中宽带轧机主传动控制系统
宣钢中型材轧机主传动调速和控制系统的应用与技术攻关

金属外壳 ,与后轴接触 ,产生 的轴 电流会流入
编 码 器 内部 ,极 易损 坏 速 度 编 码 器 内部 电路 。
不 通过 P L C和 P R OF I BUS网络 ,直接将 急停
因此 ,将 编码 器与 后轴 绝缘 隔离 ,即使 信号开关接入继 电器线 圈,并将常开 点接入相 用耐压绝缘材料使 编码器 本体 不直接 与电机 和 应 传动 柜 C uvC控制 模板 的输 入端 子上 。通 电机后轴直接接触 ,切 断转轴 电流流入 编码器 过修 改控制参数来 实现 急停功 能。改造后急停
拓 扑结构为 3 CS远程 站一 P L C一精轧 区远程
后 重 点 将 速 度 环 Kp和 T i 进 行 重 新 整 定 。Kp 站 1 一 精 轧 区远 程 站 2一 轧 机 区液 压 站 一 粗 轧
由l 5以上 降 至 1 O以下 ,降 低 比 例增 益 ;T i
由4 8~ 8 0 ms 增 至2 8 0 ms~ 3 0 0 ms , 延 长 积
形存在 许多高压脉冲 ,致使 调速 驱动系统中高 频谐波成分增多,这些谐波分量在转轴、定子 绕组 和接线部分等产生电磁感应 ,产生转轴对 原设 计中 ,轧机 急停控 制是 通过 在 P L C 2 . 4轧机 急停信号 改造
轧机主传动调速装置采用 M AS T E R
DR I VE S 6 S E 7 0系 列 变 频 器 。 轧 机 区 电气 控 制
地的脉冲电压,从而产生转轴电流。虽然在电 中编 制程 序,将 相应 区域 急停开 关接 入 P L C
机前轴上增加了接地碳刷 , 但测试轧钢过程 中, 主传 动电机产 生的轴 电流仍 可到 I O A~ 2 0 A。 的开 关量 输入 点 ,经 过 P RO F I BUS网络来 控 制实现急停 功能。此方式急停控制 中,若 P L C
宽厚板粗轧机主传动控制系统设计探究

177中国设备工程Engineer ing hina C P l ant中国设备工程 2019.10 (上)众所周知,当代世界知名高性能轧钢机设备和相关技术进入我国钢铁行业,其本身的技术应用以及针对我国实际情况的革新优化,其成为当代我国诸多工业领域占据关键地位的设备。
而作为宽厚板粗轧机中起到连接传输和控制作用的主动传动控制系统在设计方面要讲究科学性和实践应用性,因此,针对宽厚板粗轧机主传动控制系统设计重点和对策的探究非常有必要。
1 电气控制方案在当代的宽厚板粗轧机的主传动控制系统当中,得益于交流调速技术的发展和实践深入,当代交流主传动系统在今年逐步替换了传统的晶闸管整流器式的直流系统。
在当今包括机械加工、钢铁加工在内的多个产业当中,闸机主传动变频调速装置比较常见的为交—交变频系统,以及系统化的交—直—交变频系统。
两种装置系统的优缺点主要为:(1)交—交变频技术。
该形式的优势在于结构简单,电流电气控制执行效率较高,且能够承载更大的过载压力。
当然从操作的角度来说其极高的便捷度也令人满意。
但是,该种电气控制技术的缺点在于,其本身的变频的频率相对来说非常低,且存在电网侧产生谐波高的问题。
(2)交—直—交变频技术。
一方面,这种技术在变频的效率方面有较高的优势,功率因素也达到了较高的水平。
