孔无铜缺陷判读及预防
PCB孔铜断裂分析报告

孔铜断裂通常表现为电气连接失 效,可能引发电路故障或产品性 能下降。
断裂原因与影响
原因
孔铜断裂可能由多种因素引起,包括 制造过程中的缺陷、材料问题、环境 因素等。
影响
孔铜断裂可能导致电路板功能失效, 增加产品故障率,降低产品质量和可 靠性。
断裂分析的重要性
确定断裂原因
优化制ቤተ መጻሕፍቲ ባይዱ工艺
通过对孔铜断裂进行分析,可以确定 导致断裂的具体原因,为后续的改进 和预防措施提供依据。
对PCB的布局和布线进 行优化,尽量减少应力 集中区域,特别是通孔 连接处的设计。可以考 虑增加过孔的直径或优 化过孔的排布来降低应 力水平。
加强质量检测与 可靠性评估
在PCB生产和组装过程 中,增加对通孔质量的 检测环节,确保无缺陷 产品流入市场。同时, 对已生产和在役的PCB 进行可靠性评估,特别 是针对可能承受较大应 力的区域进行重点检查 。
工艺优化与改进
总结词
优化和改进制造工艺可以有效降低PCB孔铜 断裂的风险。
详细描述
通过改进钻孔、电镀和焊接等工艺过程,可 以增强PCB的机械性能和耐久性。例如,优 化钻孔参数可以减少孔内缺陷和应力,提高 孔壁的附着力和强度。
环境因素控制
要点一
总结词
环境因素对PCB孔铜断裂具有重要影响,需严格控制。
切片分析
深入观察
通过将PCB切片,可以更深入地观察孔铜内部的断裂情况。 切片分析可以揭示断裂的起始点、扩展方向以及断裂面的微 观结构。
扫描电镜分析
高倍观察
扫描电镜可以提供高倍率的观察,帮助分析孔铜断裂的具 体细节。通过扫描电镜,可以观察到断裂面的微观形貌、 晶体结构和元素分布,为后续分析提供依据。
铸件常见缺陷的产生原因及防止方法

铸件常见缺陷的产生原因及防止方法一、气孔(气泡、呛孔、气窝)特征:气孔是存在于铸件表面或内部的孔洞,呈圆形、椭圆形或不规则形,有时多个气孔组成一个气团,皮下一般呈梨形。
呛孔形状不规则,且表面粗糙,气窝是铸件表面凹进去一块,表面较平滑。
明孔外观检查就能发现,皮下气孔经机械加工后才能发现。
形成原因:1、模具预热温度太低,液体金属经过浇注系统时冷却太快。
2、模具排气设计不良,气体不能通畅排出。
3、涂料不好,本身排气性不佳,甚至本身挥发或分解出气体。
4、模具型腔表面有孔洞、凹坑,液体金属注入后孔洞、凹坑处气体迅速膨胀压缩液体金属,形成呛孔。
5、模具型腔表面锈蚀,且未清理干净。
6、原材料(砂芯)存放不当,使用前未经预热。
7、脱氧剂不佳,或用量不够或操作不当等。
防止方法:1、模具要充分预热,涂料(石墨)的粒度不宜太细,透气性要好。
2、使用倾斜浇注方式浇注。
3、原材料应存放在通风干燥处,使用时要预热。
4、选择脱氧效果较好的脱氧剂(镁)。
5、浇注温度不宜过高。
二、缩孔(缩松)特征:缩孔是铸件表面或内部存在的一种表面粗糙的孔,轻微缩孔是许多分散的小缩孔,即缩松,缩孔或缩松处晶粒粗大。
常发生在铸件内浇道附近、冒口根部、厚大部位,壁的厚薄转接处及具有大平面的厚薄处。
形成原因:1、模具工作温度控制未达到定向凝固要求。
2、涂料选择不当,不同部位涂料层厚度控制不好。
3、铸件在模具中的位置设计不当。
4、浇冒口设计未能达到起充分补缩的作用。
5、浇注温度过低或过高。
防治方法:1、提高磨具温度。
2、调整涂料层厚度,涂料喷洒要均匀,涂料脱落而补涂时不可形成局部涂料堆积现象。
3、对模具进行局部加热或用绝热材料局部保温。
4、热节处镶铜块,对局部进行激冷。
5、模具上设计散热片,或通过水等加速局部地区冷却速度,或在模具外喷水,喷雾。
6、用可拆缷激冷块,轮流安放在型腔内,避免连续生产时激冷块本身冷却不充分。
7、模具冒口上设计加压装置。
