管材弯曲成型模具磨损仿真分析_李钦奉
CP3薄壁焊管数控弯曲成形有限元

模拟与仿真SIMULATION TECHNOLOGY[摘要] 根据焊接管材的特点,通过母材试样和包含焊缝及焊缝热影响区的混合试样的单向拉伸试验以及混合试样横截面的显微硬度测试,基于拉伸过程的等应变假设和混合法则,得到了CP3焊管母材、焊缝以及焊缝热影响区的材料拉伸应力应变关系。
进而建立了薄壁CP3钛管数控弯曲有限元模型,分析了弯曲参数对焊管弯曲结果的影响,比较了均质管模型和焊管模型下,3个弯曲横截面上的壁厚分布,得到了焊缝对焊管弯曲的影响规律。
关键词: CP3 薄壁焊管弯曲成形有限元分析[ABSTRACT] According to features of CP3 weld-ed tubes, the tensile tests for parent metal and mixed metal including weld beam and heat-affected zone (HAZ) metal were carried out, and cross-sectional sample of mixed met-al are used for measuring microhardness throughout weld zone and HAZ. Then on the basis of the iso-strain assump-tion and mixture laws, stress-strain relationships of parent metal, weld beam metal and heat-affected zone metal were obtained. Moreover, FE models for NC bending of welded tubes were established. Finally, laws of parameters on the bending of welded tubes were analyzed, and wall thickness distributions of three cross sections of deformed welded and seamless tubes were compared, then effects of weld beam on bending process of welded tubes were obtained.Keywords: CP3 thin-wall welded tubes Bend forming Finite element analysis钛作为一种性能良好的材料,由于具有密度小、强度高、高低温性能好、耐腐蚀性能好等优点越来越受到青睐,广泛应用于航空航天和汽车等行业[1-2]。
管材弯曲中起皱行为的试验及有限元模拟分析

力 为一 4 a 8 55MP ,其 绝对值 远远 超过 1 r8 iT l N9 i C
管材 的强度极 [6 15 MP 工程抗 拉 强度 )。 随着  ̄ 8. E a(
A T&M 禳 界
管材 弯 曲中起皱 行 为 的试验及
有 限元模 拟分 析
摘要 :基于 管材真实力学参 数建立了管材 弯曲有限元模 型 ,该模型对部分弯管 内侧起皱 的计算 结果与试验结果基本一致。管材弯 曲内侧切向应力过大是导 致管壁材料失稳起皱 的主要原因 ,因此 随着 相对弯曲半径和相对管壁厚 增大 ,起皱 明显减轻 。经有 限元分析指 出,适 当减小模 具工作 凹槽
