高炉炼铁新技术(1)
烧结及高炉炼铁基本原理及工艺

降低了煤气还原能力,影响还原速度.
CaCO3在低温区分解放出CO2进入煤气,降低了CO的 浓度,冲淡了还原气氛
在高温区分解出的CO2与焦炭发生反应, CO2+C焦=2CO 是吸热反应,而且直接消耗焦 炭,使焦比升高.
13
二、高炉还原过程
高炉冶炼用CO,H2和固体碳作还原剂. 氧化物的还原顺序: 高炉冶炼条件下,各种氧化物由易到难的还原 顺序. CuO→PbO→FeO→MnO→SiO2 →Al2O3→MgO→CaO
三元碱度:R3=(CaO+MgO)/SiO2,一般为1.3左 右
-Q -Q -Q -Q -Q
2.碳水反应的影响:
当温度大于1000℃时:
H2O汽 + C = H2 + CO
-Q
用H2还原铁氧化物在高温区时:
FeO+H2 = Fe+H2O
+ H2O+C = H2+CO
FeO+C = Fe+CO
在低温区时,用H2还原铁氧化物的产物与CO作用
FeO+H2 = Fe+H2O + H2O+CO = H2+CO2
0 400 500 600 700 800 900 1000 1200 0C
度随温度升高而降低,即温度升高,
CO的利用率提高,是吸热反应,
2.温度对反应的影响: 曲线3是FeO+CO=Fe+CO2的平衡 气相成分线,向上倾斜,与曲线2 正好相反,是放热反应,升温对反
应不利.
曲线4是Fe3O4+4CO=Fe+4CO2的 平衡气相成分线,向上倾斜,它在
%CO
Fe
高炉炼铁生产工艺流程简介(一)

高炉炼铁生产工艺流程简介(一)高炉冶炼目的:将矿石中的铁元素提取出来,生产出来的主要产品为铁水。
付产品有:水渣、矿渣棉和高炉煤气等。
高炉:炼铁一般是在高炉里连续进行的。
高炉又叫鼓风炉,这是因为要把热空气吹入炉中使原料不断加热而得名的。
这些原料是铁矿石、石灰石及焦炭。
因为碳比铁的性质活泼,所以它能从铁矿石中把氧夺走,而把金属铁留下。
高炉的主要组成部分高炉炉壳:现代化高炉广泛使用焊接的钢板炉壳,只有极少数最小的土高炉才用钢箍加固的砖壳。
炉壳的作用是固定冷却设备,保证高炉砌体牢固,密封炉体,有的还承受炉顶载荷。
炉壳除承受巨大的重力外,还要承受热应力和部的煤气压力,有时要抵抗崩料、坐料甚至可能发生的煤气爆炸的突然冲击,因此要有足够的强度。
炉壳外形尺寸应与高炉型、炉体各部厚度、冷却设备结构形式相适应。
炉喉:高炉本体的最上部分,呈圆筒形。
炉喉既是炉料的加入口,也是煤气的导出口。
它对炉料和煤气的上部分布起控制和调节作用。
炉喉直径应和炉缸直径、炉腰直径及大钟直径比例适当。
炉喉高度要允许装一批以上的料,以能起到控制炉料和煤气流分布为限。
炉身:高炉铁矿石间接还原的主要区域,呈圆锥台简称圆台形,由上向下逐渐扩大,用以使炉料在遇热发生体积膨胀后不致形成料拱,并减小炉料下降阻找力。
炉身角的大小对炉料下降和煤气流分布有很大影响。
炉腰:高炉直径最大的部位。
它使炉身和炉腹得以合理过渡。
