过程检验流程图
质检部工作流程

一.产品检验的分类 ❖1.进货检验. ❖2.过程检验. ❖3.成品检验.
❖ 二.进货检验流程图 ❖ 结构件检验流程
入库
采
供
部
下 发
结构件
报
检
单
更换或退货
在报检单上签字
合格
外观检查
核对规格型号及尺寸
填写质量检验返修通知单
不合格
❖ 电器件检验流程
入库
核
对
采
供
部
下
电器件
外观检查
发
报
六.检测设备的计量及检定
❖ 1.负责公司检测设备的定期计量及检定.并做 好检测设备台帐..
检
单
规 格 型 号 合 格 证 说 明
书
在报检单上签字
合格
机
通绝耐来自械电缘
压
操
试
试
试
作
验
验
验
更换或退货
填写质量检验返修通知单
注、针对不允许耐压试验的元器件,将省去耐压试验步骤。
不合格
三.过程检验流程图
进入下一道工序
在周转卡上签字
合格
核
二次
对
线布
生产部上报开关柜 过程装配周转卡
检查柜内元件安装布 置是否符合图纸要求
元 件 规
置应 合理 整齐
格
美观
型
压接
号
牢固
一次 母线 之间 搭接 应自 然吻 合无 应力
返工或返修
填写质量检验返修通知单
不合格
生产部下发 成品报检单
四、成品检验流程图
外观检查
二次线美观性 牢固性检查
各种标 识检查
通电性 能检查
检验程序流程图
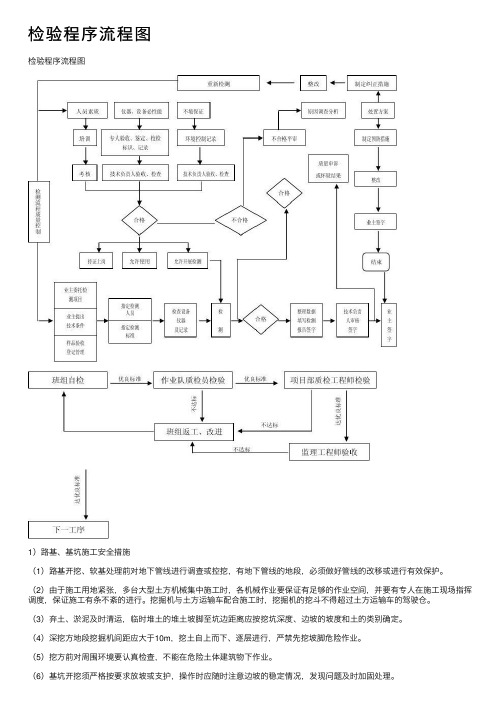
检验程序流程图检验程序流程图1)路基、基坑施⼯安全措施(1)路基开挖、软基处理前对地下管线进⾏调查或控挖,有地下管线的地段,必须做好管线的改移或进⾏有效保护。
(2)由于施⼯⽤地紧张,多台⼤型⼟⽅机械集中施⼯时,各机械作业要保证有⾜够的作业空间,并要有专⼈在施⼯现场指挥调度,保证施⼯有条不紊的进⾏。
挖掘机与⼟⽅运输车配合施⼯时,挖掘机的挖⽃不得超过⼟⽅运输车的驾驶仓。
(3)弃⼟、淤泥及时清运,临时堆⼟的堆⼟坡脚⾄坑边距离应按挖坑深度、边坡的坡度和⼟的类别确定。
(4)深挖⽅地段挖掘机间距应⼤于10m,挖⼟⾃上⽽下、逐层进⾏,严禁先挖坡脚危险作业。
(5)挖⽅前对周围环境要认真检查,不能在危险⼟体建筑物下作业。
(6)基坑开挖须严格按要求放坡或⽀护,操作时应随时注意边坡的稳定情况,发现问题及时加固处理。
2)脚⽤架、⽀架⼯程施⼯安全措施(1)钢管、扣件、螺栓的质量应符合规范规定。
不准使⽤锈蚀、弯瘪、滑⽛和有裂缝的⾦属杆件。
(2)脚⼿架纵、横距、步距应通过安全检算,满⾜结构安全需要。
(3)脚⼿架、⽀架搭设前,应对场地进⾏平整夯实、砼硬化处理,同时作好场地排⽔。
(4)脚⼿架、⽀架搭设完成后,应组织分段验收,合格后⽅准投⼊使⽤。
3)安全技术通⽤措施(1)在施⼯现场主要施⼯部位、作业点、危险区、主要通道⼝布设⾜够数量的警⽰牌、防护栏杆、标牌等,夜间设红灯警⽰,保证施⼯安全。
(2)详细编制各⼯种作业技术标准和安全操作细则。
杜绝违章⾏为,消除事故隐患,切实保障施⼯安全和重要设备不受损失。
(3)严格技术管理,在技术交底的同时,进⾏安全措施交底。
坚持⼯序技术交底制,并在施⼯中督促检查,使安全⼯作落到实处。
(4)施⼯机械在投⼊使⽤前按规定的安全技术标准进⾏检测、试运⾏和验收,确认能安全运⾏的⽅可投⼊使⽤,使⽤期间是悬挂“安全操作规程牌”,由专⼈持操作证使⽤,并定期维修。
6.4.2.3 主要分项⼯程施⼯质量保证措施1)施⼯测量(1)对所有施⼯⽤的测量仪器按计量要求定期到指定单位进⾏校定,施⼯过程中,如发现仪器误差过⼤,必须即时送修,并重新校定,精度满⾜要求之后,⽅可使⽤。
