控制图通用图选控图
控制图控制图
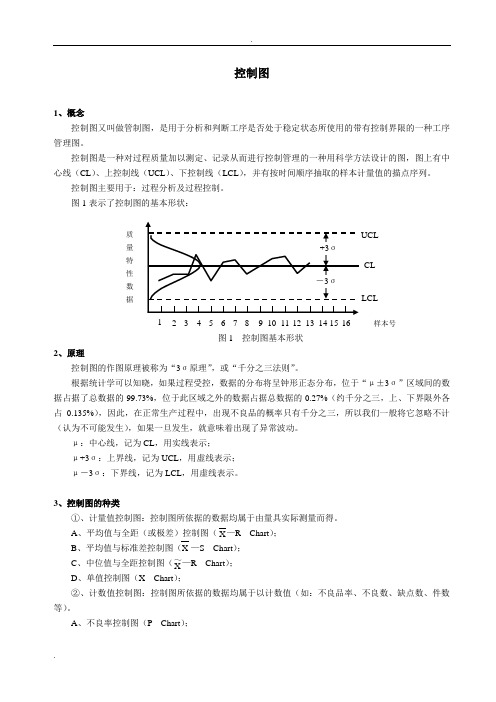
控制图1、概念控制图又叫做管制图,是用于分析和判断工序是否处于稳定状态所使用的带有控制界限的一种工序管理图。
控制图是一种对过程质量加以测定、记录从而进行控制管理的一种用科学方法设计的图,图上有中心线(CL )、上控制线(UCL )、下控制线(LCL ),并有按时间顺序抽取的样本计量值的描点序列。
控制图主要用于:过程分析及过程控制。
图1表示了控制图的基本形状:2、原理控制图的作图原理被称为“3σ原理”,或“千分之三法则”。
根据统计学可以知晓,如果过程受控,数据的分布将呈钟形正态分布,位于“μ±3σ”区域间的数据占据了总数据的99.73%,位于此区域之外的数据占据总数据的0.27%(约千分之三,上、下界限外各占0.135%),因此,在正常生产过程中,出现不良品的概率只有千分之三,所以我们一般将它忽略不计(认为不可能发生),如果一旦发生,就意味着出现了异常波动。
μ:中心线,记为CL ,用实线表示; μ+3σ:上界线,记为UCL ,用虚线表示; μ-3σ:下界线,记为LCL ,用虚线表示。
3、控制图的种类①、计量值控制图:控制图所依据的数据均属于由量具实际测量而得。
A R Chart ); B S Chart );C Chart );D 、单值控制图(X Chart );②、计数值控制图:控制图所依据的数据均属于以计数值(如:不良品率、不良数、缺点数、件数等)。
A 、不良率控制图(P Chart );质 量 特 性 数 据B、不良数控制图(Pn Chart);C、缺点数控制图(C Chart);D、单位缺点数控制图(U Chart)。
4、控制图的用途根据控制图在实际生产过程中的运用,可以将其分为分析用控制图、控制用控制图:①、分析用控制图(先有数据,后有控制界限):用于制程品质分析用,如:决定方针、制程解析、制程能力研究、制程管制之准备。
分析用控制图的主要目的是:(1)分析生产过程是否处于稳态。
控制图
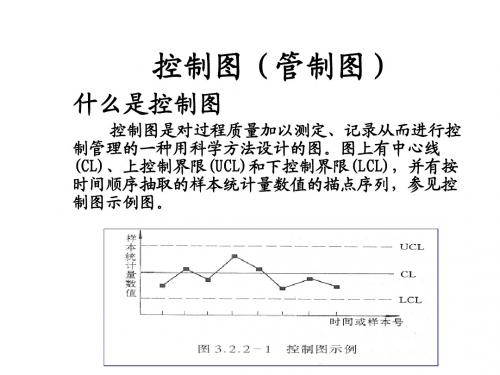
176 175 173 170 169 173 7
171 172 173 174 175 173 4
172 173 174 176 175 174 4
174 173 170 171 172 172 4
176 174 172 169 170 172 7
173 172 170 171 173 172 3
2-1
2-2 计算控制限 计算控制限是为了显示仅存在变差的普通原因时子组的均 值和极差的变化和范围。 值和极差的变化和范围。控制限是由子组的样本容量以及反 映在极差上的子组内的变差的量来决定的。 映在极差上的子组内的变差的量来决定的。 计算公式: 计算公式: UCLR=D4 UCLx=X+ A2R UCLR=D4R LCLx=XLCLR=D3 LCLx=X- A2R LCLR=D3R
控制图(管制图) 控制图(管制图)
什么是控制图
