项目进度计划的编制_生产经营管理_经管营销_专业资料
进度计划编制工序
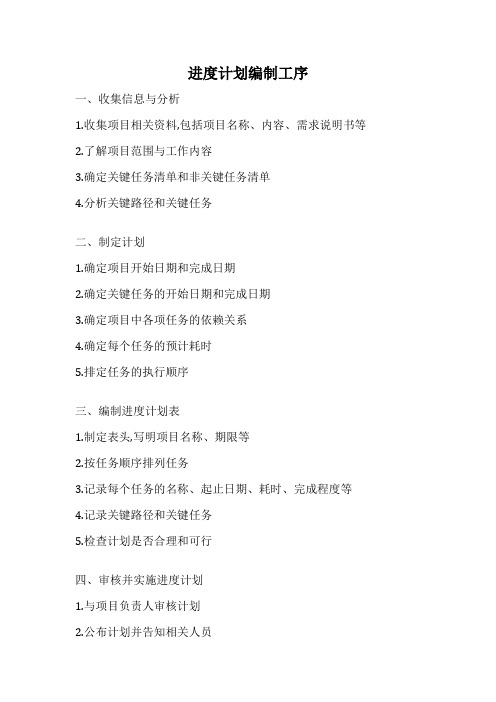
进度计划编制工序
一、收集信息与分析
1.收集项目相关资料,包括项目名称、内容、需求说明书等
2.了解项目范围与工作内容
3.确定关键任务清单和非关键任务清单
4.分析关键路径和关键任务
二、制定计划
1.确定项目开始日期和完成日期
2.确定关键任务的开始日期和完成日期
3.确定项目中各项任务的依赖关系
4.确定每个任务的预计耗时
5.排定任务的执行顺序
三、编制进度计划表
1.制定表头,写明项目名称、期限等
2.按任务顺序排列任务
3.记录每个任务的名称、起止日期、耗时、完成程度等
4.记录关键路径和关键任务
5.检查计划是否合理和可行
四、审核并实施进度计划
1.与项目负责人审核计划
2.公布计划并告知相关人员
3.排期控制及调整项目进度
4.及时跟踪实施进度并及时反馈
五、计划控制与调整
1.定期检查进度及问题
2.及时调整计划控制措施
3.重新评估计划并进行必要调整
4.反馈调整计划与整体进度。
工程建设项目前期工作进度计划表

建设局
21.
编制预算
代理公司
22.
财政预算评审
财政局
23.
工程招投标
交易中心
24.
签订合同
公证处
25.
土地平整、围墙、政策处理
所在乡镇
26.
施工准备(临时用电、用水)
施工单位
27.
工程测量定位
测绘大队
28.
质量安全监督手续
质安监站
29.
施工许可证
建设局
30.
开工建设
施工单位
初步设计和地质勘探招标
交易中心
11.
编制规划设计方案
设计单位
12.
地质勘察
勘察单位
13.
建设用地规划许可证
建设局
1项)
发改局
16.
供地(办理土地证)
国土局
17.
施工图设计
设计单位
18.
施工图审查、论证、图审
图审单位
19.
人防、消防、防雷与节能审查
职能部门
20.
工程建设项目前期工作进度计划表
序号
工作内容
相关部门
计划时间
完成时间
1.
编制可行性研究报告
代理机构
2.
财政出资意见
财政局
3.
项目受理意见书
发改局
4.
规划选址意见
建设局
5.
土地预审意见
国土局
6.
估算评审意见
财政局
7.
水土保持方案编制、批复
水务局
8.
环境影响报告编制、批复
环保局
9.
可研报告报批
发改局
10.
编制进度计划
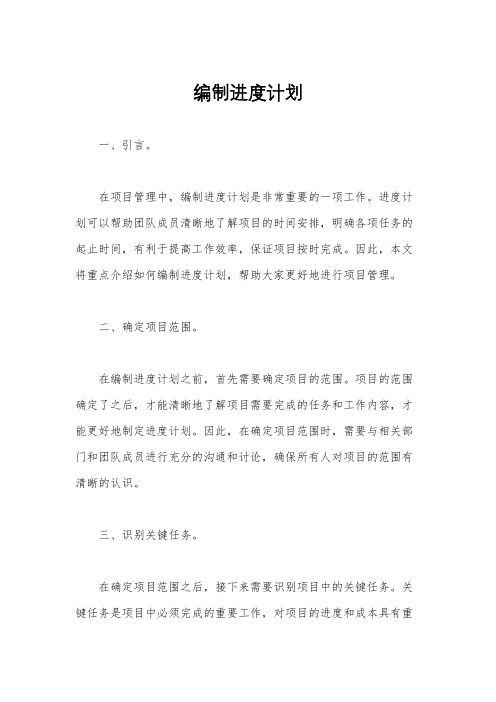
编制进度计划一、引言。
在项目管理中,编制进度计划是非常重要的一项工作。
进度计划可以帮助团队成员清晰地了解项目的时间安排,明确各项任务的起止时间,有利于提高工作效率,保证项目按时完成。
因此,本文将重点介绍如何编制进度计划,帮助大家更好地进行项目管理。
二、确定项目范围。
在编制进度计划之前,首先需要确定项目的范围。
项目的范围确定了之后,才能清晰地了解项目需要完成的任务和工作内容,才能更好地制定进度计划。
因此,在确定项目范围时,需要与相关部门和团队成员进行充分的沟通和讨论,确保所有人对项目的范围有清晰的认识。
三、识别关键任务。
在确定项目范围之后,接下来需要识别项目中的关键任务。
关键任务是项目中必须完成的重要工作,对项目的进度和成本具有重要影响。
因此,识别关键任务是制定进度计划的重要步骤。
在识别关键任务时,需要考虑任务的依赖关系、工作量大小、风险程度等因素,确保关键任务的准确性和完整性。
四、制定时间表。
在识别关键任务之后,就可以开始制定时间表了。
时间表是进度计划的核心内容,它包括了项目中各项任务的起止时间、工作量、负责人等信息。
在制定时间表时,需要充分考虑团队成员的实际工作情况,合理安排任务的时间和顺序,确保时间表的可行性和有效性。
五、监控和调整。
制定进度计划并不是一成不变的,随着项目的进行,可能会出现各种不可预测的情况,因此需要不断监控和调整进度计划。
在项目进行过程中,需要及时了解项目的进展情况,发现问题并及时进行调整,确保项目能够按时完成。
六、总结。
编制进度计划是项目管理中非常重要的一项工作,它可以帮助团队成员清晰地了解项目的时间安排,明确各项任务的起止时间,有利于提高工作效率,保证项目按时完成。
因此,需要在确定项目范围、识别关键任务、制定时间表和监控调整等方面下功夫,确保进度计划的准确性和有效性。
七、参考资料。
1. 《项目管理实务》。
2. 《项目管理案例分析》。
3. 《项目管理进度控制》。
八、附录。
项目进度计划书
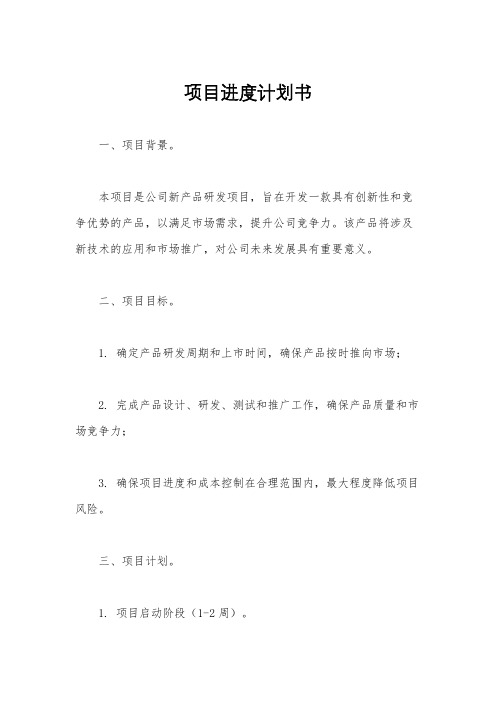
项目进度计划书一、项目背景。
本项目是公司新产品研发项目,旨在开发一款具有创新性和竞争优势的产品,以满足市场需求,提升公司竞争力。
该产品将涉及新技术的应用和市场推广,对公司未来发展具有重要意义。
二、项目目标。
1. 确定产品研发周期和上市时间,确保产品按时推向市场;2. 完成产品设计、研发、测试和推广工作,确保产品质量和市场竞争力;3. 确保项目进度和成本控制在合理范围内,最大程度降低项目风险。
三、项目计划。
1. 项目启动阶段(1-2周)。
确定项目组成员,明确各自职责和工作目标;制定项目可行性分析报告,明确项目目标和关键成功因素;确定项目实施计划和时间表,明确项目各阶段的工作内容和时间节点。
2. 产品设计阶段(2-4周)。
进行市场调研,了解市场需求和竞争对手情况;确定产品功能和性能指标,进行产品设计和方案评审;制定产品研发计划和工程进度表,明确各项工作任务和时间节点。
3. 产品研发阶段(4-8周)。
进行技术研发和试验验证,确保产品技术指标符合设计要求;进行产品原型制作和测试,验证产品性能和可靠性;进行产品改进和优化,确保产品质量和性能达到预期水平。
4. 产品测试阶段(2-4周)。
进行产品功能测试和性能测试,确保产品各项指标符合标准要求;进行产品可靠性测试和环境适应性测试,确保产品在各种条件下正常运行;进行用户体验测试和市场反馈调研,改进产品设计和功能,确保产品满足市场需求。
5. 产品推广阶段(4-8周)。
制定产品推广计划和营销策略,确定产品定位和推广渠道;进行产品宣传和推广活动,提升产品知名度和市场份额;进行产品销售和售后服务,建立客户关系和市场口碑,确保产品销售和市场份额稳步增长。
四、项目风险。
1. 技术风险,新技术应用可能存在技术难点和风险,需要加强技术研发和验证工作;2. 市场风险,市场需求和竞争情况可能发生变化,需要及时调整产品设计和推广策略;3. 成本风险,项目研发和推广成本可能超出预算,需要加强成本控制和资源管理。
项目执行计划 project execution plan

Engineering Procedure2004 SAEP-12 31August, Project Execution PlanDocument Responsibility: Project Support and Controls Dept.Saudi Aramco DeskTop StandardsTable of ContentsScope (2)12Documents (3)ApplicableInstructions (4)3Responsibilities (16)4Exhibits (18)Exhibit A - Table of Contents (18)Exhibit B - Approval Sheet (19)Exhibit C - Revision Control (20)Exhibit D - Contracting Plan Matrix (21)Exhibit E - Comparison of VariousAlternatives (22)ContractingExhibit F - Project Milestone Schedule (23)Exhibit G.1 - SAPMT Organization(Typical Design Phase) (24)Exhibit G.2 - SAPMT OrganizationPhase) (25)Construction(TypicalExhibit H - Project Responsibility Matrix (26)Exhibit I - Value Practices Schedule (27)Previous Issue: 31 May, 2000 Next Planned Update: 1 September, 2009Next Planned Update: 1 September, 2009 Project Execution Plan 1 Scope1.1 DefinitionThe Project Execution Plan (PEP) is a strategic planning document that definesobjectives, plans, requirements and related information necessary for optimumproject execution. It is a master reference guide that promotes commonunderstanding and alignment of all project participants. The PEP is prepared bythe Project Manager, with input from the Proponent and other Saudi Aramcoorganizations