Barriers of HACCP team members to guideline adherence
haccp 过程关系 英语

haccp 过程关系英语HACCP (Hazard Analysis and Critical Control Point) is a systematic approach to the identification, assessment, and control of potential hazards in the food production process. It involves seven principles that are essential for ensuring food safety:1. Conduct a hazard analysis: Identify all potential hazards associated with the food production process, including biological, chemical, and physical hazards.2. Determine critical control points (CCPs): Identify steps at which control can be applied, and prevent or reduce hazards to an acceptable level.3. Establish critical limits: Set specific criteria for each CCP that must be met to ensure that the hazard is controlled.4. Monitor CCPs: Develop a system to monitor each CCP on a regular basis to ensure that critical limits are being met.5. Establish corrective actions: Develop procedures to befollowed when a deviation occurs from a critical limit.6. Verify the HACCP system: Confirm that the HACCP system is working correctly through verification activities such as testing and record review.7. Maintain records: Keep records of all HACCP activities, including hazard analysis, CCP monitoring, corrective actions, and verification.The relationship between these principles is that they work together to form a comprehensive system that ensures food safety throughout the food production process. Each principle builds upon the previous one, creating a logical sequence of steps that must be followed to effectively control potential hazards. By implementing HACCP, food producers can identify and control potential hazards before they become problems, ensuring that consumers have access to safe, high-quality food products.。
BRC Food Safety 学习笔记汇总
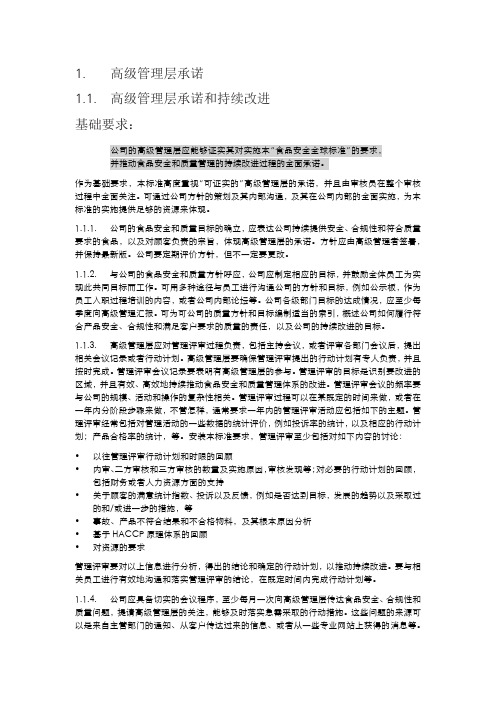
1.高级管理层承诺1.1.高级管理层承诺和持续改进基础要求:公司的高级管理层应能够证实其对实施本“食品安全全球标准”的要求,并推动食品安全和质量管理的持续改进过程的全面承诺。
作为基础要求,本标准高度重视“可证实的”高级管理层的承诺,并且由审核员在整个审核过程中全面关注。
可通过公司方针的策划及其内部沟通,及其在公司内部的全面实施,为本标准的实施提供足够的资源来体现。
1.1.1.公司的食品安全和质量目标的确立,应表达公司持续提供安全、合规性和符合质量要求的食品,以及对顾客负责的宗旨,体现高级管理层的承诺。
方针应由高级管理者签署,并保持最新版。
公司要定期评价方针,但不一定要更改。
1.1.2.与公司的食品安全和质量方针呼应,公司应制定相应的目标,并鼓励全体员工为实现此共同目标而工作。
可用多种途径与员工进行沟通公司的方针和目标,例如公示板,作为员工入职过程培训的内容,或者公司内部论坛等。
公司各级部门目标的达成情况,应至少每季度向高级管理汇报。
可为可公司的质量方针和目标编制适当的索引,概述公司如何履行符合产品安全、合规性和满足客户要求的质量的责任,以及公司的持续改进的目标。
1.1.3.高级管理层应对管理评审过程负责,包括主持会议,或者评审各部门会议后,提出相关会议记录或者行动计划。
高级管理层要确保管理评审提出的行动计划有专人负责,并且按时完成。
管理评审会议记录要表明有高级管理层的参与。
管理评审的目标是识别要改进的区域,并且有效、高效地持续推动食品安全和质量管理体系的改进。
管理评审会议的频率要与公司的规模、活动和操作的复杂性相关。
管理评审过程可以在某既定的时间来做,或者在一年内分阶段步骤来做,不管怎样,通常要求一年内的管理评审活动应包括如下的主题。
管理评审经常包括对管理活动的一些数据的统计评价,例如投诉率的统计,以及相应的行动计划;产品合格率的统计,等。
安装本标准要求,管理评审至少包括对如下内容的讨论: •以往管理评审行动计划和时限的回顾•内审、二方审核和三方审核的数量及实施原因,审核发现等;对必要的行动计划的回顾,包括财务或者人力资源方面的支持•关于顾客的满意统计指数、投诉以及反馈,例如是否达到目标,发展的趋势以及采取过的和/或进一步的措施,等•事故、产品不符合结果和不合格物料,及其根本原因分析•基于HACCP原理体系的回顾•对资源的要求管理评审要对以上信息进行分析,得出的结论和确定的行动计划,以推动持续改进。
加拿大农业及农业食品部
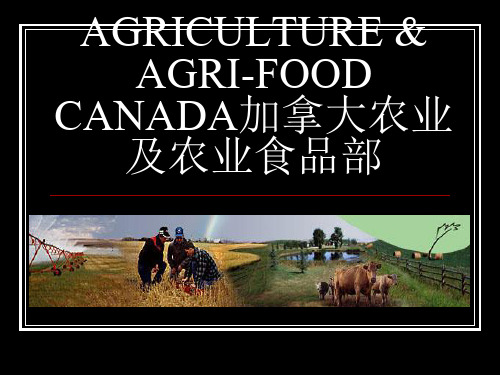
Food Safety & Quality食品安全和 质量
The Government of Canada is committed to ensuring that food produced in Canada continues to be among the safest and highestquality in the world. Canada is putting in place national, seamless food safety systems on the farm and throughout the agri-food chain - from the field to the fork. 加拿大政府承诺保证加拿大产食品继续是 最安全和最高品质的在世界范围内.加拿大正在对农场进行一个全国 的,无伤痕的食品安全系统 通过农产品链—从农田到叉子
networks to better link scientific advances to the creation of new economic opportunities与科学新技术保持更好的联络来 创造新的经济机会
International国际
The international component is designed to maximize international opportunities arising from progress on the domestic front. 国际成分被设计以 最大化进步的国际机遇在国内
加拿大正在对农场进行一个全国的无伤痕的食品安全系统通过农产品链从农田到叉子hesectoodsafetconcernswhimprovingmarketaccessopportunihesect将会改善部门能力去鉴别和回答食品安全问题和考虑通过改善市场准入和机会workingwindustryexistoodsafetmeasures同农民和工业一起工作来建造现存的食品安全措施undertakingnewmeasuresracingoodproductoodqualsharecrinformat保证新措施能保证从农场追查食品产品改善食品质量和分享重要信息sciencehecornerstonehecanadiagriculoodsectheworloodsafetenvironmentalresponsibluturesuccess科学和创新是保证加拿大农业和农产品在世界食品安全创新和对环境负责的生产的努力基础和保证其将来的成功和繁荣
食品安全体系 HACCP 基础课程 【教材】中英双语
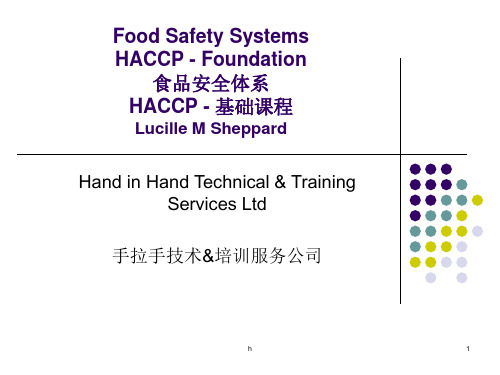
info@
h
9
© Sheppard 2010
077483 72683
H.A.C.C.P Objective H.A.C.C.P的目标
To ensure a high level of consumer protection with regards to food safety systems.
h
11
© Sheppard 2010
077483 72683
What is the role of employers? 雇主的角色?
