毕业设计英文论文翻译,五千字,翻译原文
毕业设计中英文翻译【范本模板】
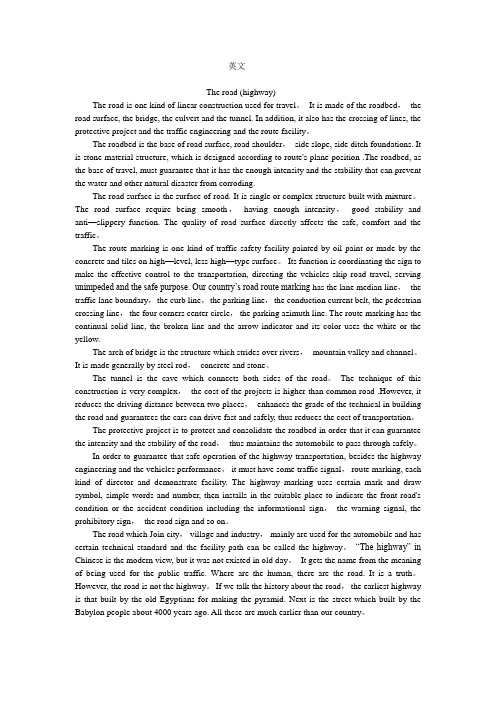
英文The road (highway)The road is one kind of linear construction used for travel。
It is made of the roadbed,the road surface, the bridge, the culvert and the tunnel. In addition, it also has the crossing of lines, the protective project and the traffic engineering and the route facility。
The roadbed is the base of road surface, road shoulder,side slope, side ditch foundations. It is stone material structure, which is designed according to route's plane position .The roadbed, as the base of travel, must guarantee that it has the enough intensity and the stability that can prevent the water and other natural disaster from corroding.The road surface is the surface of road. It is single or complex structure built with mixture。
The road surface require being smooth,having enough intensity,good stability and anti—slippery function. The quality of road surface directly affects the safe, comfort and the traffic。
毕业论文(设计)外文文献翻译及原文
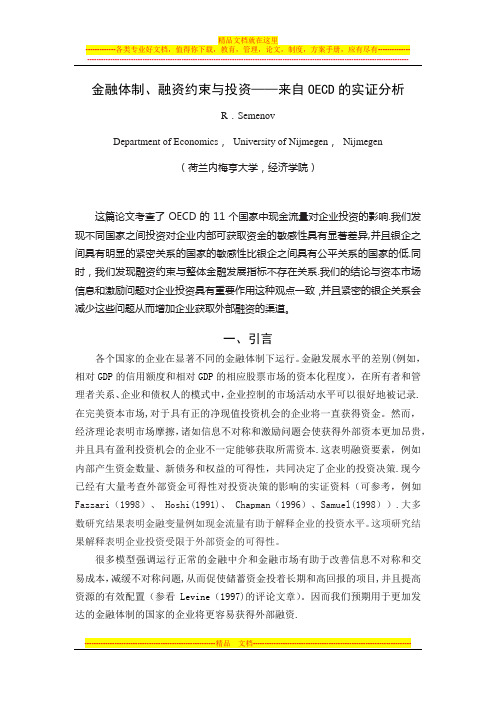
金融体制、融资约束与投资——来自OECD的实证分析R.SemenovDepartment of Economics,University of Nijmegen,Nijmegen(荷兰内梅亨大学,经济学院)这篇论文考查了OECD的11个国家中现金流量对企业投资的影响.我们发现不同国家之间投资对企业内部可获取资金的敏感性具有显著差异,并且银企之间具有明显的紧密关系的国家的敏感性比银企之间具有公平关系的国家的低.同时,我们发现融资约束与整体金融发展指标不存在关系.我们的结论与资本市场信息和激励问题对企业投资具有重要作用这种观点一致,并且紧密的银企关系会减少这些问题从而增加企业获取外部融资的渠道。
一、引言各个国家的企业在显著不同的金融体制下运行。
金融发展水平的差别(例如,相对GDP的信用额度和相对GDP的相应股票市场的资本化程度),在所有者和管理者关系、企业和债权人的模式中,企业控制的市场活动水平可以很好地被记录.在完美资本市场,对于具有正的净现值投资机会的企业将一直获得资金。
然而,经济理论表明市场摩擦,诸如信息不对称和激励问题会使获得外部资本更加昂贵,并且具有盈利投资机会的企业不一定能够获取所需资本.这表明融资要素,例如内部产生资金数量、新债务和权益的可得性,共同决定了企业的投资决策.现今已经有大量考查外部资金可得性对投资决策的影响的实证资料(可参考,例如Fazzari(1998)、 Hoshi(1991)、 Chapman(1996)、Samuel(1998)).大多数研究结果表明金融变量例如现金流量有助于解释企业的投资水平。
这项研究结果解释表明企业投资受限于外部资金的可得性。
很多模型强调运行正常的金融中介和金融市场有助于改善信息不对称和交易成本,减缓不对称问题,从而促使储蓄资金投着长期和高回报的项目,并且提高资源的有效配置(参看Levine(1997)的评论文章)。
因而我们预期用于更加发达的金融体制的国家的企业将更容易获得外部融资.几位学者已经指出建立企业和金融中介机构可进一步缓解金融市场摩擦。
毕业设计英语翻译全文
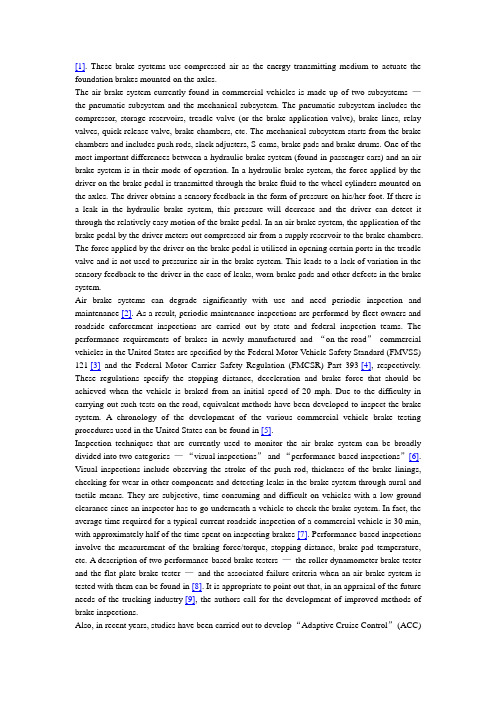
[1]. These brake systems use compressed air as the energy transmitting medium to actuate the foundation brakes mounted on the axles.The air brake system currently found in commercial vehicles is made up of two subsystems —the pneumatic subsystem and the mechanical subsystem. The pneumatic subsystem includes the compressor, storage reservoirs, treadle valve (or the brake application valve), brake lines, relay valves, quick release valve, brake chambers, etc. The mechanical subsystem starts from the brake chambers and includes push rods, slack adjusters, S-cams, brake pads and brake drums. One of the most important differences between a hydraulic brake system (found in passenger cars) and an air brake system is in their mode of operation. In a hydraulic brake system, the force applied by the driver on the brake pedal is transmitted through the brake fluid to the wheel cylinders mounted on the axles. The driver obtains a sensory feedback in the form of pressure on his/her foot. If there is a leak in the hydraulic brake system, this pressure will decrease and the driver can detect it through the relatively easy motion of the brake pedal. In an air brake system, the application of the brake pedal by the driver meters out compressed air from a supply reservoir to the brake chambers. The force applied by the driver on the brake pedal is utilized in opening certain ports in the treadle valve and is not used to pressurize air in the brake system. This leads to a lack of variation in the sensory feedback to the driver in the case of leaks, worn brake pads and other defects in the brake system.Air brake systems can degrade significantly with use and need periodic inspection and maintenance [2]. As a result, periodic maintenance inspections are performed by fleet owners and roadside enforcement inspections are carried out by state and federal inspection teams. The performance requirements of brakes in newly manufactured and “on-the-road”commercial vehicles in the United States are specified by the Federal Motor V ehicle Safety Standard (FMVSS) 121 [3]and the Federal Motor Carrier Safety Regulation (FMCSR) Part 393 [4], respectively. These regulations specify the stopping distance, deceleration and brake force that should be achieved when the vehicle is braked from an initial speed of 20 mph. Due to the difficulty in carrying out such tests on the road, equivalent methods have been developed to inspect the brake system. A chronology of the development of the various commercial vehicle brake testing procedures used in the United States can be found in [5].Inspection techniques that are currently used to monitor the air brake system can be broadly divided into two categories —“visual inspections”and “performance-based inspections”[6]. Visual inspections include observing the stroke of the push rod, thickness of the brake linings, checking for wear in other components and detecting leaks in the brake system through aural and tactile means. They are subjective, time-consuming and difficult on vehicles with a low ground clearance since an inspector has to go underneath a vehicle to check the brake system. In fact, the average time required for a typical current roadside inspection of a commercial vehicle is 30 min, with approximately half of the time spent on inspecting brakes [7]. Performance-based inspections involve the measurement of the braking force/torque, stopping distance, brake pad temperature, etc. A description of two performance-based brake testers —the roller dynamometer brake tester and the flat plate brake tester —and the associated failure criteria when an air brake system is tested with them can be found in [8]. It is appropriate to point out that, in an appraisal of the future needs of the trucking industry [9], the authors call for the development of improved methods of brake inspections.Also, in recent years, studies have been carried out to develop “Adaptive Cruise Control”(ACC)systems or “Autonomous Intelligent Cruise Control”(AICC) systems. The objective of these systems is to maintain a constant distance between two consecutive vehicles by mainly controlling the engine throttle and the brake system. While most of the research on ACC systems has focused on passenger cars, the benefits of implementing such systems on heavy trucks are significant [10].A typical ACC system for heavy