由于在炉腰部位有炉渣形成,并且粘稠的初成渣会使炉料透气性恶化,为减小煤气流的阻力,在渣量大时可适当扩大炉腰直径,但仍要使它和其他部位尺寸保持合适的比例关系,比值以取上限为宜。
炉腰高度对高炉冶炼过程影响不很显著,一般只在很小围变动。
炉腹:高炉熔化和造渣的主要区段,呈倒锥台形。
为适应炉料熔化后体积收缩的特点,其直径自上而下逐渐缩小,形成一定的炉腹角。
炉腹的存在,使燃烧带处于合适位置,有利于气流均匀分布。
炉腹高度随高炉容积大小而定,但不能过高或过低,一般为3.0~3.6m。
高炉炼铁工艺的演变与创新从传统到现代

高炉炼铁工艺的演变与创新从传统到现代随着科学技术的不断发展,高炉炼铁工艺也经历了漫长的历史发展。
从传统到现代,高炉炼铁工艺在不断演变与创新,以适应和满足时代的需求。
本文将从多个方面探讨高炉炼铁工艺的发展历程,并分析其演变和创新对于铁工业的影响。
一、传统高炉炼铁工艺的特点及问题传统高炉炼铁工艺是指早期的高炉炼铁方法,其特点是炉容相对较小,燃料多为木炭或焦炭,矿石和燃料由上部装料口输入,铁水由炉底出口排出。
传统高炉炼铁工艺在一定程度上满足了当时的铁产量需求,但也存在一些问题:1. 低炉容限制了生产能力:由于传统高炉容积较小,无法进行大规模的生产,限制了铁产量的增长。
2. 能源利用效率低:燃料多为木炭或焦炭,其燃烧效率较低,导致能源浪费。
3. 铁矿石利用率较低:传统高炉炼铁工艺无法充分利用矿石中的铁资源,大量铁含量较低的矿石无法被利用。
二、现代高炉炼铁工艺的创新与改进为了提高铁产量、能源利用效率和矿石利用率,现代高炉炼铁工艺进行了一系列的创新与改进。
1. 高炉容积的增大:现代高炉的炉容相对较大,能够进行大规模的生产,提高了铁产量。
2. 燃料的改进:现代高炉炼铁工艺多采用煤炭作为主要燃料,相比木炭或焦炭,煤炭的燃烧效率更高,能源利用效率得到提升。
3. 热交换技术的应用:现代高炉工艺中引入了热交换技术,将高温废气中的热能回收,用于预热进料和蒸汽发电,提高了能源利用效率。
4. 炉渣处理技术的改进:现代高炉炼铁工艺采用了先进的炉渣处理技术,通过加入矿粉、炼钢炉渣等辅助剂,可以调整炉渣的性质,提高铁矿石利用率。
5. 连续铸造技术的应用:现代高炉炼铁工艺中广泛使用了连续铸造技术,将熔融的铁水直接注入连续铸造机,实现了自动连续生产,提高了生产效率。
三、高炉炼铁工艺演变与创新的影响高炉炼铁工艺的演变与创新对铁工业产生了深远的影响。
1. 提高产量和效益:现代高炉的产能大大提高,生产效率显著提升,使得铁工业能够满足不断增长的市场需求。
高炉炼铁工艺技术标准最新

高炉炼铁工艺技术标准最新高炉炼铁工艺技术标准最新700字高炉炼铁工艺技术标准是指在高炉炼铁过程中所涉及到的各种操作和参数的标准。
这些标准的制定对于确保高炉正常运行、提高炼铁效率、降低能耗和保护环境具有重要意义。
下面将介绍高炉炼铁工艺技术标准的最新内容。
1. 原料配比标准:高炉炼铁的原料主要包括铁矿石、焦煤和石灰石。
原料的配比直接影响到炼铁的效果和产品质量。
