lithium ion batteries
1 Lithium-Ion Batteries (国外专著)

C hapter 1S ynopsis of the Lithium-Ion Battery MarketsR alph J. B rodd1.1 IntroductionR esearch and development of the lithium-ion (Li-Ion) battery system began in the early 1980s at Asahi Chemicals 1and was first commercialized in 1990 by Sony Corp. for the Kyocera cellular phone in the 14,500 and 20,500 cell sizes. 2The fol-lowing year Sony introduced the 18,650 cell in its camcorder. (The nomenclature for cells size: the first two numbers indicate the cell diameter in millimeters and the last three are the cell length in tenths of millimeters.) Since its introduction, the Li-Ion market has grown to about $4 billion in 2005.T he higher volumetric and gravimetric energy storage capability are key charac-teristics of the Li-Ion battery system compared to the conventional sealed nickel–cadmium (Ni–Cd), nickel-metal hydride (Ni-MH), and valve-regulated lead acid (VRLA) battery systems (Fig. 1.1 ). For a given cell size, larger values of Wh/l and Wh/kg translate into smaller and lighter cells. These characteristics became the enabling technology for the proliferation of portable battery-powered electronic devices, especially notebook computers and mobile phone applications.S afety of the system has been a watchword for Li-Ion batteries. They have the ability to self-destruct if abused. Manufacturers are careful to ensure that the cells are safe in normal operations. In addition, cell designs incorporate features such as devices that shut off current flow when an abuse condition arises. The United Nations 3as well as the transportation agency in each country have requirements for testing to ensure a safe product for shipping.T able 1.1 shows the advantages and disadvantages of the Li-Ion and Li-Ion polymer rechargeable batteries.R.J. BroddB roddarp of Nevada, Inc ,2161 Fountain Springs Drive ,H enderson ,N V 89074 , USAr alph.brodd@M. Yoshio et al. (eds.), Lithium-lon Batteries, 1 DOI 10.1007/978-0-387-34445-4_1, © Springer Science + Business Media LLC 20092 R.J. Brodd1.2 Present Market for Li-Ion CellsLithium ion cells serve the small-sealed rechargeable battery market and compete mainly with the Ni–Cd and Ni-MH cells for the various applications. The Li-Ion cells are available in cylindrical and prismatic format as well as flat plate constructions. The cylindrical and prismatic constructions use a spiral-wrap cell core where the cell case maintains pressure to hold and maintain compression on the anode, sepa-rator, and cathode. The lighter-weight polymer constructions utilize the adhesivenature of a polymer/laminate-based electrolyte to bond the anode to the cathode.F ig. 1.1 E nergy density (Wh/l) and specific energy (Wh/kg) for the major small-sealed recharge-able battery systems A dvantages D isadvantages • C hemistry with the highest energy (Wh/g) and lightest weight (Wh/kg) •Relatively expensive • No memory effect • Lightest weight • Good cycle life • R equires protection circuitry for safety and toprevent overcharge and overdischarge• High energy efficiency • Nominal 3-h charge • Good high-rate capability• Not tolerant of overcharge and overdischarge• Thermal runaway concernsA dded advantages and disadvantages of Li-Ion polymer/laminate cells • Flexible footprint • Limited high rate capability •Plasticized electrolyte •More expensive • Internal bonding of anode • Poor low-temperature performance• Cathode and separator T able 1.1 A dvantages and disadvantages of Li-ion and Li-ion polymer rechargeable cells1 Synopsis of the Lithium-Ion Battery Markets 3 As a result, it does not need outside pressure to hold the electrodes in contact with each other. A light-weight polymer-aluminum laminate pouch can substitute for a heavier metal cell enclosure. All three constructions employ the same chemistries.T he sales of Li-Ion cells are shown in Table 1.2 .4The Li-Ion market is very competitive. The data for the competing Ni–Cd and Ni-MH cells are included for comparison purposes. The market growth for Li-Ion is spectacular and driven by the proliferation of portable electronic devices such as notebook computers and cellular phone applications. In 15 years between 1991 and 2006 the sales and production of Li-Ion batteries experienced double-digit growth. The slower growth period, around 2000, occurred when cell production in China and Korea began to ramp up and may not have been included in the database.I n 1995, an 18,650 cell sold for $8, while in 2006 the same size cell with 2.6 Ah sold for about $4. Over this period the energy density of the cell more than doubled, while the price fell by 50%. The cell producers accomplished the performance improvements through engineering improvements in cell design, new carbon mate-rials for the anode, and automated high-speed production to reduce the cost. The Li-Ion market is expected to continue growing as new technology is introduced and new applications develop.T he major cell manufacturers are listed in Table 1.3 .The Japanese manufacturers (Sanyo, Sony, and Matsushita) have a clear lead but the Chinese manufacturers (BYD, Lishen) and Korean manufacturers (Samsung and LG Chemical) are challenging. There are no major Li-Ion manufacturers in the United States (or in Europe), evenC ell typeY ear1991 1992 1994 1996 1998 2000 2002 2004 2005 2006aN i–Cd 1,535 1,823 2,060 1,695 1,394 1,204 935 1,006 935 939 N i-MH 39 100 746 863 848 1,245 667 767 726 891 L i-Ion 110 152 1,292 1,900 2,805 2,458 4,019 3,899 3,790 L am Li-Ion 00002187 299 487 547 657 T able 1.2W orldwide Sales (Million of Dollars) 4a EstimatedA pplicationC ell typeN i-Cd N i-MH C y Li-Ion P r Li-Ion L am Li-IonC ellular 50 898.16 125.85 N otebook 22 422.68 16.34 2.50 M ovie 2467.98 11.91D igital still camera 56 18.88 48.17 0.94 P ower tools 575 53 20.14 0.08A udio 80 35 6.99 31.02 45.63 G ames 26.82 14.4 C onsumer 45 300C ordless phones 190 83O thers 330 178 22.854 28.98 14.42 T able 1.32005 Worldwide cell demand (Millions of Cells) 44 R.J. Brodd though they constitute large markets for devices powered by Li-Ion batteries.5 Activity in the United States is limited to several companies that supply the niche medical and military markets.1.3 Market CharacteristicsT he unit cell production for 2005 by product application is given in Table 1.4 . Cellular phone applications dominate the unit cell production. The thin, rectangular polymer/laminate cell construction has found favor in the cellular phone market and now accounts for about 13%, with the rest being the prismatic cell sizes. Notebook computers are second followed by cameras.T he period from its introduction in 1991–2002 was a time for establishing the fundamental base for materials and manufacturing processing. During this period, the processing of the materials, cell designs, and production equipment reached a high level of sophistication. The