节能降耗技术在焦化工艺中的应用
焦化厂节能降耗方案
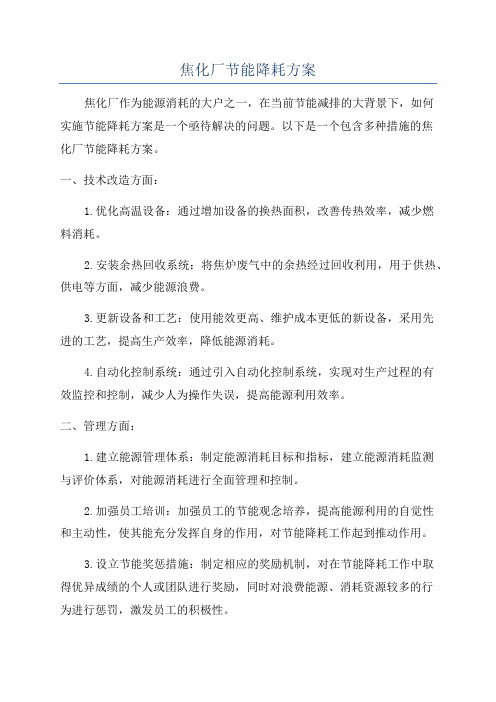
焦化厂节能降耗方案焦化厂作为能源消耗的大户之一,在当前节能减排的大背景下,如何实施节能降耗方案是一个亟待解决的问题。
以下是一个包含多种措施的焦化厂节能降耗方案。
一、技术改造方面:1.优化高温设备:通过增加设备的换热面积,改善传热效率,减少燃料消耗。
2.安装余热回收系统:将焦炉废气中的余热经过回收利用,用于供热、供电等方面,减少能源浪费。
3.更新设备和工艺:使用能效更高、维护成本更低的新设备,采用先进的工艺,提高生产效率,降低能源消耗。
4.自动化控制系统:通过引入自动化控制系统,实现对生产过程的有效监控和控制,减少人为操作失误,提高能源利用效率。
二、管理方面:1.建立能源管理体系:制定能源消耗目标和指标,建立能源消耗监测与评价体系,对能源消耗进行全面管理和控制。
2.加强员工培训:加强员工的节能观念培养,提高能源利用的自觉性和主动性,使其能充分发挥自身的作用,对节能降耗工作起到推动作用。
3.设立节能奖惩措施:制定相应的奖励机制,对在节能降耗工作中取得优异成绩的个人或团队进行奖励,同时对浪费能源、消耗资源较多的行为进行惩罚,激发员工的积极性。
三、能源利用方面:1.多能联供:通过联合供热、供电、供气等方式,实现多能联用,减少能源的浪费。
2.引进清洁能源:如太阳能、风能等,替代传统能源,降低对化石能源的依赖。
3.合理利用余热:将余热应用于供热、供电等方面。
例如,利用余热进行蒸汽发电,提高热电联供的效益。
4.循环经济利用:采用焦炉煤气循环利用技术,将焦炉煤气转化为发电或燃料,提高能源利用效率。
四、环保措施:1.精细管理:加强对各个环节的监控与管理,减少化学品的用量,降低污染物产生,并通过技术改造,提高产出物的质量,减少环境污染。
2.排放治理:对废气、废水等进行集中治理,采用高效净化设备,减少对环境的污染。
3.宣传教育:加强环境保护宣传教育,提高员工的环保意识,增强环境保护的责任感。
通过以上多种措施的综合应用,可以有效地提高焦化厂的能源利用效率,降低能源消耗,减少对环境的污染。
焦化工艺中节能降耗技术的应用探讨

焦化工艺中节能降耗技术的应用探讨随着我国工业化进程的加快,能源消耗问题日益突出,节能降耗已成为一项迫切需求。
作为重要的工业生产过程之一,焦化工艺中的节能降耗技术应用显得尤为重要。
下面,我们将对焦化工艺中节能降耗技术的应用进行探讨。
一、焦化工艺简介焦化是将煤接受高温非氧化性加热处理,制得焦炭和一些副产品的过程。
它是煤炭加工的重要环节,也是我国重要的能源产业之一。
在焦化过程中,将煤炭加热至高温,使其在缺氧条件下分解,生成焦炭和一系列有机气体,如焦油、苯等。
这些产品广泛应用于冶金、化工、建材等行业。
传统的焦化工艺对能源、环境的影响较大。
在煤炭的预处理、干馏、冷却等环节,都需要大量的热能和电能。
焦炉煤气和焦炉煤气净化处理所需的水和能耗也较大。
