3弯曲工艺与弯曲模具设计详解
合集下载
模具设计与制造第6章弯曲工艺与模具设计

06
总结与展望
弯曲工艺与模具设计的现状与挑战
现状
随着制造业的快速发展,弯曲工艺与模具设计在产品制造中占据重要地位。目前,弯曲工艺与模具设 计已经取得了长足进步,能够满足多种复杂形状的加工需求。
挑战
然而,在弯曲工艺与模具设计过程中,仍存在一些挑战,如高精度控制、复杂曲面加工、高效自动化 等方面的问题。
未来发展方向与技术前沿
柔性制造技术
随着个性化需求的增加,柔性制造技术将成为未 来发展的重点。通过柔性制造技术,可以实现快 速、高效、个性化的产品制造,提高生产效率和 降低成本。
增材制造技术
增材制造技术是一种基于数字模型的快速成型技 术,能够实现复杂形状的高精度加工。未来,增 材制造技术有望在弯曲工艺与模具设计中发挥更 大的作用。
模具材料的选择蚀性等。
常用材料
碳素工具钢、合金工具钢、硬质合金、铸铁等。
材料处理
热处理、表面处理等。
模具设计的流程与方法
设计流程
明确设计任务→收集设计资料→设计 出图→审查→修改。
设计方法
经验设计法、解析设计法、计算机辅 助设计法等。
04
弯曲工艺与模具设计的关系
THANK YOU
模具设计对弯曲工艺的影响
模具结构
模具的结构对弯曲工艺的实施具 有重要影响,合理的模具结构可 以提高弯曲效率并降低不良品率。
模具材料
模具材料的选取直接影响弯曲工艺 的效果,选用高强度、耐磨和耐热 的材料可以提高模具的使用寿命和 弯曲质量。
冷却系统
模具中的冷却系统对于控制弯曲过 程中的温度至关重要,合理的冷却 系统设计可以减少热应力,提高产 品质量。
02
弯曲工艺的基本原理
弯曲变形的过程与特点
第3章弯曲工艺与模具设计
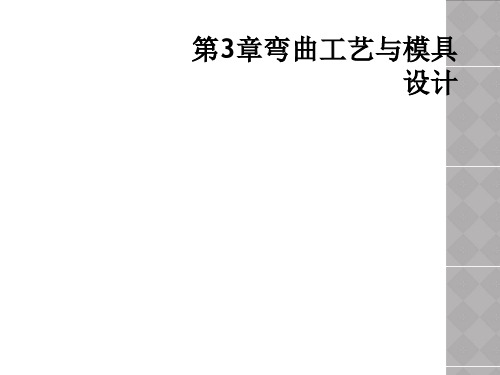
17
4. 弯曲后的翘曲与剖面畸变 ➢ 细而长的坯料弯曲件,弯曲后纵向产生翘曲变形 ➢ 在薄壁管的弯曲中,还会出现内侧面因受压应力的作用而失稳起皱的现象
18
3.3.3 弯曲力计算 1. 自由弯曲时的弯曲力 V形件弯曲力 U形件弯曲力
2. 校正弯曲时的弯曲力
F自
0.6Kb2tb
rt
F自
0.7Kb2tb
37
3.5.2 弯曲凹模工作部分深度 38
3.5.3 弯曲凸模和凹模之间的间隙 对于V形件弯曲模,凸模和凹模之间的间隙是由调节压力机的装模高度来控制的。对于U形件弯 曲模,则应选择合适的间隙。
Ztma x c ttct
式中
39
3.5.4 U形件弯曲凸模和凹模宽度尺寸的计算 U形件弯曲凸模和凹模宽度尺寸计算与工件尺寸的标注有关。一般原则是:工件标注外形尺寸 时,则模具以凹模为基准件,间隙取在凸模上;工件标注内形尺寸时,则模具应以凸模为基 准件,间隙取在凹模上。
40
