电渣焊常见缺陷产生原因分析及防止方法
焊接常见缺陷产生的原因及其预防措施

编号
责任者
文件材料题名
日
期
页次
备
注
16
HP-23〔1〕
蒙电一建
25MnG·∮60×·Ws/Ds·5G焊接工艺评定报告
17
HP-24
蒙电一建
12Cr1MoV·∮133×14·Ws/Ds·5G焊接工艺评定报告
18
HP-24〔1〕
蒙电一建
25MnG·∮60×·Ws/Ds·2G焊接工艺评定报告
19
HP-25
9
HP-12
蒙电一建
16Mn·δ=18㎜·CO2·3G焊接工艺评定报告
10
HP-13
蒙电一建
16Mn·δ=18㎜·CO2·4G焊接工艺评定报告
11
HP-14
蒙电一建
1Cr18Ni9Ti·∮60×8·Ws·5G焊接工艺评定报告
12
HP-20
蒙电一建
12Cr2MoWVTiB·∮54×·Ws/Ds
5G焊接工艺评定报告
附表01
焊接常见缺陷产生的原因及其预防措施
序号
焊接缺陷
产生因素
预防措施
1
咬边
1、焊接电流大;2、焊接过程中,在母材位置停留时间短,铁水不足。
1、在电流范围内适当减小焊接电流;2、调整焊接手法,给足铁水。
2
夹渣、夹钨
1、层间清理不干净;2、焊接时焊条不摆动或摆动幅度小;3、焊接材料选用不当;4、焊件太大;5、电弧电压太高。
1、正确选用焊接材料;2、减少单层焊道熔敷厚度,使熔渣充分浮到熔池外表;3、增大焊接电流,有规律性的运条、搅拌熔池、使熔渣与熔池金属充分别离;4、仔细清理层间焊渣;5、降低电弧电压;6、氩弧焊时焊工手法要稳,防止钨极短路。
技能培训资料:常见的焊接缺陷

1、焊接夹渣焊接夹渣缺陷是指焊后熔渣残留在焊缝中的情况。
夹渣主要有金属夹渣即夹铝或夹铜和非金属夹渣即焊条药皮、焊剂、硫化物、氧化物或氮化物留存在焊缝中。
夹渣产生的主要原因是破口清理不彻底、坡口尺寸不符合设计要求、焊条质量不合格等。
2、焊接凹坑焊接凹坑是指在收弧和断弧时操作不当而在焊道末端形成的凹陷部分。
主要产生的原因是焊接材料在焊接过程中停留时间不够,填充金属不够导致的。
其危害是导致焊缝的横截面减少,凹坑处容易产生偏析或杂质汇集,从而易形成气孔、灰渣或裂纹。
3、焊接裂纹焊接裂纹主要是指焊缝中金属原子结合遭到破坏,从而形成新的界面而形成的裂缝。
焊接裂纹按温度可分为热裂纹、再热裂纹、冷裂纹、层状撕裂。
裂纹再焊接工艺里是最严重的一种缺陷,也是导致焊接结构失效而引发事故的主要原因。
4、焊接气孔焊接气孔主要是在熔池中的气泡在金属凝固时未能及时逸出而形成的空穴。
其主要产生原因是电弧保护不到位,弧太长或者焊接材料有锈,气体保护介质不纯以及坡口处理不到位。
5、焊接咬边焊接咬边是指沿着焊趾,在焊件部分形成凹陷或者沟槽。
主要形成原因是焊接参数选择不正确、焊速太慢、电弧拉得太长、电流过大、焊枪位置不准确导致。
其危害导致焊件工作截面减小,咬边处应力集中。
6、焊接焊瘤焊瘤是指金属溢流到加热不足的焊件或焊缝上,未能与焊件和金属熔合在一起而堆积的金属缺陷。