并在运行的过程中不需要无功补偿。
但是这种相对复杂的电气控制模块的操作执行的效率却相对较低,且不能够承载较高的过载压力。
另一方面,交—直—交变频技术当下在国内的研发和应用成本是比较高的。
在实际应用中,主传动控制系统的电气控制技术的选择直接决定整个控制逻辑和应用效果,因此,需要在足够了解多种主要电气控制技术的基础上,根据产业规模、技术要求和员工团队专业水平,选择合适的电气控制方案。
而值得一提的是,在选择时,也应当充分考虑生产安全的把控以及对传统粗轧机系统问题的关注,由此综合分析,确定一种更加高效安全的电气控制系统是更合理的。
2 变频器的选用和设计(1)基础设计。
ACS6000中压传动系统在钢管轧制中的应用
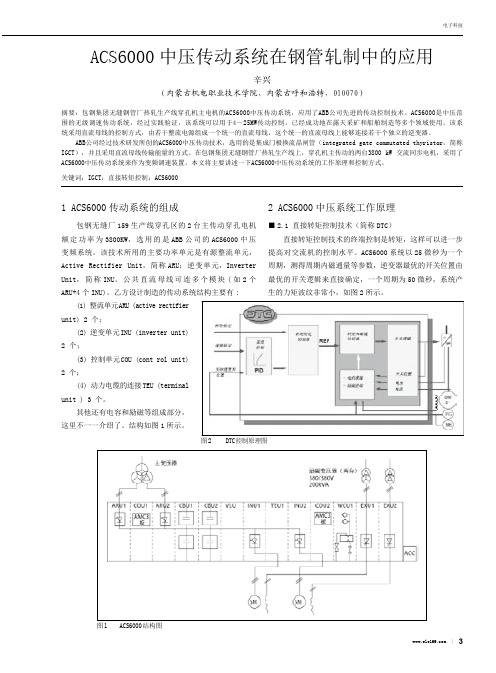
电子科技1 ACS6000传动系统的组成包钢无缝厂159生产线穿孔区的2台主传动穿孔电机额定功率为3800KW,选用的是ABB公司的ACS6000中压变频系统。
该技术所用的主要功率单元是有源整流单元,Active Rectifier Unit,简称ARU;逆变单元,Inverter Unit,简称INU。
公共直流母线可连多个模块(如2个 ARU+4个INU)。
乙方设计制造的传动系统结构主要有:(1) 整流单元ARU (active rectifierunit) 2 个;(2) 逆变单元INU (inverter unit)2 个;(3) 控制单元COU (cont rol unit)2 个;(4) 动力电缆的连接TEU (terminalunit ) 3 个。
其他还有电容和励磁等组成部分,这里不一一介绍了。
结构如图1所示。
2 ACS6000中压系统工作原理■2�1 直接转矩控制技术(简称DTC)直接转矩控制技术的终端控制是转矩,这样可以进一步提高对交流机的控制水平。
ACS6000系统以25微秒为一个周期,测得周期内磁通量等参数,逆变器最优的开关位置由最优的开关逻辑来直接确定,一个周期为50微秒,系统产生的力矩波纹非常小,如图2所示。
ACS6000中压传动系统在钢管轧制中的应用辛兴(内蒙古机电职业技术学院,内蒙古呼和浩特,010070)摘要:包钢集团无缝钢管厂热轧生产线穿孔机主电机的ACS6000中压传动系统,应用了ABB公司先进的传动控制技术。
ACS6000是中压范围的无级调速传动系统,经过实践验证,该系统可以用于4~25MW传动控制,已经成功地在露天采矿和船舶制造等多个领域使用。
该系统采用直流母线的控制方式,由若干整流电源组成一个统一的直流母线,这个统一的直流母线上能够连接若干个独立的逆变器。
ABB公司经过技术研发所创的ACS6000中压传动技术,选用的是集成门极换流晶闸管(integrated gate commutated thyristor,简称IGCT),并且采用直流母线传输能量的方式。
轧机主传动系统
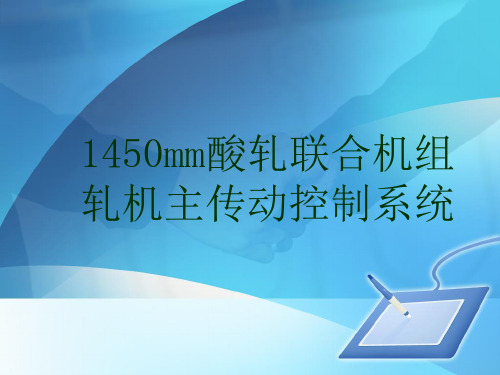
轧机主传动系统
1 基础自动化系统配 置 主传动概述 4 逆变器
2
5 6
整流器 传动设备的调试
3
主电机
基础自动化系统配置
