轿车翼子板成形工艺改进及模具设计要点分析
汽车铝合金板件成形工艺及模具结构设计
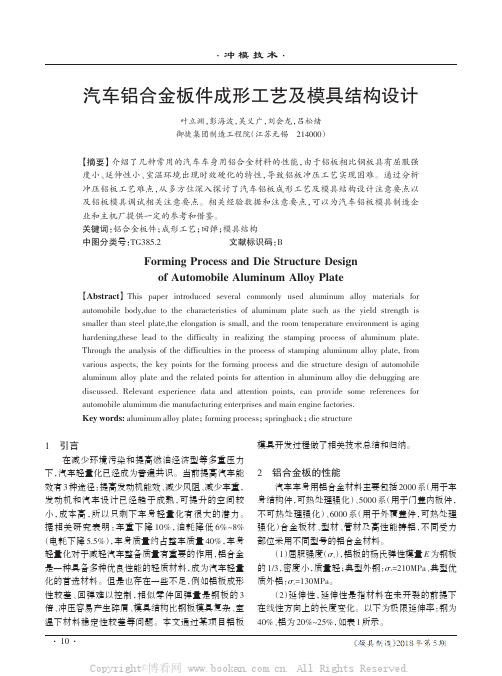
(4)由于铝板密度小,上模容易吸料,冲孔也容易
带料,废料滑出比钢板困难。结构设计时需要注意:
它没有用,铝板自动化生产中,需要在线首设置吹气
①在上模非成形部位加弹顶销,在让空部位及上下模
式分张装置,采用不间断吹气模式,吹气压力至少
周边工艺补充面上加足够多的排气孔,选用顶料型冲
起皱严重致不能压到下死点,解决相关问题后再压
件;成形性调试完成后制件外观应无明显起皱与较大
开裂;④调试完成后,做好相应记录,将调整参数反馈
给相关技术人员。
边间隙(7%~8%)t,铝板修边间隙(5%~7%)t;刀块拼
(4)型面研合:①模具倒装,以成形性调试所得样
缝间隙,钢板模具刀块拼缝间隙+0.04~0.1mm、铝板模
大补偿 5mm
图 1 CAE 数据补偿
图 5 修边碎屑多
图 2 数据补偿后仍回弹
(2)容易开裂:延伸率比钢板小,钢为 40%,铝为
20%~25%,故变形量比钢板小,极易开裂,如图 3、图 4
图 6 翻边有碎屑
《模具制造》2018 年第 5 期
Copyright©博看网 . All Rights Reserved.
系列(6022)的铝合金板材为例:新置材料的屈服强度
为 113.6MPa,存放 3 个月后的屈服强度为 126.5MPa,
所示,成形圆角和拔模角度相比钢板类零件有更高的
要求。
存放 6 个月后的屈服强度为 154.5MPa,如表 2 所示。
如果存放时间超过 6 个月,
将过硬以至于成形困难。
表1
钢板
极限延
加工时方便加垫片;②整形模具设计时要考虑后期整
形镶块后面与底面加垫片的操作可行性。
汽车翼子板成形典型案例分析

汽车翼子板成形典型案例分析
崔奎
【期刊名称】《模具技术》
【年(卷),期】2015(000)003
【摘要】汽车外形更新换代快.为了满足车身翼子板外表面流线化、艺术化和个性化,汽车翼子板造型变化多样,汽车翼子板容易出现制件叠料、开裂、少料和局部强度差等工艺问题,对这些问题的产生原因进行了分析并提出了解决措施,提高了模具设计和制造的效率.
