5)设备利用率分析
设备完好率、设备利用率、设备故障率、设备开动率
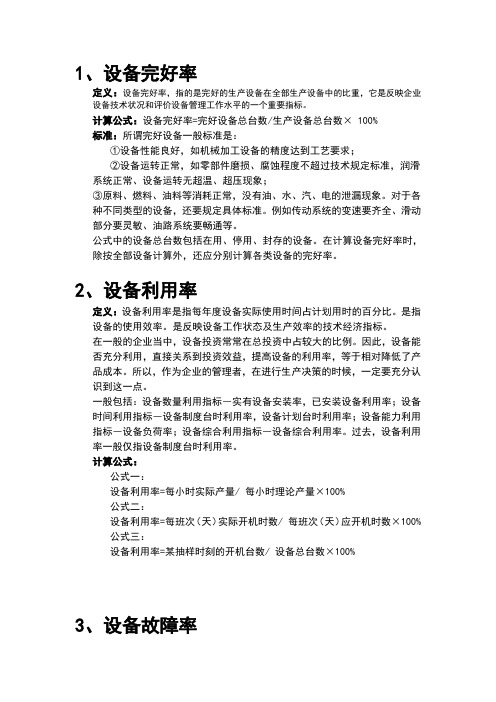
1、设备完好率定义:设备完好率,指的是完好的生产设备在全部生产设备中的比重,它是反映企业设备技术状况和评价设备管理工作水平的一个重要指标。
计算公式:设备完好率=完好设备总台数/生产设备总台数× 100%标准:所谓完好设备一般标准是:①设备性能良好,如机械加工设备的精度达到工艺要求;②设备运转正常,如零部件磨损、腐蚀程度不超过技术规定标准,润滑系统正常、设备运转无超温、超压现象;③原料、燃料、油料等消耗正常,没有油、水、汽、电的泄漏现象。
对于各种不同类型的设备,还要规定具体标准。
例如传动系统的变速要齐全、滑动部分要灵敏、油路系统要畅通等。
公式中的设备总台数包括在用、停用、封存的设备。
在计算设备完好率时,除按全部设备计算外,还应分别计算各类设备的完好率。
2、设备利用率定义:设备利用率是指每年度设备实际使用时间占计划用时的百分比。
是指设备的使用效率。
是反映设备工作状态及生产效率的技术经济指标。
在一般的企业当中,设备投资常常在总投资中占较大的比例。
因此,设备能否充分利用,直接关系到投资效益,提高设备的利用率,等于相对降低了产品成本。
所以,作为企业的管理者,在进行生产决策的时候,一定要充分认识到这一点。
一般包括:设备数量利用指标―实有设备安装率,已安装设备利用率;设备时间利用指标―设备制度台时利用率,设备计划台时利用率;设备能力利用指标―设备负荷率;设备综合利用指标―设备综合利用率。
过去,设备利用率一般仅指设备制度台时利用率。
计算公式:公式一:设备利用率=每小时实际产量/ 每小时理论产量×100%公式二:设备利用率=每班次(天)实际开机时数/ 每班次(天)应开机时数×100%公式三:设备利用率=某抽样时刻的开机台数/ 设备总台数×100%3、设备故障率定义:设备故障率是指事故(故障)停机时间与设备应开动时间的百分比,是考核设备技术状态、故障强度、维修质量和效率一个指标。
设备利用率——精选推荐

设备利用率1设备效率半导体工业极大依赖于半导体制造设备的投资,而且是同步增长的。
随着设备的硅片尺寸大直径化、设备的高精度化、自动化,设备价格日益昂贵化,工艺线的设备总投资更是成倍地增长。
对工艺线来说,在设备投资加大的同时,设备折旧的负担也加大,设备折旧与维修占硅片加工总成本的最大比重[1],设备效率和设备能力能否达到其最大利用率是决定硅片成本的重要因素之一,因此设备效率和设备能力已成为半导体制造者非常关心的问题。
国际半导体设备与材料组织(SEMI)于1999年提出了一种能准确计算设备效率的方法--全面设备效率(OEE)。
1.1OEE简介OEE考虑了设备所有的运行情况,完全依据设备的状态时间计算[2](见图1),计算方便准确,并且更加适合柔性生产设备,弥补了SEMI以往计算效率方法的不足。
SEMI将全面设备效率定义为可用效率(AE或称UpEfficiency)、生产效率(OE)、速率效率(RE)和质量效率(QE)之积,具体OEE模型如下所示[3]OEE=AE×OE×RE×QE其中,A E:%设备完好且能进行工艺的时间占总时间的比例;O E:%设备进行工艺的时间占可用时间的比例;R E:%设备加工的理论生产时间占生产时间的比例;Q E:%有效加工的理论生产时间(无废片、无回流)占总理论生产时间的比例或%工艺完成后的硅片数占总硅片数的比例。
