双曲扁壳覆盖件静态抗凹性数值模拟研究
某新能源汽车翼子板结构性能优化分析

第34卷第3期2023年9月广西科技大学学报JOURNAL OF GUANGXI UNIVERSITY OF SCIENCE AND TECHNOLOGYVol.34No.3Sept.2023收稿日期:2022-11-03基金项目:广西自然科学基金项目(2018GXNSFAA138040)资助第一作者:黄李冰,在读硕士研究生*通信作者:吴文军,博士,副教授,研究方向:复杂充液系统耦合动力学与控制研究,E-mail :******************.cn某新能源汽车翼子板结构性能优化分析黄李冰,吴文军*(广西科技大学机械与汽车工程学院,广西柳州545616)摘要:为满足轻量化技术要求,翼子板作为遮盖车轮的覆盖件通常会设计成较薄的部件,其结构性能直接影响整车的性能品质,因此需要对翼子板的结构性能进行优化分析。
文中搭建了某新能源汽车翼子板有限元模型,根据相关设计要求分别对翼子板进行模态分析、连接刚度计算和抗凹性分析,依据计算结果寻找出不满足目标值要求的指标。
经综合分析,提出以增加内支撑板的方式来改进翼子板的结构,从而解决翼子板的刚度以及抗凹性不足的问题,但一阶固有频率无法满足目标值要求。
因此,通过响应面法搭建克里金近似模型,以结构改进后的翼子板的质量和一阶固有频率为目标进行遗传算法迭代寻优,使得改进后的翼子板的整体质量稍有下降,一阶固有频率大于53.00Hz ,且其余各项指标均符合目标值要求,达到优化目的。
关键词:翼子板;有限元模型;响应面法;多目标优化;遗传算法中图分类号:U469.720.3DOI :10.16375/45-1395/t.2023.03.0010引言汽车翼子板为遮盖车轮的外壳板,其刚度的强弱直接影响整车的刚度。
为减轻汽车质量,通常将汽车翼子板设计成较薄的部件。
因汽车翼子板结构特征较少、厚度较薄,导致其在进行作业时会发生偏软或出现永久变形、刚度不足等问题[1]。
翼子板在刚度不足的情况下进行大载荷作业,会因自身结构遭到破坏而导致周边部件的振幅增大甚至会产生共振现象[2]。
双曲扁壳类汽车覆盖件刚度的试验研究(一)

双曲扁壳类汽车覆盖件刚度的试验研究(一)
双曲扁壳类汽车覆盖件刚度的试验研究报告
引言
•研究的背景和意义
•已有研究的不足之处
研究目的
•确定双曲扁壳类汽车覆盖件刚度的试验方法
•探究不同参数对覆盖件刚度的影响
方法与实验设计
•选择双曲扁壳类汽车覆盖件的样板件
•设计不同试验方案
•制定试验步骤和工艺流程
实验步骤
1.准备试验样板件和相关设备
2.确定试验参数并记录
3.依据试验方案进行试验
4.测量并记录试验结果
数据分析与结果
•对试验结果进行统计与分析
•绘制曲线图、表格等以展示数据
•讨论不同参数对覆盖件刚度的影响
结论与讨论
•总结实验结果
•分析实验的局限性并提出改进方案
•指出今后研究的方向与重点
参考文献
•列举所引用的相关研究和资料
以上是一份基本的研究报告大纲,具体内容需要根据实际情况进
行详细填写。
采用markdown格式可以方便地进行文本编辑和格式排版,在生成报告时也便于导出为其他格式的文档。
基于可变工况的车身覆盖件抗凹性全流程优化方法

基于可变工况的车身覆盖件抗凹性全流程优化方法
宋凯;王超;陈涛;周泽
【期刊名称】《机械科学与技术》
【年(卷),期】2015(034)004
【摘要】针对车身覆盖件抗凹性优化问题,在现有工程中使用有限元数值模拟方法及相应工程经验基础上,开发基于可变工况的车身覆盖件抗凹性全流程优化方法.以某车型翼子板为例,采用Tcl/Tk语言编制脚本,快速建立了考虑材料非线性和接触非线性的仿真模型,经Abaqus软件计算得到抗凹性结果,再利用简化了的脚本定制优化参数,对工况变动的结构进行优化.结果表明,此套全流程优化方法解决变工况抗凹性问题快速,高效,准确.