8、浇注系统设计要准确,选择适宜的浇注温度。
铸造缺陷的特征、鉴别、成因及防治措施

铸造缺陷的特征、鉴别方法、成因及防治措施一、多肉类缺陷的防止措施总结1、飞翅缺陷的特征、鉴别方法、成因及防治措施(1)定义和特征产生在分型面、分芯面、芯头、活块及型与芯结合面等处,通常垂直于铸件表面的厚度不均匀的薄片状金属凸起物,又称为飞边或披缝。
(2)鉴别方法肉眼外观检查。
飞翅出现在型—型、型—芯、芯—芯结合面上,成连片状,系结合面间隙过大所致。
(3)形成原因①②③④⑤⑥⑦(4)防止方法①②③④⑤⑥⑦(5)补救措施2、毛刺缺陷的特征、鉴别方法、成因及防治措施(1)定义和特征(2)鉴别方法肉眼外观检查。
(3)形成原因①②③④⑤⑥⑦(4)防止方法①②③④⑤⑥⑦(5)补救措施3、冲砂缺陷的特征、鉴别方法、成因及防治措施(1)定义和特征(2)鉴别方法肉眼外观检查。
(3)形成原因①②③④⑤⑥⑦(4)防止方法①②③④⑤⑥⑦(5)补救措施4、胀砂缺陷的特征、鉴别方法、成因及防治措施(1)定义和特征(2)鉴别方法肉眼外观检查。
(3)形成原因①②③④⑤⑥⑦(4)防止方法①②③④⑤⑥⑦(5)补救措施5、抬型/抬箱缺陷的特征、鉴别方法、成因及防治措施(1)定义和特征(2)鉴别方法肉眼外观检查。
(3)形成原因(4)防止方法①②③④⑤(5)补救措施①②6、外渗物/外渗豆缺陷的特征、鉴别方法、成因及防治措施(1)定义和特征(2)鉴别方法肉眼外观检查。
(3)形成原因①②③(4)防止方法①②③④⑤⑥(5)补救措施7、掉砂缺陷的特征、鉴别方法、成因及防治措施(1)定义和特征(2)鉴别方法肉眼外观检查。
(3)形成原因①②③④⑤⑥⑦(4)防止方法①②③④⑤⑥⑦(5)补救措施二、孔洞类1、反应气孔缺陷的特征、鉴别方法、成因及防治措施(1)定义和特征(2)鉴别方法(3)形成原因①②③(4)防止方法①②③(5)补救措施2、卷入气孔缺陷的特征、鉴别方法、成因及防治措施(1)定义和特征(2)鉴别方法(3)形成原因①②③(4)防止方法①②③④(5)补救措施①②③3、侵入气孔缺陷的特征、鉴别方法、成因及防治措施(1)定义和特征(2)鉴别方法(3)形成原因①②③④(4)防止方法①②③④(5)补救措施①②③4、析出气孔缺陷的特征、鉴别方法、成因及防治措施(1)定义和特征(2)鉴别方法(3)形成原因①②③(4)防止方法(5)补救措施①②③5、疏松(显微缩松)缺陷的特征、鉴别方法、成因及防治措施(1)定义和特征(2)鉴别方法(3)形成原因①②③④⑤⑥⑦⑧⑨⑩(4)防止方法①②③④⑤⑥⑦⑧⑨⑩(5)补救措施①②③④6、缩孔缺陷的特征、鉴别方法、成因及防治措施(1)定义和特征(2)鉴别方法(3)形成原因①②③④⑤⑥⑦(4)防止方法①②③④⑤⑥⑦⑧(5)补救措施7、缩松缺陷的特征、鉴别方法、成因及防治措施(1)定义和特征(2)鉴别方法(3)形成原因①②③④⑤⑥⑦⑧⑨⑩(4)防止方法①②③④⑤⑥⑦⑧⑨⑩(5)补救措施①②③④三、裂纹、冷隔类1、白点(发裂)缺陷的特征、鉴别方法、成因及防治措施(1)定义和特征(2)鉴别方法(3)形成原因①②(4)防止方法①②③④(5)补救措施2、冷隔缺陷的特征、鉴别方法、成因及防治措施(1)定义和特征(2)鉴别方法肉眼外观检查。
探讨铸造铜合金气孔缺陷的生成机理及对策

探讨铸造铜合金气孔缺陷的生成机理及对策铸造铜合金气孔缺陷的生成机理及对策铸造是一种常用的金属加工方法,它通过将液态金属注入模具中,待金属冷却凝固后得到所需的形状。
然而,在铸造过程中,气孔缺陷往往是一个严重的问题,它会严重影响产品的质量和性能。
因此,深入探讨铸造铜合金气孔缺陷的生成机理,寻找相应的对策措施,对于提高铸造品质具有重要意义。
