危害因素辨识(PHA)
pha(预先危险性分析)
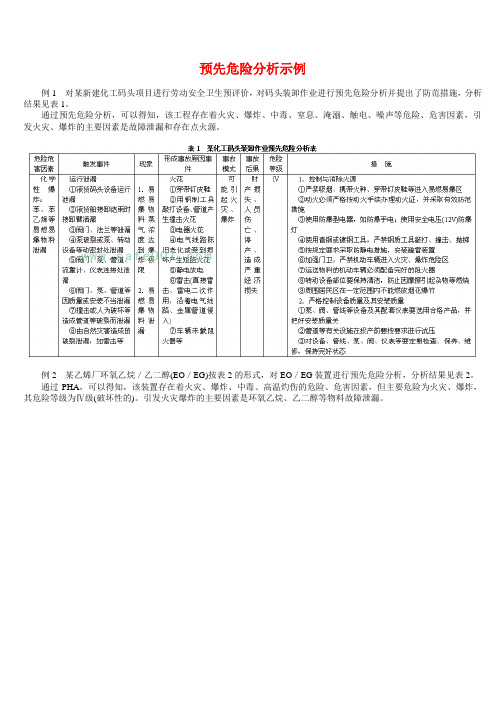
预先危险分析示例
例1 对某新建化工码头项目进行劳动安全卫生预评价,对码头装卸作业进行预先危险分析并提出了防范措施,分析结果见表1。
通过预先危险分析,可以得知,该工程存在着火灾、爆炸、中毒、窒息、淹溺、触电、噪声等危险、危害因素,引发火灾、爆炸的主要因素是故障泄漏和存在点火源。
例2 某乙烯厂环氧乙烷/乙二醇(EO/EG)按表2的形式,对EO/EG装置进行预先危险分析,分析结果见表2。
通过PHA,可以得知,该装置存在着火灾、爆炸、中毒、高温灼伤的危险、危害因素,但主要危险为火灾、爆炸,其危险等级为Ⅳ级(破坏性的)。
引发火灾爆炸的主要因素是环氧乙烷、乙二醇等物料故障泄漏。
危险有害因素识别原则:PHA、安全检查表等十大工具

危险有害因素识别原则:PHA、安全检查表等十大工具危险、有害因素的识别原则在工业生产和工程项目中,危险和有害因素是导致事故和职业病的主要原因。
为了预防这些风险,需要对危险和有害因素进行识别和评估。
以下是常见的危险、有害因素的识别原则:1.预先危险性分析(Preliminary Hazard Analysis,PHA)2.PHA是一种在活动开始之前对可能的危险和有害因素进行识别、评估和分类的过程。
它主要用于初步筛选可能存在的高风险操作或设备。
3.安全检查表(Safety Checklist)4.安全检查表是一种用于识别潜在危险的标准化工具,通常由一系列问题或检查项组成,旨在评估特定设备、系统或操作的安全性。
5.故障类型及影响分析(Failure Modes and Effects Analysis,FMEA)6.FMEA是一种系统化的故障分析工具,用于识别系统或过程中潜在的故障模式,并评估其对系统性能的影响。
7.故障树分析(Fault Tree Analysis,FTA)8.FTA是一种逻辑图解方法,用于识别和分析系统中可能的故障路径。
它通过将高级故障(顶层)分解为更低级(中间和底级)的故障类型来识别潜在的危险因素。
9.事件树分析(Event Tree Analysis,ETA)10.ETA是一种系统化的风险分析工具,用于识别特定事件链可能导致的事故后果。
它通过从初始事件开始,分析并识别可能产生的后续事件来识别潜在的危险因素。
11.作业危害分析(Job Hazard Analysis,JHA)12.JHA是一种针对特定作业任务进行的风险评估方法,用于识别作业过程中可能面临的危害因素。
13.定量风险评估(Quantitative Risk Assessment,QRA)14.QRA是一种使用数学模型对危险因素进行量化和评估的方法,以确定其可能导致的损失或影响。
15.定性风险评估(Qualitative Risk Assessment,QRA)16.定性风险评估是一种基于经验和判断的方法,用于评估危险因素的性质、严重程度和可能性。
工艺危害分析(PHA)管理规范

5.1.4 PHA的实施时机见附录B。
PHA
PHA过程通常分为计划和准备、危害辨识、后果分析、危害评估、风险评估、建议的提出、回复和关闭、PHA报告、建议的追踪9个步骤。具体流程见附件C
计划和准备