【总页数】4页(P49-52)
【作者】崔奎
【作者单位】奇瑞汽车股份有限公司,安徽芜湖 241000
【正文语种】中文
【中图分类】TG316
【相关文献】
1.翼子板成形工艺问题案例分析及解决方案 [J], 崔奎
2.汽车翼子板多工步拉延成形有限元模拟分析 [J], 陈德茂;陆斌;夏建生;龚启帆;张青;徐伟;朱雅俪;李玉良
3.汽车后翼子板拐角连接件成形工艺优化 [J], 李想; 郭奕文
4.基于正交试验的汽车翼子板拉伸成形仿真研究 [J], 蒋磊;王龙;吕中原;王大鹏;张淳波;沈军奇
5.汽车翼子板三工序冲压工艺方案及成形仿真 [J], 蒋磊;王龙;谢蛟龙;陈一哲;马培兵;刘建
因版权原因,仅展示原文概要,查看原文内容请购买。
关于汽车翼子板结构的研究

关于汽车翼子板结构的研究汽车翼子板是用于改善车辆外观和性能的重要汽车附件,通常被安装在车辆的前后轮拱上。
在汽车运动性能方面,翼子板的主要作用是增加下压力,提高车辆的牵引力和稳定性。
翼子板还可以减小阻力,提高车辆的行驶效率。
翼子板的结构设计对于车辆性能的提升具有重要的影响。
翼子板的主要结构包括翼子板表面、内部构造和安装支架。
翼子板表面通常由塑料、碳纤维或者铝合金等材料制作,表面设计需要考虑气动特性和外观美学。
内部构造包括翼子板内部的支撑结构和通风系统,以及可能的活动机构等。
而翼子板的安装支架则需要根据车辆的结构设计,以保证翼子板与车身的牢固连接。
在翼子板的设计中,气动学是一个非常重要的考虑因素。
翼子板的形状和角度可以影响空气流动,通过增加下压力和减小阻力来提高车辆的运动性能。
一些基本的气动学原理包括卡门喷嘴效应、边界层控制和振动剪切等,这些原理可以用来指导翼子板的结构设计。
翼子板的材料选择也是关键的一步。
不同的材料会影响翼子板的重量、强度和成本,所以需要根据实际需求进行合理的选择。
目前,碳纤维材料在翼子板制作中被广泛应用,因为它具有重量轻、强度高和外观美观的特点,能够很好地满足翼子板的要求。
翼子板的内部结构也需要进行精心设计。
翼子板内部的支撑结构需要考虑材料和结构的强度与重量之间的平衡,以保证翼子板在高速行驶时不会发生变形或者断裂。
通风系统则可以帮助将翼子板下方的高压气体排出,减小阻力,提高车辆速度。
而一些高级的翼子板还可能配备活动机构,可以根据车速和驾驶模式进行调整,以提高性能。
除了翼子板本身的结构设计,其与车身的连接方案也至关重要。
翼子板的安装支架需要与车辆的结构相匹配,以保证翼子板能够稳固地安装在车身上。
支架的设计需要考虑重量和强度,以保证安全可靠。
汽车翼子板的结构设计需要综合考虑气动学、材料力学和车辆工程学的知识。
通过科学的结构设计和材料选择,可以提高翼子板的性能,提升整车的运动性能和安全性。
翼子板精度提升方案浅析

i模具制造技术翼子板精度提升方案浅析田灿腾,刘志强,庞高磊广汽乘用车有限公司(广东广州511434)【摘要】以某一车型翼子板为例,通过分析翼子板在制件设计、模具设计制造、模具调试以 及精度测量方面的关键点并进行了解析,指出了问题所在并给出了解决方案。
对翼子板单品精度的提升提供了有效的解决方向和指导意见。
关键词:翼子板;精度提升;模具设计;模具调试中图分类号:T G659;T G385.2文献标识码:BD O I :10.12147/j.c n k i. 1671 -3508.2020.05.018Analysis on the Scheme of Improving the Precision of Fender【Abstract】T a k in g th e fe n d e r o f a c a r a s an ex am p le, th is p a p e r a n a ly z e s th e k ey p o in ts o f th efe n d e r in p ro d u c t d e s ig n, d