锣板未锣穿漏锣等异常8D报告格式
8D报告模板 8DReport
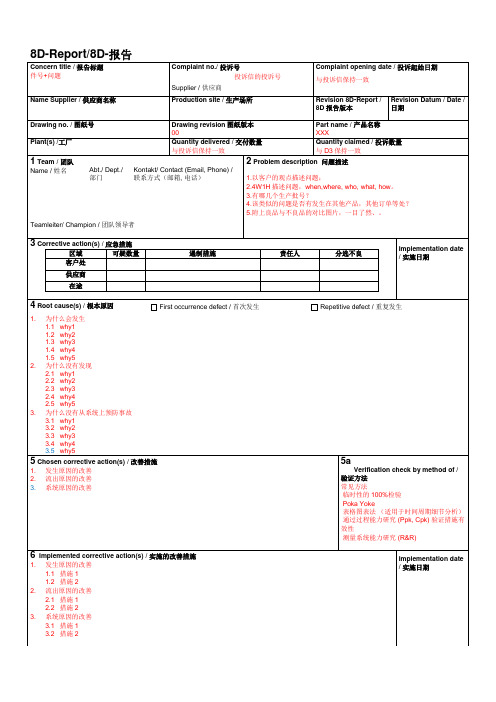
.所有的证据请编号与8D内容对应
例如:
D2.不良照片
D3.挑选指导书/断点标识照片/断点批次信息
D4.原因分析
4.1发生原因的相关作证
4.2流出原因的相关作证
4.3系统原因的相关作证
D6.改善措施
6.1.1措施1的佐证
6.1.2措施2的佐证
6.2.2....
D7预防措施
7.1相关变更文件的截图并圈出变更点
Implementation date/实施日期
Update of Design FMEA no./设计FMEA更新更新的文件需要截图并用红色方框圈出放在附件作为佐证
Update of Process FMEA no./过程FMEA更新
Update of Control plan no./控制计划更新
临时性的100%检验
Poka Yoke
表格图表法(适用于时间周期细节分析)
通过过程能力研究(Ppk, Cpk)验证措施有效性
测量系统能力研究(R&R)
6Implemented corrective action(s)/实施的改善措施
1.发生原因的改善
1.1措施1
1.2措施2
2.流出原因的改善
2.1措施1
Revision 8D-Report/8D报告版本
Revision Datum / Date/日期
Drawing no./图纸号
Drawing revision图纸版本
00
Part name/产品名称
XXX
Plant(s)/工厂
Quantity delivered /交付数量
与投诉信保持一致
Quantity claimed/投诉数量
产品零件断裂8D报告范本

Information:零件Information:供应商D0Symptom(s):问D0 Emergency Response Action(s):紧急响应措施% Effective:有效性实施有效Verification /Validation:D1 Team:Name Dept Phone D2 ProblemStatement:问题陈述李**制造中心13***************质检部14***************技术部15***************技术部16***************销售部13***************制造部14***************技术部15***************锻压车间16************D3 Interim Containment Action(s):临时措施% Effective:有效性实施有效Verification /Validation:验证D4 RootCause(s) and EscapePoint(s):根本原因及逃离点Verification:验证Verification:验证D6Implemented Permanent Corrective Action(s):永久措施实施Verification:验证5月31日在总成装配时,发现********(****)断裂,断裂处有明显锈迹,初步判断存在裂纹螺纹部位断裂,其中有80%左右断口有红锈,因为是在装车过程发生,可初步判定为螺栓本身存在裂纹1、对工装更换制度进行修订,增加“工装维修过程禁止生产”的内容,确保生产过程稳定性;2、对操作工进行培训。
100%1、由于部分工装局部维修,可能仍可继续生产,在制定相关制度时未能考虑完善,导致维修时未能及时停止生产;2、操作工对料头的危害认识不足,且以前采用工装控制,缺少相关培训Date Implemented:实施时间1、已由设备部门对工装维护制度进行修订,要求维修期间停止一切生产活动;2、行政部已组织技术、检验和下料人员进行培训,提高员工的质量意识20**-**-**20**-**-**经对内部4600余只产品进行探伤检验,未发现类似现象% Contribution:贡献率根据断口分析,产品在发生断裂前,内部存在裂纹。
8D报告模板(漏焊焊点8D分析)