1. 标注外形尺寸的U形件
图3-55 标注外形尺 寸的U形件
41
2. 标注内形尺寸的U形件
图3-56 标注内形尺寸 的U形件
42
3.6 弯曲模结构设计时应注意的问题 ➢ 模具结构应保证坯料在弯曲时不发生偏移。为了防止坯料偏移,应尽量利用零件上的孔,用定位销定位。定
位销装在顶板上时,应注意防止顶板与凹模之间产生窜动。若工件无孔,但允许在坯料上冲制工艺孔时,可 以考虑在坯料上设计出定位工艺孔。当工件不允许有工艺孔时,可采用顶杆、顶板等压紧坯料,防止弯曲过 程中坯料的偏移。 ➢ 模具结构设计时,应注意放入和取出工件的操作要安全、迅速和方便。 ➢ 对于对称弯曲件,弯曲件凸模圆角半径和凹模圆角半径应保证两侧相等,以免弯曲时坯料发生滑动和偏移。
4. 弯曲后的翘曲与剖面畸变 ➢ 细而长的坯料弯曲件,弯曲后纵向产生翘曲变形 ➢ 在薄壁管的弯曲中,还会出现内侧面因受压应力的作用而失稳起皱的现象
18
3.3.3 弯曲力计算 1. 自由弯曲时的弯曲力 V形件弯曲力 U形件弯曲力
2. 校正弯曲时的弯曲力
F自
0.6Kb2tb
rt
F自
0.7Kb2tb
37
3.5.2 弯曲凹模工作部分深度 38
3.5.3 弯曲凸模和凹模之间的间隙 对于V形件弯曲模,凸模和凹模之间的间隙是由调节压力机的装模高度来控制的。对于U形件弯 曲模,则应选择合适的间隙。
Ztma x c ttct
式中
39
3.5.4 U形件弯曲凸模和凹模宽度尺寸的计算 U形件弯曲凸模和凹模宽度尺寸计算与工件尺寸的标注有关。一般原则是:工件标注外形尺寸 时,则模具以凹模为基准件,间隙取在凸模上;工件标注内形尺寸时,则模具应以凸模为基 准件,间隙取在凹模上。
40
1. 标注外形尺寸的U形件
图3-55 标注外形尺 寸的U形件
41
2. 标注内形尺寸的U形件
图3-56 标注内形尺寸 的U形件
42
3.6 弯曲模结构设计时应注意的问题 ➢ 模具结构应保证坯料在弯曲时不发生偏移。为了防止坯料偏移,应尽量利用零件上的孔,用定位销定位。定
位销装在顶板上时,应注意防止顶板与凹模之间产生窜动。若工件无孔,但允许在坯料上冲制工艺孔时,可 以考虑在坯料上设计出定位工艺孔。当工件不允许有工艺孔时,可采用顶杆、顶板等压紧坯料,防止弯曲过 程中坯料的偏移。 ➢ 模具结构设计时,应注意放入和取出工件的操作要安全、迅速和方便。 ➢ 对于对称弯曲件,弯曲件凸模圆角半径和凹模圆角半径应保证两侧相等,以免弯曲时坯料发生滑动和偏移。
第3章 弯曲工艺与模具设计

3.2.2、影响回弹的因素 材料的机械性能 相对弯曲半径 弯曲中心角 模具间隙 弯曲件的形状 弯曲力
3.2.3、回弹值的确定 目的:作为修正模具工作部分参数的 依据。 经验公式: 1.小半径弯曲的回弹( r / t 5 ~ 8 )
0 t
