流化床煤气化工艺技术
煤气化技术介绍

煤气化技术介绍一、起源煤气化技术是指把经过适当处理的煤送入反应器如气化炉内,在一定煤气化技术工艺流程的温度和压力下,通过氧化剂(空气或氧气和蒸气)以一定的流动方式(移动床、硫化床或携带床)转化成气体,得到粗制水煤汽,通过后续脱硫脱碳等工艺可以得到精制一氧化碳气。
1857年,德国的Siemens兄弟最早开发出用块煤生产煤气的炉子称为德士古气化炉。
这项工艺引进中国后在二十世纪九十年代由山东省鲁南化肥厂经过广大工程技术人员的努力,发明了自主知识产权的对置式四喷嘴气化炉,目前已经在国内得到广泛推广应用,特别是兖矿集团煤化工项目在多处使用次技术,取得了显著的经济效益。
还有经过其他许多开发商的开发,到1883年应用于生产氨气。
煤气化技术是清洁利用煤炭资源的重要途径和手段。
二、原理煤干馏过程,主要经历如下变化:当煤料的温度高于100℃时,煤中的水分蒸发出;温度升高到200℃以上时,煤中结合水释出;高达350℃以上时,粘结性煤开始软化,并进一步形成粘稠的胶质体(泥煤、褐煤等不发生此现象);至400~500℃大部分煤气和焦油析出,称一次热分解产物;在450~550℃,热分解继续进行,残留物逐渐变稠并固化形成半焦;高于550℃,半焦继续分解,析出余下的挥发物(主要成分是氢气),半焦失重同时进行收缩,形成裂纹;温度高于800℃,半焦体积缩小变硬形成多孔焦炭。
当干馏在室式干馏炉内进行时,一次热分解产物与赤热焦炭及高温炉壁相接触,发生二次热分解,形成二次热分解产物(焦炉煤气和其他炼焦化学产品)。
煤干馏的产物是煤炭、煤焦油和煤气。
煤干馏产物的产率和组成取决于原料煤质、炉结构和加工条件(主要是温度和时间)。
随着干馏终温的不同,煤干馏产品也不同。
低温干馏固体产物为结构疏松的黑色半焦,煤气产率低,焦油产率高;高温干馏固体产物则为结构致密的银灰色焦炭,煤气产率高而焦油产率低。
中温干馏产物的收率,则介于低温干馏和高温干馏之间。
煤干馏过程中生成的煤气主要成分为氢气和甲烷,可作为燃料或化工原料。
我国循环流化床煤气化技术工艺研究现状
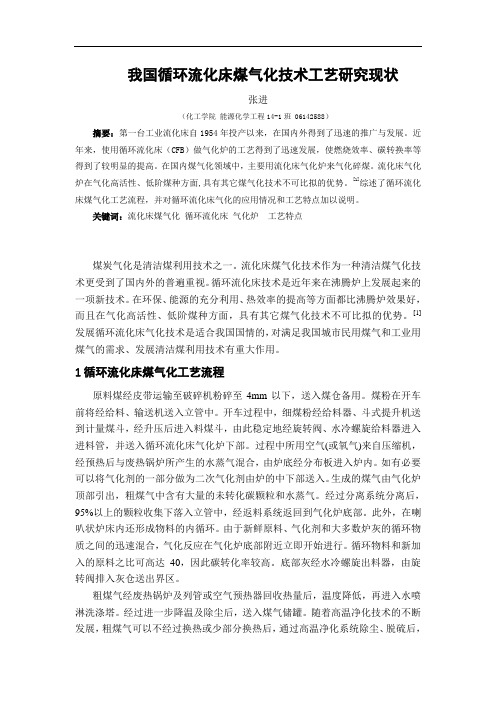
我国循环流化床煤气化技术工艺研究现状张进(化工学院能源化学工程14-1班 06142588)摘要:第一台工业流化床自1954年投产以来,在国内外得到了迅速的推广与发展。
近年来,使用循环流化床(CFB)做气化炉的工艺得到了迅速发展,使燃烧效率、碳转换率等得到了较明显的提高。
在国内煤气化领域中,主要用流化床气化炉来气化碎煤。
流化床气化炉在气化高活性、低阶煤种方面,具有其它煤气化技术不可比拟的优势。
[1]综述了循环流化床煤气化工艺流程,并对循环流化床气化的应用情况和工艺特点加以说明。
关键词:流化床煤气化循环流化床气化炉工艺特点煤炭气化是清洁煤利用技术之一。
流化床煤气化技术作为一种清洁煤气化技术更受到了国内外的普遍重视。
循环流化床技术是近年来在沸腾炉上发展起来的一项新技术。
在环保、能源的充分利用、热效率的提高等方面都比沸腾炉效果好,而且在气化高活性、低阶煤种方面,具有其它煤气化技术不可比拟的优势。
[1]发展循环流化床气化技术是适合我国国情的,对满足我国城市民用煤气和工业用煤气的需求、发展清洁煤利用技术有重大作用。
1循环流化床煤气化工艺流程原料煤经皮带运输至破碎机粉碎至4mm以下,送入煤仓备用。
煤粉在开车前将经给料、输送机送入立管中。
开车过程中,细煤粉经给料器、斗式提升机送到计量煤斗,经升压后进入料煤斗,由此稳定地经旋转阀、水冷螺旋给料器进入进料管,并送入循环流化床气化炉下部。