【总页数】4页(P599-602)
【作者】宋凯;王超;陈涛;周泽
【作者单位】湖南大学汽车车身先进设计制造国家重点实验室,长沙 410082;上汽通用五菱汽车股份有限公司,柳州545007;湖南大学汽车车身先进设计制造国家重点实验室,长沙 410082;湖南大学汽车车身先进设计制造国家重点实验室,长沙410082;湖南大学汽车车身先进设计制造国家重点实验室,长沙 410082
【正文语种】中文
【中图分类】U463
【相关文献】
1.车身外覆盖件抗凹性的分析及改进 [J], 李佩;廖毅;刘乐平
2.车身外覆盖件抗凹性的分析及改进 [J], 江昊
3.浅谈车身外覆盖件抗凹性的提升改善方法 [J], 刘洁敏; 朱红平; 陈浩; 陈超
4.白车身局部刚度及外覆盖件抗凹性试验装置设计 [J], 徐华俊;汤萍;赵益辉
5.冲压成形对车身外覆盖件抗凹性影响研究 [J], 俞祖俊;张军;陈新力;崔磊;田志俊;王祥
因版权原因,仅展示原文概要,查看原文内容请购买。
47-基于数值模拟的车门抗凹性分析

基于数值模拟的车门抗凹性分析陈学峰北汽福田汽车股份有限公司工程研究院性能开发二部 北京 102206摘要摘要::通过数值模拟方法,对车门外板等相对尺寸较大的覆盖件进行抗凹性分析,对预测和评价用户使用过程中,在覆盖件受到可能的外载荷作用下的车辆外观品质具有重要意义。
本文基于hyperworks和abaqus软件,对某车门外板进行了抗凹性分析。
关键词关键词:抗凹性;车门;数值模拟Abstract:Benefiting from the application of numerical simulation method, it's of great significance to predicting and evaluating the quality of automotive appearance by analysing the dent resistance of auto-body panel.In this paper,based on the software of hyperworks and abaqus,the dent resistance of auto-door panel is analysed.Key words;Dent resistance;Auto door;Numerical simulation1 1 概述概述概述车门外板尺寸相对比较大,带有曲率,有一定的预变形,在用户使用过程中常常会受到外载荷作用,如人为的触摸按压、行进过程中的振动以及碎石冲击等,这些载荷往往使车门外板发生凹陷挠曲,甚至产生局部的永久变形,这些将直接影响到车辆的外观品质。
此外,出于减重节能,节省成本的目的,更薄的高强度钢板在汽车钣金件中的应用越来越多,已成为一大趋势,在车门外板采用高强板后,会导致外板变软,从而引发板材局部刚度不足等一系列问题。
对于汽车外覆盖件在承受外部载荷作用下,抵抗凹陷屈曲和局部凹痕变形的能力称为抗凹性。
正高斯双曲空腹扁网壳连续化模型的等效刚度

将 Q = 2 0 = = = Q= ; M2 M 2 0代人( ) : 1得
警+ + 。 舅 =
+
薯 : + 。
2
( k N1 +^ 后 )一F , 2 2=0
0 1 a 1 M 2 M
将
㈩ 一
㈣ :
维普资讯
维普资讯
第3 期
纪延安 , : 等 正高斯双曲空腹扁网壳连续化模型的等效刚度
15 0
+
上
杆
+
图2 网格单元等效的计算模型
中面
拟壳法是在原 网壳结构及基本假定下 , 根据物理 等效 、 几何等效的原则 , 网壳结构拟化为连续的实 将 体壳进行分析计算 。故而, 连续化后的实体壳力学模型也就是将 图( ) I 视为连续 的实体壳 , 但其 刚度应是
