铁粉矿复合造块新工艺
铁矿粉造块理论及工艺
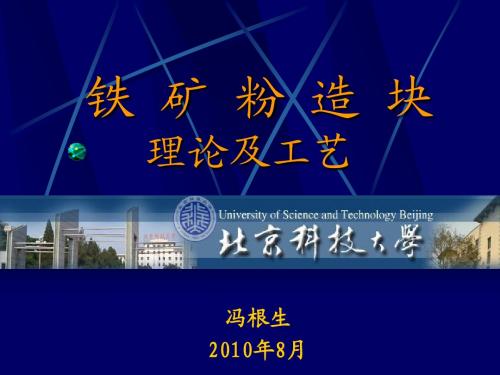
铁矿粉造块理论及工艺冯根生高炉炼铁炼铁的任务使矿石中金属铁氧化物中的铁元素和氧元素分离——还原过程;实现矿石中已还原金属与脉石的机械分离——熔化和造渣过程得到温度和化学成分合格的液态铁水炼铁系统—消耗及能耗炼铁系统:物料处理量最大、能耗最高、成本和效益压力最大的工序环节。
铁前系统物料处理量占钢铁企业65-70%。
吨铁消耗1.6-1.8吨矿石,500-550Kg燃料,产生1.5tCO2。
约280-400Kg/t炉渣。
炼铁系统—消耗及能耗铁前能耗占钢铁工业总能耗的70%左右,烧结及炼铁工序能源消耗总量占钢铁冶金过程的60%以上,占全国能源消耗总量的10%。
炼铁系统承担钢铁企业的节能、减排、增效的重任。
高炉炼铁面临的问题矿石资源和能源短缺的制约—关键问题节能、减排的压力市场环境(近几年经济危机)炼铁系统—高产、低耗、高效合理、高效(高效率、高效益)利用国内外资源,改善和稳定入炉原、燃料的质量;要优化高炉操作。
炼铁系统—高产、低耗、高效改善入炉含铁原料的质量不仅仅是提高烧结矿、球团矿的强度,更重要的是改善烧结矿和球团矿的还原性,发展间接还原,提高煤气的利用率,达到降低高炉燃料消耗;改善烧结矿和球团矿的高温冶金性能性能,进一步提高软化和熔融温度,降低软熔带的位臵,使得间接还原时间延长,从而提高煤气的利用率,达到进一步降低燃耗的作用。
炼铁系统—高产、低耗、高效布料技术(上部调剂):无钟炉顶的高炉上普遍采用大料批、重分装布料模式。
大喷煤配合使用中心加焦。
目的是使炉顶煤气流分布合理。
下部调节技术(下部调剂):根据操作条件选用不同风速、鼓风动能和合适的风口燃烧带理论燃烧温度控制炉缸燃烧带的位臵和现状及温度,满足高炉煤气合理初始分布和炉缸具有充沛的高温热量的要求。
高炉炼铁原料高炉炼铁用原料及要求主要原料包括:铁矿石烧结矿、球团矿、块矿);燃料(焦炭、粉煤)熔剂(石灰石、白云石等、萤石)高炉炼铁高炉炼铁用原料及要求—铁矿石:含铁品位高;强度好、粒度均匀、合适;理化性能指标稳定。
炼铁工艺04铁矿粉造块

第四讲 铁矿粉造块一、铁矿粉烧结生产1.烧结生产的意义烧结矿的生产是充分利用自然资源,扩大铁矿石来源。
贫矿必须经过选矿和造块才能使用;富矿加工过程中产生的富矿粉也需造块才能使用。
烧结过程中可以加入高炉炉尘、转炉炉尘、硫酸渣等其它钢铁及化工工业的若干废料,使这些废料得到有效利用,既降低成本又变废为宝,化害为利;经过烧结制成的烧结矿(与天然矿相比),粒度合适,还原性和软化性好,成分稳定,造渣性好,保证了高炉冶炼稳定顺行;烧结过程能去除有害元素。
尤其去硫率高达80%-90%。
此外还能去除部分砷、氟等有害元素。
2.烧结生产流程将经过准备处理(破碎、筛分、混匀)的烧结原料(包括燃料、熔剂、铁矿粉等)按一定比例配比,再经过加水混合造小球,所得混合料由布料器铺到烧结机台车上。
铺料厚一般为500毫米。
为了保护台车篦条,在铺入混合料之前,需要在台车上先垫一层约30毫米厚的粒度为10-20毫米的成品烧结矿作为铺底料。
