ANSI EIA ECA-364-18B-2007VISUAL AND DMENSIONAL INSPECTION....AND SOCKETS
EIA-364-23C-2006

EIASTANDARDTP-23CLOW LEVEL CONTACT RESISTANCE TEST PROCEDURE FOR ELECTRICAL CONNECTORS AND SOCKETSEIA/ECA-364-23C(Revision of EIA-364-23B)JUNE 2006ELECTRONIC COMPONENTS, ASSEMBLIES & MATERIALS ASSOCIATIONTHE ELECTRONIC COMPONENTS SECTOR OF THE ELECTRONIC INDUSTRIES ALLIANCENOTICEEIA Engineering Standards and Publications are designed to serve the public interest through eliminating misunderstandings between manufacturers and purchasers, facilitating interchangeability and improvement of products, and assisting the purchaser in selecting and obtaining with minimum delay the proper product for his particular need. Existence of such Standards and Publications shall not in any respect preclude any member or nonmember of EIA from manufacturing or selling products not conforming to such Standards and Publications, nor shall the existence of such Standards and Publications preclude their voluntary use by those other than EIA members, whether the standard is to be used either domestically or internationally.Standards and Publications are adopted by EIA in accordance with the American National Standards Institute (ANSI) patent policy. By such action, EIA does not assume any liability to any patent owner, nor does it assume any obligation whatever to parties adopting the Standard or Publication.This EIA Standard is considered to have International Standardization implication, but the International Electrotechnical Commission activity has not progressed to the point where a valid comparison between the EIA Standard and the IEC document can be made.This Standard does not purport to address all safety problems associated with its use or all applicable regulatory requirements. It is the responsibility of the user of this Standard to establish appropriate safety and health practices and to determine the applicability of regulatory limitations before its use.(From Standards Proposal No. 5105 formulated under the cognizance of the CE-2.0 National Connectors Standards Committee.Published by©ELECTRONIC INDUSTRIES ALLIANCE 2006Technology Strategy & Standards Department2500 Wilson BoulevardArlington, VA 22201PRICE: Please refer to the currentCatalog of EIA Electronic Industries Alliance Standards and Engineering Publications or call Global Engineering Documents, USA and Canada (1-800-854-7179)International (303-397-7956)All rights reservedPrinted in U.S.A.中国可靠性网 PLEASE !DON'T VIOLATETHELAW!This document is copyrighted by the EIA and may not be reproduced without permission.Organizations may obtain permission to reproduce a limited number of copies through entering into a license agreement. For information, contact:Global Engineering Documents15 Inverness Way EastEnglewood, CO 80112-5704 or callUSA and Canada (1-800-854-7179), International (303-397-7956)iiiCONTENTSClause Page1 Introduction (1)1.1 Scope ......................................................................................................................... 1 1.2 Object (1)2 Test resources (1)2.1 Equipment ................................................................................................................. 1 2.2 Fixture ....................................................................................................................... 2 3 Test specimen (2)4 Test procedure ........................................................................................................... 2 4.1 Option 1, integrated micro-ohmmeter ....................................................................... 3 4.2 Option 2, current reversal (direct current) ................................................................ 3 4.3 Option 3, offset compensation .................................................................................. 3 4.4 Option 4, alternating current ..................................................................................... 3 5 Details to be specified .. (4)6 Test documentation (4)中国可靠性网 (This page left blank)iii中国可靠性网 EIA-364-23CPage 1TEST PROCEDURE No. 23CLOW LEVEL CONTACT RESISTANCE TEST PROCEDUREFORELECTRICAL CONNECTORS AND SOCKETS(From EIA Standards Proposal No. 5105, formulated under the cognizance EIA CE-2.0 Committee on National Connector Standards, and previously published in EIA-364-23B.)1 Introduction1.1. ScopeThis test procedure may apply to any type or combination of current carrying members such as pin and socket contacts, relay contacts, wire and crimp connectors, or printed circuit board and contact.1.2. ObjectThe object of this test procedure is to detail a standard method to measure the electrical resistance of two current carrying members in mutual contact. This test procedure specifies test voltages that will not disturb insulating films on the contacting surface nor cause asperity melting. This procedure addresses the effect of thermal EMF’s, a source of measurement error.2 Test resources2.1. EquipmentLow level contact resistance measurements may be made using a discrete power source, ammeter and micro-voltmeter or an integrated micro-ohmmeter.2.1.1. Integrated micro-ohmmeterFour wire resistance meter that regulates test current, limits open circuit (source) voltage to 20 millivolts maximum, corrects for thermal EMF’s, measures voltage drop, such as a Keithley Micro-Ohmmeter model 580, HP 4338B or equivalent, may be used. These meters generally display the measured resistance directly in ohms.EIA-364-23CPage 22.1.2. Discrete Equipment2.1.2.1. Power sourcePower supply or circuit capable of regulating either alternating or direct current within 5% of desired value, and limiting the open circuit (source) voltage to 20 millivolts maximum.2.1.2.2. Ammeter or current shuntCapable of measuring either alternating or direct current within an accuracy of 2%.2.1.2.3. Micro-voltmeterCapable of measuring either alternating or direct current voltage within an accuracy of 2%2.1.2.4. Low Level CircuitLow level circuit delivering 100 milliamperes at 20 millivolts open circuit potential.2.2. FixtureThe test specimen shall be mated or fixtured as in normal service, or as specified in the referencing document. Fixturing of specimens shall not disturb the natural normal force of the mating contacts.3 Test specimen3.1 The test specimen shall be wired as specified in the referencing document. Connections may be made by use of clips, by soldering to a printed circuit board and/or wires. Subsequent measurements should be made at the same point to reduce variability due to path length changes. Soldering the sample to a printed circuit board or to wires fixes the measurement point.3.2 Voltage probes for crimp contacts shall be placed on the conductors a distance of 152.4 millimeters ± 3.0 millimeters (6.00 inch ± 0.12 inch) from each other, with the mated contacts in the center of that distance unless otherwise specified in the referencing document.4 Test procedureMeasure and record the contact resistance of the specimen under test with a test current of 100 milliamperes maximum and 20 millivolts open circuit (source) voltage maximum. One of the following options shall be used to correct for thermal EMF’s.中国可靠性网 EIA-364-23CPage 34.1. Option 1, integrated micro-ohmmeterUse an 4 wire micro-ohmmeter. The micro-ohmmeter shall employ a method to correct for thermal EMF. Such methods include; alternating current, pulsed direct current or current reversal. Integrated meters generally measure the actual test current and the voltage drop across the specimen. The measured resistance is then internally calculated and displayed.4.2. Option 2, current reversal (direct current)Apply direct current through the specimen. Measure the current and record it as I f . Measure the voltage drop across the specimen and record it as V f . Reverse the direction of current through the specimen. Do not reverse the voltage leads. Measure the current and record it as I r . Measure the voltage drop across the specimen and record it as V r .Calculate the contact resistance with the following equation:rf rf I I V V R +−= (1)NOTE ⎯ The sign of the voltage readings shall be carried into the equation to obtain aproper result.4.3. Option 3, offset compensationApply direct current through the specimen. Measure the current and record it as I . Measure the voltage drop across the specimen and record it as V 1.Remove the current from the specimen. Measure the voltage drop across the specimen as V 2. Calculate the contact resistance with the following equation:IV V R 21−= (2)4.4. Option 4, alternating currentApply alternating current through the specimen. Measure the current and record it as I . Measure the voltage drop across the specimen using a true RMS voltmeter and record it as V .Calculate the contact resistance with the following equation:IV R =(3)EIA-364-23CPage 45 Details to be specifiedThe following details shall be specified in the referencing document:5.1 Test specimen preparation or conditioning5.2 Test specimen mating conditions or fixturing5.3 Placement of test leads on specimen (see 3.2)5.4 Test current and voltage other than 100 milliamperes maximum and 20 millivolts open circuit (source) voltage maximum5.5 Number of specimens to be tested6 Test documentationDocumentation shall contain the details specified in clause 5, with any exceptions, and the following:6.1 Title of test6.2 Specimen description6.3 Test specimen preparation or conditioning6.4 Test specimen mating conditions or fixturing6.5 Test equipment used, and date of last and next calibration6.6 Test current and voltage other than 100 milliamperes maximum and 20 millivolts open circuit (source) voltage maximum6.7 Values and observations6.8 Name of operator and date of test中国可靠性网 EIA-364-23CPage 5EIA Document Improvement ProposalIf in the review or use of this document, a potential change is made evident for safety, health or technical reasons, please fill in the appropriate information below and mail or FAX to:Electronic Industries AllianceTechnology Strategy & Standards Department – Publications Office2500 Wilson Blvd.Arlington, VA 22201FAX: (703-875-8906)。
EIA-364(连接器产品常用测试规范之目录)

EIA-364(连接器产品常用测试规范之目录)Item Standard NO.Rev.Description1EIA-CB18Solid Tantalum Capacitor Shelf-Life固体的钽式电容器储存期限2EIA-364E ELECTRICAL CONNECTOR/SOCKET TEST PROCEDURES INCLUDING ENVIRONMENTAL CLASSIFICATIONS 电子连接器/插座(包括环境类)的测试程序3EIA-364-01B Acceleration Test Procedure for Electrical Connectors电子连接器的加速测试程序4EIA-364-02C Air Leakage Test Procedure for Electrical Connectors空气渗漏电子连接器的测试程序5EIA-364-03B Altitude Immersion Test Procedure for Electrical Connectors高度浸入电子连接器的测试程序6EIA-364-05B Contact Insertion, Release and Removal Force Test Procedure for Electrical Connectors电子连接器的端子插入、释放及取出测试程序7EIA-364-06C Contact Resistance Test Procedure for Electrical Connectors电子连接器的接触电阻测试程序8EIA-364-07B Contact Axial Concentricity Test Procedure for Electrical Connectors电子连接器的端子同心度测试程序9EIA-364-08B Crimp Tensile Strength Test Procedure for Electrical Connectors电子连接器的卷曲抗拉强度测试程序10EIA-364-09C Durability Test Procedure for ElectricalConnectors and Contacts端子连接器与端子的耐久性测试程序11EIA-364-10D Fluid Immersion Test Procedure for Electrical Connectors电子连接器的液体浸没测试程序12EIA-364-11B Resistance to Solvents Test Procedure for Electrical Connectors and Sockets电子连接器和插座的电阻测试程序13EIA-364-13D Mating and Unmating Forces T est Procedure for Electrical Connectors电子连接器的插入力和拔出力测试程序14EIA-364-14B Ozone Exposure Test Procedure for Electrical Connectors电子连接器的臭氧暴露测试程序15EIA-364-17B Temperature Life with or without Electrical Load Test Procedure for Electrical Connectors andSockets. 电子连接器和插座的温度寿命测试或没有电负载测试程序16EIA-364-18B Visual and Dimensional Inspection Test Procedure for Electrical Connectors and Sockets电子连接器和插座的外观与尺寸检验程序17EIA-364-20C Withstanding Voltage Test Procedure for Electrical Connectors, Sockets and Coaxial Contacts电子连接品、插座和同轴端子的耐电压测试程序18EIA-364-21C Insulation Resistance Test Procedure for Electrical Connectors, Sockets, and Coaxial Contacts电子连接品、插座和同轴端子的绝缘电阻测试程序19EIA-364-22B Simulated Life Test Procedure for Electrical Connectors电子连接器的模拟寿命测试程序20EIA-364-23C Low Level Contact Resistance T est Procedure for Electrical Connectors and Sockets电子连接器与插座的接触电阻测试程序21EIA-364-24B Maintenance Aging Test Procedure for Electrical Connectors电子连接器的维持能力测试程序22EIA-364-25C Probe Damage Test Procedure for Electrical Connectors电子连接器的探伤测试程序23EIA-364-26B Salt Spray Test Procedure for Electrical Connectors, Contacts and Sockets电子连接器、端子和插座的盐雾测试程序24EIA-364-27B Mechanical Shock (Specified Pulse) Test Procedure for Electrical Connectors电子连接器的机械震动(指定的脉搏)测试程序25EIA-364-28E Vibration Test Procedure for Electrical Connectors and Sockets电子连接器与插座的振动测试程序26EIA-364-29C Contact Retention Test Procedure for Electrical Connectors电子连接器的端子保持力测试程序27EIA-364-30A Capacitance Test Procedure for Electrical Connectors and Sockets电子连接器与插座的电容测试程序28EIA-364-31B Humidity Test Procedure for Electrical Connectors and Sockets电子连接器与插座的湿度测试程序29EIA-364-32D Thermal Shock (Temperature Cycling) Test Procedure for Electrical Connectors and Sockets电子连接器与插座的热冲击(温度周期变化)测试程序30EIA-364-35B Insert Retention Test Procedure for Electrical Connectors电子连接器的保持力测试程序31EIA-364-36B Determination of Gas-tight Characteristics test procedure for Electrical connectors and or contact systems. 电子连接器和(或)端子系统的气密特性测试程序32EIA-364-37B Contact Engagement and Separation Force Test Procedure for Electrical Connectors电子连接器端子结合力和分离力测试程序33EIA-364-38B Cable Pull-Out Test Procedure for Electrical Connectors电子连接器的电材拉拔力测试程序34EIA-364-39B Hydrostatic Test Procedure for Electrical Connectors, Contacts and Sockets电子连接器、接触和插座的液压静力测试程序35EIA-364-40B Crush Test Procedure for Electrical Connectors电子连接器v压坏测试程序36EIA-364-41C Cable Flexing Test Procedure for Electrical Connectors电报在电子连接的测试程序屈曲37EIA-364-42B Impact Test Procedure for Electrical Connectors电子连接器的机械冲压测试程序38EIA-364-45A Firewall Flame Test Procedure for Electrical Connectors电子连接器的阻燃火焰测试程序39EIA-364-46B MICROSECOND DISCONTINUITY TEST PROCEDURE FOR ELECTRICAL CONNECTORS,CONTACTS AND SOCKETS电子连接器、端子和插座的瞬断(微秒不间断)测试程序40EIA-364-48A Metallic Coating Thickness Measurement of Contacts Test Procedure for Electrical Connectors电子连接器端子喷涂层厚底测试程序41EIA-364-50A Dust (Fine Sand)Test Procedure for Electrical Connectors电子连接器的粉尘(细沙)测试程序42EIA-364-53B Nitric Acid Vapor Test, Gold Finish Test Procedure for Electrical Connectors and Sockets电子连接器与插座的硝酸蒸汽测试、黄金制品测试程序43EIA-364-54A Magnetic Permeability Test Procedure for Electrical Connectors, Contacts, and Sockets电子连接器、端子和插座的导电率测试程序44EIA-364-56C Resistance to Soldering Heat Test Procedure for Electrical Connectors and Sockets电子连接器和插座的焊接热电阻测试程序45EIA-364-59A LOW TEMPERATURE TEST PROCEDURE FOR ELECTRICAL CONNECTORS AND SOCKETS电子连接器和插座的低温测试程序46EIA-364-66A EMI Shielding Effectiveness Test Procedure for Electrical Connectors电子连接器的电磁干扰屏蔽效应测试程序47EIA-364-70B TEMPERATURE RISE VERSUS CURRENT TEST PROCEDURE FOR ELECTRICAL CONNECTORS AND SOCKETS 电子连接器与插座的温升与电流测试程序48EIA-364-71B Solder Wicking (Wave Solder Technique) Test Procedure for Electrical Connectors and Sockets电子连接器与插座的溢锡(波峰焊接技术)测试程序49EIA-364-75LIGHTNING STRIKE TEST PROCEDURE FOR ELECTRICAL CONNECTORS电子连接器的雷击测试程序50EIA-364-81A Combustion Characteristics Test Procedure for Electrical Connector Housings, Connector Assemblies and Sockets. 电子连接器塑料、组装成品与插座的燃烧特性测试程序51EIA-364-82A Corrosivity of Plastics Test Procedure for Electrical Connector and Socket Housings电子连接器与插座塑胶的塑胶腐蚀性测试程序52EIA-364-83Shell-to-Shell and Shell-to-Bulkhead Resistance Test Procedure for Electrical Connectors电子连接器的接地壳与接地壳及接地壳与主板之电阻测试程序53EIA-364-89A Space Application Test Procedure for Electrical Connectors and Sockets电子连接器与插座的空间应用测试程序54EIA-364-90Crosstalk Ratio Test Procedures for Electrical Connectors, Sockets, Cable Assemblies orInterconnect Systems电子连接器、插座、线束或互联系统的串扰率测试程序55EIA-364-91A Dust Test Procedure for Electrical Connector and Sockets电子连接器与插座的粉尘测试程序56EIA-364-95Full Mating and Mating Stability Test Procedures for Electrical Connectors电子连接器的完整互配与互配稳定测试程序57EIA-364-99Gage Location and Retention Test Procedure for Electrical Connectors电子连接器的计量位置与保留测试程序58EIA-364-100Marking Permanence Test Procedure for Electrical Connectors and Sockets电子连接器与插座的永久性标识测试程序59EIA-364-101Attenuation Test Procedure for Electrical Connectors, Sockets, Cable Assemblies or Interconnection Systems 电子连接器、插座、线束或互联系统的衰减测试程序60EIA-364-102Rise Time Degradation Test Procedure for Electrical Connectors, Sockets,Cable Assemblies orInterconnection Systems。
EIA-364-1000_01A
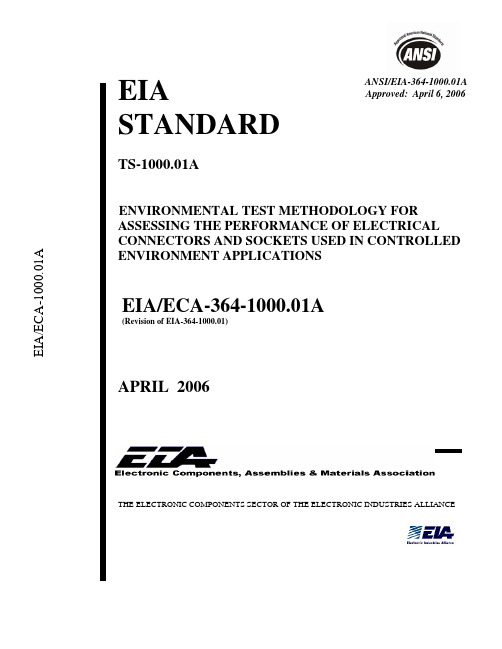
ANSI/EIA-364-1000.01AEIASTANDARDTS-1000.01AE NVIRONMENTAL TEST METHODOLOGY FOR ASSESSING THE PERFORMANCE OF ELECTRICAL CONNECTORS AND SOCKETS USED IN CONTROLLED ENVIRONMENT APPLICATIONSEIA/ECA-364-1000.01A(Revision of EIA-364-1000.01)APRIL 2006THE ELECTRONIC COMPONENTS SECTOR OF THE ELECTRONIC INDUSTRIES ALLIANCENOTICEEIA Engineering Standards and Publications are designed to serve the public interest through eliminating misunderstandings between manufacturers and purchasers, facilitating interchangeability and improvement of products, and assisting the purchaser in selecting and obtaining with minimum delay the proper product for his particular need. Existence of such Standards and Publications shall not in any respect preclude any member or nonmember of EIA from manufacturing or selling products not conforming to such Standards and Publications, nor shall the existence of such Standards and Publications preclude their voluntary use by those other than EIA members, whether the standard is to be used either domestically or internationally.Standards and Publications are adopted by EIA in accordance with the American National Standards Institute (ANSI) patent policy. By such action, EIA does not assume any liability to any patent owner, nor does it assume any obligation whatever to parties adopting the Standard or Publication.This EIA Standard is considered to have International Standardization implication, but the International Electrotechnical Commission activity has not progressed to the point where a valid comparison between the EIA Standard and the IEC document can be made.This Standard does not purport to address all safety problems associated with its use or all applicable regulatory requirements. It is the responsibility of the user of this Standard to establish appropriate safety and health practices and to determine the applicability of regulatory limitations before its use.(From Standards Proposal No. 5038 formulated under the cognizance of the CE-2.0 National Connector Standards Committee.Published by©ELECTRONIC INDUSTRIES ALLIANCE 2006Technology Strategy & Standards Department2500 Wilson BoulevardArlington, VA 22201PRICE: Please refer to the currentCatalog of EIA Electronic Industries Alliance Standards andEngineering Publicationsor call Global Engineering Documents, USA and Canada (1-800-854-7179)International (303-397-7956)All rights reservedPrinted in U.S.A.中国可靠性网 PLEASE !DON'T VIOLATETHELAW!This document is copyrighted by the EIA and may not be reproduced without permission.Organizations may obtain permission to reproduce a limited number of copies through entering into a license agreement. For information, contact:Global Engineering Documents15 Inverness Way EastEnglewood, CO 80112-5704 or callUSA and Canada (1-800-854-7179), International (303-397-7956)iCONTENTSClause Page (1)1 Introduction (1)1.1 Scope2 Test specimen (1) (1)2.1 Condition2.2 Sample (2)size (2)3 Testgroups4 Details to be specified (11) (11)documentation5 TestTable1 Test Group 1 (required for all connectors or sockets) (3)2 Test Group 2 (required for all connectors and sockets) (4)3 Test Group 3 (required for all connectors or sockets) (5)4 Test Group 4 (required for connectors or sockets with a precious metal platingon the contacts) (6)5 Test Group 5 (required for connectors or sockets with a tin-based platingon the contacts and optional for connectors or sockets with < 0.38 micronsof gold plating on the contacts) (8)6 Test Group 6 (required for connectors or sockets with a surface treatmenton the contacts or for connectors or sockets with a wipe length of0.127 mm or less) (9)7 Test Group 7 (required for connectors or sockets rated for> 50 mating/unmating cycles) (10)8 Test durations (hours) for temperature life (13)9 Test durations (hours) for temperature life (preconditioning) (14)ii中国可靠性网 CONTENTS (continued)Annex Page................................................................................................................. A-1 A Normative................................................................................................................ B-1 B Informativeiii中国可靠性网 EIA-364-1000.01APage 1TEST SEQUENCE No. 1000.01AENVIRONMENTAL TEST METHODOLOGY FOR ASSESSINGTHE PERFORMANCE OF ELECTRICAL CONNECTORS AND SOCKETSUSED IN CONTROLLED ENVIRONMENT APPLICATIONS(From EIA Standards Proposal No. 5038, formulated under the cognizance of EIA CE-2.0 Committee on National Connector Standards, and previously published in EIA-364-1000.01.)1 Introduction1.1 ScopeThis standard establishes the test procedures and test sequences to be followed when evaluating the performance of electrical connectors and sockets used in controlled environments. 1) Furthermore, it applies to contacts operating under low level circuit conditions. 2)The assumption is made that the contacts are metal. Polymer contacts, or other contact types, may require a different test methodology.2 Test specimen2.1 ConditionConnectors or sockets to be tested may be prototype parts to assess their design, or production parts to evaluate against an end user’s criteria. In either case, preparation of them for testing should consider board carrier or cable assembly processes. When access to a production or prototype soldering process to attach test specimens to a board carrier is not available, chemical and temperature exposure may be simulated by the procedures of EIA-364-11 (Resistance to Solvents Test Procedure for Electrical Connectors); and EIA-364-56, procedure 3 test condition E for a wave solder process, procedure 4 for a vapor phase reflow process, or procedure 5 level #3 for an infrared reflow process (Resistance to Soldering Heat Test Procedure for Electrical Connectors). When pressing test specimens to a board carrier or when terminating test specimens to a cable, appropriate tools should be used.1) Controlled environments are classified as no more severe than class number G1.2, according to the latest revision of EIA-364 (Electrical Connector/Socket Test Procedures Including Environmental Classifications).2) The applied voltage, generally < 50 millivolts, is not sufficient to break through any surface film. For contacts not operating under low level circuit conditions, such as those used in power applications; see the latest revision of EIA-364-70 (Test Procedure for Current vs. Temperature Rise of Electrical Connectors).EIA-364-1000.01APage 2NOTE ⎯Board carrier assembly operations are typically setup to attach all solderable components before press-fit connectors. Even so, the connectors may still besubjected to manual or automated soldering conditions during componentrework. This circumstance should be considered by the test engineer whenpreparing test specimens.2.2 Sample size2.2.1 For the test sequences in each of the test groups of clause 3, at least 100 separable contact interfaces from at least 5 connector or socket systems (plug/receptacle) should be evaluated. For low contact counts, at least 10 connector or socket systems should be tested. If Option #1A and Option #1B of test group 4 are chosen, then twice this sample size for that test sequence is required. If the connector or socket contains contacts that differ in the design of the critical area, then the sample size requirement should be applied to each design and the test results should be distinguishable.2.2.2 When a failure rate is desired, a significantly larger sample size for the test sequence in test group 4 should be tested. The user may require a larger sample size for other test groups, as well. The increase is dictated by the method of calculation chosen by the user.3 Test groupsFor an understanding of the objective of each test contained in the test groups; see annex B.中国可靠性网 EIA-364-1000.01APage 3 Table 1 - Test Group 1 (required for all connectors or sockets)Test Order Test Test procedure Condition oftest specimensTest criteria1 Low level contactresistance EIA-364-23 (termination ofconnector or socket to board carrieror cable shall be included inmeasurements)Mated None(base line measurements)2 Durability(preconditioning) EIA-364-09 (perform 5 unplug/plugcycles if the application requires upto 25 over the life of the connectoror socket; 20 cycles if theapplication requires 26-200; or, 50cycles if the application requires201 or greater)No evidence of physicaldamage3 Temperature life EIA-364-17, method A (see table 8for durations and temperatures)Mated None4 Low level contactresistance EIA-364-23 (termination ofconnector or socket to board carrieror cable shall be included inmeasurements)Mated Change in measurementsevaluated against criteriaspecified by user5 Reseating Manually unplug/plug the connectoror socket. Perform 3 such cycles. No evidence of physical damage6 Low level contactresistance EIA-364-23 (termination ofconnector or socket to board carrieror cable shall be included inmeasurements)Mated Change in measurementsevaluated against criteriaspecified by userEIA-364-1000.01APage 4Table 2 - Test Group 2 (required for all connectors and sockets)Test Order Test Test procedure Condition oftest specimensTest criteria1 Low level contactresistance EIA-364-23 (termination ofconnector or socket to board carrieror cable shall be included inmeasurements)Mated None(base line measurements)2 Durability(preconditioning) EIA-364-09 (perform 5 unplug/plugcycles if the application requires upto 25 over the life of the connectoror socket; 20 cycles if theapplication requires 26-200; or, 50cycles if the application requires201 or greater)No evidence of physicaldamage3 Thermal shock EIA-364-32, test condition I(10 cycles with the exception ofexposure times. Place athermocouple in the center of thelargest mass component of theconnector or socket that is in thecenter of the test chamber to insurethat the contacts reach thetemperature extremes beforeramping to the other temperature. )Mated None4 Low level contactresistance EIA-364-23 (termination ofconnector or socket to board carrieror cable shall be included inmeasurements)Mated Change in measurementsevaluated against criteriaspecified by user5 Cyclic temperature &humidity EIA-364-31 (Cycle the connector orsocket between 25 °C ± 3 °C at80 % ± 3% RH and 65 °C ± 3 °C at50 % ± 3% RH. Ramp times shouldbe 0.5 hour and dwell times shouldbe 1.0 hour. Dwell times start whenthe temperature and humidity havestabilized within the specifiedlevels. Perform 24 such cycles.)Mated None6 Low level contactresistance EIA-364-23 (termination ofconnector or socket to board carrieror cable shall be included inmeasurements)Mated Change in measurementsevaluated against criteriaspecified by user7 Reseating Manually unplug/plug the connectoror socket. Perform 3 such cycles. No evidence of physical damage8 Low level contactresistance EIA-364-23 (termination ofconnector or socket to board carrieror cable shall be included inmeasurements)Mated Change in measurementsevaluated against criteriaspecified by user中国可靠性网 Test Order Test Test procedure Condition oftest specimensTest criteria1 Low level contactresistance EIA-364-23 (termination ofconnector or socket to board carrieror cable shall be included inmeasurements)Mated None(base line measurements)2 Durability(preconditioning) EIA-364-09 (perform 5 unplug/plugcycles if the application requires upto 25 over the life of the connectoror socket; 20 cycles if theapplication requires 26-200; or, 50cycles if the application requires201 or greater)No evidence of physicaldamage3 Temperaturelife(preconditioning) EIA-364-17, method A (see table 9for durations and temperatures)Mated None4 Low level contactresistance EIA-364-23 (termination ofconnector or socket to board carrieror cable shall be included inmeasurements)Mated Change in measurementsevaluated against criteriaspecified by user5 Vibration EIA-364-28, test condition VII, testcondition letter D (15 minutes ineach of 3 mutually perpendiculardirections. Both mating halvesshould be rigidly fixed so as not tocontribute to the relative motion ofone contact against another. Themethod of fixturing should bedetailed in the test report.) Mated No evidence of physicaldamage6 Low level contactresistance EIA-364-23 (termination ofconnector or socket to board carrieror cable shall be included inmeasurements)Mated Change in measurementsevaluated against criteriaspecified by usera precious metal plating on the contacts)Test Order Test Test procedure Condition oftest specimensTest criteria1 Low level contactresistance EIA-364-23 (termination ofconnector or socket to board carrieror cable shall be included inmeasurements)Mated None(base line measurements)2 Durability(preconditioning) EIA-364-09 (perform 5 unplug/plugcycles if the application requires upto 25 over the life of the connectoror socket; 20 cycles if theapplication requires 26-200; or, 50cycles if the application requires201 or greater)No evidence of physicaldamage3 Temperaturelife(preconditioning) EIA-364-17, method A (see table 9for durations and temperatures)Mated None4 Low level contactresistance EIA-364-23 (termination ofconnector or socket to board carrieror cable shall be included inmeasurements)Mated Change in measurementsevaluated against criteriaspecified by user5 Mixed flowing gas EIA-364-65, class IIA (5 days tosimulate a 3-year field life; 7 days tosimulate a 5-year field life; or 14days to simulate a 10-year field life)See note None6 Low level contactresistance EIA-364-23 (termination ofconnector or socket to board carrieror cable shall be included inmeasurements)Mated Change in measurementsevaluated against criteriaspecified by user7 Thermal disturbance Cycle the connector or socketbetween 15 °C ± 3 °C and 85 °C ±3 °C, as measured on the part.Ramps should be a minimum of 2°C per minute, and dwell timesshould insure that the contacts reachthe temperature extremes (aminimum of 5 minutes). Humidityis not controlled. Perform 10 suchcycles.Mated None8 Low level contactresistance EIA-364-23 (termination ofconnector or socket to board carrieror cable shall be included inmeasurements)Mated Change in measurementsevaluated against criteriaspecified by usera precious metal plating on the contacts) (continued)Test Order Test Test procedure Condition oftest specimensTest criteria9 Reseating Manually unplug/plug the connectoror socket. Perform 3 such cycles. No evidence of physical damage10 Low level contactresistance EIA-364-23 (termination ofconnector or socket to board carrieror cable shall be included inmeasurements)Mated Change in measurementsevaluated against criteriaspecified by userNOTE ⎯ For 1-piece connectors or sockets: 1) expose unmated for 2/3 of the test duration; 2) mate each connector or socket to the same part that it was mated to during temperature life (preconditioning); and 3) expose for the remainder of the test duration. For 2-piece connectors, select either Options #1A and #1B or select Option #2.⎯Option #1A (plugs): 1) expose 1/2 of the specimens unmated for 2/3 of the test duration; 2) mate each specimen to the same receptacle that it was mated to during temperature life (preconditioning); and, 3) expose for the remainder of the test duration.⎯Option #1B (receptacles): 1) expose 1/2 of the specimens unmated for 2/3 of the test duration; 2) mate each specimen to the same plug that it was mated to during temperature life (preconditioning); and, 3) expose for the remainder of the test duration.⎯Option #2: 1) expose all plugs and receptacles unmated for 2/3 of the test duration; 2) mate each piece to the same piece that it was mated to during temperature life (preconditioning); and, 3) expose for the remainder of the test duration.Table 5 - Test Group 5 (required for connectors or sockets with a tin-based plating on the contacts and optional for connectors or sockets with< 0.38 microns of gold plating on the contacts)Test Order Test Test procedure Condition oftest specimensTest criteria1 Low level contactresistance EIA-364-23 (termination ofconnector or socket to board carrieror cable shall be included inmeasurements)Mated None(base line measurements)2 Durability(preconditioning) EIA-364-09 (perform 5 unplug/plugcycles if the application requires upto 25 over the life of the connectoror socket; 20 cycles if theapplication requires 26-200; or, 50cycles if the application requires201 or greater)No evidence of physicaldamage3 Temperaturelife(preconditioning) EIA-364-17, method A (see table 9for durations and temperatures)Mated None4 Low level contactresistance EIA-364-23 (termination ofconnector or socket to board carrieror cable shall be included inmeasurements)Mated Change in measurementsevaluated against criteriaspecified by user5 Thermal cycling Cycle the connector or socketbetween 15 °C ± 3°C. and 85 °C ±3 °C, as measured on the part.Ramps should be a minimum of2 °C per minute, and dwell timesshould insure that the contacts reachthe temperature extremes (aminimum of 5 minutes). Humidityis not controlled. Perform 500 suchcycles.Mated None6 Low level contactresistance EIA-364-23 (termination ofconnector or socket to board carrieror cable shall be included inmeasurements)Mated Change in measurementsevaluated against criteriaspecified by user7 Reseating Manually unplug/plug the connectoror socket. Perform 3 such cycles. No evidence of physical damage8 Low level contactresistance EIA-364-23 (termination ofconnector or socket to board carrieror cable shall be included inmeasurements)Mated Change in measurementsevaluated against criteriaspecified by userTable 6 - Test Group 6 (required for connectors or sockets with a surface treatment on the contacts or for connectors or sockets with a wipe length of 0.127 mm or less)Test Order Test Test procedure Condition oftest specimensTest criteria1 Low level contactresistance EIA-364-23 (termination ofconnector or socket to board carrieror cable shall be included inmeasurements)Mated None(base line measurements)2 Durability(preconditioning) EIA-364-09 (perform 5 unplug/plugcycles if the application requires upto 25 over the life of the connectoror socket; 20 cycles if theapplication requires 26-200; or, 50cycles if the application requires201 or greater)No evidence of physicaldamage3 Dust EIA-364-91 (benign dustcomposition)Unmated None4 Low level contactresistance EIA-364-23 (termination ofconnector or socket to board carrieror cable shall be included inmeasurements)Mated Change in measurementsevaluated against criteriaspecified by user (see note)5 Thermal disturbance Cycle the connector or socketbetween 15 °C ± 3 °C and 85 °C ±3 °C , as measured on the part.Ramps should be a minimum of20C./minute, and dwell times shouldinsure that the contacts reach thetemperature extremes (a minimumof 5 minutes). Humidity is notcontrolled. Perform 10 such cycles.Mated None6 Low level contactresistance EIA-364-23 (termination ofconnector or socket to board carrieror cable shall be included inmeasurements)Mated Change in measurementsevaluated against criteriaspecified by user (see note)7 Reseating Manually unplug/plug the connectoror socket. Perform 3 such cycles. No evidence of physical damage8 Low level contactresistance EIA-364-23 (termination ofconnector or socket to board carrieror cable shall be included inmeasurements)Mated Change in measurementsevaluated against criteriaspecified by user (see note)NOTE ⎯ Failure to meet the criteria does not necessarily disqualify the connector or socket. Rather, it may indicate the need for protection against particulate contamination, such as that afforded by a dust cover. For a connector or socket with a surface treatment on the contacts, a comparison of the test results to those obtained for the same connector or socket without a surface treatment on the contacts should be made. Only then can the impact of the surface treatment be determined.Table 7 - Test Group 7 (required for connectors or sockets rated for> 50 mating/unmating cycles)Test Order Test Test procedure Condition of test specimensTest criteria 1 Dielectric withstanding voltage EIA-364-20 (voltage level, ac or dc,and the orientation of the connectoror socket should be defined in thedetails of the test report)Mated No disruptive discharge No leakage current in excess of the maximum specified by user 2 Low level contact resistance EIA-364-23 (Termination of theconnector or socket to the boardcarrier or cable shall be included in the measurements. The orientation of the connector or socket should be defined in the details of the test report.)Mated None (base line measurements) 3 Durability EIA-364-09 (Perform the ratednumber of unplug/plug cycles.Retention features, such as latches, should not be deactivated. The orientation of the connector or socket should be defined in the details of the test report.)No evidence of physical damage 4 Low level contact resistance EIA-364-23 (Termination of theconnector or socket to the boardcarrier or cable shall be included inthe measurements. The orientation of the connector or socket should be defined in the details of the test report.)Mated Change in measurements evaluated against criteria specified by user 5 Dielectric withstanding voltage EIA-364-20 (voltage level, ac or dc,and the orientation of the connectoror socket should be defined in thedetails of the test report)Mated No disruptive discharge No leakage current in excess of the maximum specified by user NOTES1 Separate sets of test specimens may be used to assess dielectric withstanding voltage and the change in low level contactresistance.2 Dielectric withstanding voltage testing should involve different contacts than low level contact resistance testing.4 Details to be specifiedThe following details shall be specified in the referencing document:4.1 Rated number of durability cycles4.2 Temperature and duration for temperature life test; see table 84.3 Temperature and duration for temperature life (preconditioning) test; see table 94.4 Option used for test group 4 (see note at the bottom of table 4) and the duration of exposure to mixed flowing gas4.5 Connector or socket to be tested (supplier part number and family name)4.6 Contact plating types and thicknesses (with measurement location and technique to be used) 4.7 Plastic material(s) (generic type, color, and glass and/or mineral content)4.8 Contact alloy (CA number or other industry material designation)4.9 Surface treatment (lubricant or other, if any)NOTE ⎯If present, do not remove during preparation of test specimens.4.10 Pass/Fail criteria (if any)4.11 Any information that differs from that described in this standard.5 Test documentationDocumentation shall contain the following. Some items may be provided by the connector or socket supplier. Others may be determined by the testing laboratory.5.1 Description of test specimen(s)5.1.1 Supplier part number(s)5.1.2 Supplier family name5.1.3 Applicable industry standards5.1.4 Contact count and spacing5.1.5 Number of rows of contacts5.1.6 Plastic material (generic type, color, and glass and/or mineral content)5.1.7 Contact alloy (CA number or other industry material designation)5.1.8 Contact plating types5.1.9 Test specimen plating thicknesses, including statistical summary of the measurements 5.1.10 Surface treatment, if any5.1.10.1 Supplier name and/or generic description5.1.10.2 How and when applied to contacts5.1.11 For card edge connectors, thickness and bevel of mating card5.1.12 Photographs (optional)5.2 Preparation of test specimens5.2.1 Description of board carrier attachment method5.2.1.1 Chemical (flux, solvent, rinse, etc.) and temperature exposure5.2.1.2 Application tools used5.2.2 Description of cable/wire termination method5.2.2.1 Application tools used5.2.2.2 Cable/wire size5.2.2.3 Cable/wire type5.2.2.3.1 Plating5.2.2.3.2 Number of strands5.3 Test equipment used, and date of last and next calibration5.4 Test procedures used5.4.1 Deviation(s) to those specified, if any, including explanation(s)5.5 Schematic diagram of the circuit used to measure low level contact resistance5.6 Test results5.6.1 Mean, minimum, and maximum change in low level contact resistance, and the standard deviation of the changes, as calculated at each interval of measurement in each of the test groups5.6.2 Plots of the change in low level contact resistance (y-axis) versus cumulative % of the readings less than that change (x-axis) for each interval of measurement in each of the test groups (if requested)5.6.3 Tabulated data of the change in low level contact resistance of each circuit that includes a separable contact interface, as calculated at each interval of measurement in each of the test groups (if requested)5.6.4 Photographs (optional)5.7 A discussion of the test results5.8 Name of operator and date of testsTable 8 - Test durations (hours) for temperature lifeField temperatureTest temperatureand field life 90 °C 105 °C 115 °C57 °C for 3 years 192 24 857 °C for 5 years 288 48 1257 °C for 10 years 552 72 2460 °C for 3 years 288 48 1260 °C for 5 years 456 72 2460 °C for 10 years 840 120 4865 °C for 3 years 600 96 2465 °C for 5 years 960 120 4865 °C for 10 years 1,848 240 7285 °C for 3 years 4,176 528 14485 °C for 5 years 6,912 840 24085 °C for 10 years 13,680 1,584 432 NOTES1 Test durations pertaining to field temperatures of 57 °C, 60 °C, and 65 °C. are based on theassumption that the contact spends its entire field life at that temperature, whereas those associated with a field temperature of 85 °C are based on the assumption that the contact spends 1/3 of its field life at that temperature.2 The materials used in the construction of the connector or socket and in the components ofthe test vehicle (e.g., printed circuit cards, wiring, etc.) should be considered when selectinga test temperature.。
EIA-364-28F_(2011-01-14)_Vibration

EIASTANDARDTP-28FVIBRATION TEST PROCEDURE FOR ELECTRICAL CONNECTORS AND SOCKETSEIA-364-28FJANUARY 2011EIA StandardsElectronic Components AssociationANSI/EIA-364-28F-2011Approved: January 14, 2011E I A -364-28FNOTICEThis standard is based upon the major technical content of International Electrotechnical Commission standard 60512-2-1 2005-Febuary (was IEC 512-2, test 2a), contact resistance - millivolt level method. It conforms in all essential respects this IEC standard.EIA Engineering Standards and Publications are designed to serve the public interest through eliminating misunderstandings between manufacturers and purchasers, facilitating interchangeability and improvement of products, and assisting the purchaser in selecting and obtaining with minimum delay the proper product for his particular need. Existence of such Standards and Publications shall not in any respect preclude any member or nonmember of ECA from manufacturing or selling products not conforming to such Standards and Publications, nor shall the existence of such Standards and Publications preclude their voluntary use by those other than ECA members, whether the standard is to be used either domestically or internationally.Standards and Publications are adopted by ECA in accordance with the American National Standards Institute (ANSI) patent policy. By such action, ECA does not assume any liability to any patent owner, nor does it assume any obligation whatever to parties adopting the Standard or Publication.This major portion of this Standard is based upon the technical content of International Electrotechnical Commission standard IEC 60512-6-4, (was IEC 512-4, test 6d) Dynamic Stress, Vibration (Sinusoidal), 2002 and also IEC 60512-6-5, Dynamic Stress, Random Vibration, 1997. It differs from IEC Publication 60068-2-6 (was IEC 68-2-6, test Fc), Vibration (Sinusoidal), 2007; by specifying a single test with closely controlled conditions and methods for random vibration. These differences have been called to the attention of the U.S. Committee of Experts for IEC (or ISO) Technical Committee TC48 and resolution of these differences will be sought in future meetings of SC48. Test condition VII is based on International Electrotechnical Commission standard IEC 60068-2-34, (was IEC 68-2-34, Test Fd), Random Vibration Wide Band, 1993.This Standard does not purport to address all safety problems associated with its use or all applicable regulatory requirements. It is the responsibility of the user of this Standard to establish appropriate safety and health practices and to determine the applicability of regulatory limitations before its use.(From Standards Proposal No. SP-5212 formulated under the cognizance of the CE-2.0 National Connector Standards Committee).Published by©ELECTRONIC COMPONENTS ASSOCIATION 2011Engineering Department2500 Wilson Boulevard, Suite 310Arlington, VA 22201PRICE: Please call: IHSUSA and Canada (1-800-854-7179)All rights reservedPrinted in U.S.A.PLEASE!DON'T VIOLATETHELAW!This document is copyrighted by the ECA and may not be reproduced without permission.Organizations may obtain permission to reproduce a limited number of copies through entering into a license agreement. For information, contact:IHS15 Inverness Way EastEnglewood, CO 80112-5704 or callUSA and Canada (1-800-854-7179), International (303-397-7956)CONTENTSClause Page 1 Introduction (1)1.1 Scope (1)1.2 Object (1)1.3 Applicable documents (1)1.4 Definitions (1)2 Test resources (2)2.1 Equipment (2)3 Test specimen (3)4 Test procedure (4)4.1 Test conditions I, II, III and IV (4)4.2 Test conditions V, VI and VII (10)5 Details to be specified (16)6 Test documentation (17)Table1 Vibration conditions (4)2 Values for test condition V (13)3 Values for test condition VI (14)4 Values for test condition VII (15)Figure1 Mounting axis definitions (2)2 Vibration test curves - high frequency (displacement in mm) (6)3 Vibration test curves - high frequency (displacement in inches) (7)4 Test condition V, random vibration test curve envelope (13)5 Test condition VI, random vibration test curve envelope (14)6 Test condition VII, random vibration test curve envelope (15)(This page left blank)TEST PROCEDURE No. 28FVIBRATION TEST PROCEDUREFORELECTRICAL CONNECTORS AND SOCKETS(From EIA Standards Proposal No. 5212, formulated under the cognizance EIA CE-2.0 Committee on National Connector Standards, and previously published in EIA-364-28E.)1 Introduction1.1 ScopeThe standard test procedure details a method to assess the ability of electrical connector components to withstand specified severities of vibration.1.2 ObjectThe object of this test is to determine the effects of vibration within the predominant or random vibration frequency ranges and magnitudes that may be encountered during the life of the connector.1.3 Applicable documentsThe following documents form a part of this standard to the extent indicated herein. In the event of conflict between the requirements of this standard and the referenced documents, this standard takes precedence.1.3.1 EIA standardsEIA-364-46: Microsecond Discontinuity Test Procedure for Electrical Connectors, Contacts and SocketsEIA-364-87: Nanosecond Event Detection for Electrical Connectors, Contacts and Sockets1.4 Definitions1.4.1 AxisThe following mounting axis definitions shall be employed during the performance of this test. Figure 1 indicates a pictorial view of the axis definitions. The referencing document shall indicate the fixturing required or the axis definitions if different than as stated in figure 1. Axis definitions for symmetrical, square and “free” connectors shall be defined in the Detail Specification.1.4.1.1 X-axisAlong the longitudinal length of the test sample1.4.1.2 Y-axisThe axis perpendicular to the longitudinal length of the sample (transverse direction).1.4.1.3 Z-axisThe axis perpendicular to the fixture seating plane attached to the test table.Figure 1 - Mounting axis definitions1.4.2 The term gnThis term is the SI unit for the standard acceleration due to the earth’s gravity, which itself varies with altitude and geographic latitude. NOTE — In this standard the value of g n is 9.81 m/s 2.2. Test resources2.1 Equipment2.1.1 The monitoring transducer shall be calibrated against a standard transducer having an accuracy of ±2%. The vibration system consisting of the vibration machine, together with its auxiliary test equipment, shall be capable of generating either a sinusoidal or random excitation.2.1.2 Test equipment for random vibration shall produce random excitation that possesses a gaussian (normal) amplitude distribution, except that the acceleration magnitudes of the peak values may be limited to a minimum of three times the rms [three-sigma (3σ) limits].3 Test specimen3.1 A vibration test sample shall be a fully wired connector consisting of one of the following, as applicable;3.1.1 A connector plug and its mating connector receptacle.3.1.2 A printed circuit connector receptacle and its mating connector board(s).3.1.3 An integral, functional connector assembly.3.2 Each test sample shall be prepared with wire and other materials or processes, simulating application assembly of the sample. If normal connector mating is dependent upon forces external to the connector, then such forces and mounting arrangement shall be as closely duplicated as possible (example: printed circuit connectors). If mating is achieved with normal locking means, then only normal locking means shall be used.3.3 Method of mounting3.3.1 Test conditions I, II, III and IV (sinusoidal evaluation conditions)The specimen shall be attached to a fixture capable of transmitting the vibration conditions specified. The test fixture shall be designed so that resonant vibration inherent in the fixture within the frequency range specified for the test shall be minor. The magnitude of the applied vibration shall be monitored on the test fixture near the specimen mounting points. The test specimen shall be mounted rigidly to the test fixture as specified and shall simulate as closely as possible the normal mounting of the specimen. A minimum of 200 mm (approx 8 in) of wire or cable shall be unsupported on both ends of the connector. For specimens with attached brackets, one of the vibration-test directions shall be parallel to the mounting surface of the bracket. Vibration input shall be monitored on the mounting fixture in the proximity of the support points of the specimen.3.3.2 Test conditions V, VI and VII (random excitation conditions)The specimen shall be mounted as specified. The orientation of the specimen or direction of application of the applied vibration motion shall be specified in one or more directions. If the order of application of the different directions is critical, it also shall be specified. Any special test fixtures or jigs required to run the test shall be specified in sufficient detail to assure reproducibility of the input motion applied to the specimen. These details shall include the dimensions, the materials, temper, etc., as applicable.4 Test procedureTests and measurements before, during and after vibration shall be as specified in the referencing document.4.1 Test conditions I, II, III and IV4.1.1 Electrical load and discontinuity4.1.1.1 Unless otherwise specified in the referencing document, an electrical load of 100 milliamperes maximum with a detector capable of detecting a discontinuity of 1.0 microsecond or longer. Said monitoring shall be performed in accordance with EIA-.364-46.4.1.1.2 Unless otherwise specified in the referencing document, low nanosecond event detection shall be performed in accordance with EIA-364-87. A 100 milliamperes test current shall be applied to the areas being monitored. A detector capable of measuring an event resulting in a 10 ohm change lasting longer than 10 nanoseconds, unless otherwise specified in the referencing document.4.1.1.2.1 Low nanosecond event detection shall not be used as a substitute for the standard 1.0 microsecond requirement. This monitoring test was developed to detect different failure mechanisms than that described in 4.1.1.1. It is designed to detect large resistance fluctuations or voltage variations that may result in improper triggering of high speed digital circuits.4.1.2 Vibration conditionsVibration conditions shall be in accordance with table 1, as applicable.Table 1 - Vibration conditionsTest conditions Frequency range, Hz Peak levelg n m/s2I Low - 10 to 55II High - 10 to 500 10 98.1III High - 10 to 2,000 15 147.1IV High - 10 to 2,000 20 196.14.1.3 ResonanceA critical resonant frequency is that frequency at which any point on the specimen is observed to have a maximum amplitude more than twice that of the support points. When specified, resonant frequencies shall be determined either by monitoring parameters such as contact opening, or by use of resonance-detecting instrumentation.4.1.4 Test condition IThe specimens shall be subjected to a simple harmonic motion having an amplitude 1.52 mm (0.06 in) double amplitude (maximum total excursion), the frequency being varied uniformly between the approximate limits of 10 Hz and 55 Hz. The entire frequency range, from 10 Hz to 55 Hz and return to 10 Hz, shall be traversed in approximately 1 minute. Unless otherwise specified, this motion shall be applied for 2 hours in each of three mutually perpendicular directions (total of 6 hours). If applicable, this test shall be made under electrical load conditions.4.1.5 Test condition II [98.1 m/s2 (10 g n) peak]The specimens, while deenergized or operating under the load conditions specified, shall be subjected to the vibration amplitude, frequency range, and duration specified 4.1.5.1, 4.1.5.2 and 4.1.5.3, respectively; see figures 2 and 3.4.1.5.1 AmplitudeThe specimens shall be subjected to a simple harmonic motion having an amplitude of either 1.52 mm (0.06 in) double amplitude (maximum total excursion) or 98.1 m/s2(10 g n) peak, whichever is less. The tolerance on vibration amplitude shall be ±10%.4.1.5.2 FrequencyThe vibration frequency shall be varied logarithmically between the approximate limits of 10 Hz and 500 Hz (see 4.1.8) except that the procedure (see 4.1.4) of this standard may be applied during the 10 Hz to 55 Hz band of the vibration frequency range.4.1.5.3 Sweep time and durationThe entire frequency range of 10 Hz to 500 Hz and return to 10 Hz shall be traversed in 15 minutes. This cycle shall be performed 12 times in each of three mutually perpendicular directions (total of 36 times), so that the motion shall be applied for a total period of approximately 9 hours. Interruptions are permitted provided the requirements for rate of change and test duration are met. Completion of cycling within any separate band is permissible before going to the next band. When the procedure (see 4.1.4) is used for the 10 Hz to 55 Hz band, the duration of this portion shall be same as the duration for this band using logarithmic cycling (approximately 1-1/3 hours in each of three mutually perpendicular directions).4.1.6 Test condition III 147.1 m/s2 (15 g n) peak]The specimens, while deenergized or operating under the load conditions specified, shall be subjected to the vibration amplitude, frequency range, and duration specified in 4.1.6.1, 4.1.6.2 and 4.1.6.3, respectively; see figures 2 and 3.NOTE: g = 0.00201f 2 DA (f = frequency in hertz, DA = double amplitude in mm)Figure 2 - Vibration test curves - high frequency (displacement in mm)NOTE: g = 0.0512f 2 DA (f = frequency in hertz, DA = double amplitude in inches) Figure 3 - Vibration test curves - high frequency (displacement in inches)4.1.6.1 AmplitudeThe specimens shall be subjected to a simple harmonic motion having an amplitude of either 1.52 mm (0.06 in) double amplitude (maximum total excursion) or 147.1 m/s2(15 g n) peak, whichever is less. The tolerance on vibration amplitude shall be ±10%.4.1.6.2 Frequency rangeThe vibration frequency shall be varied logarithmically between the approximate limits of 10 Hz to 2,000 Hz (see 4.1.8) except that the procedure (see 4.1.4) of this standard may be applied during the 10 Hz to 55 Hz band of the vibration frequency range.4.1.6.3 Sweep time and durationThe entire frequency range of 10 Hz to 2,000 Hz and return to 10 Hz shall be traversed in 20 minutes. This cycle shall be performed 12 times in each of three mutually perpendicular directions (total of 36 times), so that the motion shall be applied for a total period of approximately 12 hours. Interruptions are permitted provided the requirements for rate of change and test duration are met. Completion of cycling within any separate band is permissible before going to the next band. When the procedure (see 4.1.4) of this standard is used for the 10 Hz to 55 Hz band, the duration of this portion shall be the same as the duration for this band using logarithmic cycling (approximately 1-1/3 hours in each of three mutually perpendicular directions).4.1.7 Test condition IV [196.1 m/s2 (20 g n) peak]The specimens, while deenergized or operating under the load conditions specified, shall be subjected to the vibration amplitude, frequency range, and duration specified in 4.1.7.1, 4.1.7.2 and 4.1.7.3, respectively; see figures 2 and 3.4.1.7.1 AmplitudeThe specimens shall be subjected to a simple harmonic motion having an amplitude of either 1.52 mm (0.06 in) double amplitude (maximum total excursion) or 196.1 m/s2(20 g n) peak, whichever is less. The tolerance on vibration amplitude shall be ±10%.4.1.7.2 Frequency rangeThe vibration frequency shall be varied logarithmically between the approximate limits of 10 Hz to 2,000 Hz (see 4.1.8).4.1.7.3 Sweep time and durationThe entire frequency range of 10 Hz to 2,000 Hz and return to 10 Hz shall be traversed in 20 minutes. This cycle shall be performed 12 times in each of three mutually perpendicular directions (total of 36 times), so that the motion shall be applied for a total period of approximately 12 hours. Interruptions are permitted provided the requirements for rate of change and test duration are met.Completion of cycling within any separate band is permissible before going to the next band. When the procedure (see 4.1.4.) of this standard is used for the 10 Hz to 55 Hz band, the duration of this portion shall be the same as the duration for this band using logarithmic cycling (approximately 1-1/3 hours in each of three mutually perpendicular directions).4.1.8 Alternative procedure for use of linear in place of logarithmic change of frequency Linear rate of change of frequency is permissible under the following conditions:4.1.8.1 The frequency range above 55 Hz shall be subdivided into no fewer than three bands. The ratio of the maximum frequency to the minimum frequency in each band shall be not less than two (2).4.1.8.2 The rate of change of frequency in Hz per minute shall be constant within any one band.4.1.8.3 The ratios of the rate of change of frequency of each band to the maximum frequency of that band shall be approximately equal.4.1.8.3.1 Example of alternative procedureAs an example of the computation of rates of change, assume that the frequency spectrum has been divided into three bands, 55 Hz to 125 Hz, 125 Hz to 500 Hz and 500 Hz to 2,000 Hz, in accordance with 4.1.8.1. For each band, let the constant, κ, represent the frequency change (in Hz/minute), divided by the maximum frequency (in Hz). Then the rates of change for the three bands will be 125κ, 500κ and 2,000κ, respectively. The times (in minutes) to traverse the three frequency bands are1255512550012550020005002000−−−κκκ,,,andSince the minimum total sweep time is 30 minutes,701253755001500200030κκκ++=,,whence κ = 0.0687/minute.The required maximum constant rates of frequency change for the three bands are therefore 8.55 Hz per minute, 34.2 Hz per minute and 137 Hz per minute, respectively. The minimum times of traverse of the bands are 8.2 min, 10.9 min and 10.9 min, respectively.4.2 Test conditions V, VI and VII4.2.1 Control and analysis of random vibration4.2.1.1 Spectral density curvesThe output of the vibration machine shall be presented graphically as power-spectral density versus frequency; see 4.2.1.1.1. The spectral-density values shall be within +40% and -30% (±1.5 dB) of the specified values between a lower-specified frequency and 1,000 Hz, and within +100% and -50% (±3 dB) of the specified values between 1,000 and an upper-specified frequency (2,000 Hz). A filter bandwidth will be a maximum of 1/3-octave or a frequency of 25 Hz, whichever is greater.4.2.1.1.1 Power-spectral densityPower-spectral density is the mean-square value of an oscillation passed by a narrow-band filter per unit-filter bandwidth. For this application it is expressed as g 2 / f, where g 2 / f is the mean-square value of acceleration expressed in gravitational units per number of cycles of filter bandwidth. The spectral density curves are usually plotted either on a logarithmic scale, or in units of decibels (dB). The number of decibels is defined by the equation:The rms value of acceleration within a frequency band between f 1 and f 2 is:g = f df rms 2f f 12g ∫//12where g r 2 / f is a given reference value of power-spectral density, usually the maximum specified value.4.2.1.2 Distribution curvesA probability density-distribution curve may be obtained and compared with a gaussian-distribution curve. The experimentally-obtained curve shall not differ from the gaussian curve by more than ± 10% of the maximum value.4.2.1.3 MonitoringMonitoring involves measurements of the vibration excitation and of the test item performance. When required in the referencing document, the specimen may be monitored during the test. The details of the monitoring circuit, including the method and points of connection to the specimen, shall be specified.dB = 10 g /f g /f = 20 g /fg /f2r r log log 24.2.1.4 Vibration inputThe vibration magnitude shall be monitored on a vibration machine, on mounting fixtures, at locations that are as near as practicable to the test item mounting points. When the vibration input is measured at more than one point, the minimum input vibration shall normally be made to correspond to the specified test curve; see figures 4 and 5. For massive test items and fixtures, and for large force exciters or multiple vibration exciters, the input control value may be an average of the average magnitudes of three or more inputs. Accelerations in the transverse direction, measured at the test item attachment points, shall be limited to 100% of the applied vibration. The number and location of the test points shall be specified.4.2.2 ProcedureThe specimen, or substitute equivalent mass, shall be mounted in accordance with 3.3.2 and the monitoring equipment attached, if applicable, in accordance with 4.2.1.3. The vibration machine shall then be operated and equalized or compensated to deliver the required frequencies and intensities conforming to the curves specified in test condition V, figure 4, or test condition VI, figure 5, or test condition VII, figure 6 (see 2.1). The specimen shall then be subjected to the vibration specified by the test condition letter (see tables 2, 3 and 4) for the duration as specified:3 minutes; 15 minutes; 1-1/2 hours; or 8 hours;in each of three mutually perpendicular directions, and in the order specified (see 3.3.2), as applicable.The measurements made before, during, and after the test shall be specified and if the specimen is to be monitored during the test, the details shall be in accordance with 4.2.1.3.4.2.3 Electrical load and discontinuities4.2.3.1 Unless otherwise specified in the referencing document, an electrical load of 100 milliamperes maximum with a detector capable of detecting a discontinuity of 1.0 microsecond or longer. Said monitoring shall be performed in accordance with EIA-.364-46.4.2.3.2 Unless otherwise specified in the referencing document, low nanosecond event detection shall be performed in accordance with EIA-364-87. A 100 milliamperes test current shall be applied to the areas being monitored. A detector capable of measuring an event resulting in a 10 ohm change lasting longer than 10 nanoseconds, unless otherwise specified in the referencing document.4.2.3.2.1 Low nanosecond event detection shall not be used as a substitute for the standard 1.0 microsecond requirement. This monitoring test was developed to detect different failure mechanisms than that described in 4.2.3.1. It is designed to detect large resistance fluctuations or voltage variations that may result in improper triggering of high speed digital circuits.Figure 4 - Test condition V, random vibration test-curve envelope (see table 2).Table 2 - Values for test condition V 1)Test condition letter Power spectral density, g 2/Hz Overall rms gA 0.02 5.35B 0.04 7.56C 0.06 9.26D 0.1 11.95E 0.2 16.91F 0.3 20.71G 0.4 23.91H 0.6 29.28I Superseded by Test condition letterJ J 1.0 37.80K 1.5 46.301) For duration of test; see 4.2.2.Figure 5 - Test condition VI, random vibration test-curve envelope (see table 3).Table 3 - Values for test-condition VI 1)Test condition letter Power spectral density, g 2/Hz Overall rms gA 0.02 6.21B 0.04 8.78C 0.06 10.76D 0.1 13.89E 0.2 19.64F 0.3 24.06G 0.4 27.78H 0.6 34.02I Superseded by Test condition letterJ J 1.0 43.92K 1.5 53.791) For duration of test; see 4.2.2.Figure 6 - Test condition VII, random vibration test-curve envelope (see table 4)Table 4 - Values for test condition VII 1)Test condition letter Power spectraldensity, g 2/Hz Overall rms gA 0.002 0.98B 0.005 1.55C 0.01 2.19D 0.02 3.10E 0.05 4.90F 0.1 6.93G 0.29.801) For duration of test; see 4.2.2.5 Details to be specifiedThe following details shall be specified in the referencing document:5.1 Type of sample; see 3.15.2 Number of samples to be tested5.3 Method of mounting; see 3.35.4 Test condition number; see tables 1, 2, 3 or 45.5 Electrical load conditions, all contacts, if other than 100 milliamperes maximum; see 4.1.1 or 4.2.35.6 Discontinuity requirement if other than 1 microsecond5.7 Measurement of discontinuities during vibration; see 4.1.1 or 4.2.35.8 Method of determining resonance, if applicable; see 4.1.35.9 Direction of motion and order, if critical; see 3.35.10 Tests or measurements before, during and after vibration; see clause 45.11 Duration of vibration; see 4.1.4 or 4.2.25.12 Monitoring instrumentation, if applicable; see 4.2.1.35.13 Number and location of test points, if applicable; see 4.2.1.35.14 Mounting axes definitions if other than indicated in figure 1; see 1.46 Test documentationDocumentation shall contain the details specified in clause 5, with any exceptions, and the following:6.1 Title of test6.2 Sample description include fixture, if applicable6.3 Test equipment used, and date of last and next calibration6.4 Photographs, plots, values and observations necessary for proof of conformance6.5 Name of operator and start/finish date(s) of testRevision HistoryRevision letter ProjectnumberAdditions, changes and deletionsE SP-5125 Changed test condition letter I to J. Superseded testcondition letter I by J in table 2 and 3.F SP-5212 Add paragraph 1.3.Revise paragraph 4.1.1 and 4.2.3.EIA Document Improvement ProposalIf in the review or use of this document, a potential change is made evident for safety, health or technical reasons, please fill in the appropriate information below and mail or FAX to:Electronic Components AssociationEngineering Department2500 Wilson Blvd, Suite 310.Arlington, VA 22201FAX: (703-875-8908)Document No.: Document Title:Submitter’s Name: Telephone No.:FAX No.:e-mail:Address:Urgency of Change:Immediate: At next revision:Problem Area:a. Clause Number and /or Drawing:b. Recommended Changes:c. Reason/Rationale for Recommendation:Additional Remarks:Signature: Date:2FOR ECA USE ONLYResponsible Committee:Chairman:Date comments forwarded to Committee Chairman:Electronic Components Association2500 Wilson Boulevard, Suite 310 * Arlington, VA 22201 * tel 703-907-8021 * fax 703-875-8908。
EIA-364-13C_插拔力测试标准

EIA STANDARD TP-13C M ATING AND UNMATING FORCE TEST PROCEDURE FOR ELECTRICAL CONNECTORSEIA/ECA-364-13C (Revision of EIA-364-13B) JUNE 2006THE ELECTRONIC COMPONENTS SECTOR OF THE ELECTRONIC INDUSTRIES ALLIANCE ANSI/EIA-364-13C-2006NOTICEEIA Engineering Standards and Publications are designed to serve the public interest through eliminating misunderstandings between manufacturers and purchasers, facilitating interchangeability and improvement of products, and assisting the purchaser in selecting and obtaining with minimum delay the proper product for his particular need. Existence of such Standards and Publications shall not in any respect preclude any member or nonmember of EIA from manufacturing or selling products not conforming to such Standards and Publications, nor shall the existence of such Standards and Publications preclude their voluntary use by those other than EIA members, whether the standard is to be used either domestically or internationally.Standards and Publications are adopted by EIA in accordance with the American National Standards Institute (ANSI) patent policy. By such action, EIA does not assume any liability to any patent owner, nor does it assume any obligation whatever to parties adopting the Standard or Publication.This EIA Standard is considered to have International Standardization implication, but the International Electrotechnical Commission activity has not progressed to the point where a valid comparison between the EIA Standard and the IEC document can be made.This Standard does not purport to address all safety problems associated with its use or all applicable regulatory requirements. It is the responsibility of the user of this Standard to establish appropriate safety and health practices and to determine the applicability of regulatory limitations before its use.(From Standards Proposal No. 5136 formulated under the cognizance of the CE-2.0 National Connector Standards Committee.Published by©ELECTRONIC INDUSTRIES ALLIANCE 2006Technology Strategy & Standards Department2500 Wilson BoulevardArlington, VA 22201PRICE: Please refer to the currentCatalog of EIA Electronic Industries Alliance Standards and EngineeringPublicationsor call Global Engineering Documents, USA and Canada (1-800-854-7179)International (303-397-7956)All rights reservedPrinted in U.S.A.PLEASE !DON'T VIOLATETHELAW!This document is copyrighted by the EIA and may not be reproduced without permission.Organizations may obtain permission to reproduce a limited number of copies through entering into a license agreement. For information, contact:Global Engineering Documents15 Inverness Way EastEnglewood, CO 80112-5704 or callUSA and Canada (1-800-854-7179), International (303-397-7956)CONTENTSClause Page (1)1 Introduction (1)1.1 Scope (1)resources2 Test (1)2.1 Equipment3 Test specimen (1) (1)A3.1 Method (2)3.2 MethodB (2)procedure4 TestA (2)4.1 MethodB (2)4.2 Method5 Details to be specified (3) (3)6 Testdocumentation(This page left blank)TEST PROCEDURE No. 13CMATING AND UNMATING FORCE TEST PROCEDUREFORELECTRICAL CONNECTORS(From EIA Standards Proposal No. 5136, formulated under the cognizance EIA CE-2.0 Committee on National Connector Standards, and previously published in EIA-364-13B.)1 Introduction1.1 ScopeThis standard establishes a method to determine the forces required to mate and unmate electrical connectors or protective caps with connectors, connectors/sockets with gages or devices. Unless otherwise specified in the referencing document, method A shall be used.2 Test resources2.1 EquipmentThe test equipment shall consist of:2.1.1 Mounting fixtures that allow the specimens to be mounted in their normal manner.2.1.2 Force or torque gages, of suitable range for the connector size under test, so that readings will be in the middle 50% of the scale, where practicable, with a nominal full scale accuracy of +2%.2.1.3 Attachments and accessory type equipment as required to mate the test specimens and attach the force or torque gages (arbor press, etc.).2.1.4 Gage(s) or device(s) to mate the connector/socket with (applicable to method B only).3 Test specimen3.1 Method AThe specimen shall consist of a plug and a receptacle with all applicable contacts in place. All applicable hardware shall be assembled to the specimen including skirts, hoods, cable clamps, jackscrews, guide pins or sockets unless otherwise specified. The specimen shall not be lubricated or cleaned in any manner unless otherwise specified in the referencing document. If applicable the specimen shall be terminated as specified in the referencing document.3.2 Method BThe specimen shall consist of the connector/socket and the gage(s) or device(s) as specified in the referencing document. Unless otherwise specified in the referencing document, all applicable contacts and hardware shall be installed including skirts, hoods, cable clamps, guide pins, etc. The specimen shall not be lubricated or cleaned and active latches are to be deactivated unless otherwise specified in the referencing document. If applicable, the specimen shall be terminated as specified in the referencing document.4 Test procedure4.1 Method AUnless otherwise specified, the specimen shall be mounted to mounting fixtures by the normal mounting means.4.1.1 Mating force4.1.1.1 The two mating connectors shall be brought to a position where mechanical mating begins and the force or torque gage is at zero indication.4.1.1.2 The connectors shall then be fully mated or coupled at a rate of 25.4 millimeters/minute, unless otherwise specified in the referencing document, and the peak force or torque required for mating shall be recorded.4.1.2 Unmating forceThe mated connectors shall be fully unmated at a rate of 25.4 millimeters/minute, unless otherwise specified in the referencing document, and the peak force or torque required shall be recorded. 4.2 Method BThe fixtures required to hold the specimen and the specimen shall be attached to the force measuring system then the system shall be zeroed.4.2.1 Mating force4.2.1.1 The two mating components shall be brought to a position just before mechanical mating begins and the force measuring system is indicating zero.4.2.1.2 The gage/device shall then be fully mated to the connector/socket at a rate of 25.4 millimeters/minute, unless otherwise specified in the referencing document. The peak force required for mating prior to bottoming shall be recorded.4.2.2 Unmating forcesThe gage/device shall then be fully unmated from the connector/socket at a rate of 25.4 millimeters/minute unless otherwise specified in the referencing document. The peak force required for unmating shall be recorded.5 Details to be specifiedThe following details shall be specified in the referencing document:5.1 Number of specimens to be tested5.2 Measurements to be made; mating force, unmating force, or both5.3 Rates of mating and unmating, if other than specified in 4.1.1.2, 4.1.2, 4.2.1.2 and 4.2.25.4 Depth of mating if applicable5.5 Lubrication or cleaning, if required5.6 Wire type, gage, and length if applicable5.7 Applicable hardware5.8 Force or torque requirements5.9 Test conditions, if other than standard atmospheric5.10 Applicable to method B only: Details of the device(s) or gage(s) to be used for mating/unmating to the connector/socket, as well as the method and frequency of cleaning, if required6 Test documentationDocumentation shall contain the details specified in clause 5, with any exceptions, and the following:6.1 Title of test6.2Specimen description including part number if applicable6.3 If applicable, fixturing, gage details and gage part number6.4 Test equipment used, and date of last and next calibration6.5 Test procedure and method, if other than method A6.6 Values and observation6.7 Name of operator and date of testEIA Document Improvement ProposalIf in the review or use of this document, a potential change is made evident for safety, health or technical reasons, please fill in the appropriate information below and mail or FAX to:Electronic Industries AllianceTechnology Strategy & Standards Department – Publications Office2500 Wilson Blvd.Arlington, VA 22201FAX: (703-875-8906)Revision HistoryRevision letter Projectnumber Additions, changes and deletionsC SP-5136Original test procedure is now method A.Added Method B and paragraph 2.1.4, 3.2, 4.2, 5.10and 6.3.Revised paragraph 1.1, 4.1.1.2, 4.1.2, 5.2, 5.3, 6.2and 6.5.。
Agilent E364xA Series程序可调DC电源数据手册说明书

5061-9694AgilentE3640A – E3649A Programmable DC Power SuppliesData SheetReliable Power, Repeatable Results Single and dual outputs Dual range output30 W to 100 W output power Front and rear output terminals Over-voltage protection Remote SensingGPIB and RS-232 standard Save and recall functionsGreat Performance, Outstanding PriceWith the output power of 30 to 100 W, the Agilent E364xA Series programmable DC power supplies provide great performance at a great price. All ten models deliver clean power, excellent regulation, fast transient response and built-in GPIB and RS-232 interfaces. They are designed to meet the needs of R&D design verifi cation, production testing, QA verifi cations, and other demanding applications with AgilentTechnologies’s quality and reliability.Steady OutputWith 0.01 percent load and line regulation, Agilent E364xA power supplies are able to maintain a steady output when power line and load changes occur. They also specify normal mode voltage noise and low common mode current noise. The low normal mode noise specifi cation assures clean power for precision circuitry applications, and the low common mode current provides isolation from power line current injection. Agilent E364xA power supplies specify less than 90 msec of voltage settling time at any output load condition.••••••••Remote InterfaceAgilent E364xA power suppliessupport any PC with a GPIB (IEEE-488) card or RS-232 interface. Every model ships standard with both GPIB and RS-232. The easy-to-use SCPI (Standard Commands forProgrammable Instruments) allow fast and simple programming procedures. Besides, the user manual provides suffi cient information on programming for all end users, from beginners to veterans.Broad Support VXI plug and play software drivers are available for Agilent VEE, National Instruments LabView TMand LabWindows TM . With these drivers, integration of the E364xA into your system can never be any easier. The drivers are supported under Microsoft ®Windows 98® and NT ®.Front Panel OperationAn easy-to-use rotary knob and self-guiding keypads allow you to set theoutput at your desired resolutionwithout any effort. Also, both voltageand current levels can be set to amaximum resolution of 10 mV/1 mAfrom the front panel. In addition, youcan store and recall for up to fi vecomplete power supply setups usingthe internal non-volatile memory.The output on/off button sets the output to zero. If you own a dual output model, you can view twovoltages or currents that are displayed simultaneously.Versatile PowerAgilent E364xA power supplies give you the fl exibility to select from dual output ranges. Output load isprotected against overvoltage, which can be easily monitored and adjusted from the front panel and remoteinterface. Remote sensing is availablein the rear terminal to eliminate errors caused by voltage drops on the load leads. These power supplies offer newversatile binding posts on the front panel and screw-type terminals on the rear panel. New front panel binding posts allow you to use safety testleads as well as conventional banana clips and stripped wires. An optionalrackmount kit is available. The Agilent E364xA Series employs a cooling fan with automatic speed control to reduce the acoustic noise. LabView and LabWindows are registered trademarks of National Instruments.Microsoft Windows 98 and Windows NT are US registered trademerks of Microsoft Corporation.Highly visible vacuumfl ourescent displaySelectable dual rangeprovides fl exibilityand convenienceElectronic calibration from the front panel Rotary knob for quick and analog-like control of voltage and current Tough handle for easy carriage and unitprop-upVersatile binding posts offer fl exibility to use safety test leads, banana plugs or stripped wires1 year warranty protects your investmentBuilt-in GPIB and RS-232 interfaces Cooling fan with automatic speed control for low acoustic noise Rear output and sensing terminalsStore and recall up to fi ve different operating statuses in non- volatile storage locations Set the overvoltage protection and enable the overvoltage protection circuitAgilent E3640A – E3649A Programmable DC Power Supply Specifi cationsModel Number E3640A E3641A E3642A E3643A E3644A E3645A Maximum Power30 W50 W80 W# of Outputs111111DC Output Rating (@ 0 ºC to 40 ºC)0 to 8 V/3 A or0 to 20 V/1.5 A0 to 35 V/0.8 A or0 to 60 V/0.5 A0 to 8 V/5 A or0 to 20 V/2.5 A0 to 35 V/1.4 A or0 to 60 V/0.8 A0 to 8 V/8 A or0 to 20 V/4 A0 to 35 V/2.2 A or0 to 60 V/1.3 ANet Weight 5.3 kg 5.2 kg 6.3 kg 6.2 kg 6.6 kg 6.7 kg Dimensions (without bumper)212.6 mm W x 88.5 mm H x 348.3 mm DModel Number E3646A E3647A E3648A E3649A Maximum Power60 W100 W# of Outputs2222DC Output Rating (@ 0 ºC to 40 ºC)Two0 to 8 V/3 A or0 to 20 V/1.5 ATwo0 to 35 V/0.8 A or0 to 60 V/0.5 ATwo0 to 8 V/5 A or0 to 20 V/2.5 ATwo0 to 35 V/1.4 A or0 to 60 V/0.8 ANet Weight8.2 kg8.0 kg9.2 kg9.1 kg Dimensions (without bumper)212.8 mm W x 133.0 mm H x 348.3 mm DLoad and Line Regulation ± (% of output + offset)Voltage< 0.01% + 3 mVCurrent< 0.01% + 250 µARipple and Noise (20 Hz to 20 MHz)Normal Mode Voltage< 5 mVpp/0.5 mVrms for 8 V/20 V models< 8 mVpp/1 mVrms for 35 V/60 V modelsNormal Mode Current< 4 mArmsCommon Mode Current< 1.5 µArmsAccuracy1 12 Months (@ 25 ºC ± 5 ºC), ± (% output + offset)ProgrammingVoltage< 0.05% + 10 mV (< 0.1% + 25 mV for output 2 of E3646/47/48/49 A)Current< 0.2% + 10 mAReadbackVoltage< 0.05% + 5 mV (< 0.1% + 25 mV for output 2 of E3646/47/48/49 A)Current< 0.15% + 5 mA (< 0.15% + 10 mA for output 2 of E3646/47/48/49 A)ResolutionProgram< 5 mV/1 mAReadback< 2 mV/1 mAMeter10 mV/1 mATransient Response Less than 50 µsec for output to recover to within 15 mV following a change in output current from full load to halfload or vice versa.Settling Time2< 90 msecOVPAccuracy,± (% output + offset) Activation Time3< 0.5% + 0.5 V< 1.5 msec, OVP ≥ 3 V/< 10 msec, OVP < 3 VTemperature Coeffi cient per ºC ± (% output + offset)Voltage< 0.01% + 3 mV (< 0.02% + 5 mV for output 2 of E3646/47/48/49A)Current< 0.02% + 3 mA1 Accuracy specifi cations are valid after a 1-hour warm-up with no load and calibration at 25 ºC.2 Maximum time required for the output voltage to change from 1% to 99% or vice versa following the receipt of VOLT age or APPLy command via direct GPIB or RS-232 interface.3 Average time for output to start and drop after an OVP condition occurred.Stability, constant load & temperature ± (% output + offset), 8 hrsVoltage< 0.02% + 2 mVCurrent< 0.1% + 1 mARemote SensingMax. voltage drop in each load lead1 VAC Input(47 Hz – 63 Hz)100 Vac ± 10% (Opt 0E9)/115 Vac ± 10% (Std)/230 Vac ± 10% (0E3) Warranty 1 yearProduct Regulation Designed to comply with UL3111-1; certifi ed to CSA 22.2 No. 1010.1;conforms to IEC 1010-1; complies with EMC directive 89/336/EEC (Group 1, Class A)Agilent E364xA Series Power Supplies E3640A 30-Watt Single Power Supply E3641A 30-Watt Single Power Supply E3642A 50-Watt Single Power Supply E3643A 50-Watt Single Power Supply E3644A 80-Watt Single Power Supply E3645A 80-Watt Single Power Supply E3646A 60-Watt Dual Power Supply E3647A 60-Watt Dual Power Supply E3648A 100-Watt Dual Power Supply E3649A 100-Watt Dual Power Supply Accessories IncludedUser’s Guide, Quick Reference Guide and AC power cordPower OptionsOpt. 0E3 230 Vac ± 10%Opt. 0EM 1150 Vac ± 10%Opt. 0E9 100 Vac ± 10%Other OptionsOpt. 1CM Rackmount kit*– Single Output (P/N 5063-9240)– Dual Output (P/N 5063-9243) Opt. 0L2 Extra ManualOpt. UK6 Commercial calibration with test result dataE3600A-100 Test lead kit Rackmount Kits*Agilent E3640A/41A/42A/43A/44A/45A To rackmount two instruments side-by-side Lock-link Kit (P/N 5061-9694)Flange Kit (P/N 5063-9212)To rackmount one or two instruments in a sliding support shelfSupport Shelf (P/N 5063-9255)Slide Kit (P/N 1494-0015) required for support shelfFor a single instrument, also orderFilter Panel (P/N 5002-3999)Agilent E3646A/47A/48A/49ATo rackmount two instruments side-by-side Lock-link Kit (P/N 5061-9694)Flange Kit (P/N 5063-9214)To rackmount two instruments in a sliding support shelfSupport Shelf (P/N 5063-9256)Silde Kit (P/N 1494-0015)* Rackmounting with 1CM or lock-link/fl ange kit requiresAgilent or customer support railsAgilent Support Rails-E3663ACRemove all doubtOur repair and calibration services will get yourequipment back to you, performing like new, when promised. You will get full value out of your Agilent equipment throughout its lifetime. Your equipment will be serviced by Agilent-trained technicians using the latest factory calibration procedures, automated repair diagnostics and genuine parts. You will always have the utmost confi dence in your measurements.Agilent offers a wide range of additional expert test and measurement services for your equip-ment, including initial start-up assistance onsite education and training, as well as design, system integration, and project management.For more information on repair and calibration services, go to/find/removealldoubt/fi nd/emailupdatesGet the latest information on the products and applica-tions you select./fi nd/agilentdirectQuickly choose and use your test equipment solutions with confi dence./fi nd/openAgilent Open simplifi es the process of connecting and programming test systems to help engineers design, validate and manufacture electronic products. Agilent offers open connectivity for a broad range of system-ready instruments, open industry software, PC-standard I/O and global support, which are combined to more easily integrate test system development.is the US registered trademark of the LXI Consortium.Agilent Email UpdatesAgilent DirectAgilent OpenFor more information on Agilent Technologies’products, applications or services, please contact your local Agilent office. The complete list is available at:/find/contactus Phone or Fax United States:(tel) 800 829 4444(fax) 800 829 4433Canada:(tel) 877 894 4414(fax) 800 746 4866China:(tel) 800 810 0189(fax) 800 820 2816Europe:(tel) 31 20 547 2111Japan:(tel) (81) 426 56 7832(fax) (81) 426 56 7840Korea:(tel) (080) 769 0800(fax) (080) 769 0900Latin America:(tel) (305) 269 7500Taiwan:(tel) 0800 047 866 (fax) 0800 286 331Other Asia Pacifi c Countries:(tel) (65) 6375 8100 (fax) (65) 6755 0042Email:*****************Revised: 1⅛ /06Product specifi cations and descriptions in this document subject to change without notice.© Agilent Technologies, Inc. 2002-2007Printed in USA, October 26, 20075968-7355EN5061-9694。
RJ45连接器(MODULAR JACK)产品规格书 -精华
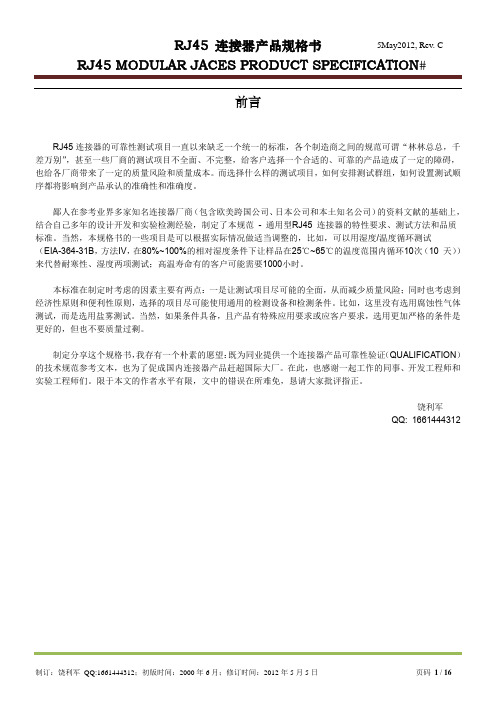
3.2 材料规格 Material Specification
3.2.1 塑胶主体 Housing :热塑性材料,阻燃等级 UL94V-0, Thermo-plastic, UL94V-0.
塑胶盖子 Cover : 热塑性材料,阻燃等级 UL94V-0, Thermo-plastic, UL94V-0.
RJ45 连接器产品规格书
5May2012, Rev. C
RJ45 MODULAR JACES PRODUCT SPECIFICATION
前言
RJ45 连接器的可靠性测试项目一直以来缺乏一个统一的标准,各个制造商之间的规范可谓“林林总总,千 差万别”,甚至一些厂商的测试项目不全面、不完整,给客户选择一个合适的、可靠的产品造成了一定的障碍, 也给各厂商带来了一定的质量风险和质量成本。而选择什么样的测试项目,如何安排测试群组,如何设置测试顺 序都将影响到产品承认的准确性和准确度。
制订:饶利军 QQ:1661444312;初版时间:2000 年 6 月;修订时间:2012 年 5 月 5 日
页码 1 / 16
RJ45 连接器产品规格书
5May2012, Rev. C
RJ45 MODULAR JACES PRODUCT SPECIFICATION
RJ45 连接器产品规格书
RJ45 MODULAR JACES PRODUCT SPECIFICATION
EIA-364-91A DUST

Test resources ...........................................................................................................
EIA
STANDARD
TP-91A
DUST TEST PROCEDURE FOR
ELECTRICAL CONNECTORS AND
SOCKETS
EIA/ECA-364-91A
(Revision of EIA-364-91)
APRIቤተ መጻሕፍቲ ባይዱ 2005
ELECTRONIC COMPONENTS, ASSEMBLIES & MATERIALS
misunderstandings between manufacturers and purchasers, facilitating interchangeability and improvement of
products, and assisting the purchaser in selecting and obtaining with minimum delay the proper product for his
Dust composition (normative) ..................................................................................