钢制压力容器焊接工艺评定、焊接规
钢制压力容器焊接工艺标准评定
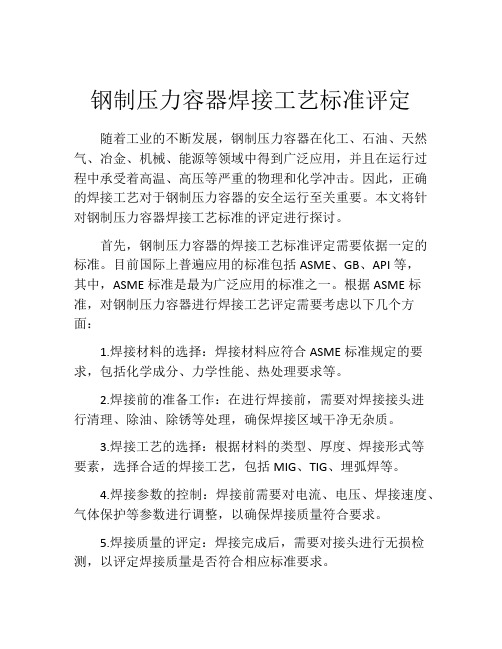
钢制压力容器焊接工艺标准评定随着工业的不断发展,钢制压力容器在化工、石油、天然气、冶金、机械、能源等领域中得到广泛应用,并且在运行过程中承受着高温、高压等严重的物理和化学冲击。
因此,正确的焊接工艺对于钢制压力容器的安全运行至关重要。
本文将针对钢制压力容器焊接工艺标准的评定进行探讨。
首先,钢制压力容器的焊接工艺标准评定需要依据一定的标准。
目前国际上普遍应用的标准包括ASME、GB、API等,其中,ASME标准是最为广泛应用的标准之一。
根据ASME标准,对钢制压力容器进行焊接工艺评定需要考虑以下几个方面:1.焊接材料的选择:焊接材料应符合ASME标准规定的要求,包括化学成分、力学性能、热处理要求等。
2.焊接前的准备工作:在进行焊接前,需要对焊接接头进行清理、除油、除锈等处理,确保焊接区域干净无杂质。
3.焊接工艺的选择:根据材料的类型、厚度、焊接形式等要素,选择合适的焊接工艺,包括MIG、TIG、埋弧焊等。
4.焊接参数的控制:焊接前需要对电流、电压、焊接速度、气体保护等参数进行调整,以确保焊接质量符合要求。
5.焊接质量的评定:焊接完成后,需要对接头进行无损检测,以评定焊接质量是否符合相应标准要求。
同时,钢制压力容器的焊接工艺标准评定还需要考虑到一系列的安全因素。
例如,焊接工艺应避免出现裂纹、变形等缺陷,避免出现焊接残留应力等因素。
此外,还需要考虑焊接过程中的防护措施,以确保焊接作业人员的人身安全。
除了以上因素,钢制压力容器焊接工艺标准评定还需要考虑到国家、行业和企业的具体要求。
不同行业、不同企业对于钢制压力容器的要求也不尽相同,因此需要根据实际情况进行相应的评估和制定相应的标准。
在评定钢制压力容器焊接工艺标准时,还需要考虑到质量控制的问题。
质量控制不仅包括焊接过程的控制,还包括焊接后的品管检验等一系列的工作。
这就需要对相应的工艺流程进行质量管理,以确保焊接工艺标准的质量符合相应的标准。
总之,钢制压力容器作为重要设备,在焊接工艺标准评定方面,需要综合考虑材料、工艺、安全和质量控制等一系列的因素。
钢制压力容器焊接通用规程

HJ350-H08MnMoA
HJ431-H08MnMoA
低碳钢与耐热型低合金钢相焊
Fe-1-1与Fe-4、Fe-5A、Fe-5B-1相焊
E4315
J427
F4A0-H08A
HJ431-H08A
HJ350-H08A
HJ101-H08A
强度型低合金钢与耐热型低合金钢相焊
Fe-1-2与Fe-4
12Cr2Mo
12Cr2Mo1
12Cr2MoG
12Cr2Mo1R
E6015-B3
R407
1Cr5Mo
E5MoV-15
R507
06Cr19Ni10
F308-H08Cr21Ni10
SJ601-H08Cr21Ni10
HJ260-H08Cr21Ni10
H08Cr21Ni10
06Cr18Ni11Ti
F347-H08Cr20
J507RH
15MnNiDR
E5015-G
W607
Q370R
E5016-G
E5015-G
J556RH
J557
20MnMo
E5015
E5015-G
J507
J557
20MnMoD
E5016-G
E5015-G
E5516-G
J506RH
J507RH
J556RH
13MnNiMoR
18MnMoNbR
20MnMoNb
HJ260-H08Cr19Ni14Mo3
H08Cr19Ni14Mo3
022Cr19Ni10
E308L-16
A002
F308L-H03Cr21
Ni10
SJ601-H03Cr21Ni10
钢制压力容器焊接工艺规范
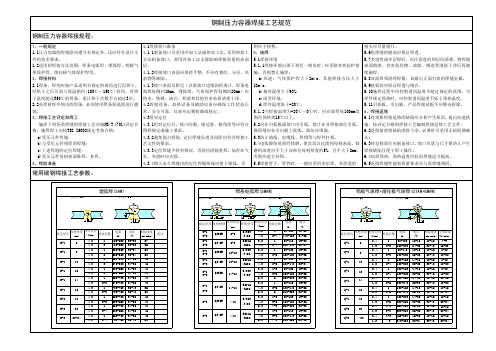
5.6角焊缝的根部应保证焊透。
5.7多道焊或多层焊时,应注意道间和层间清理,将焊缝表面熔渣、有害氧化物、油脂、锈迹等清除干净后再继续施焊。
5.8双面焊须清理焊根,显露出正面打底的焊缝金属。
5.9接弧处应保证焊透与熔合。
5.10施焊过程中应控制道间温度不超过规定的范围。当焊件规定预热时,应控制道间温度不低于预热温度。
5.11引弧板、引出板、产品焊接试板不应锤击拆除。
6、焊接返修
6.1对需要焊接返修的缺陷应分析产生原因,提出改进措施,按评定合格的焊接工艺编制焊接返修工艺文件。
6.2返修前需将缺陷清除干净,必要时可采用无损检测确认。
6.3待返修部位应制备坡口,坡口形状与尺寸要防止产生焊接缺陷且便于焊工操作。
6.4如需预热,预热温度应较原焊缝适当提高。
4.3.4熔入永久焊缝内的定位焊缝两端应便于接弧,否
则应予修整。
5、施焊
5.1焊接环境
5.1.1焊接环境出现下列任一情况时,应采取有效防护措施,否则禁止施焊:
a)风速:气体保护焊大于2m/s,其他焊接方法大于10m/s;
b)相对湿度大于90%;
c)雨雪环境;
d)焊件温度低于-20℃。
5.1.2当焊接温度为-20℃~0℃时,应在始焊处100mm范围内预热到15℃以上。
4.2焊接设备、加热设备及辅助设备应确保工作状态正常,安全可靠,仪表应定期校准或检定。
4.3组对定位
4.3.1组对定位后,坡口间隙、错边量、棱角度等应符合图样规定或施工要求。
4.3.2避免强力组装,定位焊缝长度及间距应符合焊接工艺文件的要求。
4.3.3定位焊缝不得有裂纹,否则应清除重焊。如存在气孔、夹渣时应去除。
6.5返修焊缝性能和质量要求应与原焊缝相同。
焊接工艺评定规程

3.3 已进行过“评定”,但改变第 3.3.1 条—第 3.3.1.3 条中任何一个重要参数的
类别或超出规定的适用范围时,均应重新进行“评定”。
3.3.1 钢材
3.3.1.1 钢材的分类见表 1
表1
类别
碳 素 钢
低 合 金 钢
马氏体 钢、铁 素体不 锈钢 奥氏体 不锈 钢、双
代号 Ⅰ
Ⅱ Ⅲ
钢材的分类
HP365 L360
16MnR
15CrMoR
16MnD
L415 15MnNbR 15CrMoG
16MnDR
L450
15MnV
14Cr1Mo
15MnNiDR
L485
15MnVR 14Cr1MoR
20MnMoD
L555
20MnMo 12Cr1MoV
07MnNiCrMoVDR
S240 10MnWVNb 12Cr1MoVG
