第2章机械零部件设计中的强度与耐磨性43页PPT
合集下载
机械基础教材第二章 强度与刚度知识ppt课件
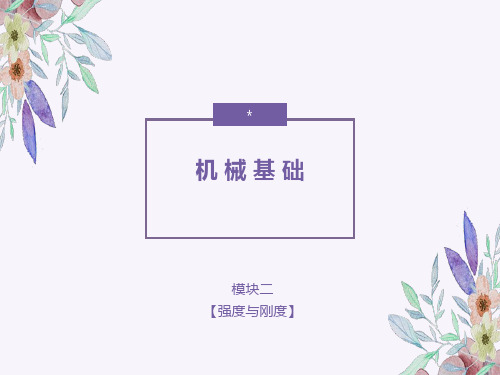
17
§2.2 拉伸和压缩时材料的力学性质 二、铸铁拉伸与压缩时的力学性能
特点:没有“屈服”和“颈缩”现象,Rm很低; 铸铁的抗压强度远大于抗拉强度; 宜作承压材料,不宜作拉杆材料。
18
§2.2 拉伸和压缩时材料的力学性质
三、塑性与冷作硬化
1.塑性
塑性是材料抵抗永久变形而不断裂的能力。工程中常用的塑性指标是断
件的左端为对象,列平衡方程为FN-F=0,则内力FN=F,如图(b)所示。
F
F
F
FN
(a)
(b)
5
§2.1 直杆轴向拉伸与压缩时的变形与应力分析 (3)应力 杆件在外力作用下,单位面积上的内力称为应力。
拉压杆横截面上各点处只产生正应力,且正应力在截面上均匀分布 。
F
FN
A
FN
——轴向拉压杆横截面上正应力的计算公式。 式中:
max
FN A
150 103
1570
MPa
95.5 MPa﹤ 所以斜拉杆 C 的D 强度足够。
31
§2.3 直杆轴向拉伸和压缩时的强度计算 五、应力集中与温差应力 1.应力集中 局部应力显著增大的现象:应力集中,使零件破坏危险性增加。
32
§2.3 直杆轴向拉伸和压缩时的强度计算 2.温差应力 由于温度变化,结构或构件产生伸或缩,而当伸缩受到限制时,结构或 构件内部便产生应力,称为温差应力或热应力。 工业生产中输送高压蒸汽的管道要设置膨胀节,以避免受温度变化影响。
二、内力与应力 (1)内力
杆件所受其他物体的作用力都称为外力,包括主动力和约束力。在外力 作用下,杆件发生变形,杆件材料内部产生阻止变形的抗力,这种抗力称为 内力(。2)截面法
将受外力作用的杆件假想地切开,用以显示内力的大小。并以平衡条件 确定其合力的方法称为截面法。如下图(a)所示,假想将杆件切开,选取杆
§2.2 拉伸和压缩时材料的力学性质 二、铸铁拉伸与压缩时的力学性能
特点:没有“屈服”和“颈缩”现象,Rm很低; 铸铁的抗压强度远大于抗拉强度; 宜作承压材料,不宜作拉杆材料。
18
§2.2 拉伸和压缩时材料的力学性质
三、塑性与冷作硬化
1.塑性
塑性是材料抵抗永久变形而不断裂的能力。工程中常用的塑性指标是断
件的左端为对象,列平衡方程为FN-F=0,则内力FN=F,如图(b)所示。
F
F
F
FN
(a)
(b)
5
§2.1 直杆轴向拉伸与压缩时的变形与应力分析 (3)应力 杆件在外力作用下,单位面积上的内力称为应力。
拉压杆横截面上各点处只产生正应力,且正应力在截面上均匀分布 。
F
FN
A
FN
——轴向拉压杆横截面上正应力的计算公式。 式中:
max
FN A
150 103
1570
MPa
95.5 MPa﹤ 所以斜拉杆 C 的D 强度足够。
31
§2.3 直杆轴向拉伸和压缩时的强度计算 五、应力集中与温差应力 1.应力集中 局部应力显著增大的现象:应力集中,使零件破坏危险性增加。
32
§2.3 直杆轴向拉伸和压缩时的强度计算 2.温差应力 由于温度变化,结构或构件产生伸或缩,而当伸缩受到限制时,结构或 构件内部便产生应力,称为温差应力或热应力。 工业生产中输送高压蒸汽的管道要设置膨胀节,以避免受温度变化影响。
二、内力与应力 (1)内力
杆件所受其他物体的作用力都称为外力,包括主动力和约束力。在外力 作用下,杆件发生变形,杆件材料内部产生阻止变形的抗力,这种抗力称为 内力(。2)截面法
将受外力作用的杆件假想地切开,用以显示内力的大小。并以平衡条件 确定其合力的方法称为截面法。如下图(a)所示,假想将杆件切开,选取杆
