有效地设计壳管式换热器
管壳式换热器设计和选型

(3) )
(4) )
(2)计算管程的压降和传热系数
a、参考表选定流速 参考表选定流速,确定管程数目,计算管程压降 参考表选定流速
l ρu 2 ( ∑ ∆pi = (∆p1 + ∆p2 )Ft N s N p = λ d + 3) 2 Ft N s N p
若管程允许压降已经有规定,可由上式计算管程数Ns. b、计算管内传热系数hi< K估则应增加管壳数,重新) 则应增加管壳数,重新) 计算。若改变管程不能同时满足h 和 计算。若改变管程不能同时满足 i> K估,和 ∑ ∆pi < ∆p允 ,则应重新估计 估(减小 ,另选一台换热器 则应重新估计K 减小 减小), 则应重新估计 型号进行试算。 型号进行试算。
(2) BIU 600--1.6--90--6/25-2 II
封头管箱,公称直径600mm, 封头管箱,公称直径600mm,管、壳程压力均为 1.6MPa,公称换热面积90平方米 普通级冷拔换热管, 1.6MPa,公称换热面积90平方米,普通级冷拔换热管, 平方米, 外径25mm,管长6m, 管程,单壳程的U 外径25mm,管长6m,2管程,单壳程的U形管式换热 器。
⑦流量小或粘度大的流体宜走壳程,因流体在有 流量小或粘度大的流体宜走壳程, 折流挡板的壳程中流动, 折流挡板的壳程中流动,由于流速和流向的不断 改变,在低Re(Re>100)下即可达到湍流, 改变,在低Re(Re>100)下即可达到湍流,以 提高传热系数。 提高传热系数。 若两流体温差较大, ⑧若两流体温差较大,宜使对流传热系数大的流 体走壳程,因壁面温度与α大的流体接近, 体走壳程,因壁面温度与α大的流体接近,以减 小管壁与壳壁的温差,减小温差应力。 小管壁与壳壁的温差,减小温差应力。 以上原则并不是绝对的,对具体的流体来说, 以上原则并不是绝对的,对具体的流体来说, 上述原则可能是相互矛盾的。因此, 上述原则可能是相互矛盾的。因此,在选择流体 的流径时,必须根据具体的情况, 的流径时,必须根据具体的情况,抓住主要矛盾 进行确定。 进行确定。
管壳式换热器设计和选型
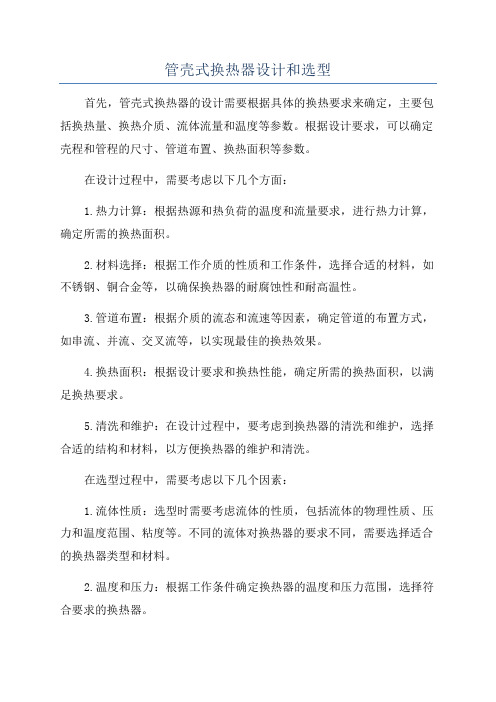
管壳式换热器设计和选型首先,管壳式换热器的设计需要根据具体的换热要求来确定,主要包括换热量、换热介质、流体流量和温度等参数。
根据设计要求,可以确定壳程和管程的尺寸、管道布置、换热面积等参数。
在设计过程中,需要考虑以下几个方面:1.热力计算:根据热源和热负荷的温度和流量要求,进行热力计算,确定所需的换热面积。
2.材料选择:根据工作介质的性质和工作条件,选择合适的材料,如不锈钢、铜合金等,以确保换热器的耐腐蚀性和耐高温性。
3.管道布置:根据介质的流态和流速等因素,确定管道的布置方式,如串流、并流、交叉流等,以实现最佳的换热效果。
4.换热面积:根据设计要求和换热性能,确定所需的换热面积,以满足换热要求。
5.清洗和维护:在设计过程中,要考虑到换热器的清洗和维护,选择合适的结构和材料,以方便换热器的维护和清洗。
在选型过程中,需要考虑以下几个因素:1.流体性质:选型时需要考虑流体的性质,包括流体的物理性质、压力和温度范围、粘度等。