trucks controls the engine throttle, the transmission and the brake system and will be interfaced with existing systems like the Antilock Braking System (ABS), Traction Control System (TCS), etc. A typical truck ABS monitors the speed of the wheels and modulates the brake system pressure in the event of an impending wheel lock-up [11]. The ABS consists of an Electronic Control Unit (ECU) that receives signals from the wheel speed sensors and processes this information to regulate the brake system pressure through modulator valves. It should be noted that ABS does not control the treadle valve to regulate the pressure in the brake system. It reduces the brake system pressure that is “commanded”by the driver when it senses an impending wheel lock-up. It cannot provide a higher pressure than that corresponding to the pedal input from the driver.It is important to note that the ABS modulates the brake system pressure only under conditions when a wheel lock-up is impending. The ABS is disengaged during “normal”braking operations. In fact, it has been pointed out in [12] that ABS is “passive during the vast majority of braking operations”. During such braking operations, the pressure of air in the brake system is the level that is commanded by the driver through the motion of the brake pedal. Hence, in order to implement ACC systems on commercial vehicles it is necessary to develop control schemes that will automatically regulate the brake system pressure during all braking operations.Motivated by the above issues, our overall objective is to develop model-based control and diagnostic systems for air brake systems. Such a model of the air brake system should correlate the pressure transients in all the brake chambers of the air brake system with the treadle valve plunger displacement (i.e., the displacement of the brake pedal) and the supply pressure of air provided from the reservoirs to the treadle and relay valves. We have already developed a model [13], and control and diagnostic schemes [14] and [15]based on this model, for the configuration of the air brake system where the primary circuit of the treadle valve is directly connected to one of the two front brake chambers. This model predicts the pressure transients in a front brake chamber during a given brake application with the input data being the treadle valve plunger displacement and the supply pressure to the treadle valve. In order to extend these control and diagnostic schemes, a model should be developed to predict the response of all the brake chambers in the air brake system. One of the steps involved in obtaining a model for the entire air brake system is to develop a model to predict the response of the relay valve, and this is the focus of this article.We will show in the subsequent sections that a relay valve has three phases (or modes) of operation and the evolution of pressure in each of the modes is different. The transition from one mode to another depends primarily on the pressure in the brake chamber and for this reason, it can be naturally modeled as a hybrid system.This article is organized as follows. In Section 2, we present a brief description of the air brake system and the experimental setup that has been constructed at Texas A&M University. A hybrid dynamical model of the relay valve to predict its pressure response is derived in Section 3. We present the equations governing the motion of the mechanical components in the relay valve and the flow of air in the system. This model is corroborated against experimental data and the resultsare provided in Section 4.2. A brief description of the air brake system and the experimental setupA layout of the air brake system found in a typical tractor is presented in Fig. 1. An engine-driven air compressor is used to compress air and the compressed air is collected in storage reservoirs. The pressure of the compressed air in the reservoirs is regulated by a governor. Compressed air is supplied from these reservoirs to the treadle and relay valves. The driver applies the brake by pressing the brake pedal on the treadle valve. This action meters the compressed air from the supply port of the treadle valve to its delivery port. Then, the compressed air travels from the delivery port of the treadle valve through air hoses to the relay valve (referred to as the service relay valve in Fig. 1) and the quick release valve and finally to the brake chambers mounted on the axles.Fig. 1. A general layout of a truck air brake system.View thumbnail imagesThe S-cam foundation brake, found in more than 85% of the air-braked vehicles in the United States [1], is illustrated in Fig. 2. Compressed air metered from the storage reservoirs enters the brake chamber and acts against the diaphragm, generating a force resulting in the motion of the push rod. The motion of the push rod serves to rotate, through the slack adjuster, a splined shaft on which a cam in the shape of an ‘S’is mounted. The ends of two brake shoes rest on the profile of the S-cam and the rotation of the S-cam pushes the brake shoes outwards so that the brake pads make contact with the rotating drum. This action results in the deceleration of the rotating drum. When the brake pedal is released by the driver, air is exhausted from the brake chamber and the push rod strokes back into the brake chamber thereby rotating the S-cam in the opposite direction. The contact between the brake pads and the drum is now broken and the brake is thus released.Fig. 2. The S-cam foundation brake.View thumbnail imagesA schematic of the experimental setup at Texas A&M University is provided in Fig. 3. Two “Type-20”brake chambers (having an effective cross-sectional area of 20 in2) are mounted on a front axle of a tractor and two “Type-30”brake chambers (having an effective cross-sectional area of 30 in2) are mounted on a fixture designed to simulate the rear axle of a tractor. The air supply to the system is provided by means of two compressors and storage reservoirs. The reservoirs are chosen such that their volume is more than twelve times the volume of the brake chambers that they provide air to, as required by the Federal Motor V ehicle Safety Standard (FMVSS) 121 [3]. Pressure regulators are mounted at the delivery ports of the reservoirs to control the supply pressure to the treadle valve and the relay valve. A cross-sectional view of the treadle valve used in the experiments is illustrated in Fig. 4. The treadle valve consists of two circuits —the primary circuit and the secondary circuit. The delivery port of the primary circuit is connected to the control port of the relay valve and the delivery ports of the relay valve are connected to the two rear brake chambers. The relay valve has a separate port for obtaining compressed air supply from the reservoir. The delivery port of the secondary circuit is connected to the Quick Release V alve (QRV) and the delivery ports of the QRV are connected to the two front brake chambers.Fig. 3. A schematic of the experimental facility.View thumbnail imagesFig. 