催化裂化装置三旋至四旋烟气温降计算及分析
12镇海炼化II催化三旋与烟机运行情况详解
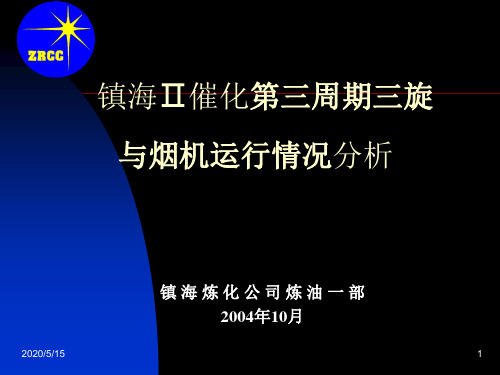
2018/10/12
停工消缺检查情况
再生器检查发现12只二级旋分器有5只旋风 器料腿灰斗堵住,堵塞部位相同,均发生在 灰斗与料腿结合处,堵塞物最下部均为旋风 分离器龟甲网的六边形衬里表皮,之上均为 疏松的再生催化剂 各二级旋分内筒体内表面衬里均有不同程度 脱开松动,有的已掉下,有的脱开后仍挂在 筒体上,其中5只灰斗堵塞的旋分器内表面 衬里脱落比较多,个别达到三分之一。
烟机
Ⅱ催化的烟机组由TP11-160型烟机、AV71-11 型轴流风机、GH530型烟机和YCH710-4型电动 发电机组成。其中烟机轴功率为16389kw、由西 安航空发动公司制造,风机流量为252000Nm3/h、 是陕西鼓风机厂当时为国内炼油企业制造的最 大型轴流风机,齿轮箱由郑州机械研究所制造, 电动发电机由上海电机厂制造。该机组于1999 年8月进行机械试车和防喘振试验,11月9日备 机成功切换至烟机组运行,实现开车一次成功, 机组投入生产后机组运行平稳,烟机轴振动一 般在35μ m 以下,最大不超过45μ m,瓦温最高 不超过55℃
3
2018/10/12
三旋
本装置三旋系为卧式结构,由西安三桥制 造,共设置288根分离单管,设计出口烟 气粉尘含量≯200mg/m3,对于设计入口 烟气粉尘浓度与筛分构成,根据原设计 ≯0.4kg/t总跑损量间接推算,三旋的入口 烟气设计粉尘含量应在400-500mg/m3之 间。该三旋于99年11月投用以来,运行情 况总体较好,出口烟气在线激光粒度仪监 测的粉尘含量基本在100mg/m3左右,并 较为稳定,烟机运行及磨损均正常。
再生器顶Mpa
两器差压Mpa 提升管Kpa 预提升段Kpa 再生滑阀Kpa 大孔分布板Kpa 主风分布管Kpa
石油催化裂化—催化裂化工艺主要操作条件分析
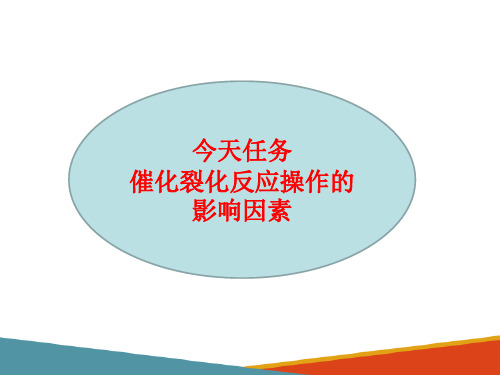
原料性质也影响产品分布,在同样转化率时,石蜡基原料的汽油及焦 炭产率较低,气体产率较高;环烷基原料的汽油产率高,气体产率低;芳 香基原料汽油产率居中,焦炭产率高。
五、空速和反应时间
空速:每小时进入反应器的原料油量与反应器催化剂藏量之比。分质 量空速和体积空速。空速大小反应映反应时间长短。其倒数为反应时间。
今天任务 催化裂化反应操作的
影响因素
七 回炼比
六 再生催化剂含碳量
一、 反应温度
催化裂化反 应操作的影
响因素
二、 反应压力(油气分压)
三 剂油比(C/O)
五 空速和反应时间
四 原料的性质
一、反应温度——以沉降器出口温度为标准
反应温度是生产中的主要调节参数,也是对产品产率和质量影响最灵 敏的参数。一方面,反应温度高则反应速度增大。另一方面,反应温度可 以通过对各类反应速率大小来影响产品的分布和质量。通过调节再生滑阀 的开度来调节反应温度。
七、回炼比
回炼比是回炼油(包括回炼油浆)的质量和新鲜原料油质量之比。回 炼比虽不是一个独立的变量,但却是一个重要的操作条件。回炼比的选取 要根据生产实际综合选定。
今天任务 催化裂化反应再生系
统的三大平衡
一、 压力平衡
