TFT屏幕工艺标准流程经过
tft-lcd生产工艺

tft-lcd生产工艺
TFT-LCD是一种液晶显示技术,全称为薄膜晶体管液晶显示器。
TFT-LCD生产工艺主要包括以下几个步骤:
1. 基板清洗:将玻璃基板放入清洗机内,通过化学溶液和超声波清洗,去除表面的污染物和杂质。
2. 蒸镀:将清洗后的基板放入真空蒸镀机内,通过热蒸发或磁控溅射的方式,将ITO(氧化铟锡)等导电材料薄膜均匀地沉积在基板上,形成液晶显示器的电极。
3. 形成图形:利用UV曝光机将光掩膜与基板层叠在一起进行曝光,然后通过显影和蚀刻的步骤,去除未曝光的部分物质,形成规定的图形。
4. 涂布液晶层:将液晶原料涂布在形成图形的基板上,然后通过加热和冷却控制液晶分子的方向和排列,形成液晶层。
5. 定位贴合:将两块涂有液晶层的基板通过真空吸附的方式,精确地对准并叠放在一起,形成液晶显示区域。
同时,在两块基板的边缘区域添加背光源、驱动IC等组件。
6. 封装:将贴合好的基板放入封装机内,通过高温封装胶或薄膜封装胶封住整个液晶显示器结构,保护液晶显示区域以及内部电路。
7. 背光模组制造:制作背光源,通常采用CCFL(冷阴极荧光
灯)或LED(发光二极管),通过封装、组装等过程,将背
光源和液晶显示器组装在一起。
8. 电功能测试:对制作好的液晶显示器进行电功能测试,确保其正常工作。
以上是TFT-LCD生产工艺的基本流程,当然还有很多其他细
节的工艺步骤,如氧化硅沉积、染料封装等。
随着技术的发展,TFT-LCD生产工艺也在不断改进和完善,以提高产品的质量
和性能。
tft生产工艺
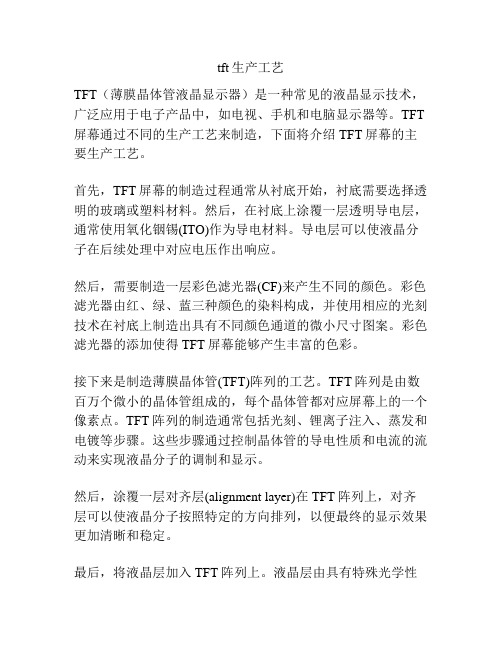
tft生产工艺TFT(薄膜晶体管液晶显示器)是一种常见的液晶显示技术,广泛应用于电子产品中,如电视、手机和电脑显示器等。
TFT 屏幕通过不同的生产工艺来制造,下面将介绍TFT屏幕的主要生产工艺。
首先,TFT屏幕的制造过程通常从衬底开始,衬底需要选择透明的玻璃或塑料材料。
然后,在衬底上涂覆一层透明导电层,通常使用氧化铟锡(ITO)作为导电材料。
导电层可以使液晶分子在后续处理中对应电压作出响应。
然后,需要制造一层彩色滤光器(CF)来产生不同的颜色。
彩色滤光器由红、绿、蓝三种颜色的染料构成,并使用相应的光刻技术在衬底上制造出具有不同颜色通道的微小尺寸图案。
彩色滤光器的添加使得TFT屏幕能够产生丰富的色彩。
接下来是制造薄膜晶体管(TFT)阵列的工艺。
TFT阵列是由数百万个微小的晶体管组成的,每个晶体管都对应屏幕上的一个像素点。
TFT阵列的制造通常包括光刻、锂离子注入、蒸发和电镀等步骤。
这些步骤通过控制晶体管的导电性质和电流的流动来实现液晶分子的调制和显示。
然后,涂覆一层对齐层(alignment layer)在TFT阵列上,对齐层可以使液晶分子按照特定的方向排列,以便最终的显示效果更加清晰和稳定。
最后,将液晶层加入TFT阵列上。
液晶层由具有特殊光学性质的液晶分子组成,可以在电场的作用下改变它们的排列。
液晶层通常由两层夹层构成,在它们之间施加电压会使液晶分子发生对齐变化,从而改变光的穿透性质。
整个TFT屏幕生产工艺通常包括数十个步骤,需要长时间和精密的操作。
每个步骤都要求高质量的材料和工艺控制,以确保最终生产出的TFT屏幕具有良好的色彩表现、视角和响应速度。
随着科技的发展,TFT屏幕的生产工艺也在不断进步,以适应更高的分辨率和更好的显示效果的要求。
