煤中硫的脱除技术
煤中硫的脱除方法
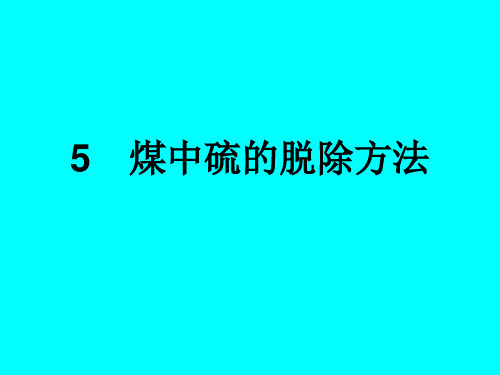
6.2 用水溶液中的氧气氧化以脱除煤中黄铁矿硫的方法
曾有人广泛进行了用空气或氧气在煤的燃点以下的多种温度下对 煤氧化的研究,测定了在最低达 70℃的多种温度下,煤有机基体的 氧化速度,在这种反应中,开始时生成过氧化物的络合物,随后生成 较稳定的碳和氧的化合物如苯酚和羰基化合物。 温度再高时将引起分 解,生成一氧化碳、二氧化碳和水,大约从 200℃开始就迅速失重。
6.1.1 原理
在梅耶斯方法中, 硫酸高铁的水溶液有选择性地氧化煤中的黄铁 矿,形成元素硫和硫酸亚铁。硫酸亚铁能溶解在水中,元素硫则可通 过水蒸汽蒸发、真空蒸发或溶剂萃取从煤中除去,而氧化剂可以再生 并循环使用。反应式如下: Fe3++H2O+FeS2→Fe2++SO42 +H++S
-
Fe2++O2 +2H+→Fe3++2H2O 含有低价和高价两种状态的铁的水萃取液, 可以用空气或氧气把 亚铁离子氧化成高铁离子而得到再生。 这个体系的一个优点是用铁来 除去铁,因此,必要时,只需把浸提溶液的一部分加以处理,以便去 除积蓄的铁。
5.1.2 煤的电选脱硫 (1)煤的摩擦静电选脱硫 下图是煤的摩擦静电选脱硫的装置示意图。待选微粉煤在高速 气流的夹带下,进入摩擦带电器,待选微粉煤由于与摩擦材料间以 及颗粒相互间的碰撞、摩擦,其中的煤颗粒与矿物质颗粒(包括硫 铁矿颗粒)分别带上了电性相反的正电荷与负电荷,因此,待选微 粉煤在从摩擦器喷出进入到具有强电场的正负极板之间时,带正电 的煤颗粒就进入负极板的集尘器,而带负电的矿物质就进入正极板 的集尘器,从而被分开。
已证明煤的煤化程度对煤的氧化速度起着重要作用, 煤化程度较 高的煤,一般氧化较慢,而煤化程度较低的煤,一般氧化较快。天然 存在于煤中的可溶性硫酸铁能很快地溶解在水中, 可成为氧气氧化黄 铁矿的载体。这一点已为形成酸性矿井水的机理研究所证明,并为同 时发生的黄铁矿浸提液的 Fe3+再生的研究所证明。因此,用水溶液中 的氧气或空气氧化煤中的黄铁矿,可能是一种 Fe3+氧化法,其实质与 上一节中讨论过的同时发生的黄铁矿浸提和硫酸铁再生的研究 (梅耶 斯法)完全相同。 用水溶液中的氧气脱除煤中黄铁矿一般有常压法、 加压法和细菌 催化氧气处理法三种。
煤的脱硫
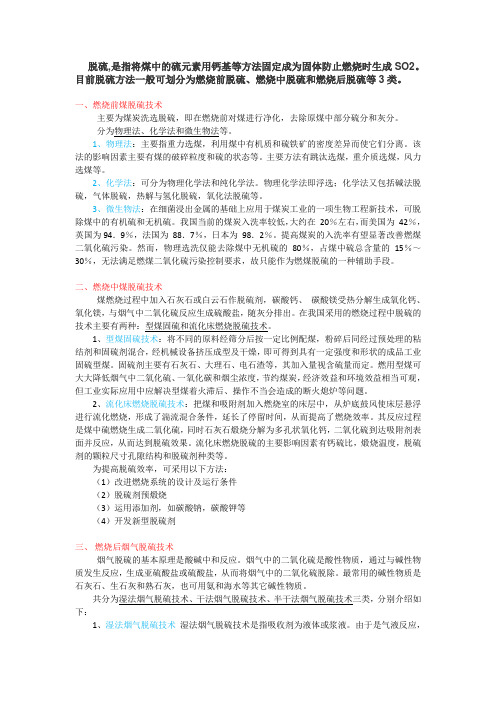
脱硫,是指将煤中的硫元素用钙基等方法固定成为固体防止燃烧时生成SO2。
目前脱硫方法一般可划分为燃烧前脱硫、燃烧中脱硫和燃烧后脱硫等3类。
一、燃烧前煤脱硫技术主要为煤炭洗选脱硫,即在燃烧前对煤进行净化,去除原煤中部分硫分和灰分。
分为物理法、化学法和微生物法等。
1、物理法:主要指重力选煤,利用煤中有机质和硫铁矿的密度差异而使它们分离。
该法的影响因素主要有煤的破碎粒度和硫的状态等。
主要方法有跳汰选煤,重介质选煤,风力选煤等。
2、化学法:可分为物理化学法和纯化学法。
物理化学法即浮选;化学法又包括碱法脱硫,气体脱硫,热解与氢化脱硫,氧化法脱硫等。
3、微生物法:在细菌浸出金属的基础上应用于煤炭工业的一项生物工程新技术,可脱除煤中的有机硫和无机硫。
我国当前的煤炭入洗率较低,大约在20%左右,而美国为42%,英国为94.9%,法国为88.7%,日本为98.2%。