催化裂化反 应再生系统 的三大平衡
二、 热平衡
三、 物料平衡
催化裂化反应—统的三大平衡 三、物料平衡
物料平衡包括催化剂和原料在数量上的平衡、单程转化 率和回炼比的平衡及催化剂的损失和补充的平衡。
• 总结:
反再系统操作关键: 三大平衡控制(压力平衡、热平衡、 物料平衡)
二、反应压力(油气分压)
油气分压提高意味着反应物浓度提高,因而反应速度加快,生焦的反 应速度也提高。
催化裂化工艺计算与技术分析

催化裂化工艺计算与技术分析[例4-1] 已知某催化裂化装置操作条件、产品分布等数据(见表4-6),求提升管油气停留时间。
解:(1)计算提升管入口油气流率,如表4-7所示。
= 26887m 3/h= 7.5 m 3/s(2) 计算提升管出口处油气流率,如表4-8所示。
1011401012732735204.22986+⨯+⨯⨯=i V= 54821m 3/h = 15.2m 3/s (3)计算油气线速 提升管横截面积:F = 0.25 πD 2= 0.25×3.14×1.22= 1.13 m 2计算入口油气流速: U i = V i /F = 7.5/1.13 = 6.6 m/s 计算出口油气流速: U o =V o /F = 15.2/1.13 = 13.5 m/s提升管内油气平均流速= 9.6 m/s(4) 计算油气平均停留时间 t = L / U m = 25 / 9.6 = 2.6 sYc =∆C k ·Rc(1+R F ) ( 4-3) 式中:∆C k ——催化剂的焦炭差,%(重);R F ——回炼比。
流量计有多种,应根据不同的流量计要求,进行校正。
(1)质量流量计是目前为许多炼厂所采用的先进的流量计,这种流量计不受检测点条件变化的影响,可以直接取得总通过量,前后数据相减即可。
(2)差压式流量计是利用流体流经节流装置时所产生的压力差实现流量测量的。
应用最广泛的节流1011161012732734931874+⨯+⨯=o V )6.65.13ln(6.65.13ln-=-=io i o m U U U U U装置是孔板,其次是喷嘴。
使用差压式流量计时,液体体积流量可用下式表示:V 实= C △实Pρ (5-1)式中:V 实—流体体积流量, m 3/h;△P —孔板前后压差,Pa ;ρ实—操作条件下流体的密度,m 3/kg ; C —常数。
流体质量流量可表示为:P CG △实实⋅=ρ (5-2)G 实——液体质量流量,t/h 。
催化裂化装置三级旋风分离器系统存在的问题及处理

管理与维护清洗世界Cleaning World第36卷第1期2020年1月0 引言三级旋风分离器在目前而言根据结构区分,主要区分为多管立式三旋、多管卧式三旋、布埃尔式三旋以及旋流式三旋四种,这四种随着我国经济发展的需要,在化工产业发展的不同时期被引进到不同的生产厂家。
随着多管式三旋的引进,我国的化工产业便将该种结构定为了研究和发展方向,并且经过不断的创新和发展,我国已经在不断突破外国的技术壁垒,研制出来了例如EPVC 、PSC 等类型的单管,这些技术的积累,已经使得多管式三级旋风分离器发展到了一定的高度,本文研究的中原油田石化总厂,其在20世纪90年代引进并投产了多管式三级旋风分离器,不过在其使用过程中发生过大大小小的问题,本文节选了三个比较严重的问题,并针对这些问题进行了简单的说明和分析。