rt r 1 3
90
90
6)弹性材料的准确回弹值需要通过试模对凸、 凹模进行修正确定,因此模具结构设计要便于拆 卸。 7)由于U形弯曲件校正力大时会贴附凸模,所以 在这种情况下弯曲模需设计卸料装置。 8)结构设计应考虑当压力机滑块到达下极点时, 使工件弯曲部分在与模具相接触的工作部分间得 到校正。 9)设计制造弯曲模具时,可以先将凸模圆角半 径做成最小允许尺寸,以便试模后根据需要修整 放大。
当工件局部边缘部分需弯曲时,为防 止弯曲部分受力不均而产生变形和裂纹, 应预先切槽或冲工艺孔(如图所示) 5.弯曲件的几何形状 如果弯曲件的形状不对称或者左右弯 曲半径不一致,弯曲时板料将会因摩擦阻 力不均匀而产生滑动偏移(如图所示), 为了防止这种现象的发生,应在模具上设 置压料装置,或利用弯曲件上的工艺孔采用 定位销定位(如图所示)
第 3 章 弯曲工艺与模具设计
3.1
3.2
弯曲的基本原理 应变中性层位置、最小弯曲半径的确定及回弹现象 弯曲力和弯曲件的毛坯尺寸计算 弯曲件的工艺性 弯曲模具的设计
3.3 3.4
3.5
3.1 弯曲的基本原理
弯曲是使材料产生塑性变形,形成一 定曲率和角度零件的冲压工序(如图所示) 弯曲材料:板料、棒料、型材、管材 弯曲方法:压弯、折弯、拉弯、滚弯、 辊弯
3.1.1 弯曲变形过程 (图3.1.1) 1、变形毛坯的受力情况 从力学角度,弯曲分为: 弹性弯曲 弹塑性弯曲 纯塑性弯曲 无硬化弯曲
03第三章弯曲工艺与弯曲模设计(冷冲压工艺及模具设计)
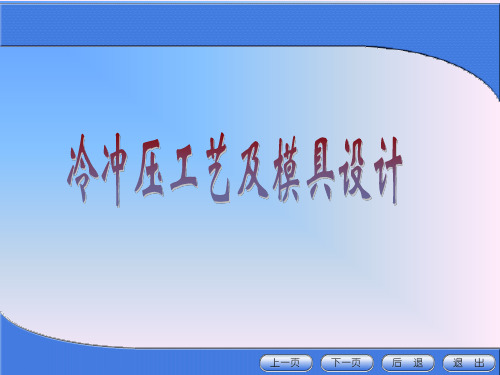
弯曲中心角为90°时部分材料的平均回弹角见表3-3。
当弯曲件弯曲中心角不为90°时,其回弹角可用下式计算:
90
90
第三章 弯曲工艺与弯曲模设计
第三节 弯曲卸载后的回弹
三、回弹值的确定(续)
3.校正弯曲时的回弹值 校正弯曲的回弹可用
试验所得的公式(见表 3.3.2)计算,符号如右图 所示。
校正弯曲圆角部分的回弹比自由弯曲时大为减小。
校正弯曲时圆角部分的较小正回弹与直边部分负回弹的抵
销 ,回弹可能出现正、零或是负三种情况。
(3)在弯曲U形件时,凸、凹模之间的间隙对回弹有较大的影响。 间隙越大,回弹角也就越大,如图3.3.5所示。
第三章 弯曲工艺与弯曲模设计
第三节 弯曲卸载后的回弹
二、影响回弹的因素(续)
生活中的弯曲零件
第三章 弯曲工艺与弯曲模设计
用 模 具 成 形 弯 曲 件 一
第三章 弯曲工艺与弯曲模设计
用 模 具 成 形 弯 曲 件 二
第三章 弯曲工艺与弯曲模设计
复习上次课内容
1.板料弯曲的变形特点?最小弯曲半径 2.表示弯曲变形程度的参数是什么?表示弯曲时成形极限的 参数是什么? 3.提高弯曲极限变形程度的方法?