直线组织管理层(领导小组)应制定PHA工作任务书,规定PHA工作组职责、任务和目标,选择工作组成员、提供工作组所需的资源和必需的培训。
导。在现场察看时,工作组应将装置与工艺流程图(P&IDs)作对照,确定图纸的准确性。现场察看是为了确保工作组对所分析的工艺和区域布置有清楚的了解,并辨识、补充完善危害清单。
后果分析
后果分析的目的是帮助工作组了解潜在伤害的类型、严重性和数量,可能的财产损失以及重大的环境影响。
5.5.1工作组应针对危害辨识清单进行后果分析,可采用定性或定量的方法进行。在后果分析时应考虑以下内容:
3.5有害物质(Hazard substance):指在泄放时或释放能量时会造成严重的人员伤害、重大的财产损失、或严重的环境危害的化学物质或材料。
3.6工艺危害分析(PHA):由“工艺危害评审(PHR)”和“后果分析(CA)”两部分组成。它采用有组织的系统化的研究方法,以寻求控制危害的各方面的一致性意见,并将结果归档,用于将来的跟进、应急计划以及与该工艺过程有关的操作、维护人员的培训。
15
应用类型
a)下列情况之一者应进行PHA:
1)研究和技术开发)
2)新改扩建项目;
3) 在用装置;
4)封存装置;
5) 装置拆除。
b)PHA也可有效地应用于以下情况:
1)变更管理活动;
2) 事故调查;
工艺危害分析PHA---易安-安全从业-安全生产-安全

工艺危害分析(PHA )工艺危害分析是PSM 的核心要素,它是有组织的、系统的对工艺装置或设施进行危害辨识,为消除和减少工艺过程中的危害、减轻事故后果提供必要的决策依据。
工艺危害分析关注设备、仪表、公用工程、人为因素及外部因素对于工艺过程的影响,着重分析着火、爆炸、有毒物泄漏和危险化学品泄漏的原因和后果。
工艺危害分析方法有很多种,PSM 推荐的危害分析方法有:1)如果……,会怎么样?”提问法;2)安全检查表;3)“如果…… ,会怎么样?”提问法结合安全检查表;4)危险性与可操作性研究;5)故障模式与后果分析;6)故障树分析;7)或者等效的其他方法。
工艺危害分析是件很耗费时间的工作,但是意义重大。
工厂需要根据自身工艺的特点选择适当的危害分析方法。
对于化工厂和石化工厂,目前最普遍采用的危害分析方法是HAZOP ,同时辅助采用安全检查表法弥补HAZOP 方法的某些不足。
HAZOP 是20 世纪70 年代由帝国化学公司(ICI)发明的一种定性危害分析方法,也是针对工艺过程最系统、有效的危害分析方法之一。
在进行工程设计时,主要是依靠各种标准、规范、设计指南以及设计人员的经验和知识来实现工艺系统的安全与可靠性。
上述标准、规范或设计指南主要反映的是“正常工况下工艺系统需要满足的情况。
由于设备故障、人为错误或外部影响等原因,工艺系统在运行过程中可能偏离正常工况,导致工艺安全事故。
此外,在项目工期紧张的情况下,设计人员的压力很大,容易犯错误,需要在工艺设计阶段就进行周全的考虑。
HAZOP 可以应用于不同行业、不同规模和复杂程度各异的工艺系统,只要是包含工艺流程的系统。
对新建项目的工艺设计、现有工艺系统的变更以及当前正在运行的装置都可以应用。
利用HAZOP 方法进行危害分析是有组织的头脑风暴活动,通常需要由一个包括不同专业人员所组成的分析小组来完成。
将复杂的工艺系统划分成不同的部分,称为节点(Node),然后针对每个节点进行具体的分析。