RecordNo.:DMQ35271-变更号 ECN No.Date Opened Last Updated Date Closed -2020/8/302020/9/42020/9/28日期Date进度Progress(%)Have you confirmedIs there serious or 姓名Name部门Dept.电话Phone刘以质量3924孙斌焊接3936许六二质量3945孟孙易质量4536数量QTY(NG/OK)日期Date进度20(0/20)2020/8/30100%302020/8/30100%98(0/98)2020/8/30100%验证D 4)Target Date Actual DateTarget DateActual DateReported by:刘顺现场宣导培训按照作业指导书要求进行划记确认,培训后签字确认,班组长及品检确认划记执行状态,------王猛现场培训并要求现场按照附件2要求进行确认,异常时及时汇报,进行在库排查 ------王猛临时措施实施后未反馈不良-按照工序焊接完成后,放入中转台,零件焊接完成后放入成品框执行焊接作业员未对零件进行划记,便直接放入成品框2020/8/302020/8/312020/8/312020/9/2作业指导书要求对零件划记确认后放入成品框,员工未执行生产一个班次430件未发现不良,划记实施后,生产一个班次430件确认无漏焊发生工序焊接完成后,放入中转台, 焊接完成后放入成品框执行工序焊接完成后,焊点划记,确认划记后放入成品框----王猛D8) 肯定团队及个人贡献Recognize Team and Individual Contributions 感谢质量部对问题调查及改善的付出,同时感谢返修部的大力支持发生原因O c c u r流出原因发生纠正流出纠正2020/8/302020/8/302020/8/312020/8/312020/9/2焊接完成后,焊点划记,确认划记后放入成品框D7) 预防再发Prevent Recurrence 发生预防Occurrence Prevention流出预防Escape Prevention文件更新Documents Update横向展开:相似产品/过程改善Similar Production(s)/Process Improve 对机台进行XXXXXXXXXXXXXXXXXXXXXXXXXXXXXXXXXXXXXXXXXXXXXXXX 发生原因Why did the problem occur?允许发生原因Why did quality system allow the problem to occur?流出原因Why did the problem escape?允许流出原因Why did quality system allow the problem to escape?D5) 永久纠正措施选择/验证Choose & Verify Permanent Corrective Action(PCA)纠正措施Permanent Corrective Action(s)有效性验证Effective ValidationD6) 永久纠正措施实施/确认Implement & Validate Permanent Corrective Actions (PCA)发生纠正Occurrence Correction流出纠正Escape Correction2020/8/30作业员作业疏忽未将工序件放入工序中焊接,直接放入成品框导致问题发生 供应商仓库Supplier Warehouse 其他Others :物理的根本原因Physical (Technical) Root Cause体系的根本原因Systemic Root Cause追溯确认Traceability Check地点Location顾客仓库Customer Warehouse 在途In TransportD3) 临时围堵措施Interim Containment Action (ICA)问题汇总汇报问题排查及调查问题改善调查支持是否已经确认了失效零件? Have you confirmed the actual failed part(s)?2020/8/29日中班,焊接区域人员在焊接时发现零件缺少3个焊点,质量部确认为零件漏焊31工序焊点。
空白8D报告范本

签名
实际完成日期
签名 D4
实际完成日期
暂时对策(内容含:1. 应急措施/短期纠正措施, 2.工厂内半成品/ 成品, 在途产品数量, 如何处理, 3.其他型号产品有无此不良, 如 无不良, 原因为何)
预计完成日期:
签名
D5
实际完成日期
长期对策(内容含:1.根治性措施,避免再次发生, 2.有无水平展开) 预计完成日期:
签名
D6 成效追踪(内容含:负责方追踪对策效果,并报告客户)
实际完成日期
预计完成日期:
签名
D7
实际完成日期
成效确认(内容含:QE/QC或生产制程追踪对策效果,客户有无再次 投诉) 预计完成日期:
签名
D8
实际完成日期
关闭此品质问题(连续三批合格或连续两个月验证合格,并有相应 的标准化作业) 预计完成日期:
品质#:
品名: 不良原因责任人分析 姓名 职级 姓名 职级 负责方:
D2
不良描述 ( 不良现象,不良数量,不良率 )
预计完成日期:
签名
D3
实际完成日期
原因分析(内容含:1.为何造成此不良(发生根本原因5WHY);2.不良 品为何流出?为什么生产制造过程没有防止问题发生?为什么品质 保证过程没有起到保护客户作用?为什么没有预测到失效的发生? 预计完成日期:
8D报告模板0

表格编号:QR-QP12-09编号:20150512D1.0D2.0零件名称零件号投诉日期Part Name :Part No.:YBS150-16-06前/YBS150-16-01后Comp. Date :数量缺陷等级首次回复客户信息Qty :Defect Grade :First information to customer :2015.05.15D2.1问题描述/Description of problems :D3.0临时措施/Temporarily measure :效果%Effect%实施日期Implem.date 100%2015.05.13100%2015.05.13D4.0根本原因/Root cause :D5.0长期措施/Corrective long term action(s):负责部门Resp.Dept.实施日期Implem.dateD6.0验证/Verification :验证/Verification :报告人/Report by :李**2015.05.20D7.0预防重复发生的措施/Actions(s) to prevent recurrence负责人responsible 实施日期Implem.date工艺流程表/Process folow chart 失效模式分析/P-FMEA 生产质量指导书/PQIP/PQI王**2015.05.22工艺、技术规范/Process and technic criterion 张**2015.05.22控制计划/CP配套供应商审核/Supplier's changed 内部流程修改/Internal procedure changed 新产品或其他产品/New products or other products 涉及其他生产厂/Involved other plant 备注/Remark D8.0总结/Summarizing关闭日期Close date 组长签字Leader by 检验规范与加工工艺作业指导书已受控下发,各相关部门按照文件要求执行,改善完成。
8D报告的格式

8D报告的格式8D 报告是解决问题的一种有效工具,在很多领域都被广泛应用,特别是在质量控制和问题解决方面。
那到底啥是 8D 报告的格式呢?且听我慢慢道来。
8D 报告一般包括 8 个步骤,就像是闯关打怪,每一步都有特定的任务和要求。
第一步是“成立小组”。
这可不是随便拉几个人凑数就行的。
得找那些对问题有了解、有相关知识和经验的人。
比如说,我们学校曾经有一次教室的投影仪总是出故障,负责解决这个问题的小组里,就有懂电子设备的老师,还有熟悉教室使用情况的后勤人员。
大家各有所长,才能更好地攻克难题。
第二步是“问题描述”。
这一步要把问题说清楚,不能含含糊糊。
比如说投影仪的问题,就得说明是画面模糊、频繁黑屏还是声音有问题等等,越详细越好。
第三步是“临时措施”。
在找到根本原因和长期解决方案之前,得先采取一些临时措施,让情况别变得更糟。
就像投影仪坏了,先借一个临时用着,别耽误上课。
第四步是“确定根本原因”。
这是关键的一步,得深挖问题的根源。
还是投影仪的例子,可能是设备老化、使用不当或者是线路故障等等。
第五步是“长期措施”。
根据找到的根本原因,制定长期有效的解决办法。
比如给投影仪定期维护、培训老师正确使用方法或者更换老化的线路。
第六步是“预防措施”。
得想想怎么防止类似问题再次发生。
比如制定投影仪的使用规范和维护计划。
第七步是“效果验证”。
看看采取的措施有没有效果,问题是不是真的解决了。
第八步是“总结与关闭”。
把整个过程总结一下,该存档的存档,该分享经验的分享经验。
总之,8D 报告的格式就像是一个有条不紊的攻略,按照步骤一步一步来,就能把问题解决得妥妥当当。
在实际应用中,8D 报告格式的好处可多了。
它能让我们的思路更清晰,避免东一榔头西一棒子。
而且,每个步骤都有明确的目标和方法,不会让我们像无头苍蝇一样乱撞。
就像上次我们学校食堂的饭菜质量出了问题,学生们抱怨连天。
学校就按照 8D 报告的格式来解决。
先成立了由食堂工作人员、校领导和学生代表组成的小组。
锣板未锣穿漏锣等异常8D报告格式

