生石灰及白云石的焙烧工艺分析
白灰流程简介(鞍钢)

白灰(轻烧白云石)煅烧简介按照鞍钢集团公司建设要求,一期建设4条公称产能900t/d的回转窑,3条回转窑用于生产活性石灰(其中任意1条回转窑均可以换烧白云石),另一条回转窑用于轻烧白云石。
二期再建设3条同规模的回转窑,最终形成7座回转窑的生产布局。
一、工艺流程石灰石(白云石)由皮带输送机送入预热器顶部料仓,然后由溜料管将石灰石(白云石)分布到竖式预热器内,石灰石(白云石)进入预热器后经窑尾约1100℃的烟气预热,约有30%左右的石灰石(白云石)在预热器中被分解,经过预热的物料由液压推杆推出,经转运溜槽进入回转窑中,物料在回转窑内经过焙烧分解,热烟气进入预热器。
烟气在预热石灰石(白云石)后经过袋式除尘器除尘由排烟机排入大气。
焙烧好的石灰(白云石)进入竖式冷却器,由底部送入的冷空气冷却后通过电磁振动给料机排出至集料斗,再经成品皮带运输机送往成品库。
冷空气在冷却器内冷却物料的同时被加热,经窑头罩进入窑内,作为助燃空气焙烧石灰石(白云石)。
工艺流程图如下:1、炼钢用石灰、烧结用石灰工艺流程2、轻烧白云石工艺流程二、主要设备煅烧石灰的设备主要由回转窑系统、竖式预热器、竖式冷却器、燃烧系统、除尘排烟系统组成。
(一)回转窑系统1、回转窑回转窑筒体全长70 m,公称内径4900mm。
窑的进料、出料端都为锥形。
窑的正常转速为1.086r/min,最高转速可以达到1.3 r/min,辅助传动转速为0.1r/min。
窑的倾斜度为3.5%。
从窑头方向看,窑逆时针方向旋转。
图1 回转窑筒体2、主传动装置主传动装置驱动窑体连续回转。
主传动装置是由一台交流变频电动机、减速机等组成。
主电机的速度是可调的,通过调节电机的转速来调节回转窑的转速。
3、支撑装置支撑装置是用来支撑整个回转部分的重量,并使筒体及滚圈能够在托轮上平稳转动。
采用两档支撑。
图2 支撑装置4、液压挡轮装置液压挡轮用来驱使轮带带动筒体向上或向下窜动。
由上挡轮和下挡轮组成。
生石灰及白云石的焙烧工艺分析

生石灰及白云石的焙烧工艺分析
石灰及白云石是使用最广泛的两种建筑材料,它们可以用于制造建筑装饰材料、建筑材料和建筑砌块等。
石灰及白云石的焙烧工艺是制造这两种材料的重要环节。
本文通过对石灰及白云石的焙烧工艺进行分析,从而了解这种工艺如何为我们提供高品质的石灰及白云石产品。
石灰及白云石的焙烧工艺相对来说比较复杂,主要包括混合、压模、焙烧三个过程。
首先,我们将选好的原材料,如石灰、白云石、粘土等混合,以便调整物料的性质,确保产品性能的一致性和稳定性。
其次,我们将混合物压入模具中,以制得所需的形状,然后将模块放入焙烧炉中,在一定的温度和时间下经过升温、维持、缓冷三个阶段的烧制,使物料内部产生一定的化学变化,从而获得高品质的石灰及白云石产品。
为了使石灰及白云石达到最佳性能,考虑到焙烧过程中温度的控制以及烧制的时间等因素也很重要。
一般情况下,石灰及白云石的焙烧温度在900℃和1120℃之间,焙烧时间一般在1-2小时。
压模混合物的温度必须在400℃以下,以免在烧制过程中造成过热破坏。
此外,放物也是焙烧工艺中需要注意的一个重要问题。