度 为1 0 。针 对 试验 中产 生 的弯 管 内侧 起皱 现 象 , 8。
结合 有 限 元模 拟 结果 ,对 比 分析 了相 对 弯 曲 半径 月
值 减 小 为6 19 MP 。 分析 认 为 ,相对 弯 曲半径 5 . a 是 左 、右 管材 弯 曲变 形程 度 的重 要 参数 ,厅 越 小 , 弯 管 内侧切 向压缩 变形越 强烈 ,当I I 到 一定数 值 达
方 向3 单 元的 毛坯 网格划 分 ,其他 采用 平 台默认 网格 2
划 分。
块
图3 相 对弯 曲半径 对起 皱影 响的试 验 结果
为 了对 比分析 弯管起 皱 的原 因 ,将 与试验 同样 条
弯 曲成形 前
件 的弯 管 有 限 元模拟 结 果 示于 图4 。弯 管 内侧起 皱 的
图2 管材 弯 曲成 形 前后 有限 元模型
1Cr18Ni9Ti管弯曲回弹影响因素的实验研究
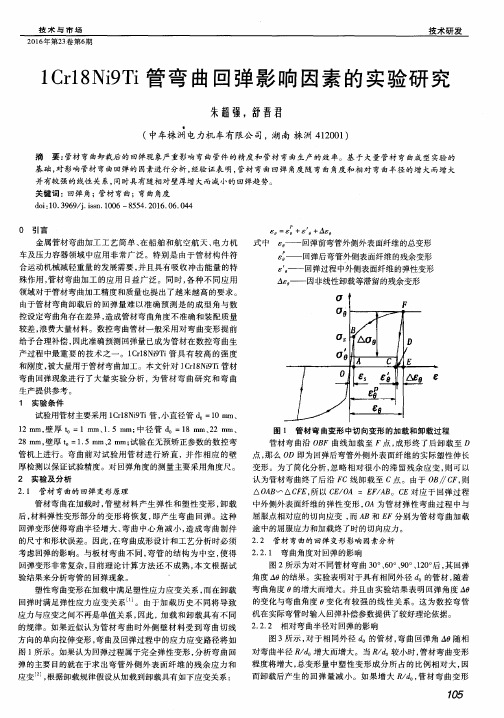
图 1所示 。如果认为 回弹过程属于完全弹性变形 ,分析弯曲 回
弹的主要 目的就在于求 出弯管外侧 外表面 纤维 的残 余应 力和
应 变 ,根 据 卸 载 规 律 假 设 从 加 载 到卸 载具 有 如 下 应 变 关 系 :
屈服点相对应 的切 向应 变 ,而 AB和 EF分别 为管材弯 曲加Байду номын сангаас 途 中的屈服应力和加载终 了时的切向应力 。 2.2 管材 弯曲的回弹变形影响因素分析 2.2.1 弯 曲角度对 回弹的影 响
TECHN0LoGY AND MARKET
Vo1.23,No.6,2016
区的位移量增 大 ,但变形程 度相对减 弱 ,弹性变形 成分 占总
回 弹 角 度
变形量的 比例增 大5 , 卸载 后4 产 生3的 弹性 回 2 复量l随 之 增O大 。并 且 ,试验结果显示 ,R/d。越大 ,弯管 回弹量 △ 随 0增大而增加 的倾 向 越 显著 。
验结果来分析弯管的回弹现象 。
’
塑性弯曲变形在加载 中满足塑性应力应变关 系,而在卸载
回弹时满足弹性应力应变关 系… 。由于加载历 史不 同将 导致
应 力与应变之间不再是单值关 系,因此 ,加 载和卸载具 有不 同
的规律。如果 近似认为管 材弯 曲时外侧壁 材料受 到弯 曲切线
方向的单 向拉伸变形 ,弯曲及 回弹过程 中的应力应 变路径将如
技 术 与 市场 2016年第23卷 第6期
技 术研发
1 Crl 8 Ni9 Ti管 弯 曲回弹影 响 因素 的实 验研 究
朱超强,舒晋君
●
(中车株洲电力机车有限公 司,湖南 株洲 412001)
管材弯曲试验及助推作用的有限元分析

■ ●
北 京理 工 大学材 料学 院 李
弭 鄂 大辛 皿
张 敬 文
首 都 航天机 械 公司 李延 民 田 鑫
直 管段 管坯 轴 向挤 弯。 因此 ,如 何合 理地 设 置助 推 装
2 助推形式及其有 限元模型
根据 现 有数控 弯管 机结 构对 助推 装 置进 行 改进 ,
到 的助 推 效 果十 分有 限。 另外 , 目前 生产 中使用 的弯 管 机简 易 助推 装 置设 置在 机 架尾 部 , 即使 能够 将 直管
坯 的一 端 装卡 在助 推 装置 上 ,助推 加 载 时也极 易 引起
.
