干切削加工刀具及其设计
摘要:干式切削是一种绿色制造工艺技术
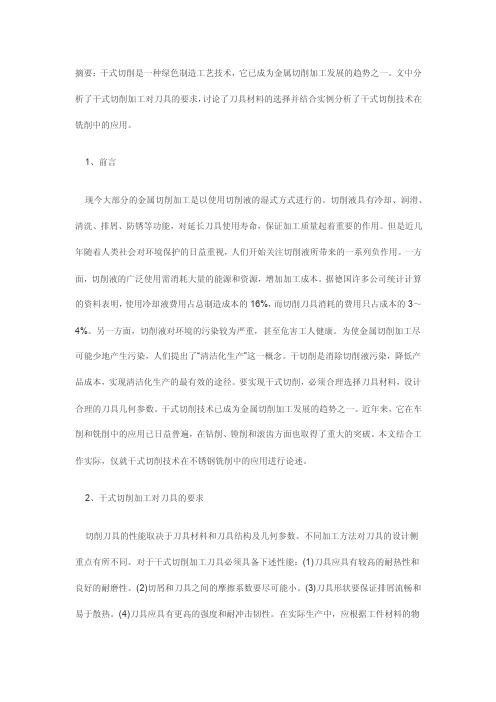
摘要:干式切削是一种绿色制造工艺技术,它已成为金属切削加工发展的趋势之一。
文中分析了干式切削加工对刀具的要求,讨论了刀具材料的选择并结合实例分析了干式切削技术在铣削中的应用。
1、前言现今大部分的金属切削加工是以使用切削液的湿式方式进行的。
切削液具有冷却、润滑、清洗、排屑、防锈等功能,对延长刀具使用寿命,保证加工质量起着重要的作用。
但是近几年随着人类社会对环境保护的日益重视,人们开始关注切削液所带来的一系列负作用。
一方面,切削液的广泛使用需消耗大量的能源和资源,增加加工成本。
据德国许多公司统计计算的资料表明,使用冷却液费用占总制造成本的16%,而切削刀具消耗的费用只占成本的3~4%。
另一方面,切削液对环境的污染较为严重,甚至危害工人健康。
为使金属切削加工尽可能少地产生污染,人们提出了“清洁化生产”这一概念。
干切削是消除切削液污染,降低产品成本,实现清洁化生产的最有效的途径。
要实现干式切削,必须合理选择刀具材料,设计合理的刀具几何参数。
干式切削技术已成为金属切削加工发展的趋势之一。
近年来,它在车削和铣削中的应用已日益普遍,在钻削、镗削和滚齿方面也取得了重大的突破。
本文结合工作实际,仅就干式切削技术在不锈钢铣削中的应用进行论述。
2、干式切削加工对刀具的要求切削刀具的性能取决于刀具材料和刀具结构及几何参数。
不同加工方法对刀具的设计侧重点有所不同。
对于干式切削加工刀具必须具备下述性能:(1)刀具应具有较高的耐热性和良好的耐磨性。
(2)切屑和刀具之间的摩擦系数要尽可能小。
(3)刀具形状要保证排屑流畅和易于散热。
(4)刀具应具有更高的强度和耐冲击韧性。
在实际生产中,应根据工件材料的物理、力学性能和工序特点,合理选用刀具材料、涂层,优化刀具结构和几何参数,并注意刀具材料与工件材料的匹配,才能设计和制造出适用于干式切削的刀具。
1)干式切削加工的刀具材料干式切削时刀具材料最重要的是必须具各高的红硬性和高的耐冲击性。
切削加工中的刀具切削角度优化考核试卷

C.主偏角
D.刀具长度
( )
2.优化刀具的切削角度可以带来以下哪些效果?
A.提高加工效率
B.降低加工成本
C.提高工件表面质量
D.所有上述效果
( )
3.在进行钢料的Байду номын сангаас削加工时,一般前角应设置为什么范围?
A. 5°~10°
B. 10°~15°
C. 15°~20°
D. 20°~25°
( )
4.以下哪种刀具切削角度适用于粗加工?
切削加工中的刀具切削角度优化考核试卷
考生姓名:__________答题日期:__________得分:__________判卷人:__________
一、单项选择题(本题共20小题,每小题1分,共20分,在每小题给出的四个选项中,只有一项是符合题目要求的)
1.以下哪项不是刀具的主要切削角度?
A.前角
( )
7.关于刀具主偏角的描述,下列哪项是错误的?
