失效模式与后果分析FMEA(PPT 71页)
合集下载
FMEA的失效模式、起源与小组成员PPT(84张)
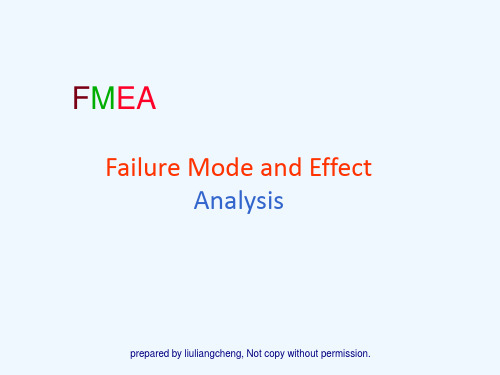
• FMEA在过程开发中运用太迟或没有改进产品/过 程循环发展
• 在产品寿命期内FMEA没有被重新评定和更新, 没有像动态工具一样被加工
• FMEA被认为太复杂或花费太多的时间
prepared by liuliangcheng, Not copy without permission.
FMEA 的起源
Introduction
prepared by liuliangcheng, Not copy without permission.
什么是 FMEA ?
FMEA 是先期质量策划中评价潜在失效模 式及其起因的一种工具
• 依照其发生在失效的风险优先排列并采取行 动排除或降低其发生的
• 为未来使用和持续改进提供文件化的预防经 验/方法
PFMEA 开始于基本的操作方法讨论完成时,完成时间早于生产 计划制定和生产批准之前
prepared by liuliangcheng, Not copy without permission.
FMEA 的关键术语
• 顾客输入 • 小组—小组的选择(横向功能小组) • 等级—等级的确定 • 风险评估 • 设计过程 • 生产过程
FMECA • Failure Mode Effects and Criticality Analysis
• 1950’s 起源于宇航和美国军方 • 对关注的问题加以分类和排列 • 将评定结果作为预防的目标
• 坚持安全的观点
prepared by liuliangcheng, Not copy without permission.
典型的FMEAs
系统
设计
过程
部件 子系统 主系统
部件 子系统 主系统
人 机 料 法
• 在产品寿命期内FMEA没有被重新评定和更新, 没有像动态工具一样被加工
• FMEA被认为太复杂或花费太多的时间
prepared by liuliangcheng, Not copy without permission.
FMEA 的起源
Introduction
prepared by liuliangcheng, Not copy without permission.
什么是 FMEA ?
FMEA 是先期质量策划中评价潜在失效模 式及其起因的一种工具
• 依照其发生在失效的风险优先排列并采取行 动排除或降低其发生的
• 为未来使用和持续改进提供文件化的预防经 验/方法
PFMEA 开始于基本的操作方法讨论完成时,完成时间早于生产 计划制定和生产批准之前
prepared by liuliangcheng, Not copy without permission.
FMEA 的关键术语
• 顾客输入 • 小组—小组的选择(横向功能小组) • 等级—等级的确定 • 风险评估 • 设计过程 • 生产过程
FMECA • Failure Mode Effects and Criticality Analysis
• 1950’s 起源于宇航和美国军方 • 对关注的问题加以分类和排列 • 将评定结果作为预防的目标
• 坚持安全的观点
prepared by liuliangcheng, Not copy without permission.
典型的FMEAs
系统
设计
过程
部件 子系统 主系统
部件 子系统 主系统
人 机 料 法
失效模式与后果分析FMEA(PPT 71页)

FMEA是一种可靠性设计的重要方法。它实际上是
FMA(故障模式分析)和FEA(故障影响分析)的组
合。它对各种可能的风险进行评价、分析,以便在现
有技术的基础上消除这些风险或将这些风险减小到可
接受的水平。及时性是成功实施FMEA的最重要因素
之一,它是一个“事前的行为”,而不是“事后的行
为”。为达到最佳效益,FMEA必须在故障模式被納
有无定单期间追踪的效益
02.09.2019
何为PFEMA?