控制图是对过程质量加以测定、 控制图是对过程质量加以测定、记录从而进行控 制管理的一种用科学方法设计的图。 制管理的一种用科学方法设计的图。图上有中心线 (CL)、上控制界限(UCL)和下控制界限(LCL) (UCL)和下控制界限(LCL), (CL)、上控制界限(UCL)和下控制界限(LCL),并有按 时间顺序抽取的样本统计量数值的描点序列, 时间顺序抽取的样本统计量数值的描点序列,参见控 制图示例图。 制图示例图。
的产品进行监测的子组频率可以是每班2 的产品进行监测的子组频率可以是每班2次,或一小时一次等。 或一小时一次等。 子组数:子组越多,变差越有机会出现。一般为25 25组 1-1-3 子组数:子组越多,变差越有机会出现。一般为25组,首次使用管 制图选用35 组数据,以便调整。 制图选用35 组数据,以便调整。 见下图) 1-2 建立控制图及记录原始数据 (见下图)
统计过程控制之通用控制图
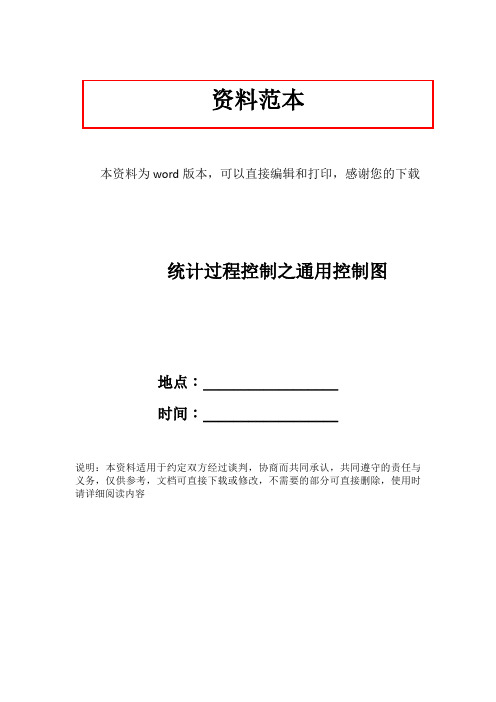
资料范本本资料为word版本,可以直接编辑和打印,感谢您的下载统计过程控制之通用控制图地点:__________________时间:__________________说明:本资料适用于约定双方经过谈判,协商而共同承认,共同遵守的责任与义务,仅供参考,文档可直接下载或修改,不需要的部分可直接删除,使用时请详细阅读内容统计过程控制(SPC)与休哈特控制图(三) 第六章通用控制图世界各国的控制图大多采用3σ方式。
在应用控制图时,需要计算控制图的控制界限并根据实测数据计算出所控制的统计量,在控制图中描点。
这两项都需要一定的工作量,尤其是p图与pn图、u图与c图,由于控制界限计算公式中含有样本大小n,控制界线随着n的变化而呈凹凸状,作图十分不便,也难于判稳、判异。
若n变化不大,虽可用n的平均数n代替n,但不精确,当点子接近控制界限时有误报与漏报异常的可能。
1981年我国张公绪教授与阎育苏教授提出的通用控制图解决了上述问题。
在通用控制图上,控制界线是直线,而且判断异常的结果也是精确的。
通用控制图已于1986年发布为国家标准GB6381。
通用控制图主要包括两个内容:标准变换和直接打(描)点法。
一、标准变换与通用图所谓随机变量的标准变换是指经过变换后随机变量的平均值变成0、方差变成1的变换,即:变换后的随机变量=(随机变量一μ)/σ这是可以理解的。
随机变量的取值减去其平均值后的平均值应为0;其次,分母为标准差,也就是说用标准差作尺度,这样,变换后的标准差应为1。
现在,对3σ控制界限的一般公式UCL=μ+3σCL=μLCL=μ-3σ进行标准变换,于是得到UCLt=(UCL-μ)/σ=3CLt=(UCL-μ)/σLCLt=(UCL+μ)/σ=3式中,下标t表示标准变换后,也表示通用的“通"。
这样,任何3σ控制图都统一变换成式(3.6. 1一2)的控制图,称为通用控制图。
通用图的优点是控制界限统一成3,0,-3,可以事先印好,简化控制图,节省管理费用,在图上容易判断稳态和判断异常。
控制图的原理及应用图解
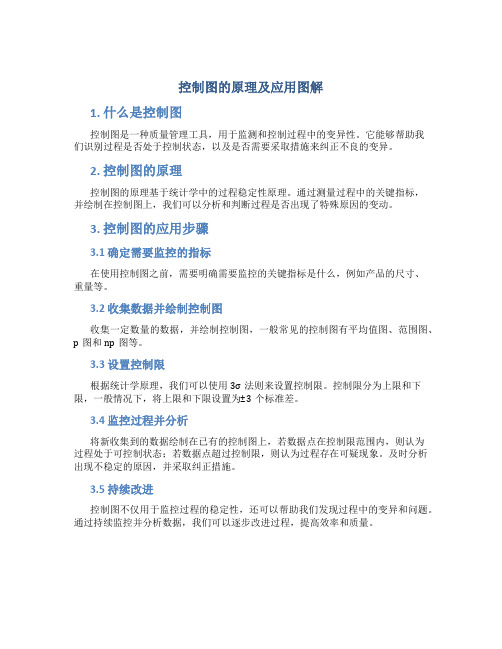
