SPC不同行业弊端
SPC理论篇

控制图设计原理说明
控制图的原理 正态分布理论中有一个结论,对抽样检验 管理是很有用,即无论均值“μ”(AVG)和 标准差“σ”取何值,产品质量特性值: 落在 ( μ±3σ )之间的概率为:99.73% 落在 ( μ±3σ )之外的概率为: (1一99.73% ) = 0.27% 大于μ-3σ或小于μ+3σ的概率:
让我们做得更好
SPC 基 础 知 识
上海新策信息工程有限公司
理论学习目标
对SPC的再认识和理解
常用统计术语复习
控制图的基本理论整理
过程能力的研究角度
综合应用的能力扩展 协同能力的整体提高
对SPC的认识和理解
SPC兴起的历史背景
SPC的概念、观念及特点 SPC与质量检验的区别 SPC究竟是什么?技术+理念+粘合剂 SPC能发展到什么地步?
世上没有任何两件事(人员、产品)是 应用 SPC 一定能够指出过程中 完全一样的 (所以有变差) 最需要改善的细节地方 过程中被可被量化的指标所产生之波动 一定有警示作用的(所以可预测) 事件、产品的变异过程通常会依据一定 的模式而产生 (所以可控制)
SPC 关注的焦点
“量” 变 引 起“ 质 变”
结 过程中被量化的指标的起伏是造成“品质 论: ”“过程稳定”是SPC的关注方向 变异的主要根源,而“品质”变异的大、小, “过程细节”是SPC关注的焦 更 点 量化指标的起伏 “品质”变异 利润多少
是决定利润多少的关键。这种因果关系如下:
因 果 因 果
SPC 系统的特点
SPC肯定不是一张简单的分析图表生成或过程
S P C
常用数理统计术语
Words and Expressions
实施SPC的过程中十大误区

SPC是什么意思SPC即统计过程控制(Statistical Process Control)。
SPC主要是指应用统计分析技术对生产过程进行实时监控,科学的区分出生产过程中产品质量的随机波动与异常波动,从而对生产过程的异常趋势提出预警,以便生产管理人员及时采取措施,消除异常,恢复过程的稳定,从而达到提高和控制质量的目的。
在生产过程中,产品的加工尺寸的波动是不可避免的。
它是由人、机器、材料、方法和环境等基本因素的波动影响所致。
波动分为两种:正常波动和异常波动。
正常波动是偶然性原因(不可避免因素)造成的。
它对产品质量影响较小,在技术上难以消除,在经济上也不值得消除。
异常波动是由系统原因(异常因素)造成的。
它对产品质量影响很大,但能够采取措施避免和消除。
过程控制的目的就是消除、避免异常波动,使过程处于正常波动状态。
统计过程控制(SPC)是一种借助数理统计方法的过程控制工具。
它对生产过程进行分析评价,根据反馈信息及时发现系统性因素出现的征兆,并采取措施消除其影响,使过程维持在仅受随机性因素影响的受控状态,以达到控制质量的目的。
当过程仅受随机因素影响时,过程处于统计控制状态(简称受控状态);当过程中存在系统因素的影响时,过程处于统计失控状态(简称失控状态)。
由于过程波动具有统计规律性,当过程受控时,过程特性一般服从稳定的随机分布;而失控时,过程分布将发生改变。
SPC正是利用过程波动的统计规律性对过程进行分析控制的。
因而,它强调过程在受控和有能力的状态下运行,从而使产品和服务稳定地满足顾客的要求。
