冷轧低碳钢连续退火生产工艺优化方案研究
低合金结构用冷轧钢带L280VK的退火工艺及优化

LU Changchun
FAN Lei
(Technique Center) (Cold-rolled Strip Mil1) (Technique Center)
Abstract: The recrystallization temperature of L280VK low——alloy structural cold-rolled strip was deter- mined with hardness ana lyzing method and metallographic testing method;and the anneMing process of the batch type anneM ing furnace was tested and optimized.
2015年第 4期
柳 钢 科 技
I
低合金结构用冷轧钢带 L280VK的退火工艺及优化
董苑 华 陆长 春 樊 雷 (技 术 中心) (冷 轧厂 ) (技 术 中心 )
摘 要 :以硬 度 分析 法 、金 相 试 验 法 测 定低 合金 结 构 用冷 轧 钢 带 L280VK再 结 晶温 度 ,并试 验 优 化 了罩 式退 火炉退 火5--艺 。
根 据 再 结 晶温 度 测 试 方 法 ,将 一 批 冷 硬 状
作 者 :董 苑 华 , 大 学 学历 , 工程 师 ,现 从 事 轧钢 工 艺 管理 与 产 品 开 发 工 作 。
态 的低 合 金 结 构 用 钢 L280VK试 样 放 进 电 阻 塔 丝 加 热 炉 ,然 后 将 炉 内温 度 依 次 加 热 到 500、
l— — 底 座 及 导 霄 ;2— — 浮 块 及 滑 杆 ;3— — 接 近 开 关 固定支架 ;4-— 撼 应块 ; 5——接近开关
冷轧Q195F钢种退火工艺制度的优化

试验方案 1 1 2 2 3 3 3 3 4 4
表2 不同试验方案性能结果
堆垛重量/t 106 105 103 109 112 112 102 98 98 97
却过程中,有一个温度最高点(热点)和最低点(冷点),通过理论和实际测量也证明了这一点,
如图1所示。 实验测得,每卷的热点在钢卷的边部,冷
点通常在钢卷心部靠内侧。堆垛方式不同,炉
内 各 卷 的 冷 点 排 序 位 置 也 是 不 同 的 (图 2所
示 )。 堆 垛 重 量 、 钢 卷 宽 度 和 带 钢 厚 度 均 对 工 艺制度有一定的影响。因此,只有综合考虑上
图4 分流冷却系统启动温度对冷却时间影响示意图 (1)500℃;(2)475℃;(3)450℃;(4)400℃ (4)出 炉 温 度 制 定 原 则 及 实 验 结 果 根 据 资 料 介 绍 , 卷 心 温 度 (冷 点 温 度 )不 高 于 160℃ 出 炉 , 钢 卷 表 面 不 会 产 生 氧 化 。 根 据 此 经 验 , 分 别 制 定 了 105、 100、 95和 90℃ 不 同 出 炉 温 度 , 并 检 验 带 钢 表 面 是 否 氧 化 。 经 多 次 实 验 得 出 , 即 使 在 105℃ 出 炉 (实 测 卷 心 温 度 小 于 160℃ ), 未 发 现 带 钢 表 面 氧 化 。 统 计 得 出 出 炉 温 度 每 提 高 5℃ , 冷 却 时 间 平 均 可 缩 短 30min。 2. 3 氢 气 吹 扫 制 度 的 改 进 (1)氢 气 吹 扫 制 度 制 定 原 则