烧结料层经点火器点火,然后台车在向前移动时依靠抽风机从上向下抽过空气,燃烧其料层中的燃料。
燃烧产生的高温,使矿粉局部熔化或软化,生成一定数量的液相。
液相是烧结矿固结成形的基础。
之后,随着温度降低,液相冷凝,矿物逐渐凝结成块,即为烧结矿。
烧结矿从烧结机尾台车上自动卸下,经过齿式单辊破碎机破碎、冷却机冷却,再进行二次破碎筛分,得到成品烧结矿。
烧结生产工艺流程(以宝钢烧结为例)3.烧结原料的准备烧结生产历来是以原料为基础的。
要保证烧结矿优质高产必须从加强原料的管理开始;在加强原料存放管理的同时,要狠抓原料的中和混匀,使配料用的各种原料,特别是矿粉化学成分的波动尽量缩小。
原料的中和可在原料场和原料仓库进行;在仓库中和时,通常是借助于移动漏矿皮带和桥式起重机抓斗,将来料在指定地段逐层铺放,堆到一定高度后,再用抓斗自上而下垂直取料来完成。
中和效果将随着中和次数的增多而改善;配料时,首先根据原料成分和高炉冶炼对烧结矿化学成分的要求,进行配料计算,以保证烧结矿的含铁量、碱度、FeO含量和含硫量等主要指标控制在规定范围内,然后选择适当的配料方法和设备,以保证配料的准确性。
铁矿粉造块
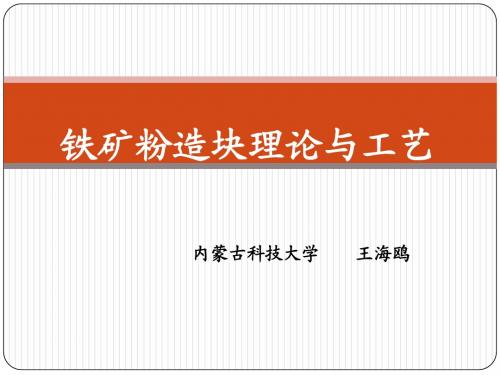
式中:Q——烧结机台时产量,t/h; F—烧结机有效抽风面积,m2 。
17
②烧结机生产能力: 用台时产量表示,即每台烧结机单位时间内生产的烧结 矿数量q(t/h): q=60KγCBL=60KγBHV 式中:Κ—烧结矿产出系数(50%~70%),Κ=K1K2K3;
K1 ——混合料的干料率,K1 =(单位体积中干混合料质量/单位体 积中湿混合料质量)×100%; K2——干混合料的烧成率, K2 =(烧成烧结矿的质量/进行烧结的干 混合料的质量)×100%; K3——烧结矿的成品率,K3=[成品矿/(成品矿十返矿)]×100%: γ——烧结矿体积密度(堆密度),取值范围为1.5~1.9 t/m3; C——垂直烧结速度,m/min; B——烧结机宽度,m; L——烧结机长度,m; H——烧结料层高度,m; V——烧结台车移动速度,m/min。
铁矿粉造块的目的与意义
1)贫矿利用:贫矿多→选矿(单体分离)→精矿粉→造块
2)将粉状料制成具有高温强度的块状料来适应高炉冶炼、直接还原 等在流体力学方面的要求。(高炉要求入炉矿石粒度大于5mm)
2)通过造块改善铁矿石的冶金性能,使高炉冶炼指标得到改善。
人造富矿的冶金性能优于天然富矿
Ⅰ、还原性好,Ⅱ、强度↑,Ⅲ、软化性↑ 3)通过造块去除某些有害杂质(如: S、As、K、Na、Zn等),回 收有益元素,消化冶金企业产生的大量粉尘和烟尘,达到综合利 用资源和保护环境的目的。
一、矿物
矿物:地壳中天然的物理化学作用和生物作用所产生的天
然元素或天然化合物,具有均一内部结晶结构、化学组成 以及一定物理、化学性质的天然化合物或自然元素称为矿 物。
矿石:是在现有的技术经济条件下能以工业规模从中提取
金属、金属化合物或有用矿物的物质总称。
铁矿粉造块PPT课件

铁矿粉造块的质量检测方法
化学分析