车载tft生产工艺

车载tft生产工艺车载TFT屏幕是车辆中常见的电子显示设备,广泛应用于车载导航系统、车载多媒体系统等。
下面是车载TFT屏幕的生产工艺。
一、基板制备车载TFT屏幕的基材通常采用玻璃基板或柔性基板。
首先,选择适当的玻璃基板或柔性基板,并对其进行切割成所需的尺寸。
然后,在基板表面涂上一层透明导电材料,比如氧化铟锡(ITO),以制作触摸屏功能。
二、涂层制备在基板表面涂覆一层透明介电层,常用的材料有聚偏二氟乙烯(PVDF)、聚醚酰亚胺(PI)等。
该层主要起到绝缘和保护导电层的作用。
三、薄膜沉积使用物理气相沉积(PVD)或化学气相沉积(CVD)等技术,在基板表面逐层沉积各种薄膜材料。
其中,最关键的是沉积两层透明导电薄膜,用于制作液晶显示器的电极。
四、光刻制程通过光学曝光和化学腐蚀等工艺,将所需的电路模式转移到涂层材料上,形成导电线路和其他电子元件的图案。
五、液晶填充将液晶材料倒入两块基板之间的空隙中,然后用封装材料封闭边缘,形成液晶层。
六、配向处理通过使用单向刷子或电场调整方法,使液晶分子沿着特定的方向排列,以确保液晶显示效果。
七、封装将两块基板通过密封胶粘合在一起,形成一块完整的TFT屏幕。
在胶水固化之前,需要进行真空抽气和灌注等工艺。
八、封装检测对封装后的TFT屏幕进行外观质量、电性能等的检测,确保产品达到要求。
九、后工艺处理对TFT屏幕进行去残留物处理、切割、蒸镀金属反射层等后处理工艺,以提高产品质量和可靠性。
十、测试和包装对生产出的TFT屏幕进行功能和质量测试,合格后进行包装和出厂。
车载TFT屏幕的生产工艺涉及多个环节和技术,需要高精度的设备和操作技术。
随着技术的不断进步,车载TFT屏幕的生产工艺也在不断改进,以提高产品质量和性能。
tft lcd工艺流程
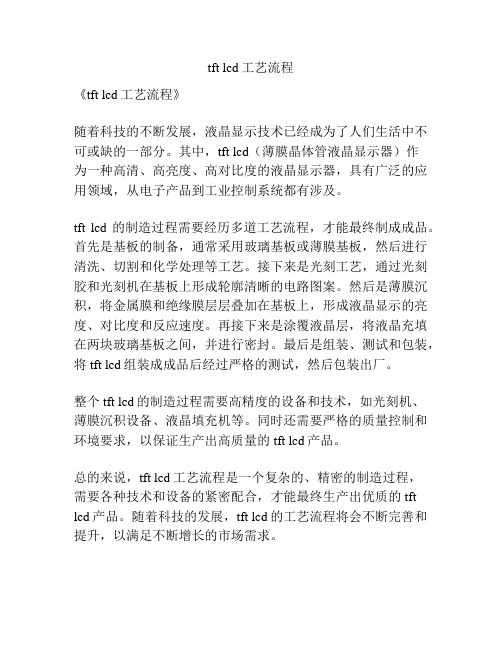
tft lcd工艺流程
《tft lcd工艺流程》
随着科技的不断发展,液晶显示技术已经成为了人们生活中不可或缺的一部分。
其中,tft lcd(薄膜晶体管液晶显示器)作
为一种高清、高亮度、高对比度的液晶显示器,具有广泛的应用领域,从电子产品到工业控制系统都有涉及。
tft lcd的制造过程需要经历多道工艺流程,才能最终制成成品。
首先是基板的制备,通常采用玻璃基板或薄膜基板,然后进行清洗、切割和化学处理等工艺。
接下来是光刻工艺,通过光刻胶和光刻机在基板上形成轮廓清晰的电路图案。
然后是薄膜沉积,将金属膜和绝缘膜层层叠加在基板上,形成液晶显示的亮度、对比度和反应速度。
再接下来是涂覆液晶层,将液晶充填在两块玻璃基板之间,并进行密封。
最后是组装、测试和包装,将tft lcd组装成成品后经过严格的测试,然后包装出厂。
整个tft lcd的制造过程需要高精度的设备和技术,如光刻机、
薄膜沉积设备、液晶填充机等。
同时还需要严格的质量控制和环境要求,以保证生产出高质量的tft lcd产品。
总的来说,tft lcd工艺流程是一个复杂的、精密的制造过程,
需要各种技术和设备的紧密配合,才能最终生产出优质的tft lcd产品。
随着科技的发展,tft lcd的工艺流程将会不断完善和提升,以满足不断增长的市场需求。
tft-lcd面板制造流程
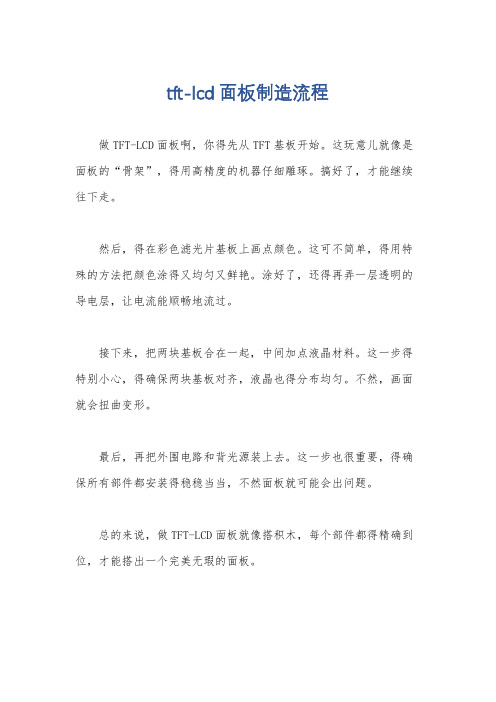
tft-lcd面板制造流程
做TFT-LCD面板啊,你得先从TFT基板开始。
这玩意儿就像是面板的“骨架”,得用高精度的机器仔细雕琢。