PHA危害识别,风险评估

沈阳山盟建筑集团
危险 原因(危害) 违章操作 拆除 氧气乙炔距离不够 未设立“禁止进入”标志 未带呼吸器等安全器材 进放受限空间 清洗工具非铝制材料 在作业现场未穿带防护服 带电子设备进入罐区及内部 现场未带安全带、安全帽 高空抛物 雷雨天作业 高空作业 违章操作 脚手架倒塌 未设立安全指示标志 未设立安全警界线 违章操作 违规指挥 消防器材不足 用火作业 未设立安全指示标志 施工现场使用明火 施工现场有易然、易爆品 施工现场用火工具摆放不合格 主要后果 火灾、人员伤亡、财产损失 火灾、人员伤亡、财产损失 人员伤亡 人员伤亡 火灾、人员伤亡、财产损失 火灾、人员伤亡、财产损失 火灾、人员伤亡、财产损失 人员伤亡、财产损失 人员伤亡、财产损失 火灾、人员伤亡、财产损失 火灾、人员伤亡、财产损失 人员伤亡、财产损失 人员伤亡、财产损失 火灾、人员伤亡、财产损失 火灾、人员伤亡、财产损失 火灾、人员伤亡、财产损失 火灾、人员伤亡、财产损失 火灾、人员伤亡、财产损失 火灾、人员伤亡、财产损失 火灾、人员伤亡、财产损失 火灾、人员伤亡、财产损失
分析人员:
现有安全控制措施 操作规程、安全培训 加强管理、立即整改 加强管理、立即整改 操作规程、安全培训 加强管理、立即整改 加强管理、立即整改 加强管理、立即整改 操作规程、安全培训 操作规程、安全培训 立即整改 操作规程、安全培训 立即整改 加强管理、立即整改 加强管理、立即整改 操作规程、安全培训 操作规程、安全培训 立即整改 立即整改 操作规程、安全培训 立即整改 按规定检查,立即整改
日期: 严重性(S) 风险度(R) 建议改正/控制措施 3 4 1 1 1 1 1 1 2 1 3 1 1 1 3 2 3 1 3 1 1 2 1 4 1 1 1 4 2 4 1 5 5 3 4 1 12 1 1 1 12 4 12 1 15 5 3 4 4 5 5 5 5 5 12 16 5 5 5 5 5
工艺危害分析(PHA)管理规范

工艺危害分析(PHA)管理规范工艺危害分析 (PHA) 管理规范是制定和管理各类工艺危害分析活动的指导方针。
PHA 是一种系统性的评估方法,用于识别和评估工艺过程中可能产生的安全和环境风险,以及采取适当的控制措施进行风险管理。
以下是一些制定和管理 PHA 的规范和步骤:1. PHA 管理团队的组建:应该由具备相关专业知识和经验的成员组成,包括工艺工程师、安全专家、环境专家和操作人员等。
团队应该具备全面和多样化的技能,以便全面评估和分析工艺风险。
2. PHA 分析方法的选择:根据工艺的复杂性和特点,选择适合的分析方法,如哈萨德和危险分析关键控制点 (Hazard Analysis and Critical Control Point, HACCP)、故障模式与影响分析 (Failure Mode and Effects Analysis, FMEA)、事件树分析(Event Tree Analysis, ETA) 等。
选择的方法应满足所需的目标和要求。
3. 工艺信息收集和整理:收集和整理与工艺相关的各类信息,如流程图、工艺参数、物料安全数据表 (Material Safety Data Sheets, MSDS)、工艺控制系统信息等。