保温时间/h 减少2 同上 减少3~4 同上
万方数据
24 物 理 测 试 2000年 第 6期
按 表 1中 , 1~ 4方 案 随 机 选 取 不 同 规 格 、 堆 垛 重 量 共 10炉 , 修 改 加 热 速 度 、 保 温 时 间 和 保 温 温 度 等 工 艺 参 数 进 行 试 验 、 跟 踪 , 取 得 力 学 性 能 数 据 (见 表 2)。
低合金钢冷轧薄板的退火工艺优化研究
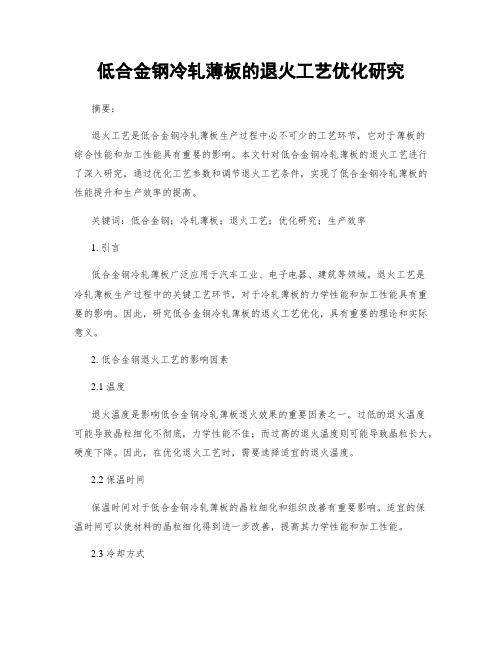
低合金钢冷轧薄板的退火工艺优化研究摘要:退火工艺是低合金钢冷轧薄板生产过程中必不可少的工艺环节,它对于薄板的综合性能和加工性能具有重要的影响。
本文针对低合金钢冷轧薄板的退火工艺进行了深入研究,通过优化工艺参数和调节退火工艺条件,实现了低合金钢冷轧薄板的性能提升和生产效率的提高。
关键词:低合金钢;冷轧薄板;退火工艺;优化研究;生产效率1. 引言低合金钢冷轧薄板广泛应用于汽车工业、电子电器、建筑等领域。
退火工艺是冷轧薄板生产过程中的关键工艺环节,对于冷轧薄板的力学性能和加工性能具有重要的影响。
因此,研究低合金钢冷轧薄板的退火工艺优化,具有重要的理论和实际意义。
2. 低合金钢退火工艺的影响因素2.1 温度退火温度是影响低合金钢冷轧薄板退火效果的重要因素之一。
过低的退火温度可能导致晶粒细化不彻底,力学性能不佳;而过高的退火温度则可能导致晶粒长大,硬度下降。
因此,在优化退火工艺时,需要选择适宜的退火温度。
2.2 保温时间保温时间对于低合金钢冷轧薄板的晶粒细化和组织改善有重要影响。
适宜的保温时间可以使材料的晶粒细化得到进一步改善,提高其力学性能和加工性能。
2.3 冷却方式冷却方式是影响低合金钢冷轧薄板组织和性能的重要因素。
不同的冷却方式对晶粒的长大和相变过程具有不同的影响。
水冷是一种常用的冷却方式,可以使晶粒得到更好的细化,提高低合金钢冷轧薄板的强度和韧性。
3. 低合金钢冷轧薄板退火工艺优化方法3.1 基于试验设计的工艺优化通过设计试验矩阵,分析不同工艺参数对低合金钢冷轧薄板性能的影响,确定最佳工艺参数组合。
采用正交试验设计等方法,有效地减少了试验次数,提高了工艺优化的效率。
3.2 数值模拟优化利用有限元数值模拟方法,对低合金钢冷轧薄板的退火工艺进行数值模拟,分析退火过程中的温度场和应力场,预测材料的织构、晶粒大小以及相变行为。
通过优化数值模拟结果,确定最佳的退火工艺参数。
3.3 综合优化方法结合试验设计和数值模拟方法,进行综合优化。
SPCC薄板冷轧及连续退火工艺研究
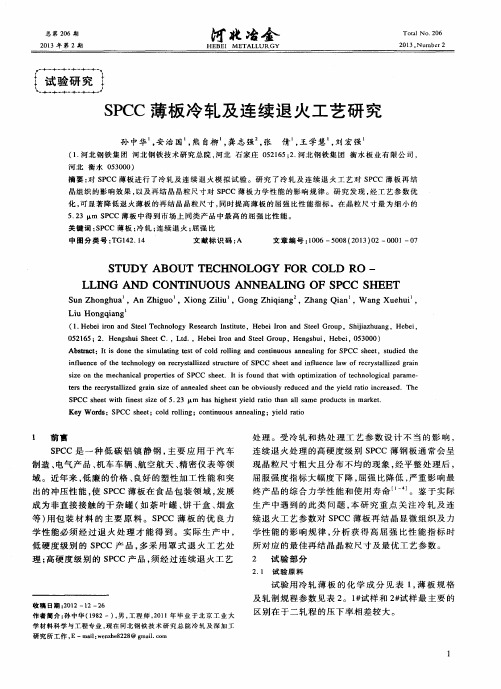
S P CC s h e e t wi t h f i n e s t s i z e o f 5 . 2 3 m h a s h i g h e s t y i e l d r a t i o t h a n a l l s a me p r o d u c t s i n ma r k e t .