不同的流体对换热器的要求不同,需要选择适合的换热器类型和材料。
2.温度和压力:根据工作条件确定换热器的温度和压力范围,选择符合要求的换热器。
3.环境限制:考虑到环境因素,如空间限制、气候条件等,选择适合的换热器尺寸和类型。
4.经济效益:综合考虑设备造价、运行费用、维护保养成本等因素,选择经济、高效的换热器。
5.供应商选择:选择有经验和信誉良好的供应商,确保提供优质的产品和服务。
总之,管壳式换热器的设计和选型需要根据具体的应用要求和工艺条件来确定,需要综合考虑热力计算、材料选择、管道布置、换热面积、清洗和维护等因素,并在选型过程中考虑流体性质、温度和压力、环境限制、经济效益和供应商选择等因素,以确保设计符合要求,选型合理可靠,并能够实现高效换热。
管壳式换热器设计总结
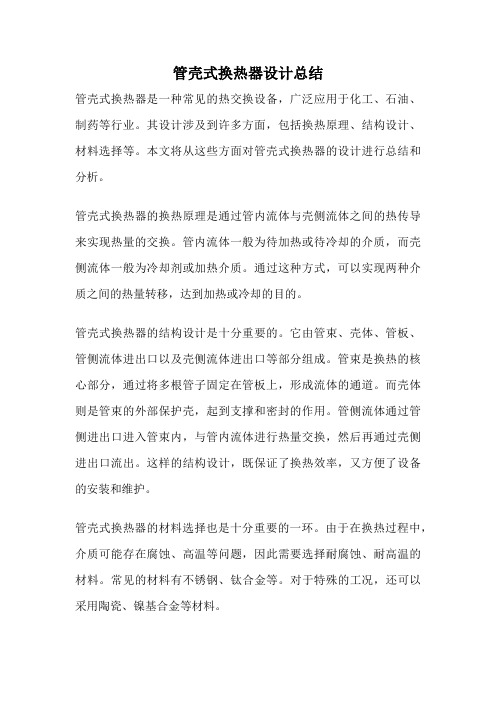
管壳式换热器设计总结管壳式换热器是一种常见的热交换设备,广泛应用于化工、石油、制药等行业。
其设计涉及到许多方面,包括换热原理、结构设计、材料选择等。
本文将从这些方面对管壳式换热器的设计进行总结和分析。
管壳式换热器的换热原理是通过管内流体与壳侧流体之间的热传导来实现热量的交换。
管内流体一般为待加热或待冷却的介质,而壳侧流体一般为冷却剂或加热介质。
通过这种方式,可以实现两种介质之间的热量转移,达到加热或冷却的目的。
管壳式换热器的结构设计是十分重要的。
它由管束、壳体、管板、管侧流体进出口以及壳侧流体进出口等部分组成。
管束是换热的核心部分,通过将多根管子固定在管板上,形成流体的通道。
而壳体则是管束的外部保护壳,起到支撑和密封的作用。
管侧流体通过管侧进出口进入管束内,与管内流体进行热量交换,然后再通过壳侧进出口流出。
这样的结构设计,既保证了换热效率,又方便了设备的安装和维护。
管壳式换热器的材料选择也是十分重要的一环。
由于在换热过程中,介质可能存在腐蚀、高温等问题,因此需要选择耐腐蚀、耐高温的材料。
常见的材料有不锈钢、钛合金等。
对于特殊的工况,还可以采用陶瓷、镍基合金等材料。
在管壳式换热器的设计过程中,还需要考虑一些其他因素。
首先是换热面积的确定,它与换热效果直接相关。
一般来说,换热面积越大,换热效果越好。
其次是流体的流速和流量,它们对换热器的换热效果和压力损失有着重要影响。
此外,还需要考虑到换热器的尺寸和重量,以及设备的安全性和可靠性等方面。
在实际应用中,还需要根据具体的工况和要求进行换热器的定制设计。
例如,在高温高压的条件下,需要采用密封性好、耐高温高压的结构和材料;在对流体的温度变化要求较高的情况下,需要采用多级换热器或增加管程等方式来提高换热效果。
管壳式换热器的设计需要考虑多个方面的因素,包括换热原理、结构设计、材料选择等。
合理的设计可以提高换热效率,降低能耗,满足工业生产的需求。
同时,还需要根据具体的工况和要求进行定制设计,以提高设备的安全性和可靠性。
管壳式换热器设计选型

管壳式换热器设计选型
一、换热器选型的基础
在管壳式换热器结构形式中,设计和选型的主要因素有:换热器的负
荷率、传热效率、凝结物沉积、对管壳换热器热性能的影响因素、管壳型
号和规格、在换热器抗冲击性能的影响、铭牌设计性能和管壳强度要求等。
1.关于管壳式换热器的负荷率
