moldflow分析案例
moldflow 案例

moldflow 案例Moldflow案例是指使用Moldflow软件进行塑料注塑成型分析的实例。
Moldflow是一款由Autodesk公司开发的塑料模具设计和分析软件,它可以帮助工程师在模具制造之前预测和优化塑料零件的成型过程。
以下是一个简单的Moldflow案例:1. 导入模型:首先,在Moldflow中导入一个三维塑料零件模型,该模型可以是自行设计的,也可以是从其他软件(如Autodesk Inventor、SolidWorks等)导入的。
2. 模型准备:对导入的模型进行必要的简化,以减少计算复杂度。
这包括删除不必要的特征、合并面、修整边等。
3. 材料选择:根据塑料零件的性能要求,选择合适的塑料材料。
Moldflow软件中包含了大量的塑料材料库,可以根据实际需求进行选择。
4. 模具设计:根据塑料零件的尺寸和成型要求,设计合适的模具结构。
这包括模具类型、腔数、冷却系统、顶出器等。
5. 网格划分:对模型进行网格划分,以便进行后续的分析。
Moldflow会自动进行网格划分,但用户可以根据需要对网格进行手动调整。
6. 分析设置:设置分析参数,包括成型条件(如注射速度、注射压力、模具温度等)、分析类型(如填充时间、冷却时间、保压时间等)以及结果输出选项。
7. 分析结果:运行分析后,Moldflow会生成一系列的分析结果,如填充曲线、压力分布图、翘曲变形图等。
这些结果可以帮助工程师评估塑料零件的成型性能,找出可能存在的问题,并进行相应的优化。
8. 结果分析与优化:根据分析结果,对模具设计和成型条件进行优化。
这可能包括修改模具结构、调整材料参数、改变成型条件等。
9. 报告生成:最后,根据分析结果和优化方案,生成相应的报告,以供后续的模具制造和生产过程参考。
这个案例仅供参考,实际的Moldflow案例可能会根据具体需求和行业领域有所不同。
总之,Moldflow案例旨在帮助工程师通过模拟塑料零件的成型过程,提高模具设计质量和生产效率。
Moldflow的模流分析入门实例[精品文档]
![Moldflow的模流分析入门实例[精品文档]](https://img.taocdn.com/s3/m/118dafb902d276a200292ef2.png)
基于MOLDFLOW的模流分析技术上机实训教程主编:姓名:年级:专业:南京理工大学泰州科技学院实训一基于Moldflow的模流分析入门实例1.1Moldflow应用实例下面以脸盆塑料件作为分析对象,分析最佳浇口位置以及缺陷的预测。
脸盆三维模型如图1-1所示,充填分析结果如图1-2所示。
图1-1 脸盆造型图1-2 充填分析结果(1)格式转存。
将在三维设计软件如PRO/E,UG,SOLIDWORKS中设计的脸盆保存为STL格式,注意设置好弦高。
(2)新建工程。
启动MPI,选择“文件”,“新建项目”命令,如图1-3所示。
在“工程名称”文本框中输入“lianpen”,指定创建位置的文件路径,单击“确定”按钮创建一新工程。
此时在工程管理视窗中显示了“lianpen”的工程,如图1-4所示。
图1-3 “创建新工程”对话框图1-4 工程管理视图(3)导入模型。
选择“文件”,“输入”命令,或者单击工具栏上的“输入模型”图标,进入模型导入对话框。
选择STL文件进行导入。
选择文件“lianpen.stl”。
单击“打开”按钮,系统弹出如图1-5所示的“导入”对话框,此时要求用户预先旋转网格划分类型(Fusion)即表面模型,尺寸单位默认为毫米。
图1-5 导入选项单击“确定”按钮,脸盆模型被导入,如图1-6所示,工程管理视图出现“lp1_study”工程,如图1-7所示,方案任务视窗中列出了默认的分析任务和初始位置,如图1-8所示。
图1-6 脸盆模型图1-7 工程管理视窗图1-8 方案任务视窗(4)网格划分。
网格划分是模型前处理中的一个重要环节,网格质量好坏直接影响程序是否能够正常执行和分析结果的精度。
双击方案任务图标,或者选择“网格”,“生成网格”命令,工程管理视图中的“工具”页面显示“生成网格”定义信息,如图1-9所示。
单击“立即划分网格”按钮,系统将自动对模型进行网格划分和匹配。
网格划分信息可以在模型显示区域下方“网格日志”中查看,如图1-10所示。