搞好了,才能继续往下走。
然后,得在彩色滤光片基板上画点颜色。
这可不简单,得用特殊的方法把颜色涂得又均匀又鲜艳。
涂好了,还得再弄一层透明的导电层,让电流能顺畅地流过。
接下来,把两块基板合在一起,中间加点液晶材料。
这一步得特别小心,得确保两块基板对齐,液晶也得分布均匀。
不然,画面就会扭曲变形。
最后,再把外围电路和背光源装上去。
这一步也很重要,得确保所有部件都安装得稳稳当当,不然面板就可能会出问题。
总的来说,做TFT-LCD面板就像搭积木,每个部件都得精确到位,才能搭出一个完美无瑕的面板。
tft lcd生产工艺

tft lcd生产工艺
TFT LCD是薄膜晶体管液晶显示器(Thin Film Transistor Liquid Crystal Display)的简称,它是一种集成了薄膜晶体管
和液晶显示技术的显示器。
TFT LCD的生产工艺主要包括以下几个步骤:
1. 制作基板:首先,需要制作好用于液晶的玻璃基板。
基板通常具有特殊的透明导电层,用于驱动液晶分子以改变光的透过性。
这些透明导电层通常使用氧化锡或氧化铟问题。
2. 制作薄膜晶体管(TFT):接下来,需要在基板上制作薄膜
晶体管。
薄膜晶体管是控制液晶分子排列和光透过性的关键部件。
制作薄膜晶体管的主要步骤包括:沉积半导体材料、光刻制作电极图案、用相应的材料制作栅极和源极,最后形成晶体管结构。
3. 制作液晶层:制作好薄膜晶体管后,需要在基板之间注入液晶物质。
液晶物质通常是有机化合物或聚合物,具有分子排列敏感性。
在制作过程中,需要在基板之间创造一个密封的空间,并将液晶物质注入其中。
4. 封装:封装是将制作好的TFT LCD组装在一起以形成最终
的显示器模块的过程。
封装过程包括将液晶层和背光源层(通常是LED背光源)粘合在一起,然后使用导电胶水将TFT LCD连接到电路板。
5. 功能测试和质量控制:最后,需要对TFT LCD进行功能测试和质量控制,确保其正常工作和高质量。
测试和控制包括像素测试、电路测试、显示效果测试等等。
总结起来,TFT LCD的生产工艺包括制作基板、制作薄膜晶体管、制作液晶层、封装以及功能测试和质量控制。
每一个步骤都需要精确的工艺和设备,以确保生产出高质量的TFT LCD显示器。
tft工艺流程

tft工艺流程TFT工艺流程TFT(薄膜晶体管)工艺是一种用于制造液晶显示器的关键技术,它通过在薄膜基底上制造晶体管阵列来控制液晶分子的取向和排列,从而实现显示功能。
TFT工艺流程是液晶显示器制造中的核心步骤之一,下面将详细介绍TFT工艺流程的各个环节。
1. 基底清洗和涂覆:首先,将基底(通常是玻璃基板)进行清洗,确保表面干净无尘。
然后,在基底上涂覆一层透明导电膜,通常使用氧化铟锡(ITO)材料。
这一步骤是为了后续制造晶体管的通道层做准备。
2. 通道层制造:在透明导电膜上使用光刻技术定义晶体管的通道层。
光刻技术通过覆盖光刻胶、曝光、显影等步骤,在导电膜上形成一系列细小的通道结构。
通道层通常采用非晶硅(a-Si)或低温多晶硅(LTPS)材料制造。
3. 金属电极制造:在通道层上制造源极和漏极电极。
这一步骤通常使用物理气相沉积(PVD)或化学气相沉积(CVD)技术,在通道层上蒸发或沉积金属材料,形成电极。
4. 门电极制造:在通道层和金属电极之间形成一层绝缘层,以隔离门电极和源极漏极。
绝缘层通常使用氧化硅或氮化硅材料制造。
5. 液晶填充:将液晶材料填充在两块基底之间形成液晶层。