在计算换热器的负荷率时,需要考虑换热器的负荷率与介质流量温度
有关,当流量温度越大,换热器的负荷率越大,但流量温度比较低时,换
热器的负荷率就较低。
在负荷率计算中,还需要考虑其他因素如液体的粘度、流体压力、换热面积、单位传热面积等。
2.关于管壳式换热器的传热效率
换热器的传热效率主要取决于换热器的几何结构,以及内、外管壳间
的接触面积大小,而内、外管壳间的接触面积的大小,又是由管壳结构型
号和规格参数决定的,所以,选择管壳型号和规格参数时,必须考虑到换
热器的传热效率。
3.凝结物沉积
凝结物沉积是管壳式换热器热性能的一个重要因素,它包括水铁、水铝、水锡等,这些凝结物会影响换热器的传热效率,严重影响换热器的使
用寿命。
管壳式换热器设计

1 概 述
2、冷凝器(condenser) 1)分离器 2)全凝器 3、加热器(一般不发生相变)(heater) 1)预热器(preheater)——粘度大的液体,喷雾 状不好,预热使其粘度下降; 2)过热器(superheater)——加热至饱和温度以 上。 4.蒸发器(etaporater)——发生相变 5.再沸器(reboiler) 6.废热锅炉(waste heat boiler)
1 概 述
2、浮头式换热器 优点:管束可以抽出,便于清洗; 缺点:换热器结构较复杂,金属耗量较大。 适用场合:适用于介质易结垢的场合。
3、填料函式换热器 优点:造价比浮头式低,检修、清洗容易,填料函处泄漏能 及时发现; 缺点:壳程内介质由外漏的可能,壳程中不宜处理易挥发、 易燃、易爆、有毒的介质。 适用场合:适用于低压小直径场合。
2 管子的选用及其与管板的连接
结构:主要有4种
2 管子的选用及其与管板的连接
3、胀焊并用 前面我们讲了胀接、焊接后,会发现它们各自有优、缺点,因而目前广泛应用了 胀焊并用的方法,这种方法能提高连接处的抗疲劳性能,消除应力腐蚀和间隙腐蚀, 提高使用寿命。 胀焊并用连接形式主要有: 1)先焊后胀:强度焊+贴胀 高温高压换热器中大多用厚壁管,胀接时要使用润滑油,进入接头后缝隙中会在焊 接时生成气体,恶化焊缝质量,只要胀接过程控制得当,先焊后胀可避免这一弊病。
3 管板结构
2、正方形和转角正方形排列
正方形和转角正方形排列,管间小桥形成一条直线通道,便于机械清洗。要 经常清洗管子外表面上的污垢时,多用正方形排列或转角正方形排列。
3 管板结构
3.组合排列法 多程换热器中。 3.2 管间距: 管间距指两相邻换热管中心的距离。其值的确定需要考虑以下几个因素: ① 管板强度; ② 清洗管子外表面时所需要的空隙; ③ 换热管在管板上的固定方法。 一般要求管间距≥1.25d0,还应符合规定:
管壳式换热器设计-课程设计
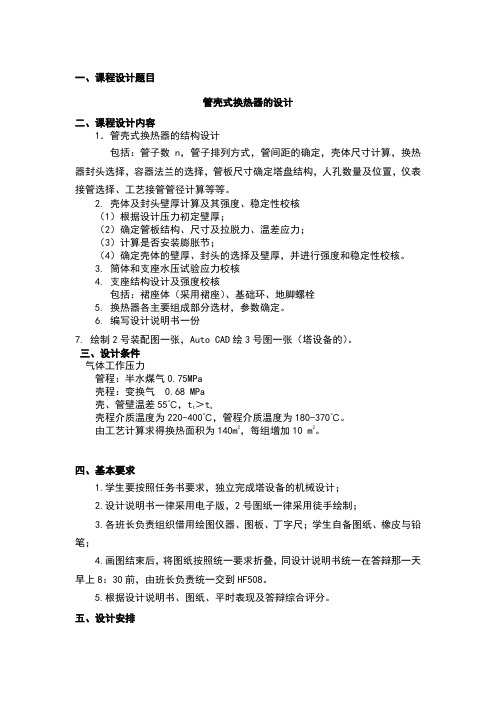
一、课程设计题目管壳式换热器的设计二、课程设计内容1.管壳式换热器的结构设计包括:管子数n,管子排列方式,管间距的确定,壳体尺寸计算,换热器封头选择,容器法兰的选择,管板尺寸确定塔盘结构,人孔数量及位置,仪表接管选择、工艺接管管径计算等等。
2. 壳体及封头壁厚计算及其强度、稳定性校核(1)根据设计压力初定壁厚;(2)确定管板结构、尺寸及拉脱力、温差应力;(3)计算是否安装膨胀节;(4)确定壳体的壁厚、封头的选择及壁厚,并进行强度和稳定性校核。