主要形成原因是焊接参数选择不符合设计要求、焊接坡口清理不到位、焊接速度太慢等。
7、焊接局部烧穿焊接局部烧穿是指焊接过程中,焊接部位熔透至坡口背面,形成穿孔现象。
主要产生原因是焊接电流太大、焊件加热过高、坡口对接空隙太大、焊接速度太慢、电弧停留时间太长等8、焊接未焊透焊接未焊透是指焊缝的熔透深度小于板厚时形成的。
在单面时,焊缝熔透到达不了焊件底部;双面焊时两道焊缝熔深总厚度小于焊件厚度而形成的。
主要形成原因有焊条位置不准确,偏离中心位置;坡口角度太小,焊接空隙小钝边太大;电流太小等。
常见质量问题防治措施专项施工方案

常见质量问题原因分析、防治措施一、主要质量问题及防治措施(一)、墙面裂缝及空鼓质量问题及防治措施1、存在问题及原因分析:(1)、墙面裂缝问题集中出现在混凝土结构及填充墙交接处、施工预留洞口、填充墙管线沟槽处、业主私自改造的墙体上等部位,这是业主投诉最多且比较难处理的问题。
墙面抹灰完成后的较长时间内会陆续出现墙面空鼓现象。
(2)、原因分析:1)、选用分包单位的材料质量及施工水平达不到要求,施工时经常不按照质量要求进行施工;2)、基层处理不合格,清理不彻底;3)、抹灰经历夏天和冬天,温差过大,混凝土结构和填充墙材料膨胀系数不一致,造成温度应力裂缝,这种裂缝一般稍大;4)、墙体材料选用的多孔砖及加气砼砌块干燥后的收缩比例较大,如砂浆强度不足或灰缝不饱满时容易出现干缩裂缝,这种裂缝一般较为细小;5)、钢板网铺设不到位、铺设过少,主要体现在钢板网紧贴墙体未留出适当间距,墙面剔凿、临时施工洞口等部位为加设钢丝网;6)甩浆用的砂浆强度不足,未进行养护,甩完浆后未达到一定强度就开始进行抹灰,致使抹灰层和墙体粘结强度不足。
7)、现场技术人员技术交底及管理检查不到位;2、防治措施:1)、选择有实力、正规的成品砂浆供应商和施工队伍,以保证材料质量和施工质量;由设计单位明确砂浆强度及品种要求。
2)、抹灰前对基层进行统一清理,除去附着在墙体表面上的砂浆、灰尘等杂物,验收合格后方可进行后续施工。
3)、为增加基层对抹灰层的粘结性,在抹灰前宜对于基层采取机械喷浆处理。
浆料采用1:1水泥砂浆加水泥重量20%的801胶,经养护至少三天后再进行墙体抹灰。
如采用人工甩浆,必须采用强度较高的砂浆,甩浆完成后必须进行养护,待达到一定强度时在进行抹灰施工。
4)、加强对填充墙砌体施工的质量控制,严格控制灰缝的饱满度及后塞部位的施工。
抹灰前应采用1:3水泥砂浆将砌块开裂(先剔槽)、凹凸不平部位抹平,并对光滑的混凝土表面进行凿毛处理。
5)、加强钢丝网的使用,钢丝网的合理使用是解决墙体裂缝的最主要手段之一,同时加强钢丝网材料验收,确保采用热镀锌钢丝网片,网孔尺寸小于20mmx20mm,其钢丝直径为1.2mm为宜,钢丝网挂网应平整、牢固,固定时必须每隔200-300mm加铁片进行固定,钢丝网片及基体搭接宽度不小于100mm。
电渣压力焊施工方法及要求试卷教案
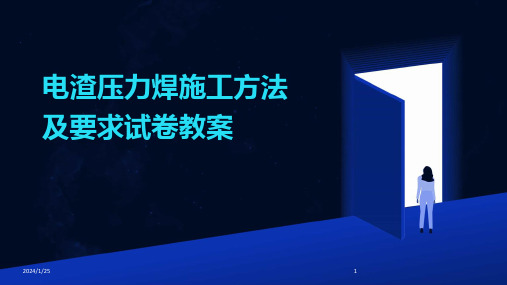