式 中:、 —壳 中面上任意一点沿曲线坐标系 A曰
k 一 中面上 曲线坐 标 系 方 向的 主曲率 ;
方向的拉密系数;
Ⅳ、2 】 一壳中面上任意一点沿曲线坐标系 Ⅳ
、 —
方向的拉应力 ;
ห้องสมุดไป่ตู้
Q 、: Q一壳中面上任意一点为在 、 面上 的横向剪力 ; 壳 中面上 任意一 点 在 面 上 的弯矩 内力 ; . s —壳 中面上任 意一点 在 面上 的平错 力 ( 向剪力 ) 纵 ;
摘 要 : 由正 交拱 架组成 的正 高斯双 曲空腹扁 网壳进 行分析 , 对 探讨 了基 于连 续化 计算模 型的
拟壳分析法, 给出正高斯双曲空腹扁网壳的等代薄膜刚度和弯曲刚度的表达式 , 按弹性小挠度 薄壳理论进行分析 , 建立 了正高斯双曲空腹扁网壳的基本方程式。
汽车覆盖件抗凹性能研究进展

动态抗 凹性 , 其中, 静态抗 凹性是 衡 量覆 盖 件抵 抗如 手 按 、 手 持、 肘压、 行李 包裹 等 静态 或 准 静态 载荷 引 起 永 久 凹痕 的能 力, 而动态 抗 凹性 是 消 抵 如停 车 场 中 车 门与 车 门的 碰 撞 , 车
进展 。
关 键 词
抗凹性能 动态抗 凹性能 刚度 汽车车身外覆盖件
中 图分 类 号 : TG 3 8 6 . 4
文献 标 识 码 : A
D OI : 1 0 . 1 1 8 9 6 / j . i s s n . 1 0 0 5 — 0 2 3 X . 2 0 1 5 . 0 1 5 . 0 1 3
0 引言
在汽车制造行业 , 为实现轻量化 , 目前较多使用的是尽
可能 薄 的超高 强度 的材料 或轻 质合金 , 在汽 车轻 量化 的发 展
过程 中 , 铝合 金部 分 替代 原 有 钢材 , 被 广 泛 应用 于汽 车 车 身 制造 1 ] , 使 其材 料特性 的变化 不仅影 响着 成形工 艺 的制定 ,
t e d l i g h t we i g h t ma t e r i a l s a n d d e s i g n s a r e p r e s e n t e d . Th e d e n t r e s i s t a n c e o f a u t o mo t i v e b o d y p a n e l h n e o f k e y d e s i g n p a r a me t e r a n d d e f i n e d mo r e s t r i n g e n t c r i t e r i o n .Th e a f f e c t s a n d t e s t p r o c e d u r e s o f s t a t i c d e n t r e s i s — t a n c e a n d d y n a mi c d e n t r e s i s t a n c e a r e b o t h we l l s u mma r i z e d ,a n d e v a l u a t e d i n d e t a i l s .I n t h e l i g h t o f t h e p r a c t i c a l a p —
ljf翻译
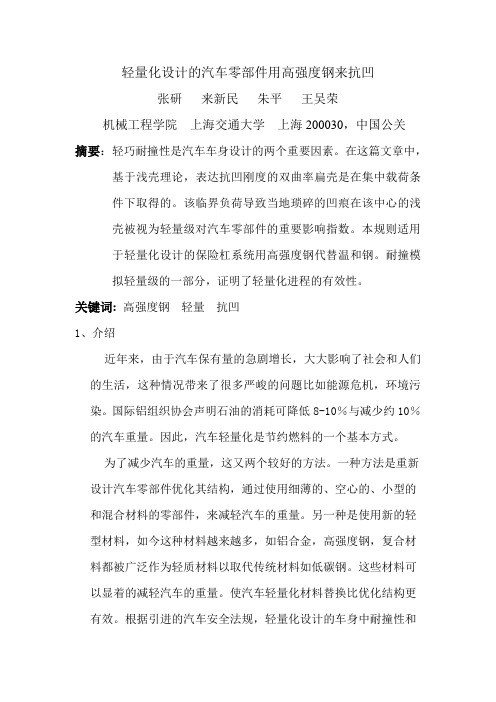
轻量化设计的汽车零部件用高强度钢来抗凹张研来新民朱平王吴荣机械工程学院上海交通大学上海200030,中国公关摘要:轻巧耐撞性是汽车车身设计的两个重要因素。
在这篇文章中,基于浅壳理论,表达抗凹刚度的双曲率扁壳是在集中载荷条件下取得的。
该临界负荷导致当地琐碎的凹痕在该中心的浅壳被视为轻量级对汽车零部件的重要影响指数。
本规则适用于轻量化设计的保险杠系统用高强度钢代替温和钢。