根据不同的铁矿石和焦煤的性质,制定合理的配比标准,确保高炉内的还原和熔化反应能够顺利进行,同时减少生产成本。
2. 炉渣成分标准:高炉炼铁产生的炉渣是含有高炉灰渣、熔渣和炉渣球等物质的复杂体系,其成分对炼铁过程和产品质量有着重要影响。
制定炉渣成分标准,旨在控制炉渣中各种氧化物和杂质的含量,使炉渣具有良好的流动性、透气性和脱硫脱磷能力。
3. 炉渣脱硫脱磷标准:高炉炼铁过程中,炉渣中的主要成分之一是含有硫和磷的物质。
高炉炼铁工艺技术标准要求对炉渣进行适当的脱硫和脱磷处理,以降低钢铁中的硫和磷含量,提高产品的质量。
4. 炉温和气氛控制标准:高炉炼铁过程中,炉温和气氛对炼铁过程和产品质量起着决定性的作用。
工艺技术标准要求对炉温和气氛进行实时监测和控制,以确保高炉内的化学反应能够充分进行,并减少不良反应和产生有害气体。
5. 炉压和风速控制标准:高炉炼铁过程中,炉压和风速对炼铁效果和能耗有着直接的影响。
制定合理的炉压和风速控制标准,可以保证高炉的正常运行,提高炼铁效率,降低能耗。
6. 冷却水质量标准:高炉炼铁过程中,冷却水用于冷却高炉的各种设备和管道,其质量对设备的寿命和运行稳定性有着重要影响。
制定冷却水质量标准,对冷却水进行定期检测和处理,可以防止设备的腐蚀和水垢的产生,延长设备的使用寿命。
7. 炉外环境保护标准:高炉炼铁过程中,会产生大量的炉渣、烟尘、废水和废气等污染物。
工艺技术标准要求在高炉炼铁过程中采取有效的控制措施,减少污染物的排放,保护环境。
以上是高炉炼铁工艺技术标准的最新内容。
高炉炼铁简介

高炉炼铁简介高炉炉前出铁高炉生产时从炉顶装入铁矿石、焦炭、造渣用熔剂(石灰石),从位于炉子下部沿炉周的风口吹入经预热的空气。
在高温下焦炭(有的高炉也喷吹煤粉、重油、天然气等辅助燃料)中的碳同鼓入空气中的氧燃烧生成的一氧化碳和氢气,在炉内上升过程中除去铁矿石中的氧,从而还原得到铁。
炼出的铁水从铁口放出。
铁矿石中不还原的杂质和石灰石等熔剂结合生成炉渣,从渣口排出。
产生的煤气从炉顶导出,经除尘后,作为热风炉、加热炉、焦炉、锅炉等的燃料。
简史和近况早期高炉使用木炭或煤作燃料,18世纪改用焦炭,19世纪中叶改冷风为热风(见冶金史)。
20世纪初高炉使用煤气内燃机式和蒸汽涡轮式鼓风机后,高炉炼铁得到迅速发展。
20世纪初美国的大型高炉日产生铁量达450吨,焦比1000公斤/吨生铁左右。
70年代初,日本建成4197立方米高炉,日产生铁超过1万吨,燃料比低于500公斤/吨生铁。
中国在清朝末年开始发展现代钢铁工业。
1890年开始筹建汉阳铁厂,1号高炉(248米,日产铁100吨)于1894年5月投产。
1908年组成包括大冶铁矿和萍乡煤矿的汉冶萍公司。
1980年,中国高炉总容积约8万米,其中1000米以上的26座。
1980年全国产铁3802万吨,居世界第四位。
高炉炼铁面临淘汰中国钢铁业急需升级换代高炉炼铁技术,适合于那些工业化初步发展的国家,生产大路货、初级钢材,但在发达国家,高炉技术正面临淘汰。