4. A sectional view of the treadle valve.View thumbnail imagesThe treadle valve is actuated by means of a pneumatic actuator and compressed air is supplied to this actuator from the storage reservoirs through a pressure regulator. The displacement of the treadle valve plunger is measured by means of a displacement transducer. A pressure transducer is mounted at the entrance of each of the four brake chambers by means of a custom designed and fabricated pitot tube fixture. A displacement transducer is mounted on each of the two front brake chamber push rods through appropriately fabricated fixtures in order to measure the push rod stroke. All the transducers are interfaced with a connector block through shielded cables. The connector block is connected to a PCI-MIO-16E-4 Data Acquisition (DAQ) board [16] (mounted on a PCI slot inside a desktop computer) that collects the data during brake application and release. An application program is used to collect and store the data in the computer.3. Modeling the response of the relay valveIn this section, we shall present a description of the model of the relay valve. We adopt a lumped parameter approach in the development of this model. Friction at the sliding surfaces in the treadle and relay valves is neglected since they are well lubricated. The springs present in these valves have been experimentally found to be nearly linear in the range of their operation (except the rubber graduating spring used in the treadle valve, see Fig. 4) and the spring constants have been determined from experimental data. Other parameters such as areas, initial deflections, etc., are measured and used in the model.In this article, our objective is to develop a model for predicting the pressure transients in the rear brake chambers actuated by the relay valve during the brake application process. The relay valve is controlled by means of the compressed air delivered by the primary circuit of the treadle valve during a brake application. We shall consider the configuration of the brake system where the delivery port of the primary circuit of the treadle valve is connected to the control port of the relay valve. Compressed air is provided from the storage reservoirs to the relay valve at its supply port and one of the delivery ports of the relay valve is connected to a rear brake chamber. We shall measure the pressure transients at the primary delivery port of the treadle valve and in the rear brake chamber in our experiments. The pressure measured at the primary delivery port of the treadle valve will be provided as input to the numerical scheme that solves the model equations developed to predict the pressure transients in the rear brake chamber.When the driver presses the brake pedal, the primary piston in the treadle valve (see Fig. 4) first closes the primary exhaust port (by moving a distance equal to xpt) and then opens up the primary inlet port (xpp>xpt, xpp being the displacement of the primary piston from its initial position). This action serves to meter the compressed air from the reservoir to the primary delivery port. We shall refer to this phase as the “apply phase”. When the pressure in the primary circuit increases to a level such that it balances the force applied by the driver, the primary piston closes the primary inlet port with the exhaust port also remaining closed (xpp=xpt). We shall refer to this phase as the “hold phase”. When the driver releases the brake pedal, the primary piston return spring forces the primary piston to its initial position. This action opens the exhaust port (xpp<xpt) and air is exhausted from the primary delivery port to the atmosphere. We shall refer to this phase as the “exhaust phase”. A detailed derivation of the model of the treadle valve can be foundin [13].A schematic of the cross-sectional view of the relay valve used in our experimental setup is presented in Fig. 5. The compressed air from the delivery port of the primary circuit of the treadle valve enters the control port of the relay valve. The resulting force pushes the relay valve piston and the exhaust port of the relay valve is closed when the relay valve piston moves a distance equal to xrpt. Once the pre-loads on the relay valve assembly gasket are overcome, the inlet port of the relay valve is opened (xrpp>xrpt, xrpp being the displacement of the relay valve piston from its initial position). Compressed air is now metered from the supply port of the relay valve to its delivery port and subsequently to the rear brake chambers. This is the apply phase associated with the operation of the relay valve. When the pressure in the delivery port of the relay valve increases to a level such that it balances the forces acting on the relay valve piston due to the compressed air from the treadle valve, the inlet port of the relay valve is closed with its exhaust port also remaining closed (xrpp=xrpt). This is the hold phase associated with the operation of the relay valve. When the brake pedal is released by the driver, air is exhausted from the primary circuit of the treadle valve and consequently from the control port of the relay valve. Due to the presence of compressed air in the delivery port of the relay valve, the relay valve piston is pushed back to its initial position and this opens the exhaust port of the relay valve (xrpp<xrpt). Thus, air is exhausted from the delivery port of the relay valve to the atmosphere. This is the exhaust phase associated with the operation of the relay valve.Fig. 5. A sectional view of the relay valve.View thumbnail imagesThe equation