耐撞模拟轻量级的一部分,证明了轻量化进程的有效性。
关键词: 高强度钢轻量抗凹1、介绍近年来,由于汽车保有量的急剧增长,大大影响了社会和人们的生活,这种情况带来了很多严峻的问题比如能源危机,环境污染。
国际铝组织协会声明石油的消耗可降低8-10%与减少约10%的汽车重量。
因此,汽车轻量化是节约燃料的一个基本方式。
为了减少汽车的重量,这又两个较好的方法。
一种方法是重新设计汽车零部件优化其结构,通过使用细薄的、空心的、小型的和混合材料的零部件,来减轻汽车的重量。
另一种是使用新的轻型材料,如今这种材料越来越多,如铝合金,高强度钢,复合材料都被广泛作为轻质材料以取代传统材料如低碳钢。
这些材料可以显着的减轻汽车的重量。
使汽车轻量化材料替换比优化结构更有效。
根据引进的汽车安全法规,轻量化设计的车身中耐撞性和安全性被视为先决条件。
高强度钢被广泛的应用于汽车上以代替传统的低碳钢。
高强度钢板可用于汽车车身来提高部件碰撞能量吸收能力和耐塑性变形能力。
汽车体重可减少通过使其零部件用一个更薄厚度的高强度钢板取代低碳钢板来制造。
与铝相比,镁,复合材料和高强度钢具有更好的经济性因为这些材料的原料和制作费用比较便宜。
此外,高强度钢可直接应用到生产线上,包括成型,焊接,装配和油漆。
经营成本节省了,因为没有必要对整个线路进行调整。
在车身外,有几个薄的金属板,其中大部分是浅水面板。
凹痕阻力是有能力保持形状对沉没挠度和地方凹痕在外力的作用下。
凹性汽车板成为汽车的一个重要方面和质量标准。
基于Abaqus的壳体有限元抗凹分析与结构优化

基于Abaqus的壳体有限元抗凹分析与结构优化王永胜;马骏;张婉飞;王丽芳【摘要】为了满足工业生产中一类产品壳体的结构改进需求,以某一壳体为例,对其进行了结构改进优化设计,建立了3种结构壳体的模型,采用Hypermesh软件做前后处理,并基于Abaqus软件,对改进前后的3种结构壳体在2个工况下进行最大位移、最大应力、最大残余变形量3种抗凹性能参数的数值计算与虚拟仿真分析,结果显示壳体3结构的抗凹性能优于壳体1和壳体2,验证了壳体结构改进优化设计的合理性和可靠性,为这类壳体的结构改进优化设计提供了理论指导和依据.【期刊名称】《科技创新与生产力》【年(卷),期】2018(000)002【总页数】3页(P83-85)【关键词】计算机辅助技术;仿真分析;结构优化;壳体;抗凹性能【作者】王永胜;马骏;张婉飞;王丽芳【作者单位】山西新华化工有限责任公司设计研究所,山西太原 030008;山西新华化工有限责任公司设计研究所,山西太原 030008;山西新华化工有限责任公司设计研究所,山西太原 030008;山西新华化工有限责任公司设计研究所,山西太原030008【正文语种】中文【中图分类】TP391.7;TP391.9;TB47在工业生产中,很多产品设计有保护外壳体,用以保护内部核心组件,同时起到美观效果。
面对国内快速发展的各种产品市场,该类壳体在工业生产及日常生活中有广泛的应用。
虽然我国用于工业生产的装备制造业已经有了很大的发展,但还存在重设备轻技术、重生产轻研发、产品更新换代慢等不足。
如果在产品的概念设计阶段即采用计算机辅助技术[1-4],就可以在制造真实物理样机之前,对产品进行各项性能测试,达到缩短研发周期、降低科研成本的目的。
笔者以工业生产中的某一壳体为例,对其进行结构改进优化设计与抗凹性能分析。
1 某产品壳体设计在工业生产中,某产品壳体的现有结构称为壳体1(见图1),由罩体及底板组成,沉头螺钉4-M6通过底板沉孔与罩体内置的4个安装凸台螺纹连接,六角头螺栓4-M8将整个壳体通过底板与直立基体壁挂连接紧固,壳体外形尺寸为1160mm×860mm×410mm,厚度为5mm。
