钢铁材料的磷化生产
第3章 钢铁的磷化

Metal grains
Amorphous precipitation
B段:电势变正,形成磷化膜非晶底层 3Me(H2PO4)2 → Me3(PO4)2 ↓+ 4H3PO4
a' 段:基体金属还在继续溶解 Fe + 2H3PO4→Fe(H2PO4)2 + H2↑
Iron phosphate
C段:电势缓慢变正,对应磷化膜的形成过程
1~60
锰系 铁系 锌钙系
1~60 5~10 1~15
[Zn2Ca(PO4)2•2H2O 浅灰→深灰 ] 结晶状 [Zn2Fe(PO4)2•4H2O] [ZnFe Mn (PO4)2•4H2O] Fe2O3 [Fe3 (PO4)2•8H2O] 灰→深灰结 晶状
锌锰系
1~60
碱金属轻铁系
暗灰彩红色 0.5~1.0 无定型
• 磷化膜由一系列大小不同的晶体所组 成 • 在晶体的连结点上形成具有细小裂缝 的多孔结构 • 多孔的晶体结构使钢铁件表面的耐蚀 性、吸附性、减摩性等得以改善
(a)锌系钼酸盐复合磷化膜
(b) 锌系钒酸盐复合磷化膜
• 磷化膜的厚度一般在1~50mm
• 具有良好的高温耐蚀性,在200~300 ℃仍具有一定的耐蚀性 • 温度过高(达450℃),膜层防蚀能力 显著下降 • 大气及矿物油、动植物油、苯、甲苯 等有机气氛中均具有很好的抗蚀能力 • 在酸、碱、雨水及水蒸气中耐蚀性能 差
铁系
P P比 100 % PH
P+H——磷化膜总量 H——Zn3(PO4)2· 4H2O P——除Zn3(PO4)2· 4H2O以外的物质
P—Zn2Fe(PO4)2· 4H2O (磷叶石,Phosphophyllite,[fsfu'filait]) H—Zn3(PO4)2· 4H2O (磷锌矿,Hopeite,[həu'pait] ) P比越高的磷化膜,其耐酸碱、防腐蚀性能越好
钢铁的锌系磷化
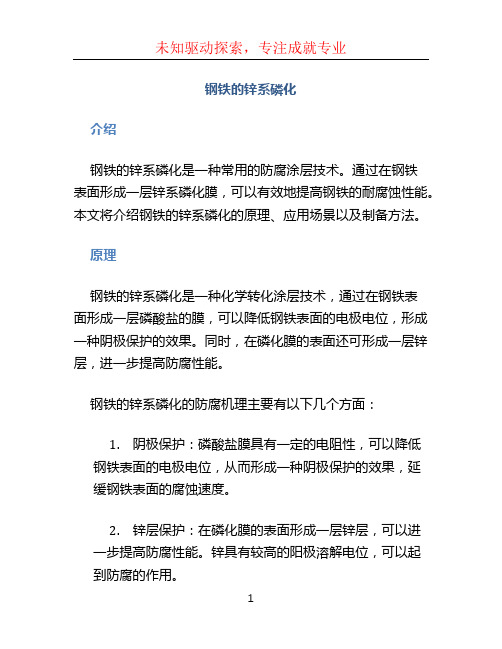
钢铁的锌系磷化介绍钢铁的锌系磷化是一种常用的防腐涂层技术。
通过在钢铁表面形成一层锌系磷化膜,可以有效地提高钢铁的耐腐蚀性能。
本文将介绍钢铁的锌系磷化的原理、应用场景以及制备方法。
原理钢铁的锌系磷化是一种化学转化涂层技术,通过在钢铁表面形成一层磷酸盐的膜,可以降低钢铁表面的电极电位,形成一种阴极保护的效果。
同时,在磷化膜的表面还可形成一层锌层,进一步提高防腐性能。
钢铁的锌系磷化的防腐机理主要有以下几个方面:1.阴极保护:磷酸盐膜具有一定的电阻性,可以降低钢铁表面的电极电位,从而形成一种阴极保护的效果,延缓钢铁表面的腐蚀速度。
2.锌层保护:在磷化膜的表面形成一层锌层,可以进一步提高防腐性能。
锌具有较高的阳极溶解电位,可以起到防腐的作用。
3.磷酸盐膜的吸附能力:磷酸盐膜具有良好的吸附能力,可以与钢铁表面的氧化铁发生反应,形成一个致密的磷酸盐膜。
这种膜具有很好的附着力和耐腐蚀性能。
应用场景钢铁的锌系磷化技术广泛应用于钢结构、汽车零部件、船舶、建筑材料等领域。
主要用于提高钢铁材料的耐腐蚀性能,延长使用寿命。
具体应用场景包括:1.钢结构:钢结构在室内外环境下易受到腐蚀,通过施加锌系磷化涂层可以有效延缓腐蚀速度,提高钢结构的耐久性。
