FMEA表格使用说明
FMEA表格使用说明
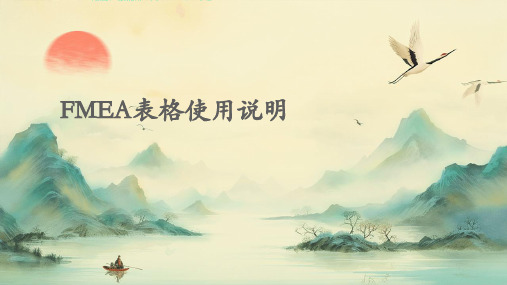
失效起因
失效起因:是指导致失效模式出现的原因或机理。 描述失效起因时,应深入分析并找出根本原因,以便采取有效的预防措施。
风险优先数
风险优先数:是根据失效模式、失效影响和失效起因的严 重程度、发生频率和检测难度等因素综合评估得出的一个 数值。
风险优先数用于确定哪些失效模式需要优先处理,以便降 低其对产品或系统的风险。
分析每个故障模式的可能原因, 记录在FMEA表格中。
列出所有功能和性能要求
在FMEA表格中列出分析对象的 功能和性能要求,作为分析的基 础。
评估风险优先数
根据故障模式的影响和故障原因 的严重程度,评估每个故障模式 的风险优先数,记录在FMEA表 格中。
分析风险优先数
比较风险优先数
将每个故障模式的风险优先数与其他故障模式进行比较,确定优先级较高的故障模式。
定义分析范围
确定FMEA分析的范围,包括需要分 析的边界条件、环境条件、操作条件 等。
填写FMEA表格
识别潜在的故障模式
根据功能和性能要求,识别出可 能发生的故障模式,并记录在 FMEA表格中。
确定故障模式的影响
评估每个故障模式对系统、子系 统或组件的性能和功能的影响, 记录在FMEA表格中。
确定故障原因
素对电源电路性能的影响。
案例三:医疗器械包装FMEA分析
总结词
医疗器械包装FMEA分析对于确保医疗器械的安全性和 有效性至关重要。
详细描述
在医疗器械包装FMEA分析中,需要对医疗器械包装的 各个组成部分进行详细的分析,包括包装材料、结构、 密封性能等。需要考虑这些组成部分在各种工况下的性 能表现,以及它们之间的相互影响。同时,还需要考虑 环境因素、使用条件和运输等因素对医疗器械包装性能 的影响。此外,还需要考虑医疗器械的特殊要求,如无 菌、防潮、防震等,以确保医疗器械的安全性和有效性 。
{品质管理FMEA}设计FMEA表格的应用

{品质管理FMEA}设计FMEA表格的应用设计潜在FMEA中的“顾客”不仅仅指“最终使用者”,还包括负责整车设计或更高一层总成设计的工程师/设计组以及负责制造、装配和服务的过程工程师/设计组。
DFMEA不是靠过程控制来克服设计中的潜在缺陷,但是必须从顾客的角度出发,考虑制造/装配过程中技术的/体力的限制。
例如:●必要的拔模(斜度)●表面处理的限制●装配空间/工具的可接近性●钢材淬硬性的限制●公差/过程能力/性能DFMEA还应该考虑产品维护(服务)及回收的技术/体力的限制,例如:●工具的可接近性●诊断能力●材料分类符号(用于回收)4.1.1设计FMEA的开发DFMEA工作应从列出设计期望做什么和不期望做什么的清单,即设计意图开始。
顾客的希望和需求应该包括在内,它们可以通过质量功能展开(QFD)、车辆要求文件、已知的产品要求和/或制造/装配/服务/回收要求等来确定。
期望特性的定义越明确,就越容易识别潜在的失效模式,进而采取预防/纠正措施。
DFMEA应该从所要分析的系统、子系统或零件的框图开始。
其目的是为了明确该框图所表征系统、子系统或零件的输入、功能及其输出、各个项目之间的主要关系。
框图中说明了分析中包括的各个项目之间的主要关系,并建立了分析的逻辑顺序。
用于DFMEA准备工作中的所有这种框图的复制件应伴随FMEA的全过程。
4.2过程FMEAPFMEA的价值体现在如下五个方面,并且正是由于这五个方面的原因减少了过程失效的风险:●确定过程功能和要求;●确定与产品和过程相关的潜在失效模式;●评价潜在失效对顾客的产生的影响;●确定制造或装配过程潜在失效的起因,确定减少失效发生或找出失效条件的过程控制变量;●编制潜在失效模式分级表,建立考虑纠正措施的优选体系;●记录制造或装配过程的结果4.2.1过程FMEA质量目标过程FMEA质量目标:1、过程改进FMEA推动过程改进作为主要目标,重点在防错方法。