fundamental underpinning of the technology pro-vided a sound basis for future expansion during the next decade. Problems were identified and methods to solve the problems were developed. From a cell engineer-ing viewpoint, the maximum capacity of an 18,650 cell would be 2.5–2.6 Ah with the materials that were available in 2002. Increase in cell capacity and energy stor-age while maintaining safety would require new materials.S tarting in 2003, a shift in the market applications began to occur, as depicted in Fig. 1.2 .6In one segment basically the drive to increase capacity and performance for the competitive notebook and cellular phone applications continues. This requires the development and introduction of higher capacity, higher p erformance anode and cathode materials. Several new high-capacity, safer compositions suchas LiMn0.3C o0.3N i0.5O2and LiMn0.5N i0.5O2cathodes were developed and are in theprocess of being put into production. In the same line, new anode materials have been developed, based on nanostructured lithium alloy anodes. These materials can drive the 18,650 cell capacity over 2.6 Ah and could approach 3.0 Ah in the future.M anufacturers P ercentage of totalS anyo 27.50S ony 13.30S amsung 10.88M atsushita 10.07B YD 7.53L G Chemical 6.45L ishen 4.52N EC 3.60M axell 3.26O thers 12.89T able 1.4M ajor Li-ion cell manufacturers, 2005 41 Synopsis of the Lithium-Ion Battery Markets 5The other segment consists of applications that do not require a significant increase in energy storage capability but emphasize lower cost and higher power for new applications such as automotive and power tools. These applications also require new cathode and anode materials to meet the market demands for low cost with high-rate performance. An example of a new material is the LiFePO 4cathode materials introduced in the market in 2003 by Valence Technology and followed byA123, which emphasized power tool applications. 7–91.4 Consumer Electronics Cellular telephones and notebook computer applications drove the market and will continue to dominate cell usage. The Bluetooth and 3G mobile phones should expand the market coupled with expansion as people shift to higher performance devices. The market for portable cellular phone and notebook computers is reaching saturation in the United States and Europe where it is expected to grow in parallel with the gross national product. Large growth areas for cellular phones and note-book computers are in Asia, especially the Chinese and Indian markets.M ovie cameras account for about 25% of cell usage. Often cameras are used intermittently and may sit on the shelf for an extended period before use. The shelf life of the Li-Ion is significantly better than Ni–Cd and Ni-MH cells, the previous battery systems for movie cameras. Digital still cameras are next. They are in the process of transitioning to Li-Ion from alkaline primary and Ni-MH cells. Most primary cells lack the high pulse current required for camera operation. Only the primary Li–FeS 2system gives fully satisfactory performance for digital still camera operation. Notebook computer and cellular phone users have learned to recharge their batteries on a regular basis so that the device gives the expected service. In addition, many mobile phones have a built-in camera and could slow the development of the digital camera market.F ig. 1.2 A split develops in the Li-ion market6 R.J. Brodd 1.5 Hand Power ToolsT he power tool market is dominated by the Ni–Cd system. In terms of cell volumes it is the third largest. However, it is heavy and has a short run time compared to Li-Ion. Previously, Li-Ion cells could not meet the very high rate capability of theNi–Cd. Recently, Li-Ion cells with excellent high-rate LiMn2O4or LiFePO4cathodematerials were introduced for power tool applications. They are about a third smaller and half the weight of the older Ni–Cd. The phosphate cathode cells have a significantly greater safety characteristic as the cells do not go into thermal runaway until heated to over 600°C. The greater safety, coupled with the superior high-rate capability of the nanostructured phosphate materials, make them ideal for this application. This market segment is price-sensitive. Because the Ni-MH has poor low temperature and poorer very high rate performance, it has not made a signifi-cant inroad against Ni–Cd. The introduction of Li-Ion–powered tools by DeWalt and Milwaukee Tool offers a growth opportunity for Li-Ion cells.1.6 Uninterruptible Power Sources, Stationary Energy Storage T he uninterruptible power source market is about $ 6–10 billion annually and is growing roughly with the gross national product. This market is dominated by lead acid batteries. The technology is slowly shifting from the flooded to the valve-regulated lead acid technology. The valve-regulated lead acid cells are sealed and do not vent hydrogen and acid vapors on charge or stand, but they are more expen-sive to produce. The main competition to the lead acid is costly pocket plate Ni–Cd, but it has an exceptionally long life. It is not unusual for Ni–Cd to have an opera-tional life of 15 years or more in this application. Increased emphasis on environ-mental controls has made lead acid and Ni–Cd vulnerable for penetration by the environmentally acceptable, higher-cost Li-Ion batteries.T his market is very price-sensitive and the cost of Li-Ion cells will need to reach $0.30/Wh to penetrate this market. The new lower-cost manganese and phosphate cathode materials could reach this cost goal. It should be noted that several large lead acid battery companies in this market recently have entered into agreements with Li-Ion producers to supply cells and batteries for evaluation purposes. This could be an indication that the more traditional lead acid producers are positioning themselves to supply Li-Ion as an alternative for lead batteries.1.7 TransportationT here are many emerging market opportunities for Li-Ion cells in transportation. The motive power market is viewed as the largest future growth opportunity for Li-Ion batteries. Once in place, the transportation market will dwarf the present1 Synopsis of the Lithium-Ion Battery Markets 7 portable device market. The Segway Transporter has shifted from Ni-MH to Li-Ion batteries. The Toyota Prius will shift from Ni-MH to Li-Ion in the next model rede-sign. These, along with the emerging boating motors for freshwater lakes, have set the stage for penetration into this huge market area. Europe is in the process of banning gasoline motors on all lakes. Several U.S. lakes now bar gasoline-powered boats, as well. Boaters must shift to electric drive and batteries to operate on the lakes. These presently use lead acid batteries. The smaller, lighter, Li-Ion battery is already marketed in Europe for this application.T he introduction of the Tesla electric vehicle in 2007 with a 200 + mile range should set the stage for the transition to electric propulsion. The new cathode and anode systems also offer the potential to replace the present lead acid SLI (starting-lighting-ignition) battery on gasoline-powered vehicles.R eferences1.A. Y oshino ,T he Chemical Industry ,146,870 (1995)2.T. N agaura and K. T azawa ,P rogress in Batteries and Battery Materials ,10,218 (1991)3. R. J. Brodd, Factors affecting U.S. production decisions: Why are there no volume lithium ionbattery manufacturers in the United States? ATP Working Paper 05-01, June, 20054. R ecommendations on the Transport of Dangerous Goods, Manual of Tests and Criteria, Thirdrevised edition, United Nations, New York and Geneva, 20025. H. Takeshita, 23rd International Seminar on Primary and Secondary Batteries, Ft. Lauderdale,FL, March 20066. R. J. Brodd, Keynote Lecture, IMLB 11, Monterey CA, June, 20027. Valence Technology, Inc., Form 10-K, June 30, 20038.S.