精馏塔控制系统(2020年10月整理).pdf
精馏塔温度控制系统设计
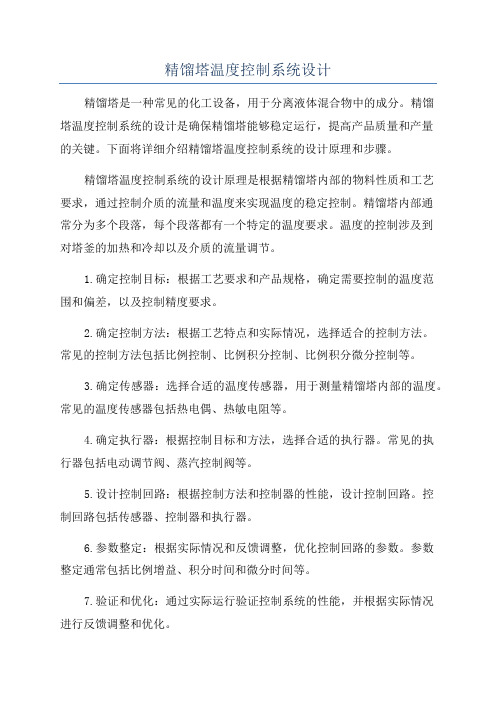
精馏塔温度控制系统设计精馏塔是一种常见的化工设备,用于分离液体混合物中的成分。
精馏塔温度控制系统的设计是确保精馏塔能够稳定运行,提高产品质量和产量的关键。
下面将详细介绍精馏塔温度控制系统的设计原理和步骤。
精馏塔温度控制系统的设计原理是根据精馏塔内部的物料性质和工艺要求,通过控制介质的流量和温度来实现温度的稳定控制。
精馏塔内部通常分为多个段落,每个段落都有一个特定的温度要求。
温度的控制涉及到对塔釜的加热和冷却以及介质的流量调节。
1.确定控制目标:根据工艺要求和产品规格,确定需要控制的温度范围和偏差,以及控制精度要求。
2.确定控制方法:根据工艺特点和实际情况,选择适合的控制方法。
常见的控制方法包括比例控制、比例积分控制、比例积分微分控制等。
3.确定传感器:选择合适的温度传感器,用于测量精馏塔内部的温度。
常见的温度传感器包括热电偶、热敏电阻等。
4.确定执行器:根据控制目标和方法,选择合适的执行器。
常见的执行器包括电动调节阀、蒸汽控制阀等。
5.设计控制回路:根据控制方法和控制器的性能,设计控制回路。
控制回路包括传感器、控制器和执行器。
6.参数整定:根据实际情况和反馈调整,优化控制回路的参数。
参数整定通常包括比例增益、积分时间和微分时间等。
7.验证和优化:通过实际运行验证控制系统的性能,并根据实际情况进行反馈调整和优化。
总之,精馏塔温度控制系统的设计是确保精馏塔能够稳定运行,提高产品质量和产量的关键。
设计步骤包括确定控制目标、控制方法、传感器和执行器的选择、设计控制回路、参数整定以及验证和优化。
合理的设计能够使温度控制更加稳定和可靠。
精馏塔控制系统设计

精馏塔控制系统设计精馏塔控制系统是指用于控制精馏装置运行的自动化系统。
精馏塔是化工过程中常用的一种分离设备,用于将混合物按照不同组分进行分离,并获得精馏产品。
精馏塔控制系统设计的目标是实现对塔内温度、压力、流量等参数的自动调节,以保持塔的稳定运行和达到设定的产品品质和产量要求。
1.系统的安全性:由于精馏塔操作涉及到高温高压的条件,系统的安全性是首要考虑因素。
安全系统应该能及时发现并处理可能的危险情况,如超压、超温等,确保塔内的操作条件始终处于安全范围内。
2.过程控制策略:根据塔的物料性质和操作要求,设计合理的控制策略。
常见的控制策略包括温度控制、压力控制、流量控制等。
需要根据塔内的反应动力学特性和传热传质特性来优化控制策略,比如采用多变量控制或者模型预测控制等。
3.仪表设备选型:根据控制策略选择合适的仪表设备,如温度传感器、压力传感器、流量计等。
仪表设备应具有高精度、稳定性好和耐高温高压等特点,以满足精馏塔操作的要求。
4.控制系统架构设计:根据控制策略和仪表设备的选择,设计控制系统的架构。
控制系统通常包括传感器、执行器、控制器和通信网络等部分。
传感器用于测量塔内的物理参数,执行器用于调节塔内的操作条件,控制器用于处理传感器的测量信号并确定下一步的控制策略,通信网络用于传输和共享数据。
5.监控系统设计:精馏塔的操作过程需要实时监控,及时发现和处理异常情况。
监控系统应能对塔内各项参数进行实时显示和记录,并提供报警、故障诊断和数据分析等功能。
监控系统可以采用人机界面、数据采集系统、故障诊断系统等多种形式。