- 1、下载文档前请自行甄别文档内容的完整性,平台不提供额外的编辑、内容补充、找答案等附加服务。
- 2、"仅部分预览"的文档,不可在线预览部分如存在完整性等问题,可反馈申请退款(可完整预览的文档不适用该条件!)。
- 3、如文档侵犯您的权益,请联系客服反馈,我们会尽快为您处理(人工客服工作时间:9:00-18:30)。
第10卷第6期塑性工程学报Vol 110 No 16 2003年12月J OU RNAL OF PLASTICIT Y EN GIN EERIN G Dec 1 2003双曲扁壳覆盖件静态抗凹性数值模拟研究(北京航空航天大学,北京 100083) 张 毅 李东升 周贤宾摘 要:基于PAM 2STAMP 及其Dent Resistance 模块对双曲扁壳模拟覆盖件的成形及静态凹痕变形过程进行分步模拟计算,通过与试验结果的对比,数值模拟分析方法的有效性得到验证;从模拟得到的载荷凹痕深度曲线中提取评定覆盖件静态抗凹性能的参数,对影响覆盖件静态抗凹性的各种因素进行了系统的分析研究。
关键词:双曲扁壳;抗凹性;数值模拟;有限元中图分类号:TG 113126+2 文献标识码:A 文章编号:100722012(2003)0620034204李东升 E 2mail :Li dongs @ 收稿日期:20032012151 引 言在汽车制造领域,把覆盖件承受外部载荷作用、抵抗凹陷弯曲及局部凹痕变形、保持形状的能力称为抗凹性。
它包括抗凹刚度、抗凹稳定性和局部凹痕抗力3个方面[1],是评价和反映覆盖件表面质量和使用性能的一项重要指标和特性,与汽车板材品质、覆盖件的结构型式设计和冲压成形工艺密切相关。
就车身覆盖件几何特点而言,以具有一定曲率的扁壳类零件为主,特别是双曲度扁壳类覆盖件,在现代轿车外形中占有很大的比重,它反映了汽车覆盖件的几何特点及冲压变形特点,试件尺寸较大,带曲率、有一定的预变形,能够真实的反映出真实覆盖件某一部分的抗凹性能,在抗凹性研究中作为模拟覆盖件被广泛应用。
近年来,有限元数值模拟技术在覆盖件成形过程分析中得到良好应用的同时,国内外也开始重视这一技术在覆盖件抗凹性预测评定中的应用,特别是覆盖件成形过程和抗凹性能预测评定的一体化,已成为覆盖件成形仿真技术应用的进一步拓展和升华。
通过有限元数值模拟技术,研究汽车板材及覆盖件在静、动态凹陷情况下的抗凹性能,不仅对直接预测和评定板材及覆盖件的抗凹性能具有直接指导意义,而且对建立汽车覆盖件抗凹性试验检验方法、评估标准以及提高汽车覆盖件抗凹性对策研究都有实用价值。
本文主要基于PAMSTAMP 对双曲扁壳模拟覆盖件的成形及静态凹痕变形过程进行分步模拟计算,在此基础上对影响覆盖件静态抗凹性能的各种因素进行深入系统的分析,为从数值模拟角度探索覆盖件成形过程和抗凹性预测评定相结合的方法途径提供可用的经验。
2 双曲扁壳静态抗凹性的数值模拟研究方法 按照多步成形的思想,对双曲扁壳静态抗凹性这个复杂过程的模拟,在PAMSTAMP 中将其分成3个阶段来实现,即扁壳成形、成形后的回弹及静态凹痕变形过程。
3个阶段独立计算,其中,成形后回弹和静态凹痕变形过程的模拟,分别建立在前一步的模拟结果基础上,通过读入前一步输出的包含零件变形历史和内部残余应力的01文件来实现模拟的连续性。
图1为成形后的试件与压子模型。
PAM 2STAMP 中专门设置了一个模块Dent Re 2sistance 用于静态凹痕变形过程模拟的实现,其原理为,压子被设为刚体,并在初始的参数设置中按照要下压的深度设定其初始位置,此时,压子必然是穿透试件的,穿透的深度等于要下压的深度。
压子是固定的,试件四周的自由结点6个自由度也被束缚。
在求解中,通过一系列隐式的迭代分析步,穿透的深度逐渐减小为0,由于压子和试件都被固定,这只能通过试件与压子接触区域的变形来实现,这样,就用这种反算法的思想实现了压子静态按压下零件静态凹痕变形过程的模拟。