-Y. C hung ,J. T. B loking ,and Y.-M. C hiang ,N ature Materials ,1,123 (2002)9.A. K. P adhi ,K. S. N anjundaswamy ,and J. B. G oodenough ,J ournal of Electrochemistry Society144,1188 (1997)。
锂离子电池质量分级评价规
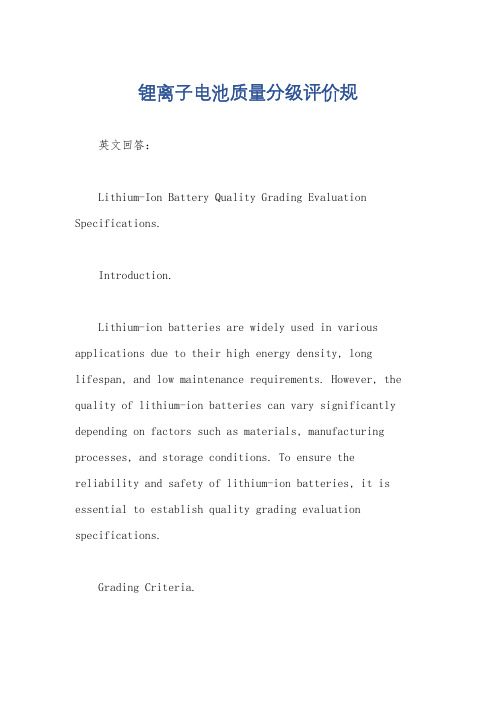
锂离子电池质量分级评价规英文回答:Lithium-Ion Battery Quality Grading Evaluation Specifications.Introduction.Lithium-ion batteries are widely used in various applications due to their high energy density, long lifespan, and low maintenance requirements. However, the quality of lithium-ion batteries can vary significantly depending on factors such as materials, manufacturing processes, and storage conditions. To ensure the reliability and safety of lithium-ion batteries, it is essential to establish quality grading evaluation specifications.Grading Criteria.The grading criteria for lithium-ion batteries should evaluate various aspects of the battery's performance and safety. Key parameters to consider include:Capacity: The amount of charge that a battery can store and deliver.Energy density: The amount of energy stored per unit volume or weight.Cycle life: The number of charge-discharge cycles that a battery can endure before reaching a specified capacity reduction.Internal resistance: The resistance to the flow of current within the battery.Voltage: The electrical potential difference between the battery's terminals.Self-discharge rate: The rate at which a battery loses its charge when not in use.Grading System.Based on the evaluation of the grading criteria,lithium-ion batteries can be assigned to different quality grades. A typical grading system may include:Grade A: Batteries with excellent performance and meet all the specified criteria.Grade B: Batteries with good performance but may have slight deficiencies in certain criteria.Grade C: Batteries with acceptable performance but may have significant deficiencies in one or more criteria.Grade D: Batteries with poor performance and fail to meet the minimum requirements.Evaluation Methods.The evaluation of lithium-ion batteries for qualitygrading can be conducted using various methods, including:Electrical testing: Measures parameters such as capacity, energy density, voltage, and internal resistance.Electrochemical testing: Analyzes the battery's chemical properties and reactions.Thermal testing: Evaluates the battery's performance under different temperature conditions.Safety testing: Assesses the battery's ability to withstand extreme conditions and potential hazards.Conclusion.Establishing comprehensive quality grading evaluation specifications is crucial for ensuring the reliability and safety of lithium-ion batteries. By evaluating key performance and safety parameters, manufacturers and consumers can effectively assess the quality of batteries and make informed choices about their use.中文回答:锂离子电池质量分级评价规范。
谁真正发明了可充电锂离子电池?

可充电锂离子电池诞生于50年前,现在它的价值无人不知,被用于笔记本电脑、手机、电动工具、电动汽车……它每年的全球销售额高达450亿美元,并有望在未来10年内突破1 000亿美元。
然而,这项变革性的发明历经近20年蛰伏方才走出实验室——美国、欧洲和亚洲的许多企业都曾想把握这项技术,却把握不住它的巨大潜能。
埃克森公司的斯坦利 • 威廷汉(Stanley Whittingham )等人于1972年开发出第一款可充电锂电池。
它由埃克森小批量生产,曾在1977年芝加哥的电动汽车展上露面,并被短暂用作纽扣电池,但未能走远,后来这家石油巨头企业放弃了它。
世界各地的众多科学家都参与了可充电锂电池研究,但在大约15年时间里,成功的希望很渺茫。
直到对的人在对的时间做了对的事,可充电锂电池才开启统治世界的旅程。
是埃克森公司发明了可充电锂电池吗?1970年代初,埃克森的科学家预测全球石油产量将于2000年达到顶峰,然后逐步下降。
企业鼓励研究人员寻找石油替代品,探索任何与石油无关的能源。
1972年秋天,年轻的英国化学家威廷汉加入位于新泽西州的埃克森研究工程公司。
到圣诞节时,他开发出一种以二硫化钛作正极、使用以锂盐为主体的液态电解质、由锂盐提供锂离子实现充放电的电池。
威廷汉的创新电池不同于此前所有电池。
它的充电原理是将锂离子传输并插入主体电极材料的原子晶格中,即所谓的“嵌入”。
该电池的性能也可谓前所未见:既可充电,又具备非常高的能量输出。
要知道那时最好的蓄电池是镍镉电池,最大输出电压仅有1.3伏,而威廷汉团队的电化学杰作能产生惊人的2.4伏电压。
1973年冬天,埃克森的经理们将威廷汉召至公司位于纽约的办公室,出席埃克森董事会的小组委员会会议。
威廷汉后来表示:“我进去解释了一遍,用时最多10分钟。
然后不到一周,他们就说想要投资这个发明。
”这看起来是一桩大事件,有可能改变世界的大事件。
威廷汉在《科学》(Science )杂志上发表了一篇论文。
锂电回收工艺流程英文
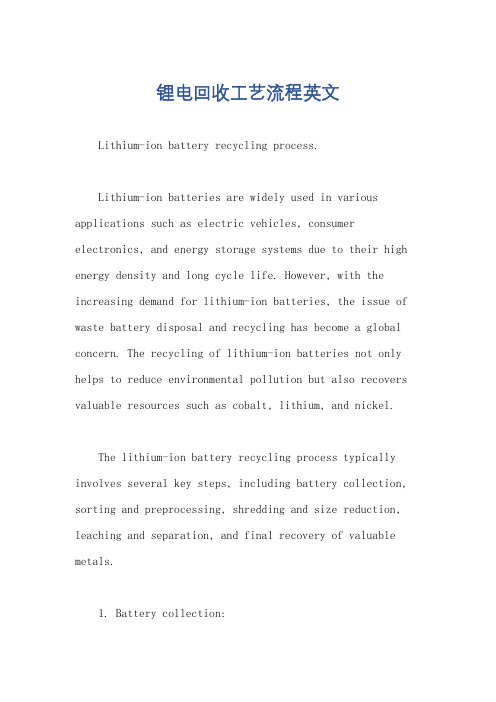
锂电回收工艺流程英文Lithium-ion battery recycling process.Lithium-ion batteries are widely used in various applications such as electric vehicles, consumer electronics, and energy storage systems due to their high energy density and long cycle life. However, with the increasing demand for lithium-ion batteries, the issue of waste battery disposal and recycling has become a global concern. The recycling of lithium-ion batteries not only helps to reduce environmental pollution but also recovers valuable resources such as cobalt, lithium, and nickel.The lithium-ion battery recycling process typically involves several key steps, including battery collection, sorting and preprocessing, shredding and size reduction, leaching and separation, and final recovery of valuable metals.1. Battery collection:The first step in the recycling process is the collection of waste lithium-ion batteries. This involves the collection of batteries from various sources such as electric vehicle dealerships, consumer electronics recycling centers, and other waste collection points. The collected batteries are then transported to the recycling facility for further processing.2. Sorting and preprocessing:At the recycling facility, the collected batteries undergo sorting and preprocessing to remove any impurities and prepare them for further recycling. This step involves sorting the batteries based on their chemistry, size, and condition. Batteries with damaged cells or leaks are separated and disposed of safely. The remaining batteries are then disassembled to separate the battery cells and remove any plastic, metal, and other non-recyclable components.3. Shredding and size reduction:After preprocessing, the battery cells are shreddedinto smaller pieces using shredding machines. This step helps to break down the battery structure and expose the internal components such as the cathode, anode, and separator. The shredded material is then further processedto reduce its size, making it easier for subsequent steps.4. Leaching and separation:In the leaching step, the shredded battery material is mixed with a suitable solvent to extract