1.2OEE的计算虽然SEMI组织已经给了OEE的计算方法,但是半导体公司根据其自身的特点给出了简单的OEE计算方法,下面将介绍两种常用的计算方法,以单台设备一天为例(1)OEE=理论生产时间÷总时间其中,理论生产时间=(当天工艺i加工的硅片数×工艺i每片理论加工时间,n为当天的工艺总数);总时间=24h。
(2)OEE=实际出产的硅片数÷理论出产的硅片数。
表1是国内某半导体制造有限公司运用第一种方法的OEE实例。
金蝶生产分析系统

金蝶生产分析系统
系统简介
提供组织架构、时刻序列维度的生产方案完成分析、生产定单执行率、产量达成率、设备稼动率、设备利用率、生产合格率、报废率、进库率的比照、同比、环比分析
质量分析包括产品完工质量分析、良品率、产品一次合格率、物料报废率〔数量/本钞票〕
保证相关治理人员把握生产方案执行情况、物料消耗和质量情况,以便采取措施,使生产方案如期执行,落低报废损失,提高产品质量。
要紧功能
1、生产方案完成情况分析
从部门、物料、生产任务单、时刻维度,提供生产方案完成分析、生产定单执行率、产量达成率、设备稼动率、设备利用率、生产合格率、报废率、进库率的比照、同比、环比分析分析及示警。
2、定单执行率分析
提供部门、物料、时刻序列的定单执行率、定单占比、定单明细的图表分析。
3、产量达成分析
提供部门、时刻序列、物料、生产任务单的产量达成率及年累计趋势图表,结构分析。
4、设备稼动率分析
提供部门、时刻序列、设备分类、设备的稼动率分析图表及明细。
5、设备利用率分析
提供部门、时刻序列、设备分类、设备的利用率分析图表及明细。
6、质量分析
质量分析包括产品完工质量分析、良品率、产品一次合格率、物料报废率〔数量/本钞票〕。
设备利用率分析

精益生产
采用精益生产理念,通过减少浪 费、提高生产效率和产品质量来 提升设备利用率。
自动化与智能化
引入自动化、智能化技术,提高 设备的自主运行能力和故障诊断 能力,降低人工干预和故障率。
数据分析与优化
运用数据分析技术,对设备运行 数据进行实时监测和优化,提高 设备运行效率和稳定性。
05 结论
设备利用率提升的成果
企业对市场需求的预测准确度也会影响设备利用率。如果预测需求过高,可能 导致设备过度使用;如果预测需求过低,可能导致设备利用率不足。
生产计划因素
生产计划安排
合理的生产计划可以确保设备在需要时能够及时投入使用, 提高设备利用率。生产计划不合理可能导致设备等待时间过 长或空转,降低设备利用率。
生产调度管理
设备实际产量
统计设备的实际产出量, 了解设备实际生产水平。
设备负荷率
计算设备的负荷率,评 估设备的工作负荷状况。
03 设备利用率影响因素分析
市场需求因素
市场需求波动
市场需求的波动会影响设备的利用率。当市场需求增加时,设备需要高负荷运 转以满足订单需求;当市场需求减少时,设备可能处于闲置状态。
预测准确性
提高了生产效率
通过优化设备配置和调度,设备利用率得到提升,从而提高了整 体生产效率。
降低了运营成本
设备利用率提升有助于减少闲置和浪费,从而降低企业的运营成 本。
增强了市场竞争力
生产效率的提高使得企业能够更好地满足市场需求,增强了企业 的市场竞争力。
对未来设备管理的展望
01
智能化管理
借助物联网和大数据技术,实现 设备的远程监控和智能调度,进 一步提高设备利用率。
生产调度管理的有效性也影响设备利用率。调度不当可能导 致设备在生产过程中的空闲时间过长,从而降低设备利用率 。
车间月度KPI指标分析
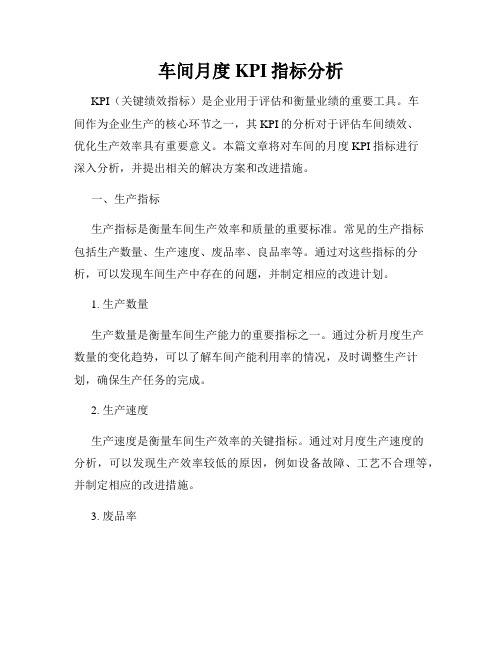
车间月度KPI指标分析KPI(关键绩效指标)是企业用于评估和衡量业绩的重要工具。
车间作为企业生产的核心环节之一,其KPI的分析对于评估车间绩效、优化生产效率具有重要意义。
