现代富氧侧吹熔池熔炼
中联富氧侧吹熔池熔炼技术处理电镀污泥危险固废
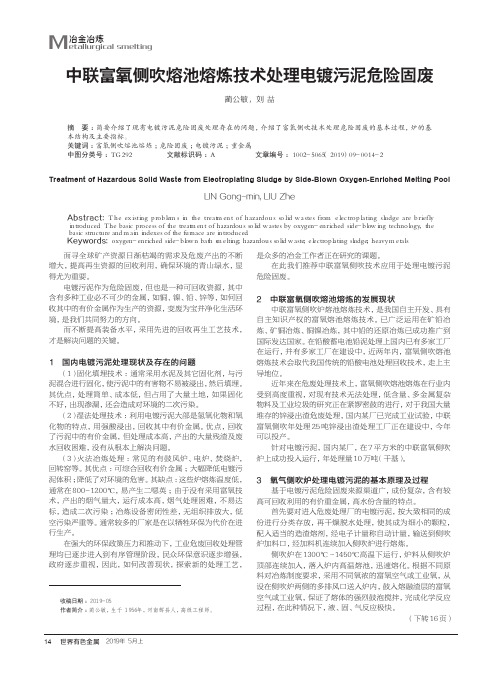
中联富氧侧吹熔池熔炼技术处理电镀污泥危险固废蔺公敏,刘 喆(新乡市中联富氧侧吹技术开发有限公司,河南 新乡 453731)摘 要:简要介绍了现有电镀污泥危险固废处理存在的问题,介绍了富氧侧吹技术处理危险固废的基本过程,炉的基本结构及主要指标。
关键词:富氧侧吹熔池熔炼;危险固废;电镀污泥;重金属中图分类号:TG292 文献标识码:A 文章编号:1002-5065(2019)09-0014-2Treatment of Hazardous Solid Waste from Electroplating Sludge by Side-Blown Oxygen-Enriched Melting PoolLIN Gong-min, LIU Zhe(Xinxiang Zhonglian Oxygen-enriched Side Blowing Technology Development Co., Ltd., Xinxiang 453731,China)Abstract: The existing problems in the treatment of hazardous solid wastes from electroplating sludge are briefly introduced. The basic process of the treatment of hazardous solid wastes by oxygen-enriched side-blowing technology, the basic structure and main indexes of the furnace are introduced.Keywords: oxygen-enriched side-blown bath smelting; hazardous solid waste; electroplating sludge; heavy metals面寻全球矿产资源日渐枯竭的需求及危废产出的不断增大,提高再生资源的回收利用,确保环境的青山绿水,显得尤为重要。
利用富氧侧吹炉熔池熔炼低品位铅锌废渣的无害化处理工艺的制作方法
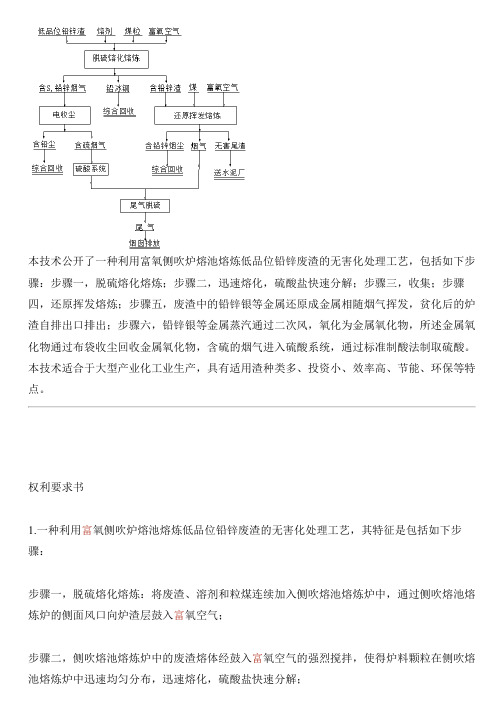