一个系统化的行动团队,目的是:
确定和评价过程的潜在失效和后果
确定可以消除或减少潜在失效发生机会的措施 过程文件化 - 确定为了使客户满意,一个过程必须要做的事
过程
尽早发现问题的过程。
解决已存在问题的过程
02.09.2019
PFMEA简介
追求整体的效益,通过系统集成的理念,从总体上保证实现零缺陷; 不制造缺陷、不接受缺陷,不传递缺陷,不向市场和顾客提供有缺陷的产品与服务; 根据质量体系的要求,每项工作都应建立规章制度和业务流程,按规定程序 实施管理,责任落实到位,不允许存在失控的漏洞; 对已产生的缺陷采取改正的措施,保证差错不延续并提前消除; 必须有产品或工作可能产生的缺陷采取预防的措施,事先排除可能产生缺陷 的各种成因和例外; 人人都是管理者,管理以人为本,充分发挥每个员工的主观能动性,以零缺陷 的工作态度和行为保证产品、经营的零缺陷;
02.09.2019
FMEA历史
虽然工程技术人员早已在其设计和制造过程中应用 了类似FMEA形式的分析方法,但第一次正式地应 用FMEA技术则是六十年代中期航天工业的一项革 新:
FMEA is most effective when it occurs before a design is released rather than “after the fact”. focus should be on failure prevention not detection. As such, FMEA is often a standard process used in the development of new products.
FMEA潜在失效模式及后果分析(PPT 77张)
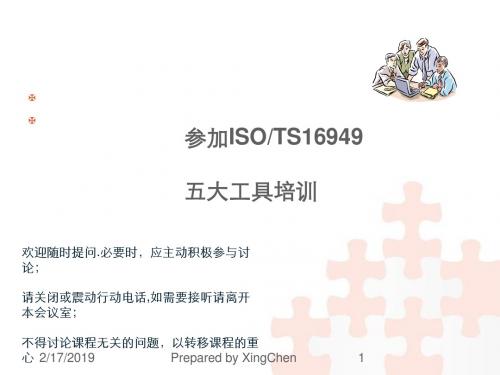
后果是 什么? 功能、特 性或要求 是什么?
有多 糟糕 ? 起因是 什么? 发生的频 率如何?
能做些什么? -设计更改 -过程更改 -特殊控制 -标准、程序或 指南的更改
会是什么问题? -无功能 -部分功能/功能 过强/功能降级 -功能间歇 -非预期功能
2/17/2019
怎样能得到 预防和探测? 该方法在 探测时 有多好?
2/17/2019
Prepared by XingChen
10
2/17/2019
Prepared by XingChen
11
下图描述了进行 FMEA的顺序。这并不是简单地填写一下表
格,而是要理解FMEA的过程,以便消除风险并策划适宜的 控制方法以确保顾客满意。
2/17/2019
Prepared by XingChen
24
8)核心小组 列出有权确定和/或执行任务的责任部门的名称和个人的姓名(建议所 有参加人员的姓名、部门、电话、地址等都应记录在一张分发表上。) 9)项目/功能 填入被分析项目的名称和其他相关信息(如编号、零件级别等)。利 用工程图纸上标明的名称并指明设计水平。在初次发布(如在概念阶 段)前,应使用试验性编号。用尽可能简明的文字来说明被分析项目 满足设计意图的功能,包括该系统运行环境(规定温度、压力、湿度 范围、设计寿命)相关的信息(度量/测量变量)。如果该项目有多种 功能,且有不同的失效模式,应把所有的功能单独列出。
16
DFMEA考虑的内容:
设计 FMEA 针对设计意图并且 假定该设计将按此意图进行生 产/装配。 制造或装配过程中可能发生的 潜在失效模式和 / 或其原因 / 机 理不需、但也可能包括在设计 FMEA当中。 当这些未包含在设计 FMEA 当 中时,它们的识别、后果及控 制应包括在过程FMEA当中。
FMEA失效模式及后果分析 (ppt 88页)
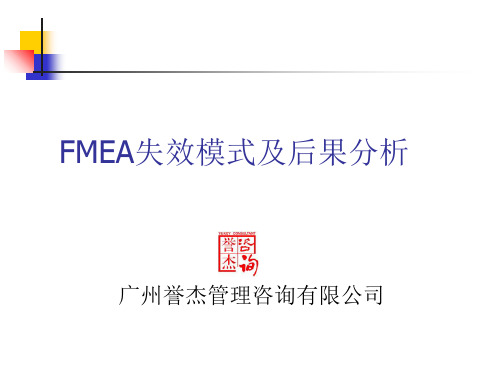
DFMEA包括任何由设计导致的、在制造和装配 过程中发生的潜在失效模式和要因。
设计更改可以减轻失效模式如防错设计
2.1FMEA的质量目标
设计改进:以此为主要目标 高风险失效模式:重视并有可实施的措施计划 分析/开发/确认或DVP&R/CP:对FM进行考虑 接口:综合及衔接框图中各种FM 吸取的教训:作为FM的输入如保修费及如回 KPC及KCC:适用时在相关过程中选择 小组:选择合适的人选(有培训)和组织者 文件:文件化要完全填写 时间性(目标:The sooner The Better)