2、高风险失效模式FMEA对小组识别的所有高风险失效模式都引起重视。
FMEA程序(含表格)
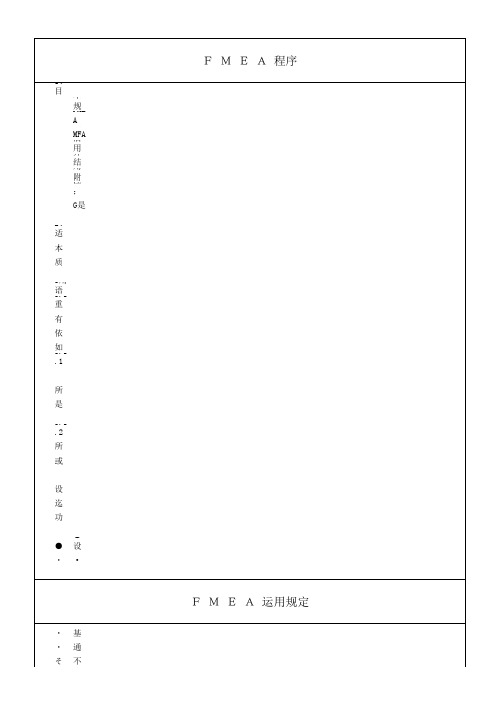
F M E A 运用规定
更により起こり得る相互作用、及び市場でのこれまでの経緯に焦点を当てる。 变更 所引起的相互作用、和市场现在的焦点都有在本范围内。 ケース3:すでに既存設計及びプロセスのFMEAが存在していて、既存の設計又はプロセス 路径3; 所有的已存设计和过程的FMEA都存在,将已存设计和过程 を、新規の環境、ロケーション又は適用方法で用いる場合。 用于新规环境、新部位和新的适用方法时。 (工場変更、別機構の機台での生産等)FMEAの適用範囲は、新しい環境又はロ (工厂变更、在其它机构的机器上生产等),FMEA的适用范围作为
F M E A 运用规定
·基本上,在量产用图纸完成前完成 ・基本的に、量産用図面が発行される前に完成。 ·通过产品开发的全阶段,进行变更,得到追加信息时 ・製品開発の全段階を通して、変更が行われたり、追加情報が得られたりした場合、絶えず
それに合わせて更新。 不断更新。 ●設計FMEAでは、設計意図の通りに製造/組立が行われるものと想定して製造又は組立の ●在设计FMEA中,通过设计意图设想制造和组装产品或对组装过程之间可能发生的 プロセスの間に生じる可能性のある潜在的故障モード又は原因/メカニズムについては、プ 潜在缺欠性故障模式和原因、设备,使用过程 ロセスFMEAで扱う。(設計FMEAに含めても差し支えはない。) FMEA处理。(包括设计FMEA也没关系) ●設計FMEAでは、設計に潜在する弱点をプロセス管理によって克服するのではなく、設計 ●设计FMEA中对管理中难以克服的弱点在设计中 段階で対処するのが基本である。 应当提前处理。 ●設計FMEAでは、工程能力/工程性能などの製造/組立プロセスの技術的/物理的限界を ●在设计FMEA中,要考虑到工程能力、工程性能等的制造/组装过程技术/ 考慮に入れる。 物理界限。 ●設計FMEAでは、製品保全及びリサイクルの技術的/物理的限界も考慮に入れる。 ●在设计FMEA中要考虑产品保全和再循环技术/物理性界限 ●設計の弱点のために発生し得る潜在的故障モードの影響及び回避策は、設計FMEAで扱う。 ●使用设计AMEA避免设计弱点所发生的潜在故障状的影响 ●設計FMEAの顧客は、“最終ユーザー”だけでなく車両又はより高レベルの組立品の設計 ●设计FMEA的用户不仅是最终用户,而且包括具有车辆或更高水平的组件设计责任的 責任を有する技術者(チーム)及び製造、組立、サービス等の部門における製造 技术者(团队)及在制造、组装、服务等部门拥有制造·过程责任的技术者。 ・プロセス 3.3 过程FMEA(工程FMEA) 設計の意図した機能 具有设计意图功能、性能的产品,在量产工程中是否可以生产的评定中使用 ・性能を持つ製品が量産の工程で生産可能か否かを評価する際に用い、工 程の不具合や不良を未然に不良発生を防止するための対策や管理方法を明確にする。プロセス 要明确为了防止工程不良和产品不良的处理方法和管理方法。 FMEAは、プロセス中に存在する弱点を製品設計変更によって克服するものではない。 过程FMEA不能因产品设计变更克服过程中存在的弱点 ●プロセスFMEAの実施タイミング ●过程FMEA的实施时机 ・ ·在实行可能性研讨阶段前进行 実行可能性検討段階の前に行う。 ・ ·在量产用具类研讨前进行 量産用治工具類を検討する前に行う。 ・ ·从每个要素部件到组装品对所有制造作业都要考虑 個々の要素部品から組立品に至るまでの、すべての製造作業を考慮する。 ●プロセスFMEAの顧客とは、通常“最終ユーザー”とするべきであるが、顧客を次工程や ●过程FMEA的客户通常应叫作最终用户,但是对后工程或 下流工程の製造、組立作業、サービス作業又は政府規制とすることもできる。 下一个工程的制造、组装作业、服务作业或政府规定的也称为客户 4. FMEA的制作 由有责任的DXC制造部进行FMEA的制作、设计、和发行, 对已作成的FMEA,本社也有责任运用和管理。但是, 经和DXC制造商部协商后,按照需要可由本社制作。有关制作要领, 请参照DXC的社内标准(TS NO. TSZ22410) 这个规定中对FMEA的记载内容进行了说明, 4.1 FMEA适用的3种情况; 进行FMEA的3个基本条件如下; 路径1; 进行新规设计、新技术、新过程时 FMEA的适用范围是设计、技术、和过程的全部范围 路径2; 所有的已存设计和过程的FMEA都有存在,变更已存设计和过程时 FMEAR的适用范围,对设计和过程的变更点、
FMEA表格填写说明

建议措施
20 21 22
责任及目标完成日 期 采取措施 纠正后的RPN
*三种设计控制方法
1防止起因或失效模式出,或减少出 现率; 2 查明起因并达到纠正措施 3 查明失效模式 优先运用1,次2,后3。 指零部件、子系统或系统投产前, 能否探测出其已发生之缺点,分为1 —10级 RPN = S x O x D 风险度=严重度x频度x探测度 *RPN大者先采取纠正措施。 *无建议措施,须填写“无”。 *零组件之设计修改才能降低严重度 。 增加探测缺点的可能性,增咖品管 检验不一定有效,需要修改过程和/ 或设计。
17 18
不易探测度 风险顺序(RPN)
1防止起因或失效模式出,或 减少出现率; 2 查明起因并达到纠正措施 3 查明失效模式 优先运用1,次2,后3。 指零部件、子系统或系统投产 前,能否探测出其已发生之缺 不易探测度 点,分为1—10级 RPN = S x O x D 风险顺序(RPN) 风险度=严重度x频度x探测度 *RPN大者先采取纠正措施。 *无建议措施,须填写“无” 。 *设计确认/验证工作→只影响 不易探测度,只有修改设计→ 严重度减少 *可考虑但不局限于下列措 施: 建议措施
填入组织部门及个人,预计完成日 期 简要记载执行状况,并记下生效日 期 将新的RPN值填入
过 程 (P) 项 目 FMEA编号 项目 过程责任
4
编制者
5
年型/车型
6 7 8 9 10 11 12 13 14 15
AIAG VDA FMEA PFMEA 第一版 中文 FMEA第五版表格

车辆:升降车窗玻璃
3mm
一步分析。
值不一定是最高的。
的量级影响严重度的话。例如“
无冲压裂纹”,失效模式可能是 失效分析可从失效模式、失效影
其它可能的过程特性-“从料箱
“裂纹长度0~10mm”-严重度4, 响或失效原因开始,假如失效链
拿轴承时不刮伤表面”,“轴承
“裂纹长度10~20mm”- 严重度 是精确的话。
失效原因,也就是说一个不足就 以及如何影响这三个方面(内部
公司可自行选择其它方法
可在失效分析(FE)完成后进行倒 失效模式将是这些产品特性的不 是一个失效原因。
工厂、客户工厂、过程步骤、车
如果产品特性有规范上下限的 新失效原因--- 当考虑“失效原
推。
足。
辆用户)。
话,要分别考虑上下限的失效模 因”时,新的“作业要素的功能
步骤2:结构分析
步骤3:功能分析
步骤4:失效分析
步骤5:PFMEA 风险分析
步骤6:优化
1. 过程项目
2. 过程步骤
3. 作业要素
1. 过程项目的功能 2. 过程步骤的功能和 3. 作业要素的功能和 1. 失效影响 (FE)
2. 过程步骤的失效模 3. 作业要素的失效原 当前针对FC的预