控制图的原理及应用图解1. 什么是控制图控制图是一种质量管理工具,用于监测和控制过程中的变异性。
它能够帮助我们识别过程是否处于控制状态,以及是否需要采取措施来纠正不良的变异。
2. 控制图的原理控制图的原理基于统计学中的过程稳定性原理。
通过测量过程中的关键指标,并绘制在控制图上,我们可以分析和判断过程是否出现了特殊原因的变动。
3. 控制图的应用步骤3.1 确定需要监控的指标在使用控制图之前,需要明确需要监控的关键指标是什么,例如产品的尺寸、重量等。
3.2 收集数据并绘制控制图收集一定数量的数据,并绘制控制图,一般常见的控制图有平均值图、范围图、p图和np图等。
3.3 设置控制限根据统计学原理,我们可以使用3σ法则来设置控制限。
控制限分为上限和下限,一般情况下,将上限和下限设置为±3个标准差。
3.4 监控过程并分析将新收集到的数据绘制在已有的控制图上,若数据点在控制限范围内,则认为过程处于可控制状态;若数据点超过控制限,则认为过程存在可疑现象。
及时分析出现不稳定的原因,并采取纠正措施。
3.5 持续改进控制图不仅用于监控过程的稳定性,还可以帮助我们发现过程中的变异和问题。
通过持续监控并分析数据,我们可以逐步改进过程,提高效率和质量。
4. 控制图的应用场景4.1 制造业在制造业中,控制图可以帮助企业监测生产线上的关键指标,例如产品尺寸、重量等。
通过控制图的分析,所产生的数据可以作为制造流程改进的依据。
4.2 服务业在服务业中,控制图可以用于监控服务质量。
例如餐饮行业使用控制图来监控食品加工过程中的关键环节,以确保食品质量符合标准。
4.3 医疗行业在医疗行业中,控制图可以用于监控医疗流程的关键环节。
例如手术室使用控制图来监控手术过程中的关键指标,以确保手术质量和安全。
4.4 金融行业在金融行业中,控制图可以用于监控交易过程中的关键指标,例如交易时间、成功率等。
通过控制图的应用,可以帮助金融机构提高交易效率和降低风险。
什么是控制图
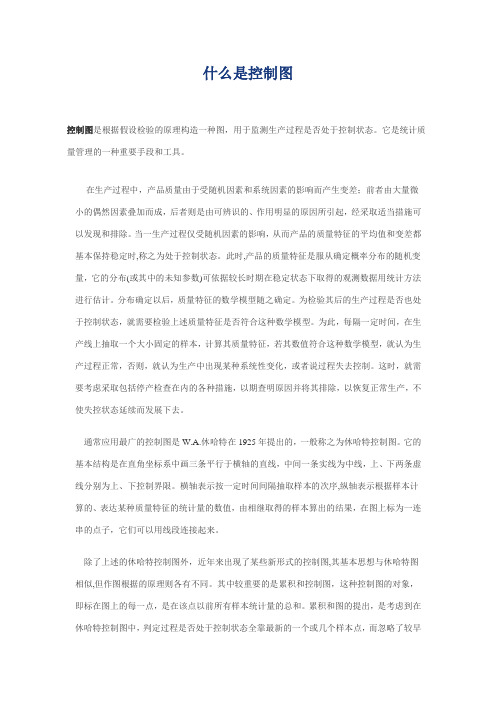
什么是控制图控制图是根据假设检验的原理构造一种图,用于监测生产过程是否处于控制状态。
它是统计质量管理的一种重要手段和工具。
在生产过程中,产品质量由于受随机因素和系统因素的影响而产生变差;前者由大量微小的偶然因素叠加而成,后者则是由可辨识的、作用明显的原因所引起,经采取适当措施可以发现和排除。
当一生产过程仅受随机因素的影响,从而产品的质量特征的平均值和变差都基本保持稳定时,称之为处于控制状态。
此时,产品的质量特征是服从确定概率分布的随机变量,它的分布(或其中的未知参数)可依据较长时期在稳定状态下取得的观测数据用统计方法进行估计。
分布确定以后,质量特征的数学模型随之确定。
为检验其后的生产过程是否也处于控制状态,就需要检验上述质量特征是否符合这种数学模型。
为此,每隔一定时间,在生产线上抽取一个大小固定的样本,计算其质量特征,若其数值符合这种数学模型,就认为生产过程正常,否则,就认为生产中出现某种系统性变化,或者说过程失去控制。
