第三章 沙型铸造(修正)
第二篇 铸造(2)-砂型铸造
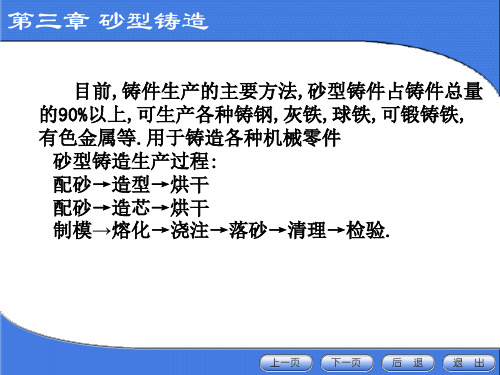
第三章 砂型铸造
第三节 浇注位置与分型面的选择
浇注位置---指金属浇注时铸件所处的空间位置 分型面---指砂箱间的接触表面 一 浇注位置选择原则: 铸件浇注位置对铸件质量,造型方法等有很大影响, 应注意以下原则: 1 铸件重要的加工面应朝下:如图 1) 若做不到,可放侧面或倾斜; 2) 若有几个加工面,则应把较大的放下面. 如导轨面是关键面,不允许有缺陷,则要放下面。
第三章 砂型铸造
目前,铸件生产的主要方法, 目前,铸件生产的主要方法,砂型铸件占铸件总量 90%以上 可生产各种铸钢,灰铁,球铁,可锻铸铁, 以上, 的90%以上,可生产各种铸钢,灰铁,球铁,可锻铸铁, 有色金属等. 有色金属等.用于铸造各种机械零件 砂型铸造生产过程: 砂型铸造生产过程: 配砂→造型→ 配砂→造型→烘干 配砂→造芯→ 配砂→造芯→烘干 制模→熔化 浇注→落砂→清理→检验. 熔化→ 制模 熔化→浇注→落砂→清理→检验.
第三章 砂型铸造
第三节 浇注位置与分型面的选择
二 铸型分型面的选择原则 ① 分型面应选在铸件最大截面处; ② 尽量减少分型面数量,最好只用一个分型面; 如图 ③ 尽量使铸件的主要加工面和加工基准面在同一 个砂箱内;如图 ④ 应使型腔和主要型芯位于下箱;如图 ⑤ 尽量选择平直面为分型面。如图
第三章 砂型铸造
第三章 砂型铸造பைடு நூலகம்
第二节 造型方法选择
二 机器造型及其工艺特点
种 类 压实式 震实式 震压式 抛砂造型 微震压实式 高压造型 射压式 机器造型的各种方法对比 主 要 特 点 用较低的比压压实铸型。机器结构简单,噪音较小,生产率 较高 靠造型机的震击来紧实铸型。机器结构简单,制造成本低。 但噪音大,生产率低,对厂房基础要求高,劳动繁重 在震击后加压,紧实铸型。机器的制造成本较低,生产率较 高,噪音大。型砂紧实度较均匀,能量消耗少 用抛砂方法填实和紧实铸型。机器的制造成本较低,生产率 较高,能量消耗少,型砂紧实度较均匀 在微震的同时加压紧实铸型。生产率较高,机器较易损坏 用较高的比压来压实铸型。生产率高,铸件尺寸准确,易于 自动化。但机器结构复杂,制造成本高 用射砂填实砂箱,再用高比压压实铸型,生产率高,易于自 动化,型砂紧实度高而均匀 适 用 范 围 用于成批生产的小铸件 用于成批生产的中、小铸件 用于成批生产的小铸件 用于成批生产的大型铸件 用于成批生产中、小铸件 用于大批生产中、小铸件 用于大批生产中、小铸件
第三章 砂型铸造

3.2.4 工艺参数的确定
加工余量 收缩率 拔模斜度 铸造圆角
工艺参数
型芯及型芯头
一、机械加工余量和最小铸孔 灰铸铁砂型铸造的机械加工余量
铸件最大 尺寸 (㎜)
浇注时 位置
<50
<120
顶面 3.5~4.5 底、侧面 2.5~3.5
120~260
顶面 4.0~5.0 底、侧面 3.0~4.0
260~500
三、铸造收缩率 铸件在凝固和冷却过程中会发生收缩而造成各部分体积和尺
寸缩小。 为保证铸件尺寸要求,需在模样(芯盒)上加大一个收缩的尺
寸。加大的这部分尺寸称收缩量,一般根据铸造收缩率来定。 铸造收缩率定义如下:
K=[(L模-L件)/L件]×100% 式中: K为铸造收缩率;L模为模样尺寸;L件为铸件尺寸。
以免形成夹渣和夹砂等缺陷。