机械零件的强度1PPT课件

O
4潘5存˚ 云教σ授研’a制 45˚
σ0 /2
σ’m
σ’a
σm
C
A E直线上任意点代表了一定循
σS
环特性r 时的疲劳极限。
CE直线上任意点N’ 的坐标为(σ’m ,σ’a )
'maxam s
说明CE直线上任意点的最大应力达到了屈服极限应力。
连接OB、OE,极限应力图划分为几个区域:
AOB区域 1r0
二、载荷的分类
静载荷 载荷
变载荷
Fca KF
工作载荷 名义载荷 计数
潘存云教授研制
(
Fn b
)min
三、应力的种类
静应力: σ=常数 变应力: σ随时间变化
平均应力:
m
m
axm
2
in
应力幅:
a
m
axm
2
in
变应力的循环特性:
σ
潘存云教授研制
-1
= r min 0
N=1/4
103 104 N
其方程为:
rN r N ( N D )
D N
N0≈107
由于ND很大,所以在作疲劳试验时,常规定一个循 环次数N0(称为循环基数),用N0及其相对应的疲劳极 限σr来近似代表ND和 σr∞。
于是有:rm N NrmN0C
CD区间内循环次数N与疲
σmax
劳极限rN的关系为:
第2章 机械零件的强度
§2-1 载荷和应力 §2-2 材料的疲劳特性 §2-3 机械零件的疲劳强度计算 §2-4 机械零件的接触强度
§2-1 载荷和应力
一、载荷的简化和力学模型 考虑到工程问题的复杂性,强度计算时,往往要对
作用在零件上的载荷进行简化——条件性计算。
机械零件的强度 PPT

各个系数的 值参见
P3541本 章附录。
❖综合影响系数对应力的影响
关于静应力:
零件的极限应力
e lim 即为材料静强度极限;
关于变应力:
e 不受k、和的影响。
可以将 作e分解:
e ae m e
其中, m为e静应力成分,故:
m e m lim
而 ae则受 k、 和 影响,考虑到有:
静应力
min max m 、 r 1
变应力关系:
m
1 2
(
max
min
)
a
1 2
(
max
min
)
r min max
注意: 1)变应力是由变载荷产生的,也估计是由静载荷产生 的。
2)在变应力作用下,零件产生的是疲劳破坏。
四、变应力作用下机械零件的失效形式—
1、概
—金属疲劳简
算应采用应力值进行计算。
3.N 106 ~ 107
次疲劳区
该段曲线只有延性材料(如钢)才有,而对于脆性材料(如有色金属及
其合金等)则无此区域。该段曲线对应的应力称为持久疲劳极限。
不同的失效概率,材料的S-N曲线也不同,失效概率依照正态分布。 一般,一批相同的试样在相同的载荷下进行试验,取其中50%未发生疲 劳破坏前的循环次数N为试验次数,即可靠度R=0、5时的极限应力及其 N作S-N曲线,故不同的可靠度下有不同的S-N曲线。
试验得rN0
r
N0——循环基数; N0=(1~10) 106
这样:
m rN
N
m r
N
0
C
rN
rm
N0 N
KN r
(N C
N
N
机械零部件设计中的强度与耐磨性

机械零部件设计中的强度 与耐磨性
欢迎来到本次演讲,我们将探讨机械零部件设计中的强度和耐磨性,了解其 定义、测试方法以及提高方法。
强度和耐磨性的定义
1 强度
指材料或结构在外力作用下抵抗变形和破坏的能力。
2 耐磨性
指材料或结构在摩擦和磨损条件下的耐用程度。
影响机械零部件强度的因素
材料
选择合适的材料,如高强度 合金或特殊合金,以满足设 计要求。
提高机械零部件强度和耐磨性的方法
采用先进材料
优化设计Βιβλιοθήκη 选择性能更好的材料,如高强度合金或复合材料。 通过优化几何形状和尺寸,减少应力集中,提 高强度和耐磨性。
表面处理
采用表面处理技术,如渗碳和氮化,增强材料 的表面硬度和耐磨性。
