车削中心主轴动静态特性分析
数控机床主轴加工过程中的动态特性控制方法
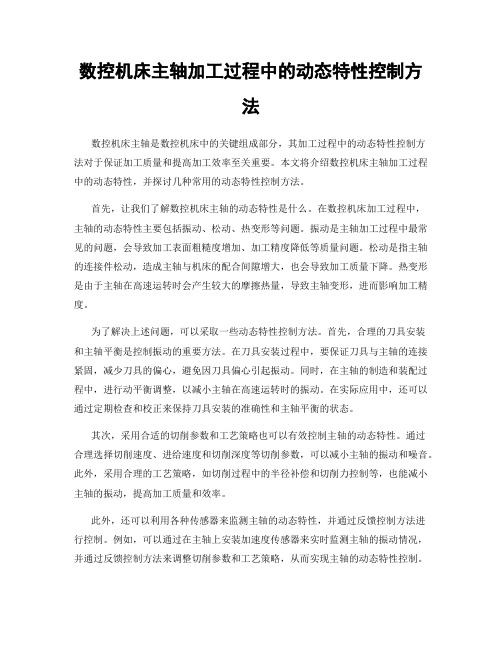
数控机床主轴加工过程中的动态特性控制方法数控机床主轴是数控机床中的关键组成部分,其加工过程中的动态特性控制方法对于保证加工质量和提高加工效率至关重要。
本文将介绍数控机床主轴加工过程中的动态特性,并探讨几种常用的动态特性控制方法。
首先,让我们了解数控机床主轴的动态特性是什么。
在数控机床加工过程中,主轴的动态特性主要包括振动、松动、热变形等问题。
振动是主轴加工过程中最常见的问题,会导致加工表面粗糙度增加、加工精度降低等质量问题。
松动是指主轴的连接件松动,造成主轴与机床的配合间隙增大,也会导致加工质量下降。
热变形是由于主轴在高速运转时会产生较大的摩擦热量,导致主轴变形,进而影响加工精度。
为了解决上述问题,可以采取一些动态特性控制方法。
首先,合理的刀具安装和主轴平衡是控制振动的重要方法。
在刀具安装过程中,要保证刀具与主轴的连接紧固,减少刀具的偏心,避免因刀具偏心引起振动。
同时,在主轴的制造和装配过程中,进行动平衡调整,以减小主轴在高速运转时的振动。
在实际应用中,还可以通过定期检查和校正来保持刀具安装的准确性和主轴平衡的状态。
其次,采用合适的切削参数和工艺策略也可以有效控制主轴的动态特性。
通过合理选择切削速度、进给速度和切削深度等切削参数,可以减小主轴的振动和噪音。
此外,采用合理的工艺策略,如切削过程中的半径补偿和切削力控制等,也能减小主轴的振动,提高加工质量和效率。
此外,还可以利用各种传感器来监测主轴的动态特性,并通过反馈控制方法进行控制。
例如,可以通过在主轴上安装加速度传感器来实时监测主轴的振动情况,并通过反馈控制方法来调整切削参数和工艺策略,从而实现主轴的动态特性控制。
最后,定期维护和保养主轴也是保证主轴动态特性稳定的重要手段。
定期清洗和润滑主轴的连接件,检查主轴的工作状态,及时更换磨损的零部件,可以延长主轴的使用寿命,保持其稳定的动态特性。
总结起来,数控机床主轴的动态特性控制方法包括合理的刀具安装和主轴平衡、采用合适的切削参数和工艺策略、利用传感器进行监测和反馈控制以及定期维护和保养主轴。
机床主轴动静态性能实验研究

表 2 主轴 静 态 变形 测试 数据 表 1主 轴静 态变 形测 试数 据 ( 第一 次 测试 ) ( 第二 次测 试 ) 主轴 作 为 机 床 的 主要 组 成 部分 , 其 性能 的好 坏 直 接 决 定 了机 床 的性 能 的高 低 。 主轴 单 元 的动 静态 特 性 加载力 刀柄前端位移 刀桶前喘位侈 裁力 刀柄前端位移 刀柄前端位移 加 裁次数 卸裁次数 卸载力 卸貔撇 卸戟力 包 括 主轴 的变 形 、 共振频率 、 临 界转 速 和 动 态 响应 等 , 加载次数 【 Ⅳ ) ( u m ) (L L m ) 1 N ) ( m ) 其对主轴的速度和精度性 能有极大的影 响, 主轴性能 初 始值 0 0 初始值 0 _ 2 9 初始值 初始值 7 测试实验f 堤 研究主轴动力学特性及工作性 能的重要 1 1 07 2 8 1 1 c2 3 1 儿1 1O l 07 吧 5 组成部分 , 在理论研究的基础上 , 通 过 实 验 测 试 验 证 2 01 8 3 2 8 9 2 1 —4 9 2 l 98 1. 8 理论模型的正确性和精确性 ,对于完善理论 模型 , 进 3 0 L 4 3 。 。 7 1 a 0 3 o 7 1 3 1 3 2 c 2 1 4 9 而使 理论 仿真结果可以直接指导主轴的设计计算 以 4 01 1 9 1 4 ∞ 0 4 4 c 3 &9 4 3 9 4 3 及 推 广 理论 仿 真 的应 用 研究 具 有重 要 意 义 。 5 。 