A.主偏角影响切削力的大小
B.主偏角影响切削温度的高低
C.主偏角越小,切削宽度越大
D.主偏角对切削液的流动无影响
( )
8.以下哪种材料的刀具适合加工高温合金?
A.高速钢
B.硬质合金
C.陶瓷
D.钨钢
( )
9.在进行高速切削时,应如何选择刀具的前角?
A.前角应适当减小
A.刀具角度不当
B.切削速度过高
C.进给量过大
D.刀具磨损严重
( )
20.以下哪些技术可以用于提高切削加工的效率和质量?()
A.高速切削
B.干切削
C.精密切削
D.数控加工
( )
三、填空题(本题共10小题,每小题2分,共20分,请将正确答案填到题目空白处)
cnc刀具工艺知识点总结
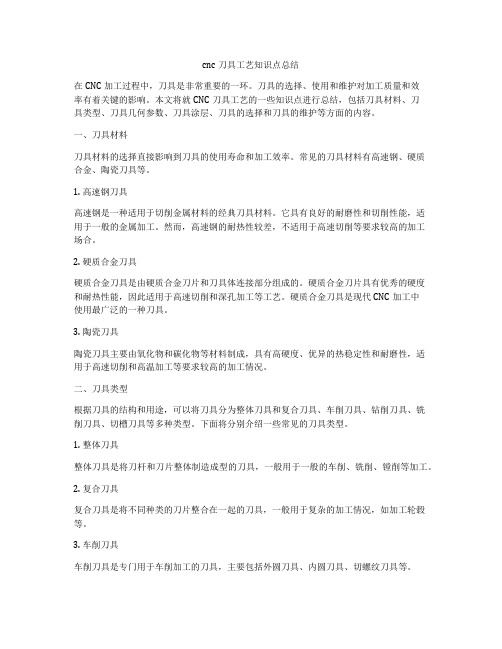
cnc刀具工艺知识点总结在CNC加工过程中,刀具是非常重要的一环。
刀具的选择、使用和维护对加工质量和效率有着关键的影响。
本文将就CNC刀具工艺的一些知识点进行总结,包括刀具材料、刀具类型、刀具几何参数、刀具涂层、刀具的选择和刀具的维护等方面的内容。
一、刀具材料刀具材料的选择直接影响到刀具的使用寿命和加工效率。
常见的刀具材料有高速钢、硬质合金、陶瓷刀具等。
1. 高速钢刀具高速钢是一种适用于切削金属材料的经典刀具材料。
它具有良好的耐磨性和切削性能,适用于一般的金属加工。
然而,高速钢的耐热性较差,不适用于高速切削等要求较高的加工场合。
2. 硬质合金刀具硬质合金刀具是由硬质合金刀片和刀具体连接部分组成的。
硬质合金刀片具有优秀的硬度和耐热性能,因此适用于高速切削和深孔加工等工艺。
硬质合金刀具是现代CNC加工中使用最广泛的一种刀具。
3. 陶瓷刀具陶瓷刀具主要由氧化物和碳化物等材料制成,具有高硬度、优异的热稳定性和耐磨性,适用于高速切削和高温加工等要求较高的加工情况。
二、刀具类型根据刀具的结构和用途,可以将刀具分为整体刀具和复合刀具、车削刀具、钻削刀具、铣削刀具、切槽刀具等多种类型。
下面将分别介绍一些常见的刀具类型。
1. 整体刀具整体刀具是将刀杆和刀片整体制造成型的刀具,一般用于一般的车削、铣削、镗削等加工。
2. 复合刀具复合刀具是将不同种类的刀片整合在一起的刀具,一般用于复杂的加工情况,如加工轮毂等。
3. 车削刀具车削刀具是专门用于车削加工的刀具,主要包括外圆刀具、内圆刀具、切螺纹刀具等。
钻削刀具是专门用于钻孔加工的刀具,主要包括中心钻、旋转钻、铰刀等。
5. 铣削刀具铣削刀具是专门用于铣削加工的刀具,主要包括立铣刀、面铣刀、滚齿刨刀等。
6. 切槽刀具切槽刀具是专门用于切槽加工的刀具,主要包括立式切槽刀、侧面切槽刀等。
三、刀具几何参数刀具的几何参数是刀具设计的关键要素,直接影响着刀具的切削性能和加工质量。
主要包括刀尖半径、刀身倾角、主偏角、切削刃倾角等。
干切削的原理及其应用

干切削的原理及其应用1. 引言干切削是一种常见的金属加工方法,广泛应用于工业生产和制造领域。
本文将介绍干切削的原理以及其在实际应用中的相关技术和优势。
2. 原理干切削是通过将刀具直接应用于金属工件表面,通过摩擦和切削力来移除材料的加工方法。
其主要原理包括以下几个方面:•摩擦力:当刀具与工件表面接触时,由于两者之间的接触面积较小,会产生较大的局部摩擦力。
这种摩擦力将刀具推进并产生切削力。
•切削力:切削力是干切削中最重要的力之一。
它是指刀具在切削过程中对工件施加的力,使刀具能够切削和去除材料。