提高煤炭的入洗率有望显著改善燃煤二氧化硫污染。
然而,物理选洗仅能去除煤中无机硫的80%,占煤中硫总含量的15%~30%,无法满足燃煤二氧化硫污染控制要求,故只能作为燃煤脱硫的一种辅助手段。
二、燃烧中煤脱硫技术煤燃烧过程中加入石灰石或白云石作脱硫剂,碳酸钙、碳酸镁受热分解生成氧化钙、氧化镁,与烟气中二氧化硫反应生成硫酸盐,随灰分排出。
在我国采用的燃烧过程中脱硫的技术主要有两种:型煤固硫和流化床燃烧脱硫技术。
1、型煤固硫技术:将不同的原料经筛分后按一定比例配煤,粉碎后同经过预处理的粘结剂和固硫剂混合,经机械设备挤压成型及干燥,即可得到具有一定强度和形状的成品工业固硫型煤。
固硫剂主要有石灰石、大理石、电石渣等,其加入量视含硫量而定。
燃用型煤可大大降低烟气中二氧化硫、一氧化碳和烟尘浓度,节约煤炭,经济效益和环境效益相当可观,但工业实际应用中应解决型煤着火滞后、操作不当会造成的断火熄炉等问题。
2、流化床燃烧脱硫技术:把煤和吸附剂加入燃烧室的床层中,从炉底鼓风使床层悬浮进行流化燃烧,形成了湍流混合条件,延长了停留时间,从而提高了燃烧效率。
脱硫技术分为燃烧前煤脱硫, 燃烧中煤脱硫
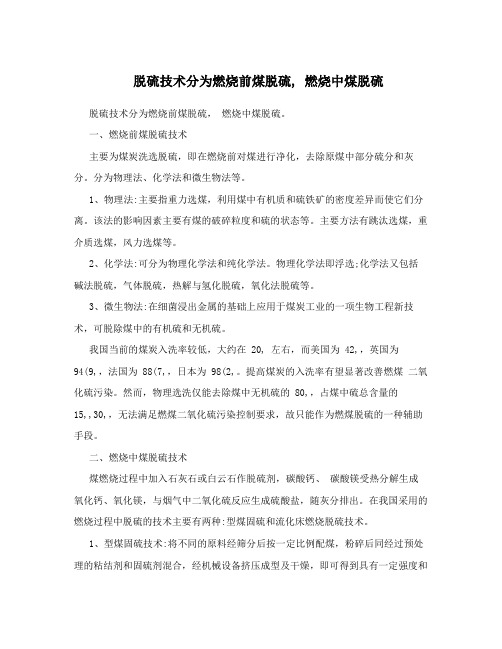
煤燃烧过程中加入石灰石或白云石作脱硫剂,碳酸钙、 碳酸镁受热分解生成氧化钙、氧化镁,与烟气中二氧化硫反应生成硫酸盐,随灰分排出。在我国采用的燃烧过程中脱硫的技术主要有两种:型煤固硫和流化床燃烧脱硫技术。
1、型煤固硫技术:将不同的原料经筛分后按一定比例配煤,粉碎后同经过预处理的粘结剂和固硫剂混合,经机械设备挤压成型及干燥,即可得到具有一定强度和形状的成品工业固硫型煤。固硫剂主要有石灰石、大理石、电石渣等,其加入量视含硫量而定。燃用型煤可大大降低烟气中二氧化硫、一氧化碳和烟尘浓度,节约煤炭,经济效益和环境效益相当可观,但工业实际应用中应解决型煤着火滞后、操作不当会造成的断火熄炉等问题。
2、流化床燃烧脱硫技术:把煤和吸附剂加入燃烧室的床层中,从炉底鼓风使床层悬浮进行流化燃烧,形成了湍流混合条件,延长了停留时间,从而提高了燃烧效率。其反应过程是煤中硫燃烧生成二氧化硫,同时石灰石煅烧分解为多孔状氧化钙,二氧化硫到达吸附剂表面并反应,从而达到脱硫效果。流化床燃烧脱硫的主要影响因素有钙硫比,煅烧温度,脱硫剂的颗粒尺寸孔隙结构和脱ቤተ መጻሕፍቲ ባይዱ剂种类等。为提高脱硫效率,可采用以下方法:
(1)改进燃烧系统的设计及运行条件
(2)脱硫剂预煅烧
(3)运用添加剂,如碳酸钠,碳酸钾等
(4)开发新型脱硫剂
三、 燃烧后烟气脱硫技术
烟气脱硫的基本原理是酸碱中和反应。烟气中的二氧化硫是酸性物质,通过与碱性物质发生反应,生成亚硫酸盐或硫酸盐,从而将烟气中的二氧化硫脱除。最常用的碱性物质是石灰石、生石灰和熟石灰,也可用氨和海水等其它碱性物质。共分为湿法烟气脱硫技术、干法烟气脱硫技术、半干法烟气脱硫技术三类,分别介绍如下:
3、干法烟气脱硫技术
干法采用固体粉末或颗粒为吸附剂,干法脱硫后烟气仍具有较高的温度(100?),排出后易扩散。主要有炉内喷钙法和活性炭法。由于炉内喷钙法的吸收剂及反应原理与湿法有些相似,这里不再详述,只介绍一下活性炭法。
脱硫的常见方式