热处理
通过热处理工艺,如淬火和回火,提高材料的 强度和耐磨性。
结论
强度和耐磨性是机械零部件设计中至关重要的考虑因素。通过合适的材料选择、优化的设计和适当的处 理方法,我们可以提高零部件的性能和耐久度。
几何形状
设计零部件的形状和尺寸, 以减少应力集中和增加强度。
加工工艺
采用先进的加工工艺,如热 处理或表面处理,以增强材 料的强度。
常用的强度测试方法
拉伸试验
通过施加拉力来测试材料 的强度和延展性。
压缩试验
通过施加压力来测试材料 的抗压能力。
扭转试验
通过施加扭转力来测试材 料的抗扭能力。
常见的耐磨性测试方法
1
滑动磨损试验
模拟零部件在滑动摩擦条件下的耐磨性。
2
磨损试样重量损失测试
通过测量试样在磨损过程中的重量损失来评估耐磨性。
3
磨损痕迹观察
观察材料或结构在磨损条件下产生的磨痕,评估其耐磨性。
欢迎来到本次演讲,我们将探讨机械零部件设计中的强度和耐磨性,了解其 定义、测试方法以及提高方法。
强度和耐磨性的定义
1 强度
指材料或结构在外力作用下抵抗变形和破坏的能力。
2 耐磨性
指材料或结构在摩擦和磨损条件下的耐用程度。
影响机械零部件强度的因素
材料
选择合适的材料,如高强度 合金或特殊合金,以满足设 计要求。
提高机械零部件强度和耐磨性的方法
采用先进材料
优化设计Βιβλιοθήκη 选择性能更好的材料,如高强度合金或复合材料。 通过优化几何形状和尺寸,减少应力集中,提 高强度和耐磨性。
表面处理
采用表面处理技术,如渗碳和氮化,增强材料 的表面硬度和耐磨性。
热处理
通过热处理工艺,如淬火和回火,提高材料的 强度和耐磨性。
结论
强度和耐磨性是机械零部件设计中至关重要的考虑因素。通过合适的材料选择、优化的设计和适当的处 理方法,我们可以提高零部件的性能和耐久度。
几何形状
设计零部件的形状和尺寸, 以减少应力集中和增加强度。
加工工艺
采用先进的加工工艺,如热 处理或表面处理,以增强材 料的强度。
常用的强度测试方法
拉伸试验
通过施加拉力来测试材料 的强度和延展性。
压缩试验
通过施加压力来测试材料 的抗压能力。
扭转试验
通过施加扭转力来测试材 料的抗扭能力。
常见的耐磨性测试方法
1
滑动磨损试验
模拟零部件在滑动摩擦条件下的耐磨性。
2
磨损试样重量损失测试
通过测量试样在磨损过程中的重量损失来评估耐磨性。
3
磨损痕迹观察
观察材料或结构在磨损条件下产生的磨痕,评估其耐磨性。
【 机 械 设 计 】第2章 强度与耐磨性

2
式中
为最大应r力, m最ax小应力
m in
max
min
2.循环特性 -1时,为对称循环变应力
此时
max min a , m 0
0时,为脉动循环变应力 此时
r 1时,为静应力
此时
min
0, m
a
max
2
max min 常数
时,为不对称循环变应力 此时
1 r 1
max m a, min m a
在综合考虑零件的性能要求和经
减载槽
济性后,采用具有高疲劳强度的材料,并配以适当的热处理和各种
表面强化处理。
适当提高零件的表面质量,特别是提高有应力集中部位的表面加工 质量,必要时表面作适当的防护处理。
尽可能地减少或消除零件表面可能发生的初始裂纹的尺寸,对于延 长零件的疲劳寿命有着比提高材料性能更为显著的作用。
σmin确定平均应力σm与应力幅σa,然后,在极限应力线图的坐标中 标示出相应工作应力点M或N。
相应的疲劳极限应力应是极限应力 曲线上的某一个点所代表的应力力。
计算安全系数及疲劳强度条件为:
Sca
m ax max
m a m a
S
根据零件工作时所受的约束来确定应力可能发生的变化规律,从而决定
