铸件常见铸造缺陷
铸件中常见缺陷

铸件中常见的主要缺陷有:1.气孔这是金属凝固过程中未能逸出的气体留在金属内部形成的小空洞,其内壁光滑,内含气体,对超声波具有较高的反射率,但是又因为其基本上呈球状或椭球状,亦即为点状缺陷,影响其反射波幅。
钢锭中的气孔经过锻造或轧制后被压扁成面积型缺陷而有利于被超声检测所发现,如图2.2所示。
2.缩孔与疏松铸件或钢锭冷却凝固时,体积要收缩,在最后凝固的部分因为得不到液态金属的补充而会形成空洞状的缺陷。
大而集中的空洞称为缩孔,细小而分散的空隙则称为疏松,它们一般位于钢锭或铸件中心最后凝固的部分,其内壁粗糙,周围多伴有许多杂质和细小的气孔。
由于热胀冷缩的规律,缩孔是必然存在的,只是随加工工艺处理方法不同而有不同的形态、尺寸和位置,当其延伸到铸件或钢锭本体时就成为缺陷。
钢锭在开坯锻造时如果没有把缩孔切除干净而带入锻件中就成为残余缩孔(缩孔残余、残余缩管),如图2.3、2.4、2.5所示。
如果铸件的型模设计不当、浇注工艺不当等,也会在铸件与型模接触的部位产生疏松,如图2.28所示。
断口照片中的黑色部分即为疏松部位,其呈现黑色是因为该工件已经过退火处理,使得疏松部位被氧化和渗入机油所致。
图2.28 W18钢铸件-用作铣刀齿,采用超声纵波垂直入射多次底波衰减法发现的疏松断口照片3.夹渣熔炼过程中的熔渣或熔炉炉体上的耐火材料剥落进入液态金属中,在浇注时被卷入铸件或钢锭本体内,就形成了夹渣缺陷。
夹渣通常不会单一存在,往往呈密集状态或在不同深度上分散存在,它类似体积型缺陷然而又往往有一定线度。
4.夹杂熔炼过程中的反应生成物(如氧化物、硫化物等)-非金属夹杂,如图2.1和2.6,或金属成分中某些成分的添加料未完全熔化而残留下来形成金属夹杂,如高密度、高熔点成分-钨、钼等,如图2.29,也有如图2.24所示钛合金棒材中的纯钛偏析。
(a)(b)(c)(d)(e)图2.29 BT9钛合金锻制饼坯中的钼夹杂:(a)剖面低倍照片;(b)X射线照相底片;(c)C扫描显示(图中四个白色点状显示为同一个缺陷,是使用水浸点聚焦探头以不同灵敏度检测的结果,其他分散细小的白色点状为与该缺陷无关的杂波显示);(d)B扫描显示;(e)3D显示5.偏析铸件或钢锭中的偏析主要指冶炼过程中或金属的熔化过程中因为成分分布不均而形成的成分偏析,有偏析存在的区域其力学性能有别于整个金属基体的力学性能,差异超出允许标准范围就成为缺陷,如图2.23和2.24、2.27所示。
常见压铸件缺陷及解决方法
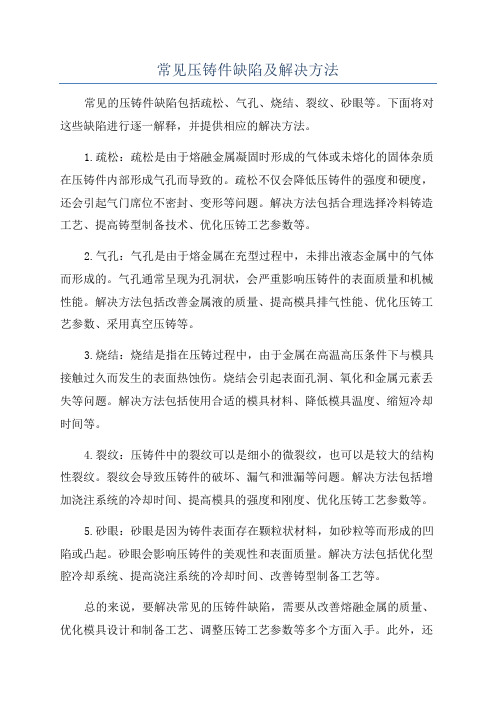
常见压铸件缺陷及解决方法常见的压铸件缺陷包括疏松、气孔、烧结、裂纹、砂眼等。
下面将对这些缺陷进行逐一解释,并提供相应的解决方法。
1.疏松:疏松是由于熔融金属凝固时形成的气体或未熔化的固体杂质在压铸件内部形成气孔而导致的。
疏松不仅会降低压铸件的强度和硬度,还会引起气门席位不密封、变形等问题。
解决方法包括合理选择冷料铸造工艺、提高铸型制备技术、优化压铸工艺参数等。
