高聚物合成工艺课后题答案
高聚物合成工艺学B 答案

一. 选择题(30分,每题3分)ACCAB CABDC二、判断并改错(20分,每题2分)(判断对错1分,改正1分)1. 利用齐格勒-纳塔催化剂可合成LDPE。
(错, LDPE→HDPE )2. 悬浮聚合突出特点是聚合速度快,同时产物分子量大。
(错,悬浮聚合→乳液聚合)3. PVC的空隙率主要影响材料的强度。
(错,强度→对增塑剂的吸收)4. 溶液聚合中溶剂极性将影响离子链的增长速度。
(正确)5. 线型缩聚影响分子量主要因素为官能团转化率、小分子含量及保持熔融状态。
(错,去掉保持熔融状态)6. 聚氨酯具有很高的强度,其中一个原因是分子链上的-C=O可与另一分子上的C形成氢键。
(C→另一分子N上的H )7. 乙烯高压聚合,当压力升高,反应过程在均相中进行时,容易产生凝胶物。
(错,容易→不会)8. 在制备溶液丁苯胶过程中,常加入一定量的四氢呋喃,目的是为了增大苯乙烯在分子链中的嵌段含量。
(错,嵌段含量→无规含量)9. 高顺式聚丁二烯橡胶所用催化剂是镍系齐格勒-纳塔催化剂。
(正确)10. 二元胺-二元酸聚酰胺的熔点随主链上的C原子数目的升高逐渐降低。
(错,逐渐降低→呈锯齿形变化)三、名词解释(每题5分,共20分)1.动态界面缩聚:在搅拌力的作用下使两相中的一相为分散相,另一相为连续相,此时大大的增加了两相的接触面积,而且界面层可以不断的更新,从而促进了缩聚反应的进行2.人造纤维:由非纤维状天然高分子化合物经化学加工得到的纤维。
P1913.阻聚剂:阻聚剂可以防止聚合作用的进行,在聚合过程中产生诱导期(即聚合速度为零的一段时间),诱导期的长短与阻聚剂含量成正比,阻聚剂消耗完后,诱导期结束,即按无阻聚剂存在时的正常速度进行。
4.透气性:一般为一定厚度的薄膜于一定时间,与规定压力下,单位面积所透过的气体体积。
四、简答题(每题5分,共20分)1、线型缩聚物生产工艺有何特点a缩聚反应为逐步进行的平衡反应b原料配比将明显影响产品分子量c缩聚物端基的活性基团将影响成型时的熔融粘度d反应析出的小分子化合物必须及时脱除2尼龙-66合成原理、融熔缩聚过程包括的主要工序:分离工序、闪蒸工序、后反应工序。
高聚物合成工艺学答案高聚物答案

高聚物合成工艺学答案高聚物答案5(指明影响引发剂引发效率的原因。
引发效率的定义是引发剂分子分解产生的初级自由基用于形成单体自由基的百分数。
影响引发效率大小的原因主要有以下几个方面:如果存在“笼蔽效应”,则引发效率降低;如果存在“诱导分解”,则引发效率降低,该影响取决于引发剂的种类;如果被引发单体的活性较大,则引发效率增加,反之,减小;1如果被引发单体浓度较低,且在溶液聚合条件下,则容易形成“笼蔽效应”,而使引发效率降低;如果聚合体系黏度较高,则“笼蔽效应”也较严重,则引发效率降低;溶液聚合时的引发效率低于本体聚合和悬浮聚合。
6(画出自由基聚合时的聚合速率变化曲线,并阐明各阶段的产生原因。
该曲线可以明显地分为诱导期、聚合初期、聚合中期、聚合后期四个阶段。
其中聚合初期属于微观动力学研究范畴,聚合中期以后为宏观动力学研究范畴。
1、诱导期的特征是聚合速率为零。
在诱导期阶段,引发剂分解产生的初级自由基,主要被阻聚杂质所终止,不能引发单体,无聚合物生成,聚合速率为零。
诱导对工业生产的危害是延长聚2合周期,增加动力消耗。
消除诱导期的根本途径是必须清除阻聚合杂质,将杂质含量控制在0.003%以下,单体纯度达99.9,,99.99,以上。
非常纯净的单体聚合时,可以没有诱导期。
2、聚合初期的特征是聚合速率等速平稳。
此阶段在诱导期过后,阻聚杂质耗尽,并由于大分子较少,体系粘度较低,单体和链自由都能进行正常聚合。
在进行微观动力学研究时,转化率控制下5,以下;在工业生产中控制在10,,20 ,以下。
3、聚合中期的特征是聚合速率自动加速。