过程中所用空气(或氧气)来自压缩机,经预热后与废热锅炉所产生的水蒸气混合,由炉底经分布板进入炉内。
如有必要可以将气化剂的一部分做为二次气化剂由炉的中下部送入。
生成的煤气由气化炉顶部引出,粗煤气中含有大量的未转化碳颗粒和水蒸气。
经过分离系统分离后,95%以上的颗粒收集下落入立管中,经返料系统返回到气化炉底部。
此外,在喇叭状炉床内还形成物料的内循环。
由于新鲜原料、气化剂和大多数炉灰的循环物质之间的迅速混合,气化反应在气化炉底部附近立即开始进行。
流化床煤气化技术的分析研究进展

流化床煤气化技术的研究进展煤气化技术有多种分类法,按煤的进料状态可分为干块进料、干粉进料和煤浆进料。
煤层中燃料运动状态,可分为固定床<亦称移动床)、流化床、气流床和熔融床. 按床层压力等级,可分为低压<< 0.3MPa )、中压<0.3 MPa〜4.5 MPa)和高压<> 4.5MPa )。
按排渣状态,可分为干法<固态)、熔聚和熔渣<液态)。
目前,应用较广泛的煤气化技术有如下几种:1)加压固定床气化技术加压鲁奇炉是典型的加压固定床气化技术,技术成熟,能利用高灰分煤,并且能在 2.41 MPa 压力下运行,适合合成液体燃料合成所需要的操作压力,可节约投资和能耗,但过程中产生大量的焦油和酚。
为克服上述缺点,又进行了新的开发,主要技术升级包括进一步提高压力、提高温度和两段引气。
2)流化床气化技术温克勒气化工艺是典型的流化床技术,最早用于工业生产,第一台工业生产装置于 1926 年投入运行。
这种炉型存在严重的缺陷,只能利用高活性褐煤,排灰含碳多,飞灰带出碳损失严重,致使碳利用率降低。
针对这些问题开发了新的流化床技术,如高温温克勒<HTW )、灰熔聚气化<KRW , U-gas)和循环流化床气化工艺。
3)水煤浆气流床气化技术水煤浆气流床气化又称湿法进料气流床气化,其中 Texaco 炉是一种率先实现工业化的水煤浆气流床气化技术,其进料方式简单,工程问题较少,具有大的气化能力,可以实现高压力<8 MPa〜10MPa)操作。
但冷煤气效率较低,氧耗较高。
为了降低过程氧耗,提高冷煤气效率,在 Texaco 气化技术基础上发展了两段进煤煤气化工艺。
4)干粉进料气流床气化技术干粉进料气流床气化技术相对湿法进料具有氧耗低,煤种适应广和冷煤气效率高等优点•其代表技术有Shell, Prenflo和日立气流床等。
Shell SCGP工艺是在K-T炉的基础上所开发的加压 K-T 气化炉。
Prenflo 气化工艺与 Shell SCGP 基本相同,只是炉体设计有所不同。
恩德炉粉煤流化床气化工艺简介

/!%(( 的粒度经干燥系统干燥至水含量 /.0 ,进入煤
贮斗中贮存, 煤斗采用 12& 安全气加压密封。 煤料通过煤仓底部的 & 个螺旋加煤机送入气化炉 底部锥体段。空气 ( 或富氧空气)和来自废热锅炉的过 热蒸汽混合作为气化剂和流化介质, 分别从一次喷嘴和 二次喷嘴进入气化炉。 一次喷嘴设在加煤机下方的气化 炉锥体部位, 与切线方向成一定的仰角和斜角, 使入炉 原料流化。 入炉煤料中大部分较粗颗粒在炉底锥体段附 近形成密相段, 呈沸腾状态。在此, 气、 固两相发生剧烈 传质和传热, 并发生燃烧反应和水煤气反应。密相段温 度分布均匀, 反应温度为 $3%’!%%%(。 这样, 煤料受热后 快速热解产生焦油、 酚和轻油等, 并在床层高温条件下 裂解成小分子。 其余入炉细粉和大颗粒因受热而裂解产
( 见图 ! ) &-" 恩德炉的工艺流程
图 !---- 恩德炉的工艺流程