1 多管式三级旋风分离器使用中常见的问题从1996年多管式三级旋风分离器在中原油田石化总厂投入使用以来,主要出现的问题案例如下所述。
(1)多管式三级旋风分离器,由于其本身混反的问题,虽然最终的浓度保持在250 mg/m 3,符合指标,但分离的效率并不是很高,从整套催化裂化的装置来看,三旋对于烟机的保护并不是很好,在其作用下,已经出现很多次动、静叶片修复的情况。
(2)多管式三级旋风分离器在吊桶角焊缝处多次出现裂纹,甚至于出现过整个吊桶角的焊盘全部开裂的情况,出现开裂之后吊桶的整体高度下降了200 mm 以上,这起裂纹问题差点导致吊桶完全脱落的生产事故。
(3)在检修的过程,由于单管之间的距离太小,对于多管式三级旋风分离器单管检修难度很大,检修的位置太多,所以耗费了一定的人力和物力、甚至于财力。
2 针对多管式三级旋风分离器问题的分析针对上述问题,本文逐点进行了详细的分析,关于分析的结果阐述如下。
(1)对于效率不高的问题,其问题原因较多,也最为复杂,主要分为五点具体如下所述。
其一,在三级旋风分离器制造和安装、使用的过程中造成了其内部单管的内外管同轴度超标,从而引发了效率低下的问题。
催化裂化装置能耗特点分析及节能措施探讨
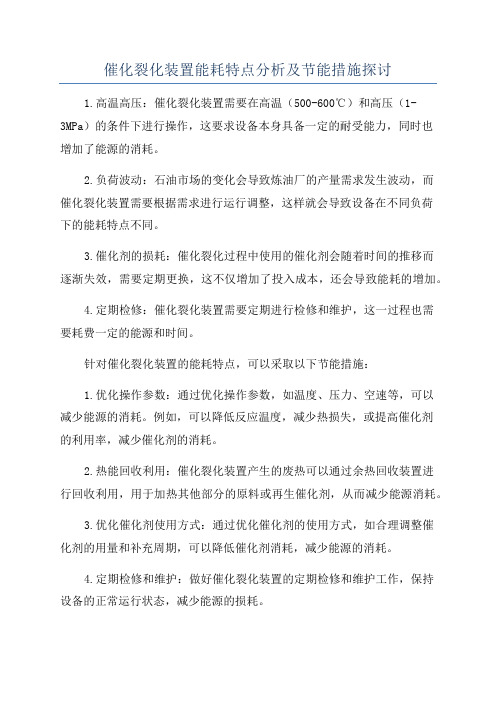
催化裂化装置能耗特点分析及节能措施探讨1.高温高压:催化裂化装置需要在高温(500-600℃)和高压(1-3MPa)的条件下进行操作,这要求设备本身具备一定的耐受能力,同时也增加了能源的消耗。
2.负荷波动:石油市场的变化会导致炼油厂的产量需求发生波动,而催化裂化装置需要根据需求进行运行调整,这样就会导致设备在不同负荷下的能耗特点不同。
3.催化剂的损耗:催化裂化过程中使用的催化剂会随着时间的推移而逐渐失效,需要定期更换,这不仅增加了投入成本,还会导致能耗的增加。
4.定期检修:催化裂化装置需要定期进行检修和维护,这一过程也需要耗费一定的能源和时间。
针对催化裂化装置的能耗特点,可以采取以下节能措施:1.优化操作参数:通过优化操作参数,如温度、压力、空速等,可以减少能源的消耗。
例如,可以降低反应温度,减少热损失,或提高催化剂的利用率,减少催化剂的消耗。
2.热能回收利用:催化裂化装置产生的废热可以通过余热回收装置进行回收利用,用于加热其他部分的原料或再生催化剂,从而减少能源消耗。
3.优化催化剂使用方式:通过优化催化剂的使用方式,如合理调整催化剂的用量和补充周期,可以降低催化剂消耗,减少能源的消耗。
4.定期检修和维护:做好催化裂化装置的定期检修和维护工作,保持设备的正常运行状态,减少能源的损耗。
5.技术改进和创新:通过技术改进和创新,如引入先进的催化剂、改进反应装置结构等,可以提高催化裂化装置的效率,降低能源的消耗。
总之,催化裂化装置的能耗特点是高温高压、负荷波动、催化剂损耗和定期检修等。
针对这些特点,可以通过优化操作参数、热能回收利用、优化催化剂使用方式、定期检修和维护以及技术改进和创新等节能措施来降低能源消耗,提高装置的能效性能。
催化裂化装置三旋存在问题分析及改造措施
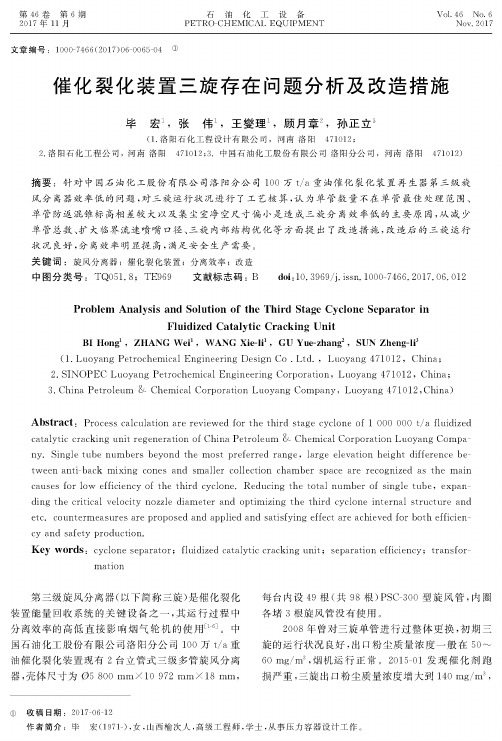