6 斟 1 5 翻 7 5 50 1 1 g 9 1主轴 静 刚 度测 试 实验 ∞ l 凰 8 6 s 循 l a 4 S 5 99 3 主轴 静 刚度 是 主 轴轴 承 和 主轴 刚度 的综 合 反 映 , 7 05 3 5 7 3 8 5 70 4 31 9 在 高速 运 转过 程 中 ,机床 主 轴 在 静 刚 度 值 低 的情 况 8 l 29 8 8 02 8 8。 3 4l _ 9 8 8c 2 4 4 9 下, 会 出现挠度 增加 , 变形加大 , 影 响加工精 度等 问 9 9 0 0 4 7 5 9 螗 8 9 1 5 3 5 8 9 9 0 0 她 I 题。 掌握准确 的主轴静刚度值是提高机床加工精度的 1O l013 l 0 l 0 1 2 4 l 1 9 9 S 4 a l 55 2 1 0 1 O1 3 5 5 2 前提 条 件 之 一 , 而 对 主轴 进 行 静 刚度 测 试 是 获 得 静 刚 根 据实 验 步 骤对 主 轴进 行 加 载 条件 下 静 刚度 测 试 实验 , 按 照上 度最直接 , 最有效 的方法 。 本文先后进行了主轴静 刚度测试实验、 模 文所述实验步骤重复测量三次 , 主轴前端在载荷作用下 的静态变形 态测 试 实 验 、 动态 响 应测 试 实 验 、 频 率 响 应 函数 测试 实 验 测试 数 据分 别 如 表 1 、 表 2和表 3 所示。 I . 1实 验 内容 和 目的 表 3主 轴静 态 变形 测 试数 据 ( 第 三 次测 试 ) 主轴静刚度口 是 指 在 切 削 力 的作 用下 主轴 抵 抗 变 形 的能 力 , 通 加载 次数 加载 力 刀柄 前端位 卸载次 数 卸载 力 刀柄前 端位 常 以 主轴前 端 产 生 单位 位 移 时 , 在位 移 方 向 上所 施 加 的作 用力 来 表 ( N ) 移 ( I I ) 移 ( m ) 示。现对某机床厂生产的 T G K 4 6 1 0 0高精度数控 卧式坐标镗床主轴 初始 值 0 — 1 0 初始值 0 — 9 4 进行 静 刚度 测 试 , 采 用 加载 装 置 对 主 轴 垂 直方 向进 行 加 载 , 并 利 用 1 1 2 6 — 2 . 5 l 1 0 4 — 2. 9 2 2 1 0 1 . 6 2 2 0 9 3 3 千分表测量刀杆前端 位移。 根据静刚度定义对测量数 据进行拟合得 3 3 0 5 7 . 4 3 2 9 5 8 . 4 到加载力与变形拟合 曲线 , 其斜率 即主轴系统的静刚度。 4 4 1 4 1 2 . 4 4 3 9 3 1 4 1 当在机床 主轴与工作 台之 间,沿 与 x轴 、 Y轴 和 z轴夹 角为 5 5 1 6 1 9 . 0 5 4 8 3 1 9. 4 3 0 0的方向施加静载荷时, 分别测量主轴相对工作 台在 x向、 Y向、 6 6 1 1 2 3 , 9 6 5 9 7 2 5. 9 z向 的 位移 , 以得 到 主 轴 部件 相 对 于 机 床工 作 台 的径 向静 刚度 和 轴 7 7 0 9 3 0 .1 7 7 0 0 3 2 . 1 向刚度 。 8 81 9 3 6 . 0 8 7 9 3 3 7 0 9 . 91 1 4 1 . 8 9 9 0 8 4 4. 1 在 工作 台和 主轴 系统 之 间施 加 作 用力 , 测量 主轴 系统 相 对 于 工 1 0 1 0 0 4 4 7 1 i 0 1 00 4 4 7 . 1 作 台面 的变形 , 寻找 机 床 的受 力薄 弱 环 节 。 试 验结 果 分 析 : 机床在承受切削力作用下抵抗变形 的能力 , 直接影响到机床的 对于以上测试数据进行拟合 , 得到静刚度表达式和拟合 曲线, 加工效 率 , 间接反 映了机床抵抗切削颤振能力 , 同时也反映了机床 所示 。 