电弧喷铝方案
大功率电弧锌铝伪合金喷涂技术及其应用
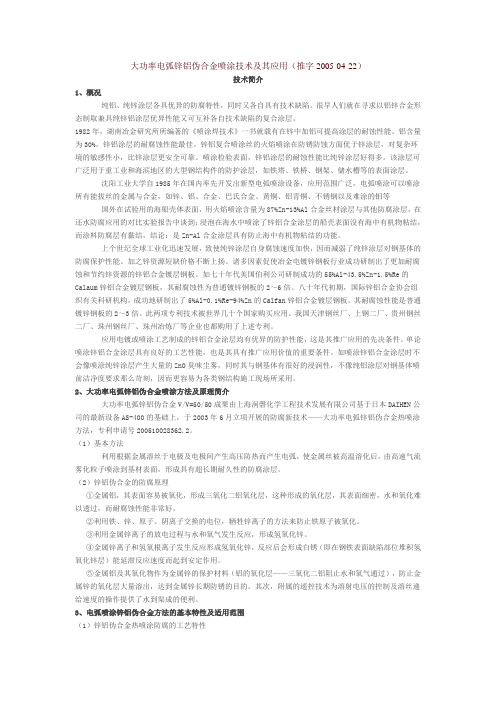
大功率电弧锌铝伪合金喷涂技术及其应用(推字2005-04-22)技术简介1、概况纯铝、纯锌涂层各具优异的防腐特性,同时又各自具有技术缺陷。
很早人们就在寻求以铝锌合金形态制取兼具纯锌铝涂层优异性能又可互补各自技术缺陷的复合涂层。
1982年,湖南冶金研究所所编著的《喷涂焊技术》一书就载有在锌中加铝可提高涂层的耐蚀性能。
铝含量为30%,锌铝涂层的耐腐蚀性能最佳。
锌铝复合喷涂丝的火焰喷涂在防锈防蚀方面优于锌涂层,对复杂环境的敏感性小,比锌涂层更安全可靠。
喷涂检验表面,锌铝涂层的耐蚀性能比纯锌涂层好得多。
该涂层可广泛用于重工业和海滨地区的大型钢结构件的防护涂层,如铁塔、铁桥、钢架、储水槽等的表面涂层。
沈阳工业大学自1985年在国内率先开发出新型电弧喷涂设备,应用范围广泛,电弧喷涂可以喷涂所有能拔丝的金属与合金,如锌、铝、合金、巴氏合金、黄铜、铝青铜、不锈钢以及难涂的钼等国外在试验用的海船壳体表面,用火焰喷涂含量为87%Zn-13%Al合金丝材涂层与其他防腐涂层,在还水防腐应用的对比实验报告中谈到;浸泡在海水中喷涂了锌铝合金涂层的船壳表面没有海中有机物粘结,而涂料防腐层有黏结,结论:是Zn-Al合金涂层具有防止海中有机物粘结的功能。
上个世纪全球工业化迅速发展,致使纯锌涂层自身腐蚀速度加快,因而减弱了纯锌涂层对钢基体的防腐保护性能。
加之锌资源短缺价格不断上扬。
诸多因素促使冶金电镀锌钢板行业成功研制出了更加耐腐蚀和节约锌资源的锌铝合金镀层钢板。
如七十年代美国伯利公司研制成功的55%Al-43.5%Zn-1.5%Re的Calaum 锌铝合金镀层钢板,其耐腐蚀性为普通镀锌钢板的2~6倍。
八十年代初期,国际锌铝合金协会组织有关科研机构,成功地研制出了5%Al-0.1%Re-94%Zn的Calfan锌铝合金镀层钢板。
其耐腐蚀性能是普通镀锌钢板的2~3倍。
此两项专利技术被世界几十个国家购买应用。
我国天津钢丝厂、上钢二厂、贵州钢丝二厂、珠州钢丝厂、珠州冶炼厂等企业也都购用了上述专利。
超音速电弧喷涂施工方案
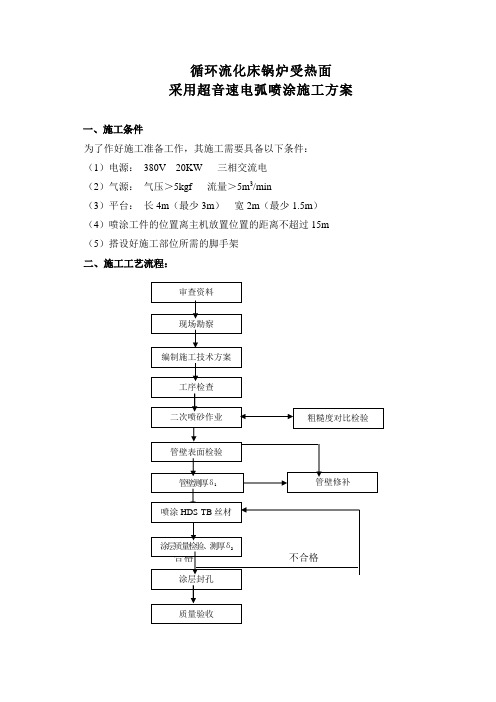
循环流化床锅炉受热面采用超音速电弧喷涂施工方案一、施工条件为了作好施工准备工作,其施工需要具备以下条件:(1)电源:380V 20KW 三相交流电(2)气源:气压>5kgf 流量>5m3/min(3)平台:长4m(最少3m)宽2m(最少1.5m)(4)喷涂工件的位置离主机放置位置的距离不超过15m (5)搭设好施工部位所需的脚手架二、施工工艺流程:三、施工技术规范:1、施工准备:①根据实际需要搭好脚手架。
②清除受热面上的大块焦、杂物等。
③对管壁需实施喷涂的部位进行全面的质量检查,如发现需要修整补强的部位应及时向甲方提出。
④利用现场已有条件进行设备就位、电气接线、气源管线连接及磨料回收帆布铺设工作。
2、表面预处理:表面预处理按照GB11373-89《热喷涂金属件表面预处理通则》进行,其处理的好坏直接影响喷涂层的结合强度。
①喷砂前,对非有效表面采用遮蔽带、硬木板或橡胶等物进行遮蔽保护。
并预留过渡区域,以保证涂层边缘光滑过渡。
②磨料选择及使用:喷砂材料应选用质坚有棱角的金刚砂必须净化,使用前应经筛选,砂内粘土及细粉尘含量不应大于5%,不得含有油污。
喷砂前要晾晒干燥,含水量应不大于1%,并存放干燥,防止受潮、雨淋、砂内混入杂质。
所用砂粒必须清洁、干燥,喷砂区域设围护及其它回收措施,确保不污染周围环境,经质量工程师确认后方可进行喷砂。
③喷砂装置:采用压力式喷砂设备④压缩空气:利用现场气源或自备空压机,空气压力范围为0.5—0.6Mpa,气体流量控制在6m3/min左右。
⑤操作方法:喷砂距离100—300mm;喷砂角度:与基体60—80℃;每次喷砂5-6m2。
除锈应从下至上进行,将凹凸不平的受热面打磨光滑平整后立即喷砂。
