爬壁遥控车说明书
行车遥控器说明书

厂家江苏南京陈经理135******** 152********行车遥控器说明书一、技术特征:1、行车遥控器超高频无线数字传输和工程学设计,智能化高、可靠/方便,接收可露天使用。
标准6点控制遥控装置,用于常规工况6点及以下各单速起重设备,如电动葫芦或单/双梁起重机或类似控制机电设备。
2、行车遥控器符合线控习惯。
电气接线与线控接线一致,便于有线控制改造。
遥控发射结构采用标准行车控制按钮形式,机械结构强度高、寿命长、故障率低、不易误操作。
3、发射器电池供电,低于国规安全电压(36V),有很好电气安全性,符合安全生产技术规程。
遥控发射器有工作指示和电池电压状态指示,可及时提醒当前操作状况和电池电压是否正常。
发射器待机状态下能自动断电,消除疏忽致使电池无为放电而消耗电能,避免误操作。
发射器低能耗。
行车遥控器接收提供辅助接点,可外接电铃或安全警示信号灯,改善安全生产条件,操作时,电铃或工作灯同步发出安全警示信号,提醒注意安全。
方便设备安装调试或检修遥控功能状态判断,接收内还设电源指示灯和信号接收指示灯。
二、技术参数:控制点数: n组互锁(含1个辅助控制点)启动/停机方式:接收上电默认控制箱通电待机状态发射无操作控制箱进入待机状态安全警示:电铃或警灯同步操控方式:单点动作(单向控制)/多点动作(同步)接收电压: AC220/380V/36/24/48(可选)接收控制电压范围: 380V以下各电压等级控制电流范围:≤5A传输频率: 300-450MHz数据通道跳码组合: 730组距离: 100米接收电缆接口: 12芯及以下0.75mm2 KVVR护套控制电缆防水等级IP65发射外形结构:标准QA1A环境条件:温度为-40-80℃,湿度不大于90%三、接线说明:1、以六点单速遥控器为例:接收机3组控制回路,每组2个控制点和1个公共端,每组2个控制点间互锁,控制接点(无源)适用380V以下电压等级控制回路。
2、共端跳线是对每组控制回路是否需隔离的选择。
Tenergy Spider 飞线无人遥控飞行器说明书

Instruction GuideSTUNT DRONEAges: 14+Item: 61360Keep the Instruction Guide for future reference. Do not discard.SpiderRead this disclaimer and instructions thoroughly before operating this device. THE USE OF THIS PRODUCT IS A SIGN OF YOUR COMPLIANCE WITH THIS DISCLAIMER. You are responsible for your own actions, behavior, and conduct while using this device. You agree to use this product in such a way that you will comply with all local and federal regulations, including, but not limited to, personal privacy laws. Tenergy Corporation will not be held liable for any damages or legal responsibilities resulting from the use of this product. This product is NOT suitable for anyone under the age of 14. For more information and guidance, please visit Safety guidelines for sUAS recreational users- Follow community-based safety guidelines, as developed by organizations such as the Academy of Model Aeronautics (AMA).- Fly no higher than 400 feet and remain below any surrounding obstacles when possible.- Keep your sUAS in eyesight at all times, and use an observer to assist if needed.- Remain well clear of and do not interfere with manned aircraft operations, and you must see and avoid other aircraft and obstacles at all times.- Do not intentionally fly over unprotected persons or moving vehicles, and remain at least 25 feet away from individuals and vulnerable property.- Contact the airport and control tower before flying within five miles of an airport or heliport.- Do not fly in adverse weather conditions such as in high winds or reduced visibility.- Do not fly under the influence of alcohol or drugs.- Ensure the operating environment is safe and that the operator is competent and proficient in the operation of the sUAS.- Do not fly near or over sensitive infrastructure or property such as power stations, water treatment facilities, correctional facilities, heavily traveled roadways, government facilities, etc.- Check and follow all local laws and ordinances before flying over private property.- Do not conduct surveillance or photograph persons in areas where there is an expectation of privacy without the individual’s permission (see AMA’s privacy policy).- Before each flight, check and ensure the drone and controller are not damaged, and that all components are working in accordance with the user instruction .- If you want to use unmanned aircraft systems for a commercial purpose: you can apply for an exemption from the FAA to operate commercially. For more information about how to apply for an exemption, visit the FAA’s “Section 333”.ADULT SUPERVISION REQUIREDAn adult should check the unit and LiPo battery for damages prior to each use. Drones have rotating blades that move at high speeds, posing a danger of damage and injury. Pilots are responsible for any action that results in damages or injury from improper operation of the drone. Adequate flying space is required. Avoid flying near interior fans and/or vents as they may affect your ability to control the drone. Keep a safe distance from streets, public thoroughfares, and power lines. Never attempt to retrieve the drone from any location higher than your reach (rooftops, trees, etc) or any location that poses a safety hazard. Never fly the drone at night. Keep drone in sight at all times during operation. Discontinue operation immediately if the drone flies out of your field of view. Do not fly near spectators. Keep away from pets, as they may become excited over R/C vehicles. Keep spinning rotors away from fingers, hair, eyes, and other body parts. Always launch from a flat surface. Never leave Drone unattended while it is turned on. Read all enclosed information before operating.LITHIUM BATTERY CAUTIONSLiPo batteries pose a serious hazard when used improperly and may result in overheating, fire, or explosions. Read all precautions and instructions regarding the care and use of LiPo batteries prior to use. The enclosed LiPo battery is to be used only with the vehicle and charger included in this package.- Keep away from flammable materials- Do not expose to direct sunlight- Do not expose to extreme heat- Do not drop or make subject to strong impact- Keep dry and away from moisture- Remove exhausted batteries as soon as possible and discard properly- Remove all batteries when toy is inactive for long periods- The supply terminals are not to be short circuitedLiPo Battery Disposal: LiPo batteries must be recycled and disposed of properly. LiPo batteries should not be disposed of with household waste. Check your local laws and regulations for information on proper battery disposal. If you are unable to identify the applicable rules in your area, please reference the instructions of the battery manufacturer.WARNING: Batteries are harmful if swallowed. Please keep away from children.6-axis Flight Control SystemAdvance Headless Flight Mode3D 360º Rolls2.4 Ghz RC TransmissionOne-Key Stunts: Tornado, Book flip and Triple Flips.Inverted FlightAuto ReturnFront Blades (Black)LEDMain FrameRear Blades (Red)Battery ChamberThrottle/Rudder StickMFB (Multi-Function Button)Short Press: 360°/180° Roll Switch Long Press + Direction: Tornado StuntShort Press: Auto Return (Headless Mode Only)Trimming ButtonHeadless Mode (Press Down)360°/180° Roll (Press Down +Direction)One-Key Stunt:Book FlipOne-Key Stunt:Triple FlipsPower On/OffSwitchElevator/Aileron StickCharge the battery for the drone1. Connect the battery to USB charging cable.2. Connect the USB charging cable to USB power source.3. The LED light will be on while charging, and off once charging completed.4. Insert the battery in to the battery chamber of the drone and connect the connector terminal.LED Charging Status Indicators On - Charging the battery Off - Charging completeCharging Time: approx 60min Fly Time: approx 5min per charge1. Unscrew the screws on the battery chambers behind the controller.2. Slide out the battery chamber cover.3. Insert 4 pieces of AAA batteries (2 for each side).4. Close the battery chamber, put the screw back on.After blinding, you can push the Throttle Stick up slightly to start the motors for takeoff. To land, push the Throttle Stick down slowly until