本篇文章将对车间的月度KPI指标进行深入分析,并提出相关的解决方案和改进措施。
一、生产指标生产指标是衡量车间生产效率和质量的重要标准。
常见的生产指标包括生产数量、生产速度、废品率、良品率等。
通过对这些指标的分析,可以发现车间生产中存在的问题,并制定相应的改进计划。
1. 生产数量生产数量是衡量车间生产能力的重要指标之一。
通过分析月度生产数量的变化趋势,可以了解车间产能利用率的情况,及时调整生产计划,确保生产任务的完成。
2. 生产速度生产速度是衡量车间生产效率的关键指标。
通过对月度生产速度的分析,可以发现生产效率较低的原因,例如设备故障、工艺不合理等,并制定相应的改进措施。
3. 废品率废品率是衡量车间质量水平的指标之一。
通过对月度废品率的分析,可以了解废品产生的原因,例如人为操作失误、工艺不完善等,并采取相应的措施减少废品率,提高产品质量。
4. 良品率良品率是衡量车间产品质量的重要指标之一。
通过对月度良品率的分析,可以评估车间质量管控的有效性,发现质量问题,并制定相应的质量改进计划。
二、人力资源指标人力资源是企业发展的核心资源,也是车间生产运作的关键因素。
通过对车间人力资源指标的分析,可以评估人力资源的配置和使用情况,并采取相应的措施提高人力资源的利用效率。
1. 生产员工数量生产员工数量是衡量车间人力资源配置情况的重要指标。
通过对月度生产员工数量的分析,可以了解是否存在人力不足或者过剩的情况,并采取相应的措施进行调整。
2. 员工绩效员工绩效是评估员工工作表现的重要指标。
通过对月度员工绩效的分析,可以了解员工的工作状况,发现绩效较低的原因,并提出相应的培训和激励计划,提高员工绩效。
三、设备效率指标设备效率对于车间的生产效率和运营成本具有重要影响。
设备利用率统计分析图表(年度)
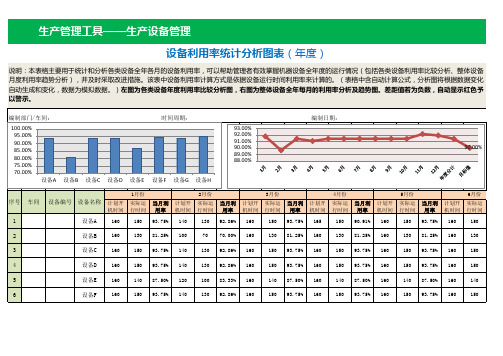
130 81.25% 160
130 81.25% 160
130 81.25% 1860
1500
93.75% 160
150 93.75% 160
150 93.75% 160
150 93.75% 160
150 93.75% 160
150 93.75% 160
150 93.75% 1900
1780
93.75% 160
设备名称
计划开 机时间
1月份
实际运 行时间
当月利 用率
计划开 机时间
2月份
实际运 行时间
当月利 用率
计划开 机时间
3月份
实际运 行时间
当月利 用率
计划开 机时间
4月份
实际运 行时间
当月利 用率
计划开 机时间
5月份
实际运 行时间
当月利 用率
计划开 机时间
6月份
实际运 行时间
设备A
160
150 93.75% 140
100 83.33% 160
140 87.50% 160
140 87.50% 160
140 87.50% 10 93.75% 140
130 92.86% 160
150 93.75% 160
150 93.75% 160
150 93.75% 160
150
7
设备G
8
设备H
设备总体利用率合计
生产管理工具——生产设备管理
设备利用率统计分析图表(年度)
说明:本表格主要用于统计和分析各类设备全年各月的设备利用率,可以帮助管理者有效掌握机器设备全年度的运行情况(包括各类设备利用率比较分析、整体设备 月度利用率趋势分析),并及时采取改进措施。该表中设备利用率计算方式是依据设备运行时间利用率来计算的。(表格中含自动计算公式,分析图将根据数据变化 自动生成和变化,数据为模拟数据。)左图为各类设备年度利用率比较分析图,右图为整体设备全年每月的利用率分析及趋势图。差距值若为负数,自动显示红色予 以警示。