of motion governing the mechanics of the operation of the relay valve piston and the relay valve assembly gasket during the apply and the hold phases is given by(1)where Mrpp and Mrv denote respectively the mass of the relay valve piston and the relay valve assembly gasket, xrpp denotes the displacement of the relay valve piston from its initial position, xrpt is the distance traveled by the relay valve piston before it closes the relay valve exhaust port, Krv is the spring constant of the relay valve assembly return spring, Fkrvi is the pre-load on the same, Arpp is the net area of the relay valve piston exposed to the pressurized air at the control port of the relay valve, Arpp1 is the net area of the relay valve piston exposed to the pressurized air at the delivery port of the relay valve, Arpp2 is the net area of the relay valve piston exposed to the exhaust port of the relay valve, Arv1 is the net cross-sectional area of the relay valve assembly gasket exposed to the pressurized air at the supply port of the relay valve, Arv2 is the net cross-sectional area of the relay valve assembly gasket exposed to the pressurized air at the delivery port of the relay valve, Ppd is the pressure of air at the delivery port of the primary circuit of the treadle valve, Prs is the pressure of air being supplied to the relay valve, Prd is the pressure of air at the delivery port of the relay valve and is the atmospheric pressure.The mass of the relay valve piston is of the order of around 0.1 kg and the magnitude of the spring and pressure forces is found to be of the order of 102 N. Thus, the acceleration required for the inertial forces to be comparable with the spring force and the pressure force terms has to be of theorder of 102–103 m/s2, which is not the case. Hence the inertial forces are neglected and the above equation reduces to(2)The equation of motion of the relay valve piston during the exhaust phase is given by(3)Neglecting inertial forces, the above equation reduces to(4)PpdArpp=Prd(Arpp1+Arpp2).Next, we will consider the flow of air in the portion of the brake system under study. The relay valve opening is modeled as a nozzle. For the flow through a restriction, if the ratio of the cross-sectional area of the upstream section to the cross-sectional area of the restriction is 4.4 or higher, the approach velocity to this restriction can be neglected and the upstream properties (such as pressure, enthalpy, temperature, etc.) can be taken to be the upstream total or stagnation properties [17]. In our case, the minimum ratio of the cross-sectional area of the supply chamber of the relay valve to the cross-sectional area of the relay valve opening (the restriction) is found to be more than this value. Hence, we can consider the valve opening as a nozzle and take the properties in the supply chamber of the valve as the stagnation properties at the inlet section of the nozzle. The flow through the nozzle is assumed to be one-dimensional and isentropic. We also assume that the fluid properties are uniform at all sections in the nozzle. Air is assumed to behave like an ideal gas with constant specific heats. Under the above assumptions, the part of the pneumatic subsystem under consideration can be visualized as illustrated in Fig. 6.Fig. 6. The simplified visualization of the pneumatic subsystem under consideration.View thumbnail imagesThe energy equation for the flow of air through the nozzle under the above assumptions can be written as [18](5)where ho is the specific stagnation enthalpy at the entrance section of the nozzle, h is the specific enthalpy at the exit section of the nozzle and u is the magnitude of the velocity of air at the exit section of the nozzle.For isentropic flow of an ideal gas with constant specific heats, the pressure (P), density (ρ) and temperature (T) are related by(6)where γis the ratio of specific heats.The mass flow rate of air from the relay valve opening at any instant of time (denoted by ) isgiven bywhere Ap is the cross-sectional area of the valve opening. This is the rate at which air is accumulating in the hoses and the brake chamber once the relay valve is actuated. Since we lump the properties of air inside the hose and the brake chamber, the mass of air in the brake chamber at any instant of time is obtained from the ideal gas equation of state as(8)where Vb is the volume of air in the brake chamber and Trd is the temperature of air in the brake chamber at that instant of time.Let us now consider the mechanics of the operation of the brake chamber. A cross-sectional view of the brake chamber is shown in Fig. 7. When the brake is applied, the brake chamber diaphragm starts to move only after a minimum threshold pressure is reached. This pressure is required to overcome the pre-loads on the diaphragm. When this pressure is attained in the brake chamber, the diaphragm moves such that the push rod is pushed out of the brake chamber. Once the brake pads contact the brake drum and steady state is reached, the volume of air in the brake chamber will be the maximum during that particular brake application. Thus, the volume of air in the brake chamber at any instant of time during the brake application process is given by(9)where V o1 is the initial volume of air in the brake chamber before the application of the brake, V o2 is the maximum volume of air in the brake chamber, Ab is the cross-sectional area of the brake chamber, xb is the displacement of the brake chamber diaphragm, i.e., the stroke of the push rod, and xbmax is the maximum stroke of the push rod.Fig. 7. A sectional view of the brake chamber.View thumbnail imagesIn our current experimental setup, the rear brake chambers are mounted on a fixture and the end of the push rod outside the brake chamber is not connected to a slack adjuster. The push rod is brought to rest during a given brake application when it strikes a plate mounted with its face perpendicular to the direction of motion of the push rod. The position of this plate can be adjusted to vary the push rod stroke. Hence, a reasonable model for the brake chamber is given by(10)where Mb is the mass of the brake chamber diaphragm, Kb is the spring constant of the brake chamber return spring and Fkbi is the pre-load on the brake chamber diaphragm return spring. It should be noted that the pressure of air in the rear brake chamber at any instant of time is assumed to be the same as the pressure of air at the delivery port of the relay valve at that instant of time. Neglecting inertial forces when compared to the force due to the pressure and spring forces, the above equation reduces toIn the case of a brake chamber mounted on an actual axle, the relationship between the push rod stroke and the brake chamber pressure has been found to be different than the one given by Eq.