ie d e s ig n a n d m a n u fa c tu rin g, d ie d e b u g g in g a n d p re c isio nm e a s u re m e n t, p o in ts o u t th e p ro b le m s a n d gives so lu tio n s. T h is p a p e r p ro v id e s an effectiv ed ire c tio n a n d g u id a n c e for im p ro v in g th e p re c isio n of fen d e r.Key words:f e n d e r; a c c u ra c y im p ro v e m e n t; d ie d e s ig n; d ie d e b u g g in g1引言翼子板是汽车覆盖件中制造难度较高的制件之 一。
汽车用翼子板设计规范

汽车用翼子板设计规范1范用本标准规定了汽车用翼子板结构、性能设计要求”本标准适用于本公司SUV、轿车、皮P车型翼子板的设计」2规范性引用文件下列文件对于本文件的应用是必不W少的.凡是注日期的引用文件,仅所注口期的版本适用丁本文件,凡是不注日期的引用文件,其最新版本(包括所有的修改单)适用于本文件.GB 11566-2009乘用车外部凸出物Q/CC 037-2010魔曲面数模设计险收标潴Q/CC SJM5-2013整车可祝间隙、段差、冏角将荻感知设计规范3术语和定义下列术语和定义适用于本标把,翼子板fender与发动机单、前保险杆、车门、侧用相配合,提高车身造型美观度,并为商保险打、轮眉等提供安装点,且能遮挡车轮及对内部零部件进行防护的外板件.3.2翼子板支架Fender bracket为翼子板提供安装位置的支架,3 3强子板加电板fender reinforced plate装配于黑干板与前组合灯配台配位的尖角处,提岛翼子极局部刚度的冬部件,4算子板配合图翼子板与周边军部件配合图圳图I所示“图1 !!子板装限图(以左翌干板为例)5翼子板结构设计5.1强子板定位孔设计翼子板主秘定位孔一般设计在与仰围下边梁、前保险杆配合拉g.依据装配T.艺要求.设置主制定位孔,如图2所示。
图2定位孔布百5.2翼子板安装结构设计5.2.1里子板安装孔布直概述翼子板安鼓孔应考虑装配时调整IT 一般翼子板标准件采用M6拨栓,翼子板安装孔标设置为e 10 mm -011 mm 圈孔,应均匀布宣保证翼子板装配完成后具有足结的刚度“ 5.2 2翼子板上部安装孔弟子板上部与机舱配合位置「高考虑防锈何题预防,保证安装点搭接面电泳充分以便援盘整车防锈也能,可从以下因素考虑!U)材料:为有效防止翼子板生锈问超t选材时翼子板材料优先选用热镀钎板0.7-HC180BD十Z 5O/5O-M-H),与契子板相连接的支架或安装件全部选用镀钟板材料,目翼子板标准件表面处理方式选用达克罗处理:注,见了•板的材料性能参考Q/DQB 425-2009宝山明族股份有限公司企业标准连线热俄常绊合金瓶层钢板及钢布.b)翼子板特征工通过增加翼子板支架,且在翼子板上的安装位生设立凹介特征(如图3).来减少翼子板与安鼓位置的的贴合而和:闵行人保护方而考虑,现翼子板支架结构Z向刚度较晶. 为防止在安装黑子板娘模时,导致翼子板安装支架变形,不建议使用乘子板与翼子板支架间审加加强筋的结构(如图4)。
模具制造工艺的优化与改进
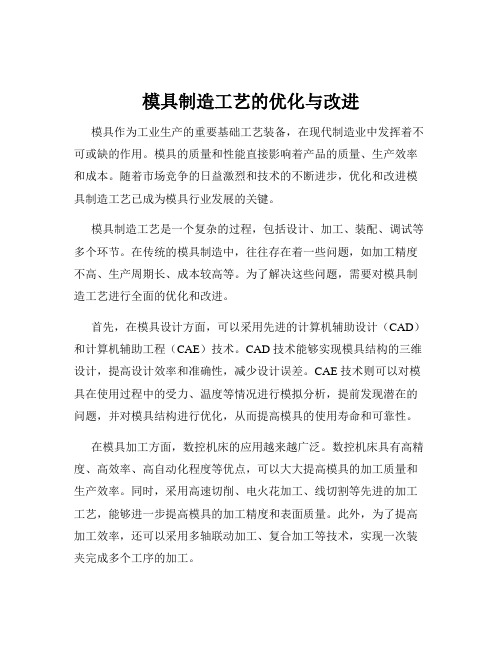
模具制造工艺的优化与改进模具作为工业生产的重要基础工艺装备,在现代制造业中发挥着不可或缺的作用。
模具的质量和性能直接影响着产品的质量、生产效率和成本。
随着市场竞争的日益激烈和技术的不断进步,优化和改进模具制造工艺已成为模具行业发展的关键。
模具制造工艺是一个复杂的过程,包括设计、加工、装配、调试等多个环节。