使表面清洁度达到GB8923-88《涂装前钢材表面锈蚀等级和除锈等级》规定的Sa3.0级,即完全去除钢材表面的锈、氧化皮、油污等附着物,并露出灰白色金属光泽,其粗糙度达到GB11373-89《热喷涂金属表面预处理通则》规定的R Z50-90μm。
电弧喷涂施工方案

电弧喷涂施工方案 The manuscript was revised on the evening of 2021电弧喷涂技术方案一)电弧喷涂的特点电弧喷涂防腐防磨原理是利用电弧喷涂设备,对两根带电的金属丝(如锌、铝等)进行加热、熔融、雾化、喷涂形成防腐防磨涂层,外加有机封闭涂层的长效防腐复合涂层,该涂层的显着特点是:(1)具有较长久的耐腐蚀耐磨寿命,其寿命可达到10个月以上,同时该防腐涂层在10个月使用期内无须其它任何维护;(2)电弧喷涂层与金属基体具有优良的涂层结合力。
二)喷涂锌铝合金的特点1、抗腐蚀抗磨性能好2、涂层结合力好在锌复合镀层表面涂状涂料,因其镀层表面具有复杂的表面形状特征,使其涂膜的密着力是一般钢材4倍,而耐食性能是常规涂装的2倍以上;3、具有良好的工艺性能喷涂纯锌涂层时会产生大量的enon臭味尘雾,因而容易使操作者得职业病,故要做好劳动保护措施。
喷锌有较高的性能价格比为达到设计上的防腐年限,对喷涂层有厚度的要求。
一般控制在120UM.防腐蚀涂装机械设备仪器要求:一)喷砂工艺根据钢材表面锈蚀程度而定。
※现场喷砂施工喷砂除锈要达到钢结构防锈防腐的工艺技术要求、施工质量要求,施工中必定要产生一定的噪声及粉尘污染。
作业要求1)采用石英砂材料,2)为防止喷砂时灰尘外逸,影响周边环境,必要时搭建喷砂棚。
二)电弧喷锌工艺1)检验依据国家标准gb/t9793-1997《金属和其它无机覆盖层热喷涂锌、铝及其它合金涂层》。
gb9795-88《热喷涂合金涂层》2)检测方法①材质:材质具有出厂合格证。
②外观:a)目视法,喷涂层外关应均匀一致,无漏喷和附着不牢的涂层。
无大熔融颗粒粘附。
b)涂层均匀,致密,无起皮,鼓泡、大容滴、大颗粒、裂纹、掉块等缺陷。
③厚度:采用测厚仪进行检查,涂层厚度均匀,平均厚度在设计厚度的+15um之间.基准表面至少应选择三处,在特大的有效表面上,以10m2为一个测量单元,即每10m2有效表面上至少应选取基准表面三处。
铝制发动机缸体内壁电弧热喷涂工艺及涂层性能的研究
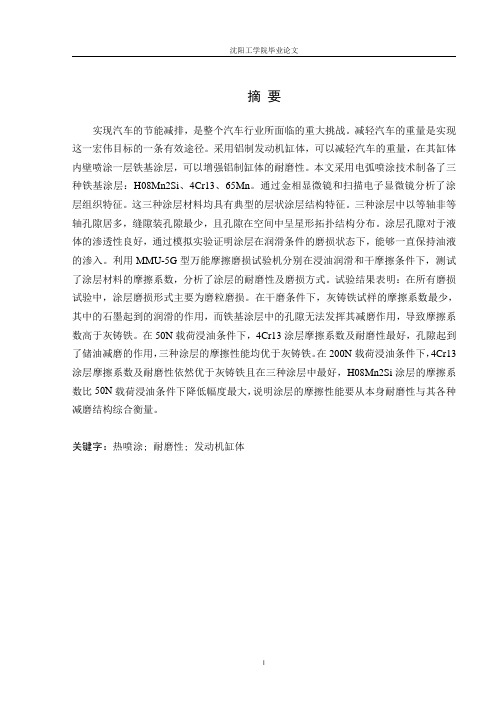
摘要实现汽车的节能减排,是整个汽车行业所面临的重大挑战。
减轻汽车的重量是实现这一宏伟目标的一条有效途径。
采用铝制发动机缸体,可以减轻汽车的重量,在其缸体内壁喷涂一层铁基涂层,可以增强铝制缸体的耐磨性。
本文采用电弧喷涂技术制备了三种铁基涂层:H08Mn2Si、4Cr13、65Mn。
通过金相显微镜和扫描电子显微镜分析了涂层组织特征。
这三种涂层材料均具有典型的层状涂层结构特征。
三种涂层中以等轴非等轴孔隙居多,缝隙装孔隙最少,且孔隙在空间中呈星形拓扑结构分布。
涂层孔隙对于液体的渗透性良好,通过模拟实验证明涂层在润滑条件的磨损状态下,能够一直保持油液的渗入。
利用MMU-5G型万能摩擦磨损试验机分别在浸油润滑和干摩擦条件下,测试了涂层材料的摩擦系数,分析了涂层的耐磨性及磨损方式。
试验结果表明:在所有磨损试验中,涂层磨损形式主要为磨粒磨损。
在干磨条件下,灰铸铁试样的摩擦系数最少,其中的石墨起到的润滑的作用,而铁基涂层中的孔隙无法发挥其减磨作用,导致摩擦系数高于灰铸铁。
在50N载荷浸油条件下,4Cr13涂层摩擦系数及耐磨性最好,孔隙起到了储油减磨的作用,三种涂层的摩擦性能均优于灰铸铁。
在200N载荷浸油条件下,4Cr13涂层摩擦系数及耐磨性依然优于灰铸铁且在三种涂层中最好,H08Mn2Si涂层的摩擦系数比50N载荷浸油条件下降低幅度最大,说明涂层的摩擦性能要从本身耐磨性与其各种减磨结构综合衡量。