Establish and maintain appropriate food safety culture 建立和维护适当的食品安全文化
Be committed to HACCP, implement system and provide adequate resources 致力于HACCP,确保体系的实施并提供充足的资源
Fines of up to £5000 per offence. 违反一次最高罚款5000英镑
For serious offences unlimited fines and maximum 2 years imprisonment. 严重违反的面临无限额罚款和两年以下的监禁
info@
HACCP plan 实施HACCP计划
Module 5 模块5
Verification
验证
Module 6 模块6
Review 评审
info@
h
2
© Sheppard 2010
077483 72683
Module 1
模块 1
Introduction to HACCP HACCP介绍
专业英语食品安全

VS
The background to this field is the globalization of the food industry, which has led to an increase in the need for cross cultural communication and understanding of food safety regulations
The importance of food safety
Food safety is critical for protecting consumer health and preventing the spread of foodborne illnesses
It is essential for maintaining the reputation and trustworthiness of the food industry, as well as for ensuring compliance with legal requirements
Allow additives
Different countries or regions have their own lists of allowed food additives, which may vary in terms of types, usage limits, and labeling requirements
Food safety also plays a vital role in international trade, as it is a prerequisite for the export and import of food products
食品经营安全管理制度英文
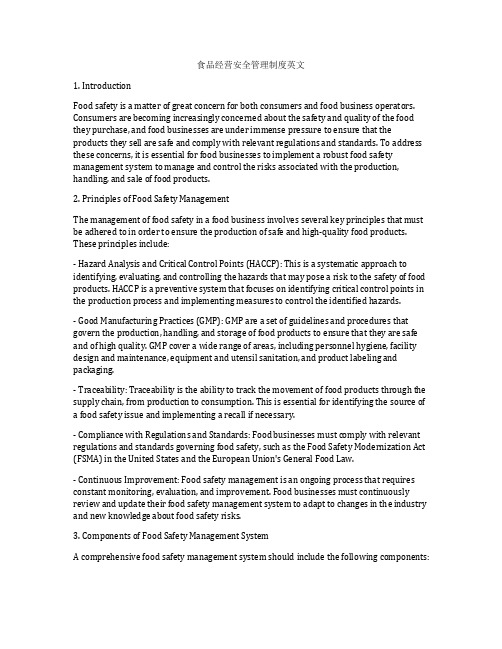
食品经营安全管理制度英文1. IntroductionFood safety is a matter of great concern for both consumers and food business operators. Consumers are becoming increasingly concerned about the safety and quality of the food they purchase, and food businesses are under immense pressure to ensure that the products they sell are safe and comply with relevant regulations and standards. To address these concerns, it is essential for food businesses to implement a robust food safety management system to manage and control the risks associated with the production, handling, and sale of food products.2. Principles of Food Safety ManagementThe management of food safety in a food business involves several key principles that must be adhered to in order to ensure the production of safe and high-quality food products. These principles include:- Hazard Analysis and Critical Control Points (HACCP): This is a systematic approach to identifying, evaluating, and controlling the hazards that may pose a risk to the safety of food products. HACCP is a preventive system that focuses on identifying critical control points in the production process and implementing measures to control the identified hazards.- Good Manufacturing Practices (GMP): GMP are a set of guidelines and procedures that govern the production, handling, and storage of food products to ensure that they are safe and of high quality. GMP cover a wide range of areas, including personnel hygiene, facility design and maintenance, equipment and utensil sanitation, and product labeling and packaging.- Traceability: Traceability is the ability to track the movement of food products through the supply chain, from production to consumption. This is essential for identifying the source of a food safety issue and implementing a recall if necessary.- Compliance with Regulations and Standards: Food businesses must comply with relevant regulations and standards governing food safety, such as the Food Safety Modernization Act (FSMA) in the United States and the European Union's General Food Law.- Continuous Improvement: Food safety management is an ongoing process that requires constant monitoring, evaluation, and improvement. Food businesses must continuously review and update their food safety management system to adapt to changes in the industry and new knowledge about food safety risks.3. Components of Food Safety Management SystemA comprehensive food safety management system should include the following components:- Food Safety Policy: The food business should have a written food safety policy that outlines its commitment to producing safe and high-quality food products. The policy should be communicated to all employees and stakeholders, and regularly reviewed and updated.- Food Safety Team: A dedicated food safety team, led by a designated food safety manager, should be responsible for implementing and managing the food safety management system. The team should be trained in food safety principles and have the authority to make decisions regarding food safety.- Hazard Analysis and Critical Control Points (HACCP) Plan: The food business should develop and implement a HACCP plan that identifies the hazards associated with its products and processes, determines critical control points, and establishes control measures to manage the identified hazards.- Good Manufacturing Practices (GMP) Procedures: The food business should have written procedures for GMP covering all aspects of production, handling, and storage of food products. These procedures should be regularly reviewed and updated to reflect changes in processes or regulations.- Product Testing and Monitoring: The food business should establish a program for testing and monitoring the safety and quality of its products. This may include regular microbiological and chemical testing, environmental monitoring, and sensory analysis.- Supplier Management: The food business should establish and implement a supplier management program to ensure that its suppliers meet the same high standards for food safety. This may include supplier audits, supplier approval processes, and regular supplier monitoring.- Training and Education: All employees involved in the production, handling, and sale of food products should receive regular training on food safety principles, procedures, and best practices. This training should be documented and regularly reviewed to ensure its effectiveness.- Incident Management and Recall Procedures: The food business should have written procedures for managing food safety incidents and implementing product recalls if necessary. These procedures should be regularly reviewed and tested to ensure their effectiveness.4. Implementation of Food Safety Management SystemThe successful implementation of a food safety management system requires the commitment and involvement of the entire organization. The following steps can help ensure the successful implementation of a robust food safety management system:- Leadership Commitment: The top management of the food business should demonstrate a strong commitment to food safety by allocating the necessary resources, setting clearobjectives, and providing visible support for the implementation of the food safety management system.- Employee Involvement: All employees should be involved in the implementation of the food safety management system through training, education, and participation in food safety activities. Employees should be encouraged to report food safety concerns and be provided with the necessary means to do so.- Communication and Training: Effective communication is essential for the successful implementation of a food safety management system. The food business should ensure that all employees are aware of the food safety policy, procedures, and their roles and responsibilities in ensuring food safety.- Documentation and Records: The food business should maintain all necessary documentation and records to demonstrate compliance with the food safety management system. This may include records of training, product testing, supplier approvals, and incident management.- Monitoring and Review: The food business should regularly monitor and review the effectiveness of its food safety management system through internal audits, management reviews, and performance indicators. Any deficiencies or opportunities for improvement should be promptly addressed.- Continuous Improvement: The food business should be committed to continuously improving its food safety management system through the identification and implementation of corrective and preventive actions, and the adoption of new best practices and technologies.5. ConclusionIn conclusion, the implementation of a robust food safety management system is essential for ensuring the safety and quality of food products. By adhering to the key principles of food safety management and implementing the necessary components, food businesses can mitigate the risks associated with food production and ensure consumer confidence in their products. The successful implementation of a food safety management system requires the commitment and involvement of the entire organization and a continuous dedication to monitoring, reviewing, and improving food safety practices.。
食品安全体系规范(HACCP)(英文版)