2.气孔:气孔是由于熔金属在充型过程中,未排出液态金属中的气体而形成的。
气孔通常呈现为孔洞状,会严重影响压铸件的表面质量和机械性能。
解决方法包括改善金属液的质量、提高模具排气性能、优化压铸工艺参数、采用真空压铸等。
3.烧结:烧结是指在压铸过程中,由于金属在高温高压条件下与模具接触过久而发生的表面热蚀伤。
烧结会引起表面孔洞、氧化和金属元素丢失等问题。
解决方法包括使用合适的模具材料、降低模具温度、缩短冷却时间等。
4.裂纹:压铸件中的裂纹可以是细小的微裂纹,也可以是较大的结构性裂纹。
裂纹会导致压铸件的破坏、漏气和泄漏等问题。
解决方法包括增加浇注系统的冷却时间、提高模具的强度和刚度、优化压铸工艺参数等。
5.砂眼:砂眼是因为铸件表面存在颗粒状材料,如砂粒等而形成的凹陷或凸起。
砂眼会影响压铸件的美观性和表面质量。
解决方法包括优化型腔冷却系统、提高浇注系统的冷却时间、改善铸型制备工艺等。
总的来说,要解决常见的压铸件缺陷,需要从改善熔融金属的质量、优化模具设计和制备工艺、调整压铸工艺参数等多个方面入手。
此外,还需要采用适当的检测手段,如金相分析、X射线检测、超声波检测等,对压铸件进行质量检验,及时排除可能存在的缺陷。
铸造缺陷种类

铸造缺陷种类
1、气孔缺陷。
铸铁件在凝固过程中未能逸出的气体留在铸件内部形成的小孔洞,内壁光滑,有气体。
表面一般情况下呈球状或椭球状,对于超声波具有较高的反射率,因此可以通过超声波进行检测。
2、缩松、缩孔缺陷。
铸铁件在冷却凝固时,体积收缩,在最后凝固的时候得不到充足的铁液的补充便会形成空洞状的缺陷,内壁粗糙,周围多伴有许多杂质和细小的气孔。
缩松呈现细小而分散的空隙,缩孔呈现大而集中的空洞。
3、偏析缺陷。
指铁合金在冶炼过程中或铁金属在熔化的过程中因为成分分布不均而形成的成分偏析,有偏析存在的区域其力学性能和整个金属的力学性能有较大的差别。
4、裂纹缺陷。
铸铁件中的裂纹主要时由于金属材料的强度难以支撑金属在冷却凝固时的收缩应力,这与金属中的合金含量、铸铁件的形状设计和铸造工艺有很大的关系。
5、冷隔缺陷。
这是指在浇注铁液时,由于飞溅、浇注中断或来自不同方向的两股金属流相遇,液态金属表面冷却形成的半固态薄膜留在铸铁件内而形成的一种隔膜状的面积型缺陷。
铸造铸件常见缺陷原因与解决方法分析
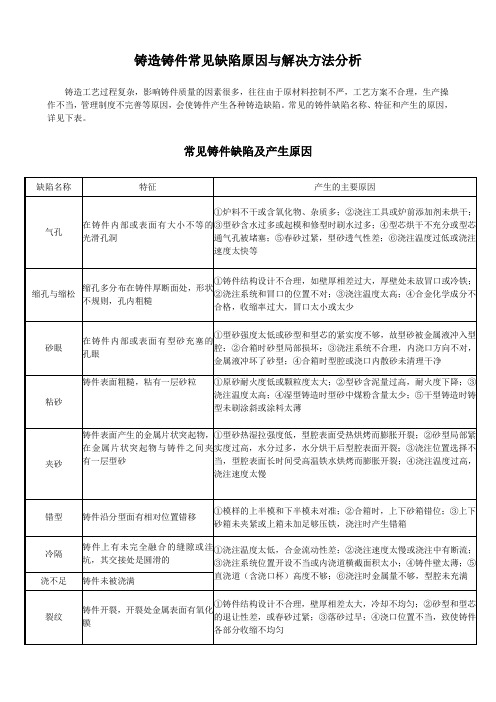
浇不到
由于金属液未完全充满型腔而产生的铸件缺肉。
提高浇注温度和浇注速度。不要断流和防止跑火。
壁间连接处尽量减小热节,尽量降低浇注温度和浇注速度。
4
渣气孔
在铸件内部或表面形状不规则的孔眼。孔眼不光滑,里面全部或部分充塞着熔渣。
提高铁液温度。降低熔渣粘性。提高浇注系统的挡渣能力。增大铸件内圆角。
5
砂眼
在铸件内部或表面有充塞着型砂的孔眼。
严格控制型砂性能和造型操作,合型前注意打扫型腔。
6
热裂
在铸件上有穿透或不穿透的裂纹(注要是弯曲形的),开裂处金属表皮氧化。