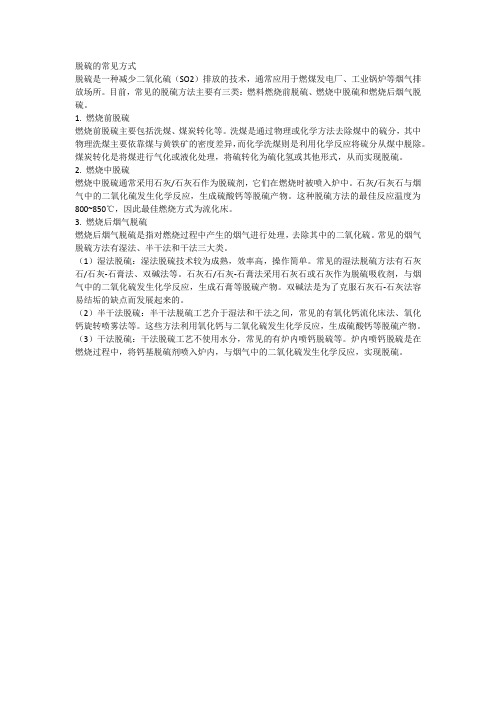
脱硫的常见方式脱硫是一种减少二氧化硫(SO2)排放的技术,通常应用于燃煤发电厂、工业锅炉等烟气排放场所。
目前,常见的脱硫方法主要有三类:燃料燃烧前脱硫、燃烧中脱硫和燃烧后烟气脱硫。
1. 燃烧前脱硫燃烧前脱硫主要包括洗煤、煤炭转化等。
洗煤是通过物理或化学方法去除煤中的硫分,其中物理洗煤主要依靠煤与黄铁矿的密度差异,而化学洗煤则是利用化学反应将硫分从煤中脱除。
煤炭转化是将煤进行气化或液化处理,将硫转化为硫化氢或其他形式,从而实现脱硫。
2. 燃烧中脱硫燃烧中脱硫通常采用石灰/石灰石作为脱硫剂,它们在燃烧时被喷入炉中。
石灰/石灰石与烟气中的二氧化硫发生化学反应,生成硫酸钙等脱硫产物。
这种脱硫方法的最佳反应温度为800~850℃,因此最佳燃烧方式为流化床。
3. 燃烧后烟气脱硫燃烧后烟气脱硫是指对燃烧过程中产生的烟气进行处理,去除其中的二氧化硫。
常见的烟气脱硫方法有湿法、半干法和干法三大类。
(1)湿法脱硫:湿法脱硫技术较为成熟,效率高,操作简单。
常见的湿法脱硫方法有石灰石/石灰-石膏法、双碱法等。
石灰石/石灰-石膏法采用石灰石或石灰作为脱硫吸收剂,与烟气中的二氧化硫发生化学反应,生成石膏等脱硫产物。
双碱法是为了克服石灰石-石灰法容易结垢的缺点而发展起来的。
(2)半干法脱硫:半干法脱硫工艺介于湿法和干法之间,常见的有氧化钙流化床法、氧化钙旋转喷雾法等。
这些方法利用氧化钙与二氧化硫发生化学反应,生成硫酸钙等脱硫产物。
(3)干法脱硫:干法脱硫工艺不使用水分,常见的有炉内喷钙脱硫等。
炉内喷钙脱硫是在燃烧过程中,将钙基脱硫剂喷入炉内,与烟气中的二氧化硫发生化学反应,实现脱硫。
煤脱硫原理

煤脱硫原理
煤是一种重要的能源资源,然而燃烧煤炭会产生大量的二氧化硫等有害气体,对环境造成严重污染。
因此,煤脱硫技术的研究和应用显得尤为重要。
煤脱硫是指通过化学或物理方法,将煤中的硫元素去除或转化为无害物质的过程。
下面将介绍几种常见的煤脱硫原理。
一、燃煤脱硫原理。
燃煤脱硫是指在燃煤过程中,通过添加脱硫剂或改变燃烧条件,使煤中的硫氧化物转化为易溶于水的硫酸盐或硫酸氢盐,从而达到脱硫的目的。
常用的脱硫剂有石灰石、石膏等。
脱硫剂与煤燃烧产生的硫氧化物发生化学反应,生成硫酸盐或硫酸氢盐,然后通过烟气净化设备进行分离和收集,最终实现燃煤脱硫。
二、湿法煤脱硫原理。
湿法煤脱硫是指将煤炭浸泡在脱硫剂溶液中,通过化学反应或物理吸附等方式将煤中的硫去除的方法。
湿法脱硫工艺具有脱硫效率高、操作简单等优点,广泛应用于燃煤电厂和工业锅炉等领域。
常见的湿法脱硫工艺有石灰石法、石膏法、氧化法等。
三、干法煤脱硫原理。
干法煤脱硫是指在煤的颗粒表面喷洒脱硫剂,通过化学反应或物理吸附等方式将煤中的硫去除的方法。
干法脱硫工艺具有设备简单、操作方便等优点,适用于一些小型燃煤锅炉和工业炉窑。
常见的干法脱硫工艺有喷雾法、流化床法等。
总之,煤脱硫技术是解决煤炭燃烧产生的硫氧化物污染的关键技术之一。
随着环保意识的增强和环保政策的不断加强,煤脱硫技术的研究和应用将会越来越受到重视,为减少大气污染、改善环境质量发挥着重要作用。
希望通过不断的研究和创
新,能够开发出更加高效、环保的煤脱硫技术,为人类创造一个更加清洁、美丽的家园。