义马煤经输送皮带、破碎机、振动筛、粉碎筛, 为
生的小颗粒由反应气体携带离开密相段, 在气化炉的上 部形成稀相区, 并在此处与二次风嘴喷入的二次风进一 步发生反应, 甲烷和高碳化合物进一步燃烧和裂解。因 此, 一般稀相段温度比密相段温度要高一些, 同时排出 的废水中基本不含焦油和酚类, 有利于环境保护。 灰渣比重较大, 由床层落到气化炉底部, 经水内冷 的螺旋出渣机排于密闭灰斗, 定期排到炉底渣车, 送出 界外。 未经过反应完全的细粉颗粒由煤气夹带从气化炉 顶部出来, 经旋风除尘器将其中较粗颗粒分离出来。较 粗颗粒靠自身重力经回流管返回气化炉底部, 再次参加 气化反应, 以提高碳转化率, 降低飞灰含碳量。 温度为 $%%’$3%(的出炉煤气, 先通过旋风除尘器, 再经飞灰沉降室后进入废热锅炉,以回收煤气中的显 热, 产生过热蒸汽。由于煤气先经过除尘器再进废热锅
三种煤气化工艺详述

三种煤气化炉技术介绍一、概述煤气化技术的开发与应用大约经历了200年的发展历史。
煤气化技术按固体和气体的接触方式可分为固定床、流化床、气流床和熔融床4种,其中熔融床技术还没有实际应用开发,各种煤气化炉的模式见图1。
图1 各种煤气化炉模式图1.固定床。
固定床气化炉是最早开发出的气化炉,如图1(a)所示,炉子下部为炉排,用以支撑上面的煤层。
通常,煤从气化炉的顶部加入,而气化剂(氧或空气和水蒸气)则从炉子的下部供入,因而气固间是逆向流动的。
特点是单位容积的煤处理量小,大型化困难。
目前,运转中的固定床气化炉主要有鲁奇气化炉和BGC-鲁奇炉两种。
2.流化床。
流化床气化炉如图1(b)所示,在分散板上供给粉煤,在分散板下送入气化剂(氧、水蒸气),使煤在悬浮状下进行气化。
流化床气化炉不能用灰分融点低的煤,副产焦油少,碳利用率低。
3.气流床。
气流床气化炉如图1(c)所示,粉煤与气化剂(O2、水蒸气)一起从喷嘴高速吹入炉内,快速气化。
特点是不副产焦油,生成气中甲烷含量少。
气流床气化是目前煤气化技术的主流,代表着今后煤气化技术的发展方向。
气流床按照进料方式又可分为湿法进料(水煤浆)气流床和干法进料(煤粉)气流床。
前者以德士古气化炉为代表,还有国内开发的多元料浆加压气化炉、多喷嘴(四烧嘴)水煤浆加压气化炉;后者以壳牌气化炉为代表,还有GSP炉以及国内开发的航天炉、两段炉、清华炉、四喷嘴干粉煤炉。
二、三种先进的煤气化工艺我国引进并被广泛采用的三种先进煤气化工艺——鲁奇气化炉、壳牌气化炉、德士古气化炉。
1.鲁奇气化炉(结构见图2)属于固定床气化炉的一种。
鲁奇气化炉是1939年由德国鲁奇公司设计,经不断的研究改进已推出了第五代炉型,目前在各种气化炉中实绩最好。
德国SVZ Schwarze Pumpe公司已将这种炉型应用于各种废弃物气化的商业化装置。
我国在20世纪60年代就引进了捷克制造的早期鲁奇炉并在云南投产。
1987年建成投产的天脊煤化工集团公司从德国引进的4台直径3800mm的Ⅳ型鲁奇炉,先后采用阳泉煤、晋城煤和西山官地煤等煤种进行试验,经过10多年的探索,基本掌握了鲁奇炉气化贫瘦煤生产合成氨的技术,现建成的第五台鲁奇炉已投产,形成了年产45万吨合成氨的能力。
流化床气化煤气设计

流化床气化煤气设计
流化床气化是一种高效的煤气化技术,通过将煤粒在高温下与氧气和蒸汽进行反应,产生可燃性气体。
这种气化技术被广泛应用于工业生产和能源开发领域,其设计和操作对于提高煤气化效率和降低环境污染具有重要意义。
首先,流化床气化煤气设计需要考虑气化反应的温度和压力。
适当的温度和压力可以促进气化反应的进行,并提高气化效率。