结 构设 计 , 机 床 各 主要 部 件 的刚 度 强 弱 和 刚 度分 配 是 否 合 理 , 材 料 拟合曲线斜率即静刚度值。如图 2 的选用是否达到最佳 等。 1 . 2试 验条 件 实验仪器包括 : 力加载装置 , 用于径向力加载 ; 力传感器 , 型号 E 为中国航天科技集团公司 Y F F 一 6 — 1 0 8 , 通过数显装置即可读取力的 蹬 大小 ; 千分表 , 精度 为 0 . O 0 1 r n m, 用 于测 量 主 轴 在 力 负 载 下 的 变 形 遒
机床静态及动态分析

这 是 一 种 数 值法 , 于 是 一 些 复 杂 的 问 题 可 以通 过 转 化 为 数 学 模 £ =B q , 于是单元 的应力为 =D Bq , 3 个主应力可 以通过下面的
关 系方程式计算 。3个不变应力张量 是 :
1 、 一o +。 + 吼
静 态 分 析计 算 结 果 显 示 的是 施 加 静 载荷 的 影 响 , 由 于变 形 速度和加速度都很小 , 于是忽略 了惯性力 和 阻尼力 。因此 , 静 态分析包括稳定的惯性 载荷 ( 如重 力和旋转 速度 ) 和 随 时 间 变 化 的载 倚 , 即近 似 地 认 为 静 态 当 量 载 荷 ( 如 通 常 以许 多 建 筑 物 代 码 定 义 的 当量 风 载 和地 震 载 荷 ) 。静 态 分 析 是 为 了确 定 施 加 不 会 导 致 严 重惯 性 和 阻 尼 效 应 的 载 荷 后 引 起 的 构 件 或 部 件 的 位移 、 应 力、 应 变 和 作 用力 。
表 2 机 床 结 构 的 挠 度值
机床
铣 床
车 床
的。例如固定 坐标 系 U v—Ux 一0和旋 转 坐 标 系 R 一R 一
R 一O , 位 移 约 束 应 用 于 解 决 固 定 面 自 由 度 问 题 。施 加 在 组 件
1 _ 2 动 态 分 析
j 2 一
+ : +口 一 一 一
r r 一d r 2 一6 2 一
:
l j 一百 匹 : +
2
6
v
我们 定 义 :
& 一 一 娶一 f l 2
一
6 一பைடு நூலகம்一 z ( +
2 √ 号
目 一 1
动 态分 析 可 以确 定 一 个构 件或 部 件 设 计 时 的 振 动 特 性 ( 固 有 频 率 和振 型 ) 。 同 时 它 可 以用 来 做 更 详 细 的 动 态 性 能 分 析 , 例 如 瞬态 分 析 、 谐 响应 分析 、 频 谱 分 析 等 。动 态 分 析 是 研 究 构 件 在振 动激 励 下 的动 态 性 能 。
数控机床主轴系统动力学特性分析
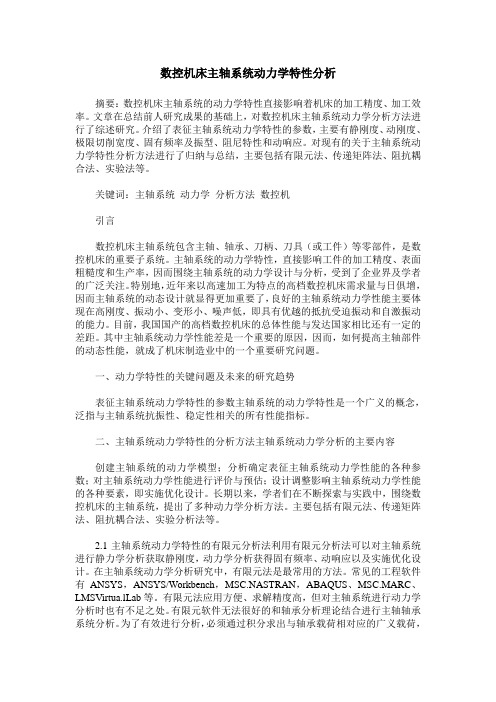
数控机床主轴系统动力学特性分析摘要:数控机床主轴系统的动力学特性直接影响着机床的加工精度、加工效率。
文章在总结前人研究成果的基础上,对数控机床主轴系统动力学分析方法进行了综述研究。
介绍了表征主轴系统动力学特性的参数,主要有静刚度、动刚度、极限切削宽度、固有频率及振型、阻尼特性和动响应。
对现有的关于主轴系统动力学特性分析方法进行了归纳与总结,主要包括有限元法、传递矩阵法、阻抗耦合法、实验法等。
关键词:主轴系统动力学分析方法数控机引言数控机床主轴系统包含主轴、轴承、刀柄、刀具(或工件)等零部件,是数控机床的重要子系统。
主轴系统的动力学特性,直接影响工件的加工精度、表面粗糙度和生产率,因而围绕主轴系统的动力学设计与分析,受到了企业界及学者的广泛关注。
特别地,近年来以高速加工为特点的高档数控机床需求量与日俱增,因而主轴系统的动态设计就显得更加重要了,良好的主轴系统动力学性能主要体现在高刚度、振动小、变形小、噪声低,即具有优越的抵抗受迫振动和自激振动的能力。
目前,我国国产的高档数控机床的总体性能与发达国家相比还有一定的差距。