2.汽车零部件:汽车零部件常暴露在潮湿、多灰尘的环境中,易受到腐蚀影响。
通过施加锌系磷化涂层可以提高零部件的耐腐蚀性能,延长使用寿命。
3.船舶:船舶在海洋环境中容易受到海水腐蚀。
通过施加锌系磷化涂层可以提高船舶的耐腐蚀性能,延长使用寿命。
4.建筑材料:建筑材料在室外环境下易受到大气环境和酸雨的腐蚀。
通过施加锌系磷化涂层可以提高建筑材料的耐腐蚀性能,延长使用寿命。
制备方法钢铁的锌系磷化有多种制备方法,常用的方法包括酸洗法、电化学法和浸泡法等。
1.酸洗法:将钢铁表面经过酸洗处理,去除表面的氧化铁和杂质,然后放入磷酸盐溶液中进行磷化反应。
这种方法制备的锌系磷化膜结构致密,耐腐蚀性能较好。
磷化处理工艺
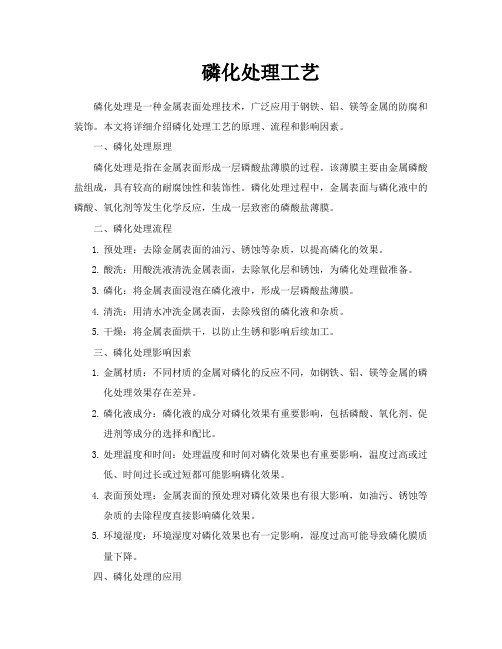
磷化处理工艺磷化处理是一种金属表面处理技术,广泛应用于钢铁、铝、镁等金属的防腐和装饰。
本文将详细介绍磷化处理工艺的原理、流程和影响因素。
一、磷化处理原理磷化处理是指在金属表面形成一层磷酸盐薄膜的过程。
该薄膜主要由金属磷酸盐组成,具有较高的耐腐蚀性和装饰性。
磷化处理过程中,金属表面与磷化液中的磷酸、氧化剂等发生化学反应,生成一层致密的磷酸盐薄膜。
二、磷化处理流程1.预处理:去除金属表面的油污、锈蚀等杂质,以提高磷化的效果。
2.酸洗:用酸洗液清洗金属表面,去除氧化层和锈蚀,为磷化处理做准备。
3.磷化:将金属表面浸泡在磷化液中,形成一层磷酸盐薄膜。
4.清洗:用清水冲洗金属表面,去除残留的磷化液和杂质。
5.干燥:将金属表面烘干,以防止生锈和影响后续加工。
三、磷化处理影响因素1.金属材质:不同材质的金属对磷化的反应不同,如钢铁、铝、镁等金属的磷化处理效果存在差异。
2.磷化液成分:磷化液的成分对磷化效果有重要影响,包括磷酸、氧化剂、促进剂等成分的选择和配比。
3.处理温度和时间:处理温度和时间对磷化效果也有重要影响,温度过高或过低、时间过长或过短都可能影响磷化效果。
4.表面预处理:金属表面的预处理对磷化效果也有很大影响,如油污、锈蚀等杂质的去除程度直接影响磷化效果。
5.环境湿度:环境湿度对磷化效果也有一定影响,湿度过高可能导致磷化膜质量下降。
四、磷化处理的应用1.防腐:磷化膜具有较高的耐腐蚀性,可用于钢铁、铝、镁等金属的防腐处理。
例如,在建筑、船舶、汽车等领域,磷化处理被广泛应用于金属结构的防腐保护。
2.装饰:磷化膜具有较好的装饰性,可用于金属表面的美化处理。
例如,在电子产品、家具等领域,磷化处理被广泛应用于产品的外观装饰。
3.耐磨:磷化膜还具有较好的耐磨性,可用于提高金属表面的耐磨性能。
例如,在机械零件、工具等领域,磷化处理被广泛应用于提高产品的耐磨性能。
4.粘合:磷化膜还可以作为粘合剂使用,将不同金属材料粘合在一起。
冷轧钢板磷化工艺流程

冷轧钢板磷化工艺流程冷轧钢板磷化工艺流程冷轧钢板磷化是将金属表面与磷化液反应,产生一层磷化物保护层的化学处理方法。
它广泛应用于钢铁制品、汽车、电器、建筑等行业,在对钢材表面进行防腐蚀、电气绝缘、增强涂层附着力等领域有广泛应用。
整体工艺流程:1. 预处理:钢板表面去油、浸蚀,使得其在后续的磷化液处理中更易于形成磷化保护层。
2. 缸槽清洗:将钢板放置于洗涤槽内,进行浸泡清洗,去除不纯物质。