在精馏塔控制系统的设计中,需要充分考虑各种可能的操作变量、工艺的稳定性、产量和能耗等方面的要求。
通过合理的控制系统设计,可以实现对精馏塔的准确控制,提高产品质量和产量,降低能耗和运行成本。
精馏塔控制关键因素和节能途径

精馏塔控制关键因素和节能途径摘要:精馏是化工生产中重要的基础操作,由于化工行业能耗非常高,如何实现高效节能已经成为社会及行业广泛关注的课题,化工产品生产组织过程中,精馏塔是主要的设备组成部分,也是节能降耗的重点,对此我们要在强化精馏塔控制的基础上,着力对节能降耗方面进行研究探讨。
关键词:精馏塔;控制;节能;气相流体一、精馏塔控制基本原理蒸馏是化学生产中分离溶液混合物的典型操作.它的本质是多级蒸馏,也就是在一定汽化压力下,采用不同的沸点或溶解液混合物组分的饱和,对低沸点或高蒸汽压力进行汽化,经过反复蒸发并在气态中部分冷凝后逐渐分离。
在此过程中,传热和传质过程同时进行,并受传质过程的控制。
原料从塔中间的合适位置进入塔内,其中塔的上部为不进给蒸馏,而下部为保留部分。
冷凝器提供液体从塔顶的相流入,然后沸腾器提供来自塔深的回流空气。
气相流体回流是精馏的一个重要特性。
总得来看,精馏塔是气体和液体之间提供接触设备,用于实施质量交换过程。
二、精馏塔控制关键因素(一)精馏塔稳定性为了使精馏塔稳定运行,必须保持精馏装置的平衡。
为确定原液中流量,只要给出蒸馏液中挥发性成分系数和蒸汽渣中挥发性成分系数,还可以确定蒸馏液和锅炉渣流量。
同时,压舱物中挥发性组分的分离程度和系数取决于气液与理论板数关系,因此,要根据残留立方体液体中挥发性成分的摩尔系数来确定,从一定程度上说,这种平衡及系数不能随意改变,否则将导致不平衡,最终改变塔的组成,导致功能不平衡。
(二)回流比例控制影响精馏塔分离效率的主要原因是与回流有关。
在操作和生产中,通常通过改变反比来控制产品的质量。
区间工作线的陡度与逆流成正比,该扇区的传递力与逆流成正比。
首先由于精馏塔理论板块数量限制在规定的板材数量范围内,即使回流程度增加到总流量一定限度值,其次根据整个塔架的材料平衡,分辨率极限。
(三)原料输入输出原料输入输出应随实际运行条件改变而改变,精馏塔控制一般设置有多个进给位置,以满足生产过程中的一些突发情况,主要是在精馏塔中准确、合适的位置方面进行精准把握,以保证流量安全。
精馏塔的控制方案

6
控制器正反作用的选择: 对象的作用:回流量增大,精馏塔温度降低,为反作用; 执行器作用:从安全考虑,当没有信号时,回流液量不
9
在采用精馏段温控时,当分离的产品较纯时, 由于塔顶或塔底的温度变化很小,对测温仪表的灵 敏度和控制精度都提出了很高的要求,但实际上却 很难满足。解决这一问题的方法,是将测温元件安 装在塔顶以下几块塔板的灵敏板上,以灵敏板的温 度作为被控变量。
10
11
人有了知识,就会具备各种分析能力, 明辨是非的能力。 所以我们要勤恳读书,广泛阅读, 古人说“书中自有黄金屋。 ”通过阅读科技书籍,我们能丰富知识, 培养逻辑思维能力; 通过阅读文学作品,我们能提高文学鉴赏水平, 培养文学情趣; 通过阅读报刊,我们能增长见识,扩大自己的知识面。 有许多书籍还能培养我们的道德情操, 给我们巨大的精神力量, 鼓舞我们前进。
7
• 过程选择、控制设备的选用:
根据生产工艺和用户要求,选用电动单元组合仪表 (DDZ-III ) (1)测温元件及变送器 被控温度在100℃以下,选用热电 阻温度计。为了提高检测精度,采用三线制接法,并配 用温度变送器; (2)控制阀 根据生产工艺安全原则及被控介质特点,控 制阀选用气关形式。 (3)控制器 根据过程特性与工艺要求,可选用PI控制规律。 根据构成负反馈系统原则,确定控制器为反作用方式。
能过小,即没有信号时阀门要开,执行器采用气关式, 为反作用; 控制器作用:考虑整个控制系统为负反馈,控制器采用 反作用 当精馏塔温度偏高时,控制器是反作用,所以控制器 的控制作用减弱;执行器也是反作用,档控制作用减 弱时,执行器的阀门开度是增大的,使回流液量增大, 从而使精馏段的温度降低,达到控制目的。
精馏塔常用控制方案简介
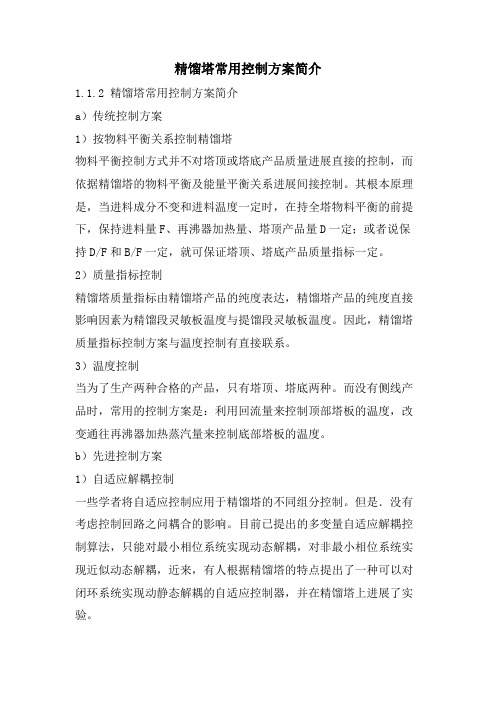
精馏塔常用控制方案简介1.1.2 精馏塔常用控制方案简介a)传统控制方案1)按物料平衡关系控制精馏塔物料平衡控制方式并不对塔顶或塔底产品质量进展直接的控制,而依据精馏塔的物料平衡及能量平衡关系进展间接控制。
其根本原理是,当进料成分不变和进料温度一定时,在持全塔物料平衡的前提下,保持进料量F、再沸器加热量、塔顶产品量D一定;或者说保持D/F和B/F一定,就可保证塔顶、塔底产品质量指标一定。
2)质量指标控制精馏塔质量指标由精馏塔产品的纯度表达,精馏塔产品的纯度直接影响因素为精馏段灵敏板温度与提馏段灵敏板温度。
因此,精馏塔质量指标控制方案与温度控制有直接联系。
3)温度控制当为了生产两种合格的产品,只有塔顶、塔底两种。
而没有侧线产品时,常用的控制方案是:利用回流量来控制顶部塔板的温度,改变通往再沸器加热蒸汽量来控制底部塔板的温度。
b)先进控制方案1)自适应解耦控制一些学者将自适应控制应用于精馏塔的不同组分控制。
但是.没有考虑控制回路之问耦合的影响。
目前已提出的多变量自适应解耦控制算法,只能对最小相位系统实现动态解耦,对非最小相位系统实现近似动态解耦,近来,有人根据精馏塔的特点提出了一种可以对闭环系统实现动静态解耦的自适应控制器,并在精馏塔上进展了实验。
2)多变量预测控制预测控制是一类以对象模型为根底的计算机控制算法,依据对象模型的不同,预测算法可粉为模型算法(MAC)、动态矩阵控制算法(DMC)、广义预测控制(GPC)等详细实现形式。
工业上应用说明:多变量预测控制到达了期望的效果,实现了常压塔的平稳操作,提高了装置适应处理量与原料性质变化的能力;并简化了控制过程,减少了劳动强度及人工干预,显著提高了产品的合格率。
1.2 问题的提出及解决问题的途径对于精馏过程中的温度控制系统,当只有塔顶、塔底两种产品,而没有侧线产品时,常用的控制方案是:利用回流量来控制顶部塔板的温度,改变通往再沸器加热蒸汽量来控制底部塔板的温度。
乙醛精制塔中自聚物的形成原因及解决措施

乙醛精制塔中自聚物的形成原因及解决措施摘要:研究了开车以来乙醛精制塔因自聚物堵塞导致无法长周期稳定运行问题,发现开车初期醋酸乙烯在塔内停留时间长、温度高是导致醋酸乙烯自聚的主要原因;经过四次技术改造后,醋酸乙烯催化剂原料活性炭中的Cl-能够与精馏系统中的H+形成盐酸,并促使乙醛自聚形成三聚乙醛、四聚乙醛,是导致塔板堵塞、中采三聚乙醛超标及馏出乙醛不合格的主要原因。
采取在T308塔中加入抑制剂,可有效降低中采三聚乙醛、四聚乙醛含量,提高馏出合格率,减缓塔内自聚物的形成并延长塔运行周期。