对铁矿粉造块进行化学分析,检测其化学成分是 否符合标准。
物理性能测试
对铁矿粉造块进行物理性能测试,如硬度、耐磨 性、耐腐蚀性等。
粒度分布测定
使用筛分法、沉降法等方法测定铁矿粉造块的粒 度分布。
质量控制的关键环节与措施
原料控制
确保原料的品质稳定,对进厂 的铁矿粉进行质量检查和控制
形状和性能的块状物料。
冷却与处理
将块状物料进行冷却、破碎、 筛分等处理,得到最终产品。
02
铁矿粉的性质与特点
铁矿粉的化学性质
01
主要成分
铁矿粉主要由铁的氧化物(如磁铁矿、赤铁矿等)组成,含有不同比例
的硅、铝、钙等杂质元素。
02 03
化学稳定性
铁矿粉在常温下较为稳定,不易与空气中的氧气发生反应。但在高温下, 铁矿粉中的铁氧化物会与碳、一氧化碳等还原剂发生还原反应,生成铁 和二氧化碳。
铁矿粉的密度一般在4.8~5.3g/cm³ 之间,与矿物成分和粒度有关。
铁矿粉的分类与用途
分类
根据矿物成分和化学成分的不同 ,铁矿粉可分为多种类型,如磁 铁矿粉、赤铁矿粉、褐铁矿粉等 。
用途
铁矿粉主要用于钢铁冶炼行业, 作为原料生产生铁、钢、钢材等 。此外,在建筑、化工、陶瓷等 领域也有一定的应用。
03
铁矿粉造块的原料与添加 剂
铁矿粉造块的原料
铁矿粉
作为主要的原料,铁矿粉 的品位、粒度、含水量等 指标对造块质量有重要影 响。
黏土或膨润土
作为主要的结合剂,黏土 或膨润土的成分、粒度、 活性等特性对造块过程和 块矿强度有关键作用。
燃料
如煤粉、焦粉等,用于提 供造块所需的热量。
铁矿粉造块PPT课件

第17页/共50页
2.2.2 烧结矿种类
2.2.2 烧结矿种类 • 非熔剂性烧结矿(酸性烧结矿、低碱度烧结矿):烧结配料中不加熔剂或只加少
量熔剂,烧结矿的碱度R<0.5。 • 自熔性烧结矿:烧结混合料中添加较多数量的熔剂,使烧结矿碱度控制在
R=1.0~1.3。 • 高碱度烧结矿:烧结混合料中加入过量熔剂,使烧结矿碱度远高于正常高炉渣碱
褐铁矿因含结晶水和气孔多,用烧 结球团造块时收缩性很大,使产品质量 降低,只有用延长高温处理时间,产品 强度可相应提高,但导致燃料消耗增大, 加工成本提高。
12
第12页/共50页
2.1 铁矿石的种类
(4)菱铁矿
• 菱铁矿为碳酸盐铁矿石,化学式为FeCO3,理论含铁量48.3%,受热分解析出 CO2,自然界中有工业开采价值的菱铁矿很少。
8
第8页/共50页
2.1 铁矿石的种类
• 磁铁矿比较致密,外观和条痕(粉末的颜色)均为铁黑色。
磁铁矿可烧性良好,因其在高温处理时氧化放热,且FeO 易与脉石成分形成低熔点化合物,故造块节能和结块强度好。
9
第9页/共50页
2.1 铁矿石的种类
(2)赤铁矿 • 又称“红矿”,主要矿物为Fe2O3,理论含铁量70%。 • 这种矿石在自然界中常形成巨大的矿床,其贮藏量和开采量都占首位,是一种比
11
第11页/共50页
2.1 铁矿石的种类
(3)褐铁矿
• 褐铁矿是含 结 晶水的氧化 铁 矿 , 其化学式 为n F e2O3·mH2O , 但绝大部分 含铁矿物 是以2 Fe2O3·3 H2O 形 式 存在 。