原因是由于转化率增高,体系内大分子浓度增加,造成粘度增大,使长链自由基的活动受阻,甚至端基包裹,难于双基终止,kt下降;而单体分子因体积较小,仍可以自由活动,能继续与链自由基碰撞而增长,kP不变或变化不大。
这样造成聚合速率Rp随kp/kt1/2的急剧增加而自动加速。
这种由于体系粘度增加所引起的不正常动力学行为称为凝胶效应。
聚合物合成工艺学思考题及 其答案
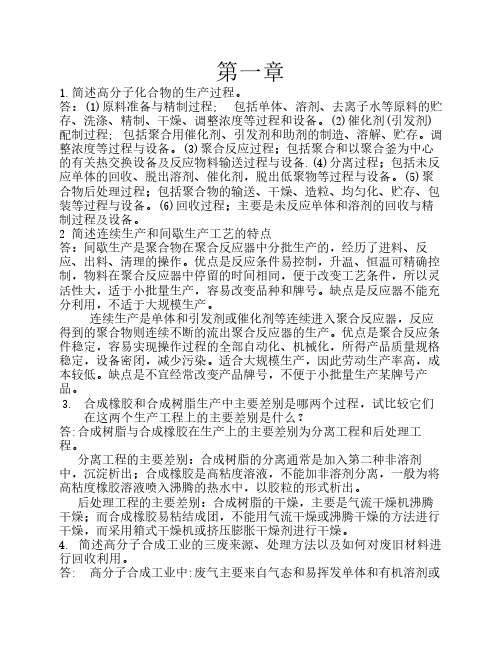
第一章1.简述高分子化合物的生产过程。
答:(1)原料准备与精制过程; 包括单体、溶剂、去离子水等原料的贮存、洗涤、精制、干燥、调整浓度等过程和设备。
(2)催化剂(引发剂)配制过程; 包括聚合用催化剂、引发剂和助剂的制造、溶解、贮存。
调整浓度等过程与设备。
(3)聚合反应过程;包括聚合和以聚合釜为中心的有关热交换设备及反应物料输送过程与设备.(4)分离过程;包括未反应单体的回收、脱出溶剂、催化剂,脱出低聚物等过程与设备。
(5)聚合物后处理过程;包括聚合物的输送、干燥、造粒、均匀化、贮存、包装等过程与设备。
(6)回收过程;主要是未反应单体和溶剂的回收与精制过程及设备。
2 简述连续生产和间歇生产工艺的特点答:间歇生产是聚合物在聚合反应器中分批生产的,经历了进料、反应、出料、清理的操作。
优点是反应条件易控制,升温、恒温可精确控制,物料在聚合反应器中停留的时间相同,便于改变工艺条件,所以灵活性大,适于小批量生产,容易改变品种和牌号。
缺点是反应器不能充分利用,不适于大规模生产。
连续生产是单体和引发剂或催化剂等连续进入聚合反应器,反应得到的聚合物则连续不断的流出聚合反应器的生产。
优点是聚合反应条件稳定,容易实现操作过程的全部自动化、机械化,所得产品质量规格稳定,设备密闭,减少污染。
适合大规模生产,因此劳动生产率高,成本较低。
缺点是不宜经常改变产品牌号,不便于小批量生产某牌号产品。
3. 合成橡胶和合成树脂生产中主要差别是哪两个过程,试比较它们在这两个生产工程上的主要差别是什么?答:合成树脂与合成橡胶在生产上的主要差别为分离工程和后处理工程。
分离工程的主要差别:合成树脂的分离通常是加入第二种非溶剂中,沉淀析出;合成橡胶是高粘度溶液,不能加非溶剂分离,一般为将高粘度橡胶溶液喷入沸腾的热水中,以胶粒的形式析出。
后处理工程的主要差别:合成树脂的干燥,主要是气流干燥机沸腾干燥;而合成橡胶易粘结成团,不能用气流干燥或沸腾干燥的方法进行干燥,而采用箱式干燥机或挤压膨胀干燥剂进行干燥。
(完整word版)高聚物合成工艺课后题答案
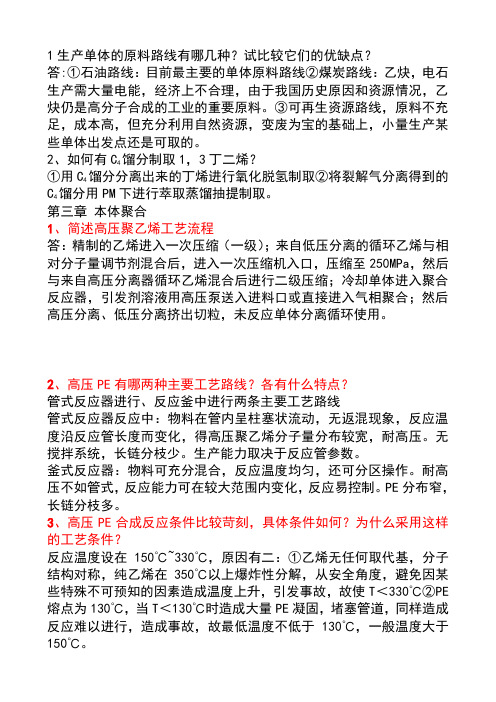
1生产单体的原料路线有哪几种?试比较它们的优缺点?答:①石油路线:目前最主要的单体原料路线②煤炭路线:乙炔,电石生产需大量电能,经济上不合理,由于我国历史原因和资源情况,乙炔仍是高分子合成的工业的重要原料。
③可再生资源路线,原料不充足,成本高,但充分利用自然资源,变废为宝的基础上,小量生产某些单体出发点还是可取的。
2、如何有C4馏分制取1,3丁二烯?①用C4馏分分离出来的丁烯进行氧化脱氢制取②将裂解气分离得到的C4馏分用PM下进行萃取蒸馏抽提制取。
第三章本体聚合1、简述高压聚乙烯工艺流程答:精制的乙烯进入一次压缩(一级);来自低压分离的循环乙烯与相对分子量调节剂混合后,进入一次压缩机入口,压缩至250MPa,然后与来自高压分离器循环乙烯混合后进行二级压缩;冷却单体进入聚合反应器,引发剂溶液用高压泵送入进料口或直接进入气相聚合;然后高压分离、低压分离挤出切粒,未反应单体分离循环使用。
2、高压PE有哪两种主要工艺路线?各有什么特点?管式反应器进行、反应釜中进行两条主要工艺路线管式反应器反应中:物料在管内呈柱塞状流动,无返混现象,反应温度沿反应管长度而变化,得高压聚乙烯分子量分布较宽,耐高压。