公司流程及流程图---检验流程

到现场检验,不合格直接要求车间现场返
修;
5
过程检验
质检员
《项目验收单》
整机加工、组装外包项目:加工过程需要
我司质检员到现场检验,不合格要求现场
返修或重新制作;
外协加工完成品自检合格后通知我司质检
去现场验收,验收合格在《项目验收单》
上签字通知市场部、供应链管理部可以发
6
成品检验
货;验收不合格要求外协厂返修或我司车 间返修,从货款中扣除返修费用; 外协加工完成品自检合格后送货到我司, 由我司质检员验收,验收合格在《项目验
的退货
4
成品组装
生产车间按照《生产计划》、图纸进行焊 接、组装成品
生产车间
《生产计划》
质检按照图纸对加工过程各环节的外观、
5
过程检验
尺寸进行检验,不合格直接要求车间现场
质检员
《检验报告》
返修
6
成品检验
质检按照图纸对成品的外观、尺寸进行检 验,不合格直接要求车间现场返修
质检员
《检验报告》
7
验收评审
质检检验结束待发货的产品需要各部门现 场评审,意见一致可以发货才允许发货
各部门
《项目评审单》
8
发货
验收合格,转发货流程
供应链管理 部
青岛XXXX有限公司
序号
步骤
1
安排生产计划
编号:XXX-QC-02-001-02
外协加工、整机组装外包检验流程
步骤内容
执行部门和 执行人
报告或表单
供应链管理部签收图纸、BOM\产品资料交 接单后制定《生产计划》,由生产经理下 发《调度令》至市场部、生产车间、总经 理,一式四联。
执行部门/ 执行人
过程流程图-范例

第 1 页,共 3 页(序号)(制造)(移动)(贮存)(检验)(项目号)(项目号)1毛坯入厂检验轴向尺寸,径向尺寸2用汽车专用盛具运至503厂产品加工毛坯堆放区外观搬运产品重量3铣端面打中心孔轴向尺寸,外圆尺寸,中心孔尺寸,各表面粗糙度,套车长度铣削参数、钻削参数(进给量、转速、吃刀量)4移动到下一工序辊式输送带速度5精车轴向尺寸,外圆尺寸,其余各部尺寸,各表面粗糙度,径向跳动车削参数(进给量、转速、吃刀量)6移动到下一工序辊式输送带速度7精车轴向尺寸,外圆尺寸,其余各部尺寸,各表面粗糙度,外圆及端面跳动车削参数(进给量、转速、吃刀量)8移动到下一工序辊式输送带速度9精车轴向尺寸,外圆尺寸,其余各部尺寸,各表面粗糙度车削参数(进给量、转速、吃刀量)10人工搬运到检验台11检验轴向尺寸,外圆尺寸,其余各部尺寸,各表面粗糙度,外圆和端面跳动,外观12人工搬运到下一工序13轧螺纹螺纹参数,表面粗糙度轧制参数(进给量、转速、吃刀量)14移动到下一工序辊式输送带速度15轧花键C 、D 花键跨棒距,齿形、齿向和累积公差,径向跳动,表面粗糙度滚轧参数(进给量、转速、吃刀量)16移动到下一工序辊式输送带速度17铣槽圆弧槽尺寸,外观,表面粗糙度铣削参数(进给量、转速、吃刀量)18人工搬运到下一工序19精车轴向尺寸,槽尺寸,其余各部尺寸,表面粗糙度,外观车削参数(进给量、转速、吃刀量)20人工搬运到下一工序21滚齿A 、B 齿轮跨棒距,齿形、齿向和累积公差,齿圈径向跳动,表面粗糙度,外观滚轧参数(进给量、转速、吃刀量)22人工搬运到下一工序23倒棱A 、B 齿轮渐开线尺寸,表面粗糙度,外观切削参数(进给量、转速、吃刀量)24移动到下一工序辊式输送带速度25剃A 齿A 