在传统的模具制造中,往往存在着一些问题,如加工精度不高、生产周期长、成本较高等。
为了解决这些问题,需要对模具制造工艺进行全面的优化和改进。
首先,在模具设计方面,可以采用先进的计算机辅助设计(CAD)和计算机辅助工程(CAE)技术。
CAD 技术能够实现模具结构的三维设计,提高设计效率和准确性,减少设计误差。
CAE 技术则可以对模具在使用过程中的受力、温度等情况进行模拟分析,提前发现潜在的问题,并对模具结构进行优化,从而提高模具的使用寿命和可靠性。
在模具加工方面,数控机床的应用越来越广泛。
数控机床具有高精度、高效率、高自动化程度等优点,可以大大提高模具的加工质量和生产效率。
同时,采用高速切削、电火花加工、线切割等先进的加工工艺,能够进一步提高模具的加工精度和表面质量。
此外,为了提高加工效率,还可以采用多轴联动加工、复合加工等技术,实现一次装夹完成多个工序的加工。
模具材料的选择也是影响模具质量和性能的重要因素。
在选择模具材料时,需要根据模具的使用要求、工作条件、生产批量等因素进行综合考虑。
目前,常用的模具材料有模具钢、铝合金、铜合金等。
为了提高模具的使用寿命和性能,可以采用新型的模具材料,如硬质合金、陶瓷等。
同时,对模具材料进行表面处理,如淬火、氮化、镀硬铬等,也能够提高模具的表面硬度和耐磨性。
在模具装配过程中,需要严格控制装配精度和装配质量。
采用合理的装配工艺和装配方法,如分组装配、修配装配等,能够保证模具的装配精度和配合精度。
同时,加强对装配过程的质量检验和控制,及时发现和解决装配过程中出现的问题,确保模具的装配质量。
翼子板安装支架冲压工艺及模具设计

李耀辉① 李晴雨② 刘英杰②
( ①苏州市职业大学机电工程学院ꎬ江苏 苏州 215014ꎻ②苏州博赢精密模具有限公司ꎬ江苏 苏州 215101 )
摘 要: 针对翼子板安装支架工件存在翻边、凸包等形状复杂且精度要求高的特点ꎬ确定采用冲压加工方 法ꎮ 通过对支架工件冲压工艺分析ꎬ提出了采用 15 个工位的级进冲压工艺方案ꎮ 重点介绍了工件 冲压排样和模具结构设计ꎬ除了采用提高带料定位精度的常规措施外ꎬ通过内、外导料板导向方式 实现带料全程精确送进导向ꎻ设计中采用上下托板和垫脚结构来增加模具闭合高度ꎬ以满足压力机 装模高度需求ꎮ 整套模具采用三维设计ꎬ便于模具的并行工程和后续数控加工程序的生成ꎮ
Keywords:the wing mounting bracketꎻlayoutꎻstamping processꎻprogressive dieꎻdie design
图 1 为Байду номын сангаас子板安装支架零件ꎬ支架的作用是将翼 子板固定在汽车车架上ꎮ 支架上设计有安装孔和加强 筋ꎬ安装孔的作用是通过螺栓实现支架和翼子板的连 接ꎻ支架弯折处设置有凸包加强筋ꎬ可增加支架本体的 强度ꎻ支架两侧的加强翻边可改变支架本体受冲击力 截面的形状ꎮ
2 模具总体方案设计
支架工件主要包含落料、冲孔、翻边和成形等冲压 工序ꎮ 支架主体上 R5 mm 的圆角特征通过成形工序 获得ꎬ圆角 区 有 一 凸 包 特 征ꎬ 凸 包 所 处 位 置 及 形 状 复 杂ꎬ凸包的成形对圆角区形状和尺寸精度会产生一定 影响[4] ꎮ 为避免凸包成形时对圆角区成形精度的影 响ꎬ可将成形区周围材料去除后进行预成形ꎬ凸包成形 后再通过整形工序对圆角区和直边特征加以改善ꎮ 支 架两侧宽度为 4 mm 的直边部分通过翻边工序获得ꎮ 由于工件工序较多ꎬ且工件尺寸不大ꎬ生产批量较大ꎬ 确定采用冲孔-切边-成形-翻边-整形-切断的级进冲 压工艺方案ꎮ
左右后翼子板延伸板多工位冲压工艺分析