接触应力是不同于以往所学过的挤压应力的。挤压应力是面接触引起 的应力,是二向应力状态,而接触应力是三向应力状态。接触应力的特点 是:仅在局部很小的区域内产生很大的应力。
§2-4 机械零件的接触强度
当两零件以点、线相接处时,其接触的局部会引起较大的应力。这局部 的应力称为接触应力。
对于线接触的情况,其接触应力可 用赫兹应力公式计算。
1.磨损过程大致可分为以下三个阶段:
式中
为最大应r力, m最ax小应力
m in
max
min
2.循环特性 -1时,为对称循环变应力
此时
max min a , m 0
0时,为脉动循环变应力 此时
r 1时,为静应力
此时
min
0, m
a
max
2
max min 常数
时,为不对称循环变应力 此时
1 r 1
max m a, min m a
在综合考虑零件的性能要求和经
减载槽
济性后,采用具有高疲劳强度的材料,并配以适当的热处理和各种
表面强化处理。
适当提高零件的表面质量,特别是提高有应力集中部位的表面加工 质量,必要时表面作适当的防护处理。
尽可能地减少或消除零件表面可能发生的初始裂纹的尺寸,对于延 长零件的疲劳寿命有着比提高材料性能更为显著的作用。
σmin确定平均应力σm与应力幅σa,然后,在极限应力线图的坐标中 标示出相应工作应力点M或N。
相应的疲劳极限应力应是极限应力 曲线上的某一个点所代表的应力力。
计算安全系数及疲劳强度条件为:
Sca
m ax max
m a m a
S
根据零件工作时所受的约束来确定应力可能发生的变化规律,从而决定
接触应力是不同于以往所学过的挤压应力的。挤压应力是面接触引起 的应力,是二向应力状态,而接触应力是三向应力状态。接触应力的特点 是:仅在局部很小的区域内产生很大的应力。
§2-4 机械零件的接触强度
当两零件以点、线相接处时,其接触的局部会引起较大的应力。这局部 的应力称为接触应力。
对于线接触的情况,其接触应力可 用赫兹应力公式计算。
1.磨损过程大致可分为以下三个阶段:
机械零件的强度与耐磨性

机械零件之间力的传递,总是通过两零件 的表面接触来实现的。对机械零件除了要有足 够的体积强度外,工作的接触表面还要有足够 的接触强度。
L ρ1 ρ2
承载前,点接触或线接触。
ρ2
ρ1
圆柱体外接触
圆柱体内接触
球体外接触
受载后,局部弹 性变形,形成小 的接触面积。
F
1
对于线接触的情况,其接触 应力可用赫兹应力公式计算。
F lim [ ] A S 塑性材料 lim S
提高强度?
[ ]
lim
S
2.应力分类
变应力——随时间变化
σ
静应力——不随时间变化或变化缓慢
t
σ
0
a σ
t 0
a
t
静应力只能由静载荷产生, 变应力可能由变载荷或静载荷产生。
§2-1 机械零件的疲劳强度计算
疲劳强度设计是以试验为基础的。
二、材料疲劳曲线(σrN—N)* ——标准试样疲劳试验
rN r
NB 10
3
A 静应力 B C
· ? · ·· ··
低周疲劳
循环基数 N 0
rN
有限寿命
D
无限寿命
rD r
N
试样破坏时 达到的循环次数
N
NC 10
4
N0
N D 107
机械零件的强度与耐磨性
断裂、磨损和腐蚀是机械零件最主要失效形式。 机器工作过程中缓慢进行的。 突发性,导致严重事故。
工业界最关注的问题。
占断裂失效 80%的概率
发生断裂的原因:工作载荷过大、材料的低 温脆性、应力集中、腐蚀和疲劳。
拉杆强度 条件:
L ρ1 ρ2
承载前,点接触或线接触。
ρ2
ρ1
圆柱体外接触
圆柱体内接触
球体外接触
受载后,局部弹 性变形,形成小 的接触面积。
F
1
对于线接触的情况,其接触 应力可用赫兹应力公式计算。
F lim [ ] A S 塑性材料 lim S
提高强度?