液晶材料通常是有机分子,具有特殊的电光特性,能够在电场作用下改变光的透过性。
6. 封装:将两块基底粘合在一起,并在边缘封装处留下一个小孔,用于注入液晶材料。
封装过程需要保证基底之间的间距均匀,并且封装材料具有良好的粘合性和耐高温性。
7. 背光模组组装:将制造好的液晶模组与背光模组组装在一起,形成完整的液晶显示器。
背光模组通常由冷阴极荧光灯(CCFL)或LED(发光二极管)组成,用于提供背光照明。
8. 检测和测试:对制造好的液晶显示器进行检测和测试,确保各个模块和功能正常工作。
测试包括亮度、对比度、响应时间等参数的测试。
TFT工艺流程是一系列复杂的步骤,每个步骤都需要精确的控制和严格的质量检验。
只有在每个环节都做好了工艺控制和质量管理,才能制造出高质量的液晶显示器。
TFT-LCD制造流程及光学规格介绍--080527
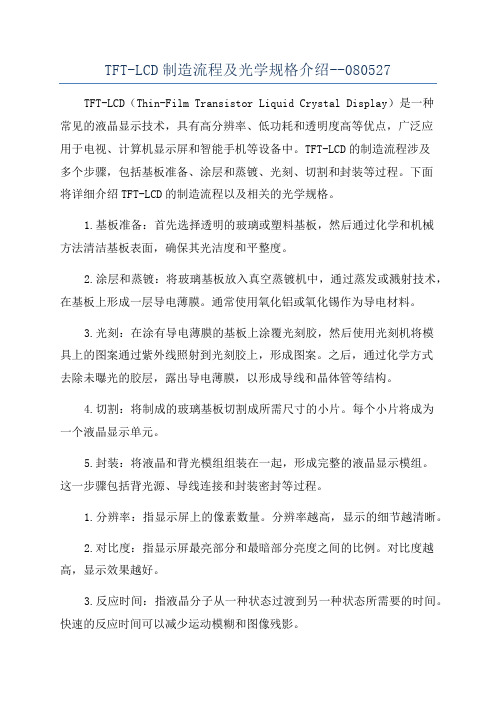
TFT-LCD制造流程及光学规格介绍--080527 TFT-LCD(Thin-Film Transistor Liquid Crystal Display)是一种常见的液晶显示技术,具有高分辨率、低功耗和透明度高等优点,广泛应用于电视、计算机显示屏和智能手机等设备中。
TFT-LCD的制造流程涉及多个步骤,包括基板准备、涂层和蒸镀、光刻、切割和封装等过程。
下面将详细介绍TFT-LCD的制造流程以及相关的光学规格。
1.基板准备:首先选择透明的玻璃或塑料基板,然后通过化学和机械方法清洁基板表面,确保其光洁度和平整度。
2.涂层和蒸镀:将玻璃基板放入真空蒸镀机中,通过蒸发或溅射技术,在基板上形成一层导电薄膜。
通常使用氧化铝或氧化锡作为导电材料。
3.光刻:在涂有导电薄膜的基板上涂覆光刻胶,然后使用光刻机将模具上的图案通过紫外线照射到光刻胶上,形成图案。
之后,通过化学方式去除未曝光的胶层,露出导电薄膜,以形成导线和晶体管等结构。
4.切割:将制成的玻璃基板切割成所需尺寸的小片。
每个小片将成为一个液晶显示单元。
5.封装:将液晶和背光模组组装在一起,形成完整的液晶显示模组。
这一步骤包括背光源、导线连接和封装密封等过程。
1.分辨率:指显示屏上的像素数量。
分辨率越高,显示的细节越清晰。
2.对比度:指显示屏最亮部分和最暗部分亮度之间的比例。
对比度越高,显示效果越好。
3.反应时间:指液晶分子从一种状态过渡到另一种状态所需要的时间。
快速的反应时间可以减少运动模糊和图像残影。
4.视角:指从不同角度观察显示屏时,图像依然能够保持良好的可视性。
广视角意味着观看者可以从不同角度获得清晰的图像。
5.亮度:显示屏的最大亮度水平。
高亮度可以提升显示效果,使图像更加鲜艳。
总结起来,TFT-LCD的制造流程包括基板准备、涂层和蒸镀、光刻、切割和封装等步骤。
而TFT-LCD的光学规格涉及分辨率、对比度、反应时间、视角和亮度等方面。
通过这些制造流程和光学规格的控制,可以生产出高质量的TFT-LCD显示屏。
- 1、下载文档前请自行甄别文档内容的完整性,平台不提供额外的编辑、内容补充、找答案等附加服务。
- 2、"仅部分预览"的文档,不可在线预览部分如存在完整性等问题,可反馈申请退款(可完整预览的文档不适用该条件!)。
- 3、如文档侵犯您的权益,请联系客服反馈,我们会尽快为您处理(人工客服工作时间:9:00-18:30)。
第二章TFT 显示器的制造工艺流程和工艺环境要求清洗—成膜—光刻—刻蚀—剥离阵列段是从投入白玻璃基板,到基板上电气电路制作完成。