平板铸件
3、应将铸件薄而大的平面放在下部、侧面或倾斜位置
以利于合金液填充铸型
铝电机端盖浇注位置
油盘浇注位置
4、应将铸件的厚大部分放在上部或侧面
以获得组织致密,外形完整的铸件
链轮的浇注位置(铸钢)
5、铸件圆周表面质量要求高,应进行立铸(三箱造型或平 作立浇)
卷扬筒的浇注位置
(1)机器造型分类
按紧实方式不同,机器造型分为 震实造型、压实造型、震压造型和抛砂造型
中小型铸件多以震压造型方法 大型铸件多以抛砂造型方法
1-工作台 2-模样 3-砂箱 4-辅助框 5-压板 6-压板架 压实造型工作示意图
1)震压造型 是利用震动和撞击力对型砂紧实
a)填砂 b)振击紧砂 c)辅助压实d)起模 震压造型机的工作过程
(3)方案Ⅲ 沿110 mm凹槽底面分 型。
金属工艺学第五版课后习题解答修图版

铸造:第四章 砂型铸件的结构设计
2.什么是铸件的结构斜度?它与起模斜度有何不同? 图示铸件的结构是否合理?应如何改正? p81
在零件设计中所确定的非加 工表面斜度为结构斜度。而 在绘制铸造工艺图中加在垂 直分型面的侧面所具有的斜 度称为起模斜度,以使工艺 简化和保证铸件质量。
铸造:第四章 砂型铸件的结构设计
6.为什么铸件要有结构圆角?图示铸件上哪些圆角不 够合理?应如何修改? p81
铸造:第四章 砂型铸件的结构设计
7.下图所示的支架件在大批量生产中该如何改进其设 计才能使铸造工艺得以简化? p81
尽量避免铸件起模方 向存有外部侧凹,以 便于起模。
铸造:第四章 砂型铸件的结构设计
p73
I方案存在错箱可能。 该零件不算太高,故 方案II稍好,从冒口
II
安放来看,II方案容 易安放。
I
铸造:第三章 砂型铸造
5.图示铸件在单件生产条件下该选用哪种造型方法?
方案I: 分型面为
大截面处,且为平面,
方案可行。
铸造:第三章 砂型铸造
5.图示铸件在单件生产条件下该选用哪种造型方法?
4 确定焊缝位置,选择焊接方法,制定 装配焊接次序。
筋 板
5000
600
6
10
3600
上翼板 300
腹板 8 800
下翼板
焊接:第四章 焊接结构设计
4 确定焊缝位置,选择焊接方法,制定装配焊接次序。
焊接方法: 手工电弧焊、二氧化碳气体保护焊
试制样机时该连杆宜采用砂型铸造方法p93当年产量为1万件时宜采用金属型铸造方法当年产量超过10万件时宜采用压力铸造方法
砂型铸造

砂型铸造-湿型铸造1 概述粘土砂型可分为湿型、干砂型和表面烘干砂型。
三者之间的主要差别在于:湿型是造好的砂型不经烘干,直接浇入高温金属液体;干砂型是在合箱和浇注前将整个砂型送入窑中烘干;表面烘干砂型只在浇注前对型腔表层用适当方法烘干一定深度(一般5~10mm,大件20mm以上)。
目前,湿型砂是使用最广泛的、最方便的造型方法,大约占所有砂型使用量的60~70%,但是这种方法还不适合很大或很厚实的铸件。
表面烘干型与干型比,可节省烘炉,节约燃料和电力,缩短生产周期,所以曾在中型和较大型铸铁件的生产中推广过。
通常采用较粗砂粒(使有高的透气性),加入较多粘土和水分,有时还在型砂中加1~2%的木屑(提高抗夹砂结疤能力),其型腔表面必须涂敷涂料。
干型主要用于重型铸铁件和某些铸钢件,为了防止烘干时铸型开裂,一般在加入膨润土的同时还加入普通粘土。
干型主要靠涂料保证铸件表面质量。
