预测性维护与全面生产维护区别及作用
全面生产维护的基石包括

设备故障预测和预防
设备故障预测:通过数据分析和技术手段,预测设备可能出现的故障,提前采取措施进 行维护。
预防性维护:定期对设备进行检查、清洁、润滑等维护工作,以预防设备故障的发生。
设备故障预防:通过优化设备设计、提高设备制造质量等方式,从根本上预防设备故障 的发生。
维护计划制定:根据设备的运行状况和历史数据,制定合理的维护计划,确保设备的正 常运行。
培养员工的持续 改进意识和能力
感谢您的观看
汇报人:
实施方法:通过收集数据、分析问题、采取措施和持续监测,不断改进维护和生产过程。
关键要素:包括员工参与、跨部门合作、标准化作业、预防性维护和精益生产等。
目标:提高产品质量、降低生产成本、增强设备可靠性,并创造一个持续改进的企业文化。
维护效果的评估和反馈
定期评估:对维护效果进行定期评估,确保生产设备的正常运行。
设备维护和维修策略
预测性维护:利用传感器和 数据分析预测设备故障,提 前采取措施
预防性维护:定期检查、更 换易损件,预防设备故障的 发生
修复性维护:设备出现故障 后,及时进行修复和更换部
件
优化性维护:通过对设备性 能的优化,提高设备的可靠
性和稳定性
持续改进
第五章
维护和生产过程的持续改进
定义:持续改进是一种不断优化生产过程和维护活动的理念,旨在提高效率、减少浪 费和降低成本。
优化生产流程:减 少浪费,提高生产 效率
引入自动化设备: 减少人工操作,提 高生产速度
制定合理的生产计 划:确保生产有序 进行,避免生产中 断
加强员工培训:提 高员工技能水平, 提升生产效率
设备可靠性管理
第四章
设备可靠性评估和改进
预防性维护、预测性维护和周期性检修区别与联系
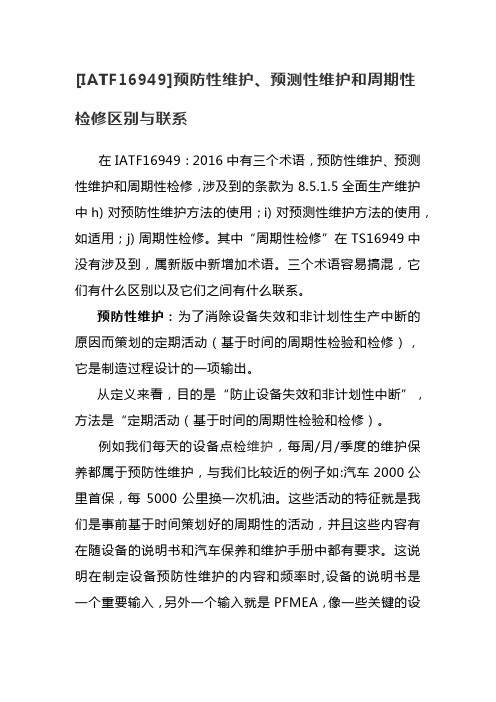
[IATF16949]预防性维护、预测性维护和周期性检修区别与联系在IATF16949:2016中有三个术语,预防性维护、预测性维护和周期性检修,涉及到的条款为8.5.1.5全面生产维护中h) 对预防性维护方法的使用;i) 对预测性维护方法的使用,如适用;j) 周期性检修。
其中“周期性检修”在TS16949中没有涉及到,属新版中新增加术语。
三个术语容易搞混,它们有什么区别以及它们之间有什么联系。
预防性维护:为了消除设备失效和非计划性生产中断的原因而策划的定期活动(基于时间的周期性检验和检修),它是制造过程设计的一项输出。
从定义来看,目的是“防止设备失效和非计划性中断”,方法是“定期活动(基于时间的周期性检验和检修)。
例如我们每天的设备点检维护,每周/月/季度的维护保养都属于预防性维护,与我们比较近的例子如:汽车2000公里首保,每5000公里换一次机油。
这些活动的特征就是我们是事前基于时间策划好的周期性的活动,并且这些内容有在随设备的说明书和汽车保养和维护手册中都有要求。
这说明在制定设备预防性维护的内容和频率时,设备的说明书是一个重要输入,另外一个输入就是PFMEA,像一些关键的设备、工装的一些易损部位,很多时候是要基于PFMEA来进行识别。
预测性维护:通过对设备状况实施周期性或持续监视来评价在役设备状况的一种方法或一套技术,以便预测应当进行维护的具体时间。
从定义来看在没有发生问题的时候,基于对设备状态的一种监控所采取的一些维护性活动,不要等到设备出故障了再去修理,而是在出现这种故障苗头的时候就要去处理它。