齿轮跨棒距,径向跳动,表面粗糙度,齿形、齿向、齿距累积误差剃削参数(进给量、转速、吃刀量)26移动到下一工序辊式输送带速度27剃B 齿B 齿轮跨棒距,径向跳动,表面粗糙度,齿形、齿向、齿距累积误差剃削参数(进给量、转速、吃刀量)28人工搬运到检验台29检验外圆尺寸,轴向尺寸,槽和螺纹尺寸,其余各部尺寸,齿轮跨棒距,齿形、齿向、齿距累积误差,径向跳动,表面粗糙度(序号)(制造)(移动)(贮存)(检验)(项目号)(项目号)(序号)(制造)(移动)(贮存)(检验)(项目号)(项目号)第 3 页,共 3 页。
产品质量检验流程图

产品质量检验流程图产品质量检验流程图一、目的本流程图旨在明确产品质量检验的全过程,确保产品质量符合规定要求,以便公司在各个业务环节中有效控制和管理工作质量。
二、流程图1、原材料检验(1)采购部门根据需求进行原材料采购,并建立采购档案。
(2)原材料到货后,质量检验部门进行抽样检验,合格后方可入库。
(3)入库的原材料需进行标识,记录相关信息,保证可追溯性。
2、半成品检验(1)生产部门根据生产计划进行半成品生产。
(2)质量检验部门对半成品进行抽样检验,合格后方可进入下一道工序。
(3)对不合格的半成品,质量检验部门需出具不合格报告,并跟踪处理结果。
3、成品检验(1)生产部门完成成品生产后,将产品提交给质量检验部门进行成品检验。
(2)质量检验部门按抽样方案进行抽样检验,并出具检验报告。
(3)检验报告需记录详细信息,包括产品名称、规格、数量、检验日期、检验人员等。
4、不合格处理(1)若在检验过程中发现不合格品,质量检验部门需立即通知相关部门。
(2)相关部门需对不合格品进行评估,决定是否让步接收、返工或报废等处理措施。
(3)质量检验部门对处理结果进行跟踪,确保措施有效。
5、质量数据分析(1)质量检验部门定期收集检验数据,进行质量数据分析。
(2)根据数据分析结果,找出产品质量存在的问题和改进的空间,制定相应的改进措施。
(3)将质量数据分析结果反馈给相关部门,促进持续改进。
6、质量体系改进(1)根据质量数据分析结果和改进措施,对公司的质量管理体系进行评估和完善。
(2)对质量管理体系的改进需经过试运行和验证,确保改进的有效性。
(3)持续关注质量管理体系的运行情况,进行监控和调整,以提高公司的整体质量管理水平。
三、流程图说明本流程图旨在清晰地描述产品质量检验的过程,确保产品质量符合规定要求。
各个步骤紧密相连,形成一体化的质量检验流程。
在实际操作中,可根据具体情况对流程进行调整和优化。
总结:本流程图明确了产品质量检验的全过程,包括原材料检验、半成品检验、成品检验、不合格处理、质量数据分析和质量体系改进等环节。
质检部工作流程

报
检
单
规 格 型 号 合 格 证 说 明
书
在报检单上签字
合格
机
通
绝
耐
械
电
缘
压
操
试
试
试
作
验
验
验
更换或退货
填写质量检验返修通知单
注、针对不允许耐压试验的元器件,将省去耐压试验步骤。
不合格
三.过程检验流程图
进入下一道工序
在周转卡上签字
合格
核
二次
对
线布
生产部上报开关柜 过程装配周转卡
检查柜内元件安装布 置是否符合图纸要求
填写质
合格
检入库
单
包装 入库
绝缘性 能检查
耐压
试验
产品
卫生 检查
不合格
填写质量检
验返修通知单
进行
返工 或返 修
备注:如因安装缺件或其他特殊原因造成产品不合格而需要发货的,必需经总经理同意,且在产品让步放行 单上签字,方可发货.