酸轧机组轧机部分的整个自动化系统由交流传动 (传动系统采用TMIEC的全数字交流变频调速装 置)、远程I/O站、高性能工艺控制器(Siemens 公司的TDC)及PLC可编程系统组成。 交流传动装置和远程I/O站与PLC之间采用 Profibus-DP网通讯。过程计算机系统和TDC与PLC 之间采用以太网通讯。
轧机主传动概述
TMDrive-70传动采用三电平PWM脉 宽调制,全数字矢量控制的整流器和 逆变器构成的传动系统。采用共同直 流母线的控制模式。
轧机主传动电机
主传动电机传动采用直流母线的方式,由 变压器、整流装置给直流母线供电,通过 逆变器给主传动变频调速电机提供驱动。
电机采用异步电机,自带编码器和风机。 风机的操作与电机联锁,由变频器进行控 制。
本传动系统使用的是三电平PWM IEGT 整流器。 实现的功能: 1.全逆变能力 2.在装置容量范围内可控制功率因数(PF) 到1.0 3.高次谐波电流最小化 4.系统不需外部谐波滤波装置和动态无功补 偿(SVC)装置。
整流器的主要技术参数: 额定容量: 8MVA and 10MVA (3400V) 输入电压: +/-2430VDC AC 输出电压: 最大3400VAC DC 输入功率因数:>0.95 能量回馈: 能 电压波动: 在进线母线上+/-10 %波动 频率: 50+/-0.5Hz 冷却方式: 水冷和空冷
传动设备的调试与维护
“Navigator”是专为TMEIC 系列传动 系统装置的调试维护工具, 它可用于TMD-70 , TMD-50, TMD-10e2 等TMEIC 的传动设备。
中压传动系统在厚板轧机主传动中的应用
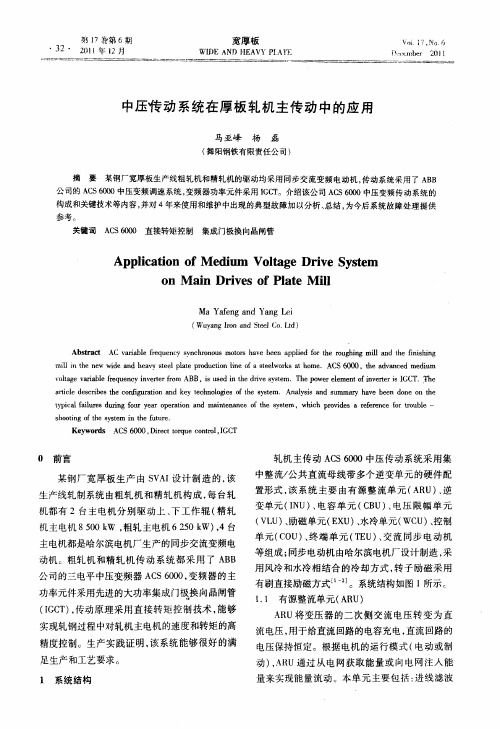
双 电平 直 流母 线 , 这样 使得 输 出电压波形 更平 滑 , 工作 电压更 高 。
+ C, P( D N 零电平),一 C, D 而不是传统 的单相
I电 源 I 主
一 (
主 变 压 器
励 磁
三 三
毒
j ; £ ;
l { {
: 蜀B : {U N I ≮ X R R 1 B I N W E 匹 U 1 审 V U U C U U 2 u L 1 2 】 c 2 丑 审 l u l U
精度控制。生产实践证 明, 系统能够很好的满 该
足生产和工艺要求 。
1 系统结 构
第 6期
马 亚峰等: 压传动系 中 统在 厚板轧机主 传动中 的应用
3 3・
装置 、 3组 IC G T相模 块 、 流 电感 等 。A U输 入 限 R 是 三相 交 流 电 , 出直 流用 三 电平 控制 方 式 : 输
13 电容单 元 ( B . C U) C U是用 来平 滑 中间 直 流 回路 电压 , 将 整 B 并
控整个传动系统和冷却系统 的功能 , 它包括 与上
位控制的接 口和本地控制的接 口。
2 软件 参数 及关 键技术
流器和逆变器解耦。本单元 主要包括直流 回路 电 容器 、 充电回路和接地开关 。 14 电压限幅单元( L ) . . VU V U在过压情况下 , L 可以实时对直流 回路电
2 1 控制器软件及系统参数 .
A C 和A8 M3 C0控制器的应用软件编程均使
・
3 4
A B公 司 自动 化 系统 用 F B( 能 图 ) 件 , B C 功 软
A S 00系统 的参数设定可使用传 动柜 面板上 C 0 6