04
质量检查与验收标准
2024/1/25
17
外观质量检查
01
02
03
04
焊缝成形良好,表面应平滑, 无裂纹、夹渣、未熔合等缺陷
。
焊渣和飞溅物应清除干净,不 得有残留。
焊缝余高应符合设计要求,且 不应大于3mm。
接头处应无明显变形,轴线偏 移不得超过规定值。
2024/1/25
18
内部质量检查
28
THANKS
感谢观看
2024/1/25
29
12
03
施工工艺流程及操作要点
2024/1/25
13
工艺流程概述
钢筋加工
按照设计要求对钢筋进行加工 ,包括切割、弯曲等。
焊接操作
启动电渣压力焊机进行焊接, 控制焊接参数,确保焊接质量 。
施工准备
包括材料、设备、人员等准备 ,确保施工顺利进行。
2024/1/25
安装焊接夹具和钢筋
将焊接夹具安装在待焊接的钢 筋上,确保钢筋位置准确。
不足之处与改进方向
虽然取得了一定的学习成果,但我也意识到自己在学习方 法、时间管理等方面还存在不足。未来,我将继续加强自 主学习和实践能力,提高学习效率和质量。
27
未来发展趋势预测
2024/1/25
技术创新与应用拓展
随着科技的不断进步,电渣压力焊技术将不断创新和完善,应用领域也将进一步拓展。例 如,采用智能化、自动化等先进技术提高焊接效率和质量;开发新型焊接材料和工艺,满 足更多特殊材料和复杂结构的焊接需求。
2024/1/25
钢筋加工时,应按照设计要求的长度和 角度进行切割和弯曲,确保钢筋尺寸准 确。
安装焊接夹具时,应确保夹具与钢筋紧 密贴合,防止焊接过程中产生位移。
常见焊接缺陷的产生原因和防止措施

1.启动焊机前,检查焊把,禁止与工件短路,遵守安全规程;
2.包裹绝缘带;
3.在坡口内引弧,加强规程教育,严肃工艺纪律
飞溅
1.焊接电流过大;
2.未采取防护措施;
3.CO2气体保护焊焊接回路电感量不合适
1.选用合适的规范参数;
2.采用涂白垩粉等措施;
3.调整CO2气体保护焊焊接回路的电感
2.选择合理的焊接规范和工艺措施,如焊前预热、控制层间温度、焊后缓冷、进行焊后热处理等。避免产生淬硬组织;
3.采取降低焊接应力的工艺措施
再热裂纹
1.过饱和固溶的碳化物在再次加热时析出,造成晶内强化;
2.焊接残余应力
1.减少焊接应力和应力集中程度,如焊前预热、焊后缓冷等以及使焊缝与母材平滑过渡;
2.在满足性能要求的前提下,选用强度等级稍低于母材的焊接材料;
4.操作不熟练;
5.坡口设计不合理,焊层形状不良
1.彻底清理层间焊道;
2.选用合理的焊接规范;
3.提高操作技术;
4.合理选用坡口,改善焊层成形
金属夹杂
1.氩弧焊采用接触引弧,操作不熟练;
2.钨极与熔池或焊丝短路;
3.焊接电流过大,钨棒严重烧损
1.氩弧焊时尽量采用高频引弧;
2.熟练操作技术;
3.选用合适的焊接规范
6.气焊火焰调整不合适、焊炬摆动幅度大,焊丝搅拌熔池不充分,对熔池保护差;
7.操作不熟练;
8.焊接环境湿度大