关键词:乙醛;三聚乙醛;四聚乙醛;盐酸;抑制剂1.乙醛精制塔运行现状及存在问题1.1乙醛精制塔工艺流程简介醋酸乙烯合成工序的粗醋酸乙烯经精馏一塔脱除解析乙炔气后,塔釜液进入精馏二塔,二塔塔顶轻组分经三级冷凝后,第三冷凝器(E308)冷凝液送精馏七塔(T307)底部,塔顶加入一定比例脱盐水进行萃取,T307顶部采出的回收液(内含VAC、Ald、丙酮及微量H2O等)进入回收液贮槽(V301);T307底部的乙醛水进入乙醛水槽(V311)后用泵给精馏八塔(乙醛精制塔,T308)加料,T308进料管线用液碱调节进料pH值在6~7。
T308塔采用醋酸乙烯装置蒸汽冷凝液闪蒸汽从塔底直接通入蒸汽加热。
T308塔顶馏出液经馏出冷凝器冷凝后部分打回流,其余送往罐场乙醛贮槽(V509)作为副产品外售。
T308塔釜废水经液位调节阀控制排至污水系统。
T308塔中部气相采出的VAC、乙醛、丙酮和水经中采冷凝器冷凝后进入精馏十二塔(T312)底部。
图1:乙醛精制塔流程简图在T312塔上部加入萃取水,T312塔塔釜萃取水经精馏九塔(T309)处理后排至中和池。
T312塔顶部采出VAC、乙醛、水进V301,V301底部设有挡板,底部富集的水通过泵送精馏七塔继续进行萃取分离,挡板溢流出的上层液通过送精馏二塔馏出槽回收。
1.2乙醛精制塔运行存在的问题1.2.1开车初期中采分层器内极易产生自聚物原设计T308塔中采为液相采出,2014年8月第一次投料开车运行大约8小时,塔内即发现有自聚现象,停车进行清理,并将塔内19-23层塔盘拆除改为集油箱。
过程控制课程设计-精馏塔温度控制系统
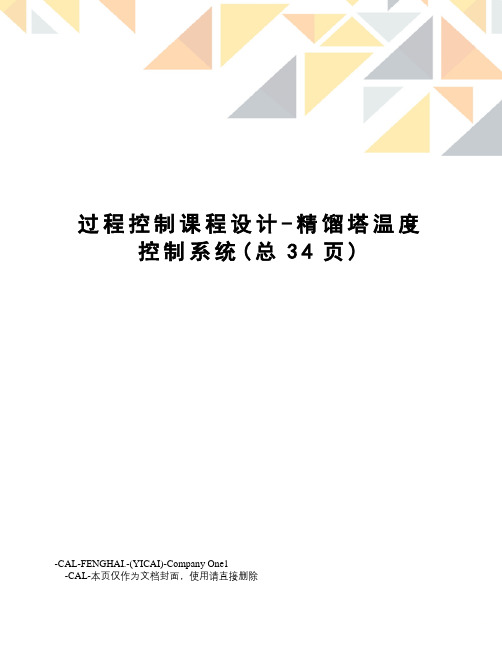
过程控制课程设计-精馏塔温度控制系统(总34页)-CAL-FENGHAI.-(YICAI)-Company One1-CAL-本页仅作为文档封面,使用请直接删除过程控制系统与仪表课程设计目录一、研究对象........................................................................................... 错误!未定义书签。
二、研究任务........................................................................................... 错误!未定义书签。
三、仿真研究要求 (4)四、传递函数计算 (5)五、控制方案........................................................................................... 错误!未定义书签。
1. 单回路反馈控制系统 (6)1) 控制方案的系统框图和工艺控制流程图............................... 错误!未定义书签。
2) PID参数整定 (7)3) 系统仿真................................................................................... 错误!未定义书签。
4) 对象特性变化后仿真 (12)2. Smith预估补偿控制系统 ................................................................ 错误!未定义书签。