当前针对FC或FM
放入制具中时不用太大力”,“
7,“裂纹长度20mm以上”- 严
拧紧螺栓直到
拧紧螺栓直到扭矩灯亮绿,此时
和控制措施。
不能再用力”,“拿取正确的润
玻璃升降电机总成
OP# 30 压入球面轴承
作业员
过程:按控制信号转化电能为机 械能; 内部工厂:在周期时间内装配, 无报废和返工; 客户工厂:电机安装到车门不会 出现停线/停顿、拣选、遏制; 用户:升降车窗玻璃
制程FMEA填写说明
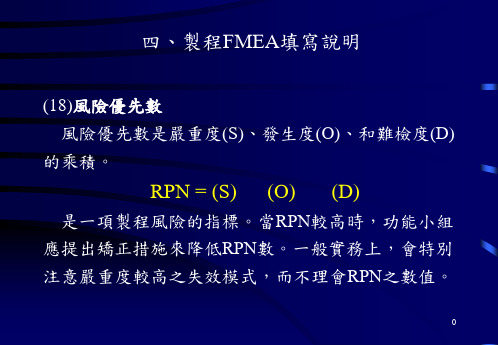
(4)考慮採取減額定(Derating)之概念:選用之零組件必須要能承受規定 之應力水準。如系統之要求200伏特電壓,則採用能承受300伏特電壓之 元件,使其強度(Strength)能遠操過所承受之應力(Stress)。
18
七、環境之控制:如前所述,一般產品使用之環境條件(如溫度、溼度、 高度、衝擊力等)均有限制。因此,吾人對其使用環境亦須有所控制。
(6)增加備用元件之考量﹔
(7)對可靠度及成本或重量限制等設計參數之間取捨作一權衡。
(8)以預防維修(Preventive Maintenance)及矯正維修(Corrective Maintenance) 兩種方式提昇系統之可維修度(Maintainability)並建立對不可靠零組件置換 /維修時間的保守估計:可維修度是指一個失效系統能在特定的停機(Downtime) 期限內恢復運作之機率。 此期限包含了行政作業、修理及後勤支援等時間。
11
六、FMEA 精義與要項說明
3. 難檢度評估 難檢度評估重點在於評估所使用的管制措施對於失效模 式偵測之困難度,也有人以偵測出之時機來評估,原本 只見於評點方式,Zigmund M. Bluvband[6] 針對MILSTD-1629A之不足,提出QUALITY ASSURANCE TASK,主要即增加一篩選因子(SCREENING FACTOR, γ),則(1-γ)就相當於是難檢度,但目前MIL-STD-1629A 尚未採用。
1
五、FMEA 實施步驟
1.任務確立及 實施對象
8. 完成FMEA表
2.決定 分析層次
FMEA第五版表格(带实例)--2019.8.17讲课教案

系统/子系统/部件 名称:
系统零部件的名称
PFMEA编号: 按公司内部规定
过程负责人: 即PFMEA负责人
保密等级: 例如:对外/机密/内部使用
步骤2:结构分析
步骤3:功能分析
步骤4:失效分析
步骤5:PFMEA 风险分析
步骤6:优化
备注
严重度 (FE) FC发生度 (O) FC/FM 探测度 AP (行动优先
过程特性。
能要求。
1 品中可探测的。 过程特性”中相 确定要 1
1 L,
的额 D 体 日 待 施以 日 1 1 1 L, 小组使
电机装配 用以组成 的操作或 如果未知的话就写NA。
对应的不足将填写在失
0 失效模式其实也是 应的不足。
实施的 0
0 NA
外措 值 人 决 及文 0 0 0 NA 用
线,其是 过程,例 工位的差
步骤1:范围定义 公司名称: 负责PFMEA的 公司
工厂地点: 地理位置
顾客名称: 顾客名或过程族名称 车型年/平 顾客车型年型/平台/款
台: 型
任务描述: PFMEA项目名称 PFMEA开始日期: PFMEA开始日期 PFMEA修订日期: 最新修订日期
跨职能小组: 小组名单
Process Failure Mode and Effects Analysis (Process FMEA) 过程失效模式及效果分析(过程FMEA)
过程名 操作或工 来识别影 内容,可分成几类。
什么:例如轴承在电机 成的,包括与4M相应的 不能实现(上一层级)功 ~ 缺陷)必须是在产 业要素的功能和 的和/或 ~ 要实施的控制措施 ~ M, C L O值 低 具 月 : 的措 月 ~ ~ ~ M, PFMEA