其型砂和砂型的质量比较容易控制,但是砂型生产周期长,需要专门的烘干设备,铸件尺寸精度较差,因此,近些年的干型,包括表面烘干的粘土政型已大部分被化学粘结的自硬砂型所取代。
2 湿型铸造2.1湿型铸造特点湿型铸造法的基本特点是砂型(芯)无需烘干,不存在硬化过程。
其主要优点是生产灵活性大,生产率高,生产周期短,便于组织流水生产,易于实现生产过程的机械化和自动化;材料成本低;节省了烘干设备、燃料、电力及车间生产面积;延长了砂箱使用寿命等。
但是,采用湿型铸造,也容易使铸件产生一些铸造缺陷,如:夹砂、结疤、鼠尾、粘沙、气孔、砂眼、胀砂等。
随着铸造科学技术的发展,对金属与铸型相互作用原理的理解更加深刻;对型砂质量的控制更为有效;加上现代化砂处理设备使型砂质量得到了一定保证;先进的造型机械使型砂紧实均匀,起模平稳,铸型的质量较高,促进了湿型铸造方法应用范围的扩大。
例如汽车、拖拉机、柴油机等工业中,质量在300~500kg以下的薄壁铸铁件,现都已成功地采用湿型铸造。
第三章 砂型铸造 Sand casting

§2 浇注位置与分型面的选择
The Choice of Pouring Location and Mould Joint
一、浇注位置的选择原则 铸件的重要加工应朝下 铸件的大平面应朝下 面积较大的薄壁部分应置于铸型下部或 倾斜放置 对易产生缩孔的铸件,厚的部分应放在 分型面附近的上部或侧面,以利安置补 缩冒口
§3 工艺参数的选择
The choice of Technological Parameters
机械加工余量 工艺参数 拔模斜度 收缩率 型芯头 一、机械加工余量和铸孔 Machining Allowance and Casting Hole GB/T11350-89 “铸件机械加工余量” GB6416 “铸件尺寸公差”
拔模斜度取值示意图
三、收缩率Rate of Shrinkage
由于合金在浇铸后的凝固、冷却过程中 有收缩,故在画铸造工艺图时应将模型 的尺寸相应放大。 放大量正好为合金的收缩量 灰口铸铁 0.7~1.0% 铸 钢 1.3 ~2.0% 铝硅合金 0.8 ~1.2% 锡青铜 1.2 ~1.4% 在画铸造工艺图时用定制的尺—缩尺
一、机械加工余量和铸孔
2、孔的加工—灰口铸铁的最小孔径 单件生产—φ30~50mm 成批生产—φ15~20mm 大量生产—φ12~15mm 注:零件图上不要求加工的孔、槽, 无论大小,原则上都要铸出。
二、拔模斜度pattern Taper
1、目的 p64 2 、表达 加工表面—结合加工余量直接画出 不加工表面—用文字注明 3、拔模斜度取值 一般取15 ’~3o,铸孔内壁取大一些3o~10o 立壁越高,斜度越小
第三章 砂型铸造 Sand cas作用:指导模型(芯盒) 设计,生产准备,铸型制造和铸件检验。 铸造工艺图的内容包括: 铸件的浇注位置、铸型分型面、型芯的 形状、固定方法、加工余量、拔模斜度、 收缩率、浇注系统、冒口、冷铁等。 举例
砂型铸造3

分产生浇不足或冷隔缺
陷,应将面积较大的薄 壁部分置于铸型下部或 使其处于垂直或倾斜位 置。
一、浇注位置选择原则
(4)对于容易产生缩孔的铸件,应使厚 的部分放在铸型的上部或侧面,以便在
铸件厚壁处直接安臵冒口,使之实现自
下而上的定向凝固。如前述之铸钢卷扬 筒,浇注时厚端放在上部是合理的;反 之,若厚端放在下部,则难以补缩。