1) 控制方案的系统框图和工艺控制流程图............................... 错误!未定义书签。
2) 控制系统方框图....................................................................... 错误!未定义书签。
精馏塔控制系统课程设计

精馏塔控制系统课程设计精馏塔控制系统课程设计一、概述精馏塔是化学工业中重要的分离设备之一,广泛应用于化工、石油、食品等领域。
精馏塔的主要功能是将混合液进行分离,得到高纯度的产品。
在生产过程中,精馏塔的控制系统对于保证产品质量、降低能耗、提高生产效率等方面具有重要作用。
因此,本课程设计旨在设计一个精馏塔的控制系统,以实现对混合液的分离过程进行精确控制。
二、设计要求1.了解精馏塔的工作原理及流程;2.分析精馏塔的工艺参数和控制要求;3.设计精馏塔的控制系统方案;4.选择合适的控制仪表和设备;5.完成控制系统的硬件和软件设计;6.进行系统调试和性能评估。
三、工作原理及流程精馏塔是一种基于蒸馏原理的分离设备。
在蒸馏过程中,混合液在精馏塔内被加热和冷却,使得不同成分的液体在特定温度下达到气液平衡状态。
通过这种方式,高纯度的产品可以从混合液中分离出来。
精馏塔的主要组成部分包括:原料液进料口、蒸汽加热器、分离器、冷凝器、产品收集器等。
四、工艺参数和控制要求精馏塔的主要工艺参数包括:进料流量、蒸汽流量、回流比、塔顶温度、塔底温度等。
控制要求包括:1.稳定进料流量,以保证原料液的供应;2.控制蒸汽流量,以维持所需的加热温度;3.调节回流比,以改变产品的纯度和产量;4.控制塔顶和塔底温度,以保证产品的质量和分离效果。
五、控制系统方案设计根据工艺参数和控制要求,可以采用以下控制系统方案:1.进料流量控制:采用流量计测量进料流量,通过调节阀控制进料流量;2.蒸汽流量控制:采用蒸汽压力传感器测量蒸汽压力,通过调节阀控制蒸汽流量;3.回流比控制:采用流量计测量回流比,通过调节阀控制回流比;4.塔顶温度控制:采用温度传感器测量塔顶温度,通过调节阀控制蒸汽流量,以维持温度稳定;5.塔底温度控制:采用温度传感器测量塔底温度,通过调节阀控制加热器的加热功率,以维持温度稳定。
六、控制仪表和设备选择根据控制系统方案,可以选择以下控制仪表和设备:1.流量计:用于测量进料流量和回流比;2.压力传感器:用于测量蒸汽压力;3.温度传感器:用于测量塔顶和塔底温度;4.调节阀:用于控制进料流量、蒸汽流量和回流比;5.加热器:用于加热原料液;6.PLC控制器:用于实现控制逻辑和数据处理。
- 1、下载文档前请自行甄别文档内容的完整性,平台不提供额外的编辑、内容补充、找答案等附加服务。
- 2、"仅部分预览"的文档,不可在线预览部分如存在完整性等问题,可反馈申请退款(可完整预览的文档不适用该条件!)。
- 3、如文档侵犯您的权益,请联系客服反馈,我们会尽快为您处理(人工客服工作时间:9:00-18:30)。
第6章精馏塔控制系统6.1 概述精馏是化工、石油化工、炼油生产过程中应用极为广泛的传质传热过程。
精馏的目的是利用混合液中各组分具有不同挥发度,将各组分分离并达到规定的纯度要求。
精馏过程的实质是利用混合物中各组分具有不同的挥发度,即同一温度下各组分的蒸汽分压不同,使液相中轻组分转移到气相,气相中的重组分转移到液相,实现组分的分离。