that have key roles in a project's execution.1.2 PurposeThe PEP serves as a communications and coordination tool that formallyestablishes the Project Manager's front-end project planning, with emphasis onidentifying issues critical to project success and defining strategies to addressthese issues. It is an agreement endorsed by the Saudi Aramco ProjectManagement Team (SAPMT), the Proponent, and Management defining theexecution of the project, including schedule, method(s) of executing the workand responsibilities of major participants. In one comprehensive document, thePEP relates the approved project scope with contracting and material plans, costinformation, summary schedules, value practices implementation, departmentalresponsibilities, and SAPMT staffing requirements. The PEP is intended toprovide strategic guidance to develop more detailed tactical planning andexecution as the project progresses.Applicationand1.3 TimingThe PEP shall be issued in accordance with the timing outlined below, which isdesigned to support the PEP's purpose of serving as a strategic planning tool:•Abbreviated PEP is mandatory for all BI's•Full PEP is mandatory for BI's- over $25MM- or recommended by the responsible Department Manager•PEPs are waived for Master Appropriation projects.PEP1.3.1 AbbreviatedTo be issued prior to release of Preliminary Engineering funds. Whenrequested, PS&CD / Project Controls & Information System Unit(PC&ISU) shall participate and assist SAPMT in the preparation of thePEP Level II Milestone Schedule.Next Planned Update: 1 September, 2009 Project Execution PlanThe Abbreviated PEP is intended to provide a framework forsubsequent planning. It is not expected that every detail required bySAEP-12 will be addressed at this time. As a minimum, the SAPMTshall address the following items using the best information currentlyavailable. It is understood that all sections are subject to furtherdevelopment and change:•Project Summary•Contracting Strategy•Organization Chart•Milestone Schedule•Value Practices•Contractor Saudization Plan•Maximizing In-Kingdom Design Work•Projects within Existing Facilities (Non-Grass Roots)•Areas of ConcernThe Abbreviated PEP will be the basis for development of the FullPEP if one is to be prepared. The Abbreviated PEP shall be updated orrevised as required to reflect major changes in plans if a full PEP is notrequired.PEP1.3.2 FullTo be issued for approval by 30% preliminary engineering completionor within 90 days of Project Proposal Start. SAPMT will report statusof PEP submittals in the PPU's comments section.The PEP shall be updated as the need arises prior to implementingmajor scope changes or significant changes in contracting plan, and atother times deemed necessary by the PEP approval authority. SAPMTmay issue a completely revised document or an addendum covering thechanged section(s) only.Documents2 ApplicableSaudi Aramco Engineering ProceduresNext Planned Update: 1 September, 2009 Project Execution PlanSAEP-13Project Environmental AssessmentsProposalSAEP-14 ProjectSAEP-31Corporate Spare Parts Data RequirementsSAEP-125Saudi Aramco Engineering StandardsSAEP-329Project Close-out ReportSaudi Aramco General InstructionsGI-0002.710 Mechanical Completion and PerformanceAcceptance of FacilitiesGI-0710.002 Classification of Sensitive DocumentsSaudi Aramco Cost and Scheduling ManualSaudi Aramco Contracting ManualSupply Chain Management Manual3 InstructionsThe PEP shall include the following sections:3.1 Table of Contents, Approval Sheet and Revision ControlFor format, see Exhibits A, B, and C.3.2 ProjectSummaryProvide a brief synopsis of the objectives, scope, and current progress status ofthe Project. Incorporate into the Project Summary:3.2.1 ProjectPurposeSummarize the purpose of the project explaining why it is being done(e.g., to increase production capacity of a plant by 100,000barrels/day).3.2.2 DesignBasisProvide a synopsis of how the project is to be accomplished (e.g., toincrease production by expanding existing facilities or by constructinga new plant) by