一、气孔缺陷的生成机理1.金属液体中的气体存在:金属液体在熔融状态下,会溶解一部分气体,如氧、氢、氮等。
当液体冷却凝固时,溶解在金属中的气体会析出形成气泡,从而导致气孔缺陷的生成。
2.气泡形成与壁流:在铸造过程中,金属液体流动速度较快,存在壁流现象。
当液体中气体被带入壁流区域时,由于流动速度减小,气体会析出形成气泡。
3.气泡的聚集与浮力:由于气泡比金属密度小,所以在凝固过程中,气泡会逐渐上浮并聚集在金属表面,形成大型气孔缺陷。
二、对策措施1.提高金属液体质量:采用优质铜合金原料,控制金属液体中杂质和气体的含量,能够降低气孔缺陷的生成。
2.控制冷速:通过调整冷却速度,可以减少气体在凝固过程中的析出,从而减少气孔缺陷的形成。
3.改善浇注系统:合理设计浇注系统,减少金属液体流动的速度和压力,能够减少壁流现象,降低气孔缺陷的发生。
4.气体除去:采用真空铸造或使用气体除去装置,能够有效地去除金属液体中的气体,从而减少气孔缺陷的生成。
5.合理的温度控制:在铸造过程中,合理控制金属液体的温度,能够减缓气泡形成的速度,有效降低气孔缺陷的发生。
总结起来,铸造铜合金气孔缺陷的生成机理是由金属液体中的气体存在、气泡形成与壁流以及气泡的聚集与浮力等因素共同作用导致的。
因此,为了减少气孔缺陷的发生,可以从提高金属液体质量、控制冷速、改善浇注系统、气体除去以及合理的温度控制等方面入手,采取相应的对策措施。
这些措施的实施可以有效地降低气孔缺陷的生成率,提高铸造品质,为相关行业的发展做出贡献。
通过对铸造铜合金气孔缺陷生成机理的探讨以及相应的对策措施的提出,我们可以更好地识别、预防和解决气孔缺陷的问题,提高铸造铜合金产品的质量和性能,满足市场的需求和要求。
常见铸造缺陷的产生原因及其预防措施
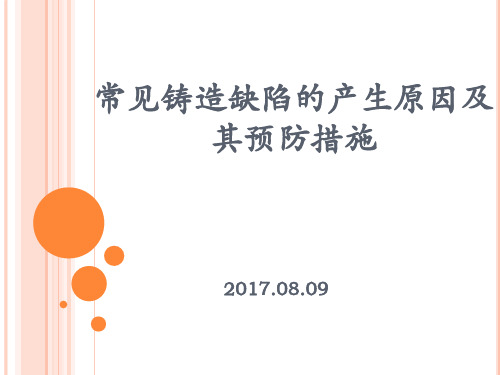
多肉产生的原因:
1、模具原因。 2、砂(芯)型起破。 3、砂(芯)型损坏 4、砂芯和砂型相接 表面不吻合
5、冷铁和模具不吻 合。
6、砂(芯)局部部 位未充满。
冷铁和模具不吻 合引起的铸件多
肉
多肉类缺陷的预防措施
(1) 提高铸型紧实度(下箱型砂的紧实度应高于 上箱的紧实度),避免局部过松;
(2)调整混砂工艺、控制水分,提高型砂强度; (3) 降低浇包的位置、降低浇注速度; (4) 铸型的分型面多压坭条或石棉绳; (5) 坭芯间的可见披缝尽量补死; (6) 需放置直接外冷铁时,外冷铁与铸件的接
根据GB/T 5611-1988《铸造术语》规定,将铸造缺陷 分为八大类。
① 多肉类缺陷 ② 孔洞类缺陷 ③ 裂纹、冷隔类缺陷 ④ 表面缺陷 ⑤ 残缺类缺陷 ⑥ 形状及重量差错类缺陷 ⑦ 夹杂类缺陷 ⑧ 性能、成分、组织不合格
分类(1)
大 类
序 号
缺陷名称
特征
1
飞翅(飞边、 产生在铸件分型面、坭芯间隙处、坭芯与
裂处金属表皮不氧化。
在铸件表面有未完全融合的缝隙或 洼坑,其交接边缘是光滑的。
热裂和冷裂(1) 热裂
图6-1 铸钢件的外热裂
冷裂
热裂和冷裂(2)
冷隔(1)
局 部 放 大
叶片机座 冷隔缺陷
冷隔(2)
典型的冷隔特 征
裂纹冷隔类缺陷的预防措施
(1) 严格按照化学成分的要求,控制钢水中的 S、 P含量;
触面一定要打磨平整; (7) 合箱后,注意保证上、下箱连接位置的紧固,
需放置压铁时上、下箱之间要用冷铁尖死。
分类(2-1)
大 类
序 号
缺陷名称
特征
孔 洞
铜铸造常见缺陷和原因

铜铸造常见缺陷和原因
铜铸造是一种广泛应用的金属加工工艺,但在生产过程中,难免会出现一些缺陷,如何避免和解决这些缺陷,是铜铸造的关键问题之一。
本文将介绍铜铸造常见的缺陷和原因,供读者参考。
1. 气孔:气孔是铜铸造中常见的缺陷之一,通常由于铜液中存