这些信息对于准确评估工艺风险和制定控制措施至关重要。
4. 风险识别和评估:通过分析和讨论工艺过程中的各个步骤和环节,识别所有可能导致事故和危害的因素。
对每个识别出来的风险进行定量或定性评估,包括潜在的影响、概率和风险等级。
评估应基于可靠性和可操作性,确保风险分析结果的准确性和可行性。
5. 风险控制措施的制定:根据风险评估结果,制定风险控制措施和应急预案。
风险控制措施应酌情考虑使用工程、管理和行为控制方法,并与操作规程和标准操作程序相结合。
应急预案应考虑事故应对、紧急撤离和事故恢复等方面。
6. PHA 报告和记录管理:编写详细的 PHA 报告,记录分析过程、评估结果和制定的控制措施。
危害因素的辨识与风险评价

辩识方法辩识危害因素的辨识方法采取一种或结合多种评估方法。
主要的评价方法有询问交谈、现场勘查、查阅有关记录、获取外部信息、平安检查〔SCL〕、工作危险源分析〔JHA〕、预先危害因素分析〔PHA〕、故障假说分析〔WI〕、失效模式与影响分析〔FMEA〕、危害与可操作性研究〔HAZOP〕。
危害因素辩识方法第一类危险源第一类危险源:系统中存在的、可能发生意外释放的各种能量或危险物质。
1、危险物质辨识:如氢气、原油、天然气、液化气、汽油、乙决、甲烷、煤油等可燃物质;硫化氢、一氧化碳、氯、氨、二氧化碳、氮气二氧化硫、甲醇等有毒物质;生产过程中使用的危险化学品。
2、能量辨识:辨识产生、供应能量和能量的载体。
包括以下几个方面:a.具的动能的各类机械运动部件、工件和人体及产生的机械性、动力性等振动部件。
b.具有势能的平台及坑、井、沟口处等场所上的人体和物体。
c.带电体的电能,包括雷电、静电;d.高温设备和管线的热外表、高温介质及剧烈热反响工艺装置的热能及低温介质所具有的冷量。
e.盛装具有能量的介质的压力容器。
f.机械性、动力性等噪声的声能。
g.化学反响的化学能。
h.紫外线、激光射频辐射,超高压电场等非电离辐射等。
第二类危险源第二类危险源:对第一类危险源控制设施和措施失控的状态和行为。
主要包括以下几个方面:1、控制设施和措施缺陷。
无控制设施和措施或控制设施不符合法律、法规、标准和设计标准等要求。
控制措施不好,起不到应有的作用。
2、人员失误:人的不平安行为中产生不良后果的行为。
3、管理缺陷:缺少规章制度、操作规程、工作职责不明确;组织不全;缺乏协调或协调不当、检查不及时、不到位;奖惩不清楚;培训不到位等。
4、作业环境和场所不良:引起设备故障或人员失误的温度、温度、风雨雪、照明、视野、噪声、扰动、通风换气,色彩、作业区环境不良等环境因素。
危险源识别方法简介一、工作危险源分析〔JHA〕:是一种较细致地分析工作过程中存在危险源的方法,把一项工作活动分解成几个步骤,识别每一步骤中的危险源和可能的事故,设法消除危险源。
初步危害分析(相关资料)

初步危害分析﹝PHA﹞初步危害分析 (PHA)初步危害分析是一種分析工具,依據運用先前危害或故障的經驗或知識,來找出未來危害、可能造成傷害的危害情況和事件,也可以用來估算針對所給定的活動、設施、產品或系統發生的機率。
此工具包含:1. 找出風險事件發生的可能性2. 對健康可能造成的傷害或損壞可能延伸的質性評估3. 運用嚴重度和發生相似度的組合給予危害相對的等級4. 找出可能改善的監測危害:一項行動或狀況造成傷害說明運用資源─機制─結果要素,但結果必須是最壞可能的會發生的結果﹝Source - Mechanism - Outcome﹞。