第五版FMEA表格(含SOD与AP说明)

S
O
D
特殊特 性
AP
备注
持续改善 历史/变更 授权(适用
问题# 时)(这一
类是可选 项)
1.过程项
结构分析(第2步) 2.过程步骤
公司名称 制造地址 顾客名称 年型/平台
分析(第2步)
公司名称: 制造地址: 顾客名称: 年型/平台:
3.过程作业要素 1.过程项功能
功能分析(第3步)
策划准备(第1步)
功能分析(第3步) 2.过程步骤的功能和产品特性
跨职能团队: 风险评估(第5步)
现行探测控制(DC)
第5步)
探测度 (D)
AP
特殊特性
筛选器代码 (选填)
预防控制
PFMEA ID编号 过程职责 保密级别
探测措施
ቤተ መጻሕፍቲ ባይዱ
改进措施(第6步) 责任人 目标完成时间 状态
PFMEA ID编号: 过程职责: 保密级别:
改进措施(第6步) 采取基于证据的措施
实际完成时间
策划准备(第1步)
析(第3步)
失 严
3.过程作业要素的功能和过程特性
1.失效影响FE 重 度
(S)
AIAG & VD
失效分析(第4步)
作业步骤的失效模式 (FM)
作业要素的失效原因(FC)
AIAG & VDA PFMEA
现行预防控制(PC)
发生度 (O)
项目: PFMEA开始日期: PFMEA修订日期:
- 1、下载文档前请自行甄别文档内容的完整性,平台不提供额外的编辑、内容补充、找答案等附加服务。
- 2、"仅部分预览"的文档,不可在线预览部分如存在完整性等问题,可反馈申请退款(可完整预览的文档不适用该条件!)。
- 3、如文档侵犯您的权益,请联系客服反馈,我们会尽快为您处理(人工客服工作时间:9:00-18:30)。
如何能 預防及發現 這種 原因及錯誤? 這種方法 發現這種問題 有多好?
34
6
跟
催
采取有效的预防及矫正措施,以及针对这些行动的跟催是需要的,但不用过分
强求。应该和所有被影响的单位沟通措施行动。一个彻底周详考虑和充分开发 的FMEA如果没有实际有效的预防和矫正措施,其价值将有限。 担当职责的工程师是负责确保所有的建议措施都已经实施或适当的对策。 FMEA是一分份动态文件,应该始终反映出最终的评估,以及最终的适切措施, 包括那些在开始量产之后所发生的措施。 A.审查设计、过程和图样,确保建议措施已经被实施,
见的催化剂,从而提高整个集体的工作水平。
除了负责工程师对FMEA具有经验和小组协助之外,在活动中拥有一 位有经验的FMEA专家以协助该小组是有一定帮助的。
11
设计FMEA是一份动态文件,且应该:
.在一个设计概念最终形成之时或之前开始, .在产品开发各阶段中,当设计有变更或获得信息增加时,要及 时、不断地修改,以及 .在最终在产品加工图样完成之前全部结束。 考虑到制造/装配的要求是相互联系的,设计FMEA在体现设计意图
B.确认该项变更编入设计/组装/制造文件中,
C.审查设计/过程FMEAs、特别的FMEA应用和控制计划
7
设 计F M E A
简 介
设计FMEA主要是由负责设计的工程师/小组采用的一种分析技术,用 来保证在可能的范围内已充分地考虑到,并指明各种潜在的失效模式及 其相关的起因/机理。应该评估最终的产品以及每个与之相关的系统、 子系统和零组件。FMEA以其最严密的形式总结了设计一个零部件、子 系统或系统时,一个工程师和设计小组的设计思想(包括:根据以往的
经验和教训,对可能出现问题的项目的分析)。这种系统化的方法体现
了一个工程师在任何设计过程中正常经历的思维过程,并使之规范化、
文件化。
8
设计FMEA能够透过以下几方面支持设计过程,以降低失效风险: .有助于对设计要求和设计方案进行客观评价; .有助于对制造和装配要求的最初设计; .提高在设计/开发过程中,考虑潜在失效模式及其对系统和运行冲击 的可能性; .为全面、有效的设计试验和开发项目的规划,提供更多的信息;