3. 筒体和支座水压试验应力校核4. 支座结构设计及强度校核包括:裙座体(采用裙座)、基础环、地脚螺栓5. 换热器各主要组成部分选材,参数确定。
6. 编写设计说明书一份7. 绘制2号装配图一张,Auto CAD绘3号图一张(塔设备的)。
三、设计条件气体工作压力管程:半水煤气0.75MPa壳程:变换气 0.68 MPa壳、管壁温差55℃,tt >ts壳程介质温度为220-400℃,管程介质温度为180-370℃。
由工艺计算求得换热面积为140m2,每组增加10 m2。
四、基本要求1.学生要按照任务书要求,独立完成塔设备的机械设计;2.设计说明书一律采用电子版,2号图纸一律采用徒手绘制;3.各班长负责组织借用绘图仪器、图板、丁字尺;学生自备图纸、橡皮与铅笔;4.画图结束后,将图纸按照统一要求折叠,同设计说明书统一在答辩那一天早上8:30前,由班长负责统一交到HF508。
5.根据设计说明书、图纸、平时表现及答辩综合评分。
五、设计安排六、说明书的内容1.符号说明2.前言(1)设计条件;(2)设计依据;(3)设备结构形式概述。
3.材料选择(1)选择材料的原则;(2)确定各零、部件的材质;(3)确定焊接材料。
4.绘制结构草图(1)换热器装配图(2)确定支座、接管、人孔、控制点接口及附件、内部主要零部件的轴向及环向位置,以单线图表示;(3)标注形位尺寸。
(4)写出图纸上的技术要求、技术特性表、接管表、标题明细表等5.壳体、封头壁厚设计(1)筒体、封头及支座壁厚设计;(2)焊接接头设计;(3)压力试验验算;6.标准化零、部件选择及补强计算:(1)接管及法兰选择:根据结构草图统一编制表格。
(完整版)HTRI管壳式换热器设计基础教程讲解

01
通过桌面快捷方式启动;
02
在开始菜单中找到HTRI软件并启动;
通过命令行启动(需要知道软件安装路径)。
03
界面布局及功能区域划分
菜单栏
包含文件、编辑、视图等常用操作;
工具栏
提供常用功能的快捷按钮;
界面布局及功能区域划分
左侧导航栏
列出可用的设计选项和工具;
主工作区
显示当前设计项目的详细信息。
界面布局及功能区域划分
在HTRI软件中,输入流体的物性参数(如密 度、粘度、导热系数等)、流量、进出口温 度等设计条件。
建立模型
求解过程
根据输入参数,软件自动建立换热器的物理 模型,包括管程、壳程、折流板、管板等结 构。
利用HTRI软件的计算功能,对模型进行传热、 流动和结构分析,得到换热器的性能参数 (如传热系数、压力降等)。
性能评估 通过数值模拟或实验手段,对优化后的换热器性能进行评 估,包括传热系数、压降、热效率等。同时,与初步设计 结果进行对比分析,验证优化效果。
05
案例分析:应用HTRI进行实际 项目设计
案例背景介绍及问题阐述
项目背景
某化工企业需设计一款高效、紧凑的管壳式换热器,用于实现两种 不同温度流体的热量交换。
核算性能
通过初步设计得到的换热器结构 参数,进行性能核算,包括传热 系数、压降、热效率等。
详细设计:结构优化和性能评估
结构优化 在初步设计的基础上,对换热器结构进行优化,如调整管 径、管长、折流板间距等,以提高传热效率、降低压降等。