由于焦化工艺使用的主要原料是煤炭,而煤炭的资源和环境约束对焦化工艺的发展提出了新的挑战。
如何在维持焦化生产能力的实现节能降耗,成为了亟待解决的问题。
二、焦化工艺中的节能降耗技术1. 高效预处理技术在焦化工艺中,煤炭的预处理是一个耗能较大、产生大量固体废物的环节。
传统的煤炭预处理技术采用了磨煤机、筛分机等设备,效率较低,制约了能源利用效率的提高。
采用高效预处理技术是焦化工艺实现节能降耗的关键。
可以借鉴其他行业先进的预处理技术,如新型煤粉制备技术、气动除灰技术等,提高煤炭预处理的效率,减少能耗。
2. 高效热能利用技术在焦化过程中,大量的热能被浪费掉了。
为了提高热能利用率,可以采用高效的热能回收技术,例如热交换器、余热发电技术等,将废热转换成电能,回馈给生产系统。
可以通过提高燃烧效率、降低热损失等手段,减少热能的浪费。
3. 清洁生产技术传统的焦化工艺中,与炉内冷却过程和煤气净化处理过程中会产生大量的废水和废气,对环境造成严重污染。
采用清洁生产技术,如水循环利用技术、煤气净化技术等,可以有效降低废水和废气的排放,减轻对环境的影响,实现循环利用。
4. 自动化控制技术在焦化工艺中,传统的生产方式大多依靠人工操作,存在能源浪费和生产效率低下的问题。
焦化厂节能降耗方案

焦化厂年度节能降耗管控方案当前焦化行业市场低迷,生产成本相对较高,公司运营面临巨大压力。
为应对市场不利局面,积极响应总公司开展节能降耗、降成本会议的精神要求,炼焦公司结合自身实际,本着“严、细、实、恒”的原则深化成本管理工作,在我公司范围内大力开展节能降耗、成本管控的工作,做到有目标、有考核、有措施、有落实、有改进,真正将炼焦公司的节能降耗、降本增效工作落到实处,特制定本方案。
一、指导思想根据炼焦公司成本管控的精神,以“降成本、增效益、强管理”为主题,以群众性合理化建议活动为载体,充分调动职工群众的积极性和创造性,全力打一场“降本增效”的攻坚战。
二、主要目标根据公司2012年度实际成本费用等情况,对2012年度目标成本费用指标进行分解、落实责任到人,全方位、全环节开展节能降耗,从技术上、管理上降成本,以保证公司年度各项生产经营目标的实现,为公司创造更多的利润。
三、领导机构:组长:副组长:成员:四、具体措施:在我们现阶段的生产中,由于市场原因,造成我们的利润大幅降低,因此,我们必须改变现场粗放的管控方式,各点工艺指标,煤焦比控制,煤焦耗热量化产回收率,筛焦粘度,水份等要对各环节控制点做好细化管控工作。
(一)备煤工段重点控制工艺:煤焦比:保证焦炭单炉产量的前提下,尽可能的使用较少的煤,确保煤焦比不超1.25,同时,在确保焦炭质量的前提下,优化各单种煤配比,降低精煤成本。
煤场管理:单种煤之间必须有3m以上的间隔,杜绝混煤,避免由于混煤造成的成本增加,出现混煤对当班班长考核200元。
配煤管理:各单种煤必须按计划配比进行配入,杜绝出现少配或多配,皮带称严禁出现断料现象,出现断料配煤室要及时打铃,监护人员必须监护好皮带称下料情况,出现上述情况对相关负责人予以最低100元罚款。
焦粉管理:焦粉必须保证配入量,烘干机和球磨机禁止空运转。
