球铁壳体件缺陷的成因分析与预防措施
球墨铸铁件产生缺陷的原因有哪些?

球墨铸铁件产生缺陷的原因有哪些?球墨铸铁件产生缺陷的原因不单是球化处理问题,那么还有什么问题?在球墨铸铁件生产中,常见的铸件缺陷除有灰铸铁件的一般缺陷外,还有球化不良、球化衰退、夹渣、缩松、石墨漂浮、皮下气孔等。
通常,产生这些缺陷的原因不单是球化处理问题,有时还有造型制芯、熔炼浇注、配砂质量、落砂清理等许多生产工序的问题,因此必须具体分析。
以便采取相应的合理措施加以解决。
(1)球化不良特征:在铸件或试棒断面上分布有明显可见的小黑点,愈往中心愈密。
金相组织中.有聚集分布的厚片状石墨原因分析:1.原铁液硫含量过高2.铁液氧化3.残余球化剂量不足4反球化元素的干扰防止方法:1.尽量选用低硫的焦炭和新生铁。
若原铁液含硫量过高,应采用炉内、炉外脱硫或相应提高球化剂的加入量。
交界铁液一定要分离干净,灰铸铁的铁掖不应混入球墨铸铁中。
球化处理时,防止炉渣出到浇包中2.操作中严防铁液氧化3.熔制配比适当、成分稳定的中间合金,并采用合适的处理温度,注意球化处理操作。
防止铁液与合金作用过分激烈或“结死”在包底4镁球墨铸铁中。
加人少量的稀土,可中和反球化元素的干扰(2)球化衰退特征:球墨铸铁铁液,停留一定时间后,球化效果会消失原因分析: 铁液的残余镁量和残余稀土量随着时间的延长会逐渐减少,过了一定时间后。
球化剂残余量已减少到不足以保证铸件球化时,就造成球化衰退镁量和稀土量逐渐减少的原因是:1. 在铁液表面的MgS、CeS与空气中氧作用,发生下列反应:2MgS+O2=2MgO气↑+2S2CeS+ O2=2CeO气+2S烟状的MgO和CeO在空气中逸损,S返回铁液与Mg、Ce作用又生成MgS、CeS,这样循环,Mg、Ce不断损失2.镁在铁液中溶解度极小,大部分镁以微小的气泡悬浮在铁液中。
当有搅拌、回包、浇注、机械振动等情况时,镁气泡会集聚上浮,并穿出铁液表面。
遇空气燃浇而损失3.镁、稀土与氧有极大的亲和力。
铁液表面的镁和稀土要逐渐氧化、镁还有蒸发损失等防止方法:1.经球化处理的铁液应有足够的球化剂残余量2.降低原铁液硫含量,并防止铁液氧化3.球化处理后应扒净渣子4.缩短铁液经球化处理后的停留时间5.在铁液表面加覆盖熔剂,如石墨粉、木炭粉、冰晶石粉等(3)夹渣(黑渣)特征: 在铸件断面上呈现暗黑色,没有光泽,主要由琉化镁、硫化锰、氧化镁、二氧化硅、氧化铁、氢化镁等所组成,是一种非金属夹杂物,可用硫印、氧印等方法显示出来。
实战专家总结球化不良缺陷的13条原因,预防措施该如何做?
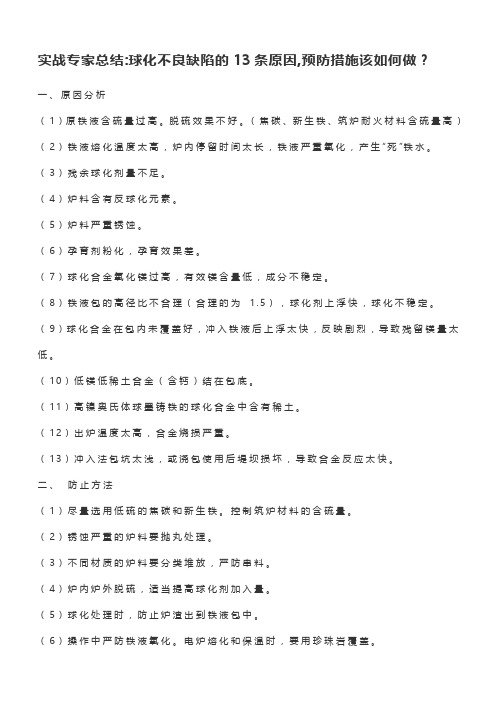
实战专家总结:球化不良缺陷的13条原因,预防措施该如何做?一、原因分析(1)原铁液含硫量过高。
脱硫效果不好。
(焦碳、新生铁、筑炉耐火材料含硫量高)(2)铁液熔化温度太高,炉内停留时间太长,铁液严重氧化,产生“死”铁水。
(3)残余球化剂量不足。
(4)炉料含有反球化元素。
(5)炉料严重锈蚀。
(6)孕育剂粉化,孕育效果差。
(7)球化合金氧化镁过高,有效镁含量低,成分不稳定。
(8)铁液包的高径比不合理(合理的为 1.5),球化剂上浮快,球化不稳定。
(9)球化合金在包内未覆盖好,冲入铁液后上浮太快,反映剧烈,导致残留镁量太低。
(10)低镁低稀土合金(含钙)结在包底。
(11)高镍奥氏体球墨铸铁的球化合金中含有稀土。
(12)出炉温度太高,合金烧损严重。
(13)冲入法包坑太浅,或浇包使用后堤坝损坏,导致合金反应太快。
二、防止方法(1)尽量选用低硫的焦碳和新生铁。
控制筑炉材料的含硫量。
(2)锈蚀严重的炉料要抛丸处理。
(3)不同材质的炉料要分类堆放,严防串料。
(4)炉内炉外脱硫,适当提高球化剂加入量。
(5)球化处理时,防止炉渣出到铁液包中。
(6)操作中严防铁液氧化。
电炉熔化和保温时,要用珍珠岩覆盖。
(7)在保证球化的前提下,尽量降低出炉温度。
(8)注意球化处理操作,调整铁液包的高径比,球化剂和硅铁上面要覆盖铁销或珍珠岩,防止铁液与球化剂作用过分激烈或“结死”包底。
(9)镁球化处理中,加入少量稀土,可中和反球化元素的干扰。
(10)包坑与堤坝按要求,损坏后要及时修复。
(11)使用配比合适、成分稳定的中间合金采用随流孕育和二次孕育。
(12)交界铁液要分离干净。
(13)厚大件球化处理时可冲入一些钼、铜、锑、铋等合金元素。
也可采用重稀土合金球化剂。
(14)使用低镁、低稀土合金,使球化处理反应平缓;减少镁的烧损。
(15)高镍奥氏体球墨铸铁处理用不含稀土的镍镁或硅镁合金。
(16)采用喂丝处理铁水包的出铁量要适当,或适当加高铁水包,留下喂丝时铁液反应空间。
球墨铸铁常见缺陷的分析与对策
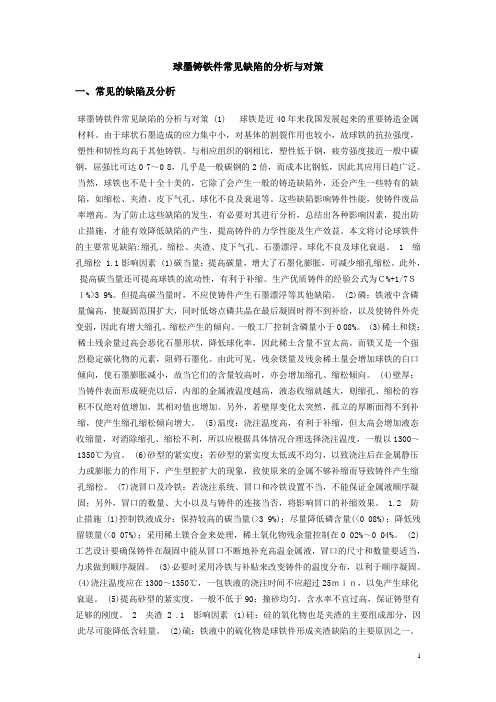
球墨铸铁件常见缺陷的分析与对策一、常见的缺陷及分析球墨铸铁件常见缺陷的分析与对策 (1) 球铁是近40年来我国发展起来的重要铸造金属材料。
由于球状石墨造成的应力集中小,对基体的割裂作用也较小,故球铁的抗拉强度,塑性和韧性均高于其他铸铁。
与相应组织的钢相比,塑性低于钢,疲劳强度接近一般中碳钢,屈强比可达0 7~0 8,几乎是一般碳钢的2倍,而成本比钢低,因此其应用日趋广泛。
当然,球铁也不是十全十美的,它除了会产生一般的铸造缺陷外,还会产生一些特有的缺陷,如缩松、夹渣、皮下气孔、球化不良及衰退等。
这些缺陷影响铸件性能,使铸件废品率增高。
为了防止这些缺陷的发生,有必要对其进行分析,总结出各种影响因素,提出防止措施,才能有效降低缺陷的产生,提高铸件的力学性能及生产效益。
本文将讨论球铁件的主要常见缺陷:缩孔、缩松、夹渣、皮下气孔、石墨漂浮、球化不良及球化衰退。
1 缩孔缩松 1.1影响因素 (1)碳当量:提高碳量,增大了石墨化膨胀,可减少缩孔缩松。
此外,提高碳当量还可提高球铁的流动性,有利于补缩。
生产优质铸件的经验公式为C%+1/7Si%>3 9%。
但提高碳当量时,不应使铸件产生石墨漂浮等其他缺陷。
(2)磷:铁液中含磷量偏高,使凝固范围扩大,同时低熔点磷共晶在最后凝固时得不到补给,以及使铸件外壳变弱,因此有增大缩孔、缩松产生的倾向。
一般工厂控制含磷量小于0 08%。
(3)稀土和镁:稀土残余量过高会恶化石墨形状,降低球化率,因此稀土含量不宜太高。
而镁又是一个强烈稳定碳化物的元素,阻碍石墨化。
由此可见,残余镁量及残余稀土量会增加球铁的白口倾向,使石墨膨胀减小,故当它们的含量较高时,亦会增加缩孔、缩松倾向。
(4)壁厚:当铸件表面形成硬壳以后,内部的金属液温度越高,液态收缩就越大,则缩孔、缩松的容积不仅绝对值增加,其相对值也增加。
另外,若壁厚变化太突然,孤立的厚断面得不到补缩,使产生缩孔缩松倾向增大。
浅析球墨铸铁件缺陷产生原因及防止措施

浅析球墨铸铁件缺陷产生原因及防止措施
1、坯料的缺陷:由于坯料的杂质含量过高,砂砾过大,沿铸缸边缘空隙较大等,都有可能导致炉内坯料缺陷大,从而产生球墨铸铁件缺陷。
2、成型工艺有问题:如砂芯型腔孔形不规则,型腔深度低,入型质量差,表面光洁度及粘结质量差等,都有可能产生球墨铸铁件缺陷。
3、浇注不合理:球墨铸铁件的浇注工艺过程中需要满足一定的条件,当不合理时,会导致溶质的不均匀分布,产生球墨铸铁件缺陷。
4、冷却不合理:冷却工艺是球墨铸铁件质量重要影响因素,冷却不合理,有可能使坯体结晶不良,从而产生球墨铸铁件缺陷。
二、防止球墨铸铁件缺陷的措施
1、提高坯料质量:在生产过程中,应加强原料检查,确保原料质量良好,并严格控制杂质含量,以减少成型过程中缺陷的发生。
2、改进成型工艺:应采用有利于消除和避免缺陷的成型工艺,如采用自动模具成型等技术,减少缺陷产生的可能性。
3、改善浇注工艺:采用有利于消除缺陷的浇注工艺,如采用连续浇铸或提高浇注压力,改善浇注品质,以减少球墨铸铁件缺陷。
4、优化冷却工艺:采用合理的冷却系统可以有效地控制坯体扩大速度,减少坯体内部残余应力,提高结晶度,以减少球墨铸铁件缺陷的产生。
三、结论
球墨铸铁件的缺陷的产生主要由坯料质量、成型工艺、浇注工艺以及冷却工艺不合理等原因引起。
因此,为防止球墨铸铁件缺陷的产生,应采取提高坯料质量、改进成型工艺、改善浇注工艺以及优化冷却工艺等措施。
只有这样,才能在生产过程中控制住缺陷,获得优良质量的球墨铸铁件。
浅析球墨铸铁件缺陷产生原因及防止措施
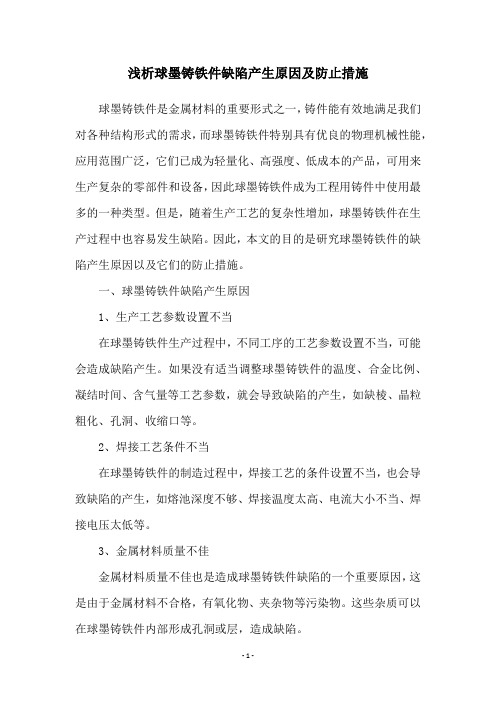
浅析球墨铸铁件缺陷产生原因及防止措施球墨铸铁件是金属材料的重要形式之一,铸件能有效地满足我们对各种结构形式的需求,而球墨铸铁件特别具有优良的物理机械性能,应用范围广泛,它们已成为轻量化、高强度、低成本的产品,可用来生产复杂的零部件和设备,因此球墨铸铁件成为工程用铸件中使用最多的一种类型。
但是,随着生产工艺的复杂性增加,球墨铸铁件在生产过程中也容易发生缺陷。
因此,本文的目的是研究球墨铸铁件的缺陷产生原因以及它们的防止措施。
一、球墨铸铁件缺陷产生原因1、生产工艺参数设置不当在球墨铸铁件生产过程中,不同工序的工艺参数设置不当,可能会造成缺陷产生。
如果没有适当调整球墨铸铁件的温度、合金比例、凝结时间、含气量等工艺参数,就会导致缺陷的产生,如缺棱、晶粒粗化、孔洞、收缩口等。
2、焊接工艺条件不当在球墨铸铁件的制造过程中,焊接工艺的条件设置不当,也会导致缺陷的产生,如熔池深度不够、焊接温度太高、电流大小不当、焊接电压太低等。
3、金属材料质量不佳金属材料质量不佳也是造成球墨铸铁件缺陷的一个重要原因,这是由于金属材料不合格,有氧化物、夹杂物等污染物。
这些杂质可以在球墨铸铁件内部形成孔洞或层,造成缺陷。
4、操作人员技术素养不足操作人员的技术素养也是产生缺陷的一个重要原因,如果操作人员缺乏技术素养,他们就不能熟练掌握工艺流程,也会导致生产过程中的缺陷。
二、防止球墨铸铁件缺陷的措施以上是球墨铸铁件缺陷的原因,那么如何防止缺陷产生呢?1、优化工艺参数设置在球墨铸铁件生产过程中,加强对工艺参数的监控,优化工艺参数设置,确保金属材料在加工上能满足一定的质量要求。
2、严格控制焊接工艺条件焊接是一项技术复杂的任务,因此我们应该在焊接工艺中严格控制各项工艺参数,确保球墨铸铁件能获得良好的焊接性能,从而防止缺陷的产生。
3、挑选优质金属材料在球墨铸铁件生产中,应该重视金属材料的质量,仅选用合格的金属材料,这样可以减少出现缺陷的概率。
4、提升操作人员技术素养提升操作人员的技术素养是防止球墨铸铁件缺陷的重要措施之一,建立科学的操作流程,以此来提高操作人员的技术水平,减少因技术不足而导致的缺陷。
球墨铸铁缺陷产生原因及应对措施
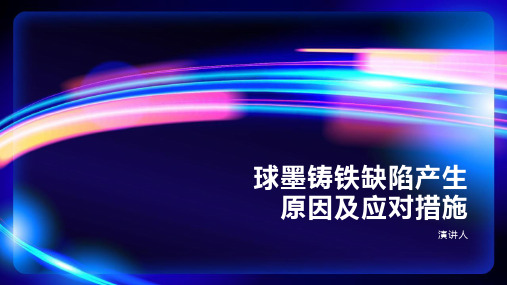
改进生产工艺
优化浇铸工艺:控 制浇铸温度、速度、
压力等参数,提高 1
铸件质量
加强质量控制:建 4
立完善的质量管理 体系,确保生产过
程符合标准要求
改进模具设计:优 化模具结构、尺寸、
2 材料等,提高铸件
成型精度
3
采用先进技术:如
快速凝固技术、电
磁搅拌技术等,提
高铸件性能
维护设备性能
01
定期检查设备,确保 其正常运行
设备维护不当:设备维护不及时,导致设备 性能下降,影响铸件质量
设备设计不合理:设备设计不合理,导致 生产过程中容易出现缺陷
球墨铸铁缺陷应对措 施
优化原材料选择
选择优质生 铁,降低杂
质含量
选用合适的 球化剂和孕 育剂,提高
球化效果
控制合金元 素含量,保 证化学成分
稳定
选用合适的 铸造工艺, 减少缺陷产
球墨铸铁缺陷产生 原因及应对措施
演讲人
目录
01. 球墨铸铁缺陷产生原因 02. 球墨铸铁缺陷应对措施 03. 球墨铸铁缺陷预防措施
球墨铸铁缺陷产生原 因
原材料质量
01 铁水成分:铁水中的碳、硅、锰等元素含 量对球墨铸铁的缺陷产生有很大影响
02 球化剂:球化剂的质量和加入量对球墨铸 铁的缺陷产生有很大影响
04
加强员工培训,提高员工的质量 意识和技能水平
定期检查设备
01
定期检查设备,确保设 备正常运行
02
定期更换磨损部件,避 免设备故障
03
定期清洁设备,保持设 备清洁
04
定期校准设备,确保设 备精度
05
定期培训员工,提高员 工操作技能
06
球铁的缺陷和防治
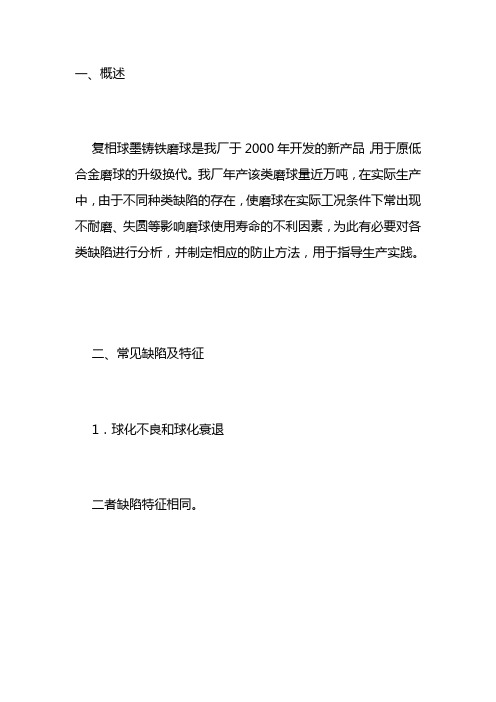
一、概述复相球墨铸铁磨球是我厂于2000年开发的新产品,用于原低合金磨球的升级换代。
我厂年产该类磨球量近万吨,在实际生产中,由于不同种类缺陷的存在,使磨球在实际工况条件下常出现不耐磨、失圆等影响磨球使用寿命的不利因素,为此有必要对各类缺陷进行分析,并制定相应的防止方法,用于指导生产实践。
二、常见缺陷及特征1.球化不良和球化衰退二者缺陷特征相同。
(1)宏观特征铸件断口为银灰色上分布芝麻状黑色斑点,其数量多、直径大,表明程度严重。
若全部呈暗灰色粗晶粒,表明球化不完全。
(2)金相组织集中分布大量厚片状石墨,其数量越多、面积越大,表明程度越严重,球化不完全时呈片状石墨。
(3)产生原因原铁液含硫高,以及严重氧化的炉料中含有过量反球化元素;处理后铁液残留镁和稀土量过低。
铁液中溶解氧量偏高是球化不良的重要原因。
选用低硫焦炭和金属炉料,必要时进行脱硫处理。
另外,应进行废钢除锈,以及增加球化剂中稀土元素用量,严格控制球化工艺。
2.缩孔和缩松特征和产生原因:缩孔产生于铁液温度下降发生一次收缩阶段。
如大气压把表面凝固薄层压陷,则呈现表面凹陷及局部热节凹陷,否则铁液中气体析出至顶部壳中聚集成含气孔的内壁光滑的暗缩孔,有时也与外界相通形成明缩孔,则内表面虽也光滑,但已被氧化。
球墨铸铁共晶凝固时间比灰铸铁长,呈粥状凝固,凝固外壳较薄弱,二次膨胀时在石墨化膨胀力作用下使外壳膨胀,松弛了内部压力。
因此在二次收缩过程中,最后凝固的热节部位内部压力低于大气压,被树枝晶分隔的小熔池处成为真空区,完全凝固后成为孔壁粗糙且排满树枝晶的疏松孔,即缩松缺陷。
宏观缩松产生于热节区残余铁液开始大量凝固的早期,包括了残余铁液的一次收缩和二次收缩,因而尺寸略大且内壁排满枝晶,呈灰暗疏松孔或蝇脚痕状黑点;微观缩松产生于二次收缩末期,共晶团或其集团间的铁液在负压下得不到补缩凝固收缩而成,常见于厚断面处。
3.皮下气孔(1)形貌特征铸件表皮下2~3mm处均匀或蜂窝状分布的球形、椭圆状或针孔状内壁光滑孔洞,直径0.5~3mm,可在热处理和抛丸清理后暴露或机加工时发现,小件中较多。
球铁件夹渣缺陷形成的影响因素分析
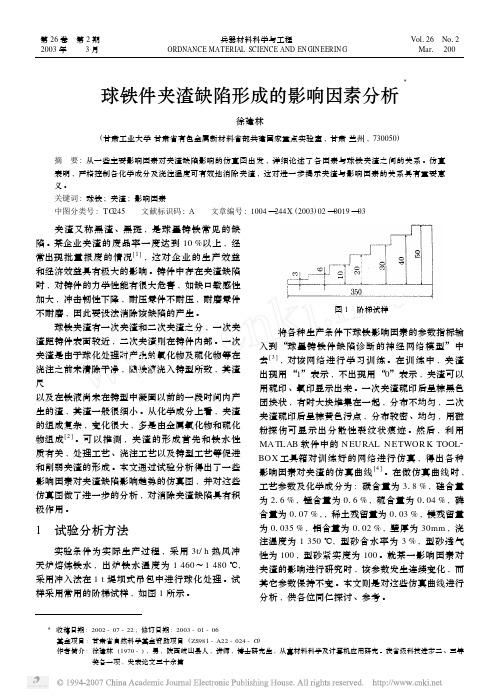
球铁件夹渣缺陷形成的影响因素分析Ξ徐建林(甘肃工业大学甘肃省有色金属新材料省部共建国家重点实验室,甘肃兰州,730050)摘 要:从一些主要影响因素对夹渣缺陷影响的仿真图出发,详细论述了各因素与球铁夹渣之间的关系。
仿真表明,严格控制各化学成分及浇注温度可有效地消除夹渣,这对进一步揭示夹渣与影响因素的关系具有重要意义。
关键词:球铁;夹渣;影响因素中图分类号:TG 245 文献标识码:A 文章编号:1004—244X (2003)02—0019—03 夹渣又称黑渣、黑斑,是球墨铸铁常见的缺陷。
某企业夹渣的废品率一度达到10%以上,经常出现批量报废的情况[1],这对企业的生产效益和经济效益具有极大的影响。
铸件中存在夹渣缺陷时,对铸件的力学性能有很大危害,如缺口敏感性加大,冲击韧性下降,耐压零件不耐压,耐磨零件不耐磨,因此要设法消除该缺陷的产生。
球铁夹渣有一次夹渣和二次夹渣之分,一次夹渣距铸件表面较近,二次夹渣则在铸件内部。
一次夹渣是由于球化处理时产生的氧化物及硫化物等在浇注之前未清除干净,随铁液浇入铸型所致,其渣尺以及在铁液尚未在铸型中凝固以前的一段时间内产生的渣,其渣一般很细小。
从化学成分上看,夹渣的组成复杂,变化很大,多是由金属氧化物和硫化物组成[2]。
可以推测,夹渣的形成首先和铁水性质有关,处理工艺、浇注工艺以及铸型工艺等促进和削弱夹渣的形成。
本文通过试验分析得出了一些影响因素对夹渣缺陷影响趋势的仿真图,并对这些仿真图做了进一步的分析,对消除夹渣缺陷具有积极作用。
1 试验分析方法 实验条件为实际生产过程,采用3t/h 热风冲天炉熔炼铁水,出炉铁水温度为1460~1480℃,采用冲入法在1t 堤坝式吊包中进行球化处理。
试样采用常用的阶梯试样,如图1所示。
图1 阶梯试样将各种生产条件下球铁影响因素的参数指标输入到“球墨铸铁件缺陷诊断的神经网络模型”中去[3],对该网络进行学习训练。
在训练中,夹渣出现用“1”表示,不出现用“0”表示,夹渣可以用硫印、氧印显示出来。
- 1、下载文档前请自行甄别文档内容的完整性,平台不提供额外的编辑、内容补充、找答案等附加服务。
- 2、"仅部分预览"的文档,不可在线预览部分如存在完整性等问题,可反馈申请退款(可完整预览的文档不适用该条件!)。
- 3、如文档侵犯您的权益,请联系客服反馈,我们会尽快为您处理(人工客服工作时间:9:00-18:30)。
中图分类号: T G 2 4 2 . 1 : 文献标识码 : A ; 文章编号 : 1 O 0 6 — 9 6 5 8 ( 2 0 1 3 ) 0 4 - 0 0 5 7 — 2
Ab s t r a c t : T h e f o r ma t i o n o f d e f e c t s a s s h r i n k a g e c a v i t y , s l a g i n c l u s i o n a n d p o o r n o d u l a r i t y w i t h d u c t i l e i r o n c a s e c a s t i n g s h a s b e e n s t u d i e d , wi t h a n a l y s i s a n d p r a c t i c e r e s u l t s i n d i c a t i n g a d i r e c t r e l a t i o n s h i p b e t w e e n t h e d e f e c t s wi t h t h e f u r a n r e s i n b o n d e d s a n d c o r e u s e d i n t h e c a s e c a s t i n g s .
( 1 . C h i n a Y i t u o G r o u p C o . L t d . , L u o y a n g 4 7 1 0 0 4 , He n a n C h i n a ;
2 . Yi t u o C a s t i n g Co . L t d . , L u o y a n g 4 7 1 0 0 4 , He n a n Ch i n a )
行 优 化设计 , 取 得 了很好 的效 果 。
1 铸 件简 介
盖 板厚 度均 为 6 0 m m, 有 5枚 主 叶片 , 主 叶片 厚度 为 8 0 m m, 另 外前 后端 盖 板 上各 有 1 O枚 副 叶 片 。叶 轮
的材质为高铬铸铁 , 产品技术要求比较严格 , 不允许
[ 1 ] 中国机械工程学会铸造分会 , 铸造手册第一 卷[ M ] . 北京 : 机械 工
业 出版社 , 2 0 0 7 . 1 0 : 3 4 4 — 3 6 0 . [ 2 ] 河 南省机械局球墨铸铁编写组 , 稀 土镁球 墨铸铁生产技术及 应
用[ M] . 郑州 : 河南省 机械局 1 9 7 6 : 2 2 2 5 — 2 3 6 . [ 3 ] 王进. 对 甲苯磺酸硬化呋 喃树脂 对球铁表层组织 的影响[ J ] . 铸 造
参 考 文 献
作者简介 : 冯晓冉( 1 9 8 4 一 ) 男, 从事高铬铸铁工艺和材料研究
4 结束 语
该球铁铸件缺陷主要是铸件砂芯过量加入的苯 磺酸消耗 了较多 的镁 、 稀土 , 导致铁液石墨畸变 , 从 而增加 了球化剂 的加人量 , 造成残余镁 、 稀土量增
加, 结果 又增 加 了铸件 缩松 、 夹 渣缺 陷 的产生 。其 主
D 0 I : l 0. 3 9 6 9 / j. 1 S S n. 1 0 0 6 —9 6 5 8. 2 0 1 3. 0 4. 0 1 8
渣浆泵在矿山 、 电力 等行业应 用广泛 , 叶轮作 为渣浆泵的核心部件 , 其质量关系到渣浆泵 的使用 寿命 , 因此不能有 冒口缩孔等铸造缺陷。部分渣浆 泵 叶轮 叶片盖板较厚 , 生产难度较大 , 冒口气缩孔 等 问题 频发 。对 此我 们 深入 分 析原 因 , 对 原 工 艺 进
技术 , 2 0 0 9 ( 6 ) : 2 5 2 — 2 5 6 .
要改进措施就是采用优质的呋喃树脂与原砂 , 降低
球 化 剂 的加入 量 。
An a l y s i s o f t h e Fo r ma t i o n o f Du c t i l e I r o n Ca s e Ca s t i n g De f e c t s a n d P r e v e n t i o n Co u n t e r me a s u r e s CHENG J u n We i , WA NG S h a o B o
有 冒 口缺 陷。 2 最初 的铸 造 工艺方 案
( 1 ) 造型设备采用 1 0 t 连续混砂机 , 呋喃树脂砂
造型。
本 次 进行 优 化 工艺 的渣浆 泵 叶 轮最 大 直 径 1 2 0 0 m m, 总高 4 0 5 m m, 流道高度为 1 5 0 m m, 前后
P r o d u c t i o n T e c h n i q u e s生产 技 术
渣浆泵叶轮铸造工艺 的优化 设计
冯 晓冉
( 石 家庄强 大 泵业 集 团有 限责任公 司 , 河北 石家 庄 0 5 0 0 3 5)
摘要 : 渣浆泵叶轮作为渣浆泵的主要过流部件 , 铸件质量要求很高。叶片和盖板较厚的叶轮有一定的生
收稿 日期 : 2 0 1 2 — 1 1 - 2 2 稿件编号 : 1 2 1 1 - 1 6 0
( 2 ) 分 型 面 选在 前 盖 板 即 吸人 口端 盖 板 中间部
位, 模型分型不分模, 成型底板 1 7 0 0 m m x 1 7 0 0 m m 。
( 3 ) 线 收 缩系数 取 2 %, ቤተ መጻሕፍቲ ባይዱ 道收 缩特殊 为 1 %。根 据 主叶 片个数 选择 5个 冒 口,画 图计算 盖 板与 叶片 的热 结 圆为 9 6 mm。根据 冒 口颈 的大小 为 热结 圆 的