Moldflow 模流分析 产品缺陷优化
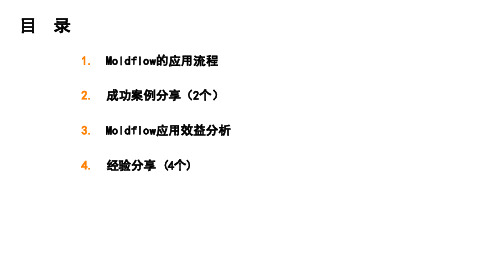
目录1.Moldflow的应用流程2.成功案例分享(2个)3.Moldflow应用效益分析4.经验分享(4个)3、演讲内容简介§①、如何用Moldflow软件解决产品外观光泽度、生产效率和翘曲变形问题。
§分享成果:如何将理论知识与实践相结合,得出容易复制、可推广的破题思路。
§②、多维度挖掘产品变形的成因,建立全面、科学评估体系。
§分享成果:技术在于不断积累和更新,拥有强大的知识库才能规避各种缺陷,防重于治!Moldflow 流程介绍一、模具设计前期流程二、首次试模后流程M F 分析M F分析案例分享(一)——解决光泽度、生产效率与变形问题产品简介1、产品概况:产品是挂机空调上的一个零件,零件名称为导风门,位于出风口上,起摆风作用,在空调关机时,处于闭合状态,为一级外观件;产品尺寸:780 x 73 x 24 ;主体壁厚:中心3.5 MM,边沿2.5MM ;材料颜色牌号供应商ABS高光白HI-121LG2、产品要求:①、一级外观件,光泽度要求100以上;②、产品不能有缩痕和S形变形;③、装配间隙要求0.8MM以内;④、每模生产周期55 S ;1、产品外观面的光泽度不够, 不到97(要求100以上);2、生产效率低,周期60秒;变形:反翘变形8MM3、升高模温后满足光泽度,产品变形和间隙大,反翘8 MM,间隙2MM (要求变形±1.5,装配间隙≤0.8 MM)间隙:2 MM 一、目前存在的问题二、原始方案§1、现状:前模热水45℃,后模、滑块接常温水25℃生产。
§2、目的:§缩小前后模的温差,防止产品变形超差。
§3、缺陷:§①、产品表面光泽度不够;§②、生产效率低;前模45℃后模25℃滑块25℃三、原因分析及改善方案(光泽度)1、原因分析:前模热水45℃,偏低,导致产品外观光泽度不够。
2、改善方案:提高前模水温;①、思路:模温机水温从45℃开始往上调整,每次上调5℃;②、现场验证:每次调整后连续生产30分钟(让模具上升到一个相对稳定的温度),并测量光泽度,直到60℃时,发现产品的光泽度达到103 ,符合要求(要求100以上);③、进一步测试:再升高模温到65℃,经过检测,光泽度没有明显提高,反而导致产品冷却后变形超标。
Moldflow模流分析报告范例

14
Shear Stress at Wall 最大剪切应力
流道系统上最大剪切应力: 2.8MPa 产品上最大剪切应力:0.4MPa
一般产品上的最大剪切应力,不要超过成型材料所允许的数值(如第8页所示, 该材料允许最大剪切应力为0.5MPa )。剪切应力太大,产品易开裂。
通过加大最大剪切应处壁厚,降低注塑速度,采用低粘度的材料,提高料温,可 减小剪切速率。
一般,脱模时相邻区域的体积收缩值相差>2%,产品表面易出现缩水。
可通过优化产品壁厚、浇口放置在壁厚区域、加大保压等措施,来降低 体积收缩。
DESIGN SOLUTIONS
18
Frozen Layer Fraction 凝固层因子
6.3s 12.2s 30.9s
Frozen Layer Fraction反映的是产品的凝固顺序。该产品在6.3秒时,红色区 域已凝固,导致安装孔位保压不足,故体积收缩较大,易出现表面缩水。 当产品100%凝固,冷流道系统凝固50%以上。产品可脱模。从而确定该产 品成型周期31s(不包括开合模时间)。 可通过优化冷却水路排布、降低局部壁厚区域的厚度、优化冷流道尺寸,来 缩短成型周期。
DESIGN SOLUTIONS
19
Sink Mark Estimate 凹痕深度
一般,凹痕数值>0.03mm,表面缩水较明显。 可通过加大基本壁厚、减小加强筋和螺栓柱等壁厚、加大保压等方式,来降 低凹痕深度。
DESIGN SOLUTIONS
20
Sink Mark Shaded 凹痕阴影显示
阴影显示凹痕的分析结果。圈示区域,肉眼看起来较明显。
22
Temperature, Part 冷却结束时产品表面温度
moldflow成功案例
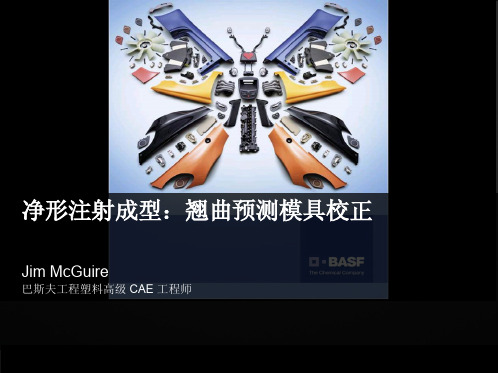
全部收缩
收缩测定 概念
软件可以帮助测量区段变更: 是收缩还是翘曲?