煅烧白云石的析气性能及其影响因素研究

煅烧白云石的析气性能及其影响因素研究白云石是一种常见的石灰岩,其石化过程被广泛应用于建筑材料、化学工业等领域。
煅烧白云石是将白云石石料加热至高温,通过石料的化学、物理性质发生变化来制造石灰的过程。
煅烧白云石的析气性能对于石灰生产的效率、产品质量以及对环境的影响具有重要意义。
本文将探讨煅烧白云石的析气性能以及影响这一过程的因素。
首先,我们来了解煅烧白云石的析气性能。
煅烧白云石的主要化学反应是碳酸钙分解为氧化钙和二氧化碳。
这个反应在高温下进行,通常在800到900摄氏度之间。
在煅烧过程中,碳酸钙分解会放出大量的二氧化碳气体,这就是白云石的析气性能。
煅烧白云石的析气性能对于石灰生产的效率起着关键作用。
高析气性能意味着石料能够更高效地释放二氧化碳气体,从而提高生产效率。
研究表明,影响析气性能的因素主要包括石料的来源和性质、煅烧过程的温度和时间以及添加剂的使用。
好的石料来源通常含有较高的纯度和较少的杂质,这有利于提高析气性能。
石料的粒度大小、晶体结构以及石料与煅烧温度的匹配也会对析气性能产生影响。
其次,影响煅烧白云石析气性能的因素还包括石料的化学成分。
石料的化学成分决定了其析气性能。
主要影响因素如下:1. 石料中的杂质含量:石料中的杂质含量会影响石料的析气性能。
例如,含有过多的硅酸盐、硫酸盐等杂质会降低析气性能。
2. 石料中钙含量的变化:石灰石石料中的钙含量对析气性能有直接影响。
一般来说,含钙量较高的石料具有较好的析气性能。
3. 石料的颗粒大小:石料颗粒的大小与析气性能之间存在一定的关联。
较小的颗粒通常具有更好的析气性能。
此外,煅烧过程中的温度和时间也会对析气性能产生重要影响。
较高的煅烧温度有助于提高析气性能,但过高的温度可能会导致过烧,从而降低析气性能。
同时,适当的煅烧时间也是确保石料充分分解的关键。
在煅烧过程中,添加剂的使用也是影响析气性能的重要因素。
添加剂可以调节石料和气氛之间的反应,从而改善析气性能。
煅烧白云石的工艺参数优化及影响因素分析

煅烧白云石的工艺参数优化及影响因素分析白云石,又称大理石或大理石石灰岩,是一种常见的建筑材料和装饰石材。
在将白云石用于建筑或装饰行业之前,需要经过一系列工艺步骤,其中最重要的过程之一就是煅烧。
煅烧是指将白云石在高温下进行加热,在此过程中发生化学反应,使石材产生颜色变化及改善物理性能的方法。
本文将对白云石的工艺参数优化以及影响因素进行分析。
煅烧白云石的目的在于改变其颜色、提升硬度和耐久性,以满足建筑或装饰方面的需求。
工艺参数的优化非常重要,因为它直接影响到石材的质量和性能。
下面将对影响煅烧效果的主要因素进行探讨。
首先,煅烧温度是影响石材质量的重要因素之一。
通过调整煅烧温度,可以使白云石发生颜色变化,并且产生不同的物理性能。
一般来说,较高的煅烧温度可以增加石材的硬度和耐久性,但同时也会增加能耗和生产成本。
因此,在确定煅烧温度时,需要综合考虑质量要求和经济效益,并进行实验验证以确定最佳温度范围。
其次,煅烧时间是影响石材质量的另一个重要因素。
过长或过短的煅烧时间都会导致石材质量下降。