用SPC做品质控制时应该如何选择合适的控制图企业在用SPC做品质控制的过程中,需要用到的工具手段就是控制图,控制图主要是一个统计管理工具。
在SPC统计过程的,为不同的数据应用不同的控制图来统计。
首先数据主要分为两大类,一个是计量型数据,另一个是计数型数据。
计量型:用各种计量仪器测出、以数值形式表现的测量结果,包括用量仪和检测装置测的零件直径、长度、形位误差等,也包括在制造过程状态监控测得的切削力、压力、温度、浓度等。
SPC控制指标解析

数据驱动和机器学习在SPC领域的应用
数据驱动:通过对大量历史数据的分析,预测未来SPC控制指标的发展趋势 机器学习:利用算法和模型,自动识别异常和预测未来指标表现 应用场景:实时监测、预警、优化生产过程,提高产品质量和生产效率
YOUR LOGO
SPC控制指标解析
XX,a click to unlimited possibilities
汇报人:XX
时间:20XX-XX-XX
目录
01
添加标题
02
SPC控制 指标概述
03
04
05
06
主要SPC 控制指标解 析
SPC控制 指标的应用 场景
如何制定和 实施SPC 控制指标
SPC控制 指标的优缺 点分析
持续改进和创新是SPC控制指标发展的重要方向。通过不断优化控制参数、改进工艺流程、提高设 备精度等方式,可以进一步提升SPC控制指标的准确性和可靠性,提高生产效率和产品质量。
SPC控制指标在持续改进和创新中的重要性不言而喻。未来,随着工业4.0和智能制造的深入推进, SPC控制指标将在生产过程中发挥更加重要的作用,为企业的可持续发展提供有力保障。
制定控制计划:为 关键过程和特性制 定控制计划,包括 控制方法、抽样计 划、验收准则等
监控和改进:持续 监控关键过程和特 性,分析数据,采 取必要的改进措施
确定适当的控制策略和控制限
根据产品特性和 过程特性选择适 当的控制策略, 如采用常规控制 图还是特殊控制 图
确定控制限,控 制限的设定应基 于工程知识和经 验,同时考虑过 程能力和客户要 求
不懂SPC?那你真的没资格说做过工艺

不懂SPC?那你真的没资格说做过工艺在制造业的广阔天地里,每一个细节都关乎产品的品质与企业的命运。
而在这些细节中,统计过程控制(SPC,Statistical Process Control)无疑是一颗璀璨的明珠。
如果你还在说“我不懂SPC”,那么不好意思,你真的没资格说做过工艺!天行健Six Sigma咨询公司解析如下:我们先来了解一下什么是SPC。
统计过程控制是一种利用统计方法对生产过程进行实时监控和控制的方法。
通过对生产过程中收集到的数据进行分析,SPC可以帮助我们及时发现生产过程中的异常波动,从而采取相应的措施进行调整,确保产品质量和生产效率的稳定。
为什么SPC如此重要呢?在现代工业生产中,产品的质量和性能直接关系到企业的竞争力。
一个优秀的产品,不仅要有良好的性能和设计,更要在生产过程中保证质量的稳定性和一致性。
而SPC正是实现这一目标的关键。
它通过对生产过程的实时监控和数据分析,帮助我们及时发现并解决问题,从而确保产品的稳定性和可靠性。
那么,如何运用SPC来提升工艺水平呢?首先,我们需要建立一套完整的SPC体系,包括数据采集、数据分析、问题识别、措施制定等多个环节。