其中主轴系统动力学性能差是一个重要的原因,因而,如何提高主轴部件的动态性能,就成了机床制造业中的一个重要研究问题。
一、动力学特性的关键问题及未来的研究趋势表征主轴系统动力学特性的参数主轴系统的动力学特性是一个广义的概念,泛指与主轴系统抗振性、稳定性相关的所有性能指标。
二、主轴系统动力学特性的分析方法主轴系统动力学分析的主要内容创建主轴系统的动力学模型;分析确定表征主轴系统动力学性能的各种参数;对主轴系统动力学性能进行评价与预估;设计调整影响主轴系统动力学性能的各种要素,即实施优化设计。
长期以来,学者们在不断探索与实践中,围绕数控机床的主轴系统,提出了多种动力学分析方法。
主要包括有限元法、传递矩阵法、阻抗耦合法、实验分析法等。
2.1主轴系统动力学特性的有限元分析法利用有限元分析法可以对主轴系统进行静力学分析获取静刚度,动力学分析获得固有频率、动响应以及实施优化设计。
数控机床主轴静动态特性分析与优化设计

数控机床主轴静动态特性分析与优化设计数控机床主轴的静动态特性分析与优化设计在机床设计中扮演着重要的角色。
主轴的质量、刚度和动力性能直接影响着数控机床的加工精度和生产效率。
因此,针对数控机床主轴的静动态特性进行分析和优化设计是非常必要的。
首先,对数控机床主轴的静态特性进行分析是基础。
静态特性主要包括主轴的刚度、负载能力和转速范围。
刚度是指主轴在受力时的变形能力,直接影响着机床的切削精度。
负载能力指主轴能够承受的最大切削力或轴向力,取决于主轴的结构和材料。
转速范围则指主轴的最大和最小可工作转速,根据机床加工要求和主轴的功率决定。
其次,对数控机床主轴的动态特性进行分析是优化设计的重要环节。
动态特性主要包括主轴的运行平稳性、动态刚度和各模态的特性频率。
运行平稳性是指主轴在工作状态下的振动情况,对加工表面质量和刀具寿命有重要影响。
动态刚度是指主轴在受力时的变形能力在一定频率下的响应能力。
各模态的特性频率则表征着主轴在不同振动模态下的响应频率和振动幅度。
针对数控机床主轴的静动态特性,可以采取以下优化设计措施。
首先是通过优选材料和适当加工工艺来提高主轴的刚度和负载能力。
其次是采用适当的轴承和润滑方式,减小主轴的摩擦和磨损,提高运行平稳性。
此外,还可以通过调整主轴的结构和参数来提高动态刚度和各模态的特性频率。
例如,增加主轴的直径、改变轴承支撑形式等。
在数控机床主轴静动态特性优化设计过程中,还需要考虑与其他系统和结构的配合,如主轴驱动装置、刀具系统等。
同时,结合实际工艺要求和机床制造能力,进行多种参数的优化设计,以实现最佳的综合性能。
总之,数控机床主轴的静动态特性分析与优化设计是非常重要的工作,直接关系到数控机床的加工质量和生产效率。
通过对主轴材料、结构和参数的优化设计,可以提高数控机床主轴的静态刚度、负载能力和动态性能,进而提高数控机床的加工精度和生产效率。
数控机床关键部件动态特性分析
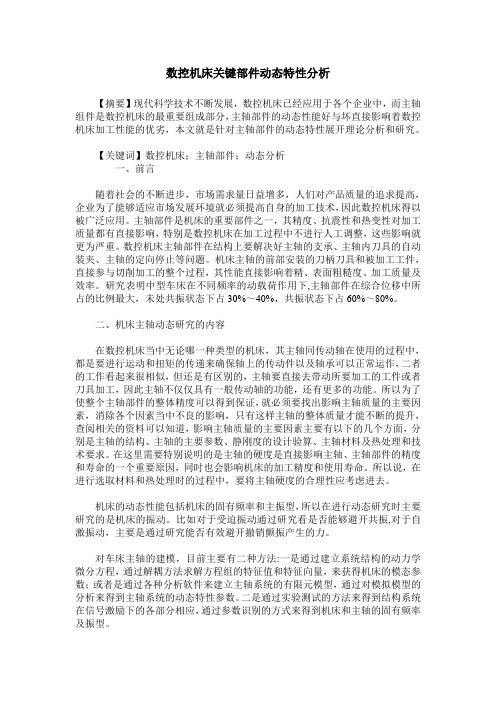
数控机床关键部件动态特性分析【摘要】现代科学技术不断发展,数控机床已经应用于各个企业中,而主轴组件是数控机床的最重要组成部分,主轴部件的动态性能好与坏直接影响着数控机床加工性能的优劣,本文就是针对主轴部件的动态特性展开理论分析和研究。
【关键词】数控机床;主轴部件;动态分析一、前言随着社会的不断进步,市场需求量日益增多,人们对产品质量的追求提高,企业为了能够适应市场发展环境就必须提高自身的加工技术,因此数控机床得以被广泛应用。
主轴部件是机床的重要部件之一,其精度、抗震性和热变性对加工质量都有直接影响,特别是数控机床在加工过程中不进行人工调整,这些影响就更为严重。
数控机床主轴部件在结构上要解决好主轴的支承、主轴内刀具的自动装夹、主轴的定向停止等问题。