第三节铸造工艺参数的确定根据国家标准gbt64141999要求的机械加工余量登记有10级称为abc第三节铸造工艺参数的确定铸件最大尺mm加工面在型公称尺寸mm120120260260500500800800125012502000120120260260500500800800125012502000顶面底面侧面顶面底面侧面顶面底面侧面顶面底面侧面顶面底面侧面顶面底面侧面454035305045403060504540060504555508056050555045400605045065504580060508080605506560508006050805605590800609050559080055909006510085565100908065120100905铸件上的孔和槽铸出与否取决于铸造工艺的可行性和必要性
便整模造型,使其加工面和加工基准 面处于同一砂箱内,以保证铸件的尺
寸精度,是床身大批量生产时的合理
方案。
二、分型面的选择
4)分型面的选择,应便于下芯、扣箱(合型)及检查型腔尺 寸。如图方案a)无法检查铸件厚壁是否均匀;而方案b)通
过增设一中箱,可在扣箱前检查壁厚以保证铸件壁厚均匀。
第三节 铸造工艺参数的确定
起模斜度≤ 测量面高度/ mm 金属模样、 塑料模样 α α/mm 木模样 α α/mm 测量面高度 /mm 起模斜度≤ 金属模样、 塑料模样 α α/mm 木模样
第二篇第3章砂型铸造

§2 浇注位置与分型面的选择 浇注位置是指浇注时铸件在铸型中所处的位 置。 选择浇注位置的 目的是为了保证铸件质量。 浇注位置的选择原则如下: 1 .铸件的重要加工面应朝下。 避免出现气孔、砂眼、夹杂
等缺陷
2 .铸件的大平面应朝下。 3. 铸件薄壁部分置于铸型下部或使其处于垂直 或倾斜位置。
52
增加外芯
方案A
上 下
凸台 妨碍起模
机床导轨 重要基准 应朝下
方案B
易产生错箱。可用于单件 生产。
53
Ⅱ
Ⅰ
型芯、型腔 大部分位于下 箱,方案合理
上箱 太高
54
上述选择浇注位置和分型面的诸原 则,对于某个具体铸件来说,往往难以 全面顾及,有时甚至相互矛盾。 因此,需要提出几种方案,抓住主 要矛盾,进行分析比较。一般说来,对 质量要求高的铸件应优先满足浇注位置 的要求,对质量要求不高或外形复杂, 生产批量又不大的铸件,应优先考虑分 型面。
第三章
砂型铸造
§1 造型方法的选择 §2 浇注位置与分型面的 选择 §3 工艺参数的确定 §4 综合分析举例
1
第三 章
生产特点:
砂型铸造
砂型铸造适合于各种金属的铸造生产,对铸件 的尺寸、形状基本没有限制。工装设备简单, 成本低,适合各种生产形式。 砂型铸造工艺方案的内容
为了获得健全的铸件、减少铸型制造的工 作量,达到优质高效益生产的目的,必须合理 的制订铸造工艺方案,并绘制出铸造工艺图。 其内容包括: 2
刮板造型
30
二 .机器造型(芯)
1.机器造型原理 如图所示
31
填 砂
进气 升 起
32
落 下 排气
撞 击
33
机械制造基础:03砂型铸造
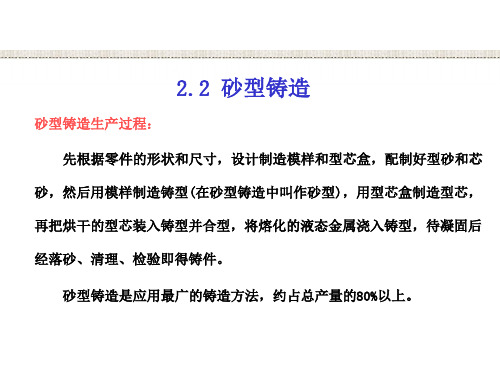
2.2 砂型铸造
图2-27 车床床身、锥齿轮的浇注位置
图2-28 吊车卷筒浇注位置
2.2 砂型铸造
2)铸件的大平面尽可能朝下 原因: 避免产生夹砂缺陷(上表面因热辐射造成膨胀、强度下降,容易拱
起或开裂)
图2-29 钳工平板较大的薄壁部分应置于铸型下部或垂直、倾斜位置 原因:防止浇不到或冷隔.