通过这套体系,我们可以对生产过程进行全面的监控和控制,确保每一个环节都在最佳状态下运行。
其次,我们需要加强对员工的培训和教育。
只有让每一个员工都了解SPC的重要性和方法,才能够确保其在生产过程中得到有效的执行。
通过培训和教育,我们可以提升员工的技能水平,增强其对SPC的理解和应用能力。
末了,我们还需要不断地对SPC体系进行优化和改进。
随着生产工艺的不断发展和变化,SPC体系也需要不断地进行适应和调整。
通过不断地优化和改进,我们可以确保SPC体系始终与生产工艺保持同步,为提升产品质量和生产效率提供有力的支持。
总之,在这个工艺为王的时代,掌握SPC不仅是对工艺人员的基本要求,更是企业保持竞争力、实现持续发展的关键。
spc概述
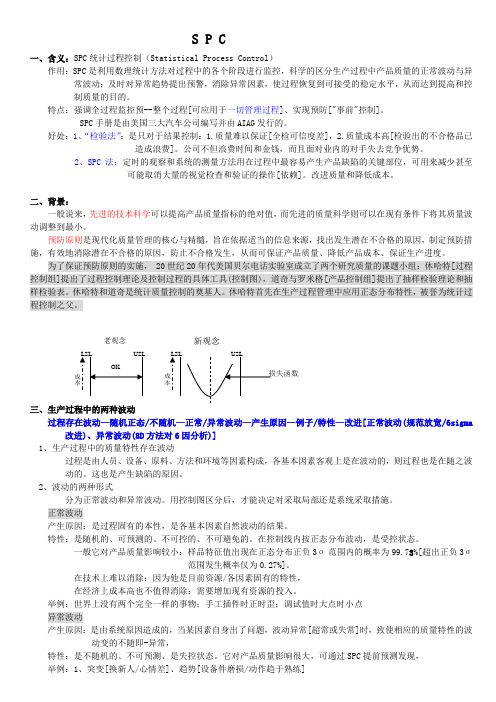
S P C一、含义:SPC 统计过程控制(Statistical Process Control )作用:SPC 是利用数理统计方法对过程中的各个阶段进行监控,科学的区分生产过程中产品质量的正常波动与异常波动;及时对异常趋势提出预警,消除异常因素,使过程恢复到可接受的稳定水平,从而达到提高和控制质量的目的。
特点:强调全过程监控预--整个过程[可应用于一切管理过程]、实现预防["事前"控制]。
SPC 手册是由美国三大汽车公司编写并由AIAG 发行的。
好处:1、“检验法”:是只对于结果控制:1.质量难以保证[全检可信度差],2.质量成本高[检验出的不合格品已造成浪费]。
公司不但浪费时间和金钱,而且面对业内的对手失去竞争优势。
2、SPC 法:定时的观察和系统的测量方法用在过程中最容易产生产品缺陷的关键部位,可用来减少甚至可能取消大量的视觉检查和验证的操作[依赖]。
改进质量和降低成本。
二、背景:一般说来,先进的技术科学可以提高产品质量指标的绝对值,而先进的质量科学则可以在现有条件下将其质量波动调整到最小。
预防原则是现代化质量管理的核心与精髓,旨在依据适当的信息来源,找出发生潜在不合格的原因,制定预防措施,有效地消除潜在不合格的原因,防止不合格发生,从而可保证产品质量、降低产品成本、保证生产进度。
为了保证预防原则的实施, 20世纪20年代美国贝尔电话实验室成立了两个研究质量的课题小组:休哈特[过程控制组]提出了过程控制理论及控制过程的具体工具(控制图),道奇与罗米格[产品控制组]提出了抽样检验理论和抽样检验表。
休哈特和道奇是统计质量控制的奠基人。
休哈特首先在生产过程管理中应用正态分布特性,被誉为统计过程控制之父。
三、生产过程中的两种波动过程存在波动—随机正态/不随机—正常/异常波动—产生原因—例子/特性—改进[正常波动(规范放宽/6sigma改进)、异常波动(8D 方法对6因分析)] 1、生产过程中的质量特性存在波动过程是由人员、设备、原料、方法和环境等因素构成,各基本因素客观上是在波动的,则过程也是在随之波动的。
使用SPC控制图时务必注意的八大常见错误,否则可能适得其反
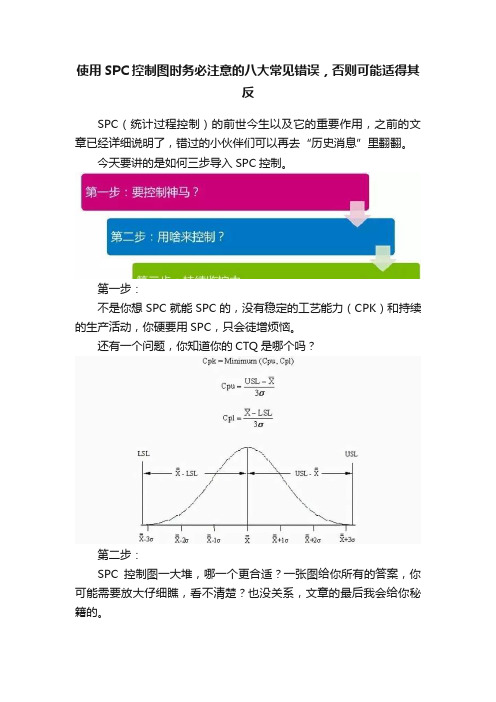