这时,就需要考虑采取包括停产检查在内的各种措施,以期查明原因并将其排除,以恢复正常生产,不使失控状态延续而发展下去。
通常应用最广的控制图是W.A.休哈特在1925年提出的,一般称之为休哈特控制图。
它的基本结构是在直角坐标系中画三条平行于横轴的直线,中间一条实线为中线,上、下两条虚线分别为上、下控制界限。
横轴表示按一定时间间隔抽取样本的次序,纵轴表示根据样本计算的、表达某种质量特征的统计量的数值,由相继取得的样本算出的结果,在图上标为一连串的点子,它们可以用线段连接起来。
除了上述的休哈特控制图外,近年来出现了某些新形式的控制图,其基本思想与休哈特图相似,但作图根据的原理则各有不同。
其中较重要的是累积和控制图,这种控制图的对象,即标在图上的每一点,是在该点以前所有样本统计量的总和。
累积和图的提出,是考虑到在休哈特控制图中,判定过程是否处于控制状态全靠最新的一个或几个样本点,而忽略了较早的样本值中所包含的信息。
Control Chart(控制图)

~ X 图 用
M3A2 1.880 1.187 0.796 0.691 0.549 0.509 0.432 0.412 0.363
控制图的类型
按用途划分
分析用控制图。用间隔取样的方法获得数据。依据 分析用控制图 收集的数据计算控制线、作出控制图 ,并将数据在 控制图上打点,以分析工序是否处于稳定状态,若 发现异常,寻找原因,采取措施,使工序处于稳定 状态;若工序稳定,则进入正常工序控制。 控制用控制图。当判断工序处于稳定状态后,用于 控制用控制图 控制工序用的控制图。操作工人按规定的取样方式 获得数据,通过打点观察,控制异常因素的出现。
控制界限的确定原理—3 控制界限的确定原理 3σ原理
确定方法 休哈特控制图控制界限是以3σ原理确定的。即以质 量特性统计量的均值作为控制中线CL; 在距均值 ±3σ处作控制上、下线。由3σ原理确定的控制图可 以在最经济的条件下达到保证 生产过程稳定的目的。
3σ原理 原理
设工序处于正常状态时,质量特性总体的均值为0, 标准偏差 为σ,设三条控制线的位置分别为CL= 0 、 UCL= 0 +kσ,LCL= 0 -kσ。
p= pn n pn =
∑(p )
i =1
k
n i
P图 C图
计算各组不合格品率pi 计算各样本的平均缺陷数 c
pi =
( pn )i
k
c=
U图 计算各样本的单位缺陷数ui
∑c
i =1
k
ni
i
c ui = i ni
k
绘制程序
作分析用控制图并判断工序是否处于稳定状态
在坐标图上画出三条控制线,控制中线一般以细实 线表示,控制上下线以虚线表示。 将预备数据各样本的参数值在控制图中打点。 根据本节介绍的控制图的判断规则判断工序状态是 否稳定,若判断工序状态不稳定,应查明原因,消 除不稳定因素,重新收集预备数据,直至得 到稳定 状态下分析用控制图;若判断工序处于稳定状态, 继续以下程序。
控制图的原理
控制图的原理一.控制图的原理-波动分布控制图观点认为:(1)当过程仅受随机因素影响时,过程处于统计控制状态(简称受控状态);由于过程波动具有统计规律性,当过程受控时,过程特性一般服从稳定的随机分布;(2)当过程中存在系统因素的影响时,过程处于统计失控状态(简称失控状态)。