《4300中厚板轧机主传动系统的扭振研究》

《4300中厚板轧机主传动系统的扭振研究》篇一一、引言在现代化钢铁生产过程中,轧机作为关键设备之一,其主传动系统的性能直接关系到生产效率和产品质量。
扭振作为轧机主传动系统中的一种常见问题,不仅会影响设备的正常运行,还可能对设备造成损害。
因此,对4300中厚板轧机主传动系统的扭振问题进行研究,对于提高轧机的生产效率和产品质量具有重要意义。
二、4300中厚板轧机主传动系统概述4300中厚板轧机主传动系统主要由电动机、联轴器、减速器、轧辊等部分组成。
在生产过程中,电动机通过联轴器将动力传递给减速器,再由减速器驱动轧辊进行轧制作业。
由于轧制过程中存在各种复杂的力学作用,使得主传动系统容易产生扭振现象。
三、扭振产生的原因及危害扭振产生的原因主要包括电动机与负载之间的转矩不匹配、系统刚度不足、传动部件制造误差等。
这些因素导致主传动系统在运行过程中产生周期性的扭转振动,不仅会影响设备的正常运行,还会导致设备部件的疲劳损伤,甚至引发严重的安全事故。
四、扭振研究方法及实验设计针对4300中厚板轧机主传动系统的扭振问题,可采用理论分析、仿真分析和实验研究等方法。
首先,通过建立主传动系统的数学模型,对扭振的产生机理进行理论分析。
其次,利用仿真软件对主传动系统进行仿真分析,预测扭振的特性和影响因素。
最后,通过实验研究验证理论分析和仿真分析的结果,为实际生产提供指导。
实验设计主要包括传感器布置、数据采集和处理、实验方案制定等步骤。
传感器用于监测主传动系统的运行状态和扭振特性,数据采集和处理用于获取扭振的相关信息,实验方案则需根据实际生产条件和需求进行制定。
五、实验结果与分析通过实验研究,可以获取4300中厚板轧机主传动系统的扭振特性和影响因素。
首先,通过对传感器采集的数据进行处理和分析,可以得出主传动系统的扭振幅度和频率等特性。
其次,通过对比不同工况下的扭振特性,可以找出影响扭振的主要因素。
最后,根据理论分析和仿真分析的结果,提出相应的优化措施和改进方案。
《2024年4300中厚板轧机主传动系统的扭振研究》范文

《4300中厚板轧机主传动系统的扭振研究》篇一一、引言在钢铁工业中,轧机是关键设备之一,其中主传动系统是轧机的核心部分。
而扭振问题则是轧机主传动系统中一个重要且复杂的问题。
随着钢铁工业的快速发展,轧机的主传动系统对材料的高效加工与处理提出了更高要求,同时也伴随着扭振现象的日益凸显。
本文针对4300中厚板轧机主传动系统的扭振问题进行研究,旨在为轧机的高效、稳定运行提供理论支持。
二、4300中厚板轧机主传动系统概述4300中厚板轧机的主传动系统通常由电机、减速器、工作辊和扭振保护装置等部分组成。
这种类型的轧机常用于加工中厚板材料,其主传动系统具有较高的承载能力和较大的扭矩传递能力。
然而,在生产过程中,由于各种因素的影响,如电机转速的波动、工作辊的不平衡等,常常会出现扭振现象。
三、扭振产生的原因及影响扭振的产生主要源于传动系统的非线性因素和外部干扰。
在4300中厚板轧机的主传动系统中,扭振现象主要表现为传动轴的周期性扭转振动。
这种振动不仅会降低设备的生产效率,还会对设备的结构造成损伤,甚至可能导致设备的故障和停机。
此外,扭振还会对产品的质量产生不良影响,如造成板材的厚度不均等。