the valuable metals. The solvent used depends on the chemistry of the battery and the type of metals being recovered. For example, acids such as sulfuric acid or nitric acid may be used to extract cobalt, lithium, and nickel from the cathode material. The leaching process helps to dissolve the metals from the solid matrix and convert them into a soluble form.After leaching, the solution is separated from thesolid waste using filtration or centrifugation. The solid waste can be further processed for the recovery of othervaluable components or disposed of safely. The separated solution contains the dissolved metals, which are then ready for the next step of metal recovery.5. Recovery of valuable metals:The final step in the lithium-ion battery recycling process is the recovery of valuable metals from the leached solution. This step involves the separation andpurification of the metals to produce a high-quality product that can be reused in the manufacturing of new batteries.Several methods can be used for metal recovery, including precipitation, solvent extraction, ion exchange, and electrowinning. The choice of method depends on the specific metals being recovered, the concentration of metals in the solution, and the desired purity of the final product. For example, precipitation methods can be used to recover cobalt and nickel by adding suitable precipitating agents to the solution. The precipitated metals are then filtered, washed, and dried to obtain a high-purity metalproduct.In addition to cobalt and nickel, lithium can also be recovered from the leached solution. Lithium recovery typically involves the use of ion exchange or solvent extraction techniques to separate lithium from other metals. The recovered lithium can then be used in the production of new batteries or other lithium-based products.Overall, the lithium-ion battery recycling process involves multiple steps that aim to efficiently recover valuable metals from waste batteries. This process not only helps to reduce the environmental impact of lithium-ion battery waste but also contributes to the sustainable useof resources by recovering and reusing valuable metals.It is worth noting that the recycling process may vary depending on the specific type of lithium-ion battery and the recycling facility's equipment and technology. However, the general steps described above provide a fundamental understanding of the lithium-ion battery recycling process and its key components.In conclusion, the recycling of lithium-ion batteries is crucial for sustainable energy storage systems. By recovering valuable metals such as cobalt, lithium, and nickel, the recycling process helps to conserve resources, reduce environmental pollution, and promote circular economy practices. As the demand for lithium-ion batteries continues to grow, it is essential to develop efficient and sustainable recycling methods to ensure the environmental and economic viability of the battery industry.。
毕业设计电动车电池参考文献英文
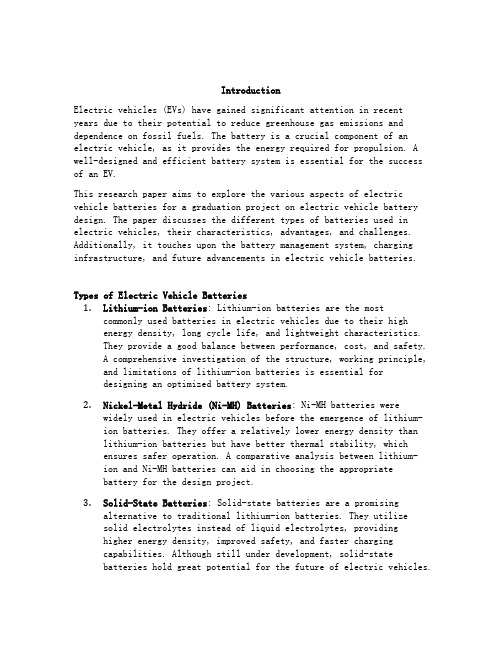
IntroductionElectric vehicles (EVs) have gained significant attention in recent years due to their potential to reduce greenhouse gas emissions and dependence on fossil fuels. The battery is a crucial component of an electric vehicle, as it provides the energy required for propulsion. A well-designed and efficient battery system is essential for the success of an EV.This research paper aims to explore the various aspects of electric vehicle batteries for a graduation project on electric vehicle battery design. The paper discusses the different types of batteries used in electric vehicles, their characteristics, advantages, and challenges. Additionally, it touches upon the battery management system, charging infrastructure, and future advancements in electric vehicle batteries.Types of Electric Vehicle Batteries1.Lithium-ion Batteries: Lithium-ion batteries are the mostcommonly used batteries in electric vehicles due to their highenergy density, long cycle life, and lightweight characteristics.They provide a good balance between performance, cost, and safety.A comprehensive investigation of the structure, working principle,and limitations of lithium-ion batteries is essential fordesigning an optimized battery system.2.Nickel-Metal Hydride (Ni-MH) Batteries: Ni-MH batteries werewidely used in electric vehicles before the emergence of lithium-ion batteries. They offer a relatively lower energy density thanlithium-ion batteries but have better thermal stability, whichensures safer operation. A comparative analysis between lithium-ion and Ni-MH batteries can aid in choosing the appropriatebattery for the design project.3.Solid-State Batteries: Solid-state batteries are a promisingalternative to traditional lithium-ion batteries. They utilizesolid electrolytes instead of liquid electrolytes, providinghigher energy density, improved safety, and faster chargingcapabilities. Although still under development, solid-statebatteries hold great potential for the future of electric vehicles.Battery Management System (BMS)The Battery Management System (BMS) is responsible for monitoring and controlling the battery’s performance, safety, and lifespan. A well-designed BMS ensures the optimal operation of the battery system, preventing overcharging, undercharging, and excessive discharge. It provides accurate state-of-charge (SOC) and state-of-health (SOH) estimations, which are crucial for maximizing the battery’s efficiency.The BMS consists of various components, including sensors, control algorithms, and battery balancing circuits. In-depth research on BMS architecture, functionality, and control strategies is necessary to design an effective battery management system for the electric vehicle.Charging InfrastructureThe availability of a robust charging infrastructure is essential for widespread adoption and convenience of electric vehicles. The research project should explore the different types of charging stations, including:1.Level 1 Charging: Level 1 charging refers to standard householdoutlets (120V), which provide a slow charging rate but are widely accessible.2.Level 2 Charging: Level 2 charging utilizes dedicated chargingstations (240V). It offers a faster charging rate compared toLevel 1 and is commonly found in residential areas, workplaces,and public charging stations.3.DC Fast Charging: DC Fast Charging, also known as Level 3charging, provides rapid charging capabilities by directlydelivering DC power to the vehicle’s battery. These chargingstations are typically located along highways and major routes.The paper should discuss the importance of a well-established charging infrastructure and address potential challenges and solutions to the deployment of charging stations.Future AdvancementsThe field of electric vehicle batteries is continuously evolving, with ongoing