机床主轴的前部安装的刀柄刀具和被加工工件,直接参与切削加工的整个过程,其性能直接影响着精、表面粗糙度、加工质量及效率。
研究表明中型车床在不同频率的动载荷作用下,主轴部件在综合位移中所占的比例最大,未处共振状态下占30%~40%,共振状态下占60%~80%。
二、机床主轴动态研究的内容在数控机床当中无论哪一种类型的机床,其主轴同传动轴在使用的过程中,都是要进行运动和扭矩的传递来确保轴上的传动件以及轴承可以正常运作,二者的工作看起来很相似,但还是有区别的,主轴要直接去带动所要加工的工件或者刀具加工,因此主轴不仅仅具有一般传动轴的功能,还有更多的功能。
所以为了使整个主轴部件的整体精度可以得到保证,就必须要找出影响主轴质量的主要因素,消除各个因素当中不良的影响,只有这样主轴的整体质量才能不断的提升,查阅相关的资料可以知道,影响主轴质量的主要因素主要有以下的几个方面,分别是主轴的结构、主轴的主要参数、静刚度的设计验算、主轴材料及热处理和技术要求。
在这里需要特别说明的是主轴的硬度是直接影响主轴、主轴部件的精度和寿命的一个重要原因,同时也会影响机床的加工精度和使用寿命。
机床主轴有限元分析报告
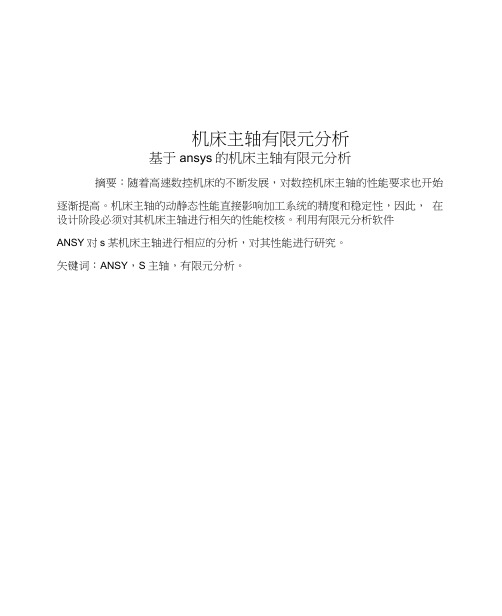
机床主轴有限元分析基于ansys的机床主轴有限元分析摘要:随着高速数控机床的不断发展,对数控机床主轴的性能要求也开始逐渐提高。
机床主轴的动静态性能直接影响加工系统的精度和稳定性,因此,在设计阶段必须对其机床主轴进行相矢的性能校核。
利用有限元分析软件ANSY对s某机床主轴进行相应的分析,对其性能进行研究。
矢键词:ANSY,S主轴,有限元分析。
研究内容52问题描述:机床主轴材料为45号钢,弹性模量为2.06 x10 5 N.mm2,泊松比为0.3,儿何参数如下图。
图1主轴不意图主轴静态特性的基本概念主轴的静态特性反映了主轴抵抗静态外载荷的能力,静力学分析实际上是为了得到机床主轴在一定静态载荷作用下所产生的变形量。
在实际生产条件下,机床的主要失效形式大部分是由于机床的刚度不足而引起。
所以主轴静刚度的计算就显得尤为重要。
所谓的主轴静刚度实际上就是主轴的刚度,是机床主轴一个非常重要的性能指标,它直接反映出主轴负担载荷与抵抗振动的能力。
如果主轴的静刚度不足,主轴在切削力的作用下,会产生较大的变形量,并可能引起振动。
这样不仅会降低机床的加工精度、增大加工工件表面的粗糖度;也会对轴承造成较大磨损,破坏主轴系统的稳定性。
因此,主轴的静刚度是衡量机床性能的重要指标。
主轴的弯曲刚度的定义可以理解为:使主轴前端产生单位径向变形时,变形方向上所需施加的力F,即:主轴的静刚度,分为轴向静刚度与径向静刚度,上面提到的弯曲刚度实际上就是径向静刚度。
通常情况下,轴向刚度没有弯曲刚度重要。
弯曲刚度是衡量主轴刚度的重要指标,通常用来代指主轴的刚度。
1・主轴有限元模型的建立及边界条件的处理为了真实、准确、有效地对主轴进行特性分析,需要对机床主轴进行相应的简化。
对主轴的简化应该遵循以下原则:(1) 忽略对分析结果影响不大的细小特征,如倒角、倒圆等;(2) 对模型中的锥度和曲率曲面进行直线化和平面化的处理;(3) 忽略对主轴静态特性影响不大的零部件结构。
高速数控车床切削的动态特性测与分析

高速数控车床切削的动态特性测试与分析摘要:以高速数控车床 CK7516GS为研究对象,对其动态特性进行了多工况的振动测试并采用 Matlab 软件对数据进行了处理。
通过数据分析得到了各个工况的振动主频范围,并把各个工况对应的主频进行了对比,同时对振源进行了分析。
测试结果表明:高速数控车床不同工况下振动主频大部分都集中在 100 Hz附近,其振动主要由切削力、电主轴旋转不平衡以及电磁力不平衡引起的。
该分析为高速数控机床的系统动态设计和振动抑制提供了参考依据。