强度校核 对优化后的换热器结构进行强度校核,确保其在操作条件 下的安全性和稳定性。
THANK YOU
设计区域
用于创建和编辑换热器设计;
管壳式换热器设计-课程设计

河南理工大学课程设计管壳式换热器设计学院:机械与动力工程学院专业:热能与动力工程专业班级:11-02班学号:姓名:指导老师:小组成员:目录第一章设计任务书 (1)第二章管壳式换热器简介 (1)第三章设计方法及设计步骤 (2)第四章工艺计算 (3)4.1 物性参数的确定 (3)4.2核算换热器传热面积 (4)4.2.1传热量及平均温差 (6)4.2.2估算传热面积 (8)第五章管壳式换热器结构计算 (9)5.1换热管计算及排布方式 (9)5.2壳体内径的估算 (12)5.3进出口连接管直径的计算 (12)5.4折流板 (13)第六章换热系数的计算 (17)6.1管程换热系数 (17)6.2 壳程换热系数 (17)第七章需用传热面积 (19)第八章流动阻力计算 (20)8.1 管程阻力计算 (21)8.2 壳程阻力计算 (22)总结 (24)第一章设计任务书煤油冷却的管壳式换热器设计:设计用冷却水将煤油由140℃冷却冷却到40℃的管壳式换热器,其处理能力为10t/h,且允许压强降不大于100kPa。
设计任务及操作条件1、设备形式:管壳式换热器2、操作条件(1)煤油:入口温度140℃,出口温度40℃(2)冷却水介质:入口温度26℃,出口温度40℃第二章管壳式换热器简介管壳式换热器是在石油化工行业中应用最广泛的换热器。
纵然各种板式换热器的竞争力不断上升,管壳式换热器依然在换热器市场中占主导地位。
目前各国为提高这类换热器性能进行的研究主要是强化传热,提高对苛刻的工艺条件和各类腐蚀介质适应性材料的开发以及向着高温、高压、大型化方向发展所作的结构改进。
强化传热的主要途径有提高传热系数、扩大传热面积和增大传热温差等方式,其中提高传热系数是强化传热的重点,主要是通过强化管程传热和壳程传热两个方面得以实现。
目前,管壳式换热器强化传热方法主要有:采用改变传热元件本身的表面形状及表面处理方法,以获得粗糙的表面和扩展表面;用添加内物的方法以增加流体本身的绕流;将传热管表面制成多孔状,使气泡核心的数量大幅度增加,从而提高总传热系数并增加其抗污垢能力;改变管束支撑形式以获得良好的流动分布,充分利用传热面积。
- 1、下载文档前请自行甄别文档内容的完整性,平台不提供额外的编辑、内容补充、找答案等附加服务。
- 2、"仅部分预览"的文档,不可在线预览部分如存在完整性等问题,可反馈申请退款(可完整预览的文档不适用该条件!)。
- 3、如文档侵犯您的权益,请联系客服反馈,我们会尽快为您处理(人工客服工作时间:9:00-18:30)。
Southwest Petroleum University G r a d u a t i o n D i s s e r t a t i o nTitle Effectively DesignShell-and-Tube HeatExchangersName ShenWeiSchool Southwest Petroleum UniversityInstructor Raojiyang2011-6-8有效地设计壳管式换热器设计壳管式换热器(STHEs)需要通过先进的计算机软件。