减少砂粒间隙。适当降低金属的浇注温度。提高型砂、芯砂的耐火度。
9
夹砂
在铸件表面上,有一层金属瘤状物或片状物,在金属瘤片和铸件之间夹有一层型砂。
严格控制型砂、芯砂性能。改善浇注系统,使金属液流动平稳。大平面铸件要倾斜浇注。
10
冷隔
在铸件上有一种未完全融合的缝隙或洼坑,其交界边缘是圆滑的。
提高浇注温度和浇注速度。改善浇注系统。浇注时不断流。
2
缩孔
在铸件厚断面内部、两交界面的内部及厚断面和薄断面交接处的内部或表面,形状不规则,孔内粗糙不平,晶粒粗大。
壁厚小且均匀的铸件要采用同时凝固,壁厚大且不均匀的铸件采用由薄向厚的顺序凝固,合理放置冒口的冷铁。
3
缩松
在铸件内部微小而不连贯的缩孔,聚集在一处或多处,晶粒粗大,各晶粒间存在很小的孔眼,水压试验时渗水。
冷隔
铸件上有未完全融合的缝隙或洼坑,其交接处是圆滑的
①浇注温度太低,合金流动性差;②浇注速度太慢或浇注中有断流;③浇注系统位置开设不当或内浇道横截面积太小;④铸件壁太薄;⑤直浇道(含浇口杯)高度不够;⑥浇注时金属量不够,型腔未充满
铸造件缺陷

铸造铸铁件常见的缺陷有:气孔、粘砂、夹砂、砂眼、胀砂、冷隔、浇不足、缩松、缩孔、缩凹、疏松、缺肉、肉瘤等。
1、气孔:气体在金属液结壳之前未及时逸出,在铸件内生成的孔洞类缺陷。
气孔的内壁光滑,明亮或带有轻微的氧化色。
铸件中产生气孔后,将会减小其有效承载面积,且在气孔周围会引起应力集中而降低铸件的抗冲击性和抗疲劳性。
气孔还会降低铸件的致密性,致使某些要求承受水压试验的铸件报废。
另外,气孔对铸件的耐腐蚀性和耐热性也有不良的影响。
此类问题可采用美嘉华技术修补铸造缺陷,简便易行,省时省工,且修复治理效果良好,并且可以针对铜、铁、钢、铝等不同材质进行修复,替代焊补工艺,避免应力损坏,为企业挽回巨大经济损失。
防止气孔的产生:降低金属液中的含气量,增大砂型的透气性,以及在型腔的最高处增设出气冒口等。
2、粘砂:铸件表面上粘附有一层难以清除的砂粒称为粘砂。
粘砂既影响铸件外观,又增加铸件清理和切削加工的工作量,甚至会影响机器的寿命。
防止粘砂:在型砂中加入煤粉,以及在铸型表面涂刷防粘砂涂料等。
3、夹砂:在铸件表面形成的沟槽和疤痕缺陷,在用湿型铸造厚大平板类铸件时极易产生。
铸件中产生夹砂的部位大多是与砂型上表面相接触的地方,型腔上表面受金属液辐射热的作用,容易拱起和翘曲,当翘起的砂层受金属液流不断冲刷时可能断裂破碎,留在原处或被带入其它部位。
铸件的上表面越大,型砂体积膨胀越大,形成夹砂的倾向性也越大。
4、砂眼:在铸件内部或表面充塞着型砂的孔洞类缺陷。
此类问题可采用美嘉华技术修补铸造缺陷,简便易行,省时省工,且修复治理效果良好,并且可以针对铜、铁、钢、铝等不同材质进行修复,替代焊补工艺,避免应力损坏,为企业挽回巨大经济损失。
5、胀砂:浇注时在金属液的压力作用下,铸型型壁移动,铸件局部胀大形成的缺陷。
为了防止胀砂,应提高砂型强度、砂箱刚度、加大合箱时的压箱力或紧固力,并适当降低浇注温度,使金属液的表面提早结壳,以降低金属液对铸型的压力。