煅烧时间过长,可能导致白云石中的矿物质过度变质,影响石材的外观和性能;而煅烧时间过短,则可能无法完全改变石材的颜色和物理性能。
因此,需要通过试验和实践来确定最适宜的煅烧时间范围,以保证石材质量的稳定性和一致性。
此外,煅烧气氛也是影响石材质量的重要因素之一。
一般而言,煅烧过程中需要提供适当的气氛环境,以控制石材中的化学反应。
在煅烧过程中,氧化性气氛和还原性气氛都可能用于不同的煅烧效果。
氧化性气氛可以使白云石产生各种不同颜色的变化,而还原性气氛可以提高石材的硬度和耐久性。
选择合适的煅烧气氛需要根据具体需求和实际情况作出调整。
此外,煅烧速率也是影响石材质量的因素之一。
过快的煅烧速率可能导致石材内部温度不均匀,从而产生开裂或其他质量问题。
因此,为了保证石材的质量和一致性,控制煅烧速率是十分重要的。
最后,煅烧白云石的影响因素还包括石材的化学成分、结构特性、初始状态等。
关于白云石的煅烧与生产与性能介绍
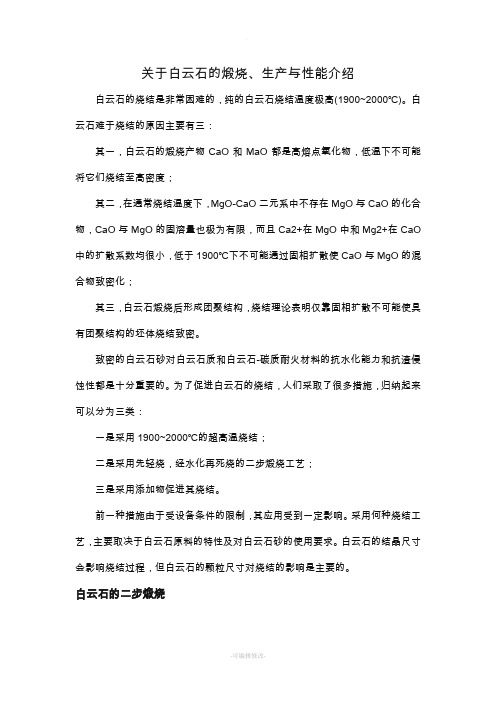
关于白云石的煅烧、生产与性能介绍白云石的烧结是非常困难的,纯的白云石烧结温度极高(1900~2000℃)。
白云石难于烧结的原因主要有三:其一,白云石的煅烧产物CaO和MaO都是高熔点氧化物,低温下不可能将它们烧结至高密度;其二,在通常烧结温度下,MgO-CaO二元系中不存在MgO与CaO的化合物,CaO与MgO的固溶量也极为有限,而且Ca2+在MgO中和Mg2+在CaO 中的扩散系数均很小,低于1900℃下不可能通过固相扩散使CaO与MgO的混合物致密化;其三,白云石煅烧后形成团聚结构,烧结理论表明仅靠固相扩散不可能使具有团聚结构的坯体烧结致密。
致密的白云石砂对白云石质和白云石-碳质耐火材料的抗水化能力和抗渣侵蚀性都是十分重要的。
为了促进白云石的烧结,人们采取了很多措施,归纳起来可以分为三类:一是采用1900~2000℃的超高温烧结;二是采用先轻烧,经水化再死烧的二步煅烧工艺;三是采用添加物促进其烧结。
前一种措施由于受设备条件的限制,其应用受到一定影响。
采用何种烧结工艺,主要取决于白云石原料的特性及对白云石砂的使用要求。
白云石的结晶尺寸会影响烧结过程,但白云石的颗粒尺寸对烧结的影响是主要的。
白云石的二步煅烧二步煅烧工艺是生产高纯度高密度镁砂时常用的工艺方法。
对白云石而言,二步煅烧对降低白云石的烧结温度和提高白云石砂体积密度的作用也是非常有效的,见表3-5-6。
白云石经1000℃左右轻烧后分解为CaO和MgO,物料比表面积增大,晶格缺陷多,增大了烧结的推动力。
但是,轻烧白云石仍保留原母盐一一白云石的颗粒形貌(即团聚体)结构疏松,含有大量气孔。
轻烧白云石中的气孔有两种类型:一是团聚体内MgO和CaO粒子围成的小气孔(半径为0.01~0.08pm),二是团聚体之间围成的大气孔(半径为0.08~4.0μm)。
气孔阻碍了白云石的烧结,须设法破坏团聚体。
白云石轻烧后的细磨及水化均能有效地破坏团聚体,使白云石易于烧结,这是二步煅烧工艺能降低白云石烧结温度的原因。
轻烧白云石工艺介绍

松绳开关
电机
制动器 变频控制器 主令控制器
卷扬提升设备构成