最后,所有的接触被去除,变形后的试件开始反弹,完成静态凹痕变形回弹的模拟。
测得压子分别在最低点和最终回弹完后试件中心结点的Z 向坐标,分别与最初状态时该点坐标进行差值,便可以得到实际的挠曲位移和凹痕深度,即所需的模拟结果。
采用位移控制的控制加载方式对双曲扁壳静态图1 成形后的双曲扁壳和压子Fig 11 The mode of the double 2curved auto 2bodypancel and the punch抗凹性进行数值模拟研究,针对成形后的扁壳试件,分别设定压子的下压深度为1、2、4、6、8mm 进行模拟,记录模拟中的最大接触载荷(即压子下压到最低位置时的载荷)及最终的凹痕深度,通过拟合得到用以进一步分析试件静态抗凹性的载荷凹痕深度曲线。
3 模拟结果的试验验证北航704教研室与宝钢技术中心共同研制的TMS 型板材抗凹性试验机系统,是一套专门用于汽车钢板抗凹性能评估的试验机,能完成板材抗凹性评估的基本试验和模拟试验,包括局部凹痕抗力试验和抗凹刚度试验。
在此基础上进行双曲度扁壳的静态抗凹性试验,得到载荷-凹痕深度曲线形式的试验结果。
试验参数与模拟参数一致:扁壳在300kN 压边力下成形,压子直径<1217mm 。
图2 载荷凹痕深度曲线模拟结果和试验结果的对比Fig 12 Comparing of the curve of force vs 1dent depth between experiment and numerical simulation图2为两种厚度ST14材料的零件数值模拟曲线和试验曲线的比较,模拟中压子下压深度按1mm 、115mm 、2mm 、215mm 的序列控制。
从图中可以看出,模拟数据和试验数据基本在一个数量级,变化趋势也基本相同,一定深度凹痕下的载荷差相差在25%以内,因此,利用PAM 2STAMP 提供的这种凹痕变形模拟方法对覆盖件抗凹性进行分析基本上是可靠的,利用它对覆盖件抗凹性进行预测评估在工程范围内也是可行的。
4 板材性能对覆盖件静态抗凹性影响趋势分析411 屈服强度对静态抗凹性的影响 覆盖件的局部凹痕行为是一种塑性变形,板材的屈服强度是影响其抗凹性的一个重要因素。
对BH340、BP340、ST14、B IF3404种屈服强度各不相同的板材进行抗凹性模拟,厚度018mm ,压子半径统一采用1217mm ,试件在200kN 压边力下成形,表1为各材料屈服强度比较。
表1 材料屈服强度Tab 11 Y ield strength of materials材料ST14BH340BP340BIF340屈服强度(MPa )162231210186图3为得到的载荷凹痕深度曲线比较图。
从图中可以看出,ST14和B IF340钢板的载荷凹痕曲图3 不同材料的载荷凹痕深度曲线Fig 13 The curve of force vs 1dent depth线明显低于BH340和BP340材料的曲线,产生一定深度凹痕所需的载荷也越小,说明前两种成形零件抵抗静态凹痕变形的能力要明显低于后两种材料的成形零件,因此,可以用载荷凹痕曲线来比较评判覆盖件的静态抗凹性。
另外,由载荷凹痕深度曲线可以插值得到产生011mm 深度凹痕所需的载荷P 011,它代表了覆盖件产生可见静态局部凹痕的临53 第6期张毅等:双曲扁壳覆盖件静态抗凹性数值模拟研究界载荷,在静态局部凹痕研究中常以该值作为衡量指标来比较评判覆盖件抵抗局部凹痕变形的能力。
图4为P 011比较。
图4 不同材料的P 011比较Fig 14 P 011of different materials从图中可以看出,屈服强度越大,以P 011衡量的局部凹痕抗力越大,从而抵抗静态凹痕变形的能力越强。