本技术公开了一种利用富氧侧吹炉熔池熔炼低品位铅锌废渣的无害化处理工艺,包括如下步骤:步骤一,脱硫熔化熔炼;步骤二,迅速熔化,硫酸盐快速分解;步骤三,收集;步骤四,还原挥发熔炼;步骤五,废渣中的铅锌银等金属还原成金属相随烟气挥发,贫化后的炉渣自排出口排出;步骤六,铅锌银等金属蒸汽通过二次风,氧化为金属氧化物,所述金属氧化物通过布袋收尘回收金属氧化物,含硫的烟气进入硫酸系统,通过标准制酸法制取硫酸。
本技术适合于大型产业化工业生产,具有适用渣种类多、投资小、效率高、节能、环保等特点。
权利要求书1.一种利用富氧侧吹炉熔池熔炼低品位铅锌废渣的无害化处理工艺,其特征是包括如下步骤:步骤一,脱硫熔化熔炼:将废渣、溶剂和粒煤连续加入侧吹熔池熔炼炉中,通过侧吹熔池熔炼炉的侧面风口向炉渣层鼓入富氧空气;步骤二,侧吹熔池熔炼炉中的废渣熔体经鼓入富氧空气的强烈搅拌,使得炉料颗粒在侧吹熔池熔炼炉中迅速均匀分布,迅速熔化,硫酸盐快速分解;步骤三,废渣中的铜和铅形成铅冰铜,沉积在炉的底部,进行收集;富含硫化物的铅锌烟气通过电收尘除尘,其中含铅的烟尘进入铅锌系统综合回收,含硫的烟气进入硫酸系统,通过标准制酸法制取硫酸;步骤四,还原挥发熔炼:经步骤三处理后的废渣加入还原煤和溶剂,同时通过侧吹熔池熔炼炉的侧面风口向炉渣层鼓入富氧空气;步骤五,废渣中的铅锌银等金属还原成金属相随烟气挥发,贫化后的炉渣自排出口排出;步骤六,铅锌银等金属蒸汽通过二次风,氧化为金属氧化物,所述金属氧化物通过布袋收尘回收金属氧化物,含硫的烟气进入硫酸系统,通过标准制酸法制取硫酸。
2.根据权利要求1所述的一种利用富氧侧吹熔池熔炼低品位铅锌废渣的无害化处理工艺,其特征是所述步骤一,侧吹熔池熔炼炉的侧面风口高度为低于静止熔池表面0.4~0.8米。
3.根据权利要求1所述的一种利用富氧侧吹炉熔池熔炼低品位铅锌废渣的无害化处理工艺,其特征是步骤一,控制炉料含水≤12%,加料量10~50吨/小时,煤粒度5~20mm,富氧浓度60%~80%,熔炼温度1050~1250ºC。
富氧侧吹熔池熔炼炉冶金炉窑热平衡的测定与计算

富氧侧吹熔池熔炼炉冶金炉窑热平衡的测定与计算富氧侧吹熔池熔炼炉冶金炉窑热平衡的测定与计算一、引言富氧侧吹熔池熔炼炉是炼钢过程中常用的设备,其热平衡的测定与计算对于炉冶金炉窑的操作和生产至关重要。
本文将对富氧侧吹熔池熔炼炉冶金炉窑热平衡的测定与计算进行深入探讨,并分享个人观点和理解。
二、富氧侧吹熔池熔炼炉的热平衡1. 热平衡的概念富氧侧吹熔池熔炼炉的热平衡是指在冶炼过程中炉内各部分热量的平衡状态。
熔炼炉内存在着多种热量的流动和转换,如化学热、辐射热、对流热等,而热平衡即是在这些热量之间达到平衡状态,确保炉内温度和热量的稳定。
2. 热平衡的测定与计算要准确测定和计算富氧侧吹熔池熔炼炉的热平衡,需要考虑炉内各部分的热量输入和输出。