(11) due to the presence of additional components such as the slack adjuster, S-cam, brake pads and brake drum [15]. Thus, the model relating the push rod stroke and the brake chamber pressure for a rear brake chamber mounted on an actual rear axle should be developed as described in [15]. Differentiating Eq. (8) with respect to time and comparing the result with Eq. (7), and using Eqs.(5), (6), (9) and (11), we obtain the equation describing the pressure response of the relay valve during the apply and hold phases as(12)where Trs is the temperature of the air being supplied to the relay valve, CD is the discharge coefficient, R is the specific heat of air, γis the ratio of specific heats of air (both R and γare assumed to be constants) and(13)Ap=2πrrv(xrpp−xrpt),with rrv being the external radius of the relay valve inlet section. The discharge coefficient (CD) is used in order to compensate for the losses during the flow. Due to the complexity involved in calibrating the valve to determine the value of the discharge coefficient, we assumed a value of 0.82 for CD as recommended in [17]. The pressure transients in the brake chamber during the apply and hold phases are obtained by solving Eqs. (2) and (12) along with the initial condition that at the start of a given brake application, the brake chamber pressure is equal to the atmospheric pressure.4. Corroboration of the modelIn this section, we corroborate the model for the relay valve by comparing its predictions against experimental data obtained from various test runs carried out over a range of supply pressures. It should be noted that the typical supply pressure in air brake systems is usually between 825.3 kPa (105 psig) and 928.8 kPa (120 psig) and this is the pressure range provided by the compressor used in our experimental setup. Eqs. (2) and (12) are solved numerically to obtain the pressure transients in the rear brake chamber during the apply and hold phases of a given brake application. The pressure measured at the delivery port of the primary circuit of the treadle valveis given as the input data to the numerical scheme. The prediction of the model for a test run is compared with the data collected during that test run and the results from various test runs are presented in Fig. 8, Fig. 9, Fig. 10, Fig. 11 and Fig. 12. In these figures, time (in seconds) and brake chamber pressure (in Pa) have been plotted on the abscissa and the ordinate respectively. The value corresponds to that instant of time at which the computer program for collecting the data is started.Fig. 8. Pressure transients at 653 kPa (80 psig) supply pressure —apply phase.View thumbnail imagesFig. 9. Pressure transients at 722 kPa (90 psig) supply pressure —apply phase.View thumbnail imagesFig. 10. Pressure transients at 584 kPa (70 psig) supply pressure —apply and exhaust phases. View thumbnail imagesFig. 11. Pressure transients at 653 kPa (80 psig) supply pressure —apply and exhaust phases. View thumbnail imagesFig. 12. Pressure transients at 584 kPa (70 psig) supply pressure —repeated application.View thumbnail imagesIt can be observed from these figures that the model is able to predict the beginning and end of each brake application reasonably well. The steady state brake chamber pressure is also predicted well by the model in all the cases. The model has also captured the pressure transients well in the exhaust phase during a complete brake application and release cycle as shown in Fig. 10 and Fig. 11. It has also predicted the pressure transients well in the case of repeated brake applications as can be observed from Fig. 12.5. ConclusionsIn this article, we have developed a hybrid model for predicting the response of the relay valve used in air brake systems of commercial vehicles. The relay valve is actuated by the compressed air from the delivery port of the primary circuit of the treadle valve. We have presented the main governing equations for the pressure transients in a rear brake chamber attached to a delivery port of the relay valve. We have corroborated this model using data obtained from experimental test runs performed over a range of supply pressures. We plan to incorporate this model of the relay valve into an overall model of the air brake system which can be used in control and diagnostic applications.References[1]S.F. Williams, R.R. Knipling, Automatic slack adjusters for heavy vehicle air brake systems, Tech. Rep. DOT HS 807 724, National Highway Traffic Safety Administration, Washington, D. C., February 1991。
毕业设计中英文翻译
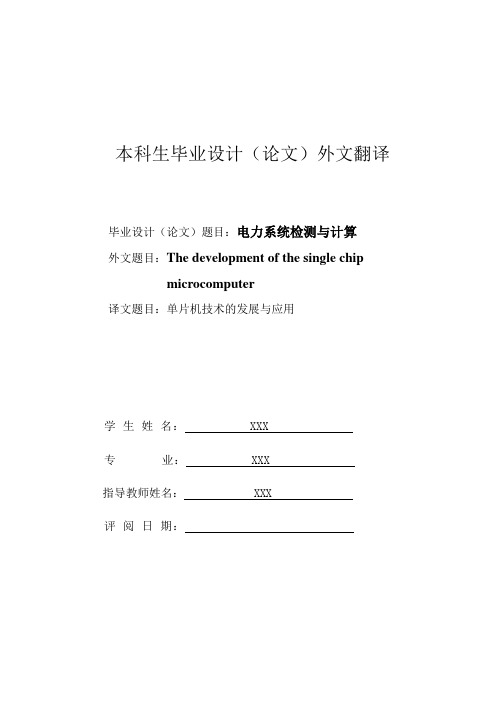
本科生毕业设计(论文)外文翻译毕业设计(论文)题目:电力系统检测与计算外文题目:The development of the single chipmicrocomputer译文题目:单片机技术的发展与应用学生姓名: XXX专业: XXX指导教师姓名: XXX评阅日期:单片机技术的发展与应用从无线电世界到单片机世界现代计算机技术的产业革命,将世界经济从资本经济带入到知识经济时代。
在电子世界领域,从 20 世纪中的无线电时代也进入到 21 世纪以计算机技术为中心的智能化现代电子系统时代。
现代电子系统的基本核心是嵌入式计算机系统(简称嵌入式系统),而单片机是最典型、最广泛、最普及的嵌入式系统。
一、无线电世界造就了几代英才。
在 20 世纪五六十年代,最具代表的先进的电子技术就是无线电技术,包括无线电广播,收音,无线通信(电报),业余无线电台,无线电定位,导航等遥测、遥控、遥信技术。
早期就是这些电子技术带领着许多青少年步入了奇妙的电子世界,无线电技术展示了当时科技生活美妙的前景。
电子科学开始形成了一门新兴学科。
无线电电子学,无线通信开始了电子世界的历程。
无线电技术不仅成为了当时先进科学技术的代表,而且从普及到专业的科学领域,吸引了广大青少年,并使他们从中找到了无穷的乐趣。
从床头的矿石收音机到超外差收音机;从无线电发报到业余无线电台;从电话,电铃到无线电操纵模型。
无线电技术成为当时青少年科普、科技教育最普及,最广泛的内容。
至今,许多老一辈的工程师、专家、教授当年都是无线电爱好者。
无线电技术的无穷乐趣,无线电技术的全面训练,从电子学基本原理,电子元器件基础到无线电遥控、遥测、遥信电子系统制作,培养出了几代科技英才。
二、从无线电时代到电子技术普及时代。
早期的无线电技术推动了电子技术的发展,其中最主要的是真空管电子技术向半导体电子技术的发展。
半导体电子技术使有源器件实现了微小型化和低成本,使无线电技术有了更大普及和创新,并大大地开阔了许多非无线电的控制领域。
毕业设计外文文献翻译(原文+译文)
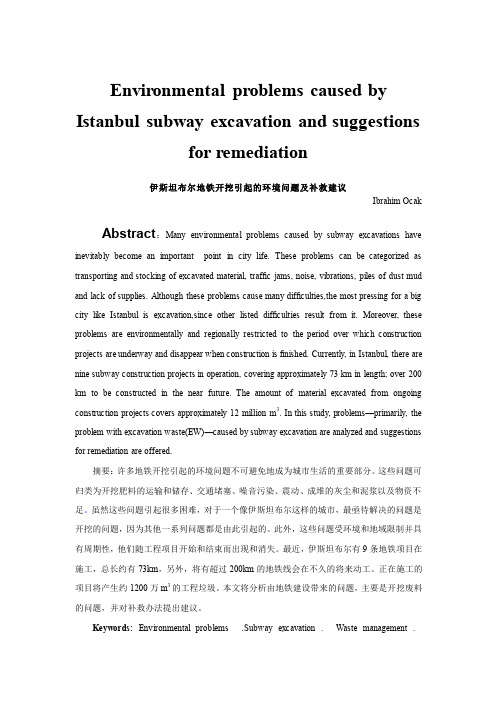