具体见下图:CF 工序是从投入白玻璃基板,到黑矩阵、三基色及ITO 制作完成。
具体见下成膜[膜[Glass 基[PR 塗布曝光 [Mask現像 刻蚀 剥離[TFT 基重复[Glass 基Cell工序是从将TFT基板和CF基板作定向处理后对贴成盒,到切割成单粒后贴上片光片。
具体见下图:Module工序是从LCD屏开始到驱动电路制作完成,形成一个显示模块。
具体示意图如下:第一节阵列段流程一、主要工艺流程和工艺制程(一)工艺流程上海天马采用背沟道刻蚀型(BCE)TFT显示象素的结构。
具体结构见下图:C'Storage capacitorITO pixel electrodeCros-s ection -C’a-Si TFTSelect lineData line对背沟道刻蚀型TFT结构的阵列面板,根据需要制作的膜层的先后顺序和各层膜间的相互关系,其主要工艺流程可以分为5个步骤(5次光照):第一步栅极(Gate)及扫描线形成具体包括:Gate层金属溅射成膜,Gate光刻,Gate湿刻等工艺制程(各工艺制程的具体介绍在随后的章节中给出)。
经过这些工艺,最终在玻璃基板上形成扫描线和栅电极,即Gate电极。
工艺完成后得到的图形见下图:第二步 栅极绝缘层及非晶硅小岛(Island )形成具体包括:PECVD 三层连续成膜,小岛光刻,小岛干刻等工艺制程(各工艺制程的具体介绍在随后的章节中给出)。
经过这些工艺,最终在玻璃基板上形成TFT 用非晶硅小岛。
工艺完成后得到的图形见下图:CCross-section CC’CSiN第三步 源、漏电极(S/D )、数据电极和沟道(Channel )形成 具体包括:S/D 金属层溅射成膜,S/D 光刻,S/D 湿刻,沟道干刻等工艺制程(各工艺制程的具体介绍在随后的章节中给出)。
经过这些工艺,最终在玻璃基板上形成TFT 的源、漏电极、沟道及数据线。
到此,TFT 已制作完成。
工艺完成后得到的图形见下图:第四步 保护绝缘层(Passivition )及过孔(Via )形成具体包括:PECVD 成膜,光刻,过孔干刻等工艺制程(各工艺制程的具体介绍在随后的章节中给出)。
经过这些工艺,最终在玻璃基板上形成TFT 沟道保护绝缘层及导通过孔。
工艺完成后得到的图形见下图:C第五步 透明象素电极ITO 的形成具体包括:ITO 透明电极层的溅射成膜,ITO 光刻,ITO 湿刻等工艺制程(各工艺制程的具体介绍在随后的章节中给出)。
经过这些工艺,最终在玻璃基板上形成透明象素电极。
至此,整个阵列工序制作完成。
工艺完成后得到的图形见下图:C至此,整个阵列工序制作完成。
简单来说5次光照的阵列工序就是:5次成膜+5次刻蚀。
(二)工艺制程在上面的工艺流程中,我们提到,阵列的工艺流程是成膜、光刻、刻蚀等工艺制程的反复使用。
以下就这些工艺制程作具体的介绍。
1、成膜顾名思义,成膜就是通过物理或化学的手段在玻璃基板的表面形成一层均匀的覆盖层。
在TFT阵列制作过程中,我们会用到磁控溅射(Sputter,或称物理气相沉积PVD)和等离子体增强型化学气相沉积(PECVD)。
A)磁控溅射(Sputter)溅射是在真空条件下,用He气作为工作气体。
自由电子在直流DC电场的作用下加速获得能量,高能电子碰撞He原子,产生等离子体。
He离子在DC电场的作用下,加速获得能量,轰击在靶材上,将靶材金属或化合物原子溅射出来,沉积在附近的玻璃基板上,最后形成膜。