3. 磷酸浸泡:将钢板放入磷酸液中浸泡,使其表面与磷酸进行反应。
4. 洗涤处理:将钢板取出,用热水或冷水进行冲洗。
5. 中和处理:将钢板放入中和液中,对其进行中和处理。
6. 工艺完成:将钢板取出,进行烘干处理。
详细描述:1. 预处理在钢板进行磷化处理之前,首先需要进行预处理。
预处理是为了去除钢板表面的不纯物质,使得钢板表面更加纯净,更有利于其与磷化液之间产生化学反应。
预处理主要分为去油和浸蚀两个步骤。
去油处理是指用特殊的化学药品去掉钢板表面的油脂。
在去油处理之前,需要先进行清洗,用水冲洗钢板表面,去除表面的灰尘和杂物。
然后加入去油剂,将钢板放入去油槽内进行浸泡处理,时间一般为1-2分钟。
去油后,需要再次用水进行冲洗,保证钢板表面绝对干净。
浸蚀处理是指将钢板放入浸蚀液中进行处理,使其表面形成钝化层,从而提高其抗腐化能力。
浸蚀液的成分通常为硝酸和氢氟酸,浸蚀液的温度一般在30℃左右,浸泡时间为5分钟左右。
浸蚀后,再次用水清洗表面,确保表面干净无油。
2. 缸槽清洗将经过预处理的钢板放入清洗槽内进行清洗,清除表面残留物。
缸槽清洗采用封闭式清洗槽,将钢板放入清洗槽内,槽内注满清洗液体,使用搅拌器,利用清洗液体的冲刷作用对钢板表面进行清洗。
清洗液的成分通常为过氧化氢和有机溶剂,清洗液的温度一般在40-50℃之间,工作时间约为2-5分钟。
清洗完毕后,使用清水对钢板进行冲洗,去除表面清洗液的残留物,确保钢板表面干净无杂质。
3. 磷酸浸泡将经过缸槽清洗的钢板放入磷酸浸泡槽中,进行磷酸浸泡处理,使其表面形成一层磷化物。
钢铁磷化作业指导书

钢铁磷化作业指导书一、作业目的钢铁磷化作业是指对钢铁表面进行磷化处理,以提高钢铁的耐腐蚀性和润滑性能。
本指导书旨在确保钢铁磷化作业的安全、高效进行,保证产品质量。
二、作业前准备1. 安全措施:a. 确保作业场所通风良好,避免有毒气体积聚;b. 工作人员必须穿戴防护服、防护手套、护目镜等个人防护装备;c. 确保作业场所有灭火器材和急救设备;d. 作业人员需接受相关安全培训,了解紧急情况下的应急处理方法。
2. 设备准备:a. 磷化槽:确保磷化槽内液位正常,温度稳定在指定范围内;b. 清洗槽:确保清洗槽内液位充足,清洗液浓度符合要求;c. 酸洗槽:确保酸洗槽内液位充足,酸洗液浓度符合要求;d. 磷化剂:确保磷化剂储存充足,质量合格。
三、作业步骤1. 钢铁表面准备:a. 清洗:将待磷化的钢铁件放入清洗槽中,使用清洗液彻底清洗表面油污、杂质等;b. 酸洗:将清洗后的钢铁件放入酸洗槽中,浸泡一段时间,去除表面的氧化物和锈蚀物;c. 冲洗:将酸洗后的钢铁件放入清水中冲洗,确保酸洗剂完全被冲洗干净。
2. 磷化处理:a. 将冲洗后的钢铁件放入磷化槽中,确保钢铁件完全浸入磷化液中;b. 控制磷化槽内的温度在指定范围内,一般为40-60摄氏度;c. 根据磷化液的浓度要求,控制磷化液的添加量和磷化时间;d. 确保磷化槽内的搅拌器正常运转,以保证液体均匀分布。
3. 磷化后处理:a. 将磷化后的钢铁件从磷化槽中取出,放入清水中彻底冲洗干净;b. 将冲洗后的钢铁件进行烘干处理,确保表面无水分残留;c. 检查磷化后的钢铁件表面是否均匀、光滑,无明显缺陷。