电炉技术炼钢是当今世界趋势。
电炉炼铁可以提升钢材质量和特殊性能,减少原材料和电力等的浪费。
在订单经济时代,生产要根据市场需求变化,但高炉炼铁技术周期长,生产产品低级,且生产的产品还需要一道甚至更长的加工链条。
电炉炼钢则可缩短钢材冶炼周期,可根据订单安排生产,原材料和动力资源浪费少,不再如高炉炼铁那样存在大量的产品积压情况。
当今社会进入材料时代后,市场需要的钢材不再是传统的材料,高炉炼铁生存空间更大为缩小,且附加值很低,以中国钢铁业为例,全国钢铁产业利润还不如开采铁矿的赚钱,原因就是因为高炉炼铁技术低级落后,不能生产高附加值产品。
高炉最新工艺技术

高炉最新工艺技术高炉作为一种重要的冶金设备,是炼钢工业中最关键的设备之一。
随着科技的不断进步,高炉的工艺技术也在不断创新和改良。
下面就介绍高炉最新工艺技术。
一、焦炭冶炼工艺技术传统的焦炭冶炼工艺存在着煤粉多次输送和喷煤过程简单等问题。
而最新的焦炭冶炼工艺技术则是采用喷气堆砌法烧结炉墙,有效降低了煤粉输送的损耗,同时也节约了大量的煤粉。
此外,新型的喷煤系统不再需要重复的喷煤过程,可以提高生产效率和能源利用率。
二、高炉炼铁工艺技术高炉炼铁主要依靠还原铁矿石中的氧化铁,以得到纯净的铁。
传统的高炉炼铁工艺存在着熟料结构松散、焦比高等问题,不能很好地满足经济效益和环保要求。
而新型的高炉炼铁工艺技术则采用了煤气稳定供给和煤炭预氧化等技术,能够提高还原反应的速度和效率,减少焦比,降低能耗和环境排放。
三、高炉炉渣处理工艺技术炉渣是高炉炼铁过程中产生的一种有害物质,含有大量的炉渣矩阵及矿物质。
传统的高炉炉渣处理工艺主要采用水浸、捞渣等方式,这种方式对环境造成负担较大。
而最新的高炉炉渣处理工艺技术则是采用高温液相还原、强化蓄热和高炉内炼铁过程中的矿渣融化等技术,能够有效降低炉渣的含量和对环境的污染。
四、高炉烟气处理工艺技术高炉烟气中含有大量有害物质,如二氧化硫、氮氧化物等,对环境和人体健康造成严重影响。
传统的高炉烟气处理工艺主要采用湿法脱硫等方式,这种方式存在着脱硫效率低、造价高等问题。
而新型的高炉烟气处理技术则是采用湿式电除尘和SCR脱硝等技术,能够高效去除烟气中的有害物质,减少环境污染。
综上所述,高炉最新工艺技术在焦炭冶炼、炼铁、炉渣处理和烟气处理等方面都取得了重大突破。
这些新技术不仅能够提高高炉的生产效率和能源利用率,还能够减少环境污染,降低能耗。
随着科技的不断进步,相信高炉的工艺技术还会有更多的创新和改良,推动整个炼钢工业的发展。
高炉炼铁工艺
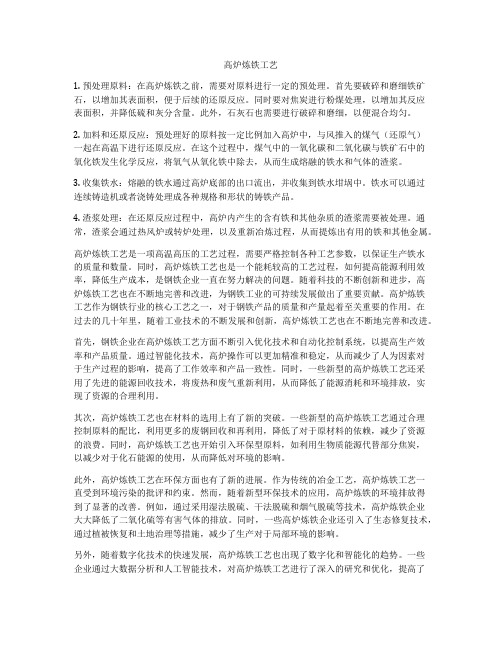
高炉炼铁工艺1. 预处理原料:在高炉炼铁之前,需要对原料进行一定的预处理。
首先要破碎和磨细铁矿石,以增加其表面积,便于后续的还原反应。
同时要对焦炭进行粉煤处理,以增加其反应表面积,并降低硫和灰分含量。
此外,石灰石也需要进行破碎和磨细,以便混合均匀。