summarizing the project's basis of design as describedin the current scoping paper.Scope3.2.3 ProjectNext Planned Update: 1 September, 2009 Project Execution PlanBriefly describe what is to be accomplished by the project, such asproject activities to be achieved, physical facilities to be built,demolished, or revamped, etc. This information will be a summary ofthe work described in the current Design Basis Scoping Paper and/orProject Proposal scope of work.3.2.4 Project Progress StatusDefine where the project currently stands in the project life cycle, inorder to establish the information basis on which the PEP is beingprepared. Briefly identify the major ongoing activities and providecurrent percent complete of project proposal, detailed engineering,procurement, and construction, as applicable.Location3.2.5 ProjectPEP should state location of project and indicate whether offshore oronshore.3.2.6 Project Shutdown RequirementsPEP should identify shutdown requirements and if it is planned duringPlant T&I.3.2.7 RelatedProjectsPEP should identify other related projects that may impact the project.3.3 ContractsThe contract development process is often intricate and interrelated and onceactions based on a particular strategy are initiated, it may not be practical orpossible to modify the strategy. An overall contracting strategy which addressesall aspects of the work must be developed and presented to management at anearly stage of every project.Strategy3.3.1 ContractingA Contracting Strategy document reflecting the SAPMT's initial viewon what type(s) of contracts to be used shall be prepared as part of eachAbbreviated PEP. This Contracting Strategy shall be updated to reflectany major changes (particularly related to OOK contracts, non-lumpsum contracts, and non-competitive awards). If a Full PEP is prepared,the Contracting Strategy shall become part of it. If a Full PEP is notprepared, the Contacting Strategy shall be updated even if other partsof the Abbreviated PEP are not.Next Planned Update: 1 September, 2009 Project Execution PlanThe Contracting Strategy shall summarize the plans for developing andprocuring the necessary contracts for the project's major contractingphases (i.e., Project Proposal, Detailed Design, Procurement andConstruction). Information shall be categorized by the majorcontracting phases mentioned and include the following:a) Type of Contract (Lump Sum Turnkey, Lump Sum, Lump SumProcure/Build, Reimbursable Cost, Unit Rate, Service Order,etc.) and the reasons for selection.b) Procurement Method (Competitive Bid, Sole Source, etc.) andreasons for selection and whether an existing General Bid slatewill be used.c) Appropriate Project and Contracting Milestones, for example:- Expenditure Request Approval (ERA)- Prepare and Issue Bid Packages- Contract Award- Mechanical Completion- On StreamThe Contacting Strategy shall include an exhibit illustrating thecontracting plan in matrix form (See Exhibit D).Plans3.3.2 ContractingA Contracting Plan is required for each contract action (or relatedcontract actions) unless the requirement has been waived (in writing)by the Contracting Representative. The Contracting Plan is the jointresponsibility of the Contracting Department and the contractproponent. After approval by the Contract Signatory, the ContractingPlan shall be incorporated into the Project Execution Plan. For moredetailed instructions, refer to the Saudi Aramco Contracting ManualVII(1) - Contract Planning and VIII(24) - Contracting Plan (Outline).Prior to carrying out a detailed analysis as part of the Contract Plan,potential contracting alternatives in the form of a summary levelschedule comparison shall be prepared (See Exhibit E).For projects involving major LSTK contracts, the option of issuing thebid package prior to ERA should be addressed. Analysis shouldinclude estimated effects on schedule, cost, and other considerationscomparing the normal procedure of issuing bid package after ERAwith a proposed option of bidding prior to ERA. This analysis shouldNext Planned Update: 1 