SPECIFICATIONREQUIREMENTSFOR AHACCP BASEDFOOD SAFETY SYSTEMCompiled by theNational Board of Experts – HACCPThe Netherlands.The Hague, the Netherlands: 3rd Version, September 2002This is the authorised English translation of the specification “Eisen voor een op HACCP gebaseerd voedselveiligheids-systeem” (3rd version, September 2002), being one of three documents which regulate the Certification Scheme for operational HACCP based food safety systems.T he two other documents; the “Certification Regulations” and the “Regulations for the National Board of Experts –HACCP” are also published by the National Board of Experts – HACCP.Certifying Bodies operating the Certification Scheme for operational HACCP based food safety systems have to comply with the “Requirements for Certification Bodies”, also established and published by the National Board of Experts – HACCP.The Certification Scheme for HACCP based Food Safety Systems is maintained by the National Board of Experts - HACCP.Certification/Registration of HACCP based Food Safety Systems on the basis of the preceding versions of this specification has been accredited by the Dutch Accreditation Council (RvA) since 1997.Copyright 2002 National Board of Experts - HACCPPrice: EURO 23,00 (excluding VAT).All rights reserved. No part of this publication may be reproduced and/or published in any form, by means of printed matters, photocopy, microfilm, recording or any other method or technology, without preceding written approval by the National Board of Experts - HACCP.National Board of Experts - HACCP,Secretariat: P.O. Box 93202, 2509 AE, The Hague, The Netherlands.Web site: email:******************************CONTENTS1 INTRODUCTION 42 SCOPE of APPLICATION 73 REFERENCE DOCUMENTS 84 TERMS and DEFINITIONS 95 HACCP SYSTEM REQUIREMENTS 125.1 Management responsibility 125.1.1 Policy5.1.2 Scope of the HACCP system5.1.3 Task, Responsibilities, Authorities5.1.4 HACCP team(s)5.1.5 Resources5.1.6 Management review5.2 Product Information 145.2.1 Product Characteristics5.2.2 Intended use5.3 Process Information 155.3.1 Flow Diagrams5.3.2 Layout5.3.3 Control and Verification of Process Information5.4 Pre-requisite program 165.5 Hazard Analysis 175.5.1 Hazard identification5.5.2 HACCP analysis (risk)5.6 Control Measures 195.6.1 Specific Control Measures5.6.2 General Control Measures5.7 Parameters and Critical Limits 205.7.1 Critical process and product parameters5.7.2 Target values, action-limit values and critical limits5.8 Monitoring and Measuring 215.9 Corrective Actions 225.10 Validation 235.11 Verification 245.12 Documentation and records 265.12.1 Documents and document control5.12.2 Records6 ANNEX I: PRE-REQUISITE PROGRAM (PRP) 277 ANNEX II: RELATIONSHIP BETWEEN THE “REQUIREMENTS” 35AND CODEX GUIDELINES FOR THE APPLICATION OF HACCP1 INTRODUCTIONReference documents; legislation; background informationFood safety is a global concern. Not only because of the continuing importance for public health, but also because of its impact on international trade. Effective Food Safety Systems shall therefore manage and ensure the safety and suitability of foodstuffs.In many countries world-wide, legislation on the safety and suitability of foodstuffs requires “HACCP” to be put in place by any food business or organisation, whether profit-making or not and whether public or private, carrying out any or all of the following activities: preparation, processing, manufacturing, packaging, storage, transportation, distribution, handling or offering for sale or supply of foodstuffs. According to EU Directive 93/43/EEC on Food Hygiene all food business operators in the European Union shall implement HACCP 1. They shall ensure that adequate safety procedures are identified, documented, maintained and reviewed on the basis of the principles used to deve lop the system of HACCP (“Hazard Analysis and Critical Control Po int”).The Joint FAO/WHO Codex Alimentarius Commission describes a series of steps, including the 7 HACCP principles giving guidance for the application of the HACCP system 2. Also, Codex advises that minimum hygiene measures should be in place before HACCP is implemented:”Prior to application of HACCP to any sector of the food chain, that sector should be operating according to the Codex General Principles of Food Hygiene, the appropriate Codex Codes of Practice, and appropriate food safety legislation.”These prerequisite programs should be well specified and documented, fully operational and verified in order to facilitate the successful application and implementation of HACCP. The General Principles of Food Hygiene 3, as recommended by Codex, form an intrinsic pa rt of this document “Requirements for a HACCP based Food Safety System”.Specific food safety requirements are detailed in legislation, hygiene codes, customer or consumer specifications. Where specific requirements do not exist, the General Principles on Food Hygiene will be applied (see Annex I). Furthermore, the 7 principles and the guidelines for the application of HACCP have been combined in this Specification with basic elements of quality management systems (ISO 9000) to establish “The Requirements for a HACCP based Food Safety System”.The reference documents used to formulate the “Requirements” have been specified in Chapter 3.The “Requirements” are primarily focused on actions and activities to ensure food safety. The assurance of food suitability is considered to be an obligatory part of a quality management system, unless deviations may lead to unsafe foodstuffs.1EU Directive 93/43/EEC on the Hygiene of Foodstuffs, dated 14 June 1993 (PbEC L175).2Codex Alimentarius Com mission, “Hazard A nalysis and Critical Control Point (HACCP) System and Guidelines for its Application”, Annex to CAC/RCP 1-1969, Rev. 3 (1997).3Codex Alimentarius Com mission, “General Principles of Food Hygiene, CAC/RCP 1-1969, Rev. 3 (1997), amended 1999.The need for a Standard or SpecificationThe specification “Requirements for a HACCP based Food Safety System” has been developed by and is placed under the authority of the National Board of Experts –HACCP in order to make a normative document/standard available. All parties involved in the food chain are represented on the National Board of Expert - HACCP. The specification can be used by Certifying Bodies to assess the continuous compliance of HACCP-based Food Safety Systems as developed and implemented by food business operators.Of course, a food business operator may also use the “Requirements” to develop its HACCP-based Food Safety System.Certification/Registration (e.g.of HACCP-based Food Safety Systems) signifies that by means of a formal statement (a certificate) and/or mark, notice is given with justified confidence that a product, process or service or system is in conformance with a pre-defined standard or (technical) specification. This includes the ability of the company to maintain conformance with the standards or specifications.In order to issue such a formal statement, the HACCP-based Food Safety System of a food business operator needs to be assessed. Certification and repetitive surveillance audits are to be effectively performed by a Certifying Body which is an independent institution (whether or not governmental) that has both the authority as well as the confidence to operate a certification system within which the interests of all involved parties are represented.For confidence the Certifying Body must use the published “Requirements” and the “Certification Regulations” in an agreed manner. The “Requirements” are documented in such a way to allow an effective assessment of the status and performance of the HACCP-based Food Safety System, as implemented by the food business operator. In the “Certification Regulations”, specific criteria are stated which have to be met by the Certifying Body when selecting a competent HACCP audit team, and rules which govern the way the certification process is designed and offered (e.g. the minimum auditor time) have to be followed.Authority is obtained when the Certifying Body is formally accredited by a recognised Body to operate the certification system for HACCP based Food Safety Systems 4 and is audited regularly by this Accreditation Body. Accreditation concerns the reliability and competence of the Certifying Body.The document “Requirements for Certification Bodies” elaborates the accreditation requirements.It must be understood that certification of a HACCP-based Food Safety System is not a guarantee of a food business operator’s continuous food safety perfor mance. The value added to a food business operator with a certified HACCP-based Food Safety System lies in the efforts made by the operating company to maintain that HACCP system and its commitment to continuously improve its food safety performance. Requirements for a HACCP based Food Safety System4The c ertification bodies must meet “General require ments for bodies operating assessment and certification / registration of quality systems”, ISO/IEC Guide 62:1996 (EN 45012) andthe Standards for auditing (ISO 10011, Part 1, 2 and 3).The requirements in this Specification provide a basis for compliance of a HACCP-based Food Safety System with (inter)national legislation and codes of practice. They include the necessary management system requirements. The structure, the sequence and interaction of the assessment process is detailed in Figure 1.In the description of every clause, the scope of the requirements is detailed. Using these clauses, the audit team assesses the documented HACCP-based Food Safety System as well as the implementation and operation of the system on the 'shop floor'. The “Requirements” lay down a generic set of requirements. An operational HACCP-based Food Safety System shall be, as a minimum, in compliance with these Requirements. In Annex II of this document each heading or paragraph of the “Requirements” refers to the corresponding text in the HACCP guidance document of Codex Alimentarius 5.Figure 1. The structure of a HACCP-based Food Safety System←↑→→→→→→→→→→In order to make the system transparent and enable assessment, the food business operator shall provide information as indicated in these “Requirements”. For each specific condition (product / product group / process / sector), specific requirements shall be detailed by the food business operator. The audit team shall assess this complete system of generic and company specific requirements.5Codex Alimentarius Com mission, “Hazard Analysis and Critical Control Point (HACCP) System and Guidelines for its Application”, Annex to CAC/RCP 1-1969, Rev. 3 (1997).The first version of these “Requirements” (then called “Criteria”) has been developed in co-operation with several Certification Bodies in the Netherlands in the area of food materials and processing, under the authority and responsibility of the National