同时,设计中需要考虑煤气化产生的气体成分和热值,以满足不同工业生产和能源利用的需求。
其次,设计中需要考虑流化床的材料和结构。
流化床的材料应具有良好的耐高温和耐腐蚀性能,以保证设备长期稳定运行。
流化床的结构设计也需要考虑气体和固体颗粒的流动特性,以确保气化反应能够充分进行。
另外,流化床气化煤气设计还需要考虑废气处理和余热回收。
废气处理可以减少气化过程中产生的污染物排放,保护环境。
余热回收可以提高能源利用效率,降低生产成本。
总的来说,流化床气化煤气设计是一个综合性的工程问题,需要考虑气化反应、设备材料和结构、废气处理和余热回收等多个方面。
通过合理的设计和优化,可以实现高效、清洁的煤气化生产,为工业生产和能源开发提供可靠的技术支持。
黄台炉循环流化床气化技术

黄台炉循环流化床气化技术全文共四篇示例,供读者参考第一篇示例:黄台炉循环流化床气化技术是一种先进的生物质能源利用技术,通过在高温、高压和氧气不足的条件下将生物质材料进行气化,将其转化为合成气,进而产生燃烧或发电所需的能源。
这项技术不仅可以有效利用生物质资源,减少环境污染,还有助于实现能源的可持续利用。
流化床气化技术是指在一定的流化速度下,通过对气化床中的颗粒物料进行搅拌和混合,使之形成类似于流体的状态,从而提高反应速率和热传导效果。
而黄台炉循环流化床气化技术则在这一基础上进一步实现了气化床内部气态组分的混合均匀和循环往复运动,从而提高了气化效率和产气质量。
黄台炉循环流化床气化技术具有以下几个显著特点:一、高效节能:循环流化床技术可以有效地减少废气和废热的排放,实现废热再利用,提高能源利用效率。
而且由于气化反应在高温、高压和氧气不足条件下进行,可以最大化地保留生物质原料中的碳元素,减少能源消耗。
二、资源综合利用:循环流化床气化技术可以利用多种生物质资源进行气化,如秸秆、木屑、废弃物等,实现资源的综合利用。
废弃物气化后可以产生高温热能、合成气等多种产品,实现废物资源化的目的。
三、环保节能:流化床气化技术采用循环流化床反应器,反应温度高、气氛调控好,能减少有害气体和颗粒物的排放,减轻对大气和环境的污染。
废热回收和再利用也有助于节能减排。
四、灵活可控:黄台炉循环流化床气化技术具有较强的操作灵活性和反应可控性,可以根据不同的生物质原料和气化条件,来调节反应器内的气气、气溶胶和颗粒物的混合均匀,以及产气量和气化效率。
五、成本优势:循环流化床气化技术相对于传统燃煤气化技术而言,设备投资、运行成本和维护费用都更低廉,利用寿命更长,更经济实用。
因此在生物质能源产业中有着广泛的应用前景。
黄台炉循环流化床气化技术是一项具有巨大潜力和发展前景的能源转化技术,可以有效推动生物质资源的利用,减少环境污染,实现绿色和可持续发展。
煤气化技术及气化炉的应用

煤气化技术及气化炉的应用目前,煤气化技术和气化炉的使用越来越广泛,我国的人口众多,国土面积也不小,但是仍旧处于资源短缺的环境污染的双重制约下。
我国的现有资源中,煤炭资源是比较充足的,占到了我国目前所有消耗能源的80%。
笔者从煤气化技术入手,对我国目前所使用的固定床气化技术、流化床气化技术和气流床气化技术进行了全面的分析和研究。
标签:煤气化技术;气化炉;煤种;应用1 固定床气化技术1.1 气化炉固定床气化技术所使用的气化炉主要是间歇固定床气化炉、鲁奇和鲁奇改进气化炉。
1.1.1间歇固定床气化炉对于间歇固定床气化炉来说,其本身的特点就是操作比较简单,但是从根本上来说其技术比较落后,而且能力和效率比较低。
对于很多间歇固定床气化炉来说,需要进行单台炉的投煤量控制,并将原料进行筛选。