1.不使用药皮剥落、开裂、变质、偏心和焊芯锈蚀的焊条。焊条和焊剂按规程要求烘烤;
2.按规程要求做好焊前清理工作;
3.选用合适的焊接规范,控制焊接电流和电弧长度;
钢筋电渣压力焊质量缺陷原因分析及防治措施

钢筋电渣压力焊质量缺陷原因分析及防治措施根据电渣压力焊在竖向钢筋焊接中的应用实践,总结钢筋电渣压力焊缺陷的表现形式,从原材料、焊接参数、焊接设备以及操作工艺方面分析焊接缺陷成因,并根据焊接缺陷产生的原因及焊接质量的影响因素,在工程项目中采取全过程的质量管理措施,取得了较好的成果,有效减少钢筋电渣压力焊中焊接缺陷的产生。
标签:电渣压力焊;焊接缺陷;缺陷成因;全过程的质量管理1 概述电渣压力焊是利用焊接电流通过两根钢筋端面间隙,在焊剂层下形成电弧过程和电渣过程,产生电弧热和电阻热,从而熔化钢筋,加工完成的一种压焊方法。
这种焊接方法比电弧焊节省钢材、工效高、成本低,适用于现浇钢筋混凝土结构中竖向或斜向钢筋连接。
该方法操作方便,有良好的技术经济效果,因而在国内得到广泛的使用。
但是,在此类工程的施工过程中发现,该工艺看似简单,而在施工中很容易出现各种质量缺陷。
如果到验收阶段才发现质量缺陷,处理将相当麻烦,不仅费工、费料,有些情况甚至无法处理,十分棘手。
为了防范于未然,把电渣压力焊质量缺陷控制在最低限度,我们结合现场施工工作实践,总结出产生电渣压力焊质量缺陷的三类原因,从“主动控制为主、被动控制为辅”的原则出发,针对缺陷产生的原因,对症下药,总结出防治焊接质量缺陷的措施。
2 缺陷的表现形式常见缺陷归纳为三类:(1)钢筋焊接后,上钢筋位置不符合要求。
如上钢筋轴线偏移或弯折,超出规范允许偏差范围。
(2)焊接后钢筋受到损伤,如钢筋表面烧伤,端口咬边等。
(3)焊包不符合要求,这一类缺陷最常见,表现为焊包不匀、夹渣、出现气孔、未焊合以及焊包上翻或下淌。
3 产生缺陷的原因分析影响焊接质量的因素很多,根据多年的实践总结,导致产生焊接缺陷的原因主要有三方面:原材料本身、焊接参数选用、焊接设备以及操作工艺方面。
3.1 原材料本身的因素(1)进行电渣压力焊的钢筋不平直。
热轧钢筋由于生产或其它方面的原因,有的钢筋端部出现弯扭不直,端口切面与钢筋长方向不垂直。
浅谈钢筋电渣压力焊接头一次合格率
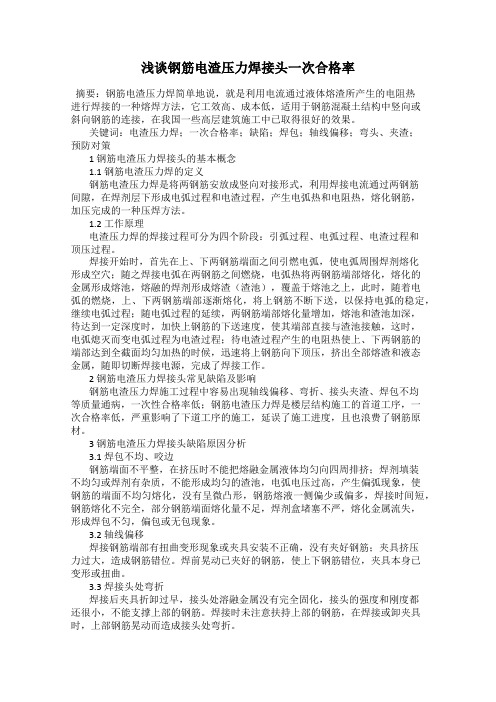
浅谈钢筋电渣压力焊接头一次合格率摘要:钢筋电渣压力焊简单地说,就是利用电流通过液体熔渣所产生的电阻热进行焊接的一种熔焊方法,它工效高、成本低,适用于钢筋混凝土结构中竖向或斜向钢筋的连接,在我国一些高层建筑施工中已取得很好的效果。
关键词:电渣压力焊;一次合格率;缺陷;焊包;轴线偏移;弯头、夹渣;预防对策1 钢筋电渣压力焊接头的基本概念1.1 钢筋电渣压力焊的定义钢筋电渣压力焊是将两钢筋安放成竖向对接形式,利用焊接电流通过两钢筋间隙,在焊剂层下形成电弧过程和电渣过程,产生电弧热和电阻热,熔化钢筋,加压完成的一种压焊方法。