Board of Experts - HACCP. The 1st version was published on May 15, 1996.Due to the modification of the Codex Alimentarius (Alinorm 97/13A, Appendix II) in 1997, a revision of the Requirements became necessary. The National Board of Experts - HACCP was also able to draw on their experience in order to improve the quality of the “Requirements”. The 2nd version of the “Requirements” was published in September 1998 and translated into English in February 1999.Recent developments with respect to HACCP-based Food Safety System and developments within Codex, as well as new proposals for Food Hygiene Regulations (thereby repealing the current referenced EU Directives and Regulations), have necessitated a further revision: this 3rd version!2 SCOPE of APPLICATIONIn this document, requirements have been specified to be used during the assessment of operational HACCP systems (HACCP-based Food Safety Systems) which ensure the safety of foodstuffs during preparation, processing, manufacturing, packaging, storage, transportation, distribution, handling or offering for sale or supply in any sector of the food chain.The “Requirements” are basically applicable to all food businesses or organisations, whether profit-making or not, and whether public or private.Obviously, the food business operators shall have identified any step in their activities which is critical to ensure food safety and shall have developed, implemented, maintained and reviewed adequate safety procedures, applying the principles of HACCP, including the general principles of food hygiene, and where appropriate the relevant codes of practice and the food safety legislation.These “Requirements” are not intended for application by sup pliers and / or service companies to food businesses, like suppliers of packaging materials, food equipment, industrial cleaning services, etc..3 REFERENCE DOCUMENTSThe “Requirements for a HACCP-based Food Safety System” are based on the following reference documents:1World-wide:Joint FAO/WHO Codex Alimentarius Commission,-General Principles of Food Hygiene, CAC/RCP 1-1969, Rev. 3 (1997), amended 1999.-Hazard Analysis and Critical Control Point (HACCP) System and Guidelines for its Application, Annex to CAC/RCP 1-1969, Rev. 3 (1997).2International level:European Union2aGeneral Food lawRegulation (EC) no 178/2002, laying down the general principles and requirements of food law, establishing the European Food Safety Authority and laying down procedures in matters of food safety, dated 28 January 2002.2bCouncil Directive 93/43/EEC on the Hygiene of Foodstuffs, dated 14 June 1993 (PbEC L175);Specific legislation and regulations concerning food safety and hygiene have been laid down in Council Directives such as 64/433/EEC for fresh meat, 71/118/EEC for poultry meat, 89/437/EEC for egg products, 92/46/EEC for dairy products, 92/5/EEC for meat products, 91/493/EEC for fishery products, 94/65/EEC for minced meat, etc..2cDocuments under 2b will be repealed by:Proposal for a Regulation of the European Parliament and of the Council on the hygiene of foodstuffs,COM/2000/0438 final, 14 July 2000 (COD 2000/0178), and others.3National level:Netherlands, Food and Commodity Act:Warenwetregeling Hygiëne van Levensmiddelen, 12 december 1994 (DGVgz/VVP/L 942587).4Where appropriate:Numerous (International, a/o. Codex) Codes of Practice, Food Commodity Standards and (national) Hygiene Codes (generic HACCP / hygiene plans).4 TERMS and DEFINITIONSAction-limit value: A value for the product or process parameter under consideration, deduced from the critical limit value, which indicates that an intervention in the process is required.Aspect: An element of the food business operation (products, processes, PRP, services) that can interact with the food safety.Certification: Action by a third party demonstrating that adequate confidence is given that a duly identified product, process or service conforms with a specific standard or other normative document.Control (verb): To take all necessary actions to ensure and maintain compliance with criteria established in the HACCP plan.Control (noun): The state wherein correct procedures are being followed and criteria are being met.Control measure: Any action and activity that can be used to prevent or eliminate a food safety hazard or reduce it to an acceptable level.Control measure, general: A measure to control a specific part of the PRP.Control measure, specific: A measure to control a CCP.Corrective action: Any action to be taken when the results of monitoring at the CCP indicate a loss of control.Critical Control Point (CCP): A step at which it is essential that a specific control measure is applied to prevent or eliminate a food safety hazard or reduce the risk to an acceptable level (see also Control measure, specific) .Critical limit: A criterion which separates acceptability from non-acceptability.Note: This criterion defines the limiting values for the product or process parameter(s) under consideration for monitoring (see action-limit values and target values).Flow diagram: A systematic representation of the sequence of steps or operations used in the preparation, processing, manufacturing, packaging, storage, transportation, distribution, handling or offering for sale of a particular food item. Food business operator: The person or persons responsible for ensuring that the requirements of thefood legislation are met within the food business under his/their control.Food handler: Any person who directly handles packaged or unpacked food, food equipment and utensils, or food contact surfaces and is therefore expected to comply with food hygiene requirements.Food hygiene: All conditions and measures necessary to ensure the safety and suitability of food at all stages of the food chain.Food safety: Assurance that food will not cause harm to the consumer when it is prepared and/or eaten according to its intended use.Food suitability: Assurance that food is acceptable for human consumption according to its intended use.General Control Measure: see: Control measure, generalHACCP (Hazard Analysis and Critical Control Point): A system which identifies, evaluates and controls hazards which are significant for food safety.HACCP audit: A systematic and independent examination to determine whether the HACCP system, including the HACCP plan and related results, comply with planned arrangements, are implemented effectively and are suitable for the achievement of its objectives.Note: Examination of the Hazard Analysis is an essential element of the HACCP audit.HACCP plan: A document prepared in accordance with the principles of HACCP to ensure control of hazards which are significant for food safety in the segment of the food chain under consideration.HACCP based Food Safety System: (a HACCP system): The organisational structure, procedures, processes and resources needed to execute the HACCP plan(s) and meet its objectives.HACCP team: Group of individuals (multi-disciplinary) who develop, implement and maintain a HACCP system.Hazard: A biological, chemical or physical agent in, or condition of, food with the potential to cause an adverse health effect.Hazard analysis: The process of collecting and evaluating information on hazards and conditions leading to their presence, to decide which are significant for food safety and should therefore be addressed in the HACCP plan.Monitoring: The act of conducting a planned sequence of observations or measurement of control parameters to assess whether a CCP is under control.Pre-Requisite Programme (PRP): Any specified and documented activity or facility implemented in accordance with the Codex General Principles of food hygiene, good manufacturing practice and appropriate food legislation, in order to establish basic conditions that are suitable for the production and handling of safe food at all stages of the food chain.Preventive action: Any measure or activity that will be used to prevent, to eliminate or to reduce the recurrence of causes for existing deviations, defects or any other undesired situation with respect to food safety.Primary production: Those steps in the food chain up to and including harvesting, hunting, fishing, milking and all stages of animal production prior to slaughter.Products, unprocessed: Foodstuffs which have not undergone a treatment, including products which have been, for example, divided, parted, severed, boned, minced, skinned, ground, cut, cleaned, trimmed, husked or milled, chilled, frozen or deep-frozen.Products, processed: Foodstuffs resulting from the application to unprocessed products of a treatment such as heating, smoking, curing, maturing, pickling, drying, marinating, extraction, extrusion, etc. or a combination of these processes and/or products; substances necessary for their manufacture or for giving specific characteristics to the products may be added.Risk: The probability of causing an adverse health effect caused by the occurrence and the severity of a particular hazard in food when prepared and consumed according to its intended use.Target value: The value of the product or process parameter(s) to be monitored, targeted within action-limit values (the range of acceptable variations) and certainly within critical limit values, thus securing a safe product.Step: A point, procedure, operation or stage in the food chain, including raw materials, from primary production to final consumption.Validation: Obtaining evidence (in advance) that the specific and general control measures of the HACCP plan are effective.Verification: The application of methods, procedures, tests and other evaluations, in addition to monitoring, to determine compliance with the specifications laid down in the HACCP plan