(二)炼焦工段:1、使用合理的加热制度,降低煤气消耗量,空气过剩系数保持在1.15---1.3之间,大烟囱禁止出现冒烟现象,每冒一次考核当班班长20元。
焦化工艺水系统介绍及节能降耗措施

焦化工艺水系统介绍及节能降耗措施河北旭阳王立召摘要:本文以焦耐院图纸为依据介绍了焦化水系统的组成和运行,并对可以改进的地方提出了自己的建议,对公司节能降耗工作提供参考。
关键词:水系统节能降耗一、前言“节能减排”工作现在已成为我国政府和社会各界的首要任务,作为一个焦化或煤化工行业,更是处于环保风暴的风头浪尖。
切实做好节能降耗工作,对于企业自身也是意义深远。
07年6月至08年5月,本人负责了河北旭阳焦化二期化产循环水系统以及全厂地下水网的建设工作,对焦化工艺水系统有一些了解和认识。
二、焦化水系统介绍焦化水系统基本可分为生活水系统、生产消防水系、冷却水系统统、再次利用水系统、污水处理及回用系统、凝水回收系统。
2.1 生活水系统由深井水直接补水,作为人们日常饮用和清洗用水。
系统呈网状,由厂区1#、4#、5#为主要水源。
系统和甲醇生活水系统联网,互为备用。
2.2 生产消防水系统本系统与甲醇消防水系统联网,由甲醇消防水池提供水源。
系统呈网状,在连接处双路备用。
主要作为备煤、炼焦、化产日常生产的一次水,间作消防用水。
2.3 冷却水系统冷却水系统分为回收循环水系统、制冷循环水系统、低温水系统。
制冷循环水系统配合制冷站使用。
低温水系统用阀门控制将2×112冷却塔与制冷站分为两个系统,夏季使用制冷站冷却,冬季使用冷却塔冷却。
2.4 再次利用水系统本系统主要包含的内容是由回收循环水和制冷循环水系统的排污水进入污水处理做稀释水。
2.5 污水处理及回用系统处理前包括酚水自流系统、剩余氨水系统、稀释水系统;处理后包括处理后压力管道(去熄焦)、处理后自流管道(外排)。
2.6 凝水收集系统主要指制冷机蒸汽冷凝水收集系统。
蒸汽冷凝水经受收集后,可直接进入锅炉再次使用,从而降低了深井水的消耗以及软化水所产生的费用。
三、存在的问题和可以改进的地方整个水系统中“中水系统”明显不足,对于“废水”的循环利用尤其是多次使用还不够。
浅谈钢铁焦化厂节能降耗措施
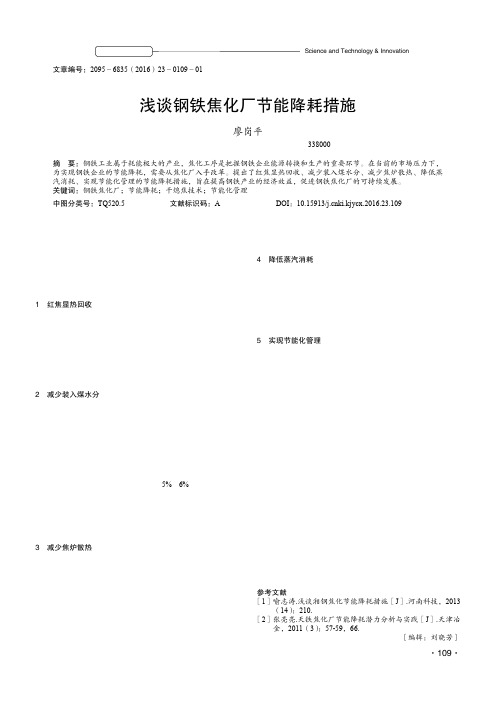
Science and Technology & Innovation ┃科技与创新・109・文章编号:2095-6835(2016)23-0109-01浅谈钢铁焦化厂节能降耗措施廖岗平(新余钢铁股份有限公司焦化厂,江西 新余 338000)摘 要:钢铁工业属于耗能极大的产业,焦化工序是把握钢铁企业能源转换和生产的重要环节。
在当前的市场压力下,为实现钢铁企业的节能降耗,需要从焦化厂入手改革。
提出了红焦显热回收、减少装入煤水分、减少焦炉散热、降低蒸汽消耗、实现节能化管理的节能降耗措施,旨在提高钢铁产业的经济效益,促进钢铁焦化厂的可持续发展。