1.2 工作原理电渣压力焊的焊接过程可分为四个阶段:引弧过程、电弧过程、电渣过程和顶压过程。
焊接开始时,首先在上、下两钢筋端面之间引燃电弧,使电弧周围焊剂熔化形成空穴;随之焊接电弧在两钢筋之间燃烧,电弧热将两钢筋端部熔化,熔化的金属形成熔池,熔融的焊剂形成熔渣(渣池),覆盖于熔池之上,此时,随着电弧的燃烧,上、下两钢筋端部逐渐熔化,将上钢筋不断下送,以保持电弧的稳定,继续电弧过程;随电弧过程的延续,两钢筋端部熔化量增加,熔池和渣池加深,待达到一定深度时,加快上钢筋的下送速度,使其端部直接与渣池接触,这时,电弧熄灭而变电弧过程为电渣过程;待电渣过程产生的电阻热使上、下两钢筋的端部达到全截面均匀加热的时候,迅速将上钢筋向下顶压,挤出全部熔渣和液态金属,随即切断焊接电源,完成了焊接工作。
2 钢筋电渣压力焊接头常见缺陷及影响钢筋电渣压力焊施工过程中容易出现轴线偏移、弯折、接头夹渣、焊包不均等质量通病,一次性合格率低;钢筋电渣压力焊是楼层结构施工的首道工序,一次合格率低,严重影响了下道工序的施工,延误了施工进度,且也浪费了钢筋原材。
3 钢筋电渣压力焊接头缺陷原因分析3.1 焊包不均、咬边钢筋端面不平整,在挤压时不能把熔融金属液体均匀向四周排挤;焊剂填装不均匀或焊剂有杂质,不能形成均匀的渣池,电弧电压过高,产生偏弧现象,使钢筋的端面不均匀熔化,没有呈微凸形,钢筋熔液一侧偏少或偏多,焊接时间短,钢筋熔化不完全,部分钢筋端面熔化量不足,焊剂盒堵塞不严,熔化金属流失,形成焊包不匀,偏包或无包现象。
非熔嘴式电渣焊焊缝质量影响因素的分析及解决方法

的温度 ,使 熔 宽 减 小 。⑤ 送 丝 速 度 增 加 ,渣 池 的 上
升过 快 ,渣 池 与 边 缘 接 触 时 间 短 ,热 量 减 小 ,使 熔 宽减 小 。⑥ 非 熔 嘴 的提 升 速 度 ( 接 速度 ) 快 ,也 焊 造成热 量不 足 而 使 熔 宽 减小 。⑦ 热 量 分 布 不 均 匀 的 原 因主要 是操 作 不 当 ,焊 枪 位 置 偏 离 ,焊 丝 不 在 焊 道 中心所 致 。焊枪 偏 离 不 仅 使 热 量 分 布不 均 还 可 能
m
R
彻
( )漏焊 现象 2 所谓 漏 焊 就 是在 焊缝 中有 一 处
或几处 焊道 无熔 敷金属 ,高 度 4 5 m 0— 5 m,造成 这 种 缺 陷的 主要 原 因是 非 熔 嘴焊 过 程 中焊 接 中 断 又重 新 引 弧造渣 所 致 。引 起 焊 接 中 断 的 原 因有 以 下 几 点 :
在 电极 与 渣 池 之 间 或 电极 与 渣 池 壁 之 间 产 生 电 弧 ,
漏铁水会破坏焊接的稳定性,产生未熔合 、未焊透、
气 孑 和夹杂 等 缺 陷 ,甚 至 造成 焊 接 中断 。产 生原 冈 L 主要有 两个 方 面 :①挡 板 与 隔板 、挡 板 与翼 缘 板 未 贴 紧等 装 配误 差 造 成 间 隙过 大 ,常 见 的装 配缺 陷如 图 6所示 。② 引弧 块 与 焊 口处 ( 缘 板 、腹 板 )贴 翼 合不 紧实 。