17
子系统FMEA的范围 一个子系统FMEA一般是一个较大系统的子组。例如,前悬吊系统 是底盘系统的一个子组。然而,子系统FMEA重点是确保所有接口 与互动都涵盖了整个由不同零组件所组成的子系统。 零组件FMEA的范围 一个零组件FMEA一般重点是在于一子系统的子组FMEA。例如, 支撑架是前悬吊(其是底盘系统的一个子系统)的零组件。
念形成阶段),应该使用临时性编号。
填入时,用尽可能简洁的文字来说明被分析项目要满足设计意图的功能, 包括该系统运行的环境相关信息(如指定温度、压力、湿度范围、设计
寿命等,是计量值/可量测的)。如果该项目有多种功能,且有不同的
失效模式,要把所有功能都单独列出。
20
10、潜在失效模式
所谓潜在失效模式是指系统、子系统或零部件有可能未达到或未完成 项目/功能栏中所描述设计意图的种类(如预期的功能丧失)。这潜 在失效模式可能是更高一级子系统或系统的潜在失效模式的起因,也 可能是比它低一级的零部件潜在失效模式的效应。 对一个特定项目及功能,列出每一个潜在失效模式。前提是这种失效 可能发生,但不是一定发生。建议将以往错误案例(TGW,thingsgone-wrong)的研究、关切点、问题报告以及小组的“脑力激荡”的 审查作为出发点。 潜在失效模式可能只发生在特定的运行环境条件下(如热、冷、干燥、 灰尘等),以及在特定的使用条件下(如超过平均里程、不平的路段、 仅在城巿行驶等),应都考虑。 注:应该用“物理的”、专业性的术语来描述潜在失效模式,而不同 于顾客所见的现象。
服务/回收利用要求
等来源,应该综合地考虑。期望特性的定义越明确,就越容易识 别潜在
的失效模式,以采取预防/矫正措施。
15
系统 子系统 零组件: 产品类型(2) 核心小组
項目/失效 (9) 潛在 失效模式 (10)
设计责任:(3)编制者:(4) 关键日期:(6)
失效 潛在效應 (11)
嚴 等 重 級 度 13 12
POTENTIAL FAILURE MODE AND EFFECTS ANALYSIS (FMEA)
潜在的失效模式及效应 分析
朱 中 平 CARL CHU
1
FM EA概 要 何谓FMEA: 是描述为一组系统化的活动,其目的是: A:发现和评价产品/过程中潜在的失效及其失效效应 B:找到能够避免或减少这些潜在失效发生的措施
21
11、潜在失效效应 潜在失效的效应就是失效模式对功能的影响,就如顾客感受的一样。 要根据顾客可能发现或经历的情况来描述失效的效应,要记住顾客可
能是内部的顾客,也可能是外部最终的顾客。要清楚地说明该失效模
式是否会冲击到安全性,或与法规不符。该效应应该依据所分析的具 体系统、子系统或零部件来说明。还要记住不同级别的系统、子系统
10
小 组 努 力
在最初的设计FMEA过程中,负责设计的工程师被预期能够直接地、 主动地从所有有关部门来代表。这些专家和负责的领域应该包括,
但不限于:装配、制造、设计、分析/测试、可靠度、材料、质量、
服务和供货商,以及负责下一个较高阶或低阶的组装、系统、子系 统或零组件的设计部门。FMEA应该成为促进相关部门间充分交换意
和零件之间还存在着系统层次上的关系。比如,一个零件的断裂可能
引起总成件的振动,从而导致系统运行的中断。这种系统运行的中断 会引起性能下降,最终导致顾客的不满、这意味着需要尽可能预见失
.根据潜在失效模式对“顾客”的冲击,对其进行分级列表,进而建立 一
套设计改进、开发和查证的优先控制系统; .为建议和跟踪降低风险的措施,提供一个公开的讨论形式; .为将来分析研究售后巿场关切情况、评价设计更改及展开更先进的设 计提供参考。
9