research and advancements. It is crucial for the researchproject to explore future developments, such as:1.Advanced Lithium-ion Batteries: Researchers are constantlyworking on improving the energy density, charging speed, andsafety of lithium-ion batteries. Advancements in materials,electrode designs, and electrolytes are expected to result in more efficient and long-lasting batteries.2.Solid-State Batteries: As mentioned earlier, solid-statebatteries hold immense potential for the future of electricvehicles. The research should discuss the current challenges faced in commercializing solid-state batteries and potentialbreakthroughs that can lead to their widespread adoption.3.Beyond Lithium-ion: Besides solid-state batteries, alternativebattery chemistries like lithium-sulfur (Li-S) and lithium-air(Li-Air) batteries are being explored for their high energydensities. Understanding these emerging battery technologies canpave the way for future advancements in EV batteries.ConclusionDesigning an efficient and reliable battery system is crucial for the success of an electric vehicle. This research paper provides a comprehensive and detailed analysis of different types of electric vehicle batteries, their characteristics, and the importance of a well-designed battery management system and charging infrastructure. Furthermore, it explores future advancements in electric vehicle battery technologies. By understanding these aspects, the research project can aim to design an optimized electric vehicle battery system that contributes to a sustainable and greener transportation future.Note: The content provided above is a suggested structure for the research paper related to the topic of “Graduation Project - Electric Vehicle Battery”. Please add relevan t and specific details from appropriate academic references to complete the paper.。
锂电工艺流程英语
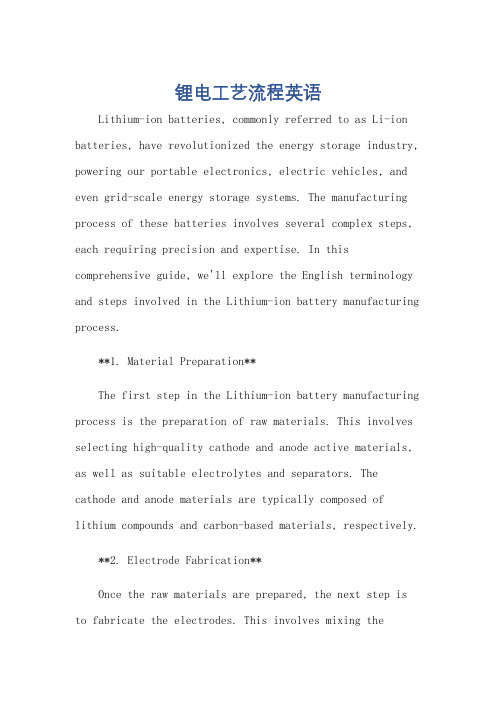
锂电工艺流程英语Lithium-ion batteries, commonly referred to as Li-ion batteries, have revolutionized the energy storage industry, powering our portable electronics, electric vehicles, and even grid-scale energy storage systems. The manufacturing process of these batteries involves several complex steps, each requiring precision and expertise. In this comprehensive guide, we'll explore the English terminology and steps involved in the Lithium-ion battery manufacturing process.**1. Material Preparation**The first step in the Lithium-ion battery manufacturing process is the preparation of raw materials. This involves selecting high-quality cathode and anode active materials, as well as suitable electrolytes and separators. The cathode and anode materials are typically composed of lithium compounds and carbon-based materials, respectively. **2. Electrode Fabrication**Once the raw materials are prepared, the next step is to fabricate the electrodes. This involves mixing theactive materials with binders and conductive additives, and then coating them onto a metal current collector. The most common metal current collectors are aluminum for the cathode and copper for the anode.**3. Electrode Drying and Cutting**After coating, the electrodes undergo a drying process to remove any moisture. Once dry, they are cut into the desired shape and size, ready for the next step in the manufacturing process.**4. Cell Assembly**Cell assembly is a crucial step, where the electrodes, electrolyte, and separator are combined to form the battery cell. The separator, typically made of porous polypropylene or polyethylene, is placed between the cathode and anode to prevent direct contact and thus, short-circuiting. The electrolyte, which is a liquid or solid material, is then added to facilitate the movement of ions between the electrodes.**5. Welding and Sealing**After assembly, the cell is sealed and welded to ensure its structural integrity and prevent leakage of the electrolyte. This step is crucial for ensuring the safety and performance of the battery.**6. Formation and Testing**The formed battery cell is then subjected to a formation process, which involves charging and discharging the cell to activate it. Following formation, the cell is tested to ensure its performance meets specifications. This testing may include capacity testing, internal resistance testing, and cycling tests.**7. Packaging and Final Testing**Once the individual cells are tested and approved, they are packaged into the final battery pack. This packaging may include additional safety features such as thermal cut-off devices and fuses. The final battery pack is then tested again to ensure it meets the required performance and safety standards.**8. Quality Control and Shipping**Quality control is an ongoing process throughout the manufacturing process. However, a final inspection is conducted before the batteries are shipped to customers. This inspection ensures that each battery meets therequired specifications and is safe for use.In conclusion, the Lithium-ion battery manufacturing process is a complex and meticulous procedure, requiring precision and expertise. Understanding the terminology and steps involved in this process is crucial for ensuring the safety, performance, and reliability of the final product. As the demand for Lithium-ion batteries continues to grow, so does the importance of understanding and improving their manufacturing processes.**锂电池生产工艺流程详解**锂电池,特别是锂离子电池(Li-ion),已彻底改变了储能行业,为便携式电子设备、电动汽车甚至电网级储能系统提供了动力。
软包锂电池英文文献

软包锂电池英文文献Soft-Packed Lithium-Ion Batteries: A Technical Overview.Lithium-ion batteries (LIBs) have revolutionized theway we power our electronic devices, with their high energy density, low self-discharge rate, and long cycle life. Among various battery configurations, soft-packed lithium-ion batteries (SPLBs) have emerged as a popular choice fora wide range of applications, thanks to their unique advantages.Advantages of Soft-Packed Lithium-Ion Batteries.SPLBs offer several advantages compared to traditional battery formats. Firstly, their flexible packaging allowsfor a more compact and lightweight design, making them suitable for space-constrained applications. Secondly, the soft packaging material enhances the battery's safety by preventing internal short circuits and mitigating theimpact of external forces. Furthermore, SPLBs offer betterheat dissipation, enabling them to operate at higher temperatures without compromising performance.Construction and Materials Used.Soft-packed lithium-ion batteries are constructed using a combination of aluminum and plastic films as the outer packaging. This packaging material is chosen for its excellent strength, flexibility, and insulating properties. Inside, the battery comprises an anode, a cathode, a separator, and an electrolyte. The choice of materials for these components is crucial for the battery's performance and safety.Working Principles.During