煤的脱硫
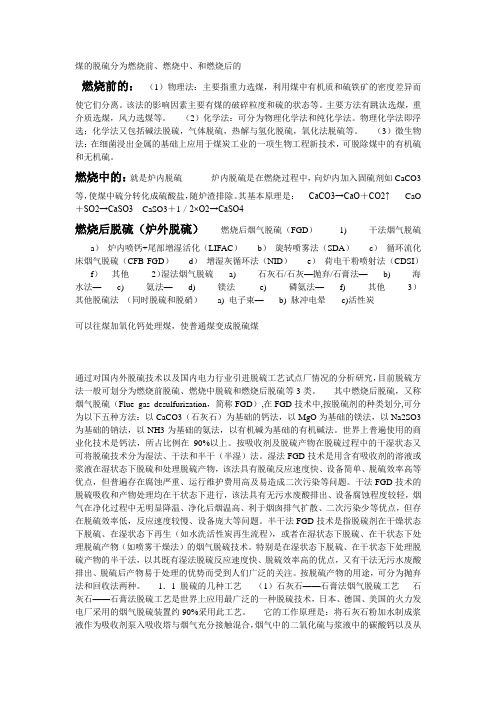
煤的脱硫分为燃烧前、燃烧中、和燃烧后的燃烧前的: (1)物理法:主要指重力选煤,利用煤中有机质和硫铁矿的密度差异而使它们分离。
该法的影响因素主要有煤的破碎粒度和硫的状态等。
主要方法有跳汰选煤,重介质选煤,风力选煤等。
(2)化学法:可分为物理化学法和纯化学法。
物理化学法即浮选;化学法又包括碱法脱硫,气体脱硫,热解与氢化脱硫,氧化法脱硫等。
(3)微生物法:在细菌浸出金属的基础上应用于煤炭工业的一项生物工程新技术,可脱除煤中的有机硫和无机硫。
燃烧中的:就是炉内脱硫 炉内脱硫是在燃烧过程中,向炉内加入固硫剂如CaCO3等,使煤中硫分转化成硫酸盐,随炉渣排除。
其基本原理是: CaCO3→CaO+CO2↑ CaO +SO2→CaSO3 CaSO3+1/2×O2→CaSO4燃烧后脱硫(炉外脱硫) 燃烧后烟气脱硫(FGD) 1) 干法烟气脱硫a)炉内喷钙+尾部增湿活化(LIFAC) b)旋转喷雾法(SDA) c)循环流化床烟气脱硫(CFB-FGD) d)增湿灰循环法(NID) e)荷电干粉喷射法(CDSI) f)其他 2)湿法烟气脱硫 a) 石灰石/石灰—抛弃/石膏法— b) 海水法— c) 氨法— d) 镁法--- e) 磷氨法— f) 其他 3)其他脱硫法(同时脱硫和脱硝) a) 电子束— b) 脉冲电晕 c)活性炭可以往煤加氧化钙处理煤,使普通煤变成脱硫煤通过对国内外脱硫技术以及国内电力行业引进脱硫工艺试点厂情况的分析研究,目前脱硫方法一般可划分为燃烧前脱硫、燃烧中脱硫和燃烧后脱硫等3类。
其中燃烧后脱硫,又称烟气脱硫(Flue gas desulfurization,简称FGD),在FGD技术中,按脱硫剂的种类划分,可分为以下五种方法:以CaCO3(石灰石)为基础的钙法,以MgO为基础的镁法,以Na2SO3为基础的钠法,以NH3为基础的氨法,以有机碱为基础的有机碱法。
世界上普遍使用的商业化技术是钙法,所占比例在90%以上。
煤脱硫的工艺流程

煤脱硫的工艺流程
《煤脱硫工艺流程》
煤脱硫是指将煤中的硫化物去除,以减少燃烧过程中产生的二氧化硫排放,保护环境。
煤脱硫的工艺流程一般包括物理方法和化学方法两种。
物理方法主要包括洗煤、重介质选矿和干法除硫等。
其中,洗煤是指采用物理化学方法去除煤中的杂质,包括硫、灰、杂质矿物质等。
通过洗煤,可以将煤中的硫化物大幅度减少,从而达到脱硫的效果。
重介质选矿是通过重力分选的方法,将煤中的硫化物和其他杂质去除,通过洗选后的煤可获得更干净的煤质。
干法除硫是指在煤的加工过程中,通过物理方法去除煤中的硫化物,包括干法磨矿、干法磨煤、干法除灰等。
这些方法主要适用于煤中硫含量较低的情况。
化学方法主要包括石灰石石膏法、碱性土治理法、氧化法等。
其中,石灰石石膏法是通过向煤燃烧过程中加入石灰石和石膏,将煤中的硫化物转化为不易挥发的石膏,从而达到脱硫的目的。
碱性土治理法是通过在煤的加工过程中加入一定量的碱性土,将煤中的硫化物与碱性土中的碱反应,形成不易挥发的化合物,从而实现脱硫。
氧化法则是通过氧化剂对煤中的硫化物进行氧化反应,将其转化为不易挥发的化合物,实现脱硫。
总的来说,煤脱硫工艺流程既可以采用物理方法,也可以采用化学方法,具体选择哪种工艺流程取决于煤的性质和硫含量。