然而,对换热器设计的基本原则,还是需要更好地了解并有效的使用这个软件。
本文阐述器热设计的基本知识,包括以下主题:壳管式换热器元件;根据施工条件和服务对壳管式换热器的分类;管程设计;壳程设计,包括管布局,节流,和壳程压力降;以及平均温差。
管程与壳程的换热与压力降基本方程是很有名的;在这里,我们着眼于这些相关应用的换热器优化设计。
先进的主体关于管壳式换热器设计,如壳程和管程液体的分配,使用多壳程,超标准的污染,将在下一期的随访文章。
壳管式换热器的组成设计师具有良好的知识关于壳管式换热器的机械特性和他们如何影响散热的设计是必不可少的。
壳管式换热器的重要组成部分包括:·外壳;·壳罩;·管;·通道;·通道罩;·管板;·挡板;·喷嘴。
其他组件包括拉杆和垫片,通过分区板,冲击板,纵向挡板,密封条,支持板和基础板。
壳管式换热器制造协会(TEMA)的标准详细描述了这些不同的组成。
壳管式换热器被分为:前部,壳,后部。
图一说明了各项建设的可能性和壳管式换热器制造协会的命名。
换热器是由字母代码描述为三个部分-例如,一个BFL式的换热器具有盖罩,挡板与纵向两通外壳,以及固定管板的后部。
基础设备的分类固定管式一个固定管换热器(图2)有许多直管固定在管板的两端焊接到外壳。
设备具有可拆卸的通道盖(例如,机场快线),帽型通道盖(例如,边界元),或者积分管板(例如,荷兰国家标准)。
固定管板结构的主要优点是它的结构简单,成本低。
事实上,固定管板式是最便宜的建造类型,只要无伸缩缝要求。
图1. 壳管式换热器及壳管式换热器的名称其他优点有,去除发动机和通道盖后容易清理管道,而且因为没有法兰接头,这种壳程液泄漏量降到了最低。
这种设计的缺点是由于管束被固定在壳上而且不能拆卸,管道外层不能被机械清洗。
因此,这种方式限制了清洗外壳。
不过,如果有一个令人满意的化学清洗方案可以被采用,则固定管板设备可以被选择清洗外壳上的污垢。
在管和壳之间温差大的情况下,管板无法吸收较大的压力,从而使其纳入了必要的伸缩缝。
这在很大程度上带走了成本低的优势。
U型管式正如其名称所示,U型管式换热器的管被弯曲成U型。
只有一个管壳在U 型换热器里。
不过,对于单管板成本低,抵消了弯曲的管和壳径(最小的U型弯曲半径) 略大引起的额外费用,使得一个U型管换热器的成本比固定管板式换热器高。
该U型管设备的缺点是,该管的内侧不能有效地进行清洗,因为U型弯将需要灵活高端的钻轴来清洗,因此,U型管换热器不应使用于管内液体比较脏的场合。
浮头式浮头式换热器是最多种类型的壳管式换热器,也是最昂贵的。
在这个设计中,管板是相对固定的外壳,另一种是自由地“浮”在外壳上。
这允许自由膨胀的管束,以及管内外的清洗。
因此,浮头式换热器可用于管程和壳程流体比较脏的场合,使这个标准的设备类型在肮脏的环境下可以使用,例如在石油精炼厂。
浮头式结构有不同的类型。
两种最常见的是拉通(TEMA T)的后背设备和拉通(TEMA T)的设计。
TEMA S 的设计(图4)是在化学过程工业(CPI)的最常见的配置。
浮头盖是对浮动管板通过螺栓固定一个巧妙的分开支持环。
这个浮头法兰位置超出了外壳并在一直径较大的壳盖内。
拆换热器,先拆除壳盖,然后再分开支持环,然后浮动顶盖在管束可以静止结束后拆除。