数 字 l 园 地
管材弯 曲试 验及助 推作 用 的有 限元分析
摘要 :利用有 限元方法分析 了两种管材 助推 弯 曲形 式、多种助推 速度对弯 管横截面短轴 变化率 和壁厚 变化率 的影I ,并 与部分试验结 果进行 了对 比分析。结 果表 明,助推块 与压 紧块 同步助推 , 1 向 可 以减 轻弯管横截 面外轮廓 扁平化 变形 ,但不 能同时调整弯 管内、外侧壁厚 变化率。采 用助推块 与 压 紧块 不 同步助推模 型 ,不仅可适 当控 制管材弯 曲变形阻力 ,还 可在进给 阶段 对管坯施 加有针对 性 的轴 向拉 伸 或压缩 变形 ,从 而可 以按照 产生缺 陷的主 、次要 影响来 有效 控 制弯管 内、 外侧壁厚 变 化 ,进 而获得较好 的管材弯 曲成 形质量 。
置 施加 有效 助推 ,消 除 或减 轻 由助推 所 带来 的 负面影 响 , 已经成 为管 材 弯 曲技术 领域 中一个 非常 重要 且 具 有实用 意 义的研 究课 题 。
管材弯曲成形的有限元模拟与实验分析

论 研 究 进 展 比较 缓 慢 。 年 来 , 算 机 技 术 的 发 展 为 近 计
收稿日期: 0— l1 2 51 6 0 作者{介: 涛(96 )男, 畸 古 17一 , 硕士生. 从事塑性成形的有限元模拟 和仿真研究
・
2 实 验 条 件 殛 有 限 元 模 型 建 立 这 里 的 实 验 和模 拟 主 要 针 对 小 直 径 管 的 回 转 牵 引 式 弯 曲 变 形 。实 验 材 料 1 r 8 9 i , 外 径 d= C l NiT 管 管 o
造 等 工 业 中 应 用 十 分 广 泛 [。 管 材 弯 曲 技 术 和 质 量 】对 1
的 要 求 也 越 来 越 高 。 是 , 于 管 材 具 有 特 殊 的 | 空 但 由 中 结 构 以 及 受 多 重 非 线 性 因 素 的 影 响 ,弯 曲 变形 的 理
有 限 元 模 拟 结 合 起 来 对 弯 曲 变 形 过 程 中 的 诸 多 现 象 进 行 比较 分 析 , 为 后 续 研 究 和 生 产 实 践 提 供 参 考 。 将
计 算 方 法 在 管 材 弯 曲 变 形 研 究 中 也 得 到 了广 泛 应 用 ,并 已在 弯 曲 加 工 类 产 品 的 设 计 和 优 化 方 面 被 证 明 是 有 效 的 嘲 在 管 材 弯 曲 的 系 统 研 究 中 , 实 验 与 。 将
目 前 。 材 弯 曲 加 工 在 航 空 航 天 、 车 、 舶 制 管 汽 船
+ 一 + “ + “-
0 ・ 4- - '
中 涉 及 的 边 界 问 题 、 触 问题 进 行 了 处 理 , 确 定 了 接 并
旋 轮 在 旋 压 过 程 中 的 轨 迹 。 利 用 该 力 学 模 型 对 工 件 进 行 数 值 模 拟 。 到 了 合 乎 实 际 的效 果 。 得 【 考文献】 参
变形曲线的能量模型与板料弹性弯曲模拟

变形曲线的能量模型与板料弹性弯曲模拟* 李凌丰 张 谦 谭建荣 摘要弯曲刚度等特定材料的物理属性的变形曲线模型受到边界约束的曲线变形最终达到平衡状态此时曲线的内在变形能达到极小它与曲线的微分几何量有关将参数化描述的几何信息与能量极小化算法相结合用变形曲线模型来模拟板料变形过程的弹性弯曲关键词多角弯曲胀形都存在着弯曲在结构分析和金属成形领域数值分析和模拟方法已成为了工业设计通过这种技术的使用降低生产成本提高工业设计的可靠性和降低产品开发过程中人财物力的巨大浪费在板料成形的计算机模拟过程中使得问题的求解难度很大几何非线性物理非线性边界条件非线性材料与模具的接触条件是动态变化的陈中奎[1]并将有限变形弹塑性有限元法引入板料冲压成形过程ÍÆµ¼ÁËÓÐÏÞÔªÁÐÊ½ÇØãô¼ª另有一些学者在2维截面分析方面做了工作Saran等与Keum等利用膜单元进行了截面分析对膜单元进行了修正李大永等着重研究了板料成形数值模拟中的2维截面分析技术[3]尽管在板料成形过程模拟绝大部分板料成形过程应该用3维模型分析但2维截面分析在板料成形分析中也有重要的作用3维整体分析存在着计算时间长边界条件难于处理等不利因素数据准备简单另一方面可以用2维截面分析程序有效地模拟尽管大多数截面并不满足平面应变或轴对称条件本文利用变形曲线能量模型模拟板料弯曲变形∗国家863/CIMS主题项目和浙江省科学技术厅项目资助∫++=du