随着环境保护要求的不断提高,对煤脱硫技术的研究和应用也将会越来越重要。
煤气脱硫方法

煤气脱硫方法介绍煤气脱硫是一种常用的煤气净化方法,能够有效去除煤气中的硫化物。
本文将介绍煤气脱硫的方法原理、常用的脱硫方法以及各种方法的适用范围和优缺点。
方法原理煤气脱硫的目的是去除煤气中的二氧化硫等硫化物,因为这些硫化物会对环境和人体健康造成严重危害。
脱硫的方法基本原理是通过吸收、吸附、化学反应等方式将硫化物转化或捕获成不易挥发或易处理的物质,从而达到脱硫的效果。
常用的脱硫方法以下是几种常用的煤气脱硫方法:1. 湿法脱硫湿法脱硫是利用液体吸收剂吸收硫化物的方法。
常用的湿法脱硫方法有以下几种:- 法拉第吸收法:通过将煤气通入吸收液中,利用法拉第定律实现硫化物的吸收。
- 碱液吸收法:使用氨水等碱性液体吸收硫化物,形成稳定的硫酸盐。
- 氧化吸收法:将煤气与氧化剂接触,在气液界面进行氧化反应,使硫化物转化为硫酸盐。
2. 干法脱硫干法脱硫是利用固体吸附剂和化学反应物直接与煤气中的硫化物发生作用,实现脱硫的方法。
常用的干法脱硫方法有以下几种: - 金属氧化物脱硫法:利用金属氧化物(如氧化铁、氧化锌)吸附和催化气相硫化物的氧化反应。
- 硫化物氧化法:利用氧化剂将硫化物氧化为硫酸盐或硫酸,达到脱硫的效果。
3. 生物脱硫生物脱硫是利用特定微生物菌种对煤气中的硫化物进行氧化还原反应,实现脱硫的方法。
生物脱硫具有环保、经济、高效的特点,逐渐得到重视和应用。
脱硫方法的适用范围和优缺点不同的脱硫方法在适用范围和优缺点上有所区别,下面将分别介绍:湿法脱硫•适用范围:湿法脱硫适用于高硫煤气、高温、高湿度、高粉尘含量的煤气净化。
•优点:脱硫效率高,脱硫剂可以循环使用。
•缺点:设备复杂,操作成本高,产生大量废水。
干法脱硫•适用范围:干法脱硫适用于低硫煤气、低温、低湿度、低粉尘含量的煤气净化。
•优点:设备简单,操作成本低。
•缺点:脱硫效率相对较低,吸附剂需要周期性更换。
生物脱硫•适用范围:生物脱硫适用于中低硫煤气。
•优点:对煤气成分适应性强,脱硫效率高,操作成本低。
- 1、下载文档前请自行甄别文档内容的完整性,平台不提供额外的编辑、内容补充、找答案等附加服务。
- 2、"仅部分预览"的文档,不可在线预览部分如存在完整性等问题,可反馈申请退款(可完整预览的文档不适用该条件!)。
- 3、如文档侵犯您的权益,请联系客服反馈,我们会尽快为您处理(人工客服工作时间:9:00-18:30)。
煤中硫的脱除技术煤中硫的脱除技术煤炭是世界上最丰富的化石燃料资源,占世界化石燃料贮量的70%以上。
目前煤炭约占世界一次能源消费的30%,按世界能源会议预测,煤炭作为一次能源的重要组成部分的地位将在相当长时间内不会改变,预计2020 年煤炭将占世界一次能源消费的33.7%。
中国是煤炭生产和消费大国,目前煤炭提供了我国一次能源的75%,在可预见的未来几十年内,煤炭仍将是我国主要的一次能源[1]。
煤炭作为能源对人类的发展作出了巨大的贡献,但在煤炭的开发与利用过程中也产生了一系列污染问题,尤其是燃烧过程中所产生的烟气产生的可见及潜在的危害,危及生态平衡与人类生存。
全球性的4大公害:大气烟尘、酸雨、温室效应、臭氧层破坏,随着经济快速发展已经严重影响人类的生存条件。