September, 2009 Project Execution Planalso include evaluation of the feasibility of using the LSTK bids in theER estimate.3.4 Material Procurement PlanThe Material Procurement Plan addresses project material requirements, theirprocurement and movement. It should define the proposed procurement andtraffic responsibilities of Saudi Aramco and the Contractor(s). Projects willreview proposed procurement actions with representatives of Material Supply.This review shall involve, at a minimum, the project Liaison Coordinator of theProjects Purchasing Division.3.4.1 Critical and Long Lead-Time Material and EquipmentPrepare an itemized listing of material and equipment consideredcritical and/or long lead items. Specific actions should be identified toensure that such items will arrive at the designated job site on or beforethe required dates irrespective if handled by Saudi Aramco or by acontractor. Examples of such actions include use of air freight,dedicated trucks, premiums, penalty and incentives, identification,prioritization, and close monitoring of critical material and its properties to the construction schedule, SAPMT representative at vendor'sshop, expediting custom clearance, unloading and placing largematerial on foundations rather than storing, etc.If procurement of major equipment and materials is on the critical pathof the project schedule, SAPMT shall consider various strategies toreduce its impact to the project schedule. Such strategies may includeearly Company procurement, early Company procurement andassignment ("novation"), Company or Project Proposal Contractorprocurement of early vendor engineering ("beneficial engineering"),and early engineering by vendors using time unit rates under theProject Proposal Contractor's contract.3.4.2 Other Material and EquipmentDesignate responsibilities between Saudi Aramco and Contractors forcost effective supply of materials and equipment to meet projectschedules.The Material Procurement Plan requires addressing maximum cost-effective usage of locally-manufactured materials, use of on-hand andsurplus material, material quantity concerns, standardization, and totalcost of ownership and takes into consideration the guidelines of SAEP-125, Saudi Aramco Engineering Standards, and the Supply ChainNext Planned Update: 1 September, 2009 Project Execution PlanManagement Manual. Furthermore, the plan should address the use ofexisting corporate agreements; vendor selection criteria; materialquality concerns; documentation; expediting; inspection; packing andmarking; shipping, clearance and receiving; storing, issuing, staging,and the return and disposal of excess project material and equipment.3.4.3 Surplus 9COM Material and EquipmentReview Surplus 9COM (previously known as Direct Charge – DC)material and equipment list that could be incorporated in the project'sdesign. Surplus 9COM material and equipment should be looked at inthe earliest stages of design so that it can be incorporated into thedesign.3.4.4 Excess 9CAT MaterialsReview Excess 9CAT (previously known as Saudi Aramco MaterialsSystem – SAMS) materials list of high-dollar-value items ($10,000 andabove) that could be incorporated in the project's design.3.4.5 Heavy/Oversize Material or EquipmentPrepare a list of heavy/oversize material or equipment. Establishresponsibilities for heavy lift requirements. Heavy lift planning formaterials and equipment, and related requirements, will be coordinatedwith the Saudi Aramco Heavy Lift Group. Consult with the MaterialsTraffic Department regarding proposed international shippingarrangements and with the Transportation Department for in-Kingdommovements of heavy/oversize material or equipment.3.4.6 Start-up, Operating, and Capital SparesEstablish responsibilities and requirements for start-up, operating, andcapital spares procurement. Ensure compliance to requirements foroperating spare parts in accordance with SAEP-31, Corporate SpareParts Data Requirements. Address the disposition of contractorprocured spares, if applicable.Duties3.4.7 CustomsAddress responsibility