使用SPC控制图时务必注意的八大常见错误,否则可能适得其反SPC(统计过程控制)的前世今生以及它的重要作用,之前的文章已经详细说明了,错过的小伙伴们可以再去“历史消息”里翻翻。
今天要讲的是如何三步导入SPC控制。
第一步:不是你想SPC就能SPC的,没有稳定的工艺能力(CPK)和持续的生产活动,你硬要用SPC,只会徒增烦恼。
还有一个问题,你知道你的CTQ是哪个吗?第二步:SPC控制图一大堆,哪一个更合适?一张图给你所有的答案,你可能需要放大仔细瞧,看不清楚?也没关系,文章的最后我会给你秘籍的。
第三步:守着控制图围观就好了......这张图背后有一堆规则在监控,有点不正常的话就会马上告诉你了。
老师说,读书要先把书读薄,然后又把书读厚。
SPC也是如此,上述三步会让你对SPC的整体框架有一个把握,但是如果真的要具备在生产现场应用的能力,你就需要继续深入去学习了,下图才是比较完整的流程。
哦,之前我说的那本“秘籍”是它:《SPC手册》,号称五大质量管理工具之一。
你要是在公众号主页留言并留下联系邮箱,我可能会把它发给你的......我们将继续SPC这个话题,做略深入一点的拓展,对SPC导入后使用过程中常见的理解性错误进行梳理。
错误一:超控制限是因为控制限太严的原故解读:SPC控制务必要准确理解清楚规格限与控制限这两个概念。
规格限:源自客户,也就是客户的要求。
控制限:是通过观察得到的数据计算出来的,不是人为主观设定。
错误二:控制图超控制限,但不超规格限就可以接受解读:控制限的衡量对象是样本子组均值,规格限的衡量对象是个体单值。
因此不能使用规格限对观察到的子组均值数据进行判定。
以X bar R图为例,我们用X bar R图对计量型过程参数做控制时,控制的统计量是X bar和R,即子组的均值和极差,而不是每个个体的单值X。
规格限是针对每个个体的单值的,而不是针对子组的均值的。
这其实也是SPC控制图最主要的一个劣势:它无法告诉我们控制的结果是否符合规格。
spc模型归纳总结
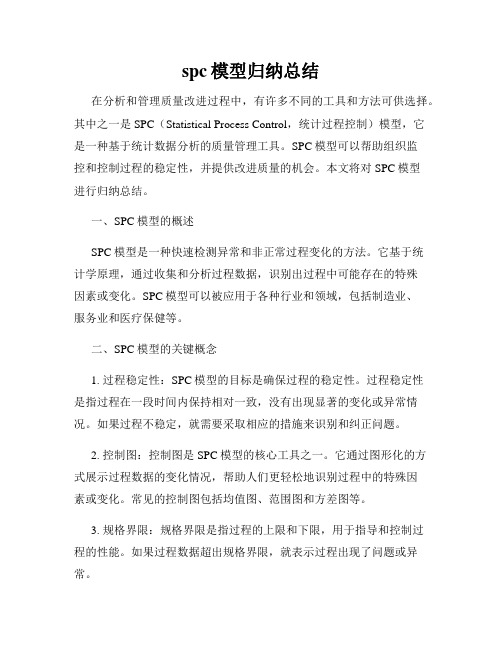
spc模型归纳总结在分析和管理质量改进过程中,有许多不同的工具和方法可供选择。
其中之一是SPC(Statistical Process Control,统计过程控制)模型,它是一种基于统计数据分析的质量管理工具。
SPC模型可以帮助组织监控和控制过程的稳定性,并提供改进质量的机会。
本文将对SPC模型进行归纳总结。
一、SPC模型的概述SPC模型是一种快速检测异常和非正常过程变化的方法。
它基于统计学原理,通过收集和分析过程数据,识别出过程中可能存在的特殊因素或变化。
SPC模型可以被应用于各种行业和领域,包括制造业、服务业和医疗保健等。
二、SPC模型的关键概念1. 过程稳定性:SPC模型的目标是确保过程的稳定性。
过程稳定性是指过程在一段时间内保持相对一致,没有出现显著的变化或异常情况。
如果过程不稳定,就需要采取相应的措施来识别和纠正问题。
2. 控制图:控制图是SPC模型的核心工具之一。
它通过图形化的方式展示过程数据的变化情况,帮助人们更轻松地识别过程中的特殊因素或变化。
常见的控制图包括均值图、范围图和方差图等。
3. 规格界限:规格界限是指过程的上限和下限,用于指导和控制过程的性能。
如果过程数据超出规格界限,就表示过程出现了问题或异常。