Environmental problems caused by Istanbul subway excavation and suggestionsfor remediation伊斯坦布尔地铁开挖引起的环境问题及补救建议Ibrahim Ocak Abstract:Many environmental problems caused by subway excavations have inevitably become an important point in city life. These problems can be categorized as transporting and stocking of excavated material, traffic jams, noise, vibrations, piles of dust mud and lack of supplies. Although these problems cause many difficulties,the most pressing for a big city like Istanbul is excava tion,since other listed difficulties result from it. Moreover, these problems are environmentally and regionally restricted to the period over which construction projects are underway and disappear when construction is finished. Currently, in Istanbul, there are nine subway construction projects in operation, covering approximately 73 km in length; over 200 km to be constructed in the near future. The amount of material excavated from ongoing construction projects covers approximately 12 million m3. In this study, problems—primarily, the problem with excavation waste(EW)—caused by subway excavation are analyzed and suggestions for remediation are offered.摘要:许多地铁开挖引起的环境问题不可避免地成为城市生活的重要部分。
毕业设计(论文)外文翻译【范本模板】
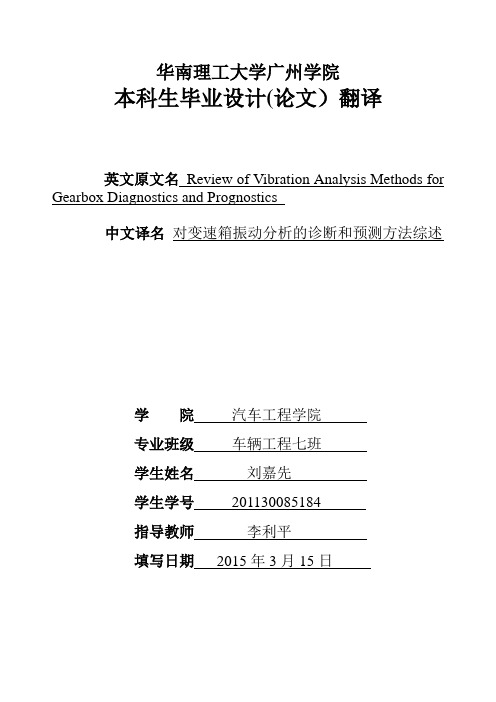
华南理工大学广州学院本科生毕业设计(论文)翻译英文原文名Review of Vibration Analysis Methods for Gearbox Diagnostics and Prognostics中文译名对变速箱振动分析的诊断和预测方法综述学院汽车工程学院专业班级车辆工程七班学生姓名刘嘉先学生学号201130085184指导教师李利平填写日期2015年3月15日英文原文版出处:Proceedings of the 54th Meeting of the Society for Machinery Failure Prevention Technology, Virginia Beach,V A, May 1-4,2000,p. 623-634译文成绩:指导教师(导师组长)签名:译文:简介特征提取技术在文献中有描述;然而,大多数人似乎掩盖所需的特定的预处理功能。
一些文件没有提供足够的细节重现他们的结果,并没有一个全面的比较传统的功能过渡齿轮箱数据。
常用术语,如“残差信号”,是指在不同的文件不同的技术.试图定义了状态维修社区中的常用术语和建立所需的特定的预处理加工特性。
本文的重点是对所使用的齿轮故障检测功能。
功能分为五个不同的组基于预处理的需要。
论文的第一部分将提供预处理流程的概述和其中每个特性计算的处理方案。
在下一节中,为特征提取技术描述,将更详细地讨论每一个功能。
最后一节将简要概述的宾夕法尼亚州立大学陆军研究实验室的CBM工具箱用于齿轮故障诊断。
特征提取概述许多类型的缺陷或损伤会增加机械振动水平。
这些振动水平,然后由加速度转换为电信号进行数据测量。
原则上,关于受监视的计算机的健康的信息被包含在这个振动签名。
因此,新的或当前振动签名可以与以前的签名进行比较,以确定该元件是否正常行为或显示故障的迹象。
在实践中,这种比较是不能奏效的。
由于大的变型中,签名的直接比较是困难的。
相反,一个涉及从所述振动署名数据特征提取更多有用的技术也可以使用。
毕业设计外文翻译原文
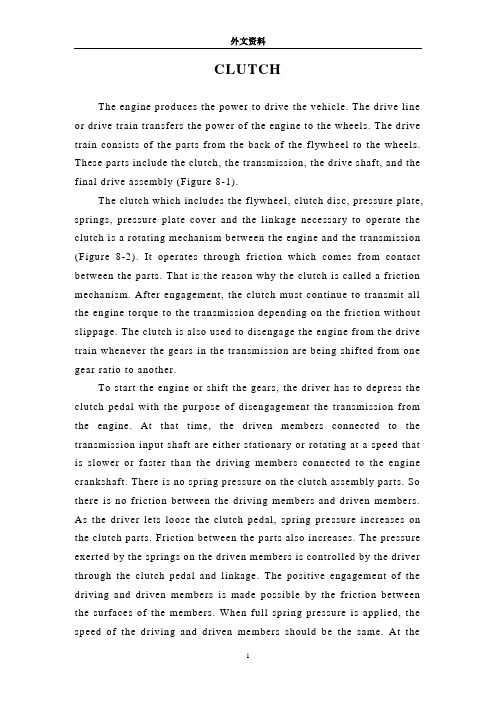
CLUTCHThe engine produces the power to drive the vehicle. The drive line or drive train transfers the power of the engine to the wheels. The drive train consists of the parts from the back of the flywh eel to the wheels. These parts include the clutch, th e transmission, the drive shaft, and the final drive assembly (Figure 8-1).The clutch which includes the flywheel, clutch disc, pressure plate, springs, pressure plate cover and the linkage necessary to operate the clutch is a rotating mechanism between t he engine and the transmission (Figure 8-2). It operates through friction which comes from contact between the parts. That is the reason why the clutch is called a friction mechanism. After engagement, the clutch must continue to transmit all the engine torque to the transmission depending on the friction without slippage. The clutch is also used to disengage the engine from the drive train whenever the gears in the transmission are being shifted from one gear ratio to another.To start the engine or shift the gears, the driver has to depress the clutch pedal with the purpose of disengagement the transmission from the engine. At that time, the driven members connected to the transmission input shaft are either stationary or rotating at a speed that is slower or faster than the driving members connected to the engine crankshaft. There is no spring pressure on the clutch assembly parts. So there is no friction between the driving members and driven members. As the driver lets loose the clutch pedal, spring pre ssure increases on the clutch parts. Friction between the parts also increases. The pressure exerted by the springs on the driven members is controlled by the driver through the clutch pedal and linkage. The positive engagement of the driving and driven members is made possible by the friction between the surfaces of the members. When full spring pressure is applied, the speed of the driving and driven members should be the same. At themoment, the clutch must act as a solid coupling device and transmit al l engine power to the transmission, without slipping.However, the transmission should be engaged to the engine gradually in order to operate the car smoothly and minimize torsional shock on the drive train because an engine at idle just develops little power. Otherwise, the driving members are connected with the driven members too quickly and the engine would be stalled.The flywheel is a major part of the clutch. The flywheel mounts to the engine’s crankshaft and transmits engine torque to the clutch assembly. The flywheel, when coupled with the clutch disc and pressure plate makes and breaks the flow of power from the engine to the transmission.The flywheel provides a mounting location for the clutch assembly as well. When the clutch is applied, the flyw heel transfers engine torque to the clutch disc. Because of its weight, the flywheel helps to smooth engine operation. The flywheel also has a large ring gear at its outer edge, which engages with a pinion gear on the starter motor during engine cranking.The clutch disc fits between the flywheel and the pressure plate. The clutch disc has a splined hub that fits over splines on the transmission input shaft. A splined hub has grooves that match splines on the shaft. These splines fit in the grooves. Thus, t he two parts are held together. However, back-and-forth movement of the disc on the shaft is possible. Attached to the input shaft, At disc turns at the speed of the shaft.The clutch pressure plate is generally made of cast iron. It is round and about the same diameter as the clutch disc. One side of the pressure plate is machined smooth. This side will press the clutch disc facing are against the flywheel. The outer side has various shapes to facilitate attachment of spring and release mechanisms. The two primary types of pressure plate assemblies are coil spri ng assembly and diaphragmspring (Figure 8-3).In a coil spring clutch the pressure plate is backed by a number of coil springs and housed with them in a pressed-steel cover bolted to the flywheel. The springs push against the cover. Neither the driven plate nor the pressure plate is connected rigidly to the flywh eel and both can move either towards it or away. When the clutch pedal is depressed a thrust pad riding on a carbon or ball thrust bearing i s forced towards the flywheel. Levers pivoted so that they engage with the thrust pad at one end and the pressure plate at the other end pull the pressure