横焊
焊件位置
水平
水平 转动
管接头或 板垂直
焊缝厚度方向 垂直于水平面
管接头 垂直
管板水平
管子和扁 钢均水平
3.3.5 焊接方法 3.3.5.1 手工电弧焊、气焊、钨极氩弧焊、气体保护焊、埋弧焊。 3.3.5.2 当焊件的同一接头使用多种焊接方法(或工艺)焊接时,可按焊缝金属厚 度或母材厚度的适用范围对每一种焊接方法(或工艺)分别评定,也可以将焊接方法(或 工艺)组合起来评定。组合评定后用于焊件时,可以采用其中的一种或多种焊接方法(或 工艺),但每一种焊接方法(或工艺)的焊缝金属厚度应在其评定的各自适用范围内。 3.3.6 焊条、焊丝
R347
氩弧焊
焊丝
H08Mn2Si H08Mn2Si H10MnSi H08CrMoA H13CrMoA H08CrMoVA H13CrMoA
国家质量技术监督局关于执行JB4708-2000《钢制压力容器焊接工艺评定》标准的意见

国家质量技术监督局关于执行JB4708-2000《钢制压力容器焊接工艺评定》标准的意见文章属性•【制定机关】国家技术监督局(已撤销)•【公布日期】2001.01.02•【文号】质技监办发[2001]003号•【施行日期】2001.01.02•【效力等级】部门规范性文件•【时效性】失效•【主题分类】标准化正文国家质量技术监督局关于执行JB4708-2000《钢制压力容器焊接工艺评定》标准的意见(2001年1月2日质技监办发〔2001〕003号)各省、自治区、直辖市质量技术监督局:《钢制压力容器焊接工艺评定》(以下简称《焊接工艺评定》)JB4708-2000,已经批准发布,并于2000年10月1日起实施。
2000版《焊接工艺评定》标准与92版《焊接工艺评定》标准相比,内容有较大的变化,为既能有效地贯彻执行2000版《焊接工艺评定》,又尽量减少压力容器制造单位不必要的重复评定工作,经研究,提出如下意见,请各有关单位严格执行:1.自发文之日起,制造压力容器的单位进行焊接工艺评定时,应按2000版《焊接工艺评定》标准进行。
2.按92版《焊接工艺评定》标准评定合格的对接焊缝双面焊试件和堆焊试件的评定项目,继续有效。
3.按92版《焊接工艺评定》标准评定合格的对接焊缝单面焊的评定项目,属于下列情况之一的,可继续有效:(1)对接焊缝单面焊试件,试样的实际弯曲角度已达到双面焊接试件要求的弯曲角度;(2)原评定合格的焊接工艺评定项目,按2000版《焊接工艺评定》要求,只补做弯曲试验的评定,并经检验合格。
4.对2000版《焊接工艺评定》标准4.3中型式试验件的评定,如焊接条件与92版《焊接工艺评定》中组合焊缝试件相同时,则组合焊缝试件评定合格的项目适用该型式试验件。
5.上述可继续有效的评定项目和需补做弯曲试验的评定项目,对有冲击要求的,如其常温冲击功平均值小于27J,按2000版《焊接工艺评定》标准要求,还须补做冲击试验的评定,并经检验合格。
压力容器焊接工艺评定

压力容器焊接工艺评定本标准规定了焊接工艺评定规则、检验方法和合格指标,适用于石油、化学工业用钢制压力容器的焊接工艺评定.1 基本原则>1.1 焊接工艺评定就是按照所拟定的焊接工艺,根据标准的规定焊接试件、检验试样,测定焊接接头是否具有所要求的性能.经过焊接工艺评定提出"焊接工艺评定报告",并结合实践经验制订"焊接工艺规程"作为焊接生产的依据.压力容器焊接工艺评定的目的在于获得焊接接头机械性能符合要求的焊接工艺.1.2 使用本标准时,必须同时遵守《钢制石油化工压力容器设计规定》、JB741-80《钢制焊接压力容器技术条件》等有关标准或技术文件.<BR>1.3 焊接工艺评定因素分为基本因素、补加因素和次要因素.基本因素是指影响焊接接头机械性能(冲击韧性除外)的焊接条件.当规定进行冲击韧性试验时则增添补加因素,补加因素是指影响焊接接头冲击韧性的焊接条件.次要因素是指不影响焊接接头机械性能的焊接条件.当规定要重新评定焊接工艺、或因变更次要因素而不需要重新评定焊接工艺时,只需修订"焊接工艺规程."1.4 评定对接焊缝焊接工艺时,采用对接焊缝试件;评定角焊缝焊接工艺时,采用角焊缝试件.当基本因素和补加因素不变时,评定合格的对接焊缝焊接工艺适用于各种焊接接头中的对接焊缝;评定合格的角焊缝焊接工艺适用于各种焊接接头中的角焊缝.1.5 当进行焊接工艺评定时,所用设备应处于正常工作状态,钢材、焊接材料必须符合相应标准的规定,施焊者技术要熟练.2 焊接工艺评定规则2.1 通用规定2.1.1 改变焊接方法,需重新评定.2.1.2 关于钢材的规定:为减少焊接工艺评定的数量,将钢材划分为五类,每类内再划分组,见表1.2.1.2.1 钢材的类别号改变时,需重新评定.2.1.2.2 当改用同组别号的钢材时,不需重新评定.2.1.2.3 在同类别号中,高组别号钢材的评定适用于低组别号钢材.2.1.2.4 当两种类别号或两种组别号的钢材组成焊接接头时,即使这两种钢材各自都已评定合格,其组合焊接接头仍需重新评定.但2.1.2.3和2.1.2.6项所列情况可去重新评定.2.1.2.5 在同类别号中,高组别号钢材的评定适用于该组别号钢材与低组别号钢材所组成的焊接接头.2.1.2.6 除类别号为Ⅳ和V的钢材外,高类别号钢材的评定适用于该类别号钢材与低类别号钢材组成的焊接接头.2.1.3 改变焊后热处理类别,需重新评定.<BR>试件应当经受基本上相当于焊件和母材在制造过程中的热处理.在热处理温度下,其保温时间不得少于制造过程中累计保温时间的80%.除气焊外,对有冲击韧性要求的焊件,当改变焊后热处理的温度范围和保温时间时,需重新评定.2.1.4 板材试件的评定也适用于管材焊件,管材试件的评定也适用于板材焊件.2.1.5 焊接工艺经评定合格后,根据试件的厚度确定适用于焊件的厚度范围.若2.2条中各种焊接方法的焊接工艺评定规则中没有规定,则按下列各项所述.2.1.5.1 对接焊缝试件取拉伸和横向弯曲试样时,适用于焊件的厚度范围应符合表2的规定.2.1.5.3 除气焊外,若试件经超过临界匠焊后热处理,则适用于焊件焊缝金属最大厚度为1.1T. 2.1.5.4 某一尺寸角焊缝试件的评定适用于各种尺寸的角焊缝.2.1.5.5 某一尺寸对接焊缝试件的评定适用于相应焊缝金属厚度(见表2或表3)的角焊缝.2.1.5.6 若焊件焊缝为不完全焊透的对接焊缝,仍按表2或表表3的规定评定其母材和焊缝金属厚度范围.2.2 各种焊接方法的焊接工艺评定规定和因素.2.2.1 气焊2.2.1.1 厚度规定<BR>焊件母材的最大厚度等于试件的厚度.2.2.1.2 基本因素a.