在气体或铜液冷却过程中产生气体导致。
解决方法包括提高铜液温度、加强铜液搅拌、采用真空铸造等方法。
2. 灰尘:铜液中的杂质和灰尘可能导致铸件表面产生黑斑和孔
洞等缺陷,解决方法包括提高铜液过滤、加强净化设备等方法。
3. 翘曲:铜铸造过程中,铜液冷却收缩可能导致铸件变形或翘曲,解决方法包括加强铜液温度控制、采用二次加热等方法。
4. 粘铸:铜液在铸模中流动不畅,可能导致铜液黏附在铸模上,从而产生粘铸现象,解决方法包括提高铜液流动性、加强铸模涂层等方法。
5. 疏松:铜铸造过程中,铸件中可能存在气体、夹杂物等杂质,从而导致铸件疏松、脆弱等缺陷,解决方法包括加强铜液搅拌、提高铜液温度、采用真空铸造等方法。
6. 热裂纹:铜液冷却收缩过程中,可能导致铸件出现热裂纹,
解决方法包括采用合适的结构设计、加强冷却设备等方法。
以上是铜铸造常见的缺陷和原因,希望对读者有所帮助。
在铜铸造过程中,应该严格控制加工参数和操作流程,从而保证铸件质量。
- 1 -。
金属化孔常见缺陷及预防

金属化孔常见缺陷及预防周仲承;王克军;符飞燕;余金;王龙彪【摘要】The plated through hole in the printed circuit boards has to endure more challenges and thermal shocks with the higher integration scale of PCB and the full implementation of “Lead-free” policy. So defects are more prone to occur. In this paper, the common defects are classified and the factors which cause the defects are analyzed. The improvement measures are given from the view of production process and the control of chemical solution.%随着印电路板集成化程度越来越高以及无铅化”全面实施金属化孔需要承受挑战和冲击也越来越多比过去更容易出现各种缺陷中对最常见缺陷进行分类和原因解析从生产工艺和药水控方面给出改善措施。
【期刊名称】《印制电路信息》【年(卷),期】2015(000)010【总页数】5页(P49-53)【关键词】印制电路板;孔金属化;常见缺陷;预防措施;改善【作者】周仲承;王克军;符飞燕;余金;王龙彪【作者单位】中南电子化学材料所,湖北武汉 430070;中南电子化学材料所,湖北武汉 430070;中南电子化学材料所,湖北武汉 430070;中南电子化学材料所,湖北武汉 430070;中南电子化学材料所,湖北武汉 430070【正文语种】中文【中图分类】TN41印制电路板(PCB)上的各种连通孔起着连接不同层间电路的作用,其金属化(Plated Through Hole,PTH)是PCB制造中极为重要的一道工序。
微孔无铜原因分析与改善

微孔无铜原因分析与改善周毅;崔青鹏;陈雯【摘要】文章主要分析了PCB制造过程中微孔出现孔无铜的各类原因以及改善预防措施,并且详细介绍了对于火山灰堵孔造成的微孔孔无铜的原因分析。