[ ]
lim
S
2.应力分类
变应力——随时间变化
σ
静应力——不随时间变化或变化缓慢
t
σ
0
a σ
t 0
a
t
静应力只能由静载荷产生, 变应力可能由变载荷或静载荷产生。
§2-1 机械零件的疲劳强度计算
疲劳强度设计是以试验为基础的。
二、材料疲劳曲线(σrN—N)* ——标准试样疲劳试验
rN r
NB 10
3
A 静应力 B C
· ? · ·· ··
低周疲劳
循环基数 N 0
rN
有限寿命
D
无限寿命
rD r
N
试样破坏时 达到的循环次数
N
NC 10
4
N0
N D 107
机械零件的强度与耐磨性
断裂、磨损和腐蚀是机械零件最主要失效形式。 机器工作过程中缓慢进行的。 突发性,导致严重事故。
工业界最关注的问题。
占断裂失效 80%的概率
发生断裂的原因:工作载荷过大、材料的低 温脆性、应力集中、腐蚀和疲劳。
拉杆强度 条件:
机械设计 徐锦康 第二章 机械零件的强度 课件

变应力下机械零件的整体强度
2.3.1 材料的疲劳曲线 变应力下材料的强度指标称为材料的疲劳极限(持久极限)。 即变应力下材料的极限应力为材料的疲劳极限。 疲劳极限:r一定时,应力循环N次后材料不发生疲劳破坏 时的最大应力,用σrN表示。 即:当工作应力σmax≤σrN时,材料可经历应力循环N次不 会发生疲劳破坏。 材料的疲劳极限σrN与变应力的循环特性r、循环次数N和 最大应力σmax有关,可由材料疲劳试验测得。 材料疲劳曲线(σ-N曲线): r一定时,σrN与N之间的关系曲线。 由材料疲劳试验测得
ϕσ =
2σ−1 −σ0
σ0
对于碳钢, σ≈0.1~0.2 对于合金钢,σ≈0.2~0.3。
变应力下机械零件的整体强度
2.3.3 影响机械零件疲劳强度的主要因素 材料的疲劳极限由光滑小试件测得,而机械零件由于几何 形状的变化、尺寸大小不同、加工质量及强化因素等的影响, 使得零件的疲劳极限要小于材料试件的疲劳极限。 (1) 应力集中的影响 零件几何形状的突变处产生应力集中,使零件疲劳强度降 低,用有效应力集中系数kσ考虑: kσ=1+q(ασ-1) 式中:ασ为理论应力集中系数, q为材料对应力集中的敏 感系数,ασ、q可由设计手册查取。 如平板上圆角处的理论应力集中系数可由图2.7查取(p29)
kσ
称为综合影响系数。
机械零件的疲劳强度计算1
变应力下机械零件的整体强度
2.3.4 零件的极限应力线图 将零件材料的极限应力线图中的直线ADG按比例向下移, 成为下图所示的直线A’D’G’ ,而极限应力曲线的 CG 部分, 由于是按照静应力的要求来考虑的,故不须进行修正。这样 就得到了零件的极限应力线图。
'
' ' (kσ )Dσa +ϕσσm = σ−1
2第二章 机械零件的强度与耐磨性

N 0 ND
N
N
m N N N lim rN r 当 C D
N0 N 无限寿命
有限寿命 疲劳极限
当 N ND
lim rN
疲劳极限 N0 r m r ND
关于疲劳曲线方程的几点说明:
rN m
注意:
N0 r N
(1)工程中常用的是对称循环应力(r=-1)下的疲劳 极限,计算时,只须把σr和σrN换成σ-1和σ-1N 即可
机械零件之间力的传递,总是通过两零件 的表面接触来实现的。对机械零件除了要有足 够的体积强度外,工作的接触表面还要有足够 的接触强度。
L ρ1
承载前是 点接触或 线接触。
ρ2
ρ2
ρ1
圆柱体外接触 受载后接 触表面产 生局部弹 性变形, 形成小的 接触面积
圆柱体内接触
球体外接触
F
1
对于线接触的情况,其接触 应力可用赫兹应力公式计算。
F lim [ ] A S 塑性材料 lim S
提高强度?
[ ]
lim
S
2.应力分类
变应力——随时间变化
σ
静应力——不随时间变化或变化缓慢
t
σ
0
a σ
t 0
a
t
静应力只能由静载荷产生, 变应力可能由变载荷或静载荷产生。
§2-1 机械零件的疲劳强度计算
摩擦系数 f
油性添加剂 极压添加剂
非极压油
含极压添 加剂的油 含脂肪 酸的油
含脂肪酸和极压添加剂的油 软化温度t/℃
极压添加剂:能和接触的金属表面起反应形成高熔点无机薄膜, 以防止在高负荷下发生熔结、卡咬、划痕或刮伤的添加剂。 水溶和油容两种极压添加剂。
- 1、下载文档前请自行甄别文档内容的完整性,平台不提供额外的编辑、内容补充、找答案等附加服务。