discharge, lithium ions move from the anode, through the separator, to the cathode. This process generates electricity, which powers the connected device. During charge, the ions flow in the opposite direction, returning to the anode. The separator ensures that the ions move through the battery safely, preventing direct contactbetween the anode and cathode, which could lead to short circuits.Applications.Soft-packed lithium-ion batteries are widely used in consumer electronics, electric vehicles, and renewable energy systems. In consumer electronics, their lightweight and compact design makes them ideal for portable devices like smartphones, laptops, and wearables. In electric vehicles, SPLBs offer high energy density and fast charging capabilities, enabling longer driving ranges and shorter charging times. In renewable energy systems, they are used to store energy generated by solar panels or wind turbines, ensuring a continuous supply of power even when the weather conditions are not favorable.Challenges and Future Developments.Despite their many advantages, SPLBs face some challenges, such as safety concerns and recycling issues. Ongoing research is focused on developing safer batterychemistries, improving their thermal stability, and enhancing their recycling potential. Future developments in SPLB technology could lead to even higher energy densities, faster charging speeds, and improved lifespans.Conclusion.Soft-packed lithium-ion batteries represent asignificant advancement in battery technology, offering unique advantages in terms of compactness, lightweight design, and safety. Their widespread use in consumer electronics, electric vehicles, and renewable energy systems underscores their importance in powering our modern, mobile world. As research continues to address the challenges associated with SPLBs, we can expect further improvements in their performance and safety, enabling even more innovative applications in the future.。
锂电池中化成和分容英文缩写
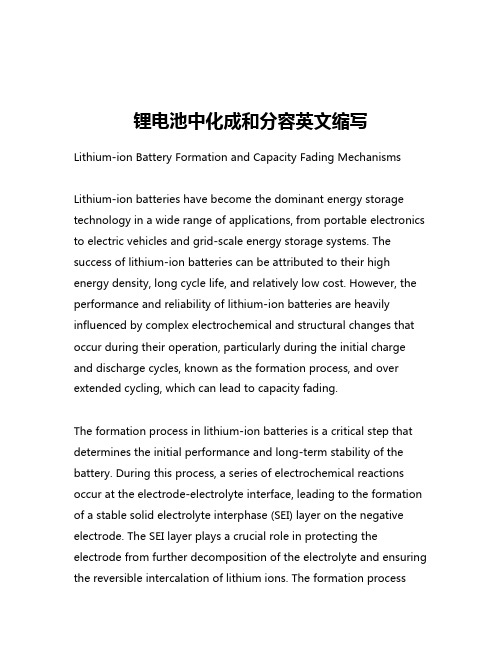
锂电池中化成和分容英文缩写Lithium-ion Battery Formation and Capacity Fading MechanismsLithium-ion batteries have become the dominant energy storage technology in a wide range of applications, from portable electronics to electric vehicles and grid-scale energy storage systems. The success of lithium-ion batteries can be attributed to their high energy density, long cycle life, and relatively low cost. However, the performance and reliability of lithium-ion batteries are heavily influenced by complex electrochemical and structural changes that occur during their operation, particularly during the initial charge and discharge cycles, known as the formation process, and over extended cycling, which can lead to capacity fading.The formation process in lithium-ion batteries is a critical step that determines the initial performance and long-term stability of the battery. During this process, a series of electrochemical reactions occur at the electrode-electrolyte interface, leading to the formation of a stable solid electrolyte interphase (SEI) layer on the negative electrode. The SEI layer plays a crucial role in protecting the electrode from further decomposition of the electrolyte and ensuring the reversible intercalation of lithium ions. The formation processtypically involves several charge-discharge cycles, during which the capacity of the battery gradually increases and stabilizes.The formation process can be divided into several stages, each with its own characteristics and implications for the battery's performance. The first stage involves the initial reduction of the electrolyte components, such as the organic solvents and lithium salts, at the surface of the negative electrode. This results in the formation of a thin, passivating layer that helps to prevent further electrolyte decomposition. The second stage involves the gradual thickening and stabilization of the SEI layer, as additional electrolyte components are reduced and incorporated into the layer.The final stage of the formation process involves the lithiation and delithiation of the active materials in both the positive and negative electrodes. During this stage, the capacity of the battery gradually increases as the lithium ions are reversibly intercalated and deintercalated from the electrode materials. The successful completion of the formation process is crucial for ensuring the long-term stability and performance of the lithium-ion battery.In addition to the formation process, capacity fading is another important aspect of lithium-ion battery performance. Capacity fading refers to the gradual loss of the battery's energy storage capacity over time, which can be caused by a variety of factors, includingelectrode degradation, electrolyte decomposition, and structural changes within the battery.One of the primary mechanisms of capacity fading in lithium-ion batteries is the gradual loss of active lithium inventory, which can occur due to the irreversible consumption of lithium ions during the formation of the SEI layer and other side reactions. As the SEI layer continues to grow and evolve over extended cycling, it can become thicker and less permeable to lithium ions, leading to a decrease in the battery's capacity.Another important mechanism of capacity fading is the degradation of the electrode materials, which can be caused by various factors, such as volume changes during lithiation and delithiation, mechanical stress, and chemical reactions with the electrolyte. These degradation processes can lead to the loss of active material, the formation of inactive regions within the electrode, and the loss of electrical contact between the active material and the current collector.In addition to these electrochemical and structural changes, capacity fading can also be influenced by environmental factors, such as temperature and state of charge (SOC). High temperatures and high SOC can accelerate the rate of capacity fading, as they can promote the decomposition of the electrolyte and the formation of additionalSEI layer components.To mitigate the effects of capacity fading and improve the long-term performance of lithium-ion batteries, researchers have developed a variety of strategies, including the design of advanced electrode materials, the optimization of electrolyte formulations, and the implementation of sophisticated battery management systems. These strategies aim to minimize the irreversible loss of active lithium, reduce the rate of electrode degradation, and maintain the structural integrity of the battery components throughout its lifetime.In conclusion, the formation process and capacity fading mechanisms in lithium-ion batteries are complex and interrelated phenomena that have a significant impact on the overall performance and reliability of these energy storage devices. Understanding these mechanisms and developing effective strategies to address them is crucial for the continued advancement and widespread adoption of lithium-ion battery technology.。