原因:便于造型操作和降低
模板制造费用。
图2-33 起重臂的分型面
2.2 砂型铸造
图2-34 三通铸钢件的分型面
2.2 砂型铸造
2)尽量避免活块、减少型芯数量,尽量采用砂垛代替型芯 原因:节省造芯操作和芯盒费用。
第一种方案需两个活块 第二种方案不需活块
图2-35 支架的分型方案
2.2 砂型铸造
图3-36 底座的分型方案 第一种方案为分模造型,上下内腔均需型芯 第二种方案为整模造型,沙垛代替型芯
单件生产:30— 50mm, 成批生产:15—20 mm, 大量生产:12—15 mm。
2.2 砂型铸造
2、起模斜度 为了使模样(或型芯)便于从砂型(或芯盒)中取出,凡垂直于分型面的立
壁在制造模样过程中必须留出一定的倾斜度,称为起模斜度 。 影响因素:立壁高度、造型方法及模样材料。 1) 立壁愈高,斜度愈小; 2) 机器造型比手工造型小; 3) 木模比金属模大; 4) 内壁应比外壁大
2.2 砂型铸造
图2-24 多触头高压微振造型机的工作原理示意图
2.2 砂型铸造
➢ 射沙造型
紧砂原理:采用射砂和压实复合方法紧实型砂。 特点:
1) 无砂箱的垂直分型的铸型; 2) 生产率高(240~300箱/小时); 3) 大批量生产小型简单件。 缺点: 1)垂直分型,下芯困难; 2) 模具精度要求高。
- 1、下载文档前请自行甄别文档内容的完整性,平台不提供额外的编辑、内容补充、找答案等附加服务。
- 2、"仅部分预览"的文档,不可在线预览部分如存在完整性等问题,可反馈申请退款(可完整预览的文档不适用该条件!)。
- 3、如文档侵犯您的权益,请联系客服反馈,我们会尽快为您处理(人工客服工作时间:9:00-18:30)。
图3-3 平板浇注时的位置 •e)尽量减少型芯的数目,最好使型芯位于下型以便下芯和检 查,同时应保证型芯在铸型中安放牢靠、排气通畅。
(2)分型面的选择 分型面为铸型组元间的接合面,选择分型面应考虑以下原则: a) 分型面应尽量采用平面分型,避免曲面分型,并应尽量选在最大截 面上,以简化模具制造和造型工艺。见图3-4。
3)最小铸出孔及槽 零件上的孔、槽、台阶等应从铸件质量及经济方 面考虑。较大的孔、槽等应铸出来,以便节约金属和机构加工工时, 同时还避免铸件局部过厚所造成的热节,提高铸件的质量,较小的 孔槽,则不宜铸出,直接加工反而方便;如有特殊要求,且无法实 行机加工的孔如弯曲孔,则一定要铸出。
(4)收缩余量 指为了补偿件收缩,模样比铸件图样尺寸增大的数值。 (5)工艺补正量 由于工艺上的原因,在铸件相应部位非加工面上增 加的金属厚度称为工艺补正量。工艺补正量可粗略地按下述经验公 式来确定, e≤0.002L, 式中e为工艺补正量(mm); L为加工面到 加工基准面间的距离(mm)
c) 地坑造型
组芯造型是用若干块砂芯组合成铸型,而无需砂箱。它可
提高铸件的精度,但成本高。适用于大批量生产形状复杂的 铸件。
d) 组芯造型
整模造型的模样是整体的,分型面是平面,铸型型腔全部在半
个铸型内,其造型简单,铸件不会产生错型缺陷。适用于铸件最 大截面在一端,且为平面的铸件。
e) 整模造型
第三节 砂型铸造
用型砂紧实成型的铸造方法称为砂型铸造。砂型铸造是应用最广泛 的一种铸造方法,其主要工序包括:制造模样,制备造型材料、造 型、造芯、合型、熔炼、浇注、落砂、清理与检验等。 一、造型方法的选择
二、铸造工艺设计
一、造型方法的选择
用造型混合料及模样等工艺装备制造铸型的过程称为造型。造型是 砂型铸造的最基本工序,通常分为手工造型和机器造型两大类。
两箱造型是造型的最基本方法,铸型由成对的上型和下型构成,操
作简单。适用于各种生产批量和各种大小的铸件。
a) 两箱造型
三箱造型的铸型由上、中、下三型构成。中型高度需与铸件两个分
型面的间距相适应。三箱造型操作费工。主要适用于具有两个分型 面的单件、小批生产的铸件。