焊丝钢号.b.可燃气体的种类.2.2.1.3 次要因素a.坡口形式b.增加或取消钢垫板.c.在同组别号内选择不同钢号的钢材作垫板.d.坡口根部间隙e.填充金属的横截面积.f.焊接位置.g.预热温度.h.不摆动焊或摆动焊.i.从氧化焰改为还原焰,不需重新评定.<BR>j.左向焊或右向焊.<BR>k.焊前清理和层间清理方法.<BR>l.有无锤击焊缝.<BR>2.2.2 手弧焊<BR>2.2.2.1 厚度规定<BR>a.若焊件母材厚度大于200Mm,则试件的厚度大于或等于焊件焊接接头的厚度除以1.3,而适用于焊件母材和焊缝金属的最大厚度为1.3T和1.3t.<BR>b.单道焊或多道焊时,其中任一焊道的厚度大于13mm,则适用于焊件母材最大厚度为1.1T.<BR>c.当规定进行冲击韧性试验时,若焊件母材的厚度小于16mm,则试件厚在是焊件的最涉厚度;而焊件母材的厚度大于或等于16mm时,试件的最小厚度应为16mm,适用于焊件母材的最小厚度为16mm.<BR>d.焊件母材和焊缝金属厚度超出2.1.5款所列的范围,需重新评定.<BR>2.2.2.2 基本因素<BR>a.焊条牌号(焊条牌号中第三位数字除外).<BR>当焊条牌不 ,用非低氢型药皮焊条代替低氢型药皮焊条,需重新评定.<BR>b.预热温度比评定合格值降低50℃以上,需重新评定.<BR>2.2.2.3 补加因素<BR>a.焊条的直径改为大于6mm,需重新评定.<BR>b.从评定合格的焊接位置改变为向上立焊,需重新评定.<BR>c.最高层间温度比评定合格值高50℃以上,需重新评定.<BR>d.电流的种类和极性.<BR>e.增加量或单位长度焊道的熔敷金属超过评定合格时,需重新评定.<BR>若焊后热处理细化了晶粒,则不必测定能量或熔敷金属体积.<BR>2.2.2.4 次要因素<BR>a.坡口形式.<BR>b.取消单面焊时的钢垫板,不需重新评定.<BR>c.坡口根部间隙.<BR>d.增加或取消非金属或非熔化的金属焊接衬垫.<BR>e.焊条直径.<BR>f.焊接位置.<BR>g.需作精根处理的根部焊道向上立焊或向下立焊.<BR>h.施焊结束后至焊后热处理前,改变原预热规定,不需重新评定.<BR>i.电流种类或极性.<BR>j.电流值或电压值.<BR>k.不摆动焊或摆动焊.<BR>l.焊前清理和层间清理方法.<BR>m.清根方法<BR>n.手工操作、半自动操作或自动操作.<BR>o.有无锤击焊缝.<BR>2.2.3 埋弧焊<BR>2.2.31 厚度规定<BR>a.若焊件母材厚度大于200mm,则试件的厚度应大于或等于焊件焊接接头的厚度除以1.3,而适用于焊件母材和焊缝金属的最大厚度为1.3T 和1.3t.<BR>b.单道焊或多道焊时其中任一焊道的厚度大于13mm,则适用于焊件母材最大厚度应为1.1T.<BR>c.当规定进行冲击韧性试验时,若焊件母材的厚度小于16mm,则试件厚度应是焊件的最小厚度;而焊件母材的厚度大于或等于16mm时,试件的最小厚度应为16mm,适用于焊件母材的最小厚度为16mm.<BR>d.焊件母材和焊缝金属厚度超出2.1.5款所列的范围,需重新评定.<BR>2.2.3.2 基本因素<BR>a.最高层间温度比评定合格值高50℃以上,需重新评定.<BR>b.电流的种类和极性.<BR>c.增加线能量或单位长度焊道的熔敷金属体积超过评定合格值,需重新评定.<BR>若焊后热处理细化了晶粒,则不必测定线能量或熔敷金属体积.<BR>d.焊丝摆动幅度、频率和两端停留时间.<BR>e.由每面多道焊改为每面单道焊,需重新评定.<BR>f.单丝焊或多丝焊.<BR>2.2.3.4 次要因素<BR>a.坡口因素<BR>b.取消单面焊的钢垫板,不需重新评定.<BR>c.坡口根部间隙.<BR>d.增加或取消非金属或非熔化的金属焊接衬垫.<BR>e.焊丝直径.<BR>f.焊剂商标名称或制造厂.<BR>g.焊接位置.<BR>h.施焊结束后至焊后热处理前,改变原预热规定,不需重新评定.<BR>i.电流种类或极性.<BR>j.电流值或电压值.<BR>k.不摆动焊或摆动焊.<BR>l.焊前处理和层间清理方法.<BR>m.清根方法.<BR>n.焊丝摆动幅度、频率和两端停留时间.<BR>o.导电嘴至工件的距离.<BR>p.由每面多道焊改为每面单道焊,不需重新评定.<BR>q.单丝焊或多丝焊.<BR>r.焊丝间距.<BR>s.半自动操作或自动操作.<BR>t.有无锤击焊缝.<BR>2.2.4 熔化极气体保护焊<BR>2.2.4.1 厚度规定<BR>a.若焊件母材厚度大于200mm,则试件的厚度应大于或等于焊件焊接接头的厚度除以1.3,而适用于焊件母材和焊缝金属的最大厚度为1.3T和1.3t.<BR>b.单道焊或多道焊时,其中任一焊道的厚度大于13mm,则适用于焊件母材最大厚度应为1.1T.<BR>c.当熔滴呈短路过渡时,适用于焊件母材最大厚度应为1.1T.<BR>d.当规定进行冲击韧性试验时,若焊件母材的厚度小于16mm,则试件厚度应是焊件的最小厚度;而焊件母材的厚度大于或等于16mm时,试件的最小厚度应为16mm,适用于焊件母材的最小厚度为16mm.<BR>e.焊件母材和焊缝金属厚度超出2.1.5款所列的范围,需重新评定.<BR>2.2.4.2 基本因素<BR>a.焊丝钢号.<BR>b.实芯焊丝或药芯焊丝.<BR>c.添加或取消附加的填充金属;附加填充金属的数量.<BR>d.焊缝金属中重要合金元素含量超出评定合格的范围,需重新评定.<BR>e.预热温度化评定合格值降低50℃以上,需重新评定.<BR>f.保护气体种类;混合保护气体配比.<BR>g.从单一的保护气体改用混合保护气体,或取消保护气体,需重新评定.<BR>2.2.4.3 补加因素<BR>a.从评定合格的焊接位置改变为向上立焊,需重新评定.<BR>b.最高层间温度比评定合格值高50℃以上,需重新评定.<BR>c.电流的种类和极性.<BR>d.增加线能量或单位长度焊道的熔敷金属体积超过评定合格值,需重新评定.<BR>若焊后热处理细化了晶粒,则不必测定线能量或熔敷金属体积.<BR>e.焊丝摆动幅度、频率和两端停留时间.