四、作业注意事项1. 严格遵守安全操作规程,佩戴个人防护装备,确保作业人员的安全;2. 定期检查和维护磷化槽、清洗槽、酸洗槽等设备,确保其正常运行;3. 定期检测磷化液的浓度和PH值,确保其符合要求;4. 严禁将有毒有害物质倾倒到排水系统中,应妥善处理废液;5. 磷化槽内应保持良好的清洁状态,定期清理沉淀物和杂质;6. 作业人员应定期接受相关培训,了解新的操作规程和安全知识。
钢铁磷化作业指导书

钢铁磷化作业指导书一、作业目的钢铁磷化是一种常见的表面处理工艺,通过在钢铁表面形成一层磷化膜,可以提高钢铁材料的耐腐蚀性能和润滑性能。
本作业指导书旨在提供详细的作业指导,确保钢铁磷化作业的质量和安全。
二、作业准备1. 磷化液准备:根据所需的磷化液配方,准确称取所需的化学品,并按照配方比例将其溶解于适量的水中。
2. 设备准备:确保作业所需的设备(如磷化槽、搅拌器、加热器等)完好无损,并进行必要的清洁和消毒。
3. 个人防护用品准备:确保所有作业人员配备了必要的个人防护用品,包括防护服、手套、护目镜、防毒面具等。
三、作业步骤1. 清洗:将待磷化的钢铁材料进行彻底清洗,去除表面的油污、灰尘等杂质。
可以使用溶剂、碱性清洗剂或超声波清洗等方法进行清洗,确保表面干净无污染。
2. 预处理:根据磷化液配方的要求,对清洗后的钢铁材料进行必要的预处理,如酸洗、酸蚀等。
预处理的目的是去除表面的氧化物和锈蚀物,为后续的磷化作业做好准备。
3. 磷化:将预处理后的钢铁材料浸入事先准备好的磷化液中,保持一定的温度和时间。
磷化液中的磷化剂会与钢铁表面的金属离子发生反应,形成一层磷化膜。
根据需要可以进行多次浸泡,以增加磷化膜的厚度。
4. 水洗:磷化完成后,将钢铁材料取出,进行充分的清洗和水洗,以去除残留的磷化液和杂质。
可以使用自来水或去离子水进行水洗,确保洗净彻底。
5. 中和:将磷化液中的废液进行中和处理,以减少对环境的污染。
可以使用中和剂将废液中的酸性或碱性物质中和至中性。
6. 除油:对磷化后的钢铁材料进行除油处理,去除表面的油污和残留的磷化液。
可以使用溶剂、碱性清洗剂或蒸汽清洗等方法进行除油处理。
7. 干燥:将除油后的钢铁材料进行充分的干燥,以去除表面的水分。
可以使用热风烘干、自然晾干或真空干燥等方法进行干燥。
四、作业注意事项1. 个人防护:在进行钢铁磷化作业时,必须佩戴好个人防护用品,包括防护服、手套、护目镜、防毒面具等。
避免磷化液接触皮肤、眼睛和呼吸道,以免引起刺激或伤害。
钢铁磷化作业指导书

钢铁磷化作业指导书标题:钢铁磷化作业指导书引言概述:钢铁磷化作业是一项重要的表面处理工艺,它能够为钢铁制品提供良好的防腐蚀性能和装饰效果。
为了保证磷化作业的质量和效率,制定一份详细的作业指导书是必要的。
本文将从五个大点出发,详细阐述钢铁磷化作业的指导要点。
正文内容:1. 磷化作业前的准备1.1 确定磷化液配方:根据不同的钢铁材料和磷化要求,选择合适的磷化液配方,包括磷酸盐、酸性添加剂和腐蚀抑制剂等。
1.2 准备工件表面:对工件进行表面清洁处理,包括去除油污、锈蚀和氧化物等,以保证磷化液能够充分接触到工件表面。
2. 磷化作业的操作步骤2.1 清洗工件:将工件浸入去污剂中清洗,去除表面的油污和杂质。