而失控时,过程分布将发生改变。
SPC正是利用过程波动的统计规律性对过程进行分析控制的。
因而,它强调过程在受控和有能力的状态下运行,从而使产品和服务稳定地满足顾客的要求。
二.控制图的原理-统计受控状态是生产过程追求的目标,此时,对产品的质量是有把握的。
控制图即是用来监测生产过程状态的一种有效工具。
控制图的统计学原理,令W为度量某个质量特性的统计样本。
假定W的均值为μ,而W 的标准差为σ。
于是,中心线、上控制限和下控制限分别为UCL=μ+KσCL=μLCL=μ-Kσ式中,K为中心线与控制界限之间的标准差倍数,Kσ表示间隔宽度。
正常情况下点子分布是正态的,落在控制界限之内的概率远大于落在控制界限之外的概率。
反之,若点子落在控制界限之外,可能是属于正常情况下的小概率事件发生,也可能是过程异常发生,相对来讲,后者发生的概率要大得多。
因此,我们宁可以为后者情况发生,这正是控制图的统计学原理。
点子落在控制界限之内是否一定处于稳态?点子落在控制界线之外是否一定出现异常?这两个问题的回答都是否定的。
更为科学的判断应根据概率统计方法对过程进行定量分析,精确计处出状态的概率值之后再进行过程状态判断。
三.控制图的原理-分类1各控制图用途:均值-极差控制图:是最常用、最基本的控制图,它用于控制对象为长度、重量、强度、纯度、时间和生产量等计量值的场合。
均值-标准差控制图:次图与上图类似,极差计算简便,故R图得到广泛应用,但当样本大小或0>10或12时,应用极差估计总体标准差的效率减低,最好应用S图代替R图。
中位数-极差控制图:由于中位数的计算比均值简单,所以多用于现场需要把测定数据直接记入控制图进行管理的场合。
控制图
P管制圖如下:
0.6 0.5
0.52 0.48
0.4
不合格率
0.36
0.3
0.32 0.28 0.3 0.26 0.24 0.24 0.2 0.16 0.1 0.1 0.14 0.18 0.12 0.1 0.26 0.22 0.2 0.3 0.3
0.34
UCL=0.41
0.24 0.2 0.15 0.12
七大手法
—控制图 控制图
2010年03月18日
七、控制图 从每日生产的生产线中所测得的零乱数据中, 找出经常发生和偶然发生事故的数据,以便帮 助找出问题原因,这就是非依靠管制图不可. 管制图分为两大类,计量值管制图和计数值管 制图 主要功能,是能够看出数据随时间变化而发 生变化的情形,从折线的高低就可以知道品 质的状况。 如果在图上再加上中心线及3δ的上下管制界 线即成为控制图。
技术质量部
控制图的判別
控制状态, 指制程安定,控制状态也称安定状态.我们通 过對制程的某种特性值收集数据,將其绘在控制图上,由 控制图來观察制程的状态.再判定制程是否处于控制状 态,可利用以下基准: 1. 控制图的点沒有逸出界外. 2. 点的排列方法沒有习性,呈随机現象. 在正常控制的状态下,控制图上的点子应是随机分布,在 中心线的上下方約有同数的点,以中心线近旁为最多,离 中心线越远点越少,且不可能显示有规则性或系統性的 現象.