the drone lands and motors stop.Basic operation:Left stick controls altitude and direction.Right stick controls the rotation forward, backward, left or right movement.360° Roll1. Bring the drone to a mid-air hover without flying towards any direction.2. While hovering, press the 360° Roll button. The remote will start beeping rapidly as the drone will enter rolling-ready mode.3. While in the rolling-ready move, tap the direction stick in the direction you want the drone to roll.While hovering, press and hold the Multi-Funtion Button (MFB), press the left stick while holding MFB:Holding MFB + Left = Counterclockwise Tornado Stunt.Holding MFB + Right = Clockwise Tornado Stunt.Backward rollRight roll1. Bring the drone to a mid-air hover without flying towards any direction.2. While hovering, short press the MFB once to switch the 360° Rolling mode to 180° Rolling mode.3. While hovering, press the 360° Roll button. The remote will start beeping rapidly as the drone will enter rolling-ready mode.4. While in the rolling-ready move, tap the direction stick inthe direction you want the drone to flip.Note:The One-Key Stunt function can not be used when:(1) Battery power is low (2) The drone is in 360° Rolling modeAuto ReturnIn headless mode, short press the Auto Return button during the flight, the drone will trace the shortest way flying back to the takeoff point.Headless ModeIn headless mode, the drone flies from your viewpoint no matter which direction the drone is flying.Eg: If you push the controller to the left the drone will fly to your left - regardless of which direction the drone is facing/pointing. In headless mode there is no need to worry about the orientation of the drone.To enter/exit headless mode:1) Before taking off, position the drone in such a way that "its front is your front".2) Press down the Headless Mode button (the Elevator/Aileron stick) to enter headless mode.3) Press the button again to get out of headless mode.Blades must be installed as shown:Front: use Black Blade A and Black Blade B Rear: use Red Blade A and Red Blade BNote:The letters A and B are printed on top side of blades.To disassemble the blade:upward.To install the blade:Match blade with the blade socket and press down.Front (Black Blades)Rear (Red Blades)BBlackABlackBRedARedGyroscope CalibrationThe built-in gyroscopic sensor measures the angular velocity and the orientation of the drone. A calibration may be necessary after shipping or a hard landing. It's a good idea to calibrate you drone if it is veering off to one side or not flying properly.Factory ResetPerforming a factory reset will reset all the current settings, including the trim and thegyroscope calibration, back to the factory settings.1. Bind the drone to the controller.2. Place drone on a flat and level surface On the controller, spin the right stick 360°, clockwise.3. All 4 LED lights on the drone will flash for a few seconds, notifying you that calibration was successful.1. Bind the drone to the controller2. Place the drone on a flat and level surface.3. Short press the trim button.4. Spin the right stick 360° clockwise5. Once complete, all settings will be factoryreset.ControllerLWH 12.7*8.9*5.7 cm / 5*3.5*2.2 inch Weight95 g / 3.4 oz Operating temperature 0°C to 40°C Control distance 50 m / 164 ftBattery4x AAA batteries (not included)DroneLWH 12.5*12.5*4 cm / 5*5*1.6 inch Weight40 g / 1.4 oz Operating Temperature 0°C to 40°C Control Distance 50 m / 164 ft Battery Capacity 380 mAhFlight Timeapprox. 5~8 minutesWhen launching the drone, face the same direction as the drone. The black blades should be in front.Practice launching, hovering, and landing before attempt to learn other moves.Flying 2 to 3 feet above the ground will reduce ground turbulence and make flying easier.When first attempting to fly in a different direction, start by tapping the Direction Stick until you get the hang of it. Always move controls slowly until you become comfortable operating the drone.Once you’ve mastered flying in different directions, practice rotational controls. Keeping the drone facing the same direction as you makes flying easier and more intuitive.Stay 2 to 3 feet away from walls and ceilings, as the drone will be drawn towards them if you fly too close.If the propeller blades come in contact with another object, or you crash, throttle down immediately to prevent further damage.If anything prevents the drone’s blades from spinning, or they become jammed, THROTTLE DOWN IMMEDIATELY. Do not attempt to fly until obstruction has been removed and damage fixed.Over time, debris such as loose hair or carpet fibers may get wound in the blades and motors. The debris should be regularly removed and cleaned to prevent buildup, and to avoid poor flying performance.。
HOBBYWING 无线遥控车型系统使用声明说明书

********USER MANUALMulti-RotorXRotor Micro 45A BLHeli_32 4in1 DShot1200Brushless Electronic Speed Controller0103Features04Specifications05User GuideThrottle Range Calibration3Once1. Power up:Once2. Throttle signal detected (arming sequence start):While measuring3. When throttle is above midstick (meauring max throttle):While measuring5. When throttle is below midstick (measuring min throttle):Once4. If throttle is above midstick for 3 seconds:This beep sequence indicates that max throttle has been storedOnce6. If throttle is below midstick for 3 seconds :This beep sequence indicates that min throttle has been storedAt this point throttle calibration values are stored. You may remove power from the ESC, or just continue running your ESC.Once7. Throttle up detected (arming sequence start):Once8. Zero throttle detected (arming sequence end):06Programming parameters07OthersNormal Start-up Process2After this, the motor will run.Definitions for Different Ports110V: 10V Power output port .(For VTx , Camera , 12V LED light and etc .)BAT: Battery Volt monitoring port with the battery voltage is to connect to the Battery Volt monitoring port on flight controller.CTR: Amp monitoring port with the amperage of 15.2mv/A is to connect to the Amp monitoring port on flight controller.GND: Ground wire ;5V: 5V Power output port . (For FC , Camera , 5V LED light and etc .)S1-4: Throttle Signal Input Ports. Port S1 is for ESC M1, S2 is for M2, S3 is for M3, and S4 is for M4.POWER INPUT:Power input soldering point , “-” for connecting the power wire - , “+” for connecting the power wire + .Although there are some protections, improper use may still cause permanent damage to the product.• Always disconnect and remove batteries after use, as the ESC may drive the motor to rotate and cause unpredictable danger if it`s still connected to the battery. Long-time contact will cause the battery to completely discharge and result in damage to the battery or/and the ESC. This will not be covered under warranty.• The open source ESC can only be flashed with the corresponding firmware (not any other firmware) when flashing or upgrading firmware, otherwise it may cause the ESC to stop working or even damage the chip inside.• This user manual is based on the operation manual for BLHeli_32 ARM rev32.x and only for reference. For more detailed information, please refer to the original BLHeli manual. Due to firmware update or other reasons, the descriptions for functions may differ, so please always take the official BLHeli manual as standard.• High performance 32-bit microprocessor with the running frequency of up to 48MHz for excellent performance. • BLHeli_32 firmware is the third generation BLHeli, following base BLHeli and BLHeli-S.• All codes use damped light mode. Damped light does regenerative braking, causing very fast motor retardation, and inherently also does active freewheeling.• The code supports features to prevent sync loss. There are tunable parameters that can make the code run well even in the most demanding situations, although default settings will work excellently in normal operating environments.• The code supports regular 1-2ms pulse width input, as well as Oneshot125 (125-250us), Oneshot42 (41.7-83.3us) and Multishot (5-25us). • Dshot signaling is supported at any rate up to at least Dshot1200. The input signal is automatically detected by the ESC upon power up.• The code also supports a beacon functionality, where the ESC will start beeping after a given time of zero throttle. This can be very useful for finding lost crafts.• On board 10V &5V BEC , powering different accessories such as FC , VTx ,Camera and LED lights and etc.1. Rampup Power:Rampup power can be set to relative values from 3% to 150%. This is the maximum power that is allowed when ramping up at low RPMs and during start-up. For low RPMs, themaximum power to the motor is limited, in order to facilitate detection of low BEMF voltages. Rampup power also affects bidirectional operation, as the parameter is used to limit the power applied during direction reversal. During startup, the actual applied power depends on throttle input, and can be lower than the maximum level set by the rampup power parameter, but the minimum level is a quarter of the maximum level.2. Temperature Protection:Temperature protection can be enabled or disabled. And the temperature threshold can be programmed. The programmable threshold is primarily meant as a support for hardware manufacturers to use, as different hardware can have different tolerances on the max temperatures of the various components used. 3. Low RPM Power Protection:Power limiting for low RPMs can be enabled or disabled. Disabling it can be necessary in order to achieve full power on some low KV motors running on a low supply voltage. However, disabling it increases the risk of sync loss, with the possibility of toasting motor or ESC. 4. Low Voltage Protection:Low voltage protection can be set between 2.5V and 4.0V per LiPo cell. Or it can be disabled. When enabled, it will limit power applied to the motor if the battery voltage drops below the programmed threshold. This feature is primarily intended for fixed wing crafts. 5. Current Protection:Current protection can be enabled to limit current. If enabled, then current will be limited to maximum the programmed value. The reaction time of the current limiting is quite fast, so current will also be limited during accelerations.The value given for current protection, is per ESC. So if setting limit to e.g. 40A for each of the ESCs in a quad (using BLHeliSuite32), then the total current limit for the four ESCs will be 160A.6. Motor Direction:Motor direction can be set to fwd / rev / bidirectional / bidirectional rev.In bidirectional mode, center throttle is zero and above is fwd rotation and below is reverse rotation. When bidirectional operation is selected, throttle calibration is disabled. 7. Demag Compensation:Demag compensation is a feature to protect from motor stalls caused by long winding demagnetization time after commutation. The typical symptom is motor stop or stutter upon quick throttle increase, particularly when running at a low RPM. As mentioned above, setting high commutation timing normally helps, but at the cost of efficiency. Demag compensation is an alternative way of combating the issue. First of all, it detects when a demag situation occurs. • In this situation, there is no info on motor timing, and commutation proceeds blindly with a predicted timing. • In addition to this, motor power is cut off some time before the next commutation.A metric is calculated that indicates how severe the demag situation is. The more severe the situation, the more power is cut off. When demag compensation is set to off, power is never cut.When setting it to low or high, power is cut. For a high setting, power is cut more aggressively. Generally, a higher value of the compensation parameter gives better protection.If demag compensation is set too high, maximum power can be somewhat reduced for some motors. 8. Motor Timing:Motor timing can be set between approximately 10 and approximately 310 in approximately 10 increments (actual accurate values here are 15/16ths of a degree).Typically a medium setting will work fine, but if the motor stutters it can be beneficial to increase timing. Some motors with high inductance can have a very long commutation demagnetization time. This can result in motor stop or stutter upon quick throttle increase, particularly when running at a low RPM. Setting timing higher will allow more time for demagnetization, and often helps.This parameter can also be set to auto. In this case the code monitors demagnetization time, and keeps timing as low as possible without having issues with demag. On well behaved motors, timing can be low in the entire power range, and thereby max power can be reduced. On not so well behaved motors, timing is increased as needed, and thereby improves margins against sync loss. 9. Maximum Acceleration:Maximum acceleration can be set between 0.1%/ms and 25.5%/ms. It can also be set to maximum, in which case acceleration is not limited. Limiting acceleration is primarily intended as a backup parameter that can be used in cases where too hard acceleration gives desyncs.When setting to e.g. 10%/ms, it means that the power applied to the motor is not allowed to increase by more than 10% per millisecond. 10. Throttle Cal Enable:If disabled, throttle calibration is disabled.11. Minimum Throttle, Maximum Throttle and Center Throttle:These settings set the throttle range of the ESC. Center throttle is only used for bidirectional operation. The values given for these settings are for a normal 1000us to 2000us input signal, and for the other input signals, the values must be scaled. For Dshot input signal, these settings have no effect. 12. Brake On Stop:Brake on stop can be set between 1% and 100%, or disabled. When not disabled, the given brake force will be applied when throttle is zero. For nonzero throttle, this setting has no effect. This feature is primarily intended for fixed wing crafts with folding props.On some ESCs this setting is not linearly programmable, it will just be enabled (at 100% force for any setting 1%-100%) or disabled (this applies to ESCs that have “EN/PWM” style fet drivers). 13. LED Control:LEDs can be controlled on ESCs that support it. Up to 4 LEDs can be turned on or off. 14. Beep Strength:Sets the strength of beeps under normal operation. 15. Beacon Strength:Sets the strength of beeps when beeping beacon beeps. The ESC will start beeping beacon beeps if the throttle signal has been zero for a given time. Note that setting a high beacon strength can cause hot motors or ESCs! 16. Beacon Delay:Beacon delay sets the delay before beacon beeping starts. 17. PWM frequency:Motor PWM frequency can be programmed between 16kHz and 48kHz. Higher PWM frequency can run motors smoother. Programmable frequency also allows for moving of small but potentially disturbing bumps in the throttle response. All ESCs have these bumps, with BLHeli_32 they can be moved in the RPM range, to a place where the system has low sensitivity to them.1. Thermal ProtectionThe ESC measures temperature within the MCU and limits motor power if the temperature is too high. Motor power is limited over a range: • If the temperature is above the threshold, motor power begins to be limited.• If the temperature is above the threshold plus approximately 150℃, motor power is limited to 25%. Motor power is not limited below 25%. 2. Stall ProtectionIf the motor has attempted to start but not succeeded for a few seconds, it will stop attempting and wait for throttle to be zeroed before attempting again. 3. Beacon---BeepsIf the ESC is armed and sees zero throttle for a given time, it beeps beacon beeps, which are approximately one beep per three seconds.4. Not activated ESC---BeepsAll ESCs shall be activated during manufacturing. If for some reason this is not done, the ESC will beep like this upon power up, before the normal operation beep sequence starts: “B, B, B… (the time interval shortens gradually)”. If for some reason activation has failed and the ESC is not regarded as a valid BLHeli_32 unit, the ESC will beep like this upon power up, before the normal operation beep sequence starts: “BBB, BBB, BBB…(the tone of the “BBB” changes from high to low)”. In this case the ESC will only accept 1-2ms pwm input signal. 5. Other Relevant InformationBLHeli official website: https:///bitdump/BLHeliBLHeli32 official documentation download website: https:///bitdump/BLHeli/tree/master/BLHeli_32%20ARM Firmware: Hobbywing_XRotor_BLHeli32...。
HOBBYWING 无线遥控车电子速控器用户手册说明书

• Built-in 5 common profiles, suitable for all 1/8 Racing, select and use instantly. (e.g. Zero timing-Blinky mode, 1/8 Off-Road Racing, 1/8 On-Road Racing, 1/8 GT Racing, 1/8 Sport mode).• There are 29 built-in adjustable parameters to set various power requirements. The parameters can be imported and exported, which is convenient for drivers to communicate with and learn from each other.• Support the firmware upgrade of the ESC (The multi-function LCD programming box G2 or OTA Programmer is needed to purchase). You can enjoy the latest functions. • Support 48 degrees Boost and Turbo timing. When matching with XERUN 4268/4274 G3 motor, the Max. Speed can be promoted by 50%, easily win your rival.• Multiple function: Low voltage protection, thermal protection of the ESC, motor and capacitor.• Built-in switch mode BEC with a maximum output of 15A and voltage adjustable from 6V to 8.4V (step: 0.1V) for usage with servos & other devices require different voltages.• The built-in reverse connection protection circuit of the ESC avoid the damage to the ESC due to reverse connection.• The record function of off-line data can read the Max. Temperature and RPM of the ESC and motor by Multifunction LCD Program Box (G2) or HW Link (OTA Programmer is needed to purchase), which is convenient for driver to analyze the running of the power system.• The record function of real-time data: Open this function by connecting the ESC with HW Link (OTA Programmer is needed to purchase) and mobile App can check throttle quantity, Voltage, Current, Temperature, RPM and other data in real time, and obtain the running status of the ESC and motor.03Features04Specifications06ESC Setup01DisclaimerPlease connect the wire correctly according to the instructions and drawing:1. Motor Wiring:There is difference between connection of sensored brushless motor and sensorless brushless motor. Please according to the following wiring method: A. Connect sensored brushless motor:There is strict wiring order from the ESC to the motor, the three A/B/C ESC wires must connect to the three A/B/C motor wires correspondingly. Next, connect the ESC sensor port and the motor sensor port with the stock 6-pin sensor cable. If you don’t plug the sensor cable in, your ESC will still work in sensorless mode even if you’re using a sensored motor. Note:If the forward and backward is reverse after installing the motor, please modify “no. 1I” parameters “Motor Rotation” to change the direction. B. Sensorless Motor Wiring:Users do not need to be worried in r egards to the connectivity with the A/B/C(ESC and motor) as ther e is no polarity. You may find it necessary to swap two wir es if the motor runs in reverse.2. Receiver Wiring:Insert the throttle control flat cable of ESC into the throttle channel (i.e. THROTTLE channel) of the receiver. Since the red line in the flat cable outputs 6-8.4v voltage to the receiver and steering servo. Please do not supply additional power to the receiver, otherwise the electric adjustment may be damaged. 3. Battery Wiring:Please make sure that the (+) pole of the ESC is connected to the (+) of the battery, and the (-) pole is connected to the (-). If connect reversely, the ESC cannot start up. (Add the picture of connecting battery here.)Warning!This is an extremely powerful system. For your safety and the safety of those around you, we strongly recommend removing the pinion gear attached to the motor before calibrating and setting this system. It is also advisable to keep the wheels in the air when you turn on the ESC.1) Illustration of power on/off: Short press the ON/OFF key to turn on the ESC in the off state, and long press the ON/OFF key to turn off the ESC.2) Beep illustration when turn on the ESC: When turn on ESC under normal conditions (i.e. it is started without pressing the SET key), the motor will emit several Beeps to indicate the LiPo cells. For example, "Beep, Beep, Beep" means 3S, "Beep, Beep, Beep, Beep" means 4S.XERUN XR8 Pro G2USER MANUALBrushless Electronic Speed Controller08Trouble ShootingIn order to make one firmware applicable to all different racing conditions, there are 5 groups of preset modes in the ESC. Users are able to change the settings of the modes provided and match suitable gear ratio. Plug-and -screw. Users can change the settings as per the control feel, track, and rename the setting mode. For example, the name can be changed from “1/8 Off-Road” to “NC2020-1900” to indicate the NC2020 uses 1900KV. This can be saved for future reference as well.Here is the method of setting parameters of ESC:1) LCD programming box set the parameters: (Please refer to the instructions of LCD programming box for detailes)parameters. You can adjust the setting via “ITEM” & “VALUE” buttons, and press the “OK(R/P)” button to save new settings to your ESC.Note: Only Multifunction LCD Program Box (G2) can work with this ESC!2) Use OTA Programmer to set parameters (Please refer to instructions of OTA Programmer for details) This ESC allows OTA Programmer connecting to the computer, that is, plug the programming wire of OTA Programmer to the programming port. Then use mobile phone to install HOBBYWING HW LINK App to set parameters.3) Data checking:recorded data to the designated area when you turn off the ESC after a run. You can check those data via a multifunction LCD program box whenever necessary. Users need to switch on the ESC after connection between the program box and the ESC has been established. Long Press the “OK(R/P)” button on any “item” page, followed by pressing the “ITEM” button again multiple times. The following 5 item pages will be displayed : Mode → ESC Temperature → Motor Temperature → Min Voltage → Max RPM. Attention!Press the “VALUE+/-” button on any profile page can get you into the next/prev preset mode. Please note that improper operation will get you into other preset mode(s).Here is the method of restore factory reset:1)Restore the default values with a multifunction LCD program boxAfter connecting the program box to the ESC, continue to press the “ITEM” button on the program box until you see the “RESTORE DEFAULT” item, and press “OK(R/P)” to factory reset your ESC.2)Restore the default values with a OTA Programmer (Use HW Link mobile phone App)Connect OTA Programmer to the ESC, enter into 【Parameters 】, click “reset” to factory reset your ESC.07Explanation for LED status1. During the Start-up Process• The RED LED keeps flashing rapidly indicating the ESC doesn't detect any throttle signal or the neutral throttle value stored on your ESC may be different from the current value stored on the transmitter. • The GREEN LED flashes “N” times indicating the number of LiPo cells you have connected to the ESC.2. In Operation• The throttle trigger is at the neutral: The RED LED turns on solid and the GREEN LED dies out when the throttle trigger is in the throttle neutral zone. The RED LED will blink to meet Blinky( Zero Timing) rules if the total value of Boost Timing and Turbo timing is 0.• Forward: The RED LED dies out and the GREEN LED blinks when your vehicle runs forward. The GREEN LED turns solid when pulling the throttle trigger to the full (100%) throttle endpoint. • Brake: The RED LED dies out and the GREEN LED blinks when you brake your vehicle. The GREEN LED turns solid when pushing the throttle trigger to the full brake endpoint and setting the ”Max. Brake Force” to 100%.• Backward: The RED LED dies out, the GREEN LED blinks when you reverse your vehicle. The GREEN LED turns solid when pushing the throttle trigger to the full brake endpoint and setting the ”reverse force” to 100%.3. When Some Protection is Activated• The RED LED flashes a short, single flash and repeats “☆, ☆, ☆” indicating the low voltage cutoff protection is activated. • The GREEN LED flashes a short, single flash and repeats “☆, ☆, ☆” indicating the ESC thermal protection is activated.• The GREEN LED flashes a short, double flash and repeats “☆☆, ☆☆, ☆☆” indicating the motor thermal protection is activated.• The GREEN LEDS flash a short, single flash and repeats “☆☆☆, ☆☆☆, ☆☆☆” indicating that the load of ESC is heavy, the Over-Current protection is activated.• The GREEN LEDS flash a short, single flash and repeats “☆☆☆☆☆,☆☆☆☆☆,☆☆☆☆☆” indicating that the temperature of ESC and capacitor is too high, the thermal protection of capacitor is activated.Programming:5Factory reset6Preset modes41A: Running Mode:Option 1: Forward with BrakeRacing mode. It has only forward and brake functions. Option 2: Forward/ Reverse with BrakeThis option is known to be the “training” mode with “Forwar d/ Reverse with Brake” functions. Hobbywing has adopted the “DO UBLE-CLICK” method, that is your vehicle only brakes on the 1st time you push the thr ottle trigger forward (brake) (1st push). The motor stops when you quickly r elease the throttle trigger and then r e-push the trigger quickly (2nd push), only then the vehicle will reverse. The reverse function will not work if your car does not come to a complete stop. The vehicle only reverses after the motor stops. This method is for preventing vehicle from being accidentally reversed.Option 3: Forward and ReverseThis mode is often used by special vehicles. It adopts the “SINGLE-CLICK” method. The vehicle will reverse immediately when you push the thr ottle trigger forward (brake).1B: Max. Reverse Force:The reverse force of the value will determine its speed. For the safety of your vehicle, we recommend using a low amount.1C: Lipo Cells:We strongly recommend that you set LiPo cells manually not automatically. When set automatically, the ESC can judge as 2S or 4S. If the battery voltage is lower than 9.5V after power on the ESC, it will be judged as 2S; if the battery voltage is between 9.5V ~13.6V, it will be judged as 3S; if higher than 13.6V, it will be judged as 4S. 1D: Cutoff Voltage:The ESC will monitor the battery voltage all the time, once the voltage is lower than the threshold value, the ESC will reduce the power to 50% instantly and cutoff the power output in 40 seconds. When enters into voltage protection, the RED LED will single flash that repeats (☆, ☆, ☆, ☆…….). Please set the “Cutoff Voltage” to “Disabled” or customized protection threshold value if you are using NiMH batteries. Option 1: DisabledThe ESC does not cut the power off due to low voltage. We do not recommend using this option when you use any LiPo battery as you will irreversibly damage the product. It is suggested to set to “Disabled”(But the battery would be damaged due to overcharged) Option 2: AutoThe ESC calculates the corresponding cutoff voltage as per the number of LiPo cells it detects and the “3.3V/cell” rule. For example, if the ESC detects a 4S, the cutoff voltage protection threshold value is 3.5x4=14.0V. Option 3: CustomizedThe customized cutoff threshold is a voltage for the whole battery pack (adjustable from 5.0V to 13.6V). Please calculate the value as per the number of LiPo cells you are using. For example, when you use a 4S and you want the cutoff voltage for each cell is 3.0V, you will need to set this item to 12V (3.0*4)1E: ESC Thermal Protection:The output from the ESC will be cut off with the value you have preset. The GREEN LED flashes (☆, ☆, ☆) when the ESC temperature reaches to the preset value. The output will not resume until the ESC temperature gets down.Warning! Please do not disable this function unless you’re in a competition. Otherwise the high temperature may damage your ESC and even your motor.1F: Motor Thermal Protection:The GREEN LED flashes (☆☆, ☆☆, ☆☆) when the motor temperature reaches to the preset value. The output will not resume until the motor temperature gets down.Warning! Please do not disable this function unless you’re in a competition. Otherwise the high temperature may damage your motor and even your ESC. For non-Hobbywing motor, the ESC may get this protection activated too early/late because of the different temperature sensor inside the motor. In this case, please disable this function and monitor the motor temperature manually.1G: BEC Voltage:BEC voltage can be adjusted between 6.0-8.4V. 6.0V is applicable to common servo. If use high-voltage servo, set to higher voltage according to voltage marking of servo. Warning: The setting BEC voltage should not be higher than the max. voltage of common servo, otherwise it will damage the servo or ESC. 1H: Sensor Mode:Option 1: Full SensoredIf use XERUN 4268/74-G2/G3 motor, it can set to full sensor mode. The power system will work in the “sensored” mode at all times. The efficiency and drivability of this mode is at the highest. And Boost 、Turbo timing can be used and get erupting power. Option 2: Sensored/Sensorless HybridThis is universal driving mode of current 1:8 power system. The ESC operates the motor in sensored mode during the low-speed start-up process, followed by switching to operating the motor in the “sensorless” mode when the RPM is increased.1I: Motor Rotation:With the motor shaft faces you (the rear end of the motor is away from you), increase the throttle input, the motor (shaft) will rotate in the CCW/CW direction if the “Motor Rotation/Direction” set to “CCW/CW”. Generally, the vehicle runs forward when the motor (shaft) rotates in the CCW direction. However, some vehicles only run forward when the motor rotates in the CW direction due to the different chassis design. In that case, you only need to set the “Motor Rotation/Direction” to “CW.1J: Phase-AC Swap:If the A/C wire of ESC connect to A/C wire of motor with crossed way (A wire of ESC connects to C wire of motor, C wire of ESC connects to A wire), set this item as Enable. Warning! When #A/#B/#C wire of ESC connect to #A/#B/#C wire of motor correspondingly, do not Set to Enable. Otherwise it will damage the ESC and motor.2A: Throttle Rate Control:This item is used to control the throttle response. It can be adjustable from 1 to 30 (step: 1), the lower the throttle rate, the more the limit will be on the throttle response. A suitable rate can help driver to control his vehicle properly during the starting-up process. Generally, you can set it to a high value to have a quick throttle response if you are proficient at throttle control.2B: Throttle Curve:The throttle curve parameter reconciles the position of the throttle trigger (in throttle zone) and the actual ESC throttle output. It is linear by default and we can change it to non-linear viaadjusting the throttle curve. For example, if adjust it to +EXP , the throttle output at the early stage will be higher (than the output when the curve is linear); if it is adjusted to –EXP , the throttle output at the early stage will be lower (than the output when the curve is linear.2C: Neutral Range:As not all transmitters have the same stability at “neutral position”, please adjust this parameter as per your preference. You can adjust to a bigger value when this happens.2D: Initial Throttle Force:It also called as minimum throttle force. You can set it according to wheel tire and traction. If the ground is slippery, please set a small throttle force. 2E: Coast:The RPM of the motor will be lowered gradually when throttle is reduced. The vehicle will not reduce speed abruptly when the throttle is reduced to return to the neutral position. The bigger the value, the more the “COAST” will be felt. Example, COAST of 0 deactivates, and a COAST of 20% would be the maximum amount of COAST. The advantages of COAST:When “TURBO DELAY” is set to “INSTANT”, the Turbo Timing will be activated right after the throttle trigger is moved to the full throttle position. When other value(s) is applied, you will needto hold the throttle trigger at the full throttle position (as you set) till the Turbo Timing initiates.5C: Turbo Increase Rate (deg/0.1sec):This item is used to define the “speed” at which Turbo Timing is released when the trigger condition is met. For example, “6 degs/0.1sec” refers to the Turbo Timing of 6 degrees that will be released in 0.1 second. Both the acceleration and heat is higher when the “Turbo increase rate” is of a larger value.5D: Turbo Decrease Rate (deg/0.1sec):After the Turbo Timing is activated and the trigger condition turns to not be met (i.e. vehicle slows down at the end of the straightaway and gets into a corner, full throttle turns to partialthrottle, the trigger condition for Turbo Timing turns to be not met), if you disable all the Turbo Timing in a moment, an obvious slow-down like braking will be felt and cause the control of vehicle to become bad. If the ESC can disable the Turbo Timing at some “speed”, the slow-down will be linear and the control will be improved.Warning !Boost Timing & Turbo Timing can effectively improve the motor efficiency; they are usually used in competitions. Please take some time to read this manual and then set these two items carefully, monitor the ESC & motor temperatures when you have a trial run and then adjust the Timing and FDR accordingly as aggressive Timings and FDR may cause your ESC or motor to be burnt.Note: Parameters 5A-5D only has function when you set the “Drive Mode” to “Full Sensored”.。
RB-D01型双层轨道式爬壁移动机器人说明书解读

前言随着经济的发展,人们对于石油、化工原料、核反应堆等的需求量逐步增加,造成储存这些产品的立式油罐的容积越来越大,也越来越高,如果采用人工来完成立式油罐的容积测量、厚度测量、焊缝探伤检查、喷漆、清洁等外围作业显然耗时费力费财,已然成为一项危险作业,而且核反应堆具有辐射,对人体危害极大,在这种背景下,人类迫切需要开发一台代替人工作业的自动化机械来完成这些任务,既可以解放劳动力,提高工作效率,降低任务成本,而且任务执行精确、到位。
故爬壁机器人应运而生。
近几年来,机器人在各个领域中得到广泛的应用和发展。
其中,爬壁机器人是能够在垂直陡壁上进行作业的机器人,它作为高空极限作业的一种自动机械装置,越来越受到人们的重视。
概括起来,爬壁机器人主要用于:(1)核工业:对核废液储罐进行视觉检查、测厚及焊缝探伤等;(2)石化企业:对立式金属罐或球形罐的内外壁面进行检查或喷砂除锈、喷漆防腐;(3)建筑行业:喷涂巨型墙面、安装瓷砖、壁面清洗、擦玻璃等;(4)消防部门:用于传递救援物资,进行救援工作;(5)造船业:用于喷涂船体的内外壁等。
在机械技术发达的国家已经采取了爬壁机器人作为他们完成油罐外围各项工作的首选工具。
比如日本足式磁吸附壁面移动机器人;美国的C-Bot壁面爬行机器人等。
爬壁移动机器人的出现将极大的降低油罐外围任务的成本、工人的劳动强度、安全性,同时提高工作效率,带来相当大的社会效益和经济效益,而且远程无线式控制将成为主流趋势。
因此,移动爬壁机器人的设计和研究有相当好的发展前景。
针对石化核能源企业的现实需求,我认为,爬壁移动式机器人最起码的功能应该有以下几点:1、机器人可沿金属(大多数)、水泥等罐壁垂直爬升和下降;2、可以在任意的某一位置停留,保证执行机构的工作环境;3、罐体表面工作时可以全覆盖;4、采用远程控制,保证用户的安全并最大程度的方便用户。
5、机器人自身带电源,因为使用线缆供电时,线缆容易绞缠、错乱和布置较慢等弊端凸显。
施罗德爬行机器人S200中文说明书
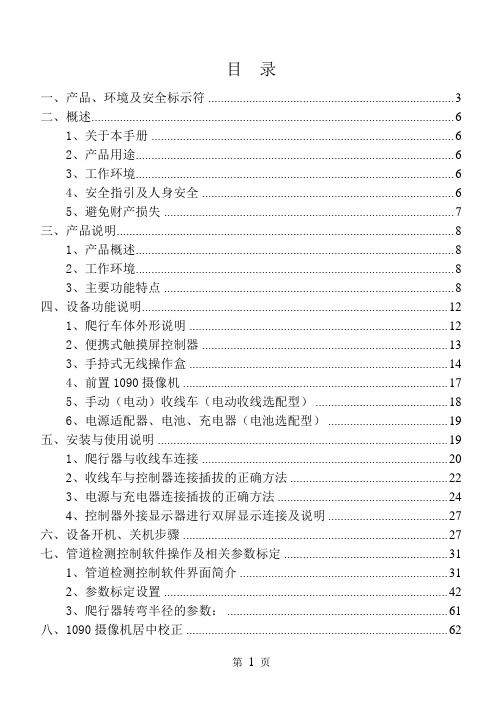
11)防水等级:IP54
手动(电动)收线车(电动收线选配型)
1)线缆测量:电子计米,距离可直接显示在监视器屏幕上;精确定位,测量最小距离精度可达±。
2)线缆长度:线缆直径7.9mm,标准配置120米,可根据用户要求配置长度;
线缆防水、防油、耐磨、耐腐蚀。
3)驱动:电动或手动收、放线。
危险警告符号:表示一些存在危险情况的环境,如果不能避免,将导致死亡和严重的伤害事故。
警告符号:表示危险的境况,如果不能避免,也可能导致死亡或严重的伤害事故。
小心符号:表示危险的境况,如果不能避免,可能导致轻微或中等程度伤害事故。
注意符号:表示和保护财产相关的安全信息,该符号意味着使用者在使用该工具前必须仔细阅读操作手册,因为操作手册里介绍了重要的安全注意事项和正确的使用方法。
2、产品用途
CCTV管道检测爬行系统主要用于市政排水管道内部快速检测和诊断。该设备配备强力照明光源和便携式控制系统,适合野外和移动工作场所。传输线缆可以根据用户需求配备,目前最长支持500米(光纤通信线缆),可将设备送至所需工作位置。爬行车部件采用防水设计可至水下检测(正压状态下),但实际操作根据水下环境而定。
安全气压检测系统:
自动检测车体、摄像系统、升降系统内部气体压力,并实时向后端设备传送数据、并能自动判断和处理异常,确保设备及工作环境的安全(下井前需充入大约10~14PIS干燥气体)。
4、主要技术参数
爬行系统:9902FA
1)适用于150mm(最小轮)以上的管道检测,配置大小轮胎及电动升降台。
2)爬行器工作电压48V,最大输出功率180W。
用户使用发电机供电时,请严格按照发电机的操作规程执行,并且能够适用本公司自带的稳压适配器!
eZRun ESC Ver Page 1 攀岩车电子调速器使用说明书

备注 2:马达鸣音可能会比较轻微,在吵闹的环境下可能无法听清,此时可仅根据 LED 的闪烁状态来进行操作。 备注 3:详见第 2 页关于参数编程设定的说明。
第三步:接线及基本设置完成,电机已经可以正常运行,行驶过程中指示灯(LED)状态说明: 当油门摇杆处于中点区域时,红色和绿色 LED 均熄灭。 前进和倒车时,红色 LED 恒亮,当油门处于正向(前进)最高点或者反向(倒车)最高点时,绿色 LED 也将点亮。 刹车时,红色 LED 快速闪烁。
保修期限
我们的产品提供自购买之日起 120 天的品质保证,因此请您务必向销售商索取购买凭证(收据或发票)。 关于保修的详细条例,请访问 下述网页:/kf.asp
产品特色
Ì 完全针对攀岩车而设计的程序算法,具有优异的启动效果、正反向运转切换性能、拖刹性能及油门线性度; Ì 支持所有无感(即无霍尔传感器)无刷电机; Ì 高品质用料,具有强大的耐电流能力; Ì 具备“正转带刹车”、“正反转带刹车”(普通电动车模适用)和“正反转(攀岩车适用)”三种运行模式; Ì 4 段最大倒车力度调节; Ì 比例式刹车:4 段最大刹车力度调节、8 段拖刹力度调节、4 段初始刹车力度调节; Ì 9 种启动加速度(Punch)调整,从柔和到非常劲暴,以便适应不同特性的场地及轮胎,防止打滑; Ì 多重保护功能:电压过低保护(支持锂电池和镍镉/镍氢电池)、温度保护、油门失控保护、堵转保护; Ì 采用软件方式进行进角调整,具有 8 个进角模式,可良好匹配各种无刷电机; Ì 单键编程设定,且有单键恢复出厂设置的功能; Ì 防水防尘设计,元器件被密封于专门开模定制的外壳内而得到良好的保护,有效延长使用寿命; Ì 可选购轻巧便携的车用电调编程设定卡,方便外场使用。设定卡界面友好,让您轻松设定功能强大的车用电调; Ì 自主知识产权,在必要的情况下,可根据客户要求进行软硬件定制。
”三之乐“遥控车产品说明书

4
广州三之乐信息科技有限公司
附 件 :
“三之乐”方案与其他产品方案的横向对比:
产品类型 三之乐遥控汽车 Helic Max
Desk Pets
X-RACER
操控方式
触控
支持
支持
支持
支持
重力感应
支持
支持
不支持
支持
任我行
支 持 ,车 辆 完 成 指
方 案 概 述
“三之乐”手机遥控车解决方案分为两部分,发射模块和手机端的控制软件。
发 射 模 块 :
模块原理 FM 或红外
电池 钮扣电池
大小 约 1.0cm*2.5cm*6.0cm 与手机连接 手机音频接口
合 作 流 程
对于有合作意向的厂家,我们会为厂家提供一个的试用版的 App 和发射器, 让厂家操控自己的车,了解我们方案。如果厂家确认同意合作。合作流程如下: 1. 厂家提供样车
厂家提供 2-‐3 辆样品车,供测试样车的各个参数,并配置到后台的数据库中; 2. 厂家提供公司 LOGO 及玩具车图片
厂家提供遥控车对应的图片、背景,和厂家 LOGO,如果厂家无法提供图片, 我们可以为厂家设计; 3. 我公司提供二维码及发射器 厂家提供玩具车的型号和确定要生产的数量,我们为每辆车生成一个二维码
图片,交付给厂家,厂家直接打印后贴在要卖的车上;同时将对应数量的发
射器交付给厂家。 4. 软件发布
天线长度 拉开 20cm,收起约 6cm 支持手机 iPhone、iPad 和安卓手机
手机软件:
本 APP 提供了对玩具汽车不同的控制模式,包括“触控”、“重力感应”以及
“任我行”等模式。用户可以选择不同的控制模式对玩具车进行操控,以达到较
- 1、下载文档前请自行甄别文档内容的完整性,平台不提供额外的编辑、内容补充、找答案等附加服务。
- 2、"仅部分预览"的文档,不可在线预览部分如存在完整性等问题,可反馈申请退款(可完整预览的文档不适用该条件!)。
- 3、如文档侵犯您的权益,请联系客服反馈,我们会尽快为您处理(人工客服工作时间:9:00-18:30)。
爬壁遥控车说明书篇一:爬壁小车简介爬壁小车简介背景及目的:现在工程中需要在高空完成一些作业(如建筑业,核工业,造船业),这些作业让人去完成很难,也很危险。
本组机器人为一辆爬壁小车,可以替人去完成这些高难度,高危险的高空作业。
依托它的高空滞留能力,我们还可以进一步开发,完成从高空对地面的监测,通过红外遥感控制也可以完成某些侦查任务,达到军民两用的效果,具有极大的现实意义。
机器人描述:本项目主要依据真空吸附原理,通过msp430单片机对电机的可编控性和红外遥感的控制原理。
本作品由履带传动,通过履带上的电磁铁间接控制吸盘,从而提供稳定的吸附力吸附在墙壁上。
在小车上有一个可以180度在竖直与履带平行的面内转动的杆1,杆1的一端带有摄像头,在小车的前部有一个固定杆2,杆2的长度和杆1相同。
在杆2上装有一个红外对管,红外对管竖直向下发射红外线。
当小车在墙上爬行的时候杆1在后面,如果红外对管发现缝隙后小车停止,同时杆2转动180度向前和杆1并排,并开始摄像。
具体内容:1)机器人结构的设计。
2)可以使杆1完成180度的转向。
3)通过履带吸盘的吸附及移动使小车在竖直墙壁上自由移动。
4)寻找有机玻璃及高分子材料制作车身,减轻小车的重量。
5) 摄像头拍摄的启动与终止。
6)使用msp430单片机编程完成以上动作。
技术难关:1、车体材料的选择。
所选的材料必须足够轻,减轻车子的载荷。
2、履带轮的吸附。
必须找到或者制作可以通过磁铁控制吸盘的履带轮。
3、两根杆的相对位置以及根据这个相对位置需要小车在检测到缝隙后需要做的移动。
4、摄像头的启动和终止。
意义:1)本组做的高空作业机器人可以沿着墙面竖直爬行,通过携带探测设备对要研究高空中的目标进行测试,弥补了现有设备通过人去完成的缺陷。
2)可应用于高空建筑物的清洗和粉刷,高空物品的传递,对地面地理环境等的监察等。
附:履带吸附机构:吸附部件:吸盘、磁铁、电铁芯吸盘吸附条件:开始时,人为地将贴墙侧的履带上的吸盘按在墙上,起到吸附作用。
接下来要解决的问题有两点:1、怎么使前后轴产生对墙壁的压力。
如果没有这个压力,只是履带吸在墙上,而小车只是被履带托住,这样小车很难稳定在墙上。
2、怎么使其他吸盘自动吸住墙壁。
小车前进时,新进入墙面的吸盘(就是原来没有吸住墙体的吸盘,在履带带动下进入墙面),怎么使它也能吸住墙壁。
这点做不到,小车在前进的过程中后面吸盘就会挨个脱落,而导致小车也掉下来。
吸附技巧:利用磁铁和电铁芯的相互作用,巧妙地将作用在吸盘上的大气压,转移到小车的前后轴。
(看图解)这样,产生的这个轴力有两个作用:1、使得小车能产生一个对墙壁的压力,也就是说,小车可以站在墙上了,而不是被吸盘托住。
2、在小车前进的过程中,由于前轴对墙体有压力,那么,在履带的带动下,吸盘经过前轮毂下,被前轴挤压,使得吸盘里面的空气排出,导致吸盘被吸附在墙体上轮子结构示意图:篇二:爬壁机器人清洁装置爬壁机器人清洁装置一、超声波清洁装置在清洁装置的设计上,于超声波清洗必须在水中进行, 故清洗头的清洗平面与玻璃平行紧贴, 于水的张力在玻璃和清洗头之间形成一层“水膜” , 避免了清洗头与玻璃的直接接触。
清洗头材料为铝, 把超声换能器产生的超声传导到水膜上, 利用超声换能器激发清洗液产生高频振动, 对浸泡在液体玻璃表面进行去污清洗, 从而对壁面进行清洗。
二、喷水清洁装置a自带水(带污水回收装置)b有辅助装备三、毛刷清洁装置篇三:爬壁幕墙清洗机器人设计说明书江西省第二届大学生机械创新设计大赛暨第三届全国大学生机械创新设计大赛江西赛区选拔赛设计说明书INSTRUCTION OF DESIGN作品名称“小蜘蛛”幕墙攀爬清洗机参赛队伍陈明登谢信韦冯江涛刘连杰郭晓欢指导老师李国臣吴文通参赛单位井冈山大学XX年4月18日目录摘要 ................................................ ....................... i 小蜘蛛幕墙攀爬清洗机设计说明书 ............................ 错误!未定义书签。
作品内容简介 ................................................ ............... 4 1 研制背景及意义 .......................................... 错误!未定义书签。
2 主要功能和性能指标 ................................................ . (2)3 设计方案 ................................................ (3)3.1 机械机构 ................................................ .. (3)3.2 控制机构 ................................................ .. (3)4 理论设计计算 ................................................ (4)4.1 真空吸附力计算 ................................................ .. (4)4.2 幕墙清洗机器人附着的力学分析 (5)5机构设计与工作原理 ................................................ . (7)5.1攀爬机构 ........................................... 错误!未定义书签。
5.2清洗机构 ................................................ (8)5.3铰接连杆支撑机构 ................................... 错误!未定义书签。
5.4换气机构 ........................................... 错误!未定义书签。
6创新点及应用 ................................................ ............ 10 7作品实物工作图 .......................................... 错误!未定义书签。
8应用前景 ................................................ 错误!未定义书签。
参考文献 ................................................ .. 错误!未定义书签。
摘要:“小蜘蛛”幕墙攀爬清洗机是基于昆虫攀爬动作的仿生原理制作而成。
在国内外现有的壁面移动机器人研究成果的基础上,结合高空作业的特点,在对幕墙清洗机器人的共性问题—附着技术、爬行技术、清洗技术进行分析的基础上。
模拟昆虫交错攀爬的动作,设计了自攀爬机构,实现了吸附机构、清洗机构和攀爬机构的有机结合。
“小蜘蛛”幕墙攀爬清洗机主要包括攀爬运动机构、吸附机构、清洗机构和控制系统等四部分组成,机械结构设计中灵活运用了四杆机构、曲柄滑块机构、齿轮机构、离合器和控制机构等,结构丰富,其创新点主要体现在:1)仿昆虫攀爬动作,采用丝杠传输机构与连杆铰接支架的升降机构,实现清洗设备的腿足式交错移动。
2)仿人工清洗习惯动作,采用曲柄滑块机构,实现玻璃幕墙的往复式擦洗。
3)采用连杆铰接支架的升降控制吸附机构控制阀门的开启与关闭,通过单片机控制,实现机构移动、换气机构与清洗机构的有机结合。
本产品可广泛用于高楼大厦的幕墙清洗,设备结构简单、灵巧便捷,实现了幕墙清洗的自动化,将人类从原始的高强度的高空作业中解脱出来。
试验表明,此型清洗机器人清洗效果明显,操作方便,对同类设备的设计有很好的参考价值。
关键词:幕墙清洗玻璃幕墙机器人负压吸附“小蜘蛛”幕墙攀爬清洗机设计说明书设计者:陈明登,谢信韦,冯江涛,刘连杰,郭晓欢(井冈山大学工学院,江西吉安 343009)作品内容简介“小蜘蛛”(转载自:小草范文网:爬壁遥控车说明书)幕墙攀爬清洗机是基于昆虫攀爬动作的仿生原理制作而成。
其主要特点是在模拟昆虫交错攀爬动作的基础上,根据高楼幕墙清洗的特点,在对幕墙清洗机器人的共性问题—附着技术、爬行技术、清洗技术进行分析的基础上。
设计了结构简单、灵活便捷的自攀爬清洗机器人。
“小蜘蛛”幕墙攀爬清洗机主要包括攀爬运动机构、吸附机构、清洗机构和控制系统等四部分组成,机械结构设计中灵活运用了四杆机构、曲柄滑块机构、齿轮机构、离合器和控制机构等,机械结构丰富,其创新点主要体现在:1)仿昆虫攀爬动作,采用丝杠传输机构与连杆铰接支架的升降机构,实现清洗设备的腿足式交错移动。
2)仿人工清洗习惯动作,采用曲柄滑块机构,实现玻璃幕墙的往复式擦洗。
3)采用连杆铰接支架的升降控制吸附机构控制阀门的开启与关闭,通过单片机控制,实现机构移动、换气机构与清洗机构的有机结合。
本产品可广泛用于高楼大厦的幕墙清洗,实现了幕墙清洗的自动化,将人类从原始的高强度的高空作业中解脱出来。
试验表明,此型清洗机器人清洗效果明显,操作方便,对同类设备的设计有很好的参考价值。
联系人:李国臣,联系电话:,E-mail: 1 研制背景及意义随着城市现代化的发展,特别是高层建筑的兴起,以玻璃幕墙为代表的幕墙结构逐步演绎成华丽的“城市外衣”,就在实现它的功能和实效的同时又衍生出了下一个问题—繁重的幕墙清洗任务,并且许多国家已对建筑幕墙的清洗要求做出了明确规定。
此外,越来越奇特的建筑结构使清洗的难度成倍增加,甚至采用传统的清洗方法己无能为力。
然而,在社会文明高度发展的今天,对生命的关爱达到了前所未有的高度,要求停止使用蜘蛛人的呼声不绝于耳。
因此人们期待新的具有人性化的清洗方式出现。
目前大多是用人工清洗,若是低些的幕墙的还好,但现在几十、几百米的幕墙水随处可见,那么幕墙的清洗问题变成了令人们头疼的一件事了。
而传统的吊篮人工操作清理的方式既危险和枯燥,劳动强度又高。
为了弥补现实生活中存在的这一缺陷;为了在清洗工作自动化上能贡献我们的一点力量与能力;也为了更好的在生活中实现清洗作业的节能操作;同时,还为了实现高新技术的绿色、环保,造福我们的子孙后代。
20世纪90年代以来,随着电子技术的飞速发展和自动化装备的不断成熟,日本的研究人员率先将目光投向自动化的清洗方式,由此幕墙清洗机器人应运而生。
目前幕墙清洗机器人技术及其理论的研究已成为热点,国内外许多科研单位都在进行相关方面的研究并取得可喜成果。