and the effectiveness of the HACCP-based Food Safety System.5 HACCP SYSTEM REQUIREMENTS5.1 Management responsibilityThe food business operator is responsible for the safety (and suitability) of the produced food.Therefor, the food business operator shall include the policy with respect to food safety in the policy of the organisation. The food business operator has ultimate responsibility for the policy of the organisation and shall document, support and communicate this policy. Periodically, the Food business operator shall verify the implementation of the policy and review the outcome.The HACCP system enables the food business operator to demonstrate his commitment and his responsibility with respect to the supply of safe products. The HACCP system ensures that all required activities are effectively defined, implemented and maintained.5.1.1 PolicyThe food business operator shall define and document (in writing) the policy of the organisation with regards to food safety. It will demonstrate the commitment of the organisation to safe food.The policy shall demonstrate that the organisation is fully aware of its position in the food chain. It will reflect the “farm-to-fork” approach, starting with the purchase and acceptance of raw materials.The policy shall be focused on the safety of foodstuffs and shall respond to the expectations and needs of its customers and consumers.The policy shall include concrete objectives 6 (proposed actions) to ensure and improve food safety for the period under consideration.The food business operator shall ensure that the policy is understood, implemented and maintained at all levels in the organisation.5.1.2 Scope of the HACCP systemThe food business operator shall define the extent (the scope) of the HACCP system. The scope shall comprise that part of the food chain and those activities of the food business for which the food operator is responsible and can be held liable: •The part of the food chain for which the food business operator is responsible begins where the responsibility of the suppliers of raw materials and ingredients ends; the responsibility of the food business operator ends where another food business in the food chain takes over the responsibility. The scope shall therefore conform with purchase and sales contracts;•All locations and process lines where food is manufactured and/or stored by the food business shall be properly indicated and be available for assessment;•All products which are supplied to the market by the food business, whether processed or handled, shall be properly specified;•All subcontracted activities (outsourced services, like packaging, storage, transport) shall be properly dealt with.For practical reasons the total product assortment may be clustered into product groups. However it is important that:6SMART objectives are Specific, Measurable, Acceptable, Realistic objectives, defined in Time.•Specific differences between individual end products have been critically evaluated;•Manufacturing and storage conditions are comparable;•Important aspects for food safety are not overlooked.A key principle is that no part of the operation of the food business can be excluded from the scope of the HACCP system; all activities must be available for assessment.5.1.3 Tasks, responsibilities and authoritiesThe food business operator shall provide appropriate documentation with respect to the tasks, responsibilities and authorities of food business operator’s employees who are in positions which involve handling food and / or controlling and ensuring the safety and suitability of the food.An organisation chart and the organisation’s reporting stru cture shall be documented.5.1.4 HACCP team(s)The food business operator shall assemble a HACCP team (or various HACCP teams if so required).The HACCP team shall develop, implement and maintain the HACCP system.The organisation shall demonstrate that the members of the HACCP team have the knowledge, expertise and different disciplines available which are required to develop, implement and maintain a HACCP system covering the total scope of the HACCP system.Minimum qualification criteria, including required expertise, shall be defined and documented for all members of the HACCP team. In addition, the assignment (including tasks, responsibilities and authorities) shall be documented for the team members.Whenever more than one HACCP team has been assembled, a co-ordinator shall be appointed to co-ordinate the development, implementation and maintenance of the HACCP system.5.1.5 ResourcesThe food business operator shall examine the requests and provide, in a timely manner, all the resources needed by the HACCP team(s) to develop, implement and maintain the HACCP system.When corrective actions, verification procedures or customers indicate that operational improvements are necessary, the food business operator shall examine the issues and provide appropriate resources to ensure food safety.5.1.6 Management ReviewThe food business operator shall review the HACCP system at planned intervals, of no more than 12 months, to ensure continuing suitability, adequacy and effectiveness. The review shall evaluate the need for changes to the HACCP system, including product safety, policy and objectives. The review shall provide evidence of the commitment to improve the HACCP system and its performance.5.2 Product Information5.2.1 Product CharacteristicsEach product (or a group of similar products: see 5.1.2) shall be fully specified and documented, including its sensitivity to and potential for safety risks.This description of the safety of the product shall encompass the food chain, ranging from raw materials used to the distribution of the finished products.The traceability of the raw materials up to and including final supply shall be described.An extensive specification of the end products is required to ensure a comprehensive assessment of the food safety procedures. This specification shall clearly define the following product characteristics:• A general product description;•Raw materials and ingredients used (composition);•General product specifications such as appearance, weight, etc.;•Specific product specifications such as chemical, microbiological and physical characteristics;•Specific requirements such as appropriate legislation, customer requirements;•General control of (chemical, microbiological and physical) safety;•Packaging, storage conditions, labelling (shelf life, product identification);•Identification of potential mishandling of the product.5.2.2 Intended useThe intended use of the product (or product group) shall be identified and documented since it has a direct influence on the required product characteristics. For instance, the product may require:•Additional preparation methods (e.g. heating) before consumption, and/or•Cooling and storage at specific temperatures, and/or•An indication of the ultimate day of use, especially after breaking the packaging, and/or•The product may be intended for use by specific (vulnerable) groups of the population, such as babies and children, pregnant women, elderly people, allergenic or sick people.The intended use of the product shall be continually reviewed; relevant legislation and regulations shall be documented. When necessary, the product characteristics and manufacturing processes may need to be adapted to conform with special legislation. Information on the label, including directions for use, may also need to be adapted. These changes shall be recorded.If mishandling or misuse of the product can result in unsafe products the products shall bear appropriate information to ensure that adequate and accessible information is available to the next persons in the food chain to enable them to handle, store, process, prepare and display the product safely and correctly. It shall be easy to identify the lot or batch when recall is required.The food business operator shall demonstrate that it has evaluated whether the intended use or misuse should include Critical Control Points such as storage conditions and preparation before consumption.。
食品质量安全控制技术的发展
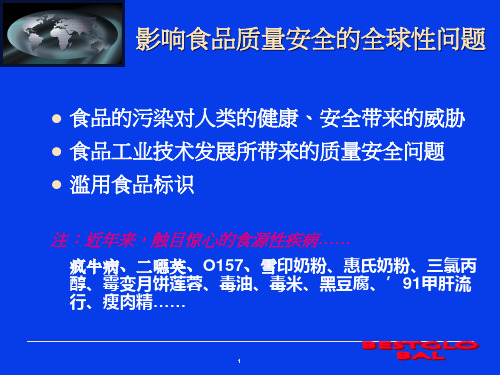
Origins of HACCP 起源
Pioneered in the 1960’s for the US space program 起源于60年 代的美国太空计划
Adopted widely by many food processors and governments afterwards 随后被食品界和政府 机构采用
和储存污染 Sales related 销售污染
32
Characteristic of Hazards 危害的性质
Biological Hazards生物性: Bacteria细菌 Viruses病毒 Protozoa (parasites)原生动物(寄生虫)
33
Characteristic of Hazards 危害的性质continue
Establish verification procedures 建立验证程序
Establish a record keeping system 建立文件保存体系
17
HACCP Control Model HACCP循环控制模式
V
HA
CCP
CL
M
CA
R
WH FW
18
How to establish HACCP
Chemical Hazards化学性: Natural - Natural toxins etc. 天然 - 天然毒素等 Intentionally added - Food additives 有意添加的 - 食品添加剂 Unintentionally added - Food contaminants 无意添加的 - 食品污染物
Identify critical control points (CCP) 确定关键控制点(步骤七)
- 1、下载文档前请自行甄别文档内容的完整性,平台不提供额外的编辑、内容补充、找答案等附加服务。
- 2、"仅部分预览"的文档,不可在线预览部分如存在完整性等问题,可反馈申请退款(可完整预览的文档不适用该条件!)。
- 3、如文档侵犯您的权益,请联系客服反馈,我们会尽快为您处理(人工客服工作时间:9:00-18:30)。