设备管理指标有哪些怎么评价设备管理水平
设备管理指标有哪些怎么评价设备管理水平设备管理是指对企业或组织的设备进行全面的管理和维护,以确保设备的正常运行和高效利用。
设备管理指标是对设备管理工作所设立的各项指标要求,用于衡量设备管理的水平和效果。
下面是几个常见的设备管理指标及其评价方法。
1.设备利用率:设备利用率是指设备在一定时间内的工作时间占总时间的比例。
评价设备管理水平可以通过设备的工作时间、停机时间和闲置时间等进行统计和分析,并计算设备的日均利用率和月平均利用率。
高设备利用率代表设备管理良好,低设备利用率可能意味着设备存在故障、维护不当或生产计划不合理等问题。
2.故障率和维修时间:故障率是指设备在一定时间内出现故障的频率,维修时间是指设备由于故障而停机修复的时间。
评价设备管理水平可以通过统计和分析设备的故障率和平均维修时间,并与预期水平进行比较。
低故障率和短维修时间表明设备管理得当,而高故障率和长维修时间可能意味着设备维护不及时或维修能力不足等问题。
3.技术状态:技术状态是指评估设备技术状况及更新换代的能力。
评价设备管理水平可以通过设备的技术更新率、技术陈旧度和设备的技术改造投入等指标进行评估。
较高的技术状态代表设备管理具备更新换代的能力,而较低的技术状态可能意味着设备滞后或老化,影响到生产效率和质量。
4.成本控制:成本控制是指降低设备管理的成本,同时提高设备利用效率。
评价设备管理水平可以通过设备的维护成本、能源消耗、备件消耗等进行评估。
较低的成本和有效控制的成本表明设备管理工作得当,而高成本可能意味着设备维护效果不佳或存在浪费。
5.安全生产:安全生产是指设备运行过程中保障员工的安全和设备的安全性。
评价设备管理水平可以通过事故发生率、事故处理时间、安全记录和设备的安全修复情况等进行评估。
较低的事故发生率和短的事故处理时间代表设备管理安全可靠,而高事故发生率和长的事故处理时间可能意味着设备管理存在安全隐患。
综上所述,评价设备管理水平需要考虑设备利用率、故障率和维修时间、技术状态、成本控制和安全生产等多个方面的指标。
设备利用率分析范文
设备利用率分析范文设备利用率是指在一定时间内,设备实际工作时间占设备使用总时间的比例。
设备利用率是衡量设备使用效率的重要指标,可以评估设备的正常运行情况,提高生产效率和降低成本。
本文将从设备利用率的定义、影响因素以及提高设备利用率等方面进行分析。
一、设备利用率的定义二、影响设备利用率的因素1.设备维护保养:设备在正常运行期间需要进行维护保养,包括定期检查、清洁、润滑、更换磨损部件等。
设备维护保养不当或者不及时,会导致设备出现故障或停机,进而影响设备利用率。
2.设备故障:设备在运行过程中可能会发生故障,导致设备停机。
设备故障包括设备自身质量问题、设计不合理、零部件老化、电气设备故障等。
设备故障频繁发生,会降低设备利用率。
3.设备调试和改型:一些生产线在生产过程中需要频繁调试和改型,以满足不同产品的生产需求。
设备调试和改型时间过长,会导致设备利用率降低。
4.工艺调整和更换:随着市场需求的变化,一些企业可能需要调整生产工艺或更换设备。
工艺调整和更换设备的过程中,设备无法正常运行,会导致设备利用率降低。
5.人为因素:操作人员的技术水平、工作积极性、协同配合等因素也会对设备利用率产生影响。
操作人员无法正确操作设备、存在违规操作行为、工艺技能不纯熟等,都会导致设备利用率下降。