关键词:钢铁焦化厂;节能降耗;干熄焦技术;节能化管理中图分类号:TQ520.5 文献标识码:A DOI :10.15913/ki.kjycx.2016.23.109 在钢铁的生产过程中,焦化环节对煤炭、水、电、煤气等能源的消耗极大,属于能源消耗大户。
焦化工序的成本占钢材生产总成本的比例也较大。
钢铁焦化环节具有生产二次能源的优势,在发展钢铁产业的过程中,应着力提高煤炭资源的利用效率,提升焦炭产出率。
合理利用炼焦过程中产生的煤气、焦油等副产品,实现节能降耗的目的。
由于焦化厂的污染物排放量高,排放出的废气、废水等污染物严重影响了自然环境,受国家政策影响,坚持发展资源节约型、环境友好型社会,钢铁焦化厂实施节能降耗措施势在必行。
1 红焦显热回收在钢铁焦化厂的生产过程中,干熄焦技术应用最为广泛。
该技术减少了蒸汽的排放量,进而降低了氰化物、焦炭粉尘等污染物的排放量,替代了传统的水熄焦技术,有利于保护生态环境,节约能源,提高焦炭质量,是我国重点推广的节能降耗技术。
干熄焦技术在钢铁炼焦过程中会产生适用于发电的动力蒸汽,降低了发电对动力煤的需求,在产生相同发电量的情况下,大大降低了燃煤发电对环境造成的破坏。
在节能减排政策的支持下,钢铁焦化厂将配备干法熄焦装置,并提高其使用效率。
焦油加工工艺改进节能降耗说明

关于工艺改进的说明介休昌盛煤气化有限公司2X15万吨焦油加工项目所采用的工艺是目前国内焦油加工最新技术,与传统工艺相比优势非常突出。
目前,该工艺已经在磁县鑫宝化工有限公司60万吨焦油加工项目及山东宝舜化工有限公司2X30万吨焦油加工项目中运行使用,总体效果很好。
该工艺的主要研发设计人员经生产运行现场实地调研,并与以上两单位现场的工艺技术人员经过充分的技术交流,把该工艺在生产运行中存在不完善之处又进行了改进,使得该工艺更合理。
主要改进的内容如下。
1、在焦油蒸馏的真空系统前增加了不凝气的洗涤装置,有效地降低了不凝气中的升华萘含量,避免了设备管道的堵塞。
2、在工业萘回流槽前增加了工业萘汽化冷却器。
把工业萘从160℃降低到110℃,避免了升华萘堵塞管道。
3、改质沥青真空系统的不凝气冷却器,采用降膜冷却器,避免了闪蒸油堵塞管道。
改进后的工艺优势明显,主要体现在如下几方面:a、在综合能耗方面,比传统工艺低40%。
首先,运用系统工程技术,重新定位各子系统的作用,重新梳理各子系统之间的关系,充分发挥各个子系统的协同作用,取消了子系统之间的重复性工作、克服了各子系统之间的内耗,从而使得整个系统的运行更合理高效,有效地降低了能耗;其次,将新的减压蒸馏技术及新型塔盘技术应用于焦油蒸馏、将差压蒸馏技术应用于工业萘蒸馏等子系统、将改质沥青使用管式炉等新技术,使得各子系统的能耗大大降低;另外,将高中温度的物料所带热量充分循环利用,节省了大量煤气、蒸汽等消耗,同时也节省了大量的循环水和新鲜水。
传统工艺加工一吨焦油的煤气单耗为100m3/t,而新工艺的煤气单耗为40m3/t,节能减排效果非常突出。
新工艺加工60万吨/年焦油的循环水用量只相当于传统工艺加工15万吨/年焦油的循环水用量及新鲜水补充量。
加工一吨焦油的蒸汽单耗也比传统工艺低50%多。