du rd du r d du r d du r d du dr du dr r E T T T )()(33332222γβα如果边界条件定义得当1 变形曲线的能量模型 1.1 变形曲线的能量 可变形曲线由Terzopoulos 等人[5]于1987年引入CAGD ÓÐÂ½ÐøÒ»Ð©ÎÄÏ׶Դ˽øÐÐÌÖÂÛ¸³ÓèÇúÏßÁ¦Ñ§ÌØÐÔÍäÇú¸Õ¶ÈµÈÆä±äÐÎÐÎ̬ÔÚÒ»¶¨³Ì¶ÈÉÏÓ뵯ÐÔÁº»ò°å¿ÇµÄ±äÐÎÐÎ̬ÏàËÆ¹â˳µÄ³Öµã[4]Çó½âÄÜÁ¿×îСµÄƽºâÐÎ̬ÇúÃær(uÈçÑØu 向和v 向有拉伸刚度和弯曲刚度模型中做了最大限度的简化以及比第二基本量更简化的部分变形曲线发生形变此时曲线的内在变形能U(r)达到极小它与曲线的微分几何量有关r(u)y(u)内在变形能定义为(1) 1.2 约束定义 曲线受特定约束作用变形曲线必须通过指定的边界点并与周围邻接曲线保持一阶几何连续2为了计算方便对能量函数E(r)求极小值从给定的已知约束条件可以直接得出一部分控制顶点的位置4还可以有目的地增加某些附加载荷增加型值点控制ͨ¹ýÔÚÄÜÁ¿·½³ÌÖÐÒýÈëÏÂÃæÎó²îÏî¼´¿ÉʵÏÖKiͨ¹ýµ÷ÕûʽÖз£Òò×ӵĴóС2 板料弯曲计算 板料的变形能可以用功能原理计算板料的变形能为(3) 板料弯曲时 板料中性层曲率 的表达式为 (4) ∑=−Ni i iu r p K12||)(||zEI M=ρ1ρ1δP W U 21==式中EI z称为抗弯刚度省写下标z板料受纯弯矩时(5)在弯曲时还有剪力与弯曲变形相应的弯曲变形能和与剪切变形相应的剪切变形能剪切变形能比弯曲变形能小得多如果从板料中取出长为dx的微段来研究长度为l板料受末端处集中力作用 约束状态是另一端位置和转角自由性能设定系数K= P/EI EI为弹性模量和惯性矩 1.0, 0, 0终止点切矢为图1显示这几种材料在其他条件相同情况下的变形状况4 结论 在变形曲线模型的能量函数中可调参数(如刚度由于没有完全摸清规律本文结合板料弯曲的工程情况能量的表达式简洁当然在弹性变形如果变形量大就会出现较大偏差摩檫约束没有考虑参 考 文 献 1 陈中奎, 施法中. 板料冲压成形过程的一种数值模拟方法. 北京航空航天大学学报, 2001, 27(3): 340 ̄343 2 秦泗吉, 王志松. 板材冲压成形中的弯曲与反弯曲变形问题的研究. 机械工程学报, 2001, 37(8): 99 ̄101,105 3 李大永, 胡平, 曹颖. 板料成形数值模拟中的2维截面分析技术. 中国机械工程, 2001, 12(7): 808 ̄811 4 经玲, 席平, 唐荣锡. 应用可变形模型进行曲线曲面光顺. 软件学报, 1998, 9(6): 464 ̄468 5Fang L, Dossard D C. Multidimensional curve fitting to unorganized data points by nonlinear minimization.Computer-Aided Design, 1995, 27(1):48~58作者简介男浙江大学机械工程及自动化系副教授制造业信息系统出版著作1本曾获得国家教委科技进步二等奖和多项省部级鉴定成果 李凌丰 联系地址。
薄壁管有芯旋转模弯成形回弹与伸长的研究的开题报告

薄壁管有芯旋转模弯成形回弹与伸长的研究的开题报告一、研究背景与目的薄壁管是一种在各种工业生产领域广泛使用的管材,尤其在汽车、航空航天、船舶和军工等领域有着广泛应用。