10-定位板
第三章 弯曲工艺与弯曲模设计
V 形 弯 曲 板 材 受 力 情 况
1-凸模 2-凹模
第三章 弯曲工艺与弯曲模设计
弯 曲 过 程
第三章 弯曲工艺与弯曲模设计
弯
曲
前
弯曲前
坐 标
网
格
的
变
化
弯曲后
第三章 弯曲工艺与弯曲模设计
窄板(B/t3) 宽板(B/t3)
项目三 弯曲工艺与模具设计

图3-18 圆角半径r>0.5t的展开长度
图3-19 90°角弯曲件
项目三 弯曲工艺与模具设计
(2)圆角半径r<0.5t弯曲件展开长度。
表3-5 r <0.5t的弯曲件坯料长度计算公式
项目三 弯曲工艺与模具设计
(3)铰链式弯曲件
图3-20 铰链式弯曲件 表3-6 卷边时中性层位移xi值
项目三 弯曲工艺与模具设计
图3-2 弯曲件的弯曲方法
项目三 弯曲工艺与模具设计
本项目以如图3-3所示的U 形零件的弯曲模设计为载体,综合训练学 生确定弯曲成形工艺和设计弯曲模具的初步能力。
图3-3 U形弯曲件零件图
项目三 弯曲工艺与模具设计
二、相关知识
(一) 弯曲变形过程及特点 1.弯曲变形过程
图3-4 弯曲变形过程
项目三 弯曲工艺与模具设计
表3-8 弯曲件长度的自由公差
表3-9 弯曲件角度的自由公差
9.弯曲件的材料
项目三 弯曲工艺与模具设计
(六)弯曲的工序安排 1.弯曲件工序安排的原则 2.典型弯曲件的工序安排
图3-29 一道工序弯曲成形
图3-30 两道工序弯曲成形
项目三 弯曲工艺与模具设计
图3-31 三道工序弯曲成形 图3-32 四道工序弯曲成形
(四)弯曲力计算 弯曲力是选择压力机和设计模具的重要依据之一。 1.自由弯曲的弯曲力 2.校正弯曲的弯曲力
表3-7 单位校正力q
3.顶件力或压料力 4.压力机吨位的确定
项目三 弯曲工艺与模具设计
(五)弯曲件的工艺性 1.弯曲半径 2.弯曲件的形状
图3-21 弯曲件的形状
项目三 弯曲工艺与模具设计
带有切口弯曲的工件,弯曲部分一般应做成梯形以便于出模。也可以 先冲出周边槽孔,然后弯曲成形,如图3-22 (b)所示。
精选弯曲工艺与弯曲模设计
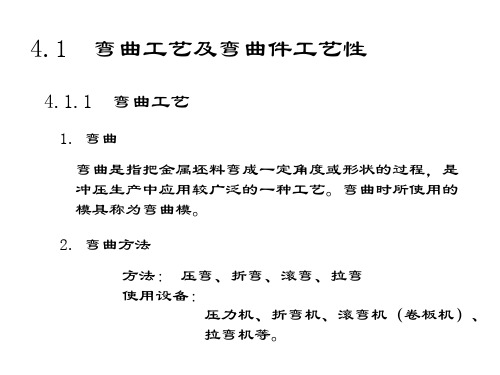
3.弯曲件的直边高度
直边高度H过小,那么直边在弯曲模上支承的长度也过小,不易形成足够的弯矩,弯曲件的形状难以控制。
如果
可加大直边高度,待弯曲成形后,再将直边的高出部分切除。
当弯曲边带有斜度时,应保证
图 4-9 直边高度要求
4.弯曲件孔边距
图 4-10 弯曲件孔边距
图 4-11 防止孔变形的措施
(5)弯曲校正力。 弯曲校正力愈大,塑性变形程度愈大,回弹愈小。
3.减小回弹的措施
1)补偿法
预先估算或试验出工件弯曲后的回弹量,在设计模具时,使弯曲件的变形量超过原设计量,工件回弹后就得到所需要的正确形状。
图 4-30 补偿法示意图
2)校正法
图 4-31 校正法示意图
校正压力集中施加在弯曲变形区,使其塑性变形成分增加,弹性变形成分减小,从而使回弹量减小。
2.弹-塑性弯曲阶段
促使材料塑性变形的弯曲力矩是逐渐增大的。由于弯曲力臂l逐渐减小,因此弯曲力处于不断上升的趋势。凸模继续下行,板料与凸模V形斜面接触后被后向弯曲。
后向弯曲
3. 塑性弯曲阶段
当凸模到达下止点时,毛坯被紧紧地压在凸模与凹模之间,使毛坯内侧弯曲半径与凸模的弯曲半径吻合,完成弯曲过程,变形由弹—塑性弯曲过渡到塑性弯曲。