<BR>f.由每面多道焊改为每面单道焊,需重新评定.<BR>g.单丝焊或多丝焊.<BR>2.2.4.4 次要因素<BR>a.坡口形式.<BR>b.取消单面焊的钢垫板,不需重新评定.<BR>c.坡口根部间隙.<BR>d.增加或取消非金属或非熔化的金属焊接衬垫.<BR>e.焊丝直径.<BR>f.焊接位置.<BR>g.需作清根处理的根部焊道向上立焊或向下立焊.<BR>h.施焊结束后至焊后热处理前,改变原预热规定,不需重新评定.<BR>i.保护气体的流量比评定合格值减少不超过10%,不需重新评定.<BR>j.熔滴过渡种类(颗粒过渡、喷射过渡、脉冲喷射过渡或短路过渡).<BR>k.电流的种类或极性.<BR>l.电流值或电压值.<BR>m.不摆动焊或摆动焊.<BR>n.焊前清理和层间清理方法.<BR>o.清根方法.<BR>p.焊丝摆动幅度、频率和两端停留时间.<BR>q.导电嘴至工件的距离.<BR>r.由每面多道焊改为每面单道焊,不需重新评定.<BR>s.单丝焊或多丝焊.<BR>t.焊丝间距.<BR>u.半自动操作或自动操作.<BR>v.有无锤击焊缝.<BR>2.2.5 钨极气体保护焊<BR>2.2.5.1 厚度规定<BR>a.若焊件母材厚度大于200mm,则焊件的厚度应大于或等于焊件焊接接头的厚度除以1.3,而适用于焊件母材和焊缝金属的最大厚度为1.3T和1.3t.<BR>b.单道焊或多道焊时,其中任一焊道的厚度大于13mm,则适用于焊件母材最大厚度应为1.1T.<BR>c.当规定进行冲击韧性试验时,若焊件母材的厚度小于16mm,则试件厚度应是焊件的最小厚度;而焊件母材的厚度大于或等于16mm时,试件的最小厚度应为16mm,适用于焊件母材的最小厚度为16mm.<BR>d.焊件母材和焊缝金属厚度超出2.1.5款所列的范围,需重新评定.<BR>2.2.5.2 基本因素<BR>a.焊丝钢号<BR>b.添加或取消预置填充金属;预置填充金属的化学成分范围.<BR>c.增加或取消填充金属.<BR>d.预热温度比评定合格值降低50℃以上,需重新评定.<BR>e.保护气体种类;混合保护气体配比.<BR>f.从单一的保护气体改用混合保护气体,或取消保护气体,需重新评定.<BR>2.2.5.3 补加因素<BR>a.从评定合格的焊接位置改变为向上立焊,需重新评定.<BR>b.最高层间温度比评定合格值高50℃以上,需重新评定.<BR>c.电流的种类或极性.<BR>d.增加线能量或单位长度焊道的熔敷金属体积超过评定合格值,需重新评定.<BR>若焊后热处理细化了晶粒,则不必测定线能量或熔敷金属体积.<BR>e.钨极摆动幅度、频率和两端停留时间.<BR>f.由每面多道焊改为每面单道焊,需重新评定.<BR>g.单丝焊或多丝焊.<BR>2.2.5.4 次要因素<BR>a.坡口形式.<BR>b.增加钢垫,不需重新评定.<BR>c.在同组别号内选择不同钢号的钢材作垫板.<BR>d.坡口根部间隙.<BR>e.增加或取消非金属或非熔化的金属焊接衬垫.<BR>f.填充金属横截面积.<BR>g.焊接位置.<BR>h.需要清极处理的根部焊道向上立焊或向下立焊.<BR>i.保护气体的流量比评定合格值减少不超过10%,不需重新评定.<BR>j.在直流电源上叠加或取消脉冲电流.<BR>k.电流种类或极性.<BR>l.电流植或电压值.<BR>m.钨极的种类或直径.<BR>n.不摆动焊或摆动焊.<BR>o.喷嘴尺寸.<BR>p.焊前清理和层间清理方法.<BR>q.清根方法.<BR>r.钨极摆动幅度、频率和两端停留时间.<BR>s.由每面多道焊改为每面单道焊,不需重新评定.<BR>t.单丝焊或多丝焊.<BR>u.钨极间距.<BR>v.手动操作,半自动操作或自动操作.<BR>w.有无锤击焊缝.<BR>2.2.6 电渣焊<BR>2.2.6.1 厚度规定<BR>焊件母材最大厚度应为1.1T.<BR>2.2.6.2 基本因素<BR>a.增加或取消非金属或非熔化的金属成形滑块.<BR>b.焊剂牌号;混合焊的混合比例.<BR>c.丝极或板极;丝极或板极钢号.<BR>d.熔嘴或非熔嘴;熔嘴钢号.<BR>e.电流值或电压值超过评定合格值±15%.<BR>f.电极摆动幅度、频率和两端停留时间.<BR>g.单丝焊或多丝焊.<BR>2.2.6.3 次要因素<BR>a.坡口形式.<BR>b.焊接面的装配间隙.<BR>c.填充金属的横截面积.<BR>d.焊前清理方法.<BR>e.焊丝间距.<BR>f.有无锤击焊缝.<BR>2.3 几种情况的规定<BR>2.3.1 当焊件的同一焊接接头使用一种以上焊接方法(或焊接工艺)时,则:<BR>2.3.1.1 按每种焊接方法(或焊接工艺)所焊母材和焊缝金属的工范围分别进行评定;或与焊件 ,使用一种以上焊接方法(或焊接工艺)焊接试件,进行组合评定.<BR>2.3.1.2 分别评定时,每种焊接方法(或焊接工艺)所适用于焊件母材和焊缝金属的厚度范围应符合表2或表3的规定.<BR>2.3.1.3 在确定适用于焊件焊接接头的最大厚度时,不能把每种焊接方法(或焊接工艺)评定后适用的厚度范围叠加.<BR>2.3.1.4 组合评定后用于焊件时,可以去掉一种或几种焊接方法(或焊接工艺), 要保证余留的每一种焊接方法(或焊接工艺)所熔敷的焊缝金属厚度都经过评定.<BR>2.3.1.5 组合评定中的每一种焊接方法(或焊接工艺)可以单独作用.<BR>2.3.2 焊件中厚边母材和薄边母材的厚度都在2.1.5款规定的范围内,则对接焊缝试件的评定适用于不同厚度母材之间的对接焊缝焊件(若试件厚度大于或等于40mm),则不限制厚边母材的最大厚度).<BR>2.3.3 不符合下列各项条件时,对接焊缝试件的评定适用于对接焊缝和角焊缝焊件的返修、补焊.<BR>2.3.3.1 焊件焊缝金属最小厚度不限.<BR>2.3.3.2 焊件母材和焊缝金属最大厚度符合2.1.5款规定的范围.但试件的厚度大于或等于40Mm时,不限制焊件母材最大厚度.<BR>2.4 耐蚀层堆焊<BR>在进行焊接工艺评定时应遵照技术文件或图样中关于堆焊耐蚀层的规定.<BR>如焊件的厚度大于或等于25mm,则试件基本的厚度可小于焊件厚度,但不得小于25mm;如焊件厚度小于25mm,则试件厚度应等于或小于焊件厚度.<BR>2.4.1 堆焊的通用基本因素和规定.