- 1、下载文档前请自行甄别文档内容的完整性,平台不提供额外的编辑、内容补充、找答案等附加服务。
- 2、"仅部分预览"的文档,不可在线预览部分如存在完整性等问题,可反馈申请退款(可完整预览的文档不适用该条件!)。
- 3、如文档侵犯您的权益,请联系客服反馈,我们会尽快为您处理(人工客服工作时间:9:00-18:30)。
Three-dimension hierarchicalflower-like Ni1.5Co1.5O4nanostructurescomposed of two-dimension ultrathin nanosheets as an anodematerial for lithium ion batteriesYuhong Jin a,Li Wang a,n,Yuming Shang a,Jian Gao a,Jianjun Li a,c,Xiangming He a,b,nna Institute of Nuclear and New Energy Technology,Beijing Key Lab of Fine Ceramics,Tsinghua University,Beijing100084,PR Chinab State Key Laboratory of Automotive Safety and Energy,Tsinghua University,Beijing100084,PR Chinac Huadong Institute of Lithium Ion Battery,Zhangjiagang,Jiangsu215600,PR Chinaa r t i c l e i n f oArticle history:Received11December2014Accepted5February2015Available online17March2015Keywords:Ni1.5Co1.5O4Flower-likeMicrostructureLithium ion batteriesEnergy storage and conversiona b s t r a c tUniform three-dimension hierarchicalflower-like Ni1.5Co1.5O4nanostructures were synthesized on alarge scale by a simple,low-temperature hydrothermal method without any template,catalyst andsurfactant,followed by a calcinating process.The obtained Ni1.5Co1.5O4products were composed of two-dimension ultrathin nanosheets with random attachment.Nitrogen sorption isotherm shows that thisstructure possesses a high specific surface area of118.8m2gÀ1with an average pore diameter of16.67nm.When tested as an anode material,the as-prepared Ni1.5Co1.5O4nanostructures exhibit aninitial discharge capacity of1461.5mAh gÀ1.After30cycles at the current density of100mA gÀ1,thedischarge capacity still keeps980.8mAh gÀ1.The obtained three-dimension hierarchicalflower-likeNi1.5Co1.5O4nanostructures show a promising anode material for lithium ion batteries.&2015Elsevier B.V.All rights reserved.1.IntroductionOver the past decades,extensive research interest on lithiumion batteries(LIBs)has been widely stimulated due to theiradvantages of high energy density,long lifespan,no memoryeffect and environmental benignity,which holds great potentialapplication in the areas of energy storage/conversion devices[1–6].Numerous efforts have been devoted to developing noveland high performance electrode materials with the aim to realizeLIBs with higher energy/power density[7–9].Among the diversematerials that have been studied as potential anode materials forLIBs,Ni x Co3Àx O4mixed oxides have been regarded as potentialelectrodes for the development of next generation LIBs due totheir favorable performance inherited from Co-based metal oxides[10–12].However,the Ni x Co3Àx O4bulk as anode material showsthe large irreversible capacity in thefirst cycle due to the lowelectronic conductivity.In order to solve this problem,synthesis ofNi x Co3Àx O4with distinct nanostructure and morphology is aneffective way to enhance the electrochemical performance for LIBs.Recently,Li and coworkers[10]prepared monodisperse NiCo2O4mesoporous microspheres by a facile solvothermal method fol-lowed by pyrolysis of the Ni0.33Co0.67CO3precursor.The dischargecapacity of the as-prepared sample can reach1198mAh gÀ1after30discharge–charge cycles at a current density of200mA gÀ1.Liand coworkers[11]demonstrated polyvinylpyrrolidone(PVP)-assisted method to prepare3-dimensional(3D)hierarchical por-ousflower-like NiCo2O4.The investigated results show that PVPplays an important role in controlling the formation of thehierarchicalflower-like structure.The as-prepared NiCo2O4exhi-bits an enhanced lithium storage capacity and excellent cyclingstability(939mAh gÀ1at100mA gÀ1after60cycles).Zheng andcoworkers[12]reported a novel and facile route for the large-scalefabrication of2-dimensional porous Ni x Co3Àx O4nanosheets,which exhibited improved lithium storage properties and goodcycle performance.Herein,we successfully developed a facile and scalable methodwithout the help of surfactant to synthesis of three-dimensionhierarchical Ni1.5Co1.5O4material.The high conductivity of Ni1.5Co1.5O4facilitates the electron transfer while three-dimension hierarchicalflower-like structure ensures the large electro-active area and the ionsdiffusion-favored pathway.All these features make the as-fabricatedNi1.5Co1.5O4possess substantially enhanced rate capability and goodcycling stability when used as the anode materials for LIBs.Contents lists available at ScienceDirectjournal homepage:/locate/matletMaterials Letters/10.1016/j.matlet.2015.02.0170167-577X/&2015Elsevier B.V.All rightsreserved.n Corresponding author.nn Corresponding author at:Institute of Nuclear and New Energy Technology,Beijing Key Lab of Fine Ceramics,Tsinghua University,Beijing100084,PR China.Tel.:þ861062794226;fax:þ861089796031.E-mail addresses:wang-l@(L.Wang),hexm@(X.He).Materials Letters151(2015)49–522.Experimental sections1mmol of Ni(NO3)2Á6H2O,2mmol of Co(NO3)2Á6H2O and 6mmol of hexamethylenetetramine(HTMA)are dissolved into the mixed solvent(ethanol/water¼20:40,volume ratio)to form a transparent pink solution under stirred for10min at room tem-perature.Then,the homogeneous solution was transferred into a Teflon-lined stainless steel autoclave.The steel autoclave was sealed and kept in an oven at901C for4h.The HTMA is mainly used as the precipitator to produce OHÀin this reaction process.After cooling down to room temperature,the hydroxide precipitate was collected by centrifugation and washed with deionized water and ethanol for several times,the green Ni1.5Co1.5O4precursor was obtained by drying at601C for24h.the Ni1.5Co1.5O4sample was obtained by annealing the precursor at3501C for3h in air with the heating rate of11C minÀ1to obtain black Ni1.5Co1.5O4power.It should be noted that the mole ratio of Co/Ni in the as-prepared product(1:1)is in disagreement with the feeding proportion of the initial reactants (2:1).This is mainly attributed to the fact that Co2þcan coordinate with NH3generated from the decomposition of HTMA more easily than the Ni2þ,and this immobilized the precipitation of the Co ion.Crystal structure of the as-prepared product was characterized by X-ray diffraction(XRD)using D8ADVANCE(3kW).The mor-phology was investigated by thefield emission scanning electron microscope(FESEM,JSM-7001F)with energy dispersive X-ray (EDX)spectroscopy.Nitrogen adsorption and desorption isotherms were performed at77K on a Quantachrome NOVA4200E(USA) volumetric adsorption system.The chemical composition of the products was measured by Inductive Coupled Plasma Atomic Emission Spectrometer(ICP-AES,Varian700).The electrochemical performance of as-prepared Ni1.5Co1.5O4 sample was evaluated using the CR2032-type coin cells.As-prepared Ni1.5Co1.5O4as active material was mixed with acetylene black as conductive