1.1.2 鲁奇炉对于鲁奇固定气化工艺来说,其工艺是比较成熟的,在进行使用的时候,需要将其温度控制在900-1000℃,实现焦油的高气化效率,实现对气化热效率的高度控制。
在多种工艺中,这种艺的熟练程度比较高,而且原料的制备和排渣的处理相对来说比较容易,适合城市煤气的供应。
1.1.3鲁奇改进气化炉鲁奇改进气化炉实在鲁奇炉的基础上进行相应的改进实现的,这种改进可是使固态的排渣变为液态排渣。
该气化炉可直接气化含水量大于20%的煤,在1400~1600℃高温气化条件下,蒸汽用量可大幅下降。
这种炉体本身的结构相对来说比较简单,一般采用的就是常规压力容器材料和常规的耐高温炉衬和循环的冷却水夹套。
1.2 原料煤要求1.3 国内应用情况对于一般气化炉的使用在我国的东北地区的使用是比较多的,利用鲁奇炉的主要是内蒙古的一些公司,使用鲁奇改进炉的是我国的山西省梅花公司。
所以,对于一般气化炉的使用比较多的,而且占到了全部使用量的60%以上。
2 流化床气化技术2.1 气化炉2.1.1 恩德气化炉恩德气化炉是经过温克勒气化炉改进得来的,是应用于生产燃料气和合成氨等。
- 1、下载文档前请自行甄别文档内容的完整性,平台不提供额外的编辑、内容补充、找答案等附加服务。
- 2、"仅部分预览"的文档,不可在线预览部分如存在完整性等问题,可反馈申请退款(可完整预览的文档不适用该条件!)。
- 3、如文档侵犯您的权益,请联系客服反馈,我们会尽快为您处理(人工客服工作时间:9:00-18:30)。
流化床煤气化工艺技术0流化床煤气化概述所谓“流态化”是一种使固体微粒通过与气体或液体接触而转变成类似流体状态的操作。
当流体以低速向上通过微细颗粒组成的床层时,工艺条件和气化指标( 1 )工艺条件①原料。
褐煤是流化床最好的原料,但褐煤的水分含量很高,一般在12 %以上,蒸发这部分水分需要较多的热量(即增加了氧气的消耗量),水分过大,也会造成粉碎和运输困难,所以水分含量太大时,需增设干燥[wiki]设备[/wiki]。
煤的粒度及其分布对流化床的影响很大,当粒度范围太宽,大粒度煤较多时,大量的大粒度煤难以流化,覆盖在炉算上,氧化反应剧烈可能引起炉算处结渣。
如果粒度太小,易被气流带出,气化不彻底。
一般要求粒度大于10mm 的颗粒不得高于总量的5 % ,小于lmm 的颗粒小于总量的10 % - 15 %。
由于流化床气化时床层温度较低,碳的浓度较低,故不太适宜气化低活性、低灰熔点的煤种。
②气化炉的操作温度。
高炉温对气化是有利的,可以提高气化强度和煤气质量,但炉温是受原料的活性和灰熔点的限制的,一般在900 ℃左右。
影响气化炉温度的因素大致有汽氧比、煤的活性、水分含量、煤的加人量等。
其中又以汽氧比最为重要。
③二次气化剂的用量。
使用二次气化剂的目的是为了提高煤的气化效率和煤气质量。
被煤气带出的粉煤和未分解的碳[wiki]氢[/wiki]化合物,可以在二次气化剂吹人区的高温[wiki]环境[/wiki]中进一步反应,从而使煤气中的一氧化碳含量增加、甲烷量减少。
( 2 )气化指标褐煤的温克勒气化指标如表4 一10 所示。
由以上的叙述可知,温克勒气[wiki]化工[/wiki]艺单炉的生产能力较大。
由于气化的是细颗粒的粉煤,因而可以充分利用[wiki]机械[/wiki]化采煤得到的细粒度煤。
由于煤的干馏和气化是在相同温度下进行的,相对于移动床的干馏区来讲,其干馏温度高得多,所以煤气中几乎不含有焦油,酚和甲烷的含量也很少,排放的洗涤水对环境的污染较小。
但温克勒常压气化也存在一定的缺点,主要是温度和压力偏低造成的。