Supplier name?:XXXXXX 有限公司Claim origin :Assembly lineClaim opening date : 2015-5-19 供应商生产厂:SV location :-SV Claim Nb. (QN):毒品调查科部分说明:(PCBA 名 称)N/ASupplier Part Number: XXXXXXSV Part Number Ref.:根据不良板子分析,我们有以下结果 -------1 .异常板子为一面OK 一面NG,分析结论为未铳透异常。
2 .通过使用2次元测量,OK 面大小为6.97mm*8.24mm ,NG 面大小是6.53mm*7.94mm 。
3 .经调查主要受T07中0.8mm 刀具加工的。
这已经发生在SV 吗4 - Other similar SV product concerned :?波及性此缺陷可能出现其他SV 同类产品吗YesNo Comments类似的技术的产品:在相同的设备/过程(应考虑所有的生产场地)的产品:V V根据生产履调查不良板子锁定在8-10PCS3 -First analysis / problem description:SV product/process qualification status :产品内部资格呢YesNo Date of qualification?:VYes NoDate of qualification?:Reviewer?(name/function) ■ :XXXX 总经理8D leader (name/function): 品质部XXXX Team members:生产部 XXX 、XXX 、XXX 、XXX 品质部 XXX 、 XXX 、XXX XXXX1 - Detailed description of the problem?:问题描述贵司客户反馈XXXXX 因铳切不良导致零件贴歪,不良图片见下图:此缺陷是已经知道(通过内部的废品分析)吗Yes NoDate and ref. of the lastincident ____________NG 面OK 面为了进一步证实异常发生原因,及波及性我们检查当时生产记录, 请参考附件。
品质异常8d报告怎么写
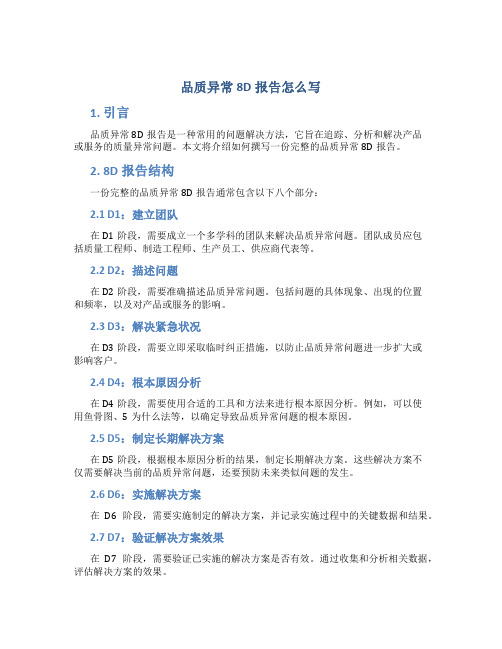
品质异常8D报告怎么写1. 引言品质异常8D报告是一种常用的问题解决方法,它旨在追踪、分析和解决产品或服务的质量异常问题。
本文将介绍如何撰写一份完整的品质异常8D报告。
2. 8D报告结构一份完整的品质异常8D报告通常包含以下八个部分:2.1 D1:建立团队在D1阶段,需要成立一个多学科的团队来解决品质异常问题。
团队成员应包括质量工程师、制造工程师、生产员工、供应商代表等。
2.2 D2:描述问题在D2阶段,需要准确描述品质异常问题。
包括问题的具体现象、出现的位置和频率,以及对产品或服务的影响。
2.3 D3:解决紧急状况在D3阶段,需要立即采取临时纠正措施,以防止品质异常问题进一步扩大或影响客户。
2.4 D4:根本原因分析在D4阶段,需要使用合适的工具和方法来进行根本原因分析。
例如,可以使用鱼骨图、5为什么法等,以确定导致品质异常问题的根本原因。
2.5 D5:制定长期解决方案在D5阶段,根据根本原因分析的结果,制定长期解决方案。
这些解决方案不仅需要解决当前的品质异常问题,还要预防未来类似问题的发生。
2.6 D6:实施解决方案在D6阶段,需要实施制定的解决方案,并记录实施过程中的关键数据和结果。
2.7 D7:验证解决方案效果在D7阶段,需要验证已实施的解决方案是否有效。
通过收集和分析相关数据,评估解决方案的效果。
2.8 D8:预防措施在D8阶段,需要制定预防措施,以确保类似的品质异常问题不再发生。
这些措施可以包括员工培训、流程改进、质量管理体系的完善等。
3. 8D报告撰写要点在撰写品质异常8D报告时,需要注意以下几个要点:3.1 清晰明了的标题报告标题应简洁明了,能够准确概括品质异常问题的核心内容。
3.2 详细描述品质异常问题在报告的第二部分,详细描述品质异常问题,包括具体现象、出现的位置和频率,以及对产品或服务的影响。
尽量使用客观的数据和事实来支持描述。
3.3 分析根本原因在报告的第四部分,进行根本原因分析时,要使用具体的工具和方法,确保分析过程可靠、科学。
- 1、下载文档前请自行甄别文档内容的完整性,平台不提供额外的编辑、内容补充、找答案等附加服务。
- 2、"仅部分预览"的文档,不可在线预览部分如存在完整性等问题,可反馈申请退款(可完整预览的文档不适用该条件!)。