磁场的作用是控制等离子体的分布,使成膜均匀。
磁控溅射的原理示意图如下:生产用磁控溅射设备如下图:具体溅射原理的介绍和详细的设备介绍参见后面相关的章节。
B )PECVDPECVD 是通过化学反应在玻璃基板表面形成透明介质膜。
等离子体的作用是使反应气体在低温下电离,使成膜反应在低温下得以发生。
其原理示意图如下:Ar S u b s t r a t e h o l d e rT a r g e t h o l d e r+plasmaGlass TargetRF power 13.56 MHz ~ 1 mTorrUsed for ITO (Indium Tin Oxide transparent conductor) and for metals (Al, Mo, Ti, Cr, etc.)RF power ~ 100 mW/cm PLASMA ~1 Torr2)T=300 ºC substrate成各类膜所使用得化学气体见下表: Feed gas Material FunctionSiH4, H2a-Si Semiconductor SiH4, N2, NH3 Si3N4 Gate insulator, passivationSiH4, N20 SiO2 Gate insulator, passivationSiH4, PH3, H2 n+ a-Si Contact layer at source and drain典型的PECVD 设备如下图:c ChamberChamberC L Transfer Transfer Pr o e s s C ha mb e r Process Heating P r oc e s s h a m b e ro a d /u nl o a d L o a d /u n l o a dCassette stationrobotrobot具体PECVD 原理的介绍和详细的设备介绍参见后面相关的章节。
2、光刻:涂胶、图形曝光、显影光刻的作用是将掩模版(Mask )上的图形转移到玻璃表面上,形成PR Mask 。
具体通过涂胶、图形曝光、显影来实现。
见以下示意图:Layer to be patternedPhotoresist coatingExposure through maskPhotoresist developingPhotoresist strippingEtching of layerA) 涂胶在玻璃表面涂布一层光刻胶的过程叫涂胶。
对于小的玻璃基板,一般使用旋转涂布的方式。
但对大的基板,一般使用狭缝涂布的方式。
见以下示意图:B) 图形曝光Resist dispenserPhotoresistSpin coating Slit (extrusion) coating涂胶后的玻璃基板经干燥、前烘后可以作图形曝光。
对于小面积的基板,可以采用接近式一次完成曝光。
但对大面积的基板,只能采用多次投影曝光的方式。
下图是Canon曝光机的工作原理图:由于大面积的均匀光源较难制作,Canon采用线状弧形光源。
通过对Mask和玻璃基板的同步扫描,将Mask上的图形转移到玻璃基板上。
C) 显影经图形曝光后,Mask上的图形转移到玻璃基板上,被光阻以潜影的方式记录下来。
要得到真正的图形,还需要用显影液将潜影显露出来,这个过程叫显影。
如果使用的光阻为正性光阻,被UV光照射到的光阻会在显影过程中被溶掉,剩下没有被照射的部分。
显影设备往往会被连接成线,前面为显影,后面为漂洗、干燥。