CL
LCL
UCL
复习题
1.统计本工序2月每天用水量,并根据统计数据绘 制控制图 2.根据下列数据绘制控制图
技术质量部
技术质量部
+3
( P为平均不合格率,n为样本数)
例: 某厂生产的包裝袋,检验其底部是否有破损 即包裝为不合格品,取30個样本,每个样本数据 50格,这些样本是在机器每天三班制的连续工 作每半小时取一次而得.
控制图
控制图控制图(Control Chart )又称管理图、休哈特图,是一种将显著性统计原理应用于控制生产过程的图形方法。
控制图是区分过程中正常波动和一场波动,并判断过程是否处于控制状态的一种工具。
正常波动是由普通原因(偶然因素、随机因素)造成的,这些因素在生产过程中大量存在,对产品质量经常发生影响,但它造成的质量波动往往比较小,在生产过程中是允许存在的,如材料成分的微小变化、设备的轻微震动、刃具的正常磨损、夹具的弹性变型等;一场波动是由特殊原因(异常因素、系统因素造成的。
这些因素在生产过程中并不大量存在,对产品质量也不经常发生影响,一旦存在,它对产品质量的影响就比较显著,如机器设备带病运转,操作者违章操作等。
控制图的控制界限就是用来区分正常波动和异常波动的。
1、控制图的基本结构1)以随时间推移而变动着的样品号为横坐标,以质量特性值或其统计量为纵坐标; 2)三条具有统计意义的控制线:上控制线UCL 、中心线CL 、下控制线LCL ; 3)一条质量特性值或其统计量的波动曲线。
2、控制图原理的解释 第一种解释:“点出界就判异”小概率事件原理:小概率事件实际上不发生,若发生即判异常。
控制图就是统计假设检验的图上作业法。
第二种解释:“抓异因,弃偶因”控制限就是区分偶然波动与异常波动的科学界限。
休哈特控制图的实质就是区分偶然因素与异常因素的。
UCLLCL样本统计量数值x 或R14 15 16 17 18按用途分类1)分析用控制图——用于质量和过程分析,研究工序或设备状态;或者确定某一“未知的”工序是否处于控制状态;2)控制用控制图——用于实际的生产质量控制,可及时的发现生产异常情况;或者确定某一“已知的”工序是否处于控制状态。
4、R X -图的绘制1)确定控制对象(统计量)一般应选择技术上最重要的、能以数字表示的、容易测定并对过程易采取措施的、大家理解并同意的关键质量特性进行控制。
2)选择控制图对于计量数据而言,R X -控制图是最常用最基本的。
控制图(Control chart)
Page-4
Page~4
一.管制图的概念:
2.管制图的定义(B):
基本上管制图功能有三:
1)决定制造工程所可能达到之目标或标准; 2)被用作为达到目标之工具; 3)可藉此判定是否已达到目标.