%Specially in Micro-hole,void in hole is a big trouble that bother PCB manufactures.With the development of Electric-production,hole in the PCB becomes smaller and smaller.So it is necessary to find the root cause and sum up the experience of the solution method in this field.By analyzing every possible cause in the PCB production,especially in front-process,this paper explained some key-points in process which are overlooked in manufacturing.【期刊名称】《印制电路信息》【年(卷),期】2012(000)009【总页数】4页(P33-36)【关键词】微孔;孔无铜;高纵横比产品【作者】周毅;崔青鹏;陈雯【作者单位】深圳崇达多层线路板有限公司,广东深圳518132;深圳崇达多层线路板有限公司,广东深圳518132;深圳崇达多层线路板有限公司,广东深圳518132【正文语种】中文【中图分类】TN411 前言随着电子行业的不断发展,印制线路板亦越来越精细,不仅表现在线宽/线距更细、更密集,层数更高,同时导通孔的孔径也越来越小,即厚径比越来越高,这不仅对钻孔工艺和设备提出了更高的要求,也对与导通相关的其他工艺如沉铜、线路、电镀等亦提出了更高的要求,由于孔径过小,很多钻孔后制程都可能对孔导通产生重要的影响。
- 1、下载文档前请自行甄别文档内容的完整性,平台不提供额外的编辑、内容补充、找答案等附加服务。
- 2、"仅部分预览"的文档,不可在线预览部分如存在完整性等问题,可反馈申请退款(可完整预览的文档不适用该条件!)。
- 3、如文档侵犯您的权益,请联系客服反馈,我们会尽快为您处理(人工客服工作时间:9:00-18:30)。
第一部分:孔无铜定义
孔无铜是指印制板金属化孔孔内开路; 在通断检测时失去电气连接性能;
金属化孔包括:通孔、盲孔和埋孔;
孔壁不导通也称“破孔”或“孔内开路”。
孔的作用及影响因素
作用:具有零件插焊和导电互连功能。 加工过程影响因素多,控制复杂:
钻孔质量:孔壁平滑度、粗糙度等 凹蚀效果:内层连接、树脂表观情况 沉铜效果:药水活性及背光级数 平板镀铜:过程控制及故障处理 图形电镀:微蚀控制及抗蚀层性能 后工序影响:微蚀控制及返工板处理等
缺陷描述16
盲孔连接不良导致开路:
失效分析
特点:盲孔层孔拐角处没有被平板层包住(表铜没 有平板层或很薄),受热后在孔铜连接处出现断开, 填孔树脂与盲孔面铜处出现明显空隙; 原因:减铜过度导致盲孔表铜没有平板层(或很 薄) ,受热后由于树脂膨胀导致开路; 措施:杜绝减铜过度,适当提高盲孔铜厚,采用其 他板料减少树脂热膨胀的影响等。
失效分析
特点:孔内无铜位置全部发生在树脂部位; 原因:除胶渣不够,树脂蜂窝状结构尚未形 成; 措施:检查凹蚀段条件,提高除胶渣能力 (如:提高浓度、温度或延长时间等)
缺陷描述7
电镀层包住平板层,切片从孔口向孔中央平板层逐渐消失:
失效分析
特点:图形层包住平板层,切片从孔口向孔中 央平板层逐渐变薄并最后消失; 原因:平板不良,平板电镀时电流密度过小、 电镀时间过短或设备故障(电接触不良)等; 措施:检查平板电镀条件,如:电流密度、时 间等。
问题界定一
从切片入手,按缺陷特征进行分类! 爬虫型:出现部位全在树脂上或全在玻璃纤维上, 前者是除钻污不够,后者则除油缸整孔能力差; 中间型:出现部位在孔壁中间,左右几乎对称; 孔角型:出现的部位在孔角,原因是余膜入孔; 孔口型:磨板过度或微蚀过度导致孔口无铜; 异孔型:孔壁粗糙度过大,孔内药水交换不畅。
现状描述2
孔内玻纤上断断续续、点状无铜!