• 褐铁矿理论含铁量随矿物中结晶水含量的不同变化在55~66%。褐铁矿呈浅褐色, 也有呈深褐色或黑色,条痕为褐色。
铁矿粉烧结生产工艺流程

铁矿粉烧结生产工艺流程简介铁矿烧结是一种重要的冶金工艺,用于将铁矿石转化为高品质的铁矿烧结块,用于炼铁。
烧结精矿是由各类铁矿石和添加剂经过一系列工艺处理得到的高温烧结产物。
在铁矿粉烧结生产工艺流程中,主要包括原料准备、烧结机烧结、冷却与筛分等步骤。
本文将详细介绍铁矿粉烧结的生产工艺流程。
1. 原料准备在铁矿烧结生产过程中,主要的原料包括铁矿粉和添加剂。
铁矿粉一般由铁矿石经过破碎、磨矿等工艺得到,其粒径一般为0-10mm。
添加剂通常包括石灰石、焦炭等,用于调节矿石的成分和熔剂的状态。
在原料准备阶段,首先需要对原料进行称量和混合。
在称量过程中,要保证原料的比例准确,以确保最终产品的质量。
混合过程中,原料需要均匀混合,以提高烧结过程中的均匀性。
2. 烧结机烧结烧结机是铁矿烧结的核心设备。
铁矿烧结机分为循环烧结机和带式烧结机两种形式,具体工艺流程略有不同。
以下是循环烧结机的烧结工艺流程:2.1 前处理铁矿粉和添加剂混合后,需要进行一系列的前处理步骤,包括湿法混合、球团化和回转烘干三个过程。
在湿法混合过程中,将混合好的原料与水进行混合,形成一定湿度的矿浆。
然后将矿浆通过球团化机进行颗粒球团化处理。
球团化是为了提高铁矿砂的堆积密度和块度,便于烧结过程中气体的传递和固相的碰撞。
球团化后的颗粒通过回转烘干机进行烘干处理。
通过烘干,将矿浆中的水分蒸发掉,使颗粒达到适合烧结的干燥状态。
2.2 点火与预热在烧结机的烧结过程中,需要先进行点火与预热步骤。
点火一般采用煤粉喷燃方式,通过煤粉与空气的混合,形成可燃气体,然后点火并燃烧形成火焰。
预热过程主要是将烧结机内部的温度逐渐升高,为后续的烧结提供条件。
2.3 烧结烧结是将颗粒矿料在高温下进行热熔和结合的过程。
在烧结机中,矿石颗粒在高温气流的作用下逐渐升温,然后进入烧结带,矿石中的焦碳燃烧产生热量,矿石颗粒逐渐烧结成固体烧结块。
3. 烧结产物处理3.1 冷却经过烧结后的铁矿块温度较高,需要进行冷却处理,以降低温度。
多种难处理铁矿均热高料层烧结、球团制备关键技术和复合造块新工艺

多种难处理铁矿均热高料层烧结、球团制备关键技术和复合造块新工艺铁矿,那可是工业的“粮食”!可要是碰到了难处理的铁矿,就像是遇上了调皮捣蛋的孩子,得费好大一番功夫才能“管教”好。
先说这均热高料层烧结,你就想想咱包饺子的时候,要把馅料均匀地包在皮里,还得保证每个饺子都有足够的馅,这难度可不低。
均热高料层烧结也是一样,要让铁矿料在高温下均匀受热,形成结实的“大饺子”——烧结矿。
这就需要精准控制温度、料层厚度和各种配料的比例。
温度低了,烧结矿不结实,一捏就碎;温度高了,又容易过烧,浪费能源不说,质量还不好。
料层薄了,产量上不去;料层厚了,又怕中间受热不均匀。
这配料就像是饺子馅里的调料,多一点少一点都会影响味道。
再说说球团制备,这就好比是做元宵。
把铁矿粉弄成一个个小球,还得保证它们结实、有强度。
这就得选好粘结剂,就像元宵得有好的糯米粉才能粘得牢。