FMEA开发小组团队(1/2)
和期
FMEA开发小组团队(2/2)
FMEA范围的确定
功能模式QFD,方框图,界面图,PFC,特性矩 阵图,示意图,PFC工艺流程图,BOM
FMEA分析方式:硬件分析法(由下至上)
例:发动机的节流阀
FMEA分析方式:功能分析法(由上至下)
例:压缩空气系统功能结构(由上而下)
2.2 DFMEA的输入(设计框图)
框图是D-FMEA分析的开始,了 解系统,子系统及零部件
框图例2
2.3 DFMEA开发必备条件
DFMEA必须聚集于最终交付顾客的设计产品,其过程反 映顾客或组织的R&D过程
DFMEA应在了解所需分析的系统、子系统、零部件的开 发信息,功能要求和特性的情况下开始,至少包括:
可靠性方块图
定义FMEA的客户(4个层次)
编写FMEA的步骤
第一步(1)确定“功能”, 要求和规范, (2)识别失效模式, (3)识别失效模式后果, (4)评估失效后果的严重度S(从1到10), (5)提出消除失效模式的建议措施
第二步 (1)识别失效模式的所有潜在原因, (2)评估失效原因发生的频度(从1到10), (3)提出消除失效原因的建议措施
设计更改可以减轻失效模式如防错设计
2.1FMEA的质量目标
设计改进:以此为主要目标 高风险失效模式:重视并有可实施的措施计划 分析/开发/确认或DVP&R/CP:对FM进行考虑 接口:综合及衔接框图中各种FM 吸取的教训:作为FM的输入如保修费及如回 KPC及KCC:适用时在相关过程中选择 小组:选择合适的人选(有培训)和组织者 文件:文件化要完全填写 时间性(目标:The sooner The Better)
FMEA开发小组团队(1/2)
和期
FMEA开发小组团队(2/2)
FMEA范围的确定
功能模式QFD,方框图,界面图,PFC,特性矩 阵图,示意图,PFC工艺流程图,BOM
FMEA分析方式:硬件分析法(由下至上)
例:发动机的节流阀
FMEA分析方式:功能分析法(由上至下)
例:压缩空气系统功能结构(由上而下)
2.2 DFMEA的输入(设计框图)
框图是D-FMEA分析的开始,了 解系统,子系统及零部件
框图例2
2.3 DFMEA开发必备条件
DFMEA必须聚集于最终交付顾客的设计产品,其过程反 映顾客或组织的R&D过程
DFMEA应在了解所需分析的系统、子系统、零部件的开 发信息,功能要求和特性的情况下开始,至少包括:
可靠性方块图
定义FMEA的客户(4个层次)
编写FMEA的步骤
第一步(1)确定“功能”, 要求和规范, (2)识别失效模式, (3)识别失效模式后果, (4)评估失效后果的严重度S(从1到10), (5)提出消除失效模式的建议措施
第二步 (1)识别失效模式的所有潜在原因, (2)评估失效原因发生的频度(从1到10), (3)提出消除失效原因的建议措施
潜在失效模式及后果分析(FMEA)
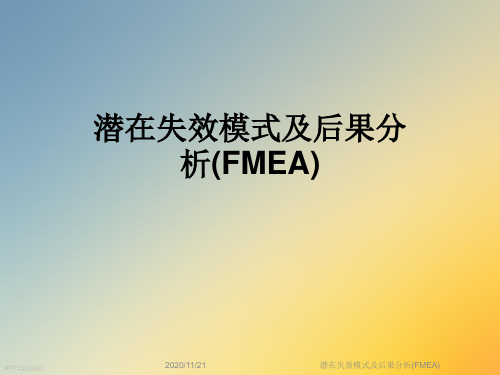
PPT文档演模板
2020/11/21
潜在失效模式及后果分析(FMEA)
•FMEA 在质量体系中
•顾客满意度的改进过程
•获得顾客需求输入
•DFMEA
•PFMEA
•更新PFMEA •控制计划 •反应计划
•过程怎样改变
•控制计划
•过程变量
•产品特性
•数据收集
PPT文档演模板
•进行适当的比较
2020/11/21
潜在失效模式及后果分析(FMEA)
•失效链
•水箱支架断裂
•1 失效原因
•水箱后倾
•1 失效模式
•2 失效原因
•水箱与风扇碰撞
•1 失效后果
•2 失效模式
•水箱冷却水管被风扇刮伤
•2 失效后果
•3 失效原因
•水箱冷却液泄漏
•冷却系统过热
•3 失效后果
PPT文档演模板
•时间
•发动机气缸损坏
2020/11/21
PPT文档演模板
2020/11/21
潜在失效模式及后果分析(FMEA)
•FMEA和FMA、FTA
• FMEA是一种事前行为:
• FMA(Failure Mode Analysis)是一种事后行 为。
• FMA是对产品/过程已经发生的失效模式分析 其产生的原因,评估其后果及采取纠正措施的一 种活动。
潜在失效模式及后果分析(FMEA)
•什么是 FMEA?