关键字:热喷涂;耐磨性;发动机缸体AbstractTo realize the energy saving and emission reduction,is a major challenge facing the entire automotive industry.Reduce the weight of the car is an effective way to achieve this ing aluminum engine block,can reduce the weight of the car,in the cylinder wall coating a layer of Fe based coating,can enhance the wear resistance of aluminum cylinder. This paper uses three kinds of Fe based coating by arc spraying technology system: H08Mn2Si,4Cr13,65Mn.The analysis of the microstructure of the coating by metallographic microscope and scanning electron microscope.These three kinds of coating materials have the typical characteristics of layered coating structure.Three kinds of coating with equiaxed non equiaxed pores are arranged,slit pores at least,and the pore space in a star topology.The pores of the coatings for liquid permeability good,wear condition through simulation experiments prove that coating on the lubrication condition,has been able to keep the oil infiltration.Universal friction and wear testing machine were soaked in oil lubrication and dry friction condition by using MMU-5G type,friction coefficient of the coating material were tested,analyzed the wear resistance and wear mode of coatings.The test results show that:in all wear test,the wear mechanisms are mainly abrasive wear.In dry friction condition,and the Fe based coating in the pores and unable to play its role in reducing wear,the friction coefficient is higher than that of gray cast iron.In the loading of50N oil immersed conditions, friction coefficient and wear resistance of4Cr13coating is the best,the pore to reduce abrasion of oil,the friction properties of three kinds of coatings are better than that of grey cast iron.In the loading of200N oil immersed conditions,the friction coefficient and wear resistance of4Cr13coating is better than the gray cast iron