•热量产生:在干切削过程中,由于摩擦和变形导致能量转化,部分能量会转化为热能。
这些热量会导致材料表面温度升高,可能会影响切削质量和工件表面精度。
3. 应用干切削方法在各个行业和领域都有广泛的应用。
以下是几个常见的应用领域:3.1 金属加工干切削在金属加工领域中被广泛采用。
它可应用于各种金属材料的加工,如钢铁、铜、铝等。
干切削具有高效、精密和灵活的特点,能够满足各种复杂形状和高精度要求的加工需求。
3.2 刀具制造干切削方法在刀具制造过程中也发挥着重要作用。
通过干切削可以对刀具进行精密的修整、修磨和抛光。
这些工艺可以提高刀具的质量和精度,同时延长其使用寿命。
3.3 高精度零件加工在一些对加工精度要求非常高的应用中,如航空航天、汽车制造等行业,干切削被广泛应用于高精度零件的加工。
通过干切削可以实现对工件表面的高精度加工,满足复杂工艺和精密装配的要求。
3.4 快速原型制造干切削在快速原型制造中也有应用。
通过使用干切削技术,可以对原型进行快速加工和制造。
这种方法可以缩短原型开发周期,并降低制造成本。
4. 技术优势干切削作为一种常见的金属加工方法,具有以下几个技术优势:•高效性:干切削方法具有高速切削和高加工效率的特点。
它可以大幅提高工件的加工效率和生产效率。
•灵活性:干切削方法适用于各种金属材料和复杂形状的加工。
它可以满足不同工件加工需求,提供灵活的解决方案。
干式切削
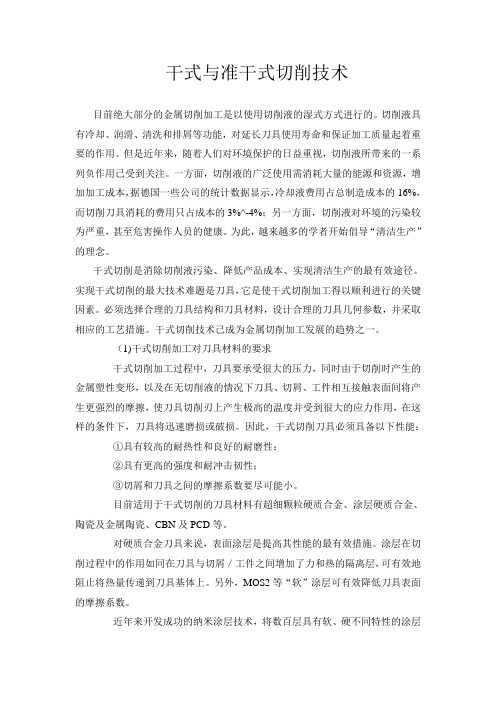
干式与准干式切削技术目前绝大部分的金属切削加工是以使用切削液的湿式方式进行的。
切削液具有冷却、润滑、清洗和排屑等功能,对延长刀具使用寿命和保证加工质量起着重要的作用。
但是近年来,随着人们对环境保护的日益重视,切削液所带来的一系列负作用已受到关注。
一方面,切削液的广泛使用需消耗大量的能源和资源,增加加工成本,据德国一些公司的统计数据显示,冷却液费用占总制造成本的16%,而切削刀具消耗的费用只占成本的3%^-4%;另一方面,切削液对环境的污染较为严重,甚至危害操作人员的健康。
为此,越来越多的学者开始倡导“清洁生产”的理念。
干式切削是消除切削液污染、降低产品成本、实现清洁生产的最有效途径。
实现干式切削的最大技术难题是刀具,它是使干式切削加工得以顺利进行的关键因素。
必须选择合理的刀具结构和刀具材料,设计合理的刀具几何参数,并采取相应的工艺措施。
干式切削技术己成为金属切削加工发展的趋势之一。
(1)干式切削加工对刀具材料的要求干式切削加工过程中,刀具要承受很大的压力,同时由于切削时产生的金属塑性变形,以及在无切削液的情况下刀具、切屑、工件相互接触表面间将产生更强烈的摩擦,使刀具切削刃上产生极高的温度并受到很大的应力作用,在这样的条件下,刀具将迅速磨损或破损。
因此,干式切削刀具必须具备以下性能:①具有较高的耐热性和良好的耐磨性;②具有更高的强度和耐冲击韧性;③切屑和刀具之间的摩擦系数要尽可能小。
目前适用于干式切削的刀具材料有超细颗粒硬质合金、涂层硬质合金、陶瓷及金属陶瓷、CBN及PCD等。
对硬质合金刀具来说,表面涂层是提高其性能的最有效措施。
涂层在切削过程中的作用如同在刀具与切屑/工件之间增加了力和热的隔离层,可有效地阻止将热量传递到刀具基体上。
另外,MOS2等“软”涂层可有效降低刀具表面的摩擦系数。