舡
覃误 差 差 帚
() a () b () c
() d
造成 焊枪 与 工件 短 路 而 损 坏 焊 枪 。另 外 ,工 件 摆 放
位置使 焊 道 未处 于垂 直 状 态 ,也 是 焊枪 位 置 偏 离 的
- 1、下载文档前请自行甄别文档内容的完整性,平台不提供额外的编辑、内容补充、找答案等附加服务。
- 2、"仅部分预览"的文档,不可在线预览部分如存在完整性等问题,可反馈申请退款(可完整预览的文档不适用该条件!)。
- 3、如文档侵犯您的权益,请联系客服反馈,我们会尽快为您处理(人工客服工作时间:9:00-18:30)。
电渣焊常见缺陷产生原因分析及防止方法
一. 概述
电渣焊是一种以电流通过液体溶渣所产生的电阻热作为热源的熔化焊接方法。
对于中厚板的焊接可以不开坡口而一次焊成,所以焊接生产效率比较高;同时也可以用于一些构件用常规焊接方法无法完成的焊接;例如箱形柱的隔板于翼板的焊接。
我公司为某工程制作的箱形柱,其隔板与两侧腹板采用气保焊焊后,再与上下翼板相焊。
由于隔板与两侧的间距较小,隔板的开孔也较小,焊工无法进入施焊,而且该焊缝需要焊透;质量要求较高;焊后须经超声波探伤达到Ⅱ级要求,所以只有采用电渣焊来解决。
二. 基本条件
1. 箱形柱的结构形式见图一
图一
2. 母材型号及规格
型号:Q345B 翼板厚40mm 。
隔板和腹板厚36mm
3. 焊接设备
⑴焊接电源:采用松下产平特性的KH Ⅱ600
⑵送丝机:松下产单驱动送丝机
⑶冷却水箱:型号YX-09KGC1HGE 松下产
⑷控制箱、焊枪、焊枪提升机构、焊枪摆动机构:杭州欣诚祥机电技术
有限公司制造。
控制箱为双极非熔咀式电渣焊控制箱。
⑸焊接操作机架为自制。
三.焊接规范
由于焊接工件的厚度比较小,故而采用单丝丝极电渣焊比较合适。
因为丝极电渣焊设备较简单、操作容易、成本较低,适合于中小厚度工件的焊接,而且焊枪不用摆动即能满足要求。
1.焊接接头装配形式见图二
图二
2.焊接材料的选用:
⑴焊丝选用强度与母材匹配的型号为ER50-6规格为ф1.6。
⑵焊剂的选用:
焊剂的选用原则:
a).造渣容易,电渣过程稳定;
b).稳弧性能较低,当熔化成渣后,具有较合适的粘度和导电度,使电弧
放电现象不致发生,才能有效避免电渣过程产生电渣-电弧夹杂过程,否则会破坏电渣焊的正常进行,甚至可使焊接中断,产生未焊透夹渣等缺陷。
基于上述原则国产焊剂可采用HJ431粒度为40-60目,进口焊剂有日铁产YF15Ⅰ。
这是一种电渣焊专用焊剂,其性能比HJ431优越。
所以电渣焊焊剂选用日铁YF15Ⅰ。
3.焊接规范
焊接规范的正确与否直接影响电渣过程的稳定性和焊接质量。
我们一开始采用的焊接规范是第一号工艺方案。
见表一:
表一.焊接规范
焊接时为减小焊接变形,应用二把焊枪左右焊缝同工艺同时焊接。
焊后经超声波探伤,发现存在以下几种焊接缺陷:
1)母材与焊道局部未熔合。
2)间断性漏焊。
3)漏渣漏铁水。