首先是炉料和燃料的热量输入,其次是废气和废渣的热量输出,还需要考虑炉壁和炉底的热量损失等。
通过对这些因素的测定和计算,可以得出炉内热平衡的状态,有助于调整冶炼过程,提高炉窑热效率。
三、富氧侧吹熔池熔炼炉的热平衡测定方法1. 热量输入的测定炉料和燃料的热量输入是熔炼过程中最主要的能量来源,其测定是热平衡计算的关键。
可以通过测定燃料的热值和炉料的热容来计算其输入的热量,确保炉内能量充足,保证冶炼过程的稳定进行。
2. 热量输出的测定废气和废渣的热量输出是熔炼炉的热平衡中的重要组成部分。
通过测定废气和废渣的温度、流量等参数,可以计算其带走的热量,进而更好地控制炉内热平衡状态。
3. 热量损失的估算在熔炼炉的运行过程中,热量损失是不可避免的。
炉壁和炉底的散热、辐射热等都会导致热量的损失。
通过对炉壁和炉底的材料和结构进行分析,可以估算热量损失,从而更好地维持炉内热平衡。
四、热平衡的重要性及个人观点热平衡的合理测定和计算对于富氧侧吹熔池熔炼炉的生产和操作至关重要。
只有保持炉内的热平衡状态,才能确保熔炼过程的稳定性和高效性。
通过有效地测定和计算热平衡,可以更好地控制熔炼过程,提高冶金炉窑的生产效率和质量。
富氧侧吹熔池熔炼处理低品位含铅物料问题分析及措施
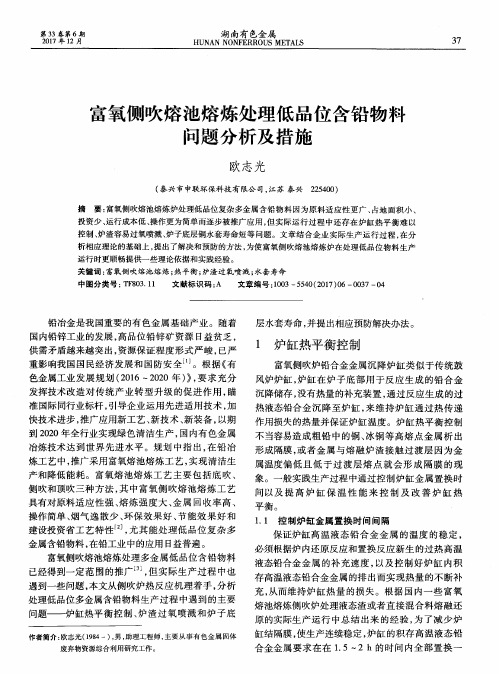
废弃物资源综合利用研究工作 。
合金金属要求在在 1 . 5~ 2 h的时间 内全部置换一
3 8
湖 南有 色金属
第3 3卷
次, 通过 控制 人 炉 原 料 的铅 品位 使 产 生 足 够 的 新 生 的过 热 液态 高温 铅 合 金 金 属 沉 降 至 炉 缸 , 不 断 置 换 出炉底逐 步 开始 降 温 的液 态 铅 合 金 金 属 , 使 炉 缸 的
作用损失 的热量并保证炉缸温度 。炉缸热平衡控制 不当容易造成粗铅 中的铜、 冰铜等高熔点金属析 出 形成 隔膜 , 或 者 金 属 与 熔 融 炉 渣 接 触 过 渡 层 因为 金 属温度偏 低且低 于过渡层 熔点 就会形成 隔膜 的现
象 。一般 实践 ห้องสมุดไป่ตู้产 过程 中通 过 控 制炉 缸 金 属 置换 时