卷扬提升设备主要由电机变频控制器、卷扬电机、 对轮抱闸(制动器)、减速机、钢绳、卷筒、主令 控制器、编码器、斜桥轨道、上料小车、配重小车 及限位报警装臵、制动电阻等组成。 变频器能够控制卷扬电机正反(上下)运行,能 够控制电机运行速度(高低速),判断电机过载。 主令控制器能够根据编码器的编码值来控制小车 上限位、下限位、加速位、减速位,能够判断小车 超速、溜车等现象。
窑规格及几个基本定义
窑的表示:竖窑一般以其有效容积的大小表示,比如250m3石 灰竖窑;回转窑一般以直径与长度进行表示,比 如∮3.6×55m。 竖窑内径:指剔出耐火材料厚度后的直径。我车间竖窑内径 为4米。 有效高度:窑底至加料面的高度。我车间竖窑有效高度为22米 高径比:竖窑有效高度与竖窑直径之比,我车间为5.5
窑规格及几个基本定义
竖窑利用系数:是指每天实际产量与竖窑有效容积之比 。我 车间竖窑的设计利用系数为0.85(全灰)。 窑壁效应:由于竖窑中物料的堆积方式不同,将明显影响气体 流动的过程。在靠近窑壁处,物料与窑壁之间的孔 隙率较物料之前堆积的孔隙率大,使气体容易从周 边通过,即在窑的同一断面上,周边的气,这一现象称为窑壁效应。
轻烧白云石生产工序单元
1、原(燃)料单元 2、混配单元 3、卷扬提升上料单元 4、竖窑煅烧控制单元 5、出灰及成品筛分单元 6、引风除尘单元 7、报警及视频监控单元
PLC控制系统组成
上位机(Wincc)
PLC300(Step7)
PLC200
数字量模块
称重模块
模拟量模块
主 令 控 制 器
探 测 料 位 计
生石灰的原料组成和生产工艺流程

生石灰的原料组成和生产工艺流程
本文主要注重介绍生石灰的原料组成和生产工艺流程:
生石灰的原料:凡是以碳酸钙为主要成分的天然岩石,如石灰岩、白垩、白云质石灰岩等,都可用来生产石灰。
将主要成分为碳酸钙的天然岩石,在适当温度下煅烧,排除分解出的二氧化碳后,所得的以氧化钙(CaO)为主要成分的产品即为石灰,又称生石灰。
在实际生产中,为加快分解,煅烧温度常提高到1000~1100℃。
由于石灰石原料的尺寸大或煅烧时窑中温度分布不匀等原因,石灰中常含有欠火石灰和过火石灰。
欠火石灰中的碳酸钙未完全分解,使用时缺乏粘结力。
过火石灰结构密实,表面常包覆一层熔融物,熟化很慢。
外贸服装由于生产原料中常含有碳酸镁(MgCO3),因此
2~
4
——仅供参考。
利用石灰竖炉煅烧白云石工业实践

C3 0。白云石在 7 0 4 ℃时一次失重 , 3  ̄70 产生部分
M0 90 3  ̄ g ; 1  ̄90 C时二 次失重 ,O0 I0  ̄ C以前分 解物 称苛性 白云石 , 10 "时重新结晶烧结[ 在 40 C 1 】 。就是 说 白云石分解分两个阶段 :首先 M C。 gO 分解形成 MO g ,然后 CC 3 a O分解形成 C O a 。当 7 0 4 "时 3  ̄70 C MO形成 ;升温到 9 0 3 ℃时 C C3 g 1  ̄90 aO 分解形成
及现有设备进行分析 ,依据炼钢及烧结对熔剂的 要求 , 结合 已掌握的白云石物理和化学特性, 出 提
暂设定焦 比:.% 72 。 竖炉利用系数按设计 0 8 . 设定。 根据竖炉现在的漏风情况,煅烧石灰石时空 气过剩系数 的确 定,依据焦炭使用量设定空气过