b、在环保方面,由于采用管式炉烟道气中的二氧化碳代替硫酸分解酚纳工艺,既减少了二氧化碳的排放量,又减少了硫酸钠废水的产生;同时,分解后产生的碳酸钠废水经苛化处理,生成碳酸钙和氢氧化钠稀溶液,氢氧化钠稀溶液再回到洗涤工段循环使用,既节省了氢氧化钠的用量,又减大大少了废水的产生。
焦化厂节能降耗方案

焦化厂节能降耗方案焦化厂作为重工业行业,能源消耗较大,排放污染物也较为严重,所以要想实现节能降耗是非常重要的。
下面是我对焦化厂节能降耗方案的一些建议。
1.优化生产工艺在焦化生产过程中,可以采用先进的焦炉技术,如热风炉、热顶炉等,使其燃烧效率更高。
此外,合理安排焦炉炉型结构,使煤气产生更加充分利用,减少能源的浪费。
另外,在配煤时合理选用合适的煤种,以降低焦化过程中的能源消耗。
2.推广余热回收利用技术焦化过程会产生大量的余热,如果能够将这些余热有效地回收利用,将能够显著地降低焦化厂的能源消耗。
可以利用余热发电、余热利用等技术,将余热转化为电力或热能供应给生产设备或周边区域。
此外,还可以将余热用于再生焦炉燃烧,提高焦化炉燃烧效率。
3.环保设施改造焦化过程中会产生大量的污水和废气,所以要想降低能源消耗,还需要对环保设施进行改造。
可以采用先进的污水处理技术,如生物法、反渗透等,将污水处理后再利用或排放。
同时,对废气进行高效治理,如安装炉顶封罩、布袋除尘器等,减少废气的排放。
4.强化能源管理建立完善的能源管理体系,制定相应的能源管理制度和标准,加强对能源的监测和分析。
通过对能源的监测和分析,找出能源消耗的主要问题和瓶颈,然后制定相应的改善措施。
此外,培养员工的节能意识,通过培训和教育等方式提高员工对能源节约的认识和重视程度。
5.加强能源技术研发焦化厂要想实现节能降耗,还需要加大对能源技术的研发和引进力度。
可以与科研院所、高校等合作,开展能源技术研发工作,推动能源技术的创新和应用。
可以开发制造更加节能高效的设备,引进先进的能源管理系统,提高能源利用效率。
综上所述,焦化厂节能降耗方案包括优化生产工艺、推广余热回收利用技术、环保设施改造、强化能源管理和加强能源技术研发等。
只有综合多种手段,全面提高能源利用效率,才能够实现焦化厂的节能降耗目标,减少能源消耗和环境污染。
焦化厂节能降耗方案

焦化厂年度节能降耗管控方案当前焦化行业市场低迷,生产成本相对较高,公司运营面临巨大压力。
为应对市场不利局面,积极响应总公司开展节能降耗、降成本会议的精神要求,炼焦公司结合自身实际,本着“严、细、实、恒”的原则深化成本管理工作,在我公司范围内大力开展节能降耗、成本管控的工作,做到有目标、有考核、有措施、有落实、有改进,真正将炼焦公司的节能降耗、降本增效工作落到实处,特制定本方案。
一、指导思想根据炼焦公司成本管控的精神,以“降成本、增效益、强管理”为主题,以群众性合理化建议活动为载体,充分调动职工群众的积极性和创造性,全力打一场“降本增效”的攻坚战。