近年来开发成功的纳米涂层技术,将数百层具有软、硬不同特性的涂层复合叠加,总厚度仅为2^-5卿,既使刀具的硬度和韧性显著增加,又使其具有优异的抗摩擦、抗磨损和自润滑性能,非常适合干式切削。
刀具与量具

刀具与量具在制造业行业中,刀具与量具是非常重要的工具。
刀具主要用于切削加工,并可精细地控制加工精度、表面质量以及工件尺寸。
量具主要用于检测工件的几何形状和尺寸,并反馈给操作者作为加工质量的参考指标。
本文将详细介绍刀具和量具的分类、使用方法、保养以及常见问题解决方法等。
刀具分类在制造业中,根据使用方式、加工材料、使用寿命等因素,刀具可分为多种类型。
下面是各种刀具类型的简单介绍:铣刀铣刀主要用于对工件进行平面或者曲面的加工,通常能够完成高精度的工作。
铣刀形状有不同的种类,如面铣刀、球头铣刀、T型槽铣刀、齿轮铣刀和插刀等。
钻头钻头用于钻孔加工,通常可分为普通钻头和特殊钻头。
普通钻头适用于加工普通材料,而特殊钻头则是根据不同材料的特点设计的。
如陶瓷钻头,硬质合金钻头等。
刀片刀片是切削工具的主要组成部分之一。
根据刀片形状的不同,它们可以分为扁形刀片、圆形刀片、三角形刀片、菱形刀片和槽形刀片等。
刀片的材料也有很多种,如碳化钨、高速钢、陶瓷、CBN等。
车刀车刀可以完成车削、车铣、钻孔等工序,其中较为常用的有内扣车刀、外扣车刀、铰孔刀和车锋刀等。
刀具的使用方法使用刀具时,要注意以下几点:1.确定加工对象,刀具型号规格应与加工对象相适应。
2.选择适当的工艺参数,如切削速度、进给量和轴向进刀量等。
3.确定好切削方向,并合理选择切削油液,以保证切削效果和切削质量。
4.确保切削工具的安装正确,刀片夹紧力度适中。
5.在使用刀具过程中,不得随意更改刀具工艺参数,以免影响整个工艺过程。
刀具的保养刀具保养是确保刀具长期使用寿命的重要环节,正确的保养方法能够延长刀具的使用寿命,减少工作故障和意外损伤的发生。
以下是刀具保养的一些常见方法:1.切削工具二次刃磨:在磨削之前需要对刀具进行清洁,并对切削刃进行合适的磨削角度处理,确保研磨之后的工具具有一定的切削能力。
2.打磨刀片表面:清洗掉污渍并研磨刀片表面,使得表面平整度达到优良的程度。
刀具及切削参数选择
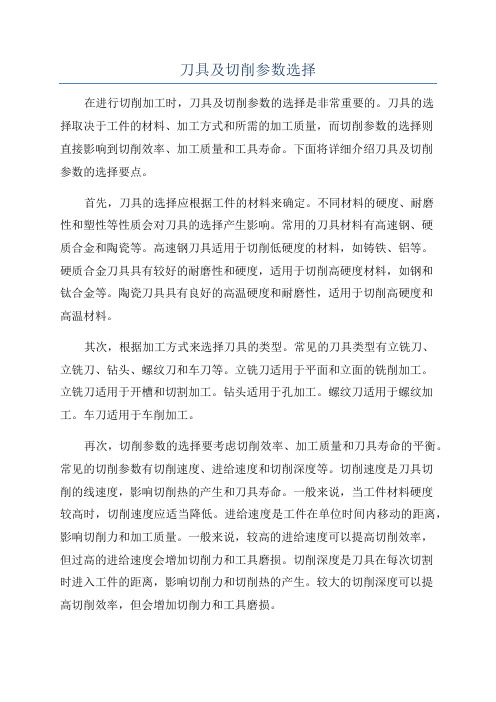
刀具及切削参数选择在进行切削加工时,刀具及切削参数的选择是非常重要的。
刀具的选择取决于工件的材料、加工方式和所需的加工质量,而切削参数的选择则直接影响到切削效率、加工质量和工具寿命。
下面将详细介绍刀具及切削参数的选择要点。
首先,刀具的选择应根据工件的材料来确定。
不同材料的硬度、耐磨性和塑性等性质会对刀具的选择产生影响。
常用的刀具材料有高速钢、硬质合金和陶瓷等。
高速钢刀具适用于切削低硬度的材料,如铸铁、铝等。
硬质合金刀具具有较好的耐磨性和硬度,适用于切削高硬度材料,如钢和钛合金等。
陶瓷刀具具有良好的高温硬度和耐磨性,适用于切削高硬度和高温材料。
其次,根据加工方式来选择刀具的类型。
常见的刀具类型有立铣刀、立铣刀、钻头、螺纹刀和车刀等。
立铣刀适用于平面和立面的铣削加工。
立铣刀适用于开槽和切割加工。
钻头适用于孔加工。
螺纹刀适用于螺纹加工。
车刀适用于车削加工。
再次,切削参数的选择要考虑切削效率、加工质量和刀具寿命的平衡。
常见的切削参数有切削速度、进给速度和切削深度等。
切削速度是刀具切削的线速度,影响切削热的产生和刀具寿命。