快 技术 进 步 , 推 广应 用新 工 艺 、 新技术 、 新装备 , 以期 到2 0 2 0年全 行业 实现 绿 色清 洁 生产 , 国内有 色 金 属 冶 炼技 术 达 到世 界 先进 水 平 。规 划 中指 出 , 在 铅 冶 炼工艺中, 推广 采用 富氧 熔池 熔 炼 工艺 , 实 现 清 洁 生 产 和 降低 能耗 。富 氧 熔 池熔 炼 工 艺 主要 包 括 底 吹 、 侧 吹 和顶 吹三 种 方 法 , 其 中 富氧 侧 吹熔 池 熔 炼 工 艺 具 有对 原料 适 应 性 强 、 熔炼强度大 、 金 属 回收 率 高 、 操 作简 单 、 烟气 逸 散 少 、 环保 效果 好 、 节 能 效 果 好 和 建设 投 资省 工 艺 特 性 , 尤 其 能处 理 低 品位 复 杂 多 金属 含铅 物料 , 在 铅工 业 中的应 用 日益普 遍 。
间以及 提 高 炉 缸保 温性 能 来 控 制 及 改善 炉 缸 热
现代富氧侧吹熔池熔炼

现代富氧侧吹熔池熔炼公司标准化编码 [QQX96QT-XQQB89Q8-NQQJ6Q8-MQM9N]现代富氧侧吹熔池熔炼主要铜镍矿根据富氧侧吹熔池熔炼工艺的特点,富氧侧吹炉的结构,工艺流程及工业生产实践,富氧侧吹熔池熔炼炉具有炉料能在液态中迅速完成气、液、固三相间的主要反应,能耗低,作业环境好等特点。
项目概况铜镍矿为拓展产品领域扩大产能,治理三度污染,提高企业的竞争力,2008年喀拉通克铜镍矿责任有限公司,决定新建一套铜镍精矿熔炼系统,以逐步替代原有的传统密闭式鼓风炉系统,由于需要处理外购镍精矿和适应镍品位低氧化镁高的原料特点,经过对瓦纽科夫熔池熔炼技术和传统密闭式鼓风炉对比决定采用具有我国自主知识产权的富氧侧吹熔池熔炼技术,改造老系统的密闭鼓风炉工艺。
项目于2008年启动,2009年开始施工,工程于2010年12月基本完成,2011年3月初开始烧炉,3月15日正式报料生产。
富氧侧吹熔池熔炼炉结构性能:富氧侧吹熔池熔炼炉主长方形立式结构,主要由炉缸、炉身、炉顶、钢架等组成。
炉缸由耐水材料砌筑而成,炉缸以上为炉身,炉身由铜水套组成。
该炉最大特点是在炉身两侧一层铜水套上开有数个一次风口,用于向熔体渣层鼓入富氧空气;在炉身两侧二层铜水套上开有数个二次风口,用于向炉内鼓入一定量的空气,使烟气中的可燃成分燃烧充分;三层铜水套以上及炉顶由钢水套组成,炉顶钢水套没有固态加料口,液态料口以及排烟口。
富氧侧吹熔池熔炼炉炼的工艺流程图炉渣冰铜 烟灰 烟气水蒸气水碎返料仓 制酸生渣场水率高镍烟气烟灰吹渣镍厂精炼制酸料仓选矿按一定比例混合均匀的原料和燃料,由皮带经炉顶的加料口加入炉内,进入炉内的物料经高温烟气干燥后落入熔池,富氧压缩空气,炉身两侧的一次风口鼓入熔体渣层,在富氧压缩空气的作用下,熔体在炉内剧烈搅拌,能迅速完成熔炼及氧化造渣过程,生成的潭锍共熔体,经虹吸放出口进入沉降电炉内澄清分离,得到渣和冰铜,高温烟气经余热锅炉,送制酸系统生产制酸。