•2.术语定义
(影响的)严重度( Severity )- 影响对顾客要求 的重要程度 - 如果失败发生,也可以和安全及其他 风险相关(1=不严重,10=非常严重)
(要因的)发生率( Occurrence )- 给定要因发
IATF16949 失效模式与后果分析(FMEA)培训课件

包括从系统--子系统--零件的策划、开发阶段有计 划地展开,由设计阶段延伸到制造和应用阶段; (全过程)
▪ 在设计阶段,改进的重点是用于指出设计上的 问题点,改进设计,用以确认产品设计是否满 足顾客要求;(关注客户要求)
▪ 在制造阶段,改进的重点是用于指出加工、装 配、生产、设计方面的问题点,反推至前一过 程或前一阶段,要求进行必须的改进。
可能有何错误? -功能丧失 -部分/全部功能
降低 -功能间歇性中断 -非预期的功能
为有可能 被预防和 探测吗?
可以做什么? -设计变更 -过程变更 -特别的控制 -标准、程序或
指南的更改
探测它 的方法 有多好?
2022/2/10
12
4. TS16949----FMEA类型
▪ 依据产品实现阶段不同可分为:
▪ 事前花时间很好地进行综合的FMEA分析,能够容 易、低成本地对产品或过程进行修改,从而减轻事 后修改的危机
▪ 适当应用FMEA是一个相互作用的过程,永无止境
2022/2/10
21
7. FMEA实施过程中注意事项--关于分值
▪ 同一小组分值要一样; ▪ 分析前的培训和思路的统一很重要; ▪ 不同过程分值可以不同(设计过程与制造过程)
2022/2/10
32
2. DFMEA分析步骤过程
产
每
品
一
或
部
系
分
统
功
能
2022/2/10
失 效 模 式 分 析
依
FMEA 表 逐 项 分 析
33
3. DFMEA分析方法
硬件法
针对零件清单上的每一个零件,一次一个的逐个分析, 直到整个产品分析完
功能法
▪ 在设计阶段,改进的重点是用于指出设计上的 问题点,改进设计,用以确认产品设计是否满 足顾客要求;(关注客户要求)
▪ 在制造阶段,改进的重点是用于指出加工、装 配、生产、设计方面的问题点,反推至前一过 程或前一阶段,要求进行必须的改进。
可能有何错误? -功能丧失 -部分/全部功能
降低 -功能间歇性中断 -非预期的功能
为有可能 被预防和 探测吗?
可以做什么? -设计变更 -过程变更 -特别的控制 -标准、程序或
指南的更改
探测它 的方法 有多好?
2022/2/10
12
4. TS16949----FMEA类型
▪ 依据产品实现阶段不同可分为:
▪ 事前花时间很好地进行综合的FMEA分析,能够容 易、低成本地对产品或过程进行修改,从而减轻事 后修改的危机
▪ 适当应用FMEA是一个相互作用的过程,永无止境
2022/2/10
21
7. FMEA实施过程中注意事项--关于分值
▪ 同一小组分值要一样; ▪ 分析前的培训和思路的统一很重要; ▪ 不同过程分值可以不同(设计过程与制造过程)
2022/2/10
32
2. DFMEA分析步骤过程
产
每
品
一
或
部
系
分
统
功
能
2022/2/10
失 效 模 式 分 析
依
FMEA 表 逐 项 分 析
33
3. DFMEA分析方法
硬件法
针对零件清单上的每一个零件,一次一个的逐个分析, 直到整个产品分析完
功能法
FMEA(失效模式与后果分析)

苏州生益科技培训教材.huangzz
4.什么时候需要开始做FMEA?