三、提高设备利用率的措施1.设备维护保养:定期进行设备维护保养,包括检查设备磨损、润滑部件、更换零部件等,确保设备处于良好的工作状态,减少设备故障和停机时间。
2.故障预防和提前维修:通过定期检查设备,及时发现潜在故障隐患,采取预防措施,避免设备故障对设备利用率的影响。
同时,对已经发生故障的设备,进行及时维修,减少停机时间。
3.优化设备调试和改型流程:减少设备调试和改型的时间,提高设备的使用效率。
可以通过标准化工艺和设备模块化设计,减少改型所需时间,提高设备的适应性和灵活性。
4.优化工作流程和人员培训:通过优化工艺流程,减少工艺调整和更换设备的频率,提高设备利用率。
5_设备利用率分析
5_设备利用率分析设备利用率是指对设备的利用程度,是衡量生产能力利用效果的重要指标之一、通过对设备利用率的分析,可以帮助企业评估设备的生产效率和资源利用效率,找出设备利用率低下的原因,并采取相应的措施提高设备利用率。
设备利用率的计算通常采用以下公式:设备利用率=实际生产时间/(实际生产时间+设备故障时间+设备维修时间)×100%设备利用率分析通常包括以下几个方面:1.设备利用率的结构分析设备利用率的结构分析是指将设备利用率按照不同的维度进行分析,查看不同因素对设备利用率的影响。
例如,可以将设备利用率按照班次、工序、产品等进行划分,找出每个维度下设备利用率的差异,并进行比较分析。
通过对不同结构下设备利用率的分析,可以帮助企业找出设备利用率低下的原因,从而采取针对性的措施提高设备利用率。
2.设备利用率的时间分析设备利用率的时间分析是指对设备利用率在不同时间维度下的变化进行分析。
例如,可以将设备利用率按照季度、月份、周次等进行划分,分析不同时间段设备利用率的变化趋势。
通过对设备利用率时间分析,可以帮助企业找出设备利用率的周期性变化规律,并采取相应的措施进行调整。
3.设备利用率的原因分析设备利用率的原因分析是指对设备利用率低下的原因进行深入剖析。
低设备利用率可能是由于设备故障率高、设备维修时间长、操作不当等原因造成的。
通过对设备利用率的原因分析,可以帮助企业找出设备利用率低下的症结所在,并采取具体的措施进行改进。
4.提高设备利用率的措施在分析完设备利用率后,需要制定具体的措施来提高设备利用率。
例如,可以采取预防性维修措施,定期检查设备运行情况,及时处理设备故障问题,减少设备维修时间;优化生产计划,合理安排生产任务,避免设备空闲时间;加强员工培训,提高操作技能,减少操作失误等。
这些措施可以帮助企业提高设备利用率,提升生产效率。
总之,设备利用率分析对于企业来说是一项非常重要的工作。
通过对设备利用率的结构分析、时间分析、原因分析以及采取相应的措施,可以帮助企业提高设备利用率,提升生产效率,实现资源的最大化利用。
设备利用率分析
设备利用率分析首先,设备利用率分析可以帮助企业了解设备的运行状态和时间分配情况。
通过对设备利用率的分析,企业可以了解到设备的运行时间、停机时间、故障时间等信息,从而发现设备的使用情况和存在的问题。
例如,如果某台设备经常出现故障或停机现象,就会影响整个生产过程的效率,导致生产计划不能按时完成。
通过设备利用率分析,企业可以及时发现这些问题,并采取相应的措施,提高设备的利用率和稳定性。
其次,设备利用率分析可以帮助企业提高生产效率。
通过对设备利用率的分析,企业可以找出生产中存在的低效环节和不合理的时间分配,从而采取措施进行优化。
例如,可以通过调整生产计划、提高设备运行效率、优化生产流程等方式,提高设备的利用率和生产效率,降低生产成本、提高产能。
另外,设备利用率分析也可以帮助企业合理规划设备更新和维护计划。