无搅拌系统,长链分枝少。
生产能力取决于反应管参数。
釜式反应器:物料可充分混合,反应温度均匀,还可分区操作。
耐高压不如管式,反应能力可在较大范围内变化,反应易控制。
PE分布窄,长链分枝多。
3、高压PE合成反应条件比较苛刻,具体条件如何?为什么采用这样的工艺条件?反应温度设在150℃~330℃,原因有二:①乙烯无任何取代基,分子结构对称,纯乙烯在350℃以上爆炸性分解,从安全角度,避免因某些特殊不可预知的因素造成温度上升,引发事故,故使T<330℃②PE 熔点为130℃,当T<130℃时造成大量PE凝固,堵塞管道,同样造成反应难以进行,造成事故,故最低温度不低于130℃,一般温度大于150℃。
反应在低压下进行,原因:乙烯常压下位气体,分子间距离远,不易反应,压缩后,分子间距离显著缩短,极大增加了自由基与单体分子之间碰撞几率,易反应,在100~300MPa下,C2H4接近液态烃,近似不可压缩状态,其次T上升,需压力也增加,才能使PE与单体形成均相状态,保持反应顺利进行。
聚合物合成工艺学每章节后面的思考题

第一章课后思考题(聚合物合成工艺学)1.简述高分子化合物的生产过程?答:(1)原料准备与精制过程:包括单体、溶剂、去离子水等原料的贮存、洗涤、精制、干燥、调整浓度等过程相设备。
(2)催化剂(引发剂)配制过程:包括聚合用催化剂、引发剂和助剂的制造、溶解、贮存、调整浓度等过程与设备。
(3)聚合反应过程:包括聚合和以聚合釜为中心的有关热交换设备及反应物料输送过程与设备。
(4)分离过程:包括未反应单体的回收、脱除溶剂、催化剂,脱除低聚物等过程与设备。
(5)聚合物后处理过程:包括聚合物的输送、干燥、造粒、均匀化、贮存、包装等过程与设备。
(6)回收过程:主要是未反应单体和溶剂的回收与精制过程及设备。
此外三废处理和公用工程如供电、供气、供水等设备。
2.比较连续生产和间歇生产工艺特点?答:连续生产:优点:聚合反应条件稳定,容易实现操作过程中的自动化;若条件一致,则产品质量规格稳定;设备密闭,减少污染;适合大规模生产;劳动生产率高,成本较低。
缺点:不便于小批量生产某牌号产品。
间歇生产:优点:反应条件以控制;物料在聚合反应器内停留时间相同;便于改变工艺条件。
缺点:不易实现操作过程的全部自动化;必须按配方规定的顺序进行;不适合大规模生产,生产能力低。
3.合成橡胶和合成树脂在生产过程中的那两个过程?试比较他们在这两个生产过程上的主要差别是什么?答:主要差别是分离过程和聚合物后处理过程;分离过程:合成橡胶:不能用第二种溶剂以分离合成橡胶,其分离方法是将高粘度橡胶溶液喷入沸腾的水中,同时进行强烈搅拌,未反应的单体和溶剂与一部分水蒸气被蒸出,合成橡胶则以直径10~20mm左右的胶粒析出,且悬浮于水中,经过滤洗涤得到胶粒;合成树脂:将合成树脂溶液逐渐加入第二种非溶剂中,而此溶剂是可以与原来的容剂混溶的,再沉淀釜中搅拌则合成树脂呈粉末状固体析出,如果通过细孔进入沉淀用溶剂中,则生成纤维状产品。
后处理过程:合成橡胶:采用箱式干燥机活挤压膨胀干燥机进行干燥;合成树脂:用加热的空气作为载热体进行气流干燥,含有机溶剂时,用加热的氮气进行干燥。
高聚物合成工艺
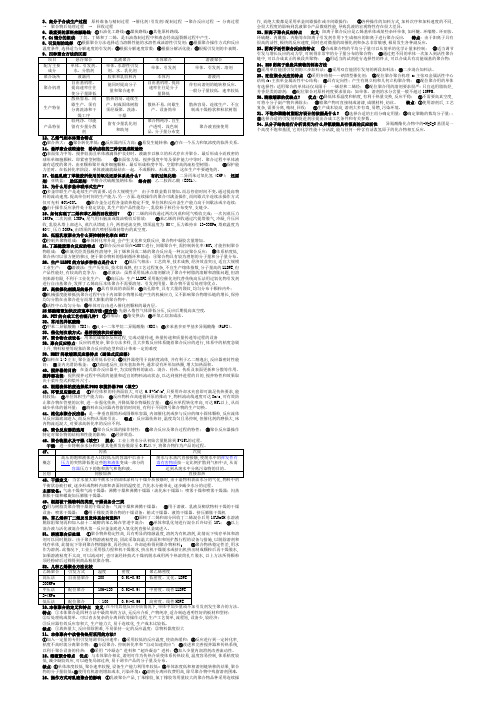
3、高分子合成生产过程 原料准备与精制过程 →催化剂(引发剂)配制过程 →聚合反应过程 → 分离过程 → 聚合物后处理过程 → 回收过程6、最重要的原料来源路线:①石油化工路线;②煤炭路线;③其他原料路线.7、C4馏分的组成:丁烷、丁烯和丁二烯,是石油炼制过程中和液态烃高温裂解过程中产生。
8、引发剂的选择 ①根据聚合方法选择适当溶解性能的水溶性或油溶性引发剂;②根据聚合操作方式和反应温度条件,选择适当分解速度的引发剂;③根据分解速度常数;④根据分解活化能;⑤根据引发剂的半衰期。