1.当一个新的系统、产品或过程开始设计时 2.当存在的设计或过程需要改变时 3.当设计或过程应用到新的地方或新的环境 4.研究或解决的问题完成后,防止问题再发生 5.设计的产品功能被确定,在产品设计被批准开始制造之前
苏州生益科技培训教材.huangzz
苏州生益科技培训教材.huangzz
诠释FMEA
在设计和制造产品时,通常有三道控制缺陷的防线:避免或消除故障起因、 预先确定或检测故障、减少故障的影响和后果。 FMEA正是帮助我们从第一道防线就将缺陷消灭在摇篮之中的有效工具。
FMEA是一种可靠性设计的重要方法。 它实际上是FMA(故障模式分析)和FEA(故障影响分析)的组合。 它对各种可能的风险进行评价、分析,以便在现有技术的基础上消 除这些风险或将这些风险减小到可接受的水平。 及时性是成功实施FMEA的最重要因素之一,它是一个“事前的行 为”,而不是“事后的行为”。 为达到最佳效益,FMEA必须在故障模式被纳入产品之前进行。 失效模式及后果分析是动态文件。 失效模式及后果分析是一个集体过程而非单一的个人过程。
目视 目视
目视/检具 检具 防错/检具 防错/检具 防错/检具 防错
高
非常高 几乎没问题可 查测出
设计(过程)控制侦测出潜在原因或不良模式的概率高
设计(过程)控制侦测出潜在原因或不良模式的概率很高 设计(过程)控制侦测出潜在原因或不良模式的概率没有问题
3
2 1
苏州生益科技培训教材.huangzz
风险优先系数(RPN)
责任及 目标完 成日期
行动结果
采取 的行 动 S O D R P N
能做些什么? -设计更改 -过程更改 -特殊控制 -标准、程序或 指南的更改
失效模式及后果分析(FMEA)

DFMEA
PFMEA
范围
1)功能模块;2)方块图;3)界面图;4)过程流程图;5)关系矩阵图;
6)示意图;7)材料清单。
功能、要求 和期望
阐明项目设计意图或过程目的,有助于确定每一个属性或功能的潜在失效模式的确定
潜在失效模 式
确定的方式或途径是产品或过程未能满足设计意图或过程要求,一个单一的要求可以 识别出多个失效模式;
1)概念;2)初始设计;3)设计完成;4)样件制造;5)设计/过程确认;6)制造开始。
公司LOGO
FMEA概要介 绍
FMEA 策略、 策划和执行的 概述
DFMEA
PFMEA
范围 重点
4、FMEA实施的影响
新设计、新技术或新制程 这时是完整的设计、技术或制程的FMEA
修改现有的设计或制程 这时是FMEA的焦点在修改设计或制程,以及由于在 修改过程中设计、制程而导致的相互作用
1、背景
FMEA概要介 绍
FMEA 策略、 策划和执行的 概述
DFMEA
PFMEA
FMEA的基 本结构
FMEA展开 的主题
1)功能、要求和产品的可交付性或需要分析的过程; 2)当功能要求不符合时的失效模式; 3)后果和失效模式的结果; 4)失效模式的潜在要因; 5)对所述失效模式的要因的措施和控制; 6)预防失效模式发生的措施。
提供公开的讨论形式
针对建议和跟踪降低风险 的措施等方面的内容;
06
为后续的提供参考
例如售后市场关切情况, 评价设计更改及开发先 进的设计;
05
01
DFMEA
04
02
建立设计改进、开发和验证 试验/分析的优先系统
通过对“顾客”的影响进 行分级列表;
PFMEA
范围
1)功能模块;2)方块图;3)界面图;4)过程流程图;5)关系矩阵图;
6)示意图;7)材料清单。
功能、要求 和期望
阐明项目设计意图或过程目的,有助于确定每一个属性或功能的潜在失效模式的确定
潜在失效模 式
确定的方式或途径是产品或过程未能满足设计意图或过程要求,一个单一的要求可以 识别出多个失效模式;
1)概念;2)初始设计;3)设计完成;4)样件制造;5)设计/过程确认;6)制造开始。
公司LOGO
FMEA概要介 绍
FMEA 策略、 策划和执行的 概述
DFMEA
PFMEA
范围 重点
4、FMEA实施的影响
新设计、新技术或新制程 这时是完整的设计、技术或制程的FMEA
修改现有的设计或制程 这时是FMEA的焦点在修改设计或制程,以及由于在 修改过程中设计、制程而导致的相互作用
1、背景
FMEA概要介 绍