或是两者兼而有之?
收缩和翘曲
翘曲验证
翘曲验证
原始设计
翘曲验证
翘曲形 状
原始设计
逆向翘 曲形状
最终翘曲
翘曲验证
原始形状和翘 曲形状
翘曲验证
原始形状和 逆向翘曲形状
翘曲验证
失败
逆向翘曲形状
最终翘曲
翘曲验证
哪里出错了?适当翘曲有哪些要求?
.31% .44%
.44% .31%
收缩测定 Z 挠度
明显收缩 (%) A 流向 B C D E F G H 结果 0.38
0.31 0.44 0.44 0.31
收缩测定 X 挠度
1.41%
1.79%
1.12%
.37%
.43%
.16%
.13%
.41%
收缩测定 X 挠度
明显收缩 (%) A 交叉流向 B C D E F G H 结果 0.73
三维分析
AMI 2011 SP2 Solver AMI 2010-R2 Mesh
三维分析
AMI 2011 SP2 Solver AMI 2011 SP 2 Mesh 1,742,403 个元素
三维分析
AMI 2011 SP2 Solver AMI 2011 SP 2 Mesh 1,742,403 个元素
捕鼠器 翘曲衍生的模具校正
捕鼠器 翘曲衍生的模具校正
经校正的模具形状
Moldflow 分析
部件轻微翘曲 或无翘曲?
您是否相信您的Moldflow分析结果?
您是否敢于根据分析结果切割模具?
Moldflow的模流分析入门实例.
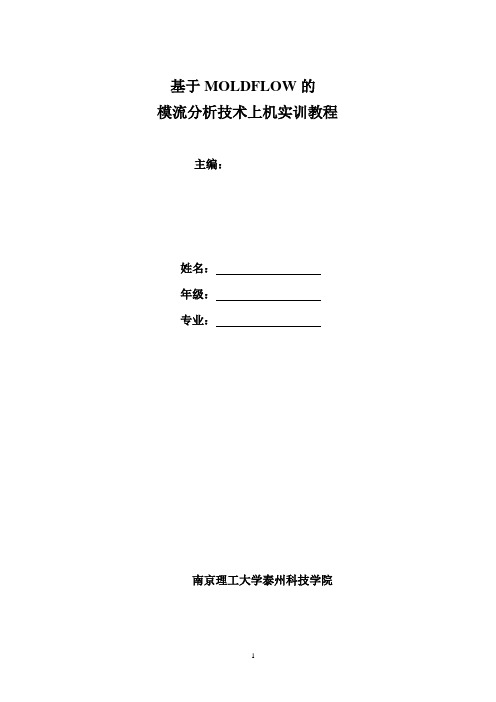
基于MOLDFLOW的模流分析技术上机实训教程主编:姓名:年级:专业:南京理工大学泰州科技学院实训一基于Moldflow的模流分析入门实例1.1Moldflow应用实例下面以脸盆塑料件作为分析对象,分析最佳浇口位置以及缺陷的预测。
脸盆三维模型如图1-1所示,充填分析结果如图1-2所示。
图1-1 脸盆造型图1-2 充填分析结果(1)格式转存。
将在三维设计软件如PRO/E,UG,SOLIDWORKS中设计的脸盆保存为STL格式,注意设置好弦高。
(2)新建工程。
启动MPI,选择“文件”,“新建项目”命令,如图1-3所示。
在“工程名称”文本框中输入“lianpen”,指定创建位置的文件路径,单击“确定”按钮创建一新工程。
此时在工程管理视窗中显示了“lianpen”的工程,如图1-4所示。
图1-3 “创建新工程”对话框图1-4 工程管理视图(3)导入模型。
选择“文件”,“输入”命令,或者单击工具栏上的“输入模型”图标,进入模型导入对话框。
选择STL文件进行导入。
选择文件“lianpen.stl”。
单击“打开”按钮,系统弹出如图1-5所示的“导入”对话框,此时要求用户预先旋转网格划分类型(Fusion)即表面模型,尺寸单位默认为毫米。
图1-5 导入选项单击“确定”按钮,脸盆模型被导入,如图1-6所示,工程管理视图出现“lp1_study”工程,如图1-7所示,方案任务视窗中列出了默认的分析任务和初始位置,如图1-8所示。
图1-6 脸盆模型图1-7 工程管理视窗图1-8 方案任务视窗(4)网格划分。
网格划分是模型前处理中的一个重要环节,网格质量好坏直接影响程序是否能够正常执行和分析结果的精度。
双击方案任务图标,或者选择“网格”,“生成网格”命令,工程管理视图中的“工具”页面显示“生成网格”定义信息,如图1-9所示。