失效分析
特点:图形层包住平板层,无铜处断断续续, 大小孔均有出现,特别在玻璃纤维上无铜的 机率更高,常发生在拖缸之后; 原因:沉铜不良(如:药水活性不足、背光 不足、温度太低等) 措施:检讨拖缸方法和程序、 提高药水活性。
缺陷描述3
孔壁夹带铜皮或杂物,塞孔导致的孔无铜:
失效分析
特点:盲孔处无铜,孔口位置无铜更严重 原因:干膜破孔,蚀刻药水进入孔内,直接 原因可能曝光不良、对偏、盲孔与下垫接触 不良; 措施:检讨干膜盖孔条件及对位情况。
缺陷描述19
特点:盲孔无铜,与内层铜分离或连接不好
失效分析
特点:盲孔无铜,与内 层铜分离或连接不好; 原因:激光窗偏,激光 孔蚀孔不良,造成激光 钻孔不良,沉铜时药水 交换不良。 措施:检查激光开窗情 况和钻孔能量等。
问题界定二
按形成原因进行分类: 活性不足 :溶液浓度低、温度低、负载低、pH值 低、药水老化等; 气泡阻塞:沉铜缸气泡和铅锡/锡缸气泡; 异物塞孔:杂物、铜皮、干膜碎、火山灰等; 除油整孔差 :玻璃纤维处难上铜 ; 除胶渣效果差:树脂上难上铜 ; 其他:抗蚀层或平板层太薄或返工等。
孔无铜缺陷判 读及预防
CCTC一厂 工艺部 苏培涛
ptsu@
课程目标
帮助学员对切片缺陷进行判读; 通过案例对原因进行分析并预防; 降低孔无铜比例,达到稳定品质的目的。
课程内容
第一部分:孔无铜定义 第二部分:原因分析 第三部分:缺陷现象及失效分析 第四部分:纠正行动及改善方案
缺陷描述17
热冲击或冷热循环后孔壁出现开路:
失效分析
特点:受热后孔壁镀铜层出现开路,没有受 热时则是完整镀层; 原因:镀层物理性能差、延展性差或孔壁铜 厚不足等; 措施:净化镀液改善结晶结构、提高镀层延 展性等,适当提高孔铜厚度,同时热冲击前 要求按规定进行烘板处理。
缺陷描述18
盲孔处无铜,孔口位置无铜更严重
缺陷描述12
孔口无铜,特别是大金属化孔孔无铜更明显。
失效分析
特点:孔口无铜,特别是大金属化孔孔无铜 更明显。 原因:磨板过度导致拐角处无铜。 措施:减少磨板压力,特别是不织布刷磨板 段的压力,检查不织布使用目数等!
缺陷描述13
孤立的地方孔内和孔口、焊盘均出现无铜:
失效分析
特点:孤立孔内、孔口和焊盘均出现无铜 原因:抗蚀不良孔无铜,主要是由于高电流密度区 镀层结晶粗糙,或镀锡后没有及时烘干等使抗蚀层 性能下降导致过蚀; 措施:改善镀层结晶结构,可通过添加光剂或延长 电镀时间、降低电流密度等,如镀锡后停留时间过 长要针对性进行改进。
失效分析
特点:平板层包住杂物塞孔导致孔无铜; 原因:钻房工艺条件差,在去毛刺高压水洗 中无法除去导致塞孔,也可能是铜粉堵塞或 自来水、药缸杂质等外来异物; 措施:改善钻孔条件、提高去毛刺高压水洗 压力、加强各药水缸过滤和净化等。
缺陷描述4
孔壁与内层线路连接不良(ICD)
失效分析
特点:凹蚀不良导致与内层连接出现开路; 原因:
缺陷描述21
盲孔孔内无铜 :
失效分析
特点:盲孔孔口处出现抗蚀不良孔无铜; 原因:在盲孔孔口处由于二次层压时B片流 动性差等原因,填胶不满导致碱蚀药水进入 造成孔内无铜;
措施:改用流动性较好B片,如高树脂含量 等。
第四部分:纠正行动及改善方案
采用D-M-A-I-C改进模式: 界定(Define):对切片缺陷进行认真界定 测量(Measure):通过通断、BB机和切片 分析(Analyze):根据具体流程进行分析 改进(Improve):针对存在问题进行改进 控制(Control):有效控制形成文件指导生产
措施:严格板件返工制度,杜绝干膜塞孔。
缺陷描述11
整孔无铜,而且大孔、小孔均无铜:
失效分析
特点:表面只有一层电镀层,孔内整孔无铜, 主要原因: 板件未沉铜就直接进行平板或图形电镀, 图形电镀时由于吊车故障等原因在微蚀缸停留时 间过长,平板层被全部蚀掉(从内层铜层形成负 凹蚀的情况进行确认)。 措施:对异常停机情况进行纠正,及时吊出微蚀缸 板件。
埋盲孔孔无铜;
其他类型孔无铜。
孔无铜因果图
化学沉铜类型介绍
沉薄铜:化学铜厚度10 ~ 20u" (0.25 ~ 0.5um) 中速铜:化学铜厚度40 ~ 60u " (1.0 ~ 1.5um)
厚化铜:化学铜厚度80 ~ 100u"(2.0 ~ 2.5um)
一厂使用ATO薄铜体系,铜层厚度约7-12 u" 注意:沉铜层不致密,很容易被空气氧化! 措施:沉铜后板件尽快进行平板电镀!