第46卷第6期 2017年11月石油化工设备PETRO-CHEM ICAL EQUIPMENTVol. 46 No. 6Nov. 2017文章编号:1000-7466(2017)06-0065-04 ①催化裂化装置三旋存在问题分析及改造措施毕宏、张伟、王燮理、顾月章2,孙正立3(1.洛阳石化工程设计有限公司,河南洛阳471012;2.洛阳石化工程公司,河南洛阳471012;.中国石油化工股份有限公司洛阳分公司,河南洛阳471012)摘要:针对中国石油化工股份有限公司洛阳分公司100万t/a重油催化裂化装置再生器第三级旋风分离器效率低的问题,对三旋运行状况进行了工艺核算,认为单管数量不在单管最佳处理范围、单管防返混锥标高相差较大以及集尘室净空尺寸偏小是造成三旋分离效率低的主要原因,从减少单管总数、扩大临界流速喷嘴口径、三旋内部结构优化等方面提出了改造措施,改造后的三旋运行状况良好,分离效率明显提高,满足安全生产需要。
关键词:旋风分离器;催化裂化装置;分离效率;改造中图分类号:TQ051.8; TE%9文献标志码:B doi:10.3969/j.issn.1000-7466. 2017. 06. 012Problem Analysis and Solution of the Third Stage Cyclone Separator inFluidized Catalytic Cracking UnitBI Hong1,ZHANG Wei1,WANG Xie-ii1,GU Yue-zhang2,SUN Zheng-ii3(1. Luoyang Petrochemical Engineering Design Co .Ltd. ,Luoyang 471012, China;2.SINOPEC Luoyang Petrochemical Engineering Corporation,Luoyang471〇12,China;3.China Petroleum &Chemical Corporation Luoyang Company,Luoyang 471012, China)Abstract:Process calculation are reviewed for the third stage cyclone of 1 000 000 t/a fluidizedcatalytic cracking untt regeneration of China Petroleum &Chemical Corporation Luoyang Company.Single tube numbers beyond the most preferred range,large elevation height difference between anti-back mixing cones and smaller collection chamber space are recognized as the maincauses for low efticiency of the third cyclone.Reducing the total number of single tube,expanding the critical