- 3、如文档侵犯您的权益,请联系客服反馈,我们会尽快为您处理(人工客服工作时间:9:00-18:30)。
Supplier name : XXXXXX有限公司Claim origin :
Assembly line
Claim opening date : 2015-5-19
供应商生产厂: SV location : - SV Claim Nb. (QN):
毒品调查科部分说明:(PCBA 名
称)
N/A
Supplier Part Number: XXXXXX SV Part Number Ref. :
Reviewer (name/function): XXXX总经理 8D leader (name/function) :
品质部 XXXX
Team members:
生产部XXX、XXX、XXX、XXX品质部XXX、
XXX、XXX XXXX
1 – Detailed description of the problem :问题描述
贵司客户反馈XXXXX因铣切不良导致零件贴歪,不良图片见下图:
根据不良板子分析,我们有以下结果:
1.异常板子为一面OK一面NG,分析结论为未铣透异常。
2.通过使用2次元测量,OK面大小为 6.97mm*8.24mm,NG面大小是6.53mm*7.94mm。
3.经调查主要受T07Ф0.8mm刀具加工的。
此缺陷是已经知道(通过内部的废品分析)吗?Yes No
Date and ref. of the last
incident
∨
这已经发生在 SV 吗?∨
2 – Other similar SV product concerned : 波及性
此缺陷可能出现其他 SV 同类产品吗?
Yes No Comments
类似的技术的产品:∨根据生产履调查不良板子锁定在8-10PCS 在相同的设备/过程 (应考虑所有的生产场地) 的产品:∨
3 –First analysis / problem description:
SV product/process qualification status :
产品内部资格呢?Yes No Date of qualification : ∨
过程是由 SV 内部限定吗?Yes No Date of qualification : ∨
At which process step, defect was created or should have been detected? created detected
Yes No Yes No Your supplier ∨∨Incoming inspection ∨∨In manufacturing line ∨∨Final inspection / Final test ∨∨Before shipment, storage and delivery (for example when editing labels): ∨∨Transportation : ∨∨Customer production line : ∨∨
OK面NG面
Identified potential root cause for defect :可能原因分析
经分析此坑槽分为两次铣切,通过测量异常品正反面,反面数据刚好与第一次铣切数据吻合,数据为6.53mm*7.94mm (可证实未加工到第二次铣切),正面数据已达到客户需求数据,我们分析可能为刀具偏短引起的,对于此结论我们采用了模拟实验验证;
由于厂内暂无此板在生产,我们使用了覆铜板替代,使用Ф1.8mm刀具按照正常胶粒到刀尖长度20.0mm,将第一次铣切做完,再使用Ф0.8mm刀具将胶粒到刀尖长度设为19.0mm进行铣切,加工后与异常板缺陷基本吻合,以此结论来看,可初步判断为刀具胶粒到刀尖长度不够造成的未铣透异常。
Root cause for non-detection of defect漏检原因
由于异常缺陷属于偏小,大小差异目视检查很难发现,管理者未针对此类异常发生、流出制作专用治具检查,因此,问题流至客户处。
4 –Containment actions : 初步采取行动
Action description Quantity
OK
Quantity
Not OK
-SV 制造线: PCB 电路板 (WIP + 成品) 调查厂内暂无相同品名在生产,其它产品从4月
22日开始已逐步完善使用治具来制中控制及出
货检查.
供应商制造线 (WIP):N\A
在供应商的成品:N/A
其他(过境、中间存储)N/A
安全组件标识标签 (组图) 科技(在纸板上的组件)
的方法吗?