而且在制备过程中,得让球团均匀地滚动,就像元宵在糯米粉里滚来滚去一样,这样才能保证每个地方都裹得均匀。
最后是复合造块新工艺,这简直就是一场“烹饪大秀”!把前面的烧结矿和球团放在一起,就像把不同的食材放在一个锅里煮,得让它们相互配合,发挥出最大的作用。
这可不容易,得考虑它们的比例、特性,就像炒菜要考虑火候和调料的搭配一样。
咱们国家是钢铁大国,对铁矿的需求那是巨大的。
要是不能把这些难处理的铁矿搞定,那可就像战士上战场没了武器,怎么能打胜仗呢?所以啊,研究这些关键技术和新工艺,那是势在必行!这不仅能提高铁矿的利用率,降低成本,还能让咱们的钢铁产业更加强大,在国际上更有竞争力。
你说,要是咱们不努力钻研这些技术,怎么能在钢铁行业里站稳脚跟呢?怎么能满足国家建设的需要呢?这可不是闹着玩的,得实实在在地干,才能有收获!总之,多种难处理铁矿均热高料层烧结、球团制备关键技术和复合造块新工艺是咱们钢铁行业发展的重要方向,得好好研究,好好应用,为国家的繁荣富强出一份力!。
铁矿粉造块PPT课件

a
10
高炉炼铁的原料
铁矿石 燃料
1800
熔剂 1600 1400 1200 1000 800 600 400 200 0
1吨生铁
a
铁矿石 焦碳 熔剂
11
烧结的主要原料:
1、选矿后得到的精矿粉、天然富矿粉和经破 碎产生的粉矿; 2、含二氧化碳、结晶水和水分较多的矿石; 3、难还原的矿石,经过烧结或者造球培烧, 变成还原性良好和稳定性高的炉料。
矿粉、瓦斯灰、轧钢皮、锻钢屑、均热炉渣、 硫酸渣等)以便回收利用。
随着钢铁工业的迅速发展,天然富矿愈 来愈满足不了生产的要求,迫使人们利用贫 矿。贫矿的开发,促进了选矿工业的发展。 但由于选矿产品—铁精矿粒度细, 不能直接 进入高炉冶炼,因此,烧结工艺就成了炼铁 生产不可缺少的一环。
a
9
烧结工艺简言之就是把粉状的原料和细小颗 粒的原料在不完全熔化的条件下,或者说不允 许整个原料都同时呈液相的条件下(物料处在熔 化温度下的时间很短)烧结在一起。
粉矿造块能充分利用资源:把大量的贫矿、多种 金属共生复合矿经选矿后得到的精矿粉和在开采、 破碎过程中产生的粉矿固结成块,即成为高炉的 “熟料”。
特别是加添了石灰石、白云石、消石灰等熔剂的 人造富矿,因高温固结时产生气孔,透气性和还 原性都较天然矿石好。因此,高炉使用熟料有利 于降低焦比,有利于高炉顺行。
a
18
液相是烧结矿固结成形的基础。之后,随 着温度降低,液相冷凝,矿物逐渐凝结成 块,即为烧结矿。烧结矿从烧结机台车上 自动卸下,经过齿式单辊破碎机破碎、冷 却机冷却,再进行二次破碎筛分,得到成 品烧结矿。
a
- 1、下载文档前请自行甄别文档内容的完整性,平台不提供额外的编辑、内容补充、找答案等附加服务。
- 2、"仅部分预览"的文档,不可在线预览部分如存在完整性等问题,可反馈申请退款(可完整预览的文档不适用该条件!)。
- 3、如文档侵犯您的权益,请联系客服反馈,我们会尽快为您处理(人工客服工作时间:9:00-18:30)。
2.2方法与流程