<BR>2.4.1.1 焊接方法.<BR>2.4.1.2 从一种焊接方法改变为几种焊接方法的联用,需重新评定.<BR>2.4.1.3 基体钢材的类别号;基体钢材的类别号为Ⅲ<BR>2.4.1.4 焊条牌号(焊条牌号中第三位数字除外);焊丝(或钢带)钢号.<BR>2.4.1.5 除以下规定外,对评定合格的焊接位置增加其它焊接位置,需重新评定.<BR>横焊、立焊或仰焊位置的评定也适用于平焊位置.管接头水平固定焊5G(图1)的评定也适用于平焊、立焊和仰焊位置.横焊、立焊和仰焊位置的评定也适用于所有焊接位置.管接头45°固定焊6G(图1)的评定也适用于所有焊接位置.<BR>特殊位置焊接的焊件可以在此特殊位置下进行评定,其结果仅对实际焊接的位置有效.<BR>2.4.1.6 预热温度比评定合格值降低50℃以上或提高层间温度,需重新评定.<BR>2.4.1.9 多层堆焊或单层堆焊.<BR>2.4.1.10 电流种类或极性<BR>2.4.2 手弧焊堆焊的基本因素和规定<BR>2.4.2.1 堆焊首层所用焊条直径.<BR>2.4.2.2 首层施焊电流比评定合格值增加10%以上,需重新评定.<BR>2.4.3 埋弧焊、熔化极气体保护焊或钨极气体保护焊堆焊的基本因素和规定<BR>2.4.3.1 埋弧焊所用的焊剂牌号;混合焊剂的事比例.<BR>2.4.3.2 作用在同一熔池上的焊丝根数.<BR>2.4.3.3 增加或取消附加的填充金属.<BR>2.4.3.4 增加或取消焊丝的摆动.<BR>2.4.3.5 焊丝或附加的填充金属公称横截面积的变化超过10%,需重新评定.<BR>2.4.3.6 线能量或单位长度焊道内熔敷金属体积比评定合格值增加10%以上,需重新评定.<BR>2.4.3.7 对熔化极气体保护焊和钨极气体保护焊来说,保护气体种类;单一保护气体或混合保护气体:混合保护气体配比.<BR>2.4.3.8 取消保护气体,保护气体流量比评定合格值降低10%以上,需重新评定.<BR>2.4.4 次要因素<BR>除2.4.1,2.4.2,2.4.3款以外的工艺因素都是次要因素.<BR><BR>3 试制制备<BR><BR>3.1 必须按焊接工艺评定要求准备母材、焊接材料、加工坡口和施焊.<BR>3.2 试件的尺寸应足够切取所要求的试样.<BR>3.3 如果一份焊接工艺规程经过评定,除冲击韧性外各项要求均已满足.当再要求冲击韧性时,只需按同样的基本因素,增加所要求的补加因素,增作一个试件,其尺寸足够切取冲击韧性试样即可.<BR>如果一份焊接工艺规程经过评定,包括冲击韧性在内都已满足要求,若其中补加因素有所变更,则只需按同样的基本因素和补加因素,增加变更的补加因素增作一个试件,其尺寸足够切取冲击韧性试样即可.<BR>3.4 各类试件焊缝的焊接位置如下列各款所述,焊接位置的规定范围见附录B.<BR>3.4.1 管材对接焊缝试件的焊接位置见图1.<BR>3.4.2 板材对接焊缝试件的焊接位置见图2.<BR>3.4.3 板材角焊缝试件的焊接位置见图3.<BR>3.4.4 套管和管板角焊缝试件的焊接位置见图4.<BR>3.4.5 特殊位置焊接焊件,可以在此特殊位置下评定,其结果仅对实际焊接的位置有效.<BR><BR>4 试件和试样的检验<BR><BR>若技术文件或图样没有规定,则试件和试样的检验按本标准执行.<BR>所规定的每一项检验都合格,方认为焊接工艺评定合格.<BR>4.1 对接焊缝试件机械性能试验<BR>4.1.1 机械性能检验项目<BR>a.拉伸试验;<BR>b.弯曲(面弯、背弯、侧弯)试验;<BR>c.冲击韧性试验(当规定外).<BR>4.1.2 若试件使用一种以上的焊接方法(或焊接工艺)完成时,则:<BR>a.拉伸试样和弯曲试样的受拉面应包括每和种焊接方法(或焊接工艺)的焊缝金属.<BR>b.当规定作冲击韧性试验时,则对于每种焊接方法(或焊接工艺)都要作冲击韧性试验.<BR>4.1.3 机械性能检验的试样类别和数量<BR>4.1.3.1 对接焊缝试件取拉伸和横向弯曲试样的类别和数量应符合表4的规定.<BR>4.1.3.2 冲击韧性试样根据GB2650-81《焊接接头冲击试验法》规定,缺口开的焊缝金属和开在近缝区,同一部位所取试样数量为3个.<BR>4.1.4 机械性能检验取样顺序<BR>4.1.4.1 板材对接焊缝试件作拉伸和横向弯曲试验时的取样顺序见图5.<BR>5.1.4.2 管材对接焊缝试件的取样顺序见图6.<BR>4.1.5 拉伸试验<BR>拉伸试验测定焊接接头的抗拉强度.试样焊缝余高应以机械方法去除,使之与母材齐平.根据试件种类、拉伸试验条件和本标准规定,从下列五种试样中选择一种进行拉伸试验.<BR>4.1.5.1 带肩板形试样见图7、表5.适用于所有厚度板材的对接焊缝试件.去除焊缝余高前允许对试件进行冷校平.<BR>a.板材厚度小于或等于25Mm的试件,采用全板厚作单个试样.<BR>b.板材厚度大于25mm的试件,根据试验条件可采用单个试样,也可以采用多片试样.<BR>c.当采用多片试样时,应使用机械方法沿试件厚度方向切割出能够在现有设备上进行试验的、尺寸近似相等且数量最少的试样.<BR>4.1.5.2 管接头带肩板形试样之一见图8.适用于外径大于75mm的所有壁厚管材对接焊缝试件.为取得图中宽度为20mm的平行平面,壁厚方向上的加工量应最少.<BR>a.壁厚小于或等于25mm的试件,采用全壁厚作单个试样.<BR>b.壁厚大于25mm的试件,可采用单个试样,或按4.1.5.1c规定采用多片试样.<BR>4.1.5.3 管接头带肩板形试样之二见图9.适用于外径小于或等于75mm的管材对接焊缝试件.<BR>5.1.5.4 管接头的全断面试样见图10,对于外径小于或等于75mm的管材对接焊缝试件也可采用如图10试样及试验方法.<BR>4.1.5.5 单肩圆形试样见图11.取样方法按GB2649-81《焊接接头机械性能试验取样法》规定.<BR>4.1.5.6 拉伸试验方法<BR>按GB228-76《金属拉力试验法》,GB2651-81《焊接接头拉伸试验法》的规定进行拉伸试验.<BR>4.1.5.7 拉伸试验合格指标<BR>如试样的抗拉强度不低于下列规定之一,则该拉伸试验评为合格.<BR>a.产品图样设计规定值.<BR>b.钢材标准规定的最低抗拉强度.<BR>c.