for payment of customs duties, based on themost recent Government regulations including compliance with propercustoms exemption requirements if any.3.4.8 Quality Assurance/Quality ControlNext Planned Update: 1 September, 2009 Project Execution PlanIdentify materials quality assurance and quality control planningrequirements. Address vendor inspection requirements and plans,including identification of materials to be factory tested andcoordination with Saudi Aramco Vendor Inspection.3.5 Precommissioning,Commissioning, and Startup PlanStartup is defined as the transitional phase between facility constructioncompletion and onstream, including all activities that bridge these two phases(i.e., precommissioning through performance acceptance). Overall projectsuccess is strongly related to startup success, which depends heavily on thedegree and thoroughness of early startup planning. Saudi Aramco GI-0002.710,Mechanical Completion and Performance Acceptance of Facilities, provide theframework for startup planning. The Best Practices "Planning for StartupModel" is a useful reference and provides tools designed to assist in developingand implementing an early startup plan. The Startup Planning Modelrecommends that 50% of the startup planning effort should be completed by theend of Project Proposal phase. By the end of detailed design the startupplanning effort should be 80% complete.The startup plan addresses the roles and responsibilities of key persons andorganizations, as well as the timing of startup planning and execution activities.The startup plan shall address the following issues:andTiming3.5.1 ResponsibilitiesSAPMT and Proponent representative shall be assigned responsibilityfor managing the planning of startup; specify when these assignmentswill be made and what their startup planning responsibilities willentail. Identify other key contributors to startup planning andexecution, including Inspection, Loss Prevention, contractors, vendors,and others as required, and define their roles and responsibilities.Provide estimated timing and duration of startup planning,precommissioning, mechanical completion, and commissioningactivities, including operations and maintenance training required priorto startup.3.5.2 Systems Turnover SequenceProvide a conceptual plan of the breakdown of the facility into systemsand the sequence in which these systems will be checked out andturned over to the Proponent. Address specific plans to implementpartial Mechanical Completions, if applicable.Next Planned Update: 1 September, 2009 Project Execution Plan3.5.3 Startup Execution Plan (SUEP) PreparationThe Startup Execution Plan (SUEP) is a planning document thatdefines the objectives, plans, requirements, and related activities andinformation necessary for a successful startup. It is a master referenceguide that promotes common understanding and alignment of allproject participants.Cost3.6 ProjectFunding3.6.1 ProjectDescribe Preliminary Engineering Funds requirements, Prior ApprovalExpenditure Request (PAER) Funds requirements if applicable, andplans for ER Estimate preparation. Also, describe the project budgetamount and provide a summary of its major elements of engineering,material, and construction if available. Describe the basis of thecurrent estimate. Identify any critical cost items that will requirespecial attention to avoid cost overruns.Control3.6.2 CostDescribe the strategies to be utilized to ensure effective cost controland accurate cost reporting throughout the project life fromPreliminary Engineering Funds approval through project close-out.Address the subjects of work breakdown structure, cost contingencymanagement, cost status reporting systems, and expenditure forecastpreparation. Identify any unique project characteristics that mayrequire deviations from standard Saudi Aramco cost controlprocedures, and provide plans for handling such cases.The project's work breakdown structure should be developed as aunified system that supports integrated cost and schedule control.Schedule3.7 Project3.7.1 