铜镍矿富氧侧吹熔池熔炼工艺
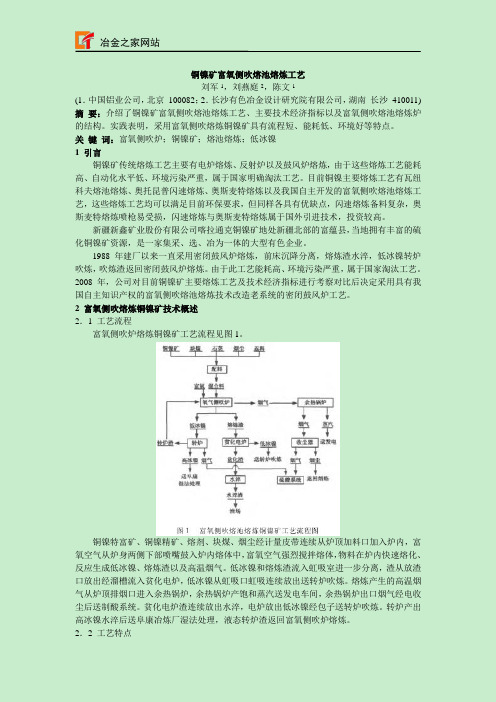
铜镍矿富氧侧吹熔池熔炼工艺刘军1,刘燕庭2,陈文1(1.中国铝业公司,北京100082;2.长沙有色冶金设计研究院有限公司,湖南长沙410011) 摘要:介绍了铜镍矿富氧侧吹熔池熔炼工艺、主要技术经济指标以及富氧侧吹熔池熔炼炉的结构。
实践表明,采用富氧侧吹熔炼铜镍矿具有流程短、能耗低、环境好等特点。
关键词:富氧侧吹炉;铜镍矿;熔池熔炼;低冰镍1 引言铜镍矿传统熔炼工艺主要有电炉熔炼、反射炉以及鼓风炉熔炼,由于这些熔炼工艺能耗高、自动化水平低、环境污染严重,属于国家明确淘汰工艺。
目前铜镍主要熔炼工艺有瓦纽科夫熔池熔炼、奥托昆普闪速熔炼、奥斯麦特熔炼以及我国自主开发的富氧侧吹熔池熔炼工艺,这些熔炼工艺均可以满足目前环保要求,但同样各具有优缺点,闪速熔炼备料复杂,奥斯麦特熔炼喷枪易受损,闪速熔炼与奥斯麦特熔炼属于国外引进技术,投资较高。
新疆新鑫矿业股份有限公司喀拉通克铜镍矿地处新疆北部的富蕴县,当地拥有丰富的硫化铜镍矿资源,是一家集采、选、冶为一体的大型有色企业。
1988年建厂以来一直采用密闭鼓风炉熔炼,前床沉降分离,熔炼渣水淬,低冰镍转炉吹炼,吹炼渣返回密闭鼓风炉熔炼。
由于此工艺能耗高、环境污染严重,属于国家淘汰工艺。
2008年,公司对目前铜镍矿主要熔炼工艺及技术经济指标进行考察对比后决定采用具有我国自主知识产权的富氧侧吹熔池熔炼技术改造老系统的密闭鼓风炉工艺。
2 富氧侧吹熔炼铜镍矿技术概述2.1 工艺流程富氧侧吹炉熔炼铜镍矿工艺流程见图1。
铜镍特富矿、铜镍精矿、熔剂、块煤、烟尘经计量皮带连续从炉顶加料口加入炉内,富氧空气从炉身两侧下部喷嘴鼓入炉内熔体中,富氧空气强烈搅拌熔体,物料在炉内快速熔化、反应生成低冰镍、熔炼渣以及高温烟气。
低冰镍和熔炼渣流入虹吸室进一步分离,渣从放渣口放出经溜槽流入贫化电炉,低冰镍从虹吸口虹吸连续放出送转炉吹炼。
熔炼产生的高温烟气从炉顶排烟口进入余热锅炉,余热锅炉产饱和蒸汽送发电车间,余热锅炉出口烟气经电收尘后送制酸系统。
现代富氧侧吹熔池熔炼
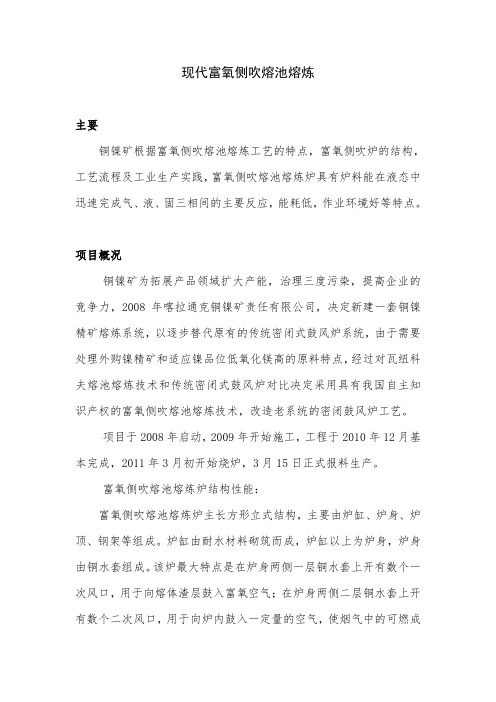
现代富氧侧吹熔池熔炼主要铜镍矿根据富氧侧吹熔池熔炼工艺的特点,富氧侧吹炉的结构,工艺流程及工业生产实践,富氧侧吹熔池熔炼炉具有炉料能在液态中迅速完成气、液、固三相间的主要反应,能耗低,作业环境好等特点。