2. 加料和还原反应:预处理好的原料按一定比例加入高炉中,与风推入的煤气(还原气)一起在高温下进行还原反应。
在这个过程中,煤气中的一氧化碳和二氧化碳与铁矿石中的氧化铁发生化学反应,将氧气从氧化铁中除去,从而生成熔融的铁水和气体的渣浆。
3. 收集铁水:熔融的铁水通过高炉底部的出口流出,并收集到铁水坩埚中。
铁水可以通过连续铸造机或者浇铸处理成各种规格和形状的铸铁产品。
4. 渣浆处理:在还原反应过程中,高炉内产生的含有铁和其他杂质的渣浆需要被处理。
通常,渣浆会通过热风炉或转炉处理,以及重新冶炼过程,从而提炼出有用的铁和其他金属。
高炉炼铁工艺是一项高温高压的工艺过程,需要严格控制各种工艺参数,以保证生产铁水的质量和数量。
同时,高炉炼铁工艺也是一个能耗较高的工艺过程,如何提高能源利用效率,降低生产成本,是钢铁企业一直在努力解决的问题。
随着科技的不断创新和进步,高炉炼铁工艺也在不断地完善和改进,为钢铁工业的可持续发展做出了重要贡献。
高炉炼铁工艺作为钢铁行业的核心工艺之一,对于钢铁产品的质量和产量起着至关重要的作用。
在过去的几十年里,随着工业技术的不断发展和创新,高炉炼铁工艺也在不断地完善和改进。
首先,钢铁企业在高炉炼铁工艺方面不断引入优化技术和自动化控制系统,以提高生产效率和产品质量。
通过智能化技术,高炉操作可以更加精准和稳定,从而减少了人为因素对于生产过程的影响,提高了工作效率和产品一致性。
同时,一些新型的高炉炼铁工艺还采用了先进的能源回收技术,将废热和废气重新利用,从而降低了能源消耗和环境排放,实现了资源的合理利用。
其次,高炉炼铁工艺也在材料的选用上有了新的突破。
高炉炼铁生产管理创新与技术进步

高炉炼铁生产管理创新与技术进步随着现代工业的发展,高炉炼铁作为铁矿石的重要生产方式,承担着重要的任务。
在高炉炼铁生产中,如何创新管理模式,推进技术进步,提高生产效率和产品质量,已成为行业发展的关键问题。
本文将从管理创新和技术进步两方面来探讨高炉炼铁生产的发展趋势。
一、高炉炼铁生产管理创新1.工艺流程优化在高炉炼铁生产中,工艺流程的优化是提高生产效率的重要途径。
通过对生产过程进行分析,不断优化工艺流程,可以提高炉内矿石的还原性能,增加炉渣的碱度,减少燃料消耗和炉缸内压力等,从而提高炉况的稳定性和生产效率。
2.智能化管理随着信息技术的发展,高炉炼铁生产管理也逐渐向智能化方向发展。
采用先进的传感技术和数据分析算法,可以对高炉炼铁生产过程进行在线监测和控制,实现生产过程的自动化和智能化管理,提高生产效率和产品质量。
3.能源节约与环保在高炉炼铁生产中,能源消耗和环境污染一直是困扰行业发展的问题。
通过引进节能环保技术,如余热回收利用、尾气净化技术等,可以有效减少能源消耗和排放污染物,提高生产的可持续发展能力。
4.人力资源管理高炉炼铁生产需要大量的技术工人和管理人员,如何合理配置人力资源,提高员工的技术水平和管理能力,对于保障生产的稳定进行是至关重要的。
建立健全的人力资源管理制度和培训体系,可以提高员工的工作积极性和生产效率。