大气污染与能源生产和利用有着直接的关系,尤其是煤炭的开发利用是烟尘、酸雨和温室效应的主要根源,臭氧层的破坏亦和煤炭开采过程中的排放甲烷(CH4)有很大关系。
其实,煤和天然气、石油一样,其本身并非污染源,只是由于洁净利用和转化技术的落后才使得以煤炭为主要能源的国家环境污染严重,煤直接燃烧带来的环境问题至今无有效根治的方法[2]。
因此,解决煤炭利用率低下、污染严重的根本途径就是合理、清洁、高效地利用煤炭资源,大力开发和应用洁净煤技术错误!未找到引用源。
,讨论并分析烟气净化技术是非常重要及必要的。
1.1煤炭利用对环境的影响煤炭在利用过程中促进了我国经济的快速增长,但是煤炭利用的效率比较低,对环境造成了一定的负面影响。
屈小娥对中国1990-2009年的环境污染进行评价,选取工业SO2排放量、工业烟尘排放量、工业粉尘排放量等污染指标,发现以煤为主的能源消费结构在支撑经济发展的同时,也带来了严重的环境污染[3]。
多数学者研究煤炭利用对大气环境的影响。
有的学者从定性的角度进行研究。
董雪玲、刘大锰认为燃煤排放的烟尘中含有大量潜在的危害物质,尤其是粒径小于10?m的可吸入颗粒物,会降低大气能见度,进而污染大气环境[4]。
路忠贤、唐永顺认为煤炭在开采过程中会产生大量的煤尘和粉尘,在燃烧过程中排放的有害气体会对大气环境造成污染[5]。
许瑞林、王体健认为江苏省的大气污染是烟煤型污染,并对江苏的城市空气质量进行统计,认为污染物按其负荷大小排序依次为降尘量、总悬浮微粒、SO2和NOX[6]。
孙楠认为煤炭利用会导致二氧化碳的浓度增加,使得全球气候发生变化[7]。
刘海滨、郭正权认为二氧化碳排放的增加需要我国加强对煤炭资源的利用[8]。
1.2煤中硫脱除技术概述1.2.1必要性除约一半用于发电外,中国煤炭的近30%用于工业锅炉,6%用于民用燃烧。
罗娇赢即提出我国煤炭利用是以直接燃烧为主,燃煤产生了大量的烟尘、SO2、CO2、NOX 等有害的污染气体[9],对大气环境造成严重的污染。
据《中国环境状况公报2013》报道,2013年,473个监测降水的城市中,出现酸雨的城市比例为44.4%,酸雨频率在25%以上的城市比例为27.5%。
其中,降水pH年均值低于5.6(酸雨)、低于5.0(较重酸雨)和低于4.5(重酸雨)的城市比例分别为29.6%、15.4%和2.5%。
全国酸雨分布区域集中在长江沿线及中下游以南,主要包括江西、福建、湖南、重庆的大部分地区,以及长三角、珠三角和四川东南部地区。
酸雨区面积约占国[10]土面积的10.6%。
中国酸雨为硫酸型,燃煤电厂等以高架源形式排放的SO2可以随大气扩散传输到较远的大方,并形成酸雨。
大量高硫煤燃烧是西南及中南地区酸雨污染严重的主要原因。
酸雨对环境的危害包括森林退化湖泊酸化,鱼类死亡,水生生物物种群减少,农田土壤酸化,贫瘠,有毒重金属污染增强,粮食、蔬菜、瓜果大面积减产,建筑物、桥梁和文物损坏等。
1.2.2充分性控制SO2排放的技术主要可分为,燃烧前脱硫(洗煤技术)、燃烧中脱硫(炉内固硫)和燃烧后脱硫(烟气脱硫,Flue Gas Desulfurization, FGD)。