例如:S=缺氧的環境,M=窒息,O=死亡運用的潛在區域在分析現存的系統或危害的優先順序時,PHA 是有用的,環境避免一項更廣泛的技術。
可以運用在產品、流程和設施規劃,也可以針對一般產品樣式評估危害型態,然後是產品等級,以及最終是特定產品。
在設計細節或操作流程有少許的資訊時,PHA 是在專案開發的初期最常被使用;如此,常成為前兆以做更進一步研究。
一般而言,在PHA中找到危害是更進一步評估其他風險管理工具。
PHA 流程•步驟 1:取得由資深管理者的風險容忍限度指示,並使用這些指示來設計/修正風險評估矩陣界限。
•步驟2:限制系統範圍關於o 實體範圍o 操作層面﹝例如:調整、開機、標準運作、緊急停止、維護等﹞o 其他假設﹝例如:維持現況﹝as-is﹞、根據原來的設計﹝as-designed﹞、在適當的地方沒有禁止措施等﹞•步驟3:找出/查證危害o 步驟 3.1:找出受保護的標的:人員、產品、設備、環境、停工期、生產力或其他。
o 步驟 3.2:找出最壞案例結果o 步驟3.3給予危害完整的說明,找出三個要素:資源─機制─結果•評估此危害的風險1. 評估最壞案例結果的嚴重度2. 評估發生的可能性3. 使用風險評估矩陣決定風險類型4. 決定風險是否可接受?如果風險可接受,進行下一個危害或停止分析•步驟5:如果風險太高,管理風險o 停止/放棄/中止o 轉移風險到其他地方o 放棄/偏離/例外o 發展防禦措施改變設計﹝Design change,♣ D﹞:透過基礎設計改變消除危害﹝例如:改變鼻胃管的連接,讓人員不會,甚至故意,錯接到 CVP 導線﹞。
- 1、下载文档前请自行甄别文档内容的完整性,平台不提供额外的编辑、内容补充、找答案等附加服务。
- 2、"仅部分预览"的文档,不可在线预览部分如存在完整性等问题,可反馈申请退款(可完整预览的文档不适用该条件!)。
- 3、如文档侵犯您的权益,请联系客服反馈,我们会尽快为您处理(人工客服工作时间:9:00-18:30)。
15
制定评价步骤
划分作业活动 -- 编制业务活动表,内容应覆盖所 有部门、区域,包括正常、非正常和紧急状况下的一切 活动。 辨识危害 -- 辨识与业务活动有关的所有危害,考 虑谁会受到伤害及如何受到伤害,准确描述危害事件, 提出危害因素。 评价风险 – 对辨识出的危害因素,进行评估。
注:这项工作要求综合各层次人员评价得出的数据,平衡评价尺度。
工厂中危险因素主要有二十大类: 工厂中危险因素主要有二十大类: 详细可参考《安全生产事故类别》
19
危害因素识别方法
个方向( 从5个方向(上、下、前、后、侧)考虑 个方向
上:
头部以上、 头部以上、地面以上悬空不接触 地面的部分
脚下、 下: 脚下、工作平面以下区域 前: 操作过程正前方区域 后: 操作过程后方区域 合作配合作业、 侧: 合作配合作业、交叉作业等
危害因素辨识
Hazard Identify
1
目录
危害因素辨识? 为什么要 危害因素辨识? 什么叫作 危害因素辨识? 危害因素辨识? 危害因素辨识? 如何进行 危害因素辨识?
2
危害因素辨识的目的 为什么要
危害因素辨识? 危害因素辨识?