N/A
许多安全组件的第一个直流:送货单 Nb. N/A
5 – Final analysis / validated root cause :最终原因
验证整个过程的根源:执行分析: 5 米 / 何人、何事,哪里时,为何,如何 / 5 为什么 / 制造或生产位置,更改 / 不合格过程、培训、维护
通过减少影响的经过验证的根本原因Root
cause %
负责人进行验证Service or function
为了进一步证实异常发生原因,及波及性我们检查当时生产记录,请参考附件。
插入附件
检查生产记录,我们发现只有1月22日B 班生产116674-01批次断过一次刀,我们确定就是断刀后更换刀具时因胶粒到刀尖长度不够发生的未铣透异常。
(请参见下面的照片)
由于作业员未按照要求作业,本应对每支上机前的刀具需测量长度、直径,而作业员只是测量了直径,忽略了长度测量,因此加上4#铣切设备侦器下测深度设置太深,而对于刀具偏短无法检测出。
(请参考下面的照片)
在这个时候,机器会判断为刀具长度是正常的,就接着开始加工,从而产生了不良。
100%
XXX
胶粒到刀尖长度不够,太短
偏短
OK
测刀状态,下测深度设置太深,引起刀具偏短检测不到。
测刀器未测刀时状态。
6 – Final corrective action plan : 改善
对所有的根本原因,在第 5 章中得到验证的行动。
Pilot
Department
Implementation date &Date
code
规划日期 实施日期 我们将采取以下行动改善此问题:
1. 为了避免操作员再次犯同样错误,我们对刀具管理做了
改进。
改进前: 所有刀具未套胶粒,由作业员自行上套环。
2.
改进后: 我们规范了所有胶粒由物料发放室安排专人压好胶粒并全数测量好长度再发放至现场使用。
3、为了防止再次发生刀具偏短异常发生,我们请来了供应商将测刀深度提高,改进后效果见下图:
3.针对刀具胶粒长度引起的异常我们对作业员进行了教育训练。
请参阅附件。
培训签到表
4.针对异常流出问题。
品质管理将这缺陷已制成图片方式贴于现场最显眼处,并培训工人这一问题的实际发生原因,如何检查此类不良,让所有检查员认识这种异常,请参阅附
件。
出货检查QC培训签
到表
XXX
XXX
XXX
XXX
生产部
工务部
生产部
品质部
2015-3-23 2015-5-23 2015-5-23 2015-5-23 2015-3 -24 2015-5-24 2015-5-23 2015-5-23
(更新控制计划、 过程旅行表和指令表 (包括维护计划) (更新图纸和规格 (包括关键的特征,… …)
胶粒由物料室安
排专人将胶粒套
好,并全数测量
长度。
刀具未套胶粒
测刀器测刀时深度提高了,刀具偏短可以检测出。
测量用于检查上述行动的成效,及相关指标:负责验证计划日期: 行动效率是/否和日期7 – Preventive actions in order to avoid recurrence on other products:防止再发
操作应该是在同类产品中的地方和进程(Cf 第 2 章)。
包含在其他制造工厂吗?
Yes No Y
操作(和相关的产品)的说明负责部门Implementation date
Planned Realized 我司将永久执行上诉改善对策,并不定时安排人员进行查
核,是否有按照规范在执行,同时我司还专为防止此类异常,特别制作了治具来制中监控及出货前全数检查,见附件治具样板图片XXX 品质部2015-4-
22
2015-4-22
治具图片
8 – capitalization actions: 是否有文件变更
Actions required : YES NO (验证 FMEA 方法的有效性)√(验证过程审计方法的有效性)√(处理设计:设计准则、标准的技能、防错、标准设备规格……)√(产品设计:设计准则,技能引用列表,……)√(在设计上的供应商管理,使市场阶段(产品验证、审核、资格,……))√(检查有效性的产品的过程资格,加大管理的制造业转移,……)√(审查维护组织)√(组织原因) √(缺乏严格,缺乏纪律) √
(审查计划控制、生产旅行表和说明文件(包括维修范围): √
Measurement date of ALL corrective actions and closure date : 2015-05-23 用于验证的负责人:XXX
Systematic dispatch to all the concerned persons。