以涟钢2005年3月烧结生产用配矿方案 为基础,将含铁原料中总比例为35.5%的铁 精矿按生产配比单独配料(用等用量的国内 精矿替代高品位富粉、中铁中硅粉以及利废 物等).在固盘造球机上制成直径为8—16 mm球团,将粉矿等含铁原料(配比64.5%)与 返矿、全部或绝大部分焦粉与熔剂一起配 料,并按传统丁艺进行~混、二混准备,将 造好的球团与二混后的原料混合后进行布 料、点火、烧结。 新T艺实验室试验流程如图l所示。烧
487
h).转鼓指数相应nI
60
40%提高到
64 00%。
表1复合造块实验室探索试验结果
说明:害妻答缫,j羞瑟嚣弩譬臻黼嘉嚣挚军龋猕溢赫尊嚣灰所。㈣舭删,
分配。
试验结果表明,当料层高度保持不变 时,采用复合造块j。艺需婴降低烧结负爪= 保持精矿中生石肛的配比(I o%)和碱 度(0
56—0
研究表明,在其它条件小变的情况下,
炉哇产 3.1显微结构分析・
总体上说,对于复合烧结块而言,无论 是矿物组成,还是显微结构都比较理想,尤 其是球团与球团之问,铁酸钙的形成、发育
完善,是一种以铁酸盐作为主要胶结相的高
质量炼铁炉料。
在复合人造块中大约有40%一50%的球
团,球团内部以结晶良好、晶形粗大互连的 Fe,O.为主,同时也有较多的橄榄石(主要是 钙铁橄榄石)粘结相生成。 在小球的中层,可清楚地看到由Fe,O。逐 渐氧化成Fe,O,的过渡带,此问Fe:0,与 Fe,O.交织混杂;小球的核心是橄榄石与 Fe,O。紧密胶结的区域;Fe,O,结晶良好,晶 形粗大互连,结构力好。橄榄石大部分为钙 铁橄榄石,但也可见少量的2FeO・SiO:生 成。
m2烧结机
为期1个月以上的1:业试验。 1)粉矿:由火车运到二烧熔剂仓,经 人l:卸料后,送至二烧配料仓(对现有配料 仓进行重新调整,一部分仓配粉矿,一部分 仓配精粉,熔剂只用生石灰一种)。 2)精矿:利用精粉料场精粉,经球团 精粉运输路线至二烧配料仓。从配料室开 始,再增加一套皮带系统,将精粉运至二烧 造球室造球。粉矿制粒与精矿造球后,通过 皮带系统运至二混混匀,进入烧结、冷却环 节。 3)成品矿:经小球烧结成品输送系统 送至低料仓,供4’高炉做:I二业扩大试验。
:l:程的投产,烧结矿供应将得到满足,现有
2台40 m2烧结机将因烧结矿强度差、环保条 件差而退出,便可以选择一台40 m2烧结机作
烧结矿产量无法满足高炉生产,2台40 m2烧
结机将继续服役,复合造块工业试验因此搁 浅。 原设想理由一:炉料供应量的变化。酸
一55—
性炉料不足。130
m2、180 m2、280
6
结论
铁粉矿复合造块新工艺是为适应我圈钢 (下转第65页)
9
结论
本文研究了在重钢原料条件下,生产熔
强度可达l
800
N,个以上。
5)熔剂性球团矿的还原率分别为
83.94%和88.34%,比基准样分别高11和 16.8个百分点,还原性好,消除了酸性球团矿 还原滞后现象。 6)熔剂性球团矿的低温还原粉化性能 和熔滴性能优良。 7)熔剂性球团矿的碱度为0.8一1.0时,
表2复合人造块冶金性能测定结果
为铁矿石复合造块工业试验及工业生产流 4
采用复合造块工艺工业试验
原计划2006年1月,随着涟钢280 m2烧结