铸件常见铸造缺陷

铸造常见缺陷特点
缺陷名称:砂眼(加工后)
铸造常见缺陷特点
缺陷名称:铸字不清 缺陷特点: 产生原因:型腔铸字部分起 模不畅,型砂粒度太粗
铸造常见缺陷特点
缺陷名称:披缝 缺陷特点:铸件表面在分模 面处旳规则缩陷。 产生原因: 砂型或砂芯分模 面处旳飞边未清除
铸造常见缺陷特点
铸造常见缺陷特点
缺陷名称:缩孔(大而集中 旳空洞 ) 缺陷特点:铸件厚、断面处 出现形状不规则旳孔眼,孔 旳内壁粗糙。 产生原因:冒口设置不正确 ;合金成份不合格,收缩过 大;浇注温度过高;铸件设 计不合理,无法进行补缩
铸造常见缺陷特点
缺陷名称:疏松(细小而分 散旳空隙) 缺陷特点:铸件厚、断面处 出现形状不规则旳孔眼,孔 旳内壁粗糙。 产生原因:冒口设置不正确 ;合金成份不合格,收缩过 大;浇注温度过高;铸件设 计不合理
铸造常见缺陷特点
缺陷名称:黑皮 缺陷特点:加工面有加工不 到旳地方 产生原因:铸件加工量不足, 铸件变形,夹偏
铸造常见缺陷特点
缺陷名称:黑皮(其二)
铸造常见缺陷特点
缺陷名称:气孔 缺陷特点:铸件内部或表面 有大小不同旳孔眼,孔旳内 壁光滑,多呈圆形。 产生原因:砂型太紧或型砂 透气性差;型砂太湿;砂芯 通气孔堵塞;浇注系统不正 确,气体排不出去
缺陷名称:表面多肉 缺陷特点:铸件表面有多出 旳部分。 产生原因:砂型或砂芯旳相 应部分掉肉。
铸造常见缺陷特点
缺陷名称:表面多肉肉(其 二)
铸造常见缺陷特点
缺陷名称:缺肉(缺料) 缺陷特点:铸件表面有缺乏 一块,可能造成报废。 产生原因:浇冒口切除时带 掉一块;
铸造常见缺陷特点
缺陷名称:表面缩凹 缺陷特点:铸件表面有缩凹。 产生原因:铸件内部收缩
铸件常见铸造缺陷
铸造常见缺陷特点
缺陷名称:砂眼 (加工后)
铸造常见缺陷特点
缺陷名称:铸字 不清 缺陷特点: 产生原因:型腔 铸字部分起模不 畅,型砂粒度太 粗
铸造常见缺陷特点
缺陷名称:披缝 缺陷特点:铸件表 面在分模面处的规 则缩陷。 产生原因: 砂型 或砂芯分模面处的 飞边未去除
铸造常见缺陷特点
缺陷名称:表面多 肉 缺陷特点:铸件表 面有多余的部分。 产生原因:砂型或 砂芯的相应部分掉 肉。
铸造常见缺陷特点
缺陷名称:表面多 肉肉(其二)
铸造常见缺陷特点
缺陷名称:缺肉 (缺料) 缺陷特点:铸件表 面有缺少一块,可 能导致报废。 产生原因:浇冒口 切除时带掉一块;
铸造常见缺陷特点
缺陷名称:表面缩 凹 缺陷特点:铸件表 面有缩凹。 产生原因:铸件内 部收缩
缺陷名称:缩孔
铸造常见缺陷特(大点而集中的空 洞) 缺陷特点:铸件厚、 断面处出现形状不 规则的孔眼,孔的 内壁粗糙。
产生原因:冒口设 置不正确
;合金成分不合格, 收缩过大;浇注温 度过高;铸件设计 不合理,无法进行 补缩
铸造常见缺陷特缺陷点名称:疏松 (细小而分散的空 隙)
缺陷特点:铸件厚、 断面处出现形状不 规则的孔眼,孔的 内壁粗糙。