化专业为执行,使执行获收益
Page-5
Page~5
一.管制图的概念:
3.管制图的种类(A)
1)计量值管制图: 制作管制图所依据之数据,均属于由量具实际量测
Page-35
Page~35
三.管制图的看法:
2. 非管制状态的判断(C):
+ 3 b
c
a Ucl
+ 2
e
+1
d
CL
仅以单边管制界限(+3σ)示例
化专业为执行,使执行获收益
Page-36
Page~36
三.管制图的看法:
化专业为执行,使执行获收益
Page-2
Page~2
一.管制图的概念:
1.管制图的历史(B): 3)美国政府于二次大战期间(1941~1942),制定了三种强制性之 战时规格,做为SQC的主要内涵;可以说美国能获得二次世界大 战之胜利,SQC之贡献极大; 4)后续英国、日本、台湾等都将统计品质管制引进工厂生产过 程中实施.
化专业为执行,使执行获收益
Page-26
Page~26
二.管制图的作法:
4.绘制管制图注意事项:
b. 双边规格 vs 单边规格(2/3): ※ 那么单边规格的产品特性如何使用管制图呢?在 产品规格或客户可接受的范围内可适当实施以下 的方法,将其转变为『双边对称』的规格,而后再 使用管制图;
化专业为执行,使执行获收益
- 1、下载文档前请自行甄别文档内容的完整性,平台不提供额外的编辑、内容补充、找答案等附加服务。
- 2、"仅部分预览"的文档,不可在线预览部分如存在完整性等问题,可反馈申请退款(可完整预览的文档不适用该条件!)。
- 3、如文档侵犯您的权益,请联系客服反馈,我们会尽快为您处理(人工客服工作时间:9:00-18:30)。
该工
某工序本身的加工质量,不包括上
序质 量
(以前)工序的影响。
分质量(本工序的质量) 总质量
上工序的影响(上影)
上工序
半
成
本工序
品
产 品
(上影) + (分质量) =(总质量)
3、两种质量诊断理论的思路
• 诊断——
将表征与标 准对照的 对比过程。
条件——
对比事
比较物
方标表
法准征
、;的
过
测
程
量
。
参
数
*§6
两种质量诊断理论—简介
? 胎教 ? 幼儿园
小学 ? ? 中学
大学 ?
病情 查体 手术准备 手术操作 术后护理
原材料
• 依质量诊断的思想,因素分三种:
总质量 (工序综合质量)
偶然因素、欲控异因、非控异因
分质量(工序固有质量)
•§6 两种质量诊断理论 (简介)
• (一) 两种质量诊断理论 • (二) 两种控制图的诊断 • (三) 两种过程能力指数的诊断
• 2、控制界限~规格线;
• 3、合理分组; • 4、经济性;
容差图
• 5、偏移大~小样本,偏移小~大样本;
• 6、一般不用大样本,而加警戒线和非随机原则;
• 7、n>10 不能用R图,应用S图。
•注意:
①如过程不合格品率很小,必须选样本量充分大。?
②实际工作中,样本量不可能无限制的增大。?