①聚合热大; ②聚合转化率低;③反应器内压力高;④易发生链转移;⑤存在一个压力和氧浓度的临界关系。
14、悬浮聚合成粒途径 粉状成粒的三种宏观成粒途径①表面张力中等,搅拌较弱且单体液滴保护良好时,液滴多以独立的形式存在并聚合,最后形成小而致密的球形单细胞颗粒,即紧密型树脂; ②表面张力低,搅拌强度中等及保护能力中等时,聚合过程中单体液滴有适度的聚并,由亚颗粒聚并成多细胞颗粒,最后形成粒度中等,空隙率高的疏松型树脂; ③保护能力差时,在低转化率阶段,单体液滴就凝结在一起,不成颗粒,形成大块,这在生产中要避免的。
17、低温乳液丁苯橡胶所使用的氧化还原体系是什么? 有机过氧化物:二异丙苯过氧化氢(CHP ); 还原剂:亚铁盐; 助还原剂:甲醛合次硫酸氢钠体系; 络合剂:乙二胺四乙酸(EDTA )。
18、为什么用多釜串联形式生产?①多釜串联生产是连续生产的需要.适合大规模生产 由于串联釜数目增加.而总停留时间不变.通过提高物料的流动速度.提高单位时间的生产能力.另一方面.连续操作的聚合可满釜操作,而间歇式半连续法操作方式仅可充料60%-80%. ②聚合釜全过程各釜放热稳定不变,单位体积反应釜生产能力高于间歇法或半连续;③由于操作反应条件处于稳定状态,其生产的产品性能均一,乳胶粒子粒径分布变窄,支链少。
19、如何实现丁二烯和苯乙烯的回收使用? ①丁二烯的回收通过两次闪蒸和尾气吸收完成;一次闪蒸压力19KPa,二次闪蒸13KPa,尾气用石脑油或煤油吸收后排放; ②苯乙烯的回收通过汽提塔脱气,冷凝,升压回收,乳胶从塔上部进入,蒸汽从塔底上升,两者逆流交换,塔顶温度为50℃,压力维持在13-33KPa,塔底温度为60℃,压力30KPa,由塔顶的蒸汽喷射泵维持塔内的真空度。
高聚物合成技术(材料211)学习通课后章节答案期末考试题库2023年
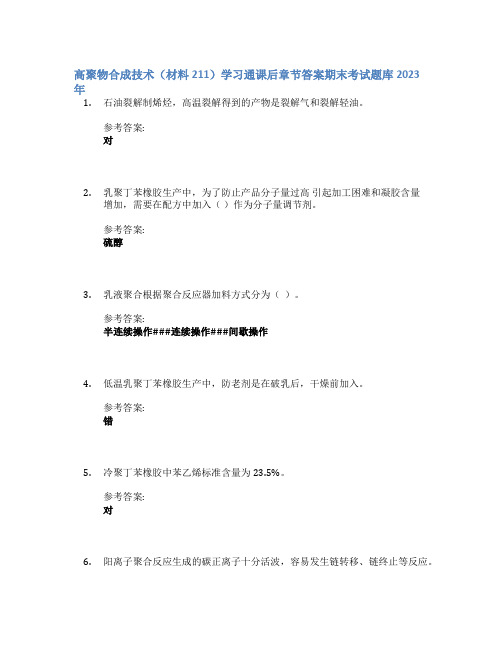
高聚物合成技术(材料211)学习通课后章节答案期末考试题库2023年1.石油裂解制烯烃,高温裂解得到的产物是裂解气和裂解轻油。
参考答案:对2.乳聚丁苯橡胶生产中,为了防止产品分子量过高引起加工困难和凝胶含量增加,需要在配方中加入()作为分子量调节剂。
参考答案:硫醇3.乳液聚合根据聚合反应器加料方式分为()。
参考答案:半连续操作###连续操作###间歇操作4.低温乳聚丁苯橡胶生产中,防老剂是在破乳后,干燥前加入。
参考答案:错5.冷聚丁苯橡胶中苯乙烯标准含量为23.5%。
参考答案:对6.阳离子聚合反应生成的碳正离子十分活波,容易发生链转移、链终止等反应。
参考答案:对7.下面单体可以由石油催化重整制得有()参考答案:二甲苯###甲苯###苯8.乳液聚合体系基本上消除了自动加速现象。
参考答案:对9.聚合方法的选择原则是()。
参考答案:产品的用途###产品的成本10.以下答案属于高聚物生产工序是()参考答案:分离回收###聚合反应###聚合物后处理###原料与引发剂的配制11.石油裂解主要生产的烯类单体是()参考答案:丙烯###1、3丁二烯###乙烯12.聚合反应机理()参考答案:连锁反应原理###逐步反应原理13.自由基聚合反应实施方法有()参考答案:乳液聚合###悬浮聚合###溶液聚合###本体聚合14.不同解离程度的离子对,对离子聚合速度的影响是不同的,其影响从大到小的顺序为:自由基离子对、松散离子对、结合离子对。
参考答案:对15.乳化剂是一种表面活性剂。
参考答案:对16.单体液滴是为胶乳颗粒增长提供单体的储存器。
参考答案:对17.乳液聚合反应开始前,单体主要以()形式存在于单体/水乳化体系中。
参考答案:单体增溶胶束###单体液滴18.引发剂遇水失活,故阴离子聚合的实施方法不宜采用()。
参考答案:乳液聚合###悬浮聚合19.低温乳聚丁苯橡胶生产中,引发体系包括()。