b) 三箱造型
脱箱造型主要采用活动砂箱来造型,在铸型合型后,将砂箱
挖砂造型的模样是整体的,但铸件分型面为曲面。为便于起模,
造型时用手工挖去阻碍起模的型砂、其造型费工、生产率低,工 人技术水平要求高。用于分型面不是平面的单件、小批生产铸件。
f) 挖砂造型
假箱造型是为克服挖砂造型的挖砂缺点,在造型前预
先做个底胎(即假箱),然后在底胎上制下箱,因底胎 不参予浇注,故称假箱。比挖砂造型操作简单,且分型 面整齐。适用于成批生产中需要挖砂的铸件。
c) 震压紧实
微震紧实是在加压坚
实型砂的同时,砂箱和 模板作高频率、小振幅 震动。此方法生产率较 高、紧实度均匀、噪声 小。广泛用于成批生产 中、小型铸件。
e) 微震紧实
抛砂紧实是利用离心
力抛出型砂,使型砂在 惯性力下完成填砂和坚 实。该方法生产率高, 能量消耗少、噪声低、 型砂坚实度均匀、适用 性广。主要适用于单件、 小批、成批、大量生产 中、大型铸模样造型,它可降低模样成本,
节约木材,缩短生产周期。但生产率低,工人技术水平要求高。 用于有等载面或回转体的大、中型铸件的单件、小批生产、如 带轮、铸管、弯头等。
i) 刮板造型
(二)机器造型
机器造型是指用机器全部完成或至少完成紧砂操作的造型工序。 机器造型铸件尺寸精确、表面质量好、加工余量小,但需要专用 设备,投资较大,适合大批量生产。 1. 机器造型方法分类 常用的机器造型方法有:压实紧实、高压紧实、震击紧实、震压 紧实、微震紧实、抛砂紧实、射压紧实、射砂紧实。 2. 各种机器造型方法的主要特征及其适用范围
(一)手工造型
手工造型是全部用手工或手动工具完成的造型工序。手工造型 操作灵活、适应性广、工艺装备简单、成本低,但其铸件质量 差、生产率低、劳动强度大、技术水平要求高,所以手工造型 主要用于单件小批生产,特别是重型和形状复杂的铸件。 1. 手工造型方法分类 根据砂型的不同特征,手工造型方法可分为:两箱造型、三箱 造型、脱箱造型、地坑造型、组芯造型;根据模样的不同特征, 手工造型方法可分为:整模造型、分模造型、挖砂造型、假箱 造型、活块造型、刮板造型。各种手工造型方法的示意图如图 所示。 2. 各种手工造型方法的主要特征及其适用范围
图4-1 熔模铸造流程图
图3-2 熔模铸造过程示意图
(二)熔模铸造的主要特点及适用范围
1)铸件的精度和表面质量较高,尺寸公差等级可达IT14-IT11, 表面粗糙度Ra值可达12.5mm-1.6mm。
2)适用于各种合金铸件。
3)可制造形状较复杂的铸件,铸出孔的最小直径为0.5mm,最小 壁厚可达0.3mm。
a) 不正确
b) 正确
图3-8 分型面的位置应能避免披缝
铸造工艺参数的选择 (1) 加工余量 指为保证铸件加工面尺寸和零件精度,在铸件工艺 设计时预先增加而在机械加工时切去的金属层厚度。零件上需要加 工的表面,应需有适当的加工余量。铸件加工余量的大小取决于铸 件的材料、铸造方法、铸件尺寸与复杂程度、生产批量、加工面与 基准面的距离及加工面在铸型中的位置、加工精度要求等。灰铸铁 件较铸钢件线收缩率小、熔点低,铸件表面较光洁、平整,故其加 工余量小,铸钢件因浇注温度高、表面粗糙、变形大、其加工余量 应比铸铁件大;非铁合金铸件表面光洁、且材料昂贵、加工余量应 比铸铁件小;铸件的尺寸愈大或加工面与基准面的距离愈大,铁件 的尺寸误差也愈大,故余量也应随之加大;
f) 抛砂紧实
射压紧实是使压缩空
气骤然膨胀,将型砂射 人砂箱进行填砂和坚实, 再进行压实。该方法生 产率高,坚实度均匀, 砂型型腔尺寸精确、表 面光滑、工人劳动强度 低、易于自动化、但造 型机调整维修复杂。主 要适用于大批、大量生 产的形状简单的中、小 型铸件。
g) 射压紧实 •射砂紧实是用压缩空气将型(芯)砂 高速射入砂箱或芯盒而进行紧实。因 其将填砂、紧实两个工序同时完成, 故生产率高,但用于造型,其坚实度 不高、需进行辅助压实。广泛用于制 芯、并开始用于造型。