单击“立即划分网格”按钮,系统将自动对模型进行网格划分和匹配。
网格划分信息可以在模型显示区域下方“网格日志”中查看,如图1-10所示。
Moldflow分析报告
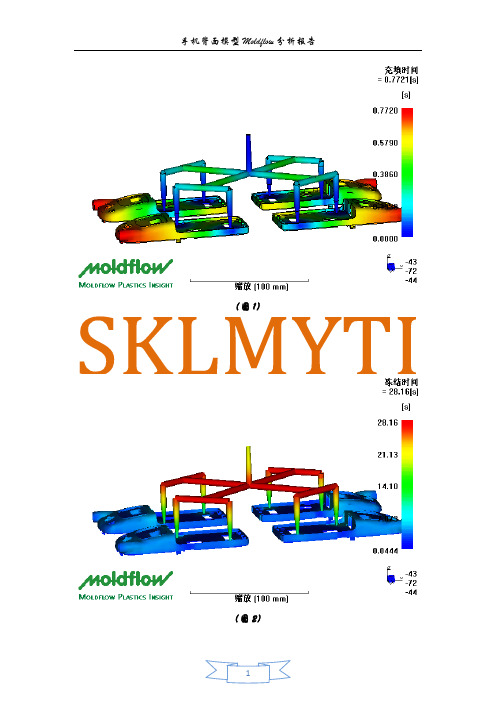
(图1)(图2)(图3)(图4)(图5)(图6)方案分析说明:1.在图1中充填时间差为0.77S,相差不大,基本可以接受。
2.在图2中制件冷却时间差较小,能够实现制件的均匀冷却。
3.在图3中流动前沿温差较大,即整个模型温差较大,但制件温度分布还是比较均匀的。
4.在图4中回路冷却介质温差较小,说明冷却回路的设置较为合理。
5.在图5中锁模力峰值为26t左右,且在12S左右降为0,较为符合要求。
6.在图6中最大变形值为0.3488mm,变形量稍微有点大。
在整个模型的分析过程中,网格漏洞的修复较为繁琐,网格厚度不均导致多次分析失败,而最后的分析结果说明整个方案也不够理想,在流动前沿温度中温差过大、V/P转换中则有未充满的区域,有需要靠保压才能充满的区域,两浇口所充填的区域大小有较大差别,内部气穴较多,有较多的熔接痕(两浇口间熔接痕较长)……因此该方案有待改进:采取改变浇口位置,两浇口充填区域平衡,减少熔接痕和气穴,修善冷却管道使变形翘曲量减少等措施。
修改后的方案分析说明:该方案在第一个方案的基础上做了两处改动:一是将其中一个浇口移到了面板的右上角,使得充填时间差减小到0.6489S,基本达到了流动平衡,但依然有较小的区域需要在保压期间才能充满;二是,将方案一中下部的冷却水管整体上移了10mm,并把空腔处的管道弯折上去了,使得上下管道的热交换效率接近,达到良好的冷却效果,而在空腔也有效地得到了冷却。
改动后的方案只是使得模型在翘曲方面的变形有所加大,但变形量依然是在能够接受的范围内,所以,总体来说,改动后的方案较好。
以下为修改后的方案:(图7)(图8)(图9)(图10)(图11)(图12)。
moldflow分析

我们采用MPI/FILL、MPI/PACK来进行分析计算。预测充填状 况、型腔压力分布、温度分布、锁模力大小、体积收缩率、熔接痕、 困气位置。
Jul 2001
Page 2
Moldflow China
制品材料
EE188AI(PP+T16) 1. 推荐注射温度 4. 推荐模具温度 240.0 degC 40.0 degC 5. 6. 7. 8. 顶出温度 不流动温度 许可剪切应力 许可剪切速率 108.0 deg.C 200.0 deg.C 0. 25Mpa 100,000 1/s
Jul 2001
Page 13
Moldflow China
小结
1. 2. 3. 4. 此方案注射较为均衡,成型压力适中,型腔压力分布较为均衡,体积收缩较 为均匀。 受投影面积影响及保压压力影响,锁模力较大,可通过调整保压压力降低锁 模力。 在制品边角处形成困气,熔料包合容易烧焦或熔接痕明显,需调整浇口位置 及顺序阀开关时间。 可采用6点顺序阀式热流道方案,建议调整下面两点喷嘴及浇口位置,减小两 喷嘴间距,调整开阀注射时间,以改善充填状况及困气情况,优化保压工艺。
剪切速率—黏度曲线
Jul 2001
PVT曲线
Page 3
Moldflow China
பைடு நூலகம்方案1
浇注系统
该模具一模一腔,采 用顺序阀式热流道系 统,6点顺序阀。