参考答案:还原剂###活化剂###过氧化物###螯合剂20.低温乳聚丁苯橡胶生产中,回收丁二烯的设备是()。
工艺学习题参考答案

高聚物合成工艺学习题参考第一章绪论【1】试述高分子合成工艺学的主要任务。
答:高分子合成工艺学是应用化学专业材料化学方向学生一门必修的专业基础课,通过学习高分子制备原理及高分子材料的制备工艺,使学生掌握通用高分子材料的工艺特点和工艺过程,了解高分子材料的制备工艺和材料的改性,对高分子材料在实际生产中有初步的认识。
为今后进一步学习有关材料科学学科的课程打下较好的基础。
高分子合成工业的基本任务。
答:将简单的有机化合物(单体),经聚合反应使之成为高分子化合物。
【2】用方块图表示高分子合成材料的生产过程,说明每一步骤的主要特点及意义。
答: 1)原料准备与精制过程特点:单体溶剂等可能含有杂质,会影响到聚合物的原子量,进而影响聚合物的性能,须除去杂质意义:为制备良好的聚合物做准备2)催化剂配制过程特点:催化剂或引发剂的用量在反应中起到至关重要的作用,需仔细调制. 意义:控制反应速率,引发反应3)聚合反应过程特点:单体反应生成聚合物,调节聚合物的分子量等,制取所需产品意义:控制反应进程,调节聚合物分子量4)分离过程特点:聚合物众位反应的单体需回收,溶剂,催化剂须除去意义:提纯产品,提高原料利用率5)聚合物后处理过程特点:聚合物中含有水等;需干燥. 意义:产品易于贮存与运输6)回收过程特点:回收未反应单体与溶剂意义:提高原料利用率,降低成本,防止污染环境【3】如何评价生产工艺合理及先进性。
答:1)生产方式2)产品性能:产品系列化3)原料路线4)能量消耗与利用5)生产技术水平:降低生产技术费塑料的原料是合成树脂和添加剂(助剂)。
根据反应机理不同,高分子聚合反应可分为连锁聚合和逐步聚合;根据单体和产物组成和结构的不同可分为加聚反应和缩聚反应。
【4】塑料生产中加入稳定剂和润滑剂的作用分别是什么?答:稳定剂的作用主要是防止成型过程中高聚物受热分解,或长期使用过程中防止高聚物受光和氯的作用而老化降解。
有热稳定剂、光稳定剂、抗氧剂等。
- 1、下载文档前请自行甄别文档内容的完整性,平台不提供额外的编辑、内容补充、找答案等附加服务。
- 2、"仅部分预览"的文档,不可在线预览部分如存在完整性等问题,可反馈申请退款(可完整预览的文档不适用该条件!)。
- 3、如文档侵犯您的权益,请联系客服反馈,我们会尽快为您处理(人工客服工作时间:9:00-18:30)。
1生产单体的原料路线有哪几种?试比较它们的优缺点?答:①石油路线:目前最主要的单体原料路线②煤炭路线:乙炔,电石生产需大量电能,经济上不合理,由于我国历史原因和资源情况,乙炔仍是高分子合成的工业的重要原料。
③可再生资源路线,原料不充足,成本高,但充分利用自然资源,变废为宝的基础上,小量生产某些单体出发点还是可取的。
2、如何有C4馏分制取1,3丁二烯?①用C4馏分分离出来的丁烯进行氧化脱氢制取②将裂解气分离得到的C4馏分用PM下进行萃取蒸馏抽提制取。
第三章本体聚合1、简述高压聚乙烯工艺流程答:精制的乙烯进入一次压缩(一级);来自低压分离的循环乙烯与相对分子量调节剂混合后,进入一次压缩机入口,压缩至250MPa,然后与来自高压分离器循环乙烯混合后进行二级压缩;冷却单体进入聚合反应器,引发剂溶液用高压泵送入进料口或直接进入气相聚合;然后高压分离、低压分离挤出切粒,未反应单体分离循环使用。
2、高压PE有哪两种主要工艺路线?各有什么特点?管式反应器进行、反应釜中进行两条主要工艺路线管式反应器反应中:物料在管内呈柱塞状流动,无返混现象,反应温度沿反应管长度而变化,得高压聚乙烯分子量分布较宽,耐高压。
无搅拌系统,长链分枝少。
生产能力取决于反应管参数。
釜式反应器:物料可充分混合,反应温度均匀,还可分区操作。