Barriers of HACCP team members to guideline adherenceMa.Patricia V.Azanza *,Myrna Benita V.Zamora-LunaDepartment of Food Science and Nutrition,College of Home Economics,University of the Philippines,Diliman,Quezon City 1101,PhilippinesReceived 29September 2003;received in revised form 9October 2003;accepted 9October 2003AbstractA cognitive-behavior model to evaluate barriers to HACCP guideline adherence by HACCP team members was developed.It was based on the theory of experiential learning where knowledge,attitude and behavior must be sequentially overcome.Twenty-seven HACCP team members from four food processors participated to assess barriers to guideline adherence.Non-awareness to HACCP guideline was a major barrier.The national government was recognized as key source of HACCP -mitment to adopt HACCP guideline was established.Also,the need for food processor management to understand that teams must be multidisciplinary to ensure guideline adherence has been established.Ó2004Elsevier Ltd.All rights reserved.Keywords:HACCP guideline;Barrier model;Adherence1.IntroductionHazard analysis critical control point (HACCP)is a food safety tool that is more recently advocated by international and national regulatory institutions as either voluntary or mandatory prescription to food processing (Gilling,Taylor,Kane,&Taylor,2001;Suwanrangsi,2000;Taylor,2001;Torres,2000;Wallace &Williams,2001).These recent advocacy efforts to propel HACCP implementation are now in fact over-whelmingly evident in most food safety government programs.Despite the orchestrated efforts of inter-national institutions like Codex Alimentarius Commis-sion (CAC)to drum up HACCP awareness and compliance,only food industries in more developed countries are currently apt to immediately implement this food safety tool.The Philippine government,as signatory of the General Agreement on Tariffs and Trade Uruguay Round Final Act,and now as member nation of World Trade Organization,abides by the provisions of the Treaty including the Agreement on the Application of Sanitary and Phytosanitary Measures (SCRA,1997).Under this Agreement,the Philippine government isencouraged to harmonize its national food safety mea-sures with international standards,guidelines and rec-ommendations developed by international regulatory agencies,primarily the CAC.The HACCP guideline has been recommended by CAC as part of its revised guidelines on the General Principles of Food Hygiene as early as 1993(Fogden,2000).In a memorandum from the Office of the President of the Philippines,Mal-aca ~nang,Philippines to the secretaries of various con-cerned food regulatory agencies and its affiliates,a directive was issued pertaining to the accreditation program for food processors that stipulates that Good Manufacturing Practices (GMP)and HACCP be the underlying systems for processing of safe foods for ex-port (Ramos,1997).Although large-scale food processing establishments have been identified as key players in Philippine econ-omy,micro-to small-scale establishments still have a significant contribution to the viability of the food economy sector.The smaller food industries in this country are numerous as a result of chronic national economic problems,which is further aggravated by the more recent political turmoils (Marfil &Pablo,2002;Pablo,Javellana,&Marfil,2002).Prompting the underdeveloped food industry sectors towards HACCP guideline awareness,implementation and adherence tends to be more difficult because these industries are reported to be ill-equipped with the required industry intrinsic support system to attain it (Taylor,2001).*Corresponding author.Tel.:+632-920-5301;fax:+632-926-1449/926-2813/920-5473/920-2091.E-mail address:ma_patricia.azanza@.ph (Ma.P.V.Azanza).0956-7135/$-see front matter Ó2004Elsevier Ltd.All rights reserved.doi:10.1016/j.foodcont.2003.10.009Food Control 16(2005)15–22/locate/foodcontLikewise,these less developed industries are less likely to invest in HACCP knowledge acquisition.Problems in guideline adherence by underdeveloped food industries have been reported to be partly miti-gated by understanding in-depth of the specific barriers to compliance(Cabana et al.,1999;Gilling et al.,2001). Utilizing the behavioral adherence model for technical barrier assessment for specific food industry has been reported previously to facilitate identification of appropriate intervention strategies for HACCP adher-ence(Gilling et al.,2001).The HACCP plan implementation is generally vested upon the efforts of a team in an establishment rather than on the commitment of a single individual.This study for thefirst time,evaluated HACCP guideline adherence barriers specific to HACCP team members of micro-to small-scale beverage and meat processors. Baseline information established in this study could facilitate HACCP implementation in the local micro-to small-scale food processing industries thru the under-standing of barriers to guideline adherence.2.Materials and methods2.1.Cognitive-behavior barrier model to HACCP guide-line adherenceThe study developed a cognitive-behavior barrier model to HACCP guideline adherence for individuals comprising the HACCP team(Fig.1).The model was established by consolidating various concepts from similar models used in assessing physician adherence to medical guideline(Cabana et al.,1999;Pathman,Kon-rad,Freed,Freeman,&Koch,1996)and food industry adherence to HACCP guideline(Gilling et al.,2001).16Ma.P.V.Azanza,M.B.V.Zamora-Luna/Food Control16(2005)15–22Briefly,the consolidated model divided the major bar-rier categories into knowledge,attitude and behavior. Subcategories of these general barriers included aware-ness,familiarity and comprehension for knowledge while the subcategories for attitude major barrier com-prised of agreement and commitment.Adoption and adherence were the subcategories for the last major barrier,behavior.The study further classified each subcategory into themes of barriers as industry intrinsic or extrinsic factors.The research proponents formulated working definitions included in the consolidated model through a series of brainstorming sessions.2.2.Survey of respondentsThe survey to assess the barriers to HACCP guideline adherence specific to HACCP team members of micro-and small-scale food processors was conducted as part of2research projects aimed to develop HACCP plans for these industries.Participating small-scale food pro-cessing industries were defined based on the amended Philippine Magna Carta for Small Scale Enterprises (Republic Act8289).Micro-scale industries were busi-ness establishments having a capital outlay of6US $30,000(PhP1.5M),excluding the cost of land where the plant and equipment are located,whereas small-scale industries have>US$30,0006$300,000(6PhP15 M).The respondents of the survey were recruited from HACCP team members of participating industries in the two earlier mentioned studies.Communications were made to HACCP team mem-bers from small-scale meat processors from Pampanga (n¼16)and micro-to small-scale beverage processors of the National Capital Region and Region4(n¼48), Philippines to recruit survey respondents.The names of government-registered beverage and meat processors were obtained from the Department of Trade and Industry,Bureau of Food and Drug,and Local Gov-ernment Units.Additional names of food processors were also obtained from professional organizations including Pampanga Association of Meat Processors and Foundation of Food Science and Technology,Inc. The names of unregistered processors,referred by other processors and vendors encountered in the test areas were also included in the lists.The modes of commu-nication used to recruit participants were through the following,used either singly or in combination:elec-tronic and ordinary mails,field visits,or telephone calls. Amongst those who responded positively to the recruitment phase of the survey were two HACCP team members of processors per test industry.2.3.The HACCP technical barrier surveyA questionnaire was designed based on the developed cognitive-behavior barrier model to HACCP principle adherence(Fig.1)for members of the HACCP teams. Briefly,it included questions on demographics and, levels of knowledge,attitude and behavior barriers of respondents to HACCP guideline.The survey tool in-cluded some questions with multiple choices for the answers and other open-ended queries(Table1).For awareness and familiarity of HACCP guideline under the knowledge major barrier,the interrogative pro-nouns:when,from whom and where were used to query about pertinent HACCP knowledge information. Questions on accessibility and adequacy of HACCP information were likewise included under the knowl-edge barrier category.The role of external sources of HACCP information including government,media, consumer,market and technical consultants in the adoption of the guideline were likewise asked.The capability of individual members to sustain guideline implementation was placed under the adherence major barrier.Follow-up questions were used to fully elucidate details of some unclear responses.The HACCP team members were individually asked to respond to the questionnaire using the face-to-face narrative interview technique.The interview was con-ducted by the research proponents who read each of the questions aloud during the interview.Respondents were given adequate time to answer each query in writing. Questions were translated to the appropriate regional dialects to which survey respondents were more familiar with when necessary.Results of the study were tabu-lated.Frequency and percentage distributions were calculated(Gatchalian,1989).3.Results and discussion3.1.Cognitive-behavior barrier model to HACCP guide-line adherenceThe developed cognitive-behavior barrier model to HACCP guideline adherence in the study(Fig.1)was modified from similar guideline adherence models gen-erated by Pathman et al.(1996)and Cabana et al.(1999) for medical guidelines,and Gilling et al.(2001)for HACCP guideline.The ladderized barrier concept for evaluation of knowledge,attitude and behavior in guideline adherence as presented by both Cabana et al. (1999)and Gilling et al.