Jul 2001
Page 4
Moldflow China
工艺参数
1. 2. 3. 4. 模温 熔体温度 注射时间 保压压力 50 MPa 40 MPa 0 Mpa : 40.0 deg.C : 230.0 deg.C : 6.8sec 保压时间 6s 4s 4s
- 1、下载文档前请自行甄别文档内容的完整性,平台不提供额外的编辑、内容补充、找答案等附加服务。
- 2、"仅部分预览"的文档,不可在线预览部分如存在完整性等问题,可反馈申请退款(可完整预览的文档不适用该条件!)。
- 3、如文档侵犯您的权益,请联系客服反馈,我们会尽快为您处理(人工客服工作时间:9:00-18:30)。
结果解释
中间数据结果
记录填充和保压过程中的多个时刻的结果。默认设置 是在填充阶段和保压阶段各记录 20 个数据点。可设置的 中间结果的数量范围为 0 到100。默认下,中间结果的 动画播放方式是以时间来控制。 ? 压力 (Pressure ) ? 平均速度(Average velocity ) ? 加权平均温度( Bulk temperature ) ? 凝固层系数( Frozen layer fraction ) ? 加权平均的剪切速读( Shear rate bulk ) ? 在模壁上的剪切应力( Shear stress at wall ) ? 体积收缩(Volumetric shrinkage ) ? 平均玻纤取向( Average fiber orientation )
从塑料到模腔壁的热传导
? 影响冷却系统性能的参数
? 模具材料热特性 : 比热;导热性 ? 料温和模温之间的温度梯度 ? 塑料和模腔壁间接触的质量:保证良好的接触
冷却液流动率与热交换
塑料 塑料/金属界面 水/金属界 冷却液面
层流(Re<2300)的温度 梯度
中间剖面结果
? 剖面结果储存了胶料经过区域沿厚度方向的数值, 因为它也是中间数据结果,所以在填充和报压的过 程中胶料所经区域的信息也是存储的几个时间点的 数据,在缺省状态下,是不保存剖面的信息的
? 在高级设置里的求解参数设置中,可以分别设置填 充和保压分析的剖面结果记录剖次数。最多可以设 置成20。最初的随时间播放的动画显示的是法向 厚度为0 的剖面层的结果。中间剖面结果包括 : ? 剪切速度( Shear rate ) ? 温度(Temperature ) ? 速度(Velocity)
图。通过鼠标选定或手工指定节点或单元的号码,来重新创建想要的X-Y 图
填充分析
选择成型材料, 设定进料位置及模温 和料温,进行填充模 拟分析。
填充时间 Fill Time
充模时间显示的 是熔体流动前沿 的扩展情况 整个填充过程, 从图中可以得到 塑料流过每一点 的时间,蓝色为 最后填充处。
作用:预估填充所需时间,预测最后填充处,填充是 否平衡,无滞流现象等。
作用:预测熔接线位置,避免熔接线影响外观或降低强 度。通过调整浇注系统来改变熔接线位置,控制波前对 接角度和温度也可以控制熔接处的质量。
气泡 Air Traps
左图紫色圆点 显示的是气泡 可能出现的位 置。
作用:预测气泡位置,避免在产品内部形成气泡,甚 至烧伤。在可能出现气泡的地方做好排气。
冷却分析
XY 图
X-Y 图是两维图,在一个周期里,一个值随着另外一 个值而改变,都可以用 X-Y 图来表示。