在这些领域中,薄壁管的强度、刚度和重量都是非常重要的指标,而管子的弯曲变形是一个非常常见的情况,这对管子的力学性能和使用寿命都会产生较大的影响。
因此,研究薄壁管的弯成形过程,尤其是回弹和伸长问题非常有意义。
本次研究的主要目的是探究薄壁管芯旋转模弯成形时出现的回弹和伸长问题,分析影响管子回弹和伸长的各种因素,并通过有限元数值模拟验证研究结果,为生产制造提供相关数据和理论支持。
二、研究内容1.调研文献,了解薄壁管弯成形的基本知识和成形机理。
2.通过有限元数值模拟和实验研究,探究影响薄壁管芯旋转模弯成形回弹和伸长的各种因素,如管材材料性能、管径、管壁厚度、芯棒直径和弯曲角度等。
3.比较分析不同情况下的回弹和伸长程度,探究管材弯曲后的力学性能和变形规律。
4.通过实验验证研究结果,检验有限元模拟模型的可靠性和准确性。
三、研究意义薄壁管弯成形回弹和伸长的问题是实际生产中经常遇到的问题,解决这一问题可以提高生产效率,降低生产成本,延长产品使用寿命。
本研究的的研究成果对于理解管材弯曲变形和弯曲后力学性能的变化规律具有一定的理论和实际意义。
同时,该研究表明,通过有限元数值模拟分析,越来越成为研究管材弯曲变形的重要手段,这种方法可以减少研究成本和时间,大大提高研究效率。
四、研究方法1.采用ABAQUS等有限元软件对薄壁管芯旋转模弯成形回弹和伸长进行数值模拟,研究各种影响因素的作用规律。
2.在数值模拟的基础上,进行实验验证和分析,研究管材的弯曲变形、回弹和伸长情况,并检测管材的力学特性和表面质量。
3.比较和分析数值模拟和实验结果之间的一致性与差异性,找出影响薄壁管芯旋转模弯成形回弹和伸长的主要因素和机理。
五、预期结果通过本次研究,预计可以得出以下几点结论:1.不同因素对芯旋转模弯成形回弹和伸长的影响程度。
基于PAM TUBE 2G的管材弯曲成形数值模拟分析

基于PAMTUBE 2G的管材弯曲成形数值模拟分析作者:陶延民刘富孙纪宁摘要:管材弯曲成形工艺是是飞机制造业中的一种非常重要的加工方法。
在实际生产过程中,管材过度减薄或开裂,管材断面形状畸变严重,管材内侧失稳起皱等问题严重影响管材弯曲成形零件质量。
PAM-TUBE 2G可以解决在管材弯曲成形工艺过程中模具设计、下料估计、精确成形模拟分析、回弹计算等所有的问题。
实际管材弯曲成形例子证明了PAM-TUBE 2G 用来解决弯管成形工艺模拟是完全合适和非常高效的。
关键词:数值模拟;管材弯曲成形;回弹前言管材弯曲成形工艺是是飞机制造业中的一种非常重要的加工方法。
在紧凑的飞机机身、发动机内部,管材件种类繁多而且具有一定数量,其形状怪异而又十分重要;在实际生产过程中,常见的缺陷有:管材过度减薄或开裂,管材断面形状畸变严重,管材内侧失稳起皱等。
在实际管材弯曲成形工艺生产中,现在突出需要我们解决的问题是:初始下料量估计问题、可成形性和可行性分析问题、成形质量控制问题和零件回弹问题。
在国内外的现代化飞机制造厂中,管材的CAE模拟对提高管材生产水平和质量有着非常关键的影响。
能够在模具投入实际的物理试模之前,判断模具的可成形性和可行性对于实际生产过程是有很大作用的,明显减少模具设计上的失误,缩短模具开发周期,减少开发成本;对模具成形过程进行详细的模拟和分析,提供非常精确的成形结果,帮助用户在公差范围内对模具进行全面质量控制,有效解决了昂贵而耗时的修模调试时间;对模具进行回弹分析和回弹自动补偿过程,并且输出经过回弹自动补偿后的模具的三维几何模型,有效解决模具设计过程中的非常困难的回弹问题。
1导管弯曲数值模拟分析过程PAM-TUBE 2G软件中管材弯曲成形工艺模拟程序原理简图如下图1所示,图1 管材弯曲成形工艺模拟程序原理简图从图1中可以看出,软件模拟的原理与实际生产过程是完全一致的,这就为软件准确模拟弯管成形工艺过程打下了坚实的基础,经过我们的用户,如奥迪(Audi)和空中客车公司(Airbus)的实际使用证明了PAM-TUBE 2G软件模拟管材弯曲成形工艺是准确有效的。