板材屈服强度每增加20MPa 左右,相应的覆盖件局部凹痕抗力提高15%左右。
由此可知,板材屈服强度是决定覆盖件局部凹痕抗力的主要因素之一,提高板材屈服强度是提高覆盖件静态抗凹性的重要途径。
412 板材厚度对静态抗凹性的影响厚度是影响覆盖件抗凹性的另一个重要因素,它不仅对覆盖件的抗凹刚度性能有最敏感的影响,而且对其局部凹痕抗力性能也有较大的影响。
图5是两种不同厚度的ST14试件在相同的条件下模拟得到的P 011比较,可以看出,在厚度从018mm 变化到110mm 时,试件的局部凹痕抗力增大了将近1倍左右,厚度对覆盖件静态抗凹性能的影响可见一斑。
图5 不同厚度试件的P 011比较Fig 15 P 011of speciment wih different thickness针对双曲扁壳上述板材性能参数的模拟结果表明,厚度和屈服强度是决定覆盖件静态局部凹痕抗力的两个重要因素,综合文献[3,4],可以用屈服强度和厚度平方乘积σs t 2来综合反映二者对覆盖件静态抗凹痕能力的影响。
5 成形条件对覆盖件静态抗凹性影响趋势分析 018mm 厚的ST14板材,分别在150、200、300、400、500、650kN 的压边力下成形,然后在参数相同的条件下(压子半径统一为1217mm )进行静态抗凹性模拟,得到如图6所示的P 011比较。
在这组参数范围内,双曲覆盖件的静态局部凹痕抗力随成形压边力的增大而增大,说明适当增加压边力可以对覆盖件抗凹性能起到一定的增强作用。
这个结论为我们改善和提高覆盖件抗凹性能提供了一个新的思路。
即在覆盖件设计外形一定的情况下,从工艺上挖掘潜力(如增加压边力),增大板材成形后的屈服应力(即加工硬化),是提高覆盖件抗凹性能的有效途径之一。
但相关研究表明,通过增加压边力提高覆盖件静态抗凹性时,要注意保证零件面内变形量不能太大,否则,如果厚度变薄太大(特别是对超薄钢板),增大成形压边力并不能起到提高局部凹痕抗力的作用,厚度的过度减薄反而会降低覆盖件的抗凹性能[1]。
图6 成形压边力对覆盖件静态抗凹性的影响Fig 16 E ffect of holding force of forming for staticdent resistance6 结 论本文应用有限元数值模拟方法对覆盖件成形过程和抗凹性预测评定相结合的方法、途径进行了探索性研究,并得到了不同参数对覆盖件静态抗凹性能的影响趋势,取得结论如下:1)数值模拟研究结果和试验结果的对比表明,利用PAM STAMP 提供的这种凹痕变形模拟方法对双曲扁壳覆盖件抗凹性进行的模拟分析是可靠的,可以将其用于覆盖件抗凹性能的预测评定。
63塑性工程学报第10卷2)厚度和屈服应力是影响覆盖件抗凹性的两个最主要因素,板材屈服强度增大20MPa 左右,相应的覆盖件局部凹痕抗力提高近15%;厚度从018mm 变化到110mm 时,局部凹痕抗力便增大了将近1倍左右。
3)用增大压边力从而增加面内变形量的方法,可以提高覆盖件抵抗静态局部凹痕变形的能力,但必须将变形量控制在一定范围内。
参考文献[1] 李东升1汽车板材及覆盖件局部凹痕抗力的研究1北京航空航天大学博士后研究报告,1998[2] 李雪峰1汽车板材抗凹性实验方法及数值模拟研究1北京航空航天大学硕士论文,2001[3] Ming F Shi ,David J Meuleman ,Christine L Alaniz ,Stephen J Zurdosky 1Prestrain E ffects on Static Dent Re 2sistance of Automotive Steels 1SAE ,1982[4] M A Mccormick ,J R Fekete 1J Meuleman ,M FShi 