二、高炉炼铁生产技术进步1.新型高炉技术随着现代冶金技术的发展,一些新型高炉技术逐渐应用于高炉炼铁生产中,如底吹炼铁技术、蓄热式高炉技术等。
这些新型高炉技术能够提高炉内的矿石还原效率,减少冶金副产物的生成,降低燃料的消耗,从而提高生产效率和产品质量。
2.炉料质量控制高炉炼铁生产过程中,炉料的质量直接影响炉内还原和熔融过程,因此炉料的质量控制是提高生产效率的关键。
采用先进的炉料配料技术和原料分析技术,可以确保炉料的合理配比和质量稳定,提高炼铁生产的稳定性和生产效率。
3.炉渣处理技术炼铁生产中生成的炉渣不仅影响了炉内的正常操作,还对环境造成了污染。
- 1、下载文档前请自行甄别文档内容的完整性,平台不提供额外的编辑、内容补充、找答案等附加服务。
- 2、"仅部分预览"的文档,不可在线预览部分如存在完整性等问题,可反馈申请退款(可完整预览的文档不适用该条件!)。
- 3、如文档侵犯您的权益,请联系客服反馈,我们会尽快为您处理(人工客服工作时间:9:00-18:30)。
4V BG D 2
22.4 PC H 120
44.8W B (V B VO2 ) 18000
4) 采用日历天数和作业率代替规定工作日数。 日历作业率=1-休风率
高炉炉缸断面积利用系数(t/m2· d)
A
高炉平均日产量(p t / d ) 2 d) 炉缸断面积( A m 2 ) (t/m ·
以上两种方法都有一定道理,炉缸断面积表达法更为合理。
4、树立高炉冶炼强化的新观念
陈旧的高炉冶炼强化观为:单位容积高炉多烧焦炭多出铁。 从这种观
念出发形成的高冶炼强化观认为:在焦比一定的条件下,提高冶炼强度就等于提 高利用系数。反之提高利用系数的办法就是提高冶炼强度。可见,用冶炼强度来
1000m3级:2.0~2.4t/m3· d 2000m3级:2.0~2.35t/m3· d 3000m3级高炉:2.0~2.30t/m3· d
高炉容积利用系数:(t/m3· d)
v
高炉平均日产量p t / d ) ( (t/m3· d) 3 高炉容积 V m ) (
高炉容积为铁口中心线平面以上至料线平面以下的容积(m3)
在
2 PB PT2 K 1.7 V BG
获得,炉腹煤气量VBG 却不能直接得到,但VBG对操作和设计高炉都具有重要意 义。
炉腹煤气量VBG与鼓风量、富氧量、喷吹物的数量和成分、湿分等因
素有关。在高炉生产喷吹煤粉的条件下,一般VBG的简便计算式为:
V BG 1.21V B 2VO2 44.8W B (V B VO2 ) 18000 22.4 PC H 120
6、建立合理的高炉生产操作统计指标
1)高炉生产效率统计与国外接轨,采用增加一个炉缸面积利用系数
(t/m2.d),以克服偏面追求高利用系数的倾向。 2) 采用燃料比取消原报表的折算焦比和综合焦比。 燃料比=入炉焦比+小块焦比+喷煤比(Kg/t) 3) 采用炉腹煤气量指数代替冶炼强度: X BG 其中
式中: VB 为不包括富氧的风量 Nm3/min.