velocity nozzle diameter and optimizing the third cyclone internal structure andetc.countermeasures are proposed and applied and satisfying effect are a cy and safety production.Key words:cyclone separator;lluidized catalytic cracking unit;separation efticiency;transformation第三级旋风分离器(以下简称三旋)是催化裂化 装置能量回收系统的关键设备之一,其运行过程中 分离效率的高低直接影响烟气轮机的使用[16]。
催化裂化装置低温热的优化利用

锅炉 给水 温度 低 , 除氧 器需 要 加 入 蒸 汽 对 除 盐水 进行 加热 , 才能 达到 除氧所 需要 的 14℃ 。 0
循环 油换热 , 另一 路经 E 22与分 馏塔 轻柴换 11
热 , 后两 路经换 热 的锅炉 给水加 以混 合 , 时 温 然 此 度达 到约 13o 0 C进入 除氧器 进行 除氧 。同时还 回 收外 系统 的蒸 汽凝 结 水 进 入 除氧 器 中 , 时 只 需 此 要 向除 氧 器 加 入 1th以下 的低 压 蒸 汽 , 能 达 / 即
油冷却器冷却至 6 0℃作为产 品出装置顶循环 回
流 自分 馏 塔 第 4层 塔 盘 抽 出, 顶 循 环 油 泵 用 ( 10 ) P 24 升压后 , 经换 热器与热水进行两次换热 后, 再经顶循冷却器将温度降至 8 0℃后返 回分馏
塔第 1 。 层
收稿 日期 :0 1— 7—0 。 21 0 2
循环 水/ 水 热
E1 O 2 1
E10 24
塔 顶油气 / 热水
顶循 油/ 水 热 ( 次) 第2
E1 0 38 P1 0 63 E1 0 B 62
El 1 22
El 0 36
热 水循 环泵
循 环 水/ 水 热
稳定 汽 油/ 轻柴 油/ 水 稳 定汽 油/ 热 热水( 1 ) 第 次 热水( 次 ) 第2
3 1 塔顶低 温热 直接 用于 锅炉给 水 .
除
P1 0 62 PI 0 5 1
除 盐水泵
锅 炉给 水泵
图 4 锅 炉 给 水 除 氧 换 热 流 程
F g 4 He tt n frp o e s o olrwae e e ain i. a r se r c s fb i tr d a r t a e o
催化裂化装置设计工艺计算方法

1.3.3稀相段直径
稀相段中点压力=0.3315MPa 稀相段温度=675+273=946K 气体体积流率=46.84m3/s 取稀相直径=9.7m 稀相线速=0.62m/s
1.3.4稀相段高度 取稀相段高度为12m
1.3.5过渡段高度 取过渡角为45度
1.3.6催化剂的停留时间
过渡段高度为1.25m
195973.42
1.3.1密相床直径
取密相床密度300kg/m3稀相段平均密度25kg/m3 密相段高度为9m 稀相段高度为12 m 密相段中点压力=0.3465MPa 密相段温度=273+671=943k 气体体积流率=44.67m3/s 取密相段线速为1.1m/s