关键词:高速数控车床;振动;动态特性 ;Matlab20世纪90年代以来,以高切削速度、高进给速度和高加工精度为主要特征的高速切削技术已经成为现代数控加工技术的重要发展方向之一。
航空航天、汽车、模具制造等对高速切削的认同与、高需求 ,推动着高速切削技术在国际上的迅猛发展。
目前,高速切削加工已成为国内外先进制造技术领域的重要科研项目之一。
笔者采用了大功率内装式电主轴、弹筒式主轴、直联结构的伺服电机和高刚性大导程滚珠丝杠等先进技术测试数控车床CK7516GS。
在数控车床CK7516GS高速车削加工过程中 ,振动是制约其加工精度的一个重要因素,对工件的加工质量具有重要的影响。
为了研究高速车床工作时的振动动态特性, 笔者针对主轴空运转、x和z空载进给运动和切削工件3种工况分别进行了现场测试和分析.该测试方法为同类机床的动态设计提供了依据.1 测试方案及内容1.1 测试目的在高速车床CK7516GS运行的不同工况下,通过加速度传感器采集机座、刀架和电主轴的振动数据,对数据进行处理和分析,从而得出其机械加工时的振动动态特性,并把各个工况对应的主频进行了对比,对振源进行了分析。
通过测试的方法来检验高速数控车床CK7516GS是否达到指定的技术要求。
1.2 测试仪器TS1102压电式加速度传感器;TS5863电荷放大器;自行设计的数据采集分析软件和台式计算机.1.3 测试系统框图测试过程中,在选取的测试点的 x,y,z方向上各安装一个压电式加速度传感器,通过自行设计的数据采集分析软件采集其对应的振动数据,其数据保存在在台式PC机上.测试系统示意框图见 1所示 .图1测试系统示意框图2、电主轴空运转测试数据及结果分析电主轴的运转是影响高速车床动态特性的重要因素,通过测试电主轴旋转时所引起的机床振动,可以获得空载时机床动态特性参数。
- 1、下载文档前请自行甄别文档内容的完整性,平台不提供额外的编辑、内容补充、找答案等附加服务。
- 2、"仅部分预览"的文档,不可在线预览部分如存在完整性等问题,可反馈申请退款(可完整预览的文档不适用该条件!)。
- 3、如文档侵犯您的权益,请联系客服反馈,我们会尽快为您处理(人工客服工作时间:9:00-18:30)。
数控机床 的发 展趋 势是智 能化 、 高速 化和精 密 化 ¨ 。主轴部件是数控机床最为关键 的部件 , J 其动、
析, 比较 了主轴 在 共振和 设计 工 况下 的振 型 , 出该 主轴 的危 险点 并进行 了相 关验 算 。 找
关键 词 : 车削 中心 主轴 模态 分析 谐 响应 中图分 类号 : G1 1 6 T 6 . 文献 标识 码 : A
Stt n y a i h r ce it n lss o pn l n t r ig c ne a i a d d n m c c a a t r i a ay i fs ide i u nn e t r c sc
L ih a ② IJ u ① n
L U n x a ① I Yo g i n
, ,
YU n Ya g①
。
HAN Jain ① il g a
( )col f ehn a E g er g ( Sho o M cai l ni e n &A t ao , ohat n n e i , hnag100 , H  ̄ c n i u m t n N r es r U i rt Seyn 104 C N; o i t e v sy ( Sho o M cai l ni en , i n g n esy f eh o g , i hu110 ,H )  ̄ colf ehn a E g er g L oi i rt o T cnl y J zo 0 1C N ) c n i a n U v i o n 2