通过对设备利用率的分析,企业可以了解到设备的运行状态和寿命情况,根据实际情况制定设备的更新和维护计划,合理安排设备的维护时间,延长设备的使用寿命,减少设备的故障和停机时间,提高设备的利用率和稳定性。
综上所述,设备利用率分析对于企业提高生产效率、降低成本、提高产能具有重要意义。
通过分析设备利用率,企业可以发现生产中存在的问题和不足,提高设备的利用率和生产效率,从而实现经济效益和社会效益的双赢。
很多企业在制造和生产领域都一直在关注和努力提高设备的利用率。
随着市场的变化和竞争的加剧,企业不断寻求提高生产效率和降低成本的方法。
而设备的利用率分析就成为了其中非常重要的一部分。
下面我们将继续讨论设备利用率分析的相关内容,深入分析其重要性和影响。
设备利用率分析是企业生产管理中非常重要的一部分。
通过对设备利用率的分析,企业可以掌握设备的使用情况和时间分配,发现设备利用率存在的问题,并提出改进措施。
通过设备利用率分析,企业可以找出设备的使用效率低下的原因,采取相应的措施解决问题,提高设备的利用率和生产效率。
在设备利用率分析中,企业需要充分了解每一台设备的生产能力、运行效率和停机时间等情况。
- 1、下载文档前请自行甄别文档内容的完整性,平台不提供额外的编辑、内容补充、找答案等附加服务。
- 2、"仅部分预览"的文档,不可在线预览部分如存在完整性等问题,可反馈申请退款(可完整预览的文档不适用该条件!)。
- 3、如文档侵犯您的权益,请联系客服反馈,我们会尽快为您处理(人工客服工作时间:9:00-18:30)。
快速换型
好处:
➢ 减少停机时间; ➢ 增加生产计划的灵活性; ➢ 减少浪费; ➢ 减少库存成本; ➢ 提高运行能力。
换型时间定义
从完成上一个型号最后一件合格产品到生 产出下一个型号第一件合格产品所花的时间。
快速换型八步法
STEP 1 STEP 2 STEP 3 STEP 4 STEP 5 STEP 6 STEP 7 STEP 8
实例
想测出一台机器的利用率状况?用什么方法呢?
大家首先想到是连续观测法 :
观测结果如下:
40 105 分分
140 25 25 25 120
分
分分分 分
利用率
非利用率
总时间=480分
利用率=
40+140+25+120 480
= 67%
工作抽样---WS法
2.1 工作抽样
工作抽样也叫WS法,是对作业者、机器的工作状态 以任意时间间隔,瞬间地观测,以时间的构成比率统计 地把握工作内容的方法。
追加次数=t2(1-P)/(S2P)-N
工作抽样实施程序
2)作成“WS观测结果集计表”
①尽量将结果用帕累托图、柱状图、圆状图表示 ②别忘了记入观测时的生产状况、作业概要
3)研讨能使用的改善案。
整理集计表、作业单元、巡回路线图、生产条件。
4)求出所需数据
运行效率
总的设备有效性 OEE 全员设备维护 TPM 快速换型 QCO
5)设备利用率分析
前言
• “工欲善其事,必先利其器”。 • 设备是投资老板的印钞机,利用率的高低影响了投资
的回报率。
• 我们要使机器设备发挥出更大的效率,除避免故障的 发生率外,还要研究如何通过计划安排和管理来有效 提高设备的使用。
• 全员生产维护(TPM)倡导一种持续改进的企业文化, 通过100%的员工100%地参与,人人主动地发现和解 决问题,有效进行预见性的维护保养,以追求最高的 设备综合效率(OEE)为目标,实现最小化与最大化。
工作中常遇到的问题
1、车间里机器的利用率实际到底是多少? 2、利用率不能再提高了吗? 3、现场的宽余率给多少最恰当? 4、如何把握每项作业的时间比率? 5、目前作业员、管理者的工作负荷如何?