4)焊缝引弧起头端不合乎质量标准规定。
四.焊接缺陷产生的原因分析及解决方法
针对以上产生的焊接缺陷,下面分别对其产生的原因进行分析并提出防止措施。
1.未熔合
(1)产生的原因:
对于未熔合缺陷,产生的因素较多,主要有以下几个方面:
a)热量不足或热量分布不均匀。
造成热量不足有以下几个方面的原因:
1)接电流较小会造成热量不足。
随着电流的不断增加,热量也不断增加,熔宽也增加;但电流大到一定数值后,加速了焊丝的熔化速度,使熔池上升速度加快,焊枪提升速度也加快,焊件所得到的线能量减少,使焊缝的熔宽反而会减小。
2)焊接电压偏低也会造成热量不足,熔宽减小。
随着电压的升高,焊缝的熔宽也增加,但电压过高会使渣池过热而沸腾,甚至在电极与渣池之间或电极与渣池壁之间产生电弧,影响焊接过程的稳定。
3)装配隙过小也会造成热量不足,因为装配间隙小,渣池上升速度快使线能量输入减小。
4)渣池深度增加,电极予热部分加长,熔化速度增加,同时还由于电流的分流增加,降低了渣池的温度,使熔宽减小。
5)送丝速度增加,会使渣池上升过快,渣池边缘的受热量减小,使熔宽减小。
6)焊枪的提升速度(焊接速度)快,也造成热量不足而使熔宽减小。
7)造成热量分布不均的原因主要是操作不当,焊丝未处于焊逢间隙的中心位置所致。
焊枪位置偏不仅热量分布不均,严重时还造成焊枪与工件短路而损坏焊枪。
另外放置工件的支架未处于水平状态而使焊道未处于垂直位置也会造成焊枪位置的偏离。
b)送丝不稳,网路电压波动大
设备不良,导电咀质量不好,网路电压波动大都会造成送丝不稳,从而影响焊接的稳定使熔宽发生变化。
c)电渣过程不稳定,经常发生短路,从而使电渣过程变成引弧—电渣夹杂过程。
这主要是由于焊接规范不合适,焊剂导电性过好造成的,由于采用的是日产铁YF15I焊剂,质量较好,焊剂的因素可排除。
2)防止措施
造成未融合的因素虽然很多,但经过对焊接过程的观察及对焊缝剖面的检验、分析认为热量不足和热量不均匀是主要原因,具体解决方法如下:
a)焊接电流不变,适当的提高焊接电压2-4V即46-48V
b)适当地减小送丝速度,由原来的216m/h减小到160m/h
c)适当减小焊枪提升速度(即焊接速度),由原来的1.5m/h减小到
1.0m/h。
d)将工件支架用水平仪调平,焊工在操作时随时观察焊枪的位置是
否在中心位置,否则随时调整,调整时要平稳,并注意不要用手
扳动焊枪。
2.间隔性漏焊
所谓间隔性漏焊就是在整条焊缝中有一处或几处焊道无熔敷金属,长度在40-50mm左右,造成这种缺陷的主要原因是电渣焊过程中焊接中断又重新引弧造渣焊接所致,造成焊接中断的原因主要有与如下几方面:
1)导电咀磨损后间隙过大使导电不良。
2)由于焊渣沸腾飞溅将导电咀堵住,使送丝不畅。
防止措施:
1)不要使用磨损大的导电咀,为此要求一个新导电咀最多焊2-3条焊缝即换新导电咀,旧的可用于CO2焊。
2)过高的焊接电压会使渣池过热甚至沸腾,同时渣池深度太小也使电渣过程不稳定,所以焊接操作时应随时观察电压的变化,若有变化应随