(2001)was adopted in this new developed model as general barrier categories.The generated working definitions for the general barrier categories included:knowledge as a body of acquired facts;attitude as mental reaction to knowledge;and behavior as the action taken as a result of knowledge acquisition and attitude development.It was hypothesized in the developed barrier model for HACCP guidance adherence that the HACCP team member designate mustfirst become aware,and beMa.P.V.Azanza,M.B.V.Zamora-Luna/Food Control16(2005)15–2217exposed to the guideline at least more than once before comprehension is attained.Having full understanding of the principles,the team member was assumed to develop the proper attitude which may subsequently lead to agreement and commitment.Such attitude was expected to cause a change in behavior through adoption and finally adherence to the guideline.However,it was ex-pected that HACCP knowledge acquisition alone could not ensure HACCP guideline compliance.Gilling et al. (2001)reported that right attitude should be supported by the appropriate industry intrinsic and extrinsic environmental factors to facilitate HACCP compliance (Fig.1).3.2.Profile of HACCP team members respondentsThe HACCP team member respondents of the study belonged to micro-to small-scale industries(Table2).It has been previously reported that micro-to small-scale food industries are generally not in the position to implement the HACCP guideline due to their small company size,lack of technical expertise and training, rapid turnover of trained personnel,and lack of appropriate resources support prerequisites to HACCP guideline adherence(Panisello&Quantick,2001;Tay-lor,2001;Torres,2000).The CAC and World Health Organization(WHO)fortunately,in its effort to address the unique needs of the small and less developed food processing industries,sponsored the development of fundamental strategies for implementing HACCP in these level of industries(WHO,1999).However,the formal schemes to facilitate the actual implementation of the strategies for underdeveloped food businesses are yet to be fully realized.The survey respondents belonged to HACCP teams comprising of4–10members representing various work divisions in their companies(Table2).Ideally,HACCP team members should be multidisciplinary consisting of individuals who have the appropriate technical skills and expertise about the product and its processes(NAC-Table1Details of survey tool used to determine technical barriers of HACCP team members to HACCP guideline adherenceBarrier Subcategories Survey itemsKnowledge AwarenessA body of acquired facts First heard or read about the guideline When have youfirst heard or read about theHACCP guideline?•Now•Last6months•Last year•Last2years•Last3years or moreFamiliarityDenotes fuller knowledge based on continues awareness but still without complete under-standing of the essence of the guideline as they were originally designed Are you able to use the term HACCP and its related concepts in casual discussions?If yes, cite specific situations.ComprehensionDenotes familiarity with the guideline with full understanding,proximate to the essence of the concept as it was originally designed What is the impact of the HACCP guideline implementable to the operations of your company?Attitude AgreementMental reaction to knowledge Belief in the HACCP guideline,in general orsome parts of it To what extent do you agree with the HACCP guideline?•Full/in general•Partial•Not at allCommitmentPledge to adopt the guideline Are you willing to pledge to adopt theHACCP guideline in your line of work? Behavior AdoptionAction taken as a result of knowledge acquisition and attitude developmentPutting the guideline into action,change inpracticeAre you willing to put the HACCP guidelineinto action?•Yes•NoAdherenceSustained adoption Do you think as a member of your company,you can sustain the implementation of theHACCP guideline in your line of work?Briefly explain your answer18Ma.P.V.Azanza,M.B.V.Zamora-Luna/Food Control16(2005)15–22MCF,1999).Unfortunately,majority of the members of the HACCP teams from the two participating meat processors essentially came from similar work sectors. The HACCP team member respondents from1meat processor were all quality control officers,while the team from the other meat processor was constituted with mostly line workers.The apparent inappropriate con-stitution of the meat HACCP teams may have been mainly based on the decision of their respective man-agements.The organizational set-up of the micro-and small-scale processing industries are not complex and major decisions are traditionally the unilateral respon-sibility of the management rather than any other sector of the company.The sectoral skewdness of the group composition for the HACCP teams for meat processors lends itself to a limited perspective and lack of technical expertise to all significant aspects of the product and its processes that might be pertinent to the HACCP plans.The memberships of the beverage HACCP teams were more appropriately assembled as multidisciplinary groups.The respondents from HACCP teams of the beverage industries were from various disciplines including personnel from:the research and develop-ment,production,quality control and,sales and mar-keting.The multidisciplinary membership of the beverage HACCP teams might not be again based on the critical view of the responsible management on the appropriate constitution of the teams but rather more as a consequence of the diminutive nature of the company. Choice of the HACCP team members was quite limited in the participating beverage processors considering the very small employment numbers which were composed of5–18workers only(Table2).The educational background of HACCP team mem-bers was quite diverse.There were those who completed tertiary education.Others,however,were only able to have vocational training and some primary education. For those teams consisting of mostly undereducated members,technical difficulties in acquiring knowledge and transposing these into implementable activities might be encountered.The apparent educational inad-equacy of some of the members of the teams might beTable2Profile of HACCP team member survey respondents coming from meat and beverage industriesFood industry profile Teammember(n)Category distribution(%)aGender Position in theestablishmentHighest educational levelMeat industry1.Meat processor small scale,30y operational,100workers,2shifts/d(8h/shift),2tnitrite-cured meat production/dFemale90Research andDevelopmentOfficer10Tertiary level8010Male10Quality controlofficer80Food Technology andNutritionManagementEducationComputer Science andEngineeringDraftsman10Secondary level10Vocational(i.e.Secretarial)102.Meat processor small scale,operational for30yrs,employed100workers,2shifts/d(8h/shift),2production/d t nitrite-cured meatFemale50Supervisor12Secondary level80 8Male50Line Worker88VocationalComputer TechnologySecretarial20Beverage industry1.Beverage processor micro-scale,12y operational,18workers,2200cup production/d(300ml cup),500bottle production/d(500ml bottle) young coconut juiceFemale50Owner25Masters level(i.e.Child Psychology)254Male50Supervisor75Tertiary levelBusiness AdministrationHotel and RestaurantManagement752.Beverage processor b micro-scale,10y operational,5workers,300 cup production/d young coconut juice(300ml cup)5Female60Supervisor20Primary level60 Male40Line Worker80Secondary level40n,number of HACCP team members per establishment.a Percent values relative to number of HACCP team members per establishment.b Cooperative-base.Ma.P.V.Azanza,M.B.V.Zamora-Luna/Food Control16(2005)15–2219further aggravated by the fact that small companies may have limited access to HACCP information and provide less resources for skill development for them(Taylor, 2001).The gender profile of the HACCP team member designates indicated inclusion of50–90%female.In a matriarchal society such as the Philippines,females tend to dominate food management concerns(Fernandez& Alegre,1988).The female-skewdness of the HACCP team composition is,therefore,expected since assurance of food safety is usually associated with women in the country.3.3.Knowledge levelThe knowledge-,attitude-and behavior-related bar-riers of HACCP team members of micro-to small-scale meat and beverage processors are shown in Table3. Results showed that most of the respondents were not aware of HACCP principles and tasks.Familiarity was the highest knowledge level achieved among the respondents.This current HACCP knowledge level of the respondents may be due in part to the inadequate and inappropriate information dissemination systems available within the country.Based on a more general industry perspective,Gilling et al.