Aspen吸收塔的设计
吸收解吸塔地详细设计和ASPEN塔设计

课程设计任务书学生姓名:专业班级:指导教师:工作部门:一、课程设计题目填料吸收塔的设计二、工艺条件1.煤气中含苯 2%(摩尔分数),煤气分子量为 19;2.生产能力:每小时处理含苯煤气2000m³,连续操作;3.吸收塔底溶液含苯≥0.15%(质量分数);4.吸收回收率≥95%;5.吸收剂为洗油:分子量 260,相对密度 0.8;6.吸收操作条件为:1atm、27℃;解吸操作条件为:1atm、120℃;7.冷却水进口温度<25℃,出口温度≤50℃。
8.吸收塔汽-液平衡 y* = 0.125x;解吸塔汽-液平衡为 y* = 3.16x;9.解吸气流为过热水蒸气,经解吸后的液体直接用作吸收剂,正常操作下不再补充新鲜吸收剂过程中热效应忽略不计;10.年工作日及填料类型:自选。
三、课程设计内容1.设计方案的选择及流程说明;2.工艺计算;3.主要设备工艺尺寸设计;(1)塔径的确定;(2)填料层高度计算;(3)总塔高、总压降及接管尺寸的确定。
4.辅助设备选型与计算。
四、进度安排1.课程设计准备阶段:收集查阅资料,并借阅相关工程设计用书;2.设计分析讨论阶段:确定设计思路,正确选用设计参数,树立工程观点,小组分工协作,较好完成设计任务;3.计算设计阶段:完成物料衡算、流体力学性能验算及主要设备的工艺设计计算;4.课程设计说明书编写阶段:整理文字资料计计算数据,用简洁的文字和适当的图表表达自己的设计思想及设计成果。
五、基本要求1.格式规范,文字排版正确;2.主要设备的工艺设计计算需包含:物料衡算,能量衡量,工艺参数的选定,设备的结构设计和工艺尺寸的设计计算;3.工艺流程图:以 3 号图纸用单线图的形式绘制,标出主体设备与辅助设备的物料方向,物流量、能流量,主要测量点;4.填料塔工艺条件图:以 2 号图纸绘制,图面应包括设备的主要工艺尺寸,技术特性表和接管表;5.按时完成课程设计任务,上交完整的设计说明书一份。
ASPEN-0-9-ASPEN_吸收稳定
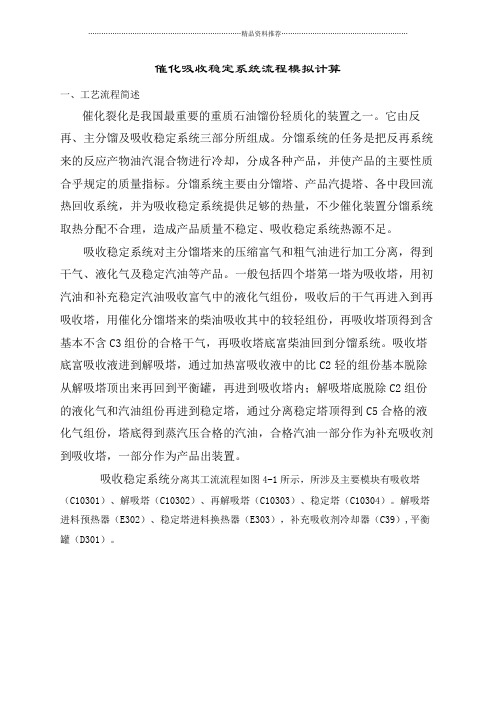
……………………………………………………………精品资料推荐…………………………………………………催化吸收稳定系统流程模拟计算一、工艺流程简述催化裂化是我国最重要的重质石油馏份轻质化的装置之一。
它由反再、主分馏及吸收稳定系统三部分所组成。
分馏系统的任务是把反再系统来的反应产物油汽混合物进行冷却,分成各种产品,并使产品的主要性质合乎规定的质量指标。
分馏系统主要由分馏塔、产品汽提塔、各中段回流热回收系统,并为吸收稳定系统提供足够的热量,不少催化装置分馏系统取热分配不合理,造成产品质量不稳定、吸收稳定系统热源不足。
吸收稳定系统对主分馏塔来的压缩富气和粗气油进行加工分离,得到干气、液化气及稳定汽油等产品。
一般包括四个塔第一塔为吸收塔,用初汽油和补充稳定汽油吸收富气中的液化气组份,吸收后的干气再进入到再吸收塔,用催化分馏塔来的柴油吸收其中的较轻组份,再吸收塔顶得到含基本不含C3组份的合格干气,再吸收塔底富柴油回到分馏系统。
吸收塔底富吸收液进到解吸塔,通过加热富吸收液中的比C2轻的组份基本脱除从解吸塔顶出来再回到平衡罐,再进到吸收塔内;解吸塔底脱除C2组份的液化气和汽油组份再进到稳定塔,通过分离稳定塔顶得到C5合格的液化气组份,塔底得到蒸汽压合格的汽油,合格汽油一部分作为补充吸收剂到吸收塔,一部分作为产品出装置。
吸收稳定系统分离其工流流程如图4-1所示,所涉及主要模块有吸收塔(C10301)、解吸塔(C10302)、再解吸塔(C10303)、稳定塔(C10304)。
解吸塔进料预热器(E302)、稳定塔进料换热器(E303),补充吸收剂冷却器(C39),平衡罐(D301)。
图4-1 催化吸收稳定系统模拟计算流程图GGGAS干气; LLPG液化气; GGOIL稳定汽油;PCOIL贫柴油;PGAS干气;FCOIL富柴油;二汽油;LPG液化气;WDGOIL5稳定汽油产品;D301平衡罐;C10301吸收塔,C10302解吸塔,C10303再吸收塔,C10304稳定塔二、需要输入的主要参数1、装置进料数据2、单元操作参数3、设计规定……………………………………………………………精品资料推荐…………………………………………………4、灵敏度分析的应用应用方案研究功能研究,考察贫汽油流量、贫柴油流量对贫气中C3含量、液化气中C2含量的影响。
吸收塔自动控制工艺设计
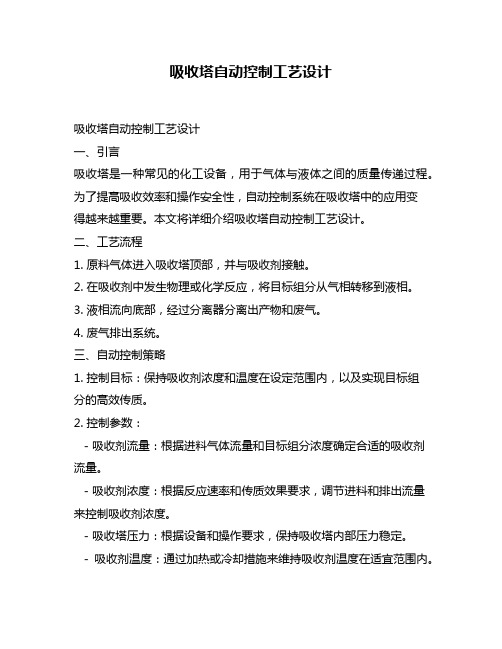
吸收塔自动控制工艺设计吸收塔自动控制工艺设计一、引言吸收塔是一种常见的化工设备,用于气体与液体之间的质量传递过程。
为了提高吸收效率和操作安全性,自动控制系统在吸收塔中的应用变得越来越重要。
本文将详细介绍吸收塔自动控制工艺设计。
二、工艺流程1. 原料气体进入吸收塔顶部,并与吸收剂接触。
2. 在吸收剂中发生物理或化学反应,将目标组分从气相转移到液相。
3. 液相流向底部,经过分离器分离出产物和废气。
4. 废气排出系统。
三、自动控制策略1. 控制目标:保持吸收剂浓度和温度在设定范围内,以及实现目标组分的高效传质。
2. 控制参数:- 吸收剂流量:根据进料气体流量和目标组分浓度确定合适的吸收剂流量。
- 吸收剂浓度:根据反应速率和传质效果要求,调节进料和排出流量来控制吸收剂浓度。
- 吸收塔压力:根据设备和操作要求,保持吸收塔内部压力稳定。
- 吸收剂温度:通过加热或冷却措施来维持吸收剂温度在适宜范围内。
- 废气排放浓度:根据环保要求,控制废气中目标组分的浓度。
四、自动控制系统1. 测量与传感器:- 气体流量计:用于测量进料气体流量。
- 液位计:用于监测吸收剂液位,以调节进料和排出流量。
- 温度传感器:用于测量吸收塔内部的温度变化。
- 压力传感器:用于监测吸收塔内部的压力变化。
2. 控制器:- 流量控制器:根据进料气体流量和目标组分浓度设定值,调节吸收剂流量控制阀的开度。
- 液位控制器:根据吸收剂液位设定值,通过调节进料和排出流量控制阀来维持液位平衡。
- 温度控制器:根据吸收剂温度设定值,控制加热或冷却设备的操作。
- 压力控制器:根据吸收塔压力设定值,调节进料和排出流量控制阀的开度。
- 废气排放控制器:根据废气中目标组分浓度设定值,调节废气排放系统的操作。
3. 执行器:- 流量控制阀:根据流量控制器的信号,调节吸收剂流量。
- 液位控制阀:根据液位控制器的信号,调节进料和排出流量。
- 加热或冷却设备:根据温度控制器的信号,进行加热或冷却操作。
吸收塔的设计选型和计算
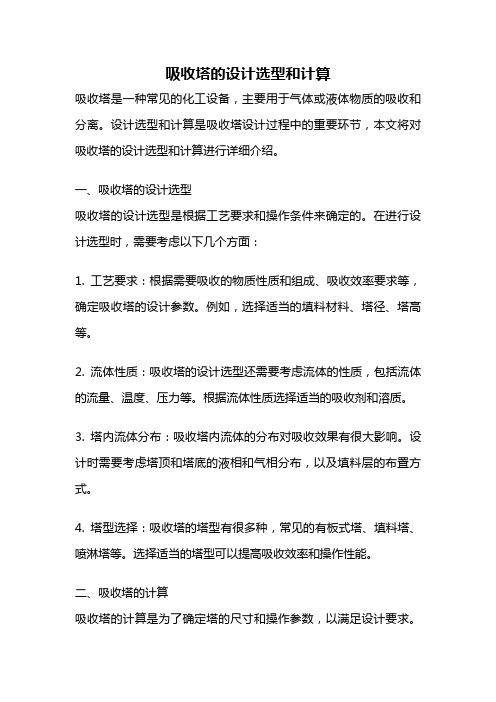
吸收塔的设计选型和计算吸收塔是一种常见的化工设备,主要用于气体或液体物质的吸收和分离。
设计选型和计算是吸收塔设计过程中的重要环节,本文将对吸收塔的设计选型和计算进行详细介绍。
一、吸收塔的设计选型吸收塔的设计选型是根据工艺要求和操作条件来确定的。
在进行设计选型时,需要考虑以下几个方面:1. 工艺要求:根据需要吸收的物质性质和组成、吸收效率要求等,确定吸收塔的设计参数。
例如,选择适当的填料材料、塔径、塔高等。
2. 流体性质:吸收塔的设计选型还需要考虑流体的性质,包括流体的流量、温度、压力等。
根据流体性质选择适当的吸收剂和溶质。
3. 塔内流体分布:吸收塔内流体的分布对吸收效果有很大影响。
设计时需要考虑塔顶和塔底的液相和气相分布,以及填料层的布置方式。
4. 塔型选择:吸收塔的塔型有很多种,常见的有板式塔、填料塔、喷淋塔等。
选择适当的塔型可以提高吸收效率和操作性能。
二、吸收塔的计算吸收塔的计算是为了确定塔的尺寸和操作参数,以满足设计要求。
吸收塔的计算主要包括以下几个方面:1. 塔径计算:根据流体的流量和操作要求,计算出吸收塔的塔径。
塔径的大小直接影响到液相和气相的接触效果和传质速率。
2. 塔高计算:根据吸收效率、塔径和填料性能等因素,计算出吸收塔的塔高。
塔高的大小决定了流体在塔内停留的时间,对传质效果有重要影响。
3. 填料计算:选择合适的填料材料,并根据填料的性能参数,计算填料层的高度和填料比表面积。
填料的选择和布置对吸收效果有重要影响。
4. 液相和气相流速计算:根据液相和气相的流量和流速要求,计算出液相和气相的流速。
流速的大小会影响到液相和气相的接触程度和传质速率。
5. 塔内压降计算:根据流体的性质和操作要求,计算出吸收塔的压降。
压降的大小对塔的能耗和操作费用有影响。
吸收塔的设计选型和计算是一项复杂而关键的工作,需要综合考虑多个因素。
合理的设计选型和计算可以提高吸收塔的吸收效率和操作性能,降低能耗和成本。
Aspen 模拟塔设计
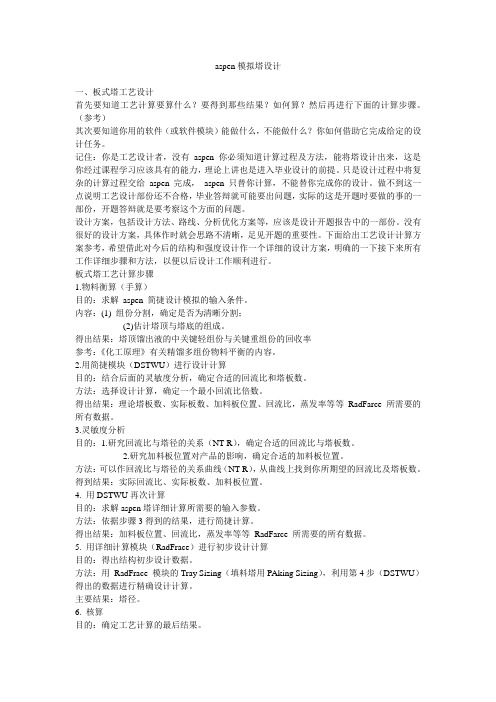
aspen模拟塔设计一、板式塔工艺设计首先要知道工艺计算要算什么?要得到那些结果?如何算?然后再进行下面的计算步骤。
(参考)其次要知道你用的软件(或软件模块)能做什么,不能做什么?你如何借助它完成给定的设计任务。
记住:你是工艺设计者,没有aspen 你必须知道计算过程及方法,能将塔设计出来,这是你经过课程学习应该具有的能力,理论上讲也是进入毕业设计的前提。
只是设计过程中将复杂的计算过程交给aspen 完成,aspen 只替你计算,不能替你完成你的设计。
做不到这一点说明工艺设计部份还不合格,毕业答辩就可能要出问题,实际的这是开题时要做的事的一部份,开题答辩就是要考察这个方面的问题。
设计方案,包括设计方法、路线、分析优化方案等,应该是设计开题报告中的一部份。
没有很好的设计方案,具体作时就会思路不清晰,足见开题的重要性。
下面给出工艺设计计算方案参考,希望借此对今后的结构和强度设计作一个详细的设计方案,明确的一下接下来所有工作详细步骤和方法,以便以后设计工作顺利进行。
板式塔工艺计算步骤1.物料衡算(手算)目的:求解aspen 简捷设计模拟的输入条件。
内容:(1) 组份分割,确定是否为清晰分割;(2)估计塔顶与塔底的组成。
得出结果:塔顶馏出液的中关键轻组份与关键重组份的回收率参考:《化工原理》有关精馏多组份物料平衡的内容。
2.用简捷模块(DSTWU)进行设计计算目的:结合后面的灵敏度分析,确定合适的回流比和塔板数。
方法:选择设计计算,确定一个最小回流比倍数。
得出结果:理论塔板数、实际板数、加料板位置、回流比,蒸发率等等RadFarce 所需要的所有数据。
3.灵敏度分析目的:1.研究回流比与塔径的关系(NT-R),确定合适的回流比与塔板数。
2.研究加料板位置对产品的影响,确定合适的加料板位置。
方法:可以作回流比与塔径的关系曲线(NT-R),从曲线上找到你所期望的回流比及塔板数。
得到结果:实际回流比、实际板数、加料板位置。
AspenPlus吸收单元设计过程例题

AspenPlus软件的吸收单元设计过程这个手册描述了使用AspenPlus软件设计一个吸收器必需的所有步骤。
这个手册同时包括设计过程中的使用技巧、劝告(建议)和注释说明。
例子如下:例1问题描述:填料塔的丙酮吸收在293K和101.32kPa(1atm)下,用水吸收丙酮,填料塔直径0.4866m,进料空气含有2.6mol%丙酮,气体出口含丙酮0.5mol%。
总的气体进料流速为14.0148kmol/h,纯水进料流速为45.36kmol/h。
简图如下:气体出口Xaceton=0.005纯水进口F=45.36kmol/hAbsorberT=293KP=1atm气体出口Xair=0.974 Xaceton=0.026 F=14,014kmol/h 液体出口Xaceton=0.00648过程登录到AspenPlus系统并开启一个空白模拟文件,那么就会出现一个流程图区域。
如需要帮助可参考“使用AspenPlus进行流程模拟”)上面显示的是Columns的子目录,单击“RateFrac”块就选择了这个块,如果单击“RateFrac ”块旁边的向下箭头就会跳出一系列的图标。
这些图标都表示相同的计算程序, 仅仅是概略简图不同而已,从中可以选择最能描述你设计的过程的块。
对于这个例子选择“RATEFRAC ”左上角的矩形块。
RateFrac 是模拟诸如吸收、气提和精馏等所有类型的多级汽液分离过程的速率型非平衡级模型。
RateFrac 模拟实际板式塔和填料塔,而不是理想化的平衡级。
一个塔有很多段组成(见右边的填料塔示意图)这些段指的是填料塔 的一部分填料或者板式塔的一块或几块塔板。
RateFrac 执行一个把所 有的段看作平衡级模型的初始化计算,用这个初始化计算的接过去计 算速率型非平衡级模型。
需要学习有关RateFrac 的更多知识和应用请 参考“RateFrac ”的帮助。
首先,使用“RateFrac ”块创建如上所示的示意图,如果需要帮助请参考“使用AspenPlus 进行流程模拟”。
Aspen吸收塔的设计
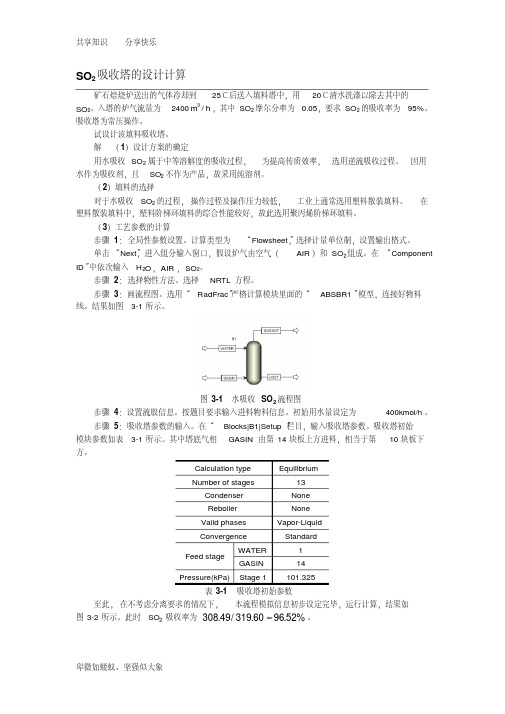
SO 2吸收塔的设计计算矿石焙烧炉送出的气体冷却到25℃后送入填料塔中,用20℃清水洗涤以除去其中的SO 2。
入塔的炉气流量为2400h m /3,其中SO 2摩尔分率为0.05,要求SO 2的吸收率为95%。
吸收塔为常压操作。
试设计该填料吸收塔。
解(1)设计方案的确定用水吸收SO 2属于中等溶解度的吸收过程,为提高传质效率,选用逆流吸收过程。
因用水作为吸收剂,且SO 2不作为产品,故采用纯溶剂。
(2)填料的选择对于水吸收SO 2的过程,操作过程及操作压力较低,工业上通常选用塑料散装填料。
在塑料散装填料中,塑料阶梯环填料的综合性能较好,故此选用聚丙烯阶梯环填料。
(3)工艺参数的计算步骤1:全局性参数设置。
计算类型为“Flowsheet ”,选择计量单位制,设置输出格式。
单击“Next ”,进入组分输入窗口,假设炉气由空气(AIR )和SO 2组成。
在“ComponentID ”中依次输入H 2O ,AIR ,SO 2。
步骤2:选择物性方法。
选择NRTL 方程。
步骤3:画流程图。
选用“RadFrac ”严格计算模块里面的“ABSBR1”模型,连接好物料线。
结果如图3-1所示。
图3-1 水吸收SO 2流程图步骤4:设置流股信息。
按题目要求输入进料物料信息。
初始用水量设定为400kmol/h 。
步骤5:吸收塔参数的输入。
在“Blocks|B1|Setup ”栏目,输入吸收塔参数。
吸收塔初始模块参数如表3-1所示。
其中塔底气相GASIN 由第14块板上方进料,相当于第10块板下方。
Calculation type EquilibriumNumber of stages13 Condenser None Reboiler None Valid phases Vapor-Liquid Convergence StandardFeed stageWATER 1 GASIN14 Pressure(kPa) Stage 1101.325表3-1 吸收塔初始参数至此,在不考虑分离要求的情况下,本流程模拟信息初步设定完毕,运行计算,结果如图3-2所示。
aspen催化吸收稳定系统流程模拟计算

催化吸收稳定系统流程模拟计算一、工艺流程简述催化裂化是我国最重要的重质石油馏份轻质化的装置之一。
它由反再、主分馏及吸收稳定系统三部分所组成。
分馏系统的任务是把反再系统来的反应产物油汽混合物进行冷却,分成各种产品,并使产品的主要性质合乎规定的质量指标。
分馏系统主要由分馏塔、产品汽提塔、各中段回流热回收系统,并为吸收稳定系统提供足够的热量,不少催化装置分馏系统取热分配不合理,造成产品质量不稳定、吸收稳定系统热源不足。
吸收稳定系统对主分馏塔来的压缩富气和粗气油进行加工分离,得到干气、液化气及稳定汽油等产品。
一般包括四个塔第一塔为吸收塔,用初汽油和补充稳定汽油吸收富气中的液化气组份,吸收后的干气再进入到再吸收塔,用催化分馏塔来的柴油吸收其中的较轻组份,再吸收塔顶得到含基本不含C3组份的合格干气,再吸收塔底富柴油回到分馏系统。
吸收塔底富吸收液进到解吸塔,通过加热富吸收液中的比C2轻的组份基本脱除从解吸塔顶出来再回到平衡罐,再进到吸收塔内;解吸塔底脱除C2组份的液化气和汽油组份再进到稳定塔,通过分离稳定塔顶得到C5合格的液化气组份,塔底得到蒸汽压合格的汽油,合格汽油一部分作为补充吸收剂到吸收塔,一部分作为产品出装置。
吸收稳定系统分离其工流流程如图4-1所示,所涉及主要模块有吸收塔(C10301)、解吸塔(C10302)、再解吸塔(C10303)、稳定塔(C10304)。
解吸塔进料预热器(E302)、稳定塔进料换热器(E303),补充吸收剂冷却器(C39),平衡罐(D301)。
图4-1 催化吸收稳定系统模拟计算流程图GGGAS干气; LLPG液化气; GGOIL稳定汽油;PCOIL贫柴油;PGAS干气;FCOIL富柴油;二汽油;LPG液化气;WDGOIL5稳定汽油产品;D301平衡罐;C10301吸收塔,C10302解吸塔,C10303再吸收塔,C10304稳定塔二、需要输入的主要参数1、装置进料数据2、单元操作参数3、设计规定4、灵敏度分析的应用应用方案研究功能研究,考察贫汽油流量、贫柴油流量对贫气中C3含量、液化气中C2含量的影响。
- 1、下载文档前请自行甄别文档内容的完整性,平台不提供额外的编辑、内容补充、找答案等附加服务。
- 2、"仅部分预览"的文档,不可在线预览部分如存在完整性等问题,可反馈申请退款(可完整预览的文档不适用该条件!)。
- 3、如文档侵犯您的权益,请联系客服反馈,我们会尽快为您处理(人工客服工作时间:9:00-18:30)。
SO 2吸收塔的设计计算
矿石焙烧炉送出的气体冷却到25℃后送入填料塔中,用20℃清水洗涤以除去其中的SO 2。
入塔的炉气流量为2400h m /3,其中SO 2摩尔分率为0.05,要求SO 2的吸收率为95%。
吸收塔为常压操作。
试设计该填料吸收塔。
解 (1)设计方案的确定
用水吸收SO 2属于中等溶解度的吸收过程,为提高传质效率,选用逆流吸收过程。
因用水作为吸收剂,且SO 2不作为产品,故采用纯溶剂。
(2)填料的选择
对于水吸收SO 2的过程,操作过程及操作压力较低,工业上通常选用塑料散装填料。
在塑料散装填料中,塑料阶梯环填料的综合性能较好,故此选用聚丙烯阶梯环填料。
(3)工艺参数的计算
步骤1:全局性参数设置。
计算类型为“Flowsheet”,选择计量单位制,设置输出格式。
单击“Next”,进入组分输入窗口,假设炉气由空气(AIR )和SO 2组成。
在“Component ID”中依次输入H 2O ,AIR ,SO 2。
步骤2:选择物性方法。
选择NRTL 方程。
步骤3:画流程图。
选用“R adFrac”严格计算模块里面的“ABSBR1”模型,连接好物料线。
结果如图3-1所示。
图3-1 水吸收SO 2流程图
步骤4:设置流股信息。
按题目要求输入进料物料信息。
初始用水量设定为400kmol/h 。
步骤5:吸收塔参数的输入。
在“Blocks|B1|Setup”栏目,输入吸收塔参数。
吸收塔初始模块参数如表3-1所示。
其中塔底气相GASIN 由第14块板上方进料,相当于第10块板下方。
表3-1 吸收塔初始参数
至此,在不考虑分离要求的情况下,本流程模拟信息初步设定完毕,运行计算,结果如图3-2所示。
此时SO 2 吸收率为%52.9660.319/49.308 。
图3-2 初步计算结果
步骤6:分离要求的设定,塔板数固定时,吸收剂用量的求解。
运用 “Design Specifications”功能进行计算,在“Blocks|B1|D esign Spec”下,建立分离要求“1”。
在“Blocks|B1|Design Spec|1| Specifications”页面,定义分离目标。
按题目要求进行设定。
结果如图3-3所示。
在“Blocks|B1|Design Spec|1|Components”页面,选定 “SO 2”为目标组分;在“F eed/Product Streams”页面,选择“LOUT ”为参考物流。
图3-3 Design Spec-1的定义 图3-4 Vary-1的定义
在“Blocks|B1|Vary”下,定义变量“1”。
在“Blocks|B1|Vary|1|Specifications”页面,设定进料流量“Feed rate”为变量,上下限分别为5、1000。
结果如图3-4所示。
至此,分离要求已设置完毕,运行计算,结果如图3-5所示。
当塔板数为13时,要达到95%的吸收率,需用水386.44kmol/h。
图3-5 吸收剂用量计算结果
步骤6:吸收塔的优化,吸收剂用量对塔板数灵敏度分析。
使用“Sensitivity”功能进行分析。
在“Modle Analysis Tools|Sensitivity”目录,创建一个灵敏度分析文件“S-1”。
在“S-1|Input|Define”页面,定义因变量“FLOW”,用于记录进塔水流量,结果如图3-6所示。
图3-6 定义灵敏度分析参数
在“S-1|Input|Vary”页面,设置自变量及其变化范围,这里假设塔板数变化,如图3-7所示。
在“S-1|Input|Tabulate”页面,设置输出格式。
设置“FLOW”为输出变量。
图3-7 设置自变量变化范围
本题为吸收塔,在塔板数变化的同时,塔底气体的进料位置也随之改变。
运用Calculator 功能,来实现这一过程。
在“Flowsheeting Options|Calculator”目录,创建一个计算器文件“C-1”。
在“C-1|Input|Define”页面,定义2个变量,如图3-8所示。
其中,“FEED”记录塔底气体进料位置,“NS”记录吸收塔塔板数。
图3-8 定义计算器变量
在“C-1|Input|Calculate”页面,编写塔底气体进料位置的Fortran语言计算语句,如图3-9所示。
图3-9 编写Fortran计算语句
在“C-1|Input|Se quence”页面,定义计算器计算顺序,如图3-10所示。
在塔B1前计算。
图3-10 定义计算器顺序
至此,吸收塔灵敏度分析计算所需要的信息已经全部设置完毕,运行计算,结果如图3-11、图3-12所示。
图3-12为利用Aspen内Plot功能,吸收剂用量对塔板数作图结果。
图3-11 灵敏度分析计算结果图图3-12 同塔板数所需吸收剂用量
步骤7:吸收塔的工艺参数。
由图3-12可得,当塔板数为大于10时,随着塔板数的增加,吸收剂用量减少不太明显,因此选择塔板数为10。
在“B locks|B1|Setup”栏目,将塔板数改为10,塔底气体进料位置为11,隐藏“C-1”和“S-1”,运行计算。
结果如图3-13所示。
此时,水用量为399.75kmol/h,7200kg/h。
图3-13 填料塔最终工艺计算结果
(4)填料塔设计
首先进行塔径计算。
在“B locks|B1|Pack Sizing”文件夹中,建立一个填料计算文件“1”。
在“Pack Sizing|1|Specifications”页面,填写填料位置、选用的填料型号、等板高度等信息,如图3-14所示。
其中填料为塑料阶梯环(PLASTIC CMR),等板高度设定为0.45m。
KOCH公司的塑料阶梯环,在Aspen Plus7.2数据中有三种尺寸1A,2A,3A。
由于填料尺寸越小,分离效率越高,但阻力增加,通量减少,填料费用也增多。
而大尺寸的填料应用于小直径塔中,又会产生液体分布不良及严重的壁流,使塔的分离效率降低。
因此初始选择2A型号,其湿填料因子为103.36(1/m)。
运行计算,结果如图3-15所示。
图3-14 填料塔信息设置
图3-15 填料塔计算结果
由图3-15可知,填料塔塔径为752mm,最大液相负荷分率0.62,最大负荷因子0.0537m/s,
塔压降0.0093bar,平均压降1.73mmHg/m,液体最大表观流速0.0046m/s,比表面积为164㎡/m³。
本例题填料塔初步计算塔径为752mm,此时最大负荷分率为0.62,相对保守,可以用塔径700mm进一步核核算。
在“B locks|B1|Pack Rating”文件夹下,建立一个填料核算文件“1”,在“Pack Rating|1|Specifications”页面,填写填料位置、选用的填料型号、等板高度等信息,如图3-16所示。
运行计算,结果如图3-17所示。
图3-16 填料塔核算参数设置
图3-17 填料塔核算参数设置
由图3-17可知,当填料塔塔径为0.7m,最大液相负荷分率0.716,在0.6~0.8之间,最大负荷因子0.062m/s,塔压降0.0142bar,平均压降 2.63mmHg/m,液体最大表观流速0.00535m/s。
因为一般填料塔的操作空塔气速低于泛点气速,对于一般不易发泡物系,液泛率为60%~80%,因此塔径选择0.7m是合理的。