2.工序安排方法
(1)简单形状一次弯曲成形
图 4-36 一道工序弯曲成形
(2)复杂形状,一般采用两次或多次弯曲成形
图 4-37 二道工序弯曲成形
图 4-38 三道工序弯曲成形
(3)对于某些结构不对称的零件,采用弯曲后再切开的方法
图 4-39 成对弯曲成形
(4)弯曲件有高精度孔时,采用先弯曲后冲孔的方法
4.4.2 弯曲力的计算
第三章:弯曲工艺与弯曲模具设计

校正弯曲时,回弹角修正量: K90
不是90°的角按下式修正: x ( / 90)90
➢ 当r/t < 8~10时,要分别计算弯曲半径和弯曲角的回弹值,再修正。
弯曲板料时
凸模的圆角半径: rp 1/(1/ r) (3 s / Et)
凸模圆弧所对中心角: p
(r
/ rp )
弯曲件的滑移
6. 最小弯曲半径 rmin
❖ r/t 小 —— 变形程度大 —— 弯曲破坏。 影响最小弯曲半径的因素:
❖ 材料的机械性能:好塑性(塑稳)、退火处理、热弯、开槽减薄 ❖ 方向性:折弯线垂直纤维方向:伸长变形能力强
❖ 板宽:B/t 小(< 3) ❖ 弯曲角:小, 直边有切向形变。 ❖ 板料表面质量和断面质量:差处易应力集中发生破坏。 ❖ 板料厚度:t小 —— 切向应变小 —— 开裂小。
弯曲件的工序安排
1. 工序安排的一般原则 ➢ 先弯外角后弯内角,后次弯曲不能影响前一次弯曲变形,前次弯曲应考 虑后次弯曲有合适的定位基准。 ➢ 当有多种方案时,要进行比较,进行优化。
2. 工序安排的一般方法 ➢ 形状简单的弯曲件可一次弯曲成形。如V形、U形、Z形。 ➢ 形状复杂的弯曲件可用两次或多次压弯成形。
➢ r/t值
小r/t: 加厚筋边或 减小 r; 其值大时拉弯
(在同条件下,r/t越小,则总变形量就越大,回弹就越小。) 工艺处理
➢ 弯曲中心角
(α越大,变形区长度越长,参与变形的区域越大,回弹越多。)
小
➢ 弯曲方式与校正力大小
(自由弯曲回弹大,校正弯曲回弹小,校正力越大回弹越小。)
➢ 工件形状
(工件形状越复杂,回弹就越少。)
弹-塑性变形: 塑性变形:
L1-L2 ,r1-r2 超过屈服极限,
弯曲工艺及模具设计

减小量,则 ( 3-源自)弯曲角(弯曲件两直边间的夹角,它与弯曲中心角度间的 关系为:)的增大量为:
( 3-3)
计算出的、()即为弯曲件的回弹量,但是与实际冲压生 产中的回弹量相比,有一定的差别,其原因是影响弯曲回 弹有多种因素。
2)影响回弹的因素 1)材料的力学性能。材料的屈服强度越大,弹性模量越小,
(二) 弯曲件质量分析
1. 弯裂 (1) 最小弯曲半径
弯曲半径是指弯曲件内侧的曲率半径(图3-5中的r)。 由弯曲变形可知,弯曲时板料的外侧受拉伸,当外侧的拉 伸应力超过材料的抗拉强度时,在板料的外侧将产生裂纹, 这种现象称为弯裂。弯曲件是否弯裂,在相同板料厚度的 条件下,主要与弯曲半径r有关,r越小,弯曲变形程度越 大,因此存在一保证外层纤维不产生弯裂时所允许的最小 弯曲半径rmin,即在板料不发生破坏的条件下,所能弯成零 件内表面的最小圆角半径称为最小弯曲半径rmin,并用它来 表示弯曲时的成形极限。
二、相关知识
(一) 弯曲变形过程及特点
1.弯曲变形过程 本章以V形件弯曲为例说明弯曲变形过程,如图3-4所