程,但由于6座高炉产量提高,2006年炼铁 产量计划为420万t(2005年为375万t),130 m2烧结机、180 m2烧结机和280 m2烧结机3台
4.1场地选择
一56一
l 5%=7550万)-Ja
2)成品率提高,可降低烧结焦粉消耗 降低成本: 560元/t
X
530万t/a×57kg/t/1000×
7.1%/68.5%=l 754万元/a
3)高炉炉料结构优化间接经济效益。 采用熟料比高。物理性能、高温性能相对较 好的炉料结构有利于高炉的顺行和稳定,其 间接经济效益巨大;同时,利用淘汰的烧结 设备生产复合炉料,可节省投资成本。
术特点与创新点
铁工业的快速发展,在深入研究含铁原料造 块特性基础上开发的集现行烧结法与球团法 优点于一体的新型铁矿造块工艺。它将细粒 铁精矿单独分出制备成球团,再与粗粒的铁 矿粉及其他原料混合后铺到烧结机上进行焙 烧,制成南酸性球团矿嵌入高碱度烧结矿而 组成的复合炼铁炉料。 与传统的烧结、球团造块T艺相比,铁 粉矿复合造块新。I二艺具有以下一些主要优 点: 1)有利于充分、合理利用现有含铁原 料。将原来烧结用的精矿作为酸性球团生产 原料,而将粉矿作为碱性烧结矿基本原料, 通过复合造块新丁艺在一台烧结机上同时制 备出由酸性球团矿和高碱度烧结矿组成的复 合人造块矿,使不同类铁矿原料得到更加合 理的利用。 2)克服细粒精矿烧结过程中料层透气 性差、难以烧结的缺点。复合造块新T艺 中,将细粒铁精矿配入适量粘结剂单独造 球,制备成生球后,再与其它由铁粉矿、熔 剂等构成混合料充分混合,布料、点火、烧 结,由生球和制粒粉料组成的烧结原料可大 大改善烧结料层的透气性,显著提高垂直烧 结速度和利用系数。新T艺克服了传统烧结 IT艺中精矿制粒效果差,导致烧结料层透气 性差的缺点。实验室探索试验研究表明,新
剂性球团矿的可行性。研究表明: 1)重钢条件下生产熔剂性球团矿,熔 剂可用消石灰,氧化镁用菱镁石,熔剂性球 团矿的碱度可在0.8~1.0之间选择。
2)碱度为1.嘴剂性球团矿的品位可达
62.1%.扣有效CaO品位比基准样高1.22个百 分点,即高2%。由于不配膨润土或少配膨 润土,SiO,要比基准样低1.26个百分点,即 下降21.4%。 3)熔剂性球团矿的焙烧温度为1
1 200—
球团矿的硫含量与基准样处于同一水平,并
未因碱度提高而提高。 8)实验室研究证明,M型复合粘结剂具 有生球质量好、球团矿强度高、品位高等优 点,但用于丁业生产尚需进一步研究。
250℃,焙烧时间为20.25
rain。
4)在上述焙烧条件下,球团矿的平均 (上接第5l页) 可明显改善铁精矿的成球性能,获得较高的 生球强度。 参考文献
l无暇.钢铁业:调整也别搞重复【N】.中国经济导 报,2006—2—8(133 1) 2朱德庆,l尊菊英.铁矿氧化球团工艺理论与没备[MI. 长沙:中南大学出版社,2005
-52-
(800。900 mm)成为可能.有利于充分利
西、南非、印度矿,国内矿主要为国内磁铁 精粉,在配料中约占30%。国外矿和国内粉 矿主要为赤铁矿和褐铁矿粉矿。
用料层的自动蓄热作用,降低烧结阎体能