一般来说,当工件材料硬度较高时,切削速度应适当降低。
进给速度是工件在单位时间内移动的距离,影响切削力和加工质量。
一般来说,较高的进给速度可以提高切削效率,但过高的进给速度会增加切削力和工具磨损。
切削深度是刀具在每次切割时进入工件的距离,影响切削力和切削热的产生。
较大的切削深度可以提高切削效率,但会增加切削力和工具磨损。
此外,还应考虑冷却润滑剂的选择和使用。
合适的冷却润滑剂可以降低切削热的产生,减小工具磨损,提高加工质量。
综上所述,刀具及切削参数的选择需要考虑工件材料、加工方式和所需加工质量。
合理选择刀具类型和切削参数可以提高切削效率、加工质量和工具寿命。
在实际应用中,还需要根据具体情况进行调整和优化。
干式切削加工技术及其应用
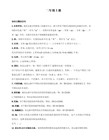
2009-5-18
id=zoom>制造业是产生工业污染的主要来源之一,其中传统加工所使用的切削液给环境造成了严重的污染。随着人们对环境保护的日益重视,尤其是环境保护法规的严格实施,对制造业产生的环境污染提出了更高的要求。一种能减少对环境污染、节约资源和能源的绿色制造技术——干切削加工技术,越来越受到人们的重视。近年来,许多发达国家在工厂条件允许的情况下正积极地采用干式切削加工技术,以达到减少切削加工 的润滑污染、降低加工成本的目的。
低温冷风切削
低温冷风切削的概念是由日本人横川和尹首先提出来的是一种在-10~-100℃冷风冷却和非常微量的植物油润滑条件下进行干式切削的技术。有关研究表明,在刀具表面涂一层薄薄的植物油,在切削加上点进行低温冷风冷却,其干式加工的效果很理想。如,在切削条件为:工件直径:?92~?98mm;切削速度45.1~48.Om/min;进给 O.5mm;切削余角:45°;刀具:刀具半径RO.4mm, SKH高速钢不重磨刀片的试验结果:以刀具后刀面磨损宽度达0.2mm为评价严重磨损的指标的话,完全干式切削时刀具切削长度为1000mm、只供给 Acc-Lube精密润滑油的刀具切削长度为1500mm、只用-12℃的冷风,切削长度为2000mm、在供给-12℃冷风的同时,在切削部位注入 1ml/h的Acc-Lube精密润滑油,切削长度为4000mm。
1 干式切削加工相关技术
干式切削加工技术是在无冷却或少许润滑油、剂的条件下,采用高切削速度进行切削加工的方法。在于式切削条件下,失去切削液、冷却、清洗、排屑的作用,切削条件非常恶劣。在切削区域会产生大量的切削热将无法及时的散发,温度和切削力大幅度上升,摩擦力增大,刀具磨损加快,生产效率降低。因此要使干式切削加工工艺得到很好地推广,充分发挥其优势,克服其缺点,就必须要很好地解决干式切削加工相关地技术难题。
- 1、下载文档前请自行甄别文档内容的完整性,平台不提供额外的编辑、内容补充、找答案等附加服务。
- 2、"仅部分预览"的文档,不可在线预览部分如存在完整性等问题,可反馈申请退款(可完整预览的文档不适用该条件!)。
- 3、如文档侵犯您的权益,请联系客服反馈,我们会尽快为您处理(人工客服工作时间:9:00-18:30)。
干切削加工刀具及其设计合肥工业大学刘志峰摘要适宜的刀具材料和刀具几何参数是干切削加工的关键条件之一。
文章在分析干切削加工对刀具要求的基础上,阐述了干切削刀具设计的要点,并结合应用实例说明了刀具设计对干切削加工的重要性。