j) 假箱造型
分模造型是将模样沿最大截面处分成两半,型腔位于上、下两个砂 箱内,造型简单省工。常用于最大截面在中部的铸件。
g) 分模造型
活块造型是在制模时将铸件上的妨碍起模的小凸台,肋条等这些部
分作成活动的(即活块)。起模时,先起出主体模样,然后再从侧 面取出活块。其造型费时,工人技术水平要求高。主要用于单件、 小批生产带有突出部分、难以起模的铸件。
a) 不正确
b) 正确
图3-4 分型面应选在最大截面处
b)尽量将铸件全部或大部放在同一砂箱以防止错型、飞翅、毛刺等 缺陷,保证铸件尺寸的精确。见图3-5。
a) 不合理
b) 合理
图3-5 分型面的位置应能减少错型、飞翅
c)应使铸件的加工面和加工基准面处于同一砂箱中。见图3-6。
a) 不合理
b) 合理
(6)分型负数 指为抵消铸件在分型部位的增厚,在模样上相应 减去的尺寸。砂型的分型面一般不可能很平整,因此干型或表面 烘干型合型后,上下型不能密合,金属液就有可能从分型面处溢 出,即“跑火”。为了防止跑火,就要在下型的分型面上铺设泥 条、油泥条或石棉绳等,使上、下型接触面密封,这样就使上箱 抬高,增加了铸件的高度或铸件顶面的厚度。制做模样时,为了 使模样符合零件图上尺寸的要求,在模样上相应减去这个抬高的 尺寸,即为分型负数。
b)重要加工面、耐磨表面等质量要求较高部位应置于下面或侧面。 见图3-1。
图3-1 汽缸浇注时的位置
c)具有大面积的薄壁铸件,应将薄壁部分放在铸型的下部,同时要 尽量使薄壁部分处于垂直位置或倾斜位置。见图3-2。
图3-2 箱盖浇注时的位置
d)具有大平面的铸件,应将铸件的大平面朝下。见图3-3。
4)工艺过程较复杂,生产同期长,制造费用和消耗的材料费用 较高,多用于小型零件(从几十克到几千克),一般不超过25kg。
二、金属型铸造
金属型铸造又称硬模铸造,是将液体金属浇入金属铸型,在重 力作用下充填铸型,以获得铸件的铸方法。 (一)金属型 为保证使用寿命,制造金属型的材料具备如下的性能:高的耐热 性和导热性,反复受热不变形,不破坏;一定的强度、韧性及耐 磨性;好的切削加工性能。金属型材料一般选用铸铁、碳素钢或 低合金钢。 (二)金属型铸造的工艺特点 1. 金属型预热 金属型预热温度主要通过试验来确定,一般不低 于150℃。 2. 刷涂料 金属型表面应喷刷一层耐火涂料(厚度为0.3mm- 0.4mm),以保护型壁表面,免受金属液的直接冲蚀和热击。
图3-6 螺栓塞头的分型面
d)若铸件的加工面很多,又不可能全部与基准面放在分型面的同一 侧时,则应使加工基准面与大部分加工面处于分型面的同一侧。 e)尽量减少分型面的数目,最好只有一个分型面。见图3-7。
a) 不合理
b) 合理
图3-7 分型面数目的确定
f)铸件的非加工表面上,尽量避免有披缝。见图3-8。 •g)分型面的选择应尽量与铸型浇注时位置一致。
第四章 特种铸造
一、熔模铸造 二、金属型铸造 三、压力铸造
一、熔模铸造
熔模铸造是用易熔材料制成模样,然后在模样上涂挂若干
层耐火涂料制成型壳,经硬化后再将模样熔化,排出型外, 从而获得无分型面的铸型。铸型经高温焙烧后即可进行浇注。 (一)熔模铸造的工艺过程 熔模铸造的工艺过程包括:蜡模制造、结壳、脱蜡、焙烧和 浇注等,其流程图及铸造过程示意图如下:
二、铸造工艺设计
铸造工艺图是表示铸型分型面、浇冒口系统、浇注位置、型芯结构 尺寸、控制凝固措施(冷铁、保温衬板)等的图样。图中应表示出: 铸件的浇注位置、分型面、型芯的数量、形状、尺寸及固定方法、 加工余量、起模斜度、浇口、冒口、冷铁的尺寸和位置。 1. 铸造方案的确定 (1)浇注位置的选择 浇注位置的选择应考虑以下原则: a)体积收缩大的合金及壁厚差较大的铸件,应按定向凝固的原则, 将壁厚较大的部位和铸件的热节部置于上部或侧部,以便设置冒口 进行补缩。