耗。另外,烧结生产率的大幅提高,也会相 应降低烧结生产能耗。 6)显著节约建厂投资。新丁艺可在烧 结机上同时制备高碱度烧结矿和酸性球团 矿,解决一些钢铁厂因资源、场地等问题无
直烧结速度、利用系数和转毁指数均逐渐增 大。
图2酸性球团“嵌入”高碱度烧结矿的复合人造块
一54-
圈3复合^造块中酸性球丽与商碱度烧结矿
3
Байду номын сангаас
烧结料复合造块质量满足高
球团与球团之问生成的铁酸盐液相量较 多,将矿粉及球团紧紧地胶结在一起,构成 较为坚实、牢I司的复合人造块骨架。 铁酸钙是强度高、还原性好的粘结相矿 物,其生成量和发育程度是改善低碱度条件 下复合人造块质量的关键。在复合人造块中 铁酸钙主要呈针状、条状、柱状、熔蚀状, 结晶较为完善,这也是复合人造块具有较好 强度和优良冶金性能的主要原因。
5经济效益计算
根据研究结果,复合造块其转鼓强度、 利用系数、成品率较之常规=I:艺分别提高了 3.6个百分点、o.487 t/(m2・h)、7.1个百分 点。 1)吨烧结矿加:I:费用按95元计算,利 用系数提高15%,烧结矿产量提高可降低成 本:
95)-c√t×530万t/a
X
4.2低碱度炉料工业试验方案
铁粉矿复合造块新工艺
中南大学 姜涛李光辉 涟钢技术中心刘素丽张克诚
1
铁粉矿复合造块新工艺的技
铁粉矿复合造块新工艺是为适应我国钢
工艺较之传统烧结工艺的利用系数提高 15%以上。 3)解决低碱度高炉炉料制备和高铁低 硅烧结矿强度差的难题。由于复合造块工艺 中,细粒铁精矿和粗粒铁矿粉按完全不同的 机理成矿,可在不降低产品产质量的条件下 显著降低原料总碱度,在烧结机上实现低碱 度炉料的生产。 高铁低硅烧结过程中,由于二氧化硅含 量的降低,导致烧结过程液相生成量低,烧 结矿强度差、粒度细。因此,对于高铁低硅 烧结来说,必须提高碱度,大力发展以铁酸 钙为主的粘结相,以改善烧结矿质量。但
低碱度炉料:通过调整精粉配比、生石 灰用量来调整碱度。’I:业试验可分小试和扩 试两个阶段进行。 4.2.1小试阶段 利用2×8 m2竖炉年检间隙,进行一周左 右小试。 1)粉矿:在中和场配料室只配粉矿, 经直拨系统、中和料场置系统直接进入二烧 配料室中和粉仓,再经配料、一混、二混。 2)精矿:利用球团配料室配料,经烘 干、造球后,用汽车转运至二烧造球问,再 由造球送至二混与中和粉混合。 3)成品矿:经小球烧结成品输送系 统,送至低料仓。 4)利用4。高炉,做人造复合块高炉炼冶 工业性试验。 4.2.2+1:业扩大试验 小试成功后,经公司决定,利用目前烧 结单车棚改造成简单的精粉接收系统,进行
3.2冶金性能
分别测定了碱度R=1.4、R=2.0条件下的
复合人造块的冶金性能,具体包括还原性
能、低温还原粉化性能和软熔性能,有关结
果如表2所示。研究结果表明。复合人造块 还原性能、低温还原粉化性能优良 (RI>93%,RDI。,在80%左右),软化、熔 融开始温度高,熔滴性能好。显然,复合人 造块的各项冶金性能指标达到了大型高炉冶 炼的要求。
上进行,料层高度为600
mm。
图1
复合造块新工艺实验室试验流程
一53—
2
3试验结果与分析 复合造块的实验室探索性试验研究结果