- 1、下载文档前请自行甄别文档内容的完整性,平台不提供额外的编辑、内容补充、找答案等附加服务。
- 2、"仅部分预览"的文档,不可在线预览部分如存在完整性等问题,可反馈申请退款(可完整预览的文档不适用该条件!)。
- 3、如文档侵犯您的权益,请联系客服反馈,我们会尽快为您处理(人工客服工作时间:9:00-18:30)。
相互接 触面
管材பைடு நூலகம் 防皱块
管材— 夹块
管材— 滑块
管材— 管材— 弯曲模 芯棒,芯球
摩擦系数 0.05
无穷大
0.15
0.1
0.05
在弯曲过程中,芯棒、防皱模、滑块是完全固定 不动,给予断面固定约束,其自由度通过各自刚体参 考点控制。 为了使管坯能随着夹块绕弯曲模一起转 动,定义夹块的参考点与管坯末端面连结约束,并定 义完全相同的自由度。 在夹块参考点与弯曲模参考 点间建立 beam 单元。 芯头与芯头,芯头与芯棒之间 建立铰链连接。 弯曲模与夹块绕 z 轴旋转运动,定义 弯曲模角位移。 设置相应的热力参数。
图 3 摩擦系数与防皱模磨损深度关系 Fig.3 The relationship between friction coefficients
and wear depth of shrink-proof die 摩擦系数与防皱模磨损深度关系: 随着摩擦系 数的增大磨损深度逐渐增大。 相同摩擦系数时,管
值模拟了弯管过程,揭示了防皱模在弯曲过程中应力的分布规律。 采用 Archard 磨损模型研究了不同管厚度、管坯材料
以及摩擦系数对弯管机防皱模磨损的影响规律。 这对弯管工艺、模具设计和模具寿命的预测能提供一些参考。
关键词:弯曲成形; 有限元; 磨损; 防皱模
中图分类号: TG386.3+1
文 献 标 识 码 :A
为了研究不同铝管、 钢管壁厚对防皱模磨损深 度的影响,设置了一组以壁厚为变量的模拟方案:铝 管壁厚分别为 0.5、1.0、1.5、2.0、2.5、3.0 mm。 钢管壁
2 磨损理论
目前可供实际应用的磨损计算模型主要有 3
个,英国 J F Archard 教授提出的 Archard 模型;美国
R G Bayer 教授提出的 Bayer 模型以及前苏联 H B 克
拉盖斯基教授提出的克拉盖斯基磨损计算模型。 前两
种实用较为广泛,Archard 模型比较适用于非连续的
变形[11]。 本文使用 Archard 模型计算防皱模磨损深度。
材 45 钢 防 皱 模 磨 损 程 度 比 铝 管 严 重 。 摩 擦 系 数 0.1~0.2,磨损变化不明显;摩擦系数 0.2~0.4,磨损 量增长幅度较大; 摩擦系数 0.2 附近存在磨损最小 值。铝管时摩擦系数的变化对防皱模磨损不明显,摩 擦系数 0.25 附近磨损出现最小值。 3.3 矩形管厚度对防皱模磨损的影响
根 据 文 献 [12] 磨 损 量 与 磨 损 系 数 、 法 向 压 力 、 滑
行距离和表面硬度有关,表示为:
V=
KFS 3HV
(1)
式中:V 为磨损的体积;K 为磨损系数:F 为法向力;
S 为滑行距离;HV 为表面硬度。 式(1)中两边分别除
以接触面积,得到:
w=
KpS 3HV
(2)
式中:w 为磨损深度。 方形铝管滑动位移 S 的计算:
Hot Working Technology 2014, Vol.43 , No. 1
管材弯曲成型模具磨损仿真分析
李钦奉, 张礼军, 李东生, 李长伟 (江苏科技大学 机械工程学院, 江苏 镇江 212003)
摘 要:建立了管材弯曲成形过程中防皱模的热力耦合模型,利用有限元软件 ABAQUS/Explicit 的非线性功能,数
表 1 摩擦副材料特性参数 Tab.1 The characteristic parameters of friction material