炉内温度要保证灰分不能软化和结渣,一般应控制在900 ℃左右,所以必须使用活性高的煤为气化原料。
气化温度低,不利于二氧化碳还原和水蒸气的分解,故煤气中二氧化碳的含量偏高,而可燃组分如一氧化碳、氢气、甲烷等含量偏低。
同时,和移动床比较,气化炉的设备庞大,出炉煤气的温度几乎和床内温度一样,因而热损失大。
另外,流态化使颗粒磨损严重,气流速度高又使出炉煤气的带出物较多。
为此进一步开发了温克勒加压气化和灰团聚气化工艺。
流化床气化工艺在固定床阶段,燃料是以很小的速度下移,与气化剂逆流接触。
当气流速度加快到一定程度时,床层膨胀,颗粒被气流悬浮起来。
当床层内的颗粒全部悬浮起来而又不被带出气化炉,这种气化方法即为流化床(沸腾床)气化工艺。
和固定床相比较,流化床的特点是气化的原料粒度小,相应的传热面积大,传热效率高,气化效率和气化强度明显提高。
常压流化床气化工艺1. 温克勒气化炉温克勒气化工艺是最早的以褐煤为气化原料的常压流化床气化工艺。
图 4 一37 是温克勒气化炉的示意,气化炉为钢制立式圆筒形结构,内衬耐火材料。
温克勒气化炉采用粉煤为原料,粒度在0 -10mm 左右。
若煤不含表面水且能自由流动就不必干燥。
对于豁结性煤,可能需要气流输送系统,借以克服螺旋给煤机端部容易出现堵塞的问题。
粉煤由螺旋加料器加人圆锥部分的腰部,加煤量可以通过调节螺旋给料机的转数来实现。
一般沿筒体的圆周设置二到三个加料口,互成1800 或1200 的角度,有利于煤在整个截面上的均匀分布。
温克勒气化炉的炉算安装在圆锥体部分,蒸汽和氧(或空气)由炉算底侧面送人,形成流化床。
一般气化剂总量的60 % ? 75 %由下面送入,其余的气化剂由燃料层上面2 . 5 - 4m 处的许多喷嘴喷人,使煤在接近灰熔点的温度下气化,这可以提高气化效率、有种于活性低的煤种气化。
通过控制气化剂的组成和流速来调节流化床的温度不超过灰的软化点。
较大的富灰颗粒比煤粒的密度大,因而沉到流化床底部,经过螺旋排灰机排出。
大约有30 %的灰从底部排出,另外的70 %被气流带出流化床。
气化炉顶部装有辐射锅炉,是沿着内壁设置的一些水冷管,用以回收出炉煤气的[wiki]显热[/wiki],同时,由于温度降低可能被部分熔融的灰颗粒在出气化炉之前重新固化。
早期的温克勒气化炉在炉低部有炉栅,气化剂通过炉栅进人炉内。
后来的气化炉取消炉栅,炉子的结构简化,同样能达到均匀布气的效果。
典型的工业规模的温科勒常压气化炉,内径5 . sm ,高23m ,当以褐煤为原料时,氧气一蒸汽常压鼓风,单炉生产能力在标准状态下为47000m " / h ,采用空气一蒸汽鼓风时,生产能力在标准状态下为9400om " / h 。
生产能力的调整范围为25 % - 150 %。
2 .温克勒气化工艺流程温克勒气化工艺流程包括煤的预处理、气化、气化产物显热的利用、煤气的除尘和冷却等。
如图 4 - 38所示。
( 1 )原料的预处理首先对原料进行破碎和筛分,制成。
一10mm 的炉料,一般不需要干燥,如果炉料含有表面水分,可以使用烟道气对原料进行干燥,控制入炉原料的水分在8 %- 12 %左右。
对于有戮结性的煤料,需要经过破赫处理,以保证床内的正常流化。
( 2 )气化预处理后的原料送入料斗中,料斗中充以氮气或二氧化碳惰性气体。
用螺旋加料器将煤料加入气化炉的底部,煤在炉内的停留时间约15min 左右。
气化剂送人炉内和煤反应,生成的煤气由顶部引出,煤气中含有大量的粉尘和水蒸气。
( 3 )粗煤气的显热回收粗煤气的出炉温度一般为900 ℃左右。