and the three kinds of coatings in the best,the friction coefficient of H08Mn2Si coating than50N under the condition of oil immersed load decrease,the friction properties of the coating itself from the wear resistance and antifriction structure comprehensive measure.Keywords:thermal spraying;wear resistance;engine block目录摘要 (I)Abstract (II)第1章绪论 (1)1.1汽车发动机材料的发展 (1)1.2热喷涂技术 (2)1.3电弧喷涂技术 (2)1.3.1电弧喷涂技术的原理及特点 (2)1.3.2热喷涂技术的优点 (3)1.3.3热喷涂技术的缺点 (4)1.4发动机缸体喷涂技术 (5)第2章实验仪器、材料及方法 (6)2.1实验仪器 (6)2.2涂层材料 (6)2.3基体材料表面预处理 (7)2.4喷涂工艺 (7)2.5实验步骤 (9)第3章涂层的组织分析 (12)3.14Cr13涂层的组织形貌及物相分析 (12)3.208Mn2Si的组织形貌及物相分析 (12)3.365Mn涂层的组织形貌及物相分析 (13)第4章涂层硬度及磨损试验 (15)4.1涂层硬度 (15)4.2涂层的磨损试验 (16)4.2.1实验设备 (16)4.2.2实验步骤 (17)4.2.3载荷50N下干摩擦10min (17)4.3.4载荷50N浸油磨损2小时 (19)4.3.5载荷200N浸油磨损2小时 (21)4.4涂层横截面的观察 (23)4.5小结 (23)第5章结论 (25)参考文献 (26)第1章绪论1.1汽车发动机材料的发展环境保护,能源消耗是如今的焦点问题。
钢结构件电弧喷铝工艺

钢结构件电弧喷铝工艺11.1概述位于沿海地区,海洋性大气对钢结构的腐蚀性强,外部环境非常恶劣,同时养护条件较差,为减少养护工作量,延长涂装体系的使用寿命,采用金属热喷涂防护体系。
具体涂装方案如下:注:1.表中漆膜厚度均指干膜厚度。
2.电弧喷铝的铝丝化学成份按GB/T3190-1996标准中L2要求,Al≥99.6%。
3.结构出厂前涂面漆一道,现场施工完后先对现场焊接区域进行手工除锈,依次补充涂装,然后全桥整体作清洗后涂第二道面漆。
11.2施工方案和场地平面布置㈠总体施工方案⑴工件由平板运输车运进涂装车间并支撑在1米高的支撑架上进行防腐施工(机械除锈、喷砂、电弧喷涂和第一道油漆),施工完毕工件运出涂装车间放置在工件存放周转场地,在工件存放地完成剩余油漆涂装,直至达到出厂要求。
⑵首先在存件区对待涂装工件进行净化处理,清理焊渣,清洗油污。
然后运输一节工件进涂装厂房进行防腐。
先对工件外表面喷砂除锈,喷砂完毕,清理钢砂后进行电弧喷铝,喷铝完毕后移支撑架对支撑架下处理不到的部位进行喷砂除锈和电弧喷铝,然后对内表面进行机械除锈。
机械除锈完毕后对铝涂层封闭一道,同时对内表面喷涂第一道油漆。
一节工件完成后继续运进另一工件至涂装车间进行下一轮工件防腐施工。
油漆干燥后工件运出涂装车间到存放区完成后几道油漆涂装,剩最后一道面漆待整桥施工完毕后在桥址现场整体涂装以保证大桥外观美观。
⑶为了提高防腐涂层质量,使电弧喷铝涂层性能良好,涂层细致、致密,使用二次雾化喷枪进行电弧喷涂。
⑷运到现场的工件经安装加工单位拼焊完毕后进行焊缝和破损处防腐涂装,不同部位均采用与原涂装方案相同的工艺进行防腐蚀施工,以保证钢结构防腐蚀涂层的完整性。
焊缝防腐施工与拼装进度同步,并利用拼装单位的拼装焊接作业平台、临时设施和起吊运输工具。
⑸整拱安装完毕,焊缝防腐处理结束后对整桥涂装最后一道面漆,面漆涂装利用现场的起吊设备。
11.3防腐蚀涂装施工工艺要求㈠外表面涂装工艺要求⑴表面净化用有机溶剂或金属清洗剂清洗钢结构表面油污,得到无油、无水、无污物、无锈斑及其他包括可溶性盐在内的洁净表面。