项目概况铜镍矿为拓展产品领域扩大产能,治理三度污染,提高企业的竞争力,2008年喀拉通克铜镍矿责任有限公司,决定新建一套铜镍精矿熔炼系统,以逐步替代原有的传统密闭式鼓风炉系统,由于需要处理外购镍精矿和适应镍品位低氧化镁高的原料特点,经过对瓦纽科夫熔池熔炼技术和传统密闭式鼓风炉对比决定采用具有我国自主知识产权的富氧侧吹熔池熔炼技术,改造老系统的密闭鼓风炉工艺。
项目于2008年启动,2009年开始施工,工程于2010年12月基本完成,2011年3月初开始烧炉,3月15日正式报料生产。
富氧侧吹熔池熔炼炉结构性能:富氧侧吹熔池熔炼炉主长方形立式结构,主要由炉缸、炉身、炉顶、钢架等组成。
炉缸由耐水材料砌筑而成,炉缸以上为炉身,炉身由铜水套组成。
该炉最大特点是在炉身两侧一层铜水套上开有数个一次风口,用于向熔体渣层鼓入富氧空气;在炉身两侧二层铜水套上开有数个二次风口,用于向炉内鼓入一定量的空气,使烟气中的可燃成分燃烧充分;三层铜水套以上及炉顶由钢水套组成,炉顶钢水套没有固态加料口,液态料口以及排烟口。
富氧侧吹熔池熔炼炉炼的工艺流程图炉铜烟灰水蒸气水碎返料仓制酸生产管网渣场水率高镍烟气烟灰吹渣镍厂精炼制酸料仓选矿按一定比例混合均匀的原料和燃料,由皮带经炉顶的加料口加入炉内,进入炉内的物料经高温烟气干燥后落入熔池,富氧压缩空气,炉身两侧的一次风口鼓入熔体渣层,在富氧压缩空气的作用下,熔体在炉内剧烈搅拌,能迅速完成熔炼及氧化造渣过程,生成的潭锍共熔体,经虹吸放出口进入沉降电炉内澄清分离,得到渣和冰铜,高温烟气经余热锅炉,送制酸系统生产制酸。
工业生产实践富氧侧吹熔池熔炼炉的特点:(1)对原料的适应性强。
炉料无需干燥,细磨等特殊处理,备料简单,含6%—9%的物料可以直接入炉;(2)熔炼迅速。
富氧侧吹炼铅工艺与熔炼过程分析
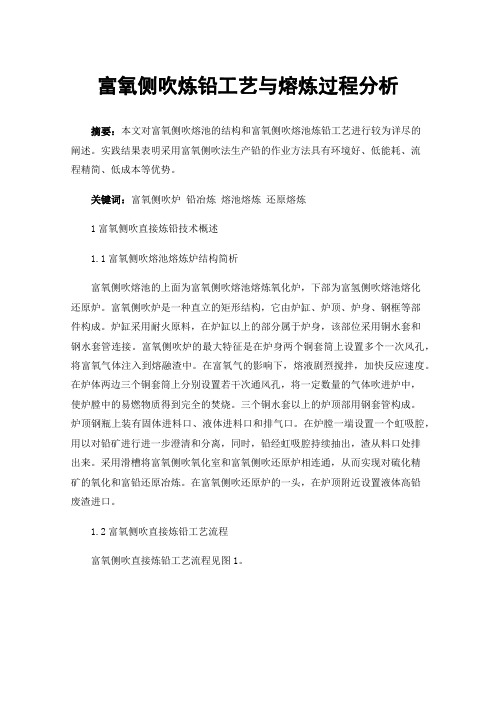
富氧侧吹炼铅工艺与熔炼过程分析摘要:本文对富氧侧吹熔池的结构和富氧侧吹熔池炼铅工艺进行较为详尽的阐述。
实践结果表明采用富氧侧吹法生产铅的作业方法具有环境好、低能耗、流程精简、低成本等优势。
关键词:富氧侧吹炉铅冶炼熔池熔炼还原熔炼1富氧侧吹直接炼铅技术概述1.1富氧侧吹熔池熔炼炉结构简析富氧侧吹熔池的上面为富氧侧吹熔池熔炼氧化炉,下部为富氢侧吹熔池熔化还原炉。
富氧侧吹炉是一种直立的矩形结构,它由炉缸、炉顶、炉身、钢框等部件构成。
炉缸采用耐火原料,在炉缸以上的部分属于炉身,该部位采用铜水套和钢水套管连接。
富氧侧吹炉的最大特征是在炉身两个铜套筒上设置多个一次风孔,将富氧气体注入到熔融渣中。
在富氧气的影响下,熔液剧烈搅拌,加快反应速度。
在炉体两边三个铜套筒上分别设置若干次通风孔,将一定数量的气体吹进炉中,使炉膛中的易燃物质得到完全的焚烧。