时调整并注意适量填加焊剂。
3)若产生了中间焊接中断,若不是属于设备故障或网路停电而是属于上述二方面原因,补救的方法是迅速将焊枪提起,以最快的动作更换导电咀或清除堵塞物,在渣池未凝固之前将焊枪放下,直到焊丝端头接触到焊缝金属,然后降低焊接电压(约40-42V)和送丝速度(约120m/h),引弧焊接使焊接平稳后,再将电压调至焊接电压,送丝速度也恢复到原焊接送丝速度。
3.漏渣漏铁水
在焊接过程中若漏渣漏铁水会破坏焊接的稳定性,产生未熔合、未焊透、气孔、夹杂等缺陷,甚至造成焊接的失败,引起漏渣和漏铁水主要有以下二方面原因:
1)护板与隔板、护板与翼板组装时未贴紧,间隙过大。
2)引弧槽与腹板和翼板贴合不良。
防止方法:
1)将护板与翼板贴合的端面用铣床或刨床加工平整,并要保证组装质量。
护板与隔板,护板与翼板之间要贴紧,其间隙不得大于1mm。
2)为使引弧槽与腹板和翼板贴紧,可采用耐火泥或耐火棉在引弧槽密封面围绕一圈再贴紧在焊缝的下端,并用千斤顶顶紧。
4.引弧起头端不合乎质量标准规定
引弧起头端不合乎质量规定的原因主要是因为引弧造渣不稳定而造成的。
因此保证引弧造渣建立渣池的稳定是解决这一问题的关键。
由于焊剂在固态时一般不导电,必须通过电弧过程来建立渣池。
为便于引弧,可在引弧槽内先放一些铁屑或铁豆,再洒上约15mm厚的焊剂,
然后通电送丝引弧。
在造渣引弧时,应将焊接电压降低至40-43V,送丝速度降低至120m/h左右,电弧引燃后应陆续加入焊剂。
当渣池达到一定深度时再恢复到原来的焊接电压和送丝速度,使电弧过程转化为电渣过程。
如果在引弧造渣时不降低电压,而是直接用较高的焊接电压,由于这一电压较高,电弧很难建立,在引弧时我们听到的连续的叭叭声就是因为这样产生的。
引弧造渣过程不稳定也是这样造成的。
五.结语
通过对电渣焊所产生的焊接缺陷及存在的问题产生的原因分析,结合实践经验,提出了有效的解决措施,调整了焊接规范(见表一中第2号工艺方案),按表一中2号方案焊接后,经超声波无损检测,合格率达到98%以上,焊缝质量满足要求。
通过理论与实践经验相结合的分析与处理,为保证焊接质量,电渣焊一定注意以下事项:
1.提出解决措施和调整焊接规范不能盲目进行,必须有的放矢地在合
理范围内调整才会取得预期的效果。
2.焊工操作的熟练程度和责任心对焊接的成功与否有很大的关系,评
定电渣焊焊工操作技术熟练程度的一般标准是:
1)一道焊缝不间断由下向上一次焊完。
2)保持整条焊缝熔宽均匀一致。
3)引弧起头端是否能保证质量规定。
为此要求焊工:
1)必须树立高尚的职业道德观念和敬业精神,任何情况下都能尽最大努力去完成工作。
2)应在任何环境和条件下,坚持质量第一,按质量标准施焊。
3)必须学会熟练调整设备,调节焊接规范参数并判断其效果。
3.一定要保证组装质量,包括坡口内的去油、水、锈、氧化皮等是否
彻底,护板的贴合是否紧密以及焊接坡口的间隙尺寸都要严格遵守工艺的要求和规定。
2007.8.8。