Ab t a t s r c :Th p n l ft r i g c ne sr s a c e e s i d e o u n n e tr i e e r h d,a d t e s rn n h p g-d mp r ee nt r s d t i lt he i a e l me s ae u e o smu ae t
s n d f rt e ma h n . C mp r d o d s h e o n so p n l e i n p r r n e a e c l i e o h c i e g o a e ft mo e ,t e k y p i t fs i de d sg e o ma c r a— wo f
静 态性 能 对 机 床 的最 终 加 工 性 能 有 着 非 常 重 要 的影
该机床的设计 阶段预测 了该车削中心主轴的应变和应
力 情况 , 主轴结 构进 一步 改进提 供 了相关 依据 。 为
响。随着机床速度和精度的提高 , 对其关键部件 的静
动态性 能 提 出了更 高 的设 计 和 加工 制 造 要 求 J 因 。 此 , 内外 研究 机构 和科 研 院所对 主轴 部件 的动 、 态 国 静
图 2所 示 。
为 09 , 轴 转 速 为 60 0rmn 计 算 直 径 D 为 .5 主 0 / i, 10m 6 m。利 用典 型条 件下切 削力 公式 进行计 算 : P=
得 切削 力 P= 5 . 4 3 9N。
() 1
图1 主轴 系统结构
一
,
有 2 6 4 14个 单元 和 2 2 74 8个 节点 。
AMX- 2 E一 5 23 0 SMN- 81 2 4I 9 SMX- l E* 89 08
.
1 IL _
l ■-
“ 29 I E+ 20 。 2 0 0 l E+ 渤 E
m% 5 8 E 4E g+ 9+ 叶0 + 7+ B 8B。 矗6 。 8
2 1 . 89 52
3 60 9 3 .7
3 5 . 78 82
4 80 9 5 .3
5 5 . 1 58 0
5 10 9 4 3 .
6 6 23 4
6 10 6 9 5 .
6 1 34 4
7 1 4 . 72 5
9 3 28 2
8 1 0 3 6
。
2m 4
72 4
2∞ 4
5
l 7
0
2 3
5
图2 主轴 支承弹簧一 阻尼模型
图4 静力 变形云图
由于 主轴轴 承 的轴 向刚度 很 大 , 尼对 横 向振 动 阻
采用 静力学 分析 , 有 限元模 型结果如 图 4所示 , 该
特性影响很小 , 以在建立有限元模型 中仅考虑径 向 所 刚度影 响 , 用 沿 轴 向均 布 的弹 簧 一 尼 单 元 来 模 拟 利 阻
性 能展 开 了广 泛 、 入 的研究 。 深
1 车削中心主轴 系统 结构
该 车 削 中心 由床 身 、 主轴 箱 、 卡盘 、 鞍 、 座 、 床 尾 纵 横 滑板 、 电动 刀 架 、 控 系 统 、 服 驱 动 系 统 、 数 伺 电气 系 统、 液压 系统 、 却系统 及 润滑 系统等 构成 。主轴 的前 冷 后 轴承 均采用 动静 压轴 承 。图 1为该 主轴系 统设计 结
主轴的最大位移 = .3 t 且发 生在 主轴前端 。 22 m, x 由式 ( ) 到 主轴 的静 刚度 K为 23 1N t 2得 0 . /x m。
=
P
() 2
如 图 5所示 , 在外 载荷 的作 用处存 在应 力集 中 , 即 主轴上 的最高 VnMis o s 应力 为 1. a e 89MP 。经查 4 C 0r 的屈服 强度 为 75M a 即使考 虑 应力集 中的情 况 , 8 P , 根 据第 四强度理 论 , 主轴强 度依 然满足 要求 。
9 8 61O
振 型
扭转
l轴 正向弯 曲 y轴负 向弯曲 ,
摆动
z轴负向弯曲 y轴正 向弯曲 z轴负向弯曲 z轴正 向弯曲
