上,将指示表的示值调 整为零,然后将测量装置放置在被 测面上进行测量,每次移动一个l 距离,读取一个读数。移动时,前 次的测点位置,就是后次测量的前 支承点位置,如此依次逐段测完全 长,最后数据处理,即可求出被测 件的直线度误差。
3
二、精密测量的新发展
• 极高精度测量方法和测量仪器的发展:0.04nm、0.01’’ • 精密在线自动测量技术的发展 • 测量数据的自动采集处理技术的发展
三、精密测量的环境条件
• 恒温条件 • 隔振条件 • 气压、自重、运动加速度和其他环境条件
四、量具和量仪材料的选择
• 根据材料热膨胀系数选择 • 根据材料的稳定性和耐磨性选择
精密和超精密加工技术
华南理工大学 陈松茂 讲师
第五章 精密加工中的测量技术
本章主要提要
2
5.1 精密测量技术概述
一、精密测量的意义
精密测量技术是机械工业发展的基础和先决条件之一。测量精度一般应 比被测件的精度高一数量级。由于有了千分尺类量具,使加工精度达到了 0.01mm,有了测微比较仪,使加工精度达到了1µm左右;有了圆度仪等 精密测量一起,使加工精度达到了0.1µm;有了激光干涉仪,使加工精度 达到了0.01µm。