电弧喷铝防腐要求及技术数据
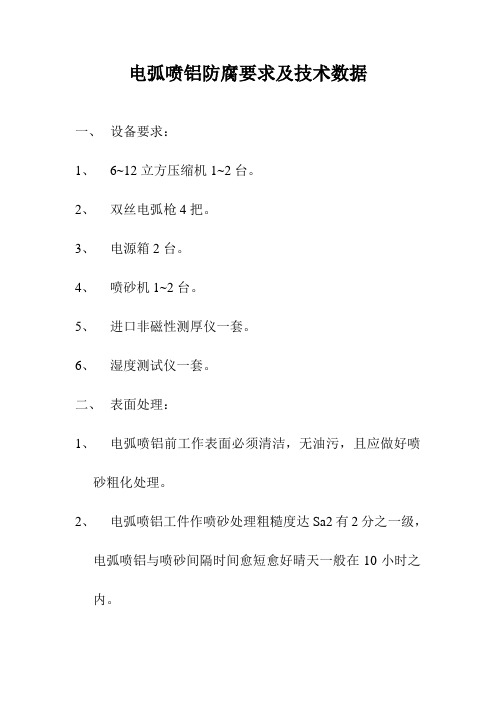
电弧喷铝防腐要求及技术数据
一、设备要求:
1、6~12立方压缩机1~2台。
2、双丝电弧枪4把。
3、电源箱2台。
4、喷砂机1~2台。
5、进口非磁性测厚仪一套。
6、湿度测试仪一套。
二、表面处理:
1、电弧喷铝前工作表面必须清洁,无油污,且应做好喷
砂粗化处理。
2、电弧喷铝工件作喷砂处理粗糙度达Sa2有2分之一级,
电弧喷铝与喷砂间隔时间愈短愈好晴天一般在10小时之内。
三、表面电弧喷铝要求:
1、对处理后对工件进行电弧喷铝加工要求涂层必须均
匀,不起绉及裂纹,掉块现象,并没有影响涂层的缺陷。
2、电弧喷铝层厚度大于150μ(用非磁性测厚仪测量)。
3、涂层结合强度可采用切格法试验,对多块铝涂层的试
验平均结合强度不得小于0.6KG/MM平方。
四、表面涂层耐腐蚀性:
电弧喷铝涂层≥150μ并加封闭常规用开林造漆厂842环氧云铁底漆,前提之下可保用20年(根据试验大气腐蚀每年平均5——10μ)。
以上是电弧喷铝的技术要求及参数。
注:如果考虑防腐及结合强度,可采用喷锌打底,电弧喷铝覆盖;842环氧云铁底漆封闭可能更好(以上供参考)。
上海南福五金喷涂塑料厂。
电弧喷涂铝涂层工艺参数优化和涂层结构分析

表 1 电弧喷涂铝涂层工艺参数因素水平表
因素 水平
1 2 3
喷涂电 流 I/ A
100 120 150
喷涂电 压 U/ V
28 32 35
雾化空气 压力 P/ MPa
0. 4 0. 5 0. 6
喷涂距离 L/ mm 150 200 250
表 2 正交试验设计方案及实验结果
试验 喷涂电 喷涂电 雾化空气 喷涂距 结合强度
同的 。极差越大 ,说明这个因素的水平改变时对试
验指标的影响越大 。极差最大的那个因素就是需
要考虑的主要因素 。按极差大小排列出各因素对
结合 强 度 指 标 影 响 的 主 次 顺 序 为 : PL I U ( 主 →
次) ;各 因素对 孔隙率 指 标 影 响 的 主 次 顺 序 为 :
PL I U (主 →次) 。
提高了 2. 30 %。从孔隙率来看 ,a 组涂层的孔隙率比
优化前降低了大约 6. 64 % ,b 组涂层孔隙率最低 ,比
优化前降低了 9. 88 %。综合考虑结合强度和孔隙率
2 个因素 ,确定优化后 b 组参数 I3 U2 P3 L 1 为最优工 艺参数 。
图 1 结合强度效应与因素水平关系图 图 2 孔隙率效应与因素水平关系图
p rocessing parameters were optimized by ort hogo nal experimental design. The optimized p rocessing parameters were : sp ray current 150A , sp ray voltage 32V , atomizing air p ressure 0. 6M Pa , and sp ray distance 150mm. The result s showed t hat t here were 9. 88 % decrease in coating poro sity and 2. 30 % increase in bond st rengt h after optimization. The p rime reason was t hat large elect ric arc power was favorable to t he interf usion of aluminum particles. Sp ray current and sp ray voltage had different effect s on t he increase of arc power. Increase of sp ray current imp roved t he quality of coatings more effectively t han sp ray voltage.