剩系 数 为 10 。 .5
进行石灰石和 白云石转换煅烧 。并根据原料结构变更期间搜集统计的数据及实际生产情 况加 以分析总结, 出 提
了相应的控制方法和措施 , 以达到换烧 白云石后生产 操作 的可控性 。 关键词: 竖炉; 煅烧 ; 白云石 ; 工业实践
1前言
在 以固体 ( 焦炭) 作为燃料 的机械化竖炉 , 多 用于煅烧生石灰。安钢烧结厂 白灰车间, 投量 的结果。此 时, 炉膛内白云石对石灰石的替换即将
完成 。
52 . 调整期操作
从 白云石和石灰石的煅烧温度来看 ,两种矿 石煅烧温度差异较大。在投入 白云石之前焦 比已
- 1、下载文档前请自行甄别文档内容的完整性,平台不提供额外的编辑、内容补充、找答案等附加服务。
- 2、"仅部分预览"的文档,不可在线预览部分如存在完整性等问题,可反馈申请退款(可完整预览的文档不适用该条件!)。
- 3、如文档侵犯您的权益,请联系客服反馈,我们会尽快为您处理(人工客服工作时间:9:00-18:30)。
关键词:关键词1:石灰成分;关键词2:生产过程;关键词3:注意点;关键词4:化治和经济已处崩溃状态,问题成堆积重难返。自小平同志主持国务院工作后,大刀阔斧地全面进行整顿,首先要抓经济建设,让全国人民能看到一些希望,我国的工业水平与国外中等水平国家都相差太远了,尤其作为人口众多的大国来说,几乎已到了自取亡国的程度,钢铁工业是发展整个工业的基础,因此小平同志加强国家工业建设狠抓不放,并作了国家全面发展规划.
此外,焙烧分厂注重强化全员设备管理,以设备稳定促产能提高。除强调操作工密切关注设备状态外,他们还建立考评制度、日检制度及操作、点检沟通协调机制,全天候确保设备稳定运行。上半年,设备故障时间同比下降15小时,有效作业率由去年的91%提高到92.3%,均创历史同期最好水平。
二、企业(公司)简介
(一)公司简介
(二)湛江钢铁项目简介
宝钢广东湛江钢铁基地项目由宝钢投资建设,按照一次规划、分布实施的原则建设千万吨级钢铁基地.
焙烧分厂以稳定生产为前提,围绕影响产能、物流的瓶颈寻求突破。以往每年夏季高温期间,粉石灰成品温度过高易造成抽取产品的槽罐车橡皮管和密封装置变形、损坏,需频繁更换备件或停产降温,产能受到影响。焙烧分厂凭借自主集成能力和经验,经过大量试验,于今年高温来临前完成了技改项目,使高温期间产品温度得以改善,6月份平均日产达430吨,超设计能力30%。针对设备堵料时间长的老大难问题,焙烧分厂强化生产跟踪管理和责任意识,努力提高物料通过管道的速度,使物流衔接更为顺畅,据统计,上半年堵料时间同比下降了20小时。
生石灰及白云石的焙烧工艺分析
摘 要:所谓石灰焙烧,从化学上来说就是把石灰石的主要成分CaCO3(碳酸钙),加热分解成CaO(氧化钙)及CO2(二氧化碳),并适当地控制CaCO3的分解率及CaO的结晶成长。为此,在焙烧炉中,必须给予石灰石以适当的温度及有效的热量。石灰石的分解温度为900℃,分解热约为420千卡/公斤,随着石灰石原料来源、纯度、颗粒大小不同,其分解过程中。CO2分压上升及向石灰石分解面的热传递也不同,因此,实际制造生石灰时,采用不同的石灰石原料,分解方法也不一。