2.2 酸洗处理:将工件浸入稀硫酸溶液中进行酸洗,去除表面的锈蚀和氧化物。
2.3 磷化处理:将工件浸入磷化液中进行磷化反应,形成磷化层。
2.4 中和处理:将磷化后的工件浸入碱性溶液中进行中和处理,以去除残留的酸性物质。
2.5 清洗和干燥:用清水冲洗工件,并进行干燥处理,以去除表面的残留物和水分。
3. 磷化作业中的注意事项3.1 安全操作:操作人员应佩戴防护手套、护目镜等个人防护装备,注意防止磷化液的溅洒和吸入。
3.2 控制磷化液浓度:根据工件的磷化要求,控制磷化液的浓度,避免浓度过高或过低对工件造成不良影响。
3.3 控制磷化时间:根据工件的材料和磷化要求,控制磷化时间,避免过长或过短导致磷化层质量不理想。
3.4 定期检测磷化液:定期检测磷化液的浓度和PH值,及时调整和更换磷化液,以保证作业质量。
3.5 废液处理:对废液进行合理处理,遵守环保要求,防止废液对环境造成污染。
4. 磷化作业的质量控制4.1 磷化层厚度检测:使用合适的测量仪器对磷化层的厚度进行检测,确保符合要求。
4.2 磷化层均匀性检测:通过目测或显微镜观察磷化层的均匀性,避免出现不均匀的情况。
4.3 磷化层附着力检测:使用合适的试验方法对磷化层的附着力进行检测,确保符合要求。
磷化简介

磷化简介磷化是金属材料防腐蚀的重要方法之一,其目的在于给基体金属提供防腐蚀保护、用于喷漆前打底、提高覆膜层的附着力与防腐蚀能力及在金属加工中起减摩润滑作用等。
按用途可分为三类:1、涂装性磷化2、冷挤压润滑磷化 3、装饰性磷化。
按所用的磷酸盐分类有:磷酸锌系、磷酸锌钙系、磷酸铁系、磷酸锌锰系、磷酸锰系。
根据磷化的温度分类有:高温(80 ℃以上)磷化、中温(50~70℃)磷化、低温磷化(40 ℃左右)和常温磷化( 10~30 ℃)。
一、磷化成膜机理磷化主要有以下过程:(1)金属的溶解过程即金属与磷化液中的游离酸发生反应:M+H3PO4 = M(H2PO4)2+H2↑(2)促进剂的加速过程为:M(H2PO4)2+Fe+[O]→M3(PO4)2+FePO由于氧化剂的氧化作用,加速了不溶性盐的逐步沉积,使金属基体与槽液隔离,会限制甚至停止酸蚀的进行。
(3)磷酸及盐的水解磷化液的基本成分是一种或多种重金属的酸式磷酸盐, 其分子式为Me(H2PO4)2,这些酸式磷酸盐溶于水,在一定浓度及pH值下发生水解,产生游离磷酸:Me(H2PO4)2=MeHPO4+H3PO43MeHPO4=Me3(PO4)2+H3PO4H3PO4=H2PO4-+H+= HPO2-4 + 2H+ =PO3-4 + 3H+由于金属工件表面的H+浓度急剧下降,导致磷酸根各级离解平衡向右移动,最终成为磷酸根。
(4 ) 磷化膜的形成当金属表面离解出的PO3-4与磷化槽液中的金属离子Zn2+、Mn2+、Fe2+达到饱和时,即结晶沉积在金属工件表面,晶粒持续增长,直到在金属工件表面生成连续不溶于水的牢固的磷化膜:3M2 + + 2PO3 -4 + 4H2O = M3 ( PO4 ) 2·4H2O ↓2 M2 + + Fe2 + + 2PO3 -4 + 4H2O= M2 Fe ( PO4 ) 2· 4H2O金属工件溶解出的Fe2+一部分作为磷化膜的组成部分被消耗掉,而残留在磷化槽液中的Fe2+则氧化成Fe3+,生成FePO4沉淀,即磷化沉渣的主要成分之一。