顾客的定义
设计FMEA中“顾客”的定义,仅仅是指“最终使用者”,还包括负责车型设计 更高 一级装配过程设计的工程师/小姐,以及在生产过程中负责制造、装配和售后服 务的工程师。 FMEA全面实施要求对所有新的部件、更改的部件以及应用或环境有变化的沿用 零件进行设计FMEA。FMEA始于负责设计工作的工程师,但对有专有权的设计 来说,可能始于其供货商。
使该产品或过程呈现了相同的状况;由于每个小组的所在环境是独一无二的
,因此各自将会个别的评价(如:评价是主观的)。
5
图一
項目/失效
潛在失效模式與效應分析作業序列
潛在 失效模式 失效 潛在效應
嚴 等 重 級 度
潛在原因/ 發 生 失效機制 度
現行的 設計管制 預防 檢測
難 檢 度
R P N
建議措施
責任與 目標 完成日期
1、FMEA编号
填入FMEA文件编号,以便查询。 注:见表1,提供了项目1-22的范例。 2、系统、子系统或零部件名称及编号 注明适当的分析级别并填入所分析系统、子系统或零件的名称、编号。 FMEA小组成员必须对这构成的系统、子系统或零组件,决定其特定 的活动。实际的裁决其分界范围为系统、子系统或零部件,且必须被 FMEA小组所设定。下列提供了说明,并在附录F提供了一些例子。 系统FMEA的范围 一个系统可以被视为由多个子系统所组成,这些子系统通常由不同小 组所设计。有些典型的系统FMEAs可能涵盖了下列系统:底盘系统、 发动机系统或内装系统等。然而,系统FMEA的重点是确保所有的接 口与互动都涵盖了整个由不同子系统所组成的系统,以及与其他车辆 系统和顾客的互相影响。
够更容易、低成本地对产品过程进行修改,从而减轻事后修改危机。
FMEA能够减少或消除原因进行预防和矫正而带来更大损失的机会。
FMEA小组应该有充分的沟通和整合。
3
图一描述了一个FMEA应该被执行的程序,它并不是简单的把表格填满的案 例,而是进一步理解FMEA的程序,以消除风险和计划能确保顾客满意 的适当控制。 当FMEAs被展开,会有三种基本的个案。每个案例都有不同的领域和重点: 个案1:新设计、新技术或新过程。该FMEA的领域是完成设计、技术或过 程。 个案2:修改现有的设计或过程(假设现有的设计或过程已经有一个FMEA)。该 FMEA的领域应该在于修改设计或过程,有可能因为某修改和市场历史 反映而有交互影响。 个案3:在一个新的环境、地点或应用上,利用的现有的设计或过程(假设现有
的同时,还要保证制造/装配能够实现设计意图。对于制造或装配
过程中可能发生的潜在失效模式和/或其起因/机理。 当过程FMEA已包括了它们的识别、效应和控制时,则不需包含在设
计FMEA中,但也可包含。
12
设计FMEA不是靠过程控制来克服设计中潜在的缺陷,但的确要考 虑制造/装配过程中技术的/物质的限制。 设计FMEA不是靠过程控制来克服设计中潜在的缺陷,但的确要考 虑制造/装配过程中技术的/物质的限制。例如: .装配空间/工具可加工性 .表面处理的限制 .钢材硬度的限制 .公差/过程能力/性能
发布的日期。 7、FMEA日期
填入编制FMEA原始稿的完成日期及最新修订的日期。
19
8、核心小组
列出被授权以确定和/或执行任务的责任个人和部门名称(建议所有小 组人员的姓名、部门、电话、地址等,都记录在一分发表上)。
9、项目/功能
填入将被分析项目的名称和其他适切的信息(如编号、零件等级等)。 利用工程图纸上标明的名称并指明设计等级。在最初发布之前(如在概
C:将上述整个过程文件化
它是对设计过程的更完善化,明确必须做何种设计和过程 才能满足顾客的需要。
2
F M E A的 实 施
由于尽可能的持续改进产品和过程是企业的趋势,所以使用FMEA作为专门技
术应用,以识别并帮助减少潜在的隐忧一直是非常重要的。对于产品抱怨的研