三、SPC模型的应用步骤1. 确定关键过程特性:在应用SPC模型之前,需要明确所关注的关键过程特性。
这些特性可以是产品的尺寸、重量、强度等等。
确定特性后,可以开始收集相关的过程数据。
2. 绘制控制图:使用收集到的过程数据,绘制相应的控制图。
控制图可以帮助识别过程的稳定性和异常情况。
例如,均值图可以帮助判断过程是否受到特殊因素的影响,范围图可以反映过程变异的程度。
3. 分析控制图并采取措施:通过分析控制图,可以判断过程的稳定性和偏离情况。
如果控制图显示出过程数据超出了规格界限或呈现异常模式,就需要采取相应的措施来改进过程。
四、SPC模型的优点和局限性1. 优点:- 提高了对过程的可视化:通过控制图,人们可以更直观地了解过程的变化情况和特殊因素。
spc误区

1.误区之一:没能找到正确的管制点。
不知道哪些点要用管制图进行管制,花费大量的时间与人力,在不必要的点上进行管制.熟不知,SPC只应用于重点的尺寸(特性的).那么重点尺寸性能如何确定呢?通常应用FMEA的方法,开发重要管制点.严重度为8或以上的点,都是考虑的对象.(如果客户有指明,依客户要求即可);2.误区之二:没有适宜的测量工具.计量值管制图,需要用测量工具取得管制特性的数值.管制图对测量系统有很高的要求.通常,我们要求GR&R不大于10%.而在进行测量系统分析之前,要事先确认测量仪器的分辨力,要求测量仪器具有能够分辨出过程变差的十分之一到五分之一的精度,方可用于制程的解析与管制,否则,管制图不能识别过程的谈判.而很多工厂勿略了这一点,导致做出来的管制图没办法有效的应用,甚至造成误导;3.误区之三:没有解析生产过程,直接进行管制.管制图的应用分为两个步骤:解析与管制.在进行制程管制之前,一定要进行解析.解析是目的是确定制程是的稳定的,进而是可预测的,并且看过程能力是否符合要求.从而了解到过程是否存在特殊原因、普通原因的变差是否过大等致关重要的制程信息。
制程只有在稳定,并且制程能力可以接受的情况下,方才进入管制状态。
4.误区之四:解析与管制脱节。
在完成制程解析后,如果我们认为制程是稳定且制程能力可接受的,那么,就进入管制状态。
制程控制时,是先将管制线画在管制图中,然后依抽样的结果在管制图上进行描点。
那么,管制时管制图的管制线是怎么来的呢?管制图中的管制线是解析得来的,也就是说,过程解析成功后,管制线要延用下去,用于管制。
很多工厂没能延用解析得来的管制线,管制图不能表明过程是稳定与受控的。
5.误区之五:管制图没有记录重大事项。
要知道,管制图所反应的是“过程”的变化。
生产的过程输入的要项为5M1E(人、机、料、法、环、量),5M1E的任何变化都可能对生产出来的产品造成影响。
换句话说,如果产品的变差过大,那是由5M1E其中的一项或多项变动所引起的。
- 1、下载文档前请自行甄别文档内容的完整性,平台不提供额外的编辑、内容补充、找答案等附加服务。
- 2、"仅部分预览"的文档,不可在线预览部分如存在完整性等问题,可反馈申请退款(可完整预览的文档不适用该条件!)。
- 3、如文档侵犯您的权益,请联系客服反馈,我们会尽快为您处理(人工客服工作时间:9:00-18:30)。
SPC统计技术运用在各行业运用中存在的弊端!