总第 2 0 6期
2 0 1 3年 第 2期
河 北 冶金
H EBEI M ETALL U R G Y
To t a l No . 2 0 6 2 0 1 3, Nu mb e r 2
, +
”+
”+
”+
。 +
+
j试验研究 {
+ + .+ 一+ . . + +
Li u Ho n g q i a n g‘
( 1 . He b e i i r o n a n d S t e e l T e c h n o l o g y R e s e a r c h I n s t i t u t e , H e b e i I r o n a n d S t e e l G r o u p ,S h O i a z h u a n g , He b e i ,
S TUDY ABOUT TECHN0LoGY FOR CoLD RO — I . I . G AND CONTⅡ OUS ANNEALⅡ G oF SP CC S HEET
S u n Zh o n g h u a ,An Z h i g u o ,Xi o n g Zi l i u ,Go n g Z h i q i a n g ,Z h a n g Qi a n ,W a n g Xu e h u i ,
试析退火工艺对冷轧低碳钢组织和性能的影响

关键词:退火工艺;冷轧低碳钢;表面活化能;再结晶 中图分类号:TG335.12 文献标识码:B 文章编号:1006-8465(2017)08-0409-01
前言
现代退火工艺一般是将材料在高温之下进行曝露,待一段时间
浅谈冷轧低碳钢DC01工艺优化的生产实践

并为生产 出满足市场需求的冷轧低碳钢 D 0 产 品 C1
奠定 了良好的工艺基础。
1 生产工艺控制情况
11 工艺路 径 .
艺优化前后的化学成分控制情况基本相 当。
表 1 化学成分
—
—
—
—
:
!
竺 型 !望
堕
N O0 4 . 0 0 00 3 . 6 0
名称 牌 号 ( : S i 优化前 DC 1 0C 2 O0 5 0 . .1 4 优化后 DC 1 031 O0 5 O . .1 t 4
本钢二冷轧建成投产初期 ,为降低冶炼工序生 产成本 ,炼钢工序采用不走 R H精炼工艺路径生产
冷轧低碳钢 D 0 , C 1 从冷轧 D 0 最终成品力学性 C1
本钢冷轧低碳钢 D 0 的生产工艺流程为 : C1 铁 水预处理 转炉冶炼_炉外精炼 连铸_ 加热一 + ÷
粗轧- 精轧 控制冷却, 卷取 ( 十 冷轧) 开卷一酸 洗、 冷连轧-连续退火 平整 精整 机能检验 ÷
Mn P S As l 02 00 . 8 00 6 . 0 .1 O0 9 1 0 .3 O2 00 . 8 00 4 . 0 .1 00 9 1 0 .3
1 热轧工艺 . 3
析 出和长大, 降低连续退火再结晶温度 , 提高 r 值。
优化前后冷轧低碳钢 D 0 热轧工艺控制情况见表 C 1
了良好 的工艺基础 。
关键 词 :冷轧 ;低碳 钢 ;工 艺优 化 中圈分类 号 :T 3 G35 文献标识码 :B
P o u t eP a t eo r s tmia i no l l dLo Ca b nS e l 11 r d ci r ci f o e sOp i z to fCo dRol w r o te 0 v c P c e DC
冷轧连续退火炉工艺论文资料
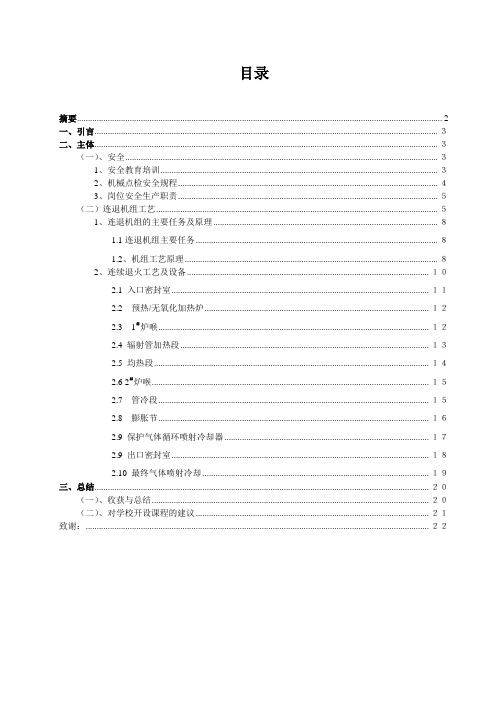
目录摘要 (2)一、引言............................................................................................................................................................ 3二、主体............................................................................................................................................................ 3(一)、安全.............................................................................................................................................. 31、安全教育培训.............................................................................................................................. 32、机械点检安全规程...................................................................................................................... 