怎么去监控设备的状态?一是直接对设备状态进行数据的监控和采集。
如利用红外热像仪,振动分析仪,超声波仪等检测设备,通过检测设备的温度和振动等运行参数,并将测得的参数与设备标准运行状态参数进行比较,从而判断是否需要进行维护,以及如何有针对性的安排维护工作。
二是对于设备的绩效(OEE、MTBF、MTTR等)进行监控。
TPM全面生产维护的作用
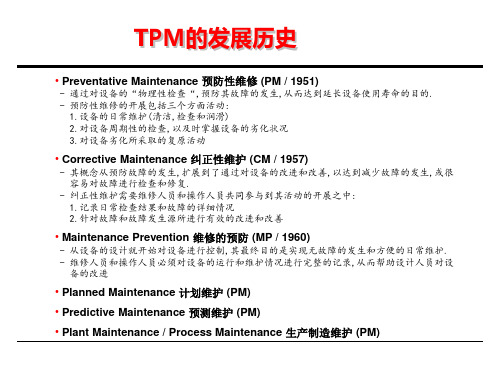
- 其概念从预防故障的发生,扩展到了通过对设备的改进和改善,以达到减少故障的发生,或很 容易对故障进行检查和修复.
- 纠正性维护需要维修人员和操作人员共同参与到其活动的开展之中: 1.记录日常检查结果和故障的详细情况 2.针对故障和故障发生源所进行有效的改进和改善
• Total Product Management 产品全面管理
• Total Profit Management 全员效益管理
• Total Plant Management 全员车间管理
• Tapping People‘s Minds 开发人的思维
• Teams Produce More 更多的产出
生产和维修的团队合作 • Total Perfection of Manufacturing 全员优化想的转变 • Total Production Management 全员生产管理 • Training People Meaningfully 员工长期的培训 • Totally Pampered Machines 完好的设备 • Total Process Management 全员制造管理
TPM的发展历史
• Preventative Maintenance 预防性维修 (PM / 1951)
- 通过对设备的“物理性检查“,预防其故障的发生,从而达到延长设备使用寿命的目的. - 预防性维修的开展包括三个方面活动:
1.设备的日常维护(清洁,检查和润滑) 2.对设备周期性的检查,以及时掌握设备的劣化状况 3.对设备劣化所采取的复原活动
• 二十世纪八十年代开始,TPM作为一套有效的管理系统,得到了人们的广泛认 同,世界上许多公司先后引进了TPM系统 • 与此同时,TPM系统本身也在不断发展完善,从最初的设备维护管理,发展
全面生产维护(TPM)讲义

预防保全时代(PM)
• 1951年,美国人最先提出了预防保全 (Productive Maintenance)的概念。主 要对机器设备进行一些简单的维护,比如 定时上油、经常擦拭灰尘、更换螺丝螺母 等。
改良保全时代(CM)
• 1957年,人们开始根据设备零件的使用周 期定期更换零件,使设备运转更加正常。 根据零件的使用周期,在零件使用寿命到 期之前更换零件,既有效地利用了零件, 又防止了故障的发生。
例2:某企业1个工作日的生产资料
日历 工作 时间 /min 1440 计划 停机 时间 /min 530 计划 利用 时间 /min 910 非计 划停 机时 间 /min 115 更换 调整 时间 /min 12 开动 时间 /min 完成 节拍 数 /min 203 返修 件数 /min 一次 合格 品数 /min 152
一、TPM预备知识
1、什么是管理? • 定义:为了实现组织的目标,所进行的计 划、组织、领导、控制和协调的诸过程。 • 管理的任务就是提高组织的效率和效能。 • 有效管理的三要素: (1)管理意识 (2)管理方法 (3)员工的行动
2、什么是机制?