SPC自1924年由美国贝尔电话实验室休哈特首创以来,成为质量管理.从”因袭管理”(即传统经验管理)发展到”过程管理”(即过程统计质量控制)的重要标志.SPC重要的手段是控制图(休哈特控制图),其主要作用:发现异常变异,及时报警,以采取纠正措施,恢复过程稳
随着QS9000到TS16949质量管理体系在中国汽车制造行业及其供应链厂商导入与实施以来,SPC成为过程控制的重要手段.这科学有效的方法也很快被其它行业迅速直接或间接引用, SPC热在制造业中迅速盛行起来,其中离不开外部各类型培训/咨询/认证机构的广泛宣传和推广.但是很多企业通过SPC实际运用,却出现意想不到的通病:原本以前相安无事的部门,居然异常众多,由于解决不力,形成一发不可收拾的局面,或现有投入或现行环境还达不到解决问题的程度,越来越多的企业感觉或发现到:花了不少培训费用,投入了相当人力和物力,并没有给企业带来预期收益;或实行下去也渐渐成为一种对外吹嘘的光环,而并没有真正服务生产实际;或因相当的测量数据采集,反而成为工作负担,使为数不少的质量负责人只是应付老板或对应客户所需,并没有为其质量管理工作带来多大意义,还不如简单的QC七大手法来的即时有效.部分企业内部的SPC实施久而久之也就不了了之.
其实SPC本没错,是科学的. SPC没有得到有效运用,究其原因,有以下分析.
1. SPC仅是一种更好的方法论,本身并不会带来实际收益.而很多人却存在认识误区:SPC 运用=质量提升.其实两者没有必然联系.在实践过程中,SPC统计结果出来,最终还是靠人的思维去分析产生的原因,靠人的经验和技艺找到解决问题的对策,靠一个有致解决问题的团队去实施,并能够在对策失败中再检讨再对策,还靠有一个不解决问题不罢休的恒心,四者缺一不可.否则一纸空文,最终落得个被上司或老板责骂不已.特别是在三资企业,不少人感叹:多一事不如少一事.
2. SPC过程能力统计,是基于过程受控状态前提下进行的.只有在这样的条件下,所得的结论才具有意义.而实际运用中,很多企业甚至完全不加确认,只要采集数据一输入,结果一输出.用这样的结论来判定过程是不可靠的.
3. SPC过程统计通过运用Xbar-R控制图, P或np管理图,单位缺陷数控制图等描点方式,
更直观地敏感地分辩过程是否存在异常点.但这种异常,仅是一种统计上的异常警报,可能是虚假的,也可能是实际的.而很多质量管理者,却盲目的都认为是生产状况存在异常,或产品质量发生状况,没有实际调查,去伪存真,而只会在办公室发号施令,决策错误屡见不鲜,甚至实施过程造成下属或关联部门抵触情绪,有些迫于压力,消极执行指令,以下瞒上等等,反而生产诸多管理新问题.企业内部经常出现”纸上谈兵”嗤之以鼻的暗自嘲弄,也就不足为怪了.
4. SPC过程控制基准,是源自汽车行业本身质量要求而来的.可以这么说因其行业质量控制成本相对较高,SPC运用实为一种经济的方法.但SPC的运用也是需要投入一定的成本,对其它传统行业,或低值产品行业,或行业本身工艺水平就不太高,甚至客户原本就要求较低的企业来讲,SPC运用好比”杀鸡用牛刀”,可能结果是:质量有改善,但质量成本也高了;也可能质量没改善,不但白花了一笔钱,还导致新的管理问题出现.过程控制在基于3σ,能力要提高到1.00以上的要求, 其能力实实在在提升也并不是件易事,常见到现场抱怨:”工程检查PASS,出荷检查PASS,甚至出货到客户也没有不良投诉,还要改进什么?”,有些企业头脑一热,或纯粹做市场宣传,打肿脸来充胖子的情况,就不多说了.这里想说的是,选择一个管理决定前,应好好的给自己号号脉:是否适合企业本身发展的阶段,人员素质是否跟得上,自己能否长抓不懈,提升竟争力的代价是否划算,现行方法可以满足要求吗,其它方法是否也可行,等等,多扪心自问下,别把传统好的东西盲目丢下,一味地去赶风.