agent and polytetrafluoroethylene as binder at a weight ratio of50:30:20to fabricate electrode.The cyclic voltammogram(CV)was performed on an electrochemical work-station(CHI660E).The discharge/charge tests were conducted on LAND batteries test system(Wuhan,China).3.Results and discussionAs observed in Fig.1a,the diffraction peaks are similar to the standard patterns of NiCo2O4(JCPDS No.20-0781),suggesting that the as-prepared Ni1.5Co1.5O4structures also are the spinel structure with similar lattice constants[13].As shown in Fig.1b,according to the results,the specific surface area calculated by the Brunauer–Emmett–Teller(BET)method and the pore volume are118.8m2gÀ1 and0.495cm3g-1.The inset in the Fig.1b shows the Barrett–Joyner–Halenda(BJH)pore size distribution indicates a narrow pore size distribution(10–20nm)centered at around16.67nm.Fig.2a demonstrates the FESEM image for the Ni1.5Co1.5O4.Obviously, uniform three-dimension hierarchicalflower-like Ni1.5Co1.5O4 nanostructures are constructed with two-dimension nanosheets with random attachment.Fig.2b–e shows the corresponding EDX mapping for Co,Ni and O elements,respectively.It is obvious that the distribution of all elements in the as-prepared sample is homogeneous.The representative EDX analysis(Fig.2f)reveals that the content of Ni and Co is3.26and3.19mol%,respectively,close to the stoichimetric molar ratio of1:1in the spinel.The Co/Ni atomic ratio is further confirmed by ICP-AES.Thefirst three CV curves were investigated at the scanning rate of 0.1mV sÀ1in the potential range of0.01–3.00V(vs.Liþ/Li)(Fig.3a). At thefirst cycle,the intense reduction peak at0.81V can be ascribed to the reduction of Ni2þand Co3þto metallic Co and Ni,and the formation of Li2O and solid electrolyte interface(SEI)layer.The following two anodic peaks at$1.7V and$2.2V can be attributed to the oxidation of metallic Ni and Co to nickel and cobalt oxides [7,9].In the second cycle,the main reduction peak shift to$1.0V due to the pulverization of the Ni1.5Co1.5O4[9].However,from the second cycle,the CV curves overlap very well,which indicates the good reversibility of the electrochemical reactions.A high rate capability is investigated as shown in Fig.3b.Even at high rate of 1000mA gÀ1,a capacity of$320mAh gÀ1can still be kept.More-over,when the current density is reduced back to100mA gÀ1,an average discharge capacity of$988mAh gÀ1can be recovered. Representative discharge–charge curves of the as-prepared Ni1.5Co1.5O4microflower electrode at a current density of100mA gÀ1 as shown in Fig.3c.The initial discharge and charge capacities are 1461.5and1098.5mAh gÀ1,respectively.The initial capacity loss during thefirst cycle can be attributed to the formation of a SEIfilm and some undecomposed Li2O phase[9,14].Fig.3d shows the corresponding discharge–charge cycling performance of Ni1.5Co1.5O4/ Li cell.It has a high initial discharge capacity followed with fast decay.However,it keeps a stable capacity of980.8mAh gÀ1from second to30th cycle.Based on the above results,Ni1.5Co1.5O4electrode possesses a large initial discharge capacity and good cycle stability,which can be attributed to unique three-dimension hierarchicalflower-like structure.This structure can increase the Ni1.5Co1.5O4/electrolyte Fig.1.(a)XRD pattern and(b)N2adoption and desorption isotherms(inset:BJH pore size distributions)of the as-prepared Ni1.5Co1.5O4sample.Y.Jin et al./Materials Letters151(2015)49–5250Fig.2.FESEM image (a,b)and corresponding EDX mapping for Co (c),Ni (d),O (e)and the corresponding EDX spectrum (f).Y.Jin et al./Materials Letters 151(2015)49–5251contact area,facilitate the transportation of Li þions and reduce volume change during discharge/charge processes.4.ConclusionsIn summary,the Ni 1.5Co 1.5O 4micro flower has been prepared by the hydrothermal method.The initial discharge and charge capa-cities are 1461.5and 1098.5mAh g À1at 100mA g À1,and then the reversible capacity still keeps 980.8mAh g À1after 30cycles,suggesting that Ni 1.5Co 1.5O 4micro flower structure is a promising anode material for LIBs.AcknowledgmentsThis work is supported by the MOST (Grant nos.2013CB934000,2011CB935902,2014DFG71590,2010DFA72760,2011CB711202,2013AA050903,2011AA11A257and 2011AA11A254)and State Key Laboratory of Automotive Safety and Energy (No.ZZ2012-011).References[1]Poizot P,Laruelle S,Grugeon S,Dupont L,Tarascon JM.Nano-sized transition-metal oxides as negative-electrode materials for lithium-ion batteries.Nature 2000;407:496–9.[2]Ji L,Lin Z,Alcoutlabi M,Zhang X.Recent developments in nanostructuredanode materials for rechargeable lithium-ion batteries.Energy Environ Sci 2011;4:2682–99.[3]Wu HB,Chen JS,Hng HH,Lou XW.Nanostructured metal oxide-basedmaterials as advanced anodes for lithium-ion batteries.Nanoscale 2012;4:2526–42.[4]Armand M,Tarascon JM.Building better batteries.Nature 2008;451:652–7.[5]Zhu B,Fan L,He Y,Zhao Y,Wang H.A commercial lithium battery LiMn-oxidefor fuel cell applications.Mater Lett 2014;126:85–8.[6]Zhou X,Huang B,Zou Y,Xie J,Yang J.Cotton-templated fabrication ofhierarchical SnO 2mesoporous microtubes as the anode material of lithium ion battery.Mater Lett 2014;120:279–82.[7]Yang L,Gao Q,Zhang Y,Tang Y,Wu Y.Tremella-like molybdenum dioxideconsisting of nanosheets as an anode material for lithium ion battery.Electrochem Commun 2008;10:118–22.[8]Wang B,Cheng J,Wu Y,Wang D,He D.Porous NiO fibers prepared byelectrospinning as high performance anode materials for lithium ion batteries.Electrochem Commun 2012;23:5–8.[9]Jin Y,Wang L,Shang Y,Gao J,Li J,He X.Facile synthesis of monodisperse Co 3O 4mesoporous microdisks as an anode material for lithium ion batteries.Electrochim Acta 2015;151:109–17.[10]Li J,Xiong S,Liu Y,Ju Z,Qian Y.High electrochemical performance ofmonodisperse NiCo 2O 4mesoporous microspheres as an anode material for Li-ion batteries.ACS Appl Mater Interfaces 2013;5:981–8.[11]Li L,Cheah Y,Ko Y,Teh P,Wee G,Wong C,et al.The facile synthesis ofhierarchical porous flower-like NiCo 2O 4with superior lithium storage proper-ties.J Mater Chem A 2013;1:10935–41.[12]Zheng F,Zhu D,Chen Q.Facile Fabrication of porous Ni x Co 3Àx O 4nanosheetswith enhanced electrochemical performance as anode materials for Li-ion batteries.ACS Appl Mater Interfaces 2014;6:9256–64.[13]He G,Wang L,Chen H,Sun X,Wang X.Preparation and performance ofNiCo 2O 4nanowires-loaded graphene as supercapacitor material.Mater Lett 2013;98:164–7.[14]Munichandraiah N,Scanlon LG,Marsh RA.Surface films of lithium:anoverview of electrochemical studies.J Power Sources 1998;72:203–10.Fig.3.(a)the first three consecutive CV curves;(b)the rate performance,(c)the discharge –charge curves for the different cycles;(d)speci fic capacity at a current density of 100mA g À1and the coulombic ef ficiency versus the cycle number.Y.Jin et al./Materials Letters 151(2015)49–5252。