③若图上的点超出下控制界限,
例
• 步骤1 计算样本平均不合格品率
将现场数据直接变 换成通用图上的 数
据,在现场不需要进 行标准变换的方法。
• 步骤2 选择参数n的选择范围 50~105
• 步骤3 计算直接打点表
• 步骤4 应用直接打点表在通用图上描点
• 步骤5 观察判断。
通用图判异的准则: 1:点子出界或恰在控制界线上; 2:界内点子的排列非随机。
б
б
CLT=(CL—μ) / б= ( μ— μ)/ б
(LCL—μ) ( μ —3 б — μ)
LCLT = —————— = ————————
б
б
—3
§5 通用控制图
• 二、直接打点法 在通用图上画出7条直线 (k=0,±1,±2,±3) 将图分成8个区域。 (现场标杆数据—μ) k= —————————— б
现场标杆数据= μ+ kб
直接打点法
• 如果在现场数据中找 出与此对应的七个数 据(称之为现场标杆 数据),则在现场测 得所控制质量指标的 数据后,将它与这七 个现场标杆数据相比 较,便立刻知道应在
通用图上哪个区域中 描点。————
• 根据具体的控制图,得出 相应的均值、标准差,带 入上式,可列出直接打点 表,然后在通用图中打点。
(一) 两种质量诊断理 论
• 1、生产线的分析方法
工序1 工序2 •工序3 •工序4 »工序5
16
上下工序是相连的、相关的、相互影响的
• 2、两种质量
用户可感知 的
最终质量
(1)工序综合质量(总质量) 不但包括第n道工序的加工质量, 而且综合了所有以上各道工序的加工质量。
(2)工序固有质量(分质量)
= ——————— =K
√nP(1-P )
DK,n=np+K√np(1-p )
(K=-3,-2,-1,0,1,2,3)
D3,55=6.4 =55×0.0389+3√55×0.0389(1-0.0389)
Dn
50 55 60 65 70 75 80 85 90 95 100 105 K 3 6.0 6.4 6.8 7.2 7.6 7.9 8.3 8.7 9.0 9.3 9.7 10.0 2 4.7 5.0 5.3 5.6 6.0 6.3 6.6 6.9 7.2 7.5 7.8 8.0 1 3.3 3.6 3.8 4.1 4.3 4.6 4.8 5.1 5.3 5.6 5.8 6.1 0 1.9 2.1 2.3 2.5 2.7 2.9 3.1 3.3 3.5 3.7 3.9 4.1 -1 0.6 0.7 0.8 1.0 1.1 1.2 1.4 1.5 1.7 1.8 2.0 2.1 -2 -0.8 -0.7 -0.7 -0.6 -0.5 -0.4 -0.3 -0.3 -0.2 -0.1 0.0 0.1 -3 - - - - - - - - - - -1.9 -1.9
Ⅰ
K=3
Ⅱ
K=2
Ⅲ
K=1
Ⅳ
K=0
Ⅴ
K=—1
Ⅵ
K=—2
Ⅶ
K=—3
Ⅷ
• nP图控制界限
UCL=μ+3б =nP+3√nP(1-P)
CL= μ = nP LCL=μ- 3б
=nP - 3√nP(1-P)
• nPT图控制界限 ±3 变换后的随机变量nPT (随机变量-μ) = ———————— б
D-nP
第三章
质量管理旧七种工具 第七种:控制图
第三章
• §1 统计过程控制 (Statistical Process Control)
• §2 控制图 • §3 计量值控制图(6种) • §4 计数值控制图(4种) • §5 通用控制图(简介) • * §6 两种质量诊断(简介)
注意:
• 1、X图上的点是一个分布,而非测量值;
;
对比
分质量~总质量
可看出上道工序的影响
• 分质量
是工序的 固有质量, 正常情况下应与
• 标准值
一致。
差别越大,上影越大 差别越小,上影越小
• 总质量
包含了 上工序影响和 本工序影响的
• 综合质量,
反映在本工序完成后的
• 测量值上。
• 4、两种质量诊断的方法
(1)用控制图诊断
总质量——全控图(休哈特图)
实时 瞬间
分质量——选控图(张公绪)
(2)用过程能力指数诊断:
总质量——总过程能力指数Cpt 阶段 分质量——分过程能力指数Cpp
(二) 两种控制图的诊断
nmin>n/2
§5 通用控制图
• 一、标准变换~通用控制图 随机变量的平均值 0,方差 1
* 以标准偏差б为单位, 各随机变量到分布中心μ的相对距离。 随机变量- μ б
UCL=μ+3б CL=μ
LCL=μ- 3б
(UCL—μ) ( μ +3 б — μ)
UCLT = —————— = ————————
大? 小?
表明过程不合格品率异常低,好状态?
样本距中心线
的标准化距离:
di= pi-P
√P(1-P)/ni
④要求下控制界限为正,一般为0。
⑤样本量不等时,控制界限?不能仅以pi的描点距离判断点是否接近 中心线?
⑥控制界限~样本大小有关?
±√ /n
··
⑦简化凹凸型控制界限成直线:用样本的平均值求控制界限。 nmax<2n,