在气化炉上部设有废热锅炉,生产的蒸汽压力在1.96 –2.16MPa ,蒸汽的产量为0.5一0.8kg/m “干煤气。
( 4 )煤气的除尘和冷却出煤气炉的粗煤气进人废热锅炉,回收余热,产生蒸汽,然后进人两级旋风分离器和洗涤塔,煤气中的大部分粉尘和水汽,经过净化冷却,煤气温度,降至350-400C ,含尘量降至5- 20mg / m3 。
加压流化床气化工艺高温温克勒(HTW )气化法高温温克勒气化法的基础是低温温克勒气化法。
它是采用比低温温克勒气化法较高的压力和温度的一项气化技术。
除了保持常压温克勒气化炉的简单可靠、运行灵活、氧耗量低和不产生液态烃等优点外,主要采用了带出煤粒再循环回床层的做法,从而提高了碳的利用率。
( l )工艺流程HTW 的气化工艺流程如图4 一39 所示。
和低温温克勒气化炉相比较,高温温克勒气化炉的主要特点是出炉粗煤气直接进人两级旋风除尘器,一级除尘器分离的含碳量较高的颗粒返回到床内进一步气化。
二级除尘器流出的气体人废热锅炉回收热量,再经水洗塔冷却除尘。
整个气化系统是在一个密闭的压力系统中进行的,加煤、气化、出灰均在加压下进行。
含水分8 %一12 %的褐煤进人压力为0 . 98MPa 的密闭料锁系统后,经过螺旋给料机输人炉内。
为提高煤的灰熔点而按一定比例配人的添加剂(主要是石灰石、石灰或白云石)也经给料机加入炉内。
经过预热的气化剂(氧气/蒸汽或空气/蒸汽)从炉子的底部和炉身适当位置加人气化炉内,和由螺旋给料机加人的煤料并流气化。
HTW 气化工艺最初是由德国的莱茵褐煤公司发明,该公司拥有并经营德国鲁尔地区的几座褐煤煤矿。
用莱茵褐煤为原料,煤的灰分中CaO + Mgo 占50 %左右;510 :占8 % ;灰熔点T , - 950 ℃,添加5 %的石灰石后提高到1100℃。
在气化压力0 . 98 MPa 的压力下,以氧气/水蒸气为气化剂,温度1000 ℃下进行的HTW 气化工艺试验,其结果和常温温克勒气化的比较如表4 - 11 所示。
由表中的数据可以看出,压力和高温下的温克勒气化,设备的生产能力大大提高,是常压的 2 倍多。
温度的提高和大颗粒重新返回床层使得碳转化率上升为96 %。
煤中加人助剂,一是可以脱除硫化氢等,并且可使碱性灰分的灰熔点提高。
气化温度提高,虽然煤气中的甲烷含量降低,但煤气中的有效成分却提高,煤气的质量也相应提高。
( 2 )工艺条件和气化指标①气化温度。
提高气化温度有利于二氧化碳的还原反应和水蒸气的分解反应,相应地提高了煤气中的一氧化碳和氢气的浓度,碳的转化率和煤气的产率也提高。
提高气化反应温度是受灰熔点的限制的。
当灰分为碱性时,可以添加石灰石、石灰和白云石来提高煤的软化点和熔点。
②气化压力。
加压气化可以增加炉内反应气体的浓度,流量相同时,气体流速减小,气固接触时间增大,使碳的转化率提高,在生产能力提高的同时,原料的带出损失减小。
在同样的生产能力下,设备的体积相应减小。
试验证明,使用水分为24.5% ,粒度为1一1.6mm 的褐煤为原料,在表压分别为0.O49MPa 和1.96MPa 下,用水蒸气/空气为气化剂时,气化强度可由930kg/( mZ•h )增加到2650kg /( m•h ) ;如用水蒸气/氧气作为气化剂时气化强度可以由1050kg/( m•h )增加到326Okg /( mZ•h )。
加压流化床的工作状态比常压的稳定。
经研究,加压流化床内气泡含量少,固体颗粒在气相中的分散较常压流态化时均匀,更接近散式流态化,气固接触良好。
此外,加压流化时,对甲烷的生成是有利的,相应提高了煤气的热值。