- 2、"仅部分预览"的文档,不可在线预览部分如存在完整性等问题,可反馈申请退款(可完整预览的文档不适用该条件!)。
- 3、如文档侵犯您的权益,请联系客服反馈,我们会尽快为您处理(人工客服工作时间:9:00-18:30)。
静强度不受 K D
的影响,故不需修正。
折线 ADEC
即为零件的极限 应力线。
D
D
3.单向稳定变应力时的疲劳强度计算
σa
进行零件疲劳强度计算时,首先根据
零件危险截面上的 σmax 及 σmin确定平均 应力σm与应力幅σa,然后,在极限应力
二.机械零件的疲劳强度计算
1. 影响零件疲劳强度的主要因素
影响零件疲劳强度的主要因素有以下三个: 1)应力集中的影响
机械零件上的应力集中会加快疲劳裂纹的形成和扩展。 从而导致零件的疲劳强度下降。
用应力集中系数 计入应力集中的影响 。
理论应力集中系数 : 、 。
有效应力集中系数 :K 、K 。
第2章 机械零部件设计中的强度 问题与耐磨性
2.1 概述 2.2 机械设计中的强度问题 2.3 机械零件的疲劳强度 2.4 机械零件的表面接触强度 2.5 机械设计中的摩擦、磨损和润滑问题
教学目标和教学重点
教学目标: 1、掌握载荷和应力的分类; 2、熟悉机械零件强度的基本概念; 3、掌握材料的疲劳特性; 4、了解机械零件的强度计算和提高零件疲劳强度的措施。
r 不同或 N 不同时,疲劳极限 rN 则不同。
在疲劳强度计算中,取
= l i m
rN
。
2.3 机械零件的疲劳强度
一.材料的疲劳特性
1、 -N疲劳曲线
用参数σ max表征材料的疲劳极限,通过实验,可 得出如图所示的疲劳曲线。称为:-N疲劳曲线
σmax
N
-N疲劳曲线
一.材料的疲劳特性
N﹥104,高周疲劳
σmax σB A B
C
σr
N=1/4 103 104
D N
N0≈107
CD段,随着N ↑ → σ max ↓,代表有限寿命区,机 械零件的疲劳大多发生在CD段。
D点以后的疲劳曲线呈一水平线,代表着无限寿命区。
σrN σr
N N0
2.3 机械零件的疲劳强度
一.材料的疲劳特性
1、 -N疲劳曲线
在原点处,对应的应力循环
次数为N=1/4。
σmax
在AB段,应力循环次数<103 , σB A B C
σ max变化很小,可以近似看 作为静应力强度。
N
BC段,N=103~104,随着
N=1/4 103 104
N ↑ → σ max ↓ ,疲劳
现象明显。
因N较小,特称为:低周疲劳。
教学重点: 1、稳定循环应力类型及参量; 2、材料的疲劳曲线及极限应力曲线。
2.2 机械设计中的强度问题
强度→工作应力 ≤ 许用应力 载荷(应力) 材料
一.载荷与应力
1.零件设计中的载荷及其分类
静载荷:不随时间变化或变化缓慢的载荷. 变载荷:随时间作周期性或非周期性变化的载荷.
注意:在设计计算中,载荷又可分为名义载荷和计 算载荷,计算载荷等于载荷系数乘以名义载荷。
2、 疲劳极限应力图(等寿命疲劳曲线)
注:1)疲劳曲线的用途:在于根据 r 确定某个 循环次数 N ቤተ መጻሕፍቲ ባይዱ的条件疲劳极限 rN 。
2)极限应力图的用途:在于根据 1 确定非 对称循环应力下的疲劳极限以计算安全系数。
3)对于切应力,只需将各式中的 换成 即可。
2.3 机械零件的疲劳强度
表面高σ频B淬/ M火pa的强化系数βq
试件种类
试件直径/mm
无应力集中
7~20 30~40
1.3~1.6 1.2~1.5
有应力集中
7~20 30~40
1.6~2.8 1.5~5
综合影响系数
试验证明:应力集中、尺寸和表面质量都只对应 力幅有影响,而对平均应力没有明显的影响。(即对 静应力没有影响)
▲ 断裂面累积损伤处表面光滑,而折断区表面粗糙。
2.3 机械零件的疲劳强度
一.材料的疲劳特性
两个概念:
1)疲劳寿命N: 材料疲劳失效前所经历的应力循环次数。
2)材料的疲劳极限 rN : 在应力比为 r的循环应力作用下,应
力循环 N 次后,材料不发生疲劳破坏时所能承受的最大应力
max ( ) max 。 (变应力的大小可按其最大应力进行比较)
在计算中,上述三个系数都只计在应力幅上,故可 将三个系数组成一个综合影响系数:
K
K D
零件的疲劳极限为:
K
K D
1
1 e
KD
1
1 e
KD
2.3 机械零件的疲劳强度
二.机械零件的疲劳强度计算
2. 零件的极限应力线图
注:由于E′C段 属于静强度,而