• 机制就是制度加方法或者制度化(结构化)了的方法。 其 含义为“因为这个方法的存在,使得一件事不得不被完成 到最好” 。 (1)机制是经过实践检验证明有效的、较为固定的方法,不 因组织负责人的变动而随意变动,而单纯的工作方式、方 法是可以根据个人主观随意改变的。 (2)机制本身含有制度的因素,并且要求所有相关人员遵守, 而单纯的工作方式、方法往往体现为个人做事的一种偏好 或经验。 (3)机制一定是经过实践检验有效的方式方法,并进行一定 的加工,使之系统化、理论化,这样才能有效地指导实践。 而单纯的工作方式和方法则因人而异,并不要求上升到理 论高度。 (4)机制一般是依靠多种方式、方法来起作用的,而方式、 方法可以是单一起作用的。例如,建立起各种工作机制的 同时,还应有相应的激励机制、动力机制和监督机制来保 证工作的落实、推动、纠错、评价等。
TPM基础之预防性及预见性维护

备设计不合理) - 设备设计时缺乏有关检查和清洁方面的详细考虑。(设备设计不合理)
正常运转.
3. 预测设备维修周期 求.
2. 在设备停转期间进 .
行检查.
12
盖普咨询
注意! 注意!
高级诊断和计算机化的维护计划只有在操 作人员充分参与的条件下才能有效采用和 执行。
否则反而会导致低效。
13
13
盖普咨询
何时实施FMEA
在过程改善调查早期 设计新系统、产品以及过程时 改变现有设计或过程时 遗留的旧的设计重新应用时 系统、产品或过程功能定义后,但在具体硬件选择或投产前
30
30
盖普咨询
FMEA的历史
60年代初首次用于宇航工业的阿波罗任务中 1974年,海军制订了有关使用FMEA的军事标准MIL-STD-1629 70年代末,汽车工业受到责任费用驱动而采用FMEA 以后,汽车工业看到用这种工具来减少与劣质有关的风险的好处
陷)
效果
27
27
盖普咨询
FMEA
如何进行
- 团队识别设计功能或过程要求的潜在失效模式
将该失效模式影响的严重程度分等级 将潜在失效原因的出现频率以及被发现的可能性分等级
- 团队将严重程度乘以出现频率再乘以被发现的可能性,计算出风险优先数 - 团队用分等级的办法使过程改善的努力有重点
6
6
盖普咨询
防止型维护
设备的预防性和预测性维护

②对于设备的绩效(OEE、MTBF、MTTR等)进行监控。
例:如果MTBF越来越短,MTTR越来越长,其实就代表着该设备的状态是处于“劣化”的情况, 这时需要提前采取一些措施。原来制定的预防性维护计划是1次/半年对它进行一次维护保养或周期 性检修,这时它的状态不好,就要考虑把它缩短为1个月就要进行周期性检修或预防性维护,这个 就属于预测性维护的范畴。
生产车间设备的 预防性和预测性维护
I AT F 1 6 9 4 9 : 2 0 1 6 对 设 备 管 理 提 出 了 明 确 的 要 求 :
8.5.1.5 全面生产维护 组织应制定、实施并保持一个形成文件的全面生产维护系统。 f) 形成文件的维护目标,例如:OEE(全局设备效率)、MTBF(平均故障间隔时间)和MTTR (平均维修时间),以及预防性维护符合性指标。维护目标的绩效应作为管理评审的输入(见 ISO9001 第9.3条) g) 维护计划和目标以及形成文件的措施计划的定期评审,以在未达到目标时采取纠正措施; h) 对预防性维护方法的使用; i) 对预测性维护方法的使用,如适用; j) 周期性检修。
同时预防性维护是制造过程设计的一项输出【8.3.5.2 制造过程设计输出 h)维护计划和说明】,在 做预防性维护的时候有两个非常重要的输入,一个输入是设备的使用说明书,说明书会告诉我们什 么时候要更换润滑油,什么时候要对一些易损件进行更换。另外一个重要的输入是PFMEA或设备 FMEA,但FMEA在工厂的运用基本上就是纸上谈兵,像一些关键或核心设备、工装夹具、易损部 位等,很多时候是要基于FMEA来进行识别。
预防性维护(Preventive maintenance):