钢结构件电弧喷铝工艺

钢结构件电弧喷铝工艺11.1概述位于沿海地区,海洋性大气对钢结构的腐蚀性强,外部环境非常恶劣,同时养护条件较差,为减少养护工作量,延长涂装体系的使用寿命,采用金属热喷涂防护体系。
具体涂装方案如下:注:1.表中漆膜厚度均指干膜厚度。
2.电弧喷铝的铝丝化学成份按GB/T3190-1996标准中L2要求,Al≥99.6%。
3.结构出厂前涂面漆一道,现场施工完后先对现场焊接区域进行手工除锈,依次补充涂装,然后全桥整体作清洗后涂第二道面漆。
11.2施工方案和场地平面布置㈠总体施工方案⑴工件由平板运输车运进涂装车间并支撑在1米高的支撑架上进行防腐施工(机械除锈、喷砂、电弧喷涂和第一道油漆),施工完毕工件运出涂装车间放置在工件存放周转场地,在工件存放地完成剩余油漆涂装,直至达到出厂要求。
⑵首先在存件区对待涂装工件进行净化处理,清理焊渣,清洗油污。
然后运输一节工件进涂装厂房进行防腐。
先对工件外表面喷砂除锈,喷砂完毕,清理钢砂后进行电弧喷铝,喷铝完毕后移支撑架对支撑架下处理不到的部位进行喷砂除锈和电弧喷铝,然后对内表面进行机械除锈。
机械除锈完毕后对铝涂层封闭一道,同时对内表面喷涂第一道油漆。
一节工件完成后继续运进另一工件至涂装车间进行下一轮工件防腐施工。
油漆干燥后工件运出涂装车间到存放区完成后几道油漆涂装,剩最后一道面漆待整桥施工完毕后在桥址现场整体涂装以保证大桥外观美观。
⑶为了提高防腐涂层质量,使电弧喷铝涂层性能良好,涂层细致、致密,使用二次雾化喷枪进行电弧喷涂。
⑷运到现场的工件经安装加工单位拼焊完毕后进行焊缝和破损处防腐涂装,不同部位均采用与原涂装方案相同的工艺进行防腐蚀施工,以保证钢结构防腐蚀涂层的完整性。
焊缝防腐施工与拼装进度同步,并利用拼装单位的拼装焊接作业平台、临时设施和起吊运输工具。
⑸整拱安装完毕,焊缝防腐处理结束后对整桥涂装最后一道面漆,面漆涂装利用现场的起吊设备。
11.3防腐蚀涂装施工工艺要求㈠外表面涂装工艺要求⑴表面净化用有机溶剂或金属清洗剂清洗钢结构表面油污,得到无油、无水、无污物、无锈斑及其他包括可溶性盐在内的洁净表面。
- 1、下载文档前请自行甄别文档内容的完整性,平台不提供额外的编辑、内容补充、找答案等附加服务。
- 2、"仅部分预览"的文档,不可在线预览部分如存在完整性等问题,可反馈申请退款(可完整预览的文档不适用该条件!)。
- 3、如文档侵犯您的权益,请联系客服反馈,我们会尽快为您处理(人工客服工作时间:9:00-18:30)。
设备内壁电弧喷铝工程施工方案中国化学建设工程第三建设有限公司2013年12月8日目录(请完善)一、工程概况 (1)二、编制依据 (1)三、施工准备 (1)四、施工程序、工艺及要求五、质量保证措施和质量保证体系六、进度计划控制措施七、安全保证体系及措施八、文明施工措施九、工程验收方案十、售后服务措施一、工程概况本工程位于。
等等。
这些请贵方填写。
喷铝一般有氧乙炔喷涂、普通电弧喷涂以及超音速电弧喷涂三种。
电弧喷涂对施工环境的要求较高,比如被处理基体表面要求达到Sa3级,粗糙度更是要求在70~100μm,且基体表面温度至少比露点高3℃以上才能进行喷涂施工。
但因其优良的防腐性能,因此还是被广泛地采用。
根据公司内部研究,决定在本工程中采用超音速电弧喷涂技术。
二、编制依据1、甲方招标文件中关于喷铝的技术要求。
2、GB9795—88《热喷涂铝及铝合金涂层》3、GB9796—88《热喷涂铝及铝合金涂层试验方法》4、GB8923—88《涂装前钢材表面锈蚀等级和除锈的等级》5、GB9793-1997《金属及非金属覆盖层一热喷涂锌、铝及其合金》三、施工准备(一)生产准备1、组织施工人员学习有关标准,规范,文件。
2、对施工人员进行有关质量方面的教育,树立以“质量求生存,以质量求发展”的思想,争取全优工程。
3、针对本工程施工特点,教育职工树立安全第一的思想和环保意识。
全面贯彻执行HSE管理规定,作到文明、安全施工,搞好本项施工任务。
4、生产准备计划根据工程特点认真抓好施工准备,使各项工作落到实处。
做好用料计划,如各种材料的牌号、规格、数量及技术指标由技术部在合同签定后三天内提出,以便采购人员早作准备,保证现场施工需要。
施工现场布置由工程管理部提出,并经甲方批准后实施。
公共关系由项目经理负责牵头,组织专人负责,提前做好。