关键词干切削刀具设计加工技术工艺方法1概述随着环境保护法律法规越来越严格,国外在汽车以及中小型制造业中,干切削的应用越来越广泛,目前在西欧已有近一半企业采用了干式切削加工,德国企业尤为普遍[2]。
日本的5生产设备市场6杂志选出的1997年日本工厂自动化行业的国内十大新闻中就包括/保护环境的加工技术具体化0。
由此可见:干切削加工技术将成为未来加工技术的发展方向之一。
干切削并不是简单地取消切削液就能实现,有意义且经济可行的干切削加工要求仔细分析特定的边界条件和掌握干切削加工的复杂因素,并为干切削工艺系统的设计提供所需的技术数据。
干切削加工刀具工作条件恶劣,寿命缩短。
因此,须合理选择刀具材料及涂层,设计合理的刀具几何参数。
本文分析干切削加工的特点,提出了干切削对刀具的具体要求,讨论了干切削刀具的设计要点。
2干切削加工对刀具的要求干切削加工就是要在没有切削液的条件下创造具有与湿切相同或相近的切削条件。
因此,对刀具提出了更高的要求。
(1)刀具应具有优异的耐高温性能目前的刀具材料,如新性能硬质合金、聚晶陶瓷和CBN等有足够的耐高温磨损性能,能够在干切削条件下使用。
此外,最有效的方法就是对刀具进行涂层。
涂层在切削过程中的作用如同在刀具与切屑之间增加了一道力和热的隔离层,可阻止将热量传递到刀具基体,因而能保证刀具切削刃锋利,使刀头硬度不会很快下降,可大大提高其耐高温性能。
生产实践证明,尽管在干切削中还不能将切削区产生的热量完全随切屑排出,但只要合理选择刀具几何形状、切削参数,将能使绝大部分切削热随切屑排出,取得良好的加工效果。
[1]。
(2)切屑和刀具之间的摩擦系数要尽可能小干切削加工时,在切削区产生的高温产生化学不稳定性、刀具与切屑之间的摩擦增大、排屑速度减慢,极易产生积屑瘤,加剧刀具磨损。
因此,须减小切屑和刀具之间的摩擦系数,最有效的方法就是进行刀具表面涂层,并设计排屑良好的刀具结构。
如大螺旋角T iAlN涂层丝锥就是具有这种性能的干切削刀具。
(3)刀具的结构要能快速排屑干切削加工中,为了保证工件加工质量和刀具寿命,要求刀具能快速排出切屑,使传入工件和刀具的热量大大减少。
(4)刀具应有更高的强度和耐冲击韧性选择适宜于干切削的刀具材料,如超细晶粒硬质合金、陶瓷和金属陶瓷刀具材料、金刚石和CBN等,也可在高速钢、硬质合金基体上进行适宜的涂层,如T iAlN涂层、T iCN涂层、T iAlN+MoS2涂层、类金刚石DLC(Diamond-Like-Carbon)涂层等。
金刚石和CBN可用于干切铸铁、过共晶铝合金、各种钢和钛合金等。
3干切削刀具设计要点及应用311干车(铣)刀具设计要点干切削刀具通常以月牙洼磨损为主要失效原因,这是因为加工中刀具与切屑接触区域的温度升高所致。
因此,通常应使刀具有大的前角和刃倾角。
但前角增大后,刀刃强度会受影响,此时应配合以适宜的负倒棱或前刀面加强单元,使刀尖和刃口有足够体积的材料和较合理的方式承受切削热和切削力,减缓冲击和月牙洼扩展,使刀尖和刃口可在较长的切削时间里保持足够的强度。
此外,配合大的刀尖前角和刀尖后角,可使刀具刃口楔角增大,减少刀具与已加工表面之间的接触长度,有效降低后刀面的磨损和破损几率。
采用如图1所示的几何形状刀片,可大大减小刀具与切屑之间的接触面积,使切屑带走大量热量。
图2为干切削和普通车、铣的加工过程示意图。