预防性维护:为了消除设备失效和非计划生产中断的原因而策划的定期活动(基于时间的周期性检 验和检修)。它是制造过程设计的一项输出。
全面生产维护(TPM)

建立对设备(shèbèi)整个寿命周期的生产维护
涉及所有部门的活动
全员参与 小组自主活动
第五页,共24页。
设
备 综 合 效
率 最 高
设备部
TPM目标(mùbiāo)
全面生产维修(Total Productive Maintenance,TPM)是消除停机时间最有力的措施,包 括例行维修、预测性维修、预防性维修和立即维修四种基本(jīběn)维修方式。
计划修理:根据日常点检、定期(dìngqī)检查的结果所提出的设备修理委托书、 维修报告、机床性能检查记录等资料编制的计划,定期(dìngqī)进行修理。这种 修理属于恢复性修理。
改善修理:即对设备的某些结构进行改进的修理,这种修理主要用于经常(jīngcháng)重复 发生故障的设备。
故障修理:当设备突然(tūrán)发生故障或由于设备原因造成废品时必须立即组织抢修,这种修 理叫做故障修理。
(Equipment Failure / Breakdown Losses) (Setup and Adjustment) (Idling and Minor Stoppage Losses) (Reduced Speed Losses) (Quality Defects and Rework) (Startup Losses)
Deming博士是在二战结束不久后在日本开始工作的,作为一个统计学家,他首次向 日本人展示了如何在制造过程中使用统计分析和如何在制造过程中使用效果数据来控 制质量。由日本工作理论建立的早期统计程序和效果质量控制概念很快成为日本工业 的—种生存方式,这种新的制造概念最终被命名为全面质量管理(TQM)。
全员参加型的保养
1980年以后
2
改良维修
IATF16949全面生产维护管理办法
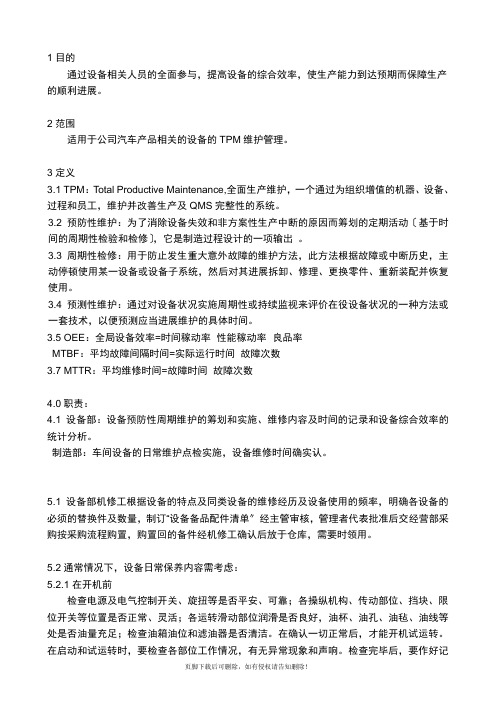
通过设备相关人员的全面参与,提高设备的综合效率,使生产能力到达预期而保障生产的顺利进展。
2范围适用于公司汽车产品相关的设备的TPM维护管理。
3定义3.1 TPM:Total Productive Maintenance,全面生产维护,一个通过为组织增值的机器、设备、过程和员工,维护并改善生产及QMS完整性的系统。
3.2 预防性维护:为了消除设备失效和非方案性生产中断的原因而筹划的定期活动〔基于时间的周期性检验和检修〕,它是制造过程设计的一项输出。
3.3周期性检修:用于防止发生重大意外故障的维护方法,此方法根据故障或中断历史,主动停顿使用某一设备或设备子系统,然后对其进展拆卸、修理、更换零件、重新装配并恢复使用。
3.4预测性维护:通过对设备状况实施周期性或持续监视来评价在役设备状况的一种方法或一套技术,以便预测应当进展维护的具体时间。
3.5 OEE:全局设备效率=时间稼动率×性能稼动率×良品率MTBF:平均故障间隔时间=实际运行时间÷故障次数3.7 MTTR:平均维修时间=故障时间÷故障次数4.0职责:4.1 设备部:设备预防性周期维护的筹划和实施、维修内容及时间的记录和设备综合效率的统计分析。
制造部:车间设备的日常维护点检实施,设备维修时间确实认。
5.1 设备部机修工根据设备的特点及同类设备的维修经历及设备使用的频率,明确各设备的必须的替换件及数量,制订“设备备品配件清单〞经主管审核,管理者代表批准后交经营部采购按采购流程购置,购置回的备件经机修工确认后放于仓库,需要时领用。
5.2通常情况下,设备日常保养内容需考虑:5.2.1在开机前检查电源及电气控制开关、旋扭等是否平安、可靠;各操纵机构、传动部位、挡块、限位开关等位置是否正常、灵活;各运转滑动部位润滑是否良好,油杯、油孔、油毡、油线等处是否油量充足;检查油箱油位和滤油器是否清洁。