全部施工准备于合同签定后十五天内做好。
生产准备框图(二)施工组织施工组织机构图(三)施工人员组织本工程主要为喷砂除锈、喷铝及油漆封闭工作内容,须配合安装进展情况,要求在机件制作完毕运抵本工地7日内完成喷砂除锈、喷铝及油漆封闭施工任务;具有很大的随机性,必须与甲方密切配合,随时跟踪。
严格按ISO9001标准(2000版)进行科学管理,合理施工,提高综合竞争力,争取达到业主满意的最高目标。
(四)材料1、钢玉砂,粒度均匀,硬度高,有棱角。
符合GB9793-1997的有关规定。
2、φ2mm—φ3mm铝丝,纯度>99.5%,铝丝必须有材质合格证及化验分析单。
符合GB3190-82标准。
3、喷铝层外表面的防腐封闭涂料为环氧树脂封闭漆,必须有产品合格证及检测报告单和生产厂家的产品说明。
4、铝丝、涂料必须按规范要求频率进行检验合格后方可施工。
(五)设备及仪器空气压缩机6—gM3 3台空气压缩机 1.5M3 2台电弧喷镀机3台油水分离具3台喷砂枪头10套高压无气喷涂机2套搅拌器1台交流电焊机1台轴流风机4台喷镀枪10把砂罐2台变压器220—24V 1台粗糙度仪1台湿膜测厚仪2台磁性测厚仪2台四、施工程序、工艺及要求(一)喷砂除锈1、喷砂的标准及工艺需求本工程需喷砂的质量级别为GB8923-88标准Sa3级,即彻底除去金属表面的油脂,氧化皮锈蚀产物等一切杂质,表面无任何可见滞留物,呈现均一的金属本色。
喷砂处理后的金属表面应是均匀的粗糙面,粗糙度RZ40-80µm,不应产生明现的凹坑和正刺。
喷砂用固体颗粒、气体等符合GB9793-1997的规定。
喷砂环境相对湿度应≤80%。
室内温度要求>3℃,喷涂施工环境为5℃-35℃。
(1)磨料刚玉砂或石英砂的粒度全部通过7号筛,不能通过45号筛,30号筛余量不得小于40%。
(2)喷嘴入口最小空气压力0.6MPa(3)喷枪枪口直径应采用φ8mm(4)喷枪与被喷射面的角度为30--750(5)喷枪与被喷射面的距离为80—200mm.(6)表面湿度不应低于露点以上30C,环境湿度应高于50C。
(7)喷砂用的空气要经过过滤,保证不含油质,水分不超过0.3%。
2、喷砂施工方法需喷铝和的钢结构均采用喷砂除锈方法,除锈标准达到Sa3级(一级)为保证除锈效果及粗糙度,石子采用钢玉砂作为磨料,砂子必须堆放在防雨,防潮棚内,砂子不得含有杂物和其它杂质。
喷砂施工时,喷砂除锈机械连结调试正常后,在砂罐里面装满砂料,持枪、看砂罐人员做好准备,起动空压机,向砂罐送气,看砂罐人员先开气阀,再开砂阀,并根据进气和出砂量的大小调整砂阀气阀,使其达到最佳状态,持枪人员选好角度开始进行喷砂施工,每次施工完毕,进行自检,符合要求后请监理复检,通过验收后填写转序单进行下道工序的施工。
(1)喷射处理的工艺要点和工艺参数压缩空气工作压力:0.52~0.7MPa(5.2~7.0kgf/cm2)为宜,以0.7MPa最理想。
喷射角:喷射方向与工件表面法线之间夹角应以15°~30°为宜。
喷射距离:喷嘴到工作距离一般取100mm~300mm。
喷嘴:由于磨损,喷嘴孔口直径增大25%时宜更换。
磨料粒度:0.5~1.5mm。
(2)操作要点a.喷砂设备应尽量接近工件,以减少管路长度和压力损失,避免过多的管道磨损,也便于施工人员相互联系。
b.喷砂软管力求顺直,减少压力损失和磨料对弯折处软管的集中磨损。
对运用中必须弯折处,要经常调换磨损方向,使磨损比较均匀,延长软管使用寿命。
c.喷砂时为了防止漏喷和空放、减少移位次数、提高磨料利用率和工作效率,应该在施工前对整个结构全面考虑,合理安排喷射位置,拟定喷射路线。
d.喷嘴移动速度视空气压力、出砂量及结构表面污染情况灵活掌握,喷嘴移动速度过快,表面处理不彻底,再补喷时会使附近已喷好的表面遭到磨损,且降低工效。
喷嘴移动速度过慢,会使工件遭到削弱。
e. 料、气比例的调节:在喷射过程中,控制适当的料、气比例是提高工效、保证质量、降低磨料损耗和节省材料的关键。
磨料过少,不能充分利用压缩空气能量,工效低,不经济。
磨料过多,管路被大量砂粒占据,每个砂粒分配的能量就有限,喷射无力,砂耗大,工效低。
因此,必须根据空气压力,喷嘴直径,结构表面锈蚀状态,处理的质量,效率等情况经常而及时地加以调整。
既要避免砂阀过小,空气量大引起磨料供应太少而影响工效,又要防止砂阀过大,空气量过小引起喷射无力,灰尘弥漫,影响视线而盲目乱喷,漏喷和复喷。