plate ba ck against its springs. This releases pressure on the driven plate disconnecting the gearbox from the engine (Figure 8-4).Diaphragm spring pressure plate assemblies are widely used in most modern cars. The diaphragm spring is a single thin sheet of metal which yields when pressure is applied to it. When pressure is removed the metal springs back to its original shape. The centre portion of the diaphragm spring is slit into numerous fingers that act as release levers. When the clutch assembly rotates with the engine these weights are flung outwards by centrifugal forces and cause the levers to pre ss against the pressure plate. During disengagement of the clutch the fingers are moved forward by the release bearing. The spring pivots over the fulcrum ring and its outer rim moves away from the flywheel. The retracting spring pulls the pressure plate a way from the clutch plate thus disengaging the clutch (Figure 8-5).When engaged the release bearing and the fingers of the diaphragm spring move towards the transmission. As the diaphragm pivots over the pivot ring its outer rim forces the pressure plate against the clutch disc so that the clutch plate is engaged to the flywheel.The advantages of a diaphragm type pres sure plate assembly are its compactness, lower weight, fewer moving parts, less effort to engage, reduces rotational imbalance by providin g a balanced force around the pressure plate and less chances of clutch slippage.The clutch pedal is connected to the disengagement mechanism either by a cable or, more com monly, by a hydraulic system. Either way, pushing the pedal down operates the dise ngagement mechanism which puts pressure on the fingers of the clutch diaphragm via a release bearing and causes the diaphragm to release the clutch plate. With a hydraulic mechanism, the clutch pedal arm operates a piston in the clutch master cylinder. Thi s forces hydraulic fluid through a pipe to the clutch release cylinder where another piston operates the clutch disengagement mechanism. The alternative is to link the clutch pedal to the disengagement mechanism by a cable.The other parts including the cl utch fork, release bearing, bell-housing, bell housing cover, and pilot bushing are needed to couple and uncouple the transmission. The clutch fork, which connects to the linkage, actually operates the clutch. The release bearing fits between the clutch fork and the pressure plate assembly. The bell housing covers the clutch assembly. The bell housing c over fastens to the bottom of the bell housing. This removable cover allows a mechanic to inspect the clutch without removing the transmission and bell housing. A pilot bushing fits into the back of th e crankshaft and holds the transmission input shaft.A Torque ConverterThere are four components inside the very strong housing of the torque converter:1. Pump;2. Turbine;3. Stator;4. Transmission fluid.The housing of the torque converter is bolted to the flywheel of the engine, so it turns at what ever speed the engine is running at. The fins that make up the pump of the torque converter are at tached to the housing, so they also turn at the same speed a s the engine. The cutaway below shows how everything is connected inside the torque converter (Figure 8-6).The pump inside a torque converter is a type of centrifugal pump. As it spins, fluid is flung to the outside, much as the spin cycle of a washing machine flings water and clothes to the outside of the wash tub. As fluid is flung to the outside, a vacuum is created that draws more fluid in at the center.The fluid then enters the blades of the turbine, which is connected to the transmission. The turbin e causes the transmission to spin, which basically moves the car. The blades of the turbine are curved. This means that the fluid, which enters the turbine from the outside, has to change direction before it exits the center of the turbine. It is this directional change that causes the turbine to spin.The fluid exits the turbine at the center, moving in a different direction than when it entered. The fluid exits the turbine moving opposite the direction that the pump (and engine) is turning. If the fluid were allowed to hit the pump, it would slow the engine down, wasting power. This is why a torque converter has a stator.The stator resides in the very center of the torque converter. Its job is to redirect the fluid returning from the turbine before it hits the pump again. This dramatically increases the efficiency of the torque converter.The stator has a very aggressive blade design that almost completely reverses the direction of the fluid. A one-way clutch (inside the stator) connects the stator to a fixed shaft in the transmission. Because of this arrangement, the stator cannot spin with the fluid - i tc a n s p i n o n l y i n t h e o p p o s i t ed i re c t i o n,f o r c i ng th e f l ui d t oc h a n g ed i re c t i o n a s i t h i t s t h e s t a t o r b l a d e s.Something a little bit tricky happens when the car gets moving. There is a point, around 40 mph (64 kph), at which both the pump and the turbine are spinning at almost the same speed (the pump alwaysspins slightly faster). At this point, the fluid returns from the turbine, entering the pump already moving in the same direction as the pump, so the stator is not needed.Even though the turbine changes the direction of the fluid and flings it out the back, the fluid still ends up moving in the direction that the turbine is spinning because the turbin e is spinning faster in one direction than the fluid is being pumped in the other direction. If you were standing in the back of a pickup moving at 60 mph, and you threw a ball out the back of that pickup at 40 mph, the ball would still be going forward at 20 mph. This is similar to what happens in the tur bine: The fluid is being flung out the back in one direction, but not as fast as it was going to start with in the other direction.At these speeds, the fluid actually strikes the back sides of the stator blades, causing the stator to freewheel on its one-way clutch so it doesn’t hinder the fluid moving through it.Benefits and Weak PointsIn addition to the very important job of allowing a car come to a complete stop without stalling the engine; the torqu e converter actually gives the car more torque when you accelerate out of a Stop. Modern torque converters can multiply the torque of the engine by two to three times. This effect only happens when the engine is turning much faster than the transmission.At higher speeds, the transmission catches up to the engine, eventually moving at almost the same speed. Ideally, though, the transmission would move at exactly the same speed as the engine, because this difference in speed wastes power. This is part of th e reason why cars with automatic transmissions get worse gas mileage than cars with manual transmissions.To counter this effect, some cars have a torque converter with alockup clutch. When the two halves of the torque converter get up to speed, this clutch locks them together, eliminating the slip page and improving efficiency.。