? 锁模力(Clamp force: XY plot ) ? 射出胶料重量的百分比( % Show weight: XY Plot) ? 进胶口出的压力( Pressure at injection location: XY Plot) ? 推荐的螺杆速度( Recommended ram speed: X要Y将中P间lo结t果)制成X-Y 图,需要重新创建该结果。当创建时,要将类型指定为X-Y
模具温度与冷却时间
? 模温增加,冷却时间增加
冷 却 时 间
模具温度
2mm厚、200mm长的产品,以中间范围的料温和 1s时间注射
在注射成型中的热量传递
辐射散热
对流散热
热量散失到 模板上
热量由熔融塑 料带入
热量从冷却水路传入或传出
影响冷却系统性能的参数
? 从塑料到模腔壁的热传导 ? 从模腔壁到水管壁的热传导 ? 从水管壁到冷却介质的热传导
注射位置压力: XY图
通过注射位置压力的 XY图可看到压力的变 化情况。熔体被注入 型腔后压力持续增高。 若压力出现尖峰(通 常在充模快结束时), 表明制件没有很好达 到平衡充模,或者由 于流动前沿物料体积 的明显减少使流动前 沿的速度提高
熔接线 Weld Lines
左图圆圈中紫 色线条显示的 是熔接线位置。
填充压力 Pressure
填充结束时模 型各点的压力, 蓝色为最低压 力,红色为最 高压力。
作用:查看填充过程中所需的最大压力,以此压力为参 考值来设置成型工艺参数和选择成型机规格。
填充温度 Temperature
填充结束时模型 各点的温度,蓝 色为最低温度, 红色为最高温度。
作用:查看温度是否超出塑料的成型温度范围。温度 过低会降低塑料的流动性,产生短射或滞流;温度过 高会使塑料发生裂解,影响产品质量。
冷却分析
选择冷却模型,设 定冷却液种类、温 度及流速,进行冷 却模拟分析。
外表面温度 Top Temperature
左图为产品外 表面温度分布。
作用:查看定模侧冷却系统的冷却效果,有无过高或过 低温度。
内表面温度 Bottom Temperature
左图为产品内统的冷却效果,有无过高或过 低温度。
内外表面温度差 Temp. Difference
左图为产品内 外表面温度差。
作用:查看产品内外侧的温度差。温差越小,产品质量 越高,根据温差调整冷却系统。
冷却的影响
? 产品品质
? 表面光洁度 ? 残余应力 ? 结晶度 ? 热弯曲??
? 生产成本
? 顶出温度 ? 循环时间
冷却合 理
冷却不 佳
质量好,成型快 质量差,成型慢
第六章 Moldflow分析 详解
结果解释
单一数据结果
在填充或保压过程中只记录单一数值结果。其结果按 节点或网格单元的数值进行存储。其动画只显示从最大 到最小值。包括:
? 填充时间(Fill time ) ? 料流前锋温度( Temperature at flow front ) ? 填充结束时刻的加权平均温度 (Bulk temperature ) ? 填充结束时的凝固层系数 (Frozen layer fraction ) ? 胶料来源(Grow from) ? 填充结束时刻的压力 (Pressure ) ? 收缩指数(Sink Index) ? 凝固时间(Time to freeze ) ? 顶出时刻的体积收缩( Volumetric shrinkage )