为富氧量,Nm3/min; WB 为湿分,g/Nm3; PC 为喷煤粉量,Kg/h; H 为煤粉的含,H量%。
VO 2
其中,大小不同级别高炉的VBG和炉缸面积是不一样的,为了把VBG 用于大小不同级别的高炉,将炉腹煤气量(VBG)除以炉缸面积定义为高
我国高炉炼铁技术新方针、新理论
许满兴 (北京科技大学)
1、前言
跨入21世纪以来,我国钢铁工业步入了快速发展轨道。从2001 ~2011年11年间,我国高炉炼铁年产量由15554万吨增加到62969.3 万吨,以2001年为起点,年均增长36.8%,增速之高创行业世界之 最。同时,我国高炉炼铁在技术操作方针、技术经济指标评价、高 炉冶炼强化理论、合理喷煤比等方面都跨入了世界先进科学理论的 行列,这为我国钢铁工业由世界钢铁大国向世界钢铁强国迈进不断 创造了条件。 本文将张寿荣院士以及著名设计大师项钟庸等炼铁专家近年来 发表的关于高炉技术操作方针和高炉冶炼强化等新观念、新理论进 行了汇集,编写出了本篇文章。
3、科学评价高炉利用系数
利用系数: v
冶炼强度 x ) ( 燃料比 y ) (
实际上冶炼强度与燃料比的关系存在着一个燃料比最低的冶 炼强度区域,这个区域一般在1.05~1.15的范围内 。
图1 高炉冶炼强度与燃料料比升高超过冶炼强度升高时,提高冶炼强度、利用系数反而会 降低; 2) 实践经验证明:低的燃料比才能有高的利用系数; 3) 降低燃料比对提高利用系数的作用和影响远大于提高冶炼强度; 各级高炉利用系数的确定(设计规范)
175
200 225 250 275
7840.3
8301.5 8762.7 9223.9 9697.6
1.98
2.10 2.21 2.33 2.44
1.000
1.059 1.117 1.176 1.236
6272.8
6641.8 7010.8 7379.7 7758.8
表3的数据说明,提高炉顶压力对炉腹煤气量和利用系数的影响 和作用,这用旧的冶炼强度观是无法解释清楚 的。
1
2 3 4 5
2.33
2.38 2.43 2.48 2.52
1.176
1.203 1.229 1.253 1.274
7379.7
7222.4 7067.7 6915.7 6766.3
旧的冶炼强度观是多鼓风、多烧焦炭、多出铁,用新的强化冶炼 观分析则刚好相反,富氧率高了,鼓风小了,冶炼强度高了,提高了 利用系数。
4V BG X BG D 2
式中D为高炉炉缸直径。 影响XBG的因素和XBG的实用价值: 设计大师项钟庸根据宝钢4000m3级高炉作了具体计算(三个表),反
映出富氧率、燃料比和炉顶压力三大因素对XBG的影响,并从中得出高炉
冶炼强化的新观念。
表1 富氧对利用系数和冶炼强度的影响
富氧率 % 0 利用系数 t/m3.d 2.23 冶炼强度 t/m3.d 1.126 入炉风量 Nm3/min. 7402.2
旧的冶炼强度观是多鼓风、多烧焦炭、多出铁,用新的强化冶炼 观分析,入炉风量基本不变(略有下降),燃料比降低,提高了利用系 数。
表3 炉顶压力对利用系数和冶炼强度的影响
炉顶压力 KPa 150 炉腹煤气量 Nm3/min. 7379.1 利用系数 t/m3.d 1.86 冶炼强度 t/m3.d 0.940 入炉风量 Nm3/min. 5903.8
5、合理喷煤比的新理论
喷煤是高炉炼铁节能降耗和降低成本的基本举措,喷煤对高炉炼铁 的价值在于:
1)降低焦比和煤耗,节约焦炭生产的投资和能耗,减缓主焦煤供应 的紧张程度。 2)以煤代焦,降低高炉炼铁生产成本,一般喷煤吨铁效益可超过200 元。 3)喷煤可降低风口前理论燃烧温度相应降低铁水中硅含量,有利于 低硅生铁冶炼,0.1%的硅相当于4-6Kg焦比,能降低吨铁能耗。