示意图如下:3、刻蚀:湿刻、干刻刻蚀分为湿刻和干刻两种。
湿刻是将玻璃基板浸泡于液态的化学药液中,通过化学反应将没有被PR 覆盖的膜刻蚀掉。
湿刻有设备便宜、生产成本低的优点,但由于刻蚀是各向同性的,侧蚀较严重。
干刻是利用等离子体作为刻蚀气体,等离子体与暴露在外的膜层进行反应而将其刻蚀掉。
等离子体刻蚀有各向异性的特点,容易控制刻蚀后形成的截面形态;但但高能等离子体对膜的轰击会造成伤害。
湿刻与干刻的原理见下图:湿刻的设备一般与后面清洗、干燥的设备连成线,见下图:干刻设备与PVD 及PECVD 设备一样,一般采用多腔体枚叶式布局。
由于设备内是真空环境,玻璃基板进出设备需要1-2个减压腔。
其余腔体为工艺处理腔。
见以下示意图:Glass substratePhotoresist Glass substratePhotoresist Isotropic wet etchingAnisotropic dry etchingEtched layer Etched layer Wet etching vs. dry etching (RIE)PhotoresistGlass substratePhotoresist O 2containing etching gasEtched layer Glass substratePhotoresistEtched layerGlass substratePhotoresistEtched layer一般金属膜采用湿刻,介质膜采用干刻。
4、脱膜刻蚀完成后,需要将作掩模的光阻去除,去除光阻的过程叫脱膜。
一般脱膜设备会与其随后的清洗、干燥设备连线。
见下图:二、辅助工艺制程阵列工序的工艺流程中,除了以上介绍的主要工艺制程外,为了监控生产线的状态,提高产品的合格率,方便对产品的管理和增加了一些辅助的制程,如:清洗、打标及边缘曝光、AOI、 Mic/Mac观测、成膜性能检测、电测等。
以下就这些辅助工艺制程逐一作个简单介绍。
1、清洗清洗,顾名思义就是将玻璃基板清洗干净。
这是整个LCD工艺流程中使用最频繁的工艺制程。
在每次成膜前及湿制程后都有清洗。
清洗有湿洗和干洗,有物理清洗和化学清洗。
其作用和用途详见下表:具体在工艺流程中,玻璃基板流入生产线前有预清洗;每次成膜前有成膜前清洗;每次光阻涂布前有清洗;每次湿刻后及脱膜后也有清洗。
一般清洗设备的结构如下:由于清洗设备的结构与湿刻及脱膜设备的结构非常相识,所以这三个制程往往统称为湿制程。
2、打标及边缘曝光为了方便生产线的管理,我们需要对在生产线流通的每一张玻璃基板和Panel打上ID,这是通过打标制程来完成的。
通常打标制程会放在栅极光刻制程中,即栅极图形曝光后,显影前。
打标一般采用激光头写入。
随着玻璃基板的增大,曝光机的制作和大面积均匀光源的获得变得较难。
为了有效利用曝光设备,在图形曝光时只对玻璃基板中间有图形的有效区域进行曝光。
之后采用一种不需要Mask的边缘曝光设备对边缘区域曝光,然后去做显影。
这一过程叫边缘曝光。
3、自动光学检测(AOI)为了提高产品的合格率,在每次显影后和刻蚀后,一般会作一次光学检测。
一般采用线性CCD对玻璃基板上的图形进行扫描,将扫描后的图像作计算机合成处理后,与设计图形作比对,以发现可能存在的问题。
此过程即称为自动光学检测。
其典型设备如下图:4、宏微观检查(MAC/MIC)微观检查主要是通过显微镜对AOI或其他检测过程中发现的问题作进一步观测确认。