由图可见,当切屑流过普通刀片前刀面时,由于接触面积大,#20#5制造技术与机床6传入刀具的热量多,从而产生月牙洼磨损,降低刀具寿命;而采用图1所示的刀片,刀具前刀面上有加强棱,刀具与切屑的接触面积也大大减小,绝大部分热量被切屑带走,切削温度可比普通刀片降低约400e ,同时也增大了剪切角,使刀具寿命显著提高,可允许采用更高的切削速度,提高了生产效率,若保持普通的切削速度,则刀具寿命可提高3~4倍。
图1 干铣刀片的几何形状对于陶瓷刀具,由于脆性较大,因此,可以选用T 型或双T 型棱面,或者研磨,或几种方法组合。
如美国Valenite 公司推荐将0.5@30b 的T 型棱面用于Al 2O 3+TiC 刀片,干式加工淬硬钢,并尽量采用大的余偏角。
根据不同刀片几何形状,半精车时的刀具余偏角为-5~30b ,常用的刀片几何形状是正方形、三角形和80b菱形。
图2 干切削和普通切削的加工过程比较对CBN 刀具,倒棱太大,加工淬硬钢时,在刀具与工件接触处产生高温使刃口很快磨损。
因此,一般不采用大倒棱,刃口可采用斜面或倒圆及负前角,尽可能大的余偏角。
建议取值范围为:(15b ~25b )@0.25mm 的T 型倒棱,再进行0101~0.03mm 的研磨。
312 干式螺纹加工刀具设计要点目前,在用丝锥攻丝时,以采用含有机氯化物抗极压的乳化液效果最好。
但有机氯化物对环境污染很大。
德国Emuge 螺纹刀具厂为减少环境污染,研制开发了&O KO 丝锥,即生态有利丝锥,它可在较广范围的材料上攻丝而无须切削液。
为了完成干式攻丝,在丝锥参数设计时必须考虑:(1)有小的摩擦阻力,以获得尺寸准确和表面粗糙度值小的螺纹;(2)槽型设计应使切屑易于卷曲,并自由离开螺孔;(3)对丝锥表面进行涂层处理,以获得理想的表面状态,减小切削应力,保护丝锥。
这种丝锥的尺寸范围有两种,即M 5~M10的加强柄尺寸系列和M 12~M20的尺寸系列。
干切削加工钢件螺纹的丝锥其槽型通常为螺旋槽,加工通孔螺纹和盲孔时的螺旋角大小不同。
如加工盲孔螺纹时,往往采用35b 的大螺旋角;当孔深大于2倍丝锥直径时,可采用小螺旋角,通常5b ,此时丝锥切削锥部长度为C/2~3牙。
而干切削加工铸铁螺纹时,无论是通孔还是盲孔,丝锥槽型均为直槽,其切削锥部长度为C/2~3牙。
对于小直径丝锥,为了提高强度和刚度,其槽型也可设计成特殊形状,如无槽挤压丝锥。
无槽挤压丝锥用于加工小直径螺纹或塑性较大材料上的螺纹是非常有效的。
干切削加工丝锥通常均需进行涂层处理,常用的涂层有TiN 或TiCN 。
图3a 是用无槽挤压丝锥干式挤压螺纹与有切削液挤压螺纹的加工螺纹孔数量比较。
由图可以看出,普通挤压丝锥加工100个螺纹孔时,切削部分的螺纹牙型就产生粘结现象,与此相比,干式挤压丝锥寿命可提高80倍。
图3b 则是湿式攻丝与干式攻丝所加工的螺纹孔数比较。
由于受到试验试件数量的限制,仅作了有限次试验,但其结果反映了干式攻丝的可能性。
(a) (b)加工条件:M 6@1)G7P 试验条件: 通孔螺纹M 5@018丝锥工件材料:锌钢板,工件材料:纯铝Ly-2 螺纹长度312mm 螺纹孔形状:盲孔,底孔直径:Á5155mm,螺纹长11mm切削速度:15m/min底孔直径:412mm(切削), 415mm(挤压)切削速度:15m/min(切削), 10m/min(挤压)机床:AG )32图3 干式与湿式加工比较除此之外,笔者对在A3、45钢等薄板件(厚2mm 以下)上加工螺纹的工艺进行了探讨,采用了新型底孔成孔工艺,并成功地应用了干式切削及挤压螺纹工艺,采用专门设计和制造的底孔成型刀具和涂层挤压丝锥可使底孔和螺纹的加工同时完成,避免了原有工艺需要焊接螺母或设计制造专用模具冲孔的麻烦,解决了长期困扰汽车、钣金等行业的薄板件螺纹加工工艺,并有优异的加工效果。