二、主要目标根据公司2012年度实际成本费用等情况,对2012年度目标成本费用指标进行分解、落实责任到人,全方位、全环节开展节能降耗,从技术上、管理上降成本,以保证公司年度各项生产经营目标的实现,为公司创造更多的利润。
三、领导机构:组长:副组长:成员:四、具体措施:在我们现阶段的生产中,由于市场原因,造成我们的利润大幅降低,因此,我们必须改变现场粗放的管控方式,各点工艺指标,煤焦比控制,煤焦耗热量化产回收率,筛焦粘度,水份等要对各环节控制点做好细化管控工作。
(一)备煤工段重点控制工艺:煤焦比:保证焦炭单炉产量的前提下,尽可能的使用较少的煤,确保煤焦比不超1.25,同时,在确保焦炭质量的前提下,优化各单种煤配比,降低精煤成本。
煤场管理:单种煤之间必须有3m以上的间隔,杜绝混煤,避免由于混煤造成的成本增加,出现混煤对当班班长考核200元。
配煤管理:各单种煤必须按计划配比进行配入,杜绝出现少配或多配,皮带称严禁出现断料现象,出现断料配煤室要及时打铃,监护人员必须监护好皮带称下料情况,出现上述情况对相关负责人予以最低100元罚款。
焦粉管理:焦粉必须保证配入量,烘干机和球磨机禁止空运转。
(二)炼焦工段:1、使用合理的加热制度,降低煤气消耗量,空气过剩系数保持在1.15---1.3之间,大烟囱禁止出现冒烟现象,每冒一次考核当班班长20元。
- 1、下载文档前请自行甄别文档内容的完整性,平台不提供额外的编辑、内容补充、找答案等附加服务。
- 2、"仅部分预览"的文档,不可在线预览部分如存在完整性等问题,可反馈申请退款(可完整预览的文档不适用该条件!)。
- 3、如文档侵犯您的权益,请联系客服反馈,我们会尽快为您处理(人工客服工作时间:9:00-18:30)。
节能降耗技术在焦化工艺中的应用
摘要:由于国家工业转型的迫切要求,节能降耗技术也引起高度重视,研究节能降耗技术在焦化工艺中的应用,分析焦化工艺、焦化节能技术、节能技术应用、相关节能措施等,为我国焦化节能提供一点建议。
关键词:焦化工艺;节能技术;应用;措施
能源消耗不仅为环境带来了巨大压力也为社会发展带了负担,特别是对于一些不可再生的能源,诸如煤炭、钢铁等,在焦化技术中,对煤炭的消耗尤其突出。
面对炼焦煤价格持续攀升、焦炭质量越来越高但焦炭价格较低的形势,焦化企业生产成本压力越来越大。
因此,焦化企业或与之有关的生产行业想要长久生存下去,得到持续性发展,节能降耗刻不容缓。
1、焦化工艺
1.1焦化工序在铁前系统的能源中心位置
焦化厂在钢铁行业是能耗大户也是节能的主力,被行业誉为“二次能源制造中心”能源利用潜力巨大。
我国正处在由钢铁大国向钢铁强国迈进的关键时期,在焦化工序努力实现焦炉大型化、工艺现代化同时,焦化厂在改造和新厂设计时节能技术的应用和开发不能忽视,然而,焦化工艺是一个复杂化学反应、高能耗铁前工序,也是能源节省的关键环节,因此,焦化节能降耗已经成为各钢铁行业普遍认同的节能关键制点。
1.2 焦炉的热量平衡
焦化工艺是一个能源转化的过程,它是将洗精煤转化成焦炭、煤气和一些化学副产品,这一过程中会产生大量的热量,其中焦炉炉体的散热占10%左右,炽热的焦炭带走的显热占40%,荒煤气带走30%的显热,烟道废气带走20%的显热。