FMEA 策略、 策划和执行的 概述
DFMEA
PFMEA
FMEA的基 本结构
FMEA展开 的主题
1)功能、要求和产品的可交付性或需要分析的过程; 2)当功能要求不符合时的失效模式; 3)后果和失效模式的结果; 4)失效模式的潜在要因; 5)对所述失效模式的要因的措施和控制; 6)预防失效模式发生的措施。
提供公开的讨论形式
针对建议和跟踪降低风险 的措施等方面的内容;
06
为后续的提供参考
例如售后市场关切情况, 评价设计更改及开发先 进的设计;
05
01
DFMEA
04
02
建立设计改进、开发和验证 试验/分析的优先系统
通过对“顾客”的影响进 行分级列表;
- 1、下载文档前请自行甄别文档内容的完整性,平台不提供额外的编辑、内容补充、找答案等附加服务。
- 2、"仅部分预览"的文档,不可在线预览部分如存在完整性等问题,可反馈申请退款(可完整预览的文档不适用该条件!)。
- 3、如文档侵犯您的权益,请联系客服反馈,我们会尽快为您处理(人工客服工作时间:9:00-18:30)。
推进零缺陷的决心 质量改进团队的建设 质量制度
零缺陷思维;质量体系;质量工具;价值观
28.06.2020
10
零缺陷质量管理技术路线
❖ 从源头保证质量 ❖ 结果的正确源自于过程的正确
❖ 标准化作业 ❖ 防错设计 ❖ 防错装置 ❖ 设计评审 ❖ DOE ❖ 8D报告 ❖ ……
28.06.2020
11
2002.2
6
零缺陷基本内涵和基本原则
基于质量战略目标,通过对经营各环节、各层次的全过程、全 方位管理,保证各环节、各层次、各要素的缺陷趋向于“零”。
追求整体的效益,通过系统集成的理念,从总体上保证实现零缺陷;
不制造缺陷、不接受缺陷,不传递缺陷,不向市场和顾客提供有缺陷的产品与服务;
根据质量体系的要求,每项工作都应建立规章制度和业务流程,按规定程序
信奉为最好的质量管理
明确提出零缺陷质量战略;
28.06.2020
5
零缺陷策略
在源头实施零缺陷质量控制和预防
产品设计满足顾客需求; 提高首次质量(First Time Quality,FTQ); 将缺陷与顾客隔绝:不接收缺陷,不制造缺陷,不传递缺陷; 制造中降低偏差和减少浪费;
28.06.2020
28.06.2020
7
零缺陷总体思考
❖ 充分考虑零缺陷质量意识对质量管理产生的变化。
✓ 树立积极的、主动的、超前的质量创新观念 ✓质量的定义是符合要求; ✓质量通过预防措施来达成; ✓质量的执行标准是零缺陷; ✓质量要用不符合要求的代价来衡量;
❖ 把握质量管理工作的趋势;
✓ 指导、协调、培训
✓ 控制 → 预防性
失效模式与后果分析 (FMEA)
作为质量管理工具,旨在尚未批产前对错误进行预防, 以保证产品质量
28.06.2020
潘尔顺副教授 上海交通大学 工业工程与管理系
1
主要内容
基本概念 故障模式 FMEA实施步骤 设计FMEA(DFMEA) 制造FMEA(PFMEA) FMEA表格及实例
28.06.2020
事前的防范是很重要的
基本概念
什么是FMEA?
FMEA(Failure Mode and Effect Analysis)即“失效模 式和效果分析”。
FMEA是一种可靠性设计的重要方法。它实际上是
FMA(故障模式分析)和FEA(故障影响分析)的组
合。它对各种可能的风险进行评价、分析,以便在现
有技术的基础上消除这些风险或将这些风险减小到可
✓ 事后解决、纠错 → 事前预防、防错设计、前瞻性
✓ 过程控制 → 设计控制
28.06.2020
8
零缺陷总体思考
❖ 研究防错技术;
✓ 正向、积极、全方位的思维方法; ✓ 充分预计可能产生的各种社会、环境、系统、过程等问题; ✓ 探索解决问题的方法; ✓ 预防和避免问题的发生;
❖ 倡导质量预防文化;
28.06.2020
13
FMEA历史
虽然工程技术人员早已在其设计和制造过程中应用 了类似FMEA形式的分析方法,但第一次正式地应 用FMEA技术则是六十年代中期航天工业的一项革 新:
FMEA is most effective when it occurs before a design is released rather than “after the fact”.