燃烧前脱硫,可去除煤中大部分的无机硫,但对有机硫却无能为力,与其他脱硫技术结合使用,才能使SO2的排放达到环保要求;燃烧中脱硫,可简化净化操作工艺,提高热利用效率,但脱硫效率较低,粉尘排放增加,且固硫生成的硫酸盐会在粉煤锅炉的高温下发生分解;燃烧后烟气脱硫,技术相对成熟、稳定、高效,是目前控制大气中SO2排放有效和应用最广的一项脱硫技术[11]。
2煤中硫燃前脱除技术在煤的燃烧或转化之前就将煤中的硫组分通过某种方法分离出去,这样就可以降低燃烧过程中硫分的含量,从而减少煤燃烧产生的二氧化硫污染。
采用的方法分别有物理方法、化学方法和微生物方法。
2.1物理脱硫技术至今为止,物理脱硫技术是唯一工业化的煤炭净化方法,我国广泛采用的跳汰法、重介质选煤法和浮选法都是属于物理净化法。
把产品与废渣分离的分选过程是煤炭物理净化的中心环节。
用物理法可以从原煤中除去泥土,页岩和黄铁矿硫。
通过煤的粉碎,使非化学键结合的不纯物质与煤脱离。
继而,利用构成煤的有机(煤的基本微观结构)与密度较大的矿物不纯物之间的比重的不同,有时还可利用二者表面润湿性、磁性、导电性的不同分离之。
主要方烤有:现代浮选法、重液体富集法、磁性分离法、静电分离法、凝聚法、细粒煤一重介质旋风分离法等。
图煤炭物理净化系统2.2化学脱硫技术化学脱硫[12]技术主要是利用强碱、强酸和强氧化剂通过化学还原、氮抽提、热解等步骤来完成煤中硫的脱除,常用的如Meyers方法、CaCl2氧化法、NaOH熔融法、(NH)40H 法以及H2O2氧化法等,尽管化学法可以脱去煤中几乎所有的无机硫和许多有机硫,但存在工艺条件复杂和成本高等问题,有时需要在一定的酸碱条件下进行,有时甚至需要在高温下进行。
对炼焦煤而言,对煤的性质影响较大,如引起煤的粘结性变差和发热量降低等。
目前仅限于实验室研究。
2.3生物脱硫技术微生物脱硫的原理是利用某些嗜酸耐热菌在生长过程中消化吸收Fe3+和So等特性,从而促进黄铁矿氧化分解与脱除,硫的脱除率在90%以上[13],微生物脱硫方法主要有堆浸法、表面氧化法、浸出法等方法。
但脱硫反应时间长,难以适应工业化脱硫的需要。
与物理和化学法相比,微生物法投资少,运行成本低,能好少,可专一性地除去极细微分布于煤中的硫化物。
2.4总结物理化学和微生物脱硫三种方法中广泛用于工业的是物理法,其成本低;微生物法已引起国内外广泛的关注,但是用于工业依旧需要不少时间的技术研究开发;化学法则是用于实验室更常见。
在今后的发展中,根据不同的煤质进行三种方法的有效结合,我觉得会是一种不错的发展方向。
3炉内脱硫技术该工艺原理是燃料和作为吸收剂的电石粉同时送入燃烧室,气流使燃料颗粒、电石粉和灰一起在循环流化床强烈扰动并充满燃烧室,电石粉在燃烧室内裂解成氧化钙,氧化钙和二氧化硫结合成硫酸钙,锅炉燃烧室温度应控制在850-900℃左右,以实现反应最佳。
一般使用循环流化床(CFB),其原理是燃料和脱硫剂由炉膛侧墙燃烧室下部给入,一次风穿过炉膛底部布风板给入,二次风侧墙燃烧室中部给入,煤粒和空气强烈混合形成“流态化”燃烧,炉膛出口安装旋风分离器和返料装置,将分离下来的物料返回炉膛燃烧,实现物料循环,使燃烧和脱硫的时间延长,达到充分燃烧和脱硫的目的,烟气送入尾部受热面与煤粉炉一样[14]。
循环流化床炉内燃煤脱硫过程主要的反应是CaCO3分解和CaO与SO2的硫化反应。
CaCO3分解的情况将直接影响脱硫剂的活性,最终影响脱硫的效果。
目前在石灰石的煅烧分解研究中,分解过程究竟受何种化学反应机理控制以及怎样控制还没有确定的结论。