示。在开始弯曲时,毛坯的弯曲内侧半径大于凸模的圆角 半径。随着凸模的下压,毛坯的直边与凹模V形表面逐渐 靠近,弯曲内侧半径逐渐减小,即
r0>r1>r2>r 同时弯曲力臂也逐渐减小,即
l0>l1>l2>lk 当凸模、毛坯与凹模三者完全压合,毛坯的内侧弯曲
5)对于较厚材料的弯曲,若结构允许,可先在弯曲圆角内 侧开槽,再进行弯曲,如图3-7所示。
2.弯曲回弹
1) 弯曲回弹现象 常温下的塑性弯曲与其它塑性变形一样,总是伴随有
弹性变形。当弯曲结束,外力去除后,塑性变形保留了下 来,而弹性变形则完全消失,使得弯曲件的形状和尺寸发 生变化而与模具尺寸不一致,这种现象称为弯曲回弹(简 称回弹)。
- 1、下载文档前请自行甄别文档内容的完整性,平台不提供额外的编辑、内容补充、找答案等附加服务。
- 2、"仅部分预览"的文档,不可在线预览部分如存在完整性等问题,可反馈申请退款(可完整预览的文档不适用该条件!)。
- 3、如文档侵犯您的权益,请联系客服反馈,我们会尽快为您处理(人工客服工作时间:9:00-18:30)。
工件的形状越复杂,一次弯曲所成形的角度数量越多,
使回弹困难,因而回弹角减小。 6.模具间隙 在压弯U形件时,间隙大,材料处于松动状态,回弹就 7.非变形区的影响
弯曲工艺和弯曲模具设计
减少回弹的措施
1.材料选择 应尽可能选用弹性模数大的,屈服极限小,机械性比较稳 定的材料。 2.改进弯曲件的结构设计 设计弯曲件时改进一些结构,加强弯曲件的刚度以减小回 弹。比如:在变形区压加强肋或压成形边翼,增加弯曲件的刚 性,使弯曲件回弹困难(如图3.2.3)。
弯曲工艺和弯曲模具设计
弯曲工艺和弯曲模具设计
4. 从模具结构采取措施 (1) 补偿法
利用弯曲件不同部位回弹方向相反的特点,按预先估算 或试验所得的回弹量,修正凸模和凹模工作部分的尺寸和几 何形状,以相反方向的回弹来补偿工件的回弹量(如图3.2.9) 。 (2)校正法 可以改变凸模结构,使校正力集中在弯曲变形区,加大变 形区应力应变状态的改变程度(迫使材料内外侧同为切向压应 力、切向拉应变 )如图3.2.10。 (3) 纵向加压法 在弯曲过程完成后,利用模具的 突肩在 弯曲件的端部纵 向加压(如图 3.2.11), 使弯曲变形区横断面上都受到压应 力,卸载时工件内外侧的回弹趋势相反,使回弹大为降低。利 用这种方法可获得较精确的弯边尺寸,但对毛坯精度要求较高。
弯曲工艺和弯曲模具设计
3.2.3
改进零件的结构设计
弯曲工艺和弯曲模具设计
3. 从工艺上采取措施
(1)采用热处理工艺 对一些硬材料和已经冷作硬化的材料,弯曲前先进行退火处理, 降低其硬度以减少弯曲时的回弹,待弯曲后再淬硬。在条件允许的情 况下,甚至可使用加热弯曲。 (2)增加校正工序 运用校正弯曲工序,对弯曲件施加较大的校正压力,可以改变其 变形区的应力应变状态,以减少回弹量。 (3)采用拉弯工艺 对于相对弯曲半径很大的弯曲件,由于变形区大部分处于弹性变形 状态,弯曲回弹量很大。这时可以采用拉弯工艺 (如图3.2.4)。
弯曲工艺和弯曲模具设计
3.1.3弯曲时变形区的应力和应变
板料在塑性弯曲时,变形区 内的应力应变状态取决于弯曲 毛坯的想对宽度 b / t 以及弯曲 变形程度。
窄板弯曲的应力状态是 平面的,应变状态是立体的。
宽板弯曲的应力状态是立 体的,应变状态是平面的。
弯曲工艺和弯曲模具设计 弯曲卸载后弯曲件的回弹