解决以上问题,我们可 以采用利用率分析法
利用率分析的用途
一 用途
1、了解人、设备的利用率状况
1)了解有多少宽余 2)改善作业分工,提高运转率 3)研究是否需要增加设备或人员 4)了解生产线作业的平衡状况
工作抽样的用语
相对精度S的参考值
工作抽样实施程序
1、明确工作抽样的目的
1) 明确为什么要进行工作抽样 2) 明确期待的精度
① 信赖度:取95%时,那么信赖度系数t=2 ② 精度:相对精度S (参考相对精度S的参考值)
工作抽样实施程序
2、明确观测对象
1) 观测对象 ◆人 ◆设备 ◆材料或产品
每个观测者最多不要超过20 个被观测对象
一天巡回次数= 被观测者数*观测者数*观测天数
工作抽样实施程序
6) 实施正式观测
A、根据观测时刻、巡回路径图进行分析(注意事项与预备观测相同) B、对各观测时刻及顺序,依次进行观测
7) 观测数据整理
1)确认观测要求的相对精度(S)
①剔除异常值 利用P’±3 √P’(1-P’)/N 剔除异常值 ②计算发生率P=X/N ③±S=2 √ (1-P)/NP是否在要求范围之内。 ④如不在,需要追加观测次数
即工作抽样是根据观测时的抽样次数来推断发生 时间长短的一种方法。
2.2 计算公式
利用率=发生率(P)=
活动项目观被测观总测次到(的N次数(X) )
工作抽样的优缺点
2.3 优点 1)不需要计时装置 2)测量效率高,而经济(成本低) 3)应用范围广 4)应用灵活、方便 5)能确保观测结果的精度
2.4 缺点 1、不能全面分解动作单元 2、观测时间和路线可能会被估算出,造成数据失真 3、作业节奏不易考评
好处:
提供下列视觉和听觉帮助:
- 目前生产状态 - 库存情况 - 设备状态 - 质量状态 - 需求援助状态 - 按节拍生产状态
Andon 板
支持小组的 快速反应
提高运行能力
工位准备状态
直观显示以工位为中心的操作。它是一种评 估系统设计、人机工程、差错预防、方法分析、 容器、工具、机器、设备和布局的过程。
TPM 是一种模式转变
“我操作,你维修” “我维修,你设计” “我设计,你操作”
“我们对我们的设备,我们 的工厂,和我们的未来都 负有责任”
TPM 目标
➢零事故 ➢零非计划停机时间 ➢零速度损失 ➢零废品 产品生命周期成本最小化
我们为什么达不 到???
持续改进 5 Why?