耐高压不如管式,反应能力可在较大范围内变化,反应易控制。
PE分布窄,长链分枝多。
3、高压PE合成反应条件比较苛刻,具体条件如何?为什么采用这样的工艺条件?反应温度设在150℃~330℃,原因有二:①乙烯无任何取代基,分子结构对称,纯乙烯在350℃以上爆炸性分解,从安全角度,避免因某些特殊不可预知的因素造成温度上升,引发事故,故使T<330℃②PE 熔点为130℃,当T<130℃时造成大量PE凝固,堵塞管道,同样造成反应难以进行,造成事故,故最低温度不低于130℃,一般温度大于150℃。
反应在低压下进行,原因:乙烯常压下位气体,分子间距离远,不易反应,压缩后,分子间距离显著缩短,极大增加了自由基与单体分子之间碰撞几率,易反应,在100~300MPa下,C2H4接近液态烃,近似不可压缩状态,其次T上升,需压力也增加,才能使PE与单体形成均相状态,保持反应顺利进行。
转化率15~30%:明显低于其他单体本体聚合,f造成大量乙烯需要循环使用。
—CH高,热容小,f提高1%,温度上升12~13℃,如果反应热不能及时移除,极易造成温度急剧上升,从而造成爆炸发生,故一般提高f困难,另外提高f,PE含量,易发生分相,需更高压力才能保持均相f上升困难。
4、本体法聚合工艺常需分段,为什么?试以本体法啊VC聚合工艺为例分析。
首先分段聚合原因:①从工程上,预聚时粘度低流动性高,对反应器要求不高,后聚时粘度高,流动性差,对搅拌器要求很高②机理上,预聚时转化率不高,粘度不大,聚合热易排出,可采用较高温度下较短时间内,利用搅拌加速反应,以使自动加速现象提前到来,缩短了聚合周期,提高了效率。
后期,降低温度,?降低,充分利用自动加速现象,使反应基本上在平稳条件下进行,避免由于自动加速现象而造成局部过热,既保证了安全生产又保证了质量。
其次,对PVC而言,当f小于20%物料固液共存,而f≥40时表现为干燥粒子,不同f物料呈现不同相态,对传质、传热要求明显不同,对反应器要求也不同,故采用了分段聚合。
5、简要讨论本体聚合的工艺特点杂质少,产品纯净;工艺流程相对较短,所需设备少;反应器要求相对较高,反应热移除相对困难;单程转化率相对较低,多采用分段聚合;产物分子量分布相对较宽,反应后期传热传质困难,凝胶效应严重。
6、自由基聚合引发剂有哪些种类?如何进行选择?其中过氧类有哪些类型?过氧化物类、偶氮类、氧化还原体系等。
过氧类有烷基过氧化氢类、过氧酸类、过氧化二烷基、过氧化二酰基、过氧化碳酸二酯类、过氧化磺酸酯类氢过氧化物等。
选择方法根据分解活性能、分解速度常数选择。
①根据聚合方法选取,悬浮、本体、溶液聚合选择油溶性引发体系,乳液聚合选择水溶性引发体系。
根据操作方式和反应温度,间歇聚合依据反应时间,连续聚合依据停留时间选取与反应时间同数量级半衰期的引发剂;高温热分解型、低温氧化还原体系。
再者根据用途不同选择,过氧类易着色,偶氮类的-CN有毒等。
7、从高分子化学原理出发,简要讨论控制自由基聚合产物分子量的主要手段根据自由基聚合原理可知,影响M主要因素:聚合反应温度,引发剂浓度、单体浓度、链转移剂种类及用量。
应严格控制引发剂使用量,严格控制反应温度;选用适当链转移剂品种及用量。
一般[I]增加,Rp 也增加,严重时反应失控,另外残留量提高,影响产物贮存性能,反应温度影响反应Ri、Rp、Rtr与程度,从而影响产物Xn。
第四章悬浮聚合1、简述悬浮聚合及其工艺特点工艺流程较短,设备要求相对简单;反应过程较易控制,反应体系中含大量水作介质;体系粘度低,反应热易除去;树脂纯度以乳液法高;三废排放量以乳液法低。
缺点:难以实现连续化生产;三废排放量比本体法高;产品纯度比本体法更低。
2、悬浮聚合基本组成和工艺过程如何?基本组成:单体(难溶于水)、溶剂水、分散剂、油溶性引发剂、分子量调节剂等。