三个铜水套以上的炉顶部用钢套管构成。
炉顶钢瓶上装有固体进料口、液体进料口和排气口。
在炉膛一端设置一个虹吸腔,用以对铅矿进行进一步澄清和分离,同时,铅经虹吸腔持续抽出,渣从料口处排出来。
采用滑槽将富氧侧吹氧化室和富氧侧吹还原炉相连通,从而实现对硫化精矿的氧化和富铅还原冶炼。
在富氧侧吹还原炉的一头,在炉顶附近设置液体高铅废渣进口。
1.2富氧侧吹直接炼铅工艺流程富氧侧吹直接炼铅工艺流程见图1。
图1 富氧侧吹直接炼铅工艺流程图富氧侧吹氧化炉和富氧侧吹还原炉是富氧侧吹法生产中的关键技术,采用滑槽将两个富氧侧吹炉串联起来,从而达到生产的目的。
富氧侧吹氧化炉产-次粗铅和高铅渣流入氧化炉的虹吸室内,一次处理后的粗铅可供使用。
虹吸将钢块不断排出,高铅渣通过滑槽向富氧侧吹还原炉内进行。
将二次粗铅和还原后的冶炼渣流入到还原炉的虹吸腔中,用虹吸将二次粗铅不断排出,在烟气中不断喷出还原渣,通过烟气提纯。
三座高炉产生的高温烟气由余热锅炉进行余热回收,富氧侧吹式氧化炉的高温烟气经余热锅炉、电收尘器后送入制酸装置,还原炉与烟化炉高温烟气经过余热锅炉、布袋除尘器后进行脱硫处理即可排空。
- 1、下载文档前请自行甄别文档内容的完整性,平台不提供额外的编辑、内容补充、找答案等附加服务。
- 2、"仅部分预览"的文档,不可在线预览部分如存在完整性等问题,可反馈申请退款(可完整预览的文档不适用该条件!)。
- 3、如文档侵犯您的权益,请联系客服反馈,我们会尽快为您处理(人工客服工作时间:9:00-18:30)。
现代富氧侧吹熔池熔炼
主要铜镍矿根据富氧侧吹熔池熔炼工艺的特点,富氧侧吹炉的结构,工艺流程及工业生产实践,富氧侧吹熔池熔炼炉具有炉料能在液态中迅速完成气、液、固三相间的主要反应,能耗低,作业环境好等特点。
项目概况铜镍矿为拓展产品领域扩大产能,治理三度污染,提高企业的竞争力,2008 年喀拉通克铜镍矿责任有限公司,决定新建一套
铜镍精矿熔炼系统,以逐步替代原有的传统密闭式鼓风炉系统,由于需要处理外购镍精矿和适应镍品位低氧化镁高的原料特点,经过对瓦纽科夫熔池熔炼技术和传统密闭式鼓风炉对比决定采用具有我国自主知识产权的富氧侧吹熔池熔炼技术,改造老系统的密闭鼓风炉工艺。
项目于2008 年启动,2009 年开始施工,工程于2010 年12 月基本完成,2011 年3 月初开始烧炉,3 月15 日正式报料生产。
富氧侧吹熔池熔炼炉结构性能:富氧侧吹熔池熔炼炉主长方形立式结构,主要由炉缸、炉身、炉顶、钢架等组成。
炉缸由耐水材料砌筑而成,炉缸
以上为炉身,炉身由铜水套组成。