在TEMA T设备中,整个管束,包括浮动磁头组件,可以移出平稳结束,因为外壳直径大于浮头法兰大。
浮头盖螺栓直接焊接到浮动管板以便于不分开支撑环。
这个设备的优点是管束可以从外壳上被移除而不用拆除外壳或者浮头盖,因此缩短了维修时间。
这种设计特别适合于U型管不能工作的地方,加热介质比较污浊的地方。
由于扩大了外壳,这个设备是成本最高的换热器形式。
图2. 固定管板式换热器图3. U型管换热器还有两种类型的包装浮头结构—外装填料式(TEMA P)和外装套环式(TEMA W)(见图1)。
然而,因为他们很容易泄漏,其使用仅限于壳液是无毒,无害并具有适度的压力和温度(40kg/cm2 和300℃)。
基于适用介质的分类基本上,介质可能是单相(如冷却或加热的液体或气体)或者两相(如冷凝或蒸发)。
由于双方有一个STHE,这可能导致几种组合的介质。
从广义上讲,服务可分类如下:·单相(包括壳程和管程);·冷凝(一边冷凝和其他单相);·汽化(一种汽化和另一边单相);·冷凝/蒸发(一边冷凝和另一边蒸发)。
下列通常用于:换热器:两边单相和过程流(即不实用)。
冷却器:过程流体和其他冷却水或空气。
加热器:过程流体和其他实用程序,如热蒸汽或热油。
冷凝器:一个冷凝蒸汽和冷却水或空气等。
冷水机组:过程是在流体分大气温度和沸腾的制冷剂或其他浓缩过程。
再沸器:从蒸馏塔和其他热点的公物(蒸汽或热油)或一个过程底流。
本文将具体侧重于单相的应用。
设计数据在讨论实际的散热设计之前,让我们看看数据,在设计开始之前必须通过过程提供数据:1.同时流量流。
2.同时进口和出口温度流。
3.操作两个压力来源。
这是必要的气体,尤其是如果不提供气体密度;它不是真的有必要为了液体,作为它们的物体与压力无关。
4.允许压降流。
这是一个非常重要的换热器设计参数。
一般而言,对于液体每个外壳为0.5-0.7kg/cm2 的允许值。
较高的压降一般为粘性液体,尤其是在管程。
对于气体,允许的值一般为0.05-0.2 kg/cm2 ,典型的为0.1 kg/cm2 。
5.污垢对于两个电阻流。
如果这是不得出,设计者应采取指定的TEMA标准或根据过去的经验。
6.物理性能平均流。
其中包括粘度,导热系数,密度,最好在两个入口和出口温度比热。
粘度数据必须提供进口和出口温度,特别是液体,因为随温度的变化可能会相当打,是不规则的(既不线性或对数)。
7.热负荷。
规定应该是壳程和管程保持一致。
8.换热器方式。
如果不能选择,设计者可以选择基于此如前所述的各类设备的特点。
事实上,设计师通常在一个更好的位置比工程师。
9.行的大小。
这是可以选取的,以配合喷嘴口径大小,以避免扩张器或缩影。
然而,对于喷嘴尺寸通常比标准的线路严格,特别是对壳程入口。
因此喷嘴大小有时必须是一个大小(或在特殊情况下甚至更多),比相应的线路,尤其是规模较大的线路。
10.首选管大小。
被指定为管外径尺寸“厚”的长度。
一些工厂的业主有一个首选外径的厚度(通常是基于库存的考虑),并可用绘图区将决定最高管长度。
许多使用者喜欢规范所有三个方面,是对库存的考虑。
11.最大壳程直径。
这是根据管束删除要求,由于起重机的能力有限。
这种限制只使用语带有可拆卸管束,即U型管和浮头交换。