四、扭振研究方法及实验设计针对4300中厚板轧机主传动系统的扭振问题,本文采用理论分析、数值模拟和实验研究相结合的方法进行研究。
1. 理论分析:通过对传动系统的力学模型进行深入分析,了解扭振的产生原因和传播路径。
2. 数值模拟:利用有限元软件对传动系统进行仿真分析,了解不同工况下的扭振特性和变化规律。
3. 实验研究:在现场进行实验测试,收集扭振数据,为后续的数值模拟和理论分析提供依据。
实验设计主要包括以下几个方面:(1)传感器布置:在关键部位安装传感器,实时监测传动系统的扭振情况。
(2)数据采集:通过传感器实时采集扭振数据,包括振幅、频率等。
(3)数据分析:对采集的数据进行分析处理,了解扭振的特性和变化规律。
五、研究结果及分析通过理论分析、数值模拟和实验研究,本文得出以下结论:1. 扭振主要源于传动系统的非线性因素和外部干扰,其中电机转速的波动是主要影响因素之一。
轧机主传动系统

实现的功能: 1.全逆变能力 2.在装置容量范围内可控制功率因数(PF) 到1.0 3.高次谐波电流最小化 4.系统不需外部谐波滤波装置和动态无功补 偿(SVC)装置。
整流器的主要技术参数:
额定容量: 8MVA and 10MVA (3400V)
输入电压:
+/-2430VDC AC
输出电压: 最大3400VAC DC
传动设备的调试与维护
“Navigator”是专为TMEIC 系列传动 系统装置的调试维护工具, 它可用于TMD-70 , TMD-50, TMD-10e2 等TMEIC 的传动设备。
基本用户界面
1450mm酸轧联合机组 主传动控制系统
谢谢
输入功率因数:>0.95
能量回馈: 能
电压波动: 在进线母线上+/-10 %波动
频率:
50+/-0.5Hz
冷却方式: 水冷和空冷
逆变器
逆变器是一种把直流电 能转变成交流电的装置。 我们常见的应急电源, 一般是把直流电瓶逆变 成220V交流的。简单来 讲,逆变器就是一种将 直流电转化为交流电的 装置。
4200KW
4200KW
4200KW
电机转速
300/900 r/min
400/1200 r/min
400/1200 r/min
400/1200 r/min
400/1200 r/min
- 1、下载文档前请自行甄别文档内容的完整性,平台不提供额外的编辑、内容补充、找答案等附加服务。
- 2、"仅部分预览"的文档,不可在线预览部分如存在完整性等问题,可反馈申请退款(可完整预览的文档不适用该条件!)。
- 3、如文档侵犯您的权益,请联系客服反馈,我们会尽快为您处理(人工客服工作时间:9:00-18:30)。
中宽带轧机主传动控制系统
摘要本文结合具体工程实例详细分析了交流同步大电动机的交交变频控制系统。
关键词交流同步电机;交交变频控制;SIMADYN D
1 概述
交交变频控制系统具有功率因数较高、运行效率高、节省成本的优势。
某中宽带工程中R1四辊可逆轧机电机6800 kW,二台,转速50/110 r/min,精轧机组四辊轧机机列由F1-F7组成,F1-F3电机7000 kW,转速160/400 r/min F4-F5电机,6500 kW,转速150/520 r/min,F6-F7电机,6000 kW转速200/650 r/min,以上电机均为交流同步电机.