因为焦化工艺这一能源转换特性,所以在焦化生产过程中,不仅要满足产品需求还要追求能源高效转化率,降低能耗水平。
1.3综合利用焦炉煤气和高炉煤气
焦炉和高炉煤气是整个钢铁行业重要的能源,也是铁前系统重要的二次源,
它们的合理使用对工序能耗起到举足轻重的作用。
焦化本身会用到数量巨大的煤气来加热管式炉、焦炉,为了向轧钢等后部工序提供优质煤气,焦化工序应尽量多使用高炉煤气,减少高炉煤气的放散。
2、节能降耗技术
2.1 煤调湿
焦化过程中不可避免面的要消耗大量的煤炭资源,因此,节能第一步便是从煤资源消耗入手。
减少装入煤水分是降低炼焦过程耗热量的一个重要举措。
炼焦煤中的水进入焦炉,既需要消耗加热煤气将之蒸发去除,同时还产生大量难处理的含酚废水。
适当降低和稳定配煤水分,不仅是节能降耗的需要,也是环保的需要、焦炉正常生产的需要。
煤调湿技术是减少和稳定装入煤水分的代表技术。
中煤调湿简称CMC,指利用焦化厂荒煤气、废气余热或干熄焦蒸汽等将炼焦配合煤水分在装炉前加热使其水分降到5%~6%,然后装入焦炉炼焦的技术。
2.1.1 煤调湿技术具有非常显著的效果
(1)焦炉生产能力提高。
CMC 技术会使单孔炭化室装煤量增加,提高焦炭产量,同时还能缩短结焦时间。
(2)降低炼焦耗热
CMC 采用烟道废热或CDQ 发电后尾蒸汽,既可以节约能源又可以利用废弃的能源。
达到充分利用焦炉余热,降低工序能耗目的。
(3)保护环境
这一过程会减少煤气冷却用水、荒煤气中的水蒸气、系统功耗、排污量,对环境保护具有重要作用。
煤料水分降低4%~5%,可减少1/3 的剩余氨水量,减轻废水处理的生产负荷。
平均每吨入炉煤可减少约38.5 kg 的CO2排放量。
2.2 红焦显热回收
干熄焦是目前应用最广、最成熟的技术就是,也是国家重点节能技术。
干熄焦技术将减少大量蒸汽排向大气,也相应减少了蒸汽中携带的大量酚、氰化物、硫化氰、氨以及焦炭粉尘等污染物,改善大气环境。
干熄焦不仅可以提高焦炭质量,还能产生大量动力蒸汽。
并且,与煤发电相比,可以更好的避免环境污染,1 万吨配套的干熄焦产生的蒸汽如用于发电,则相当于每年减少约0.1 万吨燃煤发电对大气的影响。
干熄焦技术对焦化企业技能降耗具有非常重要的意义,不仅能够为企业节省大量能源,实现企业经济效益,还能促进企业发展绿色工业,降低环境污染。
2.3 荒煤气显热回收
焦炉荒煤气带出热量占炼焦炉热能支出的30%,这个数字可谓是非常巨大的,在热回收问题上,我国多年以来难以实现进展性突破,几乎没有成功案例。
但是,今年,荒煤气显热回收技术却在这一问题上有了突破,荒煤气显热回收技术装备开发难度大,但节能潜力显著还是值得下工夫的,一座焦炉完成工业化应
用,装置荒煤气显热利用效率达32%,寿命预计可达8 年。
目前来看,这一技术能使焦炉工序能耗降低10.16kg/t;吨焦产0.6 MPa 蒸汽109 kg。
这将能大幅降低焦炉工序能耗。
3、节能降耗技术的应用
3.1汽化上升管应用
汽化上升管利用650~700℃焦炉荒煤气热量来加热带夹套的上升管中的软化水产生蒸汽的余热回收利用技术。