铸铁常见缺陷认识
SATA (KUNSHAN) Q 部
2011 May
缺陷名称:砂眼
铸造常见缺陷特缺陷点特点:铸件 内部或表面有充 满砂粒的孔眼, 孔形不规则 产生原因:型砂 强度不够或局部 没舂紧,掉砂; 型腔、浇口内散 砂未吹净;合箱 时砂型局部挤坏, 掉砂;浇注系统
;合金成分不合格, 收缩过大;浇注温 度过高;铸件设计 不合理
铸造常见缺陷特点
铸件缺陷有哪些
铸件缺陷有哪些1 气孔气孔是一种常见的铸件缺陷,它是由于铸件内部汽水压力不均衡时形成的“空气孔”,也可能是打火口时残留下来的“砂孔”等引起的汽孔。
此外,由于铸件中砂模、砂滑块等砂型材料表面腐蚀或异物污染,也会使铸件出现汽孔。
气孔的形成,会导致铸件的质量受到影响,它们多为深孔状的内控,很容易被漏检。
而且,汽孔的存在,还会影响铸件的结构强度和使用寿命。
2 挖坑挖坑是指铸件披露时出现的“穴坑、绝缘坑”等外形的缺陷。
主要是由于模具表面的不均匀性或模具颗粒、抛丸和防锈剂等异物污染,在披露过程中没有被充分清除,而且披露工艺过程中,将披露深度过大,或温度过高,也会导致披露处出现凹槽、凹坑等挖坑缺陷。
挖坑的缺陷,会降低铸件的表面质量,从而降低产品的工作性能,甚至影响正常使用。
此外,由于披露缩小了铸件的冷却面积,进一步促使披露部分熔断,增加了披露缺陷的可能性,从而破坏了铸件的均一性。
3 淤渣淤渣是指由于模具内铸造残留物残留在出铸件上形成的缺陷。
它多由于模具内部构形复杂、脱模系统设计不当,模具整体活动量不足,不能将模具内的余铸料和其他废料及产生的气体等以足够的速度排出,而形成的淤渣缺陷。
淤渣的存在,会影响铸件的表面,从而影响产品的外观、形状和工作性能,严重时甚至会使铸件的完整性受到影响,使其尺寸精度、强度、坚固性和耐腐蚀性受到影响,影响其材料等级。
4 熔断熔断是指铸件内部在较低温度时因内部结构发生变化产生的缺陷。
熔断可由多个因素引起,如模具润滑不佳、熔点太高或披露深度过大、冷却效果不好等,此外,对某些特定材料,如煤基铸铁,温度较低时受到高氮含量的影响,也会产生熔断缺陷。
熔断的存在,会影响铸件的结构强度和使用寿命,它们多为深孔状的内控,很难以被检测出来,未能及时发现和纠正,会导致铸件质量减退,乃至于产品失效。
六种铸件常见缺陷的产生原因及防止方法
六种铸件常见缺陷的产⽣原因及防⽌⽅法⽓孔(⽓泡、呛孔、⽓窝)特征⽓孔是存在于铸件表⾯或内部的孔洞,呈圆形、椭圆形或不规则形,有时多个⽓孔组成⼀个⽓团,⽪下⼀般呈梨形。
呛孔形状不规则,且表⾯粗糙,⽓窝是铸件表⾯凹进去⼀块,表⾯较平滑。
明孔外观检查就能发现,⽪下⽓孔经机械加⼯后才能发现。
形成原因1、模具预热温度太低,液体⾦属经过浇注系统时冷却太快。
2、模具排⽓设计不良,⽓体不能通畅排出。
3、涂料不好,本⾝排⽓性不佳,甚⾄本⾝挥发或分解出⽓体。
4、模具型腔表⾯有孔洞、凹坑,液体⾦属注⼊后孔洞、凹坑处⽓体迅速膨胀压缩液体⾦属,形成呛孔。
5、模具型腔表⾯锈蚀,且未清理⼲净。