基本组成在一定搅拌强度下聚合反应→固液分离→聚合物后处理(在达到反应温度时最后加引发剂)3、分散剂主要种类有哪些?水溶性高分子化合物:合成、半合成、天然聚合物,例PVA,SMA,PAA,明胶。
纤维素醚类等不溶于水的无机化合物粉末:例CaCO3,MgCO3,BaCO3等SMA钠盐(苯乙烯-马来酸酐共聚物醚类等助分散剂(表面活性剂):起调整颗粒形态和粒径作用。
4、VC悬浮聚合工艺流程和主要设备有哪些?主要设备:聚合釜,冷凝器、储液罐、氯乙烯剥离塔、分离器、沸腾床、离心机等工艺流程:①准备工作:开动搅拌,加入悬浮剂溶液、水相阻聚剂、Na2S、缓冲剂溶液②聚合,加入引发剂单体,控制一定温度聚合,保证适当的减半速度③分离,加入链终止剂,减压拖出单体,进入单体回收系统,然后?④聚合物后处理:干燥、筛分等。
5、结合反应过程,对VC工艺控制曲线进行简要分析。
(有图)a曲线为压力曲线,投料后,温度上升,故压力升高,达到恒定温度时,压力恒定,反应后期游离单体骤减少,压力开始下降,monomer消失时,压力急剧减少b曲线为物料温度控制曲线,为核心指标,温度波动≤0.2℃,除起始阶段物料温度增加外达到设定温度后,维持一条近似水平直线。
c曲线为夹套温度控制曲线,通过C控制b曲线恒定性,先高后低再高的特点,升温阶段,通过夹套物料升温,故夹套温度高。
反应初期,接近反应温度时,夹套温度下降,VC聚合放出大量的热,使物料温度恒定,夹套要降温。
自动加速阶段:PVC不溶于VC,但VC可溶于PVC,粘性凝胶,Rp上升,自动加速,放出大量的热使?上升,故夹套温度继续下降,以使b曲线恒定,反应后期,[M]下降,Rp下降,反应热减少,夹套温度开始升高,并逐渐接近物料反应温度。
6、VC单体合成工艺路线主要有哪两种?写出反应方程式并简要比较一:电石法合成工艺,CaC2+H2O→→(HCl)CH2=CHCl二:先进工艺,①乙烯与Cl2加成(加成氧化)②乙烯与氯气、氧气加成氧化(氯氧化)③二氯乙烷裂解反应。
总反应式:乙烯与氯气、氧气生成氯乙烯乙炔法需采用高能耗电石为原料,逐渐为先进工艺所取代,反应仅乙烯、氯气、氧气三种,原料易得耗能少。
第六章1、简述乳液聚合工业特点和典型工业流程优点:.聚合物始终保持高分子分散状态,物料粘度低,传热容易,比较容易实现连续聚合;部分产品可以直接应用,且不含溶剂,产品环保性好;自由基不易终止,易制得分子量较高产物。
缺点:需要固体聚合物时,后处理工艺耗能高且污染严重,破乳消耗大量助剂且废水量较大,直接干燥,体系含水量大,消耗能源多。
典型工艺流程:乳化→聚合→脱单体→后处理(工艺)2.低温乳液聚合SBR的生产中引发体系组分构成,各组分主要作用,写出反应方程式氧化还原体系:氧化剂:异丙苯过氧化氢、对[艹孟]烷过氧化氢、K2S2O8等;还原剂:亚铁盐,EDTA钠盐,双雕白块,保险粉.①亚铁盐, 对[艹孟]烷过氧化氢:产生自由基CH3-苯-C(CH3)2-O-OH+Fe2+----CH3-苯-C(CH3)2-O`+OH-+Fe3+②EDTA一二钠盐:作用与Fe2+形成易溶性络合物,防止Fe(OH)3沉淀产生,该络合物在水中离解度小,H+,OH-中都很稳定,可较长时间保持Fe2+存在.。
EDTA一二钠盐+Fe2+→EDTA-Fe2+.③吊白块作用:Fe2+经氧化后形成Fe3+,呈棕色,浓度过高会影响SBR外观,与色泽,吊白块作2级还原剂,使Fe3+再还原.4Fe3++2CH2O.NaHSO3.2H2O------4Fe2++2HCOOH+Na2SO4+8H+②③作用使体系减少FeSO4使用,有利于提高产品色泽.④保险粉作用,反应温度下降,水中O2多,阻聚作用显著保险粉与O2反应减少阻聚作用.2Na2S2O4+3O2→2Na2SO4+2H2SO4+2H2O3、乳液聚合分类典型乳液聚合、种子乳液聚合、微悬浮聚合(细乳液聚合),反相乳液聚合,核-壳乳液聚合4、表面活性剂与乳化剂有什么区别?表面活性剂:表面张力随溶质C上升先急剧下降,但达到一定C时C上升,表面张力下降不再明显,这类物质称表面活性剂。