主传动电动机为交交变频变流装置供电的交流同步机,控制装置采用SIEMENS公司的SIMADYN D全数字矢量控制系统。
每套交交变频器由三台电网自然换流无环流可逆的三相桥式变流器组成,对应同步电机定子A,B,C三相,每相连接成三相桥式电路。
三相交交变频器采用逻辑无环流、三相有中点方式,由一台原、副边三分裂整流变压器供电,两台电机整流变压器接法互相错开,以减少供电高次谐波。
输出端采用星点联接,电机定子绕组为三相星接,电机星点和变频器星点独立。
这种结构的优点是:可以采用交流偏置技术,使整流变压器二次电压降低、晶闸管电压安全系数提高、变频器容量降低、电机内无三次谐波。
同步机定子三相交交变频采用逻辑无环流三相有中点方式,其特点为:
·采用耐压4200 V晶闸管元件,交交变频器最大输出峰值电压2333 V。
·采用全关断光电检测零电流技术,使无环流切换死区减少到≤1.1 ms;
·采用LEM电压变换器,以实现实际电压值的检测。
·采用变频器输出侧直流电流检测做电流闭环控制、及电流保护。
·采用六脉冲传输同轴电缆,提高了触发系统的抗干扰能力;
·每台主柜门板都装有集中显示器,以显示各功率单元的工作情况及主柜的通风情况。
本系统采用西门子公司的SIMADYN D全数字控制系统电机实现控制,并以光线通讯加以连接,在系统中实现数据交换、监视和统一管理。
系统的基本组态如下所述:
以SIMADYN D为基础的传动控制级,完成对电机的调速控制,包括同步电机的矢量控制、电机的启停控制和电机保护,同时为了使SIMADYN D能实现本地现场数据采集,故障显示及诊断,建立了本地通讯网。
采用一套数据通讯网实现综合控制,将SIMADYN D设备及上位机有机地连接起来帮助实现高级控制和集中管理。
交流同步电动机采用自同步控制方式,定子电流由磁场定向控制系统分解为两个独立的直流分量,即电流的转矩分量IM和励磁分量IF。
与直流调速相同,转矩分量设定值由速度调节器决定,励磁分量设定值由电动机功率因数cosφ及电流模型计算出来。
与同步电动机同轴相联的光电编码器检测电动机的转子位置信号cosγ和sinγ,由转子模型单元计算出负载角cosδ和sinδ,以及励磁电流给定值Ifd。
转子位置角γ与负载角δ相加可得磁场定向旋转角θ。
根据当前电动机运行的实际反馈值及系统设定值,计算出给定电流的转矩分量及励磁分量,给定电压的转矩分量和励磁分量,再经过矢量的旋转变换和2/3变换,形成三相定子电流给定值Ia、Ib、Ic,这些值送入带电流断续自适应调节,电压前馈控制的电流调节系统。
在轧机主传动系统中,每台同步电机都配有一套SIMADYN D控制系统,以完成各自的电机控制、保护和故障诊断等任务。
SIMADYN D控制系统硬件由双高度欧洲标准尺寸的高抗干扰和容错性的插入式线路板组成,模板按功能分为通用处理器板、特殊任务处理器板、存储器板、数字输入/输出板、模拟输入/输出板,根据不同的任务需要可任意配置。
各处理器之间的数据传送通过C总线和L总线两种总线来完成,每个处理器模板都有它自己的程序和数据存储器,可以独立地完成分配给它的任务,并实现多处理器并行工作。