f.喷射完毕,应用压缩空气吹净表面的灰尘。
g.下道工序进行前如发现基体金属表面被污染或返锈,应重新处理以达到要求的表面清洁度等级。
(3)喷射作业的安全防护喷射作业的安全与防护应该包括两个方面:喷射设备的安全,可靠性以及作业人员个体防护的完整、有效。
喷射作业是在一定压力下工作的,喷射时设备的各有关部件必须具有足够的耐压强度。
其中磨料罐必须由有劳动安全部门签发的设计许可证的单位设计,由有压力容器制造许可证的工厂制造。
使用过程中,不得随意在磨料罐上施行焊接和切割等影响其强度的任何作业。
磨料罐承受的压力一般不超过0.7MPa(7kgf/cm2)。
介质为空气,按我国的规定应作水压试验。
试验压力为设计工作压力的1.25倍,砂罐上的检查孔和添料口上的密封件要经常检查,若有损坏,应立即更换。
软管需接长的的地方,接头和喷砂软管联结必须牢靠,不能因喷砂软管的移动而发生错动。
由于磨料在喷嘴出口处的速度很高,可能超过200m/s。
这对人身安全造成了很大威胁,因此,无关人员必须远离工作场所。
喷射时喷嘴不能对人,喷射人员与管理砂罐人员之间,在喷射开始、停止或调整出砂量时,必须有简单明了的信号,而且操作者必须采取全身防护。
(二)电弧喷铝1、工艺要求钢结构电弧喷铝施工前表面要进行除锈、清理、平整处理,以利于涂层与钢基表面的牢固结合,达到防护效果。
钢材的表面清理与电弧喷铝非常重要,应在控制的湿度下进行,并迅速进行底层电弧喷铝。
钢材表面除锈方法和除锈等级应与采用的涂料相适应,喷砂达到GB8923-88标准Sa3级,粗糙度RZ40-80µm,电弧喷铝层厚度不小于200µm。
2、施工准备(1)喷涂前工人进行技术培训和技术交底,学习工艺和操作规程,考试合格后持证上岗。
(2)编制喷涂工艺进行工艺实验,呈报监利工程师审批,并通过确定喷涂基本参数。
(3)检查电源、空压机、储气罐、喷枪等设备的性能和运转情况。
(4)环境测定。
3、喷涂材料及设备(1)采用电弧喷铝时,应采用Φ2mm-3mm的铝丝,铝丝符合GB3190-82标准。
(2)喷涂用压缩空气采用无油润滑空气压缩机,所产生气体符合GB9795-88标准。
(3)喷铝主要采用电弧喷涂,其具有附着力强,喷涂均匀等优点。
(4)施工用铝丝必须按规范要求频率进行检验合格后方可喷涂。
4、电弧喷铝施工技术要求(1)喷铝层厚度为200µm,验收方法采用磁性测厚仪测定,所有工件要进行100%检查。
施工单位记录,监理抽查。
对表面积大于2平方米的工件,每件测十处,每处测五点,取平均值记录。
表面积小于2平方米的工件,每件测五处,取平均值记录。
(2)喷铝层目测检查,涂层表面应无杂质、翘皮、鼓泡、裂纹、大熔滴及脱皮等现象为合格;厚度用磁性测厚仪进行检查,测得的任何一点厚度值,不得低于设计规定的最小厚度值0.15mm。
(3)喷铝层外观和附着力检查,按GB9796—88〈热喷涂铝及铝合金涂层试验方法〉标准的规定进行。
(4)喷铝层孔隙率的检查:清除喷铝层表面的油污、尘土并进行干燥,然后用浸有20g/1000ml的氯化钾溶液的试纸覆盖在喷涂层上5~10min,试纸上出现的兰色斑点不应多于1~3点/cm2为合格。
(5)喷铝涂层的每道工序完成后,要经自检、专检合格后填写质量检验报告,报监理工程师抽检确认合格,方可进入下道工序。
5、电弧喷铝施工工艺电弧喷铝的原理是利用电弧使每一个喷涂的金属粒子都达到熔融状态,以获得金属粒子间可靠的结合及较高的自身强度。
电弧喷涂时用热能来加热熔融喷涂的丝材,同时以强烈的压缩空气吹向工件,在工件上形成致密的涂层,工件升温较低,不使用可燃气体,亦不用搬运部件。
电弧喷铝操作的技术指标主要控制好喷涂厚度、喷涂间距、喷涂速度几个方面:(1)喷涂前先进行必要的工艺实验,以便确定喷涂施工技术参数并选择合理的机械设备组合。
喷涂施工技术参数主要是单枪喷涂速度、每次喷涂厚度、喷涂夹角、喷涂间距、喷嘴型号、空气压力和重叠面积等,以保证喷涂层平整、光洁、均匀、粘结性良好,并达到设计要求。
(2)喷涂前用干净的高压空气吹去经过喷砂处理的基层表面的灰尘,经喷砂的钢结构表面应尽快进行喷铝,其间隔时间愈短愈好,以免钢材表面氧化形成锈膜。
晴天或干燥的天气间隔时间不得超过8h,雨天、潮湿天气或盐雾环境,时间不得超过2h。
(3)电弧喷枪出口处与工件表面距离在80-200mm 之间。