左右后翼子板延伸板多工位冲压工艺分析I. 绪论- 研究背景和意义- 工艺简介和发展历程II. 延伸板冲压技术- 工艺特点和要求- 工艺流程和步骤- 延伸板的设计和制造技术III. 左右后翼子板多工位冲压模具- 模具设计原理和要求- 模具工艺流程和步骤- 模具加工工艺和制造技术IV. 工艺参数优化- 工艺参数的影响因素分析- 工艺参数优化方法和技巧- 工艺参数的优化实验和结果分析V. 结论与展望- 工艺的优点和不足- 未来的发展方向和研究方向- 对相关领域的参考和借鉴注:以上章节仅作参考,实际撰写时可根据自己的研究内容作适当调整。
第一章:绪论1.1 研究背景和意义随着制造业的发展和市场需求的不断增长,冲压技术作为一种高效、精度高的成形工艺被广泛应用,成为了汽车、家电、数码等制造行业的主要加工方式之一。
随着产品的复杂化和多样化,传统的单工位冲压工艺已经无法满足不同形状产品的加工需求,因此出现了多工位冲压技术。
冲压是一种通过金属板材在冲床中受力而产生的形变和分离来实现工件成形的冷加工成形方法。
多工位冲压工艺是在单工位的冲压工艺基础上发展起来的一种高效率、高质量的成形技术。
不同于单工位冲压工艺,多工位冲压工艺能够实现更加复杂的成形加工,能够同时完成多个工件的冲压加工,提高了生产效率和产品质量。
在汽车制造行业中,左右后翼子板是整车结构中关键部件之一,其外形要求高精度、高质量。
多工位冲压技术在左右后翼子板的生产应用中发挥了重要作用,可以提高生产效率,减少人力投入,同时还能确保生产质量的稳定性和一致性。
1.2 工艺简介和发展历程多工位冲压工艺是在单工位冲压技术的基础上发展而来的,其工艺形式主要分为上下模式、左右模式、前后模式和全方位模式。
多工位冲压工艺的主要特点是在同一模具上设置多个冲压工位,分别完成不同的加工工序。
多工位冲压工艺流程短、加工效率高,并且能够保证工件的加工质量和精度,已经被广泛应用于制造业的各个领域,特别是汽车、家电和数码产品等生产制造领域。
- 1、下载文档前请自行甄别文档内容的完整性,平台不提供额外的编辑、内容补充、找答案等附加服务。
- 2、"仅部分预览"的文档,不可在线预览部分如存在完整性等问题,可反馈申请退款(可完整预览的文档不适用该条件!)。
- 3、如文档侵犯您的权益,请联系客服反馈,我们会尽快为您处理(人工客服工作时间:9:00-18:30)。
轿车翼子板成形工艺改进及模具设计要点分析
摘要 对典型结构轿车翼子板进行成形工艺分析,并对其成形工艺及模具设
计进行改进,从而减少零件成形工序数及模具套数,达到降低模具开发成本及减
少零件生产成本。
关键词 翼子板;成形工艺改进;模具设计
0 引言
覆盖件的制造是汽车车身制造的关键环节,同一般冲压件相比,它具有材料
薄、形状复杂、结构尺寸大及表面质量高等特点,因此,对覆盖件的工艺设计、
模具结构设计及制造工艺均要求较高。
翼子板作为外覆盖件,因其外轮廓形状比较复杂,拉伸深度不均匀,且不对
称,同时它与车身上多个零件存在较高装配要求,故其成形工艺相对较为复杂,
为保证产品质量,经常设置6个~7个工序完成。
1 工艺分析
图1所示为典型结构的轿车翼子板零件,根据零件的结构特点,通常该零件
成形工艺为:工序1落料;工序2拉伸;工序3切周边;工序4翻边(A区域、
D区域)、斜锲翻边(B区域)、整形(E区域);工序5冲孔(E区域)、斜锲冲
孔(B区域、a孔)、斜锲整形(A区域);工序6冲孔、斜锲冲孔(b孔、c孔)、
斜锲翻边(a孔处)。该工艺方案对于零件成形没有任何问题,但其缺点是工序
较多,如果采用该方案,则模具需要开发6套,且零件生产时,除去落料工序单
独设置外,则至少需要5台机床才能成线生产。又因该零件是外覆盖件,为保证
零件生产质量,通常采用自动化生产线生产,故自动化设备也需相应配备5套。
对于以上情况,考虑如将零件成形工艺减少一个工序,则可以节约一套模具,零
件生产也可以减少一个工序,不仅可以节约模具开发成本,也可以减少零件生产
成本。特别是像笔者所在公司冲压自动化生产线只有4台设备,如要生产该零件
不仅需要增加一台机床及一套自动化设备,且在生产其他零件时,均需增加一个
工序用于穿过多出的压机,这无形中会大大增加生产成本。
