塑胶常见问题点
塑胶产品的常见缺陷及分析

塑胶产品的常见缺陷及分析塑料制品是现代生活中不可或缺的一部分。
然而,塑料制品仍然存在一些常见的缺陷,这些缺陷可能导致产品质量下降,甚至无法使用。
下面是一些常见的塑料制品缺陷及其分析。
1.气泡和气孔:塑料制品中的气泡和气孔是由于在制造过程中塑料内部的空气没有完全排除或者在冷却期间塑料表面形成的。
这些气泡和气孔会导致产品表面不光滑,并在应力作用下引起断裂。
减少气泡和气孔的方法包括将塑料完全熔化,并控制良好的冷却过程。
2.毛边和厚度不均:由于模具设计和制造不当,塑料制品的边缘可能会有毛边。
毛边的存在会影响产品的外观和使用寿命。
此外,塑料制品的厚度分布不均匀可能导致产品一些部分容易破裂。
为了解决这些问题,需要优化模具设计,并确保模具制造过程的准确性。
3.烧伤和变色:在注塑过程中,如果温度控制不当,塑料可能会被过热,导致烧伤和变色。
这些问题会影响产品的外观和性能。
要解决这些问题,需要正确控制注塑机的温度和压力,并使用合适的冷却设备。
4.变形和翘曲:塑料制品可能在使用过程中变形或翘曲,这主要是由于应力超过材料的强度限制引起的。
为了避免变形和翘曲,可以通过增加产品的结构设计,加固材料强度或者改变制造过程来提高产品的稳定性。
5.色差:塑料制品可能存在色差,这是由于原料、配方和加工条件的变化引起的。
色差会影响产品的外观一致性。
要解决这个问题,需要优化原料和配方的选择,严格控制加工过程的温度和压力,以确保产品色差的控制在可接受的范围内。
综上所述,塑料制品的常见缺陷包括气泡和气孔、毛边和厚度不均、烧伤和变色、变形和翘曲以及色差。
这些缺陷可能导致产品质量下降,影响外观和性能。
为了解决这些问题,需要优化模具设计、加强原料和配方的控制,严格控制加工过程中的温度和压力。
只有通过严格的质量控制,才能生产出高质量的塑料制品。
塑胶件外观检验标准
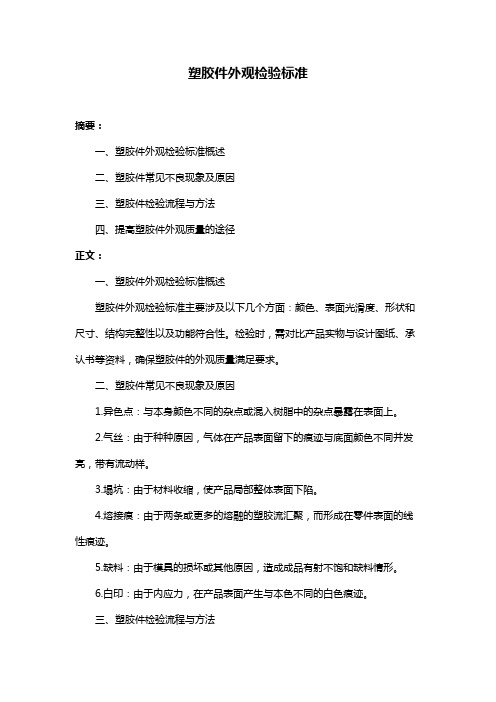
塑胶件外观检验标准摘要:一、塑胶件外观检验标准概述二、塑胶件常见不良现象及原因三、塑胶件检验流程与方法四、提高塑胶件外观质量的途径正文:一、塑胶件外观检验标准概述塑胶件外观检验标准主要涉及以下几个方面:颜色、表面光滑度、形状和尺寸、结构完整性以及功能符合性。
检验时,需对比产品实物与设计图纸、承认书等资料,确保塑胶件的外观质量满足要求。
二、塑胶件常见不良现象及原因1.异色点:与本身颜色不同的杂点或混入树脂中的杂点暴露在表面上。
2.气丝:由于种种原因,气体在产品表面留下的痕迹与底面颜色不同并发亮,带有流动样。
3.塌坑:由于材料收缩,使产品局部整体表面下陷。
4.熔接痕:由于两条或更多的熔融的塑胶流汇聚,而形成在零件表面的线性痕迹。
5.缺料:由于模具的损坏或其他原因,造成成品有射不饱和缺料情形。
6.白印:由于内应力,在产品表面产生与本色不同的白色痕迹。
三、塑胶件检验流程与方法1.检验前准备:了解产品设计要求、图纸、承认书等资料,熟悉检验标准和方法。
2.实物检验:对比实物与设计要求,检查外观质量,如颜色、表面光滑度、形状和尺寸等。
3.功能检验:根据设计要求,测试产品功能是否符合规定。
4.不良品处理:对不合格产品进行分类、记录,并采取相应处理措施。
5.检验报告:编写检验报告,记录检验结果,包括合格品数量、不良品类型及处理方法等。
四、提高塑胶件外观质量的途径1.优化原材料选择:选择优质树脂和添加剂,确保塑胶件的色泽和表面质量。
2.严格模具设计:合理设计模具结构,降低熔接痕、塌坑等不良现象的发生。
3.完善生产工艺:优化成型条件,如温度、压力、时间等,以提高塑胶件外观质量。
4.加强品质管理:严格执行检验标准,提高检验人员素质,确保产品质量。
5.及时处理不良品:对发现的不良品,要及时分析原因,采取措施予以改进,避免类似问题再次发生。
塑胶跑道施工质量通病与防治措施

一、概述塑胶跑道是一种广泛应用于体育场馆、操场和运动场地的地面材料,其施工质量直接关系到使用效果和持久性。
然而,目前在塑胶跑道施工中仍存在一些常见质量问题,例如材料选用不当、施工工艺不规范等,这些问题严重影响了塑胶跑道的使用寿命和质量。
有必要对塑胶跑道施工质量通病进行分析并提出相应的解决措施,以保障塑胶跑道施工的质量和安全。
二、塑胶跑道施工质量通病分析1. 材料选用不当在塑胶跑道施工中,材料的选用直接影响到跑道的使用寿命和性能。
一些低质量的原材料或者不符合相关标准的材料被用于施工,导致跑道质量无法得到保障。
部分厂家为了追求利润或者降低成本,选择使用劣质原料,也给塑胶跑道的质量带来了隐患。
2. 施工工艺不规范塑胶跑道的施工需要严格按照相关标准和工艺来进行,然而在实际施工过程中,部分施工人员由于对施工工艺不够了解或者工程质量意识不强,会出现一些施工工艺不规范的情况,例如材料配比不当、施工温度控制不好等,导致了施工质量的下降。
3. 质量监控不到位在塑胶跑道施工过程中,质量监控是非常重要的一环。
然而,由于一些施工单位对质量监控工作不够重视或者监控措施不到位,导致了施工中存在一些质量问题无法及时发现和解决,进而影响了跑道的施工质量。
三、塑胶跑道施工质量防治措施1. 严格控制原材料质量在塑胶跑道施工前,需要选用有相关资质和质量保障的原材料,并进行严格的质量检测。
对于每一批次的原材料,在使用前都应进行抽样检测,确保其符合相关质量标准,相应的检测报告和合格证明也应妥善保存。
2. 强化施工工艺管理施工单位应对施工工艺进行详细规范,并准备好相应的施工工艺流程和标准操作规程。
在施工现场,应配备有相关技术人员进行实时监督,并对施工人员进行培训,确保他们深刻理解相关施工工艺和标准,并按照要求进行施工。
3. 加强质量监控在施工过程中,质量监控应该贯穿始终。
施工单位应设置专门的质量监控岗位,对施工过程中关键节点进行严格监控。
塑胶件常见的缺陷产生原因及解决办法

塑胶件常见的缺陷产生原因及解决办法一、设计方面的缺陷:1.不合理的尺寸设计:塑胶件的尺寸设计不合理可能导致尺寸偏差过大、尺寸不一致等问题。
解决方法是根据塑胶件的具体用途和要求进行合理的尺寸设计,并进行合适的工艺分析和模流分析。
2.没有考虑到材料的特性:不同塑料材料具有不同的热胀冷缩系数、熔融温度等特性,设计时没有考虑到这些特性可能导致尺寸偏差、变形等问题。
解决方法是根据塑料材料的特性进行合适的设计和模具制造选型。
3.模具设计问题:模具设计不合理或者制造质量不过关可能导致塑胶件的缺陷问题。
解决方法是进行合理的模具设计,并选择专业的模具制造厂家。
4.不合理的壁厚设计:塑胶件的壁厚设计不合理可能导致塑胶件变形、收缩不均匀等问题。
解决方法是根据塑胶件的材料特性和实际使用要求进行合理的壁厚设计。
二、材料方面的缺陷:1.材料质量问题:不合格的原料质量可能导致塑胶件出现异味、颜色不均匀等问题。
解决方法是选择合格的塑料原料供应商,并进行原料的严格检验。
2.材料混合不均匀:塑料材料在加工过程中没有充分混合均匀可能导致塑胶件的颜色不均匀等问题。
解决方法是进行充分的原料预处理和混炼,确保塑料材料的均匀性。
3.熔体温度不均匀:塑料材料在注塑过程中温度不均匀可能导致塑胶件尺寸偏差、表面气泡等问题。
解决方法是调整注塑机的温度控制系统,确保熔体温度均匀稳定。
三、工艺方面的缺陷:1.注塑工艺参数设置不当:注塑过程中,如射胶压力、射胶速度、冷却时间等工艺参数设置不当可能导致塑胶件出现尺寸偏差、气泡、表面缺陷等问题。
解决方法是根据塑料的特性和产品要求进行合理的工艺参数设置。
2.模具温控不均匀:模具温度不均匀可能导致塑胶件出现收缩不一致、尺寸偏差等问题。
解决方法是进行模具温度分析和温控系统的优化。
可以采用热流道模具、快速温度控制系统等技术手段解决问题。
3.模具保养不当:模具的使用寿命长,如果没有进行定期的保养和维修可能导致塑胶件出现模纹、模具磨损等问题。
塑胶常见不良及解决方法

塑胶常见不良及解决方法塑胶是一种常见的材料,广泛应用于各种行业和领域。
然而,由于塑胶的特性以及制造过程中的一些问题,常常会出现一些不良现象。
本文将重点介绍一些常见的塑胶不良及其解决方法。
1.氣泡:塑膠制品中常見的一種不良現象是氣泡,這會在成品表面或内部形成小气囊。
气泡的形成是由于塑胶熔融时含有的空气或挥发物没有充分释放出来。
解决方法包括降低加工温度、增加熔体压力、增加注射速度和使用抗气泡添加剂等。
2.热胀冷缩:塑胶制品在温度变化下会发生热胀冷缩,导致尺寸变化。
这可能会导致配件无法正常连接或安装。
为了解决这个问题,可以采用材料改性或加工工艺改进,如增加冷却时间、降低注射温度等。
3.白化:白化是指塑胶制品表面或内部出现白色斑点或条纹。
这种现象通常是由于塑胶在注射过程中发生气泡聚集或制品未达到均匀熔融所致。
解决方法包括优化注射工艺、增加熔体压力、使用抗白化添加剂等。
4.热裂纹:热裂纹是指在塑胶产品成型过程中出现的裂纹现象。
这通常是由于塑胶在成型过程中存在过大的应力集中,导致塑胶产生裂纹。
解决方法包括改变模具设计、增加冷却时间、预混塑胶料等。
5.变色:变色是指塑胶制品在使用或储存过程中出现颜色变化。
这可能是由于塑胶材料受到光、热、氧化等外界因素的影响所致。
解决方法包括选择适当的防褪色添加剂、合理储存塑胶制品等。
6.毛刺:毛刺是指塑胶制品表面出现不平整、刺状的小颗粒。
这通常是由于模具表面不平整或注射工艺不当所导致的。
解决方法包括优化模具设计、控制注射压力、调整注射速度等。
7.缩水:缩水是指塑胶制品在冷却过程中发生体积收缩。
这可能导致尺寸偏离设计要求。
解决方法包括优化塑胶成型工艺、增加冷却时间和选择合适的材料等。
8.潜伏期延长:有些塑胶在使用一段时间后会发生不良现象,如变形、断裂等。
这可能是由于塑胶受到环境因素、应力或热老化的影响导致的。
解决方法包括选择合适的材料、控制加工温度、降低应力等。
总结起来,塑胶制品的不良现象可能是由于材料、工艺或环境等多种因素造成的。
塑胶产品外观常见不良分析

塑胶产品外观常见不良分析塑胶产品在日常生活中被广泛使用,它们可以用于制作各种产品,如家庭用品、工业部件、玩具等。
由于制作工艺以及原材料的原因,塑胶产品的外观常常会出现一些不良,这不仅会影响产品的美观度,还有可能影响产品的性能和使用寿命。
对于塑胶产品的外观不良分析非常重要。
下面我们将对常见的塑胶产品外观不良进行分析。
一、表面缺陷1. 水波纹水波纹是指塑胶产品表面出现的波纹状不平整,通常是由于注塑时模具温度不均匀或注射压力不稳定造成的。
如果注射速度过快或者模具表面磨损,也会导致水波纹的出现。
水波纹不仅影响塑胶产品外观美观度,还可能降低其强度和耐磨性。
2. 毛刺毛刺是指塑胶产品表面出现的细小而锋利的突起,在注塑工艺中,毛刺通常是由于模具设计不当或者模具磨损严重造成的。
毛刺会影响产品的手感和安全性,同时也会影响产品的使用寿命。
3. 烧结烧结是指塑胶产品表面出现的凹凸不平的现象,通常是由于模具温度设置不当或者注塑过程中料温不均匀导致的。
烧结会影响产品的美观度和尺寸精度,严重时还会导致产品的性能下降。
二、色差1. 色泽不均匀在注塑过程中,如果原料的分散性不好或者混料不均匀,就会导致塑胶产品的表面色泽不均匀。
这不仅会影响产品的外观质量,还会影响产品的一致性和品质稳定性。
三、气泡气泡是指塑胶产品表面或内部出现的空洞状现象,通常是由于注塑过程中原料受潮或者含有挥发性成分,或者注射压力不足造成的。
气泡会影响产品的外观质量和性能稳定性,甚至会导致产品的强度和密封性下降。
四、变形针对上述常见的塑胶产品外观不良,我们可以采取一些措施来进行预防和解决。
对于表面缺陷,我们可以通过优化模具设计,提高模具制造精度和加工质量,以及优化注塑工艺参数来减少水波纹、毛刺和烧结的出现。
对于色差问题,我们可以选择优质的原料并保证混料均匀,严格控制注塑工艺参数,尽量避免色泽不均匀和色斑的出现。
对于气泡和变形问题,我们可以在原料筛选和混合过程中严格控制原料含水量和挥发性成分,保证原料质量。
塑胶制品常见问题成因及解决办法
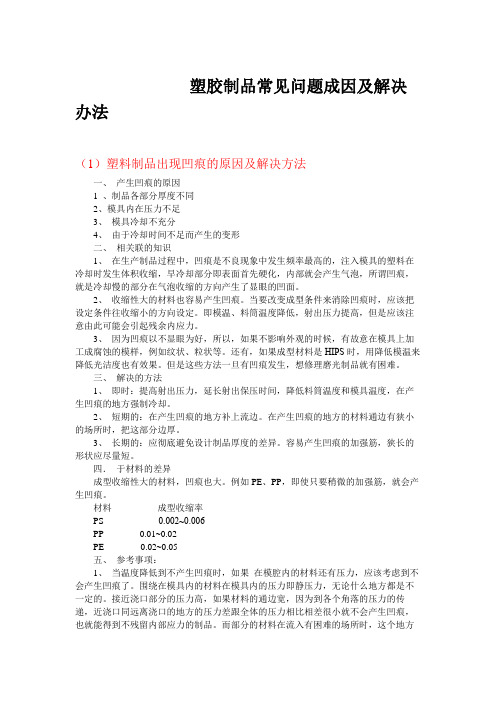
塑胶制品常见问题成因及解决办法(1)塑料制品出现凹痕的原因及解决方法一、产生凹痕的原因1 、制品各部分厚度不同2、模具内在压力不足3、模具冷却不充分4、由于冷却时间不足而产生的变形二、相关联的知识1、在生产制品过程中,凹痕是不良现象中发生频率最高的,注入模具的塑料在冷却时发生体积收缩,早冷却部分即表面首先硬化,内部就会产生气泡,所谓凹痕,就是冷却慢的部分在气泡收缩的方向产生了显眼的凹面。
2、收缩性大的材料也容易产生凹痕。
当要改变成型条件来消除凹痕时,应该把设定条件往收缩小的方向设定。
即模温、料筒温度降低,射出压力提高,但是应该注意由此可能会引起残余内应力。
3、因为凹痕以不显眼为好,所以,如果不影响外观的时候,有故意在模具上加工成腐蚀的模样,例如纹状、粒状等。
还有,如果成型材料是HIPS时,用降低模温来降低光洁度也有效果。
但是这些方法一旦有凹痕发生,想修理磨光制品就有困难。
三、解决的方法1、即时:提高射出压力,延长射出保压时间,降低料筒温度和模具温度,在产生凹痕的地方强制冷却。
2、短期的:在产生凹痕的地方补上流边。
在产生凹痕的地方的材料通边有狭小的场所时,把这部分边厚。
3、长期的:应彻底避免设计制品厚度的差异。
容易产生凹痕的加强筋,狭长的形状应尽量短。
四.于材料的差异成型收缩性大的材料,凹痕也大。
例如PE、PP,即使只要稍微的加强筋,就会产生凹痕。
材料成型收缩率PS 0.002~0.006PP 0.01~0.02PE 0.02~0.05五、参考事项:1、当温度降低到不产生凹痕时,如果在模腔内的材料还有压力,应该考虑到不会产生凹痕了。
围绕在模具内的材料在模具内的压力即静压力,无论什么地方都是不一定的。
接近浇口部分的压力高,如果材料的通边宽,因为到各个角落的压力的传递,近浇口同远离浇口的地方的压力差跟全体的压力相比相差很小就不会产生凹痕,也就能得到不残留内部应力的制品。
而部分的材料在流入有困难的场所时,这个地方有高的压力,其他地方的压力降低就会产生凹痕。
塑胶产品缺胶原因与对策

塑胶产品缺胶原因与对策
塑胶产品缺胶是塑胶成型过程中常见的缺陷之一,通常是指塑胶未能完全填满模具型腔,导致产品局部缺失或不完整。
以下是一些可能导致塑胶产品缺胶的原因及相应的对策:
1. 注塑机压力不足:增加注塑机的注射压力,以确保塑胶能够充分填满型腔。
2. 注塑速度过慢:提高注塑速度,使塑胶能够快速填满型腔,但也要注意避免产生过多的气泡。
3. 模具温度过低:提高模具温度,有助于塑胶的流动性,减少缺胶的发生。
4. 塑胶原料流动性差:选用流动性更好的塑胶原料,或添加适量的润滑剂来改善原料的流动性。
5. 模具排气不良:检查模具的排气系统,确保排气通畅,避免型腔内产生气泡导致缺胶。
6. 模具设计不合理:优化模具设计,如增加浇口数量、改变浇口位置等,以保证塑胶能够均匀地填满型腔。
7. 注塑量不足:调整注塑机的注射量,确保每次注射的塑胶量足够。
8. 原材料质量问题:检查塑胶原材料的质量,如有必要更换原材料供应商。
针对塑胶产品缺胶问题,需要根据具体情况进行分析,并采取相应的对策。
在生产过程中,及时发现并解决问题,可以有效提高产品质量和生产效率。
- 1、下载文档前请自行甄别文档内容的完整性,平台不提供额外的编辑、内容补充、找答案等附加服务。
- 2、"仅部分预览"的文档,不可在线预览部分如存在完整性等问题,可反馈申请退款(可完整预览的文档不适用该条件!)。
- 3、如文档侵犯您的权益,请联系客服反馈,我们会尽快为您处理(人工客服工作时间:9:00-18:30)。
塑膠成型
收縮下陷(SINK MARKS)
(7)有厚肉部與寬的補強肋的場合 普通補強肋厚度需控制在壁厚的0.5~0.8倍以內, 距離進澆口遠的位置或容易造成收縮下陷問題的位 置,盡量減小補強肋的肉厚.另外,為縮小與周圍的熱 收縮差,由周邊部補強肋.有根部漸漸增加肉厚.
由周邊向補強肋 的根部漸增肉厚
緩和肉厚變化可減少收縮差
成型時的材料或填充料所致的配向性,也是成型品變形的主要原 因,配向性所致的變形與模具構造有關係,如澆口的設置,形狀,大 小,數目等,影響成型品的變形有重大關係. 防止成型品的變形,只調整成型條件是很難達成的,但是為了 減少內應力所致的變形,可減低射出壓力,縮短保壓時間,減低射出 速度. 成型品的變形主要取決於成型品設計的良好與否,使用之成型 材料的適當與否,因此,成型品設計時需加以注意. 一般為防止成型品變形,可在剛成型后,以冷工模等對成型品施 加外力,矯正變形或防止進一步的變形,但成型品在使用中若再次 碰到高溫時又會復原,對此點需特別加以注意.
塑膠成型
毛
邊
(BUR分接觸噴嘴,模具發生間隙時. 改善對策:調整射座頂力. (3) 模具導柱摩損,分模面偏移或模具安裝板受損,導桿(大柱)強度 不足發生彎曲時. 改善對策: a更換模具銷. b模具安裝板整修. c模具重量超重應更換較大機臺成型. (4) 異物附著模面時. 改善對策:清除模面異物. (5) 成型品投影面過大或樹脂(塑料)溫度太高. 改善對策:(a)更換較大機臺. (b)降低塑料溫度.
熔融塑料流入分模 面或側向蕊型的對合 面間隙會發生BURR;模 具鎖模力足夠,但在澆 道與橫流道會合處產 生薄膜狀多餘樹脂為 FLUSH.(齐平面)
毛邊
塑膠成型
毛
邊
(BURR&FLUSH)
原因與對策:
(1) 模具的鎖模力不足,塑料高壓射入模具內 時會在分模面發生間隙,塑料由此縫流出 改善對策:調整鎖模力,提高鎖模噸數.如已調 至該機臺最大鎖模力還無法改善, 可更換較大型機臺成型
成形不良的產生 不良原因很多,例如: 成形材料不適當 射出成形機超負載 射出成形條件不適當 模具設計有問題 產品設計有問題 要求事項超出射出機的性能
成形不良的分類 A表面缺陷: 充填不足 凹陷 變黃 霧面 流痕 熔合線 光澤不均 顏色不均
B龜裂: C變形與尺寸不良: 龜裂 翹曲、扭轉 白化 碎裂 強度不足 D其它不良 剝離 成品附於模具 氣泡 毛邊
塑膠成型
變形(STRAIN)—翹曲、扭曲
(2)全體的收縮小,或收縮差小的場合
利用低模溫、低樹脂溫減小樹脂的熱 收縮,或利用高射出壓,長射出保持時間提 高壓縮性,充分補足熱收縮量.
塑膠成型
變形(STRAIN)—翹曲、扭曲
(3)由於分子配向造成的場合 A.利用高溫,高樹脂溫,低樹脂壓,短射出保持時 間,降低樹脂的斷應力,降低分子配向的情況. B.利用多點進澆口,減少收縮率的異方向.
塑膠成型
氣泡(BUBBLES & VOIDS)
改善對策:
a.擴大澆品或流道尺寸,使壓力有效作用於成型品 的肉厚部. b.提高保持壓力及延長冷卻時間. c.成型塑粒盡量除去含水份. d.料管溫度設定不宜偏高,可有效防止塑料分解氣 體之產生.
塑膠成型
氣泡(BUBBLES & VOIDS)
收縮下陷造成的情形
塑膠成型
氣泡(BUBBLES & VOIDS)
(2)溶融樹脂中有水分、揮發物、空氣造成的
a.材料進行預先乾燥. b.使儲料桶部的冷卻充分,降低儲料桶側溫 度,並提高背壓,使氣體能由儲料桶側排出. c.樹脂溫度過高,則氣體的發生量多,此時 則必需下降加熱缸筒的溫度.
塑膠成型
破裂(CRACKING)與龜裂(CRAXING)
塑膠成型
收縮下陷(SINK MARKS)
(4)射出量少的場合 射出量少則樹脂的壓縮少,因此需加射出量 (5)樹脂溫度高,模溫高的場合 如此,冷卻速度慢,收縮完全而產生收縮下陷,因此最 好降低樹脂溫度及模溫. (6)橫澆道、進澆道口狹小場合 橫澆道、進澆口狹小的話,壓力損失增大,樹脂壓降 低,則壓縮不完全.大部加大時澆口而橫澆道維持原 狀,但長的橫澆道壓力損失是進澆口的數倍,因此不 僅考慮進澆口對橫澆道也不可遺忘.太大的橫澆道 將會浪費材料,因此不可隨便加大.
塑膠成型
熔 合 線
定義:
熔合線(weld line)是熔融材料二 道或二道以上合 流的部分所形成 的細線.
結合線
塑膠成型
熔 合 線
熔合線發生的原因如下所示:
(1) 成型品形狀(模具構造)所致材料 的流動的方式.
(2) 熔合材料的流動性不良.
(3) 熔融材料合流處捲入空氣,揮發 物或脫模劑等異物.
定義:成型品表面裂痕嚴重而明顯者為破裂
(CRACKING).成型品表面呈毛髮狀裂紋,制品尖 銳突角處常呈現此現象謂之龜裂現象. 裂紋為成型品的致命缺陷,主要的原因如下: (1) 脫模不良所致. (3)模子溫度過低. (2) 過度充填所致. (4)制品構造上的缺陷所致.
塑膠成型
破裂(CRACKING)與龜裂(CRAXING)
嵌件---利用肉厚消減 達到均一壁厚
塑膠成型
收縮下陷(SINK MARKS) (8)模具冷卻不適當的場合 模具冷卻不適當將使熱收縮 不均一,因此厚肉部與補強肋的根部 肉厚的地方需要有足夠的冷卻.
塑膠成型
氣泡(BUBBLES & VOIDS)
定義:
熔融塑料中有水份、揮發性氣體 於成型過程進入成型品內部而殘留 的空洞現象謂氣泡(BUBBLES)成型品 肉厚處溶池冷卻過程中,由於體積收 縮所產生的間隙謂之真空泡.氣泡 與真空泡之區別要領:成型品自模具 中取出,成型品即呈現氣泡者謂氣泡. 成型品自模具中取出,待一般時間再 呈現氯泡者謂之真空泡.
C.因薄肉部的流動性不佳,因此容易因配向面造 成異方向性,薄肉處有進膠口或進膠口周圍的薄 肉處易出現波狀的變形.則必需變更進膠口位置, 或採用扇形進膠口使流動均一,進膠口立即固化, 可以減少殘留應力,減少變形.
塑膠成型
變形(STRAIN)—翹曲、扭曲
(4)側壁的內彎曲 A.公模側充分冷卻降低溫度,母模側通溫水提高溫度 側樹脂外側的收縮較內側的大.因此,外側受到以進 澆口為中心的拉力作用,可以阻止側壁往內側傾斜.
塑膠成型
收縮下陷(SINK MARKS)
定義:
成型品表面產生 凹陷的現象.這是體積 收縮所致,通常見於肉 厚部分.肋或击出的背 面.直接澆口肉厚不均 的部份.
縮水
塑膠成型
收縮下陷(SINK MARKS)
凹陷與真空泡同時發生之狀況: 成型品的中心部位肉較厚冷卻較慢,外 部冷 卻較快,此時內部(肉厚處)熔融塑料被 外側拉伸,中心部發後空隙實際為真空泡不 易冷卻的肉厚部發後於表面者為凹陷.
塑膠成型
變形(STRAIN)—翹曲、扭曲
變形的對策是依制品形狀面定,對於變形的因素有 很大的不同:
(1) 肉厚不均一,冷卻不均一的場合 因樹脂的冷卻速度不一樣,冷卻速度快的地方 收縮變小,冷卻速度慢的地方收縮大,面發生變形. 則厚肉的地方必需有效地冷卻,或距進膠口遠的地 方樹脂溫度較低,因此距離澆口近的地方冷卻,而距 進澆口遠的地方提高模溫,刻意地設置溫度差.
塑膠成型
收縮下陷(SINK MARKS)
原因對策:
(1) 射出壓低的場合 射出壓低則樹脂的壓縮不完全而產生收縮下陷,最 好提高射出壓. (2)射出壓保持時間短的場合 射出壓保持時間短,則無法彌補樹脂的熱收縮量, 另外也容易造成回流(back flow),而發生壓縮不 完全,因此延長射出保持時間. (3)射出速度過慢、過快的場合 太慢的話,固化即刻開始,壓力傳達不足,因此需 加快射出速度.另外太快的話,僅能填充少量,所 以要減緩射出速度,增加計量.
塑膠成型
充填不足/不飽模
(6) 模具溫度太冷,塑料在某一特定壓力下流動 困難.
改善對策:斟酌生產上實際需要,提 高模具溫度.
(7) 模具排氣不良時,空氣無法排除.
改善對策:防火級ABS成型時,揮發性氣體 殘渣,易造成模垢而發生排氣口 阻塞現象,應定期清除之.
塑膠成型
毛
定義:
邊
(BURR&FLUSH)
(2). 噴嘴射出口徑太小,冷料阻塞. 改善對策:加大噴嘴射出口尺寸,以3.50Z(80 ~90 tons)射出噴嘴口徑應為2.0-2.2m/mψ.
塑膠成型
充填不足/不飽模
(3) 流道設計不良時,塑料流動阻力大. 改善對策:修改流道尺寸以符合實際需要.
(4) 塑料熔化不均勻,造成射出壓力降過大所致 改善對策:適當的調整背壓與螺桿轉速,使 塑料混鍊均勻. (5) 流道中冷料井預留不足或不當,冷料頭進入 成型品而阻礙塑料之正常流動充滿模穴. 改善對策:增加冷料井儲存空間或打多段射 出移開冷 料頭使塑料充填順暢.
塑膠成型
變形(STRAIN)—翹曲、扭曲
定義:
變形可分成翹曲與 扭曲兩種現象.平 行邊變形者稱為翹 曲(WRAPING);對角 線方向的變形稱為 扭曲(TORSION).
變形
塑膠成型
變形(STRAIN)—翹曲、扭曲
這些變形為成形時的各種內部應力所致,原因 大致如下: (1) 脫模時的內部應力所致. (2) 模具溫度控制不充分或不均勻所致. (3) 材料或填充料的流動配向所致. (4) 成形條件不適當所致. (5) 成形品形狀,肉厚等所致.