1E ffect of Steel Strengthening Mechanisms on Dent Resistance of Automotive Body Pancels 1SAE ,1998[5] J A Dicellello ,R A G eorge 1Design Criteria for the DentResistance of Auto Body Panels 1SAE ,1974[6] 李东升,周贤宾1关于覆盖件抗凹性指标的理论分析1塑性工程学报,1995,2(1):43~49[7] PAM 2STAMP/OPTRIS Users Training anual ,ESIGroup ,2001The numerical simulation of double 2curved autobody panel ′sstatic dent resistanceZHAN G Y i L I Dong 2sheng ZHOU Xian 2bing(Beijing University of Aeronautics &Astronautics ,Beijing 100083)Abstract :The forming and denting process of the double 2curved panel is simulated by FEM program PAM 2STAMP.This method of numerical simulation is validated by compareing with experiment results.The simulated results is used on research of panel ’s static dent resistance ,and the influence of various factors on the static dent resistance is anal yzed and abtained.K ey w ords :double 2curved autobody panel ;static dent resistance ;numerical simulation ;FEM(上接第18页)forming process using dynamic explicit algorithm is developed.In integration ,the dynamic explicit algorithm has been used with the lumped mass matrix so that it facilitates the calculation of the dis placement and avoids the convergence problem caused by high order nonlinearity of material ,geometry and boundary conditions.The hemis pherical punch deep drawing of a square sheet is analyzed.The results of simulation are com pared with that of experiment to verify the calculated results of the program.K ey w ords :sheet metal forming ;dynamic explicit ;finite element method ;dee p drawing ;wrinkling73 第6期张毅等:双曲扁壳覆盖件静态抗凹性数值模拟研究。