乳化剂:使不溶水液体与水形成稳定胶体分散的体系的物质,一般包括表面活性剂外还有高分散无机粉末等无机物超细粉末。
5.如何选择乳化剂?①根据HLB值选择,一般MMA:HCB=12.1~13.7,EMA:HCB=11.8~12.4;②根据产品粒径选择:阴离子乳化剂胶束直径小,产物粒径小,非离子相反;③聚合反应介质特性进行选择:中性或偏碱性选阴离子或非离子,两性选阳离子;④CMC选择:同样乳化效果,CMC下降,用量下降;⑤根据反应温度选择:选择合适的昙点或浊点乳化剂。
⑥成本与来源。
6、为什么现代工业上SBR采用低温乳液聚合工艺生产为主?因为低温SBR支化程度低,交联物含量少,分子量分布窄,硫化均匀,不易硫化的低分子物含量少,产物支联密度高,冷法工艺生产SBR物理机械兴宁明显提高7、SBR低温乳液聚合生产工艺中控制B与St配比和f各为多少?为什么?St:B=28:72-30:70,f<=60%因为研究性能可知:SBR中St含量为23.5%时聚合物具有最佳性能,而St与B质量比为29:72-30:70时可使单体中St占混合单体28%-30%,而在f<=60%时,St在聚合物中含量受转化率影响很小,SBR中St基本稳定在23%左右.8.微悬浮聚合在反应机理上与乳液,悬浮聚合的异同微悬浮聚合使用了复合分散剂,使体系以乳状液进行的聚合反应,外观上与乳液聚合相似,产物粒径也相似,但机理上,微悬浮聚合与悬浮聚合相同,类似于本体聚合,引发,增长,终止发生在液滴中,液滴成核,而乳液聚合在水相中引发,胶束胶粒中增长,终止,一般微悬浮聚合使用了乳化剂作为助剂或分散剂第七章1.简述离子与配位聚合工艺特点?聚合反应都属于键式反应,具有连锁反应特点,阴离子还因活性中心不易自行终止,被成为活性聚合,合成嵌段共聚物.通过配位聚合可以生产立体规整度高的聚合物,聚合体系对水,氧极其敏感,一般要求水含量达到10的-6次方数量级2离子与配位聚合生产工艺中,催化剂对聚合物生产十分重要,它们主要有哪些种类?离子聚合而言,阳离子催化剂:质子酸,Lewis酸,其他能生成阳离子的化合物,高能射线等;阴离子催化剂主要有以下几种:碱金属及其烷基化合物,碱土金属烷基化合物,碱金属-OH化物,钠化合物,碱金属烷氧基化合物,弱碱性化合物,常用为:Na,K,KOH,RLi,萘钠等.配位聚合催化剂:Z-N引发体系,烯丙基金属化合物,茂金属引发体系,碱金属有机化合物3.顺丁橡胶生产中的粘度问题比较突出,如何控制?通过跃升反应,解决体系粘度问题,即第一步,合成较低分子量的聚合物,体系粘度不大,第二步,在聚合工序未终止前加入跃迁剂,,使聚丁二烯分子量和粘度急剧升高,通过外加终止剂终止反应,,即获得高分子量产物,又避免了反应釜长期高粘度运行带来的技术问题.4.何谓跃升反应,试举例说明.先在聚合反应中直取低分子良聚合物,以利于反应进行,反应后期,添加跃升剂,使得聚合物的分子量在短期内成倍提高,这种反应称为跃升反应.常用跃升剂为催化剂,扩联剂混合物,如:有机铝的卤化物与有机卤化物,采用Al(C2H5)2Cl/H2O/Co三元络合物引发剂,引发B聚合,低分子量时加入四氯亚甲基甲烷,使PB低分子量聚合物在短期内结合成高分子量PB,体系粘度迅速增加.5,顺丁橡胶分子结构中有几重异构体?写出其结构式6.简述我国普遍应用的集中聚丙烯主要生产工艺,并作简要比较间歇式液相本体法,液相气相组合式连续本体法,淤浆法(又称溶液聚合法)三种主要方法.前一种为自行开发,后两种为引进技术与装置.淤浆发法引进时间早,所采用催化剂效率低,生产工艺落后,须经过催化剂分解,脱活,脱灰以及分离无规PP等工序,其他两种工艺生产采用二,三代高效催化剂,部分革除了或全部革除了脱灰与脱无规物两工序.。