对于固定管板式换热器,唯一的限制是制造商的制造能力,例如管尾和法兰。
因此,浮头换热器往往局限于外壳的I.D.的1.4-1.5米,和6米或9米长度的管,而固定管板换热器,管壳长度可以有高达3米,管长度可达12米或更大。
12.结构材料。
如果管和外壳都是相同的材料制成,则所有元件应该对这种材料。
因此,只有设计管壳材料需要更加以明确。
但是,如果外壳和管道是不同的材料,所有主要部件的材料应当指明,以避免任何含糊之处。
主要成分是外壳(壳盖),管,通道(通道盖),管板和挡板。
管板可能内衬或包装。
13.特殊的考虑。
这些包括运输,条件,物色新的营运情况,以及是否连续或间歇操作。
管程设计管程计算很简单,因为管程流代表了一个圆形管道流过简单的例子。
传热系数和压力降均与管程速度不同,后者也更强烈。
一个好的设计将在允许的压降尽其所用,因为这会产生更高的传热系数。
如果所有的管程流体流过了有的管(单通管),它会产生一定的速度。
通常情况下,这个速度是低的无法接受的,因此不得不增加速度。
通过在通道上设置分区板(包括适当的衬垫),使得管程流体流过管子综述的一小部分许多次。
因此,在换热器里有两百根管子和两个通道,流体一次流过一百根管子,如果只有一个通道换热器速度将变为两倍。
通道管的数量通常是一,二,四,六,八等。
传热系数管程的传热系数是一个雷诺数常数,普朗特常数和管径的函数。
这些可以被分解成一下的基本(即:物理特性粘度、热导率、比热);管径以及非常重要的最大速度。
液体粘度变化是相当可观的;因此这个物理性质对传热系数有戏剧性的影响。
对内管湍流传热的基本方程:0.80.330.027(Re)(Pr)u N = (1)a0.80.3(/)0.027(/)(/)h D k D G c k μμ= (1)b 整理得:0.80.33h = 0.027(DG/m)(cm/k)(k/D) (1)c粘度影响传热系数通过两种对立的方式,作为雷诺常数的一个参数,并作为普朗特常数的一个参数。
因此,来自Eq.1c:0.330.8h ()αμ- (2)a0.47h ()αμ- (2)b 换句话说,传热系数反比于粘度0.47倍。
同样,传热系数正比于导热系数0.67倍。
这两个现象导致一些关于热量转移的有趣共性。
高导热促进更高的传热系数。
因此,冷却水(导热系数约为0.55千卡/h ·m ·℃)有一个极高的传热系数通常有6000千卡/h ·m 2·℃,其次是碳氢化合物(导热系数介于0.08至0.12千卡/h ·m ·℃)250-1300千卡/h ·m 2·℃,然后烃气体(导热系数 0.02至0.03千卡/h ·m ·℃)在50-500千卡/h ·m 2·℃。
氢是一种不寻常的气体,因为它有一个特别的优良的热传导性(比碳氢化合物液体的好)。
因此,它是的传热系数是油气液体的范围的上限。
图4.通过浮头式换热器的支持设备(TEMA S )图5.通过浮头换热器(TEMA T)传热系数的范围相当大的油气是由于液体的粘度发生大的变化,由少于0.1cP对乙烯和丙烯,超过1000或更多的cP沥青。
传热系数变化大的碳氢化合物气体归因于操作压力的变化大。
操作压力上升时,气体密度增大。
压降正比于第二基本形式模长平方的质量成反比的速度和密度。
因此,出于同样的压降,高速可以维持较高的密度。