- 1、下载文档前请自行甄别文档内容的完整性,平台不提供额外的编辑、内容补充、找答案等附加服务。
- 2、"仅部分预览"的文档,不可在线预览部分如存在完整性等问题,可反馈申请退款(可完整预览的文档不适用该条件!)。
- 3、如文档侵犯您的权益,请联系客服反馈,我们会尽快为您处理(人工客服工作时间:9:00-18:30)。
钢铁材料的磷化生产
一、概述:
钢件在含有磷酸盐的溶液中,经过一系 列的化学和电化学的反应,表面上生成一层 难溶于水的磷酸盐保护膜的过程称为钢的 磷化。磷化后生成的膜的颜色随着钢材中 碳含量不同而改变。低碳钢、中碳钢呈灰 白色;高碳钢及渗碳产品呈黑色。由于这 种膜有较多的细孔,经填充,浸油以及涂 漆,它在大气中就具有了较好的抗腐蚀能 力、润滑性能和良好的绝缘性能。(正常 情况,击穿电压在250≈380V,经涂装处理 后,击穿电压可在1000V)。膜的生成厚度 一般在5-20um,且与钢件的结合牢固。
3、按磷化处理方法分类
(1)化学磷化 将工件浸入磷化液中,依靠化学反应来实 现磷化,目前应用广泛。 (2)电化学磷化 在磷化液中,工件接正极,钢铁接负极进 行磷化。
4、按磷化膜质量分类
(1)重量级(厚膜磷化) 膜重7.5 g/m2以 上。 (2)次重量级(中膜磷化)膜重4.6-7.5 g/m2。 (3)轻量级(薄膜磷化)膜重1.1-4.5 g/m2。 (4)次轻量级(特薄膜磷化)膜重0.2-1.0 g/m2。
(3)刷涂磷化 上述两种方法无法实施时,采用本法,在常温下操作
,易涂刷,可除锈蚀,磷化后工件自然干燥,防锈性能 好,但磷化效果不如前两种。
四、磷化膜组成
分类 磷化液主要成份 膜组成
膜外观
锌系 Zn(H2PO4)2
磷酸锌和磷酸锌 浅灰→深灰 铁
锌钙系 Zn(H2PO4)2和 Ca (H2PO4)2
磷酸锌钙和磷酸 浅灰→深灰 锌铁
六、影响因素
1、温度 温度愈高,磷化层愈厚,结晶愈粗大。 温度愈低,磷化层愈薄,结晶愈细。 但温度不宜过高,否则Fe2+ 易被氧化成 Fe3+,加大沉淀物量,溶液不稳定。
2、游离酸度 游离酸度指游离的磷酸。其作用是促使铁 的溶解,形成较多的晶核,使膜结晶致密。 游离酸度过高,则与铁作用加快,会大量
钢件经磷化处理,其机械性能及磁性保持
不变。磷化的主要用途是:作防锈层;作 油漆底层;作变压器及电机转子、定子硅 钢片的绝缘层;材料拉拔和冷镦成型作减 磨层;因此,它常用于汽车、船舶、机械、 军事以及航天、航空等方面。
冷加工润滑用磷化膜要求 a 冷镦线材拉拔 单位面积上膜重1-10 g/m2; b 精密钢管拉拔 单位面积上膜重4-10 g/m2; c 钢铁件冷挤压成型 单位面积上膜重大于10 g/m2。
1、按磷化处理温度分类
(2)中温型 50-75℃,处理时间5-15分钟,磷化膜厚度 为1-7 g/m2,溶液游离酸度与总酸度的比值 为1:(10-15) 优点:游离酸度稳定,易掌握,磷化时间
短,生产效率高,耐蚀性与高温磷化膜基 本相同,目前应用较多。 (3)低温型 30-50℃ 节省能源,使用方便。
②Zn2+的影响,当Zn2+浓度过高 ,磷化 膜晶粒粗大,脆性增大,表面呈白色浮灰; 当Zn2+浓度过低,膜层疏松变暗。