ProjectPlanDescribe the summary logic and interdependencies used to develop theproject milestone schedule. Identify critical schedule risk items andthe potential impact of unforeseeable schedule delays.Provide Project Milestone Schedule (See Exhibit F) in bar chart formatsummarizing major project activities, including plant outages andinterfaces with other projects as applicable. The schedule shallinclude:Next Planned Update: 1 September, 2009 Project Execution Plan•contract development and award milestone dates by packages•value engineering studies•project proposal review and approval•ER estimate preparation, review, and approval•mobilization for engineering and construction•detailed engineering control points•long lead material procurement activities including release ofpurchase orders, fabrication, and delivery•interim construction milestones•Beneficial On Stream (BOS)•mechanical completion•precommissioning, commissioning, & startup•shutdowns•onstream3.7.2 Progress Measurement and Schedule ControlDescribe the methodology to be utilized to ensure accurate progressmeasurement and effective schedule control throughout the project life.Address the subjects of work breakdown structure, progress reportingsystems, responsibilities of contractors with respect to progressmeasurement and schedule control, and Critical Path Method (CPM)scheduling software requirements. The Saudi Aramco Cost andScheduling Manual provides a definition of scheduling levels of detailto be used on Saudi Aramco projects.3.8 Project Organization and Interfaces3.8.1 Establishing the SAPMTDescribe the process of establishing the SAPMT, including thefollowing:•Through review process that will be conducted to determine thetype of disciplines needed to be covered by the SAPMT.•Objectives and responsibilities (including correlation with workbreakdown structure) for the Project Manager, Senior ProjectEngineers, and other SAPMT members as appropriate.Provide organization charts for each major phase of the project(Exhibit G).Interfaces3.8.2 SAPMTNext Planned Update: 1 September, 2009 Project Execution PlanDescribe the roles, responsibilities, and reporting relationships betweenthe SAPMT, Proponent, and other parties involved in the project,including Saudi Aramco departments and contractors. Include atypical project responsibility matrix (Exhibit H).Describe how the SAPMT will provide effective and efficientcommunications among the SAPMT, proponent, support groups, andcontractors during all phases of the project.Describe how the SAPMT will provide close coordination andeffective interface with other BI SAPMTs or Proponents, whose workwill have direct impact on the Project's activities.Practices3.9 ValueThe oil and gas industry, as a whole, uses value practices that have been proventhrough experience to assist projects in reaching goals of shorter schedules andlower costs, as well as enhanced safety. The value practices outlined below areapplicable to Saudi Aramco projects and, when properly planned andimplemented, can help guide project teams to improved performance. If aproject team does not include the use of value practices as an activity in theproject plan, some value practices may be overlooked and potential benefits lost.Value practices must be implemented early in the project cycle to be effective,so the planning must reflect this approach.Provide Value Practices Implementation Schedule (Exhibit I)SAPMT may contact PS&CD/Project Performance Optimization Division(PPOD) for assistance with this section if required.Engineering3.9.1 ValueSummarize SAPMT plan for implementing Value Engineering inaccordance with the requirements of SAEP-14, Project Proposal.Identify when the VE study will be conducted and by whom.3.9.2 Best Practices ImplementationSummarize SAPMT plan for implementing Project Management'scurrently-identified or other industry best practices in accordance withPPOD guidance or the requirements of SAEP-14, Project Proposal – asappropriate. Since best practices have the greatest impact on a projectin the very early stages, it is recommended that use of best practices beplanned early and should be combined and repeated, as applicable.