轻组分的转移提供能量;冷凝器将塔顶来的上升蒸汽冷凝为液相,并提供精馏所需的回流。
精馏过程是一个复杂的传质传热过程。
表现为:过程变量多,被控变量多,可操纵的变量也多;过程动态和机理复杂。
因此,熟悉工艺过程和内在特性,对控制系统的设计十分重要。
6.1.1 精馏塔的控制要求精馏塔的控制目标是:在保证产品质量合格的前提下,使塔的回收率最高、能耗最低,即使总收益最大,成本最小。
精馏过程是在一定约束条件下进行的。
因此,精馏塔的控制要求可从质量指标、产品产量、能量消耗和约束条件四方面考虑。
1.质量指标精馏塔的质量指标是指塔顶或塔底产品的纯度。
通常,满足一端的产品质量,即塔顶或塔底产品之一达到规定纯度,而另一端产品的纯度维持在规定范围内。
所谓产品的纯度,就二元精馏来说,其质量指标是指塔顶产品中轻组分含量和塔底产品中重组分含量。
对于多元精馏而言,则以关键组分的含量来表示。
关键组分是指对产品质量影响较大的组分,塔顶产品的关键组分是易挥发的,称为轻关键组分;塔底产品的关键组分是不易挥发的,称为重关键组分。
产品组分含量并非越纯越好,原因是,纯度越高,对控制系统的偏离度要求就越高,操作成本的提高和产品的价格并不成比例增加,因此纯度要求应与使图6.1-1 精馏塔示意图用要求适应。
2.物料平衡控制进出物料平衡,即塔顶、塔底采出量应和进料量相平衡,维持塔的正常平稳操作,以及上下工序的协调工作。
物料平衡的控制是以冷凝罐(回流罐)与塔釜液位一定(介于规定的上、下限之间)为目标的。
3.能量平衡和经济平衡性指标要保证精馏塔产品质量、产品产量的同时,考虑降低能量的消耗,使能量平衡,实现较好的经济性。
4.约束条件精馏过程是复杂传质传热过程。
为了满足稳定和安全操作的要求,对精馏塔操作参数有一定的约束条件。
气相速度限:精馏塔上升蒸汽速度的最大限。
当上升速度过高时,造成雾沫带,塔板上的液体不能向下流,下层塔板的气相组分倒流到上层塔板,出现液泛现象。
最小气相速度限:指精馏塔上升蒸汽速度的最小限值。
当上升蒸汽速度过低时,上升蒸汽不能托起上层的液相,造成漏夜,使板效率下降,精馏操作不能正常进行。
操作压力限:每一个精馏塔都存在最大操作压力限制。
临界温度限:保证精馏塔的正常传热需要、保证合适的回流温度,使精馏塔能够正常操作。
6.1.2 精馏塔的扰动分析影响物料平衡的因素包括进料量和进料成分的变化、塔顶馏出物及底部出料量的变化。
影响能量平衡的因素主要包括进料温度或釜温的变化、再沸器加热量和冷凝器冷却量的变化及塔的环境温度的变化等。
扰动有可控的也有不可控的。
1. 进料流量和进料成分进料流量通常不可控但可测。
当进料流量变化较大时,对精馏塔的操作会造成很大的影响。
这时,可将进料流量做为前馈信号,引到控制系统中,组成前馈-反馈控制系统。
进料成分影响物料平衡和能量平衡,但进料成分通常不可控,多数情况下也是难以测量的。
2. 进料温度和进料热焓值进料温度和热焓值影响精馏塔的能量平衡。
控制策略是采用蒸汽压力(或流量)定值控制,或根据提馏段产品的质量指标,组成串级控制。
3. 再沸器加热蒸汽压力再沸器加热蒸汽压力影响精馏塔的能量平衡。
控制策略是组成塔压的定值控制,或将冷却水压力作为串级控制系统的副被控变量进行控制。
4.冷却水压力和温度冷却水温度的变化通常不大,对冷却水可不进行控制。
使用风冷时控制时策略是根据塔压进行浮动塔压控制。
5.环境温度环境温度的变化较小,且变化幅度不大,因此,一般不用控制。