产品的联合、自主设计、开发将有大幅的增长; 设
用
更加关注顾客,注重面向用户服务的质量问题; 计
户
质量管理工作的角色调整
质量管理工作应该适应、反映此变化;
注重“两头”
质量意识向更高层次、更高要求的转化;
质量管理工作要体现预防性、前瞻性;
为在世界制造业中获得持久的竞争能力, 应明确将质量置于公司战略的核心地位;
实施管理,责任落实到位,不允许存在失控的漏洞;
对已产生的缺陷采取改正的措施,保证差错不延续并提前消除;
必须有产品或工作可能产生的缺陷采取预防的措施,事先排除可能产生缺陷
的各种成因和例外;
人人都是管理者,管理以人为本,充分发挥每个员工的主观能动性,以零缺陷
的工作态度和行为保证产品、经营的零缺陷;
28.06.2020
✓ 这是一个渐进的过程; ✓ 领导的言行; ✓ 员工的意识和观念;
9
零缺陷总体指导思想
顾客满意
质量文化
零缺陷:
产品、工作 从源头规划质量: 人、机、料、法、环、测
SFMEA / DFMEA / PFMEA
企业价值观
企业目标
质量文化 要价值观、 目标相结 合;
设计
工艺/制造
服务
根据自身的实际,应用零缺陷管理实施十四步骤
接受的水平。及时性是成功实施FMEA的最重要因素
之一,它是一个“事前的行为”,而不是“事后的行
为”。为达到最佳效益,FMEA必须在故障模式被納
入
产
品
28.06.2020之前进行。
12
基本概念
什么是FMEA?
由于产品故障可能与设计、制造过程、使用、承包商/ 供应商以及服务有关,因此,FMEA又细分为 設計FMEA(DFMEA) 過程FMEA(PFMEA) 使用FMEA(UFMEA) 服務FMEA(SFMEA) 其中設計FMEA和過程FMEA最爲常用。
28.06.2020
3ቤተ መጻሕፍቲ ባይዱ
零缺陷管理
21世纪:质量的世纪
质量科学和管理发生着根本性的变革
人人皆顾客,事事皆过程 Everyone is customer, Everything is process
28.06.2020
4
零缺陷战略
未来五年、十年中国制造业的发展前景和目标
更多企业的制造质量跨入世界先进水平;
focus should be on failure prevention not detection.
As such, FMEA is often a standard process used in the development of new products.
28.06.2020
14
客户满意的质量杠杆示意图
2
零缺陷管理
20世纪60年代初,美国Martin公司的质量改进计划诞生了 “零缺陷(Zero Defect)”的概念;
所有的生产过程都以“零缺陷”作为质量标准,每个人通 过不懈地努力来做到“第一次就把事情做对(Do it right the first time)”;
1979年,克劳斯比著作 《质量免费(Quality is free)》;
零缺陷思维;质量体系;质量工具;价值观
28.06.2020
10
零缺陷质量管理技术路线
❖ 从源头保证质量 ❖ 结果的正确源自于过程的正确
❖ 标准化作业 ❖ 防错设计 ❖ 防错装置 ❖ 设计评审 ❖ DOE ❖ 8D报告 ❖ ……
28.06.2020
11
2002.2
6
零缺陷基本内涵和基本原则
基于质量战略目标,通过对经营各环节、各层次的全过程、全 方位管理,保证各环节、各层次、各要素的缺陷趋向于“零”。
追求整体的效益,通过系统集成的理念,从总体上保证实现零缺陷;
不制造缺陷、不接受缺陷,不传递缺陷,不向市场和顾客提供有缺陷的产品与服务;
根据质量体系的要求,每项工作都应建立规章制度和业务流程,按规定程序
信奉为最好的质量管理
明确提出零缺陷质量战略;
28.06.2020
5
零缺陷策略
在源头实施零缺陷质量控制和预防
产品设计满足顾客需求; 提高首次质量(First Time Quality,FTQ); 将缺陷与顾客隔绝:不接收缺陷,不制造缺陷,不传递缺陷; 制造中降低偏差和减少浪费;
28.06.2020
28.06.2020
7
零缺陷总体思考
❖ 充分考虑零缺陷质量意识对质量管理产生的变化。
✓ 树立积极的、主动的、超前的质量创新观念 ✓质量的定义是符合要求; ✓质量通过预防措施来达成; ✓质量的执行标准是零缺陷; ✓质量要用不符合要求的代价来衡量;
❖ 把握质量管理工作的趋势;
✓ 指导、协调、培训
✓ 控制 → 预防性
失效模式与后果分析 (FMEA)
作为质量管理工具,旨在尚未批产前对错误进行预防, 以保证产品质量
28.06.2020
潘尔顺副教授 上海交通大学 工业工程与管理系
1
主要内容
基本概念 故障模式 FMEA实施步骤 设计FMEA(DFMEA) 制造FMEA(PFMEA) FMEA表格及实例
28.06.2020
事前的防范是很重要的
基本概念
什么是FMEA?