(For example, a constructability review should be executed duringNext Planned Update: 1 September, 2009 Project Execution Planpreliminary engineering at approximately 30% and again before 20%detailed design completion.)•The following best practices have been identified as having highpayback potential for Saudi Aramco projects:- Lessons Learned- Project Definition Rating Index- Project Execution Planning Workshop (PEPW)- Scope Control & Change Management- Constructability- Schedule Optimization- Planning for StartupIt is the responsibility of the SAPMT to implement as many ofthese practices as are appropriate to ensure successful projectplanning and execution.•Should other best practices be "rolled out" by PPOD betweenrevisions of SAEP-12, project teams should investigate if thosenew best practices offer value improvement to their projects, andplan their implementation accordingly.For Lessons Learned, SAPMT shall define the plan for finding andimplementing existing lessons learned from previous projectsapplicable to the current project. As a minimum, SAPMT shallsearch the Project Management's Lessons Learned database on theSaudi Aramco intranet at the beginning of each project phase(project proposal, detailed engineering, and construction) to reviewthe latest lessons learned. Furthermore, SAPMT shall define plansfor collecting new lessons learned during the life of the project. Asa minimum, SAPMT shall collect and submit lessons learned atERA (covering the Project Proposal phase) and MechanicalCompletion (covering design, procurement, and constructionphases) in accordance with SAEP-329, Project Close-out Report.3.9.3 BenchmarkingSummarize SAPMT plans for initiating a formal benchmarkinganalysis in accordance with SAEP-14, Project Proposal. Identify whenthe benchmarking study will be conducted and by whom.3.10 Project Safety and EnvironmentalNext Planned Update: 1 September, 2009 Project Execution Plan3.10.1 Preliminary Hazard Analysis (PHA) and Hazard and Operability(HAZOP) Studies•Plans and ObjectivesSummarize SAPMT plan for implementing PHA and HAZOPstudies. The objective in performing PHA and HAZOP studies isto identify any major hazards, improve process safety, and/orminimize operability problems. An additional goal is to providefurther insight for risk management decisions by assigning aqualitative risk factor to each potential hazard or operabilityproblem.•Requirements and TimingThe SAPMT and Proponent, in conjunction with the LossPrevention Department (LPD), and Process & Controls SystemDepartment (P&CSD) shall decide which projects and specificfacilities require PHA and/or HAZOP studies. Duplicate facilitiesshould not require new PHA and/or HAZOP studies. Only new orupgrade facilities that use, produce, process, transport, or storeflammable, explosive, toxic or reactive substances in largequantities are candidates for PHA and/or HAZOP studies.The PHA studies shall normally be conducted during the projectproposal stage and the report shall be incorporated into the ProjectProposal. The HAZOP studies, if required, shall be performedduring the detailed design when the facility design is firm and nomajor design changes are forecasted. HAZOP studyrecommendations shall be incorporated into the final design of thefacility.•PHA and HAZOP Studies ExecutionThe PHA and HAZOP studies should be part of the projectproposal or detailed design contract, if Saudi Aramco decides theContractor is qualified to conduct the studies. If the Contractor isnot qualified to conduct the study, a subcontractor can be used.SAPMT shall notify LPD, P&CSD, and all other concerned partiesat least six weeks in advance of any PHA or HAZOP study so thatqualified personnel can be assigned and to participate.Next Planned Update: 1 September, 2009 Project Execution PlanA copy of the report shall be provided to LPD for review prior torelease. SAPMT shall distribute copies of PHA and HAZOP studyreports to all participants within