主轴前 8阶 的振 动 特性 , 阶振 型和频 率如 表 1所示 , 各 其 中第 二 阶主轴 振 型 图分 别 如 图 6所示 。
b a i g s p o s B s d o h E p r me r d lo h p n l e r u p r . a e n t e F A aa t c mo e s n t i t s o f i t e sai a ay i i h c s
轴承 支承 。其 中 , 前支 承 处 弹簧 刚度 为 07G / 后 . N m, 支承处 弹簧 刚度 为 06G / . N m。 为避免 在模 型转换 中丢失 特征 , 利用 A S S参 数 NY 化 建模 语言 A D P L直 接 建 立 主轴 模 型 , 均 匀 划 分 网 并 格 。主轴采 用 Sl 4 元 , 轴瓦 中点 与主轴 结合 处 od5单 i 在 的圆周 截面 上沿 圆周 均 布 4个 弹 簧 阻 尼单 元 , 元 类 单 型选择 C MBN 4, 元 长度 可 按 照 各 处 轴 承 的 内外 O I1 单 圈半径 确定 。外 圈节 点 采用 关 键 点 建立 , 圈节 点 直 内
构, 采用 外装 式 电主轴 。
对 于 加工 中心 , 主轴 部件 不仅 更为 关键 , 且其 动 而 态性 能对 切 削加工 产生 很大 影 响 。主轴在 对切 削点 处 刀具 和 工 件 造 成 的 综 合 位 移 影 响 中所 占 的 比重 在 6 % ~ 0 。因此 在加 工 中心 设 计 中 , 证 主 轴 部 件 0 8% 保 具 有较 好 的静 动态 特性 是十 分重 要 的。 。 。 J 以所 设 计 的 车 削 中 心 主轴 为 研 究 对 象 , 过 A . 通 P D L语 言建 立 主轴 的三维 有 限元参 数化 模 型 , 主轴 进 对 行静 动态 分析 , 比较 了 主轴 在 共 振 和设 计 工 况 下 的振 型 , 出该 主轴 的危 险 点并 进 行 了相 关 验 算 。从 而 在 找
g ne C nd湖『设计与研究 a h R
车 削 中 心 主 轴 动 静 态 特 性分 析
李金华① 刘永 贤① 于 杨① 韩 家亮① ②
( 东 北大 学机械 工 程 与 自动 化 学院 , 宁 沈 阳 10 0 ; ① 辽 10 4
②辽宁工业大学机械工程学院, 辽宁 锦州 110 ) 20 1 摘 要 : 以车削中心主轴为研究对 象, 采用弹簧阻尼单元模拟动静压轴承支承的方法。 建立主轴三维有限元 参数化 模 型 。同 时进行静 力学分 析 、 态分 析 , 模 分别 得 到静 刚 度 、 有频 率 和振 型 , 通 过谐 响 应分 固 并
3 结果 与 讨 论
3 1 主 轴静 态分析 .
该机床电动机功率 P 为 2 W, 3k 传动系统效率 叼
.
∥
dU ‘ l
3 - M
Dia sr设计与研究 endea S nReh g c
表 1 主 轴 固 有频 率 与 振 型
阶次 频率/ Hz 临 界 转 速 / rmn (/ i) 1 073 0 . 3 ×l~ 2 4 1 9 8 .2
国家科 技重 大专项 ( 09 X 4 0 — 5 ) 20 Z 0 0 1 0 3
2 有限元参数化建模
在 建 立有 限元 模 型 的过 程 中 , 用 弹簧 一 尼 单 采 阻 元模 拟 动静 压轴 承 的弹 性支 承 , 每个 支 承 采用 4个 沿
圆周方向均匀分布的弹簧一 阻尼单元来模拟 。分别 J 建立了使用两组弹簧来模拟主轴支承情况的模型 , 如
NODAb S OLUT ON I S TEP =1 SUB-1 T ME-1 I
S Q EV
[ Gl A V
接选择划分网格后主轴上相应节点 , 同时保证 弹簧单 元的划分数 目为 1外圈节点限制全部 自由度 , , 内圈节