表面质量:是指表面粗糙度及其表面强化的工艺 效果。表面越光滑,疲劳强度可以提高。强化工艺 (渗碳、表面淬火、表面滚压、喷丸等)可显著提高 零件的疲劳强度。
用表面状态系数 、 计入表面质量的影响。
钢材的表面质量系数βσ
βσ 1.0
抛光
0.8
磨削
精车
0.6
粗车
0.4 未加工
0.2
400 600 800 1000 1200 1400
注:当同一剖面上同时有几个应力集中源时,应采用其中最大的 应力集中系数进行计算。
有效应力集中系数kσ
ασ
ατ
2)尺寸的影响 零件的尺寸越大,在各种冷、热加工中出现缺陷,
产生微观裂纹等疲劳源的可能性(机会)增大。从而 使零件的疲劳强度降低。
用尺寸系数 、 ,计入尺寸的影响。
3)表面质量的影响
纹逐渐扩展;
▲当剩余材料不足以承受载 荷时,突然脆性断裂。
粗糙的脆性 断裂区
疲劳断裂是与应力循环次数(即使用寿命)有关的断裂。
疲劳断裂具有以下特征:
▲ 疲劳断裂的最大应力远比静应力下材料的强度极限
低,甚至比屈服极限低;
不管脆性材料或塑性材料,
▲ 疲劳断口均表现为无明显塑性变形的脆性突然断裂;
▲ 疲劳断裂是微观损伤积累到一定程度的结果。
2.应力的分类
静应力:不随时间变化或变化缓慢的应力。 变应力: 随时间变化的应力。
描述稳定循环变应力有5个参量,应力幅σa、平均应力σm 、 最小应力σmin 、最大应力σmax和循环特性系数r。但其中只有两 个参数是独立的。 注意:应力循环次数N。
2.应力的分类
非对称循环变应力
2.应力的分类
对称循环变应力
2.应力的分类
脉动循环变应力
2.应力的分类
静应力
2.3 机械零件的疲劳强度
变应力下,零件的损坏形式是疲劳断裂。
疲劳断裂过程:
初始裂纹
光滑疲劳区
粗糙的脆性 断裂区
疲劳断裂截面
变应力下,零件的损坏形式是疲劳断裂。 光滑疲劳区
疲劳断裂过程:
▲零件表层产生微小裂纹;
▲随着循环次数增加,微裂
的影响,故不需修正。
折线 ADEC
即为零件的极限 应力线。
D
D
3.单向稳定变应力时的疲劳强度计算
σa
进行零件疲劳强度计算时,首先根据
零件危险截面上的 σmax 及 σmin确定平均 应力σm与应力幅σa,然后,在极限应力
二.机械零件的疲劳强度计算
1. 影响零件疲劳强度的主要因素
影响零件疲劳强度的主要因素有以下三个: 1)应力集中的影响
机械零件上的应力集中会加快疲劳裂纹的形成和扩展。 从而导致零件的疲劳强度下降。
用应力集中系数 计入应力集中的影响 。
理论应力集中系数 : 、 。
有效应力集中系数 :K 、K 。
第2章 机械零部件设计中的强度 问题与耐磨性
2.1 概述 2.2 机械设计中的强度问题 2.3 机械零件的疲劳强度 2.4 机械零件的表面接触强度 2.5 机械设计中的摩擦、磨损和润滑问题
教学目标和教学重点
教学目标: 1、掌握载荷和应力的分类; 2、熟悉机械零件强度的基本概念; 3、掌握材料的疲劳特性; 4、了解机械零件的强度计算和提高零件疲劳强度的措施。
r 不同或 N 不同时,疲劳极限 rN 则不同。
在疲劳强度计算中,取
= l i m
rN
。
2.3 机械零件的疲劳强度
一.材料的疲劳特性
1、 -N疲劳曲线
用参数σ max表征材料的疲劳极限,通过实验,可 得出如图所示的疲劳曲线。称为:-N疲劳曲线
σmax
N
-N疲劳曲线
一.材料的疲劳特性
N﹥104,高周疲劳
σmax σB A B
C
σr
N=1/4 103 104
D N
N0≈107
CD段,随着N ↑ → σ max ↓,代表有限寿命区,机 械零件的疲劳大多发生在CD段。
D点以后的疲劳曲线呈一水平线,代表着无限寿命区。
σrN σr
N N0
2.3 机械零件的疲劳强度
一.材料的疲劳特性
1、 -N疲劳曲线
在原点处,对应的应力循环
次数为N=1/4。
σmax
在AB段,应力循环次数<103 , σB A B C
σ max变化很小,可以近似看 作为静应力强度。
N
BC段,N=103~104,随着
N=1/4 103 104
N ↑ → σ max ↓ ,疲劳
现象明显。
因N较小,特称为:低周疲劳。
教学重点: 1、稳定循环应力类型及参量; 2、材料的疲劳曲线及极限应力曲线。
2.2 机械设计中的强度问题
强度→工作应力 ≤ 许用应力 载荷(应力) 材料
一.载荷与应力
1.零件设计中的载荷及其分类
静载荷:不随时间变化或变化缓慢的载荷. 变载荷:随时间作周期性或非周期性变化的载荷.