孔无铜的特殊性
印制板致命品质缺陷之一,需加强控制; 产生原因复杂,改善难度大;
严重影响板件性能和可靠性;
孔无铜缺陷及判读是湿法人员基本功;
提高孔铜保证性是PCB厂综合实力的体现。
第二部分:原因分析
孔内无铜从加工流程上分类:
沉铜不良(如:气泡、塞孔、背光不足等) 平板不良(如:整流机无电流、镀前停留时间长等) 图电不良(如:图电微蚀过度、塞孔、抗蚀差等) 后工序微蚀过度; 酸蚀板孔无铜;
缺陷描述14
无铜处出现在孔中央而且对称,特别是小孔情况更严重。
失效分析 Fra bibliotek特点:平板层没有包住图形层,主要为抗蚀层(铅 锡层、锡层或镍层)深镀能力不足。 原因:厚径比AR值大,孔内药液交换困难: 反冲涡流增强,以致靠压力(如:摇摆、震荡等) 驱动达到孔内流动的因素被削弱; 表面张力增大; 气泡难以逸出。 措施:提高抗蚀层深镀能力,加强摇摆或震荡等。
结束语
孔无铜原因复杂,杜绝极难,我们需要:
对切片认真判读,对缺陷进行严格的界定! 深入全面检讨板件生产流程和控制参数! 过去经验只是一种参考,不是万能! 只要小心求证,相信:方法总比问题多!
持续改善:减少报废、不断提升板件品质!
缺陷描述15
大孔、小孔均无铜或铜厚不足,板面绿油下镀铜层完整 但露铜区域铜层很薄:
失效分析
特点:大孔、小孔均无铜或铜厚不足,板面绿油下 镀铜层完整但露铜区域铜层较薄; 原因:后工序微蚀过度导致孔无铜,轻微时出现孔 铜不足,严重时无铜;可能是沉镍金、OSP、喷锡、 沉锡等前处理过度;
措施:检讨前处理微蚀条件(时间、温度、浓度等)
溶胀缸膨松不够:浓度低、温度低、处理时间短及药 水寿命已到; 咬蚀能力差:药水温度低、浓度低、锰酸钾含量高、 处理时间短或药水老化; 特殊板材:高Tg、含填料板件或其他特殊材质等。 其他:可能是钻孔发热过度或烘板参数不当造成;
措施:确认具体问题进行针对性改善!
缺陷描述5
孔内无铜位置出现基本对称,全部集中在小孔中:
背光:沉铜活性的体现者
背光不足处理程序 背光测试方法如下图:
沉铜背光级数判读
注意:树脂比玻璃纤维更容易沉上铜!
图电前后判读标准
第三部分:缺陷现象及失效分析
收集21种常见缺陷图片进行分析; 以图带文从切片缺陷进行界定; 通过案例分析找出“问题背后的问题”; 将被动的事后纠正变为事前控制!
失效分析
特点:孔口边缘断铜,断铜面较整齐;
原因:基本可断定为干膜入孔,干膜由于贴膜压 力过大或贴膜到显影存放时间较长,如:大节日 干膜房内没有清板或设备故障等。 措施:缩短贴膜至显影时间,
严格返工制度。
缺陷描述10