如果采用最低抗拉强度不同的两种钢材,则为两种钢材标准规定的最低抗拉强度中的较低值.<BR>d.如属技术文件或图样规定,选用室温强度低于钢材的焊缝,则为标准规定的焊缝金属最低抗拉强度.<BR>若采用多片试样,则将多片试样组成一组,拉伸试验时应检验完整的一组试样,每片试样都应进行试验,并符合合格指标.<BR>4.1.6 弯曲试验<BR>弯曲试验测定对接接头的致密性和塑性.<BR>焊缝余高应以机械方法去除,试样的拉伸面应保留母材的原始表面.<BR>4.1.6.1 横向面弯和背弯试样<BR>若试件厚度大于20mm时,则从弯曲试样的受压面以机械方法去除多余厚度.<BR>a.试件为板材时的面弯和背弯试样见图12及表6.<BR>当试样厚度允许时,面弯和背弯试样可沿同一厚度方向切取,如图13所示.<BR>b.试件为管材时的面弯和背弯试样见图14.<BR>当管壁厚度小于或等于20mm时,试样的上下弧面不必加工成平面;管壁厚度大于20mm时,允许从受压面加工.<BR>4.1.6.2 侧向弯曲试样见图15,表7.<BR>4.1.6.3 弯曲试验方法<BR>按表8和GB232-63《金属冷热弯曲试验法》规定进行弯曲试验.试样的焊缝轴线需对准弯轴轴线.<BR>4.1.6.4 弯曲试验合格指标<BR>弯曲试样冷弯到表8规定的角度后,其拉伸面上若有长度大于1.5mm的横向(沿试样宽度方向)裂纹或缺陷,或长度大于3mm的纵向裂纹或缺陷时为不合格.试样的棱角先期开裂不计.<BR>4.1.7 冲击韧性试验<BR>4.1.7.1 冲击试样形式、尺寸等应符合GB2650-81的规定.如技术文件或图样没有要求,冲击试样缺口轴线一律垂直于焊缝表面.<BR>4.1.7.2 冲击试验方法:<BR>按GB229-84《金属夏比(U型缺口)冲击试验方法》,GB4159-84《金属低温夏比冲击试验方法》和GB2106-80《金属夏比(V型制品)冲击试验方法》的规定执行.<BR>4.1.7.3 冲击韧性试验合格指标<BR>按技术文件或图样要求确定.<BR>4.2 角焊缝试件检验<BR>组别号为Ⅱ-3、类别号为Ⅲ的钢材角焊缝应进行对接焊缝试件机械性能检验和角焊缝试件检验.<BR>除上述钢材以外的角焊0缝应进行对接焊缝试件机械性能检验,仅有角焊缝试件检验则只适用于非承角焊缝.<BR>4.2.1 板材角焊缝试件及试样见图16和表9.<BR>a.如图16所示将试件横向五等分切开,每块试样长50mm,两端长各25mm废弃.<BR>b.每一块试样取一个面进行宏观金相检验(浸蚀剂和浸蚀方法见附录C).<BR>4.2.2 套管和管板角焊缝试件及试样见图17.这两种试件的评定结果可互相通用.<BR>a.依图示位置处取试件的四分之一,作宏观金相试样;<BR>b.焊缝的起始和终了位置应在试样的中部;<BR>c.取试样的一个面作宏观金相检验;<BR>d.若以套管或管板角焊缝评定板材角焊缝,则应切取1-4个试样,每个试样取一个面作宏观金相检验.<BR>4.2.3 合格指标<BR>a.对于4.2.1款,焊脚等于T2,且不大于20mm;对于4.2.2款,最大焊脚等于管壁厚.<BR>b.焊缝表面不应有任何可见裂纹.<BR>c.宏观金相检验时,焊缝根部应熔合,焊缝金相和热影响区不得有裂纹,两焊脚之差不大于3mm.<BR>4.3 耐蚀堆焊试件检验<BR>4.3.1 渗透探伤<BR>按JB741-80附录六"渗透探伤"的规定执行.<BR>4.3.2 弯曲试验<BR>渗透探伤合格后在堆焊试件上取四个侧弯试样,其取法是平行和垂直于焊接方向各两个,或者四个试样都垂直于焊接方向.试样尺寸参照图15.<BR>按表10和GB2653-81《焊接接头弯曲及压扁试验法》的规定进行弯曲试验.如果试样有缺陷对着支持辊的试样面则是缺陷较严重的一侧.<BR>当按图15所示试样宽度大于40Mm时,变轴长度至少比试样工多6mm.<BR>弯曲试验后在试样拉伸部位内的任何方向测量不得有超过1.5mm长的开裂缺陷,在熔合线上不得有超过3mm长的开裂缺陷.<BR>4.3.3 化学成分检验<BR>化学分析取样部位如图18所示.<BR><BR>附录 A<BR>标准使用说明<BR>(参考件)<BR><BR>A.1 《压力容器焊接工艺评定》标准是确保压力容器安全可靠运行标准体系中的一个,在评定焊接工艺时还应遵守标准体系中的有关标准规定,特别是《钢制石油化工压力容器设计规定》和JB741-80《钢制焊接压力容器技术条件》.为了确保压。
钢制压力容器焊接工艺评定

钢制压力容器焊接工艺评定钢制压力容器是在工业生产过程中经常使用的一种设备。
作为容器,它需要经受压力的力量,并且还要保证内部介质不泄漏。
为了满足这些要求,焊接工艺一定要得到严格的控制和评定。
本文将介绍钢制压力容器焊接工艺评定的基本概念和流程。
什么是焊接工艺评定?焊接工艺评定是指通过对焊接工艺进行试验和评定,来判定焊接工艺的可靠性、适用性以及质量等指标。
焊接工艺评定是为了满足相关标准和规范的要求,确保焊接件符合设计要求和使用要求。
钢制压力容器焊接工艺评定的流程1. 概述在进行钢制压力容器焊接工艺评定之前,需要做好相关准备工作,包括准备焊接样品、确定评定标准等。
接下来,将一步一步介绍钢制压力容器焊接工艺评定的流程:2. 准备焊接样品在评定焊接工艺之前需要准备好焊接试样。
样品应该具有一定的代表性,通常的选择原则是选取最薄、最厚、直线焊和角焊。
样品应该具有与实际构件相同的质量、和焊接件类似的形状和尺寸、工艺类似于实际焊接过程等特点。
3. 焊接试验焊接试验是评定焊接工艺的关键环节,主要包括以下步骤:a. 固定角焊的试验在角焊焊接工艺评定中,一般使用三角板试样评定。
试样宽为300mm至500mm,板厚为确定步骤后的板厚,焊缝的长度应不小于200mm。
在进行试验之前,需要先在试样边缘处去除焊缝起始段,以此来保证试样的形状和焊缝的质量。
排除异常情况后进行剩下板件焊接,记录焊接参数和质量。
b. 固定直线焊试验在直线焊试验中,使用的是单面焊穿法焊接,首先将试样焊口排列好,再将试验端部或全长焊接,记录焊接参数并检查焊接质量。
4. 评定结果根据焊接试验的结果,对焊接工艺进行评定。
评定结果应该根据相关标准和规范作出判断,同时还需要参考实际应用情况,以确定最终的焊接工艺和焊接质量。
钢制压力容器焊接工艺评定是保证钢制压力容器的质量的重要环节。