#21#1999年第8期蜗形凸轮分度机构接触线载荷分布研究燕山大学闻岩周玉林摘要利用切片法,推导出蜗形凸轮机构接触线轴线方向上的载荷分布公式,为按强度设计及润滑分析等提供理论基础。
关键词蜗形凸轮机构载荷分布蜗形凸轮机构是一种高速分度间歇机构。
随着自动化机械发展,该机构越来越被重视。
机构的啮合原理及运动分析已趋于成熟,但机构的受力分析尚待发展。
虽然常被用于分度,但由于机构分度速度很高,动载荷很大,所以有必要对该机构进行受力及强度分析。
在分度段内,机构的主、从动件间相当于圆柱体与空间曲面接触,接触线为一个时刻变化的空间曲线,无法用赫兹公式进行计算。
本文用切片法对该机构在接触线上力的分布作一分析,导出沿接触线上的力分布公式,为强度及润滑特性等分析奠定了理论基础。
1坐标系及参数图1所示,以从动盘的中心为原点建立一静坐标系o-x yz,z轴为回转轴。
在从动盘上建立一个随从动盘转动的动坐标系o1-x1y1z1。
在凸轮上建立随凸轮转动的动坐标系o2-x2y2z2,z2轴为回转轴。
由于中心距a是尺寸及受力等计算分析的主要影响参数,为便于分析,这里定义几个系数,它们都以a为基准。
设分度盘半径为S0,滚子长为L,滚子半径为r,定义:盘径系数k D=S0/a,滚长系数k L=L/a,滚径系数k r=r/a。
图12计算模型的建立切片法是60年代末期提出的关于设计滚针轴承鼓度的理论计算法,广泛用于轴承业,是一种比较成功的方法。
本文将切片法用于蜗形凸轮机构受力分析之中,并变离散化为连续化。
根据资料[2]的基本内容,假设沿滚子轴向将滚子切成n个薄片,在载荷作用下片间的切应力对表面的影响很小,可以忽略。
变形主要在接触表面附近发生,4结语刀具干切削加工一方面要选择合理的刀具材料并进行适宜的表面涂层;另一方面须具有合理的刀具结构参数。
根据国外成功应用实例并结合笔者的研究表明:只要条件选择适当,在我国现有技术条件下,它的干切削加工是可以实现的。
干切削加工是一种理想的绿色制造工艺方法。
虽然目前干切削加工的应用范围不是很广泛,但对它的研究却已成了目前的热点之一。
国外的应用研究比较广泛,主要是迫于有关法律法规的严格要求和对干切削加工前景的看好,某些成功应用示范,推动了干切削加工技术的发展。
国内对干切削加工目前尚有不同看法,但从发展的角度看,干切削的应用是必然的趋势。
参考文献1薛儒编译1干式切削技术的使用条件1刃具研究,1997(5)2山形俊一1无给油用Í}Ë ¤·1机械H工具,1996,56(4)67-703王西彬1陶瓷刀具干切削淬硬钢的研究1工具技术11998(2)4吴元昌1&O KO丝锥及其攻丝扭矩1刃具研究,1997,15(4)5刘志峰1挤压丝锥CAD1工具技术,1997,28(11)6刘志峰1干切削加工技术的发展及应用1机械制造,1997(9)7刘志峰1干切削加工刀具材料及涂层应用1机械研究与应用,1998(3)作者:刘志峰,合肥市合肥工业大学机械系,邮编: 230009(编辑姜学文)(收稿日期:1998)08)26)#22#5制造技术与机床6。