该项技术上世纪广泛在各大钢铁公司得到应用,每小时可发生0.5MPa 饱和蒸汽,可以回收干煤炼焦过程中335 489kJ/t 的荒煤气热能,可将荒煤气所带热能70%回收。
3.2煤调湿技术开发
利用焦炉烟道废气余热、干熄焦发电机组的背压汽的综合热量、上升管换煤气的余热对装炉煤进行加热干燥,降低煤中的水分,即利用焦炉的余热对焦炉入炉煤水分进行预热调湿,利用焦炉余热能进行煤料调湿,可以将装炉煤水分由10%控制在5%~6%,它可以大大的降低炼焦工序能耗,同时还由于装炉煤含水量降低,提高了焦炉装炉煤的堆密度,提高了焦炭质量和产量,为企业带来巨大的经济效益。
3.3 热管在焦炉废气回收余热中的利用
热管换热器具有温度均匀、传递热效率高、结构简单的特点。
热管是一个封闭的管段,内装有可汽化的液体和毛细吸液芯,并抽空管段内的不凝性气体。
热管工作时利用管内工质的蒸发-冷凝循环来达到传输热量的目的。
热管可以在很小的温差下传输热、冷源之间的热量。
热管换热器在我公司一炼焦车间烟道气余热回收成功应用,并利用回收的余热通过换热器将除盐水加热至104℃,送往各系统使用。
在焦炉废气的热量也可以利用该项新技术回收焦炉的余热或者焦化生产中回收循环氨水中剩余氨水的热量等。
4、节能措施
4.1 提高炼焦煤使用效率
为减少露天煤场大风暴雨导致炼焦煤流失以及降低煤场炼焦煤变质情况,可以开展煤场均质化管理以及降低煤场库存等攻关项目。
焦化厂对煤塔锥形斗嘴进行改造,定期对煤塔组织清理,有效避免因长期挂料,洗精煤的变质,稳定煤质,改善焦炭质量。
4.2降低吨焦电耗
积极推广能源合同管理,对干熄焦循环风机进行变频改造,同时,通过降低
皮带系统空转率进行攻关、改造优化各类泵组、恢复全厂除尘风机变频调速等措施,降低吨焦电耗。
4.3提高堆密度,稳定单炉产量
炼焦车间对顶装煤车螺旋给料器装煤孔不同的装煤时间以及给煤圈数等参数进行了调整;同时还可以对平煤杆进行改造,如平煤杆加长以及在平煤杆前段安装滚轴等装置,能有效防止炭化室装煤缺角、平煤不通等现象的发生,结合单种炼焦煤性质,研究不同配比条件下,小焦炉实验以及工业实验产量最大化的粒度分布。
通过这些方法,可以很大程度上保证炭化室煤装满、装匀、装实、装平。
结语
能源大量消耗和环境严重污染的粗放型经济增长模式,影响全面建设小康社会总目标的实现,在我国工业转型的关键时期,炼焦企业充分重视节能降耗工作,在产业结构调整中要依靠先进节能技术来降低焦化工序的原料、燃料及动力的消耗,使企业降低炼焦的工序成本。
做好焦化节能降耗工作对国家、对企业来说都是极具战略意义,节能降耗必须引起每个焦化工作员工的高度重视。
参考资料
[1] 杨晓东等.钢铁工业能源消耗和二次能源利用途径和对策[J].钢铁,2000,35(12):64~68.
[2] 张京萍. 武钢炼焦荒煤气余热回收利用率达32%. 世界金属导报,2012- 05- 23
[3] 李震.我国钢铁行业节能降耗技术现状和发展趋势[J].鞍钢技术2005,46(5):5~9.。