FMEA(Failure Mode and Effect Analysis)即“失效模 式和效果分析”。
FMEA是一种可靠性设计的重要方法。它实际上是
FMA(故障模式分析)和FEA(故障影响分析)的组
合。它对各种可能的风险进行评价、分析,以便在现
有技术的基础上消除这些风险或将这些风险减小到可
✓ 事后解决、纠错 → 事前预防、防错设计、前瞻性
✓ 过程控制 → 设计控制
28.06.2020
8
零缺陷总体思考
❖ 研究防错技术;
✓ 正向、积极、全方位的思维方法; ✓ 充分预计可能产生的各种社会、环境、系统、过程等问题; ✓ 探索解决问题的方法; ✓ 预防和避免问题的发生;
❖ 倡导质量预防文化;
28.06.2020
13
FMEA历史
虽然工程技术人员早已在其设计和制造过程中应用 了类似FMEA形式的分析方法,但第一次正式地应 用FMEA技术则是六十年代中期航天工业的一项革 新:
FMEA is most effective when it occurs before a design is released rather than “after the fact”.
产品的联合、自主设计、开发将有大幅的增长; 设
用
更加关注顾客,注重面向用户服务的质量问题; 计
户
质量管理工作的角色调整
质量管理工作应该适应、反映此变化;
注重“两头”
质量意识向更高层次、更高要求的转化;
质量管理工作要体现预防性、前瞻性;
为在世界制造业中获得持久的竞争能力, 应明确将质量置于公司战略的核心地位;
实施管理,责任落实到位,不允许存在失控的漏洞;
对已产生的缺陷采取改正的措施,保证差错不延续并提前消除;
必须有产品或工作可能产生的缺陷采取预防的措施,事先排除可能产生缺陷
的各种成因和例外;
人人都是管理者,管理以人为本,充分发挥每个员工的主观能动性,以零缺陷
的工作态度和行为保证产品、经营的零缺陷;
28.06.2020
✓ 这是一个渐进的过程; ✓ 领导的言行; ✓ 员工的意识和观念;
9
零缺陷总体指导思想
顾客满意
质量文化
零缺陷:
产品、工作 从源头规划质量: 人、机、料、法、环、测
SFMEA / DFMEA / PFMEA
企业价值观
企业目标
质量文化 要价值观、 目标相结 合;
设计
工艺/制造
服务
根据自身的实际,应用零缺陷管理实施十四步骤
接受的水平。及时性是成功实施FMEA的最重要因素
之一,它是一个“事前的行为”,而不是“事后的行
为”。为达到最佳效益,FMEA必须在故障模式被納
入
产
品
28.06.2020之前进行。
12
基本概念
什么是FMEA?
由于产品故障可能与设计、制造过程、使用、承包商/ 供应商以及服务有关,因此,FMEA又细分为 設計FMEA(DFMEA) 過程FMEA(PFMEA) 使用FMEA(UFMEA) 服務FMEA(SFMEA) 其中設計FMEA和過程FMEA最爲常用。
28.06.2020
3ቤተ መጻሕፍቲ ባይዱ
零缺陷管理
21世纪:质量的世纪
质量科学和管理发生着根本性的变革
人人皆顾客,事事皆过程 Everyone is customer, Everything is process
28.06.2020
4
零缺陷战略
未来五年、十年中国制造业的发展前景和目标
更多企业的制造质量跨入世界先进水平;
focus should be on failure prevention not detection.
As such, FMEA is often a standard process used in the development of new products.
28.06.2020
14
客户满意的质量杠杆示意图
2
零缺陷管理
20世纪60年代初,美国Martin公司的质量改进计划诞生了 “零缺陷(Zero Defect)”的概念;
所有的生产过程都以“零缺陷”作为质量标准,每个人通 过不懈地努力来做到“第一次就把事情做对(Do it right the first time)”;
1979年,克劳斯比著作 《质量免费(Quality is free)》;