4)由于高风温低渣量和炉况稳定顺行是高炉保持喷煤的必要条件, 因此喷煤促进了高风温和精料技术,以及高炉设备和高炉操作技术的提 高和发展。
正因为喷煤具有以上巨大的价值和作用,造成一些企业不顾及风温
和精料水平,不断加大和提高喷煤比,造成过量喷吹即不经济喷吹,导 致炉尘中的含C量甚至超过50%。
那么什么是合理喷煤比呢?衡量合理喷煤比有哪些原则?对每一座 高炉或一座高炉不同炉龄阶段合理的喷煤比是变化的,它可以通过对高 炉操作指标的阶段统计绘制出入炉焦比、燃料比和利用系数的变化曲线 ,从中可以得出最低焦比、最低燃料比、最高利用系数对应的喷煤比, 即为所属高炉的合理喷煤比。因此所谓合理喷煤比,即是最低焦比、最 低燃料比、最高利用系数下的喷煤比。 宝钢前几年喷煤比定在200Kg/t以上,2011年前5个月与2010年相比 由200Kg/t以上降到161Kg/t,追求468Kg/t的低燃料比。合理喷煤比的原 则是:提高喷煤比不增加燃料比,提高喷煤比后煤气除尘灰中含C量不上 升(正常情况下≤20%)
2、高炉炼铁技术操作方针的进步与发展
1) 解放初至1958年大办钢铁期间高炉操作方针:大风(全风量操 作)高温4字方针。 2) 经过大办钢铁后,1959年总结出:“以原料为基础,以风为纲 ,提高冶炼强度与降低焦比并举”的操作方针。 3) 经过60、70年代的实践至80年代,提出了“高产、低耗、优质 的六字方针”。 4) 1980年又总结提出了“高产、低耗、优质、长寿”的八字方针 ,这方针一直延续到21世纪,在此过程中逐步建立了一套科学且附合 实际的评价方法。 5) 2008年在落实科学发展观,实现钢铁工业可持续发展的大背景 下,总结提出了 “高效、低耗、优质、长寿、环保”十字方针。实践 中为了突出低耗和环保,次序又调为“低耗、环保、优质、长寿、高 效”,把追求高产(高利用系数)转变为降低燃料比,从而达到高效的 目的。其中追求“高效”包括高效利用资源、高效利用能源和降低消 耗,把降低燃料比放到追求“高效”之首。
我国高炉炼铁长期以来采用提高“冶炼强度”,追求“利用系数”
为中心的“高炉强化冶炼”方针,误导正确的高炉冶炼理论,阻碍降低 焦比、燃料比、阻碍了节能减排,是一种不正确的高炉冶炼强化理论。
降低燃料比、降低吨铁炉腹煤气量为中心,用炉腹煤气量指
这是新的科学的高炉冶炼强化理论。
数XBG
对高炉合理强化程度进行定量分析,对高炉合理强化进行科学的解释,
炉炉腹煤气量指数(XBG)用作高炉强化的指标,比冶炼强度具有更强的
科学合理性和代表性。
这里有一个最基本的道理:空气中的N2基本不参加化学反应,N2在
空气中占79%,但是N2 被加热消耗大量的能量并带走大量的热量。降低 炉腹煤气量指数,就是改善透气性,降低能耗,因此这是降低能耗,节
能减排强化高炉冶炼的新观念。
表2 燃料比对利用系数和冶炼强度的影响(富氧率为1%)
燃料比 Kg/t 520 510 500 490 480 利用系数 t/m3.d 2.20 2.26 2.31 2.36 2.41 冶炼强度 t/m3.d 1.112 1.140 1.169 1.194 1.220 入炉风量 Nm3/min. 7242.6 7242.0 7241.3 7240.7 7240.1
衡量高炉的强化程度是不正确的。因此,必须建立新的高炉冶炼强化观。
高炉透气性指数:
该式是由描述高炉阻力的Carman方程式简化、变换而来的。宝钢采用K值 判断炉况,高炉长期保持顺行稳定,实现了高炉利用煤气热能和化学能达到降低 燃料比,降低能耗的良好效果。式中 K值计算时,热风压力PB和炉顶压力PT易于