6、原材料(砂芯)存放不当,使⽤前未经预热。
7、脱氧剂不佳,或⽤量不够或操作不当等。
防⽌⽅法1、模具要充分预热,涂料(⽯墨)的粒度不宜太细,透⽓性要好。
2、使⽤倾斜浇注⽅式浇注。
3、原材料应存放在通风⼲燥处,使⽤时要预热。
4、选择脱氧效果较好的脱氧剂(镁)。
5、浇注温度不宜过⾼。
缩孔(缩松)特征缩孔是铸件表⾯或内部存在的⼀种表⾯粗糙的孔,轻微缩孔是许多分散的⼩缩孔,即缩松,缩孔或缩松处晶粒粗⼤。
常发⽣在铸件内浇道附近、冒⼝根部、厚⼤部位,壁的厚薄转接处及具有⼤平⾯的厚薄处。
形成原因1、模具⼯作温度控制未达到定向凝固要求。
2、涂料选择不当,不同部位涂料层厚度控制不好。
3、铸件在模具中的位置设计不当。
4、浇冒⼝设计未能达到起充分补缩的作⽤。
5、浇注温度过低或过⾼。
防⽌⽅法1、提⾼磨具温度。
2、调整涂料层厚度,涂料喷洒要均匀,涂料脱落⽽补涂时不可形成局部涂料堆积现象。
3、对模具进⾏局部加热或⽤绝热材料局部保温。
4、热节处镶铜块,对局部进⾏激冷。
5、模具上设计散热⽚,或通过⽔等加速局部地区冷却速度,或在模具外喷⽔,喷雾。
6、⽤可拆缷激冷块,轮流安放在型腔内,避免连续⽣产时激冷块本⾝冷却不充分。
7、模具冒⼝上设计加压装置。
8、浇注系统设计要准确,选择适宜的浇注温度。
铸造过程中常见的几种缺陷
铸造过程中常见的几种缺陷铸造是一种常见的金属加工方法,通过将熔化的金属注入铸型中,经过凝固和冷却,形成所需的零件或产品。
然而,铸造过程中常常会出现一些缺陷,这些缺陷会影响到产品的质量和性能。
本文将介绍几种常见的铸造缺陷,并提供一些预防和解决这些问题的方法。
1. 气孔:气孔是铸造过程中最常见的缺陷之一。
它们通常是由于熔融金属中的气体未能完全排出而形成的。
气孔会降低产品的密度和强度,导致产品易于断裂。
为了避免气孔的产生,可以通过控制熔融金属的气体含量和改进铸造工艺来减少气孔的形成。
2. 疏松:疏松是指铸件中存在的孔洞和空隙。
疏松会降低铸件的强度和耐久性,使其易于变形和破裂。
疏松的形成通常是由于金属液体在凝固过程中不均匀收缩而引起的。
为了解决疏松问题,可以通过优化冷却过程和改进浇注系统设计来增加金属液体的充填和凝固均匀性。
3. 砂眼:砂眼是指铸件表面或内部的突起或凹陷。
砂眼的形成通常是由于铸型材料的不均匀收缩或砂芯的移位引起的。
砂眼会影响到产品的外观和尺寸精度。
为了避免砂眼的产生,可以通过优化铸型和砂芯的设计,控制铸型材料的收缩率,以及合理调整浇注温度和速度来解决这个问题。
4. 缩松:缩松是指铸件中存在的细小裂纹。
缩松会降低铸件的强度和韧性,使其易于断裂。
缩松的形成通常是由于金属液体在凝固过程中体积收缩而引起的。
为了避免缩松的产生,可以通过增加浇注温度和压力,以及优化铸型设计和浇注系统来减少金属液体的收缩。
5. 夹杂物:夹杂物是指铸件中存在的杂质和非金属物质。
夹杂物会降低铸件的强度和耐久性,导致其易于断裂。
夹杂物的形成通常是由于金属液体中的杂质和氧化物未能完全排除而引起的。