密相段直径=7.19m
1.3.2 密相段的高度 再生器密相床体积==222cm3 密相段高度==5.45m
1.2.13再生器物料平衡
入方 kg/h
I段干烟气
174422.8
II段干烟气
37492.1
待生剂待入烟 1080 气
I段主风带水 汽
3488.5
II段主风带水 670.8 汽
I段松动吹扫 汽
1500
II段松动吹扫 500 汽
焦炭
17000
循环催化剂 1010000
合计
1250100
出方kg/h
I段干烟气
1.1.2理论干空气量的计算
Ⅰ段碳燃烧生成二氧化碳需O2量706.1×1=706.1kmol/h Ⅰ段碳燃烧生成一氧化碳需O2量413.7×0.5=206.9kmol/h Ⅰ段氢燃烧生成水需O2量595×0.5=297.5kmol/h 理论需O2量=706.1+206.9+297.5=1210.5kmol/h=38736kg/h 理论需N2量=1210.5×79/21=4553.8kmol/h=127506.4kg/h Ⅰ段理论干空气量=O2+N2 =5764.3kmol/h=166242.4kg/h Ⅱ段碳燃烧生成CO2需O2量=197.6kmol/h=6323.2kmol/h Ⅱ段碳燃烧生成CO2需N2=197.6×79/21=743.4kmol/h=20813.9kg/h Ⅱ段碳燃烧生成CO2需N2== O2+ N2=941kmol/h=23137.1kg/h 1.1.3 实际干空气量
- 1、下载文档前请自行甄别文档内容的完整性,平台不提供额外的编辑、内容补充、找答案等附加服务。
- 2、"仅部分预览"的文档,不可在线预览部分如存在完整性等问题,可反馈申请退款(可完整预览的文档不适用该条件!)。
- 3、如文档侵犯您的权益,请联系客服反馈,我们会尽快为您处理(人工客服工作时间:9:00-18:30)。
式 中 : —— 钢壁 热阻 ,m ・・ ) 4 16l; 3 ( 2h ℃ /× .88( J d— —钢 壁厚度 , 2 m; 2 钢壁导热系数 , 4 1 8J( h℃) —— × . 6k/m・・ 。 8
4烟气中携带催化剂因此衬里对于该烟道124烟道外壁与空气间的传热系数a抗磨损以及长周期安全运行起到了重要作用但烟道裸露于空气中其外壁与空气间为对流同时也阻碍了烟道内烟气的散热
谶 藏米
P c e化a 设s 石h flc l De 油Ii工 计 e
催化裂化装置三旋至 四旋烟气温降计算 及分析
12 1 烟气传 热 系数a ..
作者简介 :侯 瑞峰 , 河 南省唐 河县人 。2o 男, 0 1年毕
业于石油大学( 北京 ) 学工程 系, 工 学硕士 学位 , 化 获 工程师。现从事催化裂化装置 工艺与工程设 计工作。
联 系电 话 : l O 0—8 8 7 5 4 7 l5
/
1 2 6 总 的散热 量 Q 2 .. a
燕
垛
,
Q2 (i+£ t 2一 ] 【o a=[ 。) 。 d / 7
(1 1)
式中 :——三旋至四旋间烟道总长度, m;
d—— 烟 道钢壁 直径 , 。 m。 13 出 口烟 气温 度 £ . 。
由 Q l a 以得 出下式 : 。=Q2 可
2 理论计 算分 析
123 钢壁 传热 系数 a ..