43、岗位安全生产职责...................................................................................................................... 5(二)连退机组工艺................................................................................................................................ 51、连退机组的主要任务及原理 ...................................................................................................... 81.1连退机组主要任务.............................................................................................................. 81.2、机组工艺原理................................................................................................................... 82、连续退火工艺及设备.............................................................................................................. 102.1 入口密封室..................................................................................................................... 112.2 预热/无氧化加热炉...................................................................................................... 122.3 1#炉喉........................................................................................................................... 122.4 辐射管加热段................................................................................................................. 132.5 均热段............................................................................................................................. 142.6 2#炉喉.............................................................................................................................. 152.7 管冷段........................................................................................................................... 152.8 膨胀节........................................................................................................................... 162.9 保护气体循环喷射冷却器 ............................................................................................. 172.9 出口密封室..................................................................................................................... 182.10 最终气体喷射冷却....................................................................................................... 19三、总结........................................................................................................................................................ 20(一)、收获与总结.............................................................................................................................. 20(二)、对学校开设课程的建议.......................................................................................................... 21致谢:............................................................................................................................................................ 22摘要:硅钢被誉为钢铁行业的“工艺品”,广泛的应用于各种电机和变压器的中心部件,其制造工艺复杂,装备总类多,设备自动化程度较高,生产过程困难,对各项指标的要求较高。
冷轧板的退火工艺:连续退火和罩式退火的比较

冷轧板的退火工艺:连续退火和罩式退火的比较冷轧产品是钢材中的精品,属高端产品,具有加工精细、技术密集、工艺链长、品种繁多、用途广泛等特点。
国际钢铁工业发展实践表明,随着经济社会发展,冷轧产品在钢材消费总量中的比重在不断提高,并发挥着越来越重要的作用。
冷轧后热处理是冷轧生产中的重要工序,冷轧板多为低碳钢,其轧后热处理通常为再结晶退火,冷轧板通过再结晶退火达到降低钢的硬度、消除冷加工硬化、改善钢的性能、恢复钢的塑性变形能力之目的。
冷轧板的再结晶退火在退火炉中进行,冷轧板退火炉分为罩式退火炉和连续退火炉,罩式退火炉又分为全氢罩式退火炉与普通罩式退火炉。
冷轧板退火技术的发展与罩式退火炉和连续退火炉的发展是密不可分的[10]。
退火工艺流程如图2.1所示:图2.1 退火工艺流程示意图表2.4 某钢厂罩式退火炉工艺参数热点/冷点温度CQ:710℃/640℃DQ:710 ℃/660℃DDQ:710 ℃/680℃HSLA:680℃/660℃一般生产中CQ、DQ热点和冷点温度差要大一些。
分别为90 ℃、70 ℃开始喷淋冷却温度内罩表面温度200 ℃,卷心温度:380℃左右生产调试中进行检测试验以确定不同钢卷开始喷淋冷却工艺出炉温度160 ℃出炉吊至终冷台冷却到平整温度约40 ℃图2.3 典型的罩式炉退火工艺温度曲线图罩式退火工艺罩式退火是冷轧钢卷传统的退火工艺。
在长时间退火过程中,钢的组织进行再结晶,消除加工硬化现象,同时生成具有良好成型性能的显微组织,从而获得优良的机械性能。
退火时,每炉一般以4个左右钢卷为一垛,各钢卷之间放置对流板,扣上保护罩(即内罩),保护罩内通保护气体,再扣上加热罩(即外罩),将带钢加热到一定温度保温后再冷却。
罩式退火炉发展十分迅速,2O世纪7O年代的普通罩式退火炉主要采用高氮低氢的氮氢型保护气体(氢气的体积分数2%~4%,氮气的体积分数为96%~98%)和普通炉台循环风机,生产效率低,退火质量差,能耗高;为了弥补普通罩式炉的缺陷,充分发挥罩式炉组织生产灵活,适于小批量多品种生产,建造投资灵活,可分批进行的优点,7O年代末奥地利EBNER公司开发出HICON/H 炉(强对流全氢退火炉),8O年代初德国LOI公司开发出HPH炉(高功率全氢退火炉)。
- 1、下载文档前请自行甄别文档内容的完整性,平台不提供额外的编辑、内容补充、找答案等附加服务。
- 2、"仅部分预览"的文档,不可在线预览部分如存在完整性等问题,可反馈申请退款(可完整预览的文档不适用该条件!)。
- 3、如文档侵犯您的权益,请联系客服反馈,我们会尽快为您处理(人工客服工作时间:9:00-18:30)。
随着温度的增高,原子能力会迅速扩散,导致晶 界迁移过快。故在温度较高时,通过退火工艺使晶粒 粗大,析出渗碳体。另外,在均热段,由于温度直接影
2 低碳铝镇静钢的性能分析
在冷轧低碳钢连续退火工艺优化前,机组的屈
服强度为 265 MPa,将接近上限的 270 MPa,塑性应
变比(r 值)较低,材料塑性较差,这难以满足用户使
用。机组的低碳铝镇静钢力学性能指标见表 1。
表 1 低碳铝镇静钢工艺的力学性能指标
屈服强度/MPa 抗拉强度/MPa 伸长率/% r 值
作者简介:田士张(1984-),男,湖北武汉人,大学本科,助理工程师,主要从事冷轧工作。
86
第1期
和优化后的对比如表 2 所示。
表 2 优化前和优化后的热轧工艺