五、随机文件的准备
❖ 1.填写产品合格证。 ❖ 2.填写产品出厂检验报告。
六.检测设备的计量及检定
❖ 1.负责公司检测设备的定期计量及检定.并做 好检测设备台帐..
元 件 规
置应 合理 整齐
格
美观
型
压接
号
牢固
一次 母线 之间 搭接 应自 然吻 合无 应力
返工或返修
填写质量检验返修通知单
不合格
生产部下发 成品报检单
四、成品检验流程图
外观检查
二次线美观性
牢固性检查
各种标
识检查
通电性 能检查
机械或联锁操 作性能检查
过程检验程序
PQC
流程
等级
目标
输入
作业方法描述
输出
信息
时效/反馈
职责
A
9艺卡》
3.《图纸》
4.样板
5.《抽样方法规定》
5.3过程巡检
5.3.1
PQC应在过程控制中,利用《统计技术(SPC)管理程序》对特殊性进行分析,并由车间主任对过程进行分析。
1.X(Bar)~R图
2.X(Bar)—S图
车间
●
PQC
A
98%
1.《过程检验报告》(首检)
——不合格
5.1.2
生产车间应对批准为不合格的首件进行原因分析,进行设备的再次调试,必要时提交《质量异常报告》及首件检验报告作为附页,召集相关部门讨论并分析对策。
1.《质量异常报告》
品质科科长(含副)
●
车间
A
98%
1.《过程检验报告》(首检)
5.1.3
PQC应将《首件检验报告》的不合格次数进行统计,并分析《首检检验一次合格率》
《首检检验一次合格率》
车间
持续发展办
每月5日前
PQC
A
96%
1.《工艺卡》
2.样板
3.图纸
5.2自主检验:
5.2.1
在操作过程中,在有自主检验规定时,操作员应按《工艺卡》及相关文件做产品检验,并做《过程检验报告》(自检)。《过程检验报告》(自检)在操作时间有矛盾时可由PQC协助填写,但操作员必需签名确认。
车间主任
●
FQC
●
●
1.《过程转序检验报告》
5.5.2
《过程转序检验报告》由QE审核。
《过程转序检验报告》
——审核
过程检验流程图
过程检验流程图
根据流转单生产
检验员对首件进行首检,并对
不合格的进行停工调整
对检验合格的进行记录
操作者对首件进行自检,并对
不合格的进行停工调整
按工艺卡或作业指导书的规
定频次、数量及要求进行巡回
检验并对检验结果进行判定
对不合格品进行处置,对合
格的进行记录开始
加工
自检
首检
记录
巡检
记录
终检
记录
转序或入库
完成
停工调整
不合格处置
N
N
Y
Y
N
N
Y
Y
按工艺文件规定进行完工
检验并对对检验结果进行
判定
对检验合格品的进行记录
对合格品进行转序或入库
进货检验管理流程图开始
送货单
送检理化
检验记录入库单入库
标识
审批
退货单
退货
结束
整理需要检验产品种类
有理化试验要求的物资,
由检验员委托理化试验
检验员根据检验规范等文
件对物资进行检验并对检
验结果和理化结果确认
检验合格的开“检验报
告的进行审批
合格的产品签字入库;
评审不合格的退货
执行入库或退货
N
N
Y
Y。
制程检验作业流程图
制程检验作业流程流程图1.0目的为保证产品在生产制程中得到有效检验作业,控制制程品质,降低制程返工、报废,提升产品合格率,提高不良出来的时效性,特制定本作业流程。
2.0 范围适用于(备料车间、白身车间、油漆车间、包装车间)生产过程中的检验与控制及不良品处理。
3.0 职责3.1 PMC部:计划课负责生产指令的下达,参与生产异常处理;仓务课负责完成不良品的回仓分类保管、标识确认及不良品退料的督促工作。
3.2 各生产车间:负责制程产品材料确认,首件产品品质确认及生产过程中的自检、互检工作。
反馈、参与生产异常处理;3.3品管部:首件产品确认及生产过程中的巡检、完工后检验,反馈、主导或参与品质异常处理工作,并对数据记录保存、统计、分析、改善,持续改善;3.4 相关部门:主导或参与品质异常处理及异常分析工作。