4燃后(烟气)脱硫原理与技术4.1概述烟气脱硫工艺可分为湿法、干法和半干法三种类型。
湿法脱硫是用液体吸收剂洗涤烟气,吸收烟气中的SO2;干法脱硫是以固态的粉状或粒状的吸收剂、吸附剂或催化剂脱除烟气中的SO2;半干法是介于湿法和干法之间的脱硫方法[15]。
下面主要介绍几种工业化应用较多及近年研究利用的新型烟气脱硫技术。
4.2几种烟气脱硫工艺4.2.1石灰石/石灰-石膏湿法工艺石灰石/石灰-石膏法是湿法烟气脱硫技术的代表性工艺,在工业应用最为广泛[16]。
该技术使用石灰石或石灰浆液在湿式洗涤器中吸收烟气中的SO2,发生的主要反应为:石灰法:SO2 + CaO + H2O → CaSO3H2O,2211石灰石法:SO2 + CaCO3 + H2O → CaSO32O + CO2,反应后的料液鼓入空气,将2211CaSO3氧化为CaSO4,生成副产物石膏[17]。
该工艺具有原料来源丰富、成本低廉、运行可靠、操作简单、钙利用率高( />90%)和脱硫效率高( />90%)等优点,在目前工业脱硫装置中占到85%。
该工艺副产的石膏可以进行有效利用以避免二次污染[18]。
为了促进SO2的吸收和石灰石的溶解,可以使用添加剂进行改善,以提高其脱硫率,减少石灰石用量,降低钙硫比。
廉价易得的有机酸盐为添加剂[19]的硫化实验表明,有机酸或对应的钠盐强化石灰石/石灰-石膏法,脱硫率被明显提高,稳定运行时间具有较大延长,增加了浆液的吸收容量。
液气比是影响脱硫系统性能的一个重要参数,它可以影响石灰石-石膏湿法脱硫过程脱硫率、浆液中石灰石含量及浓度等,杜谦等[20]利用并流有序降膜式湿法脱硫装置进行了液气比对石灰石-石膏湿法脱硫过程脱硫率的研究,认为在同一液气比下,脱硫率沿高度方向上升,且脱硫率的上升速率沿高度方向下降;在不同液气比下,脱硫率随液气比增加而增大。
4.2.2海水脱硫工艺海水脱硫工艺是利用天然海水脱除烟气中SO2的一种湿法烟气脱硫方法,其原理是烟气中SO2被海水吸收并在洗涤液中发生水解和氧化,然后,洗涤液被引入曝气池,提高pH值以抑制SO2气体的溢出,曝气池中鼓入空气,使SO32-被氧化成SO4 2-。
海水脱硫工艺在达到脱硫目的的同时还能满足排放标准,对海洋环境影响较小,因此,为沿海企业进行海水脱硫提供了便利。
海水脱硫主要工艺流程中国海洋大学王庆璋等[21]自主开发的利用碱厂废弃物白泥(主要成分CaCO3和Mg(OH)2)以及电厂半干法烟气脱硫废灰(主要成分Ca(OH)2和CaSO3O)作为增碱度22海水脱硫助剂,脱除烟气中SO2的工艺,脱硫后海水经自然曝气氧化或经综合处理池曝气净化达标排放标准。
该工艺SO2吸收速度快,海水用量少,无二次污染,适用于不同含硫量的煤,以废治废的该工艺明显优于其它海水脱硫工艺。
黄宗汉[22]也通过探讨的深圳西部电厂4号机组(300Mw)海水脱硫系统烟气海水脱硫工艺的实践经验,充分吸取国外设计及国内外运行经验的基础上,进一步对装置进行改进和提高,为电厂的环境保护事业做出更大贡献。
其中,提出海水脱硫工艺的进一步改进方向:曝气池面积的进一步减缩约20%左右;吸收塔向小型化靠近;取消旁路挡板甚至不设旁路烟道,以保证在机组运行时必须运行脱硫系统,或者定期切换旁路挡板,以保证挡板的灵活和可靠性。