阶段 优化前 优化后
加热温度/°C 终轧温度/°C 卷取温度/°C
1200
890
680
1200
890
720
3.3 连续退火工艺优化
退火炉作为连续退火机组的关键设备,由多个 环节组成,一般来说,包括预热段、加热段、均热段、 缓冷段、和终冷段等。退火带钢工艺流程如下:首先, 在退火炉前,带钢要进入预热段预热,再经加热段加 热,待加热至退火温度后,再进入均热段保温,使晶 粒长大;然后进入到缓冷段冷却,当达到设定温度 时,再进入过时效段进行处理,最后带钢经终冷段冷 却到 40 °C 左右,进而完成退火处理。
第 39 卷 第 1 期 2019 年 2 月
冶 金冶 金与 与材材料料
Metallurgy and materials
Vol.39 第 3N9o卷. 1 February 2019
冷轧低碳钢连续退火生产工艺优化方案研究
田士张
(佛山市高明基业冷轧钢板有限公司,广东 佛山 528000)
摘 要:在低碳钢使用过程中,经常会出现屈服强度高和开裂问题,研究发现,这是由于低碳钢力学性能受到炼 钢成分、冷轧压下率的影响,因此,需要对冷轧低碳钢连续退火生产工艺进行优化,以满足了用户使用要求。文 章阐述了低碳铝镇静钢的性能,从而进一步就冷轧低碳钢连续退火生产工艺优化措施进行了深入探讨。 关键词:冷轧低碳钢;连续退火;性能分析;生产工艺
过去,在罩式退火炉生产过程中,热轧原料采取 加热温度和开轧温度较高,终轧温度较低的生产方 式。而实践表明,采用连续退火工艺,在热轧时采用 中高温进行轧卷,这样可以使铁素体晶粒变大,进一 步析出氮化铝。通过连退工艺与热轧工艺之间的配 合,可以有效降低晶粒生长的影响度,使晶粒长大, 以提高冲压性能,增大 r 值的目的。热轧工艺优化前
1 概述
某冷轧厂,连续退火生产线采用 2080 mm 冷轧 连续退火机组,集带钢的清洗、退火、平整于一体,冷 轧连续退火机组尺寸为 (0.3~2.5)mm×(900~2080) mm,定位为高端质量的汽车板。近年来,随着冷轧产 品产量的提高,冷轧低碳钢 D 出现了冲压开裂问题。 经分析发现,由于冷轧板屈服强度偏高,在受到冲压 作用下,易于开裂。因此,为了解决这一问题,冷轧厂 对冷轧低碳钢连续退火生产工艺进行优化,以满足 机械性能和使用性能,达到用户需求。
265
345
41
1.0
在工艺优化前,对表 1 中的屈服强度、抗拉强度 和伸长率进行统计分析,发现屈服强度较高,在 220~ 300 MPa 范围内;伸长率波动较小,而抗拉强度分布 较为集中。
3 冷轧低碳钢连续退火生产工艺的优化措施
3.1 化学成分优化 为了确保产品性能的良好性,需要对钢水的化
学成分进行优化。在连续退火工艺生产过程中,由于 高温保温时间较少,在冶炼时要加强化学成分控制。 由于带钢的抗拉性能受到碳、锰含量变化的影响。因 此,为保证钢板的低屈服强度,应将保碳含量控制小 于 0.05%,同时还可以过时效时能够析出碳化物;另 外,应将锰的质量分数控制在 0.15%~0.25%范围内, 以确保锰含量的热脆性。
在钢水中,铝能消除钢的硬化性,提高冲压性 能,降低屈服强度。因此,要钢的加工性能,应提高铝 的含量。由于钢水中的氮含量过高,极于产生气泡, 从而给热轧带钢的加工性能造成影响。同时,如果氮 含量过高,还可以析出铝氮,导致奥氏体晶界面脆化, 使铸坯开裂。在冷轧时,如果氮钉在扎邦时出现位 错,将会降低塑性应变比的数值。而在退火时,通过 铝氮质点的形成及结晶,使晶粒较小的形核受到抑 制,而晶粒在较大驱动力下,能促进织构的形成,提 高冲压成型性能。一般来说,退火后为了获得良好的 冲压性能,需将钢水中铝和氮的比值控制在 8~12。 可见,在 2080 mm 冷轧连续退火工艺的化学成分优 化应用中,大大提高钢水中铝的含量,降低氮的含量。 3.2 热轧工艺优化
冷轧低碳板带作为一种通用钢材,在汽车制造、 家用电器等领域得到了广泛的应用。冷轧生产是指 在结晶温度下进行钢板轧制生产的过程。由于钢板 在轧制过程中出现硬化,从而给冲压加工带来影响。 因此,为了解决以上问题,需进行冷轧板退火处理。 退火是将冷变形后的金属加热到结晶温度,并以适 宜速度进行冷却,消除加工硬化现象的工艺。文章着 重探讨了冷轧低碳钢连续退火生产工艺优化方案。
(1)通过冷轧低碳铝镇静钢的化学成分、热轧工 艺和退火工艺的优化,2080mm 连续退火生产工艺达 到稳定状态,降低了产品的屈服强度,满足了用户使 用要求;(2)通过 2080mm 连续退火生产工艺的成功 优化,为冷轧厂今后在钢开发和汽车冲压用钢生产 提供了便利,提升冷轧厂的生产效率,给冷轧厂带来 良好的经济效益。
响到晶粒的再结晶和长大,故会影响到带钢的屈服强
度,而在过时效段,屈服强度很少受到温度的影响。
连续退火生产工艺优化前和优化后的效果见表 3。
表 3 优化前后的连续退火工艺
阶段 均热 缓冷 时效 1 时效 2 时效 3
优化前 730
670
440
420
400
优化后 800
670
440
420
4结语
综上所述,文章通过对冷轧低碳钢连续退火生 产工艺优化方案进行探讨,得到了以下几点结论: