曲柄压力机模锻
曲柄压力机简介机极其发展趋势
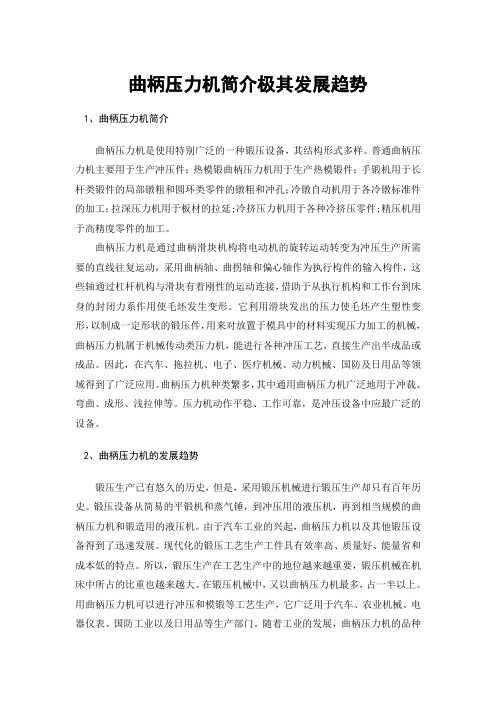
曲柄压力机简介极其发展趋势1、曲柄压力机简介曲柄压力机是使用特别广泛的一种锻压设备,其结构形式多样。
普通曲柄压力机主要用于生产冲压件;热模锻曲柄压力机用于生产热模锻件;手锻机用于长杆类锻件的局部镦粗和圆环类零件的镦粗和冲孔;冷镦自动机用于各冷镦标准件的加工;拉深压力机用于板材的拉延;冷挤压力机用于各种冷挤压零件;精压机用于高精度零件的加工。
曲柄压力机是通过曲柄滑块机构将电动机的旋转运动转变为冲压生产所需要的直线往复运动,采用曲柄轴、曲拐轴和偏心轴作为执行构件的输入构件,这些轴通过杠杆机构与滑块有着刚性的运动连接,借助于从执行机构和工作台到床身的封闭力系作用使毛坯发生变形。
它利用滑块发出的压力使毛坯产生塑性变形,以制成一定形状的锻压件,用来对放置于模具中的材料实现压力加工的机械,曲柄压力机属于机械传动类压力机,能进行各种冲压工艺,直接生产出半成品或成品。
因此,在汽车、拖拉机、电子、医疗机械、动力机械、国防及日用品等领域得到了广泛应用。
曲柄压力机种类繁多,其中通用曲柄压力机广泛地用于冲裁、弯曲、成形、浅拉伸等。
压力机动作平稳、工作可靠,是冲压设备中应最广泛的设备。
2、曲柄压力机的发展趋势锻压生产已有悠久的历史,但是,采用锻压机械进行锻压生产却只有百年历史。
锻压设备从简易的平锻机和蒸气锤,到冲压用的液压机,再到相当规模的曲柄压力机和锻造用的液压机。
由于汽车工业的兴起,曲柄压力机以及其他锻压设备得到了迅速发展。
现代化的锻压工艺生产工件具有效率高、质量好、能量省和成本低的特点。
所以,锻压生产在工艺生产中的地位越来越重要,锻压机械在机床中所占的比重也越来越大。
在锻压机械中,又以曲柄压力机最多,占一半以上。
用曲柄压力机可以进行冲压和模锻等工艺生产,它广泛用于汽车、农业机械、电器仪表、国防工业以及日用品等生产部门。
随着工业的发展,曲柄压力机的品种和数量越来越多,质量要求越来越高,压力越来越大。
它在机械制造工业以及其他工业的锻压生产中的作用越来越显著。
模锻

模 锻
模锻设备 锤上模锻工艺 胎膜锻
模 锻
模锻:使加热到锻造温度的金属坯料在锻模模膛内一次或 多次承受冲击力或压力的作用,而被迫流动成形以获得锻 件的压力加工方法。
模锻件的特点及应用
特点: 操作简单,易于实现机械化自动化, 生产率较高; 尺寸精度高,加工余量小,材料利用 率高; 锻件形状复杂; 应用: 流线完整、性能好。
长 轴 类 锻 件
短 轴 类 锻 件
蒸汽—空气模锻锤
锤上模锻
锤上模锻
锻模结构
终锻模膛
模锻模膛 预锻模膛 拔长模膛 制坯模膛 滚压模膛 弯曲模膛 切断模膛
模膛
锤上模锻
锤上模锻
锻模结构
锤上模锻
锻模结构
拔长模膛
开 式
闭 式
锤上模锻
锻模结构
滚压模膛
开 式
闭 式
锤上模锻
锻模结构
弯曲模膛
锤上模锻
锻模结构
切断模膛
锤上模锻
锻模结构
预锻模膛
预锻模膛与终锻模膛 的区别是前者的圆角 和斜度较大,没有飞 边槽。
锤上模锻
切边和冲孔 校正
模锻工艺规程
修整工序
热处理
清理 精压
锤上模锻工艺
模锻的变形工步和模锻模膛
弯曲连杆的多 模膛锻模 制坯工步,制坯模膛 (锻件初步成形) 模锻工步,模锻模膛 (锻件最终成形)
2、胎膜锻的工艺过程 胎膜锻工艺过程包括制订工艺规程、制造胎 膜、备料、加热、锻制及后续工序等。
法兰盘胎膜锻造过程,所用胎膜为套筒模,它由模筒、模 垫和冲头组成。原始坯料加热后,先用自由锻锻粗,然后 将模垫和模筒放在下砧铁上,再将镦粗的坯料平放在模筒 内,压上冲头后终锻成形,最后将连皮冲掉。
曲柄压力机

曲柄压力机简介曲柄压力机是一种常见的机械设备,利用曲柄连杆机构将来自动力系统的旋转运动转换为线性运动,从而实现对工件的压缩加工。
曲柄压力机广泛应用于金属加工、塑料加工等工业领域,具有结构简单、操作方便、加工效率高等优点。
工作原理曲柄压力机主要由曲柄连杆机构、滑块和工作台等组成。
工作时,曲柄连杆机构受到动力系统的驱动,使曲柄旋转。
曲柄的旋转运动由连杆传递给滑块,从而使滑块沿着直线轨道做往复运动。
同时,滑块上的模具通过工件,对其进行压缩加工。
结构和部件1. 曲柄曲柄是曲柄压力机的核心部件之一,它是一根轴,一端通过轴承安装在机身上,另一端与连杆相连。
曲柄的旋转运动转换为连杆的往复运动。
2. 连杆连杆是曲柄压力机的关键部件之一,它将曲柄的旋转运动转换为滑块的往复运动。
连杆一端与曲柄相连,另一端与滑块相连,实现力的传递。
3. 滑块滑块是曲柄压力机的工作部件之一,它通过连杆与曲柄相连,实现往复运动。
滑块上通常安装有模具,用于对工件进行压缩加工。
4. 工作台工作台是曲柄压力机的工作平台,用于放置工件和模具。
工件在加工过程中固定在工作台上,以保证加工的稳定性和精度。
5. 驱动系统曲柄压力机的驱动系统通常由电动机、减速器和传动装置等组成。
电动机提供动力,通过减速器和传动装置将动力传递给曲柄,驱动曲柄进行旋转。
应用领域曲柄压力机在众多行业中得到广泛应用,包括但不限于以下几个领域:1.金属加工:曲柄压力机可用于金属板材的成型、冲压、拉伸和弯曲等工艺。
2.塑料加工:曲柄压力机可用于塑料制品的注塑成型、挤出成型等工艺。
3.木工加工:曲柄压力机可用于木材的切割、镶嵌、翻边等工艺。
4.橡胶加工:曲柄压力机可用于橡胶制品的成型、硫化等工艺。
优点和局限优点1.结构简单:曲柄压力机的结构相对简单,易于维护和维修。
2.操作方便:曲柄压力机的操作相对简单,只需控制启动、停止和调整动力系统即可。
3.加工效率高:曲柄压力机的工作过程连续、稳定,能够提高加工效率。
曲柄压力机
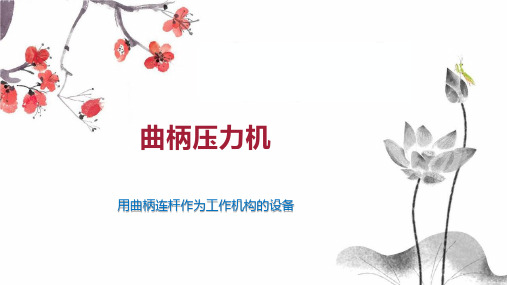
单点压力机有一个连杆,双点和四点压力机分别有两个和四个连杆。
3)按滑块数目分可分为单动压力机、双动压力机和三动压力机三种。
双动及三动压力机一般用于复杂制件的拉深。这种压力机可用于较大、较高制件的拉深。压力机的工作部分 由拉深滑块、压边滑块、工作台三部分组成。拉深滑块由主轴上的齿轮及其偏心销通过连杆带动。工作台由凸轮 传动,压边滑块在工作时是不动的。工作时,凸模固定在拉深滑块上,压边圈固定在压边滑块上,而凹模则固定 在工作台上。工作开始时,工作台在凸轮的作用下上升,将坯料压紧,并停留在此位置。
曲柄压力机
用曲柄连杆作为工作机构的设备
01 工作原理
03 技术参数
目录
02 组成 04 分类
基本信息
曲柄压力机是指采用曲柄连杆作为工作机构的压力机。曲柄压力机是最常用的冷冲压设备,其结构简单,使 用方便,动作平稳,工作可靠,广泛用于冲压、挤压、模锻和粉末冶金等工艺。
工作原理
工作原理
曲柄压力机通过传动系统把电动机的运动和能量传递给曲轴,使曲轴作旋转运动,并通过连杆使滑块产生往 复运动。
谢谢观看
技术参数
技术参数
1.标称压力(公称力)及标称压力行程(公称力行程) 曲柄压力机的标称是指曲柄旋转至下止点前。某一特定距离或曲柄转角时,滑块允许的最大作用力,此特定 距离称为标称压力行程,特定转角称为标称压力角。 2.滑块行程S 指滑块从上止点到下止点所经过的距离,它是曲柄半径或偏心齿轮、偏心轴的偏心距的两倍。 3.滑块行程次数乃 指滑块每分钟往复运动的次数。 4.最大装模高度及装模高度调节量 装模高度是指滑块在下止点时,滑块下表面到工作台垫板上表面的距离。装模高度的最大值称为最大装模高 度,滑块调整到最低位置时得到最小装模高度!封闭高度是指滑块在下止点时,滑块下表面到工作台上表面的距离, 它与装模高度之差等于工作台垫板的厚度T。装模高度调节的距离,称为装模高度调节量。
模锻工艺过程

《冲压工艺与模具设计》
锻压工艺及模具设计
模锻工艺过程
机械学院
《冲压工艺与模具设计》
锻压工艺及模具设计
模锻工艺过程
机械学院
长轴类锻件
长轴类锻件的轴线较长,即锻件的长度尺寸远大 于其宽度尺寸和高度尺寸。模锻时,毛坯的轴线 方向与打击方向垂直。在成形过程中,由于金属 沿长度方向的变形阻力远大于其他两个方向,因 此主要沿高度和宽度方向变形,而沿长度方向的 变形很小,当锻件沿长度方向截面变化较大时, 必须考虑有效的制坯工步,如卡压、拔长、滚挤、 弯曲等工步,以保证模膛完全充满。
《冲压工艺与模具设计》
锻压工艺及模具设计
模锻工艺过程
机械学院
《冲压工艺与模具设计》
可采用锻-焊组合工艺,简化模锻工艺。
《冲压工艺与模具设计》
锻压工艺及模具设计 机械学院
模锻工艺过程
模锻件结构工艺性
《冲压工艺与模具设计》
锻压工艺及模具设计
模锻工艺过程
机械学院
模锻件图设计
模锻件图是模锻生产过程、模 锻工艺过程规范制订、锻模设 计、锻模检验及锻模制造的依 据。模锻件图是根据产品图设 计的,分为冷锻件图和热锻件 图两种。
模锻工艺过程
选定分模面的原则
机械学院
齿轮坯锻件分 模面的选择
能从模膛中顺利取出; 金属易于充满模膛; 简化模具制造; 能及时发现错模; 减少余块节约金属。
《冲压工艺与模具设计》
锻压工艺及模具设计
模锻工艺过程
机械学院
2.加工余量和公差的确定
对于带有小孔和某些凹槽等结构的锻件,
即使采用可分凹模模锻,难免总会有些不 便模锻成形的部位。对于这些不便模锻成 形的部位,可以加上敷料,简化成可以将 其锻出的锻件。 锻件上凡是尺寸精度和
曲柄压力机操作规程

曲柄压力机的操作程序
1、安装模具时,模具的闭合高度必须与曲柄压力机的闭合高度匹配。
调整压力机的闭合高度时,应采用寸动冲程。
压力机的工作台不
允许处于最低极限位置,而应处于其调节量的中限,模具固定要牢靠。
2、工作前仔细检查压缩空气的压力,当压力小于3.92MPa(40kgf /cm2)时,不得开动压力机。
检查曲柄压力机的操纵系统、润滑系统
是否正常。
检查离合器、制动器及防护装置是否安全完好。
3、防止压力机滑块卡住,严禁在该设备上超负荷工作。
4、电机启动后,只有在飞轮速度正常后,才能操作滑块进行锻造,工作中,操作人员不得离开岗位,也不准清理、调整、润滑设备。
不
准将手或工具等伸入滑块行程范围内。
5、曲柄压力机的脚踏操纵板上应装安全罩,以免由于他人或其他
物体的错误压力而导致滑块突然滑动,造成意外事故。
6、大量生产,压力机长时间连续工作时,应注意检查电机、离合器、制动器、滑块及导轨等处有无过热、冒烟、打火花等现象,如果有,应在继续工作前适当冷却。
7、工作结束,使曲柄压力机滑块下降到下止点位置,关闭压缩空气,整理工作场地,做好交接班。
第十一章自由锻和模锻

第十一章自由锻和模锻第一节自由锻自由锻是利用冲击力或压力使金属在上下两个抵铁之间产生变形,从而获得所需形状及尺寸的锻件。
1.自由锻的优缺点2.自由锻的设备一、自由锻工序自由锻的工序可分为基本工序、辅助工序和精整工序三大类。
1.基本工序它是使金属坯料实现主要的变形要求,达到或基本达到锻件所需形状和尺寸的工艺过程。
如镦粗、拔长、弯曲、冲孔、切割、扭转和错移等。
实际生产中常采用的是镦粗、拔长和冲孔三个工序。
2.辅助工序是指进行基本工序之前的预变形工序。
如压钳口、倒棱、压肩等. 3.整理工序它是在完成基本工序之后,用以提高锻件尺寸及位置精度的工序。
二、自由锻工艺规程的制订制订自由锻的工艺规程包括绘制锻件图,确定变形工步,计算坯料的重量和尺寸,选定设备和工具,确定锻造温度范围和加热、冷却及热处理的方法和规范等。
1.绘制锻件图绘制锻件图应考虑以下几个因素.(1)(1)敷料如图1l—1(a)所示(2)加工余量(3)锻件公差锻件图的画法如图11—1(b)所示,2.坯料质量及尺寸计算坯料质量可按下式计算;G坯料=G锻件+G烧损+ G烧损式中 G坯料——坯料质量;G锻件——锻件质量;G烧损——加热时坯料表面氧化而烧损的质量.第一次加热取被加热金属的2~3%,以后各次加热取1.5~2.0%,G烧损——在锻造过程中冲掉或被切掉的那部分金属的质量.如冲孔时坯料中部的料芯.修切端部产生的料头等.当锻造大型锻件采用钢锭作坯料时,还要考虑切掉的钢锭头部和钢锭尾部的质量。
3.选择锻造工序选择自由锻造工序,主要是根据工序特点和锻件形状来确定,对一般锻件的大致分类及所采用的工序如表11-1所示。
三,自由锻锻件结构工艺性1.1.锻件上具有锥体或斜面的结构,从工艺角度衡量是不合理的如图11—2(a)。
因为锻造这种结构,必须制造专用工具,锻件成形也比较困难,使工艺过程复杂化,操作很不方便,影响设备的使用效率,所以要尽量避免。
应改进设汁,如图ll--2(b)。
第五章热模锻曲柄压力机上模锻

分模优点:毛边体积小。可锻深孔。用挤压、墩粗替代拔长、滚挤。
2.形状较复杂的长轴、弯曲类锻件分模面与锤上模锻,以纵向最大剖面分模。
二、余量与公差 和压力机吨位有关。与锤上模锻相比余量和公差相应减少。余量小30~50%,公差小一个等级。
曲柄压力机模锻件公差及其余量
三、锻模斜度、圆角半径、冲孔连皮 锻模斜度:无顶出机构时与锤上模锻相同。有顶出结构时斜度可显著的减少。 曲柄压力机模锻斜度(º) 圆角半径:和锤上模锻相比,圆角半径要增加。 冲孔连皮:设计同锤上模锻。
5-5 锻模结构 一、锻模结构形式 曲柄压力机工作时滑块速度低,工作平稳,装有顶出 机构,锻时上下模不压靠,锻模承受过剩能量少,不考虑 锻模承击面。 压力机模具大多数采模座+内带型槽镶块的组合形式 结构。 模架主要组成有: 模座; 导柱、导套; 顶出结构; 镶块紧固件; 镶块垫板等组成。
锤上模锻分模面
曲柄压力机模锻分模面
(2)终锻型槽有较深的孔时,应在金属最后充型的部位增加通气孔。
2.镶块的形状与尺寸 镶块的形式随锻件的形状和镶块的紧固方式而定。 镶块的种类:圆形和矩形。用压板或斜度匹配进行紧固。 镶块模壁厚度S0 S0=(1~1.5)h ≥ 40mm 镶块闭合状态的高度不大于(0.3~0.4)H(模具闭合高度)
连杆工作原理图
(2)系统构成 工作系统:称曲柄连杆机构。它由曲轴、连杆、滑块等零件组成,其作用是将曲柄的旋转运动转变为滑块的直线往复运动,由滑块带动模具工作。 传动系统:包括齿轮传动、皮带传动等机构,起能量传递作用和速度转换作用。 操纵系统:包括离合器、制动器等零部件,用以控制工作机构的工作和停止。 能源系统:包括电动机、飞轮。 支撑部分:主要指机身,它把压力机所有部分连接成一个整体。 辅助系统:如润滑系统、保护装置等。
- 1、下载文档前请自行甄别文档内容的完整性,平台不提供额外的编辑、内容补充、找答案等附加服务。
- 2、"仅部分预览"的文档,不可在线预览部分如存在完整性等问题,可反馈申请退款(可完整预览的文档不适用该条件!)。
- 3、如文档侵犯您的权益,请联系客服反馈,我们会尽快为您处理(人工客服工作时间:9:00-18:30)。
(4)模锻工艺特点:
1.锻件尺寸稳定,精度高。机架结构封闭,刚性大。
2.金属变形均匀、深而透,流线分布合理,锻造时只需锻 压一次,金属墩粗能力强,压入变形能力弱,型槽深处不 易充满。
2020/5/14
与锤上模锻充型区别
3.锻件容易产生较大毛边。金属变形时水平方向流动比锤 上模锻剧烈,锻件在上下模变形差别小。 4.对变形速度敏感的低塑性材料成型有利。
2020/5/14
(2)顶件结构形式:与顶杆数量、顶件位置、顶出器形 状及数量有关,分为单工位单顶出、单工位二顶出、三工 位六顶出等等。
2020/5/14
(3)顶杆的尺寸:设计时顶杆不能太细,要有足够的刚 度,顶杆尽量短,镶块上应有足够长度的导向部分。顶杆 的直径设计一般取10~30mm,导向部分与镶块的单边 留有0.05~0.1mm的间隙。
模架主要组成有: 模座; 导柱、导套; 顶出结构; 镶块紧固件; 镶块垫板等组成。
2020/5/14
生产中锻模结构形式: (1)单工位镶块用斜楔紧固 上下模有矩型槽。 用楔铁和键固定模垫3、7 用楔铁5固定模块4 前后位置有拉楔11和垫片9 调整设有导向机构2、12
2020/5/14
(2)三工位圆形镶块用压板紧固 圆形镶块4放在垫板3上, 压板6固定圆形镶块4, 后挡板5固定在上下模块。 设有导向机构7、8
斜度可显著的减少。
曲柄压力机模锻斜度(º)
圆角半径:和锤上模锻相比,圆角半径要增加。 冲孔连皮:设计同锤上模锻。
2020/5/14
5-3 变形工步、工步图设计及坯料尺寸确定
一、锻件变形工步的选择
直接终锻
墩粗后终锻 墩粗、预锻、终锻
第一类
杆部墩粗、预锻、终锻 冲孔、预锻、终锻
第二类
墩粗制坯、冲孔、预锻、终锻 头部冲孔、预锻、终锻
第三类
2020/5/14
多型槽、计算毛坯、制坯、预锻。终锻
平锻制坯、预锻、终锻
第四类
2020/5/14
二、工步图设计
变形工步:墩粗、弯曲、设计
设计内容:
热锻件图;
毛边槽形式;
冲孔连皮的形状和尺寸。
热锻件图设计与锤上模锻相同。
毛边槽尺寸和锤上模锻不同,
桥部高度和仓部高度比锤上模
2020/5/14
2.形状较复杂的长轴、弯曲类锻件分模面与锤上模锻,以 纵向最大剖面分模。 二、余量与公差
和压力机吨位有关。与锤上模锻相比余量和公差相应减 少。余量小30~50%,公差小一个等级。
曲柄压力机模锻件公差及其余量
2020/5/14
三、锻模斜度、圆角半径、冲孔连皮 锻模斜度:无顶出机构时与锤上模锻相同。有顶出结构时
房要求比锤上模锻低。 2.具有导向机构,设备精度高。 3.楔形工作台,可以调节锻压机闭合高度,可以避免闷车
事故。 4.具有自动顶出机构,取料方便,易实现自动化、机械化
。 5.设备造价高,锻压机的行程和压力不易任意调节,不适
应拔长、滚挤等制坯。 6.加热质量高,模具或设备操作不当,会闷车。
2020/5/14
5 曲柄压力机模锻
5.1曲柄压力机模锻 特点及其应用范围
(1)工作原理及过程
工作过2020程/5/14:按顺序1-2-3-4-56-8-9-10进行模锻。
2020/5/14
连杆工作原理图
(2)系统构成
工作系统:称曲柄连杆机构。它由曲轴、连杆、滑块等零 件组成,其作用是将曲柄的旋转运动转变为滑块的直线 往复运动,由滑块带动模具工作。
传动系统:包括齿轮传动、皮带传动等机构,起能量传递 作用和速度转换作用。
操纵系统:包括离合器、制动器等零部件,用以控制工作 机构的工作和停止。
能源系统:包括电动机、飞轮。
支撑部分:主要指机身,它把压力机所有部分连接成一个 整体。
辅助系统:如润滑系统、保护装置等。
2020/5/14
(3)设备特点: 1.工作时震动小、噪音小,劳动条件好,操作安全,对厂
锻大,毛边槽主要起容纳多余
金属的作用。
2020/5/14
毛边槽结构形式
冲孔连皮的形式和尺寸同锤上模锻。 2.预锻工步图设计 设计依据:终锻工步图设计。 设计时注意事项: (1)预锻型槽高度尺寸(点划线)应比终锻件相应高度 大2~5mm。预锻圆形截面横截面椭圆度约为终锻锻件相 应截面4%~5%。
2020/5/14
三、确定坯料尺寸
(一)原坯料尺寸的确定
(1)第一道是墩粗时,考虑H0/D0=1.5~2.5,计算出的坯料直径 为:
D0=(0.9~0.35V)坯 考虑一次行程内完成,D0应增大:
D0=(0.8~0.39)V 坯 (2)第一次变形为正挤时
(二)坯料的长度
D0=(0.9~0.5)D1 D1不小于0.7D0 反挤时
2020/5/14
二、型槽设计 1.型槽设计特点
设计的一般方法与锤上模锻相同。根据曲柄压力机的 结构及性能特点,注意以下问题: (1)曲柄压力机上下模充型能力相差不大,不要求将形 状复杂的一面放入上模。旋转体形的锻件的分模面不一定 选在锻件最大尺寸的中部。
2020/5/14
锤上模锻分模面
曲柄压力机模锻分模面
≈ D0=D1-(2~5)mm, D0 D2
2020/5/14
5-4 变形力计算与设备吨位选择
1.经验法 锻锤所需的压力P
钢种系数:0.9~1.55
P=(64~73)K F
平面图锻件投影面积(毛边槽在内)
2.理论—经验公式 平面图为圆形锻件时
P=8(1-0.00 )1 (.1 1+2 D)0 2σbF锻
2020/5/14
导向装置
本章结束
2020/5/14
平面图为非圆形锻件
2020/5/14
P 非 =8(1-0.0D 0换 )11 (.1+D 2换 )0 ( 21 + 0.1B L 锻 平 ) σbF 锻
5-5 锻模结构
一、锻模结构形式 曲柄压力机工作时滑块速度低,工作平稳,装有顶出
机构,锻时上下模不压靠,锻模承受过剩能量少,不考虑 锻模承击面。
压力机模具大多数采模座+内带型槽镶块的组合形式 结构。
(2)严格控制预锻型槽各部分的体积,终锻时金属流动 合理,避免发生金属回流、折叠等缺陷。孔径较大的孔冲 孔时设计仓部,以容纳多余金属。
2020/5/14
终锻型槽冲孔连皮结构
(3 )要考虑在终锻型 槽的定位问题。设计有 些部位尺寸和形状与终 锻型槽一致,终锻一开 始锻件与型壁接触。
(4)对于复杂的锻件 预锻型槽可以设计毛边 槽,桥部高度比终锻型 槽大30~60%。
(2)终锻型槽有较深的孔时,应在金属最后充型的部位 增加通气孔。
2020/5/14
2.镶块的形状与尺寸 镶块的形式随锻件的形状和镶块的紧固方式而定。 镶块的种类:圆形和矩形。用压板或斜度匹配进行紧固。
圆形镶块设计凸台供压板压紧
斜度与压板斜度匹配紧固
带柄圆形镶块用螺钉紧固
镶块模壁厚度S0
S0=(1~1.5)h ≥ 40mm
(5)压入充型型槽
设计时,终锻型槽的
冲孔凸台端头圆角半
2020/5/14
径要增大.
3.墩粗工步图设计 根据锻件的形状及其复杂程和生产批量采用自由墩粗
和成形镦粗。
自由镦粗
2020/5/14
成型镦粗
墩粗时要注意墩粗后坯料高度。
上下盲孔时不充满系数取1.01~1.05
2020/5/14
单向盲孔时系数取大些,为1.2~1.3
四、导向装置 压力机锻模上一般不设锁口,使用导向机构,一般模具
采用双导柱,个别有四导柱。 导向装置包括:导柱、导套。导柱和导套之间有
0.25~0.5mm间隙。 导柱要具有良好的耐磨性和韧性,可用低碳合金钢渗碳
淬火低温回火处理,导套可用青铜或黄铜制造。 导柱、导套的尺寸由压力机吨位查相关手册确定。
2020/5/14
(5)适应范围: 1.要求精度高,大批量连续生产和高生产率的模锻件。 2.多工步,多模膛,形状比较复杂的锻件。 3.各类热挤压、温挤压和多向模锻。
2020/5/14
5-2 锻件图设计
一、分模位置的选择 1.对于杆形和环形锻件可竖起分模,分模面可取在最大截
面上。
分模
分模优点:毛边体积小。可锻深孔。用挤压、墩粗替代拔 长、滚挤。
镶块闭合状态的高度不大于(0.3~0.4)H(模具闭合高度)
2020/5/14
三、顶件机构
设计目的:便于锻件从型槽中取出。顶件动作是由顶件机构产生的 推压力来实现,顶出器与锻件接触的端面是型槽的一部分。
设计顶出机构主要解决的问题:顶件位置;具体的结构形式;顶杆 的可靠性。
(1)顶件位置:毛边、冲孔连皮、锻件本体。