注意:在设计计算中,载荷又可分为名义载荷和计 算载荷,计算载荷等于载荷系数乘以名义载荷。
2、 疲劳极限应力图(等寿命疲劳曲线)
注:1)疲劳曲线的用途:在于根据 r 确定某个 循环次数 N ቤተ መጻሕፍቲ ባይዱ的条件疲劳极限 rN 。
2)极限应力图的用途:在于根据 1 确定非 对称循环应力下的疲劳极限以计算安全系数。
3)对于切应力,只需将各式中的 换成 即可。
2.3 机械零件的疲劳强度
表面高σ频B淬/ M火pa的强化系数βq
试件种类
试件直径/mm
无应力集中
7~20 30~40
1.3~1.6 1.2~1.5
有应力集中
7~20 30~40
1.6~2.8 1.5~5
综合影响系数
试验证明:应力集中、尺寸和表面质量都只对应 力幅有影响,而对平均应力没有明显的影响。(即对 静应力没有影响)
▲ 断裂面累积损伤处表面光滑,而折断区表面粗糙。
2.3 机械零件的疲劳强度
一.材料的疲劳特性
两个概念:
1)疲劳寿命N: 材料疲劳失效前所经历的应力循环次数。
2)材料的疲劳极限 rN : 在应力比为 r的循环应力作用下,应
力循环 N 次后,材料不发生疲劳破坏时所能承受的最大应力
max ( ) max 。 (变应力的大小可按其最大应力进行比较)
在计算中,上述三个系数都只计在应力幅上,故可 将三个系数组成一个综合影响系数:
K
K D
零件的疲劳极限为:
K
K D
1
1 e
KD
1
1 e
KD
2.3 机械零件的疲劳强度
二.机械零件的疲劳强度计算
2. 零件的极限应力线图
注:由于E′C段 属于静强度,而
表面质量:是指表面粗糙度及其表面强化的工艺 效果。表面越光滑,疲劳强度可以提高。强化工艺 (渗碳、表面淬火、表面滚压、喷丸等)可显著提高 零件的疲劳强度。
用表面状态系数 、 计入表面质量的影响。
钢材的表面质量系数βσ
βσ 1.0
抛光
0.8
磨削
精车
0.6
粗车
0.4 未加工
0.2
400 600 800 1000 1200 1400
注:当同一剖面上同时有几个应力集中源时,应采用其中最大的 应力集中系数进行计算。
有效应力集中系数kσ
ασ
ατ
2)尺寸的影响 零件的尺寸越大,在各种冷、热加工中出现缺陷,
产生微观裂纹等疲劳源的可能性(机会)增大。从而 使零件的疲劳强度降低。
用尺寸系数 、 ,计入尺寸的影响。
3)表面质量的影响
纹逐渐扩展;
▲当剩余材料不足以承受载 荷时,突然脆性断裂。
粗糙的脆性 断裂区
疲劳断裂是与应力循环次数(即使用寿命)有关的断裂。
疲劳断裂具有以下特征:
▲ 疲劳断裂的最大应力远比静应力下材料的强度极限
低,甚至比屈服极限低;
不管脆性材料或塑性材料,
▲ 疲劳断口均表现为无明显塑性变形的脆性突然断裂;
▲ 疲劳断裂是微观损伤积累到一定程度的结果。
2.应力的分类
静应力:不随时间变化或变化缓慢的应力。 变应力: 随时间变化的应力。
描述稳定循环变应力有5个参量,应力幅σa、平均应力σm 、 最小应力σmin 、最大应力σmax和循环特性系数r。但其中只有两 个参数是独立的。 注意:应力循环次数N。
2.应力的分类
非对称循环变应力
2.应力的分类
对称循环变应力
2.应力的分类
脉动循环变应力
2.应力的分类
静应力
2.3 机械零件的疲劳强度
变应力下,零件的损坏形式是疲劳断裂。
疲劳断裂过程:
初始裂纹
光滑疲劳区
粗糙的脆性 断裂区
疲劳断裂截面
变应力下,零件的损坏形式是疲劳断裂。 光滑疲劳区
疲劳断裂过程:
▲零件表层产生微小裂纹;
▲随着循环次数增加,微裂