在确认一切正常后,才能开机试运转。
- 1、下载文档前请自行甄别文档内容的完整性,平台不提供额外的编辑、内容补充、找答案等附加服务。
- 2、"仅部分预览"的文档,不可在线预览部分如存在完整性等问题,可反馈申请退款(可完整预览的文档不适用该条件!)。
- 3、如文档侵犯您的权益,请联系客服反馈,我们会尽快为您处理(人工客服工作时间:9:00-18:30)。
预测性维护与全面生产维护区别及作用
▼
02预测性维护
预测性维护,简单理解就是通过各种方法诊断早期故障隐患和缺陷,并在周期性检修时间内进行隐患和缺陷的消除。
预测性维修诊断方法包括:
1. 生产员工在班前的检查、设备维护人员日常的巡回检查,这是基于经验、图纸、维护手册和基准,通过五感(眼、耳、鼻、手、口)或自制的简单工具进行的手动诊断方式;
2. 利用专业监测仪器或理化分析方法,如振动分析、油液铁谱分析、油液理化分析、红外成像分析、红外温度分析等手段,对设备进行周期性的监测,结合经验和专业知识技能,判断设备存在的隐患和缺陷,也称为自动诊断方式;
3. 利用设备自带或外加的传感器,结合工艺和质量相关数据,通过数据建模,构建基于物联网的自诊断系统(也被称为工业互联网平台)。
预测性维护属于维修性范畴,难度在于如何提高预测性诊断的准确性,这包括传感器精度、诊断经验和技能知识的积累,预测性模型等复杂条件。
发展预测性维护,有利于提升制造效率,降低维护成本,是值得大力提倡的维修模式。
▼
03预防性维护
预防性维护属于可靠性范畴,是指设备本体的一些零部件,受制于经济性或工艺的制约,在通过可靠性试验后,确定输出的定期维修建议,以确保设备在设计寿命内的稳态可靠度。
在制造过程设计时,冗余设计是首要考虑的,这包含材料冗余、尺寸冗余和精度冗余,在通过相关可靠性检测和试验后,确定出各个部件的使用寿命,如某部件在试验中加工5000次,就会出现损坏,根据正常加工节拍,我们规定在5000次加工周期之前必须做出更换。
由于系统的复杂性会影响到子系统的可靠度,如整机可靠度要求是0.99,它由10个零部件组成,每一个零部件的可靠度必须达到0.999。
这给设计成本、可靠性能力、运行能耗带来风险,故优先考虑对设备结构进行简化,提倡专用设备设计和购置。
预防性维护在复杂设备和系统是不可或缺的一部分,但不适合大范围应用,除了影响维护成本和维护时间(影响生产计划)以外,在设备本身和工业备件供应质量低下的情况下,还会造成越修越坏,越坏越修的状况。
预防性维护向预测性维护过渡,是必然趋势,如按期换油(润滑脂、润滑油)向按质换油(油品检测)过渡。
同时控制关键易损零部件供应质量,也是非常重要的
举措,如轴承、润滑油品等,这对于确保制造系统可靠性和维护经济性至关重要。
备注:在工业互联网平台应用中,依据对加工数量和运动机构频率的统计,进而得出预防性维护的时间点,属于系统可靠性的组成部分,但前提必须对可靠性失效进行综合优化。
▼
04周期性检修
减少非计划停机,是实施全面生产维护的重要目标,同时也是工业互联网在预测性维护应用中的重要指标。
周期性检修,是基于预测性诊断、预防性维护周期确定的检修项目,安排在计划停机期间的维修作业。
主动性的预测性维护、预防性维护的维修通道建设数量和质量越低,非计划停机的应急维修项目越多,工业企业越没有时间安排周期性检修项目,故这是相互影响的过程,反之亦然。
工业企业应花更多的资源投入主动维护中,将预测性维护和预防性维护比重提高,这对于效率提升、成本降低的作用是显著的。
凡事预则立,不预则废。
周期性检修在时间周期上,应包含非停机的班次内消缺计划,每周安排在生产停机计划内的消缺计划,以及每月的周期性滚动停机计划内,而不只是年度计划这样的大跨度检修(如传统的小修、中修和大修计划)。
周期性检修反映了工业企业运维作业的计划性,这意味着对工业备件以及外协维修服务的需求量化,这对于提高工业供应链供给效率和供给质量,有利于促进工业互联网与工业服务产业化落地。