针对上述情况,我们对翼子板零件的数模及图纸进行分析,发现零件采用6
个工序成形,主要原因在于a、b、c处冲孔分布。a处难点在于零件翻边存在较
大负角,翻边需两序才能完成;b处难点在于零件该区域宽度较小,与A区域斜
锲整形同时分布时有冲突;c处难点在于上部的斜锲冲孔与正冲孔同时进行时存
在干涉。故如考虑在切边或翻边时同时将这些孔冲出,则可避免以上问题,零件
成形采用5个工序即可实现,故对其成形工艺进行优化,改进后的工艺方案为:
工序1落料;工序2拉伸;工序3切周边、冲孔(a孔)、斜锲冲孔(c处上侧孔);
工序4翻边(A区域、D区域)、斜锲翻边(B区域)、整形(E区域)、斜锲冲
孔(b孔);工序5冲孔(剩余正冲孔)、斜锲冲孔(B区域、c处下侧孔)、斜锲
整形(A区域)。如图2所示,即将a处、c处(上侧孔)的斜锲冲孔合并到切
边工序,b处的斜锲冲孔合并到整形工序。对于该工艺方案:a处先冲孔再翻边,
对孔的精度会产生一定影响,故要求冲孔时预先做出补偿,补偿量的多少可根据
实际模具调试情况而定;对于c处斜锲冲孔与切边同时分布,因冲孔位置与切边
位置距离较远,可采用“穿墙”结构实现,即斜锲结构布置在切刀下侧并穿过切刀;
对于b处斜锲冲孔与翻边同时分布,也同样可采用“穿墙”结构实现。
2 模具设计要点
对于该零件的模具设计及调试而言,因翼子板零件是外覆盖件,表面质量要
求高,而零件形状相对较复杂,在拉伸工序容易产生冲击线、滑移线等表面缺陷,
故2/5拉伸工序主要考虑如何解决这些问题,可通过增加工艺筋增加进料阻力、
增大凹模圆角半径、提高模具圆角R处的光洁度来减少摩擦产生的划痕等措施
加以解决,或使其移动到零件非外露面等。
1.废料刀,2.上模切刀镶块,3.下模斜锲驱动块,4.限位块,5.上模悬吊式斜
锲部件,6.上模座,7.压料器,8.下模切刀镶块,9.零件,10.下模座,11.下模切
刀镶块
1.废料盒,2.下模翻边镶块,3.下模斜锲驱动块,4.压斜器,5.上模悬吊式斜
锲部件,6.上模翻边镶块,7.氮气弹簧,8.上模座,9.聚氨酯缓冲块,10.限位块,
11.上模翻边镶块,12.零件,13.下模座
对于3/5序切边冲孔模,主要是采用了比较典型的“穿墙”结构,该部分结构
如图3所示:上模悬吊式斜锲机构布置在上模切刀镶块2下部并穿过切刀镶块,
通过该结构可以同时实现切边与斜锲冲孔,但模具设计时需注意上模切刀镶块2
应具备足够强度。对于切边模而言,由于废料刀1与切边刀块11工作时存在时
间差,故切边工序最常见的问题是在废料刀与切边刀块接触处容易产生小铁屑,
在机床运动过程中被带到模具表面或零件表面,从而影响零件外观质量,尤其是
外覆盖件,故切边工序模具设计时还应考虑如何避免铁屑的生产,对此,模具设
计时如将废料刀1与下模切刀镶块11之间预留出2mm~2.5mm间隙即可解决该
问题。同时,该模具设计时闭合高度应合适,不仅要求与生产零件的机床相适应,
同时应保证废料滑道倾角足够大,废料能自动滑出工作台以外,以保证不损坏模
具,同时保证自动化线生产的效率。
对于4/5序斜锲翻边冲孔模,翻边与斜锲冲孔同时进行结构如图4所示,在
上模翻边镶块6上做出冲头通过孔,模具设计时应保证翻边镶块具备足够强度。
同时,在采取斜锲机构翻边时,应注意斜锲驱动部件及翻边镶块复位部分不得影
响零件的进出及取放。
3 结论
随着我国汽车产能的急剧增加,汽车行业的竞争将越来越激烈,没有高品质、
低成本的产品就无法在市场上立足,故降本工作显得尤为重要。实践证明,很多
零件如翼子板、侧围外板等对其结构及工艺方案进行优化改进后,均只需5个工
序即可实现,能大大降低模具开发成本及生产成本,现昌河铃木生产的LIANA
轿车翼子板即采用该工艺方案,情况反应良好。
参考文献
[1]翁其金.冷冲压技术[M].机械工业出版社,2011.
[2]李集仁,翟建军.模具设计与制造[M].西安电子科技大学出版社,2010.