为了避免夹杂物的产生,可以通过改进金属液体的净化和过滤系统,以及优化浇注工艺和铸型设计来减少夹杂物的形成。
铸造过程中常见的缺陷包括气孔、疏松、砂眼、缩松和夹杂物。
这些缺陷会影响到铸件的质量和性能,因此在铸造过程中需要采取相应的措施来预防和解决这些问题。
- 1、下载文档前请自行甄别文档内容的完整性,平台不提供额外的编辑、内容补充、找答案等附加服务。
- 2、"仅部分预览"的文档,不可在线预览部分如存在完整性等问题,可反馈申请退款(可完整预览的文档不适用该条件!)。
- 3、如文档侵犯您的权益,请联系客服反馈,我们会尽快为您处理(人工客服工作时间:9:00-18:30)。
BG
3
铸造常见缺陷特点
缺陷名称:砂眼(加工后)
BG
4
铸造常见缺陷特点
缺陷名称:铸字不清 缺陷特点: 产生原因:型腔铸字部分起 模不畅,型砂粒度太粗
BG
5
铸造常见缺陷特点
缺陷名称:披缝 缺陷特点:铸件表面在分模 面处的规则缩陷。 产生原因: 砂型或砂芯分模 面处的飞边未去除
BG
9
铸造常见缺陷特点
缺陷名称:表面缩凹 缺陷特点:铸件表面有缩凹。 产生原因:铸件内部收缩
BG
10
铸造常见缺陷特点
缺陷名称:黑皮 缺陷特点:加工面有加工不 到的地方 产生原因:铸件加工量不足, 铸件变形,夹偏
BG
11
铸造常见缺陷特点
缺陷名称:黑皮(其二)
BG
12
铸造常见缺陷特点
缺陷名称:气孔 缺陷特点:铸件内部或表面 有大小不同的孔眼,孔的内 壁光滑,多呈圆形。 产生原因:砂型太紧或型砂 透气性差;型砂太湿;砂芯 通气孔堵塞;浇注系统不正 确,气体排不出去
BG
6
铸造常见缺陷特点
缺陷名称:表Байду номын сангаас多肉 缺陷特点:铸件表面有多余 的部分。 产生原因:砂型或砂芯的相 应部分掉肉。
BG
7
铸造常见缺陷特点
缺陷名称:表面多肉肉(其 二)
BG
8
铸造常见缺陷特点
缺陷名称:缺肉(缺料) 缺陷特点:铸件表面有缺少 一块,可能导致报废。 产生原因:浇冒口切除时带 掉一块;
BG
13
铸造常见缺陷特点
缺陷名称:缩孔(大而集中 的空洞 ) 缺陷特点:铸件厚、断面处 出现形状不规则的孔眼,孔 的内壁粗糙。 产生原因:冒口设置不正确 ;合金成分不合格,收缩过 大;浇注温度过高;铸件设 计不合理,无法进行补缩
BG
14
铸造常见缺陷特点
缺陷名称:疏松(细小而分 散的空隙) 缺陷特点:铸件厚、断面处 出现形状不规则的孔眼,孔 的内壁粗糙。 产生原因:冒口设置不正确 ;合金成分不合格,收缩过 大;浇注温度过高;铸件设 计不合理
铸铁常见缺陷认识
SATA (KUNSHAN) Q 部
2011 May
BG
1
铸造常见缺陷特点
缺陷名称:砂眼 缺陷特点:铸件内部或表面 有充满砂粒的孔眼,孔形不 规则 产生原因:型砂强度不够或 局部没舂紧,掉砂;型腔、 浇口内散砂未吹净;合箱时 砂型局部挤坏,掉砂;浇注 系统不合理,冲坏砂型
BG
2
铸造常见缺陷特点
BG
15