2.相对弯曲半径 r / t 相对弯曲变径 r / t 越大,则回弹也越大。 3.弯曲中心角 弯曲中心角 越大,表明变形区的长度越长,故回弹的 积累值越大,其回弹角越大。但对弯曲半径的回弹影响不大。
弯曲工艺和弯曲模具设计
4.弯曲方式及弯曲模具结构 采用校正弯曲时,工件的回弹小。 5.弯曲件形状
弯曲工艺和弯曲模具设计
图3.2.10
用校正法修正模具结构
弯曲工艺和弯曲模具设计
3.3.1最小相对弯曲半径( r min/ t )
1.最小相对弯曲半径的概念 最小相对弯曲半径是指:在保证毛坯弯曲时外表面不发 生开裂的条件下,弯曲件内表面能够弯成的最小圆角半径与 坯料厚度的比值,用 r min/ t 来表示。该值越小,板料弯曲 的性能也越好。 2. 影响最小弯曲半径的因素 (1)材料的力学性能 (2)工件的弯曲中心角
b/t 3
:横断面几乎不变;
b / t 3 :断面变成了内宽外窄的扇形。
弯曲工艺和弯曲模具设计
3.1.3弯曲时变形区的应力和应变
1、弹性弯曲条件 若材料的屈服应力为 σs , 则弹性弯曲的条件为:
r 1 E 1 t 2 s
2、塑性弯曲的应力与应变条件
(a)弹性弯曲; (b)弹-塑性弯曲; (c)塑性弯 曲 图3.1.5弯曲毛坯变形区的切向应力分布
回弹现象
当弯曲结束,外力去除后,塑性变形留存下来,而弹性 变形则完全消失。弯曲变形区外侧因弹性恢复而缩短,内侧 因弹性恢复而伸长,产生了弯曲件的弯曲角度和弯曲半径与 模具相应尺寸不一致的现象。这种现象称为弯曲件的弹性回 跳(简称回弹)。
弯曲工艺和弯曲模具设计
影响回弹的因素
1.材料的力学性能 材料的屈服点 s 越高,弹性模量E越小,弯曲弹性回跳 越大。
弯曲工艺和弯曲模具设计
3.1板料弯曲变形过程及变形特点
3.1.1弯曲变形过程
弯曲变形过程:如图所示V形件的弯曲,随着凸模进 入凹模深度的增大,凹模与板料的接触处位置发生变化,支点 B沿凹模斜面不断下移,弯曲力臂l 逐渐减小,接近行程终了, 时弯曲半径r继续减小,而直边部分反而向凹模方向变形, 直至板料与凸、凹模完全贴合。
3.1.2板料弯曲变形特点
通过网格试验观察弯曲变形特点(如图)。
弯曲工艺和弯曲模具设计
弯曲工艺和弯曲模具设计
图3.1.3
弯曲前后坐标网络的变化
弯曲工艺和弯曲模具设计
1.弯曲圆角部分是弯曲变形的主要变形区 变形区的材料外侧伸长,内侧缩短,中性层长度不变。 2.弯曲变形区的应变中性层 应变中型层是指在变形前后金属纤维的长度没有发生改 变的那一层金属纤维。 3. 变形区材料厚度变薄的现象 变形程度愈大,变薄现象愈严重。 4.变形区横断面的变形 变形区横断面形状尺寸发生改变称为畸变。主要影响因 素为板料的相对宽度。 (宽板) (窄板)
(3)板料的表面质量与剪切断面质量
(4) (5)板材的方向性
弯曲工艺和弯曲模具设计
图3.4.4 U形件弯曲模具 1-凸模;2-凹模;3-弹簧;4-凸模活动镶块;5、9-凹模活动镶块;6-定位销;7-转轴;8-顶板
弯曲工艺和弯曲模具设计
弯曲是使材料产生塑性变形,形成一定曲率和角 度零件的冲压工序。 弯曲毛坯的种类:板料、棒料、型材、管材
弯曲工艺和弯曲模具设计
弯曲工艺和弯曲模具设计
弯曲工艺和弯曲计
弯曲成型工艺方法:压弯、折弯、拉弯、滚弯、辊弯
(a)模具压弯; (b)折弯; (c)拉弯; (d)滚弯; (e)辊压 弯曲零件的成形方法