外部开关信号通过输入/输出模块连接,这些标准接口模块提供电气隔离、信号的匹配和变换,用于操作监视和服务的外围装置通过总线或串行接口联接起来。
同时,SIMADYN D还提供多种通讯手段与其他设备、系统进行数据传输,包括控制装置与上位机间的通讯;控制装置与HMI间的通讯;控制装置之间的通讯以及与下位机间的数据传输等等。
本项目中SIMADYN D控制系统实现交交变频同步电机矢量变换运算。
系统还分别给各个处理器设计了管理程序,用来管理通过系统内部总线的处理器之
间的数据交换,通过现场总线实现与远程I/O站的数据交换,SIMADYN D设备与上位机的数据传输以及与用于实现故障诊断、运行监控画面之间的信息传递由通讯网络完成,同时,系统支持运行中的在线调试。
软件主要功能:
闭环控制功能
开环控制功能
定位功能
逻辑控制功能
扁头定位功能
负荷平衡控制功能
防扭振控制功能
控制系统通讯
整个通讯系统按不同的通讯任务分为三个层次进行设计:
SIMADYN D本地通讯主要完成传动控制设备的现场数据采集、本地操作以及故障自诊断等任务。
信息管理通讯负责系统各类信息的收集、处理、存储、检索以及输出。
SIMADYN D与上一级控制系统之间数据传输以实现连续生产过程控制、系统协调及最佳控制。
2 SIMADYN D本地通讯
SIMADYN D作为单台电机的控制系统要实现其本身的电机控制,逻辑操作,电机保护及故障诊断等任务,这样需有一套独立的本地通讯网,以实现其本身的控制任务。
SIMADYN D配置CS7通用通讯板,SS52通讯子板挂靠在CS7通讯板完成本地通讯任务:
SS52使用SINEC L2 DP通讯协议,用以实现SIMADYN D通过现场总线与远程I/O ET200之间的数据传输,主要任务是支持SIMADYN D对现场的数据采集及控制信号传送。
为每台电机的控制装置选配两套ET200远程I/W系统,完成电机侧的现场数据采集。
电机侧ET200:
定子绕组温度检测
轴承润滑状况
轴承温度检测
电机通风状况
高压侧ET200:
定子高压开关信号
转子高压开关信号
整流变压器温度、瓦斯信号
3 信息管理及系统监控
为每台SIMADYN D控制设备配置两块通讯子板SS4。
一块SS4使用DUST1通讯协议用以实现SIMADYN D 与调试用PC机的数据通讯,主要任务是支持Service IBS服务软件的在线访问,以协助现场调试。
另一块SS4与SIEMENS公司专用操作面板OP2N进行数据交换,实现信息管理及传动系统的故障收集、显示、诊断以及对系统运行状态的显示。
完成运行参数监视、故障报警、开环调试运行等功能。
4 系统过程控制通讯
SIMAD1YN D控制设备CS7+SS52通讯子板以支持SINEC L2-DP通讯协议。
SIMADYN D控制设备配置SS52通讯子板,通过SINEC L2-DP网络完成与上位机的通讯,实现对传动系统的控制。
SINEC L2-DP是一种欧洲标准的现场总线协议,因此,在与现场其他自动化设备接口时,其兼容性比较好。
某中宽带工程高线车间主传动采用此设计方法,自投产以来运行可靠,取得了很好的效益。
参考文献
[1]钢铁企业电力设计手册编委会.钢铁企业电力设计手册[M].交流电动机调
速系统:冶金工业出版社,1996,1(25).。