只有在严格的评定标准和规范的指导下,才能确保焊接工艺的可靠性和适用性,最终保证焊接件的质量。
压力容器焊接规程
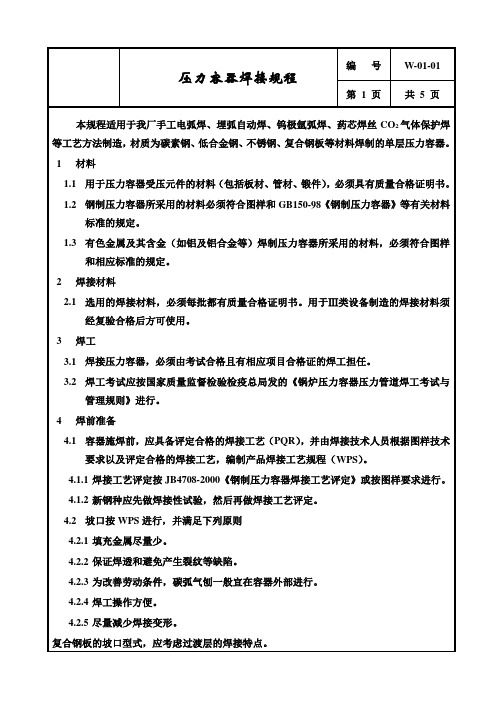
4.6装配点固焊
4.6.1装配点固焊一般应使用与焊接时相同牌号的焊条,并应相同。预热范围:点固焊道的周围,距点固焊道周边3倍工件厚度且不小于100mm的范围内。测温部位:位于距点固焊道周边50mm处。
7返修
7.1焊缝返修会降低产品质量,因此焊工在施焊过程中,应精心操作,尽量提高一次合格率,避免返修。
7.2焊缝返修按《焊缝返修工艺守则》进行。
7.3焊缝同一部位的返修次数不宜超过两次。
7.4对经过两次返修仍不合格的焊缝,需经质保工程师批准才能再返修。
7.5对于裂纹缺陷,应进行质量分析,找出原因,制订相应技术措施或交底后方可返修。
4.6.3点固焊道有裂纹时,必须清除重焊。
4.7严禁在非焊接部位引弧,如发生打弧,须将弧坑按施焊工艺条件补焊、磨平。
4.8当焊接工艺要求焊前预热时,按本规程第6条进行焊前预热。
4.9电源的接地线应与工件可靠的连接,保证导电良好防止打弧现象。
4.10为了防止焊接裂纹和减少内应力,装配时要避免强行组装。
6.5.3后热应在焊后立即进行。
6.5.4工艺文件的后热标注:
应注为a℃×bh,其中a表示后热温度
b表示保温时间,h代表小时
例:某工件,要求焊后200℃,保温1小时30分,注为200℃×1.5h。
压力容器焊接规程
编号
W-01-01
第4页
共5页
6.6产品的焊后热处理必须WPS要求或产品热处理方案(技术措施)进行。产品焊接试板必须与产品同炉热处理。
4.2坡口按WPS进行,并满足下列原则
- 1、下载文档前请自行甄别文档内容的完整性,平台不提供额外的编辑、内容补充、找答案等附加服务。
- 2、"仅部分预览"的文档,不可在线预览部分如存在完整性等问题,可反馈申请退款(可完整预览的文档不适用该条件!)。
- 3、如文档侵犯您的权益,请联系客服反馈,我们会尽快为您处理(人工客服工作时间:9:00-18:30)。
中华人民共和国行业标准JB 4708—2000JB/T 4709—2000JB 4744—2000钢制压力容器焊接工艺评定钢制压力容器焊接规程钢制压力容器产品焊接试板的力学性能检验Welding procedure qualification for steel pressure vesselsWelding specification for steel pressure vesselsMechanical property tests of product welded test coupons for steel pressure vessels2000—08—15发布 2000—10—01实施国家机械工业局国家石油和化学工业局发布关于发布《钢制压力容器焊接工艺评定》等四项行业标准的通知国机管[2000]401令有关单位:根据国家质量技术监督局规定的压力容器行业标准审批程序,现发布《钢压力容器焊接工艺评定》等四项行业标准,编号与名称如下:强制性标准:JB 4708—2000钢制压力容器焊接工艺评定(代替JB 4708—1992)JB 4710—2000钢制塔式容器(代替JB 4710—1992)JB 4744—2000钢制压力容器产品焊接试板的力学性能检验(代替GBl50—1998附录 E)推荐性标准:JB/T4709—2000钢制压力容器焊接规程(代替JB/T4709—1992)以上标准于 2000年10月1日起实施,其出版发行工作责成全国压力容标准化技术委员会按期组织完成。
国家机械工业局国家石油和化学工业局2000年 8月15日目次JB 4708—2000 钢制压力容器焊接工艺评定 (1)前言 (5)1范围 (7)2引用标准 (7)3术语 (8)4总则 (8)5对接焊缝、角焊体焊接工艺评定规则 (9)6耐蚀堆焊工艺评定规则 (21)7试验要求和结果评价 (22)附录 A(标准的附录)不锈钢复合钢焊接工艺评定 (32)附录 B(提示的附录)焊接工艺指导书和焊接工艺评定报告表格推荐格式 (33)JB/T 4709—2000 钢制压力容器焊接规程 (39)前言 (40)1范围 (41)2引用标准 (41)2焊接材料 (41)4焊接工艺评定和焊工 (41)5焊前准备 (42)6焊接 (55)7后热 (56)8焊后热处理 (56)9焊缝返修 (58)10焊接检验 (59)财录 A(标准的附录)不诱钢夏合钢焊接规程 (60)附录 B(提示的附录)焊接工艺规程推荐表格 (64)JB 4744—2000钢制压力容器产品焊接试板的力学性能检验 (69)前言 (70)1范围 (71)2引用标准 (71)3符号 (71)4产品焊接试板制备的要求 (72)5产品焊接试板试样的制备 (72)5拉伸试验 (73)7弯曲试验 (74)8冲击试验 (75)9复验 (76)JB 4708-2000钢制压力容器焊接工艺评定前言本标准对JB 4708—1992进行修订。
本标准依据JB 4708—1992实施以来所取得的经验,参照近期国际同类标准进行了下列变功:1增加“术语”和“附录 A不锈钢夏合钢焊接工艺评定”。
2撤消 JB 4708—1992中“附录 B标准使用说明”。
其中,未列人GB150钢材的评定、次要因素等技术内容己写入正文。
3增加型式试验要求,撤消 JB 4708—1992第3章、第4章和第5章中有关组合焊缝评定条款及试件图。
4 JB 4708—1992第4章在本标准中明确分为第5章“对接焊缝、角焊缝焊接工艺评定规则”和第6章“耐蚀堆焊工艺评定规则”两部分,条款顺序做了凋整,在技术内容方面有如下变化:①根据GB150—1998的变动,增加和撤消了一些钢号,对增加的钢号规定了类别、组别。
②重新定义焊后热处理类别,增加当规定进行冲击试验时重新评定条款。
③修改经评定合格后试件厚度适用于焊件厚度的有效范围。
④增加了当规定进行冲击试验时,部分焊透和不等厚对接焊件评定时试件厚度及适用于焊件厚度的条款。
⑤修改返修焊、补焊和打底焊时试件厚度及适用于焊件厚度的条款。
⑥表1变更了一些焊接工艺评定因素。
5 第6章(JB 4708—1992第4章)重新编排耐蚀堆焊重新评定焊接条件成表 9,改变了一些焊接条件。