随着石灰炉的改进,生产过程也不断变化。当初,在使用固体燃料的小型炉中,即便是作为原材料的石灰石也是很不重视的,品质和粒度只是粗略的考虑,石灰石仅用筛子把某一粒度以下筛去,就原封不动地装入炉内。关于炉子操作也几乎没有仪表装置,全靠具有丰富经验的熟练工掌握。这样的操作过程,随着大型炉,流体燃料炉的采用及随着机械化发展,生产过程也复杂起来了。可以说,石灰的反应能力对碱性氧气炼钢法,具有特殊的意义,特别是在吹炼含磷较高的生铁时,更显示出反应能力的重要性。在这样的吹炼过程中,石灰的溶解机能起着重大的作用。即石灰的溶解速度是决定冶炼时间,吹炼速度的重要因素。确认生石灰反应性的试验方法,有粗粒滴定方法及ASTM法,但作为日常检查使用时,前者比较多,粗粒滴定法是实际使用中的一种简便方法,
宝钢以钢铁为主业,生产高技术含量、高附加值钢铁精品,已形成普碳钢、不锈钢、特钢三大产品系列。2011年产量为4427万吨,位列全球钢铁企业第四位,利润总额181.5亿元,盈利居世界钢铁行业第二位。钢铁产品通过遍布全球的营销网络,在满足国内市场需求的同时,还出口至日本、韩国、欧美等四十多个国家和地区,广泛应用于汽车、家电、石油化工、机械制造、能源交通、金属制品、航天航空、核电、电子仪表等行业。围绕钢铁主业的发展需求,宝钢还着力发展相关多元产业,重点围绕钢铁供应链、技术链、资源利用链,加大内外部资源整合力度,提高综合竞争力及行业地位,形成了资源开发及物流、钢材延伸加工、工程技术服务、煤化工、金融投资、生产服务等六大相关产业板块,并与钢铁主业协同发展。
公司全部装备技术建立在当代钢铁冶炼、冷热加工、液压传感、电子控制、计算机和信息通讯等先进技术的基础上,具有大型化、连续化、自动化的特点。通过引进并对其不断进行技术改造,保持着世界最先进的技术水平。
公司采用国际先进的质量管理,主要产品均获得国际权威机构认可。通过BSI英国标准协会ISO9001认证和复审,获美国API会标、日本JIS认可证书,通过了通用、福特、克莱斯勒等世界三大著名汽车厂的QS 9000贯标认证,得到中国、法国、美国、英国、德国、挪威、意大利等七国船级社认可。
今年以来,宝钢分公司炼钢厂焙烧分厂在人员、设备未变的情况下,通过改善成品温度和设备堵料等措施,使悬浮窑产量实现新的增长,上半年共生产粉石灰7.19万吨,同比增长1600多吨,为确保企业物流平衡作出了贡献。
四号高炉投产以来,对粉石灰需求量激增,悬浮窑产能也成为宝钢分公司物流平衡的关键点之一。为此,焙烧分厂在多年稳定生产、产能趋于饱和的基础上,自我加压,向提升产能发起挑战。
宝钢集团公司(简称“宝钢”)是中国最大、最现代化的钢铁联合企业。宝钢股份以其诚信、人才、创新、管理、技术诸方面综合优势,奠定了在国际钢铁市场上世界级钢铁联合企业的地位。《世界钢铁业指南》评定宝钢股份在世界钢铁行业的综合竞争力为前三名,认为也是未来最具发展潜力的钢铁企业。 公司专业生产高技术含量、高附加值的钢铁产品。在汽车用钢,造船用钢,油、气开采和输送用钢,家电用钢,不锈钢,特种材料用钢以及高等级建筑用钢等领域,宝钢股份在成为中国市场主要钢材供应商的同时,产品出口日本、韩国、欧美四十多个国家和地区。