3
危害因素辨识目的
在公司的各项活动中普遍存在着危害因素; 危害因素辨识是开展各项安全活动的基础; 只有将存在于各项活动中的危险识别出来,评价 其风险,并采取控制措施,才能有效减少事故发 生。
27
练习
请八个分委会,使用 分析方法, 请八个分委会,使用PHA分析方法,根据专业 分析方法 不同,有侧重点地对作业环境进行分析。 不同,有侧重点地对作业环境进行分析。在11月22 对作业环境进行分析 月 日前完成《分委会危害因素辨识清单》。我们总结 日前完成《分委会危害因素辨识清单》 后,将就大家填写的情况进行讨论和分享。 将就大家填写的情况进行讨论和分享。
25
实例
在一些实际系统(工业或民用)设计中,经常 需要应用到石油液化气作为燃料或原料。在实际生 产活动中石油液化气引起的火灾和爆炸事故时有发 生。 以石油液化气火灾和爆炸事故为例,进行预先 危险性分析。
26
事故现象 危险因素 触发事件 事故后果 危险等级 防治措施
火灾
液化气外 溢 高温
爆炸
高温 高压 液化气外 溢
24
危害因素辨识更新
为保持危害因素清单的有效性,应该定期(一般为每年一 次)组织危害因素识别、风险评价和控制措施策划。 但当出现下列情形之一时,应立即更新危害因素辨识清单: 但当出现下列情形之一时,应立即更新危害因素辨识清单: 生产规模、生产设备的扩大、减少、更换; 机构职责的重新分配; 生产方式和生产工艺的变化; 法律、法规及其它要求的变化; 事故或险肇事件发生后。
故障泄漏、石油液化 Ⅳ 故障泄漏、 运行泄漏、气损失、 运行泄漏、气损失、 明火、火 人员伤亡、 明火、 人员伤亡、 花、高温 系统严重 物质 损坏、严 损坏、 重的经济 Ⅳ 损失
控制消除 火源、保 火源、 证质量、 证质量、 加强管理、 加强管理、 按规定操 作、保证 安全设施 齐全完好、 齐全完好、 防止泄漏
22
危险等级
序号 作业位置 危险因素 触发事件 事故后果 危险等级 防治措施 责任人
危险等级分为四级: 危险等级分为四级: 安全的(可忽视的) Ⅰ级:安全的(可忽视的)——不会造成人员伤亡和系统的损坏( 物质损失); 临界(极限) Ⅱ级:临界(极限)——处于事故的边缘状态,暂时还不会造成人 员伤亡和系统的损失或降低系统性能,应予以排除和控制。 危险的——会造成人员伤亡或系统损坏的,要立即采取措施。 Ⅲ:危险的 灾难性的(破坏) Ⅳ:灾难性的(破坏)——造成人员重大伤亡及系统严重损坏的灾 难性事故。
3000
第二个雇员在咖啡上滑倒,摔倒了,但 没受伤
A second employee slips on coffee, falls, and gets bruised, but no lost work time.
险肇事故 Near Miss
30000
雇员将咖啡倒在地板上,走开 了。
Employee spills coffee on floor and walks away.
23
防治措施
序号 作业位置 危险因素 触发事件 事故后果 危险等级 防治措施 责任人
危险控制的措施要首先考虑消除 消除—从根本上消除危险有害因素 消除 如不能消除,需考虑预防 预防—采取预防性的技术措施 预防 如不能预防,需考虑控制 控制—减少危害、危险的措施 控制 如不能控制,需考虑隔离 隔离—将人员和危险因素隔离(PPE、护罩) 隔离 此外还需考虑增加连锁 连锁--当操作者失误或设备运行一旦达到危险 连锁 状态时,应通过连锁装置终止危险、危害发生 警告--配置醒目的安全色、安全标志,声、光或声光组合报警装 警告 置
11
定义
什么是残余风险? 什么是残余风险?
残余风险 -- 对原有风险制定或实施改进措施后 尚存的风险。
12
危害因素辨识的工作程序 如何进行
危害因素辨识
13
方法介绍
预先危险性分析( 预先危险性分析(PHA)
预先危险性分析( 预先危险性分析(Preliminary Hazard Analysis) -- 在一个系统或子系统(包括设计、施工、 生产)运转活动之前,对系统存在的危险类别、 出现条件及可能造成的结果,作宏观的概略的 分析。
误工受伤
Lost Working Day
摔倒时,雇员的身体擦过金属抽屉,割伤了 手臂。缝了四针。
While falling, employee’s body grazes edge of metal drawer and lacerates arm. Four stitches.
300
急救事故 FAI
9
定义
什么是风险? 什么是风险?
风险 -- 是衡量某一种危险引发事故、造成伤害 或疾病的概率和后果的尺度,是危险事件发生的 可能性与后果的结合。 可能性× 风险 = 可能性×后果
10
定义
什么是风险评价? 什么是风险评价?
风险评价 -- 对已识别出的危害因素,运用一 种或几种评价方法,定性、定量或半定量地评 价其风险程度,并确定是否可容许的全过程。
16
制定评价步骤
确定危险控制计划 -- 编制计划以处理评价中发现 的、需要重视的任何问题 落实责任人
17
危害因素辨识清单
表格内容: 表格内容:
序号、作业位置、危险因素、触发条件、事故后 果、危险等级、防止措施、责任人等。
18
危险因素
序号 作业位置 危险因素 触发事件 事故后果 危险等级 防治措施 责任人
4
危害因素辨识目的
当摔倒时,雇员将头碰撞在桌子的边缘上,割断脖 子。死亡。Employee hits head on edge of desk while
falling. Breaks neck. Died.
死亡
Fatality
1 30
当雇员撞在地板上, 手臂骨折。休息四周。
Employee fractures arm as he hits the floor. Four weeks out of work.
安全隐患 Hazard
5
危害因素辨识目的
丢失一个钉子,坏了一只蹄铁; 丢失一个钉子,坏了一只蹄铁; 坏了一只蹄铁,折了一匹战马; 坏了一只蹄铁,折了一匹战马; 折了一匹战马,伤了一位骑士; 折了一匹战马,伤了一位骑士; 伤了一位骑士,输了一场战斗; 伤了一位骑士,输了一场战斗; 输了一场战斗,亡了一个国家。 输了一场战斗,亡了一个国家。
20
触发பைடு நூலகம்件
序号 作业位置 危险因素 触发事件 事故后果 危险等级 防治措施 责任人
是指直接导致事故发生的原因
21
事故后果
序号 作业位置 危险因素 触发事件 事故后果 危险等级 防治措施 责任人
事故后果主要有从人员伤害和财产损失的角度考虑, 事故后果主要有从人员伤害和财产损失的角度考虑,但 也可以包括人员健康、环保、 也可以包括人员健康、环保、公司声誉等
28
谢 谢! Thanks! !
29
6
危害因素辨识的定义 什么叫做
危害因素辨识? 危害因素辨识?
7
定义
什么是危害因素? 什么是危害因素? 什么是风险? 什么是风险? 什么是风险评价? 什么是风险评价? 什么是残余风险? 什么是残余风险?
8
定义
什么是危害因素? 什么是危害因素?
危害因素 -- 可能造成人员伤害、职业相关病症、 财产损失、作业环境破坏或其组合的根源或状态。
14
作用及目的
识别危险-识别危险-- 识别大体的危险,确定安全性关键部位。 评价各种危险的程度-评价各种危险的程度-- 危险分为4级,一级为安全, 四级为最危险。 确定安全性设计准则– 提出消除或控制危险的措施。 确定安全性设计准则– 总之,其目的是通过预先对系统存在的危险性分 析、评价、分级,而后根据其危险性的大小,在设计、 施工或生产中采取恰当的控制措施,避免事故的发生