该炉最大特点是在炉身两
侧一层铜水套上开有数个一次风口,用于向熔体渣层鼓入富 氧空气;在炉身两侧二层铜水套上开有数个二次风口,用于 向炉内鼓入一定量的空气,使烟气中的可燃成分燃烧充分; 三层铜水套以上及炉顶由钢水套组成,炉顶钢水套没有固态 加料口,液态料口以及排烟口。
富氧侧吹熔池熔炼炉炼的工艺流程图
铜镍精矿、石灰石、石英砂、烟尘、粒煤、返渣
按一定比例混合均匀的原料和燃料,由皮带经炉顶的加 料口加入炉内,进入炉内的物料经高温烟气干燥后落入熔 池,富氧压缩空气,
富氧空气 石英砂 ----- 压缩空气
熔体 烟气
1
余热锅炉
-
吹渣 选矿 水率高镍 烟气
烟灰 I 气
灰 镍厂精炼
制酸 料仓 粒煤 烟灰 烟气 水蒸气
返料仓 制酸 生产管网
炉身两侧的一次风口鼓入熔体渣层,在富氧压缩空气的作用下,熔体在炉内剧烈搅拌,能迅速完成熔炼及氧化造渣过程,生成的潭锍共熔体,经虹吸放出口进入沉降电炉内澄清分离,得到渣和冰铜,高温烟气经余热锅炉,送制酸系统生产制酸。
工业生产实践
富氧侧吹熔池熔炼炉的特点:(1)对原料的适应性强。
炉料无需干燥,细磨等特殊处理,备料简单,含6%—9%的物料可以直接入炉;(2)熔炼迅速。
鼓入熔体的富氧空气对熔体进行剧烈搅拌,炉料在液态中迅速完成气、液、固三相间主要反应;(3)渣中含铜低、金属回收率高、低冰铜品位50% —60% 、渣含铜0.48% —0.6% ,回收率达到98% 。
(4)熔炼过程简便,操作方便,炉内液面稳定可调,可以根据生产中的要求,稳定所需要的高度(950mm —1250mm )液面稳定可以避免液面波动造成风量、风压等指标的波动,便于实现自动化稳定控制,液面可调,可以根据生产需要通过调整液面高度来调整氧的利用率,得到不同品位的冰铜,有着
密闭鼓风炉操作经验的人员很容易掌握该炉和操作。
(5 )综合能耗低,节能效果好,富氧侧吹炉能充分利用炉料物质的化学反应
热,对燃料的种类、质量没有什么严格要求。
燃料消耗少、生产效率高、炉子密封性好,烟气含SO 2浓度高且
稳定连续,有利于制酸,保护环境,烟尘率低,后需设施相对投资较省。
操作参考
富氧侧吹熔炼炉的技术性能参数及操作控制参数:
结束语
结合以上工作实践和有关冶金专家的认可,技术是成熟可靠的,该技术的高效节能,环保的先进性是有着由实践检验的理论为支撑的。
该
技术具有原料性适应性强、自热熔炼、燃料消耗少,烟气SO 2浓度高,投资省等特点。
目前我国淘汰密闭鼓风炉的技术改造过程中,自主创新的白银炉基础上,加上熔池熔炼技术的特点,自主他新的双侧吹熔池熔炼富氧沸腾熔池熔炼技术孕育而生,且扩展了应用领域。