6.2 精馏塔的特性6.2.1 精馏塔的精态特性精馏塔的精态特性可以通过分析塔的基本关系来表述,即物料平衡和能量平衡关系。
以图6.1-1所示的二元简单精馏过程为例,说明精馏塔的基本关系。
1.物料平衡关系一个精馏塔,进料与出料应保持物料平衡,即总物料量以及任一组分都符合物料平衡关系。
图6.1-1所示的精馏过程,其物料平衡关系为:总物料平衡 B D F += (6.2-1) 轻组分平衡 B D f x B x D z F ⋅+⋅=⋅ (6.2-2) 由式(6.2-1)和(6.2-2)联立可得: B B f D x x z DF x +−=)( 或 BD f D x x z x F D −−= (6.2-3) 式中 F 、D 、B ——分别为进料、顶馏出液和底馏出液流量;f z 、D x 、B x ——分别为进料、顶馏出液和底馏出液中轻组分含量。
同样也可写成: BD f D x x z x F B −−= (6.2-4) 从上述关系可看出:当F D 增加时将引起顶、底馏出液中轻组分含量减少,即D x 、B x 下降。
而当F B 增加时将引起顶、底馏出液中轻组分含量增加。
即D x 、B x 上升。
然而,在F D (或F B )一定,且f z 一定的条件下并不能完全确定D x 、B x 的数值,只能确定D x 与B x 之间的比例关系,也就是一个方程只能确定一个未知数。
要确定D x 与B x 两个因数,必须建立另一个关系式:能量平衡关系。
2.能量平衡关系在建立能量平衡关系时,首先要了解一个分离度的概念。
所谓分离度s 可用下式表示:)1()1(D B B D x x x x s −−= (6.2-5) 从式(6.2-5)可见:随着分离度s 的增大,而B x 减小,说明塔系统的分离效果增大。
影响分离度s 的因素很多,诸如平均挥发度、理论塔板数、塔板效率、进料组分、进料板位置以及塔内上升蒸汽量V 和进料量F 的比值等。
对于一个既定的塔来说: )(FV f s ≈ (6.2-6) 式(6.2-6)的函数关系也可用一近似式表示:β=F V In s (6.2-7) 或可表示为: β=F V In )1()1(D B B Dx x x x −− (6.2-8) 式中β为塔的特性因子。
由式(6.2-7)、(6.2-8)可以看出,随着F V 增加,s 值提高。
也就是D x 增加,B x 下降,分离效果提高了。
由于V 是由再沸器施加热量来提高的,所以该式实际是表示塔的能量对产品成分的影响,故称为能量平衡关系式。
而且由上述分析可见:F V 的增大,塔的分离效果提高,能耗也将增加。
对于一个既定的塔,包括进料组分一定,只要F D /和F V 一定,这个它的分离结果,即D x 与B x 将被完成确定。
也就是说,由一个塔的物料平衡关系与能量平衡关系两个方程式,可以确定塔顶和塔底组分两个待定因数。
上述结论与一般工艺书中所说保持回流比D L R =一定,就确定了分离结果是一致的。
精馏塔的各种扰动因素都是通过物料平衡和能量平衡的形式来影响塔的操作。
因此,弄清精馏塔中的物料平衡和能量平衡关系,为确定合理的控制方案奠定了基础。
6.2.2 精馏塔的动态特性1.动态方程的建立精馏塔是一个多变量、时变、非线性对象。
对其动态特性的研究,人们已经做了不少工作。
要建立整塔的动态方程,首先要对精馏塔的各部分:精馏段、提留段各塔板,进料板,塔顶冷凝器,回流罐,塔釜、再沸器等分别建立各自得动态方程。
以图6.2-1所示二元精馏塔第j 块塔板为例说明如何建立单板动态方程。
总物料平衡:dt dM V V L L j j j j j =−+−−+11 (6.2-9)轻组分平衡: dt x M d y V y V x L x L j j j j j j j j j j ][1111=−+−−−++(6.2-10)式中:L 表示回流量,下标指回流液来自哪块板;V 表示上升蒸汽量,下标指来自哪一块板的上升蒸汽;M 指液相的蓄存量;y x 、分别指液相和气相中轻组分的含量,同样下标指回流液及上升蒸汽来自哪块塔板。
由于各部分的动态方程。
可整理得到整塔的动态方程组。
对于整个精馏塔来说是一个多容量的,相互交叉连接的复杂过程,要整理出整塔的传递函数是相当复杂的。
2. 动态影响分析通过上面的讨论,可知精馏塔动态方程的建立是复杂的,尤其建立一个精确而又实用的动态方程更是具有一定的难度。
因此从定性的角度来分析精馏塔的动态影响,对合理设计控制方案有积极的指导意义。
1) 上升蒸汽和回流的影响在精馏塔内,由于上升蒸汽只需克服塔板上极薄覆盖的液相阻力,因此上升蒸汽量的变化几秒钟内就可影响到塔顶,也就是说上升蒸汽流量变化的影响是相当快的。
然而由塔板下流的液相有相当大的滞后。
当回流量增加时,必须先使积存在塔板上的液相蓄存量增加,然后在这增加的液体静压柱的作用下,才使离开塔板的液相速度增加,所以对回流量变化的响应存在着滞后。
由此可得出这样的结论:要使塔上的任何一处(除塔顶塔板外)的气液比发生变化,用再沸器的加热量作为控制手段,要比回流量的响应快。
2) 组分滞后的影响V 和L 的变化,引起D x 和B x 的变化,都是通过每块塔板上组分之间的平衡施加影响的结果。
由于组分要达到静态平衡需要一定的时间,所以尽管V 的变化可较快影响到塔顶,但要使塔顶组分浓度D x 变化达到一个新的平衡仍要经过不少的时间。
同样D 的变化也是一样。
且需花费更多的时间。
组分滞后的影响是由于塔板上的组分要等到影响组分的液相或气相流量稳定较长时间后才能建立平衡。
随着塔板上液相蓄存量的增加,组分滞后增加。
因此塔板数的增加及回流比的增加,均会造成塔板上液相蓄存量的增加,从而导致组分的滞后也增加。
当再沸器加热量Q 的增加而引起V 的增加,通过改善气、液接触,可以减少组分的滞后。
3) 回流罐蓄液量和塔釜蓄液量引起的滞后影响由物料平衡关系可知:在F 一定的情况下,改变D 和B 均能引起D x 和B x 的变化。
实际上D 的变化是通过L 的变化(在回流罐液位不变时)才能影响到塔内的气液平衡,从而控制产品的质量D x 和B x 。
然而,回流罐有一定的蓄液量,从D 变化到L 的变化会产生滞后。
同样B 的变化也是通过V 的变化(在塔釜液位不变时)才能影响到塔内的气液平衡,从而控制产品的质量D x 和B x 。
塔釜的蓄液量也会使B 的变化到V 的变化产生滞后,通常塔釜截面积要比回流罐小得多,所以,由于塔釜蓄液量引起的滞后要比回流罐的蓄液量引起的滞后小。
6.3 精馏塔被控变量的选择精馏塔被控变量的选择,主要是讨论质量控制中的被控变量的确定,以及检测点的位置等问题。
通常,精馏塔的质量指标选取有两类:直接的产品成分信号和间接的温度信号。
6.3.1 采用温度作为间接质量指标对于二元精馏塔,当塔压恒定时,温度与成分之间有一一对应的关系,因此,常用温度作为被控变量。