(2001)similarly identified lack of awareness of the HACCP guideline as one of the technical barriers restricting HACCP guideline adherence in U.K.food processing establishments.However,this was true only for a small proportion of food businesses in the UK. There may be a disparity in HACCP awareness levels of food processors in the Philippines and UK.which could be attributed to the more widespread and comprehen-sive HACCP information dissemination efforts exerted by the better developed country(Gilling et al.,2001; Taylor,2001).Details of HACCP knowledge-based barriers identi-fied by HACCP team member survey respondents are presented in Table4.Since majority of the respondents did not go beyond the familiarity level,they were unable to identify intrinsic and extrinsic factors influencing knowledge barriers(Fig.1).For the few who were aware and already familiar with the HACCP guideline,time and accessibility of HACCP information were of prime importance to attain full comprehension that could eventually lead to a change in behavior.Fortunately,the Philippine national government was the main external source of information although lim-ited through the conduct of seminars/workshops by concerned agencies.The National Meat and Inspection Commission,Philippines and University of the Philip-pines Diliman were the government agencies specified by respondents to provide HACCP information.According to the respondents who graduated from tertiary education in food technology and food science relatedfields,academic institutions offering undergrad-uate degree in food technology programs now covered HACCP in their curricula.Majority of the respondents who had some level of HACCP knowledge still per-ceived that HACCP information from available sources were limited.Even if the information were made avail-able HACCP team members still felt that they were not generally given adequate time to fully comprehend it.In the Philippines,HACCP information dissemination systems usually comprised of seminars/workshops thatTable3Barriers to HACCP principle adherence by HACCP team members from micro-to small-scale meat and beverage processing industries Barrier Subcategories Percentage distribution(%)Meat industry Beverage industryTeam1 (n¼10)Team2(n¼8)Team1(n¼4)Team2(n¼5)Knowledge Non-awareness401002580 No previous exposure to HACCP principlesAwareness400500Once heard or readFamiliarity2002520>1exposure but without full understandingAttitude Agreement3002520 Full-belief in HACCP principlesCommitment4002520Pledge to adoptNo response301005060Lack of knowledge of HACCP principlesBehavior No responseLack of knowledge of HACCP principles100100100100 n,number of team members per establishment.20Ma.P.V.Azanza,M.B.V.Zamora-Luna/Food Control16(2005)15–22are characteristically providing copious amount of information for short periods of time.Evaluations of the efficacy of such HACCP seminar/workshops,however, are rarely done.3.4.Attitude and behavior levelsIn terms of attitude and behavior-related barriers, this study considers non-awareness to be translated to the inability of the team members to develop the proper attitude toward the HACCP guideline.In fact,inade-quate knowledge level is the reason for non-adoption of the guideline.To the survey respondents who only reached knowledge levels of awareness and familiarity, agreement and commitment were fortunately already expressed.Ideally,HACCP team members should have attained full comprehension to develop the proper atti-tude towards the guideline.Theoretically,the cognitive-behavior model devel-oped in this study should require that each member must have full knowledge of what the HACCP guideline is all about,develop an action concept of what appro-priate behavior would lead to the efficient functioning of the HACCP plan,develop positive attitudes towards HACCP procedures and a belief that the team is capable of implementing plans(Johnson&Johnson,1987).This model follows the basic concept of experiential learning where awareness is a requisite for expansion of skill performance(Bandura,1986;Johnson&Johnson,1987; Stage&Associates,1993).The HACCP learner there-fore,must comprehend the guideline to be able to de-velop positive attitude and behavior towards it.The application of the cognitive-behavior barrier model for HACCP guideline adherence could still be further studied particularly for HACCP team mem-bers who belong to establishments,which are already HACCP parison of results generated in this study which,is based on responses of HACCP team members from teams which are still in its early stage of HACCP plan implementation,must be compared with the results obtained from responses of those who be-longed to HACCP compliant processors.Only at this point could the model be fully evaluated and appreciated.4.Summary and recommendationsThe cognitive-behavior barrier model to HACCP guideline adherence designed in the study presents the sequence of barriers that must be overcome by HACCP team member designates tofinally reach a point con-ducive to HACCP adherence.The model starts withTable4Knowledge-based barriers to HACCP principle adherence identified by HACCP team members from micro-small-scale meat and beverage processing industriesKnowledge acquisition barriers Percentage distribution(%)Meat industry Beverage industryTeam1 (n¼10)Team2(n¼8)Team1(n¼4)Team2(n¼5)Sources of HACCP information are obtained from......Industry intrinsic sources...Co-worker600500...No response4010050100 ...Industry extrinsic sources like...Seminar/workshop conducted by...ernment4005020...Academe100100...No response501005080 Accessibility of HACCP information from identified source is......Easy00020...Not easy900750...No response101002580 Adequacy of HACCP information from identified source is......Satisfactory100250...Not satisfactory8007520...No response10100080 Adequacy of time to comprehend HACCP information from identifiedsources is......Satisfactory100020...Not satisfactory800750...No response101002580n,number of team members per establishment;total…100%due to multiple answers.Ma.P.V.Azanza,M.B.V.Zamora-Luna/Food Control16(2005)15–2221knowledge acquisition followed by proper attitude development leading to eventual behavioral change targeting adherence.The model tries to provide niches for possible identifiable barriers within the major cate-gories cited.The study was conducted to analyze barriers that impede HACCP guideline adherence of27HACCP team members from four micro-to small-scale Philip-pine food processors.The study established that non-awareness of respondents of the HACCP guidelines was the major barrier to adherence.Currently the major external source of HACCP information for the team members is the national government mainly through seminars/workshops.Respondents showed an optimistic attitude toward HACCP guideline implementation de-spite their low HACCP knowledge competence level.It is evident that the management responsible for the HACCP team membership needs to fully appreciate the fundamental concept of the group to be multidisciplin-ary.The respondents from HACCP teams were found to be multidisciplinary have been formed only accidentally since the processors involved had limited employees and had to include everyone to the team.More intensive knowledge-based intervention strate-gies specifically designed for HACCP team members must be formulated and implemented as an initial step to achieve HACCP guideline adherence.Furthermore,gov-ernment and other sources of HACCP information must continue to advocate HACCP adherence in Philippine food industries.Additional efforts on a national scale must be exerted to make HACCP information more accessible. The usefulness of the developed HACCP guideline cog-nitive-behavior barrier model could still be further stud-ied.Results from this study should be used to better educate HACCP instructors and industry implementors. ReferencesBandura,A.(1986).A social foundation of thought and action:A social cognitive theory.Englewood Cliffs,NJ:Prentice-Hall.Cabana,M.D.,Rand,C.S.,Powe,N.R.,Wu,A.W.,Wilson,M.H., Abboud,P.A.C.,&Rubin,H.R.(1999).Why don’t physicians follow clinical practice guidelines?A framework for improvement?Journal of the American Medical Association,282(15),1458–1465.Fernandez,D.G.,&Alegre,E.N.(1988).Sarap:Essays on Philippine food.Manila,Philippines:Mr.and Mrs.Publishing Company. Fogden,M.(2000).The regulatory context in the EU.In M.Brown (Ed.),HACCP in the meat industry.England:Woodhead Publish-ing Limited.Gatchalian,M.(1989).Sensory Evaluation Methods for Quality Assessment and Development.Quezon City,Philippines:University of the Philippines College of Home Economics.Gilling,S.J.,Taylor, E. A.,Kane,K.,&Taylor,J.Z.(2001).Successful hazards analysis critical control point implementation in the United Kingdom:understanding the barriers through the use of a behavioral adherence model.Journal of Food Protection, 64(5),710–715.Johnson,D.W.,&Johnson,F.P.(1987).Joining together group theory and group skills.Englewoods Cliffs,NJ:Prentice-Hall,Inc.Marfil,M.P.,&Pablo,C.(2002).1700troops coming,big number ‘‘normal’’for Balikatan02–2set next month.Philippine Daily Inquirer,17(102),A1–A18.NACMCF(National Advisory Committee on Microbiological Crite-ria for Foods)(1999).Hazard analysis and critical control point principles and application guidelines.In K.E.Stevenson,&D.T.Bernard(Eds.),HACCP a systematic approach to food safety(3rd ed.).Washington,DC:The Food Processors Institute.Pablo,C.,Javellana,J.L.,&Marfil,M.P.(2002).And300more going to Basilan.Philippine Daily Inquirer,17(102),A1–A18. Panisello,P.J.,&Quantick,P.C.(2001).Technical barriers to hazard analysis critical control point(HACCP).Food Control,12,165–173.Pathman, D. E.,Konrad,T.R.,Freed,G.L.,Freeman,V. A., &Koch,G.G.(1996).The awareness-to-adherence model of steps to clinical guideline compliance.Medical Care,34(9),873–889.Ramos,F.V.R.(1997).Memorandum from the President(May27, 1997):Accreditation Program for Food Exporters(pp.1–5).Office of the President of the Philippines,Malaca~n ang,Philippines. Stage,F.K.,&Associates(1993).Linking theory to practice case studies from working with college students.Accelerated Devt.,Inc Muncie,Indiana.SCRA(Supreme Court Reports Annotated)(1997).Ta~n ada vs.Angara(Vol.272,pp.18,40–41).Quezon City,Philippines:LPB, Inc.Suwanrangsi,S.(2000).HACCP implementation in the Thaifisheries industry.Food Control,11,377–382.Taylor,E.(2001).HACCP in small companies:benefit or burden.Food Control,12,217–222.Torres,D.H.(2000).Role of government in HACCP audit:a Cuban perspective.Food Control,11,365–369.Wallace, C.,&Williams,T.(2001).Pre-requisites:a help or a hindrance to HACCP.Food Control,12,234–240.WHO(World Health Organization)(1999).Strategies for implement-ing HACCP in small and/or less developed businesses.WHO Document WHO/SDE/PHE/FS/99.7.Geneva:WHO.22Ma.P.V.Azanza,M.B.V.Zamora-Luna/Food Control16(2005)15–22。