4.0 作业程序4.1 PMC部下发《生产日计划》给各生产车间主管,各生产车间主管根据《生产日计划》,组织安排操作工做好生产前的准备工作;4.2 各车间组长、技术员准备工装夹具、测量量具、签样等,按样品或产品工程作业标准书等准备物料进行生产。
备料、白身、总装车间:工装夹具、测量量具、签样、作业指导书、图纸、模具等。
油漆车间:色板、签样、作业指导书、图纸等。
包装车间: 签样、作业指导书、图纸、产品包装示意图、模具等。
4.3组长、技术员对首件先自检,合格报制程检验员对首件进行检验,详细参考《首件检验控制卡》。
4.4制程检验员全检或按规定频次(正常情况下每天不少于6次)及工艺图纸等要求巡检各工序制程品质状况,巡检要有相关侧重点,填写巡检记录,若不符图纸和工艺要求,则知会操作员异常状况;当生产操作工自检发现不良现象时及时隔离和标识;当产生不良品超标时,发现人即时通知本组组长到现场确认,组长到现场确认后,按《生产异常提报控制卡》进行操作,必要时组长填写《品质异常报告和处理单》交责任单位处理(来料引起的不良交品管部处理;制程引起的不良交本部车间主管处理)。
生产过程检验流程图
生产日报表/异 常联络单
OQC抽检
OK 入库 生产部/ 仓库
将已入箱的产品的工单 在ERP系统中办理入库 申请,仓管员核对无误 后封箱入库 ERP入库单
按SIP,图纸对产品进行 检验,NG退给生产部并发 出《异常联络查记录表,首 检检验报告,异常联 络单
生产部
按SOP,工单,首检样板 进行生产
生产日报表
NG 巡检
品质部
依QC工程图,控制计划, SIP进行巡检,按控制计 划对特殊性进行监控,NG 联络生产部进行改善,OK 进行有效记录
生产过程检验流程图
流程 责任部门 流程说明
人员,设备,物料,作业 指导文件,环境的准备与 确认。
文件/记录
工单,BOM表,物料 领用清单,员工技能 矩阵图,设备点检表
生产前 准备
生产部
首件制作 NG 首检 OK 生产
生产部
按生产计划,SOP要求进行 调机,试装,做首件
试样检查记录表,生 产订单
品质部
巡检记录表,异常联 络单
OK NG LQC终检 OK NG 品质部
按工单及出货计划对待检 区域的产品进行抽样检验 确认,NG开出不合格检验 报告并开出《异常联络 单》通知生产部进行改善 检验记录表,异常联 络单
生产部
按工单,SOP,SIP检验包 装,标识,密封,入箱转 待检区,针对不合格开出 异常联络单
- 1、下载文档前请自行甄别文档内容的完整性,平台不提供额外的编辑、内容补充、找答案等附加服务。
- 2、"仅部分预览"的文档,不可在线预览部分如存在完整性等问题,可反馈申请退款(可完整预览的文档不适用该条件!)。
- 3、如文档侵犯您的权益,请联系客服反馈,我们会尽快为您处理(人工客服工作时间:9:00-18:30)。
过程检验流程图
标准化文件发布号:(9312-EUATWW-MWUB-WUNN-INNUL-DQQTY-
过程检验流程图
流程代号:001 流程名称:首件检验主管部门:品质控制部
要求;
1.每批量生产,对首件进行全面检验。
2.对首件检验的依据暗检验标准、技术文件、图纸、生产状态表。
3.对首件检验标准出现异常,收集信息进行分析处理。
4.对不合格项目进行纠正后要重新检验,对记录好。
5.对无法纠正的,进行其他处理。
过程检验流程图
流程代号:002 流程名称:巡检主管部门:品质控制部
要求:
1、在生产过程中质检员监督各工位自检。
2、自检是员工自己对照作业指导书对质量把关。
3、质检员巡检需填写《巡查表》,对不合格项开具《预防、纠正
措施表》并跟踪处理完。
4、巡检依据《过程检验规范》并重把关质量控制关键点。