导热率 密度 比热容 热膨胀系数 弹性模量泊松
参数 /(W·m-1K-1) /(kg·m-3) /(J·kg-1K-1) /(μK-1)
/GPa 比
防皱模 48.15 7810 468.9
收 稿 日 期 :2013-03-17 作者简介:李钦奉(1960-), 重庆云阳人,教授,主要研究方向:现代制造技
术及装备; 电话:13605287498; E-mail:li555666@163.com
Archard 磨损公式计算在接触时所产生的磨损。廖海 平[6]等 结 合 弹 流 润 滑 理 论 以 及 滑 动 磨 损 公 式 ,对 平 底直动盘形凸轮机构的润滑特性以及磨损规律进行 了探讨。 摩擦热及其引起的温升对接触表面的力学 性能有很大的影响, 在机械系统中要进行准确的失 效分析, 了解滑动接触中固体的热应力是必不可少 的[7]。 李亮等[8]基于 Aarchard 模型模拟分析凸模磨损 状况。 潘俊杰[9]等运用 Archard 模型分析了模具在复 杂多因素耦合下的磨损分布为模具寿命预测提供依 据。 本文采用 Archard 公式利用 Abaqus 软件研究矩 形管厚度以及摩擦系数对弯管机防皱模磨损的影响 规 律,为防皱模的设计以及寿命的预测提供理论依据 。
3mm, 磨损量变化不大。
图 2 不同时刻防皱模接触表面 Von Mises 应力分布图 (MPa) Fig.2 Von Mises stress distribution of contact surface on shrink-proof die in different times (MPa)
薄壁管数控精确弯曲技术能够实现管塑性弯曲 成形过程高精度、高效率、高技术化对产品轻量化的 要求。 在航空、航天等工业,弯曲成形加工占有重要 地位 [1]。 在弯管加工过程中防皱模起重要作用,直 接影响被加工管件质量。 据统计, 机械零件的失效 主要有磨损、断裂和腐蚀 3 种方式,而磨损失效却占 60%~80%[2]。 防皱模主要失效形式为磨损,主要是 由模具与被弯曲管件之间的相对滑动引起的。 决定 磨损的因素主要有弯曲接触压力, 模具和被弯曲管 件之间的硬度差, 模具和被弯曲管件之间的摩擦系 数,模具和被弯曲管件之间的滑动速度等。
弯曲过程是管坯和各个模具之间相互接触,在 紧密配合的情况下完成的, 各个模具与管坯之间 都有接触摩擦。 选取库伦摩擦来描述管坯和模具 之间的接触情况定义各部位之间的摩擦系数如表 2 所示。
表 2 接触边界摩擦系数 Tab.2 The friction coefficients of contact boundary
随着时间的推移应力条纹越来越明显。 应力条纹的 出现是由于装配时在防皱模与芯棒之间留有一定的 间距,弯曲模转动,铝管发生塑性流动,导致防皱模 受力成条纹状。 3.2 摩擦系数对防皱模具磨损的影响
为了研究不同摩擦系数, 不同材料对防皱模磨 损深度的影响, 设置了一组以摩擦系数为变量的模 拟 方 案 : 摩 擦 系 数 为 0.1、0.15、0.2、0.25、0.3、0.35、 0.4。 模拟结束后,找出各时间点处最大接触压力,并 求出平均最大接触压力代入式(4)计算磨损量(图3)。
1 有限元模型的建立及关键技术处理
1.1 绕弯模型的建立 采用有限元软件 ABAQUS/Explicit 建立三维有
限元绕弯模型(图 1)。 绕弯成形模型由夹块、滑块、弯 曲模、防皱模、芯棒组成。将模型中夹块、滑块、芯棒、 弯曲模定义为离散刚体。 在弯曲成形过程中夹块给 管坯一定的夹持力使夹块、 管坯成为一体随着弯曲 模一起转动。 在整个弯曲过程中芯棒起内部支撑作 用并固定不动,芯头随管坯一起转动。
S=L= α°πR
(3)
180°
在有限元分析中通过计算得到严重磨损区域的
节点,计算节点处的磨损深度。各节点 i 的深度表示为:
wi=
Kp[i]S[i] 3HV
(4)