烟道钢壁为热传导传热 :
R = /2 3 2 () 6
在具体设计过程 中, 三旋至 四旋间烟道 内烟 气温降的理论计算 , 还受这些因素影响 :
() 气 流 速 越 大 , 有 利 于热 量 传 递 , 气 1烟 越 烟 通过 该烟 道 的温降越 大 ; () 道 直 径 和 长 度 越 大 , 热 面积 越 大 , 2烟 散 导 致烟 气通过 该烟道 的温降也 越大 ; () 3 环境 温度越 低 以及 空 气 流动 速 度越 大 , 越
图 2 系数 B与烟气温度的关系
a =1 尺 2 / l
() 5
( i一 u ×∑nci n 。 ) t i。
:
式中:2 a——衬里层传热热阻 , 4 16k/ m ・ × .88J( 2 h
・
[£ +£t/ 一 ] c0 (i 。)2 7 d
(2 1)
℃) 。
在催 化 裂化 装 置 能 量 回收 部 分 , 为满 足 烟 机
a =日 。 / 。 l “・ D ・
() 2
平稳运行和环保要求 , 置了三旋 ( 设 第三级旋风分
离器 ) 四旋 ( 四级旋 风 分 离器 ) 及 第 系统 , 生烟 气 再 进入 三旋 回收后 , 少量 烟 气携 带 催化 剂 粉末 , 三 经 旋底 部衬 里 烟道 进 入 四旋 , 催 化 剂 进 行 进 一 步 对
1 三旋至 四旋 烟道烟 气温 降计算
1 1 烟气 总热损 失 Q l . 。
烟气佝 热方向 一
图 1 高温烟气与环境间的传 热路径
捌
她
Rl
尺2
R 3
t
f
D/ 2
l ,l A z A
I I【d2
耐磨 I
— — — —
通 过计算 烟 道 出入 口烟 气 的焓 变 , 以得 出 可 烟气通 过该段 烟道 的总热 损失 _ 。 1 J
烟道内烟气与衬里内壁为对流传热[ : ]
第2 5卷
侯 瑞峰 . 催化裂化装置三 旋至 四旋烟 气温降计算及分析
/
式 中 :K — 烟 气 与 空 气 间 总 传 热 系 数 , —
× .8 8J ( l h q ) 4 16 l/ Ⅱ ・ ・C 。 【 2
/
/
∞
/ 。
收稿 日期 :0 8 6 2 2o —0 —1。
式() 1 中,。为最终所求量 , 和 ci i 。 均可通
过查表 或实测 获得 。
12 总 的散热量 Qa 。 . 2一 []
通过计算 总的传热系数 , 以得 出该段烟道 可
总 的散 热损失 。烟气 与环 境 间的传热 路径见 图 1 。
侯 瑞峰
( 国石 化 工 程 建 设 公 司 , 京 1o0 ) 中 北 0 11
摘要 : 绍了催化裂化装置三旋至四旋烟道 内烟气温降 的计 算方法 , 立 了对该烟道设计 有指导 意 介 建 义的理论公式 , 并对影响温 降的 因素进行 了分析。此举 既优化 了烟道 气工 艺设计又节能降耗 。 关键词 : 催化裂化装置 :烟道 ; 烟气 ; 三旋 ;四旋
烟道内衬里层为热传导传热 :
R =d 1 2 l () 4
ci 。 ——烟 气 中 各 组 分 分 子 平 均 比 热 ,
x4 16 k/ k 0・ 。 .88 J (m l℃)
式中:2 R —— 衬里 热阻 ,m ・・ /×4 16 l; ( 2h ℃) .88【 J d— —衬 里层厚 度 , , m; A— —衬里导热系数 , 416 ( h℃) × .88 m・・ 。
i ——三旋至四旋烟道人 口处温度 , ℃;
£ —— 三旋 至 四旋 烟道 出 口处 温度 , ℃;
n; — —
式 中: R —— 烟气热 阻 ,m ・ ・ /×4 16k。 ( 2h ℃) .88J
12 2 衬里 层传 热 系数 ..
烟气 中各组 分摩 尔流量 ,m 】h k0 ; /
式 中 :l 烟气传热系数 , 416k/ ・・ ; a—— × . 8J( h ℃) 8
B — 系数 ; —
“— —
烟 气质 量流速 , ( 2s ; k m ・)
D — 烟 四旋 的烟道带有耐磨衬里 , 烟道 内烟气的温降计算非 常复杂 , 故设计 中采用经验 估值。通过理论分析并结合工业实 际, 建立 了简 单有效的烟道内烟气温降计算方法。
Q 1 n) =(i一}J ×∑nci 【 f i。 () 1
通过计 算烟 气进 出 口平 均 温度 £ =(i+ f
)2查 图 2可得 系数 日。 /,
尺】 a = 】 () 3
式 中: 。 Q ——三旋至四旋烟道内烟气总的热损失 ,
×4.8 8 J h 1 6 k/ ;