6第7章(JB 4708—1992第5章)的主要变化如下:①增加耐蚀堆焊试件尺寸的规定。
②修改了对接焊缝试件外观检查和无损检测、角焊缝试件外观检查的合格指标。
③增加T<1.5mm时的试验项目和取样数量,修改了表的注。
④修改了制取多片拉伸试样规定。
⑤修改了弯曲试样加工、试验方法和合格指标。
⑧修改了冲击试验合格指标。
⑦由于⑤和⑥的变化,从而使不同钢号焊接接头力学性能和弯曲性能试验合格指标有了依锯。
⑧增加了耐蚀堆焊切取弯曲试样意图;修改了堆焊金属化学成分分析取样示意图;增加了堆焊层评定最小厚度的测量方法。
7附录 B依据正文内容变化而有所改变。
本标准从实施之日起,代替 JB 4708—1992。
本标准的附录 A是标准的附录。
本标准的附录 B是提示的附录。
本标准由全国压力容器标准化技术委员会提出并归口。
本标准负责起草单位:合肥通用机械研究所、国家质量枝术监督局锅炉压力容器安全监察局。
本标准主要起草人:戈兆文、张建茉。
参加本标准编制工作的单位及人员有:中国石化集团公司咨询公司:寿比南、杨国义。
国家质量技术监督局锅炉压力容器安全监察局:高继轩。
中国化工勘察设计办会:梁之洵。
合肥通用机械研究所:李景辰。
辽宁省质量技术监督局:王俊。
本标准于1992年4月首次发布。
本标准由全国压力容不得器标准化技术委员会负责解释。
中华人民共和国行业标准JB 4708—2000钢制压力容器焊接工艺评定代替JB 4708—1992 Welding procedure qualification for steel pressure vessels1 范围本标准规定了钢制压力容器焊接工艺评定规则、试验方法和合格指标。
本标准适用于钢制压力容器的气焊、焊条电弧焊、埋弧焊、熔化极气体保护焊、钨极气体保护焊、电渣焊、耐蚀堆焊等的焊接工艺评定。
2 引用标准下列标准所包含的条文,通过在本标准中引用而构成为本标准的条文。
本标准出版时,所示版本均为有效。
所有标准都会被修订,使用本标准的各方应探讨使用下列标准最新版本的可能性。
GB 150—1998钢制压力容器GB/T228—1987金属拉伸试验方法GB/T229—1994金属夏比缺口冲击试验方法GB/T232—1988金属弯曲试验方法GB/T713—1997锅炉用钢板GB/T912—1989碳素结构钢和低合金结构钢热轧薄钢板及钢带GB/T3087—1982低中压锅炉用无缝铜管 .GB/T3274—1988碳素结构钢和低合金结构钢热轧厚钢板和钢带GB/T3280—1992不锈钢冷轧钢板GB/T3531—1996低温压力容器用低合金钢钢板(含第一号修改单)GB/T 4237—1992不锈钢热轧钢板GB/T5310—1995高压锅炉用无缝钢管GB 6479,—1986化肥设备用高压无缝钢管GB 6654—1996压力容器用钢板(含第一、二号修改单)GB/T 8163—1987输送流体用无缝钢管GB 9948—1988石油裂化用无缝钢管GB 13296—1991锅炉热交换器用不锈钢无缝钢管GB/T 14976—1994流体输送用不锈钢无缝钢管JB 4726—2000压力容器用碳素钢和低合金钢锻件JB 4727—2000低温压力容器用低合金钢锻件JB 4728—2000压力容器用不锈钢锻件JB 4730—1994压力容器无损检测国家机械工业局国家石油和化学工业局 2000—08—15批准 2000—10—01实施3 术语本标准采用下列定义。
3.1 焊接工艺评定 welding procedure qualification为验证所拟定的焊件焊接工艺的正确性而进行的试验过程及结果评价。
3.2 焊接工艺指导书welding procedure specification为验证性试验所拟定的、经评定合格的、用于指导生产的焊接工艺文件。
3.3 焊接工艺评定报告 procedure qualification record按规定格式记载验证性试验结果,对拟定焊接工艺的正确性进行评价的记录报告。
3.4焊接接头 welded joint由两个或两个以上零件要用焊接组合或已经焊合的接点,检验接头性能应考虑焊缝、熔合区、热影响区甚至母材等不同部位的相互影响。
3.5焊件weldment用焊接方法连接的压力容器或其零部件,焊件包括母材和焊接接头两部分。
3.6试件tst piece按照预定的焊接工艺制成的用于焊接工艺评定试验的焊件。
试件包括母材和焊接接头两部分。
3.7 焊后热处理post weld heat treament能改变焊接接头的组织和性能或残余应力的热过程。
3.8 下转变温度lower transformation temperature加热期间开始形成奥氏体的相变温度。
3.9 上转变温度 upper transformation temperature加热期间完成奥氏体转变的相变温度。
3.10 横向弯曲 transverse bend焊缝轴线与试样纵轴垂直时的弯曲。
3.11 纵向弯曲longitudinal bend焊缝轴线与试样纵轴平行时的弯曲。
3.12 面弯 face bend试样受拉面为焊缝正面的弯曲。
具有较大焊缝宽度的面称为正面;当两面焊缝宽度相等则先完成盖面层焊缝一侧为正面。
3.13 背弯 root bend试样受拉面为焊缝背面的弯曲。
3.14 侧弯 side bend试样受拉面为焊缝横截面的弯曲。
4 总则4.1 焊接工艺评定应以可靠的钢材焊接性能为依据,并在产品焊接之前完成。
4.2 焊接工艺评定一般过程是:拟定焊接工艺指导书、施焊试件和制取试样、检验试件和试样、测定焊接接头是否具有所要求的使用性能、提出焊接工艺评定报告对拟定的焊接工艺指导书进行评定。
焊接工艺评定验证施焊单位拟定的焊接工艺的正确性,并评定施焊单位能力。
4.3 对于截面全焊透的T形接头和角接接头,当无法检测内部缺陷,而制造单位又没有足够的能力确保焊透时,还应增加制作型式试验件进行焊接工艺评定,经解剖试验确认方能允许施焊产品。
4.4 焊接工艺评定所用设备、仪表应处于正常工作状态,钢材、焊接材料必须符合相应标准,由本单位技能熟练的焊接人员使用本单位焊接设备焊接试件。
5 对接焊缝、角焊缝焊接工艺评定规则5.1 评定对接焊缝焊接工艺时,采用对接焊缝试件。
对接焊缝试件评定合格的焊接工艺亦适用于角焊缝。
评定非受压角焊缝焊接工艺时,可仅采用角焊缝试件。