5. 在很多培训机构/咨询/认证机构所介绍有关SPC过程判稳/判异方法,及非正态分布识别方法.如:1) 判稳原则: n=25, 界外点d=0, 或n=35, 界外点d≤1, 或n=100, 界外点d≤2; 2) 判异原则: 常用的有8大原则,如:a点出界; b连续3点,有2点在A区,至于第3点在何处不管; c连续5点,有4点在B区,至于第5点在何处不管;d连续6点呈上升或下降趋势;e连续8点在中心两侧,但无1点在C区;f连续9点在C区,或在其外排成一串,g 连续14点上下交替;h连续15点在C区上下;3) 非正态分布识别方法,如:均匀分布;左右倾向分布;指数分布;双峰分布;孤岛型分布等,以上相形细微波动的敏感分辩法则对于质量
精益管理,或理论型研究,或实验验证方面,在有充裕时间可静心分析解决问题的情况下是适合的, 实际上对于不断变化的生产现场,及有相当压力和工作负担的质量负责人来讲,包括
在讲求效益的企业内部环境,很多情况是通过以上法则发现的异常还没来得及分析解决,新
的问题和异常早已产生,久而久之异常现象不断累加,给人的感觉形同大敌当前,但当一个月度总结下来的时候,却并没有出现不良品增多,甚至各工程检查也没有出现批次不良增多迹象.”难道SPC在损人吗”,从管理角度来看,特别是在质量目标实施总量控制的企业内部管理来讲,在一定程上来说SPC分辩的异常的确是小题大做,很重要的原因:它是在UCLx/LCLx
控制界线内管理的,而非在USLx/LSLx规格要求(或客户要求)控制界线内管理,甚至当产品设计本身存在客观问题而当前无法克服时,客户有时还默许出现异常,而且从老板成本控制角度上讲,也是不经济的.故,以上外部机构所讲述的分辩法则于企业管理实际是存在一些不适宜的地方.这也是很多外部机构不能回答或解决实际问题所在的重要原因.
6. SPC过程统计控制本身也存在这样的问题,即:1)必须在过程稳定的基础上,才能把当前过程的控制线延长,作为后续判定基准.但生产过程实际是不断变化的,因此要找到或改进到一个稳定过程作为基础,对讲求时效的今天,这里花费的时间和精力未免太长,有的行业某些过程根本就不可能存在稳定的状态.而且当前所制定的控制线是否适应后续变化的情况也是很难说的,比如:客户要求加严,工艺水平提升,过程得到改进,或测量技术提升等等,先前的控制线还能成为现行变化的情况吗?前后控制过程如何把断层的控制图建立相互联系的对比分析的连续监控过程,这是当前SPC技术没能解的问题;2)SPC在运用中,目前众多同行中只是运用在一段时期的总体能力判定,并没能做到实时正确监控和指导改善,一般只用在量产前许可承认上,而量产过程监控还是很大一块空白,这与前者相关联.因此,这种以静制动的控制方法或理论,个人觉得目前的SPC理论还是需要继续研究和发展的,可能本人没有接触到更前沿的SPC理论,所以如此认为. 质量管理不应”打太极拳”,而应有点类似像股市波动一样,在变化中控制.这仅代表个人观点,没有任何针对性.在本人SPC过程质量控制实际工作中,所设计的是一种随过程σ波动而波动的曲线控制线,而不是直线型的UCL/LCL/CL,以适应过程变化时的控制变化,且与企业质量管理目标相结合,或公司政策调整而调整的过程能力统计方式,可更灵活实际的适应质量管理需要,基本上可以适应不同行业特点要求,避免了照搬照抄汽车行业运用中的SPC统计方法所带来的不适应性.。