four weeks after the study.3.10.2 Environmental AssessmentDescribe the plan for preparing the Environmental Impact Assessmentas required by SAEP-13, Project Environmental Impact Assessment.3.10.3 Project Safety ProgramDescribe the safety program for the project. The program shoulddescribe the safety objectives for the project and how the program willbe managed to ensure these objectives are met. Address the issues ofaccident prevention and contractor safety.3.11 Contractor Saudization PlanAddress what actions will be taken to promote and support the hiring andtraining of Saudi Arab personnel by contractors working on the project.3.12 Maximizing In-Kingdom Design WorkAddress what actions will be taken to promote maximizing the IK design work.Also address the feasibility of performing portions of any planned LSTK OOKdesign work IK.3.13 Projects within Existing Facilities (Non-Grass Roots)Address what actions will be taken with regards to upgrade renovation oraddition to existing facilities in the following areas.Level of design work during the project proposal development.Risk assessment for items that may impact the project cost estimate.3.14 Areas of ConcernAddress project concerns where corresponding plans of action or solutions havenot been completely defined. Any unusual efforts or procedures required forsuccessful project completion will be included in this section. Also, anyanticipated problems that may affect operability, cost or schedule should behighlighted here.3.14.1 Engineering Design。
工程进度计划编制方案范文

工程进度计划编制方案范文一、编制目的工程进度计划是指在确定项目目标和任务的基础上,根据项目具体情况,制定项目实施的时间计划和进度安排,以便合理、有效地组织和安排各项工作,保证工程按时按质完成。
编制工程进度计划的目的是为了合理安排施工任务,保证施工按时完成,提高工程质量和经济效益。
二、编制原则(一)科学性原则工程进度计划必须符合工程实际情况和规律性,科学合理,不能脱离实际。
要根据工程的实际情况,结合施工工艺和设备情况,合理安排施工顺序和时间节点,从而确定整个工程的时间计划。
(二)可行性原则编制工程进度计划必须具有可行性和操作性,不能过于理想化或超前,要考虑合理施工周期和工期计划,充分考虑各种紧急情况和可能的延期因素。
(三)全面性原则编制工程进度计划应全面考虑施工前、施工中、施工后的各种工程活动和配套措施,确保整个工程的施工安排和进度计划具有全面性。
(四)协调性原则编制工程进度计划要充分考虑各种工程活动之间的协调关系,确保不同施工环节之间的协调和衔接,避免各种冲突和矛盾。
三、编制内容(一)项目概况1. 项目名称2. 项目位置3. 项目业主4. 项目总包单位(二)项目进度目标1. 确定完整的项目进度目标清单2. 确定项目的开始和结束时间3. 确定各个阶段的时间节点(三)项目进度计划1. 分析项目阶段划分2. 制定项目的总进度计划3. 制定各个阶段的详细进度计划(四)关键路径分析1. 确定项目的关键路径2. 确定关键路径上的主要节点和工作项(五)项目资源分配1. 分析项目的资源需求2. 完成项目的资源分配计划(六)风险评估与应对1. 分析项目的风险因素2. 制定应对风险的措施3. 预留充足的缓冲时间(七)进度监控与调整1. 设立进度监控系统2. 定期进行进度监控与分析3. 及时进行进度调整和优化四、编制方法(一)确定项目目标和任务首先需要明确项目的总体目标和具体任务,了解项目的基本情况和业主的要求,明确项目的开始和结束时间,确定项目的总体工期。
工程进度管理流程

工程进度管理流程3.工作程序3.1编制工程进度计划3.1.1工程部接到公司批准的《项目开发进度计划》后,主导编制《项目工程进度计划》,并落实总工期和节点计划控制措施,同时与施工单位就进度计划相关细节内容进行深度沟通,以取得一致意见,《项目工程进度计划》由项目公司总经理审批后下发至各相关部门。
3.1.2施工单位应在开工前15天内,提交《施工组织设计》,每月25日前分别编制下一个月的阶段性施工进度计划,报监理单位和工程部审核,项目公司总经理审批后实施。
3.2工程进度检查3.2.1监理单位根据《施工组织设计》、阶段性施工进度计划,检查施工单位填报的月形象进度,现场完成工作量及工程量统计表,每月25日汇总形成《监理月报》报工程部审核。
3.2.2工程部根据《施工组织设计》、阶段性施工进度计划,检查施工单位填报的月形象进度,现场完成工作量及工程量统计表,每月底由工程部汇总形成《项目工程月报》并于当月25日前报备至项目公司总经理和运营管理部。
对工程月进度计划延误超过3天的要求施工方分析原因,制定赶工措施并实施,对拖延5天的施工单位除分析原因,制定赶工措施外,还要给予经济处罚。
3.2.3工程部对未完成当月施工进度的,应向施工单位以《工程整改通知单》形式发出预警或召开工程协调会,同时通知监理单位,以分析影响进度的原因(如设计变更、报批报建、气候、供应材料、施工单位人力及物质资源等)、采取补救措施及下一步相应的赶工方案和措施,报项目公司总经理审批后实施。
3.2.4工程部专业工程师应每天巡视现场,掌握工程形象进度,并记录在《现场工程管理日志》中,必要时应以图片方式反映。
如发现进度延迟,则应按照3.2.2处理。
3.3进度计划调整3.3.1如设计变更、气候、材料供应等客观因素或建设单位原因影响施工进度确需延迟《项目工程进度计划》,由工程部报项目公司总经理审批后进行调整;若影响节点计划需报运营管理部审核,总部运营分管领导审批后进行调整。
项目进度计划编制过程
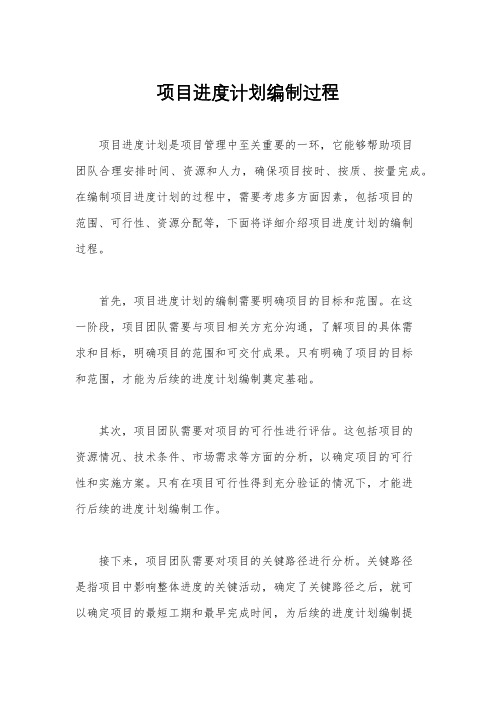
项目进度计划编制过程项目进度计划是项目管理中至关重要的一环,它能够帮助项目团队合理安排时间、资源和人力,确保项目按时、按质、按量完成。
在编制项目进度计划的过程中,需要考虑多方面因素,包括项目的范围、可行性、资源分配等,下面将详细介绍项目进度计划的编制过程。
首先,项目进度计划的编制需要明确项目的目标和范围。
在这一阶段,项目团队需要与项目相关方充分沟通,了解项目的具体需求和目标,明确项目的范围和可交付成果。
只有明确了项目的目标和范围,才能为后续的进度计划编制奠定基础。
其次,项目团队需要对项目的可行性进行评估。
这包括项目的资源情况、技术条件、市场需求等方面的分析,以确定项目的可行性和实施方案。
只有在项目可行性得到充分验证的情况下,才能进行后续的进度计划编制工作。
接下来,项目团队需要对项目的关键路径进行分析。
关键路径是指项目中影响整体进度的关键活动,确定了关键路径之后,就可以确定项目的最短工期和最早完成时间,为后续的进度计划编制提供了重要依据。
然后,项目团队需要进行资源分配和任务分解。
在这一阶段,需要明确项目所需的各类资源,包括人力、物力、财力等,以及对这些资源的合理分配和利用。
同时,需要将项目的各项任务进行详细分解,确定每个任务的工作量和工期,为后续的进度计划编制提供了具体数据支持。
最后,项目团队需要编制项目的进度计划表。
在这一阶段,需要将前期的工作成果进行整合,确定项目的总工期、里程碑节点、关键活动和各项任务的具体时间安排,形成完整的项目进度计划表。
这个过程需要考虑各种不确定性因素,合理设置缓冲时间,确保项目的进度计划具有一定的弹性和可操作性。
总的来说,项目进度计划的编制是一个系统工程,需要项目团队充分合作,充分考虑各种因素,确保项目的进度计划能够科学合理、可行可操作。
只有在项目进度计划编制过程中做到严谨、全面、周密,才能为项目的顺利实施提供有力支持。