例子:设备停机
• 第一个为什么:为什么停机了? ( 机器过载,保险烧了) • 第二个为什么:为什么会过载?(轴承润滑不够) • 第三个为什么:为什么润滑不够?(机油泵没抽上足够的油) • 第四个为什么:为什么油泵抽油不够?(泵体轴磨损) • 第五个为什么:为什么泵体轴磨损?(金属屑被吸入泵中) • 第六个为什么:为什么金属屑被吸入泵中?(吸油泵没有过滤器
生产报告及图示
➢ 监控生产在任何时间的状态; ➢ 记录历史数据以不断改善运行能力:
每小时生产状态如型号、产量等; 故障维修时间; 换型次数和时间; 计划停机时间:
质量损失; 速度损失; 其他损失时间。
生产中的能力损失
设备计划运行吗? YES
设备设置好了吗? YES
设备有能力运转吗? YES
NO 计划停机时间
NO 换型时间
NO 故障维修时间
设备在运行吗? YES
NO 其他损失(待料,早退)
设备在生产合格产品吗? YES
NO 质量损失
设备在全速运行吗? YES
NO 速度损失
生产良好
通过提高OEE改善生产率
总的可用时间 操作时间
纯操作时间
增值的 操作时间
废品损失
速度损失
停工损失
设备故障 - 2 @ 25 min 作业换型 - 2 @ 30 min
设备预防维修计划
12345678
更换空气过滤器 更换灯泡 更换皮带 更换制冷元件 更换油路过滤器 清洁油路 调节弹簧张力 调紧螺钉 检查线路 检查马达
运行有效性的目标
➢ 准确的数据收集和分析是持续改进的基础; ➢ 快速换型加强了生产的灵活性,减少了库存和生产 准备时间; ➢ 70%的维护工作都是先期进行的; ➢ 紧急故障得到快速而有效的检修,预测性/预防性 程序防止故障发生,非紧急工作排进了计划。
工作抽样实施程序
5) 设定观测时间及一日巡回次数
(1)若以把握问题点推算利用率进行工厂改善为目的,那么每周 进行一日10~20次即可。
(2)若作业是周期性的话,应是周期的整数倍或与周期相同 (3)设定宽裕率时,若作业内容不稳定,最好预算出2~4周时间 (4)避免在异常情况时观测
一日巡回次数: 总观测次数N
2) 决定观测作业单元(调查项目分类):
对作业单元要附上定义,记入作业单元构成用纸; 作业单元可以以单位作业或要素作业为分析单位。
工作抽样实施程序
3、决定观测日期
1) 确定对象车间(被观测者)有无缺勤现象 2) 确认对象车间相互协助状况 3) 掌握对象车间作业员或设备的生产量 4) 掌握对象车间作业员的协助(支援或接受他人)的工数 5) 如果确认在观测日有异常情况时,应及时调整观测日
较小的停工 – 30 min 减速 – 满负荷的80% 废品 – 2% 作业起动损失-15 min
450 400 340
310 248 243 228
51%
改进总的设备有效性
主次分析
根源分析
全员设备(预防)维护
全员设备维护是所有的员工努力通过 持续改善设备的运行来增加有效时间、提 高产品质量、加强安全性及减少设备成本 的全系统的活动。
2、标准时间的制定
二 方法
1、连续观测法 2、工作抽样法---WS法
连续观测法
1.1 定义
观测一个事件(人、设备等),用自始至终 连续不断的进行观测,然后求出其利用率状况的方法。
1.2 优点
可一目了然了解事物(人、设备等)每天 的实际状况,有益于发现和研究其问题点。
1.3 缺点 1、取样的速度慢。 2、成本高
工作抽样实施程序
4、制定观测计划
1) 理解作业内容 在进行工作抽样之前,必须先了解车间现状及相关的作业内容
2) 划分作业内容
例
若分析设备是处于运转还是停机状况时,分析单位应设定为
运转中和停机中两种。但想要了解停机理同时,就必须划分成:
@为换型号而作准备 @设备故障 @材料不足 @工的维修数据
---平均故障间隔时间 (MTBF) ---平均修复时间 (MTTR) ----预防维护时间占总维护及维修时间的百分比,
目标≥70% (PM%)
责任人 / 操作员观念
操作员有责任:监测设备,在机器 出现故障前通知维修人员进行维护,进 行日常的清洁整理及小的维护调整工作 ,并把平常观察情况反映给维修人员。
READY
对工位定期评审
• 组织3-6人的多功能团队 • 每周定期轮查工位 • 确定改善措施并进行跟踪
工位评审卡
工位
日期
人员
内容
采光照明 转身动作
评分
3 2
责任人
弯腰动作
1
料架摆放
工作空间 紧张程度 走动距离
…… 如果你是工 人的话
3 5 4 3
不舒服
------钱满仓
动手做
计划日期 实际日期
现场观察并写下换型步骤 记录时间和各种浪费 区分内部及外部活动 分析所有换型动作