设置弯管时间为 0.01 s,在管坯弯曲过程中,防皱模
受力在每个时间增量处都是变化的。 文中计算所取
的接触压力 p 为弯曲过程中最大接触应力平均值。
在数值磨损研究方面,Lundvall[3]等 研究了两弹 性体在接触过程中磨损计算利用有限元对弹性体进 行离散化处理, 并使弹性体在接触过程中遵循 Archard 磨损定律,用非光滑牛顿法进行计算。Li[4]等 建立了微观动态磨损仿真模型用以模拟磨损过程以 及预测磨损过程中的材料性能变化。 Olofsson[5]等研 究了圆柱推力轴承在润滑状态下的磨损仿真用
11.59
200 0.25
铝管(6061) 180 2700 896
17.92
73 0.33
管 坯 与 防 皱 模 均 采 用 C3D8R 缩 减 积 分 单 元 , 在绘制网格时考虑控制缩减积分单元存在的沙漏情 况。 其它模具由于是刚体所以采用离散刚体单元 R3D4。 在装配的过程中由于各个模具与管坯之间的 间隙比较小,注意控制零件相互干涉。 1.3 边界条件及载荷的施加
pi
=
p1max+p2max 3HV
(5)
3 仿真结果分析
3.1 防皱模受力分析 为了分析防皱模受力情况, 设置摩擦系数为
0.1,弯 曲 角 位 移 为 0.785 rad,弯 曲 相 对 半 径 为 2.5, 矩形管壁厚 0.5 mm 的弯曲模型计算条件。
图 2 为前 3 个时间点处防皱 模 VonMises 应力 分布情况。由图可知:弯曲过程中防皱模受力集中在 前端,产生局部应力集中。出现此现象的原因是随着 弯曲模转动管坯产生变形, 此时芯棒阻止管坯的变 形,导致管坯对防皱模的挤压力较大,防皱模后端受 力不大是由于管坯与其装配时留有一定的间距,此 处管坯无明显变形,管坯对防皱模挤压力较小。防皱 模前端发生塑性变形,应力主要以条纹的形式分布,
文 章 编 号 :1001-3814(2014)01-0112-03
Simulation on Wear of Pipe Bending Forming Die
LI Qinfeng, ZHANG Lijun, LI Dongsheng, LI Changwei
(School of Mechanical Engineering, Jiangsu University of Science and Technology, Jiangsu 212003, China) Abstract:The thermo-mechanical numerical wear model of shrink-proof die in tube bending forming process was established. The bending process was numerically simulated by using nonlinear function of the finite element software ABAQUS/Explicit. The stress distribution of shrink-proof die in the process of bending was revealed. The influences of different thickness and materials of the pipe, friction coefficients on the die wear were researched by adopting Archard′s wear model. This can provide some references for the design of die, bending process and the prediction of die life. Key words:bending forming; finite element; wear; shrink-proof die