七、磷化后处理 目的:增加磷化膜的抗蚀性、防锈性,通 常的做法是加封闭剂和浸油。
八、磷化渣 1、磷化渣的影响 ①磷化中生成的磷化渣,既浪费药品又加 大清渣工作量,处理不好还影响磷化质量, 视为不利。 ②磷化中在生成磷化渣的同时还会挥发出 磷酸,有助于维持磷化液的游离酸度,保 持磷化液的平衡,视为有利。
5、按施工方法分类
(1)浸渍磷化 适用于高、中、低温磷化 特点:设备简单,仅需加热
槽和相应加热设备,最好用不锈钢或橡胶衬里的槽子, 不锈钢加热管道应放在槽两侧。
(2)喷淋磷化 适用于中、低温磷化工艺,可处理大面积工件,如汽
车、冰箱、洗衣机壳体。特点:处理时间短,成膜反应 速度快,生产效率高,且这种方法获得的磷化膜结晶致 密、均匀、膜薄、耐蚀性好。
4、PH值 锰系磷化液一般控制在2-3之间,当PH>3 时,共件表面易生成粉末。当PH‹1.5时难以 成膜。铁系一般控制在3-5.5之间
5、溶液中离子浓度 ①溶液中Fe2+极易氧化成 Fe3+,导致不 易成膜。但溶液中Fe2+浓度不能过高,否 则,形成的膜晶粒粗大,膜表面有白色浮 灰,耐蚀性及耐热性下降。
三、磷化分类
1、按磷化处理温度分类 (1)高温型 80—90℃处理时间为10-20分钟,形成磷化 膜厚达10-30g/m2,溶液游离酸度与总酸度的 比值为1:(7-8) 优点:膜抗蚀力强,结合力好。 缺点:加温时间长,溶液挥发量大,能耗 大,磷化沉积多,游离酸度不稳定,结晶 粗细不均匀,已较少应用。
锰系
Mn(H2PO4)2 和 磷酸锰铁 Fe(H2PO4)2
灰→深灰
锰锌系 Mn(H2PO4)2 和 磷酸锌、磷酸锰、灰→深灰
Zn(H2PO4)2
磷酸铁混合物
铁系 Fe(H2PO4)2
深灰色 5-10
单位面积膜重 / g/m2 1-60
1-15
1-60
1-60
五、磷化工艺流程
除油除锈→水洗→磷化→水洗→磷 化后处理
二、化学成膜的原理:
磷酸二氢盐在磷化溶液中可以发生水解, 使溶液中的铁、锌、锰离子增多。当钢铁 零件放入溶液中,发生一系列的化学反应。 这时硝酸盐起催化作用,加剧磷酸盐与零 件间的作用,使磷酸二氢盐和正磷酸的浓 度不断增加,达到饱和状时,铁、锌、锰 离子便结晶析出而沉定在零件表面上。反 应继续进行,结晶晶粒在零件表面上不断 地长大,磷化膜生成。
析出氢,令界面层磷酸盐不易饱和,导致 晶核形成困难,膜层结构疏松,多孔,耐 蚀性下降,令磷化时间延长。 游离酸度过低,磷化膜变薄,甚至无膜。
3、总酸度 总酸度指磷酸盐、硝酸盐和酸利于加速磷化反应,使膜层晶粒细,磷化 过程中,总酸度不断下降,反映缓慢。 总酸度过高,膜层变薄,可加水稀释。 总酸度过低,膜层疏松粗糙。
1、按磷化处理温度分类
(4)常温型 10-40℃ 常(低)温磷化(除加氧化剂外, 还加促进剂),时间10-40分钟,溶液游离 酸度与总酸度比值为1:(20-30),膜厚为 0.2-7 g/m2。 优点:不需加热,药品消耗少,溶液稳定 。 缺点:处理时间长,溶液配制较繁。
2、按磷化液成分分类
(1)锌系磷化 (2)锌钙系磷化 (3)铁系磷化 (4)锰系磷化 (5)复合磷化 磷化液由锌、铁、钙、镍 、锰等元素组成。