大学毕业论文英文翻译及原文

大学毕业论文英文翻译中文译文计算机网络每个一个世纪都有一种主导地位的技术。
18世纪伴随着工业革命的到来的是大型机械系统的时代;19世纪是蒸汽机的时代,而20世纪的发展历程中,关键的技术是信息收集、处理和分发。
在其他的发展方面,我们还可以看到:遍布全球的电话网络的建立起来了,无线电广播和电视的出现了,计算机工业诞生了,并且以超乎想象的速度在成长;另外通信卫星也发射上天了。
技术的快速发展的一个直接结果是,这些领域正在快速地融合,信息收集、传输、存储和处理之间的差别正在迅速地消失。
对于具有数百个办公室的大型组织来说,尽管这些办公室分布在广阔的地理区域中,但未来期望的情景是,工作人员只要单击一下按钮,就可以查看最远处分部的状态。
随着信息收集、处理和分发能力的不断提高,我们对于更加复杂的信息处理技术的需求也增长得更快。
与其他的工业(比如汽车和航空运输业)相比,计算机工业还是非常年轻,尽管如此,计算机技术却在很短的时间内有了惊人的进展。
在计算机诞生之初的20年间,计算机系统是高度集中化的,通常位于一个很大的房间中。
该房间通常配有玻璃墙,参观的人透过玻璃墙可以欣赏到里边伟大的电子奇迹。
中等规模的公司或者大学可能会有一台或者两台计算机,而大型的研究机构最多也就几十台计算机。
要在20年内生产出大量同样功能但是体积比邮票还小的计算机,在当时的人们看来纯属科学幻想。
计算机和通信的结合对于计算机系统的组织方式产生了深远的影响。
把一台大型的计算机放在一个单独的房间中,然后用户带着他们的处理任务去房间里上机,这种"计算机中心"的概念现在已经完全过时了。
由一台计算机来处理整个组织中所有的计算需求,这种老式的模型已经被新的模型所取代,在新的模型下,由大量独立的,但相互连接起来的计算机来共同完成计算任务。
这些系统称为计算机网络(computer networks)。
如何设计这些网络,并且将这些网络组织起来,这就是本书的主题。
- 1、下载文档前请自行甄别文档内容的完整性,平台不提供额外的编辑、内容补充、找答案等附加服务。
- 2、"仅部分预览"的文档,不可在线预览部分如存在完整性等问题,可反馈申请退款(可完整预览的文档不适用该条件!)。
- 3、如文档侵犯您的权益,请联系客服反馈,我们会尽快为您处理(人工客服工作时间:9:00-18:30)。
毕业设计英文论文翻译,五千字,翻译原文如果您想找到原文wordl版本的,请您文库中搜索——毕业设计英文论文翻译,五千字,翻译原文,自己翻译,模具类——精密注射成型技术的研究进展介绍聚合物材料的精密注射成型技术,论述影响精密注射成型的因素,包括模具的精度、注塑机的控制精度、精密注射工艺控制和其它一些计算机控制技术。
分别对这些因素进行分析讨论,并给出了相关的解决方法,最后介绍了一些先进的模塑成型技术。
关键词:精密注射;注塑机;精密注射工艺;精密注射模具近年来,随着电子、电信、医疗、汽车等行业的迅速发展,对塑料制品的高精度、高性能要求与日俱增,促使精密成型技术不断地进步,新的技术不断地涌现。
精密注射成型要求制品不仅具有较高的尺寸精度、较低的翘曲变形、优良的转写性,而且还应有优异的光学性能等[ 1 ]。
注射成型是最重要的塑料成型方法之一,包括塑料的塑化、注射、保压、冷却等几个基本的过程,因此影响精密注射成型的因素也很多。
1精密模具要制造出精密的制品,精密模具是必不可少的。
模具的精度一般受模具的温度控制、模具的精密制造和模具设计时对塑料收缩率选用等影响。
1. 1模具温度的精密控制在一般精度零件的注射成型中,控制模具温度主要是为了提高生产率。
然而模具温度控制对精密注射成型的影响极大[ 2 ] ,它影响制件的收缩、形状、结晶、内应力等,因此设计模具冷热回路时要求温度分布合理,控制精度精确,最好采用模温机和冷水机控制。
模具温度控制和冷却时间对制品性能的影响及其影响因素如下[ 3 ] :(1)塑料熔体注入和模具开模的循环时间二者会在模具中产生温度差的波动,因此应该尽量减小这种波动差峰。
(2)模具内的热量转移模具的热量是通过模具体和模具内的媒体传递出去的,模具是不变的,因此对媒体的控制是关键,一般其冷却水出入口温度差小于1℃,应用平均温度理论来计算[ 4 ] ,这样能够保证热量传递的稳定性。
媒体的流量和热量转移是相互联系的,可以用模具表面温度传感器来控制媒体流量,以补偿因环境温度变化引起的模具温度变化。
(3)模具稳定状态为使模具所吸收和散发的热量保持平衡,注塑机注射出的熔体要严格保持稳定的温度。
模具周围的温度对模具也有很大的影响,一般会影响到模具内媒体对流系数的变化,因此最好在模具表面设置温度传感器,随时观察模具表面温度,并使其保持稳定。
(4)热交换效率的变化模具用久后,在冷却水管道中会出现锈斑和水垢,这时交界面的热导率降低,应对水垢及时清除。
1. 2精密模具的设计与制造模具设计的好坏是保证塑料制件尺寸精度的前提,为了提高精密注塑模的精度,在设计过程中采用计算机辅助分析是必要的,特别是对浇注系统的流动行为和模具温度调节系统热量分布的分析等。
应尽可能地应用分析模拟软件并利用接近实际的加载条件来分析模拟熔体在模具中的浇注、冷却等非稳态的过程。
模具的制造质量是保证塑料制件尺寸精度的关键,精密模具主要的制造特点是除了抛光和装配作业外,均不用手工加工。
一般模具机械加工和手工加工的比例约为6∶4~7∶3,而精密模具的机械加工和手工加工比例为9∶1。
模具材料和热处理是模具精度的保障,在成型加工过程中,模具处于高温状态,因而即使对模具零件采用低温回火,生产时高温熔体又会对零件进行重复回火而使硬度降低,同时还应考虑残留奥氏体所引起的体积膨胀。
因此一般回火温度至少应是成型加工时模具温度的两倍以上,并适当地进行低温处理以便消除残余奥氏体。
对高精度制品,要求模具成型零件的精度、组合件累计精度、模具导向件的对中精度以及分型面的平行度应该达到微米级。
模具应有足够的强度、刚度和耐磨性,在注塑压力下不易变形、磨损。
要达到以上的加工精度可采用立体加工中心、数控机床和应用CAD /CAM /CAE等新技术。
1. 3精密模具设计时物料收缩率的选用热塑性塑料制品成型时收缩率波动较大,给模具设计、确定型腔尺寸和控制制品尺寸精度带来困难[ 5 ]。
因此在模具设计时应了解塑料的收缩特性和因制件形状而造成的各部位收缩率的差异,然后采用必要的补偿措施。
对高精度塑料件可在设计前先制造简易模具,以测出成型时各部位的实际收缩率,这样便可大大提高制件的尺寸精度[ 6 ]。
1. 4精密模具浇口的设计浇口的类型、大小、位置和数量都影响制件尺寸精度。
点浇口喷射力大,但补缩效果差,对厚壁制件不适用。
浇口位置影响熔体流向和流程远近,流程愈长收缩愈大。
多浇口可以缩短流程,但熔接痕增多。
浇口的设计应该根据制件大小和所选用的材料运用分析软件并借助于实际经验来最终确定。
2精密注射成型最佳工艺参数的设定选取最佳的成型工艺参数能够减少塑料制品的收缩率。
塑料的收缩特性是指塑料的热收缩、弹性回复、塑性变形、后收缩和老化收缩的综合反映,通常是因材料吸水或分子链重排而引起,具体表现为线性收缩率和体积收缩率的变化,常用收缩特性值表示。
热塑性塑料注塑制品成型时收缩率波动较大,特别是对于结晶性塑料注塑制品更加明显,由于结晶度不仅取决于化学结构,而且还受到加工过程中冷却参数(冷却速率、熔体温度、模具温度、制品厚度)的影响,给模具设计确定型腔尺寸和控制制品尺寸精度带来困难,所以迫切需要了解注塑工艺参数对各种塑料收缩率的影响规律[ 7 ]。
制件壁厚的差异一般认为是由两个方面的因素引起的:一是高压熔体引起的模具型腔轻微变形;二是当模具开模后材料的弹性膨胀。
一般来说,质量精度能够很好地控制尺寸精度,而在较高的模具温度里熔体的粘度较低,所以粘度梯度较小,在一定的螺杆背压下,制件的质量精度就能够得到精确的控制。
然而对于液晶聚合物(LCP)来说,它恰恰需要较低的模具温度,这是因为LCP遇冷后会迅速冷却定形。
LCP有低的熔解热和有序的结构状态,因此在液体晶态向固体晶态转变之间有较小的变化,当充分冷却时,液- 固转变几乎是在瞬间完成。
在较冷的模具中,当型腔充满时,型腔中的大部分材料和浇口已经固化,因此压缩阶段很难补充熔体,因而制件的尺寸与未变形的型腔尺寸十分接近[ 8 ]。
无定型塑料较结晶型塑料收缩率低,配混料的收缩率较纯聚合物材料低,同时随着弹性体用量的增加,材料的收缩率有所降低。
塑料经增强或填充后,热容减小,刚性增大,收缩率大幅度降低,且纤维或填充剂含量愈高,收缩率愈小[ 9 ] 。
结晶型塑料制品精度还受压力的影响。
由于压力致结晶的作用,注塑压力( P1 ) 、保压压力( P2 )和补料压力( P3 )能够加速结晶过程,因此结晶度随P1、P2、P3 的增加呈上升趋势。
对于P1 ,其压力致结晶作用提高了结晶度,使收缩率增加; P2 和P3 上升,一方面因结晶度提高使收缩率增加,另一方面P2 升高能压入更多的熔体,使型腔内塑料受到充分压实; P3 升高能增大补料量, 并有效地防止倒流, 有利于降低收缩率。
因此,塑料件的收缩率是两方面作用的结果,所以收缩率随P1、P2、P3 的升高先增加后减小[10 ]。
精密塑料件不仅要求有稳定的尺寸公差,而且还要求有严格的力学性能。
这些特性主要取决于熔体在冷却阶段的热- 机械作用的历史过程。
模具温度和冷却时间对制品质量和生产率都有直接的影响。
研究发现,在给定的模具温度下,制品的尺寸精度并不随冷却时间的延长而有明显的提高,只有在一定的时间段后才有明显的作用。
在一般冷却过程中这样的关键冷却时间点有两个,在第一个冷却时间点时虽然生产的制品精度也较高,但不是最稳定的状态,而第二个冷却时间点冷却时间比较长,但能使制品的状态最稳定[ 11, 12 ]。
3用精密注塑机代替常规注塑机精密注塑机一般都采用较大的注射功率,这样除了可以满足注塑压力和注射速率方面的要求外,注射功率本身还会对制品精度起一定的改进作用。
精密注塑机的控制系统一般都有很高的控制精度,这一点是制品本身所要求的。
高的控制精度能保证各种注射工艺参数具有良好的重复精度,以避免制品精度因工艺参数波动而发生变化。
因此精密注塑机一般都对注射量、注塑压力、注射速率、保压压力、背压和螺杆转速等工艺参数采取多级反馈控制。
精密注塑要求其合模系统有足够的刚度,否则制品精度将会因合模系统的弹性变形而降低。
其次合模系统的合模力大小必须能够精确控制,否则过大或过小的合模力都将对制品精度产生不良影响。
所以在设计时,应该综合考虑模具刚度、系统刚度以及合模力的大小以精确控制制品的精度,尤其是平板薄壁制品。
当模具面积较大时,必须对导向柱进行挠度校核[ 13 ]。
精密注塑机还必须能够对液压回路中的工作温度进行精确控制,以防工作油因温度变化而引起粘度和流量变化,进一步导致注射工艺参数波动而使制品失去应有的精度。
3. 1成型制件循环时间的一致性一般典型的注塑机有三种模式:手动、半自动、全自动。
由于各种因素的影响,在前两种模式下每次模塑的循环时间不尽相同,这会影响到模具温度和物料在料筒中的停留时间,进而影响到制件的精度,因此在精密成型中应尽量采用全自动的模式[ 14 ]。
3. 2精密注塑机的温度控制和新型螺杆的设计注塑机筒上自动调温器的循环性开和关导致了料筒内熔料密度和粘度的变化,从而影响制件质量和尺寸精度的周期性波动;注塑机的喷嘴紧靠模具型腔,所以喷嘴的温度对模塑制件也有重大的影响。
现代的注塑机配备了特殊的过程控制软件来抑制温度波动,这就是比例积分微分( P ID)控制。
至少从机筒温度差电偶的观点上来看,优化P ID参数能够完全消除温度的波动[ 15 ]。
要制得高质量和稳定的塑料件,注塑机的塑化单元是非常重要的。
对塑化单元评判的重要标准是:注射量、塑化速率、注射速率、高聚物在塑化单元的停留时间。
由于塑料件质量的误差对于尺寸精度有很重要的影响,因此应精确控制注塑机的注射量。
提高注塑机计量精度的最有效方法就是用技术上能够实现的最小的螺杆直径,特别是对于轻型制件更是如此。
由于螺杆计量段的相对长度和螺杆的整体长度变小,因此物料在塑化单元中停留的时间也会变短。
螺杆螺纹也近似地变宽,可避免物料的停留时间变长,使螺杆稳定地运行。
螺槽的宽深比也相应地变小,这对制造许多工程塑料制件的小直径螺杆尤为有效。
熔体的均一性并没有因为小压缩比而减小,这是因为由非常浅的螺槽引起非常强烈的剪切速率而导致的。
喂料段是设计的难点,它必须要保证各种粒料能够均匀地喂进去。
考虑到需要较短的循环周期,塑化速率也必须足够大,因此在设计喂料段时必须有效地解决这一对矛盾。
另外,若要通过两阶段螺杆注射来达到精确控制注射量误差,这就需要熔体的计量要通过球形检测阀由注塑机注射到活塞注塑机中[ 16 ]。
以前由微处理器控制的注射成型过程不能获得的注射精确度已经通过电压比较仪成功地解决了。
电压比较仪允许从传送器和其它敏感器传来的非常精确的电压信号通过,当设定点和真实值相吻合时有一个